
Учебное пособие 800196
.pdfстатора, пазы, отверстия под вал, вентиляционные каналы и т.п.). Технологическими приемами они могут быть уменьшены, например, путем использования их для изготовления более мелких листов (например, лист ротора на последовательном штампе получают из внутреннего отхода листа статора). Однако такие возможности часто бывают ограничены.
Внешние отходы связаны с несоответствием геометрической формы сортамента стали (прямоугольник) с формой внешнего контура листа магнитопровода. Эти отходы, хоть и называют иногда «технологическими», могут быть уменьшены приближением внешнего контура листов к прямоугольнику. Тем не менее – внешние отходы определяются также чисто технологическими решениями: припуском на штамповку, картой раскроя сортамента и т.п.
Совместным трудом конструкторов и технологов отходы электротехнической стали сведены к определенному минимуму, однако проблема продолжает оставаться острой. На предприятиях отрасли до половины деловой электротехнической стали уходит в отходы, цена их снижается в десять и более раз по сравнению со стандартным сортаментом. Поэтому актуальным является поиск новых путей решения проблемы, позволяющих экономить ценный материал.
В этой связи привлекает внимание опыт образования магнитопровода из порошкового железа по так называемой порошковой технологии /25/. Суть способа состоит в том, что в качестве исходного материала используется железо в виде порошка, которому путем холодного прессования в форме придают необходимую конфигурацию магнитопровода. Прессование порошкообразного железа при достаточно большом давлении (до 9 т/см2) приводит к тому, что между частицами материала возникают силы молекулярного сцепления. Это позволяет сформовать из порошкообразного материала монолитную деталь. Для примера на рис.35 показано получение цилиндрической детали из порошкового материала. Полость матрицы 1 прессформы заполняют порошком 2 «внатрус» до самых краев. После этого пуансон 3, перемещаясь вниз, входит в отверстие матрицы и сдавливает порошок с необходимым усилием. Готовая деталь извлекается из отверстия матрицы движением вверх выталкивателя 4. Требуемые усилия прессования достигаются применением гидравлического привода.
71
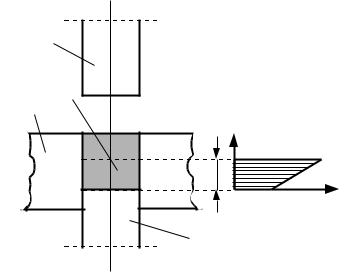
3 |
|
2 |
|
1 |
|
|
x |
l |
|
|
p |
4 |
|
Рис. 35. Формовка детали из порошкового материала
Механические детали, полученные способом порошковой технологии, обычно дополнительно упрочняют последующим спеканием, например, индукционным нагревом. Однако, этот прием неприменим при изготовлении магнитопровода, так как приводит к увеличению потерь от вихревых токов. Приемлемые результаты по достижению требуемой механической прочности магнитопровода дает добавка к железному порошку полимерного связующего или пропитка порошкового магнитопровода лаком или компаундом в ультразвуковой установке.
Получение магнитопровода способом порошковой технологии может быть усовершенствовано предварительной прокаткой порошка в стальных валках. В результате частицы железного порошка приобретают форму плоских чешуек. При заполнении таким материалом полости матрицы прессформы «в натрус» большая часть чешуек ориентируется параллельно друг к другу. Обеспечивается своеобразная «микрошихтовка» магнитопровода. Это позволяет повысить его магнитную проницаемость в требуемом направлении.
Порошковая технология, однако, имеет некоторые особенности, что требует особых подходов как при конструировании самих деталей, так и при проектировании оснастки и выборе режимов прессования. Часть усилия, развиваемого пуансоном при прессовке, расходуется на преодоление сил трения между частицами порошка и стенками полости матрицы. Поэтому усилие прессовки, возникающее в прессуемом материале, уменьшается по мере удаления от торца пуансона. В приведенном на рис. 34. примере распределение усилия в прессуемом материале по высоте детали показано справа в виде эпюры, где - высота готовой детали, x – осевая координата, р – удельное усилие в материале. Неравномерность прессующего усилия возрастает с увеличением отношения высоты детали к ее поперечному размеру, что приводит к неоднородности механических свойств детали. Этот недостаток в
72
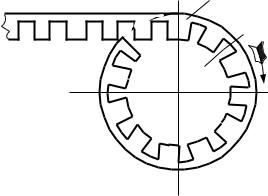
определенной мере можно уменьшить путем встречного прессования, когда части 3 и 4 прессформы одновременно движутся навстречу друг другу.
Неравномерность усилия прессования возрастает с усложнением геометрической формы детали, что характерно для большинства магнитопроводов электрических машин. Поэтому применение порошковой технологии требует особых подходов к обеспечению технологичности конструкции магнитопровода. В промышленности освоено производство двухполюсного магнитопровода статора коллекторного электродвигателя переменного тока для бытового пылесоса. Испытание этого изделия показало, что по своим параметрам оно полностью отвечает предъявляемым требованиям.
Еще одним недостатком способа является повышенный износ прессформы (стенок матрицы), что требует применения для нее специальных материалов, оптимизации режимов прессовки.
Перспективным следует считать способ изготовления магнитопровода навивкой стальной ленты на цилиндрическую оправку с изгибом ее на ребро /26/. Стальная лента 1, ширина которой равна
1
2
Рис. 36. Навивка магнитопровода статора: 1 – стальная лента; 2 – оправка.
радиальному размеру магнитопровода, обрабатывается пазовым штампом на автоматическом прессе, в результате чего с одной стороны образуются пазы (рис. 36). Затем эту ленту, изгибая на ребро, навивают на цилиндрическую оправку 2 (заштриховано). Направление вращения оправки на рисунке показано стрелкой. При таком способе очень важно обеспечить решение ряда чисто технологических задач: совпадение пазов с образованием гладких стенок, обеспечение устойчивого изгиба ленты на ребро, предотвращение «раскручивание» изделия под действием упругих сил. Решение этих задач зависит от многих факторов, в том числе от конкретной конструкции магнитопровода. В частности, практикуется согласование пазов путем применения специальных шпонок на оправке 2, скрепление соседних витков с помощью пуклевок фиксация готового магнитопровода сварными швами или стальными гильзами. Напряжения упругих сил и наклеп могут быть сняты темообработкой.
73
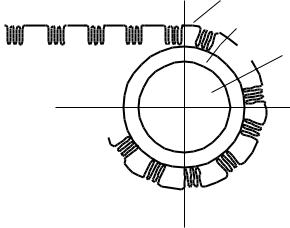
Следует отметить, что навивкой ленты с изгибом ее на ребро можно выполнять непрерывную заготовку с последующим ее делением на отдельные детали. Способ удобнее применять для получения магнитопроводов статора многополюсных машин с относительно невысокой спинкой.
1
2 3
Рис. 37. Получение зубцовой зоны ротора путем гофрирования стальной ленты: 1 – гофрированная лента; 2 – ярмо; 3 - вал
Привлекает внимание способ получения зубцовой зоны магнитопровода путем гофрирования стальной ленты /26/. Ширина ленты при этом выбирается равной осевой длине магнитопровода. Принцип получения зубцов путем гофрирования стальной ленты ясен из рис.37. В показанном на рисунке примере на вал 3 с изгибом на ребро стальной ленты намотано ярмо 2, на котором из гофрированной ленты 1 образована зубцовая зона. После сборки на роторе образуется короткозамкнутая обмотка путем заливки пазовой зоны алюминием. Способ обеспечивает практически безотходное использование электрической стали. Кроме этого образование зубцовой зоны путем гофрирования стальной ленты обеспечивает получение в пазах гладких стенок, позволяет полностью отказаться от вырубной штамповки, открывает новые возможности оптимизации конструкции электрической машины.
ГЛАВА V. ПРОИЗВОДСТВО КОЛЛЕКТОРОВ
5.1. Конструкции коллекторов
Важной и весьма сложной с технологической точки зрения частью многих электрических машин является коллектор. Его технологическая сложность заключается, с одной стороны, в том, что он состоит из большого количества деталей, выполненных из материалов очень различными физическими и технологическими характеристиками. При этом ставится задача высокой геометрической точности коллектора. С другой стороны – в процессе эксплуатации коллектор подвергается различного рода воздействием, еще более затрудняющим решение задачи обеспечения высокой геометрической точности коллектора. В первую очередь к таким воздействиям следует отнести широкий диапазон температур (от –650 до +1500С), высокие окружные скорости,
74
воздействия центробежных и вибрационных сил, токовые нагрузки, напряженная коммутация (до двух баллов).
Термопластичность изоляционных деталей коллектора наряду с высокими рабочими температурами и действующими силами создают предпосылки для возникновения необратимых деформаций его внешней цилиндрической поверхности. Это приводит к нарушению стабильности скользящего контакта между щеткой и коллектором, что вызывает повышенное искрообразование, расстройство коммутации, нарушающее нормальную эксплуатацию электрической машины.
Обеспечение стабильности формы внешней активной поверхности коллектора, его высокой надежности в течение заданного срока эксплуатации – задача, которая решается как технологическими, так и конструктивными мерами.
Важным требованием, предъявляемым к коллектору, является обеспечение безыскрового токосъема с его вращающейся поверхности. Это предъявляет определенные требования к состоянию поверхности коллектора, к материалам контактной пары «щетка-коллектор», к износоустойчивости активной поверхности коллектора и щеток. Выполнение этого требования связано не только с наличием износа, обусловленного механическим трением, но и с так называемым электроэрозионным износом. Скорость последнего связано не только с материалом компонентов «щетка-коллектор», но и с условиями их работы, в первую очередь – наличием искрения.
Искрообразование на коллекторе, как известно /27/, обусловлено многими факторами, среди которых выделим наиболее связанные с технологией производства: биение и искажение формы внешней цилиндрической поверхности коллектора; радиальное смещение отдельных пластин; неравномерность шага контактных пластин по окружности коллектора. Важным фактором, определяющим длительность и надежность эксплуатации коллектора, является надежная изоляция между отдельными пластинами, а также – относительно корпусных деталей.
Серьезной задачей производства коллектора является экономное расходование дорогостоящих материалов. Это относится, прежде всего, к активным материалам: меди и изоляции. Решается эта задача как конструктивными решениями, так и оптимизацией технологического процесса. При этом одновременно учитывается возможность наиболее рациональной утилизации отходов.
Многообразие и противоречивость специфических требований к конструкции и технологии производства коллектора привели к тому, что в настоящее время в электрических машинах используется множество различных исполнении коллектора. Они отличаются как по своей конструкции, так и процессами изготовления. Среди них чаще всего встречаются /27, 28/: арочные коллекторы (с нажимными конусами и изоляционными манжетами); коллекторы монолитной конструкции; коллекторы щелевой конструкции, коллекторы на пластмассе и др.
75
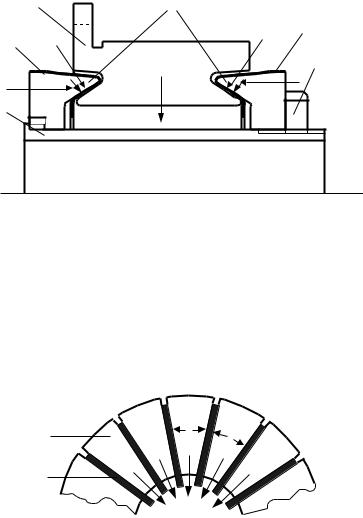
Коллекторы арочного типа, содержащие нажимные конуса и изоляционные манжеты, получили наиболее широкое распространение. Один из возможных вариантов такой конструкции показан на рис. 38. Здесь на втулке 1 размещены нажимные конуса 3, между которыми располагается пакет коллекторных пластин 2. Коллекторные пластины отделены от конусов изоляционными манжетами 4. Конуса стянуты в осевом направлении гайкой 5. Усилие стяжки передается на коническую поверхность, образуемую пакетом коллекторных пластин (показано стрелками pn).
|
2 |
3 |
|
|
|
|
4 |
4 |
pn |
|
pn |
|
|
||
|
|
|
5 |
Q0 |
рN |
Р |
Q0 |
рN |
|||
1 |
4 |
|
4 |
|
|
|
Рис. 38. Коллектор арочного типа: 1 – втулка; 2 – коллекторная пластина; 3 – нажимные конуса; 4 – манжета; 5 – гайка.
Равнодействующая сила Р действует на коллекторные пластины в направлении к оси коллектора, образуя так называемый арочный распор между каждой парой соседних пластин. Образование арочного (бокового) распора показано на рис. 39.
Pб Pб |
P |
б P |
|
1 |
|
б |
|
|
|
|
2
P1
Рис. 39. Образование распора в пакете коллекторных пластин: 1 – коллекторная пластина; 2 – миканитовая прокладка.
. Силы, действующие на каждую коллекторную пластину (стрелки P1), вследствие клинообразной формы пластин прижимают их друг другу боковыми сторонами с усилием рб, которое и называют арочным (или боковым) распором.
Усилие бокового распора является важным конструктивным и технологическим параметром арочного коллектора. Если аксиальное давление,
76
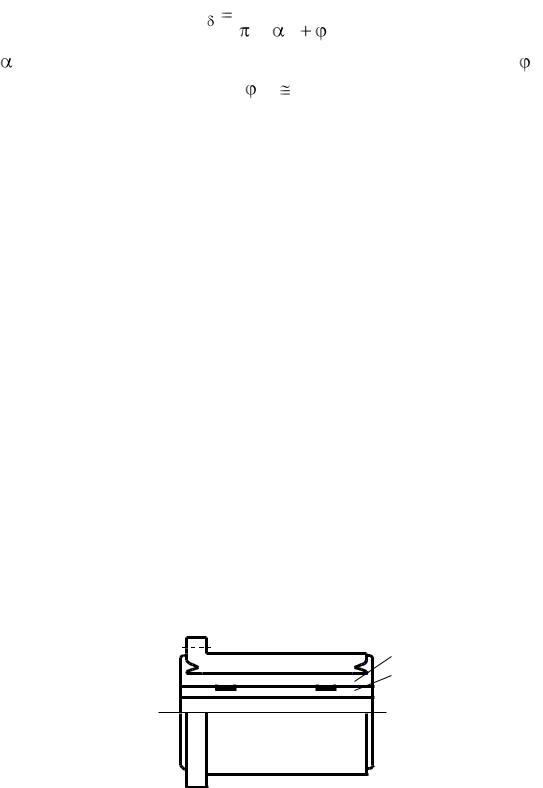
приложенное к нажимным конусам, обозначить Q0, то давление между соседними пластинами можно вычислить, как /27/:
p |
Q0 |
|
(18) |
|
|
||
|
tg( k |
си )F |
где: k - угол наклона опорной грани пластины к оси коллектора; си - угол
трения меди по миканиту (обычно |
си |
80); F – площадь боковой поверхности |
|
|
пластины.
Таким образом, коллекторные пластины клиновидной формы, образуя в пакете круговую арку, сжаты между собой боковыми поверхностями с усилием (18), что обеспечивает механическую прочность, стабильность формы и жесткость коллекторного пакета.
Пластины 1 (рис. 39) изолированы друг от друга коллекторными прокладками 2, которые чаще всего выполняются из коллекторного миканита. Таким образом, боковой распор действует между соседними коллекторными пластинами через миканитовые прокладки, что необходимо учитывать в технологическом процессе.
Известно много вариантов конструкций /27/ арочных коллекторов: со стяжными болтами; с бандажными кольцами; с пружинными и др. В основе всех этих конструкций лежит образование коллекторными пластинами круговой арки с боковым распором между ними. Арочные коллекторы широко используются в электрических машинах. Однако им свойственны ряд недостатков, что вынуждает разработчиков искать другие решения. В первую очередь следует назвать большое количество сопрягаемых поверхностей, требующих специальной обработки. Необходима тщательная обработка конических поверхностей коллекторного пакета, сопрягаемых через манжеты с нажимными конусами. Особого внимания требует при производстве, эксплуатации и ремонте равномерность распределение усилий рn (рис. 38) и p
(рис. 39) между всеми коллекторными пластинами, что обеспечит стабильность формы и его надежность в эксплуатации. Определенные проблемы имеются с обеспечением изоляции между пластинами и относительно нажимных конусов.
1
2 3
Рис. 40. Коллектор с пластмассовым корпусов:
1 – коллекторная пластина; 2 - пластмасса; 3 – втулка.
Все более широкое распространение получают коллекторы с пластмассовым корпусом, у которых указанные недостатки или отсутствуют,
77
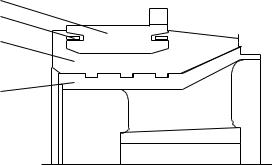
или же существенно ослаблены. Конструкция простейшего коллектора на пластмассе показана на рис. 40.
Пакет коллекторных пластин 1 запрессован в пластмассовый корпус 2, армированный стальной втулкой 3. Пластмассовый корпус получают путем заполнения разогретым пластиком специальной прессформы, в которой предварительно размещают пакет коллекторных пластин. Поэтому сопрягаемые с корпусом поверхности коллекторного пакета не требуют специальной точной обработки. В ряде конструкций удается избавиться и от миканитовых прокладок между пластинами, заменив их тем же пластиком. Таким образом, коллектор на пластмассе оказывается намного технологичнее и, следовательно, дешевле. Стальная втулка 3 позволяет обеспечить сопряжение коллектора с валом по требуемой посадке. В малых электрических машинах удается решить эту задачу без армирующей втулки, что еще больше повышает технологичность конструкции.
Для быстроходных или крупногабаритных машин коллектор с пластмассовым корпусом дополнительно снабжается стальными бандажными кольцами или специальными армирующими деталями. Вариант последней конструкции показан на рис. 41, где дан осевой разрез коллектора тягового электродвигателя электровоза. На выточки медных пластин 1 насажены с предварительным натягом изолированные армирующие кольца 2. Эти кольца создают арочный распор в пакете коллекторных пластин и уменьшают напряжение в пластмассовом корпусе 3 коллектора. Коллектор крепится на валу посредством специальной стальной втулки 4 с аксиальными охладительными каналами.
1
2
3
4
Рис.41. Коллектор с пластмассовым корпусом и армирующими кольцами: 1 – коллекторная пластина; 2 – армирующее кольцо;
3 – пластмасса; 4 – втулка
Однако широкому распространению коллекторов с пластмассовым корпусом препятствуют присущие им недостатки. Так, применяемые здесь стеклопластики АГ – 4 обладают резко выраженной анизотропией, в связи, с чем они иногда плохо воспринимают растягивающие усилия, которые порой превышают предел упругости /27/. Кроме этого, пластики плохо реагируют на
78
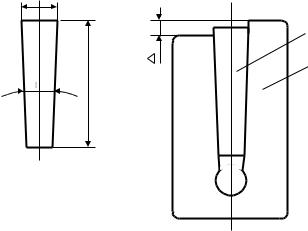
большие перепады температур, которые возникают, например, при пайке выводов. Эти и другие причины вынуждают искать другие конструктивнотехнологические решения. В этой связи следует упомянуть коллекторы щелевой конструкции. Здесь пластмассой заполняют узкий зазор, образуемый между пакетом коллекторных пластин и корпусом коллектора /27/. Применение коллекторов щелевой конструкции подтвердило их высокую технологичность при производстве и стабильность при эксплуатации.
Перечисленные примеры конструкции коллекторов, безусловно, не охватывают все исполнения, применяемые в электрических машинах. Но они обладают всеми необходимыми признаками, позволяющими раскрыть типовые технологические процессы их производства.
5.2. Материалы для активных частей коллекторов
Решение всего комплекса перечисленных выше задач производства и эксплуатации коллекторов требует для изготовления их активных частей применения специальных материалов. Для изготовления коллекторных пластин чаще всего используется медь М1. В скоростных машинах коллекторные пластины изготавливают из кадмиевой меди (до 1% кадмия). В специальных электрических машинах, большей частью в машинах малой мощности, используют медь с присадкой серебра, циркония и др.
В качестве сортамента меди используются холоднотянутые шины трапециевидного сечения. На рис. 42,а) представлено сечение сортамента коллекторной меди, на котором показаны обычно оговариваемые размеры. Стандарт на сортамент устанавливает лишь градацию размеров без их номинального значения. Так, толщина профиля «а» принимается кратной 0,01 мм, а его высота h – кратной 0,5 мм.
а) |
б) |
a |
|
|
1 |
|
h |
|
2 |
|
h |
Рис. 42. Коллекторная медь: а) форма сечения; б) входной контроль
79

При этом конкретные размеры профиля должны быть оговорены в заказе, так как они тесно увязаны с геометрией коллекторного пакета конкретного коллектора.
Точность размеров профиля имеет важное значение для качественной сборки коллекторного пакета. Поэтому на предприятии часто предусматривают входной контроль поступающего от изготовителя сортамента. Контроль производится предельным шаблоном в виде стальной пластинки с пазом (рис. 42, б). Шаблон 2 совмещается с коллекторной медью 1, с легким нажатием. Боковые грани должны плотно прилегать к стенкам паза шаблона. Профиль меди считается годным, если его верхняя сторона находится в пределах указанного на рисунке интервала h .
Отклонение размера «а» предусматриваются со знаком «минус» (см. таблицу), что обеспечивает при сборке коллекторного пакета смыкание коллекторных пластин в области их нижнего края. В результате достигается стабильность бокового распора в коллекторном пакете независимо от износа
коллектора /2/.
Таблица Допускаемые отклонения ширины полки «а» сечения коллекторной меди
Толщина |
Предельное отклонение стороны |
|||
стороны |
|
профиля а (мм) |
||
профиля |
Точность изготовления |
|||
а (мм) |
|
|
|
|
Высокая |
Повышенная |
Нормальная |
||
|
||||
|
|
|
|
|
До 3 |
-0,02 |
-0,04 |
-0,06 |
|
Свыше 3 |
|
|
|
|
до 6 |
-0,025 |
-0,05 |
-0,08 |
|
Свыше 6 |
|
|
|
|
до 10 |
-0,03 |
-0,06 |
-0,1 |
|
Свыше 10 |
|
|
|
|
до 18 |
-0,035 |
-0,07 |
-0,12 |
Медь является дорогостоящим материалом, поэтому при производстве коллекторов постоянно изыскиваются пути ее экономного расходования. Одним из решений, достоинства которого подтверждены на практике, считается использование порошковой меди. Пластины получают холодным прессованием порошка с удельным усилием до 6 т/см2 с последующей запечкой в защитной среде. При этом сводятся к минимуму отходы меди, а сами коллектора, выполненные по такой технологии, оказались более износоустойчивыми. Поэтому использование порошковой технологии при изготовлении коллекторных пластин следует считать перспективным.
Важную роль в конструкции и производстве коллекторов играют используемые изоляционные материалы. В коллекторах арочного типа с нажимными конусами широко используются миканиты. Это – материалы на
80