
Учебное пособие 800196
.pdfрешение позволяет нагрузку вала сделать более равномерной, что снизит его материалоемкость, и обеспечит сборку вала с сопрягаемыми деталями в системе отверстия. При конструировании ступенчатого вала необходимо оптимизировать не только число ступеней, но и их размеры.
В зависимости от вида имеющейся заготовки для изготовления вала она может быть подвергнута токарной обработке с последующей шлифовкой. Заготовки, полученные поперечно-клиновой прокаткой, имеют минимальный припуск и только шлифуются /11/.
Рассмотрим подробнее более сложный вариант: изготовление ступенчатого вала из пруткового сортамента порезкой последнего на цилиндрические заготовки и последующей токарной обработкой ступеней. Маршрутный техпроцесс такого вала может быть представлен следующими основными операциями: заготовительная, центровочная, токарная, фрезерная, термическая, шлифовальная, контрольная. Последовательность операций и промежуточные виды показаны на рис. 4, где движение инструментов показано стрелкой. Рассмотрим коротко содержание этих операций.
Заготовительная операция, как отмечалось выше, сводится к раскрою сортамента на заготовки. Важно правильно выбрать сортамент материала и способ получения заготовки. Диаметр прутка выбирается, исходя из максимального диаметра одной из ступеней с учетом припуска на обработку и других факторов. Величина припуска влияет на себестоимость обработки и затраты, поэтому его не назначают произвольно. Припуск увеличивается с увеличением размеров детали. На величину припуска влияют: толщина дефектного слоя заготовки, погрешность ее размеров и формы, погрешность базирования /4,5, 9/.
Дефектный слой включает величину микронеровностей поверхности, а также толщину поверхностного слоя с измененными физическими свойствами. Толщина дефектного слоя зависит от способа получения заготовки: литье в землю - 1 - 6 мм, поковка - 1,5 - 3 мм, штамповка - 0,5 - 1,5 мм, горячий прокат - 0,5 - 1,0 мм.
Погрешность геометрической формы и размеров также зависят от способа получения заготовки: искривление оси, конусность, овальность и др. Поковки имеют значительно большие погрешности формы и размеров по сравнению с прокатом. Минимальные погрешности формы и размеров имеет калиброванный сортамент, который чаще используется для валов электрических машин малой мощности.
31
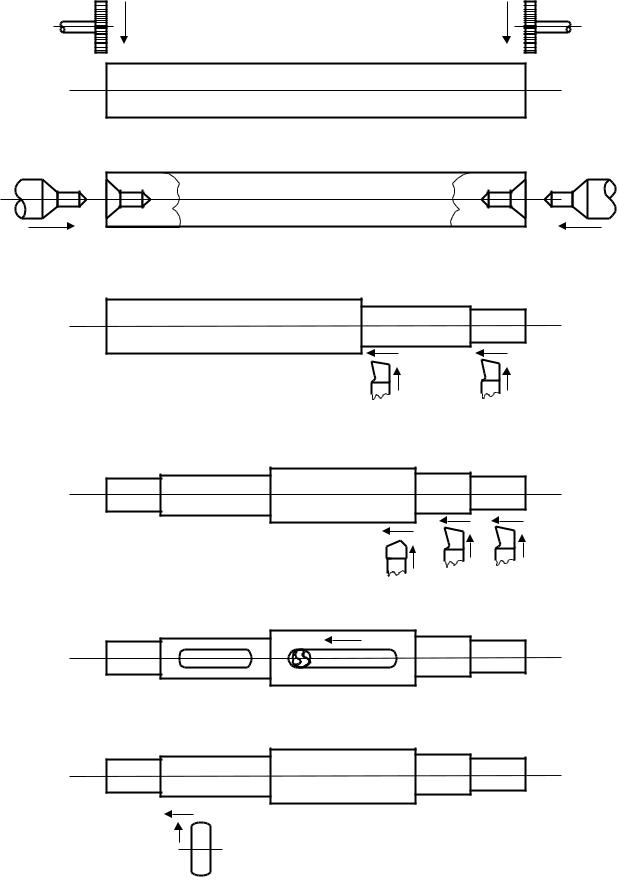
Заготовительная
Центровочная
Токарная 1
Токарная 2
Фрезерная
Шлифовочная
Рис. 4. Формообразование ступенчатого вала электрических машин малой мощности
32

Величину припуска на механическую обработку можно определить, пользуясь специальными технологическими справочниками /6/.
Центровочная операция позволяет сформировать в заготовке чистовые технологические базы, относительно которых затем обрабатывают не только сам вал, но и ротор в сборе. С этой целью на торцах заготовки после придания ей окончательного размера по длине (например, фрезерование торцов) высверливаются глухие отверстия, снабженные коническими или скругленными поверхностями (ГОСТ 14034-74), используемыми затем для установки в центрах токарного станка. Для валов электрических машин размеры этих отверстий выбирают на габарит больше, так как в этих же базах обрабатывается затем и ротор в сборе. Все эти работы удобнее выполнять на фрезерно-центровальных двухпозиционных автоматах, в первой позиции фрезеруются одновременно оба торца, а во второй - выполняются центровые отверстия.
Токарная обработка предусматривает обточку заготовки с образованием ступеней согласно чертежу вала. В условиях крупно - серийного и массового производства обточку вала выполняют за две токарные операции: вначале с одной стороны, а затем – с другой. Это объясняется тем, что один конец заготовки используется для ее вращения и для обработки оказывается недоступной. Ступени вала обрабатывают с припуском под шлифовку (0,3 0,8мм в зависимости от диаметра). Для уменьшения трудоемкости токарной операции в массовом производстве ее выполняют на токарных гидрокопировальных полуавтоматах. Ступени с припусками под шлифовку выполняются со специальными галтелями у буртика, например, канавка для выхода шлифовального круга.
Фрезерная операция выполняется, если в конструкции вала предусмотрены специальные элементы (шпоночные пазы, лыски и т.п.).
При этом используются пальцевые или дисковые фрезы в зависимости от конфигурации выполняемого элемента. Если на валу выполняется несколько шпоночных пазов (машины постоянного тока), то необходимо выполнить с одного установа.
Термообработку выполняют с целью увеличения твердости материала, что способствует повышению точности размеров и чистоты поверхности при шлифовке. Следует обратить внимание, что при быстром охлаждении детали возникает опасность ее искривления из-за возникновения температурных градиентов. Практикой установлено, что наименьшее искривление вала после термической операции достигается при погружении разогретой детали в масло в вертикальном положении. Если изгиба детали избежать не удается, в ряде случаев в техпроцессе предусматривается дополнительная операция «рихтовочная».
Ступени вала, сопрягаемые с другими деталями, шлифуется на круглошлифовальных станках. Для повышения точности и уменьшения шероховатости приходится снижать глубину резания, повышать окружную скорость шлифовального круга до 50 м/сек. Шлифование разделяют на
33
черновое и чистовое. Они выполняются за один установ в два перехода. При изготовлении вала шлифуются только ступени, используемые для сборки ротора. Шейки вала под подшипники и выходной конец шлифуются после сборки ротора.
Контрольная операция предусматривает внешний осмотр детали, контроль ступеней измерительными скобами, контроль чистоты поверхности. Проверяется также биение вала его вращением в центрах, для чего используется часовой индикатор /4/.
Валы и роторы электродвигателей единой серии 4А с высотой оси до 132 мм обрабатывают на автоматических линиях. Они содержат два участка: обработка вала и сборка ротора с чистовой обработкой. Поперечно клиновой прокат заготовок позволяет практически полностью отказаться от токарных операций /11/.
3.3. Обработка станин
Станина - главная корпусная деталь электрической машины. Сопряжение станины с подшипниковыми щитами обеспечивается специальными замками, выполненными на торцах детали. Каждый замок оформляется двумя поверхностями: цилиндрической и торцевой. Цилиндрические поверхности замков должны быть соосны между собой и с внутренней поверхностью станины, сопрягаемой с магнитопроводом статора. Торцовые поверхности замков должны быть перпендикулярны оси станины. Эти требования обусловливают точность воздушного зазора между ротором и статором, а также - нормальную работу подшипниковых узлов. Если станина снабжена лапами, то ее ось должна быть строго параллельна плоскости лап. Все перечисленные требования должны особо учитываться при выборе техпроцесса изготовления станины.
Выбор заготовки для станин определяется типом машины и ее габаритом. Для электродвигателей переменного тока массовых серий заготовки станин получают в виде отливок из чугуна или алюминиевых сплавов. Для крупных машин заготовки выполняют в виде сварных конструкций. В машинах постоянного тока, как уже отмечалось, заготовки получают порезкой стальной трубы или сваркой изогнутой в кольцо (или сегменты) стальной полосы.
Дальнейшая обработка выполняется, в основном, с соблюдением общих принципов формообразования /4/. Для обработки используются револьверные, токарные или карусельные станки. Поскольку заготовки не имеют точно обработанных поверхностей, важно на первом этапе правильно выбрать начальную (черновую) базу. В качестве таких баз используются одна из торцовых поверхностей заготовки, а также ее наружная или внутренняя цилиндрические поверхности. Обрабатывается замок или внутренняя поверхность заготовки. При этом нужно оставить небольшой припуск для окончательной обработки. Далее заготовку переустанавливают на станке, используя в качестве базы одну из предварительно обработанных
34
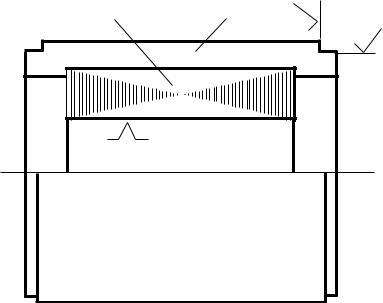
поверхностей, относительно которой обрабатывают все остальные поверхности согласно чертежу. После этого дорабатывают окончательно поверхность, использованную под черновую базу, используя в качестве базы одну из окончательно обработанных поверхностей.
Такая последовательность обработки будет оправданной, если каждому установу будет отвечать отдельная операция. Если же обработку нужно выполнить за одну операцию с несколькими установами, тогда лучше относительно первой черновой базы выполнить в отверстии заготовки технологическую проточку для чистовой базы и затем на втором установе обработать сразу все сопрягаемые поверхности станины.
После проточки станины, в которой предусмотрены лапы, на фрезерном станке фрезеруют плоскость лап. Завершается обработка станины сверлильными операциями для образования отверстий и на торцевых поверхностях под крепление подшипниковых щитов и в лапах.
При производстве электродвигателей серии 4А используется и другая последовательность обработки станины: обработка опорной плоскости лап и установочных отверстий; использование этих поверхностей в качестве технологических баз для расточки центрального отверстия и проточки замков. Станины двигателей с высотой оси 160 - 250 мм обрабатываются на шестипозиционных агрегатных станках Минского завода автоматических линий.
В электрических машинах малой мощности часто используется конструкция статора, когда магнитопровод в сборе устанавливают в литформу и на нем сверху отливают корпус (станину) из алюминиевого сплава (рис. 5).
1 |
2 |
2,5
2,5
Рис. 5. Отливка корпуса на магнитопроводе статора: 1 – магнитопровод; 2 – корпус из алюминиевого сплава
Обработка такой конструкции сводится к проточке замков с использованием в качестве технологической базы поверхности расточки магнитопровода. Это позволяет избавиться от обработки с высокой точностью
35
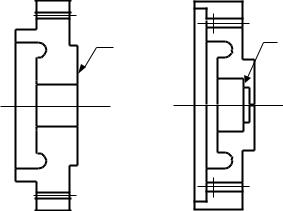
поверхностей сопряжения станины и магнитопровода. Однако такое решение имеет и недостатки: опасность деформирования магнитопровода силами, возникающими при затвердевании и усадке алюминиевого сплава. Возникают при этом и внутренние напряжения в самой станине, что может привести к появлению трещин. Поэтому такая конструкция статора не используется в машинах мощностью более 600 Вт.
3.4. Обработка подшипниковых щитов
Функция подшипниковых щитов в электрической машине - взаимное ориентирование ротора и статора и соединение их между собой. Они применяются в конструкциях с внешним диаметром сердечника статора до 1 м. В электрических машинах большего габарита чаще используют выносные стояковые подшипники.
К геометрии подшипникового щита предъявляется главное требование: цилиндрические поверхности отверстия под подшипник и замков должны быть строго соосны. В соответствии с выбранной конструкцией станины замковая цилиндрическая поверхность на щите также может быть внутренней (рис. 6, а) и наружной (рис. 6, б). Торцевая поверхность замка должна быть строго перпендикулярной оси его цилиндрической поверхности.
а) б)
Б
А
Рис. 6. Подшипниковый щит: а – с внутренним замком и сквозным отверстием под подшипник; б – с внешним замком и глухим отверстием под подшипник
Отверстие под подшипник качения выполняется в системе вала с точностью по шестому или седьмому квалитету с шероховатостью по шестому - седьмому классу по ГОСТ 2789-73. К этому элементу щита предъявляются жесткие требования и по погрешности геометрической формы.
В различных конструкциях щитов отверстие под подшипник может быть сквозным или глухим. В варианте со сквозным отверстием (рис. 6, а) последнее выполняется расточкой или разверткой на проход, его размер проще контролировать. Поэтому такой щит изготавливать легко. Однако для
36
ограничения осевого перемещения подшипника в этом случае нужно предусмотреть дополнительную деталь - подшипниковую крышку, сопрягаемую с торцевой поверхностью «А» щита, что повышает погрешность расположения опорного буртика крышки, сопрягаемого с подшипником. Это обстоятельство снижает технологичность конструкции подшипникового узла.
Вслучае глухого отверстия (рис. 6, б) его цилиндрическая и торцевая «Б» поверхности могут быть выполнены с одного установа, что обеспечивает более высокую точность их взаимного расположения. Однако такое отверстие труднее обрабатывать и контролировать. Кроме того, при сборке электродвигателя для регулировки осевого зазора (люфта) ротора приходится несколько раз снимать и устанавливать подшипниковый щит. Все перечисленные требования должны учитываться при подборе технологического процесса конкретной конструкции подшипникового щита.
Вкачестве заготовки для изготовления щита используются отливки из чугуна или алюминиевого сплава. В крупных электрических машинах заготовки могут выполняться сварными.
Особо следует отметить, что в случае выполнение щита из алюминиевого сплава отверстие под подшипник часто армируется стальной втулкой, надежно закрепленной в теле щита. Такое решение существенно повышает надежность подшипникового узла.
Подшипниковые щиты обрабатывают на токарных, револьверных или карусельных станках. При этом большое значение играет не только выбор черновой и чистовой технологических баз, но и способ закрепления заготовки для обработки. Закрепляющие усилия нужно прикладывать к заготовке таким образом, чтобы она меньше деформировалась.
Максимальная точность взаимного расположения обрабатываемых поверхностей достигается, как известно, при их обработке с одного установа. Это особенно важно при производстве асинхронных электродвигателей, где воздушный зазор между ротором и статором выполняется минимальным. Для возможности реализации такого способа на внешней поверхности заготовки подшипникового щита в некоторых конструкциях предусматривается три специальных прилива для закрепления ее в трех - кулачковом патроне.
При обработке щитов с использованием черновой базы поверхность замка и отверстие под подшипник иногда обрабатывают, оставляя небольшой припуск. Чистовую же обработку этих элементов осуществляют раздельно, используя в качестве чистовых технологических баз обработанные поверхности. При этом отверстие щита обрабатывается последним, а в качестве чистовой базы принимается окончательно обработанная поверхность замка. Такой прием позволяет при закрепление заготовки избежать приложения к ней радиальных усилий, деформирующих заготовки, и тем самым повысить точность размеров отверстия под подшипник.
Вкрупно - серийном и массовом производстве обработку щитов удобнее производить на агрегатных станках /11/.
37
При разработке техпроцесса изготовления механических деталей большое значение имеет рассмотрение нескольких вариантов его построения. В результате экономического анализа в производство должен быть рекомендован вариант, дающий наибольшую эффективность. При этом учитываются следующие показатели: капитальные вложения, себестоимость изделия, сроки окупаемости капитальных вложений, производительность труда и т.п. Этот анализ можно выполнить разными методами, например, путем сравнения с базовым техпроцессом, уже освоенным и хорошо отлаженным в производстве.
Глава IV
ПРОИЗВОДСТВО ШИХТОВАННЫХ МАГНИТОПРОВОДОВ
4.1.Раскрой сортамента
Вэлектромашиностроении широко практикуется получение деталей способом холодной штамповки, в частности - вырубной листовой штамповки. Наиболее характерной штампованной деталью электрической машины является лист шихтованного магнитопровода.
Сборку магнитопроводов электрических машин из отдельных пластин можно объяснить двумя причинами:
физической, так как изоляция отдельных пластин друг от друга ограничивает вихревые токи в магнитопроводе;
производственной, так как магнитопроводы электрических машин имеют порой настолько сложную форму, что выполнение его монолитным оказывается нетехнологичным.
Подтверждением последнему является тот факт, что часто сердечник главного полюса машины постоянного тока выполняется шихтованным, даже если он при работе машины не перемагничивается.
Листы магнитопровода изготовляют, как известно, из специальной электротехнической стали, обладающей необходимыми электромагнитными свойствами. Поэтому при изготовлении магнитопровода необходимо обеспечивать не только его геометрические и механические характеристики, но
иэлектромагнитные. Это сказывается на техпроцессе его производства. Электротехнические стали выпускаются металлургическими
предприятиями в двух сортаментах: листовой и рулонный (ГОСТ 21427.2-75). Размеры сортамента стандартизованы и обеспечивают получение деталей с минимальными отходами. Размеры листов определяется толщиной (S), шириной (а) и длинной (b). Размеры рулона определяются толщиной (S), шириной (а) ленты, и его весом.
Наиболее распространенной заготовительной операцией при листовой штамповке деталей является раскрой материала, если по ширине листа или ленты могут с учетом припуска разместиться две или более деталей. Раскрой сводится к порезке сортамента на полосы, ширина которых равна габаритному
38
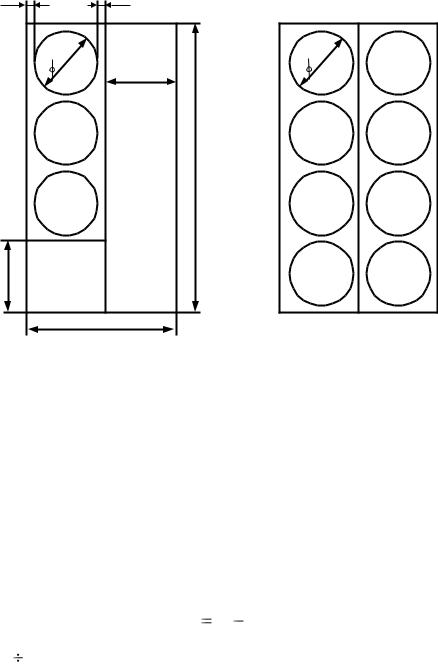
размеру детали (D) плюс припуск на штамповки (С). При этом из листа или |
||
ленты должно получаться целое число полос - заготовок. На (рис.7 |
) показаны |
|
примеры раскроя листа размером 1000 х 2000 мм для двух габаритных размеров |
||
деталей. |
|
|
а) |
б) |
|
с |
с |
|
500 |
493 |
|
|
490 |
|
|
2000 |
|
470 |
|
|
|
1000 |
|
Рис. 7. Раскрой листов: а) нерациональный; б) рациональный |
Из рисунка хорошо видно, что в случае а) получаются так называемые «немерные» отходы, которые не могут быть использованы для получения деталей заданного размера (D=500 мм). Но достаточно было уменьшить габарит детали до D=493 мм, и из того же сортамента можно получить восемь деталей вместо трех при отсутствии немерных полос.
Поэтому при проектировании электрических машин с диаметром магнитопровода до D=990 мм размер листа должен быть согласован с размером сортамента материала. Предпочтительный диаметр может быть определен по выражению:
D |
a |
c |
(2) |
|
|
||||
i |
||||
|
|
|
где: с=4 10 мм – припуск на штамповку в зависимости от габарита детали.
Раскрой листов производится в соответствии с «Картой технологического процесса раскроя и отрезки заготовок на деталь или группу деталей» (ГОСТ
3.1402-74).
Для раскроя листов и лент используется специальное технологическое оборудование: гильотинные и роликовые ножницы.
Гильотинные ножницы используют для раскроя листового сортамента (рис. 8).
39
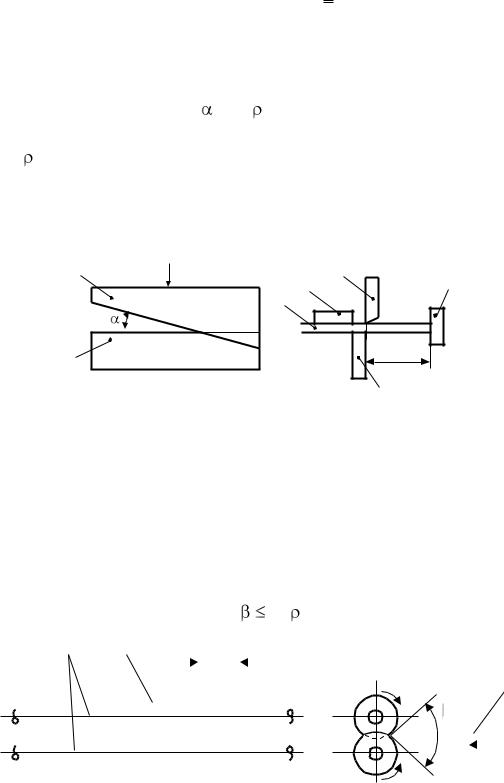
Сортамент 3 укладывают на стол и сдвигают до упора 5.Подвижны нож 1 жестко закреплен на ползуне пресса. Неподвижный нож 2 закреплен на его столе. При рабочем ходе подвижного ножа в направлении указанном стрелкой,
от сортамента отделяется полоса шириной (D+ C ). Следует обратить внимание, что усилие резания будет меньше, если увеличить угол между кромками ножей. Однако величина этого угла не должна выбираться с условием:
< tg , |
(3) |
где: - коэффициент трения в зоне резания. Невыполнение этого условия грозит смещением листа в направление резания.
Дисковые ножницы имеют режущие диски, закрепленные на параллельно расположенных валах (рис. 9)
1 |
1 |
|
|
4 |
5 |
3 |
|
2 |
D+c |
|
2 |
Рис. 8. Раскрой листа на гильотинных ножницах: 1 – нож подвижный; 2 – нож неподвижный; 3 – материал; 4 – прижим; 5 – упор
Режущие диски жестко закреплены на валах с учетом требуемого размера получаемой ленты (D+с). Материал, как показано на рисунке, подается справа, и затягиваются в зону резания силами трения между материалом и кромками дисков. Для этого угол между касательными к кромкам дисков в точке их пересечения должен выбираться из условия.
|
|
|
|
|
|
|
|
|
|
|
|
|
|
|
|
|
|
|
tg |
(4) |
|||||
|
|
1 |
2 |
|
|
|
|
|
|
D+c |
|
|
|
|
|
|
|
|
|
|
|||||
|
|
|
|
|
|
|
|
|
|
|
|
|
|
|
|
|
|
||||||||
|
|
|
|
|
|
|
|
|
|
|
|
|
|
|
|
|
|
|
|
|
|||||
|
|
|
|
|
|
|
|
|
|
|
|
|
|
|
|
|
|
|
|
|
3 |
||||
|
|
|
|
|
|
|
|
|
|
|
|
|
|
|
|
|
|
|
|
|
|
|
|
|
|
|
|
|
|
|
|
|
|
|
|
|
|
|
|
|
|
|
|
|
|
|
|
|
|
|
|
|
|
|
|
|
|
|
|
|
|
|
|
|
|
|
|
|
|
|
|
|
|
|
|
|
|
|
|
|
|
|
|
|
|
|
|
|
|
|
|
|
|
|
|
|
|
|
|
|
|
|
|
|
|
|
|
|
|
|
|
|
|
|
|
|
|
|
|
|
|
|
|
|
|
|
|
|
|
|
|
|
|
|
|
|
|
|
|
|
|
|
|
|
|
|
|
|
|
|
|
|
|
|
|
|
|
|
|
|
|
|
|
|
|
|
|
|
|
|
|
|
|
|
|
|
|
|
|
|
|
Рис. 9. Раскрой материала на роликовых ножницах: 1 – вал; 2 – режущий диск; 3 – материал
40