
Учебное пособие 800196
.pdf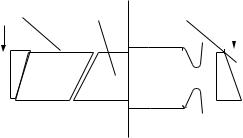
температуре, для чего пакет 1 пропрессовывают через коническое отверстие направляющего кольца 3 в отверстие прессовочного кольца 2. Последнее установлено на кольцевой опоре 4. После нагрева до температуры размягчения связующего (для шеллака +1600С) и выпечки производят перепрессовку горячего пакета во второе кольцо (рис. 51., б). При этом кольцо 2 с пакетом 1 устанавливают на приставку 5 и перепрессовывают пакет в кольцо 6 с меньшим отверстием. После охлаждения боковой распор в пакете уменьшается, поэтому для его восстановления пакет в холодном состоянии перепрессовывают в третье кольцо по схеме рис. 51, б.
1 |
|
2 |
3 |
|
|
|
|
|
|
|
|
|
|
|
|
|
|
|
|
|
|
|
|
|
|
|
|
|
|
|
|
|
|
|
|
|
|
|
|
|
|
|
|
|
|
|
|
|
|
|
|
|
|
|
|
Рис. 52. Прессовка коллекторного пакета коническими кольцами с плашками: 1 – пакет; 2 – плашки; 3 – коническое кольцо
Коллекторный пакет, запрессованной в третье кольцо, обрабатывают на токарном станке с двух установов. При этом протачивают торцы и канавки “ласточкиного хвоста”. После проточки пакет, запрессованный в кольцо, передают на сборку коллектора.
Коллекторный пакет с выступающими петушками пропрессовать сквозь отверстие цилиндрического кольца невозможно. Для радиальной опрессовки таких пакетов применяют конические кольца с плашками /3/.Устройство такого приспособления показано на Рис.52.
Коллекторный пакет 1 (показан условно пунктиром) обкладывают плашками 2, образующими внешнюю коническую поверхность. На неѐ сверху напрессовывают кольцо 3 с коническим отверстием. Прессовое усилие (показано стрелками) прикладывают к кольцу 3.Смещаясь вниз под действием прессовки, кольцо 3 перемещает плашки 2 к оси пакета, сжимая его в радиальном направлении. Плашки отделены друг от друга наклонными зазорами, что исключает попадание в зазор детали прессуемого пакета. Чаще всего прессовка ведется в три этапа: при нормальной температуре, затем - после выпечки при температуре +1600С, и, наконец, - подпрессовка холодного пакета.
Наклон образующей конуса кольца к его оси должен быть не более угла трения пары "плашка-кольцо", что обеспечит самотормозящееся соединение деталей приспособления. Это требование очень важное, так как для облегчения трения поверхности плашек и кольца смазывают, в результате чего коэффициент трения уменьшается до 0,05-0,15.
Коллекторный пакет, запрессованный в кольцо с плашками, направляют на токарную обработку. Протачивают торцы пакета и конические поверхности
91
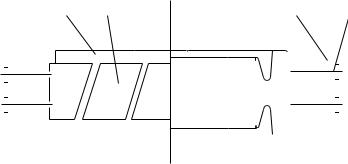
“ласточкиного хвоста”. Коллекторные пакеты большого диаметра обрабатывают на карусельных станках.
Особого внимания заслуживает проблема радиальной прессовки пакетов крупногабаритных коллекторов. Такой пакет собирают и прессуют на тщательно выверенном в горизонтальной плоскости фундаменте. Прессовка выполняется с применением цилиндрического кольца с плашками. Технологическая схема операции показана на Рис.53.
1 |
2 |
|
|
3 |
|
4 |
||||||||||
|
|
|
|
|
|
|
|
|
|
|
|
|
|
|
|
|
|
|
|
|
|
|
|
|
|
|
|
|
|
|
|
|
|
|
|
|
|
|
|
|
|
|
|
|
|
|
|
|
|
|
|
|
|
|
|
|
|
|
|
|
|
|
|
|
|
|
|
|
|
|
|
|
|
|
|
|
|
|
|
|
|
|
|
|
|
|
|
|
|
|
|
|
|
|
|
|
|
|
|
|
|
|
|
|
|
|
|
|
|
|
|
|
|
|
|
|
|
|
|
|
|
|
|
|
|
|
|
|
|
|
|
|
|
|
|
|
|
|
|
|
|
|
|
|
|
|
|
|
|
|
|
|
|
|
|
|
|
|
|
|
|
|
|
|
|
|
|
|
|
Рис. 53. Прессовка коллекторного пакета в цилиндрическом кольце с плашками: 1 – пакет; 2 – плашки; 3 – цилиндрическое кольцо; 3 – болты.
Коллекторный пакет 1 обкладывают плашками 2, образующими снаружи цилиндрическую поверхность. Соосно с пакетом на фундамент установлено цилиндрическое кольцо 3, в резьбовые отверстия которого ввернуты прессующие болты 4. Указанные болты упираются в плашки 2 так, чтобы на плашку приходилось по два болта вдоль образующей. Прессовка обеспечивается подтяжкой болтов 4. Во избежание перекоса или искривления внешней поверхности пакета затяжка болтов производится по указанной в технологическом документе схеме. После каждого цикла затяжки болтов контролируют вертикальность образующей пакета и отклонение его внешней поверхности от окружности. Как и в выше приведенных случаях, прессовка ведется в три этапа: при нормальной температуре, при нагреве до + 1600С и подпрессовка при нормальной температуре. Крупногабаритные коллекторные пакеты протачивают по торцам на карусельных станках.
5.6. Сборка арочного коллектора
Рабочее место сборщика коллекторов оборудовано верстаком, на котором установлена сборочная плита. Это - стальная плита, поверхность которой выставлена строго горизонтально. На плите располагают измерительный рейсмус, который используется для контроля точности сборки.
Технологическая схема сборки арочного коллектора приведена на Рис.54. Для наглядности здесь все детали коллектора показаны с осевым разрезом. На сборочной плите 1 вертикально устанавливают втулку 2 коллектора. На втулку
92
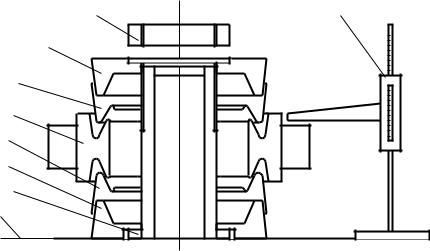
монтируют нажимной конус 3,который садится на упорный буртик втулки. На конус 3 осторожно укладывают манжету 4, которую после укладки
8 |
9 |
7 |
|
6 |
|
5 |
|
4 |
|
3 |
|
2 |
|
1 |
|
Рис. 54. Общая сборка арочного коллектора. |
несколько раз сдвигают вокруг оси, что обеспечивает еѐ плотное прилегание к конусу. С помощью подъемного устройства, соблюдая особую осторожность, устанавливают коллекторный пакет 5, который запрессован в прессовочное кольцо. Рейсмусом 6 проверяют параллельность верхнего торца коллекторного пакета и поверхности сборочной плиты. Специальным шаблоном проверяют положение пластин коллектора относительно шпоночного паза во втулке 2.Если при этом возникает необходимость изменить положение пакета, то во избежание повреждения манжеты пакет нужно приподнять и снова установить в новом положении. После этого необходимо снова рейсмусом проверить горизонтальность верхнего торца пакета.
Вкрупных коллекторах точно сориентировать пластины относительно шпоночного паза бывает очень трудно. В этих случаях шпоночный паз во втулке протягивают после окончательной сборки коллектора.
Вверхнюю коническую выточку пакета пластин вкладывают вторую манжету 6 и нажимной конус 7. Рейсмусом необходимо проверить горизонтальность торца верхнего конуса. На выступающие из-под коллекторного пакета края манжет накладывают технологический бандаж из шнура или тканой ленты, предохраняющий их от случайных повреждений. После этого на выступающий конец втулки следует навернуть гайку 8 до упора.
Собранный коллектор поступает на прессовку.
Осевая прессовка коллектора производится на гидропрессе. Для этого коллектор необходимо установить на столе пресса. Прессующее усилие прикладывают к торцу верхнего нажимного конуса 7. Следует помнить, что величина прессующего усилия строго регламентируется, и обеспечить строгое выполнение этого требования только затяжкой гайки 8 невозможно, так как часть усилия затяжки будет расходоваться на преодоление трения в резьбе. Правильно будет, не снимая усилия пресса, затянуть гайку 8 до упора, что обеспечит сохранение прессующего усилия. Прессовку коллектора производят с
93
подогревом |
до температуры размягчения связующих |
составляющих |
миканита(+1600С). После охлаждения коллектора до нормальной |
температуры |
производится его подпрессовка с подтяжкой гайки.
После выполнения операции прессовки нажимные конуса обеспечивают боковой распор в коллекторном пакете, что позволяет снять прессовочное кольцо. Эта операция выполняется выпрессовкой коллектора из кольца в специальном приспособлении на гидропрессе.
Погрешности формы сопрягаемых поверхностей и неточность сборки приводят к тому, что прессующее усилие передается от конусов не на все коллекторные пластины равномерно. Создается опасность смещения некоторых пластин при эксплуатации и преждевременного выхода из строя электрической машины. Этот недостаток устраняется так называемой динамической формовкой коллектора. Выравнивание прижатия коллекторных пластин к нажимным конусам достигается разгоном разогретого (+1600С) коллектора на специальном разгонном устройстве до скорости, на 20-25% превышающей номинальную скорость вращения якоря. При этом не прижатые к нажимным конусам коллекторные пластины под действием центробежной силы смещаются в сторону от оси, прижимаясь своим ласточкиным хвостом к конусам. Смещение пластин приведет к ослаблению бокового распора в пакете, который восстанавливается повторной осевой прессовкой коллектора на гидропрессе с подтяжкой гайки. Как правило, коллектор подвергают динамической формовке два или более раз, добиваясь такого положения, чтобы при последующей осевой прессовке гайка поворачивалась не более чем на 900.
Отделка коллектора сводится к окончательной заделке выступающих краев коллекторных манжет. С этой целью технологические бандажи следует осторожно снять, а на их место наложить штатные бандажи, предусмотренные чертежом. Они выполняются шнуром или стекловолокнистой лентой. Бандаж покрывают лаком в несколько слоев с образованием гладкой глянцевой поверхности. Такое решение способствует повышению электрической прочности корпусной изоляции коллектора. В частности - снижается вероятность разряда по поверхности бандажа, так как его гладкая поверхность в сочетании с поверхностным дутьем воздуха при вращении якоря затруднит оседание щеточной пыли на бандаже.
Готовый коллектор после проточки его наружной поверхности поступает на сборку якоря.
5.7. Производство коллекторов с пластмассовым корпусом
Коллекторы с пластмассовым корпусом находят все более широкое применение в электрических машинах. Они отличаются большим многообразием, как конструкций, так и технологических процессов их производства /29/. Технологическое разнообразие в большей степени связано со способами получения коллекторных пакетов, состоящих из медных пластин, разделенных изоляционными промежутками. Чаще это определяется габаритом
94
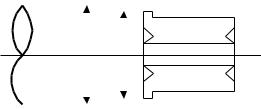
коллектора, классом напряжения, имеющимися технологическими возможностями.
Коллекторный пакет для коллекторов диаметром 30мм и выше выполняется с чередованием медных пластин и миканитовых прокладок, как было показано выше. Пакет, запрессованный в прессовочном кольце, направляется на участок пластмасс для опрессовки пластмассовым корпусом. Операция выполняется с применением специальных прессформ /23/.Коллекторный пакет нагревают до температуры 150 - 1700С и закладывают в полость прессформы, используя для базирования внешние поверхности прессовочного кольца. В прессформу закладывается также армирующая втулка, бандажные кольца, другие детали, если они предусмотрены конструкцией. Армирующие детали также закладываются подогретыми. В полость загрузочной матрицы закладывают строго определенное по весу количество прессматериала. Прессовка производится с подогревом прессформы до 150 – 1700С. Прессматериал подвергается давлению 450-600 кг/см2 . Эти режимы способствуют тому, что прессматериал размягчается и, перетекая в прессформу, заполняет еѐ полость. Время выдержки под давлением зависит от прессматериала и размеров изделия.
Для пластмассы марки АГ-4 время выдержки составляет 1мин на 1мм толщины корпуса. Извлеченные из прессформы коллекторы выпекают в печи при температуре +1600С в течение 5-6час., что улучшает электрические и механические характеристики пластмассы.
Затем коллекторы направляют на слесарную обработку для удаления литниковых выступов, облоя и снятия прессовочного кольца, а далее – на токарную обработку. При изготовлении коллекторных пакетов мелких коллекторов (диаметром менее 20 мм) приведенная выше технология с использованием миканитовых прокладок оказывается неоправданно трудоемкой. Кроме этого в низковольтных машинах применение дорогостоящего миканита нецелесообразно. В этих случаях практикуется изготовлении заготовки блока коллекторных пластин из пруткового сортамента меди. Более традиционное решение вопроса сводится к тому, что диаметр прутка выбирают, ориентируясь на внешний диаметр буртика, образуемого петушками коллекторных пластин. Этот вариант изображен на рис. 55., где d- диаметр буртика по петушкам, а D – диаметр сортамента.
D |
|
|
|
|
d |
|
|
||
|
||||
|
|
|
|
|
|
|
|
|
|
|
|
|
|
|
Рис. 55. Выбор сортамента меди
95
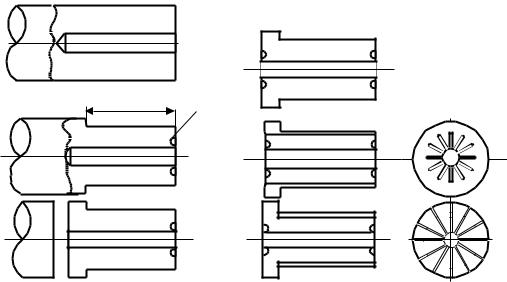
1 |
|
|
|
|
4 |
|
l |
k |
|
|
|
2 |
|
5 |
|
|
|
3 |
|
6 |
|
|
Рис. 56. Получение блока коллекторных пластин из медного прутка
Процесс получения блока пластин показан на рис. 56. Здесь в позиции 1 выполняют осевое сверление прутка, полученное при этом отверстие образует внутренний диаметр блока коллекторных пластин. На позиции 2 точением ступени длиной “1” выполняется буртик, образуемый выступающими петушками. Одновременно протачивается канавка “k”, оформляющая “ласточкин хвост” с правой стороны заготовки. Позиция 3 предусматривает отделение заготовки от сортамента. Это может быть выполнено отрезным резцом. На следующей позиции 4 производят торцовку заготовки со стороны буртика с образованием на этой поверхности второй канавки “ласточкиного хвоста”. Полученная заготовка в виде втулки с буртиком поступает на операцию (позиция 5), где с помощью протяжки коллекторные пластины отделяются друг от друга, оставаясь соединенными между собой тонкой технологической перемычкой (заштрихована). При этом между пластинами образуется узкий шлиц, ширина которого обеспечивается режущим зубом инструмента (протяжки) и должна быть достаточной для образования изоляционного промежутка завершается на следующей позиции 6, где фрезерованием дисковой фрезой отделяют друг от друга петушки коллекторных пластин. При этом важно, чтобы образуемой фрезой щели строго совпадали со шлицами между коллекторными пластина. Готовый блок коллекторных пластин передается на участок пластмасс для опрессовки пресс материалом. Заключительной операцией является токарная обработка по внешнему диаметру, в результате чего удаляется технологическая перемычка, и коллекторные пластины окончательно отделяются друг от друга. Щели между соседними пластинами будут заполнены пресс материалом. К серьезным
96
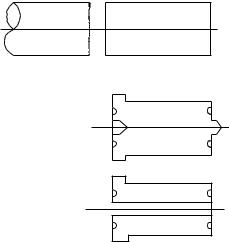
недостаткам приведенного способа можно отнести: низкий коэффициент использования меди; отходы меди в виде мелкой стружки; большой объем токарных работ. От этих недостатков свободен способ, предложенный и внедренный в производство сотрудниками кафедры технологии электрических машин малой мощности Воронежского политехнического института совместно с одним из предприятий электротехнической промышленности. Его суть состоит в том, что диаметр медного прутка выбирают, ориентируясь на диаметр активной части коллектора с учетом образования технологической перемычки между пластинами блока. В техпроцессе используются экономичные приемы формообразования в виде вырубной и объемной штамповки, как показано на рис.57. Операция 1 предусматривает рубку сортамента в закрытом рубочном штампе на цилиндрические заготовки. При этом осевая длина заготовки определяется объемом меди, необходимых для получения блока коллекторных пластин. Операция 2 – штамповочная. Она обеспечивает пластическое деформирование (осадку) заготовки с образованием буртика под петушки. Одновременно формируются канавки, образующие ласточкин хвост.
В центре выполняется углубление с выступом на противоположном торце заготовки. Этот выступ используется для фиксации заготовки в совмещенном штампе при выполнении операции 3, обеспечивающей обрубку буртика по диаметру согласно чертежу и одновременную пробивку центрального отверстия. При этом образуются отходы в виде кусочков меди, что удобно для их утилизации. Далее заготовка подвергается протяжке, фрезеровке петушков, опрессовке пластмассой и токарной обработки, как и предыдущем варианте. Расход меди и трудоемкость изделия полученного штамповкой, почти в три раза ниже, чем в предыдущем способе.
1
2
3
Рис. 57. Получение блока коллекторных пластин штамповкой
Конструкция и технология производства коллекторов с пластмассовым корпусом непрерывно развиваются, новые решения позволяют получать
97
экономические выгодные изделия, как для малых, так и для крупногабаритных машин /27/. Перспективным является также применение для изготовления активных частей коллектора новых материалов: графита, угля, композиционных материалов порошковой технологии, использования гальванических покрытий и др.
Несмотря на новые разработки бесконтактных электрических машин постоянного тока и так называемых вентильных машин /24, 26/, совершенствование конструкций и технологии производства коллекторов продолжает оставаться актуальной задачей на обозримое будущее.
98
КОНТРОЛЬНЫЕ ВОПРОСЫ
1.Каковы основные этапы развития отечественного электромашиностроения?
2.Для чего разрабатывают и осваиваются в производстве единые серии электрических машин?
3.Какие факторы влияют на качество выпускаемых промышленностью электрических машин?
4.Как можно классифицировать составные части электрической машины с учетом специфики технологии их производства?
5.Что подразумевается под производственной технологичностью конструкции электрической машины?
6.Как связаны производственная и эксплуатационная технологичность конструкций электрической машины?
7.Что называют производственным и технологическими процессами?
8.Какие составные части предусматриваются в технологическом процессе?
9.Какие типы производств существуют в электромашиностроении?
10.Каковы сущность и задачи технической подготовки производства электрических машин?
11.Что подразумевается под конструкторской подготовкой производства?
12.В чем состоит специфика подготовки производства в процессе создания новой конструкции и после освоения ее в производстве?
13.Что подразумевается под технологической подготовкой производства?
14.Какими нормативными документами устанавливается содержание конструкторской и технологической подготовки производства?
15.В каких основных технологических документах приводится описание процесса производства электрической машины?
16.Что подразумевается под принципами стандартизации, унификации и преемственности при решении конструкторских и технологических задач?
17.Как построить схему сборочного состава электрической машины?
18.Как построить технологическую схему производства электрической машины?
19.Где полезно использовать технологическую схему производства электрической машины?
99
20.Что называют замкнутым циклом производства?
21.Какие цехи электромашиностроительного завода относятся к основным?
22.Какие цехи завода и почему считаются вспомогательными?
23.Какова роль инструментального цеха на электромашиностроительном заводе?
24.Что называют сортаментом материала?
25.Какие сортаменты конструкционных материалов вам известны?
26.Что называют заготовкой для изготовления детали?
27.Какими соображениями руководствуются при выборе формы размеров заготовки?
28.Какими способами получают заготовки из пруткового сортамента?
29.Какими способами получают заготовку из листового сортамента?
30.В каких случаях применяют заготовки в виде отливок?
31.Какие способы литья используются в электромашиностроении?
32.Какие типы валов применяются в конструкциях электрических машин?
33.Какие способы изготовления ступенчатых валов электрических машин Вы знаете?
34.Для чего и как выполняются центровые отверстия на торцах вала?
35.Какие ступени вала и почему обрабатывают окончательно после сборки ротора?
36.Какие функции выполняют станина и подшипниковые щиты электрической машины?
37.Какие поверхности обеспечивают сопряжение подшипниковых щитов со станиной?
38.Как выбрать черновую и чистовую технологические базы при обработке отливок станин подшипниковых щитов?
39.Что следует понимать под принципом совмещения баз?
40.Какое оборудование используется при изготовлении валов электрических машин?
41.Какое оборудование используется для обработки станин и подшипниковых щитов?
42.Для чего магнитопровод электрической машины выполняют шихтованным?
43.По каким свойствам материала можно судить об уровне потерь мощности на перемагничивание электротехнической стали?
44.Какие сортаменты электротехнической стали предусмотрены стандартом?
45.Как производится раскрой листовой электротехнической стали?
46.Как производится раскрой рулонной электротехнической стали?
100