
Учебное пособие 800196
.pdf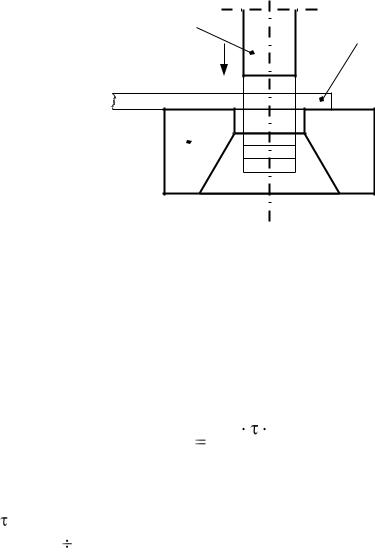
Дисковые ножницы отличаются высокой производительностью, а получаемые ленты материала с шириной (D+с) облегчают автоматизацию штамповочных работ.
4.2. Штамповка листов
Если при порезке сортамента электротехнической стали разделение полос производится последовательным взаимным перемещением материала и режущих кромок инструмента, то при вырубной штамповке отделение отхода от детали осуществляется одновременно по всему контуру детали (а иногда - по нескольким контурам). Процесс легко проследить на простейшем примере вырубки деталей в виде дисков. Схема этого процесса показана на (рис. 10)
2
3
1
Рис. 10. Вырубка дисков из полосы: 1 - матрица; 2 - пуансон; 3 - полоса материала
На рисунке показан простейший вырубной штамп. Он состоит из неподвижной 1 (матрица) и подвижной 2 (пуансон) частей. Полоса материала 3 размещается на поверхности матрицы 1. Пуансон 2, перемещаясь вниз, встречает на своем пути полосу 3 материала и, проникая в отверстие матрицы, отделяет деталь. Из сказанного следует вывод, что для вырубки детали пуансон должен развивать усилие
Р k |
L s |
(тонн) |
(5) |
|
1000 |
|
|||
|
|
|
|
где: L - длина контура вырубки (м) s - толщина листа (м)
- предел прочности материала сдвигу (кГ/м2)
k=1, 15 1,3 коэффициент, учитывающий условия штамповки Представленная на (рис. 10) схема режущего инструмента показывает
главный принцип устройства вырубного штампа. Усилие, определенное по (5), называют вырубным усилием штампа.
Пуансон и матрица жестко соединяются с верхней и нижней плитами, которые строго ориентируются друг относительно друга. Последнее обеспечивает соосность пуансона и матрицы.
41
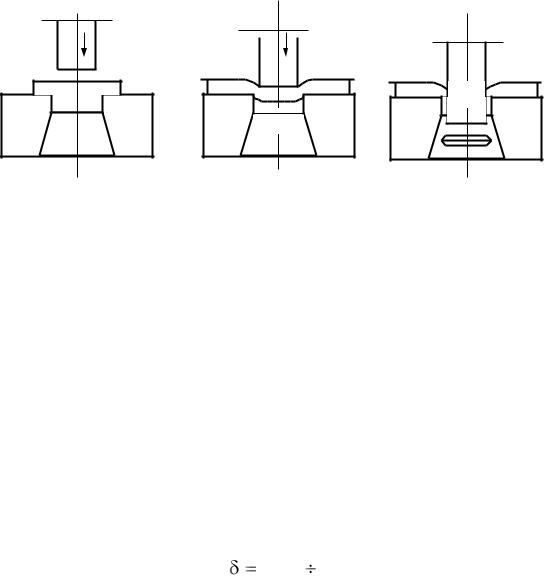
В рассмотренном на (рис. 10) примере пуансон имеет вид цилиндра, ограниченного снизу плоской поверхностью, перпендикулярной оси цилиндрической поверхности. Между цилиндром и торцем пуансона образуется острое ребро, представляющее собой его режущую кромку.
Режущая кромка матрицы образована между ее плоской верхней поверхностью и цилиндрической частью отверстия, куда проникает пуансон. Отверстие матрицы расширяется на конце, что позволяет вырубленной детали свободно подать вниз.
Рассмотрим более подробно процесс отделения детали в вырубном штампе. С этой целью удобнее изобразить схему штамповки в несколько искаженном виде, показанном на (рис. 11). Здесь толщина материала и зазор между боковыми сторонами пуансона и стенками отверстия матрицы представлены увеличенными. Рассматривая последовательно представленные на рисунке моменты штамповки, можно дать им следующее описание.
а) б) в)
Рис. 11. Фазы вырубной штамповки: а) - размещение материала; б) - деформирование материала; в) - завершение штамповки
На (рис. 11, а) показано размещение материала на поверхности матрицы при неподвижном пуансоне. Даже включается пресс, и пуансон движется вниз. Встретив на своем пути полосу материала, он деформирует ее, вдавливая в отверстие матрицы (рис. 11,б). При этом материал претерпевает все этапы деформирования: упругое, пластическое и разрушение. Из (рис. 11) хорошо видно, что, деформируя материал, пуансон и матрица создают в нем повышенную концентрацию напряжения в районе их острых кромок. Именно в этих местах и начинается разрушение материалов, в нем возникают трещины, устремляющиеся навстречу друг другу. Из (рис.11) следует, что отверстие в полосе будет определяться диаметром пуансона, а диаметр вырубленного диска будет определен величиной отверстия матрицы.
Из изложенного можно сделать вывод, что наличие зазора между пуансоном и матрицей очень важно для получения чистой детали. При этом зазор должен быть оптимальным. Его величине с учетом имеющегося опыта определяется соотношением:
(0,05 0,12)s |
(6) |
где: s - толщина листа.
42
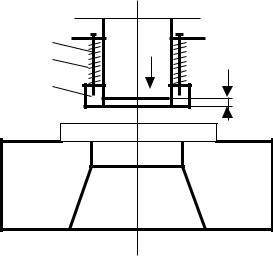
Коэффициент в скобках определяется в зависимости от толщины и механических свойств материала и является справочной величиной.
Возвращаясь к (рис. 11,в), следует обратить внимание, что проникающая в отверстие матрицы деталь оказывается сжатой радиальными силами в пределах упругой деформации. Пуансон же, проникая в отверстие полосы, испытывает со стороны последней такое же сжимающее усилие. Поэтому к усилию, необходимому для разрушения материала по контуру вырубки, добавляются силы трения материала по стенкам матрицы и пуансона.
С учетом сказанного при возвратном движении пуансона вверх упругие силы будут удерживать полосу на пуансоне. Возникает необходимость снять полосу, причем желательно - не затрачивая дополнительного труда. Эта задача решается устройством в штампе специального съемника. Простейшая конструкция съемника показана на (рис. 12)
3 |
|
2 |
|
1 |
е |
|
Рис. 12.Устройство съемника: 1 - кольцо; 2 - пружина; 3 – фиксатор
Кольцо 1 сопрягается с пуансоном по подвижной посадке. При начальном положении пуансона кольцо удерживается фиксаторами 3 так, чтобы его нижняя кромка находилась ниже режущей кромки пуансона на величину «е».
При движении пуансона вниз вместе с ним движется и кольцо 1 до упора в полосу материала. Дальнейшее движение пуансона будет сжимать пружины 2. При обратном движении пуансона (после вырубки детали) кольцо 1, прижимаемое пружинами 2 к полосе материала, снимет последнюю с пуансона. Головки фиксаторов 3, жестко соединенных с кольцом 1, свободно перемещаются при этом в отверстии верхней плиты штампа. Сжатие пружин съемника также увеличивает усилие, которое должен развивать штамп.
Все сказанное объясняет физический смысл коэффициента «К» в выражении (5).
Вырубные штампы применяются как для получения деталей, так и для пробивки отверстий. С учетом этого при конструировании штампа нужно правильно выбирать размер его рабочих органов. Так, при оформлении внешнего контура детали его размеры будут определять размеры отверстия матрицы. Размер же пуансона должен выбираться в этом случае меньше на
43
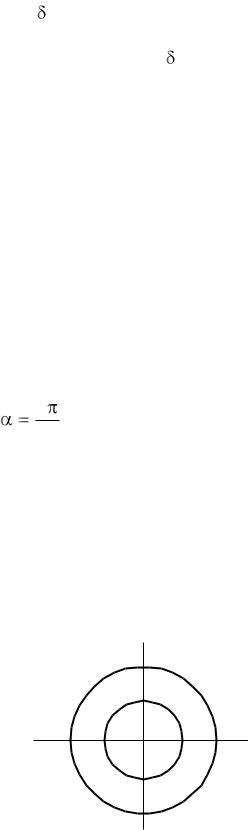
величину рабочего зазора ( ). При оформлении внутреннего контура детали его размеры определяют размер пуансона. Размеры же отверстия матрицы должны быть больше на величину рабочего зазора ( ).
4.3.Типы штампов
Вэлектромашиностроении применяются три основных типа вырубных штампов: простые; совмещенные (или компаундные); последовательные (или шаговые).
Простые штампы предназначены для производства вырубки по одному замкнутому контуру (рис. 12). Они используются для получения заготовок (например, в виде дисков), для пробивки отверстий и т.п. Их достоинства: низкая стоимость, простота наладки, автоматическое отделение детали от отхода, так как вырубленная часть свободно проваливается в отверстие матрицы. Распространение в производстве электрических машин получили так называемые простые пазовые штампы. Такой штамп при одном ходе пуансона формирует в заготовке только один паз. Для получения следующего паза заготовку нужно повернуть на угол
2
z
(7)
где z - число пазов в листе.
Эти штампы получили распространение в условиях индивидуального или ремонтного производства. В серийном производстве такие штампы целесообразно применять при наличии специальных прессов, пазовых полуавтоматов, обеспечивающих высокую производительность.
Главный недостаток пазовых штампов - опасность появления накопленной угловой погрешности. По этой причине листы магнитопровода получаются неидентичными. После шихтовки такие магнитопроводы требуют серьезной доработки.
Рис. 13. Кольцо
Совмещенные (компаундные) штампы обеспечивают вырубку детали по всем контурам за один ход блока пуансонов. Специфику совмещенного штампа можно понять на примере плоской детали в виде кольца (рис. 13). Как видно, деталь образована двумя контурами вырубки в виде концентрических
44
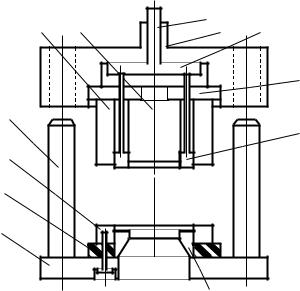
окружностей. Устройство штампа, схематически показанного на (рис. 14), обеспечивает вырубку этой детали по обоим контурам одновременно.
3 |
2 |
6 |
5 |
7 |
|||
|
|
|
4 |
11 |
|
|
|
|
|
|
12 |
10 |
|
|
|
9 |
|
|
|
8 |
|
|
|
|
|
1 |
|
Рис. 14. Схема совмещенного штампа |
Рассмотрим устройство совмещенного штампа подробнее. Матрица 1 имеет две режущие кромки, примыкающие к ее внутренней и внешней цилиндрическим поверхностям. Она жестко закреплена (например, винтами) на нижней плите 8 штампа. Снаружи матрица охвачена съемным кольцом 10, опирающимся на упругий элемент 9. Подвижная часть штампа содержит два режущих элемента: внутренний - пуансон 2, входящий в отверстие матрицы, и внешний - обсечное кольцо 3, в которое матрица входит при вырубке. Между ними расположен выталкиватель 12, приводимый в движение стержнем 6 через диск 5.Пуансон и обсечное кольцо жестко закреплены на диске 4. Вся подвижная часть штампа собрана на верхней плите с хвостовиком 7, используемой для соединения с ползуном пресса. Части штампа с необходимой точностью ориентируются друг относительно друга с помощью колонок 11 нижней плиты, входящими в соответствующие отверстия верхней плиты.
Для выштамповки детали заготовку в виде полосы нужно расположить на поверхности матрицы и включить рабочий ход пресса. Блок пуансонов, двигаяся вниз, вырубает деталь одновременно по обоим контурам. При этом пуансон 2, проникая в отверстие матрицы 1, образует отход в виде диска, свободно падающего вниз. Обсечное кольцо 3, смещая съемник 10 вниз, сжимает упругий элемент 9 и обрубает деталь по внешнему контуру матрицы. При этом матрица вместе с деталью проникает в зазор между пуансоном 2 и обсечным кольцом 3, приподнимая выталкиватель 12. Двигаяся вверх вместе с ползуном пресса и верхней плитой штампа, стержень 6 встречает упор, смещает выталкиватель 12 вниз, в результате чего вырубленная деталь падает на
45
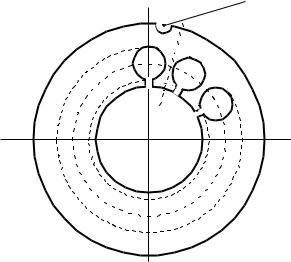
поверхность матрицы. Здесь же располагается и внешний отход материала, снятый с матрицы кольцом съемника 10. Теперь можно полосу материала сдвинуть на величину шага штамповки и вырубить новую деталь. Одновременно нужно удалить уже готовую деталь, что удлиняет рабочий цикл штамповки. Удалить готовую деталь из зоны штамповки будет еще труднее, если вдоль одной из ее кромок будут выполнены зубцы.
От рассмотренной модели легко перейти к конструкции штампа для листа ротора или статора. В этом случае матрица по своим контурам будет идентична форме детали, а блок пуансонов необходимо будет дополнить пазовыми пуансонами, расположив их строго против пазовых отверстий матрицы.
Из изложенного нетрудно понять, что совмещенный штамп обеспечивает высокую идентичность деталей. Это очень важно для обеспечения точности сборки (шихтовки) магнитопровода. Однако это качество в наибольшей степени реализуется, если при сборке будет обеспечено совпадение пазов, вырубленных одноименными пуансонами, т.к. размеры пазов и их взаимное положение в каждом листе будут строго повторять размеры и положение соответствующих пазовых пуансонов.
Для решения этой задачи в одном из контуров листа предусматривается так называемый «матричный знак» Последний выполняется в виде лунки или в виде выступа. Пример расположения матричного знака показан на эскизе статорного листа (рис. 15)
М
Рис. 15. Размещение матричного знака «М»
Следует обратить внимание, что ось матричного знака «М» не должна совпадать ни с осью паза, ни с осью зубца. Выполнение этого требования позволяет при шихтовке не только избежать поворота листа вокруг оси, но и его переворота.
В качестве матричного знака могут быть использованы и штатные элементы конструкции такие, как шпоночный паз или др. В массовых сериях
46
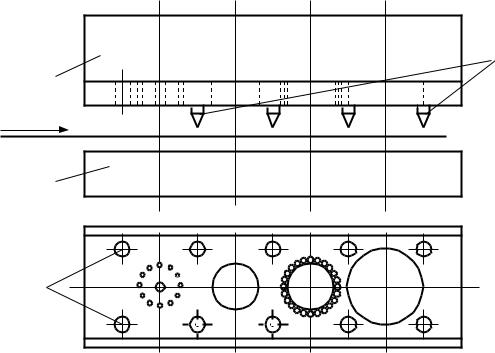
асинхронных электродвигателей матричный знак выполнен в виде выступа, что облегчает решение задачи механизации шихтовки магнитопровода.
Главный недостаток совмещенного штампа - сравнительно низкая производительность, что связано с дополнительным временем для извлечения детали из зоны штамповки.
Последовательные (шаговые) штампы в большой степени совмещают главные достоинства простых и компаундных штампов: высокая производительность и идентичность деталей. Именно по этой причине, не взирая на их высокую стоимость, последовательные штампы чаще всего используют в крупносерийном и массовом производстве. Операция штамповки в последовательном штампе разделена на несколько переходов, которые выполняются его отдельными элементами, сдвинутыми на величину шага штамповки. Для примера рассмотрим конструктивную схему и работу последовательного штампа для одновременной вырубки листов статора и ротора асинхронного двигателя (Рис. 16)
Блок матриц 1 представляет собой монолитную плиту, в которой выполнены четыре позиции формообразования роторных и статорных листов:
пробивка пазов ротора и центрального отверстия под вал; вырубка листа ротора; пробивка пазов статора; вырубка листа статора.
а) |
4 |
2 |
Подача |
полосы |
1 |
б) |
3 |
Рис. 16. Схема устройства последовательного штампа: а) вид на штамп сбоку; |
б) вид на блок матриц сверху |
Таким образом, на первой и третьей позициях штампа в отверстия матрицы проваливаются отходы, а на второй и четвертой - листы ротора и статора соответственно. Свободное удаление вырубленных отходов и деталей через отверстия матрицы позволяет поднять производительность штамповки.
47
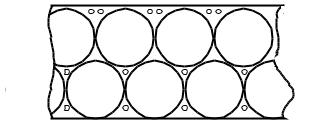
Идентичность пазовой зоны листов ротора (также как и листов статора) очевидна. Однако штамповка листов в четыре перехода ставит задачу точного позиционирования материала. В рассматриваемом примере она решается тем, что в полосе на первой позиции пробиваются дополнительные отверстия 3. При продвижении полосы на величину шага штамповки эти отверстия используются ловителями 4 для точной ориентации заготовки. Ловители 4 выполнены в виде цилиндрических стержней с коническими концами.
4.4. Автоматизация листовой штамповки
Крупносерийное и массовое производство электрических машин в современных условиях немыслимо без решения задачи автоматизации трудоемких процессов, всемерной экономии трудовых и материальных ресурсов. В производстве асинхронных электродвигателей серии 4А для штамповки листов магнитопроводов применяют в основном три способа: однооперационный автоматический - в многопозиционный штампах последовательного действия; многооперационный - в совмещенных (компаундных) штампах; смещенный - вырубка заготовок в виде дисков на «маточных» прессах и последующая их штамповка на пазовых автоматах. При использовании холоднокатаной рулонной стали, прогрессивным считается первый способ, используемый для штамповки листов диаметром до 250 мм по однорядной и двухрядной схеме /11/.
С целью экономии электротехнической стали при изготовлении листов сердечников двигателей с высотой оси 56 и 63 мм применяется двухрядная штамповка на четырехпозиционных шаговых штампах, при этом выштамповки на листе располагаются в шахматном порядке (рис. 17). Такое решение позволяет сэкономить до 8 % электротехнической стали. На автоматических линиях применяют шахматный (многорядный) метод вырубки дисковых заготовок, внешней диаметр которых равен внешнему диаметру листов статора.
Рис. 17. Схема двухрядной штамповки
На (рис. 18) показана компоновка автоматизированный технологической линии для штамповки листов электродвигателей с высотой оси 71 - 100 мм. На этом рисунке: 1 - головной пресс-автомат типа РАSR - 250 для шахматной вырубки круглых заготовок: 2 - транспортирующее устройство; 3 - три прессавтомат PASR - 160 для вырубки из круглых заготовок листов статора и ротора.
48
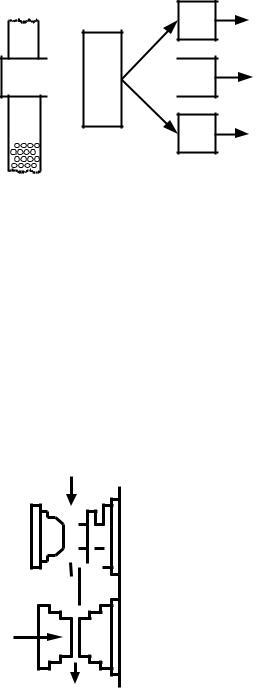
3
1 2
3
3
Рис. 18. Схема автоматизированной линии штамповки
Для штамповки листов сердечников электродвигателей с высотой оси 112 - 132 мм применяют автоматическую линию, включающую два пресс-автомата. Первый - аналогичный PARS - 250, но с усилием 2500 кН с производительностью 60 уд/мин, вырубает из полосы заготовки - диски из рулонного сортамента. Второй пресс-автомат типа «Бакинец», который обеспечивает одновременную штамповку листов ротора и статора отдельными совмещенными штампами. Эти штампы расположены один над другим, а ползун пресса движется в горизонтальном направлении (рис. 19). Стрелкой «а» показан путь готового листа статора. Стрелкой «б» показан путь внутреннего отхода в роторный штамп.
Подача
заготовки
Статорный
штамп б
а
Роторный штамп
Рис. 19. Схема штамповки на пресс-автомате «Бакинец»
Получение дисковых заготовок из рулонного сортамента позволяет сэкономить до 12 % материала.
Использование приема последовательной штамповки при большом диаметре листов становится нерациональным, так как требует применения дорогих крупногабаритных прессов. Задача решается проще, если применить систему «Тандем», где штамповку производят на двух прессах последовательно. Первый пресс штампует лист ротора, второй - лист статора. Схема штамповки по системе «Тандем» представлена на рис. 19. Этот способ пригоден для штамповки листов диаметром до 630 мм.
49
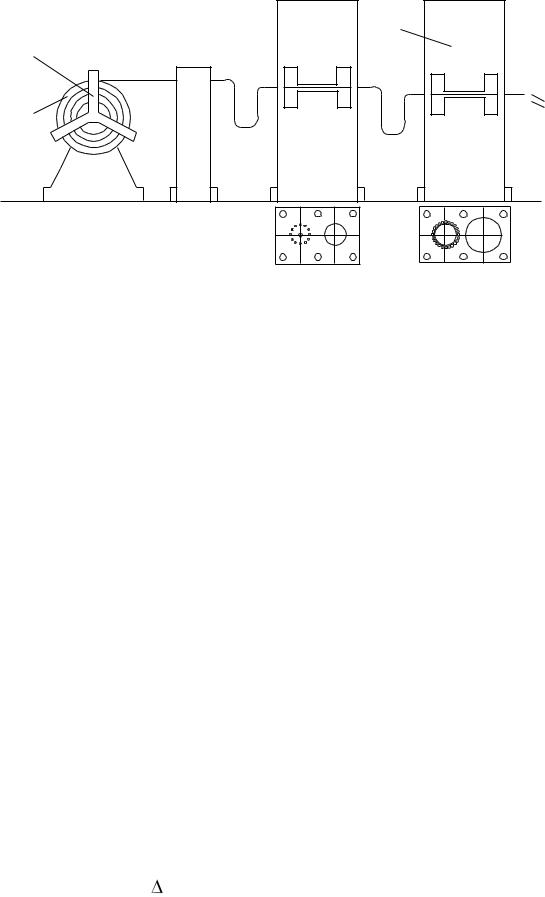
3
2
1
4 |
Рис. 20. Схема штамповки по системе «Тандем»: 1 - рулонный материал; 2 - разматывающее устройство; 3 - пресс для штамповки листа ротора; 4 - пресс
для штамповки листа статора
Штамповку листов магнитопроводов диаметром 400 - 900 мм выполняют смешанным способом. На первой операции с использованием универсального пресса получают дисковые заготовки. На второй операции для штамповки листов ротора и статора используют два пазовых автомата по схеме «Тандем». Быстроходность пазовых автоматов - 1500 уд/мин. Производительность штамповки и точность деталей повышается, если усложнить конструкцию пазового штампа: за один ход блока пуансонов он вырубает 3 - 4 паза, или - три паза ротора и четыре паза статора или др.
При автоматизации листоштамповочных работ большое значение приобретает износоустойчивость штампов, называемую в производственной практике стойкостью штампов.
4.5. Стойкость вырубных штампов
Стойкость вырубного штампа оценивается количеством деталей, которое может быть им изготовлено до полного износа. Износ штампа проявляется в том, что его режущие кромки постепенно затупляются, приобретают закругленную фаску. Режущие свойства штампа ухудшаются, на деталях появляются заусенцы. Высота заусенцев на деталях может характеризовать степень затупление штампа.
Восстановить режущие кромки штампа можно его повторной заточкой. Эта операция выполняется на плоско - шлифовальном станке. Как показано на (рис. 21,) для заточки штампа на плоских поверхностях матрицы и пуансона снимают слой толщиной h. Важно, чтобы после заточки рабочий зазор штампа остался неизменным. Вот почему отверстие матрицы снабжено цилиндрическим пояском с высотой h и только дальше расширяется на конус.
50