
Учебное пособие 800110
.pdf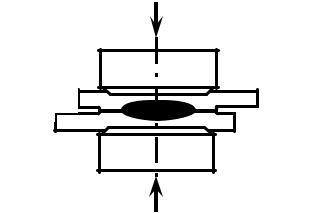
ФГБОУ ВО «Воронежский государственный технический университет»
Кафедра технологии сварочного производства и диагностики
174-2017
МЕТОДИЧЕСКИЕ УКАЗАНИЯ
к выполнению курсовой работы по дисциплине «Технология и оборудование контактной сварки» для студентов направления 15.03.01 «Машиностроение» (профиль «Оборудование и технология
сварочного производства») очной формы обучения
Воронеж 2017
1
Составитель канд. техн. наук Д.И. Бокарев
УДК 681.791 (07) ББК 34.641Я7
Б 786
Методические указания к выполнению курсовой работы по дисциплине «Технология и оборудование контактной сварки» для студентов направления 15.03.01 «Машиностроение» (профиль «Оборудование и технология сварочного производства») очной формы обучения / ФГБОУ ВО «Воронежский государственный технический университет; сост. Д.И. Бокарев.
Воронеж, 2017. 36 с.
В методических указаниях приведены необходимые сведения и рекомендации по расчету режимов сварки и трансформатора для контактных сварочных машин. Указания содержат требования к работе и порядок еe выполнения, список рекомендуемой литературы, приведены варианты заданий с эскизами предлагаемых конструкций.
Данные указания предназначены для студентов четвертого курса.
Табл. 13. Ил. 13. Библиогр.: 11 назв.
Рецензент канд. техн. наук, доц. И.Б. Корчагин
Ответственный за выпуск зав. кафедрой д-р техн. наук, проф. В.Ф. Селиванов
Печатается по решению учебно-методического совета Воронежского государственного технического университета
©ФГБОУ ВО “Воронежский государственный технический университет”, 2017
2
1 Задачи и содержание курсовой работы
Вданной работе рассматриваются вопросы выбора материала, способа сварки, оборудования применительно к контактной сварке. Задачи работы – закрепить полученные теоретические знания и выработать навыки их самостоятельного применения при решении практических задач.
Впояснительной записке приводится:
-введение;
-описание конструкции изделия и условия ее работы;
-обоснование выбора материала;
-свариваемость материала;
-расчет параметров режима сварки;
-выбор материала и конструкции электродов;
-приближенный расчет трансформатора и выбор сварочной машины.
2 Методика выполнения курсовой работы
2.1 Описание конструкции и условий эксплуатации изделия
В пояснительной записке отмечаются конструктивные особенности сварного узла с указанием отдельных деталей и их назначения (рекомендуется выполнить эскиз изделия с указанием габаритных размеров и обозначением сварных швов). Здесь же необходимо указать условия работы изделия.
По согласованию с руководителем работы допускается изменение заданной конструкции узла для улучшения ее технологичности. Необходимо самостоятельно определить конструктивные элементы изделия и сварных соединений, которые не заданы изначально. В частности, величину нахлестки, расстояние между сварными точками и т.д. [9].
Минимальная величина нахлестки – наименьшая ширина сопрягаемой части соединяемых деталей без радиуса закругления соседних элементов (стенки, полки). При радиусе закругления r < 2s
1
в нахлестку включают не только радиус, но и толщину стенки (таблица 1).
Таблица 1 |
|
Расстояние от центра |
||||
s, |
Минимальная величина |
точки или оси шва до края |
||||
мм |
нахлестки, мм |
нахлестки должно быть не |
||||
|
Алюминиевые, |
Стали, |
менее |
50 % от величины |
||
|
магниевые, |
титановые |
нахлестки. |
Расстояние ме- |
||
|
медные сплавы |
сплавы |
||||
|
жду осями соседних рядов |
|||||
0,5 |
10 |
8 |
||||
выбирают на 20 % больше |
||||||
1,0 |
14 |
11 |
||||
шага |
точек. Для каждой |
|||||
1,2 |
16 |
13 |
||||
толщины и марки металла |
||||||
1,5 |
18 |
14 |
||||
определяют |
минимальное |
|||||
2,0 |
20 |
17 |
||||
|
|
|
значение шага точек tШmin . |
|||
2,5 |
22 |
19 |
||||
3,0 |
26 |
21 |
При этом принимается, что |
|||
4,0 |
32 |
28 |
||||
если |
tШ > |
tШmin , то IШ ≤ |
||||
|
|
|
0,05IСВ , и шунтирование тока практически не влияет на электриче-
ское поле и размеры ядра. Примерный шаг точек приведен в таблице 2; для других материалов и толщин он определяется на основании справочных данных или расчетным путем [9].
Значения тока шунтирования IШ , тока во вторичном контуре
I2 и сварочного тока IСВ (протекающего через сварную точку) оп-
ределяют по формулам
IШ IСВ rЭЭ /rШ ; I2 IСВ IШ ; IСВ I2 IШ , (1)
где rЭЭ и rШ - соответственно электрическое сопротивление зоны
сварки и шунта.
Сопротивление шунта рассчитывают по формуле
rЭЭ кЭ 2 tШ /(sbпр), |
(2) |
где кэ ~ 0,4; ρ – удельное электросопротивление; tШ - шаг точек; s – толщина деталей; bпр - приведенная с учетом растекания тока
ширина шунта, равная (dк + dп)/2 (dк – диаметр контакта деталь – деталь и электрод – деталь, dп – диаметр пластического пояска). Зная
2
IСВ и rЭЭ по формуле (1) определяют rШ , а затем по формуле (2) tШ .
Таблица 2 - Рекомендуемый шаг точек при точечной сварке низкоуглеродистых сталей / алюминиевых, магниевых, медных сплавов
|
Толщина |
|
Рекомендуемый минимальный шаг точек, мм |
|
|
одной |
|
при сварке |
при сварке |
|
детали, мм |
|
2-х деталей |
3-х деталей |
1,0 |
|
12 / 15 |
20 |
|
2,0 |
|
18 / 25 |
30 |
|
3,0 |
|
26 / 35 |
40 |
|
4,0 |
|
36 / 45 |
50 |
|
6,0 |
|
50 / 65 |
80 |
Примечание: при сварке легких сплавов минимальный шаг увеличивается на 15 %, а при сварке аустенитной стали и жаропрочных сплавов шаг может быть уменьшен на 15 %. В тех случаях, когда по конструктивным соображениям принимается шаг точек меньше минимально допустимого, необходимо учитывать токи шунтирования и при отработке режима на образцах сварку производить с шагом, равным шагу на деталях.
2.2 Обоснование выбора материала конструкции
Материал для изготовления выбирают в зависимости от условий работы будущего изделия. Кроме того, при выборе материала необходимо учитывать технологичность конструкционных металлов
исплавов, их свойства, стоимость.
Впояснительной записке необходимо привести химический состав материала, его основные физические свойства, механические характеристики, вид термообработки.
2.3 Оценка свариваемости материала изделия
Оценка свариваемости базируется на литературных данных в условиях выбранного метода сварки, а также на теплофизических свойствах металла или сплава и общих представлениях о процессе образования соединений.
Должны учитываться конкретные условия протекания процессов формирования физического контакта, удаления оксидных пле-
3
нок и образования металлических связей в твердой и жидкой фазах при контактной электросварке.
Необходимо также провести анализ степени развития сопутствующих процессов: эффекта воздействия тепла на металл околошовной зоны, условий кристаллизации металла, характера и степени пластической деформации.
В результате анализа должен быть выбран оптимальный для данного материала и конструкции изделия термомеханический цикл.
2.4 Выбор и расчет параметров режима сварки
2.4.1 Выбор материала и конструкции электродов
Материал электродов выбирают в зависимости от типа свариваемого материала по ГОСТу и литературным данным.
Форму и размеры рабочей поверхности электродов выбирают в зависимости от толщины и типа материала, траектории движения электродов (таблица 3) [9].
Для листовых плоских или слегка изогнутых деталей применяют электроды с плоской рабочей поверхностью. Сферическую форму поверхности следует выбирать при сварке легких сплавов и при движении электродов по дуге окружности. Для рельефной сварки цилиндрических деталей (например, проволоки) форма рабочей поверхности вогнутая с радиусом закругления, как у детали; для конусных деталей – конусная и т.п.
2.4.2 Расчет усилия сжатия электродов
Величина сварочного усилия РСВ определяется в зависимости от типа материала и его толщины
РСВ = Кр·s, (3)
где Кр – коэффициент, зависящий от материала (таблица 4), s – толщина деталей, мм;
При необходимости в зависимости от материала и технологии сварки по литературным данным определяют ковочное усилие РК. Подбирается оптимальная циклограмма процесса (изменение усилия и тока в процессе сварки) [9].
4
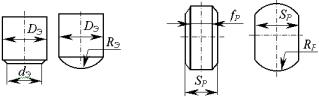
Таблица 3 - Рекомендуемые размеры электродов и роликов, мм
|
|
Размеры электродов |
|
|
Размеры роликов |
||||||||
|
Толщина |
|
|
|
|
|
|
|
|
|
|
|
|
|
деталей |
|
|
|
|
|
|
|
|
|
|
|
|
|
|
|
|
|
|
|
|
|
|
|
|
||
|
|
Углеродистые, коррозионно |
- |
Алюминиевые, магниевые |
|||||||||
|
|
стойкие, жаропрочные стали |
|
и медные сплавы |
|||||||||
|
|
dЭ |
DЭ |
|
RЭ, RР |
SР |
|
fР |
DЭ |
|
SР |
RЭ, RР |
|
0,3 |
3 |
12 |
|
15-25 |
6 |
|
3 |
12 |
|
12 |
25 |
||
0,5 |
4 |
12 |
|
25-50 |
6 |
|
4 |
16 |
|
16 |
50 |
||
0,8 |
5 |
12 |
|
50-75 |
10 |
|
5 |
16 |
|
16 |
50-75 |
||
1,0 |
5 |
12 |
|
75-100 |
10 |
|
5 |
16 |
|
16 |
75 |
||
1,2 |
6 |
16 |
|
75-100 |
12 |
|
6 |
16 |
|
16 |
75 |
||
1,5 |
7 |
16 |
|
100-150 |
12 |
|
7 |
20 |
|
20 |
75-100 |
||
2,0 |
8 |
20 |
|
100-150 |
15 |
|
8 |
20 |
|
20 |
100 |
||
2,5 |
9 |
20 |
|
150-200 |
18 |
|
9 |
25 |
|
25 |
100 |
||
3,0 |
10 |
25 |
|
150-200 |
20 |
|
10 |
25 |
|
25 |
100-150 |
||
3,5 |
11 |
25 |
|
200-250 |
22 |
|
11 |
25 |
|
25 |
150 |
||
4,0 |
12 |
25 |
|
200-250 |
24 |
|
11 |
32 |
|
32 |
200 |
||
|
Примечание: размеры D, S – минимально рекомендуемые. |
||||||||||||
Таблица 4 |
|
|
|
|
|
|
|
|
|
|
|
|
|
|
Ма т ер иа л |
|
|
|
|
|
Кр, Н/мм |
|
|||||
|
|
|
точечная сварка |
|
роликовая сварка |
||||||||
|
|
|
|
|
|
|
|
||||||
|
Низкоуглеродистая сталь |
|
1000 – 2000 |
|
2500 - 3000 |
||||||||
|
Нержавеющая сталь |
|
|
3500 – 4000 |
|
5000 – 5500 |
|||||||
|
Алюминиевые сплавы |
|
2500 – 3000 |
|
3000 – 3500 |
||||||||
|
Титан и его сплавы |
|
|
2000 – 3000 |
|
3500 – 4000 |
|||||||
|
Латунь |
|
|
|
|
|
|
2000 |
|
|
|
4000 |
2.4.3 Расчет времени сварки
Время сварки определяется, исходя из теплофизических характеристик свариваемого материала и его реакции на термический цикл. Для одноимпульсной сварки малоуглеродистой стали время
5
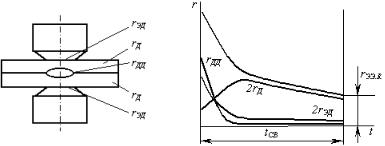
сварки (tСВ) tСВ = (0,1 – 0,3)s – при жестких режимах и tСВ = (0,8 – 1,0)s – при мягких режимах.
В других случаях tСВ выбирают по литературным данным [9].
2.4.4 Расчет сварочного тока
Детали нагреваются теплом, выделяемым при прохождении тока через них и контакты. При сварке двух деталей из одного и того же металла и равной толщины общее сопротивление rЭЭ (Ом) металла между электродами
rЭЭ = 2rД + 2rЭД + rДД , |
(4) |
где rД – собственное активное сопротивление деталей; rЭД – контактное сопротивление между электродом и деталью; rДД – контактное сопротивление между деталями (рисунок 1).
Экспериментально установлено, что в условиях контактной точечной сварки сопротивления rЭД и rДД очень быстро снижаются в процессе нагрева и у стали практически становятся равными нулю при температуре 600 0С (для малоуглеродистой стали) (рисунок 2).
Рисунок 1 - Схема сопро- |
|
тивлений при точечной |
Рисунок 2 - Кинетика измене- |
сварке |
ния электрических сопротив- |
|
лений при точечной сварке |
Таким образом, общее омическое сопротивление участка цепи между электродами в процессе контактной сварки будет определяться собственным сопротивлением свариваемых деталей. Оно может быть найдено, исходя из допущения, что физический контакт между электродом и деталью в конце сварки распространяется на
6

всю площадь диаметром dК, зависящим от приложенного к электродам усилия и толщины деталей (рис. 3).
Для стали dК = dЭ + αs (мм), где s – толщина более тонкой детали, мм; α – коэффициент, зависящий от усилия сжатия электродов. При сварке на «жестких» режимах α = 1,5 ÷ 1,7; на «мягких» - 1,0.
Таким образом, к концу сварки ток к каждой детали будет подводиться через площадки с диаметрами dК и dЭ. Для определения сечения объема, в котором находится поле линий тока, из концов диаметров проводятся прямые под углом 450. При этом деталь условно разбивается на две пластинки неравной толщины δ1 и δ2 (рисунок 3).
Собственное сопротивление пластинки толщиной δ1 + δ2, неравномерно нагретой в условиях точечной сварки с контактами неодинакового размера, можно приближенно рассчитать по формуле как полусумму сопротивлений двух пластинок толщиной 2δ1 и 2δ2 , зажатых соответственно между равными электродами dК и dЭ:
|
|
|
|
|
r |
|
|
1 |
А к |
' |
|
2 1 |
|
|
1 |
А к |
'' |
2 2 |
, |
(5) |
|||
|
|
|
|
|
|
|
Т dЭ2 |
|
|
|
|||||||||||||
|
|
|
|
|
|
Д |
2 1 |
2 2 |
Т dК2 |
|
|||||||||||||
|
|
|
|
|
|
|
|
|
|
|
|
|
4 |
|
|
|
|
|
4 |
|
|
|
|
где А1 |
и А2 – коэффициенты, зависящие соответственно от соотно- |
||||||||||||||||||||||
шений |
|
dЭ |
и |
|
dК |
, учитываю- |
|
|
|
|
|
|
|
|
|
|
|||||||
|
|
|
|
|
|
|
|
|
|
|
|
|
|||||||||||
|
|
|
|
|
|
|
|
|
|
|
|
|
|
|
|||||||||
|
|
2 1 |
|
2 2 |
|
|
|
|
|
|
|
|
|
|
|
|
|
||||||
щие, что фактическое сопротив- |
|
|
|
|
|
|
|
|
|
|
|||||||||||||
ление детали меньше сопротив- |
|
|
|
|
|
|
|
|
|
|
|||||||||||||
ления цилиндра металла, зажа- |
|
|
|
|
|
|
|
|
|
|
|||||||||||||
того между электродами диа- |
|
|
|
|
|
|
|
|
|
|
|||||||||||||
метром dК и dЭ, определяются по |
|
|
|
|
|
|
|
|
|
|
|||||||||||||
графику, |
представленному |
на |
|
|
Рисунок 3 - Схема поля тока для |
||||||||||||||||||
рисунке 4; |
Т' |
и Т" - удельные |
|
|
|||||||||||||||||||
|
|
расчета |
сопротивления детали с |
||||||||||||||||||||
электрические |
|
|
сопротивления |
|
|
неодинаковыми размерами |
кон- |
||||||||||||||||
при температурах Т1 и Т2 соот- |
|
|
тактов |
|
|
|
|
|
|
||||||||||||||
ветственно для пластинок δ1 |
и δ2 |
|
|
|
|
|
|
|
|
|
|
(при сварке стали к концу процесса Т1 = 1200 0С (0,8ТПЛ) и Т2 = 1530 0С (ТПЛ)); к – коэффициент, учитывающий неравномерность нагрева
7

пластинок толщиной δ1 и δ2. При сварке большинства сплавов к = 0,85.
Удельные электрические сопротивления определяют по формулам
Т' |
0 (1 Т1); |
(6) |
Т" |
0 (1 Т2 ), |
(7) |
где 0 - удельное сопротивление металла при 20 0С (для малоугле-
родистой стали 0 = 15·10-6 Ом·м; = 0,004 0С-1).
При сварке деталей равной толщины общее сопротивление между электродами равно 2rД, при сварке деталей разной толщины производится расчет для обеих деталей и берется их сумма.
Рисунок 4 - Зависимость коэффициента А
от отношения d
2
Количество тепла, необходимого для сварки отдельной точки Q, может быть определено из уравнения теплового баланса
Q = QПОЛ + Q1 + Q2 + Q3 (Дж), (8)
где QПОЛ – тепло, расходуемое на нагрев условно выделенного центрального столбика металла диаметром dЭ, зажатого между электродами (рисунок 5); Q1 – потери тепла на нагрев деталей вне центрального столбика; Q2 – потери тепла в электроды; Q3 – потери тепла лучеиспусканием с поверхности свариваемых деталей и конвективным теплообменом
8