
- •Введение
- •Состав МКМ
- •Механические свойства МКМ
- •вдоль волокон
- •вдоль волокон
- •Свойство
- •При сварке по флюсу обеспечиваются достаточно высокие механические свойства сварных соединений (табл. 3.2).
- •Электрошлаковая сварка. В настоящее время освоена электрошлаковая сварка заготовок толщиной 200-300 мм из алюминия и алюминиевых сплавов. Экономически выгодно применять ЭШС при толщине металла более 25 мм.
- •3.4.1. Металлургические особенности сварки
- •Ручная сварка
- •Автоматическая сварка
- •БИБЛИОГРАФИЧЕСКИЙ СПИСОК
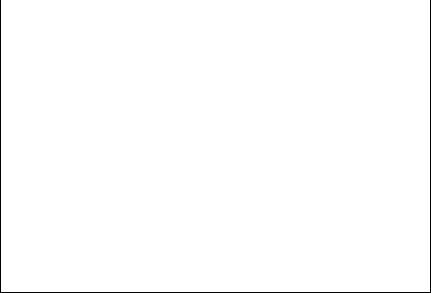
сплавов производят плавящимся и неплавящимся (вольфрамовым) электродами. В первом случае применяют постоянный ток обратной полярности, во втором - прямой.
Сварку вольфрамовым электродом сталей и сплавов с высоким содержанием алюминия с целью разрушения оксидной пленки рекомендуется выполнять на переменном токе.
Сварка вольфрамовым электродом целесообразна для материалов толщиной до 5-7 мм. Хорошее формирование обратного валика позволяет рекомендовать этот способ для сварки корневых швов на сталях повышенной толщины (остальные валики могут выполняться покрытыми электродами, плавящимся электродом под флюсом или в защитных газах).
Примерные режимы аргонодуговой сварки высоколегированных аустенитных сталей указаны в табл. 3.38.
Таблица 3.38 Режимы аргонодуговой сварки вольфрамовым электро-
дом высоколегированных сталей.
Толщина |
Тип |
|
Ток, А |
Расход ар- |
Скорость, |
металла, мм |
соединения |
|
гона, л/мин. |
м/ч. |
|
|
|
||||
|
|
Ручная сварка |
|
|
|
1 |
c |
|
35-60 |
3,5-4 |
- |
2 |
|
75-120 |
5-6 |
- |
|
отбортовкой |
|
||||
3 |
|
|
|
|
|
|
100-140 |
6-7 |
- |
||
|
|
||||
1 |
Встык без |
|
40-70 |
3,5-4 |
- |
2 |
разделки с |
|
80-130 |
5-6 |
- |
3 |
присадкой |
|
120-160 |
6-7 |
- |
|
Автоматическая сварка |
|
|||
1 |
Встык с при- |
|
80-140 |
4 |
30-60 |
2 |
|
120-240 |
6-7 |
20-30 |
|
садкой |
|
||||
4 |
|
200-280 |
7-8 |
15-30 |
|
|
|
||||
1 |
Встык без |
|
60-120 |
4 |
35-60 |
2,5 |
|
110-200 |
6-7 |
25-30 |
|
присадки |
|
||||
4 |
|
130-250 |
7-8 |
25-30 |
|
|
|
Примечание. Диаметр присадочной проволоки 1,6-2,0 мм; ток постоян-
ный прямой полярности.
322
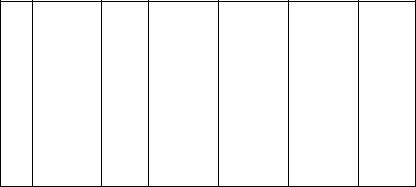
Сварку плавящимся электродом выполняют полуавтоматически или автоматически. При этом необходимо выбирать силу тока, обеспечивающую струйный перенос электродного металла, однако при таком токе на тонколистовом материале могут образовываться прожоги.
Ориентировочные режимы автоматической аргонодуговой сварки плавящимся электродом стыковых соединений из высоколегированных (аустенитных) сталей приведены в табл.
3.39.
Таблица 3.39 Режимы автоматической аргонодуговой сварки плавящимся электродом стыковых соединений аустенитных сталей
|
|
Число |
Диаметр |
|
|
Расход |
|
δ, |
Подготов- |
электрод- |
Iсв, А |
Скорость |
|||
прохо- |
аргона, |
||||||
мм |
ка кромок |
дов |
ной прово- |
|
сварки, м/ч |
л/мин |
|
|
|
локи, мм |
|
|
|||
|
|
|
|
|
|
||
1 |
|
1 |
0,5 |
30-40 |
30-45 |
6 |
|
2 |
Без раз- |
1 |
1,0 |
200-210 |
70 |
8-9 |
|
3 |
делки |
1 |
1,0 |
220-230 |
55-60 |
8-9 |
|
4 |
|
1 |
1,0 |
230-240 |
50 |
8-9 |
|
5 |
С V- |
1 |
1 |
260-275 |
45 |
8-9 |
|
6,5 |
1 |
1 |
250-280 |
35 |
8-9 |
||
образной |
|||||||
8 |
разделкой |
2 |
2 |
300-380 |
45-30 |
11-15 |
|
10 |
2 |
2 |
330-440 |
45-30 |
12-17 |
Электрошлаковая сварка. Невысокая скорость сварки и особенность кристаллизации металла сварочной ванны при ЭШС понижают вероятность образования в шве горячих трещин и уменьшают коробления изделия. Однако увеличенная величина околошовной зоны, длительное пребывание ее и металла шва при повышенных температурах приводят к необратимым изменениям в структуре и свойствах сварных соединений. В результате снижаются прочностные и пластические свойства металла, а на теплоустойчивых сталях в околошовной зоне могут возникать локальные разрушения. При сварке коррозионностойких сталей в околошовной зоне может наблюдаться ножевая коррозия, для предотвращения которой следует
323
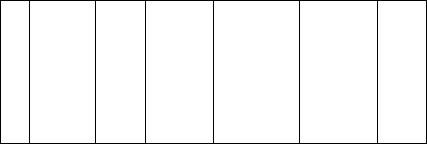
выполнять термическую обработку изделий (закалку или стабилизирующий отжиг).
Применение для электрошлаковой сварки даже фторидных безокислительных флюсов не всегда гарантирует хорошее усвоение сварочной ванной элементов, обладающих большим сродством к кислороду. Поэтому в ряде случаев приходится защищать шлаковую ванну инертным газом (аргоном).
Примеры режимов ЭШС высоколегированных сталей приведены в табл. 3.40.
Таблица 3.40
Режимы ЭШС высоколегированных сталей
δ, |
Тип элек- |
Марка |
Глубина |
Скорость по- |
|
|
|
шлаковой |
дачи электро- |
Iсв, А |
U, В |
||||
мм |
трода |
флюса |
|||||
ванны, мм |
да, м/ч |
|
|
||||
100 |
Проволока |
АНФ-7 |
25-35 |
35 |
600-800 |
40-42 |
|
3мм |
|||||||
100 |
Пластина |
АНФ-7 |
15-20 |
25 |
1200-1300 |
24-26 |
|
10×100 |
|||||||
200 |
Пластина |
АНФ-1 |
15-20 |
22 |
3500-4000 |
22-24 |
|
12×200 |
Электронно-лучевая сварка в вакууме облегчает удаление примесей и газов, но при этом увеличивается испарение легирующих компонентов стали. При глубоком и узком проваре часть газов может задерживаться растущими кристаллами в шве, что приводит к образованию пор.
Сложность аппаратуры и процесса обусловливает применение электронно-лучевой сварки в основном при изготовлении ответственных конструкций из жаропрочных сталей и сплавов.
Сварку металла толщиной до 1 мм выполняют расфокусированным пучком электронов, а при большей толщине рекомендуют остросфокусированный пучок. Для расширения технологических возможностей сварки электронный луч колеблют поперек стыка, вдоль стыка и т.п.
Режимы сварки стали 12Х18Н9Т приведены в табл. 3.41.
324
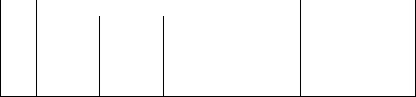
|
|
|
|
|
Таблица 3.41 |
|
|
Режимы ЭЛС аустенитной стали 12Х18Н9Т |
|
||||
δ, |
|
|
Режим сварки |
Ширина шва, мм |
||
мм |
|
U, кВ |
I, А |
Скорость сварки, м/ч |
||
|
|
|
||||
1,5 |
18-20 |
50-60 |
60-70 |
2 |
|
|
10 |
18-20 |
240 |
50 |
4 |
|
|
20 |
20-22 |
270 |
50 |
7 |
|
|
35 |
20-22 |
500 |
50 |
- |
|
Контактная сварка. Точечной и шовной сваркой соединяют детали толщиной 0,5-6 мм.
Свариваемые поверхности деталей из коррозионностойких, жаропрочных сталей и сплавов подготавливают с помощью химического травления или, в ответственных конструкциях, с помощью электрохимического полирования. Зазоры между соединяемыми заготовками должны быть минимальными и для сталей толщиной 1 мм не превышать 0,4 мм на длине 100 мм и 1,2 мм на длине 300 мм. Из-за их низкой тепло- и электропроводности стали сваривают на более жестких режимах, чем низколегированные. Повышенная прочность высоколегированных сталей заставляет существенно увеличить сварочное давление. Термическая стабильность сплавов и невысокая чувствительность к образованию трещин позволяет применять простейшие циклы сварки (рис. 3.14, а), начиная с толщины 3+3 мм, рекомендуется прикладывать ковочное усилие, в 2- 3 раза превышающее сварочное.
Для сварки используют электроды из сплава марки БрНБТ с плоской рабочей поверхностью, стойкость таких электродов при сварке сталей толщиной 1,5 мм составляет 7-8 тыс. точек. Ориентировочные режимы сварки данных сталей см. в табл. 3.42.
Сварка трением может быть использована при изготовлении деталей из аустенитных сталей. Так, при сварке деталей диаметром 127/107 мм из стали 12Х18Н9Т необходимы: частота вращения детали 900 об/мин, давление при нагреве 46 МПа, а при осадке – 17 МПа, величина осадки 7 мм, общее машин-
325
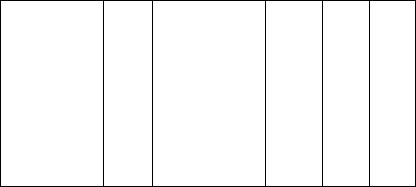
ное время сварки 30 с. Контроль процесса осуществляют по времени.
Таблица 3.42 Режимы точечной сварки легированных сталей и сплавов
Марка материала |
δ, мм |
Диаметр |
Iсв, кА |
tсв, с |
F, кН |
|
электрода, мм |
||||||
|
|
|
|
|
||
12Х18Н9Т |
1+1 |
5 |
8 |
0,16 |
7,5 |
|
ХН78Т |
|
|
|
|
|
|
15Х18Н12СЧТЮ |
3+3 |
10 |
13 |
0,36 |
15,7 |
|
ХН75НБТЮ |
1+1 |
5 |
9,8 |
0,32 |
13,3 |
|
ХН70Ю |
|
|
|
|
|
|
ВЖ85, ВЖ120 |
3+3 |
10 |
10,8 |
0,9 |
22 |
|
ХН38ВТ |
|
|
|
|
|
|
ХН70ВМТЮФ |
1+1 |
5 |
9,8 |
0,36 |
14,9 |
|
ХН77ТЮР |
|
|
|
|
|
|
ВЖ98 |
3+3 |
10 |
10,8 |
1,1 |
26 |
Диффузионная сварка. Высоколегированные стали и сплавы характеризуются низкой свариваемостью. Сварка, как правило, осуществляется в области высоких температур и давлении. Так, при сварке сплавов ХН80ТБЮА и ХН65ВМТЮ в вакууме 10-2 Па требуется удельное давление 20МПа при
1200°С и времени сварки 6 мин. В зоне соединения обнаруживаются следы границы раздела, снижающие пластичность соединения.
3.5. Сварка композиционных материалов
Особенности сварки МКМ. В настоящее время используются следующие виды сварки для соединения МКМ: контактная точечная и шовная, диффузионая в вакууме и инертных газах, электронно-лучевая, лазерная, дуговая в среде защитных газов. В таблице 3.43 приведена сравнительная оценка некоторых способов получения неразъёмных соединений МКМ.
Наибольшее распространение получили контактная и диффузионная сварка, обеспечивающие достаточно хорошее качество швов. Следует отметить, что армирующие волокна при этом не соединяются. Данные способы сварки можно при-
326
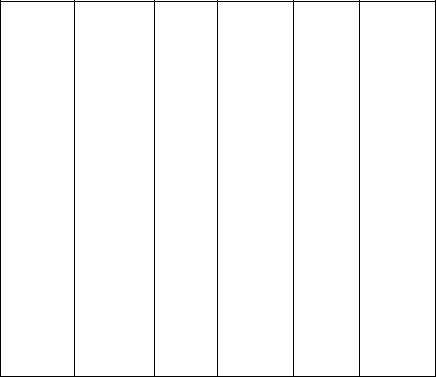
менять и для соединения элементов конструкций из МКМ между собой и с другими конструкционными материалами.
Таблица 3.43 Сравнительная оценка некоторых способов получения
неразъёмных соединений МКМ сваркой и пайкой
Способ со- |
Параметры |
К-т проч- |
Характер- |
Тип при- |
Преимуще- |
единения |
процесса |
ности со- |
ные недос- |
мен. обоственный |
|
единения |
татки |
рудования |
тип швов |
||
|
Тнаг>Тпл; |
|
Выплески |
Универс. |
Связующие |
Контактная τ=0,03-0,08с; |
0,90-0,95 |
металла, |
машины |
и герметич- |
|
сварка |
Рсв=200- |
|
разруш. во- |
контактн. |
ные |
|
800МПа |
|
локон |
сварки |
|
|
|
|
|||
Диффузи- |
Тнаг<Тпл; |
|
Большая |
Специали- |
Прочные. |
онная свар- |
τ=600-1200 |
0,90-0,95 |
трудоёмк. и |
зирован- |
Нанесение |
ка |
с; |
|
сложность |
ные уста- |
плакирую- |
Рсв<10МПа |
|
новки |
щих слоёв |
||
|
|
|
|||
|
Тнаг<Тпл; |
|
Расплавле- |
|
|
ЭЛС, |
|
ние воло- |
Универ- |
|
|
τнаг=0,2-2 с; |
|
|
|||
лазерная |
0,80-0,85 |
кон, слож- |
сальные |
Связующие |
|
сварка |
Рсв=1,33- |
|
ность осу- |
установки |
|
13,3МПа |
|
|
|||
|
|
ществления |
|
|
|
|
|
|
|
|
|
Аргоноду- |
Тнаг>Тпл; |
|
Разупрочн. |
Универ- |
Прочные и |
говая свар- |
τнаг=0,5-5 с; |
0,60-0,75 |
материала, |
сальное |
герметич- |
ка |
Рсв=0,1- |
|
поврежд. |
оборудо- |
ные |
0,5МПа |
|
волокон |
вание |
||
|
|
|
|||
Пайка кон- |
Тнаг>Тпл; |
|
Понижен- |
|
Связующие |
тактная со- |
τнаг=1-20 с; |
0,5-0,6 |
ные прочн. |
Универс. |
Нанесение |
противле- |
Рсв=0,1- |
|
и корроз. |
установки |
плакирую- |
нием |
100МПа |
|
стойкость |
|
щих слоёв |
Важной особенностью контактной и диффузионной сварки является незначительное термическое влияние сварки на волокно МКМ. Последнее объясняется тем, что при диффузионной сварке температура нагрева не превышает температуры плавления матрицы МКМ, а в случае контактной сварки, хотя процесс осуществляется при более высоких температурах, длительность нагрева не превышает сотых долей секунды.
При сварке плавлением композитов соединение обеспе-
327
чивается за счет расплавления металла матрицы. При этом температура нагрева значительно превосходит температуры плавления компонентов КМ.
В результате сильного нагрева в зоне сварки могут произойти изменение взаимосвязи материала матрицы и волокон или их расплавление. Поэтому применение сварки плавлением для соединения МКМ требует специальных технологических мер защиты армирующих волокон от расплавления.
Пайка занимает промежуточное положение между сваркой плавлением и сваркой давлением.
Контактная электросварка является наиболее распро-
страненным способом соединения заготовок из листовых МКМ. Контактную сварку выполняют на универсальном оборудовании. Образование соединения при контактной сварке происходит только за счет расплавления матрицы в зоне контакта. Армирующие волокна, входящие в структуру МКМ, не расплавляются, т. к. для процесса контактной электросварки характерна малая продолжительность сварки при больших сварочных токах и усилиях, обеспечивающих локальное плавление металла матрицы с образованием уплотнительного пояса.
Особенности образования сварной точки можно рассмотреть на волокнистом композиционном материале системы алюминий-бор марки ВКА-1 толщиной 0,8-2,0 мм с объёмным содержанием волокон бора (диаметром 80-100 мкм) от 40 до 50%, полученном методом намотки и последующей диффузионной сварки в вакууме. Слой алюминия АД-1 над бором у поверхности (плакирующий слой) для различных партий материала имел толщину 50, 100, 150, 200 и 250 мкм. Точечную сварку проводили на машинах МТПУ-300 и МТК-75 (электроды из сплава БрКд-1).
Специфическое тепловое поле, возникающее при прохождении через детали из композиционного материала ВКА-1 электрического тока, дает возможность условно представить детали в виде пакета (композиционный материал + плакирую-
328

щий слой + плакирующий слой + композиционный материал) и производить сварку пакета. При толщине плакирующего слоя 200 мкм и более образуется надежный уплотняющий поясок. На макрошлифах после травления выявляется литое ядро эллипсообразной формы (рис. 3.16, а). Однако из рис. 3.16, б видно, что при образовании литого ядра в материале ВКА-1 (сочетание ВКА-1 и Д16Т) взаимное перемешивание затруднено и затрагивает только узкую приповерхностную зону (включая не более одного слоя бора), а основная масса ядра не перемешивается.
Рис.3.16. Макроструктура сварного соединения (х10): а – материалов ВКА-1 + ВКА-1; б – материала ВКА-1 + сплав Д16
Такое явление объясняется наличием частой сетки волокон бора в материале ВКА-1. Следовательно, для ВКА-1 литое ядро представляет собой материал, где матрица нагревалась до плавления.
При сварке композиционного материала помимо получения бездефектного соединения необходимо, по возможности, чтобы соединение обладало композиционными свойствами. Только в этом случае свойства материала в конструкции не снизятся. Для материала ВКА-1 с толщиной плакирующего слоя 200 мкм и более, чтобы получить соединения за счет расплавления этого слоя, целесообразно применять мягкие режимы сварки и невысокие усилия давления.
Как показали прочностные испытания, в этом случае прочность соединения определяется только прочностью мат-
329
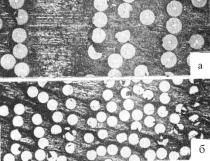
рицы материала. При сварке материала ВКА-1 (с толщиной плакирующего слоя 50100 мкм) электродами со сферической рабочей поверхностью на одноимпульсном режиме обычно наблюдается выплеск. Одной из причин этого является недостаточная толщина плакирующего слоя для образования уплотняющего пояска и удержания расплавленного металла.
В этом случае (при соответствующем подборе режима и геометрии электродов) за счет условий нагрева и неравномерного усилия сжатия металла плакирующего слоя можно обеспечить его интенсивное выдавливание в зазор соединения (практически без образования зоны расплавления).
После выдавливания расстояние между волокнами бора соединяемых деталей составляет 20-80 мкм (рис. 3.17). Такое соединение обладает так называемыми композиционными свойствами, т. е. возможностью передавать значительную часть нагрузки на рядом расположенные волокна бора. Необходимо отметить, что композиционные свойства соединения наиболее полно проявляются только при испытании многоточечных образцов или одноточечных образцов в специальных приспособлениях, исключающих их изгиб (чистый срез).
Рис. 3.17. Микроструктура сварного соединения (х50) материалов ВКА-1 + ВКА-1 при толщине плакирующего слоя 200-250 мкм (а) и
50-100 мкм (б)
330
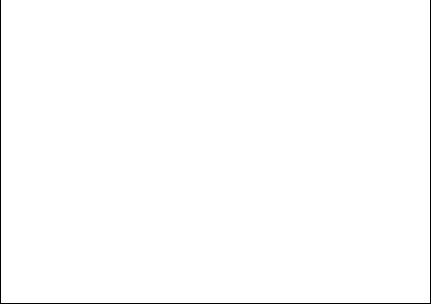
В противном случае при больших изгибающих моментах концентрация на периферии соединения становится решающим фактором, и композиционные свойства не реализуются.
Режимы сварки материала ВКА-1 приведены в табл. 3.44. Таблица 3.44 Режимы точечной сварки композиционного материала
ВКА-1 на машине МТК-75
|
|
|
Усилие, Н |
Сва |
Время |
||
|
Толщи- |
Радиус |
вклю- |
||||
Сочетание |
на мате- |
сферы |
|
|
роч |
чения |
|
|
|
|
|
|
ный |
|
|
материалов |
риалов, |
электро- |
сва- |
ковоч- |
ков. |
||
ток, |
|||||||
|
мм |
дов, мм |
роч- |
уси- |
|||
|
|
|
ное |
ное |
кА |
лия, с |
|
|
0,8 + 0,8 |
150 |
2500 |
- |
25 |
- |
|
ВКА-1 + |
1,0 + 1,0 |
150 |
3500 |
- |
30 |
- |
|
1,2 + 1,2 |
150 |
4000 |
- |
35 |
- |
||
ВКА-1 |
|||||||
1,5 + 1,5 |
200 |
5500 |
- |
45 |
- |
||
|
|||||||
|
2,0 + 2,0 |
200 |
6000 |
- |
50 |
- |
|
|
1,0 + 1,2 |
150/100 |
3500 |
7000 |
30 |
0,05 |
|
ВКА-1 + |
1,0 + 1,5 |
150/100 |
4000 |
8000 |
32 |
0,05 |
|
Д16Т |
1,2 + 1,2 |
150/100 |
4000 |
8000 |
32 |
0,05 |
|
|
1,2 + 1,5 |
150/100 |
4500 |
8000 |
35 |
0,05 |
|
ВКА-1+ |
1,0 + 1,2 |
150/100 |
3500 |
7000 |
25 |
0,05 |
|
01420 |
|||||||
|
|
|
|
|
|
||
Д16Т+Д16Т |
1,5 + 1,5 |
100 |
5000 |
11000 |
43 |
0,06 |
|
Примечание: |
толщина |
плакирующего слоя 200 |
мкм. |
|
|
Видно, что сварочный ток, необходимый для образования соединения на материале ВКА-1, в 1,1-1,3 раза больше, чем для сплава Д16Т аналогичной толщины. Это объясняется теплофизическими свойствами материала ВКА-1. На практике наибольший интерес представляет сварка материала ВКА-1 с алюминиевыми сплавами типа Д16Т и 01420. На макрошлифах в этом случае отчетливо наблюдается надежный уплотняющий поясок, образующийся за счет сплавов Д16Т или 01420 (рис. 3.16, б). Смещение литого ядра в сторону сплавов Д16Т или 01420, по-видимому, объясняется различием температур плав-
331
ления матрицы материала ВКА-1 и сплавов Д16Т и 01420, теплоемкость же в интервале 20-500°С материала ВКА-1 почти в 1,5 раза больше, чем сплавов Д16Т или 01420.
Специфические механические свойства материала ВКА-1 приводят к тому, что требования к циклограмме усилия при сварке значительно отличаются от требований к алюминиевым сплавам. Процесс пластической деформации, образование и рост контактных площадок деталь - деталь при сварке материала ВКА-1 в большой степени зависит от направления волокон бора в свариваемом пакете. Пластическая деформация поперек волокна из-за скручивания пластины в этом направлении оказывается облегченной. Поэтому контактная площадка деталь - деталь имеет вытянутую форму в направлении пониженной жесткости материала (поперек волокна). Это явление особенно четко проявляется на материале с толщиной плакирующего слоя в пределах 50-100 мкм (при малых радиусах сферы электродов и высоких усилиях давления), поскольку в этом случае наблюдается наиболее сильная пластическая деформация материала.
Один из основных дефектов при точечной сварке материала ВКА-1 - выплеск. Его возникновение связано с высокой жесткостью поверхностного слоя, очень малой толщиной плакирующего слоя и образованием несимметричной контактной площадки деталь-деталь. Образование выплеска при сварке материала ВКА-1 недопустимо, поскольку он сопровождается вырывом волокон и образованием «незалечивающихся» внутренних полостей.
На процесс сварки и качество сварных точечных соединений из материала ВКА-1 большое влияние оказывает форма и размеры электродов. Первоначально хорошие результаты были получены при использовании электродов с радиусом сферы 150 мм (для деталей толщиной 0,8-1,0 мм) и 200 мм (для деталей толщиной 1,2 мм и более). Необходимая плотность тока в контакте обеспечивается армированием электродов сталь-
332
ной шайбой с внутренним диаметром 5-8 мм. Однако использование электродов со стальной шайбой не решает полностью проблему сварки композиционных материалов типа ВКА-1. Так, электроды со стальной шайбой приводят к стабильному выплеску на материале с толщиной плакирующего слоя 50-100 мкм. Лучшие результаты для этих и больших толщин плакирующего слоя были получены при использовании электродов, обеспечивающих обжатие периферийной зоны (электрод с обжимкой). Применение электрода с обжимкой позволяет следующее: полностью ликвидировать выплеск при сварке материала с толщиной плакирующего слоя до 50 мкм; уменьшить сварочное усилие (на 20-40%) и, следовательно, снизить вероятность повреждения волокон бора; изменить характер электрического и температурных полей и повысить стабильность качества сварного соединения. Таким образом, при сварке материала ВКА-1 с толщиной плакирующего слоя 200 мкм и более на машинах МТПУ-300 и МТК-75 для образования соединения с литым ядром целесообразно применять электроды со стальной шайбой. При сварке материала с толщиной плакирующего слоя 50150 мкм на машинах МТК-75 рекомендуется применять электроды с обжимкой.
Усадка материала ВКА-1 значительно меньше, чем алюминиевых сплавов, вследствие незначительной пластической деформации каркаса из волокон бора. В связи с этим в точечных соединениях (выполненных как с образованием литого ядра, так и в твердой фазе) таких дефектов, как трещины и поры, нет. Механические свойства сварных соединений приведены в табл. 3.45. Прочность сварных точечных соединений из материала ВКА-1 при статическом срезе в 1,2-1,5 раза, а при отрыве в 2-3 раза меньше, чем сварных соединений аналогичной толщины из алюминиевых сплавов типа Д16Т. Усталостная прочность сварных соединений из материала ВКА-1 приближается к прочности соединений из сплава Д16Т. Причем, чем больше число циклов испытаний, тем меньше различие в
333
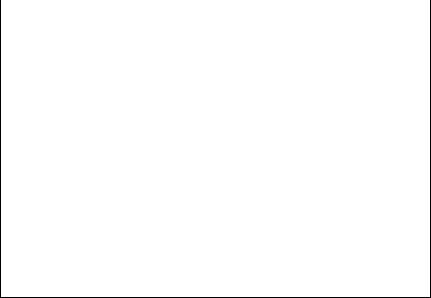
уровнях прочности.
Таблица 3.45 Механические свойства сварных точечных соединений
Сочетание |
Толщина ма |
Усилие среза (в Н) при температуре, |
Усилие от- |
||
материалов |
териалов, мм |
|
°С |
|
рыва, Н |
|
|
20 |
300 |
500 |
|
|
|
|
|
|
|
ВКА-1 + |
0,8 + 0,8 |
1850-2550 |
890-1850 |
250-650 |
290-500 |
ВКА-1 |
|
2180 |
1250 |
420 |
320 |
ВКА-1+ |
1,0 + 1,0 |
2150-3200 |
990-1450 |
280-550 |
330-620 |
ВКА-1 |
|
2610 |
1270 |
390 |
470 |
ВКА-1+ |
1,5 + 1,5 |
2100-3350 |
1210-1950 |
220-640 |
390-510 |
ВКА-1 |
|
2950 |
1650 |
490 |
440 |
ВКА-1+ |
2,0 + 2,0 |
2250-3300 |
1050-1900 |
300-650 |
350-550 |
ВКА-1 |
|
2900 |
1550 |
520 |
450 |
ВКА-1+ |
0,8 + 1,5 |
1750-2750 |
950-1550 |
300-550 |
250-500 |
Д16Т |
|
2050 |
1150 |
390 |
360 |
ВКА-1+ |
1,0 + 1,5 |
1850-3900 |
1100-1750 |
400-610 |
300-630 |
Д16Т |
|
2750 |
1560 |
440 |
480 |
ВКА-1+ |
1,5 + 1,5 |
2900-4150 |
850-1590 |
250-550 |
380-650 |
Д16Т |
|
3540 |
1310 |
450 |
470 |
Примечание: толщина плакирующего слоя 200 мкм.
При числе циклов испытаний 2х107 и более значения усталостной прочности соединений из материала ВКА-1 и сплава Д16Т практически одинаковы.
На рис. 3.18 показаны варианты использования как точечной сварки, так и сварки плавлением (АДС). С помощью точечной сварки соединяют внахлёст элементы жёсткости с обшивкой тонкостенных оболочек и панелей. Недостатком этого вида сварки является малая площадь сечения сварной точки, передающей сдвиговые напряжения.
Шовную электросварку используют при изготовлении силовых оболочек и ёмкостей, где требуются прочно-плотные соединения, а также для приварки элементов жёсткости (рис.3.19). Основным условием при контактной сварке МКМ является сохранение целостности армирующих волокон.
334
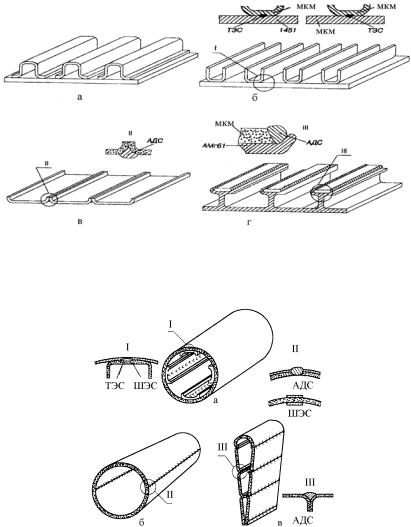
Рис. 3.18. Типовые конструкции сварных панелей из МКМ с продольными элементами жёсткости: а – стрингерная панель; б – панель с П-образными рёбрами жёсткости; в – плоская панель с рёбрами жёсткости; г – тавровая модель с накладками из МКМ
Рис. 3.19. Типовые конструкции силовых оболочек из МКМ цилиндрической формы с внутренним набором (а), конической формы с продольными швами (б) и произвольной формы с продольными рёбрами жёсткости (в)
335
Необходимо также стремиться к сокращению продолжительности температурного воздействия на волокна. Исходя из этих условий, следует ограничивать сварочное усилие и длительность нагрева.
Особенности технологии сварки МКМ на основе тита-
на. Титановые сплавы как конструкционные материалы при достаточно высоком уровне прочности имеют недостаточную жесткость, повысить которую можно путем армирования высокопрочными волокнами. Кроме того, волокнистые КМ (ВКМ) с титановой матрицей могут применяться при температурах, недопустимых для материалов с полимерной и алюминиевыми матрицами. Поэтому задачи получения КМ с титановой матрицей, армированной высокомодульными волокнами или дисперсными частицами, а также разработка методов их сварки являются весьма актуальными.
Перспективными областями для изделий из КМ на титановой основе являются авиационная и ракетная техника. Например, при изготовлении шасси самолета из КМ с титановой матрицей, армированной непрерывными SiC-волокнами, массу некоторых деталей удается снизить в 2 раза по сравнению с деталями из стали. Наряду с уменьшенной массой детали из титановых КМ имеют повышенную стойкость к коррозии под напряжением, не требуют нанесения защитных покрытий. Дисперсно-упрочненные КМ на основе титана с оксидами и карбидами могут служить для изготовления компрессорных
дисков и других изделий, эксплуатируемых при 600-700°С, а армирование титана и его сплавов повышает их жесткость и
расширяет диапазон рабочих температур до 700-800°С. Для армирования титановой матрицы применяют металлические проволоки, а также волокна карбида кремния, бора и углерода. Армирование титановой матрицы волокнами бора и карбида кремния позволяет повысить не только абсолютные, но и удельные характеристики МКМ на основе титана. Поскольку эти волокна хрупки, то для получения компактных композиций
336
Ti-B и Ti-SiC чаще используют диффузионную сварку в вакууме.
Для соединения МКМ на основе титана как между собой, так и с другими металлами применяются способы сварки в твердой фазе, плавлением, а также формирование детали одновременно с диффузионной сваркой монослоев полуфабриката. За рубежом этот способ получил наименование ГИП (HIP - heat inert pressure). Его используют, например, при присоединении (сварке) деталей к цилиндру из КМ стойки шасси самолета.
KM систем Ti-W и Ti-C получают путем диффузионной сварки в вакууме волокон с листами титана при горячем прессовании. Вольфрамовую проволоку равномерно наматывают на лист титана, затем к нему с обеих сторон прикладывают другие листы титана и контактной точечной сваркой прихватывают в нескольких местах. Далее графитовые волокна укладывали равномерно на другой лист титана, затем сверху волокна накрывали вторым листом титана, прихватывая их друг к другу контактной точечной сваркой. Перед сборкой листы титана подвергали химической очистке в щелочном растворе. Вольфрамовую проволоку протирали тканью, смоченной в спирте. Графитовые волокна использовали в состоянии поставки. Перед диффузионной сваркой образцы заворачивают в фольгу из нержавеющей стали толщиной 0,127 мм и приваривали ее к листам титана точечной сваркой вдоль кромок. Затем образцы с обеих сторон покрывают тонким слоем пасты из
алюминиевого порошка грануляцией 1 10-5 мм для предотвращения соединения фольги с графитовыми элементами пресса (пуансоном и основанием) при диффузионной сварке. Диф-
фузионную сварку осуществляют в вакууме 1,3 10-2 Па при
870°С и давлении 7 МПа. Продолжительность сварки составляла 1 ч. После сварки фольгу удаляют, а поверхность образцов подвергают химическому травлению на глубину 0,05 мм с каждой стороны. В КМ обеих систем при диффузионной свар-
337
ке происходит соединение волокон с матрицей.
При сварке обоих видов КМ применяют и аргонодуговую сварку (ручную и механизированную) вольфрамовым электродом без присадочной проволоки. Перед сваркой кромки образцов механически обрабатывают с таким расчетом, чтобы волокна равномерно подходили к торцам свариваемых кромок.
Сварку образцов из КМ системы Ti-W производят при токе, значение которого на 10 % больше, чем при сварке листов титана той же толщины. Чем выше погонная энергия сварочной дуги, тем интенсивнее взаимодействуют вольфрам и титан. Ручная сварка приводит к существенному уменьшению диаметров вольфрамовых волокон из-за более высоких значений погонной энергии сварочной дуги. В местах чрезмерного перегрева происходит полное растворение вольфрамовых волокон в титане. Образование несплошностей в сварном шве является случайным явлением. Они располагаются по границе между волокнами и титаном. Зафиксирована незначительная тенденция к образованию мелких пор в сварочном шве.
Впроцессе диффузионной сварки вольфрамовых волокон
ститаном вольфрам, отличаясь большей диффузионной подвижностью, проникает в титан, образуя переходную зону на границе W-Ti. Во время дуговой сварки степень проникновения вольфрама в титан зависит от значения погонной энергии сварочной дуги. Вольфрам образует с титаном твердый раствор. Увеличение микротвердости металла на границе W-Ti объясняется легированием титановой матрицы вольфрамом. Однако при дуговой сварке вследствие значительного перегрева в сварном шве может образоваться предельный твердый раствор Ti-W, что создает условия для сегрегации вольфрама.
Удовлетворительная свариваемость плавлением КМ на основе титана достигается при объемном содержанием волокон вольфрама до 20 %.
При аргонодуговой сварке образцов KM Ti-C получают удовлетворительные результаты в том случае, когда волокна
338