
- •Введение
- •Состав МКМ
- •Механические свойства МКМ
- •вдоль волокон
- •вдоль волокон
- •Свойство
- •При сварке по флюсу обеспечиваются достаточно высокие механические свойства сварных соединений (табл. 3.2).
- •Электрошлаковая сварка. В настоящее время освоена электрошлаковая сварка заготовок толщиной 200-300 мм из алюминия и алюминиевых сплавов. Экономически выгодно применять ЭШС при толщине металла более 25 мм.
- •3.4.1. Металлургические особенности сварки
- •Ручная сварка
- •Автоматическая сварка
- •БИБЛИОГРАФИЧЕСКИЙ СПИСОК
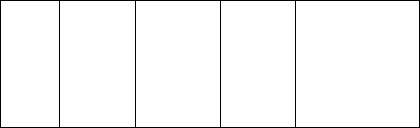
соединения из технического алюминия равнопрочны основному материалу, а при сварке алюминиевых сплавов коэффициент прочности швов около 0,9.
Таблица 3.6 Режимы плазменной сварки стыковых соединений из
алюминиевого сплава АМг6
δ, мм |
Iсв, А |
Uд, В |
Vсв, м/ч |
Расход плазмообр. |
|
газа, л/мин |
|||||
|
|
|
|
||
3 |
120 |
16 |
50 |
2-3 |
|
4 |
150 |
16 |
30 |
2-3 |
|
5 |
220 |
18 |
30 |
3-4 |
|
6 |
350 |
18 |
30 |
4-5 |
|
7 |
350 |
20 |
25 |
5-6 |
|
8 |
380 |
20 |
25 |
5-6 |
Одной из важнейших особенностей микроплазменной сварки является снижение деформации изделий на 25-30% по сравнению с обычной аргонодуговой сваркой.
Электрошлаковая сварка. В настоящее время освоена электрошлаковая сварка заготовок толщиной 200-300 мм из алюминия и алюминиевых сплавов. Экономически выгодно применять ЭШС при толщине металла более 25 мм.
ЭШС обеспечивает высокую производительность сварочных работ, что видно из сравнения двух способов сварки заготовок сечением 140x630 мм из сплава АМг6:
|
Электрошлаковая |
Аргонодуговая |
|
сварка: |
сварка: |
Подготовка кромок |
- |
X-образная |
Число проходов |
1 |
100-150 |
Продолжительность |
7 |
900 |
сварки, мин |
|
|
Плотность тока,А/мм2 |
2,5 |
12 |
Сварка производится электродами большого сечения – пластинчатыми и плавящимися мундштуками. Электродную проволоку из алюминия диаметром вплоть до 5 мм применять затруднительно, это связано с необходимостью поддержания большого вылета электрода. Нагрев алюминиевой проволоки
233
на таком вылете приводит к потере его жёсткости, колебаниям в зазоре, нарушению электрического контакта в мундштуке. Вследствие этого устойчивость процесса нарушается, в сварном шве появляются непровары и несплавления.
В качестве флюсов используют смеси фторидов и хлоридов щелочных и щелочноземельных металлов. Поскольку такие флюсы в расплавленном состоянии имеют повышенную жидкотекучесть, принимают дополнительные меры для предотвращения их утечки через возможные зазоры между поверхностями деталей и формирующих устройств: асбестовые шнуры, глину и т.д.
При сварке алюминиевых сплавов рекомендуется использование безнатриевых флюсов (например, 30% KCl; 30% MgCl; 30% LiF; 10% MgF2), так как натрий, попадая в сварной шов, концентрируется на границах зёрен и снижает прочность и пластичность сварных швов.
Электрошлаковая сварка термически не обрабатываемых алюминиевых сплавов, содержащих в качестве легирующего элемента магний, не вызывает особых затруднений.
Термически упрочняемые сплавы, где в качестве, например, легирующего элемента применяют медь, претерпевают в процессе сварки разупрочнение в зоне термического влияния и появляется опасность образования кристаллизационных трещин в металле шва.
Сплав АМг6 толщиной 140 мм сваривают пластинчатым электродом из листового модифицированного цирконием сплава АМг6 с использованием флюса АН-А301, плотность тока 2,5-4 А/мм2, при напряжении на шлаковой ванне 29-31 В. Для формирования шва применены медные водоохлаждаемые кристаллизаторы.
Прочность сварных соединений, полученных ЭШС, не уступает механическим свойствам соединений, выполненных другими способами сварки, но средний коэффициент прочности не превышает 0,8.
234
Сварку термоупрочняемых сплавов следует осуществлять в условиях интенсивного отвода теплоты от свариваемых кромок, вести процесс сварки на жёстких режимах ( при повышенных скоростях перемещения ползунов) и дополнительно легировать металл шва, компенсируя снижение механических характеристик сварного соединения в целом.
Электронно-лучевая сварка (ЭЛС). Эффективным спосо-
бом соединения деталей и узлов из алюминиевых сплавов является ЭЛС.
При ЭЛС в вакууме успешно решается вопрос разрушения и удаления оксидной плёнки с поверхности свариваемых заготовок. Это происходит вследствие механического воздействия на плёнку паров металла, а также разложения оксида алюминия в процессе контакта твёрдой плёнки с жидким алю-
минием при температуре 1450°С и остаточном давлении не более 0,13 Па по реакции
Al2O3 тв + Alж → 3AlOг.
Упругость паров субоксида AlO при высокой температуре во много раз выше, чем алюминия, поэтому реакция будет идти вправо.
ЭЛС по сравнению с другими видами сварки плавлением имеет преимущество: твёрдожидкое состояние металла шва существует в течение весьма короткого промежутка времени. Поэтому внутренние напряжения, обусловленные этим состоянием металла, не успевают привести к образованию кристаллизационных трещин. Для высокопрочных алюминиевых сплавов можно избежать разупрочнения металла в околошовной зоне при высоких скоростях сварки, обеспечивающих минимальное термическое воздействие на основной металл.
Преимущества ЭЛС по сравнению, например, с автоматической аргонодуговой сваркой (АДС) иллюстрируют показатели сварки шпангоута из алюминиевого сплава типа 2219 толщиной 60 мм, приведенные ниже:
235
|
Электронно- |
Аргонодуговая |
|
|
лучевая сварка |
сварка |
|
Число проходов |
2 |
10 |
|
Время подготовки, ч |
8 |
80 |
|
Присадочный металл, к |
- |
13,3 |
|
Качество швов |
Хорошее |
Удовлетворительное |
|
Отношение глубины к |
19 |
0,2 |
|
ширине шва |
|||
|
|
||
Коэффициент прочности |
0,75 |
0,5 |
|
Скорость сварки, м/ч |
60 |
6 |
Алюминиевые сплавы толщиной до 20 мм могут свариваться в нижнем положении. Сварка металла толщиной 20-150
ммвыполняется горизонтальным пучком снизу вверх или в горизонтальной плоскости, а сварка металла толщиной более 150
мм- горизонтальным пучком на подъём.
На качество формирования горизонтальных швов заметно влияет угол наклона пучка к стыку. В случае сварки заготовок толщиной до 150 мм лучшие результаты достигаются при сварке углом вперёд. В зависимости от толщины свариваемого металла угол наклона пучка изменяется от 5 до 15 .
При выполнении вертикальных швов на подъём на заготовках толщиной 40-250 мм для предотвращения образования внутренних дефектов в виде пустот и уменьшения вытекания жидкого металла электронный пучок в процессе сварки отклоняют на 5-17° от горизонтального положения вниз.
Для обеспечения нормальных условий формирования шва в начале и в конце стыка достаточно, чтобы размеры ввод- но-выводных планок были 50х50х5м мм. Крепятся они к свариваемым заготовкам на прихватках, выполняемых дуговой сваркой или с помощью сварочных приспособлений, обеспечивающих плотное прижатие к торцам стыка.
При сварке стыковых соединений зазор между кромками не должен превышать 0,1-0,15 мм. При использовании присадки (обычно диаметром 1,2-1,5 мм) требования к точности сборки деталей несколько снижаются: зазор между кромками
236
может быть увеличен до 0,5 мм.
Закономерности изменения параметров сварных швов от режимов ЭЛС для алюминия аналогичны зависимостям, наблюдаемым для других металлов: с увеличением тока луча ширина и глубина проплавления возрастают. Растёт глубина проплавления и при повышении ускоряющего напряжения (при постоянстве тока луча). С увеличением скорости сварки глубина проплавления снижается. При изменении скорости сварки от 20 до 80 м/ч ширина проплавления уменьшается в
1,3-1,5 раза.
В алюминиевых сплавах содержится значительное количество таких элементов, как магний (сплавы АМг3, АМг5, АМг6), цинк и магний (В95, АЦМ), литий (ВАД23, 1420), которые имеют невысокую температуру кипения. Разрежение в вакуумной камере создаёт благоприятные условия для испарения легирующих элементов с высокой упругостью паров. Так,
при 700°С упругость паров алюминия над жидким металлом равна 10-5 Па, а магния – 103 Па.
Рекомендуемые режимы ЭЛС алюминиевых сплавов даны в табл. 3.7. Однако при сварке на оптимальных режимах сплавов АМг6, В95, Д20 и 1420 недопустимого уменьшения всех легирующих элементов не наблюдается.
Временное сопротивление разрыву с увеличением количества проходов снижается на 10-30 МПа независимо от исходного состояния материала до сварки, даже на отожжённом материале. Следовательно, основную роль в этом может играть только изменение состава металла шва, что подтверждается результатами спектрального анализа. После однократного прохода с присадочной проволокой или без неё содержание магния в шве сохраняется примерно на том же уровне, что и в основном металле. После двух- и трёхкратного переплава шва количество магния уменьшается. Особенно заметны его потери, когда при третьем проходе присадочная проволока не использовалась.
237
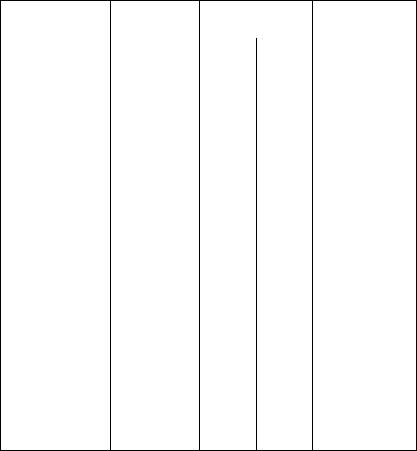
Таблица 3.7 Рекомендуемые режимы ЭЛС алюминиевых сплавов раз-
личной толщины
|
|
Параметры ре- |
Положение сты- |
||
Марка сплава |
Толщина, мм |
жима сварки |
ка при сварке |
||
|
|
Р, кВт |
Vсв, |
|
|
|
|
м/ч |
|
||
|
|
|
|
||
АМг6,ВАД1Ф |
0,6 |
0,4 |
60 |
Нижнее |
|
АМгб, ВАД23 |
2 |
1 |
90 |
-//- |
|
|
5 |
1,7 |
70 |
-//- |
|
АМгб |
10 |
2,8 |
70 |
-//- |
|
30 |
6,3 |
35 |
-//- |
||
|
|||||
|
100 |
21 |
15 |
Гор-ное |
|
|
30 |
80 |
15 |
-//- |
|
|
5 |
2,7 |
70 |
Нижнее |
|
1201 |
10 |
4,5 |
70 |
-//- |
|
40 |
18 |
70 |
Гор-ное |
||
|
100 |
30 |
20 |
-//- |
|
|
250 |
105 |
20 |
Вертикальное |
|
|
350 |
110 |
10 |
-//- |
|
1420 |
5 |
0,7 |
55 |
Нижнее |
|
10 |
2,6 |
55 |
-//- |
||
|
15 |
3,2 |
40 |
-//- |
|
В95 |
10 |
4,0 |
90 |
-//- |
|
В93 |
35 |
8,4 |
25 |
-//- |
|
АДО, АД1 |
10 |
6,3 |
70 |
-//- |
|
АЦМ |
10 |
3,8 |
70 |
-//- |
|
1963 |
5 |
2,0 |
90 |
-//- |
|
АЛ25, АЛЗО |
16 |
5,3 |
60 |
-//- |
|
АКЧ |
18 |
8,7 |
60 |
-//- |
Алюминиевые сплавы широко применяются в конструкциях криогенного назначения. Прочность сварных соединений увеличивается при снижении температуры испытаний. Среднее увеличение их временного сопротивление при 4,2 К у основного металла составляет 30-55 %, а у сварных соединений 45-65 % в зависимости от состояния основного металла.
238
Сварка лазером. Для получения качественного соединения, так же как и при ЭЛС, прежде всего необходимо обеспечить тщательную подготовку свариваемых кромок (химическое травление, с последующим шабрением) и качественную защиту шва от окисления. Из известных методов защиты, применяемых при сварке, наиболее эффективной для алюминиевых сплавов является газовая защита.
Максимальная глубина проплавления и высокое качество шва обеспечиваются при использовании гелия в качестве защитного газа. Причем обязательна защита шва с обеих сторон. В целях экономии допускается использование гелия для защиты только верхней части сварочной ванны, а для нижней, корневой, части может быть использован аргон.
Основой получения качественных сварных соединений является правильный выбор параметров режимов сварки. Специфика процесса лазерной сварки алюминиевых сплавов заключается в наличии порогового уровня мощности лазерного излучения, обеспечивающего проплавление при сварке. Например, для сплава АМг6 мощность CO2-лазера на уровне 2- 2,2 кВт сразу обеспечивает глубину проплавления 1,5-2 мм. При меньшей мощности излучения проплавление вообще отсутствует. Это явление связано с сочетанием высокого коэффициента отражения (0,97) алюминия на длине волны 10,6 мкм, высокой теплопроводности и теплоемкости алюминия. С нагревом поверхности алюминия до температур, близких к температуре плавления, коэффициент отражения резко снижается, и происходит интенсивное проплавление материала с образованием парогазового канала. Последующее увеличение мощности излучения приводит к практически линейному возрастанию глубины проплавления. Следует отметить, что указанный порог мощности зависит от свойств излучения, степени фокусировки, толщины пластины, состояния ее поверхности и скорости сварки.
Оптимальные режимы сварки излучением CO2-лазера
239
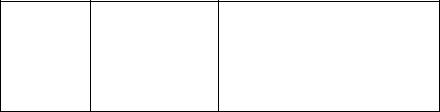
алюминиевого сплава представлены в табл. 3.8.
Таблица 3.8 Режимы сварки CO2-лазером алюминиевого сплава АМг6
δ, мм |
Р, кВт |
Скорость сварки Vсв, м/ч |
|
2,0 |
2,1 |
90 |
|
2,3 |
120 |
||
|
|||
3,0 |
2,3 |
90 |
|
2,8 |
120 |
||
|
|||
4,0 |
2,8 |
90 |
|
3,1 |
120 |
||
|
Микроструктура металла сварных соединений, выполненных лазерным излучением на оптимальных режимах, значительно отличается от микроструктуры металла соединений, полученных дуговой сваркой. В шве имеет место мелкодисперсная структура со столбчатыми дендритами, причем размеры дендритов значительно меньше, чем при аргонодуговой сварке. Выделение эвтектики и оплавление границ зерен в непосредственной близости от шва не наблюдаются. Структурные изменения в зоне термического влияния при лазерной сварке происходят на участке, в 5-6 раз меньшем, чем при аргонодуговой сварке. Размер зерна в этой зоне увеличивается незначительно. Подобная структура является благоприятной для достижения высокого уровня механических свойств и предотвращения горячих трещин.
Контактная сварка. До 50-60-х годов контактная сварка алюминиевых сплавов в авиационной промышленности широко не применялась. Это было связано с нерешенностью ряда проблем, обусловленных особенностями алюминиевых сплавов, в первую очередь наличием оксидных пленок, препятствующих прохождению электрического тока, и большими значениями теплопроводности и теплоемкости, что требовало создания быстродействующих машин большой мощности.
В настоящее время наиболее распространенный вид контактной сварки – это точечная сварка, на долю которой приходится 80% всех соединений, выполняемых этим способом.
240
В мировой практике авиастроения соединения, поученные точечной сваркой, применяют практически во всех узлах и агрегатах планера из алюминиевых сплавов: в панелях фюзеляжа, мотогондолах, крыльях, люках, створках и т.п.
Точечная сварка. Для алюминия и его сплавов точечная сварка наиболее широко применяется для толщин 0,5-5 мм. Основной тип соединения – нахлесточное. Диаметр ядра точки dя, минимальная нахлестка bН и шаг между точками tш зависят
от толщины детали δ. При изменении толщины детали от 0,3 до 6,0 мм диаметр ядра точки возрастает от 2,5 до 15 мм, величина нахлестки увеличивается от 8 до 43 мм, а минимальный технологический шаг между точками изменяется от 8 до 65 мм соответственно.
Состояние поверхностей свариваемых заготовок оказывает существенное влияние на формирование соединения, величину контактного сопротивления, склонность процесса к выплескам и образованию других дефектов. При сварке алюминиевых сплавов необходимо обеспечивать небольшое и по возможности постоянное электросопротивление пленки оксидов на поверхности изделия.
Исходную оксидную пленку удаляют в основном химическим методом. После обезжиривания в течение 3-5 мин в
водном растворе тринатрий-фосфата (Na3PO4 12H2O) и жидкого стекла (Na3SiO3) и промывки детали опускают в ванну с о д- новременным пассивированием поверхности. В качестве пассиватора наибольшее применение нашли калиевый и натриевый хромпики. Иногда свариваемые поверхности непосредственно перед сваркой (не позже чем за 2-3 ч.) подвергают механической обработке металлической щеткой.
Качество подготовки поверхностей обязательно контролируется замером величины сопротивления RЭ на установках типа машины с изоляцией одного электрода от электрододержателя. Для сплавов Д16, В95, АМг6, например, оно не должно превышать 120 мкОм.
241
Точечная сварка алюминия и его сплавов требует применения сварочных токов весьма большой плотности: до 1000 А/мм2 и выше, что значительно превосходит плотность тока при сварке малоуглеродистых сталей. Так как в результате нагрева при точечной сварке алюминиевые сплавы разупрочняются и размеры зон разуплотнения зависят от времени сварки, сплавы такого типа сваривают на жестких прижимах при длительности импульса тока 0,08-0,3 с.
Для сварки алюминиевых сплавов наибольшее применение получили электроды со сферической рабочей поверхностью.
При сварке сплавов алюминия обеспечивают минимальное выделение теплоты в контакте электрод-деталь и интенсивное охлаждение электрода. Поэтому электрическая проводимость сплава для изготовления электродов должна быть не ниже 85-90% проводимости меди.
Алюминиевые сплавы, в особенности термообрабатываемые, склонны к образованию горячих трещин в ядре. С увеличением толщины свариваемых деталей повышается склонность к образованию в ядре дефектов (трещин, раковин, рыхлот). Поэтому начиная с толщины деталей 1 мм+1 мм рекомендуется прикладывать ковочное усилие, в 2-3 раза превышающее сварочное. Дополнительное сжатие кристаллизирующегося ядра предотвращает появление дефектов в нем. Величина ковочного усилия возрастает с повышением толщины металла, радиуса сферы электродов, скорости кристаллизации (жесткости режима). Проковку начинают с небольшим, строго контролированным запаздыванием по отношению к моменту выключения тока (рис. 3.1). Проковка вообще повышает качество соединений. Она не только предотвращает образование трещин, усадочных раковин и рыхлот, но уменьшает общую деформацию деталей, снижает остаточные напряжения и резко повышает усталостную прочность точек.
242
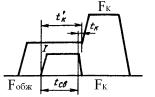
Рис. 3.1. Циклограмма одноимпульсной точечной сварки алюминиевых сплавов с ковочным давлением
Поскольку алюминий обладает высокой электрической проводимостью, сварка может сопровождаться перегревом металла в контакте между электродом и деталью и, как следствие, их схватыванием (свариванием). Для того, чтобы исключить это отрицательное явление в ряде случаев применяют теплоизолирующие прокладки из стали 12Х18Н9 толщиной 0,2-0,5 мм, которые помещают между электродом и деталью из алюминия. Такие прокладки не привариваются к деталям и электродам.
Ориентировочные режимы точечной сварки алюминиевых сплавов приведены в табл. 3.9. Однако эти режимы, как правило, требуют корректировки параметров до некоторого оптимального сочетания, обеспечивающего необходимое качество соединений и устойчивость процесса.
Сварку алюминиевых сплавов можно выполнять на машинах переменного и постоянного тока, низкочастотных и конденсаторных. Наибольшее распространение получили машины постоянного тока, так как они имеют большую мощность и наиболее универсальную форму импульса тока.
При сварке алюминиевых сплавов точки, обладая высокой прочностью при работе на срез, относительно плохо сопротивляются разрыву.
Шовная сварка. Шовная сварка используется при изготовлении изделий из алюминиевых сплавов толщиной до 4 мм, требующих герметичности. Шовная сварка может осуществляться двумя способами – прерывистым и шаговым. При первом способе свариваемые детали перемещаются относительно
243
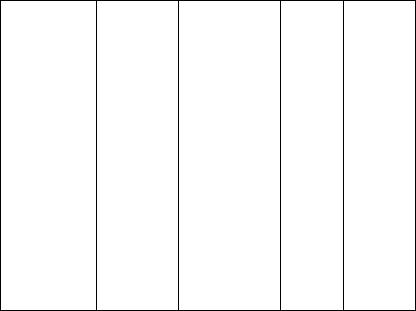
электродов машины непрерывно, а сварочный ток включается импульсами, чередующимися с паузами. Это позволяет исключить перегрев поверхности свариваемых деталей и снизить износ электродов. При втором способе включение сварного тока и перемещение деталей чередуются: сварочный ток включается при неподвижных деталях, а их перемещение – при выключенном токе и постоянном давлении.
Таблица 3.9 Режимы точечной сварки алюминиевых сплавов
Сплав |
δ, мм |
Усилие на |
Iсв, кА |
t, с |
|
электрод, кН |
|||||
|
|
|
|
||
|
0,5+0,5 |
2,45 |
15 |
0,08 |
|
Технический |
1,5+1,5 |
2,84 |
22 |
0,1 |
|
алюминий |
2,5+2,5 |
3,43 |
28 |
0,16 |
|
|
4,8+4,8 |
4,12 |
42 |
0,30 |
|
|
0,5+0,5 |
1,28 |
22 |
0,04 |
|
АМгАМ |
1,0+1,0 |
2,45 |
30 |
0,06 |
|
1,5+1,5 |
3,43 |
34 |
0,08 |
||
|
|||||
|
2,0+2,0 |
4,91 |
38 |
0,10 |
|
|
1,5+1,5 |
7,85 |
46 |
0,21 |
|
АМг6Т |
2,0+2,0 |
6,77 |
33,4 |
0,23 |
|
|
3,0+3,0 |
6,87 |
41,5 |
0,22 |
|
|
1,0+1,0 |
4,91 |
43 |
0,13 |
|
АМцАМ |
2,0+2,0 |
6,13 |
42,5 |
0,23 |
|
|
3,0+3,0 |
8,93 |
53 |
0,18 |
|
|
0,5+0,5 |
2,16 |
23 |
0,08 |
|
Д16АТ |
0,8+0,8 |
3,4 |
27 |
0,10 |
|
1,0+1,0 |
4,41 |
28 |
0,12 |
||
|
|||||
|
1,5+1,5 |
6,38 |
34 |
0,16 |
Для сварки алюминия и его сплавов используют ролики со сферической рабочей поверхностью. Ширина рабочей части роликов увеличивается с увеличением толщины свариваемых деталей. Диаметр электродов составляет 150-200 мм. При толщине металла 0,5 мм применяют электроды меньшего диамет-
ра: 40-50 мм.
Ориентировочные режимы прерывистой шовной сварки алюминиевых сплавов приведены в табл. 3.10.
244
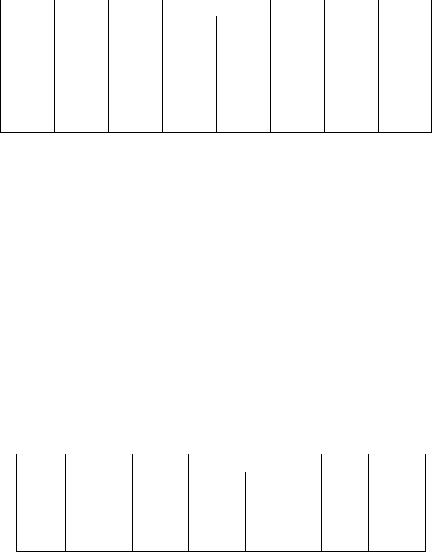
Таблица 3.10 Режимы прерывистой шовной сварки алюминиевых сплавов
δ, мм Ширина Iсв, кА |
Время, с |
Усилие Vсв, м/ч |
Шаг |
||||
|
ролика, |
|
действия |
паузы |
сжатия, |
|
точки, |
|
мм |
|
тока |
|
кН |
|
мм |
|
|
|
|
|
|
|
|
0,6+0,6 |
2,8 |
26 |
0,04 |
0,08 |
2,6 |
42 |
1,4 |
1,0+1,0 |
3,6 |
32 |
0,06 |
0,1 |
3,3 |
45 |
2,0 |
1,5+1,5 |
4,8 |
38 |
0,06 |
0,18 |
4,2 |
39 |
2,5 |
2,0+2,0 |
6,6 |
41 |
0,08 |
0,24 |
4,8 |
30 |
2,5 |
Сварка трением. Этот способ может быть достаточно эффективно использован для соединения в стык стержней одинакового диаметра, а также получения соединения стержней с
листами при соблюдении условия δ ≤ (0,25-0,3)d, где δ - толщина листа, d – диаметр стержня.
Алюминий и его сплавы характеризуются высокой способностью к схватыванию, поэтому их можно сваривать в широком диапазоне параметров процесса: скорости относительного вращения и удельного сжимающего давления.
Соединения с высокой прочностью и, особенно, пластичностью могут быть получены только в том случае, если пр е- кращение трения (остановка вращения) сопровождается достаточной пластической деформацией металла в зоне сварки.
Ориентировочные режимы сварки трением приведены в табл. 3.11.
Таблица 3.11 Режимы сварки трением алюминиевых сплавов
Марка |
Диаметр |
n, |
Давление, МПа, |
Осад- |
Время |
||
заготовок, |
при на- |
при проков- |
|||||
сплава |
об/мин. |
ка, мм |
сварки, с |
||||
|
мм |
|
греве |
ке |
|
|
|
АД1 |
20 |
3000 |
8 |
8 |
6-7 |
3 |
|
40 |
760 |
30 |
30 |
30 |
10 |
||
|
|||||||
Д16 |
40 |
760 |
100 |
100 |
20 |
13 |
При сварке трением с перемешиванием усилие прижима инструмента к поверхностям свариваемых деталей и его пере-
245
мещения составляет 5-10 кН и зависит от свойств материала, его толщины и скорости сварки. Глубина погружения инструмента в стык 0,8 - 0,9 толщины свариваемых деталей; частота вращения инструмента 1000 - 3000 об/мин, скорость сварки 4 - 40 м/ч в зависимости от толщины и состава свариваемого металла. Сварка жестко зафиксированных деталей выполняется с использованием опорной подкладки с продольной канавкой под стыком шириной 4 мм и глубиной 0,5 мм, с низкой теплопроводностью для снижения стока теплоты. Обычно это нержавеющая сталь типа 18-8, на поверхность которой как барьерное покрытие нанесен слой нитрида циркония.
При этой разновидности сварки возможны следующие дефекты: несплавление, перегрев металла и грат на лицевой поверхности, несплавление в корне шва, внутренние несплавления и т.п. Поэтому при сборке деталей под сварку необходима высокая точность: смещение оси стыка относительно инструмента не больше 0,5 мм; зазор между кромками не более 0,3 мм; повышение кромок, или депланация, со стороны набегания инструмента не больше 25 %, а со стороны его отхода - 5 % толщины свариваемого металла. Впереди инструмента полезно устанавливать прижимный ролик, который препятствует короблению деталей.
Введение рабочего инструмента в стык можно осуществлять на технологических припусках, а после его вывода из стыка необходимо забивание финишного отверстия в конце шва.
Сварка качественных тонколистовых конструкций толщиной 1,8 - 2,5 мм из сплавов АМц, АД31, АМг2, а также сплавов разного легирования, например 1201 + АМг6, выполняется на параметрах режима: n = 1420-2880 об/мин; Vсв = 6-40 м/ч; при сварке сложнолегированных сплавов n = 1420 об/мин;
Ксв = 6-14 м/ч.
Те же сплавы, но больших толщин 4 - 7 мм свариваются на параметрах n = 800-1000 об/мин; Vсв= 15-19м/ч. Такие со-
246
единения имеют прочностные характеристики на уровне 0,75 - 0,95 показателей для основного металла.
Способ позволяет выполнять не только прямолинейные швы, но и кольцевые на обечайках из сплава АМг6 на параметрах режима, которые снижают его разупрочнение: n = 800 об/мин; диаметр бурта инструмента 12 мм; Vсв = 14 м/ч. I Эта разновидность сварки алюминиевых сплавов весьма перспективна благодаря многим преимуществам по сравнению с другими способами, рассмотренными выше: не нужно придавать специальную форму кромкам и зачищать их поверхности от пленки А12О3, не нужны присадочный металл и защитный газ, возможно получение беспористых швов, сварку можно вести во всех пространственных положениях, отсутствуют дым, шум и ультрафиолетовые излучения, низкий уровень деформаций, шов формируется в твердой фазе, возможно получение крупных панелей, не нужны сварщики высокой квалификации и т.п.
Деформационное упрочнение швов при сварке трением с перемешиванием сложнолегированных алюминиевых сплавов АМг6М, 1420, 1201 и 1460 обеспечивает их более высокую прочность благодаря формированию в центральной части шва ядра с ультрадисперсной структурой, а в зоне термомеханического влияния - выгнутых, вытянутых и равноосных зерен, ориентированных в направлении движения инструмента. В результате измельчения зерен, увеличения объемной части их границ и измельчения интерметаллидных фаз их разупрочнение меньше, чем при аргонодуговой сварке неплавящимся электродом.
Способ позволяет значительно экономить металл при изготовлении ребристых панелей. Если при традиционной технологии требуется фрезерование отлитой плиты, при которой коэффициент использования материала составляет 0,07-0,2, то при сварке сплава В95Т2 этот показатель можно повысить до
0,89-0,92.
247
3.2. Сварка магниевых сплавов
Основной способ сварки – дуговая сварка в среде инертных газов. Сварка по слою флюса, как и сварка электродами с покрытием (в состав которого входят фторидные и хлоридные соли щелочных и щелочноземельных металлов), в настоящее время в промышленности практически не используются, т.к. остатки шлаков на поверхности швов вызывают коррозию сварной конструкции. Для сварки заготовок больших толщин из сплава МА2-1 разработан процесс электрошлаковой сварки. Имеется также положительный опыт электронно-лучевой и контактной сварки магниевых сплавов.
Магниевые сплавы обладают рядом специфических свойств, вызывающих затруднения при сварке. Это, прежде всего, высокая химическая активность и сильное сродство магния к кислороду. Среди промышленных металлов магний стоит на одном из первых мест по степени сродства к кислороду, мало отличаясь от кальция, бериллия и лития.
При нагреве до сварочных температур происходит активное окисление магния с образованием оксидной пленки. Соединение магния с кислородом нерастворимо в расплавленном металле и имеет температуру плавления значительно выше (2800°С), чем металл (650°С). Значительная разница в температурах плавления оксида магния и магния приводит к тому, что покрывающая поверхность ванны расплавленного металла пленка оксида магния препятствует сплавлению кромок основного металла, а также сплавлению его с присадочным. Плотность оксида магния (3,2 г/см3) значительно выше плотности металлического магния в расплаве (1,64 г/см3). Поэтому при сварке имеется опасность попадания пленки оксида магния в металл жидкой ванны, что нарушает сплошность металла шва.
Для нормального проведения процесса сварки необходимо удалять оксидную пленку со свариваемых поверхностей до начала сварки. Защита поверхности сварочной ванны от окисления является обязательным условием нормального протека-
248
ния процесса сварки. Это достигается защитой ванны с помощью расплава флюса или созданием в зоне сварки защитной атмосферы инертного газа (аргона, гелия).
Магниевые сплавы склонны к образованию кристаллизационных трещин в связи с возможностью появления по грани-
цам зёрен легкоплавких эвтектик: MgCu (Тпл = 485°С); MgNi
(Тпл = 508°С). Для повышения стойкости магниевых сплавов против образования кристаллизационных трещин их модифицируют редкоземельными элементами (например, лантаном в количестве 0,5-1%), а при сварке применяют присадочные материалы, наименее склонные к образованию горячих трещин.
Сплавы магния, особенно содержащие марганец, склонны к росту зерна металла в зоне термического влияния, поэтому не допускается их значительный перегрев (например, при скоплении в одном месте сварных швов, при многослойной сварке требуются перерывы для охлаждения металла).
В связи с большим коэффициентом линейного расширения сплавов магния при сварке возникают значительные напряжения, способные вызвать большие коробления изделий. Для их уменьшения и предотвращения возможности образования трещин рекомендуется производить сварку с подогревом, а
сваренные изделия подвергать отжигу при 250°С в течение 0,5-
1 ч.
Для предупреждения провисания сварочной ванны под действием собственного веса под свариваемый стык, как и при сварке алюминиевых сплавов, помещают специальную подкладку, изготавливаемую обычно из меди или нержавеющей стали.
Низкие значения теплоты плавления и удельной теплоёмкости магниевых сплавов обуславливают чрезвычайно большую концентрацию нагрева при сварке. Эта особенность наряду с низкой температурой плавления магния способствует локальным перегревам и пережогам металла.
Температура плавления магния несколько ниже, чем
249
алюминия (соответственно 650 и 658°С). Теплоемкость и теплопроводность магния также меньше. В силу этого для расплавления единицы объема магния требуется приблизительно на 1/3 теплоты меньше, чем для расплавления алюминия. Поэтому сварочные токи при сварке магния ниже, чем при сварке алюминия.
В связи с тем, что оксидная плёнка на поверхности магниевых сплавов является рыхлой и не защищает детали от дальнейшего окисления, магниевые полуфабрикаты, как правило, покрывают защитной плёнкой из солей хромовой кислоты. Перед сваркой с кромок и прилегающей поверхности на ширину 30 мм травлением или механическим путём тщательно удаляют эту защитную плёнку и другие загрязнения. После сварки на поверхность сварного соединения вновь наносят защитную плёнку.
Сварка в инертных газах. Для магниевых сплавов наиболее широко применяют ручную и механизированную сварку вольфрамовым электродом в среде аргона первого сорта. Значительно реже используют автоматическую сварку плавящимся электродом.
Сварка вольфрамовым электродом выполняется на пере-
менном токе, может быть использована для любых видов соединения, но нахлёсточные, угловые и тавровые соединения менее технологичны, чем стыковые. При сборке необходима тщательная подгонка кромок. Кромки под сварку зачищают механическим путём (щёткой, шабером) или химическим травлением.
В конструкциях из магниевых сплавов применяют все основные типы сварных соединений, принятые для сварки алюминиевых сплавов. Исключение составляет сварка с отбортовкой кромок: в связи с низкой пластичностью магниевых сплавов отбортовку кромок даже для металла малых толщин выполнить не удаётся.
Металл толщиной до 3 мм сваривают без разделки кро-
250
мок, при толщине листов 3-6 мм необходима V–образная разделка и при толщине более 6 мм – Х–образная разделка с притуплением 1,5 – 2 мм.
Сварку выполняют на повышенной скорости. Это позволяет свести к минимуму отрицательное тепловое воздействие сварки на металл в зоне термического влияния. Длину дуги поддерживают минимальной (1-1,5 мм) для эффективного разрушения оксидов за счёт катодного распыления и улучшения защиты зоны сварки инертным газом.
При использовании сварочной проволоки она обрабатывается химическим травлением с последующим хранением в сухом помещении не более 4 суток.
Так как автоматическая аргонодуговая сварка позволяет получать более стабильное качество сварных соединений, чем ручная, то последнюю следует применять лишь в тех случаях, когда затруднена автоматизация процесса сварки.
Для ручной сварки металла толщиной до 3 мм применяют вольфрамовые лантанированные или иттрированные электроды диаметром dэ = 2-3 мм и ток Iсв = (30-40)dэ.
Автоматическая сварка возможна для металла толщиной от 1 мм и выше в ольфрамовым электродом диаметром 2-6 мм на сварочном токе Iсв = (40-75)dэ. Диаметр присадочной проволоки 1,5-3 мм.
При аргонодуговой сварке прочность сварного соединения составляет 85-90% прочности основного металла.
Сварка плавящимся электродом целесообразна при тол-
щине металла более 5-6 мм. Сварка производится на постоянном токе обратной полярности. Листы толщиной до 5 мм рекомендуется сваривать встык за один проход без разделки кромок, толщиной 10-20 мм – с V–образной разделкой, плиты толщиной более 20 мм – с Х–образной разделкой.
Для сварки используется электродная проволока небольшого диаметра: 1-3 мм; величина тока Iсв = (130-150)dэ; скорость подачи проволоки уменьшается от 20 до 8 м/мин. при
251
увеличении диаметра проволоки от 1,2 до 3,2 мм. Аргонодуговая сварка магниевых сплавов значительно
снижает коррозионную стойкость металла шва и зоны термического влияния.
Электрошлаковая сварка. С увеличением толщины свариваемого металла более 40 мм способы дуговой сварки становятся малопроизводительными и не гарантируют достаточно высокого качества сварных соединений из-за опасности появления краевых несплавлений, связанных с неточностью направления дуги вдоль шва, а также из-за высокой вероятности образования кристаллизационных трещин, обусловленных большой жёсткостью сварного стыка.
При сварке сплавов магния большой толщины рекомендуется способ ЭШС электродными проволоками – для швов большой протяжённости и пластинчатым электродом – для швов малой протяжённости.
Удовлетворительное качество сварного соединения сплава МА2-1 сечением 57х110 мм и устойчивость процесса ЭШС получается при использовании флюсов систем LiCl – LiF и KCl-BaCl2-LiF при электрических мощностях процесса 60 и 84 кВт соответственно. По химическому составу металл шва почти не отличается от свариваемого. Доля участия основного металла в металле шва составляет 30-40%. Сварные соединения имеют механические свойства, близкие к свойствам основного металла при испытании образцов, отобранных поперёк прока-
та: σв = 202-226 МПа; σт = 157-188 МПа; ан = 0,09-0,1 МДж/м2.
Сварка лазером. Технология лазерной сварки магниевых сплавов принципиально не отличается от сварки алюминиевых сплавов. Перед сваркой соединяемые кромки необходимо протравить или зачистить шабером до блеска. Применение лазерного излучения обеспечивает хорошее формирование швов при сварке на весу, т. е. в отличие от дуговой сварки не требуется применения подкладок. Это значительно упрощает технологию изготовления сварных конструкций, особенно крупногабарит-
252

ных.
Режимы сварки сплава МА2-1 приведены в табл.3.12. Таблица 3.12
Режимы лазерной сварки сплава МА2-1
Толщина металла, мм |
Мощность излучения, |
Скорость сварки, м/ч. |
|
кВт |
|
1,8 |
2,0 |
100 |
1,2 |
2,3 |
130 |
Защита шва от окисления осуществляется гелием, подаваемым в верхнюю часть ванны, и аргоном, используемым только для защиты нижней корневой части шва.
Благоприятная структура и качественное формирование шва обеспечивают высокую стойкость к образованию горячих трещин, характерных для аргонодуговой сварке. Механические свойства сварных соединений находятся на уровне основного металла.
Контактная сварка. Для сварки магниевых сплавов можно использовать точечную контактную сварку. Так как теплопроводность и электропроводность магниевых сплавов приближаются к аналогичным показателям алюминиевых сплавов, технология и режимы сварки магниевых и алюминиевых сплавов близки.
В то же время магниевые сплавы по сравнению с алюминиевыми следует сваривать на более жёстких режимах и с меньшими усилиями сжатия, чем, например, для сплава Д16.
При сварке деталей больших толщин (более 2 мм) рекомендуется использовать ковочное усилие. Рыхлое строение поверхностных плёнок, содержащих большое количество влаги, вызывает интенсивное взаимодействие металлов в контакте электрод - деталь. Рабочая поверхность электродов быстро покрывается продуктами взаимодействия, что вызывает монотонный рост высоты ядра до полного проплавления деталей, сопровождающегося образованием выплесков и трещин. Поэтому зачистку рабочей поверхности электродов и роликов
253
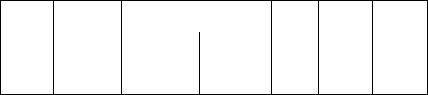
производят при сварке магниевых сплавов после 10-20 точек и после первого оборота ролика.
Перед сваркой поверхности деталей должны быть тщательно очищены химическим или механическим способом. Подготовленные детали могут храниться до сварки лишь несколько часов. Примеры режимов сварки некоторых магниевых сплавов приведены в табл. 3.13.
Для точечной сварки магниевых сплавов применяют машины постоянного тока, а также низкочастотные и конденсаторные.
Из-за диффузии меди в магниевый сплав в местах касания медных электродов с изделием коррозионная стойкость соединения снижается. Поэтому должны быть предусмотрены мероприятия, не допускающие наличия меди электродов на поверхности деталей после окончания контактной сварки.
Таблица 3.13 Режимы контактной точечной сварки магниевых сплавов
МА1, МА2, МА8 и МА2-1
Толщи- |
Радиус |
Усилие сжатия электро- |
Ток |
Время |
Время |
|
на ме- |
сферы |
дов, кН |
сварки, |
сварки, |
проков- |
|
талла, |
электрода, |
|
|
|||
сварочное |
ковочное |
кА |
с |
ки. с |
||
мм |
мм |
|
|
|
|
|
1+1 |
75 |
2,45 |
- |
29 |
0,04 |
- |
3+3 |
150 |
6,3 |
20,2 |
48 |
0,14 |
0,06 |
Нахлёсточные соединения, выполненные контактной точечной сваркой в каркасных конструкциях из магниевых сплавов, обладают низкими коррозионной стойкостью и выносливостью. Это связано с высоким уровнем концентрации напряжений в соединениях с точечным креплением обшивок на жёстком каркасе и с интенсивной коррозией в щелевом зазоре.
Одним из способов повышения служебных характеристик подобных конструкций является получение комбинированных клеесварных соединений.
Используют два варианта технологии: сварку по клею и заливку клея в зазор между соединёнными внахлёстку конст-
254
руктивными элементами.
3.3. Сварка титана и его сплавов
Вследствие высокой химической активности титана не все известные способы сварки плавлением могут быть использованы для получения сварных конструкций. Так, до настоящего времени не разработан надёжный способ сварки титана вручную покрытыми электродами.
Для соединения деталей из титана и его сплавов широко применяют дуговую сварку неплавящимся и плавящимся электродами в среде инертных газов, сварку сжатой дугой, в том числе микроплазменную, дуговую сварку под флюсом и электрошлаковую сварку, электронно-лучевую и лазерную сварку. Из способов сварки давлением наиболее широко применяется контактная и диффузионная сварка.
Металлургические и технологические особенности свар-
ки.
К числу основных затруднений, встречающихся при сварке титана, относится большая химическая активность металла при высокой температуре по отношению к газам (кислороду, азоту и водороду). Обязательным условием получения качественного соединения при сварке титана является надёжная защита от газов атмосферы не только сварочной ванны, но и остывающих участков металла шва и околошовной зоны
вплоть до температуры 300-400°С.
Из-за высокой химической активности титана по отношению к газам для защиты зоны сварки от воздуха можно применять только вакуум, инертные газы высокой степени чистоты или бескислородные фторидно-хлористые флюсы.
Взаимодействие титана с газами.
Титан, как никакой другой металл, способен растворять в себе большое количество газов, например, кислорода до 30% ат. Поэтому высокотемпературные процессы взаимодействия титана с газами приводят не только к образованию химических соединений в виде отдельных фаз на поверхности металла (ок-
255
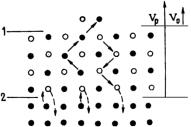
сидов, нитридов), но также и к растворению газов в металле.
При температурах выше 450°С происходит заметное растворение кислорода в титане.
Механизм окисления титана можно представить схематически как результат действия гетерогенных процессов (рис. 3.2): на границе 1 «оксид-газ» происходит адсорбция кислорода, его ионизация и воспроизводство катионного окружения за счёт извлечения катионов, а также частичная диффузия атомов кислорода в глубину оксидной фазы; на границе 2 «оксидметалл» осуществляется переход атомов кислорода в металлическую фазу с образованием твёрдого раствора внедрения и атомов титана в оксидную фазу.
Рис. 3.2. Схема окисления титана: VО – вектор скорости перемещения границы «оксид-газ»; VР – вектор скорости перемещения границы «оксид-металл»
Так как высокотемпературное окисление титана включает растворение кислорода в металлической основе и образование оксида, то общая скорость окисления V, мерой которой может быть количество кислорода, расходуемого в единицу времени, равна сумме скоростей его расхода на растворение (Vр) и на образование оксида (Vо). При Vр<Vо будет наблюдаться утолщение плёнки оксида, а при VР>Vо – её утонение.
Скорость роста плёнки на границе «оксид-газ» зависит от парциального давления кислорода, температуры, толщины плёнки, а скорость её растворения в основном зависит от температуры и градиента концентрации кислорода по глубине металла.
256
Снижение давления кислорода при вакуумировании приводит к уменьшению скорости реакции на границе «оксид-газ» и перемещению границы 1. При понижении давления кислорода и повышении температуры на поверхности титана на будет происходить образование оксидов (кислород, адсорбированный поверхностью, будет весь растворяться в металлической основе), то есть будет происходить окисление титана без образования оксидной фазы.
Поскольку Vр с течением времени уменьшается (так как снижается градиент концентрации кислорода по глубине металла), то при достижении некоторого времени t=t0, обеспечивающего реализацию неравенства Vр<Vо, на поверхности будет происходить формирование оксидов. При t<t0 поверхность будет свободна от оксидов.
При сварке в инертных газах (Ar,He), которые сами не взаимодействуют с металлами, в зоне дуги могут протекать реакции взаимодействия нагретого и расплавленного металла с примесями, содержащимися в инертных газах (O2, N2, H2, H2O и др.).
Попадание кислорода на поверхность сварочной ванны может сопровождаться реакциями:
Tiж+0,5O2=TiOж,
Tiж+0,5O2=TiOгаз.
Возможность образования оксидов другого состава в условиях незначительного парциального давления свободного кислорода в дуге, высоких температур и непрерывного перемешивания металла в сварочной ванне крайне мала.
На процесс перераспределения кислорода между атмосферой дуги и металлом сварочной ванны влияют пары титана. Расчёты процесса их взаимодействия с кислородом показали, что в газовой фазе титан не вступает в реакции с молекулярным и атомарным кислородом, и даже в периферийных участках плазмы столба дуги не должно происходить окисление паров титана. Этим можно объяснить часто наблюдаемый на не-
257
котором расстоянии от шва налет темного цвета. Он представляет собой дисперсный титан, который конденсировался из газовой фазы в процессе сварки и частично окислен (уже при контакте с воздухом).
В зоне дуги может находиться влага либо в виде паров воды, либо в виде продуктов их диссоциации
2Н2О ↔= 2Н2 + О2,
При температуре выше 4300°С возможны реакции
Н2О ↔Н + ОН,
Н2О ↔ 2Н + О, которые наиболее вероятны в центральной части дуги. Таким
образом, в результате диссоциации паров воды атмосфера дуги обогащается кислородом и водородом. Кислород затем реагирует с титаном. Возможно и прямое окисление титана парами воды.
При относительно низких температурах в ЗТВ или на поверхности закристаллизовавшегося шва образуется оксид ТiО2.
Азот так же, как и кислород, характеризуется высоким сродством с титаном, но меньшей склонностью к хемосорбции. В результате взаимодействия азота c титаном образуется нитрид титана по реакции
Tiж + 0,5N2г = TiNтв.
Так как нитрид титана в газовой фазе не существует, то образование газообразного TiN не происходит.
Хемосорбция азота (как и кислорода) происходит, в основном, в более холодной хвостовой части сварочной ванны. Поскольку скорость растворения кислорода в титане больше скорости растворения азота, то при нагреве титана в атмосфере воздуха основную роль во взаимодействии играет кислород.
Кислород и азот стабилизирует α-фазу, поэтому при повышенной концентрации этих элементов в поверхностном слое формируется так называемый альфированный слой, характеризующийся повышенной твердостью и низкой пластичностью.
В зависимости от парциального давления водорода в ат-
258
мосфере дуги и его содержания в свариваемом металле может наблюдаться либо насыщение шва водородом, либо его выделение из сварочной ванны. Последнее имеет место при сварке в условиях надежной защиты аргоном достаточной чистоты или при сварке в вакууме. Повышение парциального давления водорода в защитной атмосфере в результате диссоциации паров влаги и ее прямого взаимодействия с титаном приводит к насыщению водородом металла шва и зоны термического влияния.
Дополнительное по сравнению с основным металлом насыщение швов кислородом, азотом и водородом недопустимо. Как и для титановых сплавов в целом, примеси внедрения - газы - вызывают хрупкое разрушение сварных соединений, увеличивают их склонность к образованию холодных трещин, замедленному разрушению, пористости.
Взаимодействие титана с флюсом. Основное требова-
ние, которому должен отвечать флюс для сварки титана, это полное отсутствие оксидов. Наличие во флюсе даже таких стойких оксидов, как Al2O3, ZrO2 , TiO2, не исключает окисления металла шва, только полное удаление из флюса оксидов обеспечивает в наплавленном металле содержание кислорода менее 0,1 %.
При сварке титана под флюсом возможны реакции двух типов: реакция титана с компонентами флюса и реакция оксидов титана с флюсом.
Так, для трёхкомпонентного флюса системы CaF2- BaCl2- NaF реакции взаимодействия жидкого титана с отдельными компонентами данной системы можно записать в следующем виде:
Ti + nMeG ↔ TiGn + nMe, Ti + 0,5nMeG2 ↔ TiGn + 0,5nMe.
Продуктами этих реакций в условиях сварочной ванны являются газообразные щелочные или щелочноземельные элементы и галогениды, не растворимые в жидком металле. Эти
259
реакции не приводят к загрязнению металла сварочной ванны неметаллическими включениями, но могут сопровождаться переходом в сварочную ванну элементов из флюса.
Реакции взаимодействия оксидов титана с флюсом можно записать в следующем виде:
TiO2тв + 2CaF2 ↔ 2CaOтв + TiF4г;
TiO2тв + 4NaFж ↔ 2Na2Oтв + TiF4г;
TiO2тв + 2BaCl2ж ↔ 2BaOтв + TiCl4г.
При температурах выше 1000-1100°С последняя реакция не развивается, поэтому можно сделать вывод, что в качестве компонентов флюса больше всего подходят фториды, обладающие способностью реагировать с оксидами титана. Однако экспериментальные исследования показали, что флюс, полностью состоящий из фторидов, обладает пониженными технологическими свойствами. Лучше результаты получаются при частичной замене фторидов хлоридами.
Поскольку титан имеет сравнительно высокую температуру плавления, то сварочные флюсы для него должны обладать повышенной тугоплавкостью. Поэтому фториды и хлориды титана, имеющие низкую температуру плавления и кипения (так, TiF4 кипит при 284°С; TiCl4 плавится при 150°С, а кипит при 360°С), не могут быть использованы в качестве компонентов флюса.
Хорошие результаты получены при использовании в качестве основы флюса CаF2, который способен интенсивно взаимодействовать с водяным паром с образованием фтористого водорода. Эта реакция приводит к удалению влаги из зоны сварки и защите металла шва от насыщения водородом и кислородом.
Выбор оптимальных составов флюсов усложняется тем, что в системах CаF2 с более легкоплавкими хлоридами образуются многочисленные эвтектики, а области концентраций расплавов, обладающих достаточно высокой температурой плавления, весьма ограничены. Так, в системе CаF2- BaCl2-
260
NaF обнаружено более 20 эвтектик разного состава. При содержании во флюсе на основе CaF2 до 5 % NaF предельная концентрация в нем BaCl2 для обеспечения достаточной тугоплавкости не должна превышать 20-25 %.
В ИЭС им. Е.О.Патона для сварки титана и его сплавов разработан ряд бескислородных галогенидных флюсов серии АНТ. Эти флюсы обеспечивают надежную защиту ванны расплавленного металла, остывающие участки шва и ЗТВ от вредного контакта с газами воздуха.
Конечные структуры и свойства сварного соединения во многом определяются сварочным термическим циклом.
При сварке титана потери энергии меньше, чем при сварке, например, стали. Концентрированный сварочный нагрев приводит к более значительному градиенту температур, обусловливающему возрастание внутренних напряжений.
Скорость охлаждения в околошовных участках ЗТВ при равных условиях сварки у титана приблизительно в 2-3 раза меньше, чем у стали. Примерно во столько же раз для титана, по сравнению со сталью, увеличивается и время пребывания металла околошовного участка ЗТВ в области высоких температур.
Для титановых швов характерен узкий интервал кристаллизации. Так как пластичность металла в этом интервале высока, сварные швы стойки против образования кристаллизационных трещин.
Сварные соединения титана отличаются и малым временем пребывания в температурном интервале хрупкости. Для швов легированных сплавов это время составляет 1,2 с, а для металла в ЗТВ - 0,7-1,0 с. Высокая деформационная способность металла в ЗТВ в температурном интервале хрупкости обеспечивает стойкость сварных соединений и против образования подсолидусных трещин. Это является важным достоинством титановых сплавов.
В зоне сплавления в процессе контакта твердого и жид-
261
кого металлов развивается химическая неоднородность. Именно здесь расположен концентрационный пик водорода.
Следует отметить, что отрицательное влияние термического цикла сварки на механические свойства околошовного участка ЗТВ зависит не столько от его структуры (величины зерна), сколько от чистоты металла, содержания примесей - газов. При достигнутом уровне чистоты полуфабрикатов из технического титана термический цикл сварки не оказывает заметного влияния на свойства околошовного участка ЗТВ, несмотря на имеющее место резкое укрупнение зерна. Отсутствие критических изменений свойств в ЗТВ технического титана, несмотря на значительные структурные и фазовые превращения, является показателем хорошей свариваемости этого металла. В то же время в ЗТВ сплавов на основе титана, особенно средне- и высоколегированных, эти превращения нередко приводят к резкому снижению пластичности и образованию хрупких фаз, а в ряде случаев к возникновению холодных трещин.
Растягивающие напряжения и деформации возникают в титане при сварке как поперек, так и вдоль шва. Величина деформаций несколько больше, чем, например, в сталях аустенитного класса. Это обусловлено тем, что при относительной близости значений коэффициентов линейного расширения и характера температурных полей при сварке обоих металлов модуль упругости титана в два раза ниже, чем у стали.
Дуговая сварка титановых сплавов в среде инертных га-
зов. Сварка в среде инертных газов применяется как неплавящимся (автоматическая, механизированная; ручная), так и плавящимся (автоматическая, механизированная) электродом. Из дуговых способов сварки титана самым распространенным является сварка неплавящимся вольфрамовым электродом. Этот способ наиболее универсален, позволяет осуществлять сварку в различных пространственных положениях, быстро переналаживать оборудование при изменении типа соединений и
262
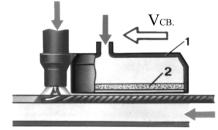
толщины свариваемых заготовок, обеспечивать высокое качество соединений.
Сварка неплавящимся электродом. Качество сварных со-
единений определяется главным образом надежностью защиты зоны сварки и чистотой инертного газа. Для сварки титана, в основном, применяют аргон 1-го и высшего сорта и гелий высокой чистоты.
Наибольшее распространение в сварочном производстве получила струйная защита зоны сварки, осуществляемая непрерывным обдувом сварочной ванны и остывающих участков соединения, хотя обеспечить надежную защиту в этом случае достаточно сложно. Для этого разработаны специальные горелки, насадки, подкладки и другие приспособления.
Для защиты остывающих участков сварного соединения используют насадки, закреплённые на горелке (рис.3.3).
Рис. 3.3. Подача защитного газа в зону сварки через сопло и насадку – 1; 2 – газовая линза, обеспечивающая ламинарность потока газа
Ширина насадки выбирается с учетом размеров ЗТВ, а длина при сварке тонкой пластины может быть приближенно определена по выражению
I = (0,006 Iсв2Uд2)/(t2Vсвb),
где Iсв - сварочный ток, A; Uд - напряжение дуги, В; t - темпе-
ратура, ниже которой металл не следует защищать (t ≈ 400 °С); Vсв - скорость сварки, см/с; b - толщина металла, см.
Для защиты обратной стороны швов и прилегающих к ним нагретых участков сварного соединения применяют съем-
263
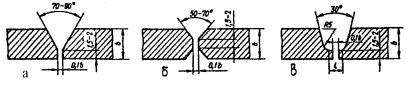
ные медные подкладки с формирующей канавкой и системой отверстий для подачи инертного газа.
Сварка титана неплавящимся электродом осуществляется на постоянном токе прямой полярности. В качестве катода используется вольфрамовый стержень марок ЭВЛ (лантанированный) и ЭВИ (иттрированный).
Качество сварных соединений во многом определяется технологией подготовки кромок под сварку. Последовательность операций зависит от исходного состояния заготовок.
Торцы кромок листовых заготовок после холодной штамповки и резки на ножницах зачищаются напильником или шабером. Торцы деталей после газовой резки обрабатываются на глубину, как правило, не менее 5 мм. Непосредственно перед сваркой кромки на ширине 15-20 мм от стыка зачищаются металлической щеткой, обезжириваются ацетоном и обезвоживаются спиртом. Ответственные конструкции после механической обработки подвергают химическому травлению и последующему осветлению.
При сварке титана для исключения перегрева околошовных участков ЗТВ ограничивают величину сварочного тока, которая обычно не превышает 300 А. Это позволяет без разделки кромок за один проход сваривать металл толщиной до 3 мм. Стыковые соединения больших толщин выполняют многослойными с разделкой кромок и подачей присадки (рис. 3.4).
Поскольку с увеличением зазора между свариваемыми деталями возрастают поперечные укорочения, сборку рекомендуется производить с минимальным зазором.
Рис. 3.4. Типичные виды разделки кромок для многос6лойной сварки титановых сплавов толщиной 4-10 мм (а), 10-25 мм (б) и свыше 10 мм
(в)
264
При многослойной сварке металла толщиной 5-25 мм наблюдается чрезмерный разогрев ЗТВ, при котором защита с помощью удлиненных насадок становится малоэффективной. Нагретый металл насыщается вредными примесями, в peзультате чего снижается пластичность и возрастает склонность к появлению трещин. Возможно также появление межслойного несплавления. Ориентировочные режимы ручной и автоматической сварки приведены в табл. 3.14 и 3.15.
Таблица 3.14 Ориентировочные режимы ручной аргонодуговой сварки
титановых сплавов
Толщина |
Число |
Сварочный ток |
Напряжение дуги Uд, В |
|
металла δ, мм |
проходов n |
Iсв, А |
||
|
||||
1 |
1 |
40-60 |
10-14 |
|
2 |
1 |
70-90 |
10-14 |
|
3 |
2 |
120-130 |
10-15 |
|
4 |
2 |
130-140 |
11-15 |
|
5 |
2-3 |
140-160 |
11-15 |
|
10 |
10-14 |
160-200 |
11-15 |
Для регулирования сварочного тока, а также для создания падающей характеристики у источников питания с жесткой характеристикой сварочный пост должен быть оснащен балластными реостатами типа РБ-200, РБ-300 и др.
На рис. 3.5 приведена схема поста для автоматической сварки неплавящимся электродом. Здесь следует отметить, что при ручной аргонодуговой сварке в производственной практике защитные насадки 8 применяются достаточно редко.
Эффективным процессом сварки титановых сплавов является аргонодуговая сварка неплавящимся вольфрамовым электродом с применением флюсов-паст, состоящих из фторидов и хлоридов щелочных и щелочноземельных металлов. Этот процесс обеспечивает глубокое проплавление при низкой погонной энергии, уменьшает зону термического влияния, снижает вероятность образования пор в швах. Применение флю-
265
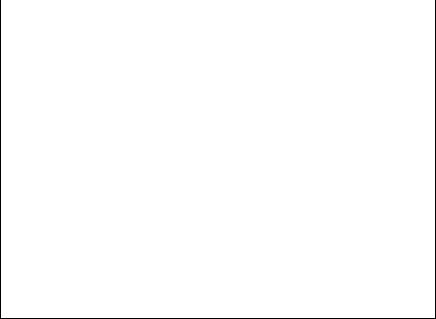
сов-паст позволяет почти в 2 раза снизить величину сварочного тока без изменения глубины проплавления при скорости сварки 15 м/ч; при увеличении скорости сварки до 25-30 м/ч этот эффект почти исчезает.
Таблица 3.15 Ориентировочные режимы автоматической аргонодуго-
вой сварки титановых сплавов
δ, мм |
n |
Iсв, А |
Uд, В |
Vсв, м/ч |
Vпод, м/ч |
Расход аргона, л/мин. |
|||
|
|
|
|
|
|
|
|
|
|
|
|
|
|
|
|
В горел- |
В на- |
Для за- |
|
|
|
|
|
|
|
щиты об- |
|||
|
|
|
|
|
|
ку |
садку |
ратной |
|
|
|
|
|
|
|
|
|
стороны |
|
1 |
1 |
60-80 |
8-10 |
25-30 |
- |
5-7 |
5-8 |
1-2 |
|
|
|
|
|
|
|
|
|
|
|
2 |
1 |
120-160 |
8-10 |
20-25 |
- |
8-10 |
10-13 |
3-4 |
|
3 |
1 |
200-240 |
10-12 |
15-20 |
- |
12-15 |
14-18 |
4-5 |
|
5 |
1 |
180-210 |
9-11 |
10-13 |
- |
14-16 |
16-20 |
4-6 |
|
2-3 |
200-240 |
13-15 |
13-15 |
60-80 |
14-16 |
16-20 |
4-6 |
||
|
|||||||||
6 |
1 |
180-210 |
10-12 |
10-15 |
- |
14-16 |
16-20 |
5-8 |
|
2-3 |
220-250 |
11-13 |
10-15 |
120-180 |
14-16 |
16-20 |
5-8 |
||
|
|||||||||
8 |
1 |
190-240 |
10-12 |
6-10 |
- |
15-18 |
16-20 |
5-8 |
|
2-3 |
240-290 |
11-13 |
6-10 |
50-100 |
15-18 |
16-20 |
5-8 |
||
|
Примечание. При сварке листов большой толщины следует увеличить
число проходов.
Экспериментальные данные позволяют считать, что наблюдаемый эффект связан с изменением геометрических характеристик и электрических параметров дуги (сжатие столба дуги и увеличение плотности на аноде), обусловленных комплексом взаимосвязанных процессов: экранированием метала вокруг сварочной ванны жидким флюсом и стабилизацией в пределах сварочной ванны анодного пятна; повышением теплопроводности дугового промежутка в связи с появлением в дуге примесей молекулярных паров флюса; деионизацией пе-
266
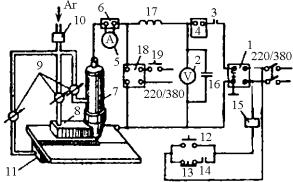
риферийных участков дуги в результате захвата электронов проводимости частицами паров флюса и продуктов его взаимодействия со свариваемым металлом.
Рис. 3.5. Схема сварочного поста для автоматической аргонодуговой сварки титановых сплавов: 1 – источник питания; 2 – вольтметр постоянного тока; 3 – контактор включения сварочной цепи; 4 – балластный реостат; 5 – амперметр постоянного тока; 6 – шунт; 7 – горелка; 8 – защитная насадка; 9 – ротаметры; 10 – электромагнитный клапан подачи защитного газа; 11 – формирующая подкладка; 12 – кнопка «Пуск»; 13 – кнопка «Стоп»; 14 – контакты самоблокировки катушки контактора; 15 – катушка контактора;16 – конденсатор защиты; 17 – защитный
дроссель; 18 – осциллятор; 19 – кнопка включения осциллятора
Но при этом способе сварки требуется более высокая точность сборки свариваемых заготовок, т. к. при больших смещениях кромок и зазорах нарушается сплошность плёнки жидкого флюса впереди сварочной ванны.
Способ сварки неплавящимся электродом углубленной или погруженной дугой также позволяет за один проход сваривать металл средних толщин. Однако к его основным недостаткам относятся чрезмерная ширина шва и большие размеры околошовной зоны
Для повышения производительности можно использовать такие способы сварки, как двумя вольфрамовыми электродами, расположенными в плоскости, перпендикулярной оси шва; с присадочной порошковой проволокой.
В промышленности находят применение разновидности
267
сварки неплавящимся электродом в среде защитных газов: им- пульсно-дуговая, плазменная, микроплазменная, с электромагнитным перемешиванием сварочной ванны.
При плазменной сварке титана применяют такие же средства защиты, как и при сварке неплавящимся электродом. Без разделки кромок за 1 проход сваривают листы толщиной до 14 мм.
Микроплазменную сварку деталей из титана толщиной менее 0,3 мм выполняют по отбортованным кромкам. Для более толстых металлов могут быть выполнены стыковые и нахлесточные швы. Для получения качественных швов при микроплазменной сварке предъявляются высокие требования к сборке соединений. Микроплазменная сварка нашла применение при изготовлении тонкостенных титановых труб. Импульсная микроплазменная сварка, когда нагрев и плавление металла осуществляются в течение импульса тока, позволяет уменьшать деформацию кромок, устранять провисание шва и уменьшить пористость.
Сварка плавящимся электродом диаметром 1,6-5 мм применяется для стыковых, тавровых и нахлёсточных соединений из титана и его сплавов толщиной 3 мм и более в нижнем положении. При этом способе сварки можно получить оптимальные свойства сварных соединений путем выбора состава металла шва как изменением химического состава плавящегося электрода, так и в результате регулирования в нем доли основного металла.
Устойчивое горение дуги с минимальным разбрызгиванием расплавленного металла, хорошее качество формирования и защита шва обеспечиваются при сварке на обратной полярности и при определенном соотношении сварочного тока, напряжения на дуге, скорости подачи электродной проволоки и величины вылета электрода, а также при использовании источников питания с жесткой или пологопадающей ВАХ. Сварка может осуществляться как в аргоне, так и гелии, но
268
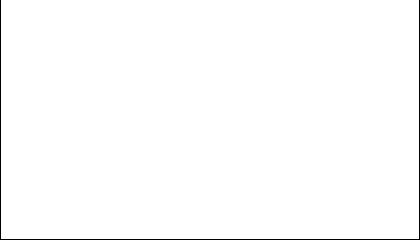
лучше результаты получаются при использовании смеси из 80
%(по объёму) гелия и 20 % аргона.
Втабл.3.16 приведены ориентировочные режимы сварки плавящимся электродом.
Таблица 3.16 Ориентировочные режимы сварки титана плавящимся
электродом в среде инертных газов без разделки кромок
|
|
|
|
Vсв, |
Вылет электрод- |
Расход за- |
|
δ, мм |
dэ, мм |
Iсв, А |
Uд, В |
щитного га- |
|||
м/ч |
ной проволоки, мм |
||||||
|
|
|
|
|
|
за, л/мин. |
|
3-8 |
1,6 |
350-450 |
28-36 |
25-40 |
20-25 |
30-40 |
|
22-28 |
20-30 |
||||||
|
|
|
|
|
|||
|
|
|
|
|
|
|
|
10-12 |
1,6-2 |
440-520 |
38-40 |
20-35 |
20-28 |
70-90 |
|
30-34 |
35-45 |
||||||
|
|
|
|
|
|||
15 |
3 |
600-650 |
42-48 |
25-30 |
25-30 |
70-100 |
|
30-32 |
35-50 |
||||||
|
|
|
|
|
|||
16-36 |
5 |
780-1200 |
46-52 |
15-25 |
40-55 |
100-120 |
|
34-38 |
50-60 |
||||||
|
|
|
|
|
Примечание. В числителе приведены режимы сверки в гелии, в знаме-
нателе - в аргоне.
При сварке в монтажных условиях соединений из титана, расположенных в разных пространственных положениях (например, стыковка труб), находит применение метод полуав-
томатической импульсно-дуговой сварки плавящимся элек-
тродом в среде аргона. Полуавтоматическая сварка титановой проволокой диаметром 1,2-2 мм с питанием от генератора импульсов обеспечивает перенос одной капли металла при каждом импульсе тока. Принудительный, направленный перенос электродного металла значительно улучшает формирование швов, выполняемых полуавтоматом, и делает возможной полуавтоматическую сварку в среде аргона в вертикальном и даже потолочном положении.
Автоматической сваркой под флюсом для титана можно выполнять все основные типы соединений: стыковые, угловые,
269
тавровые, нахлесточные при толщине соединяемых элементов от 3 до 40 мм.
Сварка выполняется на постоянном токе обратной полярности. При сварке на прямой полярности или переменном токе резко ухудшается качество формирования шва.
Сварка выполняется при минимально допустимом расстоянии между поверхностью свариваемого металла и нижней точкой мундштука (вылета электродной проволоки). Это связано с высоким удельным электросопротивлением титана. Увеличение вылета электродной проволоки приводит к ее чрезмерному разогреву, насыщению вредными газовыми примесями, нарушению стабильности процесса сварки и, как следствие, к ухудшению качества формирования шва и механических свойств. Максимально допустимая величина вылета электродной проволоки зависит от ее диаметра:
dэ, мм |
2,5 |
3 |
4 |
5 |
Вылет, мм |
13-14 |
15-16 |
17-19 |
20-22 |
Подвергнутая вакуумному отжигу на заводе-изготовителе сварочная проволока должна храниться в плотно закрывающихся герметичных контейнерах, по возможности заполненных инертным газом. Поскольку прошедшая вакуумный отжиг проволока обладает способностью адсорбировать влагу и пары летучих веществ, то промывка растворителями и протирке такой проволоки перед сваркой не рекомендуется. При намотке сварочной проволоки на кассету следует применять меры, исключающие ее загрязнение.
Автоматическая сварка под флюсом осуществляется с использованием проволоки диаметром до 5 мм. Применение проволоки большего диаметра затруднено вследствие её повышенной жесткости.
Для сварки титана и его сплавов применяют проволоки выпускаемые по ГОСТ 27265-87. Использование этих проволок обеспечивает получение качественных соединений.
Для защиты нагретого и расплавленного металла от
270
взаимодействия с воздухом используют специальные бескислородные тугоплавкие флюсы, состоящие из фторидов и хлоридов щелочных и щелочноземельных металлов. Несмотря на то, что флюсы марок АНТ-1, АНТ-3, АНТ-7 не гигроскопичны, на поверхности частиц в процессе хранения адсорбируется влага - основной источник насыщения металла шва водородом и кислородом в процессе сварки. Поэтому флюсы перед сваркой должны быть подвергнуты прокалке при температуре 350400°С в течение 1,5-2 ч. Количество влаги во флюсе, поступающем на сварку, не должно превышать 0,05 %. Прокалка флюса должна производиться в муфельных печах на противнях из нержавеющей стали с крышками, чтобы полностью исключить засорение флюса.
При автоматической сварке титана под флюсом на оптимальных режимах в металле шва полностью отсутствуют поры, трещины, шлаковые включения. Швы обладают высокой прочностью и пластичностью. Так, для сплава ОТ4 толщиной
10 мм σв = 793-851 МПа; δ = 14,6-15,3%; ϕ = 31,8-33,4 %; KCV
примерно 9,6 мДж/м2. Техника автоматической сварки титановых сплавов под флюсом практически не отличается от техники сварки стали. Стыковые соединения толщиной до 10 мм можно успешно сваривать с одной стороны. Сварку соединений толщиной от 3 до 6 мм следует производить без зазора или с небольшим зазором на остающейся технологической подкладке из титана, а также на съемной медной водоохлаждаемой подкладке с защитой обратной стороны стыка инертным газом. Сварку на флюсовой подушке осуществляют без зазора, но при этом на металле толщиной 8-10 мм выполняют V-образную разделку кромок с углом раскрытия 90° и величиной притупления не менее 50 % от толщины свариваемого металла.
Стыковые соединения толщиной 10-16 мм целесообразно выполнять двухсторонней сваркой с Х-образной разделкой на медной водоохлаждаемой подкладке с защитой инертным газом обратной стороны стыка.
271
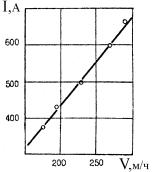
Глубина проплавления находится в прямой зависимости от плотности сварочного тока. При выборе оптимального режима сварки глубину проплавления определяют опытным путем на имитирующей сварной стык наплавке, выполненной на достаточно толстой титановой пластине.
На основе экспериментальных данных установлена зависимость величины сварочного тока от скорости подачи электродной проволоки (рис. 3.6).
Рис. 3.6. Зависимость величины сварочного тока от скорости подачи электродной проволоки
Величину заполнения разделки кромок металлом электродной проволоки можно определить по эмпирическому уравнению, из которого следует, что величина заполнения разделки кромок прямо пропорциональна скорости подачи электродной проволоки и ее диаметру и обратно пропорциональна
скорости сварки:
S Кз = (πdэ2 Vпп)/(4Vсв),
где S - площадь поперечного сечения разделки кромок стыка, мм; Кз - коэффициент заполнения разделки, учитывающий расход металла электродной проволоки на создание усиления сварного шва, Kз = 1,2-1,3; dэ - диаметр электродной проволоки, мм; Vпп - скорость подачи проволоки, м/ч; Vсв - скорость сварки, м/ч.
272
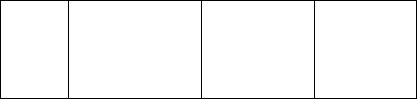
Экспериментально для каждого диаметра электродной проволоки установлены величины предельно допускаемых сварочных токов (табл.3.17).
Таблица 3.17 Величины предельно допускаемых сварочных токов при
автоматической сварке титана под флюсом
dэ, мм |
Максимальный сва- |
Плотность тока, |
Кнапл, |
рочный ток, А |
А/мм2 |
г/А ч |
|
2,5 |
620 |
126,5 |
16,0 |
3,0 |
650 |
92,0 |
15,5 |
4,0 |
850 |
67,7 |
14,5 |
5,0 |
950 |
48,4 |
14,0 |
При сварке на токах, превышающих предельно допустимую величину, усиление шва становится узким и высоким, а проплав приобретает эллипсоидную форму. Швы, выполненные на меньших сварочных токах, имеют удовлетворительную форму.
Достоинством автоматической сварки титана под флюсом является возможность ее осуществления на стандартном серийно выпускаемом сварочном оборудовании без значительных конструктивных изменений. В качестве источников питания применяются серийные преобразователи или выпрямители, обеспечивающие необходимую величину сварочного тока.
Электрошлаковой сваркой целесообразно сваривать титан и его сплавы толщиной более 40 мм. К числу преимуществ электрошлаковой сварки относится благоприятный для титана термический цикл – низкие скорости нагрева и охлаждения сварного соединения, что способствует получению швов без внутренних дефектов типа пор, шлаковых включений, а также исключает образование закалочных структур.
Для сварки используют плавленые бескислородные фто- ридно-хлоридные флюсы АНТ (для технического титана и его низколегированных сплавов), АНТ-4 и АНТ-6 (для высокопрочных легированных титановых сплавов). К особенностям
273

этих флюсов относятся сравнительно высокие температуры
плавления (выше 1400°С). Шихта флюсов изготавливается из химически чистых компонентов.
Фторидные флюсы типа АНТ-2 в расплавленном состоянии весьма жидкотекучи. Поэтому необходима очень тщательная подготовка деталей к сварке. Зазоры между формирующими подкладками и кромками свариваемых деталей не должны превышать 0,5 мм. Зазоры между поковками и кокилем уплотняют сухим асбестом.
Чтобы избежать загрязнения наплавленного металла газами применяют дополнительную защиту шлаковой ванны аргоном (рис. 3.7), что позволяет снизить содержание кислорода в 10 раз, а азота и водорода – в 6-7 раз и получить удовлетворительный химсостав наплавленного металла (N2 – 0,06%; О2 –
0,11%; Н2 – 0,01%).
Большое внимание уделяется подготовке поверхностей под сварку. Наличие загрязнений, оксидных плёнок и альфированных (газонасыщенных) слоёв не допускается. Сварка по этим слоям сопровождается переходом примесей-газов в шов и приводит к его охрупчиванию.
Рис. 3.7. Устройство А-1022 для ЭШС титановых сплавов проволочными электродами: 1 – подающий механизм; 2 – проволочный электрод; 3 – мундштук; 4 – свариваемая деталь; 5 - формирующий медный ползун; 6 – газовый коллектор; 7 – металлическая ванна; 8 – закристаллизовавшийся сварной шов; 9 – медная токоподводящая вилка; 10 – штуцера
274
Для очистки поверхностей применяют, как правило, механическую зачистку окалины (если она имеется) и последующее химическое травление.
В связи с большим электросопротивлением титана короткие швы (длиной до 300-400 мм) сваривают с применением пластинчатых электродов и плавящихся мундштуков. Швы большой протяжённости можно выполнять проволочными электродами.
При сварке технического титана, однофазных α- и псевдоα- сплавов, а также низколегированных (α+β)- сплавов титана используют плавящиеся электроды того же состава, что и основной металл.
Сварка высокопрочных двухфазных (α+β)- сплавов электродом, близким по составу с основным металлом, как правило, не даёт положительных результатов. Поэтому приходится искать электроды, обеспечивающие оптимальный состав шва, отличающийся от состава основного металла. Так, для сварки сплава ВТ6 (6,1%Al; 4,2%V) лучшие результаты получаются при использовании электродов из сплава АТ6 (6,5%Al; 0,9%Cr). Достаточно прочные и пластичные швы для сплава ВТ6 получаются при использовании составных электродов, изготовленных из полос сплава ВТ6 и ВТ1-00 в соотношении 70% к 30%. Флюсы типа АНТ-2 в расплавленном состоянии весьма электропроводны. Поэтому при сварке пластинчатыми электродами рабочее напряжение электрошлакового процесса оказалось возможным снизить до 16-18 В. Это позволило свести к минимуму перегрев металла шва и околошовной зоны. Глубина проплавления обычно не превышает 3-4 мм.
Минимальная плотность тока, обеспечивающая равномерное плавление пластинчатого электрода, составляет 2,5-3,5 А/мм2.
Максимальный сухой вылет пластинчатого электрода не должен превышать 450-500 мм. При больших значениях вылета электрода наблюдается заметный его разогрев. Поэтому необходим промежуточный токоподвод, который обеспечивал бы
275
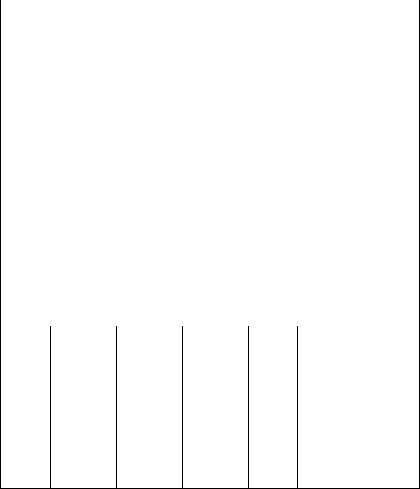
возможность сохранения постоянного вылета. Ориентировочные режимы электрошлаковой сварки титана и его сплавов приведены в табл. 3.18.
Таблица 3.18 Режимы электрошлаковой сварки титана и его сплавов
|
Зазор ме- |
Число |
|
Расход |
|
|
проволоч- |
|
|
||
δ, мм |
жду кром- |
ных элек- |
Iсв, А |
аргона, |
Примечание |
|
ками, мм |
тродов |
|
л/мин. |
|
|
Сварка пластинчатыми электродами |
||||
|
|
|
|
|
|
|
|
|
|
|
U = 16-18 В, глуби- |
30-50 |
23-25 |
- |
1200-1600 |
5-6 |
на шлаковой ванны |
|
|
|
|
|
20-30 мм |
50-80 |
23-25 |
- |
1600-2000 |
7-10 |
|
80-100 |
24-26 |
- |
2000-2400 |
10-12 |
|
100-120 |
24-26 |
- |
2400-2800 |
12-14 |
|
|
|
Сварка плавящимся мундштуком |
|||
|
|
|
|
|
|
|
|
|
|
|
U = 19-22 В, глуби- |
100-110 |
30-32 |
1-2 |
2510-2980 |
25 |
на шлаковой ванны |
|
|
|
|
|
30-40 мм |
200-250 |
30-32 |
2-3 |
4760-6210 |
35-40 |
|
300-350 |
32-34 |
3 |
7590-9260 |
45-50 |
|
400 |
32-40 |
4 |
10970 |
50 |
|
|
Сварка проволочными электродами диаметром 5 мм |
||||
|
|
|
|
|
|
|
|
|
|
|
U = 30-34 В, |
40-60 |
30-32 |
1 |
760-830 |
45 |
Vп = 120 м/ч, сухой |
вылет эл-да 40-60 |
|||||
|
|
|
|
|
мм, глубина шлако- |
|
|
|
|
|
вой ванны 30-40 мм |
60-80 |
30-32 |
1 |
760-830 |
45 |
|
80-100 |
30-32 |
1 |
760-830 |
45 |
|
100-120 |
30-32 |
2 |
1520-1660 |
50 |
|
120140 |
30-32 |
2 |
1520-1660 |
50 |
|
140-160 |
30-32 |
2 |
1520-1660 |
50 |
|
Для сварки титана и его сплавов созданы отечественные специализированные установки, питание которых осуществля-
276
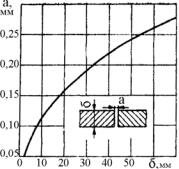
ется от трансформаторов с жёсткой вольт-амперной характери-
стикой типа ТШС-1000-3, ТШС-3000-1, ТШС-3000-3.
Электронно-лучевая сварка применяется при изготовле-
нии сложных и ответственных конструкций. Однопроходную ЭЛС титановых сплавов выполняют при толщине металла начиная от 0,5 мм до 150 мм, а в лабораторных условиях и до 190 мм.
При ЭЛС титана и его сплавов для получения качественных швов требуется значительно большая точность сборки изделий под сварку и строгое соблюдение допустимых размеров между кромками (рис.3.8), которые перед сваркой тщательно зачищаются (как правило, шабрением).
Рис.3.8. Зависимость допустимого размера зазора в стыке при ЭЛС титановых сплавов от их толщины
Широкий диапазон толщин свариваемых заготовок, возможность варьирования параметрами сварки, обеспечивающими требуемую глубину проплавления, а также особенности электронно-оптических систем различных сварочных пушек затрудняют назначение режимов сварки конкретных деталей и требуют проведения дополнительных работ по их подбору. Но, несмотря на это, можно ориентировочно определить исходные параметры ЭЛС титановых сплавов толщиной до 75 мм, пользуясь зависимостью, приведенной на рис. 3.9.
277
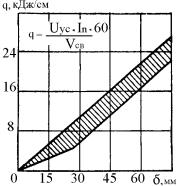
Рис.3.9. Зависимость энергии, необходимой на единицу длины шва при ЭЛС, от толщины свариваемых титановых сплавов
Качество формирования шва при сварке лазером обеспечивается подгонкой свариваемых деталей и строгим соблюдением допустимых зазоров между кромками.
Высокие эксплуатационные свойства сварных соединений могут быть получены лишь при тщательной защите зоны шва. При лазерной сварке деталей из титановых сплавов необходимо осуществлять их защиту как с верхней, так и с нижней стороны. При этом обязательно следует защищать не только сварочную ванну, но и остывающие участки металла шва и
ОШЗ до температуры 400-500°С, что обеспечивается использованием сопла с дополнительным хвостовиком для подачи инертного газа. Для защиты зоны сварки применяют инертные газы высокой степени чистоты или бескислородные фториднохлоридные флюсы. Для защиты поверхности шва и плазмоподавления используется гелий, а для защиты остывающей поверхности шва и его корня можно использовать аргон.
Режимы лазерной сварки некоторых титановых сплавов представлены в табл.3.19.
Рекомендуется выполнять лазерную сварку титановых сплавов на повышенных скоростях (более 90 м/ч). При уменьшении скорости увеличивается ширина шва, образуются не-
278
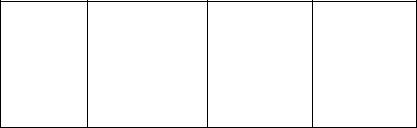
благоприятные структуры, повышается вероятность газонасыщения металла и склонность к образованию холодных трещин.
Таблица 3.19 Режимы лазерной сварки некоторых титановых сплавов
Марка сплава |
Толщина металла, |
Мощность, кВт |
Скорость сварки, |
|
|
мм |
|
м/ч |
|
ВТ6 |
3,0 |
3,0 |
80 |
|
5,0 |
4,0 |
80 |
||
|
||||
ВТ28 |
2,0 |
4,0 |
160 |
|
3,0 |
3,3 |
100 |
||
|
||||
ПТ-3В |
3,0 |
4,0 |
160 |
|
5,0 |
4,0 |
100 |
||
|
Контактная сварка. Титановые сплавы характеризуются хорошей свариваемостью на жёстких режимах. Невысокие тепло- и электропроводность титановых сплавов позволяют осуществлять сварку при сравнительно невысоких плотностях тока.
Точечная сварка листового титана и его сплавов даёт хорошие результаты даже без защиты зоны сварки инертным газом благодаря плотному контакту между деталями.
Важным условием получения качественного соединения деталей является очистка поверхности металла от оксидных плёнок и загрязнений. Перед сваркой рекомендуется проводить травление листов в осветляющем кислотном растворе, например: 30% азотной кислоты; 3% плавиковой кислоты; 67% воды (в объёмных долях) с последующей промывкой в воде, обезжириванием и обезвоживанием протиркой ацетоном и спиртом. После такой обработки контактное сопротивление не превышает 50-60 мкОм. Последующая выдержка на воздухе приводит к росту толщины оксидов и увеличению контактного сопротивления, поэтому длительность перерыва между травлением и сваркой не должна превышать 45-50 ч.
Общая схема технологического процесса производства сварных узлов аналогична рассмотренной выше.
279
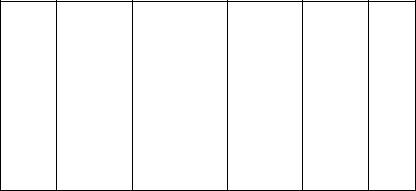
Точечная сварка титановых сплавов может выполняться на серийно выпускаемых контактных машинах без каких-либо существенных конструктивных изменений. Режимы точечной контактной сварки титановых сплавов приведены в табл. 3.20.
Таблица 3.20 Режимы точечной контактной сварки титановых сплавов
|
Радиус |
|
|
|
Диа- |
|
δ, мм |
электродов, |
Iсв, кА |
t, с |
Р, кН |
метр |
|
ядра , |
||||||
|
мм |
|
|
|
||
|
|
|
|
|
мм |
|
0,3+0,5 |
25-40 |
4,5 |
0,08-0.10 |
1,5-2,0 |
3.0 |
|
0,8+ 0,8 |
50-75 |
5,5 |
0,10-0,15 |
2,0-3,4 |
4.0 |
|
1,0 + 1,0 |
75-100 |
6,0 |
0,15-0,20 |
2,5-2,94 |
5,0 |
|
1,2+1.2 |
75-100 |
6.5 |
0,20-0,25 |
2,94-3,4 |
5.5 |
|
1,5+1,5 |
75-100 |
7,0 |
0.25-0,30 |
3,43-3,9 |
6,0 |
|
1,7+ 1,7 |
75-100 |
7,5 |
0,25-0,30 |
3,7-4,2 |
6,5 |
|
2,0+2,0 |
100-150 |
9,0 |
0,30-0,35 |
4,4-4,9 |
7,0 |
|
2,5+2,5 |
100-150 |
10,0 |
0,30-0,35 |
5,9-7,4 |
8,0 |
Шовная сварка используется для соединения листов из титановых сплавов толщиной до 2-2,5 мм, при этом желательна защита зоны сварки инертным газом.
Для титана наиболее приемлемо шаговое перемещение деталей и включение тока в момент остановки роликов. При этом создаются благоприятные условия для кристаллизации расплава под давлением и обеспечивается более глубокий провар без перегрева наружной поверхности. Скорость вращения роликов при выключении тока нарастает до максимальной величины и снижается до нуля в момент включения тока.
Шовную сварку титановых сплавов выполняют по отбортовке или внахлестку на серийно выпускаемом оборудовании без каких-либо существенных конструктивных изменений. При сварке титана обязательно наружное водяное охлаждение роликов, т. к. оно способствует не только уменьшению износа роликов, но и повышает качество сварного соединения благодаря уменьшению времени пребывания разогретого металла в
280
контакте с газами атмосферы.
При увеличении толщины свариваемых металлов от 0,3 до 3,0 мм сварочный ток возрастает от 5 до 12 кА, длительность импульсов увеличивается от 0,08 до 0,28 с, усилие сжатия увеличивается от 0,98 до 8,8 кН, а скорость сварки уменьшается от 1 до 0,3 м/мин. При этом ширина шва возрастает от
2,5 до 9,5 мм.
Механические свойства соединений, полученных шовной сваркой, несколько ниже по сравнению с точечными соединениями вследствие более длительного пребывания металла при повышенных температурах. При механических испытаниях разрушение происходит по основному металлу.
Сварка трением. В некоторых случаях для получения соединения между заготовками с компактным сечением используют сварку трением. Оптимальный режим сварки заготовок диаметром 16 мм из сплава ОТ4 следующий: давление нагрева 59 МПа; деформация 2 мм; давление осадки 98 МПа; деформация 4 мм; длительность цикла сварки 5 с. Механические свойства сварного соединения при этом получаются на уровне свойств основного металла.
Диффузионная сварка. Одним из основных условий получения качественного соединений при диффузионной сварке титана и его сплавов является развитие физического контакта между поверхностями свободными от оксидных пленок.
Кинетика утончения оксидных пленок при нагреве за счет растворения кислорода в титане, описывается выражением, полученным аппроксимацией экспериментальных данных:
∆y2=4,8 1014 exp(-247000/RT)τ,
где ∆y – толщина растворимого слоя оксида, нм; T – темпера-
тура отжига, °K; R – газовая постоянная, Дж/моль K; τ - длительность отжига, с.
После механической (или любой другой) обработки, обеспечивающей удаление оксидов с поверхности титана, вновь образующаяся оксидная пленка на воздухе при комнат-
281
ной температуре достигает толщины около 1,7 нм через 2 ч. и 3,5 нм спустя 40-45 суток.
Очистка титана от естественных оксидных пленок за счет растворения кислорода в металлической основе при нагреве
протекает очень быстро. Так, уже при температуре 600°C для растворения оксидной пленки толщиной 3,5 нм требуется всего 16 с. Но на открытой поверхности за это же время даже при разряжении воздуха в вакуумной камере до 10-5 Па образуется мономолекулярный слой кислорода, который затем переходит в оксид.
При диффузионной сварке титана давление газа в контактном зазоре между свариваемыми поверхностями может существенно отличаться от давления газа в вакуумной камере. Это связано с тем, что при нагреве в зазоре между двумя пластинами из титана, помещенными друг на друга, развивается процесс автовакуумирования, заключающийся в следующем. В начальный момент давление кислорода в контактном зазоре в любой точке равно его давлению в вакуумной камере и определяется откачивающей способностью вакуумной системы. Титан при нагреве, окисляясь, поглощает кислород из окружающего объема. Поскольку объем газа между свариваемыми поверхностями во много раз меньше объема газа, окружающего соединяемые детали (газа, содержащегося в вакуумной камере), то окисление титана может сопровождаться значительным снижением давления кислорода в зоне контакта и, как следствие этого, появлением потока газа из объема вакуумной камеры в приконтактный зазор. Так как интенсивность взаимодействия металла с кислородом возрастает с повышением температуры, то это должно приводить к увеличению поступления газа в зону контакта. Глубина проникновения кислорода в зазор между свариваемыми поверхностями будет определяться соотношением количества кислорода, поступающего в зону контакта и прореагировавшего с титаном в процессе окисления. Результаты расчетов показали, что в контактном зазоре в
282
результате развития эффекта автовакуумирования могут создаться условия безокислительного нагрева и образования поверхностей с высокой реакционной способностью к схватыванию.
Такие условия, например, создаются при сечении заготовок с r ≥ 10 мм; чистоте обработки контактных поверхностей
чистовым точением, обеспечивающем h ≤ 10мкм и разряжении в сварочной камере до 10-1 Па. Следует отметить, что в этих условиях на внешних поверхностях будет происходить образование оксидов за счет взаимодействия титана с остаточными газами вакуумированного пространства.
Основные технологические параметры режима диффузионной сварки в порядке убывания их влияния на прочность соединения располагаются в последовательности: температура, давление, время сварки – при сварке в интервале температур
ниже конца полиморфного превращения − и давление, температура, время сварки - при сварке в области существования β- фазы.
Диффузионная сварка титановых α- и α+β- сплавов обычно выполняется в интервале температур полиморфного превращения, значения которых приведены в табл. 3.21.
|
|
|
|
|
|
Таблица 3.21 |
|
|
Температура |
полиморфного превращения титановых |
|||||
сплавов |
|
|
|
|
|
|
|
|
|
|
|
|
|
|
|
|
Марка |
Температура поли- |
|
Марка |
Температура поли- |
||
|
морфного превра- |
|
морфного превра- |
|
|||
|
сплава |
|
сплава |
|
|||
|
|
щения, 0С |
|
щения, 0С |
|
||
|
ВТ1-0 |
|
885-900 |
|
ВТ6 |
980-1010 |
|
|
ВТ3-1 |
|
960-1000 |
|
ВТ6С |
950-990 |
|
|
ОТ4-0 |
|
850-930 |
|
ВТ8, ВТ9 |
980-1020 |
|
|
ОТ4-1 |
|
910-950 |
|
ВТ14 |
920-960 |
|
|
ОТ4 |
|
920-960 |
|
ВТ18 |
990-1020 |
|
|
ВТ5 |
|
930-980 |
|
ВТ20 |
980-1020 |
|
|
ВТ5-1 |
|
950-990 |
|
ВТ22 |
840-880 |
|
|
|
|
|
283 |
|
|
Сварка β-сплавов осуществляется в β-области, что обусловлено низкими температурами α+β↔β-превращения этих материалов (~720-800°C) и высоким сопротивлением деформа-
ции легированных β-растворов в области нижеуказанных температур.
Величина удельных сварочных давлений и времени сварки взаимосвязаны и могут изменяться в широких пределах. При изготовлении, например, тонкостенных конструкций, величина удельных давлений ограничивается устойчивостью (или допустимой деформацией) свариваемых заготовок, а длительность сварки выбирается из условия получения требуемого качества соединения. Фактором, влияющим на эти параметры, является исходная микроструктура сплава. Чистота обработки контактных поверхностей должна быть максимально высокой и ограничивается экономическими соображениями.
Применительно к процессу диффузионной сварки для регламентирования исходного микроструктурного состояния свариваемых заготовок целесообразно выделение четырех основных типов структур: I - мелкозернистая, характеризуемая
диаметром α - зерен D (D≤15мкм), включающая в себя глобулярные, равноосные и с вытянутыми зернами α-фазы структуры; II – пластинчатая (мелкопластинчатая) без видимых границ исходных β-зерен, характеризуемая шириной α-пластин – b и величиной α-колоний – d (b≤1 мкм; α≤20 мкм); III – пластинчатая с видимыми границами исходных β-зерен, характеризуемая диаметром бывших β-зерен D (D= 230-500 мкм); IV – смешанная, характеризуемая объемным содержанием материала с пластинчатой структурой Vпл (10%<Vпл<50%). При Vпл<10% структуру сплава следует отнести к I типу, а при Vпл>50% - к III типу.
Ориентировочные режимы диффузионной сварки сплава ОТ4 с подготовкой контактных поверхностей точением приведены в табл. 3.22.
284
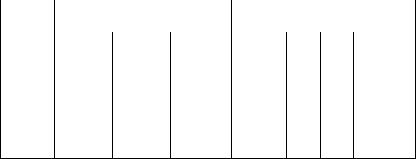
Режимы диффузионной сварки сплава ОТ4 |
|
Таблица 3.22 |
||||||||
|
|
|
|
|||||||
|
|
|
|
|||||||
Тип |
Режимы диффузионной свар- |
Механические свойства соеди- |
||||||||
микро- |
|
ки |
|
|
|
нения |
|
|
||
струк- |
T , 0С |
P, МПа |
τ |
σ |
ψ |
, % |
δ |
, % |
KCV, |
|
туры |
св |
|
, мин |
в, МПа |
|
|
МДж/м2 |
|||
|
|
|
|
|
|
|
|
|||
I |
950 |
0,5-2,0 40-180 |
780 |
41 |
18 |
0,83 |
|
|||
II |
950 |
4,0-6,0 |
40-60 |
820 |
20 |
12 |
1,40 |
|
||
III |
950 |
5,0-12 |
40-90 |
830 |
18 |
11 |
1,40 |
|
||
IV |
950 |
1,0-2,5 |
40-60 |
750 |
25 |
14 |
1,12 |
|
||
I-IV |
1000- |
2,0-4,0 |
40-90 |
830 |
18 |
11 |
1,35 |
|
||
1025 |
|
|||||||||
|
|
|
|
|
|
|
|
|
|
Применение диффузионной сварки (ДС) для соединения деталей и узлов летательных аппаратов из титановых сплавов позволяет получать принципиально новые типы изделий сложной конфигурации, например, конструкций канальноготипа, гофровых и ячеистых слоистых панелей, а также длинномерных заготовок переменного сечения путём стыковки отдельных профилированных элементов (см. табл. 3.23).
Типовой процесс получения конструкции методом ДС включает:
−сборку свариваемых элементов в технологической осна-
стке;
−нагрев собранной садки в вакууме или защитной среде до температуры сварки;
−приложение сварочного давления в течение заданного времени;
−охлаждение, разборку садки и извлечение сваренной де-
тали;
−контроль качества сваренной детали.
При ДС элементов тонкостенных конструкций из титановых сплавов различного типа применяются следующие методы создания сварочного давления.
285
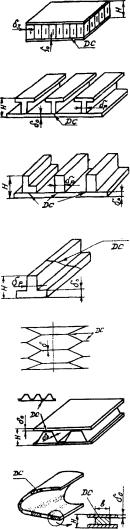
Таблица 3.23 Основные виды полученных диффузионной сваркой кон-
струкций летательных аппаратов
Вид конст- |
Эскиз конструкции |
Геометрич. |
Св. давле- |
Метод |
рукции |
|
параметры |
ние, МПа |
ДС |
|
|
H/δ = 200 |
|
|
Сотовые па- |
|
H = 10-80 мм |
0,5 |
Вакуум- |
нели |
|
δ0 = 0,5-2 мм |
ный |
|
|
|
|||
|
|
δз = 0,1 мм |
|
|
|
|
H/δ = 5-20 |
|
|
Ребрист. |
|
H = 50-100 |
|
Диа- |
стрингерные |
|
мм |
2-20 |
фрагмен- |
панели |
|
δр = 5-15 мм |
|
ный |
|
|
δ0 = 10-20 мм |
|
|
|
|
H/δ = 1-5 |
|
|
Ребристые |
|
H=50-200 мм |
10-50 |
Прессо- |
заготовки |
|
δр= 15-200 |
||
|
вый |
|||
панелей |
|
мм |
|
|
|
|
|
||
|
|
δ0 = 20-50 мм |
|
|
Длинномерн. |
|
H/δ = 3-20 |
|
|
заготовки |
|
|
|
|
переменного |
|
H=50-200 мм |
10-30 |
-//- |
сеч. типа |
|
δр = 10-50 мм |
|
|
поясов лон- |
|
δ0 = 10-50 мм |
|
|
жеронов |
|
|
|
|
Пластинча- |
|
δ = 0,5-1 |
|
|
тые сильфо- |
|
=500-1000 |
10-30 |
-//- |
ны |
|
мм |
|
|
|
|
|
|
|
Гофровые и |
|
H = 10-30 мм |
|
Прессо- |
|
δ0 = 0,5-2 мм |
|
вый, |
|
ячеистые па- |
|
10-30 |
||
нели |
|
δз = 0,2-1,5 |
|
диафраг- |
|
мм |
|
менный |
|
|
|
|
||
|
|
|
|
|
Конструкция |
|
H = 2-5 мм |
|
Диа- |
|
δ0 = 0,5-1 мм |
2-10 |
фрагмен- |
|
носка крыла |
|
|||
|
Н/b = 0,1-0,2 |
|
ный |
|
|
|
|
||
|
|
|
|
|
|
|
286 |
|
|
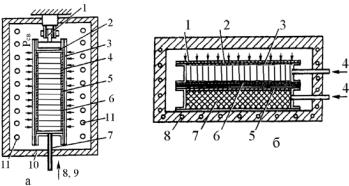
1. Вакуумный метод (рис. 3.10) применяется при ДС тонкостенных конструкций, например, сотовых панелей с заполнителем из фольги толщиной 0,05-0,1 мм и обшивками толщиной 0,5-1,0 мм. При этом свариваемые элементы собираются в пакет и размещаются в герметичном тонколистовом контейнере из коррозионно-стойкой стали, который устанавливается в нагревательной камере печи на жестком основании (контейнере с графитовой плитой толщиной 100 мм), служащем базовой поверхностью и обеспечивающей плоскостность свариваемых сотовых пакетов.
Рис. 3.10. Схемы вакуумного метода диффузионной сварки: а - с мягким контейнером: 1 - узел подвески; 2 - компенсатор; 3 - технологический лист; 4 - обшивка; 5 - сотоблок; б - контейнер; 7 - труба; 8 - вакуум; 9 - аргон; 10 - печь; 11 - нагреватели; б - с жестким контейнером: 1- контейнер; 2 - обшивка; 3 - технологическая прокладка; 4 - вакуум, аргон; 5 - медный лист; 6 - сотоблок; 7 - графитовая плита; 8 - нагреватели
В контейнере создается контролируемая атмосфера инертного газа (аргона). Сварочное давление создается за счет разности атмосферного давления и давления аргона в полости контейнера, которая не может превышать 0,1 МПа. Величина давления на поверхность контейнера составляет на режиме ДС р = 0,01 МПа, что соответствует сварочному давлению обши-
287
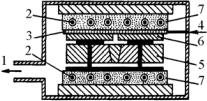
вок на стенки сот заполнителя р = 0,5 МПа. Время сварки - 1,5 ч.
2. Вакуум-компрессионный метод (рис. 3.11), или диа-
фрагменный метод, применяется при ДС конструкций с отно-
сительной толщиной привариваемых элементов Н/δ = 5...20, например, для сварки ребристых стрингерных панелей при толщине стенки стрингера до 1015 мм.
Рис. 3.11. Схема вакуум-компрессионного (диафрагменного) метода диффузионной сварки: 1 - вакуум; 2 - нагреватели; 3 - диафрагма; 4 - аргон; 5 - оснастка; 6 - накладки; 7 – керамические плиты
Сварочное давление создается подачей в диафрагму газа под давлением до 1,0 МПа, что позволяет реализовывать давление в контакте ребер с полотном панели в диапазоне 2-20 МПа. Диафрагма, представляющая собой тонкостенный мешок из коррозионно-стойкой стали, располагается между свариваемыми деталями и жесткими плитами оснастки. Свариваемые детали, собранные с технологической оснасткой, служащей для предотвращения потери устойчивости привариваемых ребер, размещаются либо в контейнере (при сварке в печи сопротивления), либо в вакуумной камере специализированной установки.
3. Прессовый метод (рис. 3.12) применяется при ДС конструкций с относительной толщиной привариваемых элемен-
тов Н/δ = 1...5, например, при сварке оребрённых заготовок, имеющих ребра толщиной свыше 15 мм, пластинчатых сильфонов или для получения длинномерных заготовок переменного сечения стыковкой отдельных профилированных элементов (пояса лонжеронов).
288
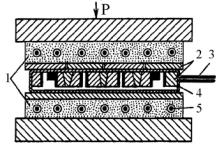
Рис. 3.12. Схема прессового метода диффузионной сварки: 1 - керамические плиты; 2 - оснастка (малоуглеродистая сталь); 3 – вакуумный коллектор; 4 - контейнер; 5 - нагреватели
Данный метод позволяет реализовывать сварочное давление порядка 10-50 МПа, создаваемое за счет усилия сжатия плит гидравлического пресса. Технология сборки и размещения свариваемых деталей в оборудовании при сварке ребристых панелей аналогична технологии диафрагменного метода ДС.
Вакуумным методом ДС изготавливают сотовые пакеты - полуфабрикаты, из которых стандартными методами механической обработки, обработки давлением, размерного химического травления и сварки плавлением получают заданные сотовые конструкции. В настоящее время освоена промышленная технология ДС плоских сотовых пакетов с габаритными размерами до 2000х1000 мм и высотой 10-80 мм. Обшивки выполняются из листов сплава ВТ6ч толщиной 0,5-2,0 мм, сотовый заполнитель - из фольги сплава ВТ6чПС толщиной 0,08 мм, ячейка, заполнителя квадратная, со стороной а = 8 мм. Применение ДС сотовых конструкций перегородок позволило снизить массу конструкции на 30 %, уменьшить трудоемкость механической обработки и сборочных работ на 40 % и повысить КИМ при изготовлении конструкции до 0,7.
При ДС стрингерных панелей (рис. 3.13) используется диафрагменный метод создания сварочного давления (рис.
3.11).
289