
- •Введение
- •Состав МКМ
- •Механические свойства МКМ
- •вдоль волокон
- •вдоль волокон
- •Свойство
- •При сварке по флюсу обеспечиваются достаточно высокие механические свойства сварных соединений (табл. 3.2).
- •Электрошлаковая сварка. В настоящее время освоена электрошлаковая сварка заготовок толщиной 200-300 мм из алюминия и алюминиевых сплавов. Экономически выгодно применять ЭШС при толщине металла более 25 мм.
- •3.4.1. Металлургические особенности сварки
- •Ручная сварка
- •Автоматическая сварка
- •БИБЛИОГРАФИЧЕСКИЙ СПИСОК
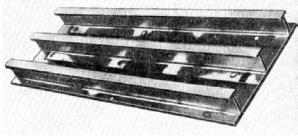
Данный метод позволяет упростить технологию сборки деталей под сварку, а также обеспечить необходимое сварочное давление и деформацию деталей независимо от неточностей сборки и подгонки деталей или их конструктивных особенностей.
Рис. 3.13. Натурный образец ДС стрингерной панели из сплава ВТбч. Габаритные размеры 1300х500х100 мм
ДС панели осуществлялась по следующему режиму: Т =
930 °С, Рдиаф = 0,3 МПа (рсвар = 10 МПа), τ = 2 ч, остаточное давление в камере установки составляло 1,3 10-3 Па. После ос-
тывания садки и выкатывания нижней плиты из камеры производилась разборка приспособления и извлечение сваренной панели.
3.4.Сварка сталей
3.4.1.Металлургические особенности сварки
При сварке плавлением сталей возможно развитие процесса окисления металла и легирующих компонентов шва кислородом, содержащимся в защитных газах, шлаках сварочной ванны, оксидах (окалине, ржавчине), находящихся на кромках деталей и поверхности электродной проволоки.
Кислород с железом образует три оксида: FeO (22,3%O2), Fe3O4 (27,6%O2) и Fe2O3 (30,1%O2). При высокой температуре сварочной дуги за счет атомарного кислорода образуется низший оксид
Fe + O ↔ FeO,
290
который при понижении температуры может переходить в
высшие оксиды Fe3O4 и Fe2O3.
Оксид FeO способен растворяться в жидком металле и после остывания металла сварочной ванны может оставаться в сварочном шве в виде пленок, окаймляющих зерна, что сильно снижает пластические свойства шва. Высшие оксиды Fe3O4 и Fe2O3 не растворяются в жидком металле, и если они не всплывают на поверхность сварочной ванны, то остаются в металле шва в виде шлаковых включений.
Железо и легирующие элементы могут окисляться также кислородом сложных газов СО, СО2 и паров воды Н2О.
В сварочной ванне легирующие элементы могут окисляться при взаимодействии с FeO
Me + FeO ↔ MeO + Fe.
Это приводит к тому, что их содержание в металле уменьшается. Образовавшиеся оксиды могут оставаться в шве в виде газовых пор и шлаковых включений, что значительно снижает механические свойства сварных соединений.
Процесс перевода растворённого оксида FeO в форму нерастворимых соединений с последующим их удалением в шлак называется раскислением. В качестве раскислителей при сварке сталей используют марганец, кремний, титан, алюминий и другие элементы, обладающие большим. чем железо, сродством к кислороду. Раскислители вводятся в сварочную ванну через электродную проволоку, покрытия электрода и флюс.
Раскисление марганцем происходит по реакции
[FeО] + Mn↔ Fe + (MnO).
Оксид марганца мало растворим в железе, но сам хорошо растворяет в себе оксид железа FeO, увлекая его за собой в шлак.
Раскисление кремнием происходит по реакции
2[FeO] + Si↔2Fe +(SiO2).
Оксид кремния плохо растворим в железе и всплывает в шлак. Раскисление кремнием сопровождается образованием
291
комплексных соединений, которые также переходят в шлак
MnO+SiO2=(MnO·TiO2),
FeO+TiO2=(FeO·TiO2).
Раскисление алюминием
3[FeO]+2Al=3Fe+(Al2O3).
Алюминий более энергичный раскислитель, чем титан, но он образует тугоплавкие оксиды, которые очень медленно переходят в шлак и частично остаются в шве. Кроме того, он способствует окислению углерода, что приводит к пористости шва.
Одной из особенностей металлургических процессов при сварке под флюсом средне- и низколегированных сталей является легирование шва марганцем и кремнием за счет их восстановления из оксидов MnO и SiO2, находящихся во флюсе. В высокотемпературной зоне протекают восстановительные реакции:
2[Fe]+(SiO2)↔2(FeO)+[Si], [Fe]+(MnO)↔(FeO)=[Mn].
Образовавшийся при этом оксид FeO частично всплывает в шлак, а частично растворяется в жидком металле; марганец и кремний полностью остаются в металле шва. При увеличении напряжения дуги возрастает количество расплавленного флюса
ипереход марганца и кремния в шов увеличивается.
Вхвостовой части сварочной ванны в зоне понижения температур протекают реакции раскисления оксидов железа кремнием и марганцем с последующим образованием ком-
плексных нерастворимых в металле соединений (MnO SiO2), легко переходящих в шлак. При недостаточном содержании в сварочной ванне марганца и кремния может происходить раскисление оксида железа углеродом
[FeO]+[C]=[Fe]+{CO}.
Образовавшийся оксид углерода может приводить к пористости.
Аналогичные процессы протекают при сварке легирован-
292
ных сталей под низкокремниестыми флюсами АН-26, ФЦЛ-2, предназначенными для сварки нержавеющих сталей. И хотя окислительное действие низкокремнистых флюсов, особенно не содержащих MnO, на металл сварочной ванны невелико, все же оно достаточно, чтобы полностью или в значительной степени окислить и перевести в шлак такие элементы, как титан, алюминий, цирконий и др. В этом случае восполнение окисленных элементов осуществляется подбором электродной проволоки соответствующего химического состава.
Для подавления процесса окисления при сварке легированных сталей используют флюсы на основе фторидных и хлоридных солей щелочных и щелочноземельных металлов. Например, флюс АНФ-5, его основу составляет CaF2(75-80%) и
NaF (17-25%).
При сварке в активных защитных газах (СО2) газовая среда дуги имеет окислительный характер. Поэтому при сварке низколегированных сталей происходит окисление как железа, так и легирующих компонентов с образованием FeO, SiO2, MnO, CO и др. В общем виде эти реакции могут быть выраж е- ны уравнением
[FeO] + [C, Si, Mn, Al и др.] ↔ (SiO2, MnO, Al2O3 и др.) + +{CO, SO2, H2O и др.} + Fe.
Для подавления реакций окисления, а также пополнения выгоревших элементов при сварке в углекислом газе низколегированных сталей применяют специальные электродные проволоки с повышенным содержанием марганца и кремния, например, Св-08ГС, Св-12ГС, Св-08Г2С и др. При применении этих проволок в зоне пониженных температур сварочной ванны протекают реакции раскисления
[FeO] + Si ↔ Fe + (SiO2),
[FeO] + Mn ↔ Fe + (MnO),
т. е. кремний и марганец раскисляют оксид железа FeO и, в дальнейшем сами окисляясь, всплывают на поверхность сварочной ванны.
293
При недостаточном содержании кремния и марганца в сварочной ванне будет происходить выгорание углерода, вызывающее кипение сварочной ванны и приводящее к образованию пор.
Впроцессе сварки высоколегированных сталей окисление (выгорание) отдельных легирующих элементов может быть столь значительным, что сталь в зоне сварки может оказаться по шкале структур сталью другого класса.
Химический состав высокопрочных сталей достаточно жестко сбалансирован. Поэтому для получения качественного соединения технология сварки должна обеспечивать надежную защиту от выгорания легирующих элементов и от растворения
вметалле шва азота (из воздуха) и водорода, выделяющегося при разложении влаги, попадающей в зону сварки. В связи с этим в качестве основных видов сварки при создании ответственных силовых конструкций принята аргонодуговая сварка и электронно-лучевая (для массивных конструкций).
Окислению сварочной ванны при сварке в среде аргона способствуют примеси, находящиеся в защитном газе в виде свободного кислорода и паров воды. При этом окисляется в основном углерод с образованием газообразного оксида СО.
Для подавления реакции окисления углерода в сварочной ванне должно находиться достаточное количество раскислителей.
Иногда к аргону добавляют некоторое количество углекислого газа (10-15%) или кислорода (до 5%). Это приводит к интенсификации процесса образования оксида углерода и кипению сварочной ванны. Бурно выделяющиеся пузырьки захватывают и выносят из ванны находящиеся в ней газы, что приводит к снижению вероятности образования пор.
Взависимости от содержания легирующих элементов стали условно можно разделить на низколегированные (содержание легирующих элементов до 4%), среднелегированные (до 9%) и высоколегированные (более 9%).
294
3.4.2. Сварка низколегированных сталей
Низколегированные стали обладают хорошей свариваемостью всеми видами сварки. Обеспечение равнопрочности металла шва нетермоупрочненных сталей не вызывает затруднений.
При сварке на форсированных режимах низколегированных сталей толщиной более 10-15 мм с содержанием углерода на верхнем пределе (0,25%) возможно образование закалочных структур в металле шва и околошовной зоне при повышенных скоростях охлаждения.
При небольшом количестве закалочных структур их влияние на механические свойства сварных соединений незначительно. Однако при увеличении доли таких структур в шве и околошовной зоне пластичность металла и его стойкость против хрупкого разрушения ухудшаются. Режим сварки большинства низколегированных сталей следует ограничивать достаточно узкими по значению погонной энергии пределами. В ряде случаев, например при микролегировании ванадием и азотом, а также другими элементами, склонность низколегированной стали к росту зерна в околошовной зоне при сварке незначительна.
Обеспечение равнопрочности металла шва с основным металлом достигается, в основном, за счет легирования его элементами, переходящими из основного металла. Иногда для повышения прочности и стойкости против хрупкого разрушения металл шва дополнительно легируют через сварочную проволоку.
Стойкость металла шва против кристаллизационных трещин при сварке низколегированных сталей в целом достаточно высокая, однако она может понижаться в связи с усилением отрицательного влияния углерода некоторыми легирующими элементами, например кремнием. Повышение стойкости против образования трещин достигается уменьшением содержания в шве углерода, серы и некоторых других элемен-
295
тов за счет применения сварочной проволоки с пониженным содержанием указанных элементов, а также выбором соответствующей технологии сварки (последовательность выполнения швов, обеспечение благоприятной формы провара).
Сварка покрытыми электродами. Покрытые электроды для ручной дуговой сварки по ГОСТ 9466-75 «Электроды, покрытые металлические для ручной дуговой сварки и наплавки. Классификация, размеры и общие технические требования» изготавливают диаметром от 1,6 до 12 мм и длиной от 250 до 450 мм, однако основной объём работ выполняется электродами диаметром 3-6 мм.
Стержни электродов изготавливают из сварочной проволоки, выпускаемой по ГОСТ 2246-70. В состав покрытия электродов входят следующие компоненты.
Ионизирующие и стабилизирующие – это соединения, содержащие ионы щелочных металлов с низким потенциалом ионизации (Na2CO3, K2CO3, CaCO3, NaF, то есть поташ, мел, мрамор, полевой шпат и т.п.)
Газообразующие компоненты − вещества, разлагающиеся с выделением большого объёма газа – мрамор, мел или органические вещества: декстрин, крахмал, целлюлоза, которые при нагреве ещё до расплавления металла в результате разложения и окисления дают много газообразных продуктов: СО2,
СО, Н2, О2.
Образующееся значительное количество газов обеспечивает хорошую защиту от атмосферы воздуха и, в частности, от азота. В то же время эта газовая среда является сама окислительной по отношению к железу и легирующим элементам.
Шлакообразующие компоненты – минералы: полевой шпат; мрамор, мел; глинозём; флюорит; кварцевый песок; иногда гематит; марганцевая руда, титановый концентрат. При сплавлении компоненты образуют шлаки различного состава и основности.
Раскислители и легирующие компоненты – кремний,
296

марганец, титан и др., используемые в виде порошков сплавов этих элементов с железом (так называемых ферросплавов), быстро растворяющихся в жидкой стали. Алюминий в покрытие вводят в виде порошка – пудры.
Некоторые компоненты могут выполнять несколько функций одновременно, например, мел, который, разлагаясь, выделяет много газа (CO2), оксид кальция идёт на образование шлака, а пары кальция имеют низкий потенциал ионизации и стабилизируют дуговой разряд, CO2 служит газовой защитой.
Режимы сварки выбирают в зависимости от толщины металла, типа сварного соединения и пространственного положения шва.
При сварке, например корневых швов, в разделке на металле толщиной 10 мм и более используют электроды диаметром 3-4 мм. Рекомендуемые для данной марки электрода значения сварочного тока, его род и полярность выбирают согласно паспорту электрода. Ориентировочные режимы многослойной ручной дуговой сварки стыковых соединений приведены в табл. 3.24.
Таблица 3.24 Режимы многослойной ручной дуговой сварки стыковых
соединений низколегированных сталей
Марка |
Диаметр |
Сварочный |
Длина валика, выпол- |
|
электрода, |
няемого одним элек- |
|||
электрода |
ток, А |
|||
мм |
тродом, мм |
|||
|
|
|||
УОНИ 13/45 |
4 |
130-160 |
120-160 |
|
УОНИ 13/55 |
5 |
170-200 |
200-250 |
Сварка под флюсом. Автоматическую сварку обычно выполняют электродной проволокой диаметром 3-5 мм, полуавтоматическую – проволокой 0,8-2 мм. Равнопрочность соединения достигается за счет подбора соответствующих составов флюсов, электродных проволок и выбора режима сварки.
При сварке низколегированных сталей обычно применя-
ют флюсы марок АН-348-А (SiO2 - 42%; MnO –36,5%; CaF2 – 6,5%; MgO – 7%; CaO до 6,5%; Al2O3 до 4,5%; Fe2O3 – до 2,0%,
297
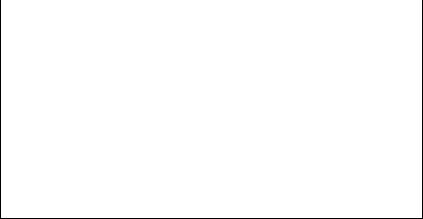
Р – до 0,12% и S до 0,15%), ОСЦ-45 и электродные проволоки марок Св-08ГА, Св-10ГА, Св-10Г2. Легирование металла шва марганцем за счет проволок и кремнием за счет провара основного металла при подборе соответствующего термического цикла (погонной энергии) позволяет получать металл шва с требуемыми механическими свойствами. Ориентировочные режимы сварки приведены в табл. 3.25.
Таблица 3.25 Ориентировочные режимы сварки под флюсом низколе-
гированных сталей
Толщина |
Подго- |
Тип шва |
Д-р элек- |
|
Напря- |
Ско- |
|
металла |
тродной |
Сила тока, |
рость |
||||
или катет |
товка |
и способ |
проволо- |
А |
жение |
сварки, |
|
кромок |
сварки |
дуги, В |
|||||
шва, мм |
ки, мм |
|
м/ч |
||||
|
Без раз- |
|
|
|
|
|
|
8 |
делки, за- |
Односто- |
4 |
550-600 |
26-30 |
48-50 |
|
зор 2-4 |
ронний |
||||||
|
|
|
|
|
|||
|
мм |
|
|
|
|
|
|
12 |
То же |
Двусто- |
5 |
600-700 |
30-34 |
30-32 |
|
ронний |
|||||||
|
V- |
Односто- |
|
Проходы |
|
|
|
Свыше 16 |
5 |
1-й 750-800 |
30-35 |
20-22 |
|||
образные |
ронний |
||||||
|
|
|
|
2-й 800-900 |
|
|
Примечание. Ток постоянный обратной полярности.
Для низколегированных термоупрочненных сталей с целью предупреждения разупрочнения шва в зоне термического влияния следует использовать режимы с малой погонной энергией, а для нетермоупрочненных – наоборот, с повышенной, при этом многослойные швы на толстом металле рекомендуется выполнять двумя дугами, а при сварке одной дугой перед наложением первого слоя производить подогрев основного ме-
талла до температуры 150-200°С.
Металл швов, сваренных под флюсом, благодаря значительной доле участия основного металла и достаточному содержанию легирующих элементов обладает более высокой стойкостью против коррозии, чем металл швов, сваренных по-
298
крытыми электродами обычного состава.
Сварка в защитных газах. При сварке низколегированных сталей широко применяется сварка в углекислом газе или в смеси углекислого газа с кислородом (до 30%) и аргоном (до 80%). Добавка кислорода позволяет уменьшить концентрацию легирующих элементов в металле шва, что иногда целесообразно для повышения пластичности. Помимо этого кислород, связывая водород, уменьшает вероятность образования пор.
Добавка в углекислый газ аргона изменяет технологические свойства дуги (глубину проплавления, форму шва) и позволяет регулировать концентрацию легирующих элементов в металле шва.
Аргон и гелий в «чистом» виде в качестве защитных газов применяют редко – только при сварке конструкций ответственного назначения.
При автоматической и полуавтоматической сварке обычно используют электродную проволоку диаметром 1,2-3,0 мм марок Св-08ГС, Св-08Г2С, Св-12ГС, Св-08ХГ2С и др.
Увеличение напряжения дуги может повышать угар легирующих элементов и приводить к снижению механических свойств шва. Сварка на повышенных силах тока приводит к получению металла шва с пониженными показателями пластичности и ударной вязкости, что объясняется повышенными скоростями охлаждения.
Ориентировочные режимы сварки в СО2 приведены в табл. 3.26. Свойства металла шва, выполненного на этих режимах, соответствуют свойствам металла шва, выполненного электродами типа Э50А.
Применение омеднённой проволоки во многом позволяет повысить устойчивость горения дуги и улучшить качество сварного соединения.
Электрошлаковую сварку (ЭШС) применяют при изго-
товлении конструкций из толстолистовых сталей. При сварке используют флюсы АН-8, ФЦ-7 и др. В зависимости от сост а-
299
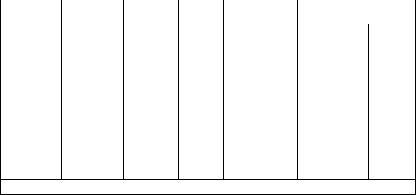
ва стали используют следующие проволоки: Св-10Г2, Св08ГС, Св-08ХГ2СМА и др.
Таблица 3.26 Ориентировочные режимы сварки низколегированных
сталей в среде СО2
Тол- |
Ка- |
|
|
|
Диам. |
|
|
На- |
Ско- |
Расход |
|
||
|
Чис- |
|
элек- |
|
|
рость |
газа на |
|
|||||
щина |
тет |
Зазор, |
|
Сила тока, |
пряже- |
сварки |
|
||||||
метал- |
шва |
мм |
ло |
|
тродн. |
|
А |
ние ду- |
одного |
один |
|
||
слоев |
|
пров., |
|
слой, |
|
||||||||
ла, мм |
, мм |
|
|
|
|
ги, В |
слоя, |
|
|||||
|
|
|
|
|
|
мм |
|
|
|
|
м/ч |
л/мин |
|
|
|
|
|
|
Стыковые швы |
|
|
|
|
|
|||
1,2-2,0 |
|
- |
0,8-1,0 |
1-2 |
|
0,8-1,0 |
|
70-100 |
18-20 |
18-24 |
10-12 |
|
|
3-5 |
|
- |
1,6-2 |
1-2 |
|
1,6-2,0 |
|
180-200 |
28-30 |
20-22 |
14-16 |
|
|
6-8 |
|
- |
1,8-2,2 |
1-2 |
|
2 |
|
250-300 |
28-30 |
18-22 |
16-18 |
|
|
8-12 |
|
- |
1,8-2,2 |
2-3 |
|
2 |
|
250-300 |
28-30 |
16-20 |
18-20 |
|
|
|
Ориентировочные |
режимы |
ЭШС |
приведены в табл.3.27. |
|||||||||
Режимы ЭШС низколегированной стали |
Таблица 3.27 |
||||||||||||
|
|
|
|||||||||||
Толщина |
Сила тока |
Напря- |
Число |
Диаметр |
|
Скорость, м/ч |
|||||||
жение |
элек- |
|
|
|
|
|
|
||||||
металла, |
на 1 элек- |
|
электродов. |
подачи |
сварки |
||||||||
мм |
|
трод, А |
сварки, тро- |
|
мм |
|
|||||||
|
|
|
|
В |
дов* |
|
|
|
электродов |
|
|
||
30 |
|
350-370 |
32-34 |
|
1 |
|
2,5 |
|
172 |
|
0,9-1,0 |
|
|
70 |
|
650 |
47 |
|
1 |
|
3 |
|
371-400 |
1,0-1,1 |
|
||
90 |
|
600-620 |
42-46 |
|
2 |
|
3 |
|
300 |
|
1,6 |
|
|
150 |
|
450-500 |
44-50 |
|
2 |
|
3 |
|
220-240 |
0,8-0,9 |
|
||
200 |
|
550 |
46-48 |
|
2 |
|
3 |
|
250 |
|
0,5 |
|
|
250 |
|
500-550 |
50-55 |
|
2 |
|
3 |
|
230-250 |
0,4-0,5 |
|
||
340 |
|
400-450 |
46-48 |
|
3 |
|
3 |
|
200-220 |
0,3 |
|
*электрод проволочный.
Контактная сварка. Низколегированные стали характеризуются хорошей свариваемостью при использовании контактной сварки. Требования к подготовке свариваемых поверхностей значительно ниже, чем при сварке алюминиевых и титановых сплавов.
Так, холоднокатаную сталь даже не подвергают дополни-
300
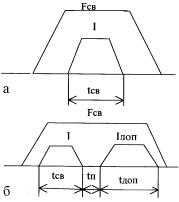
тельной подготовке, т. к. тонкий слой масла мало влияет на процесс сварки. Детали из конструкционных горячекатаных сталей или холоднокатаных, но прошедших термообработку, подвергают механической, дробеструйной обработке поверхности, химическому травлению. При этом снимают толстый неоднородный слой оксидов, заменяя его тонкой и сравнительно однородной плёнкой оксидов. Обработка щётками и дробеструйная зачистка создают микрорельеф, обеспечивающий лучшие условия для разрушения поверхностных плёнок при сварке. Химическое травление сталей проводят в растворах серной или соляной кислот, либо в растворах на основе фосфорной кислоты.
Низколегированные низкоуглеродистые стали могут свариваться в широком диапазоне параметров режима. Из-за малой чувствительности к термическому циклу и небольшой склонности к трещинообразованию применяют машины с простейшим циклом сварки (рис. 3.14,а) либо с двумя импульсами тока (при толщине не более 3 + 3 мм).
Рис. 3.14. Циклограммы точечной сварки: а – с постоянным усилием и одним импульсом; б – то же, но с дополнительным импульсом тока
Из-за малой прочности сварочное усилие устанавливают небольшим. В связи с достаточно высокой тепло- и электро-
301
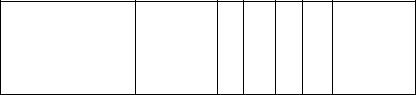
проводностью отдают предпочтение более жёстким режимам. При точечной сварке низколегированных сталей с повышенным содержанием углерода в зоне термического влияния могут образоваться закалочные структуры и возникать трещины. Поэтому после сварки таких металлов обычно проводят термообработку точек между электродами машины. При помощи дополнительного импульса тока (см. рис.3.14,б). Величину тока второго импульса подбирают из условия нагрева зоны термического влияния до температуры, близкой к Ас1. Длительность дополнительного импульса обычно в 1,5 раза боль-
ше сварочного.
Сварку таких сталей ведут на мягких режимах. Чем больше толщина сталей, тем тщательнее должна быть проведена термообработка точек. В некоторых случаях используется трёхимпульсный режим: первый импульс - сварочный, второй - замедляющий скорость кристаллизации и охлаждения, третий - термообрабатывающий.
Для сварки используют электроды с плоской рабочей поверхностью. Ориентировочные режимы точечной сварки низколегированных сталей приведены в табл.3.28.
Таблица 3.28 Режимы точечной сварки низколегированных сталей
Относительное содер- |
Толщина ме- |
dэ, |
Iсв, tсв, |
F, |
Диаметр ядра |
||
жание углерода |
талла, мм |
мм |
кА |
с |
кН |
точки, мм |
|
Низкое |
1 + 1 |
5 |
13,7 |
0,14 |
4,3 |
4 |
|
3 + 3 |
10 |
15,7 |
0,25 |
11,7 |
9 |
||
|
|||||||
Повышенное |
1 + 1 |
5 |
10 |
0,46 |
7 |
4 |
|
3 + 3 |
10 |
16,8 |
1,3 |
15 |
9 |
||
|
Сварка трением. Низколегированные стали можно сваривать в широком диапазоне параметров режима (скорость вращения n и удельное давление р). При этом можно использовать цикл сварки с постоянно приложенным давлением.
Оптимальные режимы сварки трением некоторых сталей представлены в табл. 3.29.
302
Таблица 3.29 Режимы сварки трением низкоуглеродистых сталей
Марка ста- |
Диаметр |
n, |
Р, МПа |
Величина |
Время |
||
заготовки, |
при на- |
при |
|||||
ли |
об/мин. |
осадки, мм |
сварки, с |
||||
|
мм |
|
греве |
осадке |
|
|
|
20Х |
12 |
3000 |
39,2 |
39,2 |
4 |
4 |
|
25Г2С |
22 |
1500 |
44,1 |
44,1 |
4 |
10 |
|
30ХГСА |
10 |
1500 |
98 |
98 |
4 |
2 |
|
38ХМЮА |
10 |
1500 |
98 |
98 |
4 |
2 |
|
40Х |
15 |
1260 |
29,4 |
68,6 |
6 |
- |
|
4Х13 |
10 |
1500 |
117 |
117 |
3-4 |
3 |
Диффузионная сварка. Получение диффузионно-сварного соединения с высокими механическими свойствами между деталями с компактным сечением из низколегированных сталей не вызывает затруднений. Контактные поверхности перед сваркой могут быть обработаны, например чистовым точением с последующим обезжириванием. Сварка производится в ва-
кууме около 0,1 Па при температуре 940°С, удельном давлении 16 МПа в течение 5-10 мин.
3.4.3. Сварка среднелегированных сталей
Высокий уровень механических свойств среднелегированных сталей, а также их восприимчивость к закалке обусловливают ряд специфических трудностей, возникающих при сварке.
Первой и наиболее серьёзной трудностью при сварке среднелегированных сталей, особенно с повышенным содержанием углерода и легирующих элементов, является необходимость предупреждения возникновения холодных трещин в околошовной зоне и в металле шва. Во всех случаях для среднелегированных сталей, содержащих свыше 0,15%С, следует предусматривать меры, обеспечивающие повышение стойкости сварных соединений против образования трещин и, прежде всего, подогрев перед сваркой и термообработку конструкции сразу же после завершения сварки. Вероятность трещинообра-
303
зования тем больше, чем больше содержится в стали углерода и легирующих элементов, повышающих восприимчивость стали к закалке, а также чем больше толщина металла.
Второй трудностью сварки среднелегированных сталей является предупреждение возникновения кристаллизационных трещин в металле шва. Методы предупреждения кристаллизационных трещин при сварке среднелегированных сталей мало отличаются от применяющихся при сварке углеродистых сталей. Для этого снижают содержание в шве серы, углерода и других элементов, уменьшающих стойкость металла шва против образования кристаллизационных трещин, и повышают содержание таких элементов, как марганец, хром и др., увеличивающих стойкость металла шва против образования кристаллизационных трещин.
Третья трудность состоит в необходимости получения сварного соединения с механическими свойствами, близкими к свойствам основного металла. Поскольку для повышения стойкости металла шва против образования холодных и кристаллизационных трещин ограничивают содержание в нем углерода и некоторых легирующих элементов, достигнуть равнопрочности с основным металлом в общем случае весьма затруднительно.
Для обеспечения хорошего качества сварных соединений этих сталей используют две группы технологических мероприятий:
-подогрев свариваемых кромок, просушка и прокалка сварочных материалов, применение слабоокислительных или безокислительных флюсов, тщательная очистка поверхности основного металла и сварочной проволоки;
-увеличение числа проходов при сварке, использование легированных сварочных проволок и других способов модификации металла шва, уменьшение погонной энергии сварки (для ограничения роста зерна в околошовной зоне).
Приближённая оценка необходимости и температуры
304
предварительного нагрева (для снижения скорости охлаждения) может быть осуществлена по эквиваленту углерода Сэ. Если при подсчёте эквивалента углерода окажется, что
Сэ≥0,45%, то необходим предварительный подогрев. При сварке металла относительно небольшой толщины (до 6-8 мм) и сварных узлов небольшой жёсткости предельные значения Сэ, при которых нет необходимости в подогреве, могут быть повышены до 0,55%.
Увеличение степени легирования при повышенном содержании углерода повышает устойчивость аустенита, и практически при всех скоростях охлаждения околошовной зоны, обеспечивающих удовлетворительное формирование шва, распад аустенита происходит в мартенситной области. Поэтому такие стали, как правило, сваривают без предварительного подогрева, но с использованием специальных технологических приёмов: сварка каскадом, блоками, короткими или средней длины участками, а также путём использования специальных устройств, подогревающих выполненный шов и тем самым увеличивающих время пребывания его в определённом температурном интервале.
Сварка покрытыми электродами. Для сварки среднеле-
гированных сталей выбирают электроды в зависимости от прочности и химического состава свариваемой стали. При этом нужно учитывать, что легирование металла шва происходит не только за счёт наплавленного металла, но и за счёт перехода легирующих элементов из основного металла в шов, что приводит к повышению его прочности и одновременно снижению пластичности. Поэтому, как правило, выбирают такие электроды, которые содержат меньше легирующих элементов, чем основной металл.
При сварке без предварительного подогрева можно использовать аустенитные электроды, но при этом регламентируется время с момента окончания сварки до проведения термообработки изделия. Если сваривают среднелегированные стали
305
с относительно невысоким содержанием углерода (0,12- 0,17%), то последующую термообработку проводят в редких случаях. Разделку заполняют каскадом или горкой.
Если требуется термообработка (отпуск) сваренного изделия, но она не может быть выполнена (например, из-за крупных размеров), то на кромки деталей, подлежащих сварке, наплавляют аустенитными или низкоуглеродистыми электродами незакаливающийся слой металла. Детали с наплавленными кромками сваривают аустенитными или низкоуглеродистыми (и с низким содержанием водорода) электродами без подогрева и последующей термообработки.
Режимы сварки выбирают в зависимости от толщины металла в соответствии с паспортом электрода.
Сварка под флюсом. При изготовлении конструкций из среднелегированных сталей толщиной 4 - 50 мм из всех механизированных процессов сварка под флюсом находит наибольшее применение. В отдельных случаях под флюсом сваривают и более тонкий, и более толстый металл.
При сварке под слоем флюса швы имеют повышенную склонность к образованию горячих трещин. Это связано с увеличением доли основного металла в металле шва, так как в сварочную ванну с расплавленным металлом поступают легирующие элементы, содержащиеся в основном металле, в том числе и углерод. Поэтому при сварке под флюсом необходимы подготовка кромок, техника и режимы сварки, при которых доля основного металла в шве будет минимальной.
В зависимости от состава и назначения свариваемой стали и требований, предъявляемых к сварным соединениям, используют низкоуглеродистую проволоку Св-08А и легированные проволоки, например Св-10ГН, Св-08ГСМТ, Св-18ХГС, Св-08ХМФА, Св-08Х21Н10Г6, Св-08Х20Н9Г7Т и др.
При использовании электродной низкоуглеродистой проволоки или низколегированной, не содержащей достаточное количество элементов-раскислителей, сварку выполняют под
306
кислыми высокоили среднемарганцовистыми флюсами, например АН-348-А, ОСЦ-45.
При сварке низколегированными проволоками, содержащими раскислители в достаточном количестве, применяют низкокремнистые, низкомарганцовистые флюсы, такие, как АН-15, АН-23.
При использовании высоколегированных аустенитных проволок сварку выполняют только под слабо окислительными или безокислительными флюсами, например АН-20
Этим способом можно сваривать стали толщиной до 25 мм без разделки кромок с двух сторон: сварочный ток – 850900 А, напряжение дуги – 38-42 В, скорость сварки – 18 м/ч.
Сварку под флюсом элементов больших толщин осуществляют с увеличенным числом проходов; для повышения сопротивления сварного соединения образованию холодных трещин многослойную сварку деталей толщиной свыше 40 мм можно выполнять с «мягкой прослойкой», для чего первые слои выполняют сварочной проволокой марки Св-08ГА.
Сварные соединения, особенно больших толщин или жёстких конструкций, непосредственно после сварки рекомендуется подогревать в течение 1 часа, не давая шву и околошовной
зоне остывать ниже температуры 200°С.
Сварка в защитных газах находит широкое применение при изготовлении конструкций из среднелегированных сталей. К технологическим особенностям сварки среднелегированных сталей в защитных газах следует отнести тщательную осушку газа с целью предельного снижения содержания водорода в металле шва, а также использование режимов сварки, обеспечивающих пониженные скорости остывания сварных соединений. Эти меры необходимы для повышения стойкости сварных соединений против образования трещин.
Среднелегированные высокопрочные стали в большинстве случаев сваривают в инертных газах или их смесях с активными газами (фагоне).
307
Марка присадочной или электродной проволоки выбирается в зависимости от состава и свойств свариваемых сталей. Так, при сварке молибденовых, хромомолибденовых и хромомолибденованадиевых сталей следует использовать проволоки, содержащие эти элементы, например, Св-08ХМ, Св-08ХМФА и др. При сварке в углекислом газе в составе проволоки обязательно, кроме других легирующих элементов, должны присутствовать раскислители – кремний, марганец, а иногда и титан – Св-08ГСМТ, Св-08ХГСМА, СВ-ХГСМФА и др.
При сварке среднелегированных высокопрочных сталей используют низкоуглеродистые легированные и аустенитные высоколегированные проволоки, например Св-10ХГСН2МТ, Св-03ХГН3МД, Св-08Х20Н9Г7Т, Св-Х21Н10Г6 и др. Однако при этом равнопрочности металла шва и свариваемой стали получить не удаётся.
Получить агрегатную равнопрочность сварного соединения и основного металла можно за счёт эффекта контактного упрочнения мягкого металла шва. В наиболее полной степени эффект контактного упрочнения может быть реализован при применении так называемой щелевой разделки, представляющей собой стыковые бесскосные соединения с относительно узким зазором.
Техника полуавтоматической сварки в среде защитных газов позволяет вести процесс сварки короткими и средней длины участками (каскадом, горкой), сокращать до минимума перерыв между наложением слоёв многослойного шва, регулируя термический цикл сварки и тем самым добиваясь наиболее благоприятных структур в околошовной зоне.
При автоматической сварке этого эффекта добиваются применением двухили многодуговой сварки дугами, горящими в разных плавильных пространствах таким образом, чтобы тепловое воздействие от выполнения последующего слоя на ОШЗ предыдущего происходило при необходимой температуре.
308
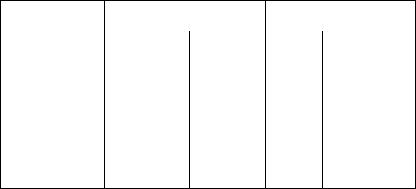
Ориентировочные режимы ручной сварки вольфрамовым электродом среднелегированных сталей приведены в табл.3.30.
Таблица 3.30 Режимы ручной сварки вольфрамовым электродом сред-
нелегированных сталей
|
Стыковое соединение |
Соединение с |
|||
Толщина метал- |
отбортовкой |
||||
|
|
||||
ла, мм |
Iсв, А |
Расход ар- |
Iсв, А |
Расход аргона, |
|
|
гона, л/мин. |
л/мин. |
|||
1,0 |
40-70 |
3,5-4,0 |
35-60 |
3,5-4,0 |
|
1,5 |
50-85 |
4-5 |
45-80 |
4-5 |
|
2,0 |
80-130 |
5-6 |
75-120 |
5-6 |
|
3,0 |
120-160 |
6-7 |
100-140 |
6-7 |
|
4,0 (V- образная |
|
|
- |
|
|
разделка): |
|
|
- |
||
|
|
|
|||
1 – проход |
60-90 |
5-6 |
|
||
|
|
||||
2 - проход |
60-90 |
5-6 |
|
|
Процесс полуавтоматической сварки неплавящимся электродом в аргоне перспективен для изделий с криволинейными и короткими швами. Ориентировочные режимы сварки приведены в табл. 3.31.
Таблица 3.31 Режимы полуавтоматической сварки среднелегирован-
ных сталей неплавящимся электродом в аргоне.
Тол- |
|
Диаметр, мм |
|
|
|
|
|
Рас- |
|
щина |
Подготов- |
|
|
|
|
|
Vпп, |
Vсв, |
ход |
садочной |
|
|
Iсв, А |
Uсв, В |
|||||
ме- |
элек- |
|
арго- |
||||||
талла, |
ка кромок |
прово- |
трода |
|
|
|
м/ч. |
м/ч |
на, |
мм |
|
локи |
|
|
|
|
|
л/мин |
|
0,8 |
Без раз- |
1,0 |
1,5 |
|
60-70 |
9-10 |
30-35 |
30-35 |
5-6 |
делки |
|
||||||||
|
|
|
|
|
|
|
|
|
|
1,0 |
То же |
1,6 |
1,5 |
|
70-80 |
10-11 |
20-23 |
20-23 |
5-6 |
1,5 |
То же |
1,6 |
2,0 |
|
135-150 |
10-11 |
30-32 |
30-32 |
6-7 |
2,0 |
Скос кро- |
2,0 |
2,0 |
|
180 |
10-12 |
25-26 |
25-26 |
6-7 |
мок, 40° |
|
||||||||
3,0 |
То же |
2,0 |
2,5 |
|
190-200 |
10-12 |
16-18 |
16-18 |
7-9 |
4,0 |
То же |
2,0 |
3,0 |
|
190-200 |
10-12 |
12-13 |
12-13 |
7-9 |
|
|
|
|
309 |
|
|
|
|
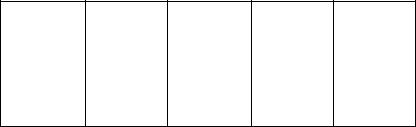
Ориентировочные режимы автоматической сварки среднелегированных сталей в среде аргона приведены в табл.3.32. Сварка ведётся на прямой полярности, напряжение на дуге 11-
13 В.
Таблица 3.32 Режимы автоматической сварки среднелегированных
сталей в среде аргона
|
|
Диаметр при- |
|
|
|
Толщина ме- |
Iсв, А |
садочной |
Vпп, м/ч. |
Vсв, м/ч. |
|
талла, мм |
проволоки, |
||||
|
|
|
|||
|
|
мм |
|
|
|
1,0 |
65-80 |
- |
40-50 |
36-45 |
|
1,5 |
90-110 |
0,8-1,0 |
45-55 |
-//- |
|
2,0 |
100-120 |
-//- |
55-57 |
-//- |
|
3,0 |
130-150 |
-//- |
57-65 |
-//- |
Электрошлаковой сваркой целесообразно выполнять сварные соединения конструкций большой толщины. Наряду с высокой производительностью и экономичностью сварочных работ, при этом обеспечивается и высокое качество сварных соединений, главным образом благодаря высокой стойкости металла околошовной зоны и шва против образования трещин.
Однако при неблагоприятных условиях при электрошлаковой сварке могут возникать кристаллизационные трещины в металле шва, а также горячие и холодные трещины в околошовной зоне. Трещины-отколы возникают через несколько часов по окончании сварки преимущественно в начале шва, особенно после возобновления прерванного процесса сварки, а также при большой жесткости соединяемых элементов. Их образование можно предотвратить, если соединения сразу же после сварки подвергнуть высокому отпуску. Способствует предупреждению образования трещин и некоторое замедление процесса сварки, достигаемое путем уменьшения силы сварочного тока и увеличения ширины шва. Для упрочнения и удешевления изготовления сварных конструкций используют местную термообработку.
310

Для ЭШС среднелегированных сталей применяют флюсы марок АН-8, АН-22 и др. Флюс мало влияет на состав металла шва, но в случае необходимости легирования шва элементами, обладающими большим сродством к кислороду (Al,Ti) следует применять флюсы на основе фторидов или систем CaF2-CaO-
Al2O3.
Электродные проволоки в зависимости от состава свариваемой стали и требований, предъявляемым к шву, выбирают из числа легированных и высоколегированных проволок, например: Св-08ХГ2С, Св-08ГСМТ, Св-18ХМА и др.
Типичные режимы электрошлаковой сварки среднелегированных сталей приведены в табл.3.33.
Таблица 3.33 Режимы электрошлаковой сварки среднелегированных
сталей
Толщина |
Число |
Iсв, А |
Uсв, В |
|
металла, мм |
электродов |
|||
|
|
|||
30-60 |
1 |
400-500 |
40-46 |
|
90-120 |
2 |
То же |
46-50 |
|
150-200 |
3 |
То же |
48-50 |
Электронно-лучевая сварка обеспечивает получение со-
единений с высокой стойкостью против образования холодных трещин, а также минимальной величиной сварочных деформаций. Отмеченные преимущества способа обусловлены высокой концентрацией и большой скоростью нагрева, кинжальной формой проплавления основного металла, большими скоростями кристаллизации и охлаждения сварочной ванны и сварного соединения в целом.
Погонная энергия однопроходной электронно-лучевой сварки в несколько раз меньше, чем при других видах сварки плавлением. Благодаря большим скоростям нагрева и охлаждения в электронно-лучевых соединениях формируется весьма мелкозернистая структура металла шва и предельно ограничиваются перегрев и разупрочнение околошовной зоны. Элек-
311
тронно-лучевая сварка с большой скоростью значительно повышает производительность процесса, в особенности при замене многослойной электродуговой сварки однопроходной электронно-лучевой.
При электронно-лучевой сварке термоупрочненных сталей сварные соединения практически равнопрочны основному металлу, тогда как при аргонодуговой сварке эти соединения имеют значительное разупрочнение. При других способах сварки плавлением таких показателей достичь не удается.
К трудностям электронно-лучевой сварки среднелегированных сталей средних и больших толщин относится чувствительность к повышенному содержанию в основном металле углерода, легирующих элементов и газов, в частности кислорода. Так, например, при сварке сталей толщиной более 30 мм с содержанием более 0,2% С в швах возникают кристаллизационные трещины. Если содержание кислорода в стали превышает 0,02%, электронно-лучевая сварка становится практически невозможной из-за повышенного разбрызгивания жидкого металла и образования пор в шве. В то же время при сварке сталей толщиной до 25 мм при соответствующем выборе режима сварки обеспечивается качественное соединение без пор и трещин даже при содержании 0,3% С (например, сварка трубчатых узлов из стали ЗОХГСНА).
Контактная сварка, сварка трением и диффузионная сварка среднелегированных сталей практически не отличаются от сварки низколегированных сталей.
3.4.4.Сварка высоколегированных сталей
Кчислу основных трудностей, которые приходится преодолевать при сварке высоколегированных сталей и сплавов, относятся: обеспечение стойкости металла шва и околошовной зоны против образования трещин; обеспечение коррозионной стойкости сварных соединений; получение и сохранение в процессе эксплуатации требуемых свойств сварного соедине-
312
ния; получение плотных швов.
Металл сварных швов у высоколегированных сталей мартенситного и мартенситноферритного классов под действием термического цикла сварки может закаливаться с образованием мартенсита. Это может привести к образованию холодных трещин. Для предупреждения образования холодных трещин рекомендуется использовать сварочные материалы, по химическому составу близкие к основному металлу, и сварку выполнять с предварительным или сопутствующим нагревом
до 200-450°С. Температура подогрева тем выше, чем больше в стали содержание углерода, толщина металла и жёсткость узлов. Обычно не позже, чем через 2 часа после сварки необходим высокий отпуск. Если невозможен подогрев и последующий отпуск, то следует использовать сварочные материалы, дающие в шве хромоникелевый материал аустенитного или ау- стенитно-ферритного класса. В этом случае металл шва будет иметь высокие пластические свойства, но сварное соединение будет неоднородным по структуре, и при этом не достигается равнопрочности соединения.
При сварке аустенитных сталей и сплавов в металле шва
иОШЗ могут возникать горячие трещины. Они могут наблюдаться в виде как мельчайших микронадрывов, так и видимых трещин. Их появление связано с наличием напряжений усадки
иформированием при сварке крупнозернистой структуры, особенно ярко выраженной в многослойных швах, когда кристаллы последующего слоя продолжают кристаллы предыдущего слоя. Повышению стойкости швов способствует ограничение содержания в металле шва вредных примесей и измельчение структуры, для чего в шве достаточно иметь 2-3% пер-
вичного δ- феррита, что обеспечивается легированием шва ферритообразующими элементами (Cr, Ti, Mo, Si и др.). Измельчение структуры швов у высоколегированных сталей достигается использованием для сварки электродов с фтористокальциевым покрытием и фторидных сварочных флюсов. Уме-
313
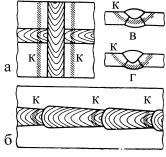
ренные режимы сварки повышают стойкость швов к горячим трещинам.
Обладая высокой коррозионной стойкостью, аустенитные и хромистые стали подвержены опасному виду коррозионного разрушения - межкристаллитной коррозии.
После воздействия на сталь или шов критических температур (500-800°С) выпадают комплексные карбиды железа и хрома. Выпадение этих карбидов влечет за собой обеднение хромом (ниже 10-12%) пограничных слоев зерен или кристаллитов твердого раствора и соответствующую потерю коррозионной стойкости металла
В процессе сварки отдельные участки околошовной зоны подвергаются нагреву до температур, могущих вызвать распад твердого раствора и выпадение карбидов. Впоследствии в этих участках может развиваться межкристаллитная коррозия. Межкристаллитная коррозия может поразить также участки шва, подвергавшиеся повторному воздействию сварочного нагрева, а именно: места пересечения швов (рис. 3.15, а), места возобновления сварки после смены электродов (рис. 3.15, б), первый шов при двусторонней сварке (рис. 3.15, в, г). Этот вид коррозии может наблюдаться и на границе шов - основной металл в виде так называемой ножевой коррозии, охватывающей по ширине всего несколько зерен.
Рис. 3.15. Межкристаллитная коррозия в результате сварочного нагрева: а - при сварке пересекающихся швов; б - при возобновлении сварки после смены электродов; в, г - при двустороннем шве; К - места выпадения карбидов, подверженные коррозии
314
Ножевая коррозия наблюдается преимущественно в сталях, стабилизированных титаном или ниобием.
Известны следующие средства борьбы с межкристаллитной коррозией при сварке высоколегированных сталей и сплавов:
1.Снижение содержания углерода в основном металле и металле шва до 0,02-0,03%.
2.Легирование сталей и швов титаном, ниобием и др. Обладая большим сродством к углероду, чем хром, эти элементы дают устойчивые карбиды. В результате карбиды хрома не образуются, и развитие межкристаллитной коррозии исключается.
3.Закалка от 1050-1100°С. При нагреве под закалку карбиды хрома растворяются в аустените, а быстрое остывание фиксирует однородное строение стали или сплава.
3.Отжиг в течение 2-3 ч. при температуре 850-900°С с охлаждением на воздухе приводит к наиболее полному выпадению карбидов и стабилизации их состава. При последующем воздействии более низких критических температур обеднения хромом вследствие выпадения карбидов не произойдет.
Для предупреждения ножевой коррозии применяют также некоторые технологические приемы, направленные на уменьшение перегрева металла в околошовной зоне. К ним относятся: сварка короткой дугой на максимальных скоростях; сварка очередного валика после полного остывания предыдущего и др. Термообработка сварных изделий далеко не всегда возможна, поэтому наиболее эффективными средствами предупреждения межкристаллитной коррозии являются снижение содержания в стали и шве углерода и легирование их такими энергичными карбидообразующими элементами, как титан и ниобий.
Нержавеющие стали подвержены также коррозионному растрескиванию. Коррозионное растрескивание сварных швов возникает в результате совместного воздействия растягиваю-
315
щих напряжений и агрессивных солей (MgCl, NaCI), некоторых кислот. Основными мерами предупреждения коррозионного растрескивания сварных швов являются: повышение в них содержания никеля более 40% и предупреждение коробления и наклепа сварного изделия, способствующих возникновению растягивающих напряжений в отдельных объемах металла.
Основной причиной образования пор при сварке высоколегированных сталей и сплавов является водород, поступающий в сварочную ванну в основном из сварочных материалов: флюса, присадочной проволоки, электродного покрытия или защитного газа. Эффективное средство предупреждения пор - удаление влаги из флюсов, электродных покрытий и газов. Флюсы и электроды необходимо прокаливать непосредственно перед сваркой, а газ осушать в процессе сварки.
Необходимость получения и сохранения в процессе эксплуатации заданных свойств сварного соединения иногда вызывает значительные трудности. Например, при длительной эксплуатации сварных соединений стали Х18Н10Т при повышенных температурах (500…750°С) происходит падение пластичности швов и основного металла в результате старения. Оно сопровождается выделением по границам зерен вторичных карбидов и интерметаллидов. Для борьбы с этим видом охрупчивания рекомендуется снижение в металле шва содержания углерода и нагрев сварного соединения до температур выше 900°С, при которых происходит распад вторичных карбидов и интерметаллидов.
Технологические особенности сварки высоколегирован-
ных сталей и сплавов заключаются в следующем. Пониженная теплопроводность и высокий коэффициент линейного расширения обусловливают усиленное коробление конструкций и узлов из высоколегированных сталей и сплавов. Поэтому для их сварки применяют режимы, которые характеризуются минимальной концентрацией нагрева. При одной и той же силе
316
тока глубина провара аустенитной стали больше, чем углеродистой. Поэтому для получения заданной глубины провара снижают величину тока на 10-15%.
Высокое удельное электросопротивление рассматриваемых сталей по сравнению с низколегированными требует применения уменьшенных вылетов электродной проволоки при механизированных способах сварки.
Ряд дополнительных специфических требований характерен для коррозионностойких сталей. В частности, при сварке не допускается попадания брызг присадочного металла или металлической ванны на основной металл. В месте приварки брызг обычно образуются очаги межкристаллитной коррозии или коррозионного растрескивания. По этой же причине запрещается возбуждать дугу на основном металле шва. Особое внимание необходимо обращать на крепление сварочного кабеля к свариваемой конструкции. При плохом контакте сталь подгорает, подплавляется, нередко обогащаясь в этом месте медью. Это также потенциальные очаги коррозионного разрушения и межкристаллитной коррозии.
Лучшей коррозионной стойкостью обладают гладкие швы с плавным переходом к основному металлу.
Складки на поверхности шва, углубления между чешуйками, щели или непровары в корне шва при воздействии агрессивной среды могут явиться возможными очагами сосредоточенной и щелевой коррозии. В связи с этим в сварных конструкциях из коррозионностойких сталей, если корень шва соприкасается с агрессивной средой, недопустимы стыковые соединения в замок или на остающейся подкладке. Здесь должно быть отдано предпочтение стыковым соединениям с полным проваром корня шва.
Во избежание коррозии остатки шлаковой корки на поверхности швов и основного металла после сварки должны быть тщательно удалены. Очистка способами, при которых образуются вмятины и забоины, нежелательна. В этих местах
317
может произойти коррозионное растрескивание металла.
При изготовлении изделий из высоколегированных сталей и сплавов применяют все основные виды сварки плавлением: под флюсом, покрытыми электродами, в среде защитных газов, плазменную, контактную, электрошлаковую, электрон- но-лучевую, а также специальные виды сварки: диффузионную в вакууме, сварку трением и др.
Сварка покрытыми электродами. При сварке этим спо-
собом используют постоянный ток обратной полярности. Легирование наплавленного металла обеспечивается за счёт металла электродного стержня. Некоторое дополнительное его легирование осуществляется введением необходимых легирующих компонентов в покрытие электрода.
Электроды для сварки высоколегированных сталей с особыми свойствами должны удовлетворять требованиям ГОСТ 10052-75. Большое разнообразие служебного назначения этих сталей определяет и большой типаж электродов для их сварки. Стандартом предусмотрено 49 типов электродов для сварки хромистых и хромоникелевых сталей, коррозионностойких, жаропрочных и жаростойких высоколегированных сталей мар- тенситно-ферритного, ферритного, аустенитно-ферритного и аустенитного классов.
Выбор марки электрода зависит от марки свариваемой стали и конкретных условий эксплуатации конструкции. Некоторые марки покрытых электродов для сварки высокохромистых сталей приведены в табл.3.34.
Высокое электросопротивление сталей требует применения укороченных электродов и меньшей плотности тока при сварке покрытыми электродами.
Типичные механические свойства металла швов высоколегированных коррозионностойких сталей (при комнатной температуре), выполненных ручной дуговой сваркой покрытыми электродами, приведены в табл.3.35.
318
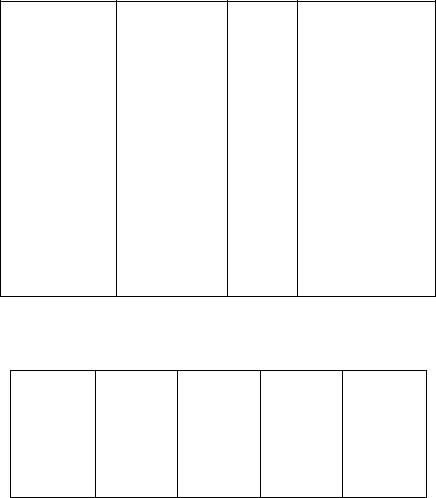
Таблица 3.34 Электроды для сварки высоколегированных сталей
Марка и класс ста- |
|
Марка |
Марка сварочной про- |
|
Тип электрода |
волоки для электрод- |
|||
ли |
|
электрода |
ного стержня |
|
|
|
|
||
Ферритная 08Х13, |
|
|
|
|
мартенситнофер- |
Э12Х13 |
УОНИ |
Св-12Х13 |
|
ритная 12Х12, мар- |
13/1Х13 |
|||
|
|
|||
тенситная 20Х13 |
|
|
|
|
Мартенситные: |
Э12Х11НМФ |
КТИ-9 |
Св-12Х11НМФ |
|
15Х11МФ |
||||
Э14Х11НВМФ |
ЦЛ-32 |
Св-10Х11НВМФ |
||
14Х11В2МФ |
||||
|
|
|
||
Мартенситно- |
|
|
|
|
ферритные: |
Э12Х11НМФ |
КТИ-10 |
Св-10Х11НВМФ |
|
15Х12ВНМФ |
Э08Х19Н10Г2МБ |
|||
18Х12ВМБФ |
|
ЭА-898/12 |
Св-07Х19Н10Б |
|
|
|
|
||
14Х17Н2 |
|
|
|
|
Ферритная |
Э06Х13Н |
ЦЛ-41 |
Св-06Х14 |
|
08Х12НДЛ |
||||
|
|
|
||
Аустенитная |
Х25Н20С3Р1 |
АНВ-31 |
- |
|
20Х25Н20С2 |
(ТУ ИЭС 321-81) |
Таблица 3.35 Механические свойства металла швов высоколегированных коррозионностойких сталей, выполненных ручной дуго-
вой сваркой покрытыми электродами
Марка элек- |
σт, МПа |
σв, МПа |
δ,% |
ан, МДж/м2 |
тродов |
|
|
|
|
ЦЛ-11 |
360 |
600 |
24 |
0,7 |
ОЗЛ-7 |
400 |
640 |
25 |
1,0 |
Л-38М2 |
300 |
600 |
30 |
0,9 |
Л-40М |
350 |
600 |
24 |
0,7 |
СЛ-28 |
- |
600 |
38 |
1,2 |
НЖ-13 |
450 |
600 |
26 |
1,0 |
Сварка под флюсом. Этот вид сварки применяется при изготовлении конструкций из металлов толщиной 5-50 мм, характеризуется высокой производительностью и имеет ряд преимуществ перед ручной сваркой. При сварке под флюсом, как и при других методах механизированной сварки плавлением,
319
можно получать швы практически любой длины без перерывов, резко уменьшается число кратеров. Это имеет большое значение, так как на высоколегированных швах возможность образования кристаллизационных трещин в кратерах значительно выше, чем на углеродистых. Но самое большое значение имеет постоянство условий сварки под флюсом и, как следствие, постоянство химического состава и свойств металла шва. Это очень важно в отношении высоколегированных сталей и сплавов, потому что незначительное изменение химического состава металла шва может привести к образованию в нем кристаллизационных трещин или существенному ухудшению его коррозионных или жаропрочных свойств. Например, повышение в металле аустенитного шва количества углерода на 0,02-0,03% в ряде случаев может привести к потере его коррозионной стойкости, а повышение содержания кремния на 0,2-0,3% может быть причиной образования кристаллизационных трещин и т. д. Сварка под флюсом дает возможность получать гладкие швы практически без чешуек с плавным переходом к основному металлу. Такие швы отличаются более высокой коррозионной стойкостью по сравнению со швами, выполненными вручную. Это еще одно немаловажное преимущество сварки под флюсом перед всеми видами ручной сварки. Поскольку для предупреждения образования горячих трещин сварку желательно выполнять швами небольшого сечения, рекомендуется использовать электродную проволоку диаметром 2-5 мм. Из-за повышенного электросопротивления и, как следствие, нагрева электрода его вылет уменьшают в 1,5-2 раза по сравнению со сваркой низколегированных сталей. Ориентировочные значения сварочного тока и напряжения дуги при сварке под флюсом приведены в табл. 3.36.
При сварке используют фторидные флюсы и флюсы, содержащие прочные оксиды: АНФ-5 (75-80% CaF2, 17-25% NaF); АНФ-6 (70% CaF2, 30% Al2O3); АНФ-7 (80% CaF2,20% CaO), 48-ОФ-6 (52,5% CaF2; 23,5% Al2O3; 19,5% CaO; до 4%
320
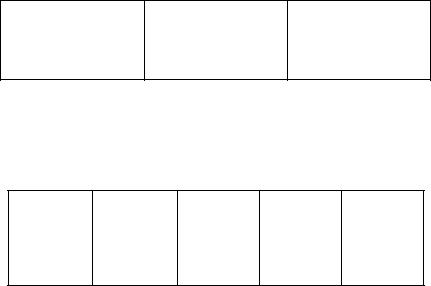
SiO2, до 0,3% MnO). Оксиды кремния и марганца содержатся в качестве примесей, попавших из сырьевых материалов. Для сварки высоколегированных сталей разработано несколько типов керамических флюсов на основе: фторида кальция и Al2O3;
CaO-CaF2-TiO2; MgO-TiO2-Al2O3-CaF2.
Таблица 3.36 Значения сварочного тока и напряжения дуги при сварке
под флюсом высоколегированных сталей.
диаметр электродной |
Iсв, А |
Uд, В |
|
проволоки, мм |
|||
|
|
||
2 |
180-300 |
26-30 |
|
3 |
250-350 |
28-35 |
|
4 |
35-450 |
30-36 |
Ориентировочные режимы автоматической сварки под флюсом аустенитной стали 12Х18Н9Т без разделки кромок приведены в качестве примера в табл. 3.37.
Таблица 3.37 Режимы автоматической сварки под флюсом аустенитной
стали без разделки кромок
Толщина ме- |
Зазор между |
Iсв, А |
Uд, В |
Vсв, м/ч. |
|
талла, мм |
кромками, мм |
||||
|
|
|
|||
6 |
1,5-2 |
650-700 |
34-38 |
47 |
|
8 |
2-3 |
750-800 |
36-38 |
40 |
|
10 |
2,5-3,5 |
750-900 |
38-40 |
32 |
|
12 |
3-4 |
900 |
38-40 |
25 |
Дуговая сварка в защитных газах широко распростране-
на в производстве сварных конструкций из высоколегированных сталей и сплавов. Благоприятной особенностью аргоно- и гелиеводуговой сварки является стабильность дуги, высокое качество сварных швов, обусловленное хорошей защитой зоны сварки от воздуха, и, что особенно важно, возможность наложения швов, занимающих произвольное положение в пр о- странстве. При аргонодуговой сварке защита дуги и сварочной ванны от воздуха более надежна, чем в случае использования гелия, так как аргон тяжелее воздуха.
Аргонодуговую сварку высоколегированных сталей и
321