
Методическое пособие 592
.pdf
Рис. 6.6. Диаграмма предельных напряжений
6.3. Концентрация напряжений
Концентраторы напряжений. Замечено, что во многих случаях детали, имеющие определенную конструктивную форму и качество поверхности, обладают меньшим пределом выносливости, чем образцы из такого же материала. Объясняется это влиянием местных резких изменений внутренних сил упругости в материале , называемых концентрацией напряжений.
Причинами появления концентрации напряжений являются резкие изменения формы детали, внутренние металлургические дефекты материала (инородные включения и раковины, образовавшиеся при формировании исходных слитков), технологические дефекты вследствие обработки, а так же случайные надрезы и царапины на поверхности детали. Указанные причины называются концентраторами напряжений. Формулы для определения номинальных напряжений, полученные при исследовании простых деформаций (растяжение, сжатие, сдвиг, изгиб, кручение), оказываются непригодными для определения напряжений, вызванных концентраторами (такие напряжения называют местными). Местные напряжения могут быть определены общими методами теории упругости или экспериментально.
Теоретический коэффициент концентрации. Концентрация напряжений оценивается теоретическим коэффициентом концентрации k , представляющим собой отношение
наибольшего местного напряжения к номинальному. Номинальным напряжением называется напряжение, вычисленное по формулам сопротивления материалов без учета концентрации. Так, в образце с надрезом (рис. 6.7), подверженном действию растягивающих центральных сил Р, напряжение по сечению m - m, площадь которого Fm , распределяется неравномерно:
наибольшее значение его |
max |
в зависимости от формы надреза в большей или меньшей |
|
|
|
|
|
степени превышает номинальное |
n |
определяемое по формуле: |
|
|
|
|
|
|
|
|
61 |

|
|
|
|
P |
. |
|
|
|
|
n |
|
|
|
|
|
||
|
|
Fm |
|
|
||||
|
|
|
|
|
|
|||
Теоретический коэффициент концентрации: |
|
|
|
|
|
|
||
|
|
|
max |
. |
|
(6.7) |
||
|
K |
|
|
|||||
|
|
|
|
|
|
|
||
|
|
|
n |
|
|
|||
Для касательных напряжений K |
max / n . |
|
|
|
|
|
|
|
При напряжениях, постоянных |
во времени, коэффициент |
K |
достаточно хорошо |
|||||
|
|
|
|
|
|
|
|
характеризует прочность детали, изготовленной из хрупкого материала однородной структуры |
|
(например, из инструментальной стали). При достижении местными напряжениями |
max |
|
|
величины, равной B , произойдет разрушение детали. |
|
Рис. 6.7. Концентрация напряжений при растяжении образца с надрезами
Эффективный коэффициент концентрации. Для деталей, изготовленных из пластичных материалов, влияние концентрации напряжений при постоянной нагрузке оказывается
меньшим, чем это определяется коэффициентом |
K . В этом случае, после того как напряжения |
|
max |
достигнут предела текучести, рост их |
прекращается. Дополнительная нагрузка |
|
|
воспринимается средними волокнами, напряжения в них растут. Процесс роста напряжений в средних волокнах продолжается до тех пор, пока не прекратится течение материала в крайних волокнах ( в точках m). Только после этого возобновляется рост напряжений в крайних
волокнах до величины |
B |
и происходит разрушение детали. Таким образом, на стадии, близкой |
|
|
к разрушению, у образца из пластичного материала по сечению с надрезом распределение напряжений оказывается более равномерным. В этом случае влияние концентрации оценивается эффективным коэффициентом концентрации при напряжениях K 1 меньшим, чем коэффициент
K . Для весьма пластичных материалов (малоуглеродистая сталь, красная медь) коэффициент K 1 принимается равным единице и эффект концентрации при статической нагрузке не
учитывается.
При расчетах на циклическую прочность концентрация напряжений характеризуется эффективным коэффициентом концентрации при циклических напряжениях:
62

|
K |
1 |
, |
(6.8) |
|
1K |
|||
|
|
|
|
|
где |
1 - предел выносливости гладкого образца диаметром d; |
1K - предел выносливости |
||
образца с надрезом того же диаметра в надрезанном сечении. |
|
|||
Как |
правило, эффективный коэффициент |
концентрации меньше теоретического. Это |
объясняется относительным уменьшением пика напряжений в зоне наибольшего влияния пластических деформаций, которые развиваются в слоях металла, расположенного под основанием надреза. Определенную роль играет упрочнение материала в процессе циклического нагружения.
Некоторые типичные концентраторы напряжений приведены на рис. 6.8. Эффективный
коэффициент |
концентрации для приведенных примеров зависит |
от вида |
деформации |
||||
(растяжение, |
изгиб, |
кручение) |
и |
от |
соотношения |
между |
параметрами |
D,d,R,t, ,h, h1 ,b.(Подробные данные приведены в справочнике 6,т.1]). |
|
|
а |
б |
в |
г |
д |
е |
Рис. 6.8. Конструктивные концентраторы напряжений:
а – ступенчатый переход; б – эллиптическая галтель; в – кольцевая выточка; г – поперечное отверстие; д – шпоночный паз; е – внутренний угол
6.4. Факторы, влияющие на прочность при переменных напряжениях
Причины, определяющие циклическую прочность. Циклическая прочность материалов определяется рядом факторов, главнейшим из которых являются: форма и размеры детали, состав и структура материала, влияние остаточных напряжений, способ приложения нагрузки (частота нагружения, перегрузки, паузы), влияние окружающей среды (температура, коррозионные свойства среды).
63
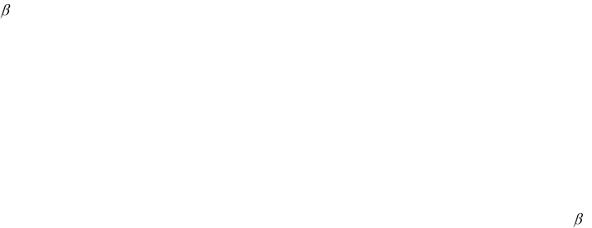
Исследование влияния этих факторов (и многих других) на выносливость производится на специальных установках имитирующих реальные условия работы деталей.
Форма детали. Как указывалось выше, резкие изменения поперечного сечения приводят к концентрации напряжений. Поэтому при конструировании деталей нужно избегать резких ступенчатых переходов, а при необходимости изменения сечения переходы выполнять с помощью галтелей больших радиусов R (рис. 6.8,а, е). С целью уменьшения концентрации напряжений галтели выполняют по соответствующим кривым, например по дуге эллипса, параболы или гиперболы (рис. 6.8, б).
Качество поверхности. Дефекты поверхностных слоев деталей, испытывающих чаще всего наибольшие напряжения, являются источниками концентрации напряжений. Предел выносливости может быть увеличен в несколько раз за счет уменьшения шероховатости поверхности данной детали. Известно, например, что острая царапина глубиной 0,1 мм, нанесенная абразивом, приводит к снижению предела выносливости на 40 %.
Чувствительность разных материалов к влиянию шероховатости поверхности неодинакова. Высококачественные стали более чувствительны, чем менее качественные. Относительно малой чувствительностью к влиянию шероховатости поверхности обладает чугун. Степень влияния качества поверхности на выносливость зависит также от вида деформации испытываемых деталей (большее влияние проявляется при изгибе, меньшее при растяжении - сжатии).
Влияние качества поверхности оценивается коэффициентом качества поверхности детали П , который представляет собой отношение предела выносливости образца, имеющего такое
же качество поверхности, как и у рассчитываемой детали , к пределу выносливости образца с полированной поверхностью.
Размеры детали. При увеличении размеров образца или детали предел выносливости снижается. При этом эффективный коэффициент концентрации увеличивается и приближается к значению теоретического коэффициента концентрации напряжений.
Понижение циклической выносливости с увеличением размеров детали объясняется тем, что при больших размерах увеличивается вероятность появления металлургических дефектов, являющихся концентраторами напряжений, а так же дефектов в поверхностном слое, обычно наиболее напряженном.
Влияние размеров детали на прочность оценивается коэффициентом размера M , который
представляет собой отношение предела выносливости детали заданных размеров к пределу выносливости образца диаметром 7,5 мм.
Частота нагружений. Скорость изменения напряжений мало влияет на величину предела выносливости. Некоторое повышение предела выносливости наблюдается при увеличении частоты нагружений выше 1000 циклов в секунду. Перерывы нагружения (паузы) повышают предел выносливости, однако это повышение не велико (не более чем на 10-15 %) и тем больше, чем чаще и продолжительнее перерывы в нагружении.
Влияние температуры. С увеличением температуры предел выносливости уменьшается. Это важно учитывать при расчете деталей, работающих при повторно - переменных нагрузках в условиях высоких температур (лопатки паровых и газовых турбин, клапаны двигателей внутреннего сгорания и т.д.). Например, для стали 30ХМ увеличение температуры от 20 до 5000 C снижает предел выносливости на 22 %.
64

Влияние коррозионной среды. Многие детали машин и приборов работают в условиях речной, грунтовой и морской вод, электролитов, газов и т.п. которые вызывают коррозию. При работе детали в коррозионной среде не существует абсолютного предела выносливости и устанавливается лишь условный предел выносливости, величина которого ниже прела выносливости некоррозионной среды. В более агрессивных средах (морская вода, электролиты и т.п.) наблюдается значительное снижение предела выносливости.
6.5. Расчет на прочность при переменных напряжениях
Уравнение прочности. Выполняя расчет на прочность детали, испытывающей циклические нагрузки, необходимо прежде всего установить значение наибольшего по
абсолютному значению напряжения, нормального |
max или касательного |
max . |
|||||
|
Далее на основании имеющихся сведений определяется значение предела выносливости |
||||||
R |
при данном коэффициенте асимметрии цикла |
R . |
Предел выносливости определяется с |
||||
|
|
|
|
|
|
|
|
учетом всех факторов, влияющих на его значение. |
|
|
|
|
|
||
|
В результате расчетное уравнение принимает вид: |
|
|
||||
|
|
|
|
R |
|
, |
(6.9) |
|
max |
max |
|
n |
|||
|
|
|
|
||||
|
|
|
|
|
|
где n - коэффициент запаса прочности по нормальным напряжениям.
Аналогично вводятся коэффициенты запаса по касательным напряжениям n и при сложном нагружении n.
Коэффициент запаса прочности. Для определения коэффициента запаса воспользуемся линейной схематизированной диаграммой предельных напряжений (рис.6.9). На этой диаграмме точка M соответствует максимальному напряжению данного цикла, а точка N - пределу выносливости при таком же значении R. В соответствии с данными рис.6.9 и выражением (6.9) :
R |
max n |
( m |
|
|
a )n |
|
|
m n |
a n . |
(6.10) |
|||
Уравнение предельной прямой АВ диаграммы может быть представлено в виде уравнения |
|||||||||||||
прямой в отрезках: |
|
|
|
|
|
|
|
|
|
|
|
|
|
|
|
m n |
|
|
|
a n |
|
1. |
|
|
|
(6.11) |
|
|
|
B |
1 |
|
|
|
|
|
|||||
|
|
|
|
|
|
|
|
|
|||||
На основании выражения (6.11) получим: |
|
|
|
|
|
|
|
|
|
|
|||
|
|
n |
1 |
|
|
|
|
|
|||||
|
|
|
|
|
|
|
|
|
|
|
|
||
|
|
|
|
a |
m |
. |
|
(6.12) |
|||||
|
|
|
|
|
|
|
|||||||
|
|
|
|
|
|
|
|
|
|
|
|||
|
|
|
|
1 |
|
|
B |
|
|
Выражение (6.12) получено без учета влияния концентрации напряжений, размеров и качества поверхности детали. Указанные факторы в большей степени влияют на прочность при переменных напряжениях и в меньшей степени при постоянном напряжении. Учитывая это обстоятельство, коэффициент запаса следует вычислять по выражению
n |
|
|
1 |
|
|
|
, |
(6.13) |
|
|
|
|
|
|
|||||
|
K |
|
|
|
|||||
|
|
|
a |
|
m |
|
|
||
|
|
|
|
|
|
||||
|
|
П М |
1 |
|
B |
|
65

где |
K - эффективный коэффициент концентрации напряжений; |
m - коэффициент |
размера; |
П - коэффициент качества поверхности. |
|
По аналогии при расчете на прочность при действии переменных напряжений в случае, когда деталь находится в условиях чистого сдвига, коэффициент запаса определяется по выражению:
n |
|
|
1 |
|
|
|
. |
(6.14) |
|
|
|
|
|
||||||
|
|
ф |
|
||||||
|
|
K |
|
|
m |
|
|
||
|
|
П М |
1 |
|
B |
|
Все рассмотренные выше вопросы циклической прочности относились к случаю линейного напряженного состояния. При совместном действии нормальных и касательных напряжений применяется эмпирическая формула:
|
1 |
|
1 |
|
1 |
|
, |
|
|
(6.15) |
|
n2 |
|
n2 |
|
n2 |
|
|
|||
|
|
|
|
|
|
|
||||
где n - искомый коэффициент усталостной прочности; |
n - |
коэффициент |
запаса |
|||||||
усталостной прочности в предположении, что касательные напряжения |
отсутствуют; n - |
коэффициент запаса по касательным напряжениям, установленный в предположении, что
0 .
Рис. 6.9. К определению запаса прочности при переменных напряжениях
Допускаемое напряжение. Найдем допускаемое напряжение в случае растяжения - сжатия и изгиба. По определению в соответствии с формулой (6.10) при требуемом коэффициенте
запаса прочности n |
: |
|
|
|
|
|
|
|
|
|
|
|
R |
|
a |
|
|
m |
m . |
(6.16) |
|
|
R |
n |
|
n |
|
n |
|
a |
||
|
|
|
|
|
|
|
|
66

На основании формулы (6.13) выражения для допускаемых амплитудного и среднего напряжений запишутся в виде:
|
|
|
|
|
|
|
|
|
|
|
1 |
|
|
|
|
; |
|
|
|
|
|
|
|
|
a |
|
n |
|
(K Д |
|
|
) |
|
||||
|
|
|
|
|
|
|
|
|
|
|
|
|||||||
|
|
|
|
|
|
|
|
|
|
|
|
|
|
|||||
|
|
|
|
|
|
|
|
|
|
|
1 |
|
|
, |
|
|||
|
|
|
|
|
|
m |
|
n |
|
(K Д |
|
|
) |
|
||||
|
|
|
|
|
|
|
|
|
|
|
|
|
||||||
|
|
|
|
|
|
|
|
|
|
|
|
|
|
|
||||
где |
- характеристика |
цикла; |
K Д |
|
|
К |
|
- |
коэффициент |
снижения предела |
||||||||
|
|
|
|
|||||||||||||||
|
|
П |
М |
|||||||||||||||
|
|
|
|
|
|
|
|
|
|
|
|
|
|
|
|
|
||
выносливости; |
1 / |
В . |
|
|
|
|
|
|
|
|
|
|
|
|
|
|
|
|
Подставляя значения |
а |
и |
m |
|
в формулу (6.16) получаем: |
|
||||||||||||
|
|
|
|
|
|
|
|
|
|
|
|
|
|
|
|
|
||
|
|
|
|
|
|
|
|
|
|
1 ( |
|
1) |
|
. |
|
|
(6.17) |
|
|
|
|
|
|
R |
|
n |
|
(K Д |
|
) |
|
|
|||||
|
|
|
|
|
|
|
|
|
|
|
|
|||||||
|
|
|
|
|
|
|
|
|
|
|
|
|
||||||
Ориентировочные значения коэффициентов |
|
M |
и |
П |
приведены на графиках (рис. 6.10 и |
|||||||||||||
|
|
|
|
|
|
|
|
|
|
|
|
|
|
|
|
|
||
6.11). |
|
|
|
|
|
|
|
|
|
|
|
|
|
|
|
|
|
|
|
Рис. 6.10. Графики изменения коэффициента, учитывающего размеры детали из стали: |
|
|
|
1 – углеродистой при отсутствии местных напряжений; 2 – легированной |
( |
в |
1000 1200МПа ) при отсутствии концентрации напряжений и углеродистой при |
|
|
умеренной концентрации; 3 – легированной при наличии концентрации напряжений; 4 - имеющей высокую степень концентрации напряжений
67

Рис. 6.11. Графики изменения коэффициента, учитывающего состояние поверхностных слоев образцов:
1 – полированные; 2 – шлифованные; 3 – обработанные резцом; 4 – с мелкой насечкой;5 – после проката; 6 – корродированны в пресной воде; 7- корродированны в морской воде
68
Глава 7. ТРЕБОВАНИЯ, ПРЕДЪЯВЛЯЕМЫЕ К МЕХАНИЗМАМ
7.1. Факторы, определяющие работоспособность механизмов и их деталей
Качество механизма. Качеством механизма называется совокупность свойств, определяющих степень пригодности использования его по назначению. Механизм должен удовлетворять требованиям, указываемым в техническом задании на проектирование. В общем случае качество конструкции механизма определяется: а) простотой конструкции; б) технологичностью; в) экономичностью (высоким КПД); г) размерами и массой; д) надежностью и долговечностью.
Технологичность конструкции механизма определяется удобством изготовления и сборки его деталей, а также степенью использования стандартизованных и унифицированных деталей и сборочных единиц.
Изготовление простых деталей менее трудоемко, не требует специального сложного оборудования и инструмента.
Важнейшим показателем эксплуатационного качества механизма является надежность, которая характеризуется вероятностью безотказной работы с необходимой точностью на протяжении заданного времени и в заданных условиях эксплуатации, а также необходимой прочностью деталей, рациональной жесткостью, износостойкостью, виброустойчивостью, теплостойкостью.
Прочность. Поломки и большие остаточные деформации деталей из-за их недостаточной прочности могут стать причинами отказа в работе и потери точности механизма. Опасные напряжения в деталях, приводящие к разрушению, могут возникнуть не только от рабочих усилий, но и от сил, обусловленных вибрацией, тряской при эксплуатации (например, в авиационных приборах) и транспортировке.
Недостаточная объемная прочность деталей механизма чаще всего проявляется сразу, т.е. приводит к явному отказу в работе, в то время как недостаточная поверхностная прочность большей частью является причиной постепенной потери работоспособности. Например, появление выкрашивания рабочих поверхностей в шарикоподшипниках и зубчатых передачах ведет к увеличению потерь на трение, нагреву, повышению динамических нагрузок и износа.
Износостойкость. Работе любого механизма сопутствует изнашивание - процесс постепенного изменения размеров и формы деталей при трении. При скольжении трущихся поверхностей нарушаются фрикционные связи, что сопровождается деформированием, оттеснением материала, срезом внедрившегося материала. Износ может иметь несколько иную природу, когда между соприкасающимися поверхностями попадают твердые частицы (абразивы), царапающие и срезающие частицы металла.
Износ поверхностей подвижно соединенных деталей изменяет характер сопряжения, что приводит к ухудшению условий работы и снижению прочности деталей механизмов.
Жесткость. Деформации деталей механизмов возникают из-за действия сил, изменения температуры, наличия остаточных напряжений и приводят к изменению размеров и формы деталей, характера их сопряжения. Чрезмерные деформации существенно влияют на работоспособность механизма. Так, например, изгиб валов вызывает неравномерный износ, увеличение сил трения и даже заедание в подшипниках скольжения, ухудшает условия работы подшипников качения, является одной из причин неравномерного распределения нагрузки по контактным площадкам кинематических пар.
Теплостойкость. Для нормального функционирования многих машин и приборов необходимо обеспечить определенный температурный режим, т.к. обильное тепловыделение и
69

плохой отвод тепла могут привести к различным неполадкам и неисправностям. Так, при повышении температуры стальных деталей свыше 300-400оС, а деталей из легких сплавов и пластмасс - до 100-150оС наблюдается понижение их нагрузочной способности.
Выделяемое тепло ухудшает свойства применяемых смазок (понижается вязкость), что может привести к повышенному износу или заеданию сопряженных поверхностей.
Даже небольшое изменение температуры деталей механизма вызывает температурные деформации, изменяющие размеры деталей и характер сопряжения в подвижных соединениях. Большая температурная погрешность возникает в приборах с упругими элементами, модуль упругости материала которых зависит от температуры.
Виброустойчивость. Под виброустойчивостью понимают способность механизма работать при воздействии вибраций. Вибрации влияют на силы трения, могут привести к усталостному разрушению детали. Особенно опасно явление резонанса, которое наступает в случае совпадения частот собственных колебаний детали и периодически действующих сил, вызывающих вибрации.
7.2.Материалы
При выборе материалов необходимо учитывать механические, технологические и физикохимические свойства, а также стоимость и дефицитность их. Для изготовления деталей в машиностроении и приборостроении широко применяются чугуны и стали, сплавы цветных металлов, особенно на основе меди и алюминия, а также неметаллы.
Чугуны. Чугунами называются железоуглеродистые сплавы, содержащие больше 2% углерода. Они обладают хорошими литейными свойствами и худшими по сравнению со сталями пластическими свойствами. В зависимости от структуры чугуны делятся на белые, ковкие и серые. Белые чугуны обладают высокой твердостью и хрупкостью, плохо обрабатываются резанием. Ковкие чугуны высокопластичны, хорошо обрабатываются, имеют большую плотность. Стоимость изготовления деталей из этих чугунов на 30-100% превышает стоимость изготовления деталей из серого чугуна.
Серые чугуны (ГОСТ 1412-70) обладают средней прочностью, малой ударной вязкостью, наилучшими литейными свойствами, хорошо обрабатываются резанием и демпфируют колебания, поэтому находят широкое применение.
Стали. В зависимости от содержания углерода стали делятся на низкоуглеродистые (С 0,25%), среднеуглеродистые (С=0,25...0,60%) и высокоуглеродистые (С 0,6%). При малом содержании углерода, стали, обладают высокой пластичность и свариваемостью. С увеличением содержания углерода повышается прочность, уменьшается пластичность и ухудшается свариваемость.
Для улучшения механических свойств сталей применяют легирующие присадки: никель, хром, молибден, вольфрам, титан, марганец, кремний и пр. Введение легирующих примесей увеличивает стоимость стали.
По способу производства различают стали обыкновенного качества, качественные и высококачественные; по применению - стали строительные, конструкционные, инструментальные и с особыми свойствами.
Углеродистые стали обыкновенного качества (группа Б по ГОСТ 380-71) применяются для изготовления корпусных деталей методом штамповки или сварки, а также для изготовления крепежных деталей. Качественные (ГОСТ 1050-74) и легированные стали (ГОСТ 4543-71) применяются для изготовления различных деталей машин: валов, осей, зубчатых колес, червяков, фрикционных катков и т.п.
70