
Модуляторы тока для импульсно-дуговой сварки. Зайцев А.И., Чуриков И.А
.pdfА.И. Зайцев, И.А. Чуриков
МОДУЛЯТОРЫ ТОКА ДЛЯ ИМПУЛЬСНО_ДУГОВОЙ СВАРКИ
Воронеж 2001
3
Введение
Важной задачей в области сварки является активное управление технологическим процессом с целью получения высококачественных соединений, в частности, процессом электрической дуговой сварки плавящимся электродом, которая получила наибольшее распространение.
Вследствие капельного переноса расплавленного электродного металла в сварочную ванну, процесс сварки носит дискретный характер, состоящий из периодически повторяющихся микроциклов. Металлургические реакции в электродном металле протекают в основном на стадии капли. От идентичности протекания микроциклов зависит стабильность формирования шва и свойства наплавленного металла. Однако из-за ряда причин как внутренних, обусловленных физической природой сварочной дуги, так и внешних, случайных: ток, напряжение, длина дугового промежутка, характер переноса электродного металла в процессе сварки значительно изменяется. Это вызывает изменение условий протекания отдельных микропроцессов и, следовательно, изменение свойств сварочного соединения.
Для обеспечения стабильности качества сварных соединений требуется активно управлять процессом сварки на стадии капли. Такие возможности предоставляет способ импульсного управления. Известный способ импульсно-дуговой сварки плавящимся электродом в аргоне, разработанный в И.Э.С. им. Е.О.Патона, обеспечивает активное сокращение времени роста капли и перенос ее строго в сварочную ванну в любом пространственном положении [1]. Перспективным является активное управление не только переносом, но и расплавлением каждой капли электродного металла [2, 81-92]. Для этого должны сохраняться одинаковые параметры энергии (напряжение, ток, длина дуги и время расплавления капли до заданных размеров), идущей на расплавление каждой капли , то есть осуществляется точная дозировка энергии при постоянстве ее параметров.
Способ импульсно-дуговой сварки с управляемым переносом достаточно хорошо разработан и исследован для сварки плавящимся электродом в аргоне. Разработка методов управления
4
переносом металла при сварке в СО2 и порошковой проволокой является актуальной задачей, поскольку они применяются в масштабе.
Как одну из областей применения, можно указать сварку неповоротных стыков магистральных трубопроводов, где необходим строго направленный перенос электродного металла в сварочную ванну, находящуюся в положениях отличных от нижнего при небольшом сварочном токе. Аналогичные задачи стоят при сварке корпусов судов и других сложных металлоконструкций.
Развитие силовой полупроводниковой техники и теории дискретных систем позволяет создавать высокоэффективные системы дискретного управления сварочными процессами.
5
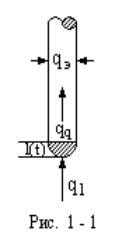
1.Особенности импульсного питания сварочной дуги
сплавящимся электродом
1.1.Анализ факторов, влияющих на плавление и
перенос электродного металла
Важнейшими характеристиками электро-дуговой сварки плавящимся электродом являются плавление и перенос электродного металла через дуговой промежуток. Эти процессы неразрывно связаны и оказывают значительное влияние на устойчивость процесса сварки, разбрызгивание расплавленного металла, формирование шва, а также на интенсивность металлургических реакций между металлом, шлаковой и газовой фазами. От температуры капли и от времени ее нахождения при высокой температуре зависит полнота протекания металлургических реакций. В зависимости от условий сварки мгновенная скорость расплавления и характер переноса сильно меняются.
С точки зрения качества сварных соединений изменение температуры капель в процессе сварки является нежелательным, так как при этом может измениться ход металлургических реак-
ций [3].
Рассмотрим известную простейшую схему передачи тепла сварочной дуги к электроду при сварки плавящимся электродом [4], представленную на рис. 1-1.
В начальный момент после отделения капли вся тепловая мощность дуги q1, идущая на нагрев электрода, выделяется непосредственно на торце электрода и распространяется по нему путем теплопроводности, вызывая его нагрев и плавление. Потерями теплоты через боковую поверхность можно пренебречь [5]. С образованием капли жидкого металла мощность дуги q1, идущая на нагрев электрода, выделяется непосредственно на торце электрода и распространяется по нему путем теплопроводности, вызывая его нагрев и
плавление. Потерями теплоты через боковую поверхность можно пренебречь [5]. С образованием капли жидкого металла условия
6
передачи теплоты дуги электроду ухудшаются, так как часть теплоты будет расходоваться на бесполезный перегрев металла капли, а также на испарение металла с поверхности капли занятой активным пятном, то есть q2 < q1. Поэтому мгновенная скорость роста массы капли будет замедляться по мере увеличения размеров капли до ее отрыва от электрода, после чего процесс повторяется. Это явление отмечено многими исследователями [4,6,7,8]. Между активным пятном и каплей на электроде преобладает конвективная теплопередача [9,10]. Поэтому теплопроводность металла капли мало влияет на условия теплопередачи от дуги к электроду, которые при равных условиях определяются лишь размерами капли.
В соответствии с [4] тепловой баланс плавления электрода может быть представлен в виде:
|
|
|
Таблица 1 |
Приход |
|
Расход |
|
Теплоты |
Плавление |
Испарение ме- |
Перегрев |
дуги Qэ в |
стержня |
талла |
металла в |
% |
Q2 в % |
Q3 в % |
капле Q4 в % |
100 |
50-60 |
20 |
20-30 |
Из таблицы видно, что затраты теплоты на бесполезный перегрев металла капли составляют примерно 50 % теплоты, расходуемой на плавление электрода.
Основная характеристика плавления - скорость расплавления электрода - зависит от состава электродной проволоки и покрытия (флюса, защитного газа), режима сварки, плотности тока и его полярности, вылета электрода, подогреваемого проходящим током и некоторых других факторов [3,4,11,12,13]. Скорость расплавления электрода при всех прочих равных условиях, главным образом, определяется условиями выделения и передачи тепла в анодной и катодной областях и зависит от полярности тока.
Связь между явлениями в дуге и технологическими характеристиками электродов и проволок (с защитой) создает возможности регулирования технологических свойств сва-рочных электродов, которые можно осуществлять двумя путями: электрическими парамет-рами системы питания - внешний способ регули-
7
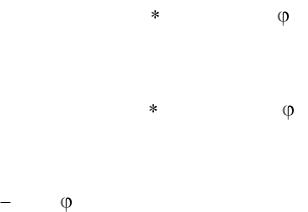
рования; и введением в дугу различных веществ, изменяющих энергетические процессы в ней [3].
Поскольку нас интересует внешнее регулирование, ниже будет проведен анализ влияния энергетических параметров питания на процесс плавления электрода.
1.1.1. Влияние полярности на плавление электрода
Полярность электрода оказывает большое влияние на процесс плавления электрода. Сварочная дуга по тепловому действию может быть представлена как сумма трех источников тепла : анодного , катодного и столба дуги [3]. Согласно такому представлению тепловая энергия, выделяемая непосредственно на катоде равна:
Рк = I [Uк - ( |
3 |
kТ + )] , |
(1-1) |
|
2 |
||||
|
|
|
Энергия, выделяемая на аноде
Pa=I [Ua + ( |
3 |
kT + )] , |
(1-2) |
|
2 |
||||
|
|
|
где Uк, Ua - катодное и анодное падение напряжения; k - постоянная Больцмана;
( 23 kT + ) - энергия, приносимая на анод электронами.
Выражения в квадратных скобках носят название эффективных падений катодного и анодного напряжений и обозначаются соответственно Uкэ и Uaэ , причем Uaэ практически не зависит от состава проволоки, покрытия флюса, состава газовой среды при газоэлектрической сварке, режима сварки [3,10,14] . В отличие от анодного падения напряжения Uкэ изменяется в широких пределах в зависимости от состава и состояния поверхности проволоки, состава покрытия, флюса, защитного газа и прочего [3,15] .
Полярность оказывает значительное влияние на температуру капель электродного металла, по которой можно судить об эффективности использования тепла на расплавление электрода. Температура капель электродного металла в зависимости от условий сварки находится в интервале температур плавления и ки-
8
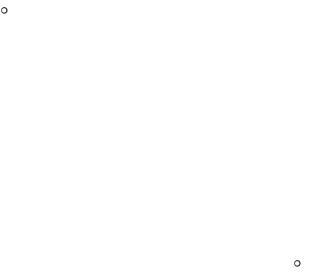
пения. При сварке тонкопокрытыми электродами при всех прочих равных условиях на прямой полярности температура капель на 100-200 С ниже, чем на обратной [4]. Электроды с нормальной толщиной покрытия и с низким номинальным напряжением (МРЗ, УОНИ 13) имеют близкие значения температуры капель на обеих полярностях. Электроды с высоким номинальным напряжением дуги (ВСЦ1, ЦМ7, Флитвелд 5, Шилдарк 85) имеют температуру капель выше на прямой полярности [3] .
При сварке в аргоне плавящимся электродом установлено [16,17,18,19,20], что теплосодержание капель электродного металла на обратной полярности при одинаковых значениях тока и скорости плавления больше, чем на прямой полярности. Разница температур полярности составляет 300-600 С.
Скоростная киносъемка процесса плавления электрода показывает [17], что при обратной полярности анодное пятно находится на торце электрода, то есть на жидком металле капли. Тепло, выделяемое на аноде, передается электроду исключительно через жидкий металл капли. Согласно существующему мнению [17,21,22,23], с ростом величины тока плотность его в анодном пятне не изменяется, а поверхность капли, занимаемая пятном, растет. Ввиду постоянства площади контакта капли с твердым электродом с ростом тока капли перегреваются до температуры кипения [17] и затем температура их не повышается, так как значительное количество тепла расходуется на испарение металла.
Однако, видимо, можно говорить о постоянстве значения плотности тока анодного пятна, рассматривая его статическую модель. В работе [24] показано при помощи скоростной киносъемки, что анодное пятно находится в динамическом равновесии, определяемом процессом каплеобразования. После отрыва капли анодное пятно имеет наибольшую плотность тока. По мере роста капли анодное пятно растет, а плотность тока в нем уменьшается [22]. Однако пятно, стремясь занять стабильное положение и стремясь к установившемуся состоянию, не успевает его достигнуть, так как происходит отрыв капли и процесс повторяется. Таким образом, при сварке на обратной полярности передача тепла дуги осуществляется только через жидкий металл капли.
9
На прямой полярности катодное пятно на электроде беспорядочно движется [3,4,17,25], часто перемещаясь с капли на боковую поверхность электрода. Тепловой поток из дуги в электрод как бы раздваивается. Часть тепла передается проволоке через каплю, остальная часть - непосредственно через боковую поверхность электрода. Перегрев капли уменьшается, ускоряется плавление проволоки. Следовательно, при сварке в инертных газах на прямой полярности тепло дуги расходуется более рационально, то есть термический к.п.д. процесса каплеобразования выше. Однако, вследствие неустойчивого горения дуги и разбрызгивания металла сварка, как правило, ведется на обратной полярности.
При сварке в углекислом газе плавящимся электродом, также как и в инертных газах, теплосодержание капель на прямой полярности значительно ниже, чем на обратной и ниже по абсолютной величине, чем в инертных газах [18].
При сварке порошковой проволокой сохраняются те же закономерности, которые характерны для сварки в защитных газах. При одинаковых плотностях тока теплосодержание капель близко к теплосодержанию капель при сварке в углекислом газе и ниже чем в аргоне, что объясняется [18] значительными затратами энергии дуги на диссоциацию газов воздуха, вызывающую сжатие столба дуги и изменение условий теплопередачи в капле.
1.1.2. Виды переноса и основные факторы, влияющие на него
Важнейшим фактором, влияющим на кинетику роста капли на торце электрода, является характер переноса электродного металла через дуговой промежуток. Различают следующие виды переноса:
1)крупнокапельный с короткими замыканиями,
2)крупнокапельный без коротких замыканий,
3)мелкокапельный без коротких замыканий,
4)струйный мелкокапельный,
5)перенос металла парами, сопутствующий всем видам переноса,
6)неустойчивый.
При рассмотрении переноса обычно делаются следующие
10
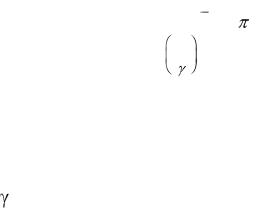
допущения [9,26]:
1)столб дуги неподвижен и соосен с электродом,
2)процессы в столбе дуги стабильны и не изменяются во времени,
3)равнодействующая сил, приложенных к расплавленному металлу электрода, находится под действием сил: силы тяжести, силы поверхностного натяжения, электромагнитной силы, силы реактивного давления паров и ионов, нейтрализовавшихся на катоде, аэродинамической силы, силы давления газов и паров, образующихся внутри капель.
Характер переноса и размеры капель определяются соотношением сил, приведенных выше, которые зависят от режима сварки, материала электродов и газовой среды, состояния поверхности проволоки и ее диаметра, полярности тока.
Сила тяжести во всех случаях постоянна для капель одинаковой массы и оказывает влияние лишь при сварке на малых токах.
Силы поверхностного натяжения удерживают каплю на торце электрода во всех случаях и зависят от природы жидкости, ее температуры и наличия примесей. Примеси значительно снижают поверхностное натяжение железа в жидком состоянии. Наиболее поверхностно активны сера и кислород [18,27,28].
Все сварочные шлаки также значительно снижают поверхностное натяжение [29].
С ростом температуры капли поверхностное натяжение уменьшается [30,31]. В работе [26] на основе формулы Этвеша получено выражение для оценки поверхностного натяжения:
P = |
4,2(Ткр Т ) |
r , |
( 1-3 ) |
||||
|
2 |
|
|||||
пн |
|
э |
|
||||
|
|
М 3 |
|
|
|||
|
|
|
|
|
|
|
|
где Ткр - критическая температура для данного металла; Т - температура расплавленного металла в данный мо-
мент в исследуемой координате;
М- молекулярный вес;
-плотность;
11
rэ - радиус электрода.
Многими исследователями отмечено [9,32,33,34,35,36,4142], что при всех прочих равных условиях важнейшим фактором, определяющим характер переноса, является величина сварочного тока. Это связано с электродинамической силой (пинч-эффект), сжимающей проводник с током, в результате чего появляется равнодействующая сила, отрывающая каплю от электрода. Величина электродинамической силы пропорциональна квадрату величины сварочного тока [37] и ее действие, отрывающее каплю от электрода, проявляется в каждом конкретном случае при величине сварочного тока, большей некоторого критического значения [9]. При изменении сечения проводника (электрод-столб дуги) возникает осевая сила, направленная от меньшего сечения к большему [37]. При ручной дуговой сварке, радиус столба дуги меньше радиуса электрода, поэтому пинч-эффект будет препятствовать отрыву капли. Значение тока, при котором возникает отрывающее каплю действие пинч-эффекта, называют первым критическим током [9]. Эта величина зависит от радиуса электрода и столба дуги. С увеличением тока над первым критическим размер капель будет уменьшаться и при достижении током значения, которое называют вторым критическим, наблюдается резкое уменьшение размеров капель и возрастание числа их. Описанные явления характерны для сварки в аргоне. Кроме того, переносу будет способствовать гидростатическое движение, создаваемое радиальной составляющей плотности тока в жидком металле и столбе дуги. Как известно, в аргоне столб дуги имеет форму конуса, расширяющегося к изделию, благодаря чему в нем из-за разности электромагнитных сил возникают мощные плазменные потоки, выравнивающие давление по оси столба. Под каплей давление газа оказывается меньше, чем в самой капле, и она в форме конуса втягивается в столб дуги. Из торца электрода с большой частотой отделяются капли очень малых размеров, создается впечатление непрерывной струи жидкого металла. Это явление наблюдается на обратной полярности при токах больших второго критического. Сварка электродами с покрытием производится при малых плотностях тока, электромагнитные силы малы и практически не влияют на характер переноса. Однако электроды
12