
Методическое пособие 277
.pdf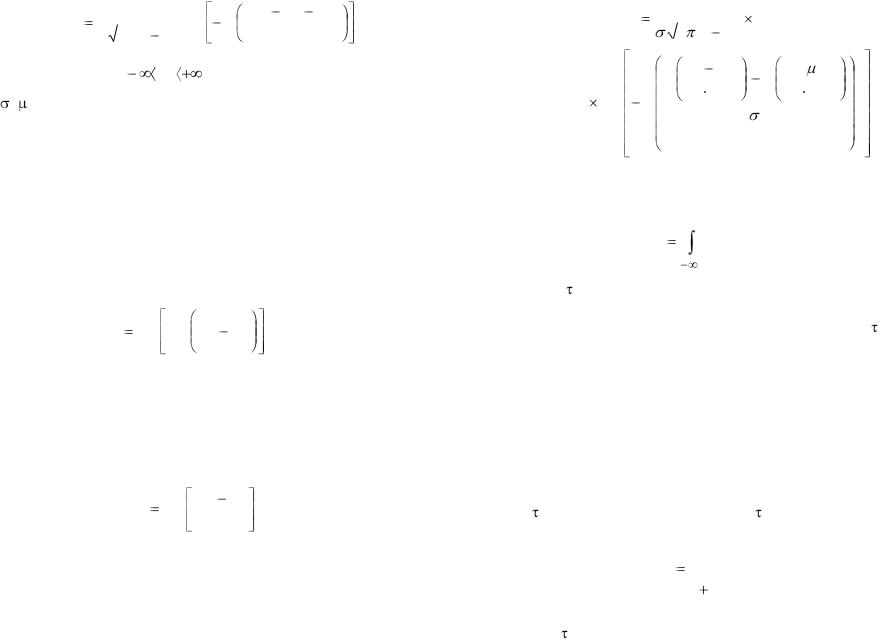
f0 |
(lnt) |
1 |
|
exp |
1 |
|
ln(t |
t0 ) lnμ |
, |
||
|
|
|
|
2 |
|
|
ζ |
||||
|
|
|
|
|
|||||||
|
|
ζ 2π (t |
t0 ) |
|
|
|
|||||
|
|
|
|
|
lnt |
|
|
|
|
(2.8) |
где , и tо – соответственно среднеквадратичное отклонение, среднее и начальное время до отказов.
Величины этих параметров являются функциями качества диэлектрика. Функция плотности отказов является накопленной частотой отказов в данный момент времени.
Наступление времязависимого пробоя может быть ускорено термически и электрически. Коэффициент температурного ускорения времязависимого пробоя между двумя температурами есть отношение времен до отказа при температуре испытаний и определенной рабочей температуры. Коэффициент температурного ускорения определяется как
AT |
exp |
Ea |
1 |
1 |
, |
(2.9) |
||
k |
|
Ts |
|
T0 |
||||
|
|
|
|
|
|
где Тs – температура испытаний; Т0 – предполагаемая рабочая температура; Еа – энергия активации, 0,3 эВ.
Определенный экспериментально с использованием тестовых емкостей коэффициент ускорения электрическим полем (АEF) для ТDDВ между двумя полями, так же как и для фактических ЗУ, согласуется с моделью
A |
exp |
E0 |
Es |
, |
(2.10) |
|
|
||||
EF |
|
EEF |
|
|
|
|
|
|
|
где Еs, Е0 – тестовая и рабочая напряженности полей, МВ/см, ЕEF – экспериментально определенная напряженность, 0.062 МВ/см. Подставляя ускоряющие факторы для температуры (2.9) и напряжения (2.10) в (2.8), получим распределение отказов при времязависимом пробое для конкретных рабочих условий из результатов ускоренных испытаний:
61
f0 (lnt) |
|
|
|
|
|
1 |
|
|
|
|
|
|
|
|
|
|
|
|
|
|
|
|
|
|
|
|
|
|
|
|
|
|
|
|
|
|
|
|
|
|
|
|
|
2 |
|
(t |
t0 ) |
|
|
|
|
||||
|
|
|
|
|
|
|
|
||||||
|
|
|
|
|
|
t |
t0 |
|
|
|
2 |
||
|
|
|
|
ln |
ln |
|
(2.11) |
||||||
|
1 |
|
|
At |
AEF |
At AEF |
|||||||
exp |
|
|
|
|
|
|
|
|
|
|
|
|
, |
2 |
|
|
|
|
|
|
|
|
|
|
|
||
|
|
|
|
|
|
|
|
|
|
|
|
|
Часть выборки, имеющей время отказа в диапазоне от 0 до t, рассчитывается по уравнению
|
ln t |
|
Q(ln η) |
f0 (lnt)d ln t, |
(2.12) |
где Q(ln ) – функция распределения вероятности отказов, представляющая накопленный процент отказавших приборов как функцию времени. Квантиль распределения Q(ln ) является не только функцией времени, электрического поля и температуры, как следует из уравнения (2.11), но так же размеров приборов и плотности скрытых дефектов.
Скрытые дефекты, по определению, это дефекты, которые не вызывают отказы приборов до определенного времени испытаний.
При прогнозе для приборов другой площади, отличной от площади приборов, для которых фактические коэффициенты были получены, необходимо иметь соотношение между Q(ln ) и площадью прибора. Q(ln ) связана с плотностью скрытых дефектов и площадью прибора уравнением /41/:
Q(ln η) |
|
|
1 |
|
, |
(2.13) |
|
|
|
|
|||
1 |
1 |
|
||||
|
|
|
|
|||
|
|
|
|
|
||
|
As D(ln η) |
|
|
|
||
|
|
|
|
|
|
где D(ln ) – плотность скрытых дефектов как функция логарифма времени; As – площадь испытываемых приборов.
62

Путем решения уравнений (2.12) и (2.13) для D(ln ), Qо(ln ) для определенных рабочей температуры Т0, электрического поля Е0 и площади прибора А0 может быть рассчитана следующим образом:
Q0 |
(ln η) |
|
|
1 |
|
, |
(2.14) |
|
|
|
|
|
|
||||
|
As |
1 |
|
|||||
|
1 |
1 |
|
|
||||
|
|
|
|
|
|
|||
|
A0 |
|
Q(ln η) |
|
||||
|
|
|
|
|
|
|
Времязависимые отказы или скорость отказов nо(ln ) при определенных температуре, электрическом поле и площади прибора должна быть:
n0 |
(ln ) |
1 |
|
dQ0 (ln |
) |
. |
(2.15) |
|
1 Q0 |
(ln ) |
|
d (ln |
) |
||||
|
|
|
|
|
Решение уравнения (2.15) численным методом приводит к следующим результатам:
предсказываемая скорость отказов в ЗУ при номинальных напряжениях и температурах может быть получена из результатов ускоренных испытаний на тестовых структурах;
для данной плотности скрытых дефектов может быть определена продолжительность ТЭТ, требуемая для того, чтобы снизить интенсивность отказов до желаемого уровня;
также могут быть определены оптимальные условия ТЭТ (температура и напряжение) для данного прибора, которые могут дать желаемую скорость отказа.
2.4. Прогнозирование надежности затворного окисла и оптимизация отбраковочных испытаний
Зависящий от времени пробой диэлектрика привлек значительное внимание как принципиальный механизм отказа в МОП-схемах. Чтобы снизить интенсивность отказов в процессе эксплуатации, обычно проводятся испытания на принудительный отказ (burn-in), которые позволяют отбраковать потенциально ненадежные изделия. Однако, количественная модель, позволяющая прогнозировать влияние длительности, напряжения и температуры при испытании на принудительный
63
отказ на последующий срок службы, отсутствует. В /42, 43/ представлена общая модель для определения условий зависящего от времени пробоя от времени, напряжения и температуры. Основываясь на этой модели, рассмотрим концепцию эффективной толщины и зависимость от поля вида 1/Еох для пробоя SiO2, а также общую методику прогнозирования надежности затворного окисла и оптимизации условий отбраковочных испытаний. Из измерений на линейно изменяющемся во времени напряжении определяется функция распределения дефектов как функция дефектов, связанных с шероховатостью (характеризуемые как эффективная толщина окисла). Надежность окислов, характеризуемая этим распределением дефектов, соответствующая данным условиям принудительных испытаний, может быть рассчитана для любой площади окисла, рабочего напряжения и температуры.
Ускорение напряжением и температурой.
Основываясь на испытаниях при постоянном напряжении на окислах малой площади (площадь <400 мкм2) логарифм времени до пробоя ВD, как было показано в /32/, следует обратно пропорциональной полевой зависимости:
BD 0 exp |
G |
0 exp |
GX ox |
, |
(2.16) |
|
Eox |
Vox |
|||||
|
|
|
|
|||
где Xox – толщина окисла; Vox – напряжение на окисле; |
G=350 |
мВ/см и o( 10–11 с) – соответственно наклон и точка пересечения графика ln( BD) от 1/Еох /13/.
Ранние отказы были приписаны дефектам на или вблизи границы раздела Si-SiO2. Исследование /43/ показало корреляцию между низкими пробивными полями и присутствием декорированных дефектов упаковки. Авторы приписали ранние отказы локальным уплотнениям и нарушениям сплошности окисла, вызванными преципитатами металлов. В работе /15/ показано, что пробой, индуцированный дефектами, может быть достаточно точно промоделирован с использованием
64
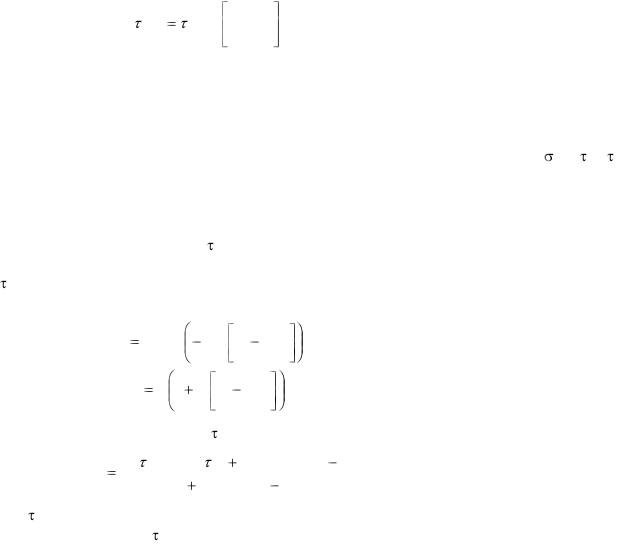
концепции эффективного утонения: дефекты моделируются как локальное утонение окисла, такое что
BD 0 exp |
GX eff |
, |
(2.17) |
|
Vox |
||||
|
|
|
где Xeff – эффективная толщина окисла в наиболее слабом месте. Эта концепция используется для того, чтобы моделировать не только физически тонкие места в окисле, но также шероховатости на границе раздела (приводящие к более высоким полям) и локальные участки, имеющие отличающийся химический составом, который может увеличивать скорость захвата заряда или снижать высоту потенциального барьера на границе Si–SiO2 (более низкие G). Все эти возможные источники дефектов математически эквивалентны локальному утонению окисла в (2.17).
В правой части (2.17) o и G являются единственными температурнозависимыми величинами. Путем представления o(Т) в форме Аррениуса с энергией активации Eb и разложе-
ния G(T) в ряд Тейлора по 1/Т получаем:
η0 (T ) |
η0 exp |
|
|
Eb |
|
1 |
|
|
1 |
|
, |
|
(2.18а) |
|||||
|
|
|
k |
|
|
|
|
|
|
|
||||||||
|
|
|
|
|
|
T 300 |
|
|
||||||||||
G(T ) |
G 1 |
δ |
|
1 |
|
1 |
|
|
, |
|
(2.18б) |
|||||||
|
|
|
|
|
|
|
|
|
|
|
|
|
||||||
k |
|
|
T |
300 |
|
|
||||||||||||
|
|
|
|
|
|
|
|
|
|
|||||||||
Энергия активации для |
|
bd, Etbd получается /38/: |
|
|||||||||||||||
EtBD |
ln[ |
BD (Ts ) / |
|
0 ] |
|
(Eb / k)(1/ Ts |
1/ 300) |
, (2.19) |
||||||||||
|
1 (δ/k)(1/ Ts |
|
1/ 300) |
|
||||||||||||||
|
|
|
|
|
где =(k/G)dG(T)/d(1/T); k – постоянная Больцмана; Т – абсолютная температура; o и G – величины, определенные ранее при комнатной температуре.
Из уравнения (2.19) следует, что энергия активации не является постоянной: она является функцией срока службы окисла. Это значит, что энергия активации является функцией
65
обоих факторов – напряженности поля и качества окисла, так как срок службы сильно зависит от обоих параметров. Путем объединения (2.19) с соответствующими результатами в температурном диапазоне между 25 oС и 150 oС, и ЕB были определены как 0,0167 и 0,28 эВ соответственно /43/. Так как для пробоя, индуцированного дефектами, энергия активации увеличивается со временем пробоя, ожидаемая энергия активации для ранних (низкий накопленный процент) отказов должна быть меньше, чем для более поздних отказов. Это предположение согласуется качественно с наблюдаемыми изменениями в ~ln( 50/( 60) в логарифмически нормальном распределении для различных температур испытаний. Другим следствием (2.19) является то, что хотя энергия активации для типичного ускоренного испытания (с 10 ч до 10 с, при температуре с 25 oС до 150 oС) находится в пределах 0,2-0,4 эВ, фактическая энергия активации для типичных значений срока службы (10 лет при 25-125 oС) составляет 0,5-0,6 эВ /43/.
Пределы масштабирования. Законы масштабирования и требования к характеристикам устанавливают минимально допустимую толщину затворного диэлектрика или эквивалентно максимальное допустимое поле. Используя (2.17) и температурную модель, представленную в /43/, максимально допустимое поле для окисла толщиной teff при десятилетнем сроке
службы при 125 оС оценивается как 7 МВ/см (Vох/teff) /33/. Это поле соответствует минимальной teff 80 Å для Vох=5,5 В и 50 Å
для V= 3–6 В. Другими словами, любой окисел, имеющий дефектное состояние, характеризуемое teff <80 A (для работы при
5,5 В) или teff <50 A (для работы при 3-6 В), как ожидается, откажет за время до 10 лет при 125 оС. Эти толщины могут быть
интерпретированы как собственные предельные значения для времязависимого пробоя, т. е. окисел должен быть по крайней мере толщиной 80 Å для работы при 5,5 В и толщиной 50 Å для работы при 3,6 В. Следует отметить, что эти условия согласуются с типичными максимально допустимыми токами утечки затвора (1 мкА/см2), которые характерны для поля 7 МВ/cм (по теории Фаулера-Нордгейма).
66
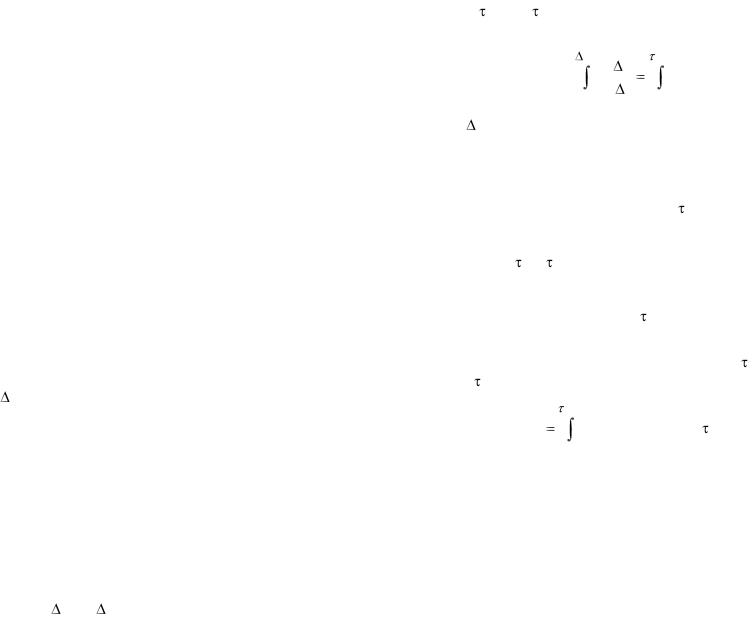
2.5. Модель накапливающихся повреждений Модель накапливающихся повреждений концептуаль-
но предполагает, что прохождение носителей заряда вызывает повреждение окисла, которое приводит к увеличению электрического поля или скорости прохождения носителей и, следовательно, увеличивает скорость деградации. Эта положительная обратная связь обычно вызывает пробой окисла. Физический механизм может включать образование положительного заряда на катоде /2, 3/, захват электронов вблизи анода, резонансное туннелирование и т. д. Существуют значительные доказательства, подтверждающие, что дырки включаются в генерацию повреждений, хотя захват дырок может и не быть обязательным процессом, ответственным за пробой.
В рассматриваемой до сих пор модели температура и приложенное напряжение, как предполагается, остается постоянным в течении всего срока службы окисла. Для того, чтобы применить эту модель к случаю, где напряжение и температура зависят от времени (т. е. испытания на линейноизменяющемся напряжении, испытания на принудительный отказ и последующая работа и т. д.), должен быть определен прирост повреждений d , вводимых в единицу времени. В общем, скорость, с которой окисел повреждается, является функцией напряжения испытаний, температуры и дефектов шероховатости
(teff). Можно так же сказать, что скорость зависит от числа повреждений, вводимых ранними испытаниями, т. е. окисел мо-
жет быть более (или менее) восприимчив к последующим воздействиям, когда уровень повреждений увеличивается.
Предполагая, что скорость, с которой вводятся повреждения, зависит только от мгновенного уровня повреждений, но не зависит от истории предыдущих испытаний, скорость деградации может быть выражена как:
d /dt=f( )g(V,T,teff), |
(2.20) |
где функциональная форма f и g неизвестны в данный момент и напряжение и температура являются зависящими от времени
[V=V( ), T=T( )]. Уравнение (2.20) интегрируется методом разделения переменных:
BD d |
BD |
|
|
|
|
g(V ,T ,teff ), |
(2.21) |
|
f ( ) |
||
0 |
0 |
|
|
|
|
||
где BD – пороговый уровень повреждений для разрушающего |
|||
пробоя. Оба интеграла равны постоянной C. |
|
||
Для испытаний при |
постоянном напряжении и темпе- |
||
ратуре, второй интеграл в (2.21) может быть вычислен: |
|
||
С=g(Vox,T,teff) BD. |
(2.22) |
||
Сравнивая (2.22) и (2.17), получаем: |
|
||
BD= o(T)exp(G(T)teff/Vox)=C/g(Vox,T,teff). |
(2.23) |
||
Функциональная форма g имеет вид: |
|
||
g(Vox,T,teff)=C/ o(T)exp(-G(T)teff/Vox). |
(2.24) |
Подставив g в (2.21), определим условия пробоя для зависящего от времени напряжения V=V( ) и температуры
T=T( ):
|
BD |
|
1 |
exp [–G(T)Xeff/V]dt/ 0(T), |
(2.25) |
|
0 |
|
Пробой при напряжении, линейно изменяющемся во времени. Так как испытания на линейно изменяющемся напряжении значительно короче, чем испытания на постоянном напряжении, весьма желательно уметь характеризовать технологию окисла и прогнозировать надежность из результатов пробоя на линейно изменяющемся напряжении.
Если применить (2.25) для случая испытания при линейно изменяющемся напряжении, когда
V(t)=Rt, T(t)=TVBD, |
(2.26) |
где R – скорость развертки, В/с, условие пробоя примет вид:
67 |
68 |
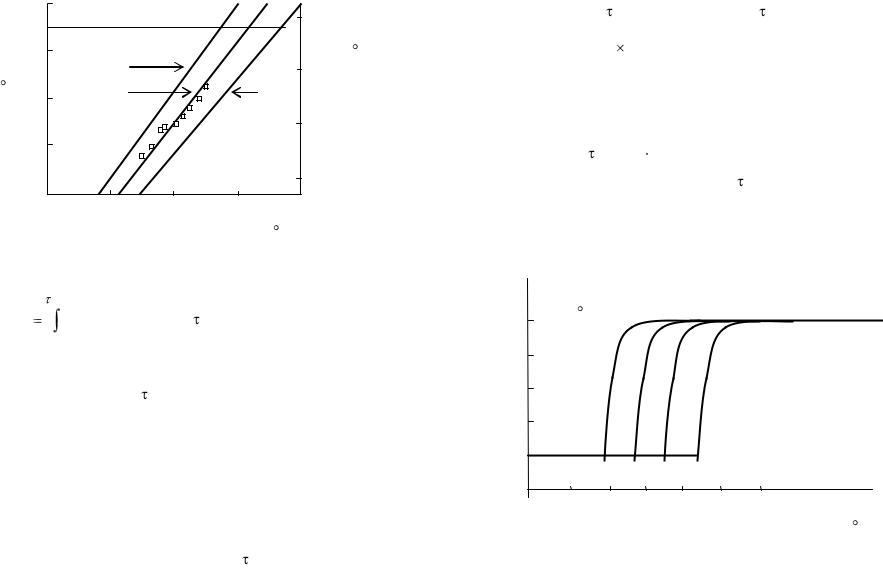
tBD, |
|
|
10 лет |
|
|
105 |
tBD, с при |
лет |
|
|
|
|
|
|
7,8 В и |
при |
100 |
|
|
|
|
25 С |
|
5,5 В и |
|
0,1 |
|
|
103 |
|
|
125 |
С |
-2 |
1 В/с |
|
10 |
|
|
|
10 |
|
|
|
|||
|
|
|
|
|
|
|
|
|
|
|
|
|
|
101 |
|
|
10-4 |
|
|
|
|
|
|
|
10-6 |
|
|
|
10-1 |
|
|
|
|
|
|
|
|
||
|
|
5 |
7 |
9 |
11 |
13 |
|
|
|
|
|
|
VBD, В при 25 |
С |
|
|
|
Рис. 2.1 Корреляция между tBD и VBD |
|
||||
|
|
BD |
|
|
|
|
|
|
1 |
|
exp [–G(T)Xeff/Rt]dt/ 0(TVBD), |
|
(2.27) |
||
|
|
0 |
|
|
|
|
|
что после интегрирования даст: |
|
|
1=VBD2/[RG(TVBD) 0(TVBD)Xeff]exp[-G(TVBD)Xeff/VBD, (2.28)
где VBD=RtBD /3/. Уравнение (2.28) может быть решено численно для определения Xeff, соответствующего измеренному VBD. Однако, так как зависимость экспоненциального сомножителя от Xeff в (2.28) доминирует над зависимостью предэкспоненциального коэффициента от Xeff, возможно получить близкое к точному решение для Xeff путем подстановки в предэкспоненциальный член Xeff =80 Å:
Xeff =VBD/G(TVBD)ln{VBD2/[RG(TVBD) o(TVBD)80(Å)]}. (2.29)
Подставляя (2.29) в (2.17), получаем приблизительное соотношение между VBD при линейно изменяющемся напряжении при температуре TVBD, и tBD, временем до пробоя постоянном напряжении тестирования при температуре Т:
69
tBD= o(TtBD)[VBD2/RG(TVBD) o(TVBD)
80(Å)]G(TtBD)VBD/G(TVBD)Vox. (2.30)
Для типичного случая, когда испытания на линейно изменяющемся напряжении проводятся при комнатной температуре (TVBD=25 oC и TtBD=T), уравнение (2.30) упрощается до
tBD= |
o(T)[3,6 10 |
8 |
2 |
/(VsR)] |
[G(T)/350](V |
/V ) |
, |
(2.31) |
|
VBD |
BD |
ox |
|||||
где G(T) (выраженное в МВ/см) и |
o(T) даны в (2.18). |
|
Следовательно, сроку службы 10 лет при 5,5 В и 125 оС соответствует VBD=11,5 В при 1 В/с, а сроку службы 100 лет соответствует VBD=12 В при 1 В/с (рис. 2.1).
Чтобы проверить корреляцию между пробоем на ли-
Условия испытаний: 10 ч,
100
75
50 Напряжениеиспытаний 6В 6,5В 7В 7,5В
25
0
9 |
10 11 |
12 13 |
14 VBD, В |
VBD[В] при 1В/с и 25 С Рис. 2.2 Экспериментальные результаты испытаний
на линейном развертывающем напряжении, следующие после испытаний на принудительный отказ обнаруживают резкое падение пробивных напряжений как и предусматривалось времязависимой моделью испытаний
70
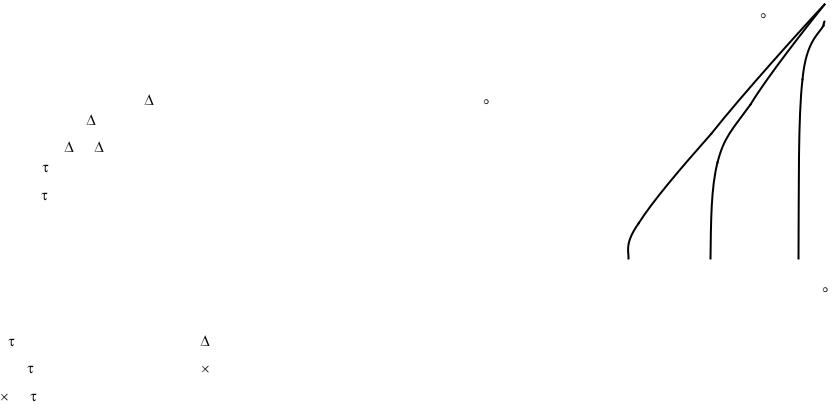
нейно растущем напряжении и времязависимом пробоем (2.31), были проведены испытания на окисле c толщиной
125 Å.
Как видно из рис. 2.1, существует очень хорошее согласие между экспериментальными результатами и расчетом.
Экспериментальные результаты были получены при 7,8 В (для испытаний при постоянном напряжении) и 1,0 В/с (для испытаний при линейно увеличивающемся напряжении) для 125 Å окисла (U+ поле на подложке р-типа с ориентацией [100] , смещенной в режим аккумуляции). Каждая точка представляет напряжение пробоя и время до пробоя для определенного кумулятивного процента отказов.
Испытания на принудительный отказ. Другое важное применение (2.15) – моделирование влияния испытаний на принудительный отказ на последующий срок службы окисла /43/. При добавлении ступени испытаний на принудительный отказ, условия пробоя (2.15) – просто сумма повреждений, вводимых во время "выжигания", BI, и тех, которые вводятся
во время работы прибора, |
OP: |
|
|
|
1= BI+ |
OP, |
(2.32a) |
1=[tBI/ |
o(TBI)]exp[-G(TBI)Xeff/VBI] + |
|
|
+ [tOP/ |
o(TOP)]exp[–G(TOP)Xeff/VOP], |
(2.32б) |
при этом окисел подвергается "выжиганию" при VBI, Вольт, и IBI, Кельвин, для tBI, сек, и имеет последующий срок службы
tOP при VOP, Вольт, и TOP, Кельвин.
Решая (2.32б) относительно срока службы tOP, можно определить влияние данных условий "выжигания" на последующий срок службы прибора:
tOP= o(TOP)exp[G(TOP)Xeff/VOP][1- |
BI] |
(2.33а) |
tOP= o(TOP)exp[G(TOP)Xeff/VOP] |
|
|
[1– BI/to(TBI)exp[–G(TBI)Xeff/VBI]. |
(2.33б) |
Срок |
103 |
|
|
Условия испытаний: 150 С, |
|
|
|||||
|
|
|
|
||||||||
службы, |
|
|
|
|
|
||||||
|
|
|
10 ч |
|
|
|
|
|
|
||
лет |
|
|
|
|
|
|
|
|
|
||
|
|
|
на принудительный отказ |
|
|
||||||
при |
102 |
|
|
|
|
||||||
|
|
|
|
|
|
|
|
|
|
||
5,5 В, |
|
|
|
|
|
|
|
|
|
|
|
125 С |
|
|
|
|
|
|
|
|
|
|
|
после испы |
101 |
|
|
|
|
|
|
|
|
|
|
таний на |
|
|
|
|
|
|
|
|
|
|
|
|
|
|
|
|
|
|
|
|
|
|
|
принудите- |
|
|
|
Напряжение |
|
6,5В |
7В |
7,5В |
|||
льный от- |
|
|
|
испытаний на |
|
|
|
|
|
|
|
каз |
100 |
|
|
принудитель- |
|
|
|
|
|
|
|
|
|
|
|
|
|
|
|
||||
|
|
|
|
ный отказ |
|
|
|
|
|
|
|
|
10-1 |
|
|
|
|
|
|
|
|
|
|
|
|
|
|
|
|
|
|
|
|||
|
|
|
|
|
|
|
|
|
|
|
|
|
10-1 |
100 |
101 |
102 |
103 |
Первоначальный срок службы при 5,5 В, 125 С Рис. 2.3 Представление результатов рис 2.2 в терминах договечности при рабочих условиях. Результаты испытаний на линейной развертке
71 |
72 |
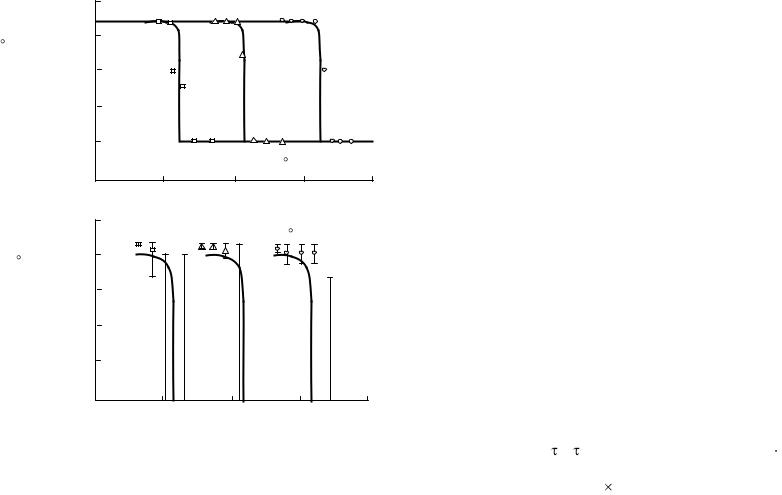
Среднее VBD, В |
20 |
|
|
|
|
|
|
|
|
|
|
|
|
|
|
при 0,5 В/c, |
|
|
|
|
|
|
|
25 C после |
1 |
|
|
|
|
|
|
испытаний |
|
|
|
|
|
|
|
на принудите- |
1 |
|
|
|
|
|
|
а) |
|
Время |
104 с |
103 с |
102 с |
|
|
5 |
испытаний |
|
|
|
|
|
|
|
|
|
|
|
|
||
|
0 |
|
|
|
|
|
|
|
|
Температура испытаний 150 C, Xox 125 Å |
|
||||
|
10 |
11 |
|
12 |
13 |
14 |
|
|
Напряжение испытаний, В на принудительный отказ |
||||||
VBD, В |
18 |
Температура испытаний 150 С, Xox 125 Å |
|
||||
|
|
||||||
при 0,5 В/c, |
|
|
|||||
17 |
на принудительный отказ |
|
|
|
|||
25 С |
|
|
|
|
|
|
|
|
|
|
|
|
|
|
|
после испы- |
|
|
|
|
|
|
|
таний |
16 |
|
|
|
|
|
|
б) |
15 |
|
|
|
|
|
|
|
14 |
Время |
|
104 с |
103 с |
|
|
|
|
|
|
|
|
|
|
|
13 |
|
|
|
|
|
|
|
10 |
11 |
|
12 |
13 |
14 |
|
|
|
|
|
|
|
На- |
|
Рис. 2.4 Результаты испытаний на линейно развертывающем |
|||||||
напряжении, которые следуют за испытанием на принудительный |
|||||||
отказ, обнаруживают резкое падение пробивных напряжений как и |
|||||||
представлялось моделью. Среднее напряжение пробоя для четырех |
|||||||
окислов, |
подвергнутых |
идентичным |
испытаниям |
на |
|||
принудительный отказ представлено на графике (а). Интервалы на |
|||||||
рис. (б) показывают полный диапазон измеренных пробивных |
|||||||
напряжений для четырех окислов, тестируемых при каждом |
|||||||
условии испытаний |
|
|
|
|
|
Сравнивая (2.33б) и (2.17), видим, что первые два произведения дают первоначальное время жизни окисла, т. е. срок службы без "выжигания". Следовательно, величина, заключенная в квадратные скобки в (2.33б) соответствует части пер-
73
воначального срока службы окисла, остающейся после испытаний на принудительный отказ. Эта величина представлена на рис. 2.2 как функция Xeff, так же как соответствующее напряжение пробоя на линейном развертывающем напряжении [используя (2.28)] и ожидаемое время жизни при 5.5 В и 125 оС перед "выжиганием" [используя (2.17)].
Как показано на рис. 2.2, только небольшая часть образцов уцелеет после "выжигания", т.е. для 7 В "выжигания" все окислы, имеющие пробивные напряжения между 11,5 В и 12 В, как прогнозируется, должны быть значительно повреждены в период "выжигания". Такой же вывод следует из сравнения ожидаемого срока службы после "выжигания" с первоначальным сроком службы окисла перед "выжиганием", как показано на рис. 2.3: из окислов, остающихся после "выжигания", только те, которые имеют срок службы в пределах половины одной декады, имеют значительно уменьшенный срок службы (т.е. сокращение более чем на 10 % от первоначального срока службы) после "выжигания".
Для проверки влияния "выжигания" на последующую прочность окисла, 125 Å окислы (100 мкм2) подвергались испытаниям на "выжигание" с последующим напряжения пробоя VBD на линейной развертке. В соответствии с (2 измерением.25) и (2.28) условия пробоя для этого эксперимента:
1=[ BI/ o(TBI)]exp[–G(TBI)tox/VBI]+3,6 108[VBD2/(VsR)]
exp(–G(TBI)tox/VBD). |
(2.34) |
Четыре различных образца были испытаны для каждого режима "выжигания". Среднее напряжение пробоя для четырех образцов для каждого теста представлено на рис. 2.4, а как функция напряжения "выжигания". Также показаны предсказанные моделью результаты. Более внимательный анализ перехода от устойчивых окислов (нормальные VBD) к сильно поврежденным окислам (очень низкие VBD) показывает, что только незначительное число окислов повреждается при "выжигании", как следует из (2.34) и показано на рис. 2.4, б. Сред-
74

нее напряжение пробоя для четырех окислов, подвергнутых идентичным испытаниям на принудительный отказ представлено на графике (а). Интервалы на рис. (б) показывают полный диапазон измеренных пробивных напряжений для четырех окислов, тестируемых при каждом
3. Влияние масштабирования на отказы СБИС 3.1. Основные алгоритмы масштабирования
Масштабирование размеров интегральных приборов и топологии были движущей силой развития технологии. В табл. 3.1 представлены два алгоритма масштабирования для размера приборов и параметров материалов /44/
Первый алгоритм характеризует идеальное масштабирование и второй - реальное уменьшение, используемое для получения увеличенной плотности схем без введения добавочных электрических напряжений на транзисторы с минимальной длиной канала.
Табл. 3.2 показывает влияние масштабирования на электрические параметры приборов для двух алгоритмов табл. 3.1.
Таблица 3.1 Влияние идеального масштабирования и компромиссного уменьшения размеров приборов и параметров материалов
Коэффициент масштабирования |
Идеальное |
Компромисс- |
к>1 |
масштабиро- |
ное масшта- |
Размеры |
вание |
бирование |
|
|
транзисторов |
|
|
|
Длина канала lE |
1/к |
1 |
Ширина канала ZE |
1/к |
1/к |
Толщина затвора окисла tox |
1/к |
1 |
Толщина полевого окисла tFox |
1/к |
1/к |
Глубина перехода xj |
1/к |
1/к |
Размеры контактов А |
1/к |
1/к |
Ширина линии W |
1/к |
1/к |
Толщина металла t |
1/к |
1/к |
Параметры материала |
|
|
Легирование подложки Na |
к |
1 |
Доза имплантации |
к2 |
зависит от |
|
|
мас- |
|
|
штабиров- |
|
|
вания на- |
|
|
пряжения |
|
|
|
Таблица 3.2 Влияние размеров масштабирования для алгоритмов табл. 3.1 на электрические параметры приборов. Представлены
случаи масштабированных и немасштабированых напряжений
Источник напря- |
1/k |
1 |
1 |
жения |
|
|
|
Ток пробоя* I |
1/ k 1/k |
1/k |
1/k |
CMOS |
1/ k |
k** |
1/k |
Ток/контакт/размер |
|
|
|
Плотность тока в |
k1,5 |
k3 |
k |
металле |
|
|
|
Ток в контактных |
k1,5 |
k3 |
k |
Ячейка хранения |
1/k |
1/k |
1/k2 |
окисла Cox |
|
|
|
75 |
76 |
Заряд ячейки хра- |
1/k2 |
1/k |
1/k2 |
нения QCRIT |
|
|
|
Поле в окисле |
1 |
k |
1 |
Емкость перехода |
1/k |
1/k1,5 |
1/k1,5 |
Сj |
|
|
|
Накопленный заряд |
1/k2 |
1/k1,5 |
1/k1,5 |
p-n-перехода |
|
|
|
Мощность рассеи- |
1/k1,5 |
k |
1/k |
вания на затворе |
|
|
|
Задержка затвора td |
1/k1,5 |
1/k2 |
1 |
*- случай насыщенной скорости: колонка справа для предельного насыщения
**- улучшенные характеристики: продолжительность продолжительность цикла постоянна
3.2.Влияние масштабирования на среднюю наработку
до отказа Комбинация размеров масштабируемых приборов и па-
раметров материалов и результирующие электрические параметры могут быть введены в модели механизмов отказов для того, чтобы предсказать тенденции в надежности и будующее влияние каждого механизма отказа. Рассматривается влияние масштабирования на электромиграцию, пробой окисла, инжекцию горячих носителей и вызванные радиацией программные ошибки.
Злектромиграция. Электромиграция - транспорт ионов проводящего металла, возникающий от прохождения электрического тока. Она является модификацией температурноактивируемого процесса самодиффузии, вызванного передачей момента от электронов проводимости /44/. Отказ осуществляются в металлических линиях или когда положительная дивергенция потока ионов приводит к аккумуляции вакансий и непосредственно к обрыву схемы, или когда отрицательная дивергенция приводит к образованию холмов и в конце концов к замыканию между расположенными рядом или пере-
77
крывающими друг друга слоями металлизации. Наработка до отказа по отношению к электромиграции для металлизации и контактов следует общей форме:
MTTF=(1/j2)exp(EA/kT), |
(3.1) |
где j - плотность электрического тока; EA - энергия активации; k -постоянная Больцмана; T - абсолютная температура.
Поперечное сечение металлизации и контактов сокращается пропорционально квадрату коэффициента масштабирования. Для наихудшего случая немасштабированного напряжения ток увеличивается линейно с коэффициентом масштабирования и следовательно плотность тока увеличивается как куб коэффициента масштабирования. Для металлических проводников существует добавочная линейная зависимость коэффициента масштабирования от ширины линии, так что отношение масштабированного к немасштабированному времени наработки до отказа следующим образом зависит от коэффициента масштабирования:
для отказа, обусловленного электромиграцией,
MTTFs/MTTFu=1/k7. (3.2)
Контакты металлизации к диффузионным областям могут также отказывать выше описанным способом в точках минимального покрытия металлом ступени контактного окна
/44/.
Механизм отказов типа обрыв металла на ступенях имеет раздельные коэффициенты для обоих ширины контакта и покрытия ступеньки. Для квадратных контактов в диапазоне от 1,5 мкм до 3,0 мкм следующие соотношения были найдены эмпирически:
отказы в контактных окнах из-за электромиграции
MTTF3/MTTFn=1/к9 |
(3.3) |
Энергия активации для обоих процессов для Al-Si металлизации 0,5 эВ.
78

Добавочный механизм отказа вследствие электромиграции может преобладать в контактах к мелким диффузионным переходам, который обуславливается непрерывным процессом электромиграции кремния из контакта под действием потока электронов и последующей обратной диффузией Al в пустоты до тех пор, пока утечка не осуществляется /44/. Механизм отказа контакта, обусловленный током утечки имеет квадратичную зависимость от глубины p-n-перехода и, вследствие оттеснения тока, линейную зависимость от раcтояния до края контакта. Плотность тока, которая должна быть использована в этом случае является линейной приведенной к краю плотностью тока. Эмпирически, зависимость времени наработки до отказа для механизма отказа, связанного с утечкой, от масшбирования тогда должна иметь следующий вид:
MTTF=1/k2. |
(3.4) |
Энергия активации для электромиграции кремния из контакта 0,9 эВ.
Пробой окисла. Интенсивность отказов, связанная с окислом, имеет очень сильную полевую зависимость, и относительно слабую температурную зависимость (0,3 эВ). Исторически, для широкого диапазона технологий окисла и толщин при небольшом проценте отказов, временная зависимость отказов имеет типичное ускорение мегавольт на сантиметр при низких рабочих полях /44/. Следовательно, для того же самого распределения дефектов, масштабирование толщины окисла при неизменном напряжении будет давать более высокую скорость отказа и следовать соотношению
MTTFs/MTTFu=10-7(k-1)V/Tox, |
(3.5) |
где V/Tох выражается в МВ/см.
Это очень высокое полевое ускорение совместно с резко падающей скоростью отказов окисла приводит к отбраковке ИС приборов со слабым окислом кратковременными испытаниями при повышенных рабочих напряжениях. Однако так как масштабирование продолжается в сторону уменьшения тол-
79
щины и дальше, нормальные рабочие поля могут приблизиться к тем, которые характерны для собственной деградации (старение) и коэффициент полевого ускорения сильно сокращается /44/. Коэффициент полевого ускорения для 100 A окислов был сообщен на уровне 100 MВ/см /44/. Отбраковка скрытых дефектов при этих высоких нормальных полях имеет ограниченную эффективность вследствие низких ускоряющих факторов и может даже ухудшать характеристики надежности вследствие износа окисла.
Деградация окисла характеризуется для данной технологии количеством заряда, которое может пройти через этот окисел при данном приложенном поле, перед тем как осуществится пробой. Ток Фаулера-Нордгейма через окисел приблизительно экспоненциально зависит от электрического поля в окисле. Следовательно, для случая постоянного напряжения MTTF масштабированных тонких окислов будет сокращаться экспоненциально с коэффициентом масштабирования
MTTFs/MTTFu~exp- /[Eох(1–1/k)]. |
(3.6) |
Эффекты горячих носителей. Горячими носителями являются те электроны и дырки в канале и области отсечки, которые получают достаточно много энергии от продольного электрического поля, создаваемого напряжением исток-сток, так что их распределение по энергиям оказывается много выше, чем то, которое можно представить в случае их равновесия с решеткой. Когда эти носители получают энергию, соответствующую первому критическому уровню ( 1,5 эВ в Si), они приобретают способность к ударной ионизации (создание добавочных электронно-дырочных пар), которая обеспечивает умножение тока истоксток и тока подложки /44/. Если электроны продолжают получать энергию, они могут достигнуть второй ступени ( 3 эВ), где они могут быть инжектированы над энергетическим барьером в SiO2. Существует также пороговое электрическое поле для этих процессов в кремнии,
105 В/см. Выше этого поля скорость получения энергии от поля выше скорости потери энергии через оптические фононы.
80