
- •ХИМИЧЕСКАЯ
- •Производство фосфорной кислоты
- •Функциональная схема производства экстракционной фосфорной кислоты
- •Сернокислотное разложение апатита
- •Фосфорные удобрения
- •Азотнокислое разложение фосфатов. Получение сложных удобрений
- •Производство аммиачной селитры
- •Раствор аммиачной селитры (60-80%) поступает в
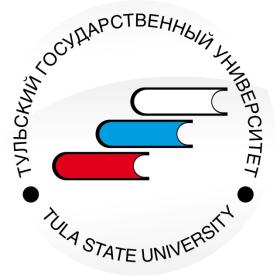
ХИМИЧЕСКАЯ
ТЕХНОЛОГИЯ
Лекция №9
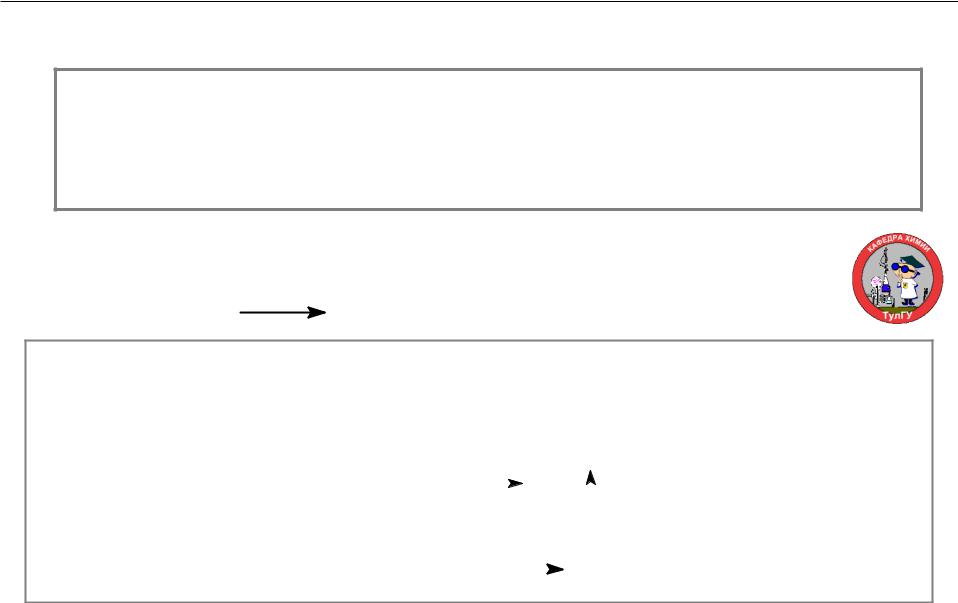
Производство фосфорной кислоты
Функциональная схема производства экстракционной фосфорной кислоты
Сложность состава исходного сырья, которое не может быть унифицировано, приводит к существованию ряда вариантов технологических схем его переработки. Одним из хорошо исследованных является сернокислотное разложение апатитового концентрата, получаемого обогащением хибинской апатито-нефелиновой руды и содержащего около 39% Р2О5. Его
разложение – гетерогенная реакция “жидкость – твердое тело”.
Ca5F(PO4)3 + 5 H2SO4 + 5n H2O
(1)
3 H3PO4 + 5 CaSO4 nH2O + HF
Выделение примесей облегчается переходом их в другую фазу. Кальциевая составляющая выпадает в осадок в виде гипса (CaSO4), вторая уходит в газовую фазу в виде фтороводорода HF. Функциональная схема
производства ЭФК включает разложение измельченного сырья в реакторе (экстракторе), фильтрацию твердого осадка, упаривание фосфорной кислоты до товарной концентрации и очистку отходящих газов. Твердый отход получил название “фосфогипс”. Образующийся фтороводород взаимодействует с пустой породой сырья
SiO2 + 4 HF |
|
SiF4 |
|
+ 2 H2O |
|
||||
|
|
Поэтому при промывке отходящих газов водой оба летучих продукта улавливаются в виде кремнефтористоводородной кислоты H2SiF4.
SiF4 + 2 HF |
|
H2SiF6 |
|
2
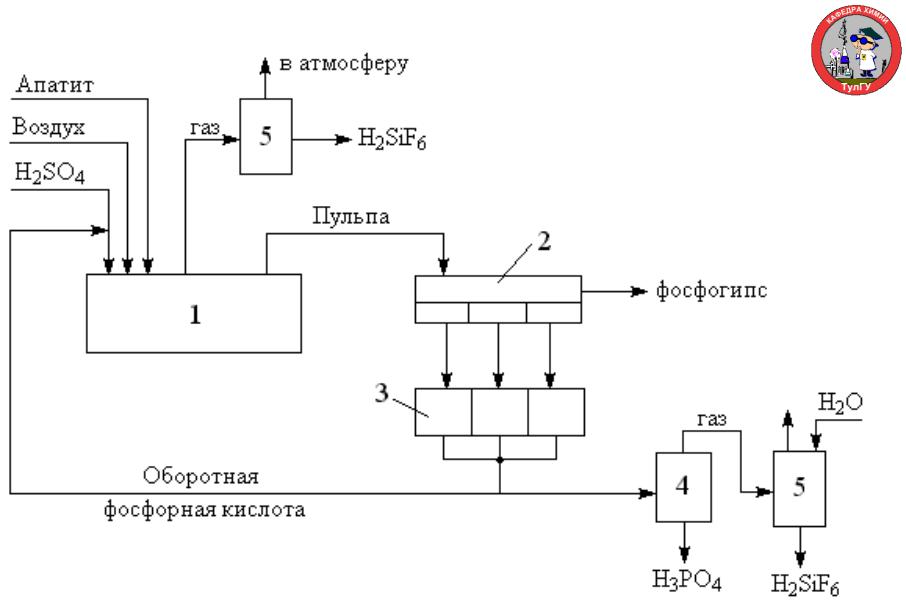
Функциональная схема производства экстракционной фосфорной кислоты
1 – реактор разложения апатита (экстрактор); 2 – вакуум фильтр; 3 – сборник фильтратов;
4 – колона выпарки фосфорной кислоты; 5 – система очистки газов. |
3 |
|
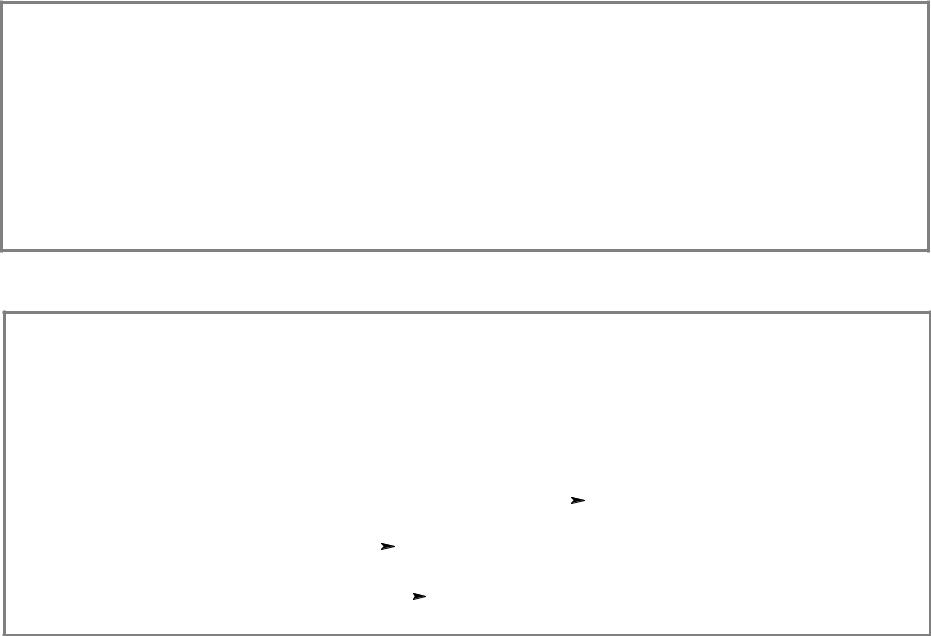
Сернокислотное разложение апатита
С растворением апатита происходит образование твердого CaSO4, который плохо растворим. Связывание Са2+ в CaSO4 должно увеличивать скорость растворения апатита. Образующаяся корка CaSO4 сначала замедляет
растворение, а затем блокирует поверхность, и растворение практически прекращается. Поэтому есть некоторая оптимальная концентрация CaSO4, при которой степень извлечения фосфора из сырья будет максимальной. К
концентрации Н2SO4 в реакторе предъявляются жесткие требования: строгое поддержание этой концентрации на
оптимальном уровне во всем объеме реакционной зоны.
Реакционный узел - последовательность секций с интенсивным перемешиванием реагентов в каждой из них и перетоком между ними для организации движения реакционной массы по каскаду. В первых секциях
происходит растворение апатита. Остальные секции работают как дозреватели, в них формируются кристаллы CaSO4. Между последней и первой секциями организован интенсивный рецикл.
Образование продукционной фосфорной кислоты
Включает отделение осадка CaSO4 (фосфогипса) и концентрирование кислоты. В зависимости от условий разложения образуются кристаллы CaSO4·2Н2О (дигидрат) или CaSO4·0,5Н2О (полугидрат). В дигидратном процессе температура 343-353 К и концентрация фосфорной кислоты 25-35 %. В полугидратном процессе эти показатели составляют 358-378 К и 35 мас. %. Фосфогипс отделяют на вакуум-фильтре. Фильтрат направляют на выпаривание, где концентрация кислоты увеличивается до 52-54 %. Это и есть продукционная кислота. При выпаривании из кислоты удаляется 80-90 % фтора в виде HF. Отходящие из реактора и из узла выпаривания фторсодержащие газы в системах очистки поглощаются с образованием кремнефтористоводородной кислоты.
2 Ca3(PO 4)2 |
+ 10 CO |
+ 6 SiO 2 |
|
P4 + 10 CO 2 + 6 CaSiO 3 |
||||
|
||||||||
P4 + |
5 O 2 |
|
|
|
P2O 5 |
|
|
|
|
|
|
|
|
||||
P2O 5 |
+ 3 H2O |
|
|
2 H3PO 4 |
|
|
||
|
|
|
|
4
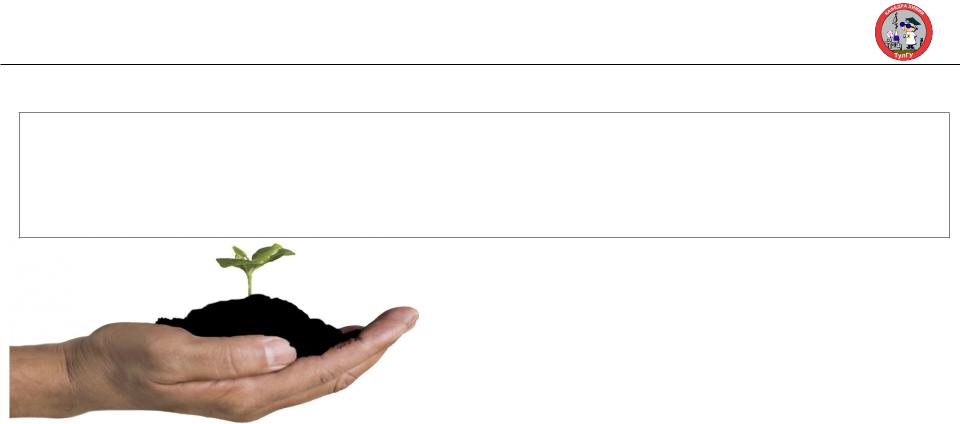
ои
П
сон
о
сте аг ав
ро
у
ах
(п
ли
оП мь аго
и
ресвн че гаыо ск етнйс
о
твуо
м
ма уд ум нао со знб ст ачр оя
ен
и
ни
ю
юи
я)
Производство минеральных удобрений
Классификация минеральных удобрений
Минеральные удобрения являются одним из важнейших для хозяйственной деятельности человека видов продукции химической промышленности. Минеральные удобрения классифицируют по трем главным признакам - агрохимическому назначению, составу и свойствам.
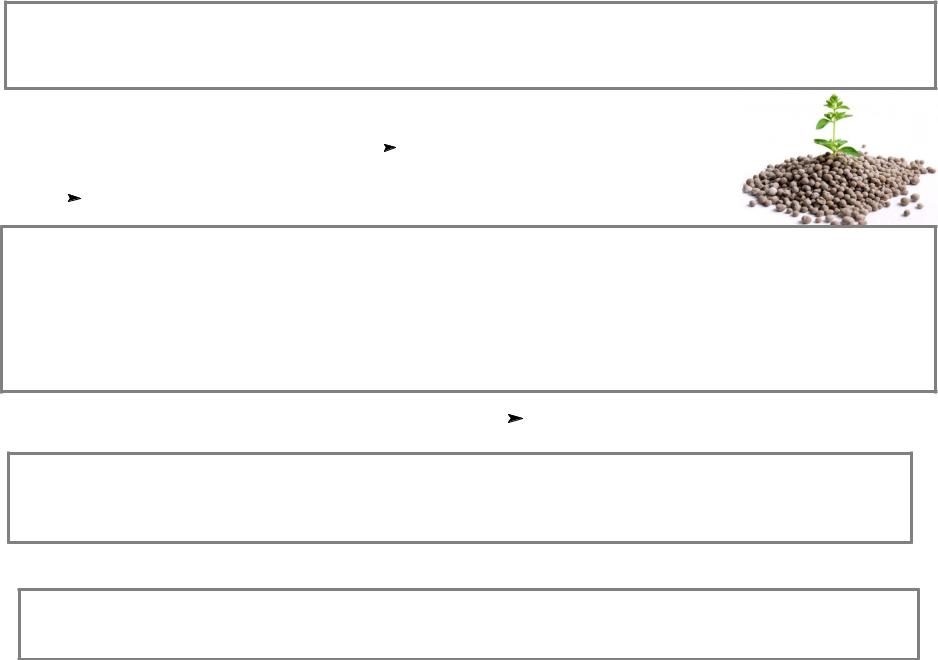
Фосфорные удобрения
Методы переработки природных фосфатов в удобрения: механические, термические и методы кислотного разложения. Один из методов механической обработки - измельчение фосфатов. Полученная фосфористая мука при использовании в кислых
почвах медленно растворяется в почвенных водах и становится долговременно действующим удобрением. Фосфорные удобрения могут быть получены термическим разложением фосфатов при температурах 1200 – 1800ºС.
|
|
Производство простого суперфосфата |
|||
2 Ca5F(PO4)3 + 7 H2SO4 + |
6,5 H2O |
|
|
(1) |
|
|
|||||
|
|
|
|
|
|
|
3 [Ca(H2PO4)2 H2O] |
+ 7 [CaSO4 0,5 H2O] + 2 HF + 227,4 кДж |
|
||
|
|
Разложение протекает в две стадии. На первой стадии около 70% апатита реагирует с серной кислотой. При этом образуется фосфорная кислота и полугидрат сульфата кальция (1). Эта стадия характеризуется образованием поверхностных пленок CaSO4 на
зернах фосфата. Структура образующейся корки обусловлена скоростью кристаллизации твердой фазы, зависящей от пресыщения раствора сульфатом кальция, которое определяется в свою очередь концентрацией серной кислоты, температурой и другими факторами. Поэтому необходима оптимальная концентрация серной кислоты, сочетающая достаточную скорость растворения апатита с образованием рыхлой пленки, более проницаемой для диффузии серной кислоты к поверхности фосфата. Первая стадия заканчивается через 20 – 40 минут после смешения фосфата с серной кислотой. После полного исчезновения серной кислоты начинается вторая стадия разложения, в которой оставшийся апатит (~ 30%) разлагается фосфорной кислотой:
Ca F(PO ) |
+ 7 H PO |
4 |
+ 5 H O |
|
5 [Ca(H2PO4)2 H2O] + HF |
(2) |
|
|
|||||||
5 |
4 3 |
3 |
2 |
|
|
|
Образующийся монокальцийфосфат в отличие от сульфата кальция не сразу выпадает в осадок. Он постепенно насыщает раствор фосфорной кислоты, после чего начинает выкристаллизовываться в виде Ca(H2PO4)2 H2O и протекает значительно
медленнее, чем реакция (1), что объясняется низкой активностью фосфорной кислоты и кристаллизацией твердых фаз. Она начинается в суперфосфатных камерах и длится в течение 5 – 20 суток хранения суперфосфата на складе.
Производство двойного суперфосфата
Двойной суперфосфат – концентрированное фосфорное удобрение. Получаемое разложением природных фосфатов фосфорной кислотой. Оно содержит 42 – 50 % усвояемого P2O5, что в 2-3 раза больше, чем в простом суперфосфате. В отличие от
последнего двойной суперфосфат почти не содержит балласта – сульфата кальция. Процесс протекает по уравнению (2).
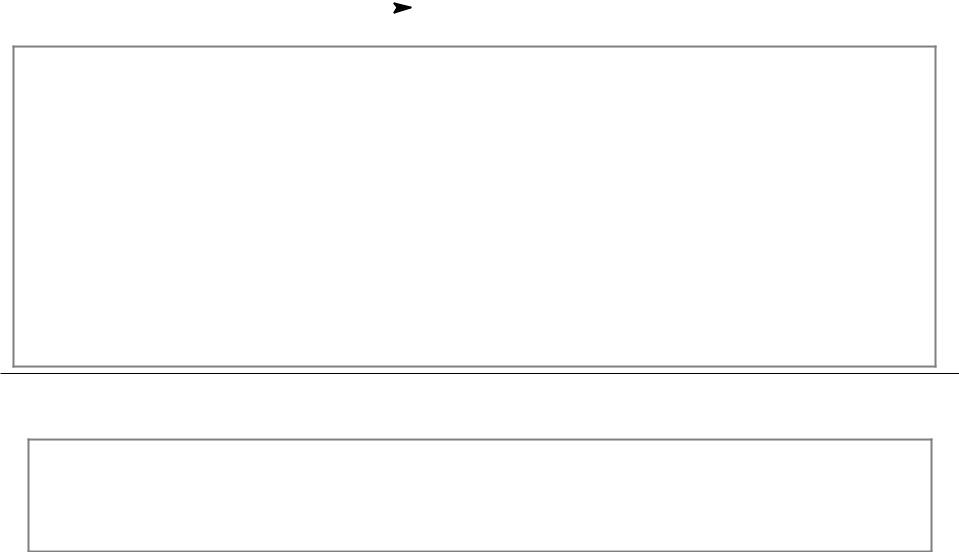
Азотнокислое разложение фосфатов. Получение сложных удобрений
Ca F(PO ) + 10 HNO |
3 |
|
3 H3PO4 + 5 Ca(NO3)2 + HF |
(3) |
|
|
|||||
5 |
4 3 |
|
|
|
В результате образуется азотнокислая вытяжка, раствор, содержащий нитрат кальция и свободную фосфорную кислоту. Существует ряд методов дальнейшей переработки азотнокислой вытяжки. Во многих процессах вытяжку нейтрализуют аммиаком получая фосфаты аммония (NP- удобрения). Если перед гранулированием нейтрализованной пульпы к ней добавляют соли калия (KCl, K2SO4), то получают тройное NPK-удобрение – нитроаммофоску. Во многих процессах
азотнокислой переработки фосфатов нитрат кальция, образующийся в реакции (3), удаляют из реакционной смеси выпариванием. Разработка таких схем дает возможность комплексной переработки фосфатного сырья и создания практически безотходных производств, исключающих сброс отходов, в частности фосфогипса. Азотнокислый метод разложения фосфатов позволяет наряду с получением NPK-удобрений попутно выделять из сырья такие ценные продукты как стронций, редкоземельные элементы и др., находящие применение в различных отраслях промышленности.
Производство азотных удобрений
Важнейшими видами минеральных удобрений являются азотные удобрения: аммиачная селитра, карбамид, сульфат аммония, водные растворы аммиака и др.
Азотные удобрения отличаются друг от друга по содержанию азота, по форме соединений азота (нитратные, аммонийные, амидные), фазовому состоянию (твердые и жидкие).
7
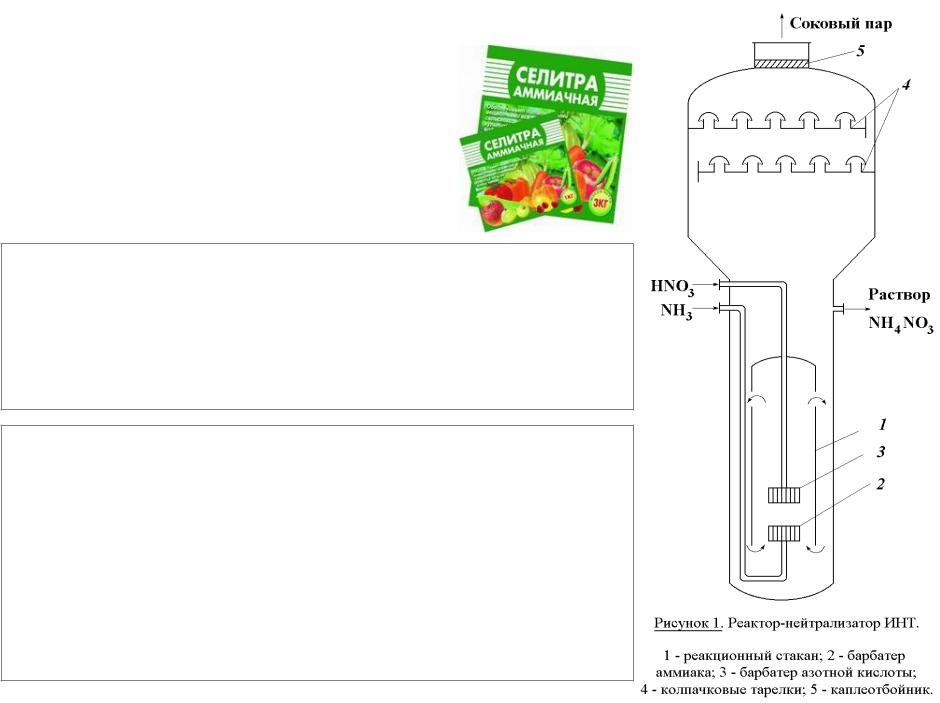
Производство аммиачной селитры
Аммиачная селитра или нитрат аммония (NH4NO3)
– кристаллическое вещество белого цвета, содержащее 35% азота в аммонийной и нитратной формах, обе формы легко усваиваются растениями. Гранулированную аммиачную селитру применяют в больших масштабах перед посевом и для всех видов подкормок. В меньших масштабах ее используют для производства взрывчатых веществ.
Для получения аммиачной селитры применяют ряд технологических приемов. Во-первых, гранулирование. Суммарная поверхность однородных гранул меньше поверхности такого же количества мелкокристаллической соли, поэтому гранулированные удобрения медленнее поглощают влагу из воздуха. В основе процесса производства аммиачной селитры лежит гетерофазная реакция взаимодействия газообразного аммиака с раствором азотной кислоты.
В настоящее время наиболее распространены схемы с частичным упариванием раствора за счет тепла нейтрализации. Нейтрализацию осуществляют в аппарате ИТН (использование тепла нейтрализации) (рисунок 1). Аппарат состоит из двух цилиндров (внешний и внутренний). Во внутренний подается газообразный аммиак и разбрызгивается азотная кислота. Внутренняя часть представляет собой реакционное пространство, внешняя – зона испарения. Отвод тепла из зоны реакции необходим не только для выпаривания раствора, но и во избежание перегрева и разложения азотной кислоты и аммиачной селитры. Соковый пар, образующийся как результат испарения воды из реакционного раствора используется для подогрева реагентов и упаривания реакционного раствора.
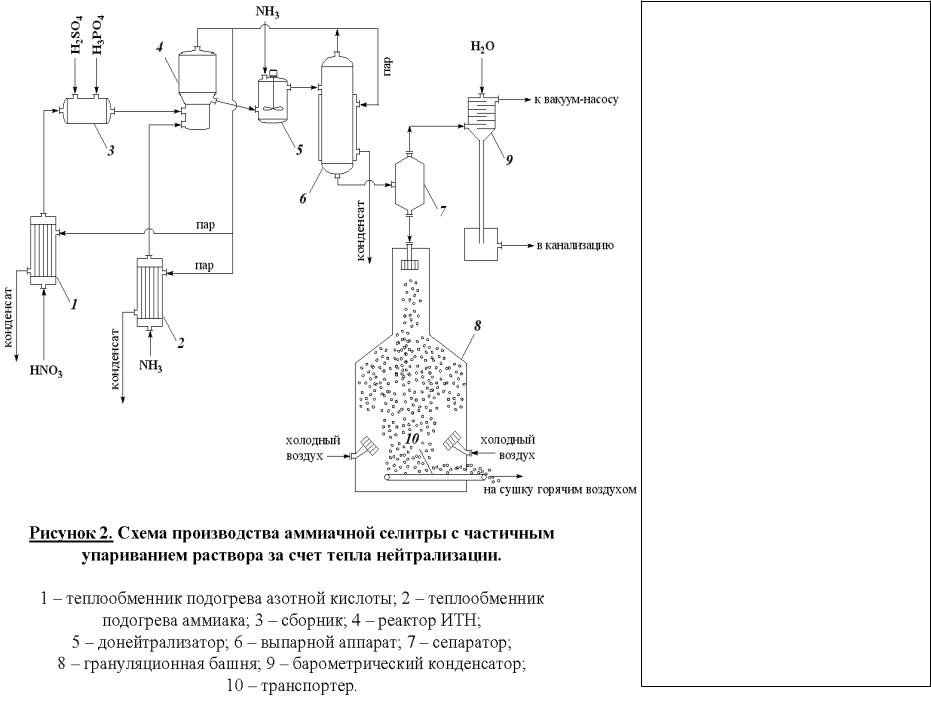
Раствор аммиачной селитры (60-80%) поступает в
донейтрализатор (5). Сюда добавляют аммиак как нейтрализующий агент и вещества уменьшающие слеживаемость удобрений Выпарку проводят в 2 или 3 ступени с использованием в качестве греющих агентов сокового пара из аппарата ИТН, вторичного пара выпарки и свежего насыщенного пара. Для простоты на схеме показан один выпарной аппарат (6). В выпарной установке плав доводят до содержания в нем NH4NO3 98 – 99%.
Гранулирование производят путем разбрызгивания плава в полой железобетонной башне (8) высотой 30 – 35 м. Падающие капли застывают в гранулы в потоке холодного воздуха, поступающего противотоком с помощью вентиляторов. Окончательная сушка осуществляется горячим воздухом во вращающемся сушильном барабане.