
Буровое оборудование карьеров,конспкты
.pdf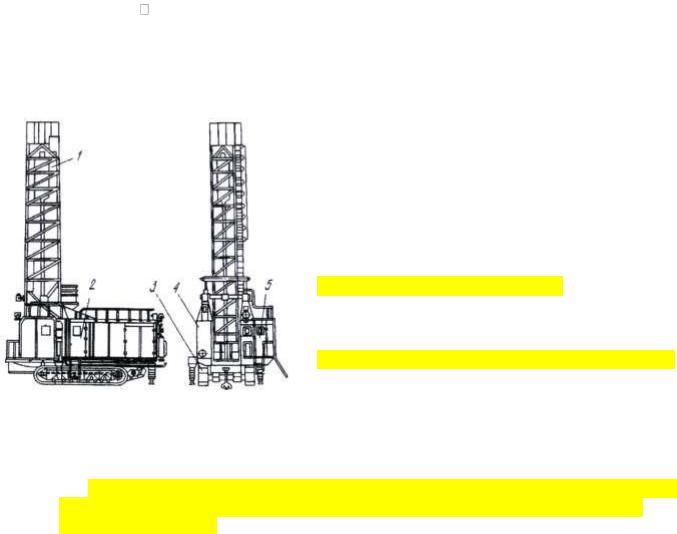
Вертлюг имеет привод шпинделя, что позволяет одновременное свинчивание верхнего и нижнего ниппелей буровой штанги при наращивании и разборке бурового става в процессе бурения скважины и по окончании её проходки, а также сокращение затрат времени на выполнение вспомогательных операций. Однако патронная подача с рабочим ходом 1 м снижает производительность станка. В целях достижения плавности хода в качестве привода ходового механизма установлены асинхронные двигатели с тиристорными станциями управления.
Модернизированная система сухого пылеулавливания обеспечивает состояние атмосферы воздуха в зоне работы станка в отношении запылённости в пределах допустимых санитарных норм. Кабина с пультом управления установлена на пружинных амортизаторах, существенно уменьшающих вибрации на рабочих местах. Для облегчения переноса кабеля при маневрах и перегонах на станках смонтирован кабельный барабан. Благодаря принятым изменениям в станках уменьшаются непроизводительные затраты времени на выполнение вспомогательных операций, повышается производительность станка, снижается трудоёмкость и увеличивается комфортность работы обслуживающего персонала.
С 2002 г. УГМК «Рудгормаш» изготавливаются гидрофицированные станки СБШ- 160/200-40 с электрическим и дизельным приводом. Мачта станка выполнена открытого типа из прямоугольных труб с расположением внутри её карусельной кассеты для размещения шести штанг. При создании этого станка приняты наиболее прогрессивные решения, что позволяет достигнуть часовую производительность в диапазоне крепости пород f = 6 18 соответственно 35-25 м/ч. Однако станок имеет недостаточную
крутильную жёсткость мачты с открытой передней панелью и открытую схему циркуляции рабочей жидкости в системе гидропривода, что требует значительных объёмов жидкости по сравнению с системой замкнутого типа. Воронежским заводом горно-обогатительного оборудования серийно изготавливаются станки СБШ-250МНА-32 (рис. 6.15). Эти станки имеют
высокий уровень механизации операций по сборке и разборке бурового става, обеспечивают автоматизацию режимов бурения и горизонтирования станка.
Рис. 6.15. Станок шарошечного бурения СБШ-
250МНА 32:
1 – мачта, 2 – машинное отделение, 3 – гусеничные тележки, 4 – бак пылеподавляющий установки,
5 – передняя дверь кабины машиниста Основные конструктивные отличия – оборудование
верхнего привода вращения бурового става с непрерывным ходом подачи 8 м с воздушноводяной системой пылеподавления.
Станок СБШ-250-55 имеет следующие особенности: установка на мачте двух сепараторов, что позволяет бурить скважины глубиной до 55 м; трёхкратная
канатно-полиспастная система подачи от двух лебёдок; увеличенный наружный диаметр штанги (с 203 до 219 мм), обуславливающий рост скорости воздушного потока в затрубном пространстве с 25 до 45 м/с; механизированы вспомогательные операции по наращиванию бурового става в процессе бурения.
Станок СБШ-270ИЗ производства ОАО «Ижорские заводы» осуществляет проходку взрывных скважин в горных породах любой крепости при открытом способе добычи полезных ископаемых.
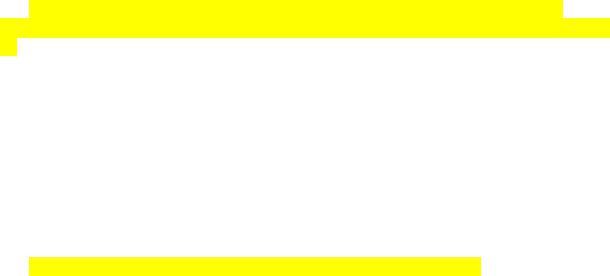
Буровой станок оборудован просторной кабиной, обеспечивающей оператору хороший обзор и работу с соблюдением всех норм безопасности по воздействию внешних факторов (шума, вибрации, запылённости, освещённости, температуры).
Основные технологические параметры бурения отображаются на цветных шкалах и цифровом индикаторе (глубина бурения, частота вращения бурового става, усилие подачи, нагрузка на двигатель вращателя, скорость проходки).
Механизмы станка (вращатель бурового става, подачи, хода) приводятся в действие двигателями постоянного тока с питанием от тиристорных преобразователей. Система управления обеспечивает высокую заводскую готовность, снабжена диагностикой с возможностью замены ячеек и блоков без подналадки системы.
Станок СБШ-320-36 предназначен для бурения скважин, диаметром 320 мм и глубиной до 36 м с осевым усилием до 600 кН в породах с коэффициентом крепости до 18. Ход непрерывной подачи (17,5 м) осуществляется двумя канатами, образующими четыре пятикратных полиспаста, два из которых расположены ниже головки бурового става, а два – выше. Привод лебёдок, на барабаны которых навиваются канаты, производится при бурении от гидромоторов, а при спуско-подъёмных операциях – электродвигателями. Увеличенный расход воздуха на единицу площади забоя по сравнению с другими станками позволяет повысить эффективность очистки скважины от продуктов разрушения и скорость бурения. Большая жёсткость металлоконструкции станка достигнута благодаря применению каркаса ферменного типа и установки станка при бурении на четыре гидродомкрата. В хвостовой части рамы установлено два кабельных барабана, позволяющих механизировать уборку и переноску кабеля при переездах станка.
Механическое оборудование станков
Станки шарошечного бурения для открытых горных работ имеют ходовую базу, раму, на которой устанавливается мачта с вращательноподающим механизмом бурового става, лебёдку подъёма става, механическое, электрическое, гидравлическое оборудование и компрессорную установку, размещённые в машинном отделении, кабину машиниста с пультом управления.
Перемещение станка для выполнения операций по обуриванию забоя осуществляется гусеничным или пневмоколёсным ходовыми механизмами. Все выпускаемые в России станки шарошечного бурения имеют гусеничный ход. Зарубежные фирмы изготавливают ряд типоразмеров станков на пневмоколёсном ходу (фирма "Роббинс" США).
В большинстве случаев станки шарошечного бурения имеют в качестве ходовой базы гусеничный ход экскаваторов (2СБШ-200-32 - Э- 1003, 2СБШ-200-40 - Э-1252, ЗСБШ-200-60 - Э-1602) или унифицированный гусеничный ход (6СБШ-200-40 - УГ-60, СБШ-250МНА- 32 - УГ-60М, СБШ-
250-55 - УГ-70). На ходовые тележки станка опирается платформа, представляющая собой сварную пространственную раму из профилированного проката. Сверху рама закрыта листовой сталью, для установки механизмов и оборудования. Оборудование, смонтированное на платформе, защищено кузовом от воздействия атмосферных осадков, пыли и низких отрицательных температур в зимний период.
Питание станка ЗСБШ-200-60 (см. рис. 6.14) электроэнергией от низковольтной сети переменного тока напряжением 380 В осуществляется посредством гибкого кабеля через кабельный барабан 7, управление станком
– из кабины 1. На гусеничные тележки 4 опирается платформа станка, на которой смонтирована мачта 9, устанавливаемая в рабочее и транспортное положение двумя гидроцилиндрами 3. В рабочем положении мачта фиксируется телескопическим подкосом 8, а транспортном – на задней опоре 6. Перед опусканием мачты в транспортное положение её необходимо отсоединить от передней опоры, а гидроцилиндры опустить до соприкосновения мачты с задней опорой. Перед бурением раму станка устанавливают
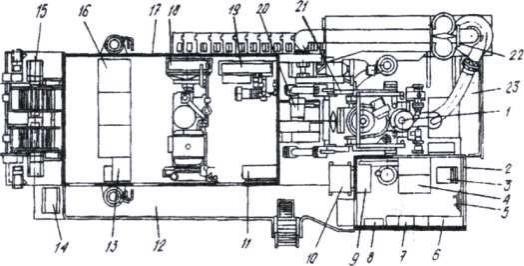
в горизонтальное положение четырьмя гидравлическими домкратами – передними 2 и задними 5.
В передней части платформы (рис. 6.16) по продольной оси станка на передней опоре 21 находится рабочий орган 1, все узлы которого смонтированы внутри мачты. Между рабочим органом и машинным отделением 17 на платформе размещена лебёдка 20 подъёма бурового става. С левой стороны передней части платформы (по ходу движения станка) расположена установка 22 сухого пылеулавливания с трёхступенчатой очисткой и замкнутым потоком. В задней части платформы размещены: машинное отделение, в котором установлены компрессорная установка 18 для удаления буровой мелочи из скважины и три станции управления 16; два настенных электрошкафа 13, гидросистема 19, состоящая из бака, силового и вспомогательного насосов, приводов, гидроблоков; вспомогательное оборудование. Машинное отделение представляет собой сварную панельную конструкцию с люками и проёмами в стенах и крыше для облегчения обслуживания во время эксплуатации станка и демонтажа оборудования при ремонте. В машинном отделении установлен верстак 11 с тисками для ремонтных работ. Необходимый для работы материал, долота и масла хранятся в приямке средней части платформы. Вход в машинное отделение – с площадки 12 кабины управления. На площадке размещён сварочный трансформатор 14. Для создания комфортных условий в машинном отделении установлены два осевых вентилятора.
Рис. 6.16. Размещение оборудования на платформе станка ЗСБШ-200-6
С правой стороны передней части платформы расположена кабина управления 2 – рабочее место машиниста станка. Конструктивно это сварная панель, снабжённая амортизаторами для снижения вибрации. В кабине предусмотрены две двери: входная со стороны машинного отделения и выходная со стороны рабочей площадки 23. Внутри кабины расположен пульт управления 4 станком, электрошкаф 9 с аппаратурой автоматизации процесса бурения, щит 8 управления кондиционером, шкаф 7 для одежды, тумбочка 6, откидное сидение 5 и огнетушитель. Перед пультом управления смонтировано поворачивающееся кресло 3 оператора. Стены кабины утеплены, пол (деревянный настил) покрыт линолиумом. На крыше кабины управления размещены прожекторы для освещения рабочего органа и пути передвижения станка, со стороны входной двери – кондиционер 10.
Для центрирования станка при передвижении необходимо отсоединить заднюю сторону передней опоры от задних кронштейнов и с помощью гидроцилиндров передвинуть её вместе с мачтой вперёд до упора, затем мачту зафиксировать в задней опоре. При передвижении станка питающий кабель автоматически разматывается или
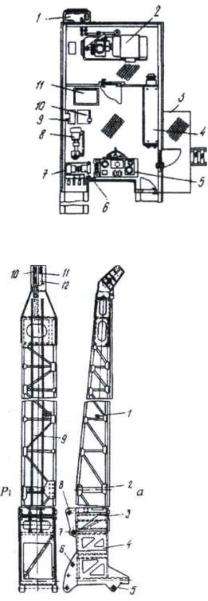
наматывается на кабельный барабан 15, смонтированный в задней части платформы. Рама станка СБШ-250МНА-32 (рис. 6.17) выполнена в виде сварного каркаса 7, об-
шитого металлическими листами. На раме размещено машинное отделение, в котором расположены насос пылеподавления 8, трансформатор 9, ящик для инструментов 10, выпрямитель 11, маслоохладитель 1 компрессора 2, трап машинного отделения 3, шкаф управления 4, маслонасосная станция 5 и насос закачки воды 6. Машинное отделение имеет дверные проёмы, герметизированные резиновыми уплотнениями. Для монтажа и демонтажа оборудования в средней части крыши машинного отделения предусмотрено два люка. В компрессорном отделении имеются две боковые двери и съёмный люк крыши.
Рис. 6.17. Машинное отделение станка СБШ-250МНА-32
Мачты станков шарошечного бурения представляют собой сварные пространственные фермы из профильной стали открытой или закрытой конструкции. Мачты открытой конструкции, позволяющие лучший доступ
к буровому ставу и приводу вращателя станка, применены на станках 2СБШ-200-32, 2СБШ- 200-40 и 6СБШ-200-40 конструкции СКБ ИГД им. А.А. Скочинского.
Мачта станка 6СБШ-200-40 (рис. 6.18) – сварная пространственная разъёмная ферма, состоящая из основания 4 и собственно мачты 2, шарнирно соединённых между собой осью 7.
В рабочем положении мачта с основанием фиксируется двумя накидными болтами 3. Для бурения направленных скважин конструкция станка допускает наклон мачты в плоскости, продольной оси станка. Осью поворота мачты при этом служат два передних шарнира 5, с помощью которых основание мачты крепится к раме станка.
Рис. 6.18. Мачта станка 6СБШ-200-40
Кроме того, основание имеет два сектора с тремя отверстиями 6 для фиксации мачты под нужным углом бурения (90, 75, 60 град, к горизонтали). Положение мачты в пространстве определяется совмещением определённого отверстия сектора с опорным пальцем на платформе станка. При переводе мачты из рабочего в транспортное положение откидывают болты 3, и мачта 2 поворачивается относительно оси 7, переводится в горизонтальное положение при неподвижном вертикальном основании 4.
Наклон мачты для бурения скважин, опускание её в транспортное и подъем в рабочее положение производится двумя гидроцилиндрами, штоки которых шарнирно соединены с осями 8. В передней плоскости мачты крепятся направляющие вертлюга. Передвижение вертлюга по направляющим 9 осуществляется с помощью системы блоков для подъёмного каната, один конец которого закреплён на барабане лебёдки, а другой огибает блоки 1, 10, 11, 12, установленные на мачте, и крепится к вертлюгу.
Для ограничения грузоподъёмности блок 12 установлен на рычаге, один конец которого шарнирно прикреплён к мачте, а другой подпружинен. При достижении предельного натяжения каната пружина сжимается, и рычаг воздействует на конечный выключатель, отключающей двигатель лебёдки.
В отличие от станков 2СБШ-200-32, 6СБШ-200-40, где мачты разъёмные и состоят из шарниров соединённых между собой основания и мач-
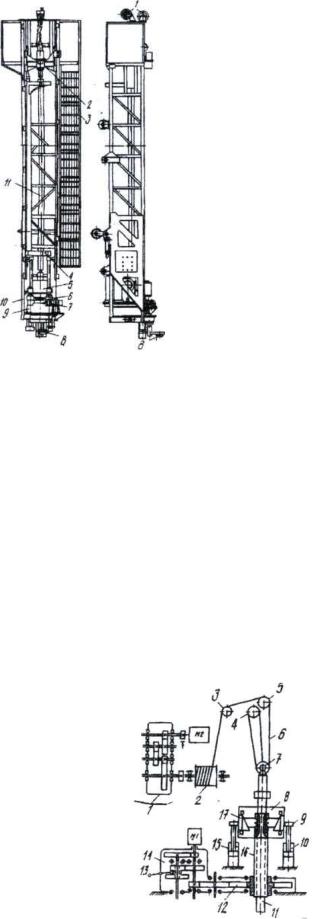
ты, в рабочем органе станка ЗСБШ-200-60 (рис. 6.19) мачта цельная и шарнирно соединена с передней опорой.
Лебёдка подъёма бурового става смонтирована на платформе. Механизм подачи штанг (кассета) 4 расположен внутри мачты. Такая конструкция обеспечивает наклон мачты в плоскости продольной оси станка и позволяет бурить вертикальные и наклонные скважины. Передняя опора, являющаяся основанием мачты, крепится к платформе с помощью двух шарниров, образующих ось поворота мачты. Рабочий орган оснащён лестницей с площадкой. Мачта представляет собой сварную конструкцию из труб квадратного сечения и листового металла с открытой передней панелью.
Рис. 6.19. Мачта станка 3СБШ-200-60
В качестве привода вращателя рабочего органа установлен электродвигатель постоянного тока ДЭВ-808 мощностью 68 кВт с управлением от тиристорного преобразователя. На мачте смонтированы: вращателъно-подающий механизм (вращатель 9,
лестница 3, гидропатрон 5, два напорных гидроцилиндра 6), механизм подачи штанг 4 (кассета со штангами 11 и цилиндр поворота кассеты), механизм развинчивания бурового става (гидроключ) 7, блоки 1 подъёмного каната, вертлюг 2, гидроцилиндры 10 установки мачты в рабочее и транспортное положения, приспособление для смены долота 8.
Сборка и разборка бурового става осуществляется с помощью механизма подачи штанг-кассеты 4, которая вмещает 4 буровые штанги, фиксируемые в гнёздах нижнего и верхнего секторов, соединённых трубой. На штангах и нижнем секторе кассеты имеются риски, облегчающие установку штанг в соответствующие гнезда кассеты. Кассета устанавливается на кронштейны и люнет, прикреплённые к мачте. Гидроцилиндром, прикреплённым к мачте, кассета поворачивается с подачей штанг на ось бурения. Кроме четырёх штанг в кассете имеется пятая штанга, соединённая с вертлюгом и забурником. При наращивании или укорачивании бурового става 11 кассета подаётся на ось бурения и тогда производится свинчивание или развинчивание штанг.
На мачте станка СБШ-250МНА-32 (рис. 6.20) смонтированы механизмы, с помощью которых выполняются основные операции процесса бурения: спуск и подъем бурового става; создание осевого усилия на долоте; вращение инструмента; сборка и разборка бурового става; подвод воз- душно-водяной смеси к забою скважины.
Рис. 6.20. Мачта станка СБШ-250МНА-32
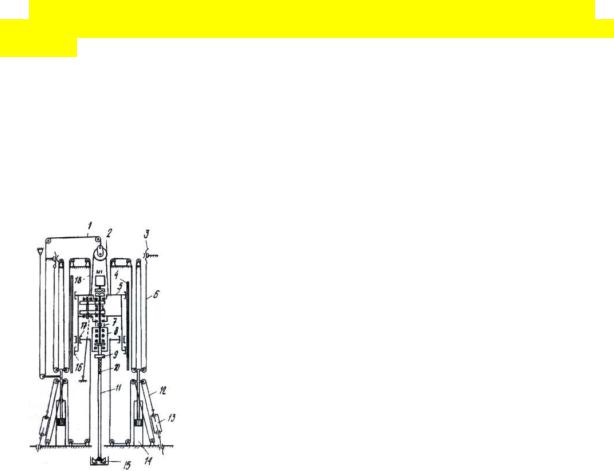
Каркас 1 мачты представляет собой сварную пространственную ферму, пояса которой выполнены из равнобокого уголка, а решётка из уголков и швеллеров. Нижняя 8, средняя и верхняя 19 обвязки выполнены из швеллеров. К средней обвязке приварены цапфы 12, которыми мачта устанавливается в подшипниках, расположенных в кронштейнах машинного отделения. На цапфах происходит поворот мачты при установке её в рабочее или транспортное положение. Балка 14 служит для упора штоков гидроцилиндров подъёма мачты.
Вдоль всего каркаса с двух сторон закреплены направляющие швеллеры 15, по которым в процессе бурения перемещаются вращатель 16 и натяжная каретка 18. Вращатель вместе с буровым ставом поддерживается канатами 2 механизма подачи. Верхние блоки механизма подачи закреплены на верхнем поясе каркаса мачты, а нижние блоки и гидроцилиндры – на нижнем поясе. На нижнем поясе каркаса находится механизм 9 свинчивания и развинчивания штанг.
На средней обвязке мачты устанавливается прожектор 13 для освещения в тёмное время суток механизмов, находящихся в верхней части мачты. В верхней части направляющих швеллеров во избежание переподъема вращателя при разборке бурового става установлен конечный выключатель 17. К задней стенке мачты на подшипниковых опорах крепится сепаратор, в котором устанавливаются три буровые штанги. Для предотвращения попадания шлама в механизм свинчивания нижний торец мачты закрыт отбойным щитом. Для питания гидроцилиндров, предназначенных для выполнения вспомогательных операций, служит блок гидроаппаратуры 10. Внизу на мачте смонтирована установка 7 для отдува буровой мелочи от устья скважины, а вверху таль – грузоподъёмностью 0,5 т. Мачта снабжена лестницей для осмотра, ремонта и ухода за мачтой, головкой бурового снаряда 3 и вращателем 16.
Вращательно-подающие механизмы
По принципу устройства и передачи буровому ставу вращения, подачи и осевого усилия вращательно-подающие механизмы станков шарош-ечного бурения выполняются двух типов. Станки ЗСБШ-200-60 и 6СБШ- 200-40 имеют вращательно-подающий механизм патронного типа с нижним расположением вращателя. Такой механизм выполняет в процессе бурения основные (вращение и подача бурового долота на забой) и вспомогательные по сборке и разборке бурового става операции. Механизм патронного типа станка ЗСБШ-200-60 (рис. 6.21) состоит из вращателя 14, закреплённого на платформе станка гидропатрона 8 и двух гидроцилиндров подачи 10 и 15. Двигатель M1 постоянного тока мощностью 60 или 68 кВт в зависимости от модификации станка через двухскоростной редуктор, переключаемый рычагом 13, передаёт вращение полому шестигран-
Рис. 6.21. Кинематическая схема вращательноподающего механизма патронного типа станка 3СБШ-200- 60
ному шпинделю 16, проходящему через ступицу ведущей шестерни 12 редуктора. Внутри шпинделя 16 проходит буровой став 11, который получает вращение от шпинделя через зажимные кулачки 17 гидропатрона 8. Патрон посредством траверсы 9 и гидроцилиндров перемещается на длину хода поршней, передавая буровому ставу усилие подачи. Основной недостаток такого вращательно-подающего механизма – ограниченный рабочий ход подачи, равный 1 м. Это требует разжатия
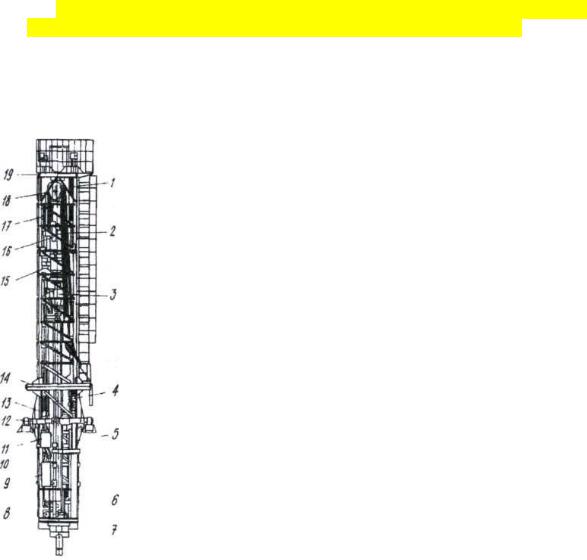
кулачков и холостого подъёма патрона в исходное положение после каждого рабочего хода подачи, что увеличивает затраты времени на выполнение вспомогательных операций и усложняет зажатие и освобождение бурового става кулачками гидропатрона при обмерзании штанг продуктами разрушения в зимний период.
Маневровые подъем и опускание бурового става после окончания бурения скважины или а целях её очистки в процессе бурения осуществляется с помощью лебёдки, состоящей из асинхронного двигателя М2, трёхступенчатого редуктора 1 и барабана 2. На барабан навивается канат 6, огибающий систему блоков 3-4-5, которые установлены на верхнем конце мачты, и блок 7, закреплённый на вертлюге бурового става.
Нижнее расположение вращателя позволяет сместить центр тяжести станка вниз, получить облегчённую конструкцию мачты и повысить устойчивость станка при переездах с поднятой мачтой.
Станки СБШ-250МНА-32, СБШ-250-55 и СБШ-320-36 имеют вращательноподающий механизм шпиндельного типа с канатной системой подачи. В этом случае возможна непрерывная подача на длину штанги и благодаря этому отсутствие холостых перехватов при подаче инструмента на забой, а следовательно, существенное сокращение затрат времени на выполнение вспомогательных операций и повышения производительности станка. Согласно кинематической схеме вращательно-подающего механизма с канатно-полиспастной системой подачи станка СБШ-250МНА-32
(рис. 6.22) вращение от электродвигателя M1 мощностью 68 кВт постоянного тока через зубчатую муфту и шлицевой вал передаётся входному валу двухступенчатого редуктора 5.
От выходного вала редуктора вращение получает шинно-шлицевая муфта 7, служащая для предохранения электродвигателя и редуктора от вибрации. Через опорный узел 8 на вращающийся буровой снаряд (9, 10, 11, 15) передаётся осевое усилие от нижних канатов механизма подачи, закреплённых на ползунах 17 опорного узла, Каретки 16 вращателя движутся по направляющим 4 мачты. Опорный узел 8, в свою очередь, может перемещаться относительно кареток. Электродвигатель с редуктором и блоком 2 подвешен на канатах 18 и 1.
Каретка вращателя через полиспастную систему соединена со штоком одного из гидроцилиндров подачи 14. Ниже опорного узла расположено сальниковое устройство для подачи воздуха или воздушно-водяной смеси в буровой став. Четырёхкратная полиспастная система производит подачу вращателя на 8 м при ходе поршня 2 м и состоит из канатов 6 и 12, концы которых соединены с кареткой вращателя. При движении штоков цилиндров вверх натягиваются нижние канаты и вращатель движется вниз.
Рис. 6.22. Кинематическая схема вращательно-подающего механизма шпиндельного типа станка СБШ-250МНА-32
При опускании штоков натягиваются верхние канаты и происходит подъем вращателя. Натяжение канатов регулируется спомощью, винтовых устройств 3 и 13. Осевое усилие подачи создаётся с помощью гидроцилин-
дров. На станках СБШ-320-36 осевое усилие создаётся регулируемым гидродвигателем, соединённым через редуктор с барабаном лебёдок подачи (рис. 6.23).
Буровой став приводится во вращение от двигателя M1 постоянного тока через двухступенчатый редуктор 2 и шинно-зубчатую муфту 4. Принципиально устройство вращателя станка СБШ-320-36 аналогично устройству вращателя станка СБШ-250МНА- 32. Осевое усилие до 600 кН на буровой став 11 передаётся через опорный узел 5 двумя канатами 9, образующими пятикратные нижние полиспасты.
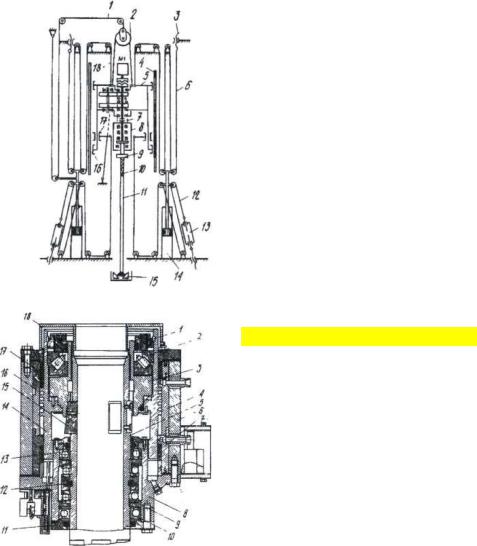
Подвижные блоки 6 полиспастов установлены на раме опорного узла, а неподвижные 10 – закреплены в основании мачты. Канаты 9 огибают желобчатые барабаны 7 и 8 лебёдок подачи и далее идут к неподвижным блокам 1, установленным в верхней части мачты, образуя пятикратные полиспасты. Подвижные нижние блоки 3 закреплены на вращателе. При бурении вращатель опускается вслед за опорным узлом. Лебёдки подачи при бурении приводятся от гидродвигателей М3 и обеспечивают регулируемую по скорости и осевому усилию подачу инструмента на забой, а при спускоподъёмных операциях – от электродвигателей М2. Одновременно включение двигателей исключается. Рабочая подача бурового инструмента на забой производится в режиме
«Бурение», остальные перемещения – в режиме «Вспомогательные операции».
Рис. 6.23. Кинематическая схема вращательно-подающего механизма с канатно-полиспастной системой подачи станка
СБШ-320-36
Гидропатрон станка ЗСБШ-200-60 обеспечивает зажатие бурового става и передачу ему усилия подачи на забой. Гидропатрон (рис. 6.24) установлен на верхнем круглом конце шестигранного пологого шпинделя
5 и смонтирован в расточке траверсы 6, имеющей у основания четыре отверстия. Два отверстия расположенные по центральной оси служат для крепления штоков гидроцилиндров подачи, а два, смещённые по отношению к оси, – для крепления бронзовых втулок, скользящих по направляющим патрона. Направляющие неподвижно закреплены на мачте станка и коробке передачи вращателя.
Рис. 6.24. Гидропатрон станка 3СБШ-200-60
Снизу к траверсе болтами крепится корпус 8, в котором смонтирована опора шпинделя, состоящая из двух упорных 9 и двух радиальных 10 подшипников и разрезного кольца 12.
Корпус сверху и снизу закрыт крышками 11 с уплотнениями. Усилие подачи от траверсы 6 на вращающийся шпиндель 5 передаётся через корпус 8, верхнюю крышку, наружную обойму верхнего радиального подшипника 13, упорный подшипник и разрезное кольцо 12.
Во внутренней расточке траверсы смонтирована гильза 4, в которой перемещается поршень 14 с уплотнительными кольцами 16. Полости между поршнем и гильзой сверху и снизу закрыты уплотнениями 17 и через каналы в гильзе 4 и нижнем 7 установочном кольце соединены с гидросистемой станка. При подаче масла в верхнюю полость поршень 14 начинает смещаться вниз и через гайку 1 и радиально-упорный шарикоподшипник 2 воздействует на планшайбу 3, надетую на верхний конец шпинделя и вращающуюся вместе с ним. Вращаясь вместе со шпинделем, планшайба может скользить вдоль него и воздействовать своими скошенными пазами на сопряжённые с ней скошенные поверхности трёх кулаков 15. Установленные в окнах шпинделя кулачки, перемещаясь, зажимают штангу и передают ей осевое усилие и крутящий момент. При поступлении масла в нижнюю полость поршень поднимается и через подпятник поднимает планшайбу. При этом кулачки освобождаются и разжимают штангу. Для
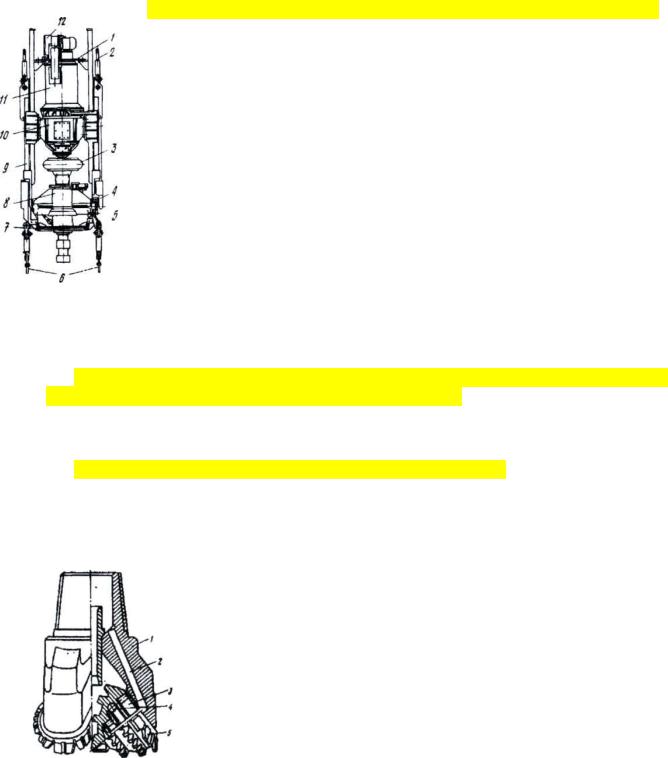
предотвращения попадания пыли и влаги в гидропатрон на него надета крышка 18. Крайнее верхнее и нижнее положения гидропатрона на величину рабочего хода ограничиваются конечными выключателями, на который воздействует упор, закреплённый на траверсе патрона.
Вращатель бурового става станка СБШ- 250МНА-32 (рис. 6.25) состоит из электродвигателя и редуктора, опорного узла и шиннозубчатой муфты.
Приводом вращателя является электродвигатель 11 постоянного тока, соединённый через фланец с редуктором 10, которому он передаёт вращение. К корпусу редуктора прикреплены каретки 9, служащие для направления движения вращателя вдоль мачты. Концы кареток скреплены траверсой 7 и фланцем 1, на котором смонтирован вентилятор 12 охлаждения двигателя. На выходном валу редуктора посажена шинно-зубчатая муфта 3, соединяющая его со шпинделем опорного узла 8.
Рис. 6.25. Вращатель бурового става станка СБШ-250МНА-32
На цапфах узла крепятся шарниры 5, служащие для передачи осевого усилия от канатов 6. Подъем става осуществляется с помощью канатов 2. При подъёме и опускании вращатель скользит по направляющим мачты вкладышами 4. Опорный узел, в свою очередь, может перемещаться по кареткам на некоторое расстояние.
Породоразрушающий буровой инструмент
Работа станков шарошечного бурения в значительной степени зависит от правильного выбора и эксплуатации породоразрушающего инструмента. Отсутствие опыта в подборе шарошечных долот для конкретных условий обуславливает неудовлетворительное использование высокопроизводительных буровых станков, получение низкой скорости и высоких затрат на бурение [3].
Буровой породоразрушающий инструмент представляет собой шарошечное долото, выполненное из корпуса и шарошек, свободно вращающихся на цапфах (рис. 6.28). Корпус долота сваривается из секций 1, на цапфах 3 каждой из которых с помощью подшипников 4 устанавливается шарошка 5. Шарошка является рабочей частью долота и представляет собой конус, на поверхности которого расположены фрезерованные или
твердосплавные зубья. Под воздействием осевого усилия при перекатывании шарошек по забою они зубьями взаимодействуют с забоем скважины, создавая в породе напряжения, превышающие прочность породы и вызывающие её разрушение. Разрушенная порода удаляется с забоя сжатым воздухом или промывочным раствором. В долотах с продувкой дополнительно в лапах и цапфах сверлят каналы 2 для направления части потока сжатого воздуха в опоры шарошек для их охлаждения, смазки и предотвращения зашламовывания.
Рис. 6.28. Устройство шарошечного долота
Верхняя часть корпуса долота заканчивается резьбовым ниппелем, с помощью которого долото соединяется со ставом буровых штанг. При
вращении бурового става вращается корпус долота и шарошки. Причём частота вращения шарошки во столько раз больше частоты вращения долота, во сколько раз диаметр долота больше диаметра основания конуса шарошек.
Величина усилий, воздействующих зубьями на породу, пропорциональна усилию подачи, создаваемому на долоте и частоте вращения, Эта величина тем больше, чем дальше расположен зуб от оси скважины. Зубья, расположенные на вершине шарошек,
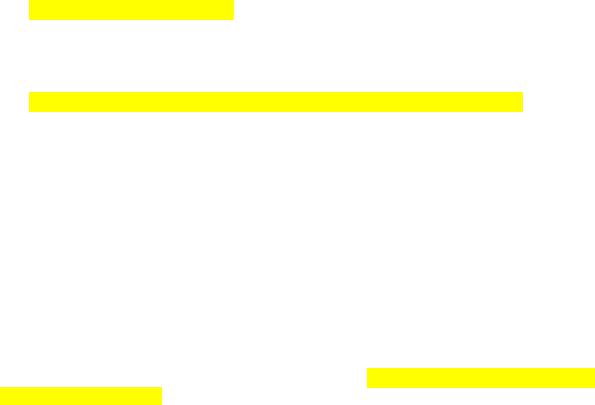
работают в почти безударном режиме и разрушают породу, благодаря смятию и скалыванию при проскальзывании. Зубья, расположенные у основания конуса шарошек, имеют наибольшую энергию удара и разрушают породу ударом и скалыванием.
Шарошечные долота работают в тяжёлых условиях, подвергаясь интенсивному истиранию и высоким динамическим нагрузкам. Поэтому к материалу долот предъявляются повышенные требования. Сталь шарошек должна обладать высокой прочностью и вязкостью, чтобы не происходило поломок и смятия зубьев. Она должна иметь повышенную износостойкость рабочих поверхностей. Наиболее полно этим требованиям удовлетворяют конструкционные легированные цементируемые малоуглеродистые стали. Шарошки изготавливают из легированных малоуглеродистых сталей. Для увеличения твёрдости поверхность шарошек цементируют на глубину 1,5-2 мм, а затем закаливают. Для уменьшения износа долот по диаметру тыльную сторону шарошек армируют трубчато-зернообразным сплавом ТЗ или цилиндрическими вольфрамокобальтовыми стержнями.
Долота классифицируются по числу шарошек на одно- и двух-, трёх, четырёх- и многошарошечные. Трехшарошечные долота являются наиболее распространёнными. Они хорошо сочетают в себе достаточную динамичность работы, устойчивость на забое
имеханическую прочность опор. Многошарошечные долота применяются для бурения скважин большого диаметра (более 600 мм).
Долота различают также по геометрии наружной поверхности шарошек с одно- и многоконусными шарошками, самоочищающиеся и несамоочищающиеся, со смещёнными осями и без смещения осей. В долотах самоочищающегося типа зубчатый венец одной шарошки входит в межвенцовую впадину второй шарошки, что позволяет выполнить шарошки большого диаметра и разместить в них более прочные опоры. Кроме того, самоочищающиеся долота хорошо работают в вязких, склонных к слипанию породах. В зависимости от условий применения выпускают зубчатые, зубчато-штыревые
иштыревые долота. Зубчатые долота разрушают породу на забое стальными фрезерованными зубьями, а штыревые – штырями из твёрдого сплава, запрессованными или впаянными в тело шарошек.
Шарошки свободно вращаются на цапфах. Шарошки долот малого диаметра вращаются на подшипниках скольжения с одним шариковым замковым рядом. В шарошках долот большого диаметра предпочтение отдают роликовым подшипникам. Для получения наилучших показателей при шарошечном бурении необходимо производить выбор параметров долот в соответствии с горногеологическими условиями работы и физикомеханическими свойствами буримых пород. Под параметрами шарошечного инструмента понимают конструктивные особенности, характеризующие эффективность разрушения породы на забое, стойкость долота в целом и его отдельных элементов, т. е. работоспособность инструмента. Анализ конструкций серийно выпускаемых шарошечных долот позволяет выделить три группы параметров; геометрическая форма шарошек и их размещение относительно оси долота; геометрическая форма зубьев, их количество, расположение и характер армирования; тип опоры шарошек и наличие обдува подшипников или их герметизации. Каждый из названных параметров оказывает определённое влияние на эффект разрушения породы и долговечность отдельных рабочих элементов долота. Поэтому при выборе шарошечного долота необходимо, чтобы основные его параметры соответствовали условиям бурения. Это позволит получить высокую производительность при проходке скважин и наибольший срок службы инструмента, т.е. обеспечить наилучшие технико-экономические показатели при бурении.
Геометрическая форма шарошек и их размещение относительно оси долота оказывает существенное влияние на характер разрушения породы на забое и долговечность рабочих элементов долота. В зависимости от геометрической формы шарошки могут быть одно- и многоконусные, иметь совершенный или несовершенный конус. Последнее характеризует степень проскальзывания зубьев при перекатывании шарошек по забою и величину