
Котиков Г.С. Учебное пособие Сварка и резка металлов
.pdf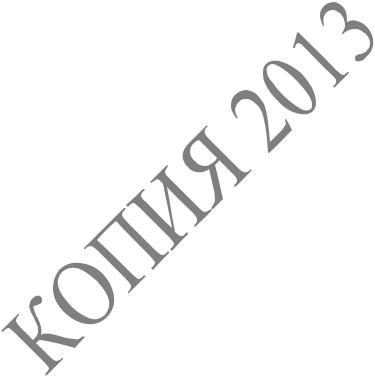
Рудно-кислые покрытия. В них входят окислы железа и марганца, кремнезем, ферромарганец. Вводят органические добавки (целлюлозу, крахмал), которые при сгорании образуют защитные газы. При плавлении идет интенсивная экзотермическая реакция, повышающая скорость расплавления. При большом содержании марганцевой руды образуется дым вредный для сварщика.
Рутиловые покрытия. Помимо рутила, состоящего, в основном, из двуокиси титана TiO2, в покрытие введен кремнезем, ферромарганец, карбонаты кальция или магния. По технологическим качествам покрытия близки к рудно-кислым, но дают лучшее формирование сварного шва, меньшее разбрызгивание металла и выделение газов.
Фтористо-кальциевые покрытия. В них входят ферромар-
ганец, плавиковый шпат, карбонаты кальция и магния. Газовая защита ванны обеспечивается двуокисью и окисью углерода, образующихся при разложении карбонатов под действием температуры.
Органические покрытия. Состоят, в основном, из оксицеллюлозы, к которой добавлены шлакообразующие материалы, двуокись титана, силикаты, легирующие присадки и в качестве раскисляющих - ферромарганец. Электроды с такими покрытиями особенно пригодны для работ в монтажных и полевых условиях. Рассмотрим несколько составов электродных покрытий.
Рудно - кислые. Титановый концентрат (титанат закиси железа FeOTiO2) 37%; марганцевая руда (перекись марганца) 21%; полевой шпат (силикат алюминия, натрия и калия) 13%; ферромарганец (содержит 70% Mn) 20%; крахмал 9%.
Рутиловые. Рутил (минерал, состоящий, в основном, из TiO2) 48%; магнезит (минерал, состоящий, в основном, из MgCO2) 5%; полевой шпат 30%; ферромарганец 15%; декстрин (производная крахмала) 2%.
Фтористо - кальциевые. Мрамор 53 - 61%; плавиковый шпат 15 - 18%; кварц 0 - 9%; ферромарганец 2 - 7%; ферросилициум 3 - 10%; ферротитан 9 - 15%.
21
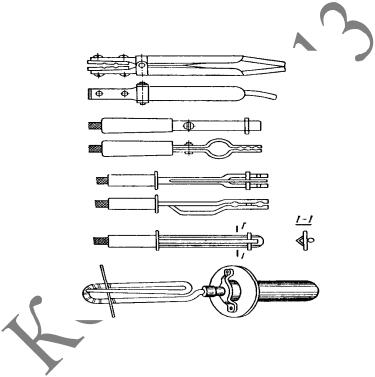
7. Ручная дуговая сварка плавящимся электродом
Рабочее место сварщика со всеми необходимыми приспособлениями и подводом сварочного тока называется сварочным постом. Изделия небольших размеров укладывают для сварки на сварочный стол высотой 500-700 мм, рабочей поверхностью которого служит стальная или чугунная плита. Очень часто организуется передвижное рабочее место сварщика, огражденное переносными щитами. Это практикуется при сварке изделий больших размеров в заводских условиях, а также в условиях монтажных и ремонтных площадок.
Рис. 7.1. Различные конструкции держателей электродов
Основным рабочим инструментом сварщика является держатель электродов, от которого в значительной мере зависит удобство работы. Держатель должен прочно удерживать электрод, обеспечивать надежный контакт и допускать быструю и удобную смену электродов без прикосновения к токоведущим и нагретым металлическим частям держателя. Держатель должен иметь минимальный вес и удобный захват. Ток к держателю подводится гибкими проводами, не стесняющими движения руки сварщика. Некоторые конструкции держателей электродов
22
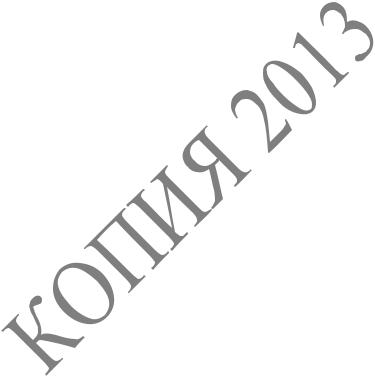
показаны на рис. 7.1.
Для защиты от ожогов сварщик надевает брезентовый комбинезон, а голову защищает от искр и брызг металла специальной шапкой. Для защиты кистей рук от ожогов и излучений дуги сварщик надевает брезентовые рукавицы. Лицо сварщика защищается от ожогов и излучений дуги щитком. Щиток имеет смотровое окошко со специальным защитным цветным стеклом, задерживающим опасные излучения дуги. Снаружи цветное стекло защищается бесцветным сменным стеклом, воспринимающим брызги металла.
Для очистки металла сварщик пользуется щетками из стальной проволоки, зубилами и специальными молоточками для отбивания шлака. Для проверки размеров шва сварщик пользуется калибрами и шаблонами. Для замера сварочного тока каждый сварочный пост имеет амперметр, расположенный удобно для сварщика.
7.1. Зажигание дуги
В начальный момент воздух между концом электрода и основным металлом не ионизирован и не проводит электрического тока. Зажигание дуги может быть осуществлено двумя приемами. Можно повышать напряжение между электродом и изделием, пока не произойдет пробой газового промежутка; возникающий при этом искровой разряд автоматически переходит в дуговой. Для пробоя промежутка между электродами около 1 мм требуется напряжение порядка 1000 В . В этом случае для зажигания используется вспомогательный ток высокого напряжения и высокой частоты, не оказывающий физиологического действия на человека, то есть применяются описанные ранее осцилляторы.
На практике обычно дуга зажигается предварительным замыканием электрода на изделие. Прикосновением электрода к изделию замыкается накоротко сварочная цепь, в которой возникает ток замыкания, создающий магнитное поле. Одновременно при замыкании происходит разогрев и оплавление металла в точках соприкосновения электрода с изделием. При отрыве электрода и размыкании цепи энергия исчезающего магнитного поля повышает напряжение на промежутке разрыва. С повыше-
23
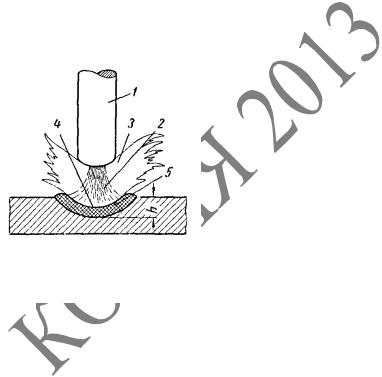
нием напряжения пробивается слой газа между электродом и изделием, что вызывает возникновение разряда, в котором энергия магнитного поля переходит сначала в электрическую, а затем в тепловую, нагревающую газ и создающую ионизацию газового промежутка.
При зажигании дугового разряда проходит стадия его развития и перехода в стационарную форму. Стационарный разряд характеризуется равенством мощностей, получаемых разрядом из цепи и отдаваемых окружающему пространству. Если получаемая мощность больше отдаваемой, то идет развитие разряда; если отдаваемая мощность больше получаемой, то интенсив-
ность разряда уменьшается и наступает его затухание. Процесс развития нормального дугового разряда от момента зажигания до достижения стационарного состояния занимает несколько десятых долей секунды.
В установившейся сварочной дуге конец электродного стержня и поверхность изделия расплавлены, так что дуга горит между жидкими электродами. Столб дуги имеет обычно коническую или сфе-
рическую форму, расширенную от электродного стержня к изделию (рис. 7.2). Пламя имеет значительные размеры и содержит, главным образом, пары материалов электродов, реагирующие с окружающим атмосферным воздухом. Поверхность жидкой ванны на изделии не остается плоской, так как действием механических сил, создаваемых дугой, или так называемого дутья дуги, поверхность жидкого металла вдавливается.
Образующееся углубление или ямка в жидком металле называется кратером. Длина дуги в нормальных условиях сварки должна быть малой; обычно она равняется (или меньше) диаметру применяемого электрода. Действием дуги металл рас-
24
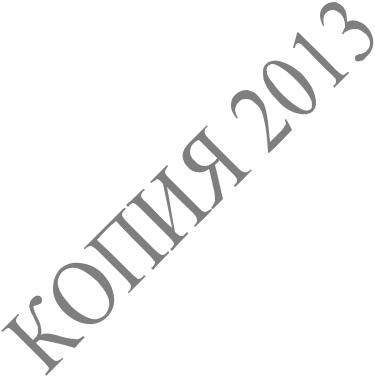
плавляется на глубину, называемую глубиной расплавления или глубиной провара.
7.2. Плавление и перенос металла
Плавление электрода под действием дуги происходит равномерно по следующей приближенной зависимости, установленной опытным путем:
q= I t г/А ч ,
где g - количество расплавленного электродного металла; а - коэффициент плавления, определяемый опытным путем; / - ток дуги; t - время горения дуги.
В процессе сварки происходят потери жидкого металла вследствие его окисления воздухом и через шлак, а также вследствие испарения и разбрызгивания за пределы ванны. Все эти процессы создают так называемые потери металла на угар и разбрызгивание.
Приращение массы изделия в результате сварки (или вес наплавки) равняется весу расплавленного электродного металла за исключением потери на угар и разбрызгивание.
Масса наплавки определяется по формуле
qn = q - q или qn = n I t.
Условно в среднем можно принимать gn = 0,87g. Непосредственным наблюдением не удается уловить процесс
перехода расплавленного металла с электрода в ванну. Применение более мощных средств исследования, в том числе скоростной киносъемки, показало, что основная часть электродного металла переходит на изделие в форме капель, причем наблюдаются две формы переноса - крупнокапельная и мелкокапельная или струйная. При крупнокапельном переносе на конце электрода образуется капля жидкого металла, которая быстро увеличивается, затем быстро движется вперед, вытягиваясь по направлению к изделию. При этом происходит или полное замыкание дугового промежутка мостиком жидкого металла, или заметное его укорочение. Затем мостик жидкого металла разрывается так, что большая часть металла остается на изделии, меньшая - на электроде, и дуга приобретает нормальную длину. Процесс повторяется с довольно правильной периодичностью и сопровождается переносом на изделие 20 - 50 капель в секунду,
25
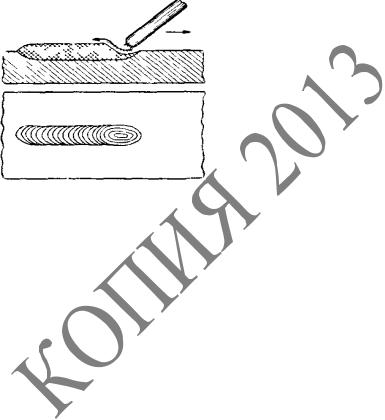
приблизительно одинакового размера.
Наряду с переносом более или менее крупных капель происходит также перенос очень мелко раздробленного расплавленного жидкого металла – мелкокапельный или струйный перенос.
Металл электрода, попадая в ванну, перемешивается с основным металлом, образуя металл шва. Дутье газов дуги оказывает механическое давление на металл шва и отбрасывает его со дна на поверхность (рис. 7.3). Отбрасывание происходит пульсациями, что придает поверхности наплавленного металла чешуйчатость. Крупнокапельный перенос дает грубую и крупную чешуйчатость, а мелкокапель-
ный - более гладкую и почти не заметную чешуйчатость шва. Наплавка металла на изделие возможна как в нижнем поло-
жении, когда поверхность изделия горизонтальна и перенос металла с электрода на изделие происходит сверху вниз в направлении действия силы тяжести, так и в вертикальном или в потолочном положении. При потолочном положении сварки расплавленный металл должен переноситься с электрода в ванну снизу вверх против направления действия силы тяжести. Возможность вертикальной и, в особенности, потолочной сварки доказывает, что процесс переноса металла в сварочной дуге не является простым падением капель под действием силы тяжести. Перенос металла производится совместным действием многих факторов.
Различные исследования показали, что перенос металла всегда происходит от изделий малых размеров к большим. Крупно- и мелкокапельный перенос - это поток капель жидкого металла от электрода к изделию. Крупнокапельный перенос происходит преимущественно при работе на малых токах электродами с
26
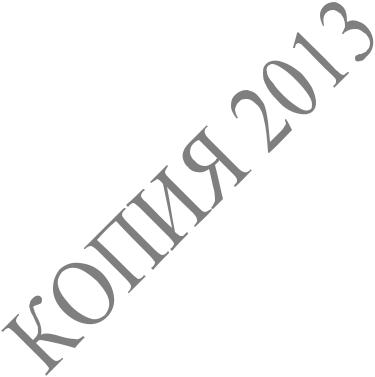
тонкой обмазкой. С увеличением тока и количества обмазки на электроде процесс приближается к мелкокапельному.
7.3. Нагрев металла дугой
Интенсивность нагрева металла дугой определяется в первую очередь мощностью дуги. Она зависит и от ряда других факторов, таких как род и полярность тока, материал электрода, расположение дуги по отношению к металлу и др. Не вся мощность дуги используется для нагрева металла - неизбежны потери мощности на излучение, теплообмен с окружающей средой, потери вместе с испаряющимся и разбрызгиваемым металлом, на нагрев шлаков и т. д.
Мощность дуги, расходуемая на нагрев металла, называется эффективной мощностью Qэф, кал/сек.
Значение отношения эффективной мощности к полной называется эффективным к. п. д. процесса нагрева металла дугой и обозначается эф.
Для различных случаев дуговой сварки это отношение приведено в таблице.
Элек- |
Непла- |
Плавящийся с |
Плавящийся с |
Плавящийся для |
трод |
вящийся |
тонким по- |
качественным |
сварки под |
|
|
крытием |
покрытием |
флюсом |
эф |
0,5-0,65 |
0,65-0,75 |
0,7-0,85 |
0,80-0,90 |
Величина к.п.д. может колебаться в довольно широких пределах. Тепловая мощность дуги Qэф расходуется на плавление основного металла и электрода.
Электрод в дуге нагревается двояким путем. Конец электрода нагревается за счет бомбардировки его заряженными частицами. При постоянном токе I = const мощность, расходуемая на оплавление конца электрода, остается приблизительно постоянной. Вследствие быстроты плавления электрода нагрев конца электрода не успевает распространиться на длину более 1 см. Кроме того, электрод дополнительно прогревается равномерно по всему объему за счет джоулева тепла проходящего по электроду тока:
q=0,24 I2 R t,
где R - сопротивление электрода.
27
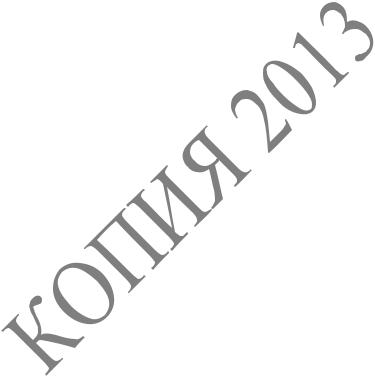
Нагрев вызывает увеличение сопротивления электрода и соответственно увеличение количества джоулева тепла.
Несмотря на постоянство тепловыделения на конце электрода, скорость его плавления растет за счет нагрева джоулевым теплом. Значительное ускорение плавления электрода нежелательно, так как нарушается нормальное соотношение между количеством расплавленного основного и электродного металла.
Чрезмерное ускорение плавления электрода к концу его использования является одним из факторов, ограничивающих увеличение тока для данного электрода. Равномерность плавления электрода способствует покрытие электрода, оно не проводит тока, не нагревается джоулевым теплом и охлаждает стержень электрода, не давая ему разогреться.
Значительно сложнее процесс нагрева дугой свариваемого изделия. Здесь суммируются непосредственное воздействие дуги на основной металл и перенос тепла вместе с каплями электродного металла. Для проведения расчетов и создания общей картины процесса прибегают к упрощенным моделям, при следующих условиях:
1)нагреваемый металл принимают за полубесконечное тело, т.е. его толщина значительно превышает глубину расплавления;
2)источник тепла считают точечным, что допустимо при рассмотрении нагрева в точках, находящихся от источника тепла на расстояниях, значительно превышающих радиус пятна нагрева;
3)допускают, что источник тепла действует непрерывно с постоянной тепловой мощностью.
Рассмотрим сначала нагрев металла неподвижным источником тепла при установившемся стационарном состоянии процесса нагрева. Установившееся состояние теоретически наступает через длительное время нагрева. Практически состояние, близкое к установившемуся, для обычных объектов сварки наступает через промежуток времени от нескольких секунд до нескольких минут. При длительном нагреве поверхности полубесконечного тела неподвижным непрерывно действующим точечным источником тепла температура любой точки тела, находящейся на расстоянии R от источника тепла, определяется выражением
28
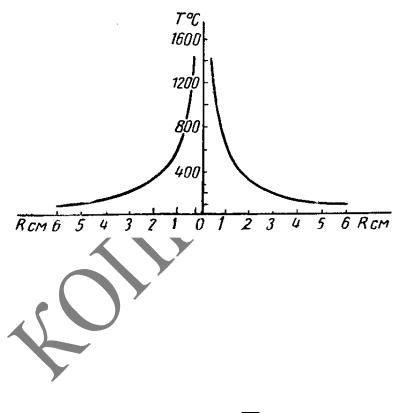
T (R) |
q |
, |
|
||
2 R |
где q - тепловая мощность источника, кал/сек; - коэффициент теплопроводности нагреваемого металла, кал/см сек град; R – расстояние от рассматриваемой до точки от источника тепла, см.
Зависимость температуры от расстояния иллюстрируется гиперболой (рис. 7.4).
Рис. 7.4. График распределения температур
При расстоянии R 0 температура Т , что показывает неприемлемость данной модели при приближении к источнику. По мере удаления от источника температура уменьшается пропорционально расстоянию R.
Если источник движется, то формула приобретает вид:
|
|
q |
|
VR |
|
T (R) |
|
|
e . |
||
|
R |
||||
2 |
|
|
|
Обозначим через коэффициент VR ,
где V - скорость перемещения источника, см/сек; - коэффициент теплопроводности металла, см/сек;
= /c ,
с- удельная теплоемкость, кал/ г град; - плотность, г/ см3.
29
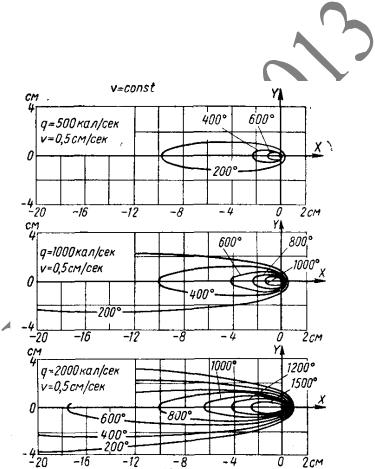
Множитель всегда меньше единицы, поэтому температура в точке впереди источника меньше, чем сзади на том же расстоянии.
В направлении, перпендикулярном движению источника,
|
2q |
|
VR |
|
|
VR |
|
T (R) |
|
e 2 . Обозначим коэффициент |
|
че- |
|||
|
2 |
||||||
2 R |
рез Z, тогда очевидно, что 1eZ еУ .
Если подставить численные значения в формулы, то мы получим график распределения температуры (рис. 7.5). Изотерма температуры плавления металла «очерчивает» контур сварочной ванны, но неточно, поскольку схема становится неточной на малых расстояниях от источника.
Рис. 7.5. Температурное поле движущего источника
30