
Котиков Г.С. Учебное пособие Сварка и резка металлов
.pdf
пературу выше 2500-2700° С; разница в 400-600° безоговорочно решает вопрос в пользу ацетилена.
14.3. Сварочное пламя
Рассмотрим ацетилено - кислородное пламя, имеющее наибольшее значение для сварочной техники. Полное сгорание
ацетилена происходит по уравнению С2Н2 + 2,5 О2 = 2СО2 + Н2О.
Эта формула дает лишь состав начальных и конечных продуктов сгорания ацетилена и не отражает сложных промежуточных процессов, происходящих в пламени и имеющих существенное значение для процесса сварки.
В зависимости от хода реакции сгорания ацетилена сварочное ацетилено - кислородное пламя имеет форму, схематически показанную на рис. 14.2. Во внутренней части ядра пламени 1 происходит постепенный подогрев до температуры воспламенения газовой смеси, поступающей из мундштука.
Рис. 14. 2. Сварочное пламя ацетилено – кислородной смеси
В тонкой наружной оболочке ядра происходит частичный распад ацетилена C2 H2 = 2С + Н2 с выделением твердых частиц углерода. Раскаленные твердые частицы углерода ярко светятся, поэтому оболочка ядра является самой яркой частью сварочного пламени, несмотря на то, что температура относительно невысока (не превышает 1500° С). Ядро называется также первой зоной пламени. По внешнему виду ядра визуально определяют состав газовой смеси и исправность горелки.
Зона 2 является самой важной частью сварочного пламени, так как в ней развивается наивысшая температура. В этой зоне проходит первая стадия сгорания ацетилена за счет первичного кислорода, поступающего из баллона. Она называется сварочной или второй зоной. В сварочной зоне проходит реакция
С2Н2 + О2 = 2СО + Н2.
61

Как видно из этого уравнения, в результате реакции получается смесь, состоящая из окиси углерода СО и водорода H2, обладающая восстановительными свойствами по отношению к окислам многих металлов, в том числе и к окислам железа. Поэтому сварочная зона иногда называется также восстановительной зоной. Факел, или хвост пламени, образует наружную или третью зону 3, в которой за счет кислорода атмосферного воздуха протекает вторая стадия горения ацетилена, что точнее отображает состав газов наружной зоны:
2СО + Н2 + 1,33 О2 + 6N2 = 2СО2+ Н2О + 6N2.
В этой зоне основными составными частями, помимо азота, являются двуокись углерода CO2 и пары воды, а также продукты их диссоциации. Как двуокись углерода, так и водяные пары при высоких температурах окисляют железо, поэтому наружная зона, или факел пламени, называется также окислительной зоной.
На рис. 14.2. схематически показано так называемое нормальное пламя, характеризующееся ярким, резко очерченным с ядром цилиндрической формы и белого цвета, в котором отношение газов О2 к C2H2 =1,1 - 1,2. При увеличении этого отношения, т. е. относительном увеличении содержания кислорода или уменьшении содержания ацетилена в смеси, форма и строение пламени меняются; особенно заметны изменения ядра пламени. Увеличение содержания кислорода в смеси ускоряет реакции окисления, ядро пламени укорачивается, уменьшается образование свободного углерода, ядро бледнеет, приобретает синеватую окраску и коническую заостренную форму.
С уменьшением указанного отношения отношения, т. е. с уменьшением содержания кислорода или увеличением содержания ацетилена в газовой смеси, реакции окисления замедляются, поэтому ядро пламени удлиняется; увеличивается количество свободного углерода, частицы которого появляются и в сварочной зоне; очертания увеличенного ядра становятся размытыми и теряют четкость. При значительном избытке ацетилена частицы углерода появляются и в наружной зоне, пламя становится коптящим, удлиняется и приобретает красноватую окраску. При некотором навыке по виду пламени можно достаточно точно
62

установить нормальный состав газовой смеси, не пользуясь измерительными приборами для расхода газов.
Сварочная зона нормального пламени состоит преимущественно из смеси СО и H2, восстанавливает окислы железа и мало влияет на содержание углерода в расплавленной стали. Нормальное пламя может быть названо восстановительным по отношению к окислам металла и нейтральным по отношению к углероду в металле. Пламя с некоторым избытком кислорода будет частично выжигать углерод и по отношению к нему может быть названо окислительным, или обезуглероживающим. Пламя с избытком ацетилена будет повышать содержание углерода в наплавленном металле и называется науглероживающим.
Температура пламени различна в различных его точках и зависит от состава газовой смеси и степени чистоты применяемых газов. Наивысшая температура наблюдается по оси пламени, причем она незначительна в первой зоне или ядре пламени, достигает максимума в сварочной зоне, на расстоянии 2-3 мм от конца ядра, и снова падает в третьей, или наружной зоне.
Максимальную температуру ацетилено - кислородного пламени определяли многие исследователи как теоретически - путем расчетов, так и экспериментально - непосредственным измерением. Оба метода дают удовлетворительное совпадение результатов.
Рис. 14. 3. Распределение температуры по оси пламени
63

На рис. 14.3 приведена диаграмма изменения температуры по оси нормального пламени. Мощность сварочной ацетилено – кислородной горелки определяется часовым расходом ацетилена
иподбирается по приблизительной эмпирической формуле
А= к s,
где s – толщина металла, мм. к – эмпирический коэффициент. Для углеродистой стали принимают среднее значение к=100.
Горелку настраивают для работы на нормальном пламени. Тепловое воздействие на металл зависит не только от мощности пламени, но и от угла наклона оси пламени к поверхности металла. Наиболее интенсивно действует пламя, когда его ось перпендикулярна к поверхности металла и уменьшается с увеличением угла наклона. Таким образом, с уменьшением толщины металла для регулирования температуры нагрева свариваемого участка горелку необходимо наклонять к поверхности металла во избежании прожога (рис. 14.4).
Рис. 14.4. Угол наклона горелки в зависимости от толщины металла
Горелку сварщик держит в правой руке, если же требуется добавление присадочного металла, то сварщик держит присадочный пруток в левой руке. Присадочный пруток располагается под углом 45° к поверхности металла, причем конец его должен быть погружен в ванну расплавленного металла. Газовая сварка может производиться в нижнем, вертикальном и потолочном положениях. Существует два способа выполнения газовой сварки - так называемые левый и правый способы.
При обычно применяемом левом способе сварки впереди перемещается присадочный пруток, за ним следует горелка. Сварной шов остается сзади горелки, пламя направлено вперед, на основной металл. Наиболее удобно для сварщика в этом случае перемещать горелку вдоль шва справа налево.
64

При правом способе сварки впереди перемещается горелка, за ней следует присадочный пруток, расположенный между швом и горелкой.
Рис. 14. 4. Способы газовой сварки: а) – левый; б) - правый
Этот способ дает лучший к. п. д. использования тепла пламени, а потому повышает производительность сварки и соответственно снижает удельный расход газов. Несмотря на указанное преимущество, правый способ применяется довольно редко. Это объясняется тем, что преимущество данного способа заметно проявляется лишь при сварке металла толщиной более 5 мм, что редко встречается при газовой сварке. При сварке металлов малых толщин правый способ, не имея заметных преимуществ, увеличивает опасность прожога металла.
Присадочные проволоки для газовой сварки применяются разного состава, соответственно характеру основного металла. Диаметр проволоки выбирается в соответствии с толщиной основного металла. Для приблизительного подбора диаметра присадочной проволоки можно пользоваться эмпирической формулой
d = S/2 +1,
где d – диаметр присадочной проволоки, мм; s – толщина основного металла, мм.
Для газовой сварки низкоуглеродистой стали используется присадочная проволока тех же марок, что и для электродов при дуговой сварке.
Вместо электродных обмазок, применяемых при дуговой сварке, в газовой сварке довольно широко пользуются флюсами, применение которых является необходимым для газовой сварки
65
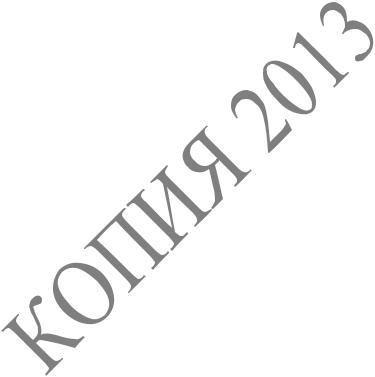
чугуна, цветных металлов и некоторых специальных сталей. Флюсы добавляют в ванну для растворения окислов и образования легкоплавких шлаков, хорошо всплывающих на поверхность ванны. Во флюсы могут вводиться восстановители и присадки, легирующие наплавленный металл. Флюсы применяются в форме порошков и паст, наносимых на основной металл так или на присадочную проволоку.
Применение газовой сварки обширно и разнообразно. Газовую сварку применяют там, где преобладает сварка металлов малых толщин (1 – 3) мм. Важное значение имеет газовая сварка в прокладке и монтаже трубопроводов самых разнообразных назначений, в особенности малых диаметров. Газовая сварка является незаменимым мощным средством в ремонтных мастерских, в сельском хозяйстве и т. д.
Качество сварных соединений, выполняемых газовой сваркой, выше, чем при дуговой электродами с тонкой ионизирующей обмазкой, но несколько уступает дуговой сварке, выполненной качественными электродами. Основная причина некоторого снижения прочности сварных соединений состоит в том, что при газовая сварке не производится легирования наплавленного металла, в то время как при дуговой сварке качественные электроды, содержащие в обмазке ферросплавы, производят довольно значительно легирование. Таким образом, газовая защита, обеспечиваемая восстановительной зоной сварочного пламени, для получения качественного сварного соединения менее эффективна, чем действие качественных электродных обмазок при дуговой сварке.
Производительность газовой сварки, значительная при малых толщинах основного металла, быстро снижается с увеличение его толщины. При малых толщинах (0,5 – 1,5 мм) газовая сварка по производительности может превосходить дуговую. С увеличением толщины металла до 2 – 3 мм скорости газовой и дуговой сварки уравниваются, а затем разница в скоростях быстро возрастает с увеличением толщины металла в пользу дуговой сварки. Таким образом, экономически газовая сварка наиболее приемлема для сварки малых толщин металла.
66

15. Электрическая контактная сварка
При электрической контактной сварке, или электрической сварке сопротивлением, нагрев осуществляют пропусканием электрического тока достаточной силы через место сварки, оказывающее омическое сопротивление прохождению электрического тока. Разогретые детали механически сдавливают или осаживают. Таким образом, контактная сварка относится к группе сварки давлением.
По форме выполняемых соединений различают три основных вида контактной сварки: стыковую, точечную и шовную (рис.
15.1).
При стыковой сварке через стык соединяемых деталей приблизительно одинакового сечения пропускается ток. После разогрева зоны сварки производится осадка.
15.1. Способы контактной сварки: а) – стыковая: б) – точечная: в) -
роликовая
При точечной сварке соединяемые детали, чаще всего листы, собирают внахлестку и зажимают между двумя медными электродами, подводящими ток к месту сварки и имеющими форму усеченного конуса. Ток проходит от одного электрода к другому через толщу соединяемых деталей и производит местный разогрев до расплавления металла. Давлением, приложенным к электродам, производят осадку. Полученное сварное соединение имеет в плане форму пятна (рис. 15.2). Это пятно называется точкой.
Рис. 15.2. Структура сварной точки: 1 – литое ядро; 2 – зона влияния
67

При шовной сварке электроды, подводящие ток к изделию и производящие осадку, имеют форму роликов, катящихся по изделию, поэтому такой способ сварки называется также роликовой сваркой. При шовной сварке листы соединяются плотным непрерывным швом.
Контактная сварка основана на использовании джоулева тепла. Полезным для процесса сварки является тепло, выделяемое в основном металле, и тепло, освобождаемое на контакте между соединяемыми деталями. Количество тепла, выделяемое на контактах между электродами и основным металлом, в большинстве случаев является вредным для процесса сварки, так как подгорает поверхность изделия и ускоряется износ электродов. В процессе сварки сопротивление основного металла и сопротивление контакта между частями не остаются постоянными. Сопротивление металла прохождению тока быстро растет с повышением температуры, а в значительной степени оно зависит и от приложенного к нему давления.
Рис. 15.3. Поверхность контакта
С увеличением давления сопротивление падает и, наоборот, возрастает при уменьшении давления. С увеличением давления сминаются выступы на поверхности металла, площадь действительного физического соприкосновения возрастает, а высота выступов уменьшается (рис. 15.3). В результате с повышением давления сопротивление контакта уменьшается. Кроме того, увеличение давления в большей или меньшей степени разрушает пленку окислов и загрязнений на поверхности металла, что также понижает общее сопротивление контакта.
При охлаждении металла по окончании сварки, прежде всего, происходит затвердевание расплавленной зоны. Кристаллизация начинается с наружных слоев расплавленной зоны и продолжа-
68
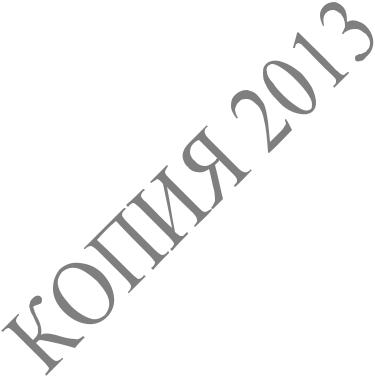
ется к ее середине, образуя типичную столбчатую структуру литого металла. Кристаллизация сопровождается усадкой металла, ведущей при недостаточном давлении к образованию усадочных раковин.
Охлаждение металла происходит весьма быстро, и если сталь способна к закалке, то возможно образование закалочных структур (мартенсита) в зоне сварки с возрастанием твердости металла и возможным образованием трещин. В этой же зоне нередко наблюдается рост зерна.
Оба эти явления ведут к снижению пластичности металла в зоне сварки, особенно заметно понижается его ударная вязкость.
Трансформаторы имеют падающую внешнюю характеристику, так что рабочий ток на данной ступени трансформатора зависит от омического и индуктивного сопротивлений свариваемого изделия. С переключением ступени трансформатора естественно меняются внешняя характеристика, ток короткого замыкания и ток рабочий.
Для контактной сварки процесс осадки не менее важен, чем процесс нагрева. Осадочные устройства в простейших машинах малой мощности приводятся в движение усилием работающего, что допустимо при сварке мелких деталей, когда усилие и работа осадки очень незначительны. Такие устройства бывают педальными, рычажными, иногда пружинными. Для более мощных машин применяется механизированный привод, в первую очередь, электропривод с электродвигателем. Для машин, не требующих особенно быстрого перемещения при осадке, используют гидравлический привод. Значительно быстрее действует и чаще применяется привод пневматический; нередко используется и комбинированный пневмо-гидравлический привод.
15. 1. Стыковая контактная сварка
Стыковая контактная сварка имеет две основные разновидности: сварка без оплавления, иногда называемая сваркой сопротивлением, и сварка оплавлением.
Первый способ состоит в следующем. Детали, зажатые в машине, доводят до соприкосновения и сжимают под небольшим давлением, обеспечивающим удовлетворительный контакт свариваемых поверхностей. Затем включают сварочный ток, кото-
69

рый разогревает металл изделия, в особенности зону, прилегающую к контакту, так как здесь имеется значительное переходное сопротивление контакта. Сварщик наблюдает за разогревом металла и после нагрева до ярко-белого каления производит осадку, одновременно выключая сварочный ток прерывателем. Место сварки имеет значительное утолщение вследствие высадки металла.
Сварка без оплавления пригодна и дает хорошие результаты для металлов, обладающих хорошей свариваемостью в пластическом состоянии (например, низкоуглеродистая сталь). Металл соединяемых деталей должен быть однородным.
Сечение участка сварки должно быть простым, компактным, с небольшим отношением периметра к сечению. Такими сечениями являются, например, круг, квадрат, прямоугольник с малым отношением сторон. Сечения с более развитым периметром - тонкая полоса, тонкостенная труба, уголок, двутавр, рельс и т. п. - малопригодны для сварки без оплавления, так как при этом трудно обеспечить необходимое равномерное распределение тока по площади сечения. В подобных случаях применяется стыковая сварка оплавлением.
Второй способ - сварка оплавлением - имеет две разновидности: прерывистое и непрерывное оплавленния. При прерывистом оплавлении зажатые детали в первой стадии процесса оставляют разъединенными; после включения напряжения питающей сети между деталями создается напряжение холостого хода вторичной цепи. Затем детали приводят в кратковременное соприкосновение и снова разъединяют. В результате происходит размыкание сварочного
Рис. 15.5. Сварка оплавлением тока силой в тысячи и десятки тысяч ампер, что сопровождает-
70