
Котиков Г.С. Учебное пособие Сварка и резка металлов
.pdf
ся сильным искрением и разбрызгиванием расплавленного металла под действием магнитного поля вторичного контура. Повторяя ряд быстро следующих одно за другим замыканий и размыканий сварочной цепи, можно в короткое время вызвать оплавление всего сечения сварки.
При замыканиях в первую очередь оплавляются неровности и выступы на свариваемых поверхностях, которые постепенно выравниваются.
Когда достигнуто равномерное оплавление всей поверхности свариваемого участка, производят быструю осадку с приложением повышенного давления и в процессе осадки выключают сварочный ток. Под значительным давлением почти весь расплавленный металл выдавливается из зоны сварки, образуя так называемый грат, а место сварки получает сравнительно небольшое усиление. Грат, содержащий большое количество окислов металла, механически непрочен и легко удаляется со сварного стыка.
При непрерывном оплавлении сближение деталей происходит достаточно медленно и равномерно. Процесс в этом случае идет следующим образом. На зажатые в машину и разъединенные детали подается напряжение вторичной цепи, затем начинается медленная подача деталей в сторону сближения. Соприкосновение происходит сначала лишь в немногих отдельных точках, в которых возникают весьма высокие плотности тока вследствие замыкания сварочной цепи. В результате происходит местное расплавление и испарение металла, который выбрасывается наружу в плоскости стыка под действием магнитного поля.
Контакт в точках первоначального соприкосновения нарушается, но вследствие непрерывного перемещения деталей в соприкосновение входят новые точки, процесс повторяется и т. д. Происходит непрерывное расплавление и выбрасывание металла из плоскости стыка, между деталями непрерывно проходит ток по кратковременным мостикам жидкого металла. Когда достигнуто равномерное и достаточное оплавление всей поверхности стыка, производится быстрая осадка давлением. Постоянная и равномерная скорость сближения деталей, необходимая при
71

сварке непрерывным оплавлением, трудно выполнима при ручной работе, и этот процесс осуществляется обычно лишь на машинах с механизированным приводом осадки.
Сварка оплавлением имеет ряд существенных преимуществ. Металл, подлежащий сварке, даже если он плохо сваривается в пластическом состоянии, часто хорошо поддается сварке оплавлением, например, технически чистые медь и алюминий. Можно сказать, что почти все металлы и сплавы могут быть сварены по способу оплавления. В процессе оплавления выравниваются все выступы и неровности на поверхности сварки, поэтому поверхность стыка под сварку не требует какой-либо особой подготовки. В процессе оплавления сгорают и удаляются вместе с расплавленным металлом загрязнения его поверхности.
Выравнивание сечения в процессе оплавления позволяет равномерно оплавить и разогреть сечения даже очень сложной формы, с сильно развитым периметром, например, успешно могут быть сварены листы толщиной 1 мм при длине сварного стыка 1200 мм и более. Могут быть сварены между собой во
многих случаях разнородные металлы, например, быстрорежущая и углеродистая стали, медь и алюминий и т. д., несмотря на значительные различия их физических свойств. Указанные преимущества обеспечили сварке оплавлением широкое применение в промышленности, поэтому современные стыковые машины
обычно приспособлены к этому процессу. Некоторым недостатком сварки оплавлением является довольно значительная потеря металла на оплавление, что может иметь значение при высокой стоимости металла, например, быстрорежущей стали.
16. Термическая резка металлов
Под термической резкой металлов мы будем подразумевать процессы, при которых металл в зоне реза нагревается до высоких температур и удаляется из полости реза в расплавленном жидком виде в форме расплавленных шлаков и окислов. Для
72
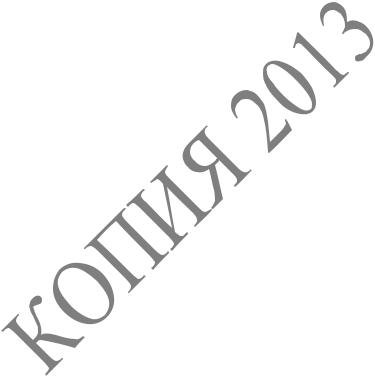
термической резки пользуются оборудованием, аппаратурой и материалами, сходными с применяемыми в процессах сварки металлов. Поэтому во многих случаях целесообразно рассматривать термическую резку вместе со сваркой, хотя цели этих двух процессов противоположны. Промышленное применение термической резки весьма велико: обрезка и обдирка слитков, обрезка и разрезка проката, обрезка и зачистка отливок, разрезка и раскрой листов, обрезка кромки под сварку, вырезка заготовок и готовых деталей.
В процессе резки металл может удаляться из полости реза чисто термическим процессом - расплавляется и вытекает. Но наиболее важный для техники металл - железо - легко окисляется, а в чистом кислороде может гореть подобно тому, как магний горит на воздухе; в результате металл превращается в окислы и шлаки, удаляемые из полости реза. В одних процессах резки преобладает термический процесс, в других - химический, но всегда оба эти процесса действуют совместно; в продуктах, удаляемых из полости реза, всегда можно обнаружить как металлическое железо, так и его окислы,
К термическому и химическому действию может присоединяться механическое действие струи газа, электрода и пр, выталкивающее жидкие и размягченные продукты из полости реза. Термическая резка выполняется разными способами; наиболее важный и изученный способ - газокислородная резка, основанная на использовании химической реакции сгорания железа в кислороде.
Более новый способ плазменной резки основан на использовании высокотемпературной плазменной струи. Способ быстро развивается и уже имеет крупное промышленное значение. В перспективе могут найти применение струя фтора и световой луч, обычный и усиленный лазером.
16.1. Газокислородная резка
Газокислородная резка основана на способности железа сгорать в струе чистого кислорода с выделением значительного количества тепла по реакции 3Fe + 202 = Fe3 О4.
73

Из этого уравнения следует, что на сжигание 1 г железа расходуется 0,38 г (или 0,27 л) кислорода или на 1 см3 железа расходуется 2,1 л кислорода. Действительный расход кислорода на 1 см3 железа в процессе резки может быть как выше, так и ниже указанного теоретического значения ввиду того, что часть металла выдувается из полости реза в неокисленном виде и вытекающий шлак содержит не только окислы, но и металлическое железо. Выделяемое при горении железа довольно значительное количество тепла оплавляет поверхность металла, и получающийся жидкий металл увлекается в шлак вместе с расплавленными окислами. Количество тепла от сгорания железа при резке в 6 - 8 раз превышает количество тепла, выделяемое подогревательным пламенем резака. Железо или сталь не загораются в кислороде при низких температурах; кислород, например, хранят и перевозят в стальных баллонах. Для начала горения металла в кислороде его нужно подогреть; температура начала горения зависит от состава металла и находится в пределах 1000 -
1200° С. Температура начала горения повышается с увеличением содержания углерода в металле при одновременном понижении температуры плавления металла. Настоящая высококачественная кислородная резка металла возможна лишь в том случае, если металл горит в твердом состоянии. Если же металл загорается лишь при расплавлении, то в процессе резки происходит значительное расплавление и вытекание металла из полости реза и рез получается широким и неровным, как при тепловых методах резки.
|
Процесс газокислородной резки |
|
можно представить следующим об- |
|
разом (рис.16.1). Смесь кислорода с |
Рис. 16.1. Газокислородная |
горючим газом 4 выходит из подо- |
|
|
резка |
гревательного мундштука резака 1 и |
|
74 |

сгорает, образуя подогревательное пламя 5. Подогревательным пламенем металл нагревается до температуры начала горения, тогда по осевому каналу 2 режущего мундштука подается технически чистый кислород. Режущий кислород попадает на нагретый металл 3 и зажигает его. Начинается горение металла; при этом выделяется значительное количество тепла, которое совместно с подогревательным пламенем разогревает нижележащие слои металла, и горение быстро распространяется в глубину на всю толщину металла, прожигая сквозное отверстие, через которое режущая струя кислорода 6 выходит наружу, пробивая металл.
Если перемещать далее резак по прямой или кривой линии с надлежащей скоростью, то сжигание металла будет происходить по этой линии и металл будет разрезаться.
Таким образом, кислородная резка складывается из нескольких процессов: подогрева металла, сжигания металла в струе кислорода, выдувания расплавленного шлака из полости реза. Подогревательное пламя не тушат, и оно горит в течение всего процесса резки, так как количество тепла, выделяемого при сжигании железа недостаточно для возмещения всех потерь тепла зоны резки. Если подогревательное пламя потушить, то процесс резки быстро прекращается, металл охлаждается настолько, что кислород перестает на него действовать, и реакция горения металла в кислороде прекращается.
Для возможности успешного проведения кислородной резки разрезаемый металл должен удовлетворять определенным требованиям. Температура начала горения металла должна быть ниже температуры его плавления, т. е. металл должен гореть в твердом, нерасплавленном состоянии. Температура плавления окислов металла, образующихся при резке, должна быть ниже температуры плавления самого металла,. В этом случае окислы легко выдуваются из полости реза и режущий кислород получает беспрепятственный доступ к нижележащим слоям металла. Теплота сгорания металла должна быть достаточно большой, иначе требуется слишком мощное подогревательное пламя. Теплопроводность усиливает охлаждение зоны резки и затрудняет необходимый подогрев металла.
75

Практически указанным условиям удовлетворяет лишь железо и его технические сплавы - стали. Большинство других металлов, применяемых в технике и строительстве, не удовлетворяет указанным условиям и не поддается кислородной резке.
Чугун не режется вследствие низкой температуры плавления и высокой температуры начала горения; он горит в кислороде в расплавленном состоянии, что исключает возможность получения качественного реза. Медь не режется вследствие высокой теплопроводности и малой теплоты сгорания. Алюминий не режется вследствие чрезмерной тугоплавкости образующегося окисла и т. д. Стали высокоуглеродистые, высоколегированные, высокохромистые и т. д., не поддающиеся нормальному процессу газокислородной резки, могут быть разрезаны с использованием специальных приемов.
Для резки необходим чистый кислород; даже незначительное количество примесей заметно снижает скорость резки и сильно повышает расход кислорода. В качестве горючего для подогревательного пламени при кислородной резке может быть использован любой горючий газ, а также жидкое горючее - бензин, бензол, керосин и т. д.
16.1.1. Газокислородные резаки
Рис.16.2. Устройство газокислородного резака
В газокислородном резаке конструктивно объединены подогревательная и собственно режущая части. Подогревательная часть газокислородного резака по принципу устройства, конструкции и методам расчета аналогична сварочным горелкам. В зависимости от давления горючего газа подогревательная часть может быть инжекторной или безинжекторной. Инжектор необходим при использовании в качестве горючего газа ацетилена низкого давления. При ацетилене среднего давления или горю-
76

чих газах, подаваемых под достаточным давлением, можно пользоваться резаками с безинжекторным подогревательным устройством. В промышленности обычно пользуются резаками с инжекторным подогревательным устройством независимо от давления применяемого горючего газа.
Главной особенностью бензореза (резак, работающий на жидком горючем) является наличие испарительной камеры, в которой горючее превращается в пары; поступающие в камеру смешения, где они образуют горючую смесь с подогревательным кислородом для питания подогревающего пламени. Также изготовляют специальные резаки для различных назначений - для срезки заклепочных головок, для вырезки жаровых труб в паровых котлах, для вырезки круглых отверстий малого диаметра, под сборочные болты, для строгания и поверхностной обработки металла и т. д.
16.2. Плазменная резка
Процессы плазменной резки отличаются от сварки лишь величиной отдельных параметров. Если увеличить ток в плазменной сварочной горелке и поток газа, то плазменная струя будет проплавлять насквозь металл небольшой толщины и процесс сварки перейдет в процесс резки, что иногда используется на практике.
Плазмотроны. Горелку для плазменной резки, или плазменный резак, в настоящее время называет плазмотроном. Плазмотрон для резки отличается от плазменной сварочной горелки размерами, большей электрической мощностью, большим расходом газа, обязательным охлаждением. Наиболее существенные части плазмотрона - электроды и сопло для выхода газа, образующего плазменную струю (рис. 16.1). До недавнего времени материалом электрода служил исключительно вольфрам. В отдельных конструкциях плазмотронов были попытки применять электроды угольные (графитные) и водоохлаждаемые медные, но значительного применения они не получили. С 1966 г. началось применение для электродов металла циркония. Электрод введен в
металлический корпус плазмотрона и электрически изолирован от него. С другой стороны к корпусу присоединено сопло с ка-
77

либрованным выходным обжимающим каналом для плазменной струи.
Рис. 16.3. Плазмотрон
Сопло, изготовленное из меди, интенсивно охлаждается проточной водой. Диаметр выходного канала сопла при средних режимах 3 - 5 мм. Сопло (после электрода) - наиболее изнашивающаяся часть плазмотрона - постепенно обгорает под действием плазменной струи, брызг разрезаемого металла и пр. и довольно часто сразу выходит из строя при нарушениях нормальной работы плазмотрона. Поэтому сопло делают сменным (конструкция его допускает быструю и удобную замену) и электрически изолируют от корпуса плазмотрона. Электрически изолированное сопло можно присоединить к полюсу источника тока, а разрезаемый материал не включать в электрическую цепь. В этом случае снижается к. п. д. плазмотрона и увеличивается износ сопла, но зато появляется возможность резать неэлектропроводные материалы - стекло, керамику и т. п. Дуга стабилизируется, становится устойчивой и жесткой, плазменная струя
78

формируется непрерывной подачей рабочего газа в плазмотрон в количестве нескольких кубических метров в час.
Рис. 16.4. Подача плазмообразующих газов: а) – аксиально; б) - тангенциально
Плазмообразующий или рабочий газ, образующий плазменную струю, может подаваться или аксиально вдоль оси электрода, или тангенциально (рис. 16.4).
Простейшие плазмотроны для ручной резки находят промышленное применение на металлах, не поддающихся газокислородной резке.
Газы для плазмотронов. Рабочий газ для плазменной резки имеет первостепенное значение. Плазменная резка была создана и первоначально развивалась на использовании аргона в качестве рабочего газа. Аргон имеет ряд положительных качеств: уменьшает износ и обеспечивает продолжительную работу вольфрамового электрода; мало изнашивает сопло плазмотрона; в аргоне ввиду малой его теплопроводности и теплоемкости легко зажигается и устойчиво горит дуга при сравнительно низких
79

напряжениях, что облегчает выполнение требований техники безопасности; не реагирует с разрезаемым металлом и не загрязняет его. Наряду с перечисленными преимуществами аргон имеет и существенные недостатки. Это - одноатомный газ, его молекула состоит из одного атома и не может диссоциировать при нагреве, поэтому аргон может воспринимать тепло только за счет теплоемкости, а запас тепловой энергии в аргоне даже при высоких температурах незначителен. Этот малый запас тепла плохо передается металлу, так как аргон отличается и низкой теплопроводностью.
В результате производительность резки сравнительно низка, значительно ниже, чем при других газах. Кроме того, аргон дорог, а расход газов при резке значителен. Остальные инертные газы, в том числе гелий, вообще для резки недоступны из-за дефицитности и высокой стоимости. Значительно эффективнее для резки двухатомные газы. Такой газ при нагреве диссоциирует с расщеплением молекулы на два свободных атома. Диссоциация поглощает много тепла, на поверхности металла при охлаждении газа идет обратный процесс объединения двух свободных атомов в двухатомную молекулу; при этом энергия, затраченная на диссоциацию, освобождается и передается металлу, нагревая его.
Таким образом, диссоциированный, или атомарный газ содержит большой запас энергии и легко передает ее металлу.
Из двухатомных газов большого внимания заслуживает водород. Он имеет очень высокую теплоемкость и высокую теплопроводность, легко диссоциирует при нагревании, переходя в атомарную форму и поглощая большое количество энергии (52 000 ккал/кг), которую легко отдает металлу, быстро нагревая его. Плазменная струя водорода является особенно "горячей", расплавляет и режет металл быстрее, чем другие газы. Одновременно она усиливает износ сопла. Обычно считают, что водородная плазма слишком горяча и применяют водород не в чистом виде, а в смеси с аргоном или азотом. К недостаткам водорода относится его взрывоопасность в смеси с воздухом.
Представляет интерес недефицитный двухатомный азот. Он пригоден для плазменной резки после достаточной очистки, ко-
80