
Процесс каталитического крекинга лекция 6-8
.pdfСПБГУАП группа 4736 https://new.guap.ru/i03/contacts
5.1. Каталитический риформинг
Одной из важнейших характеристик бензинов является детонационная стойкость, определяющая способность их противостоять самовоспламенению при сжатии. Показателем детонационной стойкости бензинов является октановое число (ОЧ), показывающее (в % объемных) содержание изооктана (ОЧ = 100) в смеси с н-гептаном (ОЧ = 0), которая по детонационной стойкости эквивалентна бензину, испытуемому в стандартных условиях (на одноцилиндровых моторных установках УИТ-85 или УИТ65). Октановое число на установках определяют двумя методами: моторным (по ГОСТ 511 -82) и исследовательским (по ГОСТ 8226-82).
Детонационная стойкость бензинов определяется их углеводородным составом. Наибольшей детонационной стойкостью обладают ароматические углеводороды, самой низкой — нормальные парафины. Промежуточное положение по этому показателю занимают нафтены, а изопарафиновые и олефиновые углеводороды имеют детонационную стойкость, большую, чем нафтены, но меньшую, чем ароматические. Увеличение степени разветвленности и снижение молекулярной массы повышает детонационную стойкость.
Самую низкую детонационную стойкость (следовательно и ОЧ) имеют бензины прямой перегонки из большинства нефтей, состоящие, в основном, из н-парафинов, причем она снижается с повышением температуры конца кипения. Октановые числа таких бензинов, выкипающих до 180°С, не превышают 40-50 ед. (м.м.). Исключение составляют аналогичные бензиновые фракции, получаемые из некоторых сахалинских и азербайджанских нефтей нафтенового основания и имеющие ОЧ = 71-73 (м.м.). В табл. 5.1 приведены октановые числа некоторых бензиновых прямогонных фракций и их групповой углеводородный состав.
Характеристика некоторых прямогонных бензиновых фракций
Показатели |
|
Сырье |
|
|
парафиновое |
нафтеновое |
|
Характеристика сырья: |
85-180 |
105-180 |
85-180 |
Пределы кипения, °С |
|
|
|
Углеводородный состав, |
|
|
|
% мас.: |
|
|
|
арены |
12 |
15 |
15,9 |
циклоалканы |
24 |
22 |
44 |
алканы |
64 |
62 |
40 |
Октановое число |
43 |
39 |
47 |
Для использования прямогонных бензиновых фракций в качестве высокооктановых компонентов автобензинов их необходимо подвергнуть процессу, в котором за счет химических превращений в этих фракциях увеличилось бы содержание ароматических углеводородов, углеводородов изостроения и понизилось бы содержание парафинов и нафтенов. Таким процессом является каталитический риформинг, основным назначением которого является ароматизация бензиновых фракций. При необходимости получения из ароматизированных катализатов (риформатов) индивидуальных ароматических углеводородов (бензол, толуол, орто- и параксилолы) используют сочетание риформинга и экстракции. Каталитический риформинг является одним из главнейших процессов в составе современного нефтеперерабатывающего завода.
Первая установка риформинга пущена по лицензии фирмы UOP в 1949 г. Это был «полурегенеративный платформинг», т.е. каталитический риформинг на алюмоплатиновом катализаторе в реакторах с его стационарным слоем и с периодической остановкой установки для регенерации катализатора.
Основными лицензиарами процесса каталитического риформинга за рубежом являются 9 фирм, приведенных в табл. 5.2. Ведущая из них — UOP, по лицензиям
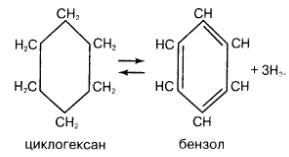
СПБГУАП группа 4736 https://new.guap.ru/i03/contacts
которой в мире построено около 800 установок (фирменное название процесса «платформинг»).
В бывшем СССР разработкой теории каталитического риформинга и конструктивным оформлением технологических схем занимались «ВНИИНефтехим» и «Ленгипронефтехим». Суммарная мировая мощность каталитического риформинга на 01.01.1999 г. составила 487,7 млн.т/ год. Если учесть, что на эту дату в мире перерабатывалось около 2 млрд.т нефти, то на долю каталитического риформинга приходится 20-25%.
В настоящее время большинство установок риформинга российских заводов работает на алюмоплатиновом катализаторе АП-64 и бифункциональных платинорениевых катал и заторах серии К.Р.
Для производства риформатовс целью выделения из них индивидуальных ароматических углеводородов в нашей стране созданы следующие типы установок: Л- 35-6 с блоком Л-24/300, Л-35-8/300Б и ЛГ-35-8/300Б, Л-35-12/300А. Эти установки скомбинированы с блоками экстракции, использующими диэтиленгликоль (ДЭГ) и предназначены для извлечения бензола и толуола из риформатов. В качестве сырья используют фракцию 62-105°С.
Для производства толуола и ксилолов спроектированы и внедрены установки типов: Л-35-11/300 и Л-35-9, Л-35-11/300 и 350-200, Л- 35-И/300А. Они работают на сырье, выкипающем в пределах 105140°С.
5.2. Основы химизма процесса каталитического риформинга
Процесс каталитического риформинга осуществляется при повышенной температуре в присутствии катализаторов, имеющих в своем составе платину или платину совместно с другими металлами (рением, кадмием), которые наносят на окись алюминия, промотированную галогенами (хлором или фтором).
Основными реакциями при каталитическом риформинге являются дегидрирование (дегидрогенизация) шестичленных нафтенов и дегидроциклизация парафинов, приводящие к образованию ароматических углеводородов.
Способность шестичленных нафтенов в присутствии никеля и металлов платиновой группы при 300°С полностью превращаться в ароматические углеводороды была открыта Н.Д.Зелинским еще в 1911 г. Дегидрированию могут подвергаться только шестичленные нафтены: циклогексан — в бензол, метилциклогексан — в толуол и т.д. При этом нафтеновое ядро всегда теряет 3 молекулы водорода, превращаясь в ароматическое:
Реакция дегидрирования обратима, и при температурах ниже 300°С равновесие сдвигается влево. С повышением температуры равновесие все более сдвигается вправо.
Голоядерный пятичленный нафтен, содержащийся в бензинах (циклопентан) непосредственно не дегидрируется, но его гомологи (метилциклопентан и др.) в присутствии платиновых и других активных катализаторов риформинга вначале изомеризуются (I) с образованием шестичленного ядра (равновесие сдвигается вправо с понижением температуры), а затем шестичленное ядро нафтена дегидрируется до ароматического (II):
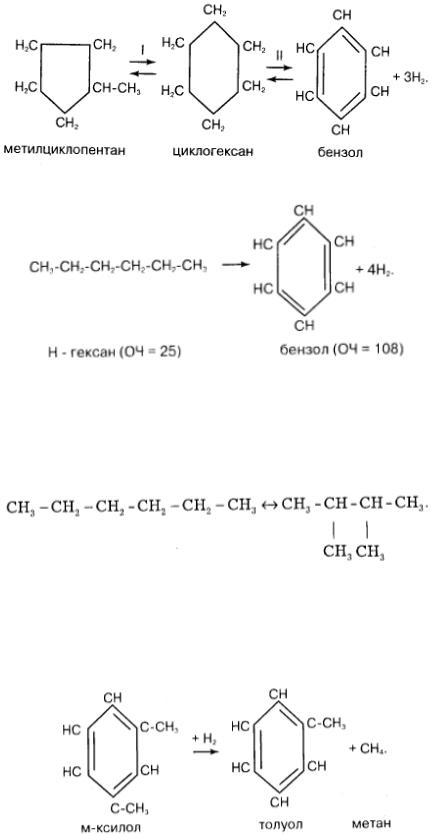
СПБГУАП группа 4736 https://new.guap.ru/i03/contacts
Второй важнейшей реакцией ароматизации, протекающей в процессе риформинга, является дегидроциклизация парафинов (алканов):
Дегидроциклизация парафинов является практически необратимой, но протекает медленнее и менее глубоко и селективно, чем дегидрогенизация нафтенов. Кроме того, она сопровождается гидрокрекингом (температура промышленного риформинга >500°С) парафинов С,-С . При этом имеет место изомеризация парафиновых углеводородов С.-С6 с образованием высокооктановых изомеров. Например, нормальный гексан (ОЧ = 25) изомеризуется в 2,3-диметилбутан (ОЧ = 95):
Однако ее значение в процессе риформинга ничтожно, так как для этой реакции благоприятны более низкие (350-380°С) температуры.
Алкилароматические углеводороды, содержащиеся в сырье и образующиеся в результате риформинга, могут подвергаться изомеризации и деалкилированию. Так, м-ксилол частично изомеризуется в о- и п-кси- лолы, а также, теряя одну метильную группу, превращается в толуол:
Образующийся при этом метан, так же как легкие углеводороды (от метана до бутанов включительно) — продукты реакции гидрокрекинга — пополняют собой углеводородную составляющую водородсодержащего газа, побочного, но весьма важного продукта риформинга.
СПБГУАП группа 4736 https://new.guap.ru/i03/contacts
Нарядус деалкилированием протекают и реакции уплотнения, продуктами которых являются конденсированные ароматические углеводороды (ал кил нафталины, алкилинданы и др.) в количестве 0,5-0,7% на исходное сырье риформинга.
5.3. Основные факторы процесса риформинга
Качество сырья. Основными показателями, определяющими качество и пригодность сырья для процесса риформинга, являются: углеводородный и фракционный состав, а также содержание в нем веществ, вызывающих дезактивацию катализаторов.
Поскольку преобладающей реакцией процесса является дегидрирование нафтенов, предпочтительным его сырьем служат бензиновые фракции с их высоким содержанием. Выход риформатов из бензиновых фракций, богатых нафтенами, на 3,5-5%, а иногда на 10-12% больше, чем из парафинистого сырья, при выработке катализата с одним и тем же октановым числом.
При риформинге бензиновых фракций из парафинистых нефтей преобладающими являются реакции дегидроциклизации алканов и гидрокрекинга, позволяющие даже из низкооктанового парафинистого сырья получать катал изаты, пригодные для выработки автобензина А-76 в смеси с другими компонентами.
Присутствие в сырье риформинга алифатических непредельных соединений крайне нежелательно, так как при этом водород циркулирующего водородсодержащего газа нерационально расходуется на гидрирование непредельных углеводородов. Поэтому для каталитического риформинга применяют бензиновые фракции прямогонного происхождения. Риформинг же бензиновых фракций вторичного происхождения (например, термического крекинга) возможен только в смеси с прямогонным сырьем после предварительной глубокой гидроочистки.
Фракционный состав сырья каталитического риформинга определяется целевым назначением процесса. Если целью каталитического риформинга является получение катализатов для производства высокооктановых бензинов, оптимальным сырьем для этого служат фракции, выкипающие в пределах 85-180°С. Применение сырья с температурой начала кипения ниже 85°С нежелательно, так как при этом будет иметь место повышенное газообразование за счет гидрокрекинга, при этом за метного увеличения ароматизации сырья не происходит, так как углеводороды С6 ароматизируются наиболее трудно. Кроме того, применение такого сырья приведет к непроизводительной загрузке установки балластными фракциями.
В связи с этим фракции, выкипающие ниже 85°С и имеющие сравнительно высокое октановое число, вовлекаются в товарные бензины, как компоненты в чистом виде, либо направляются на изомеризацию.
Наличие в сырье фракций, выкипающих выше 180°С, также нежелательно, так как при этом увеличивается отложение кокса на катализаторе за счет реакций уплотнения тяжелокипящей части сырья, что приводит к потере активности катализатора.
Если риформинг проводится для получения бензола и толуола, сырьем служат узкие бензиновые фракции, выкипающие в пределах 62-85 и 85-105°С соответственно. В первой из них бензол образуется из циклогексана, метилциклопентана и н-гексана, во второй фракции толуол образуется из метилциклогексана, диметилциклопентана и н-гептана.
Для получения суммарных ксилолов используют узкую фракцию, выкипающую в пределах 105-127°С.
Сернистые соединения являются одними из основных дезактиваторов катализаторов риформинга. Содержание серы в сырье этого процесса должно быть минимальным. Особенно чувствительны к сере платино-рениевые катализаторы; допустимое ее содержание в этом случае не должно превышать 0,5 ppm. Ограничивают также содержание азота 0,5 ppm и влаги 10 ppm.
Применительно к платиновому катализатору (АП-64) показано, что для его дезактивирования на 70-80% достаточно 6-7% мае. серы от количества платины, нанесенной на оксид алюминия (т.е. при содержании платины в катализаторе 0,6% мае. для указанной степени дезактивирования достаточно 0,04% мас. серы). В присутствии водорода сернистые соединения сырья превращаются в сероводород, а
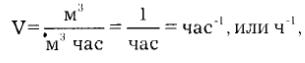
СПБГУАП группа 4736 https://new.guap.ru/i03/contacts
азотистые — в аммиак. Поэтому перед риформингом сернистого сырья его обязательно подвергают предварительной гидроочистке.
При высоком содержании влаги в циркулирующем водородсодержащем газе (ВСГ) из катализатора вымывается активирующий его галоген (в виде НС1 или HF), однако чрезмерно низкое ее содержание отрицательно влияет на свойства носителя (оксида алюминия). Поэтому содержание влаги в газе поддерживают в пределах (1,0-1,5) • 10-3 % об. Чрезмерно низкая влажность может снизить продолжительность без регенерационного цикла и выход жидких продуктов даже более, чем завышенная влажность.
Максимально допустимое содержание металлоорганических микропримесей (мышьяк, свинец) в гидроочищенном сырье риформинга составляет мышьяк 1 ррb и свинца 20 ррb (1 ррb — 1 мг/тонну).
Температура и объемная скорость подачи сырья. Реакции ароматизации являются высокотемпературными: 470-520°С на платино-рениевом и 480-530°С на платиновом катализаторах.
Объемной скоростью подачи сырья называют объем сырья, проходящий через единицу объема катализатора в час, поэтому объемная скорость имеет размерность:
Ароматизацию парафинов (дегидроциклизацию) целесообразно проводить при более высоких температуре и объемной скорости подачи сырья. Так, при риформинге практически парафинистого сырья на двух разных режимах были получены катализаты с равным (60% мас.) содержанием ароматических углеводородов, но при 500°С и V = 1,5 ч -1 выход катализата составил 80% мас. на сырье, а при 510°С и V = 5 ч-1 — 87% мас., причем выход кокса (в % мас. на сырье) во втором случае значительно ниже.
Объемная скорость подачи сырья в промышленных процессах риформинга различного назначения может быть в пределах от 1 до 2 ч-1. При постоянной объемной скорости повышение температуры (ужесточение режима) увеличивает степень ароматизации сырья, но уменьшает выход катализата за счет усиления реакций гидрокрекинга. Чем больше содержание нафтенов в сырье и чем селективнее катализатор, тем больше выход катализата при одном и том же содержании в нем ароматических углеводородов. Ужесточение режима возможно и при постоянной температуре за счет снижения объемной скорости, в этом случае степень ароматизации также возрастает.
Таким образом, факторы температуры и объемной скорости подачи сырья тесно связаны, поэтому умелое использование их сочетания позволит на одном и том же катализаторе достичь оптимального результата по выходу риформата и степени его ароматизации.
Основные реакции в процессе риформинга (дегидрирование нафтенов, дегидроциклизация парафинов) идут с поглощением тепла, реакция гидрокрекинга — с его выделением. Поскольку катализатор распределяется при проведении риформинга в 3-х реакторах (ступенях) и в каждой ступени преобладают те или иные реакции, возникает температурный перепад при прохождении сырья через слой катализатора. Преобладающей реакцией в первой ступени является дегидрирование циклогексановых ув., во второй ступени преимущественно протекает дегидроизомеризация циклопентанов, в третьем реакторе протекают реакции ароматизации парафинов. Суммарный перепад температур зависит от соотношения этих реакций в каждой ступени. Температурные перепады, особенно в первой ступени, являются в некоторой степени характеристикой активности катализатора. По мере ее снижения уменьшаются температурные перепады по реакторам и суммарный перепад.
Температурный перепад в первом реакторе зависит также от химического состава сырья: чем больше в сырье нафтенов, тем больше температурный перепад.
Давление водорода и кратность циркуляции водородсодержащего газа.
Повышение давления водорода в системе риформинга, при прочих равных условиях,
СПБГУАП группа 4736 https://new.guap.ru/i03/contacts
препятствует ароматизации сырья. Однако высокое давление водорода необходимо для насыщения непредельных продуктов побочных реакций гидрокрекинга. Если давление водорода невысоко, на поверхности катализатора протекает глубокое уплотнение ненасыщенных углеводородов с образованием кокса. Ведение процесса под давлением водорода позволяет значительно (в зависимости от селективности катализатора) подавить коксообразование.
При увеличении парциального давления* водорода его гидрирующее действие возрастает. Высокое парциапьноедавление водорода достигается циркуляцией через зону реакции сухого газа, получаемого в результате процесса и содержащего 80-90% об. водорода (остальное — газообразные углеводороды). Высокая степень (кратность) разбавления паров реакционной смеси водородсодержащим газом увеличивает продолжительность работы катализатора. Промышленные кратности циркуляции ВС Г находятся в пределах 900-1500 м1 газа на 1 м1 сырья при указанной концентрации водорода в ВСГ.
При постоянной объемной скорости подачи сырья с увеличением кратности циркуляции ВСГ сокращается длительность пребывания паров бензина в зоне реакции, из чего следует, что гидрирующее действие водорода ограничено уменьшением глубины ароматизации. Кроме того, при увеличении кратности циркуляции ВСГ растет расход энергии на компримирование газа и расход топлива в трубчатой печи для его подогрева — возрастают эксплуатационные расходы.
Таким образом, практически целесообразную величину кратности циркуляции ВСГ устанавливают, исходя из качества сырья, активности катализатора, глубины процесса
иэкономических соображений.
Вреакторах платформинга (риформинга на платиновых катализаторах) давление ВСГ поддерживают на уровне 3,5-4,0 МПа, что позволяет значительно снизить закоксовывание катализатора и соответственно увеличить межрегенерационный пробег установок до нескольких месяцев, а в ряде случаев — до 1,5-2 лет. Практически при работе на алюмоплатиновом катализаторе АП-64 на старых установках каталитического риформинга давление поддерживается от 2,5 до 3,0 МПа. На более современных установках с использованием биметаллических катализаторов рабочее давление составляет 1,4 МПа (установка ЛГ-35-8/ 300Б) и 1,8-2,0 МПа (установка ЛЧ-35-11/600 и ЛЧ-35-11/1000). При использовании отечественных катализаторов серии КР на установках периодческого действия минимальная скорость ихдезактивации соответствует давлению 1,4-1,5 МПа.
5.4. Катализаторы риформинга
Разработку промышленной каталитической ароматизации бензинов начали на базе относительно малоактивных и малоселективных катализаторов типа оксидов хрома и молибдена. В системе процесса, названного гидроформингом, поддерживали давление ВСГ на уровне 1,4 МПа, что приводило к закоксовыванию катализатора, который приходилось регенерировать каждые 6-8 ч. В связи с этим каждый реактор был дублирован. Невысокая активность катализатора позволяла рассчитыватьлишь на более или менее полную дегидрогенизацию нафтенов и на очень малое превращение (дегидроциклизацию) парафинов.
Дальнейшее развитие и совершенствование процесса риформинга шло в направлении разработки высокоактивных и высокоселективных катализаторов. Важнейшим этапом этого развития явился переход от окисных хромо-молибденовых к платиновым катализаторам, и в настоящее время в промышленности используются катализаторы платиновой группы — алюмоплатиновый АП-64, а также биметаллические катализаторы серии КР (КР-104, КР-108, КР-110) и РБ-1. Катализаторы серии КР и РБ, кроме платины, имеют в своем составе рений и кадмий соответственно.
Платиновый катализатор относится к бифункциональным: активный носитель (окись алюминия или алюмосиликат) обладает кислотными центрами, на которых протекают реакции изомеризации нафтеновых колец, гидрокрекинг парафинов и незначительная изомеризация образующихся при гидрокрекинге парафинов и олефинов (с последующим насыщением олефинов водородом). Платина, тонко диспергированная
СПБГУАП группа 4736 https://new.guap.ru/i03/contacts
и нанесенная равномерно на поверхности носителя, обладает гидрирующимидегидрирующими свойствами и положительно влияет на реакции дегидрирования и дегидроциклизации.
Для усиления активности носителя к его поверхности подают галоген (хлор или фтор в виде НС1 или HF соответственно). Галоген (чаще всего хлор) вводят в период регенерации катализатора или вместе с сырьем. Гидрокрекирующая активность носителя определяется количеством активных центров, находящихся вблизи «кристаллитов» платины и предохраняющих их от закоксовывания.
Дегидрирующая активность платинового катализатора имеет максимум при содержании платины на носителе всего 0,08% мае., однако промышленные катализаторы содержат 0,5-0,6% мае. платины. Соотношение масс осажденной платины и подаваемого галогена близко к единице.
К биметаллическим катализаторам относится платино-рениевый, в котором на тех же носителях находятся оба металла в количествах, примерно равных (по -0,4% мае.). Присутствие второго металла (рения) препятствует рекристаллизации платины — укрупнению ее кристаллитов с течением времени и, соответственно, уменьшению числа ее активных центров. Промышленный процесс на этом катализаторе назвали рени-формингом. Платино-рениевый катализатор позволяет вести процесс при 470500°С и 1,4-2,0 МПа. Кроме рения, в качестве второго металла используют германий, иридий, олово и свинец.
Характеристика катализаторов риформинга приводится в табл. 5.4 (основные показатели). Заданное октановое число катализата — не менее 85.
Основные показатели катализаторов риформинга
|
Показатели |
АП-64 |
КР106А |
КР104А |
КР- |
КР-110 |
|
|
|
|
|
108 |
|
|
Химический состав, % |
|
|
|
|
|
|
мае.: |
|
|
|
|
|
|
платина |
0,62 |
0,6 |
0,36 |
0,36 |
0,36 |
|
рений |
— |
0,3 |
0,21 |
0,36 |
0,20 |
|
кадмий |
— |
— |
0,25 |
0,25 |
0,25 |
|
хлор |
0,75 |
1,75 |
1,2 |
1,35 |
1,35 |
|
сульфат-ион |
— |
— |
— |
0,38 |
0,38 |
|
Насыпная плотность |
0,64 |
0,63 |
0,64 |
0,63 |
0,63 |
|
катализатора, г/см3 |
|
|
|
|
|
|
Коэффициент |
0,97 |
|
1,05 |
|
|
|
прочности, кг/мм, |
|
|
|
|
|
|
средний |
|
|
|
|
|
|
Размер экструдатов, мм: |
|
|
|
|
|
|
диаметр |
|
|
2,8 |
|
|
|
длина |
|
|
5 |
|
|
|
Удельная поверхность, |
195 |
— |
|
210 |
|
|
м2Д, не менее |
|
|
|
|
|
|
температура процесса, |
510 |
510 |
500 |
490 |
490 |
|
°С |
|
|
|
|
|
|
октановое число |
86 |
86,5 |
89 |
85,0 |
86 |
|
бензина по м.м. |
|
|
|
|
|
|
выход дебутанизиро |
83 |
80 |
80 |
84 |
84 |
|
ванного бензина %, не |
|
|
|
|
|
|
менее м.м. |
|
|
|
|
|
Алюмоплатиновый катализатор АП-64 осерняют при изготовлении в целях недопущения дезактивации его при хранении, загрузке и для подавления чрезмерной крекирующей функции его при пуске на свежем катализаторе.
СПБГУАП группа 4736 https://new.guap.ru/i03/contacts
Катализаторы серии КР, в отличие от АП-64, поставляются не осерненными, что делает их более чувствительными к условиям хранения и загрузки. При пуске установок, для подавления повышенной крекирующей способности этих катализаторов требуется их осернение.
5.5. Принципиальные технологические схемы каталитического риформинга
Современные установки каталитического риформинга для производства высокооктановых компонентов автобензина состоят из трех блоков: предварительной гидроочистки; каталитического риформинга; стабилизации и фракционирования катализата.
Блок предварительной гидроочистки сырья каталитического риформинга.
Основным назначением предварительной гидроочистки сырья является удаление из него веществ, дезактивирующих монометаллические, биметаллические и полиметаллические платиновые катализаторы риформинга. К этим веществам относятся: соединения серы и азота, металлоорганические соединения, содержащие мышьяк, медь и др., а также непредельные соединения, входящие в состав бензинов вторичного происхождения.
Удаление этих веществ осуществляется на гидрирующих алюмо-ко- бальтили алюмо-никель-молибденовых катализаторах. Продукты гидрирования этих веществ (сероводород и аммиак) удаляются из гидрогенизата в сепараторе ВСГ. Соединения металлов отлагаются на катализаторе гидроочистки и постепенноснижаютегоактивность. Удаление воды в отпарной колонне позволяет подготовить гидрогенизат для блока каталитического риформинга по содержанию влаги.
Принципиальная схема блока предварительной гидроочистки бензинов приведена на рис. 5.1. Сырье насосом Н-1 подается для нагрева продуктами реакции в теплообменник Т- I, проходит через змеевик печи П и поступает в реактор Р с температурой 330-350°С. Давление в реакторе находится в пределах 3,5-4,0 МПа. В реакторе проходит гидрирование сырья риформинга под давлением циркулирующего водородсодержащего газа. Гидрогенизат отдает свое тепло в рибойлереТ-2 для нагрева низа колонны К, и направляется для охлаждения в воздушный холодильник АВО и водяной холодильник X, далее в сепаратор С, где происходит отделение водородсодержащего газа от гидрогенизата. Водородсодержащий газ возвращается в систему циркуляции, а нестабильный гидрогенизат — в стабилизационную колонну К. Часть ВСГ, смешиваясь водородсодержащим газом риформинга, поступает на прием циркуляционного компрессора П К, а затем — втройник смешения с сырьем перед входом в теплообменник Т-1. Гидрогенизат из сепаратора С, пройдя теплообменник Т-3, поступает в среднюю часть колонны К, на верх которой подается орошение насосом Н-2 из газосепаратора Е. Сверху колонны К удаляется легкая часть сырья вместе с летучими продуктами реакции, которая, пройдя воздушный конденсаторхолодильник АВО и водяной холодильник X, собирается в газосепараторе Е, из верхней части которого сухой газ сбрасывается на факел, а вода из нижней части, по мере ее накопления — в закрытую канализационную систему. Стабильный гидрогенизат с низа колонны К через теплообменник Т-3 поступает в систему каталитического риформинга.
Катализаторы гидроочистки. Для предварительной гидроочистки сырья каталитического риформинга используют катализаторы марок АКМ, АНМС, ГО-3О-7,
ГО-70.
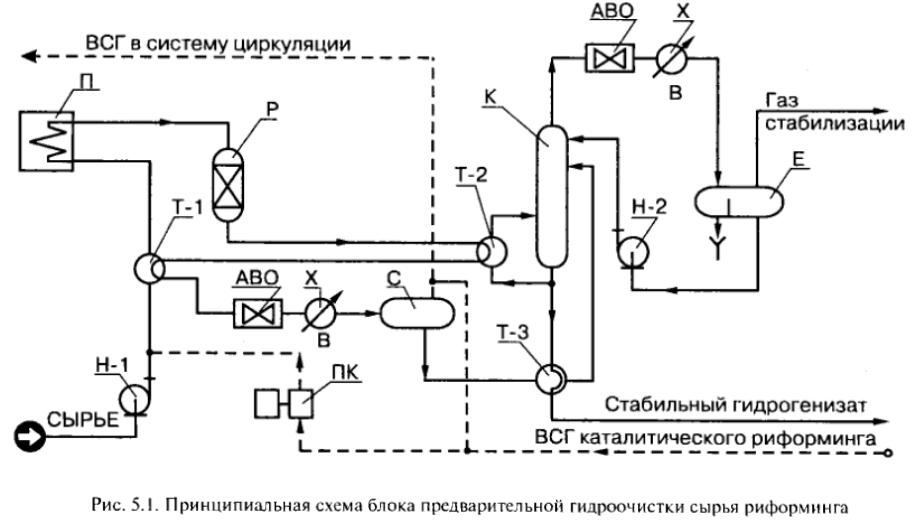
СПБГУАП группа 4736 https://new.guap.ru/i03/contacts

СПБГУАП группа 4736 https://new.guap.ru/i03/contacts
Т а б л и ц а 5 . 5
Основная характеристика катализаторов гидроочистки
Показатели |
|
Катализаторы |
|
|
|
АКМ |
АНМС |
ГО-ЗО-7 |
Г0-70 |
Цвет |
Сине- |
Голубовато |
Зеленовато- |
Голубовато |
катализатора |
голубой |
- белый |
белый |
- белый |
|
||||
|
|
|
|
|
Размер гранул, |
|
|
|
|
мм: |
|
|
|
|
длина |
4-7 |
4-7 |
— ' |
— |
|
|
|
|
|
диаметр |
4-5,5 |
4-5,5 |
2 ±0,5 |
1,8-5 |
|
|
|
|
|
Содержание |
|
|
|
|
активных |
|
|
|
|
компонентов, % |
|
|
|
|
мае.: |
|
|
|
|
окись кобальта |
4 |
— |
— |
— |
(СоО), не |
|
|
|
|
менее |
|
|
|
|
закись никеля |
— |
4 |
4 |
4 |
(Ni,0), не менее |
|
|
|
|
|
|
|
|
|
трехокись |
12 |
12 |
17-19 |
12 |
молибдена |
|
|
|
|
(МоО_,), не |
|
|
|
|
менее |
|
|
|
|
Содержание |
|
|
|
|
вредных |
|
|
|
|
примесей, % |
|
|
|
|
мае., не более: |
|
|
|
|
окись железа |
0,16 |
0,13 |
0,20 |
0,15 |
(Fe,Oj) |
|
|
|
|
|
|
|
|
|
окись натрия |
0,08 |
0,2 |
0,1 |
0,1 |
(Na,0) |
|
|
|
|
|
|
|
|
|
Насыпная |
0,64- |
0,64-0,74 |
0,8-0,9 |
0,64- |
плотность, |
0,74 |
|
|
0,78 |
r/CMJ |
|
|
||
|
|
|
|
|
Индекс |
1,1 |
1,2 |
1,0 |
1,2 |
прочности на |
|
|
|
|
раскалывание, |
|
|
|
|
кг/мм, средний |
|
|
|
|
Удельная |
100 |
100 |
200 |
330 |
поверхность, |
|
|
|
|
м2/г, не менее |
|
|
|
|
Основные реакции, протекающие при гидроочистке. В бензинах сернистые соединения представлены меркаптанами (R-SH), сульфидами (R-S-R') и дисульфидами (R-S-S-R'). Кроме указанных соединений, в бензиновых фракциях вторичного происхождения присутствуют непредельные углеводороды. При высоких температурах они склонны к полимеризации и образованию кокса.
Меркаптаны, сульфиды и дисульфиды легко гидрируются в соответствующие углеводороды при сравнительно мягких температурных условиях. Реакции гидрирования указанных сернистых соединений протекают следующим образом: