
1672
.pdfединения и скапливаются в виде валиков над дефектами [3, 4]. Формы этих скоплений соответствуют очертаниям выявляемых дефектов.
Данный метод контроля отличается высокой чувствительностью при выявлении тонких и мелких трещин, простотой и оперативностью выполнения, а также наглядностью результатов. Этот метод широко применяют для контроля продольных сварных швов конструкций, изготовленных из магнитных материалов. Например, для выявления трещин и узких (стянутых) непроваров в стыковых швах трубопроводов, сваренных дуговыми способами. Для повышения чувствительности метода выпуклости швов перед испытанием целесообразно удалить.
|
Чувств тельность магнитопорошкового метода определяют сле- |
дующ е факторы: |
|
С |
|
|
размер част ц порошка и способ его нанесения; |
напряженность приложенного намагничивающего поля; |
|
|
род пр ложенного тока (переменный или постоянный); |
|
форма, размер глу ина залегания дефектов; |
и ор ентац я дефектов относительно поверхности изделия и на- |
|
|
правлен я намагничивания; |
|
состоян е форма поверхности сварного соединения; |
|
способ намагничивания; |
янный илибАпеременный) существенно не влияет на обнаружение поверхностных дефектов. Однако можно отметить некоторое преимуще-
Частицы ферромагнитного порошка должны иметь диаметр 5…10
мкм, а для выявления глу око залегающих дефектов они должны быть
более крупными. Род используемого для намагничивания тока (посто-
ство применения постоянного тока, обусловленное тем, что постоянный ток создает магнитное поле, глубоко проникающее в металл. Вместе с тем сварные соединения из металла толщиной 20 мм не следует намаг-
ничивать постоянным током, так как их невозможно размагнитить после |
|
контроля. |
Д |
|
|
Магнитными методами контроля наиболее уверенно выявляются |
|
|
И |
плоскостные дефекты (трещины, непровары и несплавления), наибольший размер которых ориентирован под прямым или близким к нему углом относительно направления магнитного потока. Дефекты округлой формы (поры, шлаковые включения и раковины) не могут создавать достаточного потока рассеяния и, как правило, при контроле этим методом обнаруживаются плохо [3, 4].
Практикой установлено, что магнитопорошковым методом выявляются поверхностные и подповерхностные (на глубине не более 2 мм) трещины с раскрытием от 0,001 мм, глубиной (высотой дефекта) от 0,05 мм и длиной не менее 0,5 мм.
31
Если на поверхности контролируемого сварного соединения имеются резкие переходы (например, усиление валика шва, грубая чешуйчатость, подрезы) или крупные микронеровности, то магнитный порошок интенсивнее скапливается не над дефектами, а в местах переходов и углублений. Следовательно, при контроле сварных швов с усилением или грубой чешуйчатостью нельзя однозначно судить о наличии внут-
Сренних дефектов.
Магнитный контроль можно производить в приложенном магнитном поле ли при остаточной намагниченности. Контроль в приложенном магн тном поле производится в тех случаях, когда деталь выполне-
чиваютна из магн томягкого материала. Для выполнения контроля при оста-
точной намагн ченности сварное соединение предварительно намагни- , а после снят я намагничивающего поля на его поверхность наносят магн тную суспензию или порошок. Поскольку такой контроль возможен только при достаточно большой остаточной намагниченности сварного соед нен я, его применяют для проверки деталей из магни-
тотвердых матер алов.
В |
практ ке магнитного контроля используются следующие виды |
намагн |
ч ван я сварных соединений: комбинированное, циркулярное и |
полюсное [3, 4]. Ком инированное намагничивание производят только в |
|
приложенномбмагнитном поле, а циркулярное и полюсное – как в при- |
два или несколькоАмагнитных полей.
ложенном магнитном поле, так и при остаточной намагниченности.
При ком инированном намагничивании одновременно применяют
Циркулярное намагничивание используют для выявления продольных дефектов типа трещин, непроваров и вытянутых шлаковых включений. Его выполняют посредством пропускания тока по контролируемой детали или через проводник, помещенный в имеющееся в ней
отверстие. Циркулярное намагничивание наиболее эффективно при |
|
Д |
|
контроле цилиндрических деталей. |
|
Полюсное намагничивание подразделяют на продольное, попе- |
|
|
И |
речное и нормальное. При продольном полюсном намагничивании направление магнитного поля совпадает с осью сварного шва. Продольное намагничивание осуществляют с помощью электромагнитов, постоянных магнитов или соленоидов.
Дефектоскопы, предназначенные для магнитопорошкового метода контроля, включают в себя источники тока, устройства для подвода тока к детали, для полюсного намагничивания (соленоиды, электромагниты), для нанесения на контролируемую деталь порошка или суспензии, а также измерители тока (или напряженности поля). В дефектоскопах наиболее часто используют циркулярное намагничивание, пропуская переменный ток по детали (или через стержень), и продольное полюс-
32
ное намагничивание постоянным током. Для магнитопорошкового контроля обычно используют дефектоскопы трех видов: стационарные универсальные, передвижные и переносные специализированные.
уть магнитографического контроля (рис. 5.2) заключается в намагничивании контролируемого участка сварного шва и околошовной зоны с одновременной записью магнитного поля на магнитную пленку
Си последующим считывании полученной информации с помощью специального устройства магнитографического дефектоскопа [3].
и
бАР с. 5.2. Схема магнитографического контроля:
1 – намагничивающее устройство; 2 – магнитная пленка; 3 – дефект; 4 – сварной шов
Магнитографический метод в основном применяют для контроля стыковых швов, выполненных сваркой плавлением (преимущественно швов магистральных трубопроводовД). Этим методом можно контролировать сварные узлы и конструкции толщиной до 25 мм.
Практикой установлено, что магнитографическим методом уверенно выявляются внутренние плоскостные дефекты, вертикальный размер которых составляет 8…10% от толщины сварного шва. При снятом усилении шва максимальная чувствительностьИконтроля к указанным дефектам достигает 5%.
При магнитографическом контроле сварные узлы и конструкции намагничивают с помощью специальных электромагнитов, реже применяют циркулярное намагничивание. Для обнаружения внутренних дефектов намагничивание производят постоянным током, а для выявления поверхностных и подповерхностных дефектов – переменным.
Вихретоковая дефектоскопия. Физическую сущность этого метода можно пояснить следующим образом [3]. Если установить рядом две катушки индуктивности (например, трансформаторы без сердечника) и по одной из них, например, катушке I (рис. 5.3), пропускать ток, то при изменении силы тока в этой катушке или при изменении взаимного рас-
33
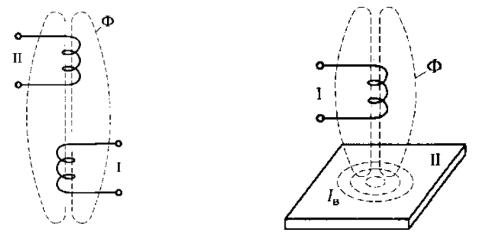
положения катушек I и II в катушке II будет наводится электродвижущая сила.
В процессе выполнения данного метода контроля функцию катушки II выполняет сварной узел, в котором наводятся вихревые точки Iв (рис. 5.4). Вихревые токи протекают в поверхностном слое сварного узла со стороны источника поля. Плотность и распределение вихревых токов в сварном узле зависят от его геометрических и электромагнит-
ных параметров. При наличии дефектов в сварном узле увеличивается |
|
сопрот влен е поверхностного слоя, что приводит к ослаблению вихре- |
|
вых токов, которые регистрируются катушкой-датчиком. |
|
С |
|
и |
|
Рис. 5.3. Схема из двух взаимосвязан- |
Рис. 5.4. Схема образования вихревых |
ных катушек: |
токов в контролируемом объекте: |
Ф – магнитный поток; I и II – катушки |
Ф – магнитный поток; I и II – катушки |
бА |
|
Таким образом, метод вихретоковой дефектоскопии основан на |
|
Д |
регистрации изменения поля вихревых токов, наводимых в сварном узле
следующие
1) |
внешний осмотр сварного соединения и устранение наружных де- |
|
фектов, препятствующих проведению контроля; |
2) |
установку полезадающей системы 1 на контролируемое изделие 2 |
3) |
и пропускание тока через катушку возбужденияИ; |
сканирование поверхности контролируемого объекта вдоль про- |
|
|
дольной оси датчиком 3 с использованием блока регистрирующих |
|
приборов 4; |
4) |
расшифровку результатов контроля и оценку качества изделия. |
Вихретоковая дефектоскопия, применяемая для контроля точечной сварки алюминиевых сплавов, пока не нашла широкого применения при контроле сварных швов, так как электропроводность отдельных зон
34

шва и околошовной зоны значительно изменяется, что создает сильные помехи при выявлении дефектов сварки.
С |
|
при |
|
Р с. 5.5. Схема вихретоковой дефектоскопии: |
|
бА |
|
1 – полезадающая с стема; 2 – контролируемое сварное соединение; 3 – датчик; |
|
4 – блок рег стр рующ х |
оров; стрелками показаны направления перемеще- |
|
ния датчика |
|
Д |
Рис. 5.6. Схема регистрации параметров электромагнитного поля: |
|
1 – полезадающая (генераторная) катушка; 2 – измерительная катушка; 3 – контро- |
|
|
И |
лируемое сварное соединение; I1 – ток в полезадающей катушке; U2 – напряжение в измерительной катушке
Вихретоковые методы контроля подразделяются в основном в соответствии с полезадающими системами. Полезадающие системы различают проходные (в которых катушка с током охватывает детали) и накладные (в которых катушку с током устанавливают на деталь торцом). Измерительные катушки (датчики) могут выполнятся отдельно от полезадающих (генераторных) и обычно располагаются вблизи поверхности контролируемого сварного соединения. Схема регистрации параметров электромагнитного поля приведена на рис. 5.6.
35
|
|
Контрольные вопросы |
|
1. |
На каком физическом эффекте основано выявление дефектов сварных соедине- |
||
ний магнитным и вихретоковым методами? |
|||
2. |
Какие факторы влияют на чувствительность магнитных и вихретоковых методов |
||
контроля сварных соединений? |
|
||
3. |
Какие схемы намагничивания применяются при выполнении контроля магнит- |
||
ными методами? |
|
|
|
4. |
Для каких сварных соединений применяется метод вихретоковой дефектоско- |
||
пии? |
|
|
|
5. |
Как осуществляется регистрация параметров электромагнитного поля при вих- |
||
соединений |
|
||
ретоковой дефектоскоп |
? |
|
|
6. |
Как м образом в контролируемой детали образуются вихревые токи? |
||
С7. Для как х сварных |
|
применяется магнитографический метод контроля? |
|
|
бА |
||
|
|
|
Д |
|
|
|
И |
36
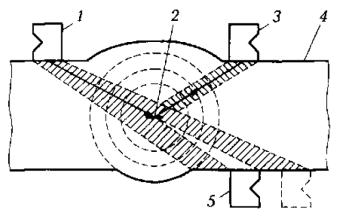
6. УЛЬТРАЗВУКОВОЙ КОНТРОЛЬ СВАРНЫХ СОЕДИНЕНИЙ ЭХО-МЕТОДОМ
Методы ультразвуковой дефектоскопии основаны на исследовании распространения упругих колебаний частотой 0,50…25 МГц в ма-
териале сварного соединения.
Сродными, они на более широко используются при дефектоскопии материалов для о наружения внутренних дефектов [3, 4]. В продольной
Упругие колебания характеризуются следующими параметрами: частотой, длиной волны и скоростью. В твердых телах могут образовываться продольные, поперечные, поверхностные и нормальные колеба-
ния (волны).
Прираспространении в однородном твердом теле интенсивность
Продольные поперечные волны являются объемными и одно-
волне част цы среды коле лются вдоль направления ее распространения, а в поперечной – перпендикулярно направлению ее распространения.
ПрибАультразвуковом контроле (УЗК) сварного соединения 4 (рис. 6.1) преобразователь 1 излучает акустическую волну. От встреченного на пути препятствия в виде дефекта 2 акустическая волна частично отражается и регистрируется преобразователемД1, а частично (зеркально от дефекта) принимается преобразователем-приемником 3. Ослабленная акустическая волна фиксируется преобразователем-приемником 5.
ультразвуковой волны падает из-за явления затухания, вызванного по-
глощен ем |
рассеянием звуковой энергии. Коэффициент затухания |
складывается из коэффициентов поглощения и рассеяния. |
И
Рис. 6.1. Схема ультразвукового контроля сварного соединения: 1 – преобразователь-излучатель; 2 – дефект;
3 и 5 – преобразователи-приемники;
4 – сварное соединение
37
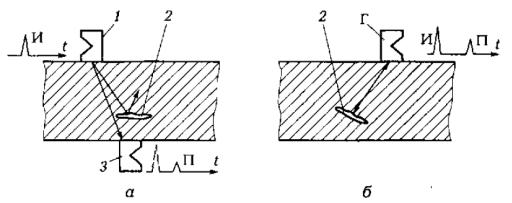
Для контроля сварных соединений наиболее широко применяются два метода обнаружения дефектов: теневой и эхо-метод (рис. 6.2).
Теневой метод применяется только при наличии двухстороннего доступа к контролируемой детали. Признаком наличия дефекта при теневом методе контроля является резкое уменьшение амплитуды или полное исчезновение отраженного сигнала.
Эхо-метод выполняется либо двумя преобразователями, один из которых является излучателем, а второй приемником, либо одним искателем, работающ м в импульсном режиме и излучающим короткий зонд рующ й мпульс, а во время паузы принимающий отраженный
. Последн й вариант эхо-метода называется эхо-методом с со-
вмещенным скателем-излучателем. |
|
С |
|
сигнал |
|
Рис. 6.2. Схемы теневого метода (а) и эхо-метода с совмещенным |
искателем (б) |
бА |
|
о наружения дефектов сварных соединений:
1 – преобразователь-излучатель; 2 – дефект; 3 – приемник; 4 – излучатель-искатель; И – вводимый сигнал; П – сигнал отДдефекта; t – период распространения сигнала
При эхо-методе акустический преобразователь генерирует короткий ультразвуковой импульс, отражающийся от дефекта, а затем принимающийся этим преобразователем. Признаком наличия дефекта в сварном соединении при использовании эхоИ-метода является увеличение амплитуды эхо-сигнала, пропорциональное площади отражателя.
Основные измеряемые характеристики дефекта. Наиболее про-
стой измеряемой характеристикой дефекта является амплитуда эхосигнала. Однако эта характеристика не позволяет однозначно определить размеры дефекты, так как зависит от характера его поверхности (зеркальная или шероховатая), а также от ее ориентации по отношению к направлению распространения луча и формы (плоская или округлая).
Несмотря на указанную неоднозначность, разделение дефектов на допустимые и недопустимые производят по амплитуде эхо-сигнала. Для этого сравнивают амплитуды эхо-сигналов от реального дефекта в сварном соединении и от дефекта в тест-образце сварного соединения, принятого за эталонный и имеющего искусственные отражатели (угловые
38

или сегментные, с внутренней отражающей плоскостью, цилиндрической поверхностью, боковым или плоскодонным отверстием). Тестобразцы изготавливают из металла, по акустическим свойствам соответствующего металлу контролируемого шва. В табл. 6.1 приведены акустические характеристики некоторых металлов.
|
|
Акустические характеристики некоторых металлов |
Таблица 6.1. |
||||||||||
|
|
|
|
||||||||||
|
|
|
|
|
Длина |
|
|
|
|
|
|
||
|
|
Скорость рас- |
|
волны, |
Коэффициент |
Модуль |
|
Плотность |
|||||
|
Металл |
пространения |
|
мм, при |
затухания |
упругости |
|
||||||
|
|
|
|
|
|
|
|
-10 |
|
|
3 |
||
С |
волны, м/с |
|
частоте |
δmax, см-1 |
E·10 |
|
, |
|
ρ, г/см |
||||
|
|
|
2,5 |
МГц |
|
Па |
|
|
|
||||
ci |
ct |
|
λi |
|
λt |
|
|
|
|
|
|
||
|
|
|
|
|
|
|
|
|
|
||||
|
Алюм н й |
6260 |
3080 |
|
2,50 |
|
1,23 |
0,050 |
7 |
|
|
|
2,7 |
|
(сплавы) |
|
|
|
|
|
|||||||
|
|
|
|
|
|
|
|
|
|
|
|
|
|
|
(сплавы) |
6000 |
3500 |
|
2,40 |
|
1,40 |
- |
16 |
|
|
4,5 |
|
|
|
|
|
|
|
|
|
|
|
|
|
|
|
|
Титан |
|
|
|
|
|
|
|
|
|
|
||
|
Сталь |
5850 |
3230 |
|
2,34 |
|
1,30 |
0,080 |
20 |
|
|
7,8 |
|
|
Медь |
4700 |
2260 |
|
1,89 |
|
0,91 |
0,044 |
10 |
|
|
8,9 |
|
|
Примечание. Индекс i имеют характеристики продольных волн, а индекс t – попе- |
||||||||||||
|
речных. |
|
|
|
|
|
|
|
|
|
|
|
|
определяетбАГОСТ 14782 – 86. Если эхо-сигнал от реального дефекта больше, чем от искусственного, принятого за эталонный по инструкции, то деталь бракуется.
Форму, размеры и глу ину залегания искусственных отражателей
Координаты дефекта можно определять с помощью специальной шкалы на дефектоскопе, специальной приставки к нему или расчетом
(рис. 6.3). Д И
Рис. 6.3. Схемы определения координат дефекта при контроле сварного соединения прямым (а) и наклонным (б) искателями:
Н – глубина залегания дефекта; L – расстояние от искателя до дефекта; r – полярная координата расположения дефекта; α – угол между нормалью к поверхности детали и нормалью к поверхности дефекта
39
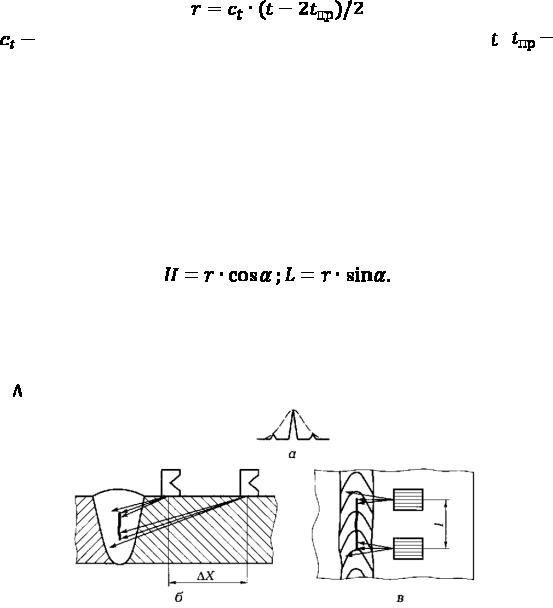
|
Расстояние от точки ввода луча до дефекта по его ходу определя- |
||||||
ется по формуле |
|
|
|
|
|
||
где |
скорость распространения поперечной волны, м/с; , |
пе- |
|||||
риод распространения волны соответственно от пьезопластины до де- |
|||||||
фекта и обратно и в призме преобразователя, с. |
|
|
|||||
|
Прямым |
искателем |
определяют |
глубину |
залегания |
дефекта |
|
(рис. 6.3, а), используя для этого скорость продольной волны и время ее |
|||||||
движен я до дефекта на глубину залегания Н. |
|
|
|||||
|
Наклонным |
скателем можно определить расстояние r от искателя |
|||||
до дефекта по скорости c и времени движения волны t, а затем, зная |
|||||||
Сугол ввода луча α, |
глубину залегания Н, мм, дефекта и расстояние |
||||||
L, мм (р с. 6.3, |
): |
|
|
|
|
|
|
|
Условные размеры дефекта определяют при перемещении наклон- |
||||||
ного |
скателя в пределах, где значение эхо-сигнала, отраженного от де- |
||||||
найти |
|
|
|
|
|||
фекта, увел ч вается от минимального до максимального, а затем вновь |
|||||||
до м н мального (р с. 6.4, а). Также можно определить условную ши- |
|||||||
рину X и условную длину дефекта l (рис. 6.4, б, в). |
|
|
|||||
|
бА |
|
|
||||
|
Рис. 6.4. Схемы определения условных размеров дефекта: |
|
|||||
|
|
|
|
Д |
|
||
|
а – протяженности; б – глубины распространения; в – длины |
|
|||||
|
Основные параметры ультразвукового контроля. Минимальный |
||||||
размер выявляемых дефектов зависит от частоты ультразвуковых коле- |
|||||||
баний: чем больше частота, тем лучше обнаруживаются дефекты малых |
|||||||
размеров. |
|
|
|
И |
|||
|
|
|
|
|
|
||
|
Волны низкой частоты и большей длины огибают малые дефекты |
||||||
без отражения от них. |
|
|
|
|
|||
|
Абсолютная чувствительность методов ультразвукового контроля |
||||||
определяется размерами минимального дефекта, уверенно выявляемого |
|||||||
в реальном сварном соединении, а предельная чувствительность – ми- |
|||||||
нимальными размерами искусственного отражателя в тест-образце, уве- |
40