
1672
.pdf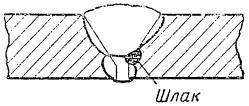
Прожог – это дефект в виде сквозного отверстия в сварном шве, образовавшегося в результате вытекания части металла сварочной ванны. Причинами прожога являются чрезмерно высокая погонная энергия, заниженная скорость сварки, чрезмерный зазор между свариваемыми деталями и т.п. Особенно часто прожоги возникают при сварке тонких деталей, т.е. когда ширина сварочной ванны превышает толщину дета-
Слей.
Внутренние дефекты. Газовые включения (поры) образуются при перенасыщен сварочной ванны газами вследствие загрязненности
кромок здел я, дл нной дуги, влажности обмазки и флюсов, вредных чисткипримесей влаги в защитных газах и т.п. Размеры пор колеблются от
микроскоп ческ х до 2…3 мм в диаметре. Поры снижают прочность и плотность швов. В малом количестве поры могут и не влиять на работоспособность соед нений.
ШлаковыебАвключения (шлаки) появляются обычно вследствие плохой зач стки кромок от окалины и ржавчины, а чаще от плохой зашлака при многослойной сварке (рис. 1.8). Значительные по велич не острые включения могут вызывать местную концентрацию
напряжен й, а также снижать прочность соединений. Микроскопические шлаковые включения – загрязнения в виде нитридов, фосфидов, сульфидов, легкоплавких эвтектик, окиси железа снижают пластичность швов. Небольшие округлые включения обычно не опасны.
Рис. 1.8. Шлаковое включениеДна кромкеИв многослойном шве
Металлические включения имеют место при аргоно-дуговой сварке неплавящимся электродом и обычно состоят из частичек вольфрама.
Непровары представляют собой несплошности значительной величины (раскрытия) на границах между основным и наплавленным металлом или незаполненные металлом полости в сечении шва. Встречаются непровары по кромкам (рис. 1.9, а), по сечению и в корне шва (рис. 1.9, б, в, г). Непровары образуются при загрязнении кромок, неправильной подготовке кромок, неправильном или неустойчивом режиме сварки и т.п. Непровары могут снизить работоспособность соединения за счет ослабления рабочего сечения шва и, кроме того, острые непровары могут создать концентрацию напряжений в шве.
11
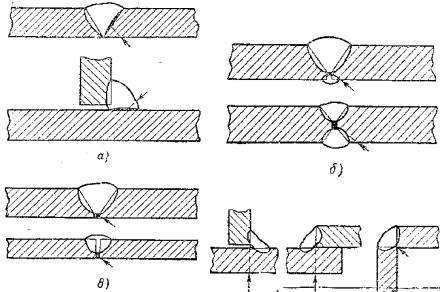
Трещины считают самым опасным дефектом сварки. Они могут микро- и макроскопическими, а в зависимости от происхождения – горячими и холодными.
СибАР с. 1.9. Непровары в стыковых швах:
а – по кромке; – в середине шва; в – в корне шва; г – в угловых швах
Горячие трещины при сварке образуются в процессе затвердевания металла, вследствие резкого снижения пластических свойств метал-
ла в этом интервале температур и развития растягивающих деформаций. Холодные трещины образуются в результате протекания фазовых превращений, приводящих к снижениюДпрочностных свойств металла, и воздействия сварочных напряжений. Холодные трещины могут образовываться как на этапе завершения охлаждения, так и во время вылеживания сварных конструкций в течение некоторого периода времени после сварки. И Иногда трещины развиваются в процессе эксплуатации вследствие раскрытия сварочных микротрещин, а также зарождения разрушения металла от надрезов, вызванных непроваром, шлаковыми включениями
и прочими дефектами [1].
Трещины могут быть продольными и поперечными и располагаться в металле шва или в зоне термического влияния.
Трещины вследствие своей чрезвычайной опасности – недопустимый дефект. Сварные соединения с трещинами, как правило, подлежат исправлению. Однако в связи с развитием науки о прочности появились воззрения о допустимости некоторых трещин в тех случаях, когда имеются условия к прекращению их роста. Критические размеры таких трещин рассчитывают на основе уравнений линейной механики разрушения и специальных экспериментов.
12
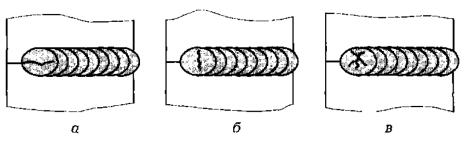
Продольные трещины (рис. 1.10, а) проходят вдоль сварного шва. Они могут образовываться в металле шва и в зоне термического влияния основного металла. Конфигурация таких трещин, главным образом, определяется очертаниями линии сплавления основного металла и металла шва. Продольные трещины могут возникать вследствие наличия высокотемпературной хрупкости металла (горячие трещины) или при
Сего замедленном разрушении (холодные трещины).
Рис. 1.10. Трещины разных типов:
Поперечныебтрещины (рис. 1.10, б) проходят поперек сварного шва. Они могут о разовываться в металле шва, зоне сплавления и зоне термического влияния основного металла. Такая ориентация поперечных трещин связана с влиянием продольных составляющих сварочных напряжений. Причины их возникновения те же, что и продольных, и
а – продольная; – поперечная; в – разветвленная
они также могут ытьАгорячими и холодными.
Разветвленные трещины (Дрис. 1.10, в) представляют собой группы соединенных трещин, образованных от одной общей трещины. Такие
трещины могут образовываться в металле шва и зоне термического влияния основного металла. Конфигурация этих трещин определяется
микроструктурой зон сварных соединений, а также характером терми- И
ческих, фазовых, ликвационных и механических напряжений. Причины их возникновения те же, что и продольных.
Основные причины образования наружных дефектов при контактной сварке приведены в табл. 1.2.
13
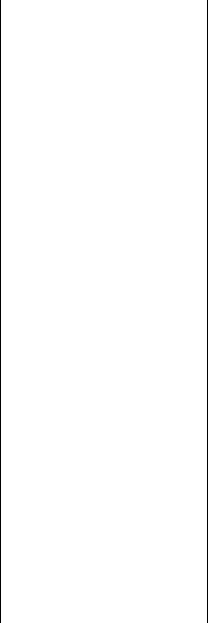
|
|
|
|
|
|
Таблица 1.2. |
|
|
|
|
|
Наружные дефекты сварных соединений, |
|
||
|
характерные для контактной сварки, и причины их образования |
|
|||||
|
Виды дефектов |
|
Возможные причины образования дефектов |
||||
|
Неправильная |
форма |
от- |
Неправильная заточка или неравномерный износ ра- |
|||
|
печатков |
|
электродов |
в |
бочих поверхностей электродов; перекос деталей и |
||
|
точечном или роликовом |
электродов при сварке; избыточная скорость ролико- |
|||||
С |
|
вой сварки |
|
||||
|
соединении |
|
|
|
|||
|
Глубокая вмятина на по- |
|
|
||||
|
верхности |
детали |
от |
Большая длительность импульса тока; недостаточное |
|||
|
электрода |
перегрев де- |
давление электрода; чрезмерный сварочный ток |
|
|||
|
тали |
|
|
|
|
|
|
|
сильный |
Загрязнение поверхностей свариваемых деталей или |
|||||
|
Местный |
|
прожог |
ли |
электродов; недостаточное давление электродов; не- |
||
|
плеск |
|
наружный |
вы- |
правильная форма контактных поверхностей |
элек- |
|
|
|
расплавленного |
тродов; чрезмерная скорость роликовой сварки |
лег- |
|||
|
металла |
бА |
|
||||
|
|
|
|
|
|
ких сплавов |
|
|
|
|
|
|
|
Малое усилие сжатия электродов; недостаточное ох- |
|
|
|
|
|
|
|
лаждение электродов; недостаточное ковочное дав- |
|
|
Трещ на |
|
|
|
|
ление электродов при сварке легких сплавов; |
чрез- |
|
|
|
|
|
мерное время запаздывания подачи ковочного давле- |
||
|
|
|
|
|
|
||
|
|
|
|
|
|
ния; из ыточная длительность импульса сварочного |
|
|
|
|
|
|
|
тока |
|
|
Выход литого металла на |
|
|
||||
|
поверхность |
соединения |
Недостаточно тщательная очистка поверхностей сва- |
||||
|
и темна поверхность зо- |
||||||
|
риваемых деталей и электродов; малое усилие сжатия |
||||||
|
ны его выхода. Повреж- |
электродов; избыточная длительность импульса сва- |
|||||
|
дение |
|
плакирующего |
||||
|
слоя при сварке сплавов |
рочного тока; избыточный сварочный ток |
|
||||
|
|
|
|||||
|
типов Д16 и В95 |
|
|
|
|||
|
Раздавливание и трещи- |
Недостаточное расстояние между сварными точками |
|||||
|
и кромкой соединения; завышенный сварочный ток; |
||||||
|
ны металла у кромки со- |
чрезмерная длительность импульса тока; избыточное |
|||||
|
единения |
|
|
|
|
ковочноеДдавление |
|
|
Контрольные вопросы |
1. |
Какие дефекты характеризуют свариваемостьИметалла? |
2. |
Каковы критерии количественной и качественной оценки дефектов? |
3. |
Какими факторами оценивается критичность дефекта? |
4. |
По каким причинам образуются холодные трещины? |
14
2. ВИЗУАЛЬНО-ИЗМЕРИТЕЛЬНЫЙ КОНТРОЛЬ СВАРНЫХ СОЕДИНЕНИЙ
Визуально-оптический контроль – один из наиболее простых, общедоступных и высокопроизводительных видов неразрушающего кон-
троля [2, 3]. |
|
|
Используют два варианта выполнения визуально-измерительного |
контроля: |
|
|
внешн й осмотр сварных соединений изменение их геометриче- |
|
ск х размеров после изготовления партии деталей; |
|
акт вный внешний осмотр, т.е. контроль, выполняемый в процессе |
|
сварки с спользованием оперативной обратной связи в целях ре- |
С |
|
|
гул рован я технологических режимов. |
|
В зуальнозмерительный контроль выполненных сварных со- |
й конструкц й и конструкций и узлов производят в целях:
выявлен я деформаций, поверхностных трещин, подрезов, прожо-
гов, наплывов, кратеров, свищей, пор, раковин и других несплош- |
|
единен |
|
ностей |
дефектов формы швов; |
проверки геометрических параметров сварных швов и допустимо- |
|
сти |
дефектов. |
Визуальныйобнаруженныхконтроль сварных соединений производится в первую |
очередь, т.е. до использованияАостальных неразрушающих методов контроля (радиационного, ультразвукового и др.). Перед визуальным контролем поверхности основногоДметалла и сварного соединения (наплавки) очищают от влаги, шлака, брызг металла, ржавчины и других загрязнений, препятствующих проведению контроля [3].
Геометрические измерения сварных швов выполняют после визу-
ального контроля или одновременно с ним. Измерения деталей, подго-
товленных
тролируемая
примыкающие
ной
И
не менее 5 мм – для стыковых соединений, выполненных дуговой и электроконтактной стыковой сваркой оплавлением при номинальной толщине свариваемых деталей до 5 мм включительно;
не менее номинальной толщины стенки детали – для стыковых соединений, выполненных дуговой, электронно-лучевой или электроконтактной стыковой сваркой оплавлением, а также сваркой встык нагретым элементом при номинальной толщине свариваемых деталей от 5 до 20 мм;
15
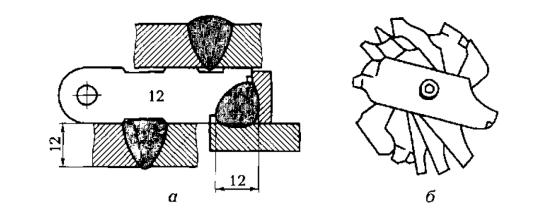
не менее 20 мм – для стыковых соединений, выполненных дуговой
|
или электроконтактной стыковой сваркой оплавлением при номи- |
|
нальной толщине свариваемых деталей свыше 20 мм, и для стыко- |
|
вых и угловых соединений, выполненных газовой сваркой, неза- |
|
висимо от номинальной толщины стенки свариваемых деталей, а |
|
также при ремонте дефектных участков сварных соединений; |
С |
|
|
не менее 5 мм – для угловых, тавровых, торцевых и нахлесточных |
сварных соединений и соединений (в том числе при вварке труб в трубные доски), выполненных дуговой сваркой, независимо от ном нальной толщины свариваемых деталей;
проведениемного металла продуктов коррозии, препятствующих проведению кон-
не менее 50 мм – для сварных соединений, выполненных электрошлаковой сваркой, независимо от номинальной толщины свари-
ваемых деталей.
Перед |
визуально-измерительного контроля поверх- |
ность |
в зоне контроля подлежит очистке [3, 4] от ржавчины, |
троля объекта(на контрол руемых поверхностях допускается наличие цветов побежалости, в случае если это оговорено в производственно-
окал ны, загрязнен й, краски, масла, влаги, шлака, брызг расплавлен-
технической документации). Зона очистки должна определяться в нормативной документации на вид конкретной работы или на конкретную конструкцию.
А Д
Рис. 2.1. Схема специального шаблона (с маркировкойИ12) для контроля сварных швов (а) и набор шаблонов для контроля угловых швов (б)
Параметры шероховатости очищенных для проведения контроля поверхностей деталей, сварных соединений, а также поверхностей разделки кромок деталей, подготовленных под сварку, не должны превышать значений Ra, равного 12,5, и Rz, равного 80.
При визуально-измерительном контроле применяют:
лупы, в том числе измерительные;
линейки металлические;
угольники поверочные с углом 90° лекальные;
16
|
штангенциркули и штангенглубиномеры; |
|
|
щупы; |
|
|
угломеры с нониусом; |
|
стенкомеры и толщиномеры индикаторные; |
||
|
микрометры; |
|
нутромеры микрометрические и индикаторные; |
||
С |
|
|
|
калибры; |
|
|
эндоскопы; |
|
|
шаблоны (р с. 2.1), в том числе специальные и универсальные |
|
|
(напр мер, т па УШС), радиусные, резьбовые и др.; |
|
змерительный |
|
|
|
пл ты поверочные; |
|
|
плоскопараллельные концевые меры длины с набором специаль- |
|
|
ных пр надлежностей; |
|
|
штр ховыемерыдлины(стальные измерительные линейки,рулетки). |
|
|
В зуально- |
контроль проводят и невооруженным |
личения.бА
глазом, ( ли) с пр менением визуально-оптических приборов до 20кратного увел чен я (луп, микроскопов, эндоскопов, зеркал и др.).
Для контроля основного металла и металла сварных соединений (наплавок) при зготовлении, строительстве, монтаже, ремонте и реконструкции технических устройств и сооружений используют лупы с 2 - 7-кратным увеличением, а при оценке состояния технических устройств и сооружений в процессе их эксплуатации – лупы до 20-кратного уве-
Технология измерительногоДконтроля. Измерительный контроль геометрических размеров сварного соединения – размеров конструк-
тивных элементов сварных швов, геометрического положения осей или поверхностей сваренных деталей, углубленных впадин между валиками
шва и чешуйчатости поверхности шва, выпуклости и вогнутости корней односторонних швов и других следует проводитьИв местах, указанных в
рабочих чертежах, а также в местах, где соответствие указанных показателей допустимым значениям вызывает сомнение при визуальном контроле [3].
Выпуклость (вогнутость) стыкового шва оценивается по максимальной высоте (глубине) расположения его поверхности от уровня расположения наружных поверхностей деталей. В случае, когда уровни наружных поверхностей деталей одного типоразмера (диаметр, толщина) не совпадают, измерения следует производить относительно той поверхности, которая расположена выше (рис. 1.2, а). В случае если несовпадение уровней поверхностей деталей обусловлено разной их толщиной, оценку выпуклости (вогнутости) поверхности шва выполняют относительно линии, соединяющей края поверхности шва в одном сечении (рис. 1.2, б). Размеры выпуклости (вогнутости) стыкового и углово-
17
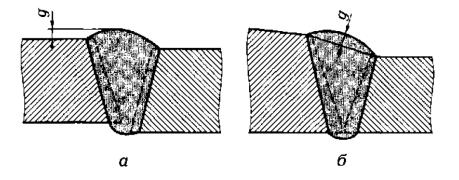
го швов определяются с помощью универсальных или специальных шаблонов.
Выпуклость (вогнутость) корня шва оценивается по максимальной высоте (глубине) расположения его поверхности относительно уровня расположения внутренних поверхностей сваренных деталей.
С |
|
|
|
|
при |
|
|||
|
Р с. 2.2. Схемы измерений выпуклости (вогнутости) стыкового |
|||
|
шва g |
разных уровнях наружных поверхностей деталей, вы- |
||
|
сборке |
соединения под сварку (а) и |
||
|
званных |
х смещением при |
||
|
|
|
неодинаковой толщиной деталей (б) |
|
|
|
А |
||
|
|
|
Контрольные вопросы |
|
5. |
Какие параметры проверяют при инструментальном контроле сварных швов? |
|||
6. |
Какова цель внешнего осмотра сварного соединения? |
|||
7. |
Какие дефекты выявляются внешним осмотром? |
|||
8. |
|
|
Д |
|
Какие инструменты применяют при внешнем и инструментальном контроле |
||||
сварных соединений? |
|
|
||
|
|
|
|
И |
18
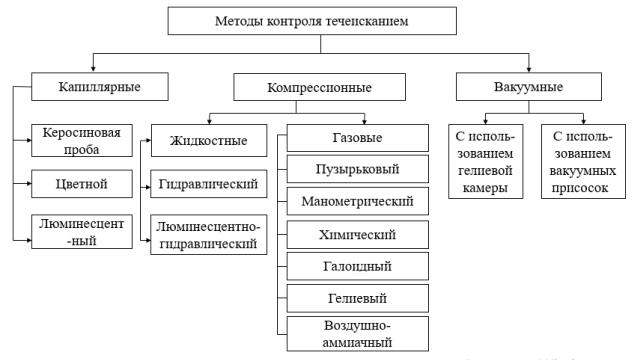
3. КОНТРОЛЬ ГЕРМЕТИЧНОСТИ СВАРНЫХ СОЕДИНЕНИЙ
Герметичность – это способность конструкции ограничивать проникновение жидкости или газа сквозь входящие в нее элементы и их соединения [2, 4]. Степень герметичности определяется утечкой газа или жидкости в единицу времени.
СИспытание конструкций на герметичность, или контроль течеисканием, выполняют с применением пробных веществ (жидкостей или газов), которые легко проникают через сквозные дефекты и хорошо различ мы в зуально ли с помощью приборов – течеискателей и других
ненияхсредств рег страц .
Контроль тече сканием позволяет обнаруживать в сварных соедиосновном металле сварных конструкций сквозные дефекты типа трещ н, непроваров, газовых пор, свищей, прожогов и др. размеры
сквозныхбАдефектов ввиду невозможности измерения их линейных размеров условно оцен вают потоком пробного вещества, протекающего через дефект в ед н цу времени.
Согласно ГОСТ 18353 – 73 различают капиллярные, компрессионные вакуумные методы контроля течеисканием. Подразделение этих методов в зависимости от вида и способа индикации, применяемых пробного вещества и аппаратуры, а также технологических особенностей показано на рис. 3.1.
Д И
Рис. 3.1. Классификация методов контроля течеисканием
19
Выбор метода контроля течеисканием определяется уровнем требований к степени герметичности испытуемого объекта, действующей газовой нагрузкой на оболочку и наличием пробных веществ, допустимых к применению.
Капиллярные методы. Капиллярные методы контроля основаны на явлении капиллярного проникновения жидкости, обладающей высо- Ской смачивающей способностью, в сквозные дефекты сварного соеди-
нения [3].
При спользовании этих методов на одну поверхность изделия, предвар тельно оч щенную от загрязнений, обильно наносят прони-
теликающую ж дкость, например, керосин, а на другую – адсорбирующее
покрыт е в в де меловой обмазки, состоящей из 350…480 г молотого
мела ( каол на), разведенного в 1 л воды.
Выждав определенное время, контролируемое соединение осматривают, выявляя сквозные дефекты по желтым пятнам керосина на меловой обмазке. Для лучшего проявления этих пятен в керосин добавля-
диаметромболее0,1 мм.
ют крас ярко-красного цвета или люминесцирующие вещества.
Данный метод позволяет выявить сквозные дефекты с эффективным
Другие капиллярныеАметоды контроля течеисканием основаны на использовании пенетрантов – красок (цветной метод) или люминофоров (люминесцентный метод).
Метод керосиновой про ы применяют для контроля герметичности сварных соединений наливных емкостей, нефтяных резервуаров,
цистерн, а также других конструкций, в которых доступ к сварным
швам возможен с о еих сторон. Д
Компрессионные методы. Компрессионные методы контроля ос-
нованы на создании в замкнутом испытуемом объекте избыточного давления пробного вещества (жидкости или газаИ) и регистрации на наружной поверхности этого объекта участков его течи. В зависимости от вида применяемого пробного вещества различают жидкостные (гидравлические) и газовые методы контроля течеисканием.
Жидкостные (гидравлические) методы течеискания применяют при контроле различных замкнутых систем (например, паровых котлов, нефтехимической аппаратуры и др.), работающих под давлением. При использовании этого метода контролируемую сварную конструкцию заполняют рабочей жидкостью или водой и герметизируют. Затем с помощью гидравлического насоса создают в ней избыточное давление и, выдержав под этим давлением некоторое время, производят визуальный осмотр наружной поверхности [2, 4]. Признаком наличия дефектов в этом случае является появление капель жидкости (например, воды) или отпотевание наружной поверхности.
20