
1583
.pdfВкладыши из алюминиевых антифрикционных сплавов бывают двух типов: монометаллические и биметаллические. Надежная работа монометаллических вкладышей обеспечивается только в том случае, когда сплав, помимо высоких антифрикционных свойств, является и высокопрочным конструкционным материалом.
Основанием для биметаллических вкладышей чаще всего служит мягкая сталь, но может применяться и высокопрочный алюминиевый сплав типа дуралюмина. При заливке алюминиевых сплавов на стальную ленту возможно образование хрупкого промежуточного слоя – химического соединения алюминия с железом. Поэтому метод плакирования более целесообразен. Пластическая деформация вследствие плавки, кроме того, значительно улучшает структуру заэвтектических сплавов.
Отличительной особенностью алюминиевых сплавов является высокий коэффициент линейного расширения (вдвое больший, чем в стали); для них необходимо применять специальные конструкции подшипников.
Сплав АСМ. Микроструктура состоит из кристаллов химического соединения AlSb и двойной эвтектики: твердого раствора магния и сурьмы в алюминии и химического соединения AlSb.
Поставляемая заготовка. Биметаллическая полоса поставляется с толщиной сплава АСМ 0,9-1,5 мм и толщиной стального основания (из стали 08) 1,3-4,7 мм. Вкладыши изготовляют штамповкой из этой полосы. Чистовую расточку рабочих поверхностей вкладыша необходимо производить на больших скоростях с малой глубиной резания, применяя большие передние углы и тщательную доводку инструмента. Полезно применять охлаждение керосином или скипидаром.
Область применения – серийное производство в тракторной промышленности. Применение сплава АСМ для автомобильных двигателей дало неудовлетворительные результаты. Возможно применение сплава АСМ в качестве заменителя Бр. С30 для вкладышей быстроходных дизелей.
Недостатки:
1)худшая по сравнению с баббитами прирабатываемость к шейкам валов;
2)технология приготовления сплава, вследствие опасности ликвации сурьмы и необходимости перегрева расплава до высоких температур, представляет некоторые трудности;
60
3) низкое качество биметаллической ленты (плохое приставание, наличие газовых пузырей, вызывающих вспучивание слоя при нагреве и т. д.).
Сплав ACC-6-S. Микроструктура состоит из кристаллов химического соединения AlSb, двойной эвтектики (α-твердый раствор магния и сурьмы в алюминии и химическое соединение AlSb) и свободных включений чистого свинца. Коррозийная стойкость такая же, как у баббита Б83.
Поставляемая заготовка представлена в виде калиброванных биметаллических полос. Стальное основание (сталь 08 или 10) может иметь толщину 1,4-5,0 мм, сплав – от нескольких десятых до 1,5 мм и выше. Биметаллическая полоса может подвергаться отжигу при температуре 5500 °С. Происходящая при этом полная рекристаллизация облегчает последующую штамповку вкладышей. Детали изготовляют штамповкой без механической обработки стальной части вкладыша.
Область применения. Благодаря наличию свинца обладает более высокими противозадирными свойствами, чем сплав АСМ. Применение в автомобильных двигателях дало отрицательные результаты.
Сплав АН-2,5. Микроструктура состоит из пластичного твердого раствора никеля в алюминии и эвтектики (α-твердый раствор плюс химическое соединение), располагающейся по границам зерен твердого раствора.
Коррозионная стойкость. Сплав не подвержен коррозионному разрушению при работе в среде масел.
Способ изготовления. Заготовки получают отливкой в кокиль. Может быть получен биметалл: сталь – сплав АН-2,5 для штамповки вкладышей.
Область применения. Применяется в виде монометаллических вкладышей для коренных и шатунных подшипников четырехцилиндровых дизелей мощностью 40 л.
Сплав АЦК. Микроструктура состоит из твердого раствора кремния и цинка в алюминии и эвтектики (твердый раствор и кремнистая составляющая). В литом состоянии эвтектика располагается по границам зерен твердого раствора, в прокатанном – в виде включений, вытянутых в направлении прокатки. Коррозионная стойкость такая же, как и у сплава АСМ.
Поставляемая заготовка. Биметаллическую ленту поставляют после плакирования с последующей калибровкой и рекристаллизационного отжига. Вкладыши изготовляют штамповкой.
61
Область применения. При испытании тракторных двигателей сплав АЦК показал лучшие результаты, чем сплав АСМ.
Преимущества сплава АЦК перед сплавом АСМ:
1)более низкая температура плавки (750 вместо 8500 °С), что уменьшает опасность появления газовых пузырей;
2)введение в сплав кремния и цинка легче, чем введение сурь-
мы;
3)легче прокатывается;
4)легче обрабатывается резанием (для сплава АЦК малопроизводительную алмазную расточку можно заменить протягиванием);
5)лучшая прирабатываемость.
Высокооловянистые алюминиевые сплавы. Микроструктура со-
стоит из твердого раствора и низкоплавкой эвтектики алюминия и олова, содержащей 99,5 % олова и плавящейся при температуре
2280 °С.
Поставляемая заготовка – калиброванные биметаллические полосы. Основание готовится из армко-железа. Для лучшего сцепления сплава с армко-железом применяется подслой из сплава АМК. После калибровки полосы проходят рекристаллизационный отжиг при температуре 550-5700 °С. Вкладыши изготовляют штамповкой.
Область применения. Проверки на двигателях автомобилей показали, что износ шеек вала из сплава не превышал износов, наблюдавшихся при работе с вкладышами, залитыми баббитом БТ.
9. МАХОВИКИ. КОНСТРУКЦИИ МАХОВИКОВ
Основное назначение маховика – обеспечить необходимую равномерность вращения вала двигателя. Вследствие этого уменьшается амплитуда изменения угловой скорости вала. Маховики выполняют и вспомогательные функции. Так как они имеют большие размеры, то для прокручивания вала двигателя при регулировках или пуске двигателя с помощью маховика требуется относительно небольшое усилие; энергия, накопленная в маховике при прокручивании вала перед пуском двигателя, позволяет осуществить вспомогательные такты рабочего цикла в процессе пуска.
Маховики обычно используют для присоединения устройств отбора мощности двигателя; на нем наносят метки ВМТ.
Маховик аккумулирует избыточную энергию в периоды времени, когда Мд > Мn; в периоды времени, когда Мд < Мn, маховик отдает на-
62
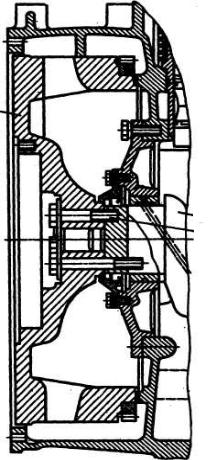
копленную кинетическую энергию для прохождения мертвой точки фаз газораспределения, моментов зажигания или начала впрыска топлива. В двигателях с воздушным охлаждением на маховике часто монтируют вентилятор. В карбюраторных двухтактных двигателях в маховике нередко устанавливают устройства для получения электрического тока для освещения и зажигания.
При больших окружных скоростях маховики отливают или штампуют из малоуглеродистых сталей. Для упрощения балансировки обрабатывают все поверхности маховиков. Маховики быстроходных двигателей подвергают балансировке вместе с валом и другими вращающимися деталями, установленными на валу или маховике.
Для создания достаточного момента инерции при минимальной массе маховик выполняют в виде обода, связанного со ступицей тонким диском, или в форме одного диска. Для съема мощности в стационарных и судовых двигателях к диску крепят на болтах детали муфты.
В современных автомобильных и тракторных двигателях мощность снимается, как правило, с помощью плоской фрикционной муфты, и одна из поверх- ностей маховика в форме диска используется как ведущая поверхность трения.
На маховике крепится зубчатый венец, с которым при пуске входит в зацепление шестерня пускового устройства. Маховики с ободом крепятся на конусе с помощью шпонки, гайки или винта со стопорящим замком.
Все дисковые маховики крепятся на фланце вала или непосредственно на конце вала. Зубчатые венцы сваривают из среднеуглеродистого стального проката необходимого сечения, затем надевают (охладив маховик или подогрев венцы), либо напрессовывают с небольшим натягом, после чего стопорят штифтами или винтами.
Коленчатые валы тракторных двигателей нередко подключают к трансмиссии под нагрузкой. Поэтому их маховики
63
выполняют в виде толстых дисков, обеспечивающих не только большой момент инерции, но и интенсивный отвод теплоты от трущихся поверхностей дисков сцепления в металл маховика, способствуя этим увеличению работоспособности сцеплений.
При использовании маховика в качестве вентилятора в двигателях воздушного охлаждения обод со ступицей соединяют спицами, которым придают форму лопастей (рис. 12).
В многоцилиндровых двигателях, работающих с гидродинамическими передачами на электрогенераторы и гребные валы, маховики отсутствуют, так как моменты инерции колес насосов, роторов генераторов, валов с винтами и деталей соединительных муфт оказываются достаточными для достижения необходимой равномерности вращения вала двигателя. Зубчатое колесо валоповоротного устройства в таких случаях выполняют на фланце ведущей части соединительной муфты. Конструкции крепления маховиков на валу определяются формой маховика.
Конус обеспечивает плотность посадки и центрирование даже при многократных снятиях маховика, разгружает шпонку, однако применение конуса нецелесообразно в тех случаях, когда необходима точная фиксация маховика вдоль вала с центрированием по цилиндрической расточке с натягом (см. рис. 12). В последнем случае конец вала в картере можно уплотнить с помощью неразъемных манжетных сальников. Предотвращение сдвига маховика вдоль оси вала обеспечивается упором и креплением маховика болтами или центральным винтом со стопорением; окружное усилие воспринимается штифтами или призонными болтами.
Маховики отливают из серых (от СЧ 18-СЧ 30 до СЧ 35-СЧ 45) и специальных чугунов; если маховик имеет поверхности, подвергающиеся изнашиванию, то металл должен иметь перлитную структуру.
Конструкция диска и обода определяется устройствами для съема мощности и пуска двигателя. Наиболее часто для съема мощности используют диск маховика.
Определение размеров и расчет маховиков на прочность
Форму и размеры маховика выбирают при компоновке двигателя. Окончательные размеры устанавливают по необходимой величине момента инерции маховика, которую определяют по допустимой степени неравномерности вращения вала двигателя:
δ=(ωmax–ωmin)/ωср,
64
где ωmax и ωmin – соответственно максимальное и минимальное значения угловой скорости вала двигателя в течение рабочего цикла; ωср – среднее значение угловой скорости, ωср=0,5(ωmax+ωmin).
Изменение кинетической энергии А движущихся деталей двигателя и потребителя мощности при изменении угловой скорости от
ωmax до ωmin составит
A=J∙(ωср)2∙δ,
где J – приведенный к коленчатому валу момент инерции движущихся масс двигателя и потребителя.
Для транспортных двигателей момент инерции маховика проверяют на трогание с места и разгон экипажа до определенной скорости wэ при допущении, что трогание с места происходит за счет кинетической энергии маховика, освобождающейся при уменьшении частоты его вращения после включения сцепления от начальной величины n до некоторой конечной nl, при которой работа двигателя достаточно
устойчива:
A0=0,5∙(π/30)2∙(n2–nl2).
Величина n1 зависит от типа двигателя, трансмиссии, состояния дороги и составляет обычно 500-1000 об/мин. Начальное значение n выбирается в пределах (1,5-2,5)∙n1.
Приобретенная экипажем энергия
AЭ=0,5∙MЭwЭ2,
где Мэ – масса экипажа.
Кинетические энергии А0 и Аэ связаны уравнением
A0=AЭ/(ηM ηn),
где ηM – механический КПД двигателя; ηN – механический КПД передачи; ηN=0,75-0,9. Следовательно,
J0 π2(n2–nl2) ηM ηN=900 MЭwЭ2. (1)
Скорость экипажа wэ связана с частотой вращения nl уравнением
wЭ= π Dk nl/(60 i)
где Dk – диаметр колеса (с учетом деформации шин) или начальный диаметр ведущей звездочки гусеничного движителя; i – полное передаточное отношение трансмиссии.
Подставляя значения MЭ, wЭ и nl в формулу (1), получим
J0=MЭ Dk2 nl2/(4 (n2–nl2) ηM ηN i2).
Следует отметить, что данный метод определения величины J0 является условным и не соответствует действительному процессу трогания экипажа с места: при трогании экипаж разгоняется воздействием водителя или регулятора на орган управления двигателем при
65
увеличивающейся или постоянной частоте вращения вала последнего, т.е. за счет энергии топлива, а не за счет кинетической энергии маховика, запас которой в процессе разгона экипажа может даже увеличиваться.
Допускаемые значения окружной скорости маховиков (м/с), не более:
-чугунных 70;
-стальных литых 100;
-стальных штампованных 110.
Допустимые напряжения σ (МПа) для маховиков:
-Чугунных до 108;
-Стальных до 196.
Ориентировочные значения диаметров маховиков автомобильных и тракторных двигателей составляют 300-500 мм.
Внешний диаметр маховика выбирают с учетом размеров установки (расстояние между продольными балками, на которых устанавливают фундаментную раму судового двигателя, расстояние между лонжеронами рамы автомобиля и др.), размеров устройств для съема мощности (диаметр шкива, диаметр поверхности трения сцепления) и пуска двигателя (например, расстояние между осями валов двигателя и электростартера), а также из допустимой величины окружной скорости на максимальном диаметре при номинальной частоте вращения.
В диске маховика наиболее опасные напряжения растяжения в тангенциальном направлении имеют место на поверхности диаметра расточки посадочного отверстия.
Маховики двигателей массового производства подвергают выборочной проверке на разрыв при частоте вращения (1,8-2,8) от номинальной.
10. ПЕРСПЕКТИВЫ РАЗВИТИЯ АВТОМОБИЛЬНОГО ДВИГАТЕЛЕСТРОЕНИЯ
Какими должны быть современные двигатели внутреннего сгорания
Разработчикам современных двигателей приходится, подобно античным мореплавателям, прокладывать курс между Сциллой конкурентных параметров и экологической Харибдой. Нынешний мотор должен быть, с одной стороны, технически совершенным: мощным,
66
надежным, тяговитым, экономичным и при этом относительно недорогим. С другой стороны, ему необходимо соответствовать строгим экологическим требованиям, которые ужесточаются не по дням, а по часам. Только три года назад вступили в силу требования Евро II, а ныне Евро III и уже маячат еще более строгие Евро IV. Они диктуют не вполне логичные, с точки зрения простого автомобилиста, технические решения: новый двигатель иной раз оказывается слабее предшественника, обрастает не очень понятными, но весьма дорогими системами, которые не повышают, а порой и снижают его потребительские характеристики. Что поделаешь: конструкторы снова и снова идут на компромиссы – какие уж тут рекордные параметры, когда во главу угла поставлены (законодательно!) экологические критерии
– остаться хотя бы «при своих».
Итак, вперед, через воздушный фильтр! Впускные трубопроводы переменной длины, которые три года назад встречались как экзотика только на самых свежих моторах, стали привычным, если не банальным решением: их применяют на двигателях «Ауди», «Фольксваген», «БМВ», «Опель» и даже «Дэу».
Двигатель автомобиля «Мерседес-Бенц-S500» (Евро IV) с регулируемым впускным трубопроводом, тремя клапанами на цилиндр, одним распределительным валом в головке, роликовыми толкателями и системой отключения четырех из восьми цилиндров при работе с неполной нагрузкой имеет следующие характеристики: 4966 см3; 220
кВт/299 л.с.; 460 Н/м при 3000 об/мин.
Усложнение конструкции? Несомненно! С другой стороны, оптимизация крутящего момента: никаких «провалов» и «подхватов», двигатель тянет ровно во всем диапазоне оборотов.
Агрегаты наддува получили довольно широкое распространение не только на дизелях, но и на бензиновых моторах. А вот приводные нагнетатели так и остались редкостью («Мерседес-Бенц-CLK» и SLK, «Ягуар-XJR», некоторые модели «Дженерал моторc»). Зато турбокомпрессор выступил в новом качестве: так называемый наддув низкого давления – это не средство повышения мощности, как зачастую рассматривают любой наддув. Иными словами, задача не в том, чтобы сжечь побольше топлива ради дополнительных сил, а чтобы дать меньшему количеству сгореть с максимальной эффективностью
(«Фольксваген-1,8 Т», «Вольво-2,0 Т» (118 кВт/160 л.с.) и 2,5 Т (142
кВт/193 л.с.), «СААБ-2,0 Турбо» (113 кВт/154 л.с.). Хотя своей спортивной специальности турбокомпрессор не забыл, и у этих моделей существуют «заряженные» версии с «правильным» наддувом («Воль-
67
во-Т4» (147 кВт/200 л.с.) и Т5 (176 кВт/240 л.с.), «СААБ-2,0 Турбо» (136 кВт/185 л.с.).
Регулируемый турбокомпрессор двигателя «БМВ» имеет электрическое управление. Рядный шестицилиндровый дизель «БМВ» (Евро III) оборудован четырехклапанной схемой газораспределения, неразделенной камерой сгорания, системой впрыска «коммон рейл», роликовыми толкателями, регулируемым турбокомпрессором и промежуточным охлаждением воздуха.
В системах подачи топлива – небольшая революция. Впервые серийные моторы с непосредственным впрыском бензина в цилиндр появились в Европе на «Мицубиси-Каризма» в 1998 году. В этом году список таких моделей и фирм расширится. Первым из европейцев в нем оказался «Вольво», следующим, по прогнозам, будет «Фольксваген». Считается, что именно двигатели с впрыском топлива в цилиндр (его и называют непосредственным) позволят достичь наилучших экономических и экологических характеристик. Правда, злые языки утверждают, что мотор «Мицубиси-GDI» с трудом уложился в нормативы Евро III по выбросу окислов азота и совсем «не лезет» в перспективные Евро IV, но до введения последних еще немало времени. Зато по экономичности «Мицубиси-Каризма» с таким мотором уже сегодня вплотную приближается к дизельным машинам. В европейском пробеге через 12 стран автомобиль (заметим, среднего класса) показал средний расход бензина 4,83 л / 100 км при средней скорости 90,47 км/ч. Минимальный расход на одном из участков составил 3,69
л / 100 км!
Нажимая на педаль газа, водитель механически открывает дроссельную заслонку. Так было. Теперь появились автомобили («Мерсе- дес-Бенц», «Ауди», «Шевроле»), на которых заслонкой управляет электронная система, а педаль превратилась в банальный потенциометр, с помощью которого водитель высказывает свои пожелания мотору. В недалеком будущем дроссельную заслонку, как досадную помеху во впускном тракте, «отменят» вовсе, заменив регулировкой подъема впускных клапанов или (в отдаленной перспективе) их электрическим или электрогидравлическим приводом.
Устройство для регулировки фаз в механизме газораспределения из экзотики тоже превратилось в обыденность. Моторы «Ауди», «БМВ», «Хонды», «Тойоты» уже немыслимы без него. Увлечение многоклапанностью проходит. Головки с четырьмя и даже пятью клапанами на цилиндр оказались нужны далеко не всем моторам. Если от двигателя не требуется особо высокой литровой мощности, то
68
вполне можно обойтись тремя («Мерседес-Бенц», «Хендэ», «Тойота») или даже двумя клапанами («БМВ», «Фольксваген», «МерседесБенц», «Форд»). Наряду с ними тот же «Фольксваген» успешно применяет пятиклапанные моторы, но повальная «мода на многоклапанность» прошла. Ведь помимо неоспоримых достоинств (высокое качество продувки и наполнения цилиндров), такая конструкция имеет и «обратную сторону» (сложность, проблемы с охлаждением головки, увеличенные потери на трение). Теперь, похоже, количество клапанов выбирают не по принципу «больше, чем у конкурента», а руководствуясь реальной необходимостью для конкретной модели двигателя. Кстати, даже в многоклапанных головках все клапаны часто приводятся одним распределительным валом («Хонда», «МерседесБенц», «Опель») для снижения потерь на трение. Ради этого и новинка из разряда «хорошо забытое старое» – роликовые толкатели клапанов.
А как развивались в последние три года дизельные двигатели? Повсеместное распространение получили неразделенные камеры сгорания (непосредственный впрыск), многоклапанные головки цилиндров и турбонаддув. Причем все эти новшества можно увидеть собранными воедино в одном моторе («Мерседес-Бенц», «Опель», «БМВ», «Пежо»). Легковой дизель с «непосредственным» впрыском потребовал серьезной ревизии приборов питания. Привычные топливный насос и форсунки сдают позиции новомодной системе «коммон рейл», где топливо находится в общем ресивере под постоянным давлением, а доступ к форсункам ему открывают клапаны, управляемые электроникой («Мерседес-Бенц», «ФИАТ», «БМВ», «Пежо», «Ситроен», «Рено»). Таким образом удается реализовать сложные законы подачи топлива, необходимые двигателю с неразделенной камерой сгорания, снизить шум и токсичность, практически исключить дымление. Хотя аккумуляторная система впрыска, по идее, очень схожая с «коммон рейл», известна давно.
Но «коммон рейл» позволяет достичь максимум 135 МПа, тогда как топливные насосы высокого давления (ТНВД) – до175 МПа. Чем выше давление, тем большей тонкости распыла топлива можно добиться – во благо рабочему процессу и, естественно, мощностным, экономическим и экологическим показателям. Поэтому среди дизелистов нашлись «отщепенцы», которые не пошли по «общему пути» (именно так переводится «коммон рейл»). Концерн «Фольксваген» первым начал серийное производство легковых дизелей с насосфорсунками. С ними давление впрыска смогли увеличить до 205 МПа
69