
1583
.pdfбольшого размера со специальной голограммой (с 1998 г. цвет упаковки изменен на бело-красный), а кольца упакованы раздельно в специальных пакетах. Кроме того, в настоящем комплекте маслосъемные кольца – наборные (коробчатые кольца для вазовских моторов фирма не делает). Номер на упаковке поддельных колец также не совпадает с номером в каталоге фирмы. Так что отличить подделку не составит большого труда.
3. ТЕХНОЛОГИЯ ИЗГОТОВЛЕНИЯ И РЕМОНТА РАСПРЕДЕЛИТЕЛЬНОГО ВАЛА
Распределительный вал предназначен для передачи движения клапанам от коленчатого вала. Он выполняется обычно за одно целое с кулачками и некоторыми элементами привода механизма газораспределения.
Механизм газораспределения является одним из наиболее ответственных и нагруженных устройств современного двигателя. При его проектировании требуется решать сложный комплекс противоречивых вопросов. Основные параметры механизма должны быть такими, чтобы организовать эффективное протекание процессов газообмена, которые определяют получение высоких мощностных и экономических показателей двигателя. Кроме того, конструкция механизма газораспределения должна обеспечить исключительную надежность работы клапанов во всем диапазоне скоростных и динамических нагрузок. Все детали механизма должны отвечать предъявляемым требованиям долговечности и не усложнять конструкцию.
Решение перечисленных выше проблем зависит от конструкции механизма газораспределения и, в особенности, профиля кулачка распределительного вала. Трудность проектирования распределительных валов непрерывно возрастает. Повышается напряженность деталей механизма, в связи с увеличением мощности и частоты вращения коленчатого вала двигателя. В двигателях применяются кулачки двух основных типов: спрофилированные выбранным законом образования контура профиля (выгнутый, тангенциальный, вогнутый) и спрофилированные на основе математических зависимостей кинематики клапана. Последний тип получил наибольшее распространение, так как обеспечивает достаточную плавность работы и отсутствие ударов в приводе клапана за счет снижения наполняемости цилиндра. В каж-
20
дой из перечисленных систем имеются как положительные, так и отрицательные стороны.
Распределительный вал газораспределительного механизма служит для передачи вращающего момента. При расположении вала в головке цилиндров привод осуществляется цепной или зубчатоременной передачей в блоке цилиндров посредством шестерен. Распредвал в зависимости от области применения изготовляется из различных материалов. Самый распространенный – сталь.
Распределительные валы изготовляют из цементуемой или углеродистой стали. Кулачки и шейки подвергают цементации или поверхностной закалке. Диаметр вала выбирают в соответствии с радиусом начальной окружности кулачка. Подшипниками нижних валов служат стальные залитые баббитом или алюминиевые втулки, запрессованные в картер или блок. Шейки вала в этом случае делают увеличенного диаметра с таким расчетом, чтобы через отверстия втулок прошли кулачки вала. Для облегчения монтажа диаметр шеек уменьшают от переднего конца вала к заднему.
При верхнем расположении распределительные валы вращаются в отверстиях алюминиевых или реже чугунных кронштейнов. В последние устанавливаются вкладыши с заливкой из антифрикционного сплава.
Примерная технология изготовления детали следующая. В сталеплавильных электрических печах производят жидкий металл с разливкой в слитки (сталь 20Х). Слиток подвергают предварительной термической обработке, которая состоит из высокого отпуска. Происходит снижение внутренних напряжений, снижение твердости для обдирки слитка. Далее производится прокатка и штамповка слитка методом горячей деформации с последующим охлаждением. После этого следует термическая обработка заготовки – нормализация с последующим охлаждением на воздухе.
При нормализации происходит перекристаллизация стали, устраняющая крупнозернистую структуру. Далее следует очистка от окалины. Затем проводится правка детали, после чего следует механическая обработка заготовки, во время которой изготовляют деталь и далее подвергают ее цементации. Процесс цементации ведут при 910930 °С в течение 6-12 часов. Окончательные свойства цементованных изделий достигаются в результате термической обработки, выполняемой после цементации.
21
Вданном случае проводится высокий отпуск при температуре 620 °С с целью предотвращения образования остаточного аустенита при последующей закалке.
Закалка проводится при температуре 820 °С. Это обеспечивает измельчение зерна и полную закалку цементованного слоя и частичную перекристаллизацию и измельчение зерна сердцевины.
Заключительным этапом термической обработки цементованных изделий во всех случаях является низкий отпуск при 160-180 °С, переводящий мартенсит закалки в поверхностном слое в отпущенный мартенсит, снижающий напряжения. Твердость поверхностного слоя после термической обработки HRC 58-62, а сердцевины HRC 30-42.
Контроль качества термической обработки состоит из макроанализа, который применяют для выявления неметаллических включений, и микроанализа, который позволяет определить структуру стали, глубину и твердость цементованного слоя.
Впроцессе термической обработки возможны поводка и коробление детали. Для проверки поводки и коробления осевые детали устанавливают в приспособления между центрами и с помощью индикатора определяют биение. Чаще всего контроль качества после термической обработки производят замером твердости на твердомерах.
Контроль качества термической обработки детали, выявление внутренних и внешних дефектов в металле осуществляются с помощью магнитного, рентгеновского, люминесцентного, ультразвукового
идругих физических неразрушающих методов контроля.
После контроля качества термической обработки проводят окончательную механическую обработку, которая заключается в проведении шлифования. После этого получают готовую деталь. После термической обработки структура поверхностного слоя данного распределительного вала – отпущенный мартенсит и карбиды (возможно сохранение остаточного аустенита, но для его разложения после цементации применяют высокий отпуск при температуре 620 °С).
Сердцевина детали состоит из феррита и мартенсита. Данная термическая обработка обеспечивает высокую твердость цементованного слоя, прочность и достаточную вязкость сердцевины.
Типовой технологический маршрут процесса восстановления распределительного вала при ремонте (для двигателя ЗМЗ-53) будет состоять из следующих операций: 1) подготовительная; 2) мойка и очистка; 3) дефектация; 4) подрезка торцов; 5) наплавка кулачков вала; 6) правка вала по шейкам; 7) обдирочное шлифование наплавленных кулачков; 8) наплавка поверхности под шестерню и эксцентрик; 9) на-
22
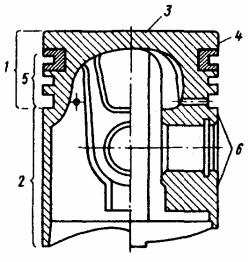
плавка опорных шеек; 10) правка вала; 11) обдирочное шлифование поверхностей под эксцентрик и шестерню, опорных шеек; 12) фрезерование шпоночного паза; 13) закалка опорных шеек, шестерни и кулачков; 14) правка вала; 15) шлифование предварительное опорных шеек; 16) шлифование предварительное кулачков; 17) шлифование окончательное опорных шеек; 18) правка вала; 19) шлифование окончательное кулачков; 20) приемочный контроль; 21) мойка; 22) консервация.
4.ТЕХНОЛОГИЯ ИЗГОТОВЛЕНИЯ ПОРШНЯ
Вконструкции поршня принято выделять следующие элементы (рис. 1): головку 1 и юбку 2. Головка включает днище 3, огневой (жаровой) 4 и уплотняющий 5 пояса. Юбка поршня состоит из бобышек 6
инаправляющей части.
На рис. 2 |
представлены наиболее |
|
|
|
|
|
|
|
|
|
|
|
|
|
|
|
|
|
|
3 |
|
|
|
|
|||
типичные в настоящее время конструк- |
|
|
|
|
|
|
|
||||||
|
|
|
|
|
|
|
|
|
|
|
|||
|
|
|
|
|
|
|
|
4 |
|
||||
ции поршней автотракторных двигате- |
|
|
|
|
|||||||||
|
|
|
|
|
|
|
|
|
|
|
|||
лей различного типа. |
|
1 |
|
|
|
|
|
|
|
|
|
||
|
|
5 |
|
|
|
|
|
|
|||||
Сложная |
конфигурация |
поршня, |
|
|
|
|
|
|
|
|
|
||
|
|
|
|
|
|
|
|
|
|
|
|||
быстро меняющиеся по величине и на- |
|
|
|
|
|
|
|
|
|
|
|
||
правлению тепловые потоки, воздейст- |
|
|
|
|
|
|
|
|
|
|
|
||
|
|
|
|
|
|
|
|
|
6 |
|
|||
вующие на его элементы, приводят к |
|
|
|||||||||||
|
|
|
|
|
|
|
|
|
|
|
|||
неравномерному распределению тем- |
|
2 |
|
|
|
|
|
|
|
||||
ператур по его объему и, как следствие, |
|
|
|
|
|
|
|
|
|
|
|
||
к значительным переменным по време- |
|
|
|
|
|
|
|
|
|
|
|
||
ни локальным термическим напряже- |
|
|
|
Рис. 1. Основные элементы |
|
||||||||
ниям и деформациям (рис. 3). |
|
|
|
|
|
||||||||
Теплота, |
подводимая к |
поршню |
|
|
|
|
|
поршня |
|
через его головку, контактирующую с рабочем телом в цилиндре двигателя, отводится в систему охлажде-
ния через отдельные его элементы в следующем соотношении, %: в охлаждаемую стенку цилиндра через компрессионные кольца – 60...70, через юбку поршня – 20...30, в систему смазки через внутреннюю поверхность днища поршня – 5...10. Поршень также воспринимает часть теплоты, выделяющейся в результате трения цилиндра и поршневой группы.
23
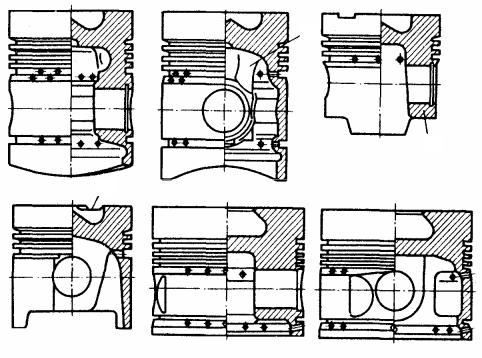
При проектировании поршня используются статистические данные по конструктивным параметрам его элементов, отнесенным к диаметру цилиндра.
1
2
3
Рис. 2. Конструкция поршней дизелей: 1 – ребра, соединяющие днище и бобышки поршня; 2 – бобышки со скошенным внутренним торцом; 3 – вырез под клапан
Конструктивные параметры основных элементов поршня
Высота поршня Н определяется высотой головки h. При малой Н существенно возрастает влияние на характер движения поршня несоблюдение при производстве и эксплуатации зазоров, допускаемых между его элементами и зеркалом цилиндра, что может интенсифицировать процессы образования перекладин, вызвать нарушение газо- и маслоуплотнения, повышенные износы стенок канавок компрессионных колец.
Высота головки поршня определяет его габариты и массу, в связи с чем ее выбирают минимально необходимой для обеспечения нормального температурного режима ее элементов. Особое внимание при этом обращается на температуру в зоне канавки верхнего компрессионного кольца и в бобышках поршня.
Материалы и технология изготовления поршней
Для изготовления поршней автотракторных ДВС в настоящее время в основном используют алюминиевые сплавы, реже серый или ковкий чугун, а также композиционные материалы.
24

25
в)
а) |
б) |
|
Рис. 3. Температурное поле (а) и минимальные главные напряжения поршня дизеля (б), полученные с помощью конечно-элементной модели (в)
25
Алюминиевые сплавы имеют малую плотность, что позволяет снизить массу поршня и, следовательно, уменьшить инерционные нагрузки на элементы цилиндропоршневой группы и КШМ. При этом упрощается также проблема уменьшения термического сопротивления элементов поршня, что в сочетании с хорошей теплопроводностью, свойственной данным материалам, позволяет уменьшить теплонапряженность деталей поршневой группы. К положительным качествам алюминиевых сплавов следует отнести малые значения коэффициента трения в паре с чугунными или стальными гильзами.
Однако поршням из алюминиевых сплавов присущ ряд серьезных недостатков, основными из которых являются невысокая усталостная прочность, уменьшающаяся при повышении температуры, высокий коэффициент линейного расширения, меньшая, чем у чугунных поршней, износостойкость, сравнительно большая стоимость.
В настоящее время при изготовлении поршней используют два вида силуминов: эвтектические с содержанием Si 11...14 % и заэвтектические с содержанием Si 17...25 %.
Увеличение содержания Si в сплаве приводит к уменьшению коэффициента линейного расширения, повышению термо- и износостойкости, но при этом ухудшаются его литейные качества и растет стоимость производства.
Для улучшения физико-механических свойств силуминов в них вводят различные легирующие добавки. Добавка в алюминиевокремниевый сплав до 6 % меди приводит к повышению усталостной прочности, улучшает теплопроводность, обеспечивает хорошие литейные качества и, следовательно, меньшую стоимость изготовления. Однако при этом несколько снижается износостойкость поршня. Использование в качестве легирующих добавок натрия, азота, фосфора увеличивает износостойкость сплава. Легирование никелем, хромом, магнием повышает жаропрочность и твердость конструкции.
Заготовки поршней из алюминиевых сплавов получают путем отливки в кокиль или горячей штамповкой. После механической обработки они подвергаются термической обработке для повышения твердости, прочности и износостойкости, а также для предупреждения коробления при эксплуатации. Кованые поршни пока используются реже, чем литые.
Чугун в качестве материала для поршней по сравнению с алюминиевым сплавом обладает следующими положительными свойствами: более высокими твердостью и износостойкостью, жаропрочностью, одинаковым коэффициентом линейного расширения с материалом
26
гильзы. Последнее позволяет существенно уменьшить и стабилизировать по режимам работы зазоры в сочленении юбка поршня – цилиндр. Однако большая плотность не позволяет использовать его широко для поршней высокооборотных автомобильных двигателей. Данный недостаток может быть частично нивелирован включением в структуру чугуна шаровидного графита, что позволяет отливать элементы поршня существенно меньшей толщины. Как следует из сказанного выше, ни силумины, ни чугун в полной мере не являются оптимальными материалами для изготовления поршней.
В связи с этим в настоящее время ведется активная работа по использованию для поршней керамических материалов, которые наилучшим образом отвечают требованиям, предъявляемым к материалам поршневой группы. Это малая плотность при высокой прочности, термо-, химико- и износостойкости, низкой теплопроводности и необходимом значении коэффициента линейного расширения.
Один из практических способов использования керамики состоит в изготовлении деталей поршня из металлоили полимерокомпозиционных материалов. Матрицей (основой) первого типа материалов является алюминий или магний, а в качестве наполнителя используют керамические и металлические порошки или волокла пористых материалов. Основу полимерокомпозиционных материалов составляют полимерные материалы с наполнителем из волокон углерода, стекла, порошков металлов или керамики. Они обладают малой плотностью, высокими антифрикционными свойствами и применяются для элементов с небольшими тепловыми нагрузками, например для изготовления юбки поршня.
Перспективным является армирование элементов поршня керамическими волокнами из оксида алюминия и диоксида кремния.
При содержании в основном материале до 40...50 % оксида алюминия получается аморфное керамическое волокно с диаметром 2...3 мкм, успешно работающее при температурах 1200...1300 °С. Если содержание оксида алюминия превышает 70 %, получается структура волокна, приближающаяся к кристаллической, что способствует высокой термической стабильности изделия.
Основными проблемами, сдерживающими широкое использование керамики для изготовления поршней автотракторных двигателей, являются хрупкость, низкая прочность на изгиб, склонность к трещинообразованию и усталости, а также высокая стоимость.
Материал поршня должен быть возможно малой плотности, иметь низкий коэффициент линейного расширения, обладать износо-
27
стойкостью, высокой теплопроводностью, в том числе при повышенных температурах, иметь хорошую обрабатываемость. При этом важными являются комплексные характеристики материала, а не только отдельные его свойства. В зависимости от назначения двигателя и типа конструкции поршня могут быть применены различные материалы. Поршни двигателей многих типов, прежде всего автомобильных и тракторных, изготовляют из легких сплавов литьем в кокиль или штамповкой. В первом случае применяются эвтектические силумины типа 4Л25 (11-13 % Si) и заэвтектические, содержащие присадки меди, никеля, магния и марганца. Поршни штампуют из сплавов АК4 и АК4-1, отличающихся высокими прочностными свойствами при повышенных темперах.
Несмотря на то, что масса поршней из алюминиевого сплава меньше массы поршней из чугуна, последний также применяется для изготовления поршней быстроходных двигателей. Из легированного серого и высокопрочного чугунов типов СЧ 24-СЧ 45 и ВЧ 45-5 изготовляют поршни форсированных тепловозных и среднеоборотных двигателей. При повышенной по сравнению с алюминиевыми сплавами температуре плавления чугуна устраняется обгорание кромок на поверхностях, обращенных к камере сгорания.
В составных поршнях для изготовления головки применяют жаростойкие стали типа 20Х3МВФ. На изготовление из стали переходят, если максимальная температура в наиболее нагретых зонах поршня превышает ориентировочно 450 °С. В ряде случаев (накладки поршней двухтактных двигателей) применяют высоколегированные жаропрочные стали.
5.КОМПОЗИЦИОННЫЕ МАТЕРИАЛЫ
ВДЕТАЛЯХ ДВИГАТЕЛЕЙ
Применение композиционных материалов в деталях двигателях позволяет достичь снижения расхода топлива, повышения мощности, снижения уровня шума, повышения экологической безопасности и увеличения долговечности.
В настоящее время находят применение следующие технологии:
1. Жидкая штамповка со сквозной пропиткой волокнистой керамической вставки.
Это технология для производства точных заготовок поршней двигателей внутреннего сгорания с керамической волокнистой встав-
28
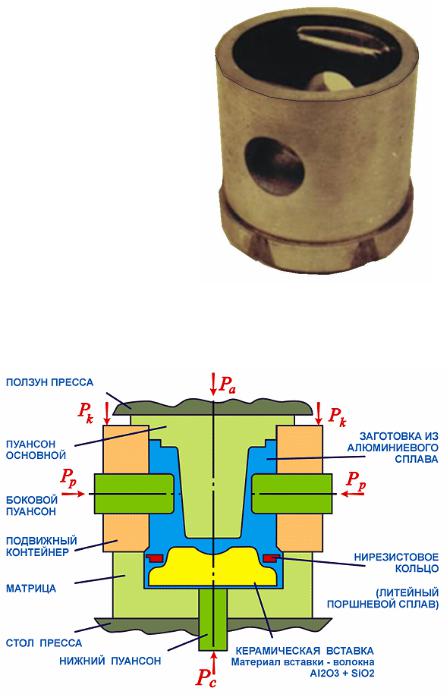
кой и нирезистовым кольцом. Разработана специальная технология производства вставок из керамических волокон необходимой структуры, плотности и геометрии.
Материал поршня (матричный сплав) – литейный алюминиевый сплав.
Метод производства – жидкая штамповка со сквозной пропиткой волокнистой керамической вставки.
Материал керамической вставки – алюминийкремнеземистые волокна диаметром 2...4 мкм, модулем упругости 150 ГПа, переделом прочности 1700 МПа, плотностью (объемное содержание волокон) 10...20 % и содержанием неволокнистой составляющей не более
5 %.
Метод жидкой штамповки в сочетании с упрочнением головки поршня керамическими волокнами по сравне-
Рис. 4. Композитные поршни для двигателей внутреннего сгорания
нию |
с |
традици- |
|
|
онной |
техноло- |
|
||
гией |
кокильного |
|
||
литья |
|
позволяет: |
|
|
снизить |
расход |
|
||
металла |
на |
|
||
30...40 %; полу- |
|
|||
чить |
плотную и |
|
||
мелкозернистую |
|
|||
структуру |
без |
|
||
дефектов и газо- |
|
|||
вой |
пористости; |
|
||
повысить |
меха- |
|
||
нические и физи- |
|
|||
ческие |
свойства |
Рис. 5. Схема жидкой штамповки поршня на специальном |
||
материала |
порш- |
прессе |
||
ня на |
15...20 %; |
|
добиться высокой термической стабильности упрочняющего эффекта; существенно повысить термоустойчивость и снизить износ рабочих поверхностей поршня без появления термических трещин на кромках;
29