
1583
.pdfШлифовать коренные шейки сравнительно жестких одноколенчатых и двухколенчатых валов можно и на обычных круглошлифовальных станках. Однако, как правило, шейки валов шлифуют на специализированных станках. При шлифовании коренных шеек вал устанавливают в центрах с применением люнетов.
При достаточно больших масштабах выпуска коренные шейки шлифуют на многокамневых станках, имеющих автоматический цикл врезного шлифования с выхаживанием, правкой круга и прибором активного контроля. Многокамневое шлифование предъявляет большие требования к однородности шлифовальных кругов в комплекте. Круги имеют диаметр 1000-1100 мм и ширину 25-85 мм.
Шатунные шейки шлифуют обычно одним кругом поочередно. В качестве технологической базы выбирают поверхность коренных шеек, а для угловой ориентации – отверстия во фланце или, реже, базовой площадке на шейках колен.
Шлифуют на станках с двусторонним приводом, причем при установке в приспособлении ось коренных шеек смещена от оси вращения шпинделя на величину радиуса кривошипа.
В последнее время для шлифования коренных и шатунных шеек коленчатых валов созданы автоматические линии.
Так, автоматическая линия фирмы «Нортон» (США), предназначенная для окончательного шлифования шатунных шеек коленчатого вала шестицилиндрового двигателя, состоит из шести последовательно работающих станков, на каждом из которых в автоматическом цикле обрабатывают определенную шейку. На всех позициях линии все шейки обрабатывают одновременно. В линии установлен один резервный полуавтомат. Станки линии соединены транспортером с гибкой связью и снабжены загрузочными устройствами. Станки имеют пневматические устройства активного контроля, по команде которого при достижении требуемого размера шейки от нее отводятся шлифовальные круги. Автоматический цикл работы каждого станка линии состоит из следующих элементов: установка вала и его закрепление в патроне, ускоренная и рабочая подача шлифовального круга, автоматический контроль размеров, отвод шлифовальных кругов, съем детали и правка кругов.
Если при обработке размеры шлифуемых шеек будут отклоняться на величину больше допустимой, то станок автоматически останавливается, в то время как остальные станки линии могут продолжать работу. Независимая работа станков позволяет производить смену круга и ремонт станка без остановки работы всей линии. В этих случаях в
40
работу вводится резервный станок. Производительность линии – 60 валов в час.
Автоматическая линия из четырех автоматов для шлифования шатунных шеек создана и на отечественном заводе ХСЗ.
Окончательную отделку шеек коленчатого вала производят суперфинишированием, а также наружным хонингованием с полированием шеек тонкой абразивной лентой. Шейки валов, обрабатываемые суперфинишированием, требуют очень тщательной доводки для получения предельной геометрической формы на окончательной операции шлифования. Это может быть наружное хонингование, при котором происходит более интенсивный съем металла, чем при суперфинишировании, что позволяет несколько исправить погрешность формы и предъявляет менее строгие требования к окончательному шлифованию шеек.
Полирование абразивной лентой производят на специальных станках в одну или две операции. Предварительное полирование обычно выполняют лентой с абразивным порошком зернистостью 180-240, а окончательное – зернистостью 240-300.
Снимаемый припуск лежит в пределах 0,006-0,015 мм. Полирование ведется при скорости вращения вала v = 10-20 м/мин. Шероховатость поверхности соответствует 9-10-му классам чистоты.
6.4. Балансировка коленчатых валов
Коленчатые валы подвергают балансировке. При большом выпуске коленчатых валов эту операцию производят на автоматических балансировочных станках или автоматических линиях. Одна из таких линий для балансировки коленчатого вала восьмицилиндрового V- образного автомобильного двигателя (ЗИЛ-130) создана ЭНИМСом. Она состоит из двух балансировочных автоматов моделей МА-24 и МА-25 и контрольного автомата модели МА-36. Так как один балансировочный станок недостаточно уменьшает неуравновешенность (в 15-20 раз), то для еще большего снижения неуравновешенности на линии применяют двукратное автоматическое определение неуравновешенности коленчатого вала с последующим ее устранением и контролем. Предварительное устранение неуравновешенности производят радиальным сверлением на определенную глубину отверстия диаметром 20 мм в крайних противовесах вала. Окончательную же балансировку производят сверлением отверстий диаметром 12 мм в
41
средних противовесах. Начальная неуравновешенность коленчатого вала в результате его обкатки на этой линии снижается в 30-50 раз и становится не более 30 г/см. Производительность линии – 54 вала в час. Коленчатые валы подвергают многократному контролю, как в процессе обкатки, так и после нее.
Обычно проверяют диаметральные размеры шеек, отверстия под подшипник во фланце, длину коренных и шатунных шеек и расстояние от базового торца, радиуса кривошипа, а также биение шеек и торца фланца относительно крайних коренных шеек, взаимное расположение коренных и шатунных шеек по длине и расстояние от базового торца, угловое расположение всех кривошипов, положение установочного отверстия и шпоночной канавки относительно коренных и шатунных шеек.
Для измерения применяют как общепринятые средства (скобы с микроиндикаторами, индикаторные приспособления), так и специальные приспособления для комплексного окончательного контроля.
Такие приспособления применяют для комплексного контроля линейных размеров, радиуса кривошипа, положения установочного отверстия и шпонки.
Непараллельность (смешение) оси шатунной шейки относительно коренных шеек проверяют также специальным прибором.
6.5. Обкатка крупных коленчатых валов
Заготовками для крупных стальных валов обычно являются поковки с удлиненными концами от 200 до 300 мм для зажима в патроне и поддержания в люнете. Поковка отличается значительной величиной припуска. При этом в коленах шатунные шейки при получении заготовки не формируются сплошными, поэтому коэффициент использования металла у таких поковок низкий.
ВНИИТяжмашем разработан процесс изготовления заготовок с помощью высадки и гибки на прессах, что позволяет получать заготовки валов со значительно меньшими припусками и без вырезки металла под шатунные шейки, как в поковках.
При этом способе под высадку и гибку предварительно обтачивают заготовку с длиной больше, чем у готовой поковки, с проточенными шейками 1-14. Затем производят высадку фланцев (№ 13 и 14) на гидропрессе с подогревом до температуры 9000 °С и затем последующую гибку, начиная с колена № 1 и последовательно № 2, 3, 4, 5,
42
6. Металл подогревают до температуры 900-9500 °С периодически после каждой операции гибки очередного колена.
Характерными особенностями изготовления крупных коленчатых валов из поковок являются многократная разметка под обработку на различных операциях и вырезка металла под шатунные шейки.
Шатунные шейки обкатывают на специальных токарных станках при неподвижном вале. Вал устанавливают на станке по размеченному центру шейки так, чтобы обрабатываемая шейка находилась в центре суппортной рамы. Суппортная рама станка вместе с установленными на ней резцами вращается вокруг шейки, производя ее обкатку.
7. ИЗГОТОВЛЕНИЕ КЛАПАНОВ
Головка клапана является его наиболее нагруженной частью. В головке возникают высокие неравномерные механические напряжения изгиба от действия газов, ударных нагрузок при посадке клапана и термические напряжения.
Наибольшая концентрация напряжений возникает на поверхности посадочного конуса и в зоне от головки к стержню клапана. Механические и термические напряжения изменяются циклически, поэтому разрушение головок клапанов носит усталостный характер. Кроме того, головки выпускных клапанов подвергаются воздействию высокотемпературной газовой коррозии. При наличии в бензинах антидетонаторов (тетраэтил свинца) коррозия посадочного конуса клапана и седла в головке цилиндров или блоке становится более интенсивной.
Температура в центре головки выпускных клапанов карбюраторных двигателей достигает 800-820 °С, а впускных – 500 °С.
Надежная работа клапанов обеспечивается конструктивными и технологическими решениями, из которых основными являются:
1)выбор материалов для клапана, седла и направляющей втулки;
2)подбор конструктивных параметров и форм, чтобы осуществлялись наименьший приток теплоты от отработавших газов и интенсивный теплоотвод;
3)повышение жаропрочности и износостойкости;
4)применение механизмов поворота клапанов, действующих автоматически;
5)эффективное охлаждение.
43
При форсировании двигателей температура клапанов повышается, поэтому клапаны защищают от коррозии. Наибольший защитный эффект удается получить при металлокерамическом покрытии головки клапана, которое наносят путем напыления и последующей термической обработки. При этом на поверхности клапана образуется пористый слой с оксидной пленкой. Клапаны с металлокерамическим защитным покрытием имеют значительно большую жаропрочность, чем клапаны, у которых посадочный конус покрыт стеллитом или алитирован.
Для повышения теплоотвода от головки к стержню выпускные клапаны делают полыми; внутренние полости заполняют примерно на 40 % металлическим натрием, имеющим температуры плавления 98 °С и кипения 183 °С. Температура кипения металлического натрия ниже температуры головки клапана, поэтому давление в полости не повышается. Отвод тепла от головки клапана происходит при взбалтывании силами инерции расплавленного натрия, имеющего высокую теплопроводность. Максимальная температура головки при этом понижается на 100 °С, а температура стержня клапана несколько повышается, поэтому при проектировании должен быть предусмотрен интенсивный теплоотвод от направляющей втулки.
В настоящее время разработаны методы ковки клапанов с полыми стержнями без обработки резанием полостей. Это снизило стоимость изготовления клапанов и позволило делать стержни с малым наружным диаметрам (до 10-12 мм) при внутреннем диаметре полости в стержне около 8 мм. Обкатка стержня клапана роликом значительно повышает его износостойкость (в 1,5-1,8 раза).
Теплота от клапана отводится через его седло и стержень. Температура выпускного клапана может быть понижена с помощью следующих конструктивных мероприятий (кроме натриевого охлаждения):
1)укорочения направляющей втулки так, чтобы она не выступала
впатрубок и не омывалась отработавшими газами;
2)возрастания диаметра стержня клапана (в направляющей втулке), для увеличения поверхности теплоотвода;
3)литья направляющей втулки как единого целого с головкой цилиндров, что понижает максимальную температуру примерно на 125 °С и среднюю на 70 °С.
Для лучшего теплоотвода диаметр стержня выпускного клапана должен быть на 10-15 % больше, чем впускного клапана. У впускных
44
клапанов направляющую втулку делают короче для увеличения проходного сечения в патрубке.
Плотная посадка клапана на седло может быть обеспечена только при наличии зазора в клапанном механизме.
Для установления зазора в механизме привода предусматривается регулировочное устройство, обычно в виде шпильки с закаленной опорой, ввертываемой в одно из плеч коромысла.
Материалы, применяемые для изготовления клапанов
Впускные клапаны в зависимости от напряженности рабочего процесса и частоты следования рабочих циклов изготовляют из среднеуглеродистых, легированных хромом и никелем сталей 40Х, 45Х, 45ХН, 50ХН, а также хромокремнистых и хромокремнемолибденовых сталей 40Х9С2, 40Х10С2М, 30Х13Н7С2. Для выпускных клапанов форсированных двигателей, кроме указанных и им подобным, применяют специальные клапанные аустенитные стали 12Х18Н9Т, 45Х14Н14В2М, 45Х22Н4МЗ и им подобные, не теряющие своих свойств при высоких температурах и знакопеременных нагрузках.
Клапаны в зависимости от марки стали подвергают различным методам термической и термохимической обработки (закалке с отпуском, цементации, азотированию, хромированию) для придания поверхностям, работающим на изнашивание и удар, необходимой твердости (фаски должны иметь НRС 32-45, стержень НRС 43-65).
Также клапаны изготовляют из хромокремнистых 38ХС, хромоникелевых 40ХН и 50ХН и хромоникельмолибденовых 40ХНМА сталей. Для выпускных клапанов применяют жаропрочные стали 30Х13Н7С2, 40Х10С2М. Выпускные клапаны, изготовленные из хромоникелевых сталей с аустенитной структурой, содержащих до 20 % хрома и до 15 % никеля, выдерживают температуры около 850 °С.
Долговечность клапанов может быть повышена путем:
1)наварки стеллита (сплава, содержащего 60 % Ni и 15 % Cr) на посадочный конус или индуктивной закалки этой поверхности;
2)наварки высоколегированного сплава на опорную плоскость стержня;
3)хромирования стержней клапана (толщина слоя 10-25 мкм); при этом снижается износ и уменьшаются отложения нагара на стержнях;
4)хромирования посадочного конуса (в дизелях);
5)применения внутреннего натриевого охлаждения;
6)использования автоматических устройств, обеспечивающих проворачивание клапана при каждом подъеме за счет проскальзыва-
45
ния тарелки клапана, опирающейся на коническую поверхность и промежуточные шарики.
Толкатели изготовляют цельными, составными, сварными или с запрессованными опорами для штанги. В качестве материала применяют сталь или чугун. В комбинированных конструкциях на опорную часть стального толкателя наплавляют отбеленный чугун. Цилиндрические и опорные торцовые поверхности стальных толкателей цементируют. Глубина цементованного слоя составляет 0,7-1,5 мм. В чугунных толкателях с наплавленными рабочими поверхностями глубина отбеленного слоя колеблется в пределах 1,5-2,5 мм. Глубина слоя, закаленного с помощью ТВЧ, составляет 2,5 мм. Твердость рабочих торцов толкателя не должна быть ниже НRС 54-56, а боковых цилиндрических поверхностей – не менее НRС 45.
Распределительные валы штампуют из стали или отливают из чугуна. Стоимость изготовления литых валов ниже. Для валов используют закаливаемые стали 45, 40Г и 50Г или цементуемые стали 20 и 20Г.
Рабочие поверхности шеек вала и поверхностей кулачков подвергают термической обработке ТВЧ с глубиной закалки 2-5 мм или цементации на глубину 1,5-2,2 мм. Твердость поверхности должна быть не менее НRС 54-62. Пружины клапанов изготовляют из сталей 65, 65Г, 50ХФА.
8.ГИЛЬЗЫ ЦИЛИНДРОВ
8.1.Конструкции гильз цилиндров
Стенки цилиндра двигателя образуют совместно с поршнем, кольцами и поверхностью камеры сгорания пространство переменного объема, в котором совершаются все рабочие процессы двигателя внутреннего сгорания. Стенка цилиндра должна быть тщательно обработана и образует с поршневыми кольцами пару скольжения.
Цилиндры и гильзы цилиндров нагружаются силами давления газов, боковой нагрузкой от поршня и температурной нагрузкой. Переменная по величине и направлению боковая нагрузка вызывает изгиб и вибрацию цилиндра и ослабляет его крепление к картеру. Стенки цилиндра под действием возникающих при движении поршня сил трения подвергаются, кроме того, износу.
46
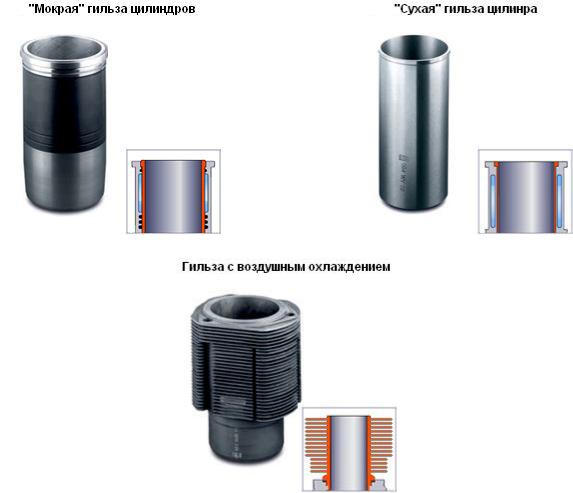
Гильзы цилиндров должны быть прочными, жесткими, износостойкими, обеспечивать возможно меньшие потери на трение поршня о поверхность цилиндра. Внешняя и внутренняя поверхности гильз должны обладать антикоррозионной устойчивостью. Конструкция гильз должна также обеспечивать надежность уплотнений в местах стыков гильз с головкой и блоком цилиндров.
|
|
|
|
|
|
|
|
б) |
|
а) |
|
|||
|
|
|
||
|
|
|
|
|
|
|
|
|
|
в)
Рис. 9. Конструкции гильз цилиндров: а) – «мокрая» гильза; б) – «сухая» гильза; в) – гильза с воздушным охлаждением
Гильзы цилиндров могут являться как самостоятельной конструкционной единицей двигателя («мокрые» гильзы и гильзы двигателей воздушного охлаждения), так и элементом ремонтной технологии, предусмотренной заводом-изготовителем (например, «сухие» гильзы для двигателей, где цилиндры выполнены заодно с блоккартером).
В автомобильных и тракторных двигателях наибольшее распространение получили чугунные гильзы.
47
По конструкции гильзы цилиндров современных автомобильных и тракторных двигателей можно разделить на три основные группы
(рис. 9).
«Мокрые» гильзы
Конструкцией двигателя с водяным охлаждением предусмотрена полость в картере двигателя, так называемая «рубашка охлаждения». Гильза, соприкасающаяся свой поверхностью с охлаждающей жидкостью, находящейся в «рубашке охлаждения», называется «мокрой». «Мокрые» гильзы цилиндров обеспечивают лучший отвод тепла, но картер двигателя с такими гильзами обладает меньшей жесткостью. Большое распространение эти гильзы получили на грузовых и тракторных двигателях в силу своей высокой ремонтопригодности. Как правило, выпускаемые производителями «мокрые» гильзы не требуют перед установкой какой-либо доработки. Изношенные «мокрые» гильзы в большинстве случаев не ремонтируют, а заменяют новыми без снятия двигателя с шасси. Для предотвращения прорыва газов в охлаждающую жидкость и просачивания этой жидкости в цилиндр и картер двигателя, «мокрые» гильзы комплектуются уплотнительными прокладками. Внутренняя поверхность гильз тщательно обрабатывается (хонингуется) для того, чтобы обеспечить наличие требуемой масляной пленки для смазки поршневых колец. Двигатели с «мокрыми» гильзами устанавливаются почти на все современные коммерческие автомобили.
«Сухие» гильзы
Гильзы, не имеющие соприкосновения с охлаждающей жидкостью, называются «сухими» гильзами. Конструкцией некоторых двигателей предусмотрена при изготовлении установка в блок картера гильз, изготовленных из износостойкого материала, что создает оптимальные условия для работы цилиндро-поршневой группы. Например, некоторые модели двигателей машин марок «Хонда», «ЛэндРовер», «Фольксваген», «Ауди», «Вольво» и многих других производителей, имеют алюминиевый блок цилиндров (для уменьшения веса силового агрегата) и установленные в него «сухие» гильзы (для увеличения ресурса и повышения ремонтопригодности).
Но самое широкое распространение «сухие» гильзы получили в сфере капитального ремонта двигателя. «Незагильзованный» блок цилиндров современного двигателя имеет несколько предусмотренных технологией расточек с последующей установкой в него ремонтных поршней. Установка «сухих» гильз позволяет не менять блок двигателя даже после износа цилиндра, расточенного в последний
48
ремонтный размер. Производители гильз выпускают заготовки гильз, то есть гильзы, имеющие запас по длине и внешнему диаметру, которые после токарной обработки запрессовываются с натягом в блок цилиндров. Такие гильзы, как правило, не имеют обработанной внутренней поверхности. Они растачиваются и хонингуются только после установки гильзы в блок цилиндров. Поверхность блока цилиндров под установку тоже повергается тщательной обработке: расточке и в некоторых случаях хонингованию. Гильза с упором устанавливается в блок под давлением, с натягом (в среднем 0,03-0,04 мм). Для гильз, не имеющих упора, натяг больше. Наружная поверхность «сухих» ремонтных гильз, как правило, подвергается шлифовке, для увеличения плотности прилегания к блоку цилиндров.
Гильзы могут фиксироваться при установке верхним буртом, нижним буртом или вообще могут устанавливаться без упора. Некоторые японские производители, например «Исузу», изготавливают двигатели с тонкостенными стальными гильзами, имеющими покрытие из пористого хрома. Такие гильзы не подвергаются механической обработке и устанавливаются в блок цилиндров без натяга, с небольшим усилием, и удерживаются в блоке за счет прижатия широкого бурта гильзы головкой блока. Блок картера с сухими гильзами имеет повышенную жесткость по сравнению с блоком, в который установлены «мокрые» гильзы.
Гильзы цилиндров для двигателей с воздушным охлаждением
В двигателях воздушного охлаждения конструкция оребрения и необходимость создания охлаждающих воздушных потоков не позволяют применять блок-картерный тип отливки. В этих двигателях применяют отдельно отлитые цилиндры с воздушными ребрами, расположенными чаще всего перпендикулярно оси цилиндра. Эти гильзы цилиндра крепятся к верхней части картера короткими шпильками через опорный фланец (несущие цилиндры) или при помощи анкерных (несущих) шпилек. Гильзы цилиндров двигателей воздушного охлаждения изготавливают как из одного (монометаллические), так и из двух (биметаллические) металлов. Монометаллические цилиндры делают из чугуна, реже из стали или легких сплавов. Из биметаллических цилиндров получили распространение чугунные и стальные цилиндры с залитыми (или навитыми) алюминиевыми ребрами. Широкое распространение двигатели с воздушным охлаждением получили среди производителей тяжелой строительной техники. Ярким приме-
49