
Лекция 1. Общая характеристика производства химической аппаратуры
.pdfТЕХНОЛОГИИ МАШИНОСТРОИТЕЛЬНОЙ ОТРАСЛИ
ВВЕДЕНИЕ
Химическая аппаратура характеризуется большим разнообразием ее типов, различающихся как по конструктивным признакам, так и по видам применяемых материалов, что приводит к необходимости применения многочисленных и значительно различающихся по характеру методов обработки деталей и сборки аппаратов. Все это создает определенные трудности при выборе технологических методов, применяемых при изготовлении аппаратуры.
Задача дисциплины ТМО - снабдить инженера-механика сведениями, необходимыми ему при проектировании и изготовлении аппаратуры. Основными вопросами такого характера являются заготовительные и отделочные операции – разметка, резка и гибка листов на листогибочных машинах, обработка отверстий, изготовление отдельных деталей и сборочных единиц. И поскольку аппараты состоят из отдельных типовых сборочных единиц, для описания сборочных процессов выбраны аппараты, наиболее распространенные в промышленности.
В пособии рассматриваются также вопросы сборки и сварки корпусов, контроля качества сварных соединений, технического освидетельствования и испытаний сосудов на герметичность, установки арматуры и контрольно-измерительных приборов, а также транспортировки негабаритных аппаратов.
3
Лекция 1 ОБЩАЯ ХАРАКТЕРИСТИКА ПРОИЗВОДСТВА
ХИМИЧЕСКОЙ АППАРАТУРЫ 1.1 Основная номенклатура аппаратов
Номенклатура химического аппаратостроения определяется в основном потребностями химической, нефтяной, нефтехимической, микробиологической и газовой отраслями народного хозяйства.
Классификация, химической аппаратуры по назначению крайне условна, так как в различных установках аппараты одной конструкции могут предназначаться для различных технологических целей. Поэтому в основу классификации положены важнейшие физико-химические процессы, происходящие в аппарате. С этой точки зрения приняты следующие, номенклатурные группы аппаратуры:
1 - теплообменные аппараты, в которых тепловой поток про-ходит через стенку, разделяющую среды: пластинчатые; ко- жухо-трубчатые теплообменники, теплообменники типа «труба в трубе», конденсаторы и испарители, аппараты воздушного охлаждения, погружные и оросительные холодильники, конденсаторы, подогреватели и т.д.;
2 - массообменные аппараты, в которых передача тепла и массы производится при непосредственном контакте сред. Нередко, одновременно с тепло-массопередачей, в таких аппаратах происходят и химические реакции. К этой группе аппаратуры относятся колонны ректификационные, экстракционные, абсорберы, адсорберы и десорберы, колонны синтеза, выпарные башни и т.д.;
3 - аппараты-реакторы, в которых происходят основные химические превращения продуктов. Большей частью реакция в этих аппаратах происходит в присутствии катализатора при высоких температуре и давлении. В состав этой группы входят реакторы, регенераторы, реакционные камеры и т.д.;
4 - нагревательные аппараты огневого действия: газовые
4
топки, огневые подогреватели, трубчатые печи, элементы котловутилизаторов и т.д;
5 - аппараты, предназначенные для разделения сред и очистки продуктов от примесей: пылеуловители, циклоны, гидроциклоны, сепараторы, фильтры, центрифуги, отстойники и т.д.; 6 - мешалки - аппараты, предназначенные для смешения
сред;
7 - сосуды для хранения продуктов: шаровые и цилиндрические емкости для хранения сжиженных газов, мерники, сборники и промежуточные емкости технологических установок.
Примеры: Реактор-мешалка-рубашка охлаждения; Вращающаяся печь обжига извести
Проведенная стандартизация и нормализация химической аппаратуры привела к расширенному применению ее в технологических производствах, не связанных с химической и нефтехимической отраслями промышленности, а именно - в металлургических и энергетических установках, в технологических процессах стройиндустрии, пищевой промышленности, производстве фосфорных и азотных удобрений.
Нередки случаи агрегатирования аппаратов, когда в состав агрегата входят различные по назначению аппараты, например в конструкции колонной аппаратуры включены кожухотрубчатые теплообменники или секции аппаратов воздушного охлаждения.
Пример: Колонна отгонки нитробензола Абсорбер с брызголовушкой
1.2 Классификация аппаратов по конструктивно-
технологическим признакам
Химическая аппаратура классифицируется по следующим признакам:
А - эксплуатационные параметры; Б - толщина стенки корпуса аппарата;
В - виды материалов, применяемых для изготовления; Г - конструктивные характеристики;
5
Д - габаритность.
А - Эксплуатационные параметры. К эксплуатационным параметрам относятся производительность, температура, рабочее давление и состав рабочей среды. Указанные параметры определяют основные характеристики элементов аппарата - диаметр; толщину стенки, материал. В зависимости от величин указанных параметров аппараты делятся на четыре группы.
Для установления методов изготовления и сборки аппаратов, объемов контроля сварных соединений необходимо определить группу сосуда в зависимости от расчетного давления, температуры стенки и характера среды по табл. 1.1.
Таблица 1.1 – Классификация аппаратов по режимным параметрам
Группа |
Расчетное давле- |
Температура |
Рабочая среда |
|
сосудов |
ние, МПа (кгс/см2) |
стенки, °С |
|
|
|
|
|
|
|
1 |
свыше 0,07 (0,7) |
независимо |
Взрывоопасная или пожаро- |
|
|
|
|
|
опасная, или 1-го, 2-го |
|
|
|
|
классов опасности |
|
|
|
|
по ГОСТ 12.1.007 |
2 |
до 2,5 (25) |
ниже |
-70, |
|
|
|
выше 400 |
|
|
|
свыше 2,5 (25) |
ниже |
-70, |
|
|
до 4 (40) |
выше 200 |
|
|
|
|
|
|
|
|
свыше 4 (40) |
ниже |
-40. |
|
|
до 5 (50) |
выше 200 |
|
|
|
|
|
Любая, за исключением |
|
|
свыше 5 (50) |
независимо |
||
|
|
|
|
указанной для 1-й группы |
|
до 1,6 (16) |
от -70 до -20 |
||
|
сосудов |
|||
|
|
от 200 до 400 |
||
|
|
|
||
3 |
свыше 1.6 (16) |
|
|
|
|
до 2.5 (25) |
от -70 до 400 |
|
|
|
|
|
|
|
|
свыше 2,5 (25) |
|
|
|
|
до 4 (40) |
от -70 до 200 |
|
|
|
свыше 4 (40) |
|
|
|
|
до 5 (50) |
от -40 до 200 |
|
|
4 |
до 1,6 (16) |
от -20 до 200 |
|
|
|
|
|
|
|
6
Б - толщина стенки корпуса аппарата. По толщине стенки сосуды аппаратов делятся на тонкостенные и толстостенные. Такое деление предопределяет выбор технологии изготовления и применяемого оборудования. Сосуды с толщиной стенки до 36 мм включительно относятся к тонкостенным, выше 36 мм к толстостенным. Величина 36 мм определена несколькими конструктивными и технологическими признаками:
1 - все основное универсальное заготовительное оборудование (ножницы, листоправильные и листогибочные машины) рассчитаны преимущественно на толщину листа до 36 мм включительно. Для толщин выше 36 мм применяются специальные машины;
1 - толстостенные сосуды или их элементы, изготовленные из углеродистых сталей, должны подвергаться термической обработке;
3 - сварка корпусов сосудов из элементов толщиной свыше
36 мм производится преимущественно автоматическим электрошлаковым методом.
В- виды материалов, применяемых для изготовления.
Взависимости от эксплуатационных и конструкторских требований корпуса аппаратов изготовляются из однослойного или двухслойного листового проката. Однослойные корпуса изготовляют из углеродистых, легированных и высоколегированных сталей. Выбор металла определяет особенность выполнения заготовительных операций, способ и вид подготовки кромок под сварку, технологию сборки и сварки, вид испытаний и транспортировку аппаратов.
Г - конструктивные характеристики. Конструктивные характеристики аппаратуры и ее элементов, повторяемость их в производстве предопределяют технологическую специализацию производств химического машиностроения и совершенствование уровня технологии. Технологическая классификация этой аппаратуры по общим технологическим операциям и построение технологических потоков в соответствии с указанной классификацией
7
позволяют создать оптимальную технологию производства аппаратуры. Так, в отечественном химическом машиностроении, созданы специализированные производства пластинчатых и кожухотрубчатых теплообменников, которые организованы по признаку диаметра теплообменников; производства колонной аппаратуры, специализированные по видам тарелок, и много других производств аппаратуры, в основу которых заложены идентичные технологические процессы изготовления.
Пример: Специализация по диаметрам корпусов, крышкам
Д - габаритность. В зависимости от габаритов аппаратов технология их сборки может существенно различаться. Габаритные аппараты отправляются на монтажные площадки в полностью собранном виде. Аппараты негабаритные поставляются на монтажные площадки в блочном исполнении максимальной заводской готовности и там их изготовление заканчивается.
При поставке аппарат должен быть укомплектован. В комплект сосуда должны входить:
-сосуд в собранном виде или отдельно транспортируемые части с ответными фланцами, рабочими прокладками и крепежными деталями, не требующими замены при монтаже; приспособления и запасные части;
-техническая документация;
-фундаментные болты для крепления сосуда в проектном положении;
Детали и сборочные единицы, которые при отправке в сборе с сосудом могут быть повреждены, допускается снять и отправить в отдельной упаковке.
Торкретирование, футеровка штучными материалами, теплоизоляция осуществляются на монтажной площадке. Материалы для торкретирования, футеровки, теплоизоляции, а также неметаллические (керамические и др.) элементы для защиты внутренней футеровки в поставку сосуда могут не входить.
Транспортируемые части негабаритных сосудов следует поставлять с приваренными приспособлениями для сборки мон-
8
тажного соединения под сварку
Впоставку негабаритных сосудов, свариваемых на монтажной площадке из транспортируемых частей, входят сварочные материалы и пластины металла для проведения контрольных испытаний сварных швов. Сварочные материалы и пластины должны отвечать установленным требованиям.
Сосуды в собранном виде или части негабаритных сосудов следует поставлять с приваренными деталями для крепления изоляции, футеровки, обслуживающих площадок, металоконструкций. Приварные детали для крепления изоляции следует применять стандартных типов.
Впоставку тяжеловесного или негабаритного сосуда входят специальные траверсы, опорные устройства (цапфы), тележки или салазки для опоры нижней части сосуда, монтажные хомуты, съемные грузозахватные устройства, специальные строповые устройства и устройства для перевода сосуда из горизонтального положения в вертикальное.
Изготовленные из труб детали (змеевики, секции, коллекторы, трубные пучки и др.), если они составляют части негабаритных сосудов или изготавливаются отдельно от сосудов, следует поставлять собранными на специальных подкладках.
Вкомплект сосудов с механизмами и внутренними устройствами (реакторы, кристаллизаторы, емкости с погружными насосами и др.) входят электродвигатели, редукторы, насосы.
1.3 Общие технологические требования к конструированию и изготовлению аппаратов
Аппараты, работающие под давлением, изготовляются в соответствии с действующими требованиями правил безопасности Госгортехнадзора РФ (ПБ 03-576-03) и отраслевого стандарта ОСТ-26-291-91 «Сосуды и аппараты сварные стальные. Технические требования».
При проектировании сосудов и аппаратов следует обеспечивать технологичность конструкции, надежность работы в тече-
9
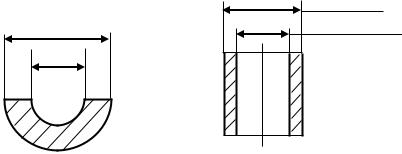
ние установленного срока службы, безопасность при изготовлении, монтаже, ремонте, диагностировании и эксплуатации, возможность осмотра внутренней поверхности, очистки, промывки, продувки и ремонта, контроля технического состояния сосуда при диагностировании, а также контроля давления и отбора среды перед вскрытием сосуда.
Сосуды, которые не могут транспортироваться в собранном виде, могут проектироваться из частей, соответствующих по габариту требованиям к перевозке транспортными средствами. Деление сосуда на транспортируемые части следует указывать в технической документации.
Расчет на прочность выполняет и несет ответственность разработчик сосуда. При необходимости расчет согласовывается со специализированной экспертной организацией.
Для изготовления сосудов и аппаратов в зависимости от их конструкции и размеров применимы все виды промышленной сварки, кроме газовой, которая допускается только для труб условным диаметром до 80 мм с толщиной стенки не более 4 мм.
За базовые размеры диаметров аппаратов принимают диаметры отбортованных днищ по ГОСТ 6533-88. Для аппаратов, выполняемых с иными днищами, за базовые размеры принимают
(рис.1.1):
-наружный диаметр аппаратов, изготовляемых из труб;
-внутренний диаметр всех остальных аппаратов.
|
Днб - труба |
Дн |
Двб - обечайка |
Дв |
|
Рисунок 1.1 – Базовые размеры диаметров аппаратов
10
Аппараты снабжаются люками или смотровыми лючками. Сосуды должны быть снабжены необходимым количе-
ством люков и смотровых лючков, обеспечивающих осмотр, очистку и ремонт сосудов, а также монтаж и демонтаж разборных внутренних устройств.
Сосуды с внутренним диаметром более 800 мм должны иметь люки, а с внутренним диаметром 800 мм и менее - лючки.
Внутренний диаметр круглых люков должен быть не менее 400 мм. Размеры овальных люков по наименьшей и наибольшей осям в свету должны быть не менее 325x400 мм.
Внутренний диаметр круглых или размер по наименьшей оси овальных лючков должен быть не менее 80 мм. Люки, лючки необходимо располагать в местах, доступных для обслуживания.
Сосуды, состоящие из цилиндрического корпуса и решеток с закрепленными в них трубками (теплообменники); и сосуды, предназначенные для транспортировки и хранения криогенных жидкостей, веществ не вызывающие коррозии и накипи, допускается изготовлять без люков и лючков независимо от диаметра сосудов.
Крышки люков должны быть съемными. На сосудах, изолированных на основе вакуума, допускаются приварные крышки.
Крышки массой более 20 кг должны быть снабжены подъ- емно-поворотными или другими устройствами для их открывания и закрывания. Конструкция шарнирно-откидных или вставных болтов, хомутов, а также зажимных приспособлений люков, крышек и их фланцев должна предотвращать их самопроизвольный сдвиг.
При наличии на сосудах штуцеров, фланцевых разъемов, съемных днищ или крышек, внутренний диаметр которых не менее указанных выше для люков, обеспечивающих возможность проведения внутреннего осмотра, допускается люки не предусматривать.
Внутренние устройства в аппаратах (змеевики, тарелки, перегородки, переливные устройства и др.), препятствующие
11
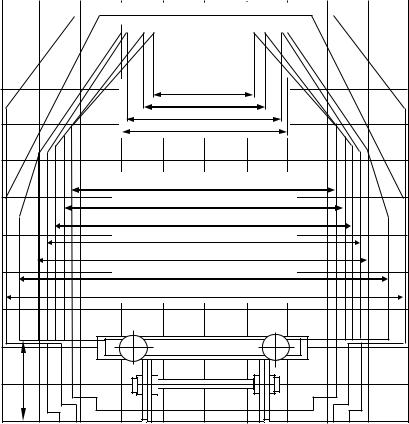
осмотру корпуса и его ремонту, выполняются съемными. Габаритные размеры оборудования в сборе должны вписы-
ваться в габарит подвижного состава железнодорожного транспорта (рис. 1.2).
2500 |
2000 |
1500 |
1000 |
500 |
0 (мм) |
500 |
|
1000 |
1500 |
2000 |
2500 |
|||||||
|
|
|
|
|
|
Габарит приближения строений |
|
|
|
|
|
|
5500 |
|||||
|
|
|
|
|
|
|
|
|
|
|
||||||||
|
|
|
|
|
|
|
|
|
|
|
|
|
|
|
|
|
||
|
|
|
|
|
|
|
|
|
|
|
|
|
|
|
|
|
5000 |
|
|
|
|
|
|
|
|
|
|
|
|
|
|
|
|
|
|
||
|
|
|
|
|
|
|
|
|
|
|
|
|
|
|
|
|
|
|
|
1240 (габарит) |
4500 |
|
1400 (0 и I степень) |
|
|
1760 (II степень) |
|
|
2000 (III и IV степень) |
4000 |
|
|
3500 |
1625 |
(габарит) |
|
|
1700 (0 степень) |
3000 |
1800 |
(I степень) |
|
|
1900 (II степень) |
2500 |
2000 |
(III степень) |
|
|
2225 (IV степень) |
2000 |
|
|
|
2450 |
|
|
|
|
1500 |
1230 |
|
1000 |
|
|
|
|
|
500 |
Рисунок 1.2 – Зоны габаритности |
|
Когда оборудование не может быть спроектировано габаритным, оно должно состоять из минимального числа транспортабельных поставочных блоков с возможно меньшими степенями
12