
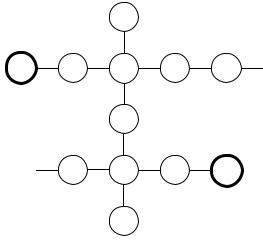
высокая химическая стойкость (благодаря чему эти стекла получили широкое применение в технологии получения чистых веществ, из них изготавливают различные реакторы, ампулы, тигли);
высокая прозрачность для излучения инфракрасной и ультрафиолетовой областей светового диапазона, до длины волны порядка 4 мкм, поэтому являются ценным оптическим материалом (линзы, призмы и т. д.);
по электрическим свойствам относятся к хорошим высокочастотным диэлектрикам, у них ε = 3,8; tgδ = 2·10- 4 (на частоте 106 Гц); ρv более 1016 Ом.
Для повышения технологических характеристик в состав стекол вводят оксиды щелочных металлов, при этом существенно снижаются электрические свойства, что связано с изменением структуры материала: происходит разрыхление пространственной сетки (обрыв связей) и образование тупиковых ветвей (рис. 4.31).
Рис. 4.31. Схема структуры щелочных стекол
Разрыхление кислородного каркаса вызывает понижение температуры размягчения стекла, с другой стороны слабосвязанные щелочные ионы под действием теплового движения могут срываться с мест закрепления и перемещаться из одной ячейки сетки в другую, при этом усиливается ионно-релаксационная поляризация (рост tgδ и ε) и одновременно уменьшается ρv материала.
103
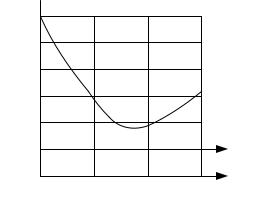
Изменение электрических свойств стекла зависит от радиуса щелочного иона (чем меньше радиус иона, тем больше его подвижность). Ион натрия имеет меньший размер, чем ион калия, следовательно, отрицательное влияние оксида натрия (Na2O) сильнее. При одновременном присутствии оксида натрия и оксида калия (K2O) электрические свойства стекла могут быть значительно лучше, чем при присутствии одного из оксидов — полищелочной эффект (нейтрализующий эффект) (рис. 4.32).
tgδ
Рис. 4.32. Зависимость tgδ силикатного стекла от содержания в нем оксидов натрия и калия
Стекла, содержащие в больших количествах оксиды тяжелых металлов (титан, свинец и т. д.) характеризуются малыми потерями даже при значительной добавке щелочных окислов. Атомы многовалентного металла, встраиваясь в структурную сетку стекла, не образуют тупиковых ветвей, поэтому увеличение их концентрации не приводит к возрастанию релаксационных потерь. Более того, становясь на месте существующих обрывов ветвей, такие ионы могут соединить оборванные концы и укрепить пространственную сетку.
Технология получения силикатных стекол
Технология получения силикатных стекол относительно проста. Сырьем для производства является: кварцевый песок (SiO2), сода (Na2CO3), (К2СО3), известняк (СаCO3), доломит (СаCO3 · MgCO3), по-
левой шпат (Al2O3 · 6SiO2 · K2O).
104
Сырьевые материалы измельчают, отвешивают в нужных соотношениях и перемешивают. Полученную шихту загружают в печь и варят при температуре 1200 – 1400 ° С. Шихта (технологическая смесь) плавится, летучие составляющие (пары воды, углекислый газ, сернистый газ (SO3) и т. д.) удаляются, оставшиеся окислы химически реагируют между собой, образуя однородную стекломассу, из которых и формируется изделие. Формовку осуществляют: выдуванием, центробежным литьем, вытяжкой, прессованием, отливкой и т. д.
Изделия подвергают отжигу для снятия местных механических напряжений.
Области применения стекол
Электровакуумные стекла используются для изготовления баллонов, ножек и других деталей электровакуумных приборов. Значения температурного коэффициента линейного расширения (αl ) стекла и соединяемых с ним материалов должны быть близки.
Боросиликатные или алюмосиликатные стекла с добавлением щелочных оксидов используются в качестве стеклоприпоев. Название стекла (платиновое, молибденовое, вольфрамовое) определяется не составом стекла, а тем, что значения αl этих стекол близки к αl платины, молибдена, вольфрама.
Изоляторные стекла легко металлизируются и используются в качестве герметизирующих вводов в металлические корпуса различных приборов (конденсаторов, трансформаторов и т. д.) обычно для этой цели используется щелочное силикатное стекло.
Из цветных стекол изготавливают светофильтры, эмали, глазури. Обычные силикатные стекла прозрачны в видимой части светового спектра. Использование добавок предает стеклам соответствующую окраску: СаО — синюю, Cr2O3 — зеленую, MnO2 — фиолетовую или коричневую и т. д.
Лазерные стекла — рабочие тела в твердотельных, в которых генерирующими центрами являются активные добавки, равномерно распределенные в диэлектрической прозрачной матрице. Наиболее
105
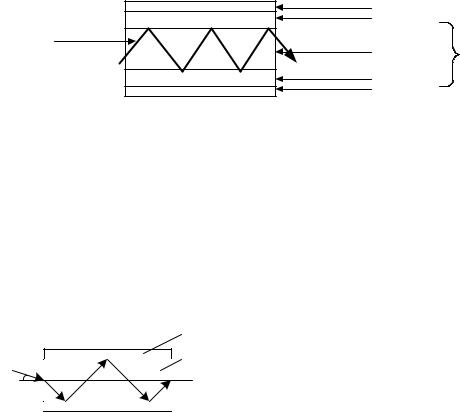
часто используемые активные добавки — активированные ионы неодима Nd3+.
Стекловолокно получается вытяжкой через фильеру (тоненькое отверстие). Получают тонкие волокна 4 – 7 мкм, которые в дальнейшем обрабатывают методами текстильной технологии (стеклоткань, стеклоленты и т. д.). Для изготовления стекловолокон используют следующие виды стекол: щелочные алюмосиликатные, безщелочные и малощелочные алюмоборосиликатные стекла.
Световоды используются для передачи изображения, при этом используют волокна, диаметр которых менее 15 мкм.
В сердцевине и в оболочке световодов применяются стекла с разными показателями преломления, причем у сердцевины показатель преломления должен быть больше, чем у оболочки. Полимерное покрытие используется для защиты стекла от влаги и улучшения гибкости волокна (рис. 4.33).
оптический |
полимерное покрытие |
|
оболочка |
|
|
сигнал |
|
|
|
|
|
|
сердцевина |
стекло |
|
оболочка |
|
|
полимерное покрытие |
Рис. 4.33. Принципиальная схема волоконного световода
Принцип действия световода заключается в следующем. Световой луч, падая из среды с показателем преломления n1, на поверхность с показателем преломления n2 под углом большим предельного, при этом произойдет полное внутреннее отражение сигнала
(рис. 4.34).
γ |
γ − апертурный угол |
|
Рис. 4.34. Принцип действия световода |
106
4.6.4. Ситаллы
Ситаллы представляют собой стеклокристаллические материалы, получаемые путем почти полной стимулированной кристаллизации стекол специально подобранного состава. Эти материалы непрозрачны в видимом свете, от стекол они отличаются кристаллическим строением, а от керамики — значительно меньшими размерами кристаллических зерен.
Всостав стекломассы вводят добавки, дающие зародыши кристаллизации (частицы металлов и их соединения). Важно стимулировать процесс кристаллизации равномерно по всему объему и получить материал с однородной структурой. После получения изделия обычного стекла его подвергают двухступенчатой термической обработке:
первая ступень: при температуре 500 – 700 ° С происходит образование зародышей кристаллизации;
вторая ступень: при температуре 900 – 1100 ° С происходит развитие кристаллической фазы.
Вситаллах содержание кристаллической фазы составляет 95 %, размеры кристаллов порядка 0,05 – 1 мкм.
К достоинствам ситаллов относятся: повышенная механическая прочность.
возможность получения, как малого, так и большого температурного коэффициента линейного расширения (ситаллы с малым αl
очень нагревостойки); большие возможности получения материалов с заранее задан-
ными свойствами, т. е. можно варьировать как рецептуру стекломассы, так и режимы кристаллизации;
Ситаллы разделяются на установочные и конденсаторные. Материалы, подобные ситаллам, за рубежом называется пироке-
рамом, девитрокерамом, стеклофарфором и т. д.
107
4.6.5. Керамика
Под керамикой понимают большую группу диэлектриков с разнообразными свойствами, объединенных общностью технологического цикла.
К достоинствам керамики относятся:
высокие электрические характеристики при достаточно высокой механической прочности.
стабильность и надежность характеристик; возможность получения материалов с заранее заданными свой-
ствами (варьирование состава массы и технологии); отсутствие ограничений на форму и габариты изделия.
Кристаллическую фазу образуют различные химические соединения или твердые растворы этих соединений, она определяет электрические свойства керамики.
Стекловидная фаза керамики — прослойки стекла, связывающие кристаллическую фазу. Ее состав и количество определяют технологические свойства керамики, ее плотность, степень пористости и гигроскопичность.
Наличие газовой фазы (газы в закрытых порах) обусловлено способом обработки массы и ведет к снижению электрической и механической прочности, а также к росту диэлектрических потерь (при повышенных напряжениях происходит ионизация).
Технология изготовления керамики
Сырьем для производства керамики являются природные минералы (кварц, глинозем, тальк, а также оксиды и карбонаты различных металлов).
Выбор метода изготовления керамики зависит от свойств материала, особенностей конфигурации изделия и массовости заказа на производство.
Любая технологическая схема включает следующие операции: тонкое измельчение и тщательное смешивание исходных ком-
понентов;
108
пластификация массы и образование формовочного полуфабри-
ката;
формование заготовок путем прессования пластической протяжкой или выдавливанием через мундштук, горячим литьем под давлением, отливкой в формы и т. д.;
спекание изделий или высокотемпературный обжиг — наиболее ответственная операция. При температуре более 1300 ° С происходит выжигание пластификатора и завершающиеся химические реакции между компонентами. Эта операция может производиться в окислительной, нейтральной или восстановительной среде.
Классификация и свойства керамических материалов
По техническому назначению керамические изделия подразделяются на следующих два вида:
установочная керамика, которая используется в различного рода изоляторах (опорные, проходные, подвесные); конструкционных деталях, подложках интегральных схем, ламповых панелях, корпусах резисторов, каркасах катушек индуктивности, основаниях электропечей и т. д.;
конденсаторная керамика, из которой изготавливают до 60 % от всех производимых типов электрических конденсаторов.
По электрическим свойствам керамические изделия подразделяются на следующих два вида:
низкочастотная керамика; высокочастотная керамика.
Рассмотрим основные типы установочной керамики. Изоляторный фарфор по электрическим свойствам представ-
ляет собой низкочастотный материал. Сырьем для производства этого фарфора являются: каолин (Al2O3 · 2SiO2 · H2O), кварцевый песок (SiO2) и полевой шпат.
При обжиге, взаимодействуя, каолин и кварцевый песок образуют муллит (3Al2O3 · 2SiO2), являющийся кристаллической фазой керамики. Промежутки между кристаллическими зернами заполняются
109
полевым шпатом, который является стекловидной фазой. Следовательно, материал имеет низкую пористость, высокую плотность, водонепроницаемость, высокие механическую и электрическую прочность. Однако из-за большого содержания щелочных оксидов в стеклофазе материал характеризуется высокими диэлектрическими потерями (tgδ = 10- 2). Именно поэтому изоляционный фарфор относится к низкочастотной керамике.
Радиофарфор занимает промежуточное положение между низкочастотной и высокочастотной керамикой. При его производстве в состав шихты вводят окись бария, при этом резко снижаются tgδ и удельная электропроводность этого материала. Если в составе шихты фарфора содержится до 40 % глинозема, то у нее высокая пластичность, следовательно, из нее можно изготовить как мелкие, так и крупногабаритные изделия.
Квысокочастотным керамическим материалам относятся ультрафарфор, алюминоксид (корундовая керамика) и брокерит. К высокочастотной установочной керамике относятся цельзиановая, стеатитовая и форстеритовая керамика.
Ультрафарфор характеризуется низким значением tgδ, высокой механической прочностью и удовлетворительными технологическими параметрами.
Алюминоксид или корундовая керамика содержит 95 – 99 % глинозема. Глинозем бывает двух модификаций: γ-Al2O3 (низкотемпературная модификация) и α-Al2O3 (высокотемпературная модификация) — корунд, у которого высокие электротехнические характеристики. Для увеличения доли корунда в глиноземе производят его предварительную термообработку с введением специальных добавок, например, если к 80 % глинозема добавить бариевое стекло, то это способствует увеличению электрофизических характеристик материала и ускоряется спекание.
Кдостоинствам алюминоксида можно отнести: низкий tgδ при повышенных температурах и частотах электрического поля; высокую нагревостойкость (до 1600 ° С); высокую механическую прочность и
110
теплопроводность (коэффициент теплопроводности в 10 – 20 раз выше, чем у изоляционного фарфора).
Недостатки алюмоноксида: непластичен; высокая температура спекания; высокая абразивность, приводящая к сложностям при обработки изделия.
Брокерит — материал, содержащий 95 – 99 % оксида бериллия (ВеО) характеризуется высокими свойствами. В частности, его теплопроводность в 200 – 250 раз превышает теплопроводность стекол и ситаллов. Брокерит применяется в особо мощных СВЧ приборах, для изготовления подложек для микросхем, металлизированные изделия из него позволяют получать согласованные спаи с медью.
Для высокочастотных конденсаторов используется конденсаторная керамика с относительной диэлектрической проницаемостью до 230, величиной tgδ менее 6·10- 4 на частоте 1 МГц и электрической прочностью Епр = 8 – 12 кВ/мм. Конденсаторная керамика изготавливается на основе рутила (TiO3), перовскита (титанат кальция СаTiO3), титаната стронция (SrTiO3).
Эта керамика подвержена электрохимическому старению, а также у нее высокие отрицательные значения температурного коэффициента диэлектрической проницаемости, αε = (-1500 ¸ -3000) ×10−6 К- 1, т. е. такую керамику используют для конденсаторов, в которых не предъявляется требования по температурной стабильности.
Повышение термостабильности керамических конденсаторов добиваются путем введения в керамику компонентов с положительными αε , например, титаноциркониевая керамика (TiO2 – ZrO 2) и
(СаTiO3 – СаZrO3), лантановая керамика (LaAlO3), станнатная кера-
мика (CaSnO3).
Для низкочастотных конденсаторов используют керамику на основе титаната бария (ВаTiO3) и твердых растворов с сегнетоэлектрическими свойствами (ε = 900 – 8000), у которых относительная диэлектрическая проницаемость зависит от температуры, частоты и напряженности электрического поля, при относительно высокой величине tgδ в пределах 2·10-3 – 2,5·10 -2.
111
4.7. КОМПОЗИЦИОННЫЕ ДИЭЛЕКТРИЧЕСКИЕ МАТЕРИАЛЫ
Композиционные материалы (КМ) — материалы, состоящие из двух и более компонентов и обладающие специфическими свойствами, отличными от суммарных свойств их составляющих.
Особенности композиционных материалов: состоят из двух и более компонентов;
особое значение имеют свойства материала на границе раздела компонентов;
свойства композита не повторяют свойства его отдельных компонентов.
Возможны различные подходы к классификации КМ:
по природе компонентов (полимерные, керамические и т. д.); по расположению компонентов (изотропные и анизотропные); по структуре композиции (матричные, слоистые, каркасные, во-
локнистые); по геометрии армирующих элементов (порошки, гранулы, во-
локна, пленки, ткани и т. д.); по количеству компонентов: полиматричные (один наполнитель
и несколько матриц) и полиармированные (одна матрица и несколько наполнителей).
Армирующие компоненты
Выбор наполнителя диктуется требованиями, предъявляемыми к композиционному материалу и технологии его получения.
Армирующие компоненты увеличивают прочность, жесткость, износостойкость, ударную вязкость, теплопроводность и теплостойкости КМ. Одновременно они уменьшают температурный коэффициент линейного расширения, пористость и возможность модификации поверхности материала.
К недостаткам армирующих компонентов относятся ограничения на технологию получения КМ и снижение времени жизни некоторых связующих.
112