
Ceramic Technology and Processing, King
.pdf
Firing 243
Figure 8.7: Tube Furnace, Commercial. Tube furnaces are available in a variety of sizes and temperature capability. (Courtesy of CM Furnaces).
Notice that the tube is free and floating, and though not visible, it is supported on a muffle tube made from a coarser-grained refractory. The shell is split around the tube because this region is hot during a run and has to expand. Otherwise, it would distort and compromise the muffle tube support.
Ceramic Quality
The problems are with sag, thermal shock, strength, and chemical reactions with the ware.
Sag. As the operating temperature increases, the tube will have an increased tendency to sag. There are three ways to cope with this problem. Physically support the tube, especially in the hot zone. Select a ceramic more resistant to sag or from another supplier. Finally, increase the purity
244 Ceramic Technology and Processing
of the ceramic tube. Soft glass phases on the grain boundaries result in lower temperature capability. When the glass softens, the ceramic will deform under stress. Central support of the tube reduces the bending stress and helps to stabilize the structure. The manufacturer will have drawings. Ask about the ceramic purity. Most alumina ceramics have some glassy grain boundary phase. These glasses are softer (lower softening temperature) when they contain alkalies than they are when containing alkaline earths. High purity ceramics (99%+) are best, but are more susceptible to thermal shock. SiC refractories have a low tendency to sag. Metals are predictable; there is much more data available on properties with temperature. The Metals Handbook, by ASM, is a good source of data. Nickel alloys are used for air atmosphere tube furnaces.
Thermal Shock. Fine-grained, dense ceramics are susceptible to thermal shock, which can usually be prevented by slow heating and cooling. Thermal expansion and conductivity are important properties. Low expansion and high thermal conductivity result in better thermal shock resistance.
Modulus of elasticity can be varied by control of the porosity, and in the case of zirconia, by the amount and kind of stabilizer. Ceramic suppliers are a good source of information. Coarse-grained ceramics have a lower modulus and are less apt to fracture by thermal shock. Ask the furnace manufacturer about their ceramic suppliers.
Chemical Reactions. Exposure to certain chemicals can degrade the ceramic tube. In particular, fluxes will lower the softening point. A few such fluxes are Na, K, Li, B, and halogens. One can expect a shorter tube life when these are present. As the temperature is increased, just about everything reacts with just about everything else. One needs to make judicious choices to avoid reactions between the ware, setter, and the tube. The following strategy can be helpful. On a fragment of tube material, place a small fragment of the setter, and on that place a small fragment of the ware. When fired, one can observe these reactions without fluxing down the whole furnace. One can test many combinations in the same run, saving a lot of time. Heating elements are also susceptible to impurities.
Firing 245
SiC and MoSi2 are protected from oxidation by a silica film. One can destroy this film with CO, CO2, halogens, and hydrogen. An oxide layer on the surface protects metal elements; fluxes can dissolve this oxide layer. The supplier has more information on things that can happen.
Microstructure. Strength of a ceramic part is largely controlled by flaws in the structure. These are introduced during production of the powder and during processing. Some suppliers do a better job of controlling these flaws than others, so the problem becomes one of finding the right supplier. Ask for statistical process control data. If they do not have this data, go elsewhere. One can also request the relationship between strength and grain size. Unbridled grain growth weakens the structure. Heating for long periods at a high temperature can result in grain growth, weakening the tube.
Cements. It is common to fasten the wire heating element to the tube with a refractory cement. Constituents in the cement can attack the element and cause it to fail. Generally, calcium aluminate based cements cause the least trouble with alumina tubes.
Design
There are many things to consider with the kiln design, including things that place stresses on the furnace parts.
Mechanical Restraints. As the furnace heats and cools, the tube must be free to change its size and shape. For example, the tube becomes longer as it is being heated. If it is restrained, it will be in compression. However, this is not the problem. As the furnace cools, it is in tension and it will crack. Ceramics are strong in compression but weak in tension, especially at high temperatures.
246 Ceramic Technology and Processing
Bending stresses. Unless the tube is supported in the hot zone, the sample in the hot zone will place bending stresses on the tube. Ordinarily, this is not a problem as the weight of the sample and its setter is small and the temperature is well below the softening point.
End Seals. All tubes are produced with irregular ends due to break out when diamond sawing. For an air atmosphere, there usually is not the need for an end seal, but if there is, then the tube ends have to be ground flat.
Winding stresses. Often, the heating element is a wire that expands and contracts when heated and cooled. Bear in mind that the wire is constrained by the tube and the cement. To impart slack, wind the coil slightly loose.
Poison Fingers. It has been known for a long time that oils and perspiration from human skin will cause metals to corrode, especially at elevated temperatures. The oils and perspiration from some people are more corrosive than others. Use gloves when handling metal heating elements. If one touches the metal with their bare hands accidentally, clean it with a detergent and rinse.
Leads. Figure 8.6 suggests that the electrical connections are connected to lead throughways that have a substantial reduction in resistivity. It is common practice to double up the wire element from the tube to the lead throughways. All of this helps to confine the heat in the hot zone and to retard the connections from oxidizing. Lead throughways are often refractory metals but can be stainless steel. They are connected by a thread and nut.
Operating Problems
Tube furnaces fired in air are not especially difficult to operate, but they do have some problems.
Firing 247
Thermal Gradients. Since the tube loses heat from both ends, there are bound to be thermal gradients. The uniform hot zone is very short, making it difficult to fire a sample evenly. Often to remedy this problem, the winding is more closely spaced at the ends of the hot zone in an attempt to flatten out the gradient. When the heating element is not a wire, this approach is not available for small furnaces, so keep the sample short or the tube long.
A carriage or boat inserts and holds the sample in the furnace. Typically, these have a short but manageable life. Most problems involve chemical reactions with the sample. An intermediate setter compatible with both is one answer. When there is a liquid phase, use the boat once.
Powder or refractory grain around the sample will adsorb the liquid and prevent a burn through that could destroy the heating element. After sintering, the powder or grain has to be removed. If it sinters hard, this will be very difficult. Coarse-grain packs do not sinter hard so one can easily crumble it off. Some powders, such as BN, do not sinter well and can be removed.
Element Degradation. Metal heating elements will eventually break. Recrystallization of the wire over time will make it brittle. Also, the wire can evaporate, thinning the cross section and making it weaker. Platinum will do this, depositing platinum crystals on the cooler ends of the tube. The main problem is that the element reacts with the tube, cement, or the atmosphere. Metal oxidation is a complex process and is dependent upon the oxygen partial pressure and temperature. For an air furnace element, the atmosphere should be oxidizing.
Check List, Tube Furnaces, Air
•Ceramic quality
•Chemical compatibility
•Stresses
•Refractory cements
•Winding life
•Thermal gradients
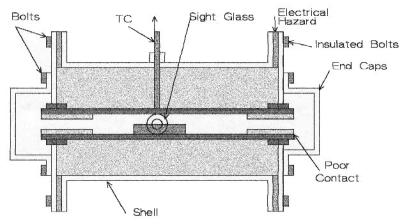
248 Ceramic Technology and Processing
Tube Furnaces, Reducing
A good feature of tube furnaces is that one can control the atmosphere by purging. End seals provide a closed volume with an extended length through which one can pass gas. Tube materials include alumina, fused silica, graphite, and refractory metals such as Mo and Ni/Cr alloys. Resistive heating is usually employed, with graphite or refractory metal heating elements. When the tube is impervious, the heating element can be in air and the same materials used in air furnaces can be used for heating elements. Atmosphere composition is often Ar, He, H2, or a CO/CO2 ratio. The gas is sometimes chosen for specific chemical reasons dictated by the materials being heat treated. Figure 8.8 depicts a general sketch of a reducing furnace.
Figure 8.8: Tube Furnace, Reducing Atmosphere. End seals isolate the tube so that a variety of atmospheres can be used to heat treat or sinter samples.
Three subjects will be discussed: materials quality, design, and operating problems. Figure 8.8 will be referred to in the following section.
Firing 249
Materials Quality
Graphite. Furnace parts are made from good-quality graphite. It is useful to ask about the graphite grade in furnace construction and then to give the graphite company a call. Generally, one recommends finely-grained, dense, and fairly strong graphite. Graphite has all kinds of impurities that react with the sample and discolor it. By heating graphite to a high temperature in chlorine, one can remove these impurities. This treatment is commercially available. The entire graphite interior, including the fiber insulation, tube, boat, and refractories can be purified.
Carbon fiber is used for insulation around graphite tubes. This can be bulk fiber or formed parts. Fiber insulation is a lower cost variety, but contains volatile substances that can get into the furnace atmosphere.
Ceramics. One can use impervious alumina or fused silica in neutral or reducing atmospheres. Sometimes, fused silica is called quartz; this is not accurate nomenclature as they are all fused silica. The same criterion applies to reducing furnace tubes and to oxidizing atmosphere furnaces. Make sure that the atmosphere will not reduce the oxide tube.
Metals. A continuing problem with firing in reducing atmospheres is binder burnout. Being in a controlled atmosphere and a closed system, how are the binders removed? Ni/Cr alloy muffles are available and can be installed in a low temperature furnace. The atmosphere in the muffle can be selected and the burnout precisely controlled. The part is very weak after burnout. A good idea is to set the part on the same setter that will be used in the firing. As such, one will not have to handle the part during the transfer to the high temperature furnace. Some furnace systems have gas control mechanisms for handling the burnout reaction products.
Reducing atmosphere furnaces can have refractory metal tubes. These tubes are Ni/Cr alloys for low temperatures or Mo at higher temperatures. Mo is not commonly used in tube furnaces as it is in other types of furnaces.
Stainless steel threads and sliding fits will tend to gall. To prevent
250 Ceramic Technology and Processing
galling, one should coat these parts with an anti galling compound. This compound contains copper and aluminum flakes in a greasy material and is available at an auto parts store.
Design
Proper design of the furnace components is very important since manufacturers are not perfect. It is not advisable to assume that the equipment is properly designed just because it was made by a major manufacturer. There is a trend toward SPC and improved product quality, with ISO 9002 certification. This certification is not a guarantee of quality, but it does show that the manufacturer is conscious of quality issues and is complying with some standards.
Purging. The best way to purge a tube furnace is to pump a vacuum and then back fill with the atmosphere. Leaks can be a major problem and may not be easily detected if the vacuum pump is not isolated from the furnace with an isolation valve. With the isolation valve closed, the decay of the vacuum can be observed and, if this happens, there is a leak that can be found and sealed. A cold trap to remove unwanted gaseous species is necessary for attaining a decent vacuum and to protect the pump. It is not necessary to attain a high vacuum for purging and backfill, but the pump should be at least a standard fore pump. With the use of a thermocouple gage and isolation, one can evaluate the vacuum system. It is not uncommon to find leaks in the system, especially on threaded joints. Stainless is hard to thread and a ragged thread has a good chance to leak. Teflon tape is good enough to seal a threaded joint if the thread is well cut. All of the interior furnace materials absorb gases that desorb as the temperature increases. When the atmosphere is critical, the furnace can be pumped down again after heating. This type of equipment is hardly high vacuum technology. The atmosphere is there to control bulk composition and to prevent oxidation of the graphite.
Resistors. For this discussion, the resistor material is graphite. There are essentially two designs: a tube and a slotted cylinder. These are shown in Figure 8.9.
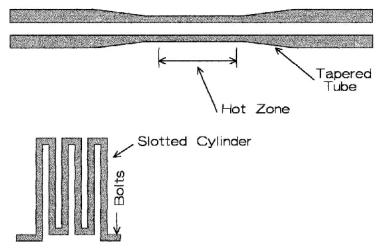
Firing 251
Figure 8.9: Graphite Heating Elements. Heating elements can be in tubular or castellated cylindrical design.
The tube element has a tapered section to increase the resistance in the central part of the tube. This concentrates the heat in the hot zone. It also weakens the tube, but graphite fortunately becomes stronger as the temperature is increased. There are two problems: the ID of the tube is restricted, and electrical contact to the power supply is random. Electrical contact is by a slip joint that may or may not allow the start of the run. When lucky, the contact will occur and as the temperature increases, the tube OD expands to maintain electrical continuity. The ID of the tube is stingy. For a lab furnace, the ID could be as small as 2.5 inches. It takes a lot of amps to heat a low resistance element, resulting in a big installation to fire a very small sample. Slotted hollow cylinders with a flange for connections are shown in the other sketch. In this design, the resistance is greater, reducing amperage. Smaller power supply and positive electrical continuity are substantial advantages. The element is bolted to the power source. Until there is a better connective design, the slotted cylinder is the preferred choice.
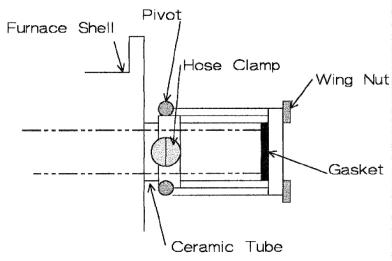
252 Ceramic Technology and Processing
End Closures. All slip cast ceramic tubes are diamond sawed on both ends. As the saw blade leaves the cut, the last little bit of the ceramic fractures leaves a small projection. This small projection should be removed by grinding. Figure 8.10 depicts a typical end seal.
Figure 8.10: Furnace End Closure. A ceramic tube can be sealed with a commercial end closure.
Use a hose clamp to hold onto the ceramic tube. Pivoted wing nuts fit into slots in the stainless end plate and clamp it securely against the end of the tube with a rubber gasket. The little projection that sticks out from the saw cut interferes with obtaining a good seal. The ends of the ceramic tube have to be diamond ground to obtain a seal. Look at the ends of the tube. If there is a sloppy little projection on either end, the ends have to be ground.
In Figure 8.8, the end seals have "O" rings on the end bells, and this works without difficulty. This furnace was built so that it could be pressurized up to 500 psi, principally for firing Si3N4 in an N2 atmosphere. This makes the bells heavy and a little difficult to handle.