
Ceramic Technology and Processing, King
.pdfGrinding 323
Outside Contractors
One can contract work to a variety of preexisting machine shops that also machine ceramics; these machine shops do advertise.4 Metal working shops are plentiful. This is advantageous as skills or capabilities can be selected; there are very talented people who will be delighted to do business. Another big advantage is that shops do not get paid until completion of the work and to specification. It is surprising how efficiency is promoted when money is involved. Perhaps, the main virtues of contracting with outside shops are the skills, experience, and delivery time. For such a contract, one recommends establishing a good rapport with a free exchange of information.
3.0 TYPES OF GRINDING
There is no intent to make this section comprehensive, as that is beyond the scope of this discussion. The intent is for general familiarization and some specialized comments that may be helpful. First under consideration will be a summary of grinding methods.
Grinding Methods
There are many types of grinding machine operations. The most common grinding methods for ceramics are as follows: surface, cylindrical, cutoff, universal, belt, and lap grinding. There are a variety of attachments that can be added to the grinding machine for grinding, such as IDs, faces, slots, holes, and chamfers; these will be briefly discussed.
324 Ceramic Technology and Processing
Surface Grinding
These machines have three slides: vertical, cross, and lengthwise. There are several ways to secure the parts that need to be ground. Magnetic chucks are useful but if the ceramic is not magnetic, one will need to glue the parts to a steel plate that is ground flat and parallel. Hot melt adhesives have excellent holding power and are available as sticks at any hardware store. Place the ground steel plate on a hot plate and rub the stick to melt the adhesive onto the surface. Preheat the parts on the hot plate and press them onto the adhesive with a twisting motion to seat them snug. As everything is blistering hot, use a tool. After grinding, reheat the assembly and remove the part. Again use a tool to prevent burns. The adhesive is soluble in trichloroethylene, which is a safew, non ignitable solvent. Trichloroethylene is somewhat toxic so one should use a hood or vent to prevent vapor inhalation. Waxes are commonly used for cementing parts, but waxes are not as good as hot melt adhesives for securing the part. With waxes, the part may come loose with resulting damage.
Another way to mount the parts is with steel blocks placed on the sides and held in place with the magnetic chuck. These can come loose, so care is required for safety.
One usually uses coolants when grinding ceramics. The supplier of the grinding wheels will recommend the coolant suitable for this application. The coolant is held in a sump that has a baffle, allowing the swarf to settle out. It is pumped with a nozzle directly onto the sample surface just in front of the wheel contact. Replace the coolant and clean out the sump regularly, depending upon the amount of use.
There are a variety of grinding wheel sizes and shapes, each of which is preferred for the job in hand. Besides configuration, the wheel has specifications on grit size, bond, and concentration. One uses coarse grits, such as 120 size grits, to remove most of the stock. One uses finer sizes, such as 220-325, for finishing. For fine-grained, dense ceramics, the preferred bond is resinoid. Coarse, friable ceramics, such as some refractories, are so abrasive that a metal bond is necessary because of its better wear resistance. These often use grit sizes on the coarser end.
There are two principle types of diamond: natural and synthetic. Rough grinding applications usually use natural, as it is more durable.
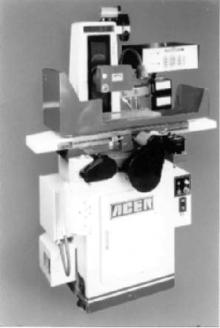
Grinding 325
Synthetic diamond grit is almost exclusively used for fine ceramics as it is more friable and freer cutting. It is available in a few grades based on friability. Additionally, synthetic is quite a bit less expensive than natural diamond.
Concentration numbers range from 50% to 100% representing the amount of diamond in the bond, with 100% being the maximum amount of diamond that can be successfully incorporated. Fine ceramics use 100% concentration. Figure 9.5 is of a surface grinder designed especially for ceramics.
Figure 9.5: Surface Grinder. Grinding machines should be rigid and dampen vibrations. (Courtesy of Chand Kare)
326 Ceramic Technology and Processing
The principle differences between this machine tool and a metal working machine pertain to the parameters relevant to grinding ceramics. These are CNC controlled and include wheel speed, table motions, depth of cut, and coolant flow.
Ceramics are more sensitive to surface damage than metals because ceramics are brittle while metals are usually ductile. Additionally, almost all ceramics are thermal insulators whereas almost all metals are thermal conductors. This results in the contact surface temperature, for a ceramic grinding, running hotter than for a metal. The machine, in Figure 9.5, has a cast iron base that is more rigid than a weldment structure. Table motion can be either servomotor driven or the more conventional hydraulic system. Grinding wheels are a critical part of the grinding process. One important wheel factor is the distribution of abrasives in the wheel bond. It turns out that it is difficult to evenly disperse a coarse-grained material in a finegrained, metal, or polymer powder. The two materials tend to segregate when handled.5
The coolant is selected and filtered for the particular ceramic being ground. Now, how are all these parameters chosen for a particular situation? Part of the answer is by experience and part by measuring the grindability. With grinding metals the "G" ratio is often used. This is an efficiency factor relating to the ratio of wheel wear to the amount of metal removed. However, for ceramics, the "G" ratio is so high due to the use of diamond wheels that it is not useful in this case. Instead, one way is to measure a grindablity factor. This factor relates the material removal rate to the wheel speed and the normal force between the abrasive tool and the work piece. Figure 9.6 illustrates this test stand.
Testing proceeds by forcing the end of a standard (3x4x45 mm) test bar against a diamond-grit-coated belt with a coolant. Adjustable weights determine the normal force. Use a fresh position on the belt for each measurement. Belt speed is adjustable. One measures the change in length of the test bar with time. A general guideline is that with low grindability ceramics, grinding becomes more difficult, advising slower wheel speeds, less down feed, free cutting wheel specifications, ample coolant of the appropriate type, and slower transverse table motion. In other words, take it easy.
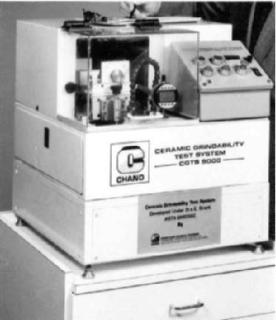
Grinding 327
Figure 9.6: Grindability Test System. The test results help in selection of wheel specifications and grinding conditions. (Courtesy of Chand Kare)
Cylindrical Grinding
A simple cylindrical grinder merely rotates the part, with limited tooling options. One can grind ODs and IDs. Inside diameters have special problems in that the geometry imposes stresses on the ceramic surface. The wheel diameter is usually small, requiring a high-speed, internally-grinding spindle. For long ID grinding, deflection is more critical because of the longer lever arm holding the wheel. Depending on the tolerance factor, one may need to make the setup as rigid as possible.
328 Ceramic Technology and Processing
CutOff
To minimize the volume of removable material and to increase the cutting speed, the diamond blades for cutoff purposes are usually thin. The blade thickness for lab use is often 0.035 inches. Unit pressures are high, making resin bonds short lived. One uses resin bonds to minimize damage to the ceramic, but ordinarily one uses metal bonds. Only the rim of the disc contains the diamond abrasive that is easily damaged when bent or when a piece breaks out. The diamond-containing rim of the blade is wider than the steel disc, providing clearance so that the disc clears the sides of the cut in the ceramic. When the cutoff blade enters the workpiece at an angle, it is deflected down the slope and the steel disc will rub. Also, the side of the diamond-containing rim will rub and wear. When the set of the rim is gone, the blade will not clear the sides of the cut and for all practical purposes the blade will be prematurely worn out. Encounter between the blade and ceramic surface should be at 90 degrees, and when it is not, a small notch should be cut where the blade is to enter the work so that it will not wander off square.
One can use cutoff blades on a surface grinder or on a cutoff machine. Many lab machines use an 8-inch diameter blade. On the surface grinder, one can gang up the blades with spacers between each blade. This is especially useful when grinding many identical parts, like test bars. These discs are smaller, where 4-inch D and 0.020-inch thickness is common.
Figure 9.7 is of a CNC-controlled, cutoff machine that either uses single or ganged cutoff blades with controlled wheel speed and feed rate.
Universal Grinders
These are versatile grinding machines that have more than one spindle and the capability of multiple setups. These machines are very expensive and not commonly found in the lab. One may need such machines for some types of complicated or high precision work. Some manufacturers include air bearings and vibration absorbing bases with multiple (3) spindles.
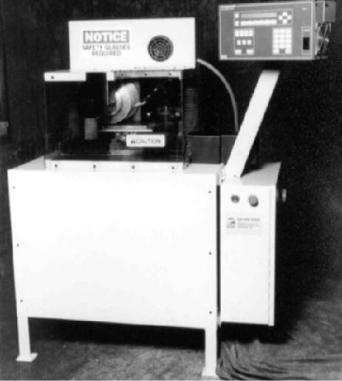
Grinding 329
Figure 9.7: Cutoff/Gang Slicer. Multiple cuts with ganged wheels speed up the cutoff process. (Courtesy of Chand Kare)
Belt Grinders
The belts are essentially sanding belts such as those found in wood working. Diamond abrasives are available but not common. The problem with belt grinding on ceramics is that the pressure between the belt and ceramic is limited, resulting in a low rate of cut. It is not practical to use belts on hard, dense ceramics, except perhaps for polishing a curved surface where the belt conforms the contour.
330 Ceramic Technology and Processing
Laps
One uses laps for superfinishing or polishing. Superfinishing calls for a loose abrasive in oil on a metal lap. While the surface shows good readings with a profilometer, it retains scratches. Polishing is done on
fabric lap surface and uses a variety of abrasives for different applications. a The combination of fabric and abrasive is often specific for each material.
Table 9.1 lists some examples.
Table 9.1: A Variety of Fabrics, Abrasives, and Coolants for Different Materials
Material |
Fabric |
Abrasive |
Coolant |
|
|
|
|
Alumina |
Nylon |
Diamond |
Oil |
|
|
|
|
Zirconia |
Texmet6 |
Diamond |
Oil |
|
|
|
|
Glass |
Felt |
CeO2 |
Water |
|
|
|
|
Plastic |
Felt |
Al2O3 |
Water |
|
|
|
|
The Ceria and Alumina polishes are obtained from ophthalmic supply houses.
4.0 OTHER MACHINING METHODS
Several of these machining methods will be briefly mentioned.
Ultrasonic
This method places an ultrasonic probe just above the part surface, in a water bath containing an abrasive. The abrasive vibrates, impinging on
Grinding 331
the surface and nibbling it away. Hole shape is that of the tool, making this method especially useful for odd shapes. Tool material is often a soft metal (often copper) that resists abrasion. Soft metals tend to smear rather than cut and can be durable under these conditions.
Electro Discharge Machining (EDM)
Tooling for EDM looks similar to that used for ultrasonic in that there is a shaped probe just above the surface of the ceramic. With the ceramic grounded and the probe charged, an electric spark erodes the ceramic surface. For this to happen, the ceramic has to be an electrical conductor, placing a restriction on where the technique is applicable.
Check List, Grinding
•Grinding Shop Departmental In the lab Outside sources
•Grinding Method Surface Cylindrical Cutoff Universal Belts
Laps
•Other Methods Ultrasonic EDM
332 Ceramic Technology and Processing
REFERENCES
1.D. Johnson-Walls, A. G. Evans, D. B. Marshall, and M. R. James, "Residual Stresses in Machined Ceramic Surfaces," J. Am. Ceramics Soc. 69[1] 44-47 (1986).
2.A. G. King, "Chemical Polish and Strength of Alumina," Materials Science Research Vol.3, (Plenum Press, 1966), pp. 529-38.
3.Alan G. King and W. M. Wheildon. Ceramics in Machining Processes. New York: Academic Press, 1966, p 63.
4.American Ceramic Society Bulletin, Westerville, Ohio.
5.Roland H. Chand, Personal Communication.
6.Buehler trade name.