
Автоматизация процессов дробления
.pdf
vk.com/club152685050 | vk.com/id446425943
Л12.1. Автоматизация процессов дробления.
В процессе добычи полезного ископаемого в подземных условиях в некоторых случаях возникает необходимость в дополнительной подготовке добытого полезного перед погрузкой его на транспортные средства (конвейеры, скипы). Это связано с тем, что куски полезного ископаемого, поступающего из забоя, не всегда имеют допустимые габариты, а попадание негабаритных кусков на транспортные устройства приводит в некоторых случаях к возникновению таких аварийных ситуаций, как заштыбовка мест перегрузок, заклинивание затворов на погрузочных пунктах и в дозаторах на подземных установках.
Применяемые в подземных условиях дробильные установки, оснащённые щековыми или конусными дробилками, выполняют процесс дробления в основном по одностадийным технологическим схемам.
Рисунок 1. Конусная дробилка крупного дробления ККД-900
Дробилка состоит из станины 1 (рис.1), дробильной чаши 2, траверсы 4, эксцентрика 9, дробящего конуса 3, приводного вала 12, привода 13. Станина дробильная чаша и траверса, которые соединяются между по образуют корпус. Внутри корпуса установлены и дробящий конус. дробящего установлен во расточке эксцентрика. Расточка выполнена образом - она смещена и под углом поверхности. через подпятник скольжения 10 упирается на центрального станины и соединяется при помощи зубчатой передачи с приводным 12, располагается в горизонтальном патрубке станины. Приводной вал соединяется с ведомого привода при упругой 13. дробилки имеет натяжное винтовое устройство. К центрального станины 1 прикреплен цилиндр 16, с поршня 15 и опорного
1
vk.com/club152685050 | vk.com/id446425943
вала 14 удерживает дробящий в положении и дистанционное регулирование разгрузочной щели Камера образуется наружной поверхностью броней 7 дробящего конуса и поверхностью 6 дробильной чаши. Когда эксцентрик вращается, дробящий конус получает гирационное в результате которого при броней 6 и 1 происходит дробление а при броней друг от – его Габариты подвергающегося определяются величиной разгрузочной А она, в свою очередь, измеряется при максимальном удалении
брони 1 от брони 6 и определяется физико-механическими перерабатываемого материала. Узлы трения дробилок необходимо обеспечивать смазкой. Это осуществляет
установка густой смазки |
и |
жидкой смазки. |
смазка |
к |
зубчатой |
опорному валу |
и |
||||
приводного |
густая – к |
|
подшипнику |
5 и |
уплотнению |
8 дробящего конуса, |
а |
к |
|||
подшипникам привода. |
|
|
|
|
|
|
|
|
|
|
|
Когда эксцентриковая |
втулка вращается, |
ось вала |
конуса |
траекторию в |
виде |
||||||
канонической |
поверхности, вершина |
которой |
в |
подвеса. Благодаря чему |
при |
эксцентриситете вращения оси конуса от до подвеса, то есть от камеры чем меньше от подвеса, тем этот радиус, а, следовательно, и ход сжатия подвижного конуса.
Основные параметры конусных дробилок:
Ширина приемного отверстия, мм
Ширина разгрузочной щели, мм
Производительность, м3/ч
Мощность главного привода, кВт
Автоматика дробильных установок должна обеспечивать: а) контроль уровня горной массы в приемном и загрузочном бункерах; б) контроль за параметрами смазки; в) управление пуском двигателей; г) регулирование загрузки дробилки.
Оптимальный процесс работы дробильных агрегатов может быть осуществлен только на базе автоматического программного управления, которое для получения надлежащего экономического эффекта должны разрабатываться с учетом конструктивных особенностей и условий эксплуатации дробильных агрегатов.
В общем случае регулирование загрузки дробилки необходимо, чтобы не допустить возникновения аварийных ситуаций вследствие случайных изменений крепости и крупности горной массы. Такое регулирование может выполняться непрерывно при использовании питателей с регулируемым приводом и дискретно, когда привод питателя нерегулируемый.
При этом система управления комплексом может быть реализована на двух уровнях сложности:
1.Местное управление и блокировка оборудования для предотвращения перегрузок оборудования (по мощности, уровню, производительности). Электрическая блокировка обеспечивает правильную последовательность пуска и остановки оборудования. Положение регулирующих органов оборудования в этом случае должно обеспечивать работу в его номинальном режиме.
2.Управление технологическим комплексом с использованием промышленных контроллеров и систем управления операторского уровня для регистрации данных, управления, расчета в реальном времени заданных значений параметров и изменения в реальном времени предельных значений параметров комплекса.
Процесс дробления как объект управления представлен на рис. 2.
2
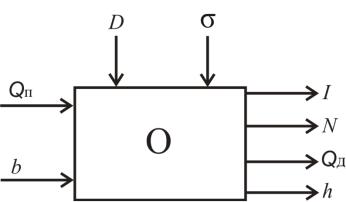
vk.com/club152685050 | vk.com/id446425943
|
Характеристика технологического комплекс дробления как объект управления |
|||||||||
приведена в табл. |
|
|
|
|
|
|
|
|||
Процесс |
|
Управляемые |
|
Управляющие |
Возмущающие |
|
|
|||
дробления |
|
величины |
|
параметры |
|
параметры |
|
|
||
как |
объект |
|
Мощность |
|
Производительность |
Гранулометрический |
|
|||
управления |
|
электропривода, |
дробилки |
по |
состав |
и |
физико- |
|
||
|
|
|
потребляемая |
при |
исходной |
руде; |
механические |
свойства |
|
|
|
|
|
дроблении; уровень |
частота |
качаний |
исходной руды. |
|
|||
|
|
|
материала в |
пасти |
подвижного |
Износ |
|
футеровки |
|
|
|
|
|
дробилки |
|
элемента |
дробилки; |
дробилки |
|
|
|
|
|
|
|
|
ширина |
|
|
|
|
|
|
|
|
|
|
разгрузочной щели |
|
|
|
как |
|
|
Процесс дробления можно оценить по ряду выходных параметров, таких |
|||||||||
потребляемые ток I и мощность N приводного двигателя, производительность дробилки |
||||||||||
QД |
, уровень заполнения камеры дробления h. В качестве управляющих воздействий |
|||||||||
выступают |
производительность |
питателя |
QП , подающего |
материал в камеру |
дробления, и размер разгрузочной щели b. Внешние возмущающие воздействия (крупность D и прочность σ исходного материала) носят случайный характер.
Количество перерабатываемого материала измеряют конвейерными весами, крупность дробленого продукта можно контролировать различными гранулометрами.
Наличие верхнего уровня руды на различных участках дробилки дает информацию о перегрузке или о забивке нижней разгрузочной щели. Для контроля верхнего уровня используются сигнализаторы наличия руды и гамма-реле, а для токопроводящих руд - электродные уровнемеры.
Контроль нижнего уровня в приемных бункерах необходим не только для получения информации о количестве материала, но и для предохранения питателей от разрушения падающими кусками руды при загрузке бункера (на пластинчатом питателе постоянно должен оставаться небольшой слой материала).
Нижний уровень контролируют преимущественно с помощью гамма-реле. Датчики-реле нижнего уровня в приемных бункерах применяются также в схемах
сигнализации и защиты.
Для автоматического обнаружения посторонних металлических предметов устанавливаются стандартные металлоискатели и металлоуловители.
Контроль температуры узлов трения и обмоток электродвигателей может быть осуществлен с помощью термоили тензорезисторов, а регистрация - многоточечных автоматических мостов переменного тока со встроенными контактными устройствами, которые используются в схемах защиты и сигнализации.
3
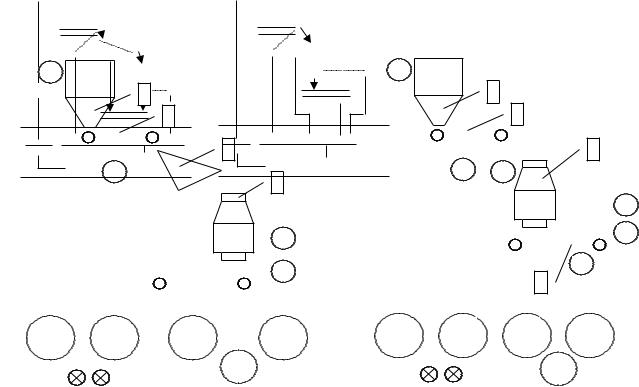
vk.com/club152685050 | vk.com/id446425943
Все современное дробильное оборудование оборудовано системами централизованной смазки. Аппаратура для контроля системы смазки, поставляемая, как правило, комплектно с дробилкой, включает приборы для измерения температуры масла, уровня в маслобаке и давления в маслопроводе.
|
а |
|
|
б |
|
LE |
|
LE |
1 |
1-1 |
1 |
|
1-1 |
|
|
2 |
|
|
2 |
|
3 |
|
|
4 |
|
|
4 |
2-7 |
LE |
|
2-5 |
2-5 |
||
|
|
|
|
|
|
|
|
|
|
|
EE 2-1 |
|
|
|
|
|
2-1 |
|
|
|
FE 2-2 |
|
|
|
|
EE |
|
|
|
||
|
|
|
|
|
|
|
5 |
||
|
|
|
|
|
|
|
|
|
|
H LA |
NS |
FC |
ЕI |
H |
LA |
NS |
FC |
Y |
|
L |
1-2 |
2-4 |
2-3 |
2-2 |
L |
1-2 |
2-6 |
2-4 |
2-3 |
|
|
|
H |
|
|
|
|
H |
|
|
|
|
|
|
|
|
|
Рис. 3 Схемы автоматизации процесса дробления
а – по потребляемой мощности; б – по удельному расходу энергии 1 – бункер; 2 – питатель пластинчатый; 3 – грохот; 4 – дробилка конусная; 5 - конвейер
Главная цель автоматизации процесса дробления сводится к максимальному использованию мощности, передаваемой на дробление, при
ограничениях на производительность дробилки и гранулометрический состав дробленого продукта. Простейшие системы управления дробильными агрегатами строятся по принципу стабилизации одного из выходных параметров дробилки.
К таким системам относятся одноконтурные САР уровня заполнения камеры дробления, тока (мощности) приводного двигателя с использованием в качестве управляющего воздействия производительности питателя.
Автоматическая система управления дробильным агрегатом должна не допускать перегрузки дробилки по мощности и уровню материала в пасти, но при этом должно обеспечиваться полное использование возможностей агрегата.
Перегрузка дробилки по потребляемой мощности может возникнуть, когда производительность по исходной руде превышает допустимое значение, определяемое гранулометрическим составом, и физико-механическими свойствами руды, и шириной разгрузочной щели.
4
vk.com/club152685050 | vk.com/id446425943
Перегрузка дробилки по количеству материала в пасти дробилки возникает, если производительность по исходной руде превышает максимально возможный расход через дробилку при данной ширине разгрузочной щели.
При автоматическом управлении процессом дробления используют следующие принципы:
а) стабилизация производительности дробилки по исходной руде изменение частоты вращения привода питателя (Q=const, n = var)
б) стабилизация мощности, потребляемой электроприводом дробилки, изменением частоты вращения привода питателя (P=const, n = var) – рис. 3а
в) стабилизация суммарного сигнала производительности и мощности с воздействием на частоту вращения привода питателя (Uq+Up=const, n=var) – рис. 3б
г) стабилизация уровня руды в пасти дробилки с воздействием на частоту вращения привода питателя (H=const, n=var).
Принцип (а) эффективен при переработке руды с малыми колебаниями физикомеханических свойств. Датчиком производительности в системах, реализующих этот принцип, служат весоизмерители или дозаторы.
Реализация принципа (б) позволяет не допустить перегрузки дробилки по мощности при переработке любых типов руд. Датчиками активной мощности в системах, реализующих этот принцип, служат ваттметровые преобразователи серии E 800, преобразующие величину активной мощности в стандартный токовый сигнал 4-20 мА.
Реализация принципа (в) позволяет поддержать максимальную загрузку дробилки независимо от колебаний гранулометрического состава и физико-механических свойств исходной руды. Принцип реализуется двухконтурной системой автоматического регулирования. Первый контур осуществляет стабилизацию руды в дробилку изменением частоты вращения вала питателя, второй – корректирующий, осуществляет изменение задания первому контуру при изменении активной мощности вследствие изменения крупности и физико-механических свойств руды.
Реализация принципа (г) обеспечивает максимальную загрузку дробилки по уровню материала вне зависимости от свойств исходной руды. Однако техническая реализация этого принципа затруднена из-за сложности непрерывного контроля уровня загрузки дробилки. Этот принцип может быть реализован для управления дробилками, снабженными приемными воронками, где уровень заполнения можно контролировать с помощью акустического датчика УКЗ-1.
В устройстве контроля заполнения конусной дробилки (УКЗ-1) используется метод измерения акустического сигнала, излучаемого приемной воронкой дробилки при подаче в нее исходного питания, с последующим преобразованием этого сигнала в электрический токовый сигнал.
Для непрерывного контроля уровня в дробилке также находят применение уровнемеры радарного типа.
Уровнемер УЛМ-31А1 представляет из себя систему измерения уровня, состоящую из одного или нескольких радиолокационных датчиков уровня. В данном уровнемере УЛМ-31А1 используется непрерывное модулированное по частоте радиоизлучение 5
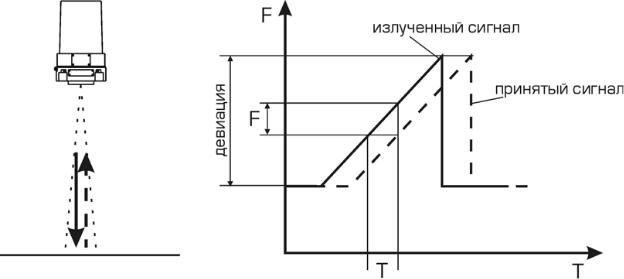
vk.com/club152685050 | vk.com/id446425943
(FMCW). Принцип действия такого уровнемера заключается в следующем. Микроволновый генератор датчика уровня формирует радиосигнал, частота которого изменяется во времени по линейному закону – линейный частотномодулированный сигнал. Этот сигнал излучается в направлении продукта, отражается от него, и часть сигнала через определенное время, зависящее от скорости света и расстояния, возвращается обратно в антенну. Излученный и отраженный сигналы смешиваются в датчике уровня, и в результате образуется сигнал, частота которого равна разности частот принятого и излученного сигналов F и, соответственно, расстоянию от антенны до измеряемого продукта. Дальнейшая обработка сигнала осуществляется микропроцессорной системой датчика уровня и заключается в точном определении частоты результирующего сигнала и пересчете ее значения в значение уровня наполнения резервуара.
Уровнемер УЛМ-31А1 выдаёт унифицированный токовый выходной сигнал 4-20мА и имеет цифровой интерфейс RS-485. Также имеет встроенные электромеханические реле для сигнализации достижения критических уровней.
Максимальная абсолютная погрешность измерения прибора - ±3мм.
Рис. 4. Принцип действия радарного уровнемера.
САР уровня горной массы в дробилке позволяет исключить ее переполнение в режиме работы с максимальной производительностью. Однако в такой системе не обеспечивается защита главного двигателя дробилки от перегрузки, невозможно регулировать производительность дробилки.
САУ процессом дробления, построенная на принципе стабилизации тока (мощности) в статорной цепи приводного двигателя дробилки, обеспечивает наибольшую производительность при дроблении прочных материалов. При слабых породах в такой системе управления загрузкой может происходить переполнение (завал) дробилки или приемного устройства, в которое поступают продукты дробления.
Наиболее целесообразным является комбинированное регулирование загрузки дробилки. Вариант САУ процессом дробления, поддерживающий заданное значение
6

vk.com/club152685050 | vk.com/id446425943
весовой производительности щековой дробилки и ограничивающий уровень материала в камере дробления и ток электродвигателя дробилки, представлен на рис. 5.
Рис. 5 Структурная схема автоматического управления процессом дробления (комбинированный вариант): Б – бункер; ЛП – ленточный питатель с регулируемым приводом; ДЩ – дробилка щековая; ОК – отгружающий конвейер; ДП, ДТ, ДУ – датчики
соответственно производительности дробилки Qдр , тока двигателя I и уровня h заполнения камеры дробилки; РУ – регулирующее устройство; Ml, M2 – электродвигатели
питателя и дробилки; QП – производительность питателя; Qдр зад , Iзад , hзад – заданные значения соответственно производительности, тока двигателя и уровня
заполнения дробилки; UРУ – сигнал регулирующего устройства.
Основным контуром регулирования является контур регулирования по току (мощности), потребляемому приводным двигателем дробилки. Ток (мощность) характеризуется условиями дробления и физико-техническими данными горной массы, поступающей в дробилку: растет с увеличением крупности кусков и крепости поступающей горной массы и наоборот. Кроме того, увеличение (уменьшение) тока (мощности), потребляемого приводным двигателем дробилки, соответствует уменьшению (увеличению) ее производительности. Следовательно, система стабилизации по току (мощности) может быть использована для изменения производительности дробилки, что достигается изменением уставки по току (мощности). Стабилизация по току (мощности) приводного двигателя дробилки осуществляется изменением производительности питателя.
Дробильная установка в рассматриваемом варианте включает в себя бункер, ленточный питатель с регулируемым электроприводом постоянного тока, щековую 7
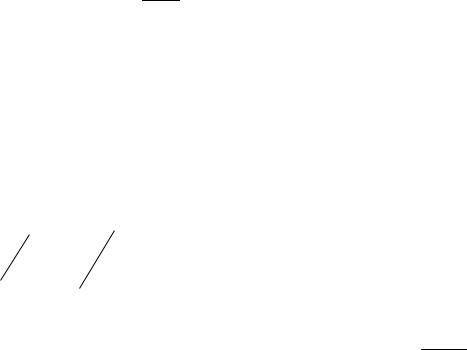
vk.com/club152685050 | vk.com/id446425943
дробилку с нерегулируемым асинхронным электроприводом и отгружающий конвейер. В качестве датчика производительности используются электротензометрические конвейерные весы, датчика уровня – фотоэлектрический уровнемер (осветитель с фотодатчиком), датчика тока – датчик нагрузки, чувствительным элементом которого является трансформатор тока, включаемый в статорную цепь асинхронного двигателя дробилки. Регулирующее устройство может быть выполнено на базе магнитного усилителя.
Переходные процессы в дробилке, работающей с постоянной частотой ω и амплитудой А качания щеки, можно описать, используя уравнение материального баланса:
|
|
|
|
|
|
d M |
+QДР =¿ QП , ¿ |
|
||||
|
|
|
|
|
|
d t |
|
|
|
|
|
|
|
где QДР , QП |
– производительность соответственно дробилки и питателя, т/ч; М |
||||||||||
– запас материала в дробилке, т. |
|
|
|
|
|
|
|
|
||||
|
Запас материала в дробилке обусловливает инерционность аппарата. |
|||||||||||
Дифференциальное уравнение дробилки по параметрам h и |
QП имеет вид |
|||||||||||
|
|
|
|
T |
0 |
dΔh+ Δh=K |
0 |
ΔQ |
П |
, |
|
|
|
|
|
|
|
dt |
|
|
|
|
|||
|
T = |
γSном |
М |
ном |
|
|
|
|
|
|
|
|
|
|
= |
|
|
|
|
|
|
|
|
|
|
где |
0 |
m |
|
Qдр . ном |
– постоянная |
времени, характеризующая |
||||||
|
|
способность дробилки накапливать и расходовать материал; γ – плотность материала,
|
ΔQдр |
|
т/м3; Sном – площадь верхнего сечения пасти дробилки, м2; |
m= Δh |
– |
коэффициент пропорциональности, определяемый статической характеристикой дробилки (рис. 3.3); K0=l/m – передаточный коэффициент.
Зависимость Qдр=ϕ(h) |
нелинейна и имеет ограничения по уровню hmax и |
производительности Qдр max |
при данных частоте вращения вала и амплитуде А |
колебаний щеки дробилки. |
|
8

vk.com/club152685050 | vk.com/id446425943
Рис. 6. Статическая характеристика щековой дробилки |
|
|
|
|
||||||||
|
Передаточная функция щековой дробилки по каналу QП – h имеет вид |
|
||||||||||
W01 |
( p)= |
Δh( p) |
= |
|
K0 |
. |
|
|
|
|
|
|
ΔQП ( p) |
T 0 p+1 |
|
|
|
|
|
|
|||||
|
|
|
|
|
|
|
|
|
|
|||
|
Передаточная |
|
|
функция |
дробилки |
по |
каналу |
QП |
– |
QДР |
||
с учетом запаздывания |
τ , обусловленного способом |
измерения |
QДР |
с |
помощью |
датчика производительности, установленного на отгружающем конвейере на некотором расстоянии lДП от разгрузочной щели дробилки, может быть представлена выражением
W02 |
( p)= |
ΔQдр( p) |
−рτ |
, |
||||
|
ΔQп( p) |
=e |
|
|||||
|
|
|
|
|
|
|
||
|
|
lДП |
|
|
|
|
|
|
где |
τ = νок |
, |
с; νок |
– скорость движения ленты отгружающего конвейера, м/с; |
||||
lДП |
|
– расстояние установки датчика ДП. |
Алгоритмическая структурная схема системы автоматического регулирования процесса дробления щековой дробилки в линейном представлении приведена на рис. 7.
Регулирующее устройство РУ, питатель и электродвигатель дробилки ЭД представлены апериодическими звеньями с соответствующими передаточными коэффициентами и постоянными времени.
9

vk.com/club152685050 | vk.com/id446425943
Рис. 7 Алгоритмическая структурная схема системы автоматического регулирования процесса дробления
Нелинейные звенья Н31 и Н32 отражают задержку действия обратных связей по уровню заполнения камеры дробления и току двигателя дробилки при текущих значениях этих параметров ниже их заданных значений. До высоты уровня горной массы
0,6 hmax в камере дробления регулирование ведется только по производительности дробилки, при превышении этого уровня – по уровню загрузки и производительности.
При перегрузке двигателя дробилки вступает в действие обратная связь по току и вызывает уменьшение подачи горной массы в дробилку. Таким образом, комбинированная САР процесса дробления обеспечивает требуемую производительность дробилки, защиту ее электродвигателя от перегрузки, исключает переполнение камеры дробления.
10