
- •ХХХХ . ХХХХХХ . ХХХ ХХХХХХ . ХХХХХХХХ
- •Состав транспортных бизнес–процессов
- •Внутризаводские системы транспортировки грузов
- •рис. 4.9. Схемы маятниковой системы маршрутных перевозок
- •Рис. 4.15. Организационная структура энергетического хозяйства
- •Рис. 6.3. Фрагмент жизненного цикла ресурсов предприятия
- •Показатели информационной характеристики задачи АСОИУ
- •Наименование показателя
Коротких М.Т.
Технология и организация промышленного производства
Часть 2 Конспект лекций
|
|
|
Содержание |
|
1. |
Основные принципы построения технологических |
Стр. |
||
|
||||
процессов обработки деталей машин |
3 |
|||
2. |
Технология сборки машин |
11 |
||
3. |
Основы автоматизации машиностроительного |
|
||
производства |
|
|
18 |
|
4. |
Организация машиностроительного производства |
30 |
||
5. |
Подготовка |
и |
организация |
высокотехноло |
|
производства |
|
|
54 |
6. |
Организация вспомогательных цехов и служб предприятия |
|||
|
|
|
|
76 |
7. |
Стратегическое и оперативное планирование производства |
|||
|
|
|
|
94 |
8. |
Основы организации управления производством |
120 |
||
9. |
Основы управления персоналом предприятия |
137 |
1.Основные принципы построения технологических процессов обработки деталей машин
Современные сложные машины состоят из тысяч и даже миллионов деталей, и
решение |
многовариантной |
задачи |
построения |
оптимального |
технологическ |
процесса изготовления для каждой из них, было бы совершенно нереальной задачей. |
|||||
Однако, даже поверхностное знакомство с этими деталями показывает, что многие из |
|||||
них похожи по форме, изготовлены из одних и тех же материалов, требования к |
|||||
точности и шероховатости поверхностей многих деталей близки. |
|
||||
Близкие |
категории свойств |
определенных групп |
деталей должны определять |
сходство технологических процессов их изготовления. И, если для какой-то детали определить оптимальный технологический процесс, то, наверное, и для похожих деталей такой процесс может оказаться оптимальным, или близким к оптимальному.
Профессором |
Соколовским |
|
А. .И […] была |
выдвинута |
идея |
типизации |
технологических |
процессов |
в |
машиностроении, основывающаяся |
на |
создании |
|
классификации |
деталей, объединяемых в группы |
по сходности |
категорий свойств |
(форме, свойствам материала, размерам, точности и шероховатости поверхности), типу производства.
Отдельные типы деталей могут объединяться тогда общим, оптимальным для данных условий, технологическим процессом.
Классификация деталей может быть построена с любым уровнем определения отличительных признаков и в настоящее время строится по схеме:
Класс – подкласс –группа – подгруппа – тип Класс – это совокупность деталей определенной конфигурации, объединенных
общностью технологических задач.
Тип – это совокупность сходных деталей, для которых в данных производственных условиях разрабатывается общий технологический процесс.
Таким образом, |
детали, |
относящиеся к |
одному типу, отличаются настолько |
незначительно, что |
могут |
изготавливаться |
с применением одного и того |
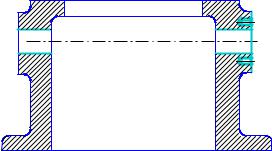
оборудования, по общему технологическому маршруту, зачастую, с применением одинакового инструмента и оснастки.
Для деталей же более отличающихся друг от друга, относящихся к отдельным группам, могут быть построены оптимальные технологические операции, с единым содержанием и последовательностью технологических переходов. Эти типовые технологические операции существенно повышают эффективность построения общих технологических процессов, так как позволяют использовать оптимальные процессы изготовления определенных поверхностей (или их совокупности) конкретной детали.
Эти типовые технологические операции повторяются при изготовлении деталей, относящихся к определенной группе.
Например, при изготовлении определенной группы корпусных деталей, типовой является операция обработки точного глубокого отверстия и торцевой плоск поверхности и отверстий, расположенных концентрично оси глубокого отверстия
(рис.1.1).
Рис.1.1 |
Такие операции обычно выполняются на горизонтально-расточных ,станках применением типовой оснастки (борштанг, расточных резцов, торцевых фрез и т.д.).
Таким образом, классификация деталей машин и типизация технологических процессов является средством, позволяющим сократить время на технологическую подготовку производства, а сами технологические процессы приблизить оптимальным.
На базе объединения деталей в группы профессором Митрофановым С.П. […] был предложен групповой метод обработки деталей, при котором для групп однородной продукции устанавливаются однотипные методы обработки при использовани одинакового или переналаживаемого оборудования и оснастки.
При реализации этого метода для построении технологических процессов, детали группируются по общности, применяемых при их обработке, оборудования, оснастки, наладки и структуры технологической операции.
Естественно, что такой метод рационально применять в условиях серийного производства. В массовом производстве есть смысл потратить усилия на оптимизацию технологического процесса изготовления конкретной данной детали, вплоть до разработки специального оборудования именно для ее изготовления.
При |
применении |
этого |
метода |
оказалось |
рациональным |
разрабо |
технологический процесс, |
оснастку |
для некоторойкомплексной детали, реальной |
или специально спроектированной, содержащей в своей конструкции все основные элементы (поверхности), присущие деталям данной группы. Поэтому комплексная деталь относится к данной группе, являясь наиболее сложным ее представителем. Если для такой детали разработать оптимальный технологический процесс обработки и

оснастку, то любой представитель данной группы деталей может быть изготовлен с
применением данного технологического процесса |
и |
оснастки |
при необходим |
||||
подналадке. |
|
|
|
|
|
|
|
Естественно, что чем более простая деталь изготавливается по такой технологии, тем |
|||||||
большее количество технологических переходов не применяется |
(рис. |
1.2). |
|||||
Эскизы |
деталей |
Комплексная деталь |
|
||||
Технологические |
|
10 |
9 8 |
7 6 5 4 3 |
2 |
1 |
|
переходы |
|
11 |
|
|
|
|
|
|
|
|
|
12 |
13 |
14 |
|
Подрезать торец 1
Точить пов-ть 7
Точить поверхность 2,3
Точить поверхность 5
Точить канавку 6
Нарезать резьбу 4 Точить поверхность 8,9
Сверлить отверстие 12 Зенкеровать отверстие 13,14
Точить фаску 10 Отрезать деталь 11
Рис.1.2
Несмотря на предложенные методы типизации, проектирование технологических процессов остается довольно сложной задачей решаемой в опред последовательности:
1.Анализ исходных данных
2.Определение типа производства
3.Определение класса, группы и типа детали. Выбор типового или группового
|
технологического |
процесса |
в |
качестве |
аналога |
для |
проект |
||
|
технологического процесса изготовления данной детали. |
|
|
|
|||||
4. |
Выбор технологии изготовления заготовки для данной детали. |
|
|
||||||
5. |
Выбор |
технологических |
баз |
для |
получения |
отдельных |
поверхносте |
составление плана их обработки.
6.Разработка технологического маршрута обработки
7.Разработка технологических операций
Для оценки возможности реализации и эффективности разработанног технологического процесса производятся дополнительные этапы работ:
1.Нормирование технологического процесса
2.Расчет его экономической эффективности
3. Определение требований техники безопасности
a. Основные этапы разработки технологических процессов изготовления деталей машин
1.1.1 Анализ исходных данных
Для проектирования технологических процессов необходимо наличие все информации о свойствах объекта производства, об условиях его испытания и(или) приемки. Такая информация может содержаться в чертежах, цифровых моделях.
Существенным является также информация об объеме выпуска изделий определенный период.
Естественно, что разработчик технологических процессов использует большие объемы справочно-нормативной документации, стандартов, типовые технологические процессы. В настоящее время эта документация все более представляется в вид электронных баз данных, которые используются не только человеком, но все более и более автоматизированными системами.
Предполагается, что на стадии проектирования, детали прошли анализ на технологичность и на стадии разработки технологического процесса вмешательство технолога в конструкцию изделия невозможно.
Дело в том, что при проектировании конкретного процесса обработки у технолога могут возникнуть идеи об изменении конструкции детали, которое может существенно удешевить ее обработку или повысить качество.
Такие изменения конструкции, в принципе, возможны, но требуют значительных усилий по согласованию.
Требования к технологичности конструкции зависят от объема выпускаи типа производства. Конструкции деталей машины выпускаемой в единичном производстве
и конструкции |
деталей для условий массового производства |
могут разител |
отличаться. Какую |
бы замечательную машину(например, автомобиль) |
не удалось |
построить в кустарных мастерских, испытать ее, убедиться в ее уникальных качествах, при переходе к ее массовому производству придется полностью переработать рабочие чертежи деталей.
Это связано с тем, что чертеж детали зачастую определяет технологический процесс получения заготовки для ее изготовления. Чертеж детали получаемой горячей объемной штамповкой будет предусматривать уклоны на свободных поверхностях,
перпендикулярных |
плоскости |
разъема |
штампа. Такие |
уклоны |
конструктор, |
естественно, не |
предусмотрит, |
предполагая |
получение |
детали |
фрезерованием. |
Обычно конструкция литой детали настолько специфична, что другими методами ее изготовить либо невозможно, либо чрезвычайно трудоемко.
На этом этапе производится анализ технологических возможностей изготовления продукции в данных условиях производства. В реальных условиях технологическая подготовка производства проводится:
-для вновь создаваемого производства. В этом случае, на данном этапе, определяется возможность изготовления данной продукции с использованием всего спектра технологического оборудования, имеющегося на мировом рынке;
-для конкретного производства в условиях отсутствия инвестиций в его развитие. Определяется возможность производства заданной продукции на имеющемс оборудовании и при существующем персонале;
-для конкретного производства в условиях возможных инвестиций в его развитие. Определяется рациональность применения различных, новых технологических
методов, прогрессивного оборудования, которое следует приобрести, необходимость переквалификации или привлечения дополнительной рабочей силы.
1.1.2 Определение типа производства
Для определения типа производства необходимо знать коэффициент закрепления операций, который на начальной стадии проектирования технологического процесса точно не определяется. Ориентировочно он определяется исходя из предполагаемой длительности операции и фонда времени рабочего места:
Кз = (FmКот)/(Ntшт),
где F – месячный фонд одосменной работы рабочего места, m – число рабочих смен, Кот – коэффициент, учитывающий непроизводительные простои рабочего места, N – требуемый месячный выпуск изделий, шт/мес, tшт – штучное время, час (определяется
на |
данном |
этапе |
приблизительно, по |
аналогии |
с |
похожими |
изделиями, по |
укрупненным расчетам, таблицам и т.д.). |
|
|
|
|
Как уже отмечалось, тип производства должен учитываться при разработке технологического процесса, и во многом определяет его структуру, применяемое оборудование и т.д. (табл.1).
Таблица 1
Организационно – технические характеристики типов производства
Характеристики |
|
|
Тип производства |
|
|
|
|
|||||
технологических |
Массовое |
Крупно- |
|
Средне- |
|
Мелко- |
|
Единичное |
|
|||
процессов |
Кз=1 |
серийное |
|
Серийное |
|
Серийное |
|
|
||||
|
|
|
10>Кз>1 |
|
20>Кз>10 |
|
40>Кз>20 |
Кз>40 |
|
|||
Форма организа- |
Непреры- |
Непреры- |
|
Переменно |
|
Группо- |
|
Предметная |
|
|||
ции |
производст- |
вно пото- |
вно |
пото- |
|
поточная |
|
вая |
|
|
|
|
венного процес- |
чная |
чная |
|
или |
груп- |
|
|
|
|
|
||
са |
|
|
|
|
|
повая |
|
|
|
|
|
|
|
|
|
|
|
|
|
|
|
|
|
||
Вид |
технологи- |
Типовые и единичные |
|
Типовые, |
|
Группо- |
|
Единичные |
|
|||
ческих |
|
|
|
|
групповые |
|
вые |
и |
|
|
||
процессов |
|
|
|
|
и |
единич- |
|
единич- |
|
|
|
|
|
|
|
|
|
|
ные |
|
|
ные |
|
|
|
Принцип |
Концентрация |
|
|
Дифферен- |
|
Концентрация |
|
|
||||
построения |
|
|
|
|
циация |
|
|
|
|
|
||
технологических |
Обработка многоместная |
или одно- |
|
Обработка |
|
|
||||||
операций |
местная |
с |
непрерывной |
|
многоместная или одно- |
|
||||||
|
|
раздельной установкой |
|
|
|
местная |
|
с одновреме- |
|
|||
|
|
|
|
|
|
|
|
|
нной установкой |
|

Оборудование |
Специа- |
|
Специаль- |
|
Универ- |
|
|
Универсальное, |
станки |
|
||||||
|
льное |
|
|
ное |
и |
спе- |
|
сальное |
|
|
с ЧПУ |
|
|
|
|
|
|
|
|
|
циализиро- |
|
специали- |
|
|
|
|
|
|
|
|||
|
|
|
|
ванное |
|
|
зированное |
|
|
|
|
|
|
|
||
|
|
|
|
|
|
|
|
станки |
|
|
|
|
|
|
|
|
|
|
|
|
|
|
|
|
ЧПУ, |
|
|
|
|
|
|
|
|
|
|
|
|
|
|
|
|
гибкие |
|
|
|
|
|
|
|
|
|
|
|
|
|
|
|
|
модули |
|
|
|
|
|
|
|
|
Оснастка |
Неразбор- |
|
Сборно-разборные |
|
|
Универ- |
Универсаль- |
|
||||||||
|
ные |
спе- |
|
приспособления, |
|
|
сально |
|
ные |
безна- |
|
|||||
|
циальные |
|
специализированные |
|
|
наладоч- |
ладочные |
|
||||||||
|
приспосо- |
|
наладочные |
|
|
|
ные |
при- |
приспосо- |
|
||||||
|
бления |
|
|
приспособления |
|
|
способ- |
бления |
|
|||||||
|
|
|
|
|
|
|
|
|
|
|
ления |
|
|
|
|
|
Метод |
Базирование |
|
без |
- |
выБазирование |
|
|
без |
- |
выБазирование |
|
|||||
обеспечения |
верки, |
работа |
на |
нас- |
|
верки |
и |
с |
выверкой, |
с выверкой, |
|
|||||
точности |
троенных |
|
|
станках, настройка по пробным |
настройка |
|
||||||||||
|
активный контроль |
|
|
деталям |
или |
комбини- |
по |
пробным |
|
|||||||
|
|
|
|
|
|
|
|
рованная |
|
|
|
проходам и |
||||
|
|
|
|
|
|
|
|
|
|
|
|
|
|
промерам |
|
1.1.3 Определение класса, группы и типа детали
Выбор типового или группового технологического процесса в качестве аналога для проектирования технологического процесса изготовления данной детали возможен при отнесении детали к определенной классификационной группе, типу.
Предполагается, что на стадии проектирования деталь классифицируется исходя из ряда ее конструктивных и технологических признаков и ее характеристики могут быть отражены в конструкторско-технологическом коде. В общем виде, такой код состоит из кода классификатора ЕСКД и технологического кода (рис.3.3).
Обозначение детали по |
Технологический код |
ЕСКД ГОСТ2.201-80 |
детали |
ХХХХ . ХХХХХХ . ХХХ ХХХХХХ . ХХХХХХХХ
Порядковый регистрационный номер Код классификационной характеристики
Код организации разработчика
Рис.3.3
Код классификационной характеристики определяет класс, подкласс, группу,
подгруппу, вид детали. Дополнительный же технологический код детали определяет ее размерные характеристики, группу материала, основной
технологический метод изготовления(например, детали изготавливаемые литьем, детали обрабатываемые резанием и т.д.), вид исходной заготовки, параметры точности
и шероховатости поверхности, виды дополнительной обработки, массу детали. Таким образом, обозначение детали будет состоять из20 знаков и сведущему человеку может рассказать о детали, как о объекте производства, очень многое (хотя , конечно, это обозначение не заменит чертеж и для проектирования технологического процесса недостаточно).
Смысл такого кодирования заключается в селекции деталей на ста предварительного анализа, определении технологических возможностей производства, подборе типовых технологических процессов.
Особенно эффективен конструкторско-технологический код при машинном анализе и применении систем автоматизированной подготовки производст, ва частности, систем автоматизированной разработки технологических процессов.
1.1.4 Выбор технологии изготовления заготовки для данной детали
Вид заготовки обычно задается чертежом детали и определяется на стадии ее
проектирования, исходя из требуемой формы( например, некоторые формы можно |
|
|||||||||
получить только литьем), требований к свойствам материала( особо |
прочные |
|
||||||||
стальные изделия можно получить только |
при |
получении |
заготовки |
го |
||||||
пластической |
обработкой, |
например, |
ковкой), |
исходя из |
размеров, экономических |
|
||||
соображений, |
требований |
к |
точности |
и |
шероховатости |
необрабатыва |
||||
поверхностей и т.д. |
|
|
|
|
|
|
|
|
||
Естественно, что на стадии проектирования участвуют специалисты технологи, |
||||||||||
определяющие технологические возможности получения той или иной заготовки. Но |
|
|||||||||
для |
многих |
деталей |
выбор |
заготовки |
может |
осуществляться |
и |
на |
проектирования технологического процесса, если из чертежа непосредственно не следует конкретный вид заготовки, и существует многовариантность выбора метода (прокат, литье, обработка давлением…) или разновидности метода(литье в кокиль, литье под давлением, литье по выплавляемым моделям…).
Для выбора оптимального метода изготовления заготовки производят сравнение вариантов стоимости заготовки с учетом стоимости ее черновой обработки.
Сзаг = МзЦм –МоЦо + СзарТ(1 + Сн/100),
Где Мз – масса заготовки, Цм – цена материала заготовки, в зависимости от метода ее получения, Мо - масса отходов при обработки заготовки (стружки), Цо – цена отходов,
Сзар- часовая тарифная ставка рабочих, используемых при черновой |
обработке |
заготовок, Т – время черновой обработки заготовки, Сн |
|
- цеховые накладные расходы. |
|
Естественно, чем точнее способ получения заготовки, тем меньшие припуски могут |
|
оставляться на обрабатываемых поверхностях под последующую |
обработку. А |
некоторые поверхности, при применении точного способа получения заготовки, могут и не требовать дальнейшей обработки. Тогда стоимость последующей обработки заготовки может значительно снижаться. Однако точные способы получения заготовок
могут быть значительно дороже и выигрыш от уменьшения объема обработки может не окупить удорожания стоимости заготовки.
Выбор заготовки предполагает расчет припусков на все, обрабатываемые в последующем, поверхности, определении всех размеров и точности заготовки, и разработки ее чертежа. Расчет припусков на
обрабатываемые поверхности предполагает знание последовательности обработки, которая на данной стадии разработки технологического процесса еще неизвестна. Поэтому на этой стадии припуски определяются по укрупненным нормативам, исходя из точности, характерных размеров поверхности и выбранного технологического метода получения заготовки.
Вопросы для самопроверки:
1. По каким свойствам объединяются детали при типизации технологичес процессов?
2.По какому принципу объединяются детали при организации группового метода их обработки?
3.Чем отличается комплексная деталь от деталей входящих в группу?
4.Перечислите последовательность этапов разработки технологического процесса.
5.Чем отличается класс деталей от типа деталей?
6.Какие виды технологических процессов используются в условиях массовог производства?
7.Какой вид оборудования используется в средне-серийном производстве?
8.Какой вид оснастки используется в массовом производстве7
9.Какие формы организации производственного процесса используются в условиях единичного и мелкосерийного производства?
10.Почему тип производства на стадии проектирования технологического процесса можно определить только ориентировочно?
Образец карты тестового контроля:
1.Какие детали можно объединить в группу при применении типового мето разработки технологических процессов:
а). Карданный вал, ось колеса, шпиндель станка б). Маховик, крышка двигателя, шпиндель станка
в). Коленчатый вал двигателя, поршень, рукоятка переключения скоростей.
2.Кто определяет метод изготовления заготовки детали машины: а). Конструктор б). Технолог
в). Конструктор и технолог совместно
3.В каком типе производства применяется работа на настроенных станках автоматический контроль в процессе обработки:
а). Массовом и крупносерийном б). Единичном и серийном в). Крупносерийном
4. В каком типе производства целесообразно применять заготовки полученны горячей объемной штамповкой:
а). Серийном, массовом б). Единичном, серийном
в). Во всех типах производства
5. В каком типе производства целесообразно применять заготовки полученны литьем:
а). Серийном, массовом б). Единичном, серийном
в). Не зависит от типа производства, а зависит от формы заготовки
2. Технология сборки
Сборочные работы, в зависимости от типа производства, составляют от 20 до 40%
общей |
трудоемкости |
изготовления |
машины. Эти |
работы |
обычно |
требуют |
значительных затрат физического труда слесарей сборщиков. Если в |
условиях |
|||||
массового |
производства, |
например, автомобилей широко применяются |
средства |
автоматизации и мехагн изации сборочных процессов, то в индивидуальном и мелкосерийном производстве, особенно при создании уникальной техник, экспериментальных экземпляров новых машин проблемы автоматизации сборочных работ практически не решены.
В зависимости от типа производства и вида изделия сборка может быть организована различным способом.
При массовом производстве наиболее эффективной является подвижная поточная сборка, при которой изделие перемещается по специализированным рабочим местам, где выполняются простейшие сборочные операции. Такие места могут быть оснащены специальными средствами механизации или быть полностью автоматизированы. (При такой форме организации сборки выпускают изделия бытовой техники, компьютеры, боеприпасы…). Такую форму организации сборки предложил Генри Фо, рдешая
задачу массового выпуска автомобилей. При сборке автомобиля количество сборочных операций довольно велико, поэтому длина такого конвейера составляет сотни метров, а с учетом конвейеров сборки отдельных узлов автомобиля– многие
километры. Конечно, внутри |
|
производственных |
зданий |
|
такие |
конвей |
||
располагается во много рядов и на нескольких уровнях по высоте. В |
то же |
время |
||||||
продолжительность элементарных сборочных операций при |
сборке |
автомобил |
||||||
составляет не более нескольких минут, что позволяет обеспечить малый такт выпуска |
||||||||
изделия. |
(обычно |
с конвейера, менее чем через |
минуту, сходит |
собранный |
||||
автомобиль). |
|
|
|
|
|
|
|
|
При производстве крупногабаритных изделий(электрогенераторов, турбин, |
||||||||
самолетов, судов, |
станков…) применяют поточную стационарную |
сборку. В |
этом |
|||||
случае |
изделия, |
находящиеся |
в |
различных стадиях |
сборки, |
располагаются |
неподвижно, на специальных стапелях, а специализированные рабочие места (бригады рабочих с соответствующим оборудованием) перемещаются от изделия к изделию, производя соответствующие сборочные операции.
В условиях единичного и мелкосерийного производства такие виды сборки экономически неоправданы и сборка обычно выполняется высококвалифицированных специалистов, производящих все действия по сборке, регулировке и требуемым испытаниям. При этом трудоемкость сборки продолжительность существенно выше. Так постройка подводной лодки п индивидуальному проекту может занимать до нескольких лет. Во время же второй мировой войны поточная сборка подводных лодок позволяла Германии выпускать
одну подводную лодку в день, в США же производилось в день до нескольких судов |
|
|
водоизмещением 10000т. |
|
|
Сборка заключается в соединении сопрягаемых сборочных единиц и деталей |
|
|
путем приведения в соприкосновение основных баз– сопрягаемых поверхностей. |
|
|
Такие поверхности определяют положение деталей относительно |
друг, |
др |
выполняются с наибольшей точностью и определяют во многом качество машины. |
|
|
Так суппорт токарного станка устанавливается на направляющих |
поверхностя |
|
станины и может перемещаться по ним в одном направлении. От точности этих |
|
|
поверхностей станины будет зависеть точность(прямолинейность) перемещения |
|
|
суппорта – одна из важнейших характеристик качества станка. |
|
|
Впроцессе сборки детали соединяется неподвижно или подвижно относительно друг друга. Такие соединения могут быть разъемными, когда соединение можно разобрать, например, для замены детали, узла (соединения по подвижным и переходным посадкам, резьбовые) и неразъемными, когда разборка невозможна без разрушения какого либо элемента (заклепочные, сварные, клеевые…).
Впроцессе сборки требуется производить ряд специфических операций, которые
требуют |
затрат |
энергии |
и |
имеют |
определенную |
временную |
протяжен, |
||||
уменьшение которой, также как и при обработке деталей, |
наталкивается на |
||||||||||
физические ограничение. |
|
|
|
|
|
|
|
|
|||
Конечно время завертывания винта можно уменьшить, повысив скорость вращения |
|||||||||||
специального |
|
инструмента, |
но |
возникающие |
динамические |
нагрузки, при |
|||||
определенной |
скорости, приведут |
к |
разрушению |
либо |
|
, винталибо |
|
резьбы. |
|||
Автомобилистам |
|
известно, что время завинчивания |
винта |
для крепления колеса |
вручную доходит до 1 минуты, с применением же специального механизированного инструмента на автомобильном заводе время завинчивания всех четырех винтов не превышает 1 секунды, т.е. уменьшено до предела.
Время же реализации таких соединений как сварное, клеевое определяются особенностями протекания теплофизических, металлургических, химических процессов.
Сложность современных машин (количество деталей самолета, судна может достигать нескольких миллионов) определяла бы очень большую продолжительность процесса последовательной сборки деталь за деталью.
Поэтому сборку ведут параллельно во времени собирая узлы изделия, группы деталей, которые монтируют на базовую деталь(или узел). Так собранная турбина
устанавливается |
в |
корпус |
корабля, причем |
одновременнов |
корпус |
могут |
монтироваться и управляющая аппаратура, вооружение (пушки, ракетные установки и |
|
|||||
т.д.). В корпус |
самолета(планер) устанавливается |
собранный двигатель, который |
|
|||
обычно и производится даже на другом предприятии. |
|
|
|
|||
Узел машины это сборочная единица, которая имеет самостоятельные функции, |
|
|||||
которые могут быть испытаны вне машины. Например, топливный насос, масляный |
|
|||||
фильтр и т.д. В соответствии с этим узлы могут быть унифицированы, производиться |
|
|||||
самостоятельно |
и |
применяться |
в различных |
машинах. Сборочные |
единицы, |
называемые группами, обычно самостоятельных функций не имеют и выделяются из общей сборки по принципу удобства соединения деталей в группу в отдельно процессе, с целью сокращения общего времени сборки машины.
Для построения технологического процесса сборки технологами производится анализ конструкции машины для выявления составляющих ее, деталейузлов, возможности вычленения групп деталей сборка которых возможна отдельно. Конечно, при проектировании машины конструктор должен уделять внимание технологичности машины, возможности сборки ее в параллельных во времени процессах. Если машина
спроектирована неправильно, то никакие усилия технолога по оптимизац технологии ее изготовления не приведут к положительным результатам.
Поэтому конструктор при проектировании машины должен руководствоваться определенными стандартными правилами.
Так требования к составу сборочной единицы предполагают:
-расчленеие ее на рационалтьное число частей с учетом принципа агрегатирования;
-виды используемых соединений деталей и узлов должны позволять автоматизацию или механизацию сборочных работ;
-сборка изделия не должна предполагать применения сложного технологического оснащения;
- конструкция сборочной единицы должна предусматривать базовую |
составную |
|||
часть, которая является основой для расположения других составных частей; , и |
||||
т.д. |
|
|
|
|
Среди |
многих |
требований, обеспечивающих |
технологичность |
машины, |
наибольшее значение имеет требование взаимозаменяемости всех ее узлов и деталей. Принцип взаимозаменяемости, закладываемый при проектировании искусственных объектов, не используется природой. Как известно, каждый природный организм
уникален |
и приходится предпринимать |
специальные усилия в случае замены |
отдельных |
частей живых организмов. На |
первом этапе развития машинного |
производства, вплоть до начала20-го века многие машины создавались в процессе пригонки отдельных деталей друг к другу. Например, размеры шеек вала задавались в виде номинальных. Без регламентации допуска на изготовление, а размер подшипниковой втулки задавался с требованием выполнить его по полученной шейке вала с определенным зазором. В этих условиях изготовить подшипниковую втулку можно было только после изготовления вала. Это увеличивало цикл изготовления машины и не позволяло производить ее ремонт с использованием запасных частей. Хотя принцип взаимозаменяемости был известен со средних ,векови даже был внедрен при производстве огнестрельного оружия еще по указу Петра1, появление первых стандартов и его широкое применение относится именно к началу 20-го века.
Несмотря на кажущуюся эффективность взаимозаменяемости применение этого принципа имеет ряд ограничений, так как в ряде случаев значительно удорожает изготовление машины. Это связано с тем, что качество функционирования отдельных узлов и машины в целом зависит отклонений замыкающих звеньев, которые определяются допускаемыми отклонениями всех входящих в размерную цепь звеньев
(рис.1.).

Çð |
|
Äð |
|
Äêâ |
Äêí |
Рис.1 Так в роликовом подшипнике качения должен быть зазор Зр между роликами1 и
кольцами 2 и 3, что обеспечивает свободу движения подшипника. В то же время большая величина этого зазора резко снижает качество подшипника, так как приводит к «болтанке» установленного в нем вала, значительным динамическим нагрузкам (ударам), нарушает точность кинематических связей деталей, установленных на валу с другими деталями машины. Но этот зазор возникает в процессе сборки подшипника и зависит от точности изготовления его деталей, причем максимальная и минимальная,
возможная величина этого зазора равны: |
|
|
|
||
Зр макс = |
(Дкн макс – Дкв мин – Др мин)/2 |
|
|
||
Зр мин = |
(Дкн мин - Дкв макс – Др макс)/2 |
|
|
||
Для повышения качества подшипников колебания зазора стремяться свести к |
|||||
минимуму, но это требует чрезвычайно точного выполнения всех его деталей, что |
|||||
привело бы к значительному(на порядки) его удорожанию. Поэтому, даже в этом |
|||||
простейшем |
случае, от |
принципа |
полной |
взаимозаменяемости |
приходит |
отказываться и применять так называемую селективную(с использованием отбора) сборку. В этом случае допуски на изготовление отдельных деталей можно расширить, но потом, перед сборкой детали сортируют на отдельные группы, подбирая в этих группах истинные размеры так, чтобы при сборке получить минимальные колебания зазоров в подшипниках. Естественно, что часть (по теории вероятности очень малая)
деталей не найдет себе применения, но эти потери с лихвой окупятся за счет снижения точности обработки отдельных элементов.
В реальных машинах размерные цепи могут состоять из десятков взаимосвязанных размеров и полная взаимозаменяемость, часто не только экономически не оправдана, а даже невозможна. Поэтому, на практике, при сборке машин применяют не только метод подбора, но и метод пригонки, когда отдельные элементы обрабатывают«по месту» с учетом требуемых размеров замыкающего звена.
Методы достижения точности замыкающих размеров размерных и кинематических цепей при сборке машин в соответствии со стандартами подразделяются:
-метод полной взаимозаменяемости, основанный на расчете размеров замыкающего звена по максимальным и минимальным допустимым размерам составляющих размерную цепь звеньев(метод макимум минимум). Этот м етод обеспечивает полную взаимозаменяемость, но требует довольно точного выполнения размеров составляющих звеньев (деталей) и применим в массовом и крупносерийном производстве, когда число размеров, входящих в размерную цепь невелико.
-При методе неполной взаимозаменяемосьти допуски на размеры составляющих
звеньев расширяют (чтобы удешевить производство деталей), По теории вероятностей отклонения размеров составляющих звеньев(реальных деталей) на
практике при сборке могут компенсировать друг друга(детали с отклонениями в большую сторону с деталями имеющими отклонения в меньшую сторону. Кроме того, размеры с отклонениями близкими к центру поля допуска встречаютс значительно чаще, чем с крайними предельными отклонениями. Такой принцип обеспечения взаимозаменяемости рационально применять в серийном и массовом
|
производстве, при сложных многозвенных размерных цепях. |
|
|
|
|||||||
- |
Метод |
групповой |
взаимозаменяемости |
применяют |
при создании соединени |
||||||
|
высокой точности, когда полная взаимозаменяемость либо недостижима, либо |
||||||||||
|
связана с чрезвычайно большими затратами. В этом случае детали изготавливают |
||||||||||
|
по расширенным допускам, а потом сортируют на группы(например, при |
||||||||||
|
производстве подшипников качения). Такая сборка целесообразна в массовом и |
||||||||||
|
крупносерийном производстве. |
|
|
|
|
|
|
|
|||
- |
Сборка |
методом |
пригонки |
трудоемка |
и |
применяется |
в |
единичном |
|||
|
мелкосерийном |
производстве. Метод |
регулирования |
снижает |
|
трудоемкость |
|||||
|
пригонки и требует применения в конструкции специальных |
регулирующи |
|||||||||
|
устройств, которые могут несколько усложнять конструкцию машины. |
|
|
Машина, состоящая из множества деталей, которые группируются в узлы, подузлы, группы деталей может быть собрана множеством способов, плоть до последовательной сборки «деталь за деталью».
Выбор же оптимального технологического процесса является сложной задачей, для решения которой приходится применять многие математические методы(линейное и нелинейное программирование, теорию массового обслуживания и .т)..д Причем оптимизация технологии сборки требует построения целевой функции в качестве
которой |
может |
использоваться |
минимальная |
себестоимость |
, издврелиямя |
|
производства изделия или различные комбинации этих функций. |
|
|
||||
При построении технологического процесса сборки машины используется ряд |
||||||
практических правил, суммирующих накопленный производственный опыт. Общая |
||||||
сборка |
машины |
начинается с |
установки базирующей |
детали |
или базирую |
сборочной единицы машины, роль которой обычно выполняет корпусная деталь. Это может быть рама, станина, корпус, основание и т.д.
Базирующую деталь устанавливают или закрепляют в удобном для сборки положении. Иногда эту деталь закрепляют в специальном приспособлении, которое либо увеличивает жесткость детали, либо позволяет ее поворачивать или перемещать требуемым при сборке способом.
При поточной подвижной сборки это приспособление, зачастую, перемещается вместе с изделием до завершения процесса сборки. Иногда же оно позволяет закреплять изделие до окончания процесса сборки и перемещать собранное изделие в рабочую среду (судостроительный стапель).
При сборке отдельных узлов также выявляется базовая деталь, которую принимают за основу при сборке узла.
При разработке процесса сборки необходимо учитывать доступность места сборки, поэтому, в первую очередь, устанавливают узлы и детали, минимально затрудняющие установку последующих узлов и деталей. При этом необходимо учитывать возможность размещения монтажного инструмента.

Следует подчеркнуть, что несмотря на широкие возможности комбинаторики в выборе технологического процесса сборки машины, возможности качественной, производительной сборки закладываются на стадии проектирования конструктором.
Разработанную последовательность сборки машины изображают в вид графической схемы сборки(рис.2). На схему общей сборки наносятся условные обозначения деталей и сборочных единиц, поступающих на общую сборку. Схема наглядно показывает в какой последовательности на базовую деталь устанавливаются узлы и детали. Нарушение последовательности, предусмотренной этой схемой недопустимо.
Çîíà |
|
|
|
|
Деталей |
|
003 |
|
|
|
|
007 |
018 |
001 |
|
|
004 |
012 |
005 |
|
|
|
||
|
|
008 |
011 |
|
Групп |
|
01.002 |
|
|
|
|
|
|
|
Узлов |
Корпус |
00.01.01 |
|
00.02.02 |
|
|
|
||
Машины |
|
|
|
Машина |
|
|
|
|
Рис.2.1
Кажется очевидным, что разборку машины можно произвести в обратном порядке, однако в процессе сборки могут применяться неразъемные соединения. Целью же разборки может быть дефектация машины после испытаний, упаковка для отправки заказчику, в тех случаях, когда разобранная машина более транспортабельна, ремонт. Поэтому для разборки машины составляются специальные схемы, соответствующие целям разборки.
Такое схематическое представление технологического процесса сборки отличается
наглядностью ,и зная продолжительность |
и стоимость |
выполнения отдельных |
операций сборки, можно легко оценить время сборки машины и стоимость процесса. |
||
При определении времени выполнения отдельных операций сборки, производимых |
||
с применением ручного труда, используются |
статистические |
экспериментальные |
оценки. При этом , конечно, определение норм времени должно производиться с учетом средних возможностей слесарей сборщиков.
|
Трудоемкость процессов сборки обуславливает разработку средств ее механизации |
||||||||
и |
автоматизации. |
В |
настоящее |
время, особенно |
в |
условиях |
массового |
||
крупносерийного |
производства |
широко |
применяются |
промышленные |
, робо |
||||
позволяющие в |
ряде |
случаев |
полностью |
освободить |
человека |
от |
выполн |
сборочных |
операций. |
Возможности |
промышленных |
роботов, хотя |
и |
|||
совершенствуются с каждым годом, но до настоящего времени значительно уступают |
||||||||
возможностям человека. Поэтому изделия для автоматической сборки, зачастую, |
||||||||
проектируют, |
учитывая |
достигнутые |
возможности |
автоматизации |
сборочны |
|||
процессов. Так, многие резьбовые соединения оказалось целесообразным переводить |
||||||||
на сварные, |
клеевые, |
заклепочные, |
которые значительно проще выполняются |
|||||
автоматами. |
В то |
же |
время |
ремонтопригодность |
таких |
изделий |
значител |
|
снижается. |
|
|
|
|
|
|
|
|
Многие знают, что в настоящее время при ремонте бытовой техники, оказывается рациональным заменять целые агрегаты, ремонт которых либо невозможен, либо экономически неоправдан.
Высокий уровень автоматизации сборочных операций достигнут в настоящее время только в условиях массового и крупносерийного производства, хотя требования рынка определяют необходимость выпуска изделий максимально удовлетворяющих индивидуальным требованиям потребителя. Так известно, что обладание людьми одинаковыми вещами, вызывает чувство некоторого дискомфорта. Производство же отличающихся друг от друга вещей в условиях поточного производства существенно
усложняет |
технологические |
задачи. Первые |
попытки, решить |
эту |
проблему, |
|||
предприняты на заводах, производящих автомобили Мерседес. В настоящее время их |
||||||||
собирают в условиях максимально автоматизированной |
поточной , сбпорки |
|||||||
индивидуальным заказам, когда входящие в сборку узлы могут варьироваться исходя |
||||||||
из требований заказчика. Так определенный кузов может оснащаться теми или иными |
||||||||
сидениями, |
радиоэлектронным |
оборудованием |
и . Это.д |
требует |
решения |
|||
сложнейших |
задач |
логистики, которое |
стало |
возможным |
при |
применени |
современных средств вычислительной техники.
Вопросы для самопроверки:
1.Виды организационных форм процессов сборки машин.
2.На какие элементы может разделяться конструкция в процессе ее изготовления?
3.Какие виды соединений применяются при сборке машин?
4.В каком типе производства рационально применять поточную стационарную сборку?
5. Какие методы |
достижения |
точности |
замыкающих |
размеров |
размерных |
кинематических цепей Вы знаете? |
|
|
|
|
6.В каких случаях не рационально использовать метод полной взаимозаменяемости?
7.Перечислите методы снижения трудоемкости процессов сборки машин.
Образец карты тестового контроля:
1.Какие технологии применяются при сборке машин? а). Свинчивание, склеивание, сварка.
б). Сверление, долбление, притирка.
в). Пригонка, опиливание, шабрение, распиливание.
2.В каких случаях производят сборку с пригонкой деталей друг по другу? А). При изготовлении особо точных машин и приборов.
Б) При изготовлении крупногабаритных конструкций. В) При изготовлении оптических приборов.
3. Основы автоматизации машиностроительного производства
Цели автоматизации:
Социальные - высвободить человека от тяжелого, физического, не творческого труда, от труда разрушительно влияющего на здоровье. Следует
отметить, что список профессий, признанных вредными для здоровья, постоянно расширяется. Например, новые современные методы обработки, такие как электронно-лучевая, ионная, плазменная, лазерная связаны с вредными для здоровья излучениями.
Экономические - увеличение производительности и, как следствие, снижение себестоимости. Ускорение выпуска новой продукции, повышении ее качества и получения преимуществ на рынке.
Автомат - устройство выполняющее по заданной программе без участия человек все действия в процессах получения, преобразования, передачи и использования материалов, энергии и информации.
Автоматизация - применение технических средств, экономико-математических методов и систем управления, освобождающих человека от непосредственного участия в процессах получения, преобразования, передачи и использования материалов, энергии и информации.
3.1.Механические автоматы - машины, в которых все действия, в том числе по управлению, выполняются за счет механической энергии движения частей.
Механические автоматы известны много столетий, примером их являются механические часы, различные механические музыкальные устройства ( шарманка, музыкальные шкатулки,...). Развертывание
массового производства товаров потребления в период первой промышленн революции впервые поставило вопрос о применении технологических механических автоматов, первыми из которых стали прядильные и ткацкие станки. Их применение позволило резко повысить производительность труда при производстве тканей.
Естественно, этот опыт пригодился, когда потребовалось производить машины в массовом количестве. Первым предметом потребления, требующим огромных затрат труда, но выпускаемым в массовом

количестве, явился автомобиль.
Надо отметить, что заслуга Генри Форда не только в разработке конструкций
автомобиля, в чем он не был первым, а именно в обосновании его массового применения. До него автомобиль рассматривался не более как забавная игрушка.
При производстве автомобиля применяются тысячи разнообразных процессов обработки, поэтому задача автоматизации значительно расширилась и усложнилась. Однако уже на заводах Форда применялись первые обрабатывающие токарные автоматы.
(Высокую производительность при массовом выпуске автомобиля обеспечивали за счет применения, также предложенной Фордом, поточной сборки.)
Механический автомат (любой) имеет определенную структуру и состоит: силовой привод – программатор - передаточные механизмы - инструмент
В настоящее время в качестве силовогопривода используется в основном электропривод ( ранее - энергия ветра, воды, пара,...).
Современное развитие электропривода позволяет получать компактные преобразователи
электрической энергии в механическую, |
легко дозировать энергию, регулировать |
|||
параметры движения (скорость). |
|
|
|
|
К недостаткам электропривода |
следует отнестипростоту |
получения |
только |
|
вращательного движения, хотя для |
технологических целей требуется широкий |
спектр |
видов движения инструмента относительно обрабатываемой заготовки.
В качестве инструмента используются режущий инструмент, инструмент для обработки
давлением, и другие типы инструмента как, например, в вязальной машине (специальные
иглы).
Разнообразие движений инструмента в различных технологических автоматах требует применения специальных механизмов для преобразования вращательного движения
силового привода в возвратно-поступательное, возвратно-вращательное, поступательное и другие виды механического движения. Известны тысячи видов таких механизмов, однако
широкое применение в механических автоматах нашли только некоторые из них:
кулисный механизм, кривошипный, кулачковый, мальтийский, храповой и др.
Для преобразования параметров движения используются также гид-равлический и
пневматические приводы, позволяющие получать поступательное движение с плавно
регулируемыми параметрами.

Но воздействие на обьект производства |
инструмент должен производить в строго |
||||
заданной |
последовательности. Для |
этого |
служит |
механический |
программат, |
определяющий время работы того или иного механизма, а иногда и характер его движения.
Электромеханические автоматы - отличаются от механических тем, что управление осуществляется последовательно-параллельным распределением электрических сигналов. Преимущество их определяется тем, что электроэнергию значительно проще передавать в заданную
точку пространства, чем механическую энергию, устройства переключения могут быть
более компактные. Однако каждый исполнительный механизм при этом получает отдельный электропривод, что может существенно удорожать конструкцию.
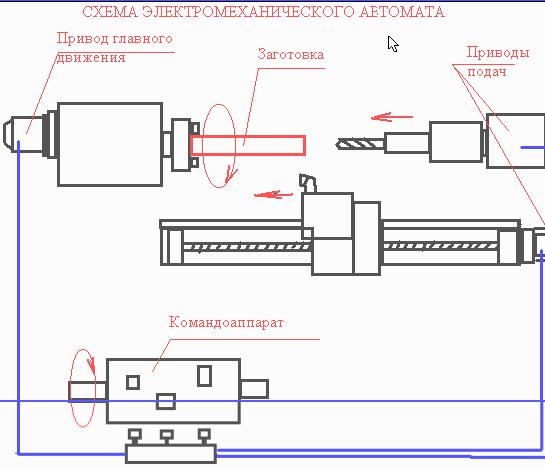
Как это не парадоксально, механический технологический автомат, освободив человека |
|
|||||||
от рутинного труда, оставил ему наиболее не творческую работу по загрузке. Сложность |
|
|||||||
алгоритмизации |
этой |
работы значительно |
сдерживала применение |
механически |
||||
автоматов в технологии. |
|
|
|
|
|
|
|
|
Для решения этой проблемы были предложены многие оригинальные |
|
|
|
|||||
решения: |
|
|
|
|
|
|
|
|
- применение групповой заготовки (пруток, лента). |
|
|
|
|
||||
-автоматизированные загрузочные устройства различного вида - |
|
|
|
|||||
бункера, позволяющие ориентировать и подавать на обработку изделия. |
|
|
||||||
Применение технологических автоматов, выполняющих отдельную |
|
|
|
|||||
технологическую |
операцию |
оказывается |
не |
выгодным, если не автоматизируются |
||||
остальные операции. Поэтому МА обычно объединяют в автоматические линии, состоящие |
|
|||||||
из отдельных механических автоматов, связанных автоматическими системами передачи |
||||||||
заготовок. |
|
|
|
|
|
|
|
|
АЛ - это |
совокупность |
технологического |
оборудования, |
установленного |
в |
|||
последовательности |
технологического |
процесса, соединенного |
автоматическими |
|||||
транспортными и загрузочно-разгрузочными |
|
|
|
|
|
|||
устройствами и одной общей системой управления. |
|
|
|
|
||||
Автоматические |
линии |
такого |
типа создаются |
для производства |
конкретных |
видов |
продукции и их конструкция (траектория движения инструмента, параметры этих движений,
держатели инструмента и заготовок) соответствуют технологии и конструкции данного конкретного изделия.
При изменении характера выпускаемой продукции обычно необходимо построение новой
линии. |
Так как |
капитальные |
затраты при этом очень высоки, то |
такие автоматические |
||
линии |
применяются только |
для выпуска |
изделий |
массового |
применения(подшипники |
|
качения, сигареты, бутылки, продукты питания и т.д.). |
|
|
||||
Теоретически |
производительность АЛ |
может |
быть беспредельна, но ограничения |
динамики движения механизмов не позволяют ее сделать сколь угодно большой. Кроме

того, существуют ограничения и самих технологических процессов. Так резец не может сколь угодно быстро двигаться относительно заготовки.
Наибольшую производительность, там, где нет существенных ограничений самого метода обработки, обеспечивают роторные линии, в которых транспортное непрерывное
движение заготовки совмещено с ее обработкой.
Контрольные вопросы:
1.Что определяет время обработки изделия на механическом автомате?
2.Почему автоматические линии из механических автоматов нашли применение только при массовом выпуске изделий?
3.Какую функцию в механическом автомате выполняют передаточные механизмы?
4.Какую функцию в механическом автомате выполняет распределительный вал? 5.Какими факторами ограничена производительность автоматической линии, состоящей
из механических автоматов?
6.Почему роторные автоматические линии обеспечивают значительно большую производительность изготовления?
3.2Станки с цикловым и числовым программным управлением
Внастоящее время до75% машиностроительной продукции выпускается в условиях мелкосерийного и индивидуального производства.
Это различное технологическое оборудование, изделия авиастроения, судостроения, космическая техника и т.д. Для мелкосерийного производства большое
значение имеет скорость переналадки оборудования, возможности (технологические)такой

переналадки. Первый станок, позволяющий изменять последовательность и характер действий при смене управляющей программы, был изготовлен в 1949 году.
Развитие базы вычислительной техники позволило создать (1958г) реально действующий станок 1К62ПУ. Это была модернизация универсального токарного станка, в
котором ручные органы управления были заменены на силовые следящие приводы.
К настоящему времени конструктивная схема станка сЧПУ, элементная база претерпели существенные изменения.
Система ЧПУ - это совокупность взаимосвязанных и взаимодействующих технических и программных средств, обеспечивающих управление станком.
Ктехническим средствам относятся: приводы главного движения, приводы подач, приводы механизмов смены инструмента изаготовок, элементы электроавтоматики, датчики обратной связи,...
Кпрограммным средствам относятся: управляющие программы,
вычислительные устройства, устройства, формирующие управляющие сигналы для исполнительных механизмов.
Применение станков с ЧПУ целесообразно:
1.При изготовлении деталей малыми партиями, когда отсутствует оснастка для обработки на других станках и изготавливать ее нецелесообразно.
2.При обработке сложных крупногабаритных деталей.
3.При обработке деталей, имеющих незначительные конструктивные отличия (можно у станка производить корректировку программы).
4.Во вредных производствах.
По особенностям управления системы ЧПУ делятся: 1. Устройства с постоянной структурой (NC).

Они создаются для конкретного станка и имеют систему команд, связанную только с конкретным типом оборудования (в настоящее время практически не применяются) (сист.2ТП, Н22,Н33).
2.Устройства с программной реализацией специфики работы оборудования (CNC). Они едины по структуре, более универсальны, а специфика станка записывается в
ППЗУ. |
|
|
|
3.Устройства для управления группой станков от ЭВМ, находящихся |
|
||
в иерархической связи (DNC). |
|
|
|
4.Устройства, предполагающие |
программирование |
непосредственно у станка |
и |
управление его работой с терминала. (HNC) |
|
|
|
По способу задания движения рабочих органов оборудование ЧПУ |
|
||
бывает: ПОЗИЦИОННЫМ, |
КОНТУРНЫМ, |
КОМБИНИРОВАННЫМ |
и |
АДАПТИВНЫМ.
При позиционном программируется только конечное положение рабочих органов системы, а траектория их перемещения непрограммируется и обеспечивается конструкцией системы. Скорость же перемещения обычно максимально возможная, по конструктивным ограничениям, или задается постоянной.
Такое управление называют прямоугольным ,и несмотря на его простоту, оно имеет достаточно широкое распространение.
Контурное управление позволяет программировать перемещение по нескольким
координатам, при функциональной связи этих координат между собой. Увязка перемещения по различным координатам позволяет программировать перемещени
инструмента по определенной траектории, требуемой технологической задачей.
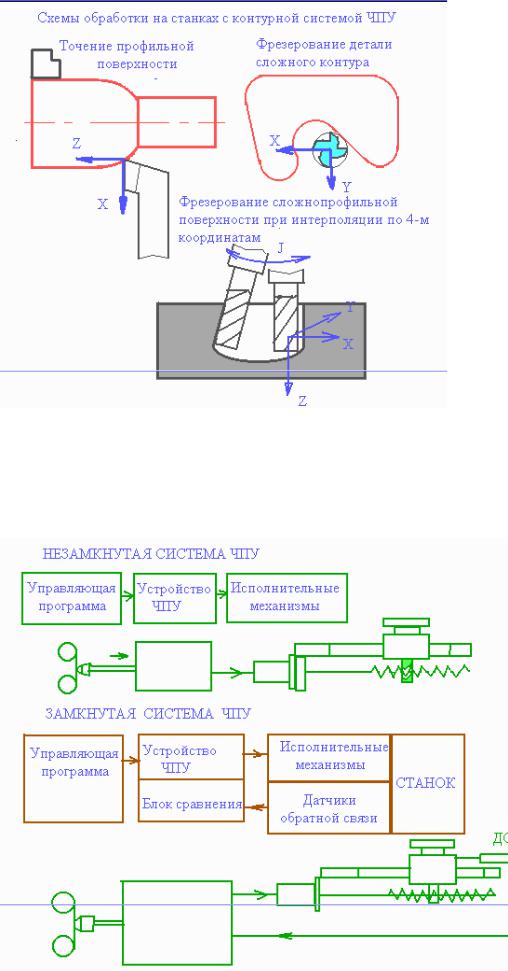
Для управления станками в серийном производстве применяют цикловое управление,
имеющее много общего с прямоугольнымЧПУ, но отличающееся тем, что величина
перемещения рабочих органов задается настройкой путевых выключателей, упоров, барабанов и т.д.
Такие системы требуют большего времени на настройку при переходе на выпуск нового
изделия и их применение оправдано в серийном производстве. Различают замкнутые и незамкнутые системы ЧПУ
Незамкнутые системы применяются в простейших станках, имеют
большие погрешности перемещения рабочих органов (за счет люфтов,

накопления ошибок).
Управляющие программы для станков с ЧПУ
Информация о порядке обработки изделия на станке вводится по кадрам. КАДР - это часть управляющей программы, вводимая и обрабатываемая как единое целое и
содержащая не менее одной команды.
В каждом кадре записывается только тачасть программы, которая изменяется по отношению к предыдущему кадру.
Кадр состоит из слов, определяющих назначение следующих за ними данных.
Например:
N3 - порядковый номер кадра
G02 - подготовительная функция
(G01 - перемещение по прямой к точке
G02,G03 - круговая интерполяция по часовой или против)
X- Координаты конеченой точки перемещения по осям,
Y- ( например, X+037540 (375,4мм)
Z-
I - координаты центра дуги при круговой интерполяции
J-
K-
F4 - код подачи (например, F0060 (60мм/мин)) S2 - код частоты вращения шпинделя
T2 - номер инструмента
M2 - вспомогательная функция (смена инструмента, смена стола, включение охлаждения, зажим заготовки ...).
L3 -ввод и отмена коррекции геометрической информации.
LF - конец кадра.
Чтобы составить программу перемещения рабочих органов станка надо связать с ним определенную систему координат. Ось Z выбирается параллельно оси главного шпинделя станка, ось X всегда горизонтальна. При составлении программы пользуются понятием нулевой, исходной и фиксированной точки .

Подготовка управляющей программы включает:
1.Анализ чертежа детали и выбор заготовки.
2.Выбор станка по его технологическим возможностям(размеры, возможности
интерполяции , количество инструментов и т.д.).
3.Разработка технологического процесса изготовления детали, выбор режущего инструмента и режимов резания.
4.Выбор системы координат детали и исходной точки для инструмента. 5.Выбор способа крепления заготовки на станке.
6.Простановка опорных точек, построение и расчет перемещения инструмента.
7.Кодирование информации
8.Запись программы на программоноситель, ее редактирование и отладка.
Применение станков с ЧПУ значительно обострило проблему использования человека в
производственных условиях. Выполнение всех действий по изготовлению детали станком в автоматическом режиме
оставило человеку наиболее тяжелую и не творческую работу установкепо и снятию заготовок. Поэтому, одновременно с развитием станочных систем с ЧПУ, велись работы по созданию систем способных заменить человека при выполнении специфических действий, требующих применения "РУЧНОГО" труда.
Фрезерный станок и многооперационный станок (обрабатывающий центр) с числовым программным управлением
3.3 Промышленные роботы
Промышленный робот (ПР) это механический манипулятор с прог-
раммным управлением.
Манипулятор - механическое устройство, имитирующее или заменяющее действия человеческих рук на обьект производства.
Промышленные роботы подразделяются на технологические (изме-

няющие свойства обьекта) и транспортные.
Технологический робот производит сварку, транспортный робот перемещает заготовки в
зону обработки.
По грузоподьемности подразделяются на: Масса обьекта
сверхлегкие |
до 1 кг |
легкие |
1 - 10 кг |
средние |
10 -100 кг |
тяжелые |
1001000 кг |
сверхтяжелые более 1000 кг
Сверхлегкие роботы собирают прибор, тяжелый робот перемещает крупногабаритные заготовки.
ПР подразделяются также по количеству степеней свободы рабочего органа, по системе ЧПУ (замкнутая и незамкнутая, контурная и
позиционная, CNC, DNC, HNC).

Зона обслуживания транспортного робота и траектория перемещения заготовки
Внастоящее время широкое распространение получили транспортные роботы, осуществляющие загрузку технологического оборудование, доставку заготовок со склада и транспортировку деталей на склад. При производстве штамповочных операций транспортные роботы осуществляют подачу заготовок на штамп и снятие их.
Широкое применение получили роботы производящие сварку кузовов автомобилей, их окраску. Роботы применяются при сборке радиоэлектронной аппаратуры, часов и др. приборов.
Всовокупности с технологическим оборудованием с системами ЧПУ промышленные роботы образуют базу для комплексной автоматизации производства.
Роботы сваривают кузова легковых автомобилей и устанавливают деревянные панели на станок для обработки (примеры применения роботов)
Контрольные вопросы:
1.Какие системы ЧПУ позволяют обрабатывать сферические поверхности на токарных станках?
2.Какие системы ЧПУ целесообразно применять на сверлильных станках?
3.По скольки координатам возможна интерполяция при обработке заготовок на токарных станках? - на фрезерных станках?
4.Чем отличаются системы циклового программного управления от
систем ЧПУ?
5.Какие функции выполняют промышленные роботы?
Образец вопросов карты тестового контроля.
1.На каких операциях целесообразно применение систем ЧПУ с контурным управлением?
А). При точении ступенчатых валиков.
Б) . При фрезеровании поверхностей двойной кривизны. В). При обработке отверстий в печатных платах.
2.Какие виды роботов применяются при окраске сложнопрофильных деталей? А). Технологические с контурным управлением.
Б). Крупногабаритные с позиционным управлением. В). Транспортные с контурным управлением.
4.Организация промышленного производства
Организация производственного процесса
4.1 . Производственный процесс и его структура
Производственный процесс представляет собой совокупность всех действий людей и орудий труда, необходимых на данном предприятии для изготовления продукции (ГОСТ 14.005-83).

Технологический |
процесс (ГОСТ |
3.1109-82) является |
частью |
||||
производственного процесса, содержащей целенаправленные действия |
|||||||
по изменению и (или) определению состояния предмета. |
|
|
|||||
Законченная часть техпроцесса , выполняемая на одном рабочем |
|||||||
месте, называется технологической операцией. |
|
|
|||||
Производственный |
процесс |
состоит |
из |
трудов |
|||
автоматических процессов, а также естественных процессов, не |
|||||||
требующих |
, как |
правило, затрат |
труда (например, |
время на |
|||
охлаждение отливок, старение заготовок). |
|
|
|
||||
Имеющая |
на |
практике |
классификация |
производственн |
|||
процессов, |
позволяет |
построить |
код |
производственного |
процесса. |
Макет этого кода представлен на рис. 2.1.
Номер производственного процесса
Признак цеха
Признак характера объекта производства
Признак степени автоматизации производственного процесса
Признак характера выполняемых технологических операций
Признак назначения производственного процесса
Рис. 2.1. Макет кода производственного процесса
Описание макета кода производственных процессов Признак назначения производственных процессов занимает один
первый разряд кода и имеет следующие значения: 1 – основные производственные процессы
2– вспомогательные производственные процессы
3 – обслуживающие производственные процессы
Основные |
производственные |
|
процесуществляютсы |
|||||
непосредственное |
изменение |
формы |
или |
состояния |
матер |
|||
продукции, |
являющейся |
в |
соответствии |
со |
специализа |
|||
предприятия товарной, например, в авиационном производстве– это |
||||||||
процессы |
изготовления |
деталей |
самолета |
и |
сборки из |
|
них , узл |
агрегатов и самолета в целом, на инструментальных заводах– это
изготовление инструмента. |
|
процессы осуществляют |
Вспомогательные |
производственные |
изготовление продукции, как правило, используемой на самом
предприятии, |
для |
обеспечения |
нормального |
функционировани |
||||||
основных |
|
процессов, например, изготовление |
технологической |
|||||||
оснастки , |
средств |
механизации |
и автоматизации |
собственног |
||||||
производства, |
запасных |
|
частей |
для |
|
ремонта |
действую |
|||
оборудования, |
производство |
на предприятии |
всех видов энерги |
|||||||
(электроэнергия, газ, пар, и др.) |
|
процессыобеспечивают |
|
|||||||
Обслуживающие |
|
производственные |
|
|||||||
основные и вспомогательные процессы услугами, необходимыми для |
||||||||||
их нормального функционирования, например, |
транспортные |
и |
||||||||
складские. |
|
|
|
|
|
|
|
|
|
|
Признак |
характера |
выполняемых |
технологических |
опер |
||||||
занимает один второй разряд и имеет следующие значения: |
|
|
||||||||
1 – заготовительные технологические операции |
|
|
|
|||||||
2 – обрабатывающие технологические операции |
|
|
|
|||||||
3 – сборочные технологические операции |
операции осуществляют |
|||||||||
Заготовительные |
|
технологические |
||||||||
изготовление литых, сварных, кованых и других заготовок. |
|
|
||||||||
Обрабатывающие |
|
технологические |
операции осуществляют |
|||||||
обработку резанием, термообработку деталей, гальванопокрытие. |
|
|||||||||
Сборочные |
технологические |
операции осуществляют сборку |
узлов |
и |
||||||
изделий и их упаковку. |
|
|
|
|
|
|
|
|
||
Признак |
степени |
|
автоматизации |
производственного |
проц |
|||||
занимает один третий разряд и имеет следующие значения: |
|
|
||||||||
1 – ручные производственные процессы |
|
|
|
|
||||||
2 – механизированные производственные процессы |
|
|
3 – автоматизированные производственные процессы
4 – автоматические производственные процессы
Ручные производственные процессывыполняются без помощи
механизмов, например слесарные работы, ручная разметка заготовки и другие.
Механизированные производственные процессывыполняются
рабочими с помощью средств, снижающих величину физических нагрузок, например работа на универсальном токарно-винторезном станке.
Автоматизированные производственные процессычастично
выполняются без участия человека , за которым могут остаться только функции загрузки, корректировки, наблюдения, например при работе
на полуавтоматическом станке. |
процессыполностью |
|
Автоматические |
производственные |
высвобождают рабочего от выполнения операций, оставляя за ним функции наблюдения за ходом производства, загрузки заготовок и выгрузки готовых деталей, например при работе на обрабатывающем центре, станке с ЧПУ.
Признак характера объекта производствазанимает один четвертый
знак и имеет следующие значения: 1 – простые процессы 2 – сложные процессы
Простые процессы состоят из последовательно выполняемых
операций, например изготовление одной детали, партии одинаковых деталей, группы разных по конструкции деталей, но имеющих технологическое сходство и обрабатываемых на одном рабочем месте, участке, линии, а также процессы сборки изделия или его .узлов Структура такого процесса(порядок выполнения операций) определена технологией изготовления деталей или сборочных единиц (ДСЕ).
Сложные процессы состоят из последовательно и параллельно
выполняемых операций, например изготовление сборочной единицы
(узла) из |
нескольких |
деталей |
или |
всего , |
изделиянапример |
изготовление изделия с использованием разузлования (См. рис.2.2). |
|||||
Вершины |
определяют изделие, ДСЕ, а |
дуги – |
количество |
вхождений |
деталей в узлы и узлов в изделие. На рис. 2.2. представлено прямое вхождение. Полное вхождение можно посчитать, например вхождение детали 1 в изделие 1 составляет: 10 х 6 х 2 = 120.

2 |
|
|
|
о |
И1 |
|
|
|
|
2 |
|
|
|
|
|
|
|
|
|
|
|
|
|
|
|
1 |
|
|
|
|
|
|
|
|
|
10 |
|
|
|
|
У1 |
о |
|
|
|
о |
|
У2 |
|
|
|
6 |
|
|
|
|
|
|
|
2 |
|
|
||
|
|
|
|
|
|
|
|
|
|
|
||
1 |
|
|
|
|
|
|
|
|
|
4 |
|
|
1 |
|
|
|
|
|
|
|
|
|
5 |
|
|
У3 |
о |
|
У4 |
о |
У5 |
о |
У6 |
о |
|
|
|
|
5 |
|
|
|
|
|
10 |
|
|
||||
|
|
|
|
|
|
|
|
|
|
|
||
10 |
|
|
|
|
|
|
|
|
|
1 |
|
|
о |
|
|
о о |
о |
о |
|
о |
о |
о |
|
|
|
Д1 |
Д2 Д3 |
Д4 |
Д5 |
|
Д6 |
|
Д7 |
Д8 |
|
|
||
Рис. 2.2. Пример разузлования изделия |
|
|
|
|
|
|
|
|||||
Структура |
сложного |
процесса |
|
зависит |
как |
от |
||||||
технологических процессов изготовления и сборки, так и от порядка их |
||||||||||||
выполнения, определяемого конструкцией ДСЕ |
|
|
|
|||||||||
Признак цеха занимает |
два |
разряда, |
пятый и шестой. |
Значения |
берутся из классификатора структурных подразделений конкретного предприятия.
Номер производственного процесса занимает три разряда, седьмой,
восьмой и девятый. Он привязан к конкретному структурному подразделению машиностроительного предприятия. Создается классификатор производственных процессов машиностроительного предприятия в привязке к структурным подразделениям.
4.2. |
Основные |
принципы |
орга |
|
производственного процесса |
|
|
||
|
Основными |
принципами являются: |
дифференциация, |
|
концентрация и интеграция, специализация, |
пропорциональность, |
параллельность, прямоточность, непрерывность, ритмичность, автоматичность, гибкость, электронизация.
Значение и важность этих принципов |
в |
конкретных усло |
||||
производства |
могут |
меняться. В |
связи |
с |
развитием |
|
совершенствованием машиностроительного |
производства |
возникают |
||||
новые принципы или утрачивают силу прежние. |
|
|
|
|||
Принцип |
дифференциации предполагает |
|
разделение |
производственного процесса на отдельные технологические процессы, операции, переходы, приемы, движения. Анализ особенностей каждого элемента частичного процесса позволяет выбрать наилучшие условия для его осуществления, обеспечивающие минимизацию суммарных затрат всех видов ресурсов. Это применительно к обычному оборудованию (станкам).
Принцип концентрации операций и интеграции производственного процесса применяется на современных обрабатывающих центрах и
станках с ЧПУ, роботах. Операции становятся более объемными, сложными на прогрессивном оборудовании в сочетании с бригадным принципом организации труда. На поточных линиях в едином комплексе решаются задачи обработки, сборки транспортировки ДСЕ. Эффективность гибких производственных систем обеспечивается за счет взаимной координации процессов проектирования, изготовления,
транспортирования , контроля, складирования, |
обслуживания |
и |
||||||
управления всей сложной производственной системой. |
|
|
||||||
Принцип специализации основан на ограничении разнообразных |
||||||||
элементов производственного процесса. В частности |
выделяются |
|||||||
группы |
рабочих, |
специализирующихся |
по |
профессиям, что |
||||
способствует росту их квалификации и производительности труда. |
||||||||
Однако |
целесообразная организация |
производства |
в |
некотор |
||||
случаях требует овладения смежными профессиями, чтобы обеспечить |
||||||||
взаимозаменяемость |
рабочих |
в |
процессе |
производства. Иногда |
||||
переключение рабочих с одного вида работ |
на другие |
позвол |
||||||
снизить |
нагрузки, |
вызванные |
монотонностью |
и |
однообразие |
|||
операций. |
Уровень |
специализации |
рабочего |
места |
определяетс |
|||
коэффициентом закрепления |
операций зо К, то |
есть |
количеством |
деталеопераций, выполняемых на рабочем месте за определенный промежуток времени. :
Кзо = nто/ ср ,
где:
nто – число наименований технологических операций, выполняемых за плановый период (например, месяц)
ср - - расчетное число загруженных рабочих мест цеха (участка)
При Кзо = 1 обеспечивается узкая специализация рабочего места и создаются предпосылки для роста производительности труда за счет выработки трудовых навыков рабочих, возможностей технического оснащения труда и т. п.
При закреплении за рабочим местом нескольких деталеопераций или отсутствии постоянного закрепления возникают потери времени при переходе рабочего с одной операции на другую, замедляется выработка трудовых навыков. Специализация производственных участков, цехов, заводов предполагает ограничение номенклатуры деталей изделий, обрабатываемых (или собираемых) в этих производственных подразделениях. Если объем выпуска и трудоемкость детали ил изделия одного наименования обеспечивают полную загрузку рабочих мест, создаются одно-предметные поточные линии, предметнозамкнутые участки или даже специализированные заводы.
Принцип пропорциональности предполагает относительно равную
пропускную |
способность |
всех |
структурных |
подразд, |
|
выполняющих |
основные, вспомогательные |
и |
обслуживающие |
||
процессы. Нарушение этого |
принципа приводит к |
возникновению |
“узких мест” в производстве, или к неполной загрузке рабочих мест, участков, цехов, к снижению эффективности функционирования всего машиностроительного предприятия.
Коэффициент пропорциональности Кпр рассчитывается по формуле:
Кпр = 1 – nуч.уз. / nобщ,
где:
nуч.уз – число участков (или групп оборудования) являющихся “узким местом”;
nобщ – общее число участков (или групп оборудования).
Принцип параллельности заключается в максимально возможном
совмещении отдельных производственных процессов во времени, что может существенно сократить время от запуска в производство до
выпуска |
готовой |
продукции. Параллельность |
достигается |
при |
|||||
обработке одной детали на одном станке несколькими инструментами, |
|||||||||
одновременной |
|
обработкой |
разных |
деталей |
одной |
партии |
|||
нескольких |
|
рабочих |
местах |
или |
одновременном |
выпол |
|||
вспомогательных |
работ (ручных) |
с |
основными (машинными) |
работами. Соблюдение принципа параллельности ведет к сокращению длительности производственного цикла и времени пролеживания ДСЕ.
Принцип прямоточности заключается в обеспечении кратчайшего
пути движения ДСЕ в процессе их производства. Не должно быть возвратных движений объектов производства на участке, в цехе, на
предприятии. Оборудование на участке располагается по х технологического процесса. Применяемся в основном для массового производства.
Принцип непрерывности предполагает сокращение до возможного
минимума перерывов в процессах производства. Перерывы могут возникать по технологическим или по организационным причинам. Перерывы по технологическим причинам необходимо устранять путем
синхронизации |
|
|
технологических |
|
операций. Перерывы |
|
по |
|||
организационным |
|
причинам |
должны |
устраняться |
||||||
совершенствования |
системы |
оперативно-календарного планирования |
||||||||
(ОКП). |
|
|
|
заключается |
в |
выпуске |
|
равных |
||
Принцип |
ритмичности |
|
||||||||
соответствии с планом объемов продукции предприятием, цехом, |
||||||||||
участком, рабочим |
местом |
за |
определенную |
единицу |
време. |
|||||
Ритмичность |
|
позволяет |
|
наиболее |
эффективно |
|
исполь |
|||
производственную мощность предприятия и каждого его структурного |
||||||||||
подразделения. |
|
|
|
|
заключается |
в |
автоматиза |
|||
Принцип |
|
автоматичности |
производственных процессов. Это приводит к увеличению объема
производства, сокращению затрат |
живого |
труда, к |
повышению |
|||
качества работ, замене рабочих обрабатывающими центрами |
||||||
роботами. Уровень автоматизации определяется коэффициентом Ка. |
|
|||||
где: |
Ка = ta / tобщ., |
|
|
|
|
|
|
|
|
|
|
|
|
ta – количество автоматизируемых производственных процессов; |
|
|||||
tобщ – общее количество производственных процессов. |
по |
струк |
||||
Этот |
коэффициент |
может |
считаться |
как |
подразделению, так и в целом по предприятию.
Принцип гибкости обеспечивает эффективную организацию работ,
дает возможность мобильно перейти на выпуск другой продукции,
входящей в производственную программу предприятия, или на выпуск |
|
|||||
новой продукции при освоении ее производства при |
наименьши |
|||||
потерях ресурсов. Наибольшее развитие этот принцип получает там, |
|
|||||
где внедряются САПР КТ, обрабатывающие центры, станки с ЧПУ, |
|
|||||
автоматические |
средства |
контроля, складирования, перемещения |
|
|||
объектов производства. |
|
|
|
|
|
|
Значения |
каждого |
из |
принципов |
меняется |
при |
раз |
производства. Так, раньше наибольшее значение имели принципы, |
||||||
связанные с созданием поточного производства: непрерывность, |
|
|||||
параллельность, |
прямоточность. |
В настоящее |
время все |
большее |

значение приобретают автоматичность и гибкость производственных процессов.
4.3. Производственный цикл и его структура
Производственным |
циклом (ПЦ) |
называется |
промежуток |
времени от начала |
до завершения |
производственного проце. |
Например, производственный цикл изготовления детали– это период от поступления материала в обработку до окончания изготовления детали, а производственный цикл изделия– это период времени от запуска исходного материала и полуфабрикатов в обработку
окончания |
изготовления |
и |
комплектации |
предназначенного |
||
реализации изделия. Структура ПЦ представлена на рис. 2.2. |
|
|||||
Длительность производственного цикла является одной |
||||||
важнейших характеристик уровня организации производства. Расчет |
||||||
длительности |
производственного |
цикла |
имеет |
многоц |
||
назначение. |
Он используется при разработке производственно |
|||||
программы цехов, загрузки рабочих мест и оборудования , для расчета |
||||||
размера незавершенного производства (НЗП) и т. д. |
|
|
||||
Время |
выполнения |
одной |
|
операции, в |
течение |
которого |
изготавливается одна партия одинаковых или несколько различных деталей, называется операционным циклом Топ.
Производственный цикл
|
|
|
|
Время выполнения |
|
|
|
|
|
|
|
|
|
|
Время перерывов |
|
|
|||||||||||||||
|
|
|
|
|
операций |
|
|
|
|
|
|
|
|
|
|
|
|
|
|
|
|
|
|
|
|
|
||||||
|
|
|
|
|
|
|
|
|
|
|
|
|
|
|
|
|
|
|
|
|
|
|
|
|
|
|
|
|
|
|
|
|
|
|
|
|
|
|
|
|
|
|
|
|
|
|
|
|
|
|
|
|
|
|
|
|
|
|
|
|
|
|
|
||
|
Операцион |
|
|
Обслуживаю |
|
|
Естествен |
|
|
|
|
Время |
|
|
|
Время |
|
|
||||||||||||||
|
ный цикл |
|
|
|
щие |
|
|
|
ные |
|
|
|
|
внутри |
|
|
междусмен |
|
||||||||||||||
|
|
|
|
|
|
|
|
|
процессы |
|
|
процессы |
|
|
|
сменных |
|
|
|
ных |
|
|
||||||||||
|
|
|
|
|
|
|
|
|
|
|
|
|
|
|
|
|
|
|
|
перерывов |
|
|
перерывов |
|
||||||||
|
|
|
|
|
|
|
|
|
|
|
|
|
|
|
|
|
|
|
|
|
|
|
|
|
|
|
|
|
|
|
|
|
|
|
|
|
|
|
|
|
|
|
|
|
|
|
|
|
|
|
|
|
|
|
|
|
|
|
|
|
|
|
|||
Технологические операции |
|
|
|
Подготовительнозаключительные работы |
|
|
Контрольные |
|
|
Транспортные |
|
|
Ожидания |
|
|
Комплектования |
|
|
Партионности |
|
|
Обеденные |
|
|
|
Между рабочими сменами |
|
|
Выходные и праздничные дни |
|||
|
|
|
|
|
|
|
|
|
|
|
|
|
|
|
|
|
|
|
|
|
|
|
|
|
|
|
|
|
|
|
|
|
Рис. 2.2. Структура производственного цикла
Производственный цикл сложного процесса– это совокупность простых процессов. Он часто начинается с запуска в производство первой заготовки и заканчивается выпуском готового изделия или сборочной единицы. Производственный цикл включает циклы выполнения технологических Тт, контрольных Тк, транспортных Ттр и складских Тск операций, естественных процессов Те и время перерывов
Тпер:
Тц = f(Тт , Тк , Ттр , Тск , Те , Тпер ).
При организации производственного процесса учитываютс регламентированные перерывы, возникающие внутри рабочих смен и между ними.
Внутрисменные перерывы возникают при обработке деталей партиями из-за их пролеживания в ожидании обработки всей партии перед ее транспортировкой на следующую операцию(перерывы партионности); при несогласованности времени окончания одной и
начала другой операции, выполненных на одном рабочем месте, из-за |
|
||||||
чего |
детали |
или |
партии |
деталей |
пролеживают |
в |
о |
освобождения рабочего места (перерывы ожидания).
Длительность производственного цикла выражается обычно в календарном времени (днях).
Существует три вида построений производственных циклов по времени:
-последовательный;
-параллельный;
-параллельно-последовательный.
При последовательном виде движения обработка партии деталей на каждой последующей операции начинается лишь после того, как вся партия прошла обработку на предыдущей операции.
Определение технологического цикла изготовления партииn на m операциях рассчитывается по следующей формуле:
m
Тц(посл) = n∑ti/Ci , I=1
где:
n – количество деталей в партии; m – число операций обработки;

ti – норма времени i-ой операции;
Ci – количество рабочих мест на i-ой операции.
Рассмотрим пример 1 определения длительности технологического цикла при последовательной обработке деталей
Исходные данные примера 1:: n = 3 детали
m = 4 операции t1 = 10 мин.
t2 = 40 мин.
t3 = 20 мин.
t4 = 10 мин.
Расчет ТЦ при последовательной обработке деталей:
1.nt1/C1 = 3х10/1 = 30 мин.
2.nt2/C1 = 3х10/1 = 120 мин.
3.nt3/C1 = 3х10/1 = 60 мин.
4 .эnt4/C1 = 3х10/1 = 30 мин.
Графическое изображение представления длительности ТЦ при последовательной обработке деталей представлено на рис2.3.
N |
ti |
Ci |
|
|
|
|
|
|
|
|
|
|
|
|
|
Время, мин. |
|
|
|
|
|
|
|
|
|
|
|||||||||
оп |
|
|
|
|
|
|
|
|
|
|
100 |
|
|
|
|
|
|
200 |
|
|
|
|
|
|
300 |
|
|
|
|
||||||
|
|
|
20 |
40 |
60 |
80 |
|
|
120 |
|
|
160 |
|
|
|
220 |
|
260 |
|
|
|
320 |
|
360 |
|||||||||||
|
|
|
|
|
|
|
|
||||||||||||||||||||||||||||
|
|
|
|
|
|
|
|
|
|
|
|
|
|
|
|
|
|
|
|
|
|
|
|
|
|
|
|
|
|
|
|
|
|
|
|
05 |
10 |
1 |
|
|
|
|
|
|
|
|
|
|
|
|
140 |
180 |
240 |
280 |
340 |
|
|
||||||||||||||
|
|
|
30 |
|
|
|
|
|
|
|
|
|
|
|
|
|
|
|
|
|
|
|
|
|
|
|
|
|
|
|
|
|
|
|
|
|
|
|
|
|
|
|
|
|
|
|
|
|
|
|
|
|
|
|
|
|
|
|
|
|
|
|
|
|
|
|
|
|
|
|
|
|
|
|
|
|
|
|
|
|
|
|
|
|
|
|
|
|
|
|
|
|
|
|
|
|
|
|
|
|
|
|
|
|
|
|
|
|
|
|
|
|
|
|
|
|
|
|
|
|
|
|
|
|
|
|
|
|
|
|
|
|
|
|
|
|
|
|
|
|
|
|
|
10 |
40 |
1 |
|
|
|
|
|
|
|
|
|
|
|
|
|
|
|
|
|
|
|
|
|
|
|
|
|
|
|
|
|
|
|
|
|
|
|
|
|
|
|
|
120 |
|
|
|
|
|
|
|
|
|
|
|
|
|
|
|
|
|
|
|
|
|
|
|
|
|
|||
|
|
|
|
|
|
|
|
|
|
|
|
|
|
|
|
|
|
|
|
|
|
|
|
|
|
|
|
|
|
|
|
|
|
|
|
|
|
|
|
|
|
|
|
|
|
|
|
|
|
|
|
|
|
|
|
|
|
|
|
|
|
|
|
|
|
|
|
|
|
|
|
15 |
20 |
1 |
|
|
|
|
|
|
|
|
|
|
|
|
|
|
|
|
|
|
|
|
|
|
|
|
|
|
|
|
|
|
|
|
|
|
|
|
|
|
|
|
|
|
|
|
|
|
|
|
|
|
60 |
|
|
|
|
|
|
|
|
|
|
|
|
|
|
|
|
||
|
|
|
|
|
|
|
|
|
|
|
|
|
|
|
|
|
|
|
|
|
|
|
|
|
|
|
|
|
|
|
|
|
|
|
|
|
|
|
|
|
|
|
|
|
|
|
|
|
|
|
|
|
|
|
|
|
|
|
|
|
|
|
|
|
|
|
|
|
|
|
|
|
|
|
|
|
|
|
|
|
|
|
|
|
|
|
|
|
|
|
|
|
|
|
|
|
|
|
|
|
|
|
|
|
|
|
|
20 |
10 |
1 |
|
|
|
|
|
|
|
|
|
|
|
|
|
|
|
|
|
30 |
|
|
|
|
|
|
|
|
|
|
|
||||
|
|
|
|
|
|
|
|
|
|
|
|
|
|
|
|
|
|
|
|
|
|
|
|
|
|
|
|
|
|
|
|||||
|
|
|
|
|
|
|
|
|
|
|
|
|
|
|
|
|
|
|
|
|
|
|
|
|
|
|
|
|
|
|
|
|
|
|
|
|
|
|
|
|
|
|
|
|
|
|
|
|
|
|
|
|
|
|
|
|
|
|
|
|
|
|
|
|
|
|
|
|
|
|
|
|
|
|
|
|
|
|
|
|
|
|
|
|
|
|
|
|
|
|
|
|
|
|
|
|
|
|
|
|
|
|
|
|
|
|
|
Тц(посл) = 240 мин.
Рис. 2.3. Графическое изображение представления длительности ТЦ при последовательной обработке деталей
Положительные моменты:
-просто организовать производственный процесс;
-оборудование и рабочие работают бесперебойно;
-простой учет.
Отрицательные моменты:
-большая длительность производственного процесса;
-большое незавершенное производство(партионное пролеживание);
Область применения: обработка малыми партиями
Для сокращения длительности производственного цикла можно передачу деталей с одной операции на другую по мере их обработки вести не всей партией, а поштучно либо разделить всю партию на
несколько |
частей и |
передавать |
каждую из них на |
последующ |
операцию |
по мере |
ее обработки |
на предыдущей. Такая |
передача |
деталей практикуется, в частности, при параллельном движении.
При параллельном движении передача предметов труда (деталей) на
последующую операцию осуществляется поштучно, либо транспортной партией сразу после обработки на предыдущей операции. Как видно из графика (рис. 2.4.), в общем случае при переводе деталей с операции на операцию поштучно длительность операционного цикла равна:
m
Тц(пар) = Р∑ti/Ci + (n-p)tmax/Cmax,
i=1
где:
Р- величина транспортной партии (или поштучно), шт;
tmax – время выполнения наиболее продолжительной операции, мин.; Cmax – число рабочих мест на наиболее продолжительной операции.
Рассмотрим пример 2 определения длительности технологического цикла при параллельной обработке деталей
Исходные данные примера 2::
Р = 1;
Cmax = 1;
tmax = 40 мин. n = 3 детали
m = 4 операции t1 = 10 мин.
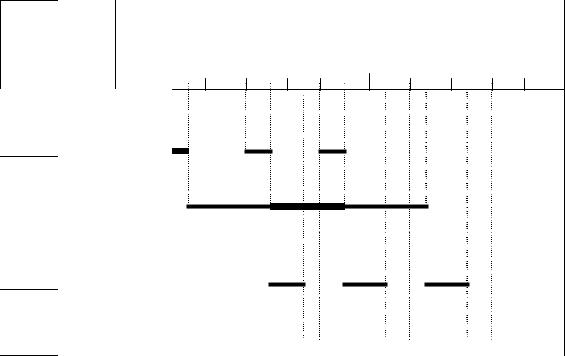
t2 = 40 мин.
t3 = 20 мин.
t4 = 10 мин.
Расчет ТЦ при параллельной обработке деталей:
Тц(парт) = Рt1/c1 + Pt2/C2 + Pt3/C3 + Pt4/C4 + (n-1)t2/Cmax =
= (10 + 40 + 20 + 10) + (3-1)40 = 160 мин.
График параллельной обработки деталей представлен на рис2.4.
N |
ti |
Ci |
|
|
Время, мин. |
|
|
|
||
оп |
|
|
|
|
|
|
|
|
|
|
|
|
20 |
40 |
60 |
80 |
100 |
120 |
140 |
160 |
180 |
05 |
10 |
1 |
|
|
|
|
|
|
|
200 |
|
|
10 |
10 |
|
10 |
|
|
|
|
|
10 |
40 |
1 |
|
|
|
|
|
|
|
|
|
|
40 |
|
40 |
|
|
40 |
|
|
|
15 |
20 |
1 |
|
|
|
|
|
|
|
|
|
|
|
|
20 |
|
20 |
|
20 |
|
|
20 |
10 |
1 |
|
|
|
|
|
|
|
|
10 |
10 |
10 |
|||
|
|
|
|
|
|
Рис. 2.4. График параллельной обработки деталей
Положительные моменты:
-длительность производственного цикла снижается по сравнению
споследовательной обработкой деталей.
Отрицательные моменты:
- простои рабочих мест при условии не равенства или кратности операций (простои на коротких операциях).
Область применения
Применяется в том случае, когда время операций примерно равно или кратно друг другу. Это непрерывно-поточное производство.
При |
параллельно-последовательном |
виде |
движения |
передаются на последующую операцию по мере ох обработке предыдущей – поштучно или транспортной партией, при этом время выполнения смежных операций частично совмещаются та образом, что партия деталей обрабатывается на каждой операции без перерывов.
m-1
Тц(n-n) = Тц(посл) - ∑τi , i=1
где:
τi - частичное перекрытие времени выполнения каждой пар смежных операций, мин.
τi = tmin(n-p) ,
где:
tmin продолжительность менее длительной операц рассматриваемой пары смежных операций
Рассмотрим пример 3 определения длительности технологического цикла при последовательно-параллельной обработке деталей
Исходные данные примера 3:: n = 3 детали
m = 4 операции t1 = 10 мин.
t2 = 40 мин.
t3 = 20 мин.
t4 = 10 мин.
Расчет ТЦ при последовательнопараллельной обработке
деталей:
Τц(n-n) = 240 – [10(3-1) + 20(3-1) + 10(3-1)] = 160 мин.
|
τ1 |
= 10(3-1) = 20; |
|
|
τ2 |
= 20(3-1) = 40; |
|
|
τ3 |
= 10(3-1) = 20; |
|
График |
последовательно-параллельной |
обработки |
|
представлен на рис2.5. |
|

N |
ti |
Ci |
|
|
|
|
|
|
|
|
|
|
|
|
|
|
|
Время, мин. |
|
|
|
|
|
|
|
|
|
|
|||||||
оп |
|
|
|
|
|
|
|
|
|
|
100 |
|
|
|
|
|
|
200 |
|
|
|
|
|
|
300 |
|
|
|
|||||||
|
|
|
20 |
40 |
60 80 |
|
|
|
120 |
160 |
|
|
|
220 |
260 |
|
|
|
|
320 |
360 |
||||||||||||||
|
|
|
|
|
|
|
|
|
|
||||||||||||||||||||||||||
|
|
|
|
|
|
|
|
|
|
|
|
|
|
|
|
|
|
|
|
|
|
|
|
|
|
|
|
|
|
|
|
|
|
|
|
05 |
10 |
1 |
|
|
|
|
|
|
|
|
|
|
|
|
|
140 |
|
|
180 |
|
240 |
|
280 |
340 |
|
||||||||||
|
|
|
|
|
|
|
|
|
|
|
|
|
|
|
|
|
|
|
|
|
|
|
|
|
|
|
|
|
|
|
|
|
|||
|
|
|
30 |
|
|
|
|
|
|
|
|
|
|
|
|
|
|
|
|
|
|
|
|
|
|
|
|
|
|
|
|
|
|
||
|
|
|
|
|
|
|
|
|
|
|
|
|
|
|
|
|
|
|
|
|
|
|
|
|
|
|
|
|
|
|
|
|
|
|
|
|
|
|
|
|
|
|
|
|
|
|
|
|
|
|
|
|
|
|
|
|
|
|
|
|
|
|
|
|
|
|
|
|
|
|
|
|
|
|
20 |
|
|
|
|
|
|
|
|
|
|
|
|
|
|
|
|
|
|
|
|
|
|
|
|
|
|
|
|
|
|
||
10 |
40 |
1 |
|
|
|
|
|
|
|
|
|
|
|
|
|
|
|
|
|
|
|
|
|
|
|
|
|
|
|
|
|
|
|||
|
|
|
|
|
|
|
|
|
|
|
|
|
|
|
|
|
|
|
|
|
|
|
|
|
|
|
|
|
|
|
|
|
|||
|
|
|
|
|
|
120 |
|
40 |
|
|
|
|
|
|
|
|
|
|
|
|
|
|
|
|
|
|
|
|
|
||||||
|
|
|
|
|
|
|
|
|
|
|
|
|
|
|
|
|
|
|
|
|
|
|
|
|
|
|
|
|
|
|
|
|
|
|
|
|
|
|
|
|
|
|
|
|
|
|
|
|
|
|
|
|
|
|
|
|
|
|
|
|
|
|
|
|
|
|
|
|
|
|
|
|
|
|
|
|
|
|
|
|
|
|
|
|
|
|
|
|
|
|
|
|
|
|
|
|
|
|
|
|
|
|
|
|
|
|
|
15 |
20 |
1 |
|
|
|
|
|
|
|
|
|
|
|
|
|
|
|
|
|
|
|
|
|
|
|
|
|
|
|
|
|
|
|
|
|
|
|
|
|
|
|
|
|
|
|
|
60 |
20 |
|
|
|
|
|
|
|
|
|
|
|
|
|
|
|
|
|
||||||
|
|
|
|
|
|
|
|
|
|
|
|
|
|
|
|
|
|
|
|
|
|
|
|
|
|
|
|
|
|
|
|
|
|
|
|
|
|
|
|
|
|
|
|
|
|
|
|
|
|
|
|
|
|
|
|
|
|
|
|
|
|
|
|
|
|
|
|
|
|
|
|
|
|
|
|
|
|
|
|
|
|
|
|
|
|
|
|
|
|
|
|
|
|
|
|
|
|
|
|
|
|
|
|
|
|
|
|
20 |
10 |
1 |
|
|
|
|
|
|
|
|
|
|
|
|
|
30 |
|
|
|
|
|
|
|
|
|
|
|
|
|
|
|
|
|
||
|
|
|
|
|
|
|
|
|
|
|
|
|
|
|
|
|
|
|
|
|
|
|
|
|
|
|
|
|
|
|
|
|
|||
|
|
|
|
|
|
|
|
|
|
|
|
|
|
|
|
|
|
|
|
|
|
|
|
|
|
|
|
|
|
|
|
|
|
|
|
|
|
|
|
|
|
|
|
|
|
|
|
|
|
|
|
|
|
|
|
|
|
|
|
|
|
|
|
|
|
|
|
|
|
|
|
|
|
|
|
|
|
|
|
|
|
|
|
|
|
|
|
|
|
|
|
|
|
|
|
|
|
|
|
|
|
|
|
|
|
|
|
Тц(П-П) = 160 мин.
Рис. 2.5. График последовательно-параллельной обработки деталей Положительные моменты:
-длительность производственного цикла снижается сравнению с последовательной обработкой деталей.
-отсутствуют простои рабочих мест на коротких операциях.
Помимо |
рассмотренных |
составляющих |
для |
определ |
длительности |
производственного |
цикла |
необходимо |
|
межоперационное время и время естественных процессов. |
|
|
Пути сокращения длительности производственного цикла
1.Сокращение времени технологических операций, путем применения прогрессивных техпроцессов и оборудования.
2.Сокращение подготовительно-заключительных работ путем внедрения оптимальных размеров партий.
3. Сокращение простоев путем внедрения - п предупредительного обслуживания рабочих мест.
4. Внедрение АСУ цехом.
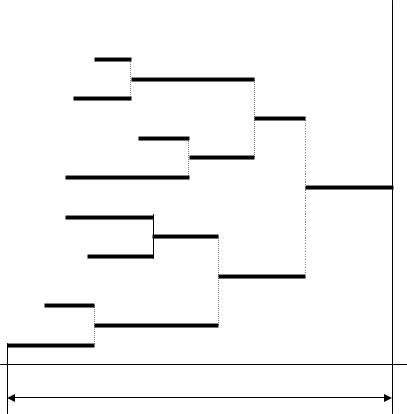
4.4. Производственный цикл сложного процесса
Производственный цикл сложного процесса представляет собой общую продолжительность комплекса координированных во времени простых процессов, входящих в сложный процесс изготовления изделия или партии их. При этом должно использоваться разузлование (См. рис. 2.2), На его основе разрабатывается цикловой график изготовления изделия, пример на рис. 2.6.
Д2 |
У3 |
Д1 |
У1 |
Д4 |
У4 |
Д3 |
И1 |
Д6 |
У5 |
Д5 |
У2 |
Д8 |
У6 |
Д7 |
Ти |
Рис. 2.6. Цикловой график изготовления изделия |
Цикловой график, построенный для условий, когда изготовление деталей и сборка не лимитируются составом оборудования ,цехо участков, т.е. возможна максимальная параллельность выполнения работ. Длительность такого цикла будет минимальной.
Цикл сложного производственного процесса можно сократить как за счет уменьшения циклов простых процессов, так и путем увеличения степени параллельности их выполнения или уменьшения (устранения) перерывов между ними.
Мероприятия по сокращению производственных циклов.
1. Совершенствование конструкций изделий с точки зрени повышения ее технологичности и степени унификации.
2.Совершенствование технологии, внедрение прогрессивных техпроцессов, приводящих к снижению трудоемкости обработки; комплексная механизация, автоматизация, концентрация операций и др.
3.Внедрение современной системы планирования и организации производства.
4.Рациональная планировка рабочих мест в соответствии последовательностью технологических операций.
5.Улучшение обслуживания рабочих мест.
6.Замена естественных процессов соответствующ технологическими операциями, например, индукционной сушкой, искусственным старением отливок, деталей в термопечах.
7.Уплотнение режима работы цехов и предприятия, т.е. переход
на 3-х сменную работу, организация сквозных бригад. |
|
|
|
|
|
|||||
Существуют |
различные |
|
методы |
|
оперативно-кален |
|||||
планирования (ОКП) и управления производством: |
|
|
|
|
|
|||||
Прежде |
всего, разрабатываются |
на |
основании |
производственной |
||||||
программы изготовления изделий– диспетчерский график (подетальная |
|
|||||||||
производственная программа). Производится разузлования изделий, затем в |
|
|||||||||
соответствии с расцеховкой формируется номенклатура, закрепления ДСЕ |
|
|||||||||
за цехами. В соответствии с календарно-плановыми нормативами(КПН), |
|
|||||||||
учитывающими |
размеры |
партий, производственные |
|
циклы |
детали |
|||||
формируется диспетчерский график для каждого цеха на месяц. ПРБ цехов |
|
|||||||||
формируют сменные задания на участки и рабочие места. |
|
|
|
|
|
|||||
Существуют автоматизированные системы планирования и учета |
||||||||||
выполнения сменных заданий. |
|
|
|
|
|
|
|
|
||
Для |
рациональной |
организации |
работы |
|
в |
цехах |
ос |
|||
производства |
|
внедряются |
системы |
планово-предупредите |
обслуживания рабочих мест. Работа по этой системе заключается в следующем:
1) на основании диспетчерских графиков на месяц производят расчет потребностей в:
-материалах;
-технологической оснастке;
-оборудовании;
-основных производственных рабочих;
2)под каждое сменное задание ведется комплектация по рабочим местам:
-технологическим процессом;
-материалом;
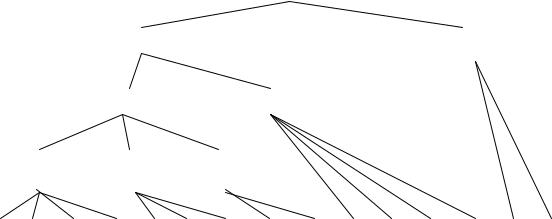
-технологической оснасткой.
4.5.Производственная структура предприятия и цеха
Производственные структуры предприятия можно классифицировать:
1. ПС |
заводов |
с |
полным |
технологическим . |
цикломОни |
имеют |
все |
|
заготовительные, |
обрабатывающие |
и |
сборочные |
цехи |
с |
компл |
||
вспомогательных и обслуживающих подразделений (ЗИЛ, КАМАЗ). |
|
|
2. ПС заводов с неполным технологическим циклом. К ним относятся заводы, получающие заготовки в порядке кооперирования от других заводов посредников.
3. ПС |
заводов (сборочных), выпускающие |
машины |
только |
из |
деталей, |
изготовляемых другими предприятиями, например автосборочные заводы. |
|
|
4.ПС заводов, специализирующиеся на производстве заготовок определённого вида. Они имеют технологическую специализацию (завод “Станколит”).
5.ПС заводов подетальной специализации, производящие отдельные группы деталей или отдельные детали (завод шарикоподшипников).
Производственная |
|
структура |
|
|
машиностроительного |
|
предприяти |
||||||||||||||||||||||||||||||||||||
представлена на рис.2.7. |
|
|
|
|
|
|
|
|
|
|
|
|
|
|
|
|
|
|
|
|
|
|
|||||||||||||||||||||
|
|
|
|
|
|
|
|
|
|
|
|
|
|
|
|
|
|
|
|
|
|
|
|
|
|
|
|
|
|
|
|
|
|
|
|
|
|
|
|
|
|
|
|
|
|
|
|
|
|
|
|
|
|
|
|
|
|
|
|
|
|
|
|
|
Машиностроительное |
|
|
|
|
|
|
|
|
|
|
|
|
||||||||||
|
|
|
|
|
|
|
|
|
|
|
|
|
|
|
|
|
|
|
|
|
|
предприятие |
|
|
|
|
|
|
|
|
|
|
|
|
|
|
|
|
|
||||
|
|
|
|
|
|
|
|
|
|
|
|
|
|
|
|
|
|
|
|
|
|
|
|
|
|
|
|
|
|
|
|
|
|
|
|
|
|
|
|
|
|
|
|
|
|
|
|
|
|
|
|
|
|
|
|
|
|
|
|
|
|
|
|
|
|
|
|
|
|
|
|
|
|
|
|
|
|
|
|
|
|
|
|
|
|
|
|
|
|
|
|
|
|
|
|
|
|
|
Цехи |
|
|
|
|
|
|
|
|
|
|
|
|
|
|
|
|
|
|
|
Хозяйства |
|
|
|
|
|
|||||||
|
|
|
|
|
|
|
|
|
|
|
|
|
|
|
|
|
|
|
|
|
|
|
|
|
|
|
|
|
|
|
|
|
(обслуживающие) |
|
|
|
|
|
|||||
|
|
|
|
|
|
|
|
|
|
|
|
|
|
|
|
|
|
|
|
|
|
|
|
|
|
|
|
|
|
|
|
|
|
|
|
|
|
||||||
|
|
|
|
|
|
|
|
|
|
|
|
|
|
|
|
|
|
|
|
|
|
|
|
|
|
|
|
|
|
|
|
|
|
|
|
|
|
|
|
|
|
|
|
|
|
|
|
|
|
|
|
|
|
Основные |
|
|
|
|
|
|
Вспомогательные |
|
|
|
|
|
|
|
|
|
|
|
|
|
|
|
|
|
|||||||||
|
|
|
|
|
|
|
|
|
|
|
|
|
|
|
|
|
|
|
|
|
|
|
|
|
|
|
|
|
|
|
|
|
|
|
|
|
|
|
|
|
|
|
|
|
|
|
|
|
|
|
|
|
|
|
|
|
|
|
|
|
|
|
|
|
|
|
|
|
|
|
|
|
|
|
|
|
|
|
|
|
|
|
|
|
|
||
|
|
|
Заготови |
|
|
|
Обрабаты |
|
|
Сборочные |
|
|
|
|
|
|
|
|
|
|
|
|
|
|
|
|
|
|
|
|
|||||||||||||
|
|
|
тельные |
|
|
|
вающие |
|
|
|
|
|
|
|
|
|
|
|
|
|
|
|
|
|
|
|
|
|
|
|
|
|
|
|
|
|
|||||||
|
|
|
|
|
|
|
|
|
|
|
|
|
|
|
|
|
|
|
|
|
|
|
|
|
|
|
|
|
|
|
|
|
|
|
|
|
|
|
|
|
|
|
|
|
|
|
|
|
|
|
|
|
|
|
|
|
|
|
|
|
|
|
|
|
|
|
|
|
|
|
|
|
|
|
|
|
|
|
|
|
|
|
|
|
|||
|
Раскройный |
|
Литейный |
|
|
Кузнечно-штамповочный |
|
|
Кузнечно-прессовый |
|
Механический |
|
|
Покрытий |
|
|
|
Термический |
|
Механосборочный |
|
Окончательной сборки |
|
|
Ремонтно-механический |
|
|
Инструментальный |
|
Электроремонтный |
|
Энергетический |
|
|
Транспортное |
|
|
Складское |
|
||||
|
|
|
|
|
|
|
|
|
|
|
|
|
|
|
|
|
|
|
|
|
|
|
|
|
|
|
|
|
|
|
|
|
|
|
|
|
|
|
|
|
|
|
|
Рис. 2.7. Производственная структура машиностроительного предприятия
Рабочее место – это звено производственного участка.
Первичным подразделением структуры производства является рабочее место – часть производственной площади, где рабочий или группа рабочих выполняет отдельные операции по изготовлению продукции или обслуживанию процесса производства, используя при этом соответствующее оборудование и техническую оснастку.
Как было показано ,вышепри рассмотрении вопросов автоматизации производства, рабочее место может обслуживаться и промышленным роботом или
представлять |
ячейку автоматизированного |
производства |
изменяющий свойства или |
контролирующий объект производства тем или иным технологическим методом. |
|||
Выделение такой структурной единицы в |
общей структуре производс |
||
определяется |
невозможностью |
применения |
одновременно |
технологических методов воздействия в силу специфики применяемых физических, химических или других воздействий. Так невозможно одновременно точить и фрезеровать заготовку, штамповать и окрашивать и . т.дВ соответствии со спецификой применяемых технологических методов развивалась и сформировалась
специализация рабочих. Такие профессии как токарь, фрезеровщик, |
формовщик, |
|
|
термист и т.д. стали массовыми. |
|
|
|
Надо отметить, что в кустарном производстве такой специализации на начальной |
|
||
стадии не существовало, и изготовитель хомутов |
производил все действия |
п |
|
обработке дерева, кожи, являясь и столяром и кожевником и шорником. |
|
|
|
Так как на рабочем месте выполняется только часть технологического процесса |
|
||
по изготовлению изделия, для получения готовой продукции |
рабочие |
мест |
|
объединяют в участки, цехи - административно |
обособленные |
подразделения, |
|
выполняющие определенную часть |
|
|
|
Отделом главного технолога составляется планировка участков, структурных подразделений предприятия с указанием в ней наличия и расположения технологического и прочего оборудования. В условиях автоматизированных производств бывают и вертик планировки цехов. Так возникают технические этажи.
Производственная структура цеха
Под производственной структурой цеха понимается сос участков, рабочих мест, служб и формы взаимосвязи между ними.
В зависимости от формы специализации производственные подразделения предприятия организуются по следующим типам производственной структуры: технологическому, предметному и смешанному (предметно-технологическому).
Технологический принцип: оборудование устанавливается на
участках и образуются:
-участок фрезерной обработки;
-участок токарной обработки;
-участок зубонарезных станков и т.д.
Технологическая структура предопределяет четкую технологическую обособленность. Следовательно, оборудование расположено не по ходу технологического процесса, по
группам. Например, на текстильных предприятиях организуются прядильные, ткацкие, отделочные цехи; на металлургических - доменные, сталеплавильные, прокатные. Внутри цехов по принципу технологической однородности создаются участки. При такой структуре цехи и участки выполняют определенные операции на оборудовании, расположенном по однотипным группам. Этот тип производственной структуры упрощает руководство цехом или участком: мастер, отвечающий за группу однородных станков, может всесторонне изучить их; при чрезмерной загрузке одного станка работа может быть передана на любой освободившийся станок.
Технологическая структура позволяет маневрировать расстановкой людей, облегчает перестройку производства с одной номенклатуры изделий на другую, что особенно важно в
условиях рыночной экономики. Но, не смотря на это данный |
вид |
производственной |
|||
структуры, |
считается самым не эффективным, что связано |
с |
неизбежностью |
частых |
|
переналадок оборудования, так как на каждом из них |
обрабатываются разные вид |
||||
продукции, ограничивая этим возможность применения специальных станков, инструментов, |
|||||
приспособлений. Это ведет к пролеживанию деталей в |
ожидании |
своей |
обработ, |
||
удлинению |
цикла производства, снижению фондоотдачи, коэффициента использования |
оборудования по времени, производительности труда. Кроме того, при технологической производственной структуре нет ответственности за качество конечной продукции, так как каждый цех, участок выполняет часть технологического процесса. Возрастают транспортные
перевозки, встречные |
грузопотоки, |
так |
как оборудование расставлено |
не по ход |
|||
технологического процесса. |
|
|
|
|
|
||
Не |
смотря на неэффективность |
такого построения |
производственной |
структуры, ее |
|||
применение неизбежно |
в условиях единичного и мелкосерийного типа производства с |
||||||
большой номенклатурой |
деталей. |
|
|
|
|
|
|
Этот |
принцип |
эффективен |
при |
единичном |
и |
мелкосер |
|
производстве. |
|
|
|
|
|
|
|
|
Предметный принцип: формируются специализированные участки |
||||||
по изготовлению деталей: |
|
|
|
|
|
-участок по изготовлению детали 1;
-участок по изготовлению детали 2.
Предметный тип производственной структуры– самый прогрессивный. Но его применение в чистом виде возможно лишь в крупносерийном и массовом производстве. Все цехи и участки специализируются по предметному принципу, что позволяет расположить оборудование по ходу технологического процесса, применять высокопроизводительные станки, инструменты, штампы, приспособления. Но, прежде всего оборудование в цехах
при использовании предметного принципа располагают в порядке последовательног выполнения технологических операций. Оно здесь разнородно и предназначено для изготовления отдельных деталей или составных частей изделий. Цехи делятся на отдельные
предметные |
участки, например, |
участки по |
изготовлению валов шестерен, поршней. |
Оборудование устанавливается так, чтобы обеспечить движение деталей по кратчайшему |
|||
пути. Детали |
обрабатывают |
партиями, время |
операции на отдельных станках не |
согласовано со временем операций на других.
Детали во время работы хранят у станков и затем транспортируются всей партией. Предметные участки стремятся по возможности осуществить законченный(замкнутый) цикл производства изделий. Такие участки (цехи) называются предметно-замкнутыми. Как правило, они оснащены всем комплексом оборудования, необходимых для изготовления продукции. Замкнутый цикл производства достигается при совмещении в одном и том же цехе разнообразных технологических процессов. По целому ряду причин это не всегда возможно. В машиностроении чаще всего в одном предметном цехе совме
обработочную и сборочную |
стадии производственного процесса. Научно-технический |
||||
прогресс, проявляющийся |
в |
применении |
новых |
ресурсосберегающих |
технологий |
комплексной механизации и автоматизации производства, приводит к территориальному сближению отдельных стадий производственного процесса и к отказу от обособления их в отдельных цехах.
При организации цехов и участков по предметному принципу создаются благоприятные
условия |
для |
применения |
передовых |
методов |
организации |
производства . |
и |
|||
Расстановка оборудования по ходу выполнения технологических операций резко сокращает |
|
|||||||||
путь движения |
обрабатываемых деталей |
и затраты |
времени |
на |
|
их транспортиров. |
||||
Возникают благоприятные предпосылки для организации поточных и автоматических линий, |
|
|||||||||
более полно используется оборудование, рабочие специализируются на выполнение узкого |
|
|||||||||
круга операций, в результате чего повышается их квалификация, улучшается организация |
|
|||||||||
труда, усиливается ответственность за качество выпускаемых изделий. При этом мастер |
|
|||||||||
полностью отвечает за весь цикл |
изготовления |
|
.изделияВсе |
это |
|
ведет к росту |
||||
производительности труда и снижению себестоимости продукции. К недостаткам, присущим |
|
|||||||||
предметным цехам и участкам, можно отнести не полную загрузку |
оборудования |
на |
||||||||
отдельных операциях вследствие небольшого объема работ. |
|
|
|
|
|
|
Предметный |
принцип |
применим |
для |
серийного |
и |
мас |
производства. Такие участки называются предметнозамкнутыми. |
|
|
||||
Смешанная структура характеризуется наличием |
на одном |
и том же предприятии |
|
основных цехов, организованных и по предметному, и по технологическому принципу. Обычно заготовительные цехи организуются по технологическому принципу. Это связано с тем, что в заготовительных цехах мощное производительноеоборудование, на котором производятся заготовки для любого вида продукции, так как в противном случае оно будет недогружено. Обрабатывающие и сборочные цехи создаются по предметномуили смешанному принципу в зависимости от массовости выпускаемой продукции. Этот тип производственной структуры практически применим в производстве любого типа. Она более
распространена |
и |
применяется на |
большей |
части |
машиностроительных |
предприятиях, |
||
легкой промышленности (обувная, швейная), мебельной и некоторых других отраслях. |
||||||||
Достоинства |
и |
недостатки |
рассматриваемого |
типа |
производственной |
стр |
||
соответствуют принципу построения каждого цеха: предметному или технологическому. |
|
|||||||
При выборе |
типа производственной |
структуры следует помнить, |
что |
он |
предопределяется условиями производства. Главными здесь являются, прежде всего, тип производства (массовый, серийный, единичный), специализация предприятия (предметная, технологическая или предметно-технологическая), характер и номенклатура выпускаемой продукции.
При традиционном подходе к определению структуры и организации работы цехов общий объем работ расчленяется на отдельные операции по изготовлению деталей или сборке изделий. Эти работы концентрировались на участках, построенных по технологическому принципу.
Структурная схема организации производственного процесса состоит в ,томчто если участки, сформированные из станков одинакового технологического назначения, то при такой структуре возникают многочисленные прямые и обратные связи технологически специализированными участками для изготовления множества деталей.
При использовании предметно-замкнутой структуры в цехе имеются участки, построенные по принципу подетальной специализации при пересечении внешних и внутренних связей.
Здесь конечные цели производственной системы складываются из целей обособленных участков, выпускающих законченные детали.
Ориентация участков на конечный результат сокращает производственные связи, упрощает |
|
||||||||
порядок планирования и управления ходом работ. Такой метод организации производства |
|
||||||||
называется программно-целевым. |
|
|
|
|
|
|
|||
Сущность |
программно-целевого подхода заключается в формировании |
целей |
и |
||||||
достижений с помощью специальных программ и ресурсов. |
|
|
|
|
|||||
Программно-целевой метод предусматривает такое построение организационных структур |
|
||||||||
систем планирования и управления цехами и участками, которое сопровождается: |
|
|
|
||||||
- целевой |
(подетальный или предметной) специализацией участков, осуществляемой с |
|
|||||||
помощью |
конструкторско-технологического |
классификатора |
деталей |
с |
учетом |
||||
относительной трудоемкости при формировании загрузки каждого участка; |
|
|
|
||||||
- |
унификацией и |
типизацией технологических |
маршрутов |
или процессов за |
сч |
||||
сосредоточения в каждом подразделении таких однородных деталей или изделий, которые |
|
||||||||
бы обеспечивали однонаправленность их движения |
в процессе производства; |
|
|
|
|||||
- |
перестройкой |
производственной структуры |
участков, цехов |
под |
их |
целевую |
|
||
специализацию в соответствии с оптимальным организационно-технологическим маршрутом |
|
||||||||
изготовления деталей, закрепленных за каждым участком. |
|
|
|
|
|
||||
В |
основе формирования производственных |
участков в цехе лежат |
классификация |
||||||
предметов, |
изготовляемых в цехе, и закрепление их за определенными группами рабочих |
|
мест. При этом детали или изделия группируются по конструктивно-технологическим
признакам |
с |
учетом |
параметра, х рактеризующего |
меру |
близости |
конструктивно- |
технологических групп деталей. |
|
|
|
Критерий экономической эффективности и целесообразности выбора того или иного типа
производственной |
структуры |
находит |
выражении |
в |
системе |
технико-экономичес |
показателей. К числу таких показателей относятся: |
|
|
|
-состав производственных цехов и обслуживающих хозяйств, их специализация;
-размеры производственных цехов и обслуживающих хозяйств по численности ППП;
-мощность оборудования, стоимость основных фондов;
-удельный вес разных видов специализации , цеховучастков (предметных, технологических, предметно-технологических);
-соотношение между основными, вспомогательными и обслуживающими подразделениями по количеству оборудования и занимаемых площадей в каждом из них;
-производительность труда и трудоемкость производства;
-длительность производственного цикла изготовления основных видов продукции;
-себестоимость основных видов продукции;
-протяженность транспортных маршрутов;
-грузооборот предприятия общий и по видам транспорта;
-ряд других показателей, учитывающих специфику отрасли.
Пути совершенствования производственной структуры
Основные пути совершенствования производственной структуры подразумевают:
-регулярное изучение достижений в области проектирования и развития производственных структур с целью обеспечения мобильности и адаптивности структуры предприятия нововведениям и новой продукции;
-укрепление и разукрепление предприятий и цехов;
-поиск и реализация более совершенного принципа построения цехов;
-оптимизация числа и размеров производственных подразделений предприятия;
-соблюдение рационального соотношения между основными, вспомогательными и обслуживающими цехами;
-постоянная работа по рационализации планировки предприятий;
-обеспечение пропорциональности между всеми цехами предприятия;
- обеспечение |
соответствия компонентов |
производственной |
структуры |
предприятия |
||
принципу |
пропорциональности |
по |
производственной |
мощности, прогрессивности |
||
технологических |
процессов, уровня |
автоматизации, квалификации |
кадров |
и других |
||
параметров; |
|
|
|
|
|
|
-обеспечение соответствия структуры принципу прямоточности технологических процессов
сцелью сокращения длительности прохождения предметов труда;
- |
обеспечение |
соответствия |
уровня |
качества |
процессов |
в |
(производственной |
структуре предприятия) |
уровню |
качества входа |
системы. Тогда |
и |
качество выхода системы будет высоким; -создание внутри крупного предприятия(объединения, акционерного общества, фирмы)
юридически самостоятельных мелких организаций с предметной или технологической специализацией производства;
-быстрое изменение производственного профиля в условиях рыночной экономики, совершенствование специализации и кооперирования;
-развитие комбинирования производства;
-сокращение нормативного срока службы основных фондов;
-соблюдение графиков планово-предупредительного ремонта основных производственных фондов предприятия, сокращение продолжительности проводимых ремонтов и повышение их качества, своевременное обновление фондов;
- достижение конструктивно-технологической однородности продукции в результате широкой унификации и стандартизации;
-повышение уровня автоматизации производства;
-создание бесцеховой, где это возможно, структуры управления предприятием.
Соблюдение рационального соотношения между основными, вспомогательными и обслуживающими цехами и участками должно быть направлено на повышение удельного веса основных цехов по количеству занятых рабочих, стоимости основных фондов, доли прибыли в общей прибыли предприятия.
В структурном отношении экономика предприятия должна формироваться как экономика отдельных звеньев и цехов. Пропорциональность входящих в состав предприятия звеньев
характеризуется |
рациональным |
соотношением |
производственной |
мощности |
цехов |
участков, связанных между собой совместным изготовлением конечного продукта. |
|
Развитие комбинирования приводит к комплексному использованию сырья и материалов, экономии живого и овеществленного труда, а также уменьшению вредного воздействия на окружающую среду.
Конструктивно-технологическая однородность продукции создает хорошие условия для углубления специализации производства, организации поточного и автоматизированного изготовления изделий, повышению их качества и снижению издержек, что необходимо в
условиях рыночной экономики. |
|
|
|
|
|
|
|||
Бесцеховая |
структура |
управления |
предприятием |
приводит |
|
к |
совершенство |
||
управления |
его |
подразделением, сокращению |
обслуживающего |
и |
|
управленческого |
аппарата, а, следовательно, к снижению издержек производства и лучшему реагированию на изменение спроса на продукцию. Правильно построенная производственная структура предопределяет пропорциональность всех цехов и служб предприятия, что, в свою очередь,
положительно |
влияет |
на |
улучшение |
технико-экономических |
показателей: уровень |
|||
специализации |
|
и |
кооперирования, ритмичность |
изготовления |
продукции, рост |
|||
производительности |
труда, улучшение |
качества |
изделий, сокращение |
численности |
управленческих кадров, наиболее целесообразное использование трудовых, материальных и финансовых ресурсов, увеличение прибыли.
Вопросы:
1.Производственный процесс и его структура
2.Основные принципы организации производственного процесса
3.Производственный цикл и его структура
4.Производственный цикл сложного процесса
5.Производственная структура предприятия и цеха
5.Подготовка и организация высокотехнологичног производства
5.1. Содержание и этапы инновационных процессов
Впрошлом, когда существовала централизованная плановая
экономика, обновление продукции на машиностроитель предприятиях, внедрение новых конструкторских и технологических решений осуществлялось директивно, соответствии утвержденными годовыми и пятилетними планами внедрения новой техники, результатов научно-технического прогресса.
Переход к рыночным отношениям разрушил эту систему, предприятия оказались в ситуации, когда им самим необходимо решать вопросы, какую и в каких количествах выпускать продукцию, где брать деньги на освоение новых технических решений, как, кому и по какой цене сбывать готовую продукцию. При этом надо
конкурентоспособным, то есть надо осуществлять маркетинговую деятельность, занять определенную нишу на рынке товаров. Все это возможно только при условии своевременного обновления, внедрения новых технических решений. Вместо прежней системы внедрения новой техники машиностроительные предприятия столкнулись
неизвестными |
ранее |
проблемами |
использования |
иннов, |
|
организации инновационных процессов их инвестированием. |
|
||||
Под инновацией (новшество, |
нововведение) понимается |
новое |
|||
техническое, технологическое, организационное |
или иное |
решение, |
|||
планируемое |
предприятием |
к |
использова. Инновацииию |
||
классифицируются на: |
|
|
|
|
|
-технические ; |
|
|
|
|
|
-организационные;
-информационные;
-социальные;
- экономические |
инновации представляют |
собой |
но |
|
Технические |
||||
конструкторско-технологические решения, выражаемые в виде новых |
||||
конструкторских решений ДСЕ, готовых изделий, а также новой |
||||
технологии |
их |
изготовления. Материальным |
воплощением |
|
технических инноваций являются конструкторская и технологическая |
|
|||
документация, |
опытные |
образцы, технологическое |
оборудование |
и |
оснастка.
Организационные инновации отражают новые методы организации
и планирования, используемые в производственно-хозяйственной
деятельности предприятия, например изменение организационных |
|
|||||||
форм |
производственных |
процессов(переход |
к |
использованию |
||||
предметно-замкнутых |
участков, поточных |
линий |
и.), |
|
||||
использование иных методов нормирования труда(хронометраж по |
|
|||||||
методу моды, метод моментальных наблюдений и .),т.дизменение |
|
|||||||
системы планирования на предприятии и т.д. |
|
|
|
|
||||
Информационные инновации – это различные формы внедрения |
|
|||||||
новых |
информационных |
технологий, позволяющие, |
например, |
|
||||
внедрить электронный документооборот, ERP- |
систему |
и CALS- |
|
|||||
технологии. |
|
|
|
|
|
|
|
|
Социальные инновации представляют собой улучшение условий |
|
|||||||
труда, отдыха, быта |
работающих, |
повысить |
безопасность |
и |
||||
привлекательность |
труда (например, |
гибкий |
график |
работы, |
рациональная система организации питания персонала в обеденный перерыв и т.д.).
Экономические инновации – это усовершенствование каких-либо
элементов экономической системы предприятия (например, изменение системы расчетов с поставщиками и заказчиками, использование эффективных мотиваций труда работающих и т.д.).
На практике машиностроительных предприятий под инновацией понимают те из них, которые непосредственно влияют на технический уровень и конкурентоспособность производимой продукции, то есть технические инновации.
Эффективность организации инновационных процессов влияет на показатели результативности производственной деятельност предприятия:
-величину затрат
-объем прибыли;
-объем продаж.

Проведением инновационных процессов на машиностроительном
предприятии |
занимаются |
конструктора, технологи, системные |
|
аналитики, |
исследователи, |
экономисты, |
экперементальные |
производства. Их задача заключается в обеспечении предприятия возможностью обновлять выпускаемую продукцию с у требований потребителей.
Существуют этапы инновационного процесса:
1)создание технических инноваций;
2)внедрение технических инноваций;
3)коммерциализация технических инноваций. Этапы инновационного процесса представлены на рис. 3.1.
Этап 1 |
Этап 2 |
Этап 3 |
Создание инноваций |
Внедрение |
Коммерциализация инноваций |
|
инноваций |
|
Научные исследования и |
|
Объем производства и продаж |
разработки, подготовка |
|
|
|
|
|
конструкторской, |
|
|
технологической |
|
|
документации и т.д. |
|
|
|
|
|
Жизненный цикл инноваций
Рис. 3.1. Этапы инновационного процесса
На этапе 1 проводятся научные исследования, опытно-
конструкторские работы. Результат этого этапа: констукторскотехнологическая документация, опытные образцы и данные об их испытаниях, наличие технологического оборудования и техоснастки. Имеются большие затраты на, конструкторскиеНИР и технологические разработки, создание опытных образцов.
На этапе 2 идет освоение новой продукции. Имеет место рост
объемов производства и объемов продаж.
Этап 3 инновационного процесса характеризуется значительным
ростом объемов производства и продаж, Затраты на производство
полностью |
покрываются |
выручкой |
от |
реализации |
продук, |
предприятие начинает получать прибыль. |
|
|
|
Суммарная длительность всех трех этапов инновационного процесса
составляющая |
от |
нескольких |
лет |
до |
нескольких |
десятил, |
||
называется жизненным циклом инноваций. |
|
|
|
|
||||
Жизненный |
цикл |
инноваций |
несколько |
|
отличается |
|||
жизненного |
цикла |
продукции |
|
предприятия. ЖЦ |
продукции |
дополнительно включает в себя затраты(кроме инноваций сферы разработки и производства изделий) по всему жизненному циклу изделия, включая этапы эксплуатации, ремонтного обслуживания, утилизацию.
Сокращение |
этапов 1 и 2 позволяет осуществлять ускоренную |
|||||
техническую |
подготовку |
производства |
и |
опытное |
вне |
|
продукции. Это, как правило, осуществляется за счет внедрения CALS |
||||||
– технологий в |
сочетании |
с |
созданиемERP – систем. При |
этом |
||
предполагается |
заключение |
лицензионных |
договоров |
использование запатентованных изобретений, полезных моделей, промышленных образцов, ноу-хау.
5.2. Организация |
научно-исследовательских |
работ |
||||
изобретательства |
|
|
|
|
|
|
Научные |
исследования – |
это |
специфический |
в |
||
профессиональной |
|
интеллектуальной |
деятельности, имеющей |
|||
своеобразные конечные результаты. Такими |
результатами |
|
могут |
|||
быть: |
|
|
|
|
|
|
-новые знания, идеи, информация, методы, представления, изложенные в научных отчетах;
-новые идеи и знания, подготовленные для практического
использования |
в |
форме |
конструкторской |
и |
технологич |
||
документации, методик, изготовленных опытных образцов; |
|
||||||
- идеи, |
овеществленные |
в |
новых |
осваиваемых |
изделия, |
внедренных технологических процессах, методах управления.
При классификации НИР можно выделить фундаментальные исследования, прикладные исследования, разработки.
Фундаментальные исследования – это научные исследования,
расширяющие представление человека о материальном мире; они являются базовыми для развития технического прогресса. Это чистая или академическая наука.
Прикладные исследования имеют целью практич
использование результатов фундаментальных исследований.
Разработки (ОКР) – это переходная стадия от фундаментальных и
прикладных исследований к подготовке и освоению производства. Здесь идеи воплощаются в техническую документацию, опытные образцы.
Основные стадии НИР Первая стадия - разработка технического задания. Включает в себя:
-литературно-патентная проработка темы(отечественная и зарубежная);
-уточнение задачи и исследования;
-технико-экономическое обоснование темы;
-техническое задание и плановая калькуляция темы.
Вторая стадия – разработка технического предложения. Включает в
себя:
-анализ технического задания;
-анализ источников НТИ;
-техническое предложение.
Третья стадия – проведение теоретических и экспериментальных
исследований. Этапы:
1)теоретические разработки; разработка методики исследования, теоретические обоснования, расчеты, выявление необходимости экспериментальных работ, составление методики их проведения;
2)проектирование, изготовление макетов и экспериментальных образцов;
3)экспериментальные работы, осуществляемые в ОКБ.
Четвертая |
стадия – оформление |
результатов НИР. Составляется |
||
отчетная |
документация, включая |
материалы |
по |
новизне |
целесообразности использования результатов НИР, по экономической эффективности темы. Составляется проект технического задания на ОКТ; составление программы работы комиссии по приемки темы.
Пятая стадия – приемка темы (на научно-техническом совете) и
подписание акта заказчиком о принятии НИР.
Большое влияние на цикл и качество НИР ок организационная структура научных учреждений. В крупных НИИ при установившейся тематике создаются спец. подразделения по направлениям работ, например, отдел теоретических исследований со спец. лабораториями по тематике. Это приводит к увеличению численности работников НИИ.
На машиностроительных предприятиях организуют ОПРИ (отдел патентоведения, рационализации и изобретательства). Этот отдел занимается следующими вопросами:
-организация патентной работы;
-организация рационализаторской работы;
-организация изобретательской работы.
ВРоссийской Федерации(РФ) основным документом, регламентирующим вопросы изобретательства, является “Патентный закон РФ”. Он регулирует отношения, возникающие в связи с
созданием, правовой |
охраной |
и |
использованием |
об |
||
промышленной |
собственности: изобретений, |
полезных |
моделей, |
|
промышленных образцов. Права на эти виды промышленно
собственности |
охраняет |
закон, и |
подтверждают |
документы, |
|
выдаваемые |
РОСПАТЕНТОМ: патенты |
на |
изобретение |
||
промышленные |
образцы, свидетельство |
на |
полезную |
модель. Эти |
документы удостоверяют приоритет, авторство и исключительные права на использование данных видов промышленной собственности.
Изобретением могут быть признаны устройство, способ, вещество.
Чтобы претендовать на получение правовой охраны они должны соответствовать следующим условиям:
1)быть новыми, то есть не известными из достигнутого уровня техники;
2)иметь высокий, именно изобретательский уровень;
3)быть промышленно применимыми, то есть могут быть использованы в промышленности или других отраслях..
Патент на изобретение действует в течение20 лет со дня поступления заявки в Патентное ведомство.
Полезные модели – это конструкторское выполнение изделий и их
составных частей. Это так называемые “малые изобретения”. Свидетельство на полезную модель действует5 лет. Можно продлить еще на 3 года.
5.3.Организация конструкторской подготов производства
Результаты НИР используются в КПП новых изделий. При этом необходимо учитывать основные требования экономичес, эксплутационного, конструкторского, технологического, организационно–производственного характера к изделию, которые обязаны удовлетворять конструкторы в процессе КПП.
Основные стадии КПП:
-техническое задание (ТЗ);
-техническое предложение;
-эскизный проект;
-технический проект;
-рабочий проект.
Техническое задание
На этой стадии подготавливается по рекоме маркетинговых исследований, как правило, заказчиком. Указываются назначение изделия и его основные параметры(производительность, мощность, точность, надежность и др.), потребность в данном изделии и ориентированный годовой выпуск.
Техническое предложение
На этой стадии подготавливается разработчиком на основе ТЗ техническое предложение. Определяется возможность удовлетворения
всех |
требований |
ТЗ |
в |
данных |
производственных . ус |
||
Утверждается и становится основой для дальнейших проектных работ. |
|||||||
Эскизный проект |
|
|
|
|
|
|
|
На |
стадии эскизного |
проекта изготавливают чертежи общи |
|||||
видов, |
спецификации |
деталей, |
|
сборочных |
единиц (ДСЕ), |
||
изготавливают |
макеты, проводят |
промежуточный |
технико– |
||||
экономический анализ. |
|
|
|
|
|
||
Технический проект |
|
|
|
|
|
|
Это наиболее трудоемкая стадия. На этой стадии проводят следующие работы:
-проводят все расчеты, связанные с обеспечением прочности, жесткости, надежности всех ДСЕ;
-обеспечивают технологичность изделия;
-изготавливают чертежи;
-готовят пояснительную записку по ,ТЭОперечню работ, необходимых для подготовки рабочей документации, как к опытным образцам, так и к изделиям серийного производства. Все документы утверждаются той организацией, которая выдала ТЗ.
Рабочий проект
На этой стадии осуществляется разработка следующей рабочей документации для:
-опытного образца;
-установленной серии;
-установившегося производства.
При этом возможны объединения стадий ЭП – ТП и другие. КПП решаются еще следующие вопросы:
-чертежное хозяйство по ЕСКД;
-унификация и стандартизация конструкций;
-технологичность конструкций;
Унификация и стандартизация конструкций повышает качество,
снижает трудоемкость разработок. Этими вопросами на предприятии занимается базовый конструкторский отдел стандартизации (БКОС).
Применяются следующие коэффициенты:
-коэффициент унификации изделия;
-коэффициент стандартизации;
-коэффициент преемственности;
-обобщенный показатель унификации и стандартизации.
Коэффициент унификации изделия;
Этот коэффициент характеризует конструкторскую унификацию и рассчитывается по формуле
Кун = |
Nун |
|
------------, |
3.1. |
|
|
Nобщ |
|
где:
Nун - количество типоразмеров деталей, унифицированных с деталями других изделий; Nобщ - общее количество типоразмеров деталей.
Унификация устраняет излишнее разнообразие конструкций самих изделий, форм и размеров деталей и заготовок, профилей и марок материалов. При этом создаются условия для специализированного производства повторяющихся ДСЕ.
Коэффициент стандартизации;
Этот коэффициент характеризует уровень стандартизации рассчитывается по формуле:
Кст = |
Nст |
|
------------, |
3.2. |
|
|
Nобщ |
|
где:
Nст - количество типоразмеров стандартных деталей в изделии; Nобщ - общее количество типоразмеров деталей.
Стандартизация устанавливает необходимый минимум типов и параметров машин, механизмов, приборов, средств автоматизации, материалов, полуфабрикатов и комплектующих изделий с учетом развития машиностроительной отрасли.
Коэффициент преемственности;
Этот коэффициент характеризует уровень преемственности деталей в изделии и рассчитывается по формуле:
Кпр = |
Nз |
|
------------, |
3.3. |
|
|
Nобщ |
|
где:
Nз -номенклатура заимствованных деталей в изделии.
Обобщенный показатель унификации и стандартизации.
Данный коэффициент определяет обобщенный уровень унификации, стандартизации и преемственности и рассчитывается по формуле:
Кусп = - Кун + Кст + Кпр ,
3.4.
Технологичность конструкций |
|
|
|
|
Для |
повышения |
эффективности |
организационной |
систем |
создания и освоения новой техники играет их производственная и эксплуатационная технологичность.
Под производственной технологичностью понимают степень соответствия конструкции изделия оптимальным производственнотехнологическим условиям его изготовления при заданном объеме производства.
Эксплуатационная технологичность изделия проявляется в сокращении затрат времени и средств на техническое обслуживание и ремонт изделия, находящегося в эксплуатации у потребителя.
Существуют показатели, характеризующие технологичность конструкций. (табл.3.1).
Таблица 3.1.
Система основных показателей технологичности
Показатели |
Расчетная формула |
Принятые обозначения |
|
|
|
|
|
|
Производственные абсолютные |
|
|
|
|
|
|
Суммарная материалоемкость |
|
Gчр – расход материала на заготовки из |
|
изделия |
Gо = Gчр + Gц + Gн |
черных металлов; |
|
Gц – то же из цветных металлов; |
|||
|
|
Gн - то же из неметаллических |
|
|
|
материалов |
|
Суммарная трудоемкость |
|
tз –трудоемкость заготовительных работ; tм – то |
|
изделия |
tиз = tз + tм + tсб + tп |
же механической обработки; tсб – то же |
|
|
сборочных работ; tп – то же прочих работ |
||
|
|
||
|
|
|
|
Себестоимость изделия |
S |
|
|
|
Производственные относительные |
|
|
|
|
|
|
Удельная материалоемкость |
gу = Gо/P |
P – определяющий эксплуатационный |
|
параметр изделия (производительность, |
|||
изделия |
|
||
|
мощность и т. д.) |
||
|
|
||
|
|
|
|
Коэффициент использо- |
Kим = Gч/Gо |
Gч - чистая масса изделия |
|
вания материалов |
|
|
|
Удельная трудоемкость |
tу = tиз/P |
|
|
изделия |
|
|
|
Удельная себестоимость |
Sу = S/P |
|
|
изделия |
|
|
|
|
Эксплуатационные абсолютные |
|
|
|
|
|
|
Трудоемкость |
|
|
|
профилактического |
tоб |
|
|
обслуживания |
|
|
|
Трудоемкость |
tр |
|
|
эксплуатационных ремонтов |
|
|
|
|
Эксплуатационные относительные |
|
|
|
|
|
|
Удельная трудоемкость |
tуоб = tоб /P |
|
|
обслуживания изделия |
|
|
|
Удельная трудоемкость |
tур = tр /P |
|
|
эксплуатационных ремонтов |
|
|
|
Удельные затраты на |
Sуоб = Sоб /P |
|
|
обслуживание изделия |
|
|
|
Удельные затраты на |
Sуp = Sp /P |
|
|
эксплуатационные ремонты |
|
|
Организационная |
структура |
конструкторской |
под |
производства |
среднего |
машиностроительного |
предп |
представлена на рис. 3.3. |
|
|

Главный
инженер
Служба новой техники |
|
Инструментальная служба |
|
||
|
|
|
|
|
|
|
|
|
|
|
|
Отдел подготовки производства и технической документации
Генеральный директор
Главный |
Зам. ген |
конструктор |
директора по |
|
качеству |
|
|
|
|
|
|
|
|
|
Серийно-конструкторский отдел |
|
Опытно-констукторское бюро |
|
|
Базовый конструкторский |
отдел стандартизации |
|
|
|
|
|
|
|
|
|
|
|
Начальник службы информационных технологий
Служба информационных |
технологий |
Рис. 3.3. Организационная структура конструкторской подготовки производства среднего машиностроительного предприятия

5.4. |
Организация |
технологической |
подгото |
производства |
|
|
Технологическая подготовка производства(ТПП) представляет собой совокупность взаимосвязанных процессов, обеспечивающих технологическую готовность машиностроительного предприятия к выпуску изделий заданного уровня качества при установленны сроках, объеме выпуска и затратах.
Основные функции ТПП:
1)обеспечение технологичности конструкции изделия на стадиях
ТПП;
2)разработка технологических процессов;
3)проектирование и изготовление средств технологического оснащения;
4)метрологическое обеспечение;
5)сокращение сроков ТПП;
6)обеспечение качества на всех стадиях ТПП;
7)организация и управление процессом ТПП.
Технологическая подготовка производства является трудоемким и дорогостоящим процессом, предшествующим изготовлению нового
изделия. На |
внедрение |
новых |
технологических |
процессов |
изготовление |
технологической |
оснастки |
капиталовло |
составляют до 80% всех затрат на ТПП.
Обеспечение технологичности конструкции изделия на стадиях ТПП
Раскрыть задачу “Расчет КИМ”
Разработка технологических процессов
Общая классификация технологических процессов дана на рис. 3.4.
Технологические
процессы
Единичные |
|
Унифицированные |
|
|
|
|
|
|
Типовые |
|
Групповые |
|
|
|
Рис. 3.4. Общая классификация технологических процессов
Этапы разработки технологических процессов:
-составление расцеховок и маршрутных карт(маршрута движения детали;
-кодирование операций;
цех 1 |
цех 4 |
цех 5 |
цех 4 |
цех 3 |
СГД |
●------------- |
●------------ |
●---------------- |
●--------------- |
●------------- |
● |
005 |
010 |
015 |
020 |
025 |
030 |
005005 |
010005 |
015005 |
020015 |
025005 |
030005 |
005010 |
010010 |
015010 |
020020 |
025010 |
030010 |
-составление операционных карт;
-составление ведомостей технологической оснастки;
-составление пооперационных норм времени.
В операционных картах описывают . операциитех, переходы; указывают наименования операций(токарные, фрезерные, сверлильные, шлифовальные и др.).
Показателями норм времени являются: сетка, разряд, ставка, норма времени, расценок.
Ведомость технологической оснастки
Основной массив в задаче “Автоматизированный учет применяемости технологической оснастки” имеет следующую структуру:
-шифр цеха;
-шифр детали;
-шифр операции;
-шифр технологической оснастки.
Данная задача позволяет сократить сроки ТПП за счет наведения элементарного порядка в части учета . ТОТо есть не надо будет дополнительно проектировать ТО и ее изготавливать.
Проектирование и изготовление технологической оснастки
Этапы проведения работ:
1)получение чертежа из ОГК;
2)разработка расцеховок – ОГТ;
3)разработка маршрутных карт и технологических процессов– ТБ цехов;
4)разработка ТЗ на проектирование ТО – ТБ цехов;
5)проектирование ТО – ОГТ;
6)изготовление ТО – ИНО, инструментальный цех;

7)испытание ТО – ИНО, инструментальный цех;
8)использование ТО – цехи основного производства.
Организационная структура ТПП
Организационная структура проведения ТПП для машиностроительных предприятий представлена на рис. 3.5.
Генеральный директор
|
|
|
Главный |
|
|
|
|
|
|
|
|
|
|
|
|
|
|
Зам. |
|
|
|
Начальник |
|
|||||||||
|
|
|
инженер |
|
|
|
|
|
|
|
|
|
|
|
|
генерального |
|
|
|
службы |
|
|||||||||||
|
|
|
|
|
|
|
|
|
|
|
|
|
|
|
|
|
|
|
директора по |
|
|
информацион- |
|
|||||||||
|
|
|
|
|
|
|
|
|
|
|
|
|
|
|
|
|
|
|
производству |
|
|
ных технологий |
|
|||||||||
|
|
|
|
|
|
|
|
|
|
|
|
|
|
|
|
|
|
|
|
|
|
|
|
|
|
|
|
|
|
|
||
|
|
|
|
|
|
|
|
|
|
|
|
|
|
|
|
|
|
|
|
|
|
|
|
|
|
|
|
|
|
|
||
|
|
|
|
|
|
|
|
|
Зам. главного |
|
|
|
|
|
|
|
|
|
|
|
|
|
|
|
||||||||
|
|
|
|
|
|
|
|
|
|
инженера по |
|
|
|
|
|
|
|
|
|
|
|
|
|
|
|
|||||||
|
|
|
|
|
|
|
|
|
|
|
|
ТПП |
|
|
|
|
|
|
|
|
|
|
|
|
|
|
|
|
|
|||
|
|
|
|
|
|
|
|
|
|
|
|
|
|
|
|
|
|
|
|
|
|
|
|
|
|
|
|
|
|
|
||
|
|
|
|
|
|
|
|
|
|
|
|
|
|
|
|
|
|
|
|
|
|
|
|
|
|
|
|
|
||||
|
Отдел главного технолога |
|
Отдел главного металлурга |
|
|
Отдел главного сварщика |
|
|
Инструментальный отдел |
|
|
Отдел ТПП и ТД |
|
|
|
|
|
Цехи основного производства |
|
|
|
|
|
|
Служба информационных технологий |
|
||||||
|
|
|
|
|
|
|
|
|
|
|
|
|
|
|
|
|
|
|
|
|
|
|
|
|
|
|
|
|
||||
|
|
|
|
|
|
|
|
|
|
|
|
|
|
|
|
|
|
|
|
|
|
|
|
|
|
|
||||||
|
|
|
|
|
|
|
Инструментальные цехи |
|
|
|
Центральный |
инструментальный склад |
|
|
Технологическое бюро |
|
|
Бюро труда и зарплаты |
|
|
|
|
||||||||||
|
|
|
|
|
|
|
|
|
|
|
|
|
|
|
|
|
||||||||||||||||
Рис. 3.5. Организационная |
структура проведения ТПП для средни |
|||||||||||||||||||||||||||||||
машиностроительных предприятий |
|
|
|
|
|
|
|
|
|
|
|
|
|
|
|
5. 5. Концепция создания систем автоматизированного проектирования конструкций и технологичес процессов в составе интегрированных АСУ CALSи - технологий
Целью концепции является определение основных принципов создания, развития и функционирования САПР КТ в сос интегрированной АСУ с учетом функционирования CALS-технологии.
Под |
CALS- |
технологией |
понимается |
непрерыв |
информационная поддержка жизненного |
цикла изделий(ЖЦИ). О |
ЖЦИ речь шла на первой лекции. Девять фиксированных этапов ЖЦИ являются основой для формирования единого информационного пространства ИАСУ, отражающего информационные характеристики системы в пространстве и времени. В настоящей концепции рассматривается только 4 этапа ЖЦИ:
-САПР К основного изделия;
-САПР К техоснастки;
-САПР ТП основного изделия;
-САПР программных продуктов для станков с ЧПУ. Основные вопросы концепции:
1) методические основы создания САПР КТ;
2) общая структура САПР КТ;
3) задачи САПР КТ;
4) общие требования к САПР КТ;
5) порядок взаимодействия субъектов САПР КТ; 6) обеспечение безопасности и защиты данных в САПР КТ;
7) экономическое обоснование проектных решений.
1.Методические основы создания САПР КТ
Необходимо иметь, как минимум, следующие методические
материалы: |
|
|
|
|
- |
методические |
основы |
проведения |
предпроек |
обследования объекта автоматизации |
(в том числе САПР К, САПР Т, |
|||
SCADA-система, АСУП); |
|
|
|
- методические материалы по разработке системного проекта.
В первом |
документе должны быть отражены |
следующие |
||
вопросы : |
|
|
|
|
-организация обследования; |
|
|
|
|
-разработка |
системы |
классификации |
и |
кодир, |
используемой при - обследовании объекта автоматизации (ОА); |
|
-обследование организационной структуры ОА;
-обследование существующего состава функциональных задач
икомплекса технических средств на ОА.
-обследование существующей системы классификации кодирования технико-экономической, управленческой и правовой информации.
-обследование функциональной структуры ОА. Во втором документе должно быть отражено:
- правила построения функциональной, информационной и динамической моделей на основе идеологии САДТ и ПППDesign Idef или других кейс–средств.
Системный |
проект |
для |
ИАСУ |
должен |
базироваться |
следующих |
общесистемных |
|
принципах |
и |
|
информационного обеспечения АСУ: |
|
|
|
а) общесистемные принципы:
-принцип новых задач;
-принцип первого руководителя;
-принцип замкнутости контура управления ;
-принцип выравнивания пропускной способности всех звеньев
ИАСУ;
-принцип эффективности ИАСУ ;
-принцип документальности проектных решений;
-принцип наглядности проектных решений ;
-принцип актуализации проектных решений ;
-принцип поддержки системы на высоком научно-техническом уровне;
-принцип автоматизации проектирования ИАСУ;
б) принципы информационного обеспечения:
-принцип достаточности информации для решения задач ИАСУ;
-принцип |
одноразового |
ввода |
|
информации |
в |
И |
|
многократного ее использования всеми пользователями системы; |
|
|
|||||
- |
принцип |
очередности |
внедрения |
функциональных |
|
зада |
|
ИАСУ(уровни иерархии решаемых задач); |
|
|
|
|
|||
- |
принцип |
классификации |
и |
кодирования |
|
- те |
|
экономической, управленческой и правовой информации; |
|
|
-принцип унификации и стандартизации форм документов ;
-принцип повышения качества технологического процесса обработки данных;
-принцип привязки ИО отдельных конкретных задач к ИО САПР
КТ;
-принцип актуализации ИБД системы ;
-принцип безбумажной технологии обработки информации;
-принцип защищенности информации от несанкционированного
кней доступа и обеспечение безопасности;
-принцип сетевого подхода при создании ИО САПР КТ;
2. Общая структура САПР КТ
САПР КТ является частью интегрированной системы АСУ, без которой невозможно осуществить как автоматизацию инженерного труда, так и автоматизацию управленческого труда в режимеCALS-
технологии. |
|
|
|
|
|
|
|
|
Корпоративная |
вычислительная |
сеть |
ИАСУ |
предпри |
||||
позволяет |
создать |
единую |
телекоммуникацию |
|
между |
|||
элементами |
ИАСУ. |
Кроме |
того, |
предусматривается |
|
создание |
||
отдельных локальных вычислительных сетей (ЛВС) для САПР К, САПР |
||||||||
Т, СЧПУ |
имеющих |
возможность |
информационного |
|
выхода |
|||
корпоративную вычислительную сеть ИАСУ, Internet и электронную |
||||||||
почту. |
|
|
|
|
|
|
|
|
Для создания, ведения ИБД конструкторско-технологического |
||||||||
назначения, |
приобретения, |
освоения |
и |
разработки(при |
||||
необходимости) серверных |
приложений, клиентских |
|
модулей |
|||||
(CAD/CAM/CAE/Технорма), |
системы |
PDM |
(электронного |
|||||
конструкторско-технологического |
документооборота), |
обучения |
пользователей и подготовки кадров по CALS-технологии должен быть
организован отдел, входящий в УИТП (управление информационных технологий предприятия).
При ОГК, ОМА, ОГМ должны создаваться автоматизированные рабочие места (АРМ) конструктора по проектированию изделий.
При ОГТ, ОМА, ОГМет, ОГС, ОГМ должны создаваться АРМы конструктора по проектированию технологической оснастки.
При ОГТ, ОГМет, ОГС, ОМА, технологических бюро (ТБ) цехов должны создаваться АРМы технолога по разработке технологических процессов
При ОАСУ ТП (ОГТ) должны создаваться АРМы технолога по управляющим программам для станков с ЧПУ.
При ОГК, ОГТ, ОГМет, ОГС, ОМА, ОГМ, ОГЭ должны создаваться АРМы расчетчика.
В центральной базе данных АСУП на Web сервере хранится как чисто АСУП–овская информация(по функциональной подсистеме “Управление маркетингом”), так и информация по САПР КТ(п
функциональным подсистемам “САПР К”, “САПР Т” и по управляющим |
|
|||||
программам для СЧПУ). |
|
|
|
|
|
|
ОМИ в результате проведения маркетингового анализа должен |
|
|||||
выдавать в ОГК,ОМА свои предложения по освоению новых изделий |
|
|||||
или модернизации существующих. На основании выявленных |
|
|||||
требований к |
новым |
изделиям |
со |
стороны |
рынка , ОГКОМА |
|
разрабатывают технические задания на изделие в электронном виде |
|
|||||
и приступают к проектированию и инженерному расчету изделий по |
|
|||||
системе CAD/CAE на созданных у них автоматизированных рабочих |
|
|||||
местах конструктора основных изделий и расчетчика. |
|
|
||||
ОСАПР |
КТ |
при |
этом |
осуществляет |
ак |
|
(корректировку) |
конструкторско-технологической базы данных и |
|||||
организует архивацию конструкторской документации в электронном |
|
|||||
виде. |
|
|
|
|
|
|
На основании трехмерных электронных моделей издели, |
||||||
конструкторской |
документации в |
электронном |
виде, выпущенных |
|
ОГК и ОМА должны проводится следующие проектные работы:
-проектирование технологических процессов ( ОГТ,ОГМет, ОГС, ОМА, ТБ цехов);
-проектирование технологической оснастки (ОГТ, ОМА, ОГМет, ОГС, ОГМ);
-разработка управляющих программ для станков с ЧПУ.
В результате проведения указанных проектных работ выдается соответствующая документация в электронном виде, которая должна хранится, корректироваться отделом ОСАПР КТ в технологической документации
3. Задачи САПР КТ
Цель создания САПР КТ
Целью создания САПР КТ является повышение эффективности работы технических структурных подразделений предприятия. Это осуществляется за счет:
-улучшения их информационного обслуживания;
-использования эффективных информационных технологий;
-обеспечения единого информационного пространства н предприятии;
-использования общей системы телекоммуникаций;
-автоматизации функциональных подсистем и задач САПР, К САПР Т в режиме CAD/CAM/CAE/PDM технологии.
В процессе создания, эксплуатации и развития САПР КТ решаются следующие задачи:
Традиционные задачи
Наличие элементов САПР К и САПР Т на предприятии. Разработка программного обеспечения для станков с ЧПУ на технологических процессов, составленных вручную. Отсутствие локальной вычислительной сети (ЛВС) для реализации САПР К, САПР Т.
Задачи, ставшие актуальными в настоящее время
Внедрение |
функциональной |
|
подсистемы “Управление |
|
|||||
маркетингом”, которая является основополагающей для жизненного |
|
||||||||
цикла |
изделий |
и |
плановых |
задач. |
СозданиеАСУП |
ИБД |
|
||
конструкторско-технологического |
назначения |
на |
основе , |
Л |
|||||
созданных для реализации САПР К, САПР Т. Выход в глобальные сети |
|
типа Internet и использование электронной почты(ЭП). Наличие децентрализованного решения задач САПР К, САПР Т, в технических структурных подразделениях предприятия в сетевом вариант. Частичное решение задач по инженерным расчетам (CAE)/
|
|
Перспективные задачи |
|
|
|
Внедрение функциональных |
подсистем и задач САПР К, САПР Т , |
|
|||
на основе системыPDM (ИБД и электронный документооборот). |
|
||||
Создание |
ИБД |
конструкторско-технологического |
назначения |
н |
|
основе корпоративной вычислительной сети интегрированной АСУ |
|
||||
предприятия с выходом вInternet, ЭП. Полное внедрение задач по |
|
||||
инженерным расчетам (CAE). |
|
|
|
||
Наличие |
интегрированной |
системы управления |
предприятием |
|
учетом CALS-технологии.
4.Общие требования к САПР КТ
КСАПР КТ предъявляются следующие общие требования:
1)САПР КТ должна обеспечивать автоматизацию функциональных технических задач в сетевом варианте;
2)САПР КТ должна обеспечивать максимальную гибкость, открытость и способность к саморазвитию;
3) в |
процессе |
формирования |
ИБД |
конструк- |
||
технологического |
назначения |
должен |
соблюдаться |
при |
разумной достаточности, то есть необходимо обеспечить входной информацией выполнение всех функций САПР КТ при постепенном поэтапном наращивании ресурсов;
4) в процессе эксплуатации САПР |
КТ |
должен соблюдатьс |
принцип “привлекательности” отдела САПР |
КТ, то |
есть необходимо |
обеспечить опережающее развитие уровня сервисных услуг в ядре системы по отношению к возможностям ее пользователей и других
информационных систем; |
|
|
|
5) САПР |
КТ должен |
обеспечить |
высокую надежность и |
живучесть , то |
есть отказ |
какой-либо |
компоненты не долж |
приводить к отказу всей системы;
6)построение и развитие САПР КТ должно основываться на отечественных ГОСТах и международных стандартах в предела разумной целесообразности;
7)САПР КТ должна иметь адекватную систему безопасности и защиты информации.
5. Порядок взаимодействия субъектов САПР КТ
Генеральным заказчиком САПР КТ является генеральн директор предприятия или заменяющее его .лицоОперативное управление САПР КТ в целом осуществляет начальник Управления информационных технологий предприятия, ОСАПР КТ. Структуру и организационные принципы определяет Генеральный заказчик.
Оперативное |
управление |
задачами |
САПР |
КТ |
осуществля |
|
специалистами |
технических |
служб |
предприятия(ОГК, ОГТ, ОМА, |
|||
ОГС, ОГМет, ОГМ, ОГЭ) в |
лице |
конструкторов, |
технологов и |
|||
инженеров-расчетчиков. |
|
|
|
|
|
Порядок взаимодействия между пользователями САПР регламентируются нормативными и распорядительными актам предприятия
6. Обеспечение безопасности и защиты данных в САПР КТ
Степень обеспечения безопасности и защиты данных в САПР КТ должна быть адекватна степени угрозы их разрушения
несанкционированного использования, а также |
ценности |
самой |
||
информации. Для |
обеспечения безопасности |
и |
защиты |
данны |
ОСАПР КТ производит анализ риска и на |
его |
основе |
строит |
|
проводит политику безопасности. |
|
|
|
|
Для защиты |
информации разрабатывается и |
реализуется |
план |
защиты, а также осуществляется постоянный контроль за работой
системы в целях предотвращения нарушения защиты. |
|
||
Отнесение |
информации |
к |
определенному |
конфиденциальности производится на основании действующих нормативных актов, на предприятии.
7. Экономическое обоснование проектных решений
Обоснование проектных решений должно производиться на всех стадиях разработки САПР КТ:
-техническое задание; -системный проект;
-рабочий проект; -внедрение.
На стадии технического задания производится предварительное
обоснование проектных решений. |
|
|
|
||
На |
стадии |
системного |
проектирования |
и |
|
проектирования |
производится |
уточненный |
расчет |
затрат |
экономической эффективности от принятых проектных решений.
На стадии внедрения производится расчет фактических затрат и
фактической |
экономической |
эффективности |
от |
внедре |
||
проектных решений. |
|
|
|
|
|
|
Для |
проведения |
экономического |
обоснования |
проект |
||
решений необходимо осуществить следующее: |
|
|
|
-определить трудовые, материальные и финансовые затраты; -определить источники экономической эффективности; -принять методику расчета экономической эффективности от
внедрения ИАСУ и ее компонентов; -произвести расчет экономической эффективности.
Вопросы:
1.Содержание и этапы инновационных процессов
2.Организация научно-исследовательских работ и изобретательства
3.Организация конструкторской подготовки производства
4.Организация технологической подготовки производства
5.Концепция создания систем автоматизированного проектирования конструкций и технологических процессов в составе интегрированных АСУ и CALSтехнологий
6.Организация вспомогательных цехов и сл
предприятия
6.1. Организация инструментального хозяйства
Основной задачей инструментального хозяйства предприятия является своевременное обеспечение производства качественной технологической оснасткой (режущим и мерительным инструментом,
приспособлениями и штампами) при минимальных издержках на их приобретение, изготовление и эксплуатацию.
При этом инструментальное хозяйство машиностроительного предприятия решает следующие конкретные задачи:
1)определение потребности предприятия в техоснастке;
2)планирование приобретения (изготовления) и обеспечение производства техоснасткой;
3)организация рациональной эксплуатации техоснастки и технического надзора;
4)обеспечение рабочих мест техоснасткой;
5)организация учета и хранения техоснастки.
Классификация технологической оснастки:
1. По характеру использования:
- стандартная техоснастка – оснастка универсального применения , которая производится специализированными фирмами и может быть
приобретена |
по |
разовым |
закупкам |
или |
поставляет |
долговременным |
|
договорам |
между |
|
предприяти |
инструментальными предприятиями. |
|
|
|
-специальная техоснастка, изготавливаемая в инструментальном цехе предприятия или заказываемая у специализированных фирм.
2. По назначению:
-группы;
-подгруппы;
-виды;
-разновидности;
-типы.
Например, группа режущего инструмента: резцы, фрезы, сверла; фрезы: цилиндрические, торцевые.
Группа штампов, которая имеет подгруппы штампов для горячей объем ной штамповки, вырубные штампы для листовой штамповки, вытяжные штампы.
Группа литейной оснастки, группа станочных приспособлений и т.д.
Планирование обеспечения производства технологической оснасткой
Потребность машиностроительного предприятия по каждому виду технологической оснастки включает ее расход в плановом периоде и
изменение остатков оборотного фонда на конец и начало того же периода:
Иоп =Иор + (Иофк – Иофн),
где:
Иоп – потребность технологической оснастки в плановом периоде, шт.; Иор – расход технологической оснастки за плановый период, шт.;
Иофк, Иофн – величина оборотного фонда технологической оснастки соответственно на конец и начало планового периода, шт.
Величина расхода технологической оснастки определяется на основе норм их расхода.
Для единичного и мелкосерийного производства норма расхода техоснастки определяется на 1000 рублей валовой продукции за отчетный период. Расход техоснастки в этом случае определяется по формуле:
Иор = Nвп Ио/1000 , |
4.2 |
где:
Иор – расход техоснастки в плановом периоде, шт.;
Nвп – объем валовой продукции в плановом периоде, руб.;
Ио - фактический расход данного вида техоснастки, приходящийся на 1000 рублей валовой продукции отчетного периода, шт./1000 руб.
В массовом и крупносерийном производстве расход техоснастки определяется по формуле:
|
1000 tм λ |
|
Ио = |
|
, |
|
||
|
60 Ти (1-р/100) |

где:
Ио – норма расхода инструмента на 1000 операций, шт./1000 оп.;
tм – норма машинного времени, необходимого для выполнения одной операции данным инструментом, мин.;
λ – число одновременно работающих инструментов данного типоразмера, шт.;
Ти – стойкость инструмента до полного его износа, час.; р – величина, характеризующая случайную убыль инструмента, %.
На рис. 4.3 приведена структура цехового оборотного фонда техоснастки.
К оличест во тех осн астки
Перех од ящ ий зап ас
Стр аховой зап ас
В заточке и в ремон те
На рабочи х м естах основных цехов
Врем я, дни
Рис. 4.3. Структура цехового оборотного фонда техоснастки
Момент поступления техоснастки из цен инструментального склада (ЦИСа) осуществляется при максимальном уровне переходящего запаса
Основная часть запаса техоснастки на предприятии хранится в ЦИС-е. Регулирование складских запасов техоснастки, расходуемой в
больших количествах, осуществляется, как |
правило, по |
системе |
||||
“максимум-минимум”. Оборотный фонд |
техоснастки |
предприятия |
||||
складывается из оборотного фонда техоснастки данного вида во всех |
||||||
цехах предприятия, а также страхового |
и |
переходящего |
запаса в |
|||
ЦИС-е. |
|
|
|
|
|
|
Организация инструментального хозяйства в цехах |
|
|||||
|
основного производства |
|
|
|||
Основной |
задачей |
цехового |
информационного |
хозяйс |
является своевременное |
обеспечение рабочих мест данного цеха |
||||||
доброкачественной |
техоснасткой |
при |
минимальных |
разме |
|||
оборотного фонда. Эта задача решается в цехе службой БИХ(бюро |
|||||||
инструментального |
хозяйства) под |
руководством |
заместителя |
||||
начальника |
цеха |
по |
техническим |
|
вопросам. Начальнику |
БИХ |

подчиняются все ИРК(инструментально-раздаточные |
кладовые) |
||||
цеха. |
|
|
|
|
|
Мнемосхема работы инструментального хозяйства в цехах основного |
|||||
производства представлены на рис. 4.5. |
|
|
|||
Цех основного производства |
ПРБ цеха |
|
|
||
|
|
|
|
|
|
|
|
|
План производства |
|
|
|
|
|
на месяц |
|
|
|
|
|
|
Потребность в |
|
|
|
|
Начальник |
ТО и заявки |
|
|
|
|
на ТО |
ОИХ |
|
|
|
|
БИХ |
|
|
|
|
|
|
|
|
|
|
|
Выдача |
Передача |
|
|
|
|
указаний на |
|
|
|
|
|
ремонт ТО и |
ТО на |
|
|
|
|
заточку |
ремонт |
|
|
|
|
инструмента |
|
|
|
Учетные |
|
ИРК |
|
|
|
данные по |
|
|
|
|
|
техоснастке по |
|
|
|
|
|
цеху (ИРК) |
|
|
|
|
|
|
|
|
Получение |
|
|
|
|
|
новой и |
|
|
|
|
|
отремонти |
|
|
|
|
|
рованной |
|
|
|
|
|
ТО |
|
Выдача заявок |
Выдача заявок |
|
|
Передача |
ЗУ |
|
Получение ТО |
инструмента |
|
||
на ремонт ТО |
на заточку |
|
на заточку |
|
|
|
инструмента |
|
из ИРК |
|
|
|
|
|
|
Получение |
|
|
|
|
|
заточенного |
|
|
|
|
|
инструмента |
|
|
|
Производственные |
|
|
|
|
|
|
участки |
|
|
Рис. 4.5. Мнемосхема работы инструментального хозяйства в цехах |
|||||
|
основного производства |
|
|||
ОИХ – отдел инструментального хозяйства, ЗУ – заточной участок, |
|||||
ИРК – инструментально-раздаточные кладовые. |
|
Функции БИХ цеха: Оперативный контроль остатков инструмента и определение потребностью Контроль качества (износа) инструмента и оснастки и определение потребности в заточке или ремонте.
Обеспечение рабочих мест инструментом и надзор за правильностью его использования.
6.2. Организация ремонтного хозяйства
Задачей |
организации |
ремонтного |
хозяйства |
является– |
|
обеспечение |
бесперебойной |
эксплуатации |
оборудования |
заданными точностными характеристиками и эксплуатационными показателями при выполнении плановых заданий.
Годовые затраты на ремонт и техническое обслужива оборудования составляют 10-25 % от первоначальной стоимости оборудования.
В себестоимости продукции ремонт оборудования составляет6-
8 %.
Организация ремонтного хозяйства и технического осмотра оборудования базируется на системе планово-предупредительного ремонта (ППР).
Основные функции ремонтной службы предприятия:
1)паспортизация и аттестация оборудования;
2)разработка техпроцессов ремонта оборудования;
3)планово-предупредительный ремонт оборудования (ППР);
4)модернизация оборудования.
Управление ремонтным хозяйством – это управление, с точки зрения процессной модели предприятия, ресурсами предприятия. В данном случае необходимо рассматривать ресурсы– “Основные средства”.
Ремонтом зданий, сооружений занимаются: отдел капитального строительства (ОКС) и строительно-ремонтный цех (СРЦ).
Отдел главного механика (ОГМ) занимается ремонтом машин и оборудования различного назначения.
Отдел главного энергетика(ОГЭ) занимается ремонтом электрооборудования, электрических, инженерных сетей и сетей связи.
Основная доля ремонтных работ ложится на ОГМ.
На машиностроительных предприятиях используются три основные формы организации выполнения ремонтных работ:
-централизованная;
-децентрализованная;
-смешанная.
При централизованной форме организации все ремонтные
работы |
выполняются |
общезаводскими |
службами |
ремонт |
||
хозяйства, административно и функционально подчиненными ОГМ. |
||||||
При децентрализованной форме организации большая часть |
||||||
ремонтных |
работ |
и |
технического |
обслуживания, изготовление |
||
запасных частей и сменных деталей |
|
выполняются |
ремонтны |
|||
бригадами |
в цехах основного производства, |
а ОГМ осуществляет |
||||
только |
функционально-техническое |
|
руководство |
ремон |
||
производством. Однако |
капитальный |
|
ремонт |
оборудова |
осуществляется |
силами |
ремонтно-механического |
цеха |
специализированных предприятий. |
|
||
При смешанной |
форме организации |
присутствую |
одновременно централизованная и децентрализованная форм организации ремонтных работ.
На практике |
для |
осуществления |
ремонта и |
техничес |
обслуживания технологического и энергетического оборудования, |
||||
средств автоматизации и механизации применяют систему планово- |
||||
предупредительного ремонта (ППР). |
|
|
||
Системой |
ППР |
оборудования |
называется |
совокуп |
запланированных организационных и технических мероприятий по уходу, надзору, обслуживанию и ремонту оборудования.
Это все необходимо для предотвращения прогрессивн нарастающего износа, предотвращения аварий и как следствие, поддержание оборудования в состоянии постоянной готовности к работе.
Виды работ
-техническое обслуживание;
-текущий ремонт;
-средний ремонт;
-капитальный ремонт.
Техническое обслуживание (ТО)- это комплекс операций по поддержанию работоспособности оборудования при использовании
по назначению, хранении и транспортировки(например, осмотры, промывки, проверки на точность и другие).
Текущий ремонт()ТР осуществляется в про эксплуатации для гарантийного обеспечения работоспособности оборудования. В процессе текущего ремонта заменяют отдельные износившиеся или поломанные детали, устраняют дефекты в работе оборудования путем регулировки, выполняют крепежные работы и т.д.
Средний ремонт(СР) – заменяют и восстанавливают основные изношенные детали, проводят сборку, регулирование и испытание под нагрузкой.
Капитальный ремонт (КР)– выполняется полный комплекс работ, обеспечивающих восстановление технико-экономических и эксплуатационных параметров оборудования: точности, жесткости, скорости, производительности и других. Эта работа сопряжена с полной разборкой оборудования.
ТР, СР, КР – выполняют по плану работники ремонтного цеха. |
|
||||||||
В |
|
процессе |
ремонта |
иногда |
делают |
моде |
|||
оборудования. |
|
|
|
|
|
|
|
|
|
В |
характеристиках |
оборудования |
основными |
показателям |
|||||
надежности |
является |
безотказность, характеризуемая |
средним |
||||||
временем |
|
работы |
до |
первого |
|
отказа |
и |
, дол |
|
характеризуемая временем |
жизни |
|
оборудования присоблюдении |
системы ППР.
Ремонты, вызванные отказами или авариями оборудования,
называются аварийными (неплановыми) |
|
|
||
Система |
ППР |
базируется |
на |
, нормативахкоторые |
дифференцируются |
по |
группам |
оборудования. Важнейшими |
нормативами являются:
-ремонтный цикл и его структура;
-межремонтный период;
-категория сложности ремонта;
-трудоемкость ремонтных работ;
-нормы расходов материалов, запасных частей, смазочных и обтирочных материалов;
-продолжительность ремонта;
-нормы запасов быстро изнашиваемых деталей.
Ремонтный цикл – это период работы оборудования от начала эксплуатации до капитального ремонта или между последовательными капитальными ремонтами.
Например, для металлорежущего оборудования
Трц = 24000 βп βм βу βт,
(4.4)
где:
24000 – нормативный ремонтный цикл, станко-часах, установленный по результатам научных исследований; βп – коэффициент, учитывающий тип производства;
βм - коэффициент, учитывающий вид обрабатываемого материала; βу - коэффициент, учитывающий условия эксплуатации; βт - коэффициент, учитывающий размеры оборудования.
Структура ремонтного цикла включает порядок чередования и количество осмотров, проверок и ремонтов.
Например, структура ремонтного цикла между капитальны ремонтами для металлорежущих станков массой до10 тонн состоит из 5 осмотров (О), и 4-х текущих ремонтов (ТР):
КР-О-ТР-О-ТР-О-ТР-О-ТР-О-КР
Межремонтный период определяется по формуле:
Тмр = Трц / nc +nт + 1,
где:
Тмр – межремонтный период; Трц - ремонтный цикл;
nc –число средних ремонтов; nc – число текущих ремонтов.
Периодичность |
технического |
обслуживания |
определяется |
формуле: |
|
|
|
То = Трц / nc +nт + nо + 1,
где: |
|
|
nо – число технических обслуживаний. |
|
|
Категория |
ремонтной |
сложности механической |
электрической части определяется количеством единиц ремонтной сложности по каждой единице технологического оборудования.
Трудоемкость |
ремонтных |
и |
обслуживающих |
ра |
устанавливается на |
единицу ремонтной |
сложности по видам |
работ |
(слесарных , станочных). За единицу ремонтной сложности принята ремонтная сложность условного оборудования, трудоемкость капремонта которого для среднего ремонтного цеха составляет50 часов (для механической части) и 12.5 часов (для энергетической
части). |
|
|
|
|
|
Для |
проведения |
всех |
расчетов |
по |
ППР |
информационные технологии. Разрабатывают и ведут эти планы специальные бюро ППР при ОГМ.
6..3. Организация транспортного хозяйства
Назначение транспортного хозяйства: Перевозка грузов за пределами предприятия и перевозка грузов внутри предприятия.
В транспортном хозяйстве могут быть следующие средст перевозок:
-автомобили;
-железнодорожные вагоны;
-грузовые самолеты;
-водные транспортные средства.
Основным |
показателем |
работы |
транспортного |
|
хозяйс |
||
является |
грузооборот. |
Под |
грузооборотом |
понимается |
общее |
||
количество |
грузов (в тоннах), |
перемещаемое |
в единицу |
времени |
|||
(смена, сутки, месяц, год) на предприятии на единицу длины (км) |
|
||||||
Грузовой |
поток – |
это |
объем |
грузов, перемещаемый в единицу |
|||
времени между двумя пунктами. Для планирования и учета грузовых |
|||||||
потоков |
используют “Шахматку”. По грузообороту и |
грузовым |