
Kopia_kniga_nikiforov_tekhnologia
.pdfначинается движение продольной подачи от кулачка К1 0 . Формула кинематических связей механизмов цепи поворота револьверной головки приведена ниже:
XII − К9 − М4 − VIII − 32/66 − 66/32 − XIV − 32/32 − XV − Д1 − Д2 − XX −
револьверная головка (РГ).
Работа механизмов цепи начинается тогда, когда упор на диске К9 (рис. 1.38) с помощью рычага включит однооборотную муфту М4 . Вращение от вспомогательного управляющего вала VIII через муфту М4 поступает на зубчатое колесо 32, которое через зубчатые колеса 66 − 32 и 32 − 32 сообщает один оборот кривошипному валику XV (рис. 1.39). За первую половину оборота валика суппорт (при неподвижной рейке) отойдет вправо на расстояние, равное удвоенному радиусу R, определяющему положение кривошипного пальца П на диске Ж. Одновременно торцовый кулачок 4, действуя на двуплечий рычаг 5, выводит фиксатор 2 из отверстия револьверной головки 1. После этого палец И диска Д1 входит в один из шести пазов диска Д2 механизма «мальтийский крест» и поворачивает револьверную головку на 60 градусов. Палец двуплечего рычага 5, перемещаясь по кривой спада торцового кулачка 4, освобождает фиксатор 2, который под действием пружины 3 фиксирует револьверную головку на новой позиции. Кривошипный валик XV, продолжая вращаться, за время второй половины оборота переводит кривошип Ж в крайнее правое положение, подготавливая выполнение следующего перехода.
Наладка токарно-револьверного автомата
Наладка станка с кулачковой системой автоматического управления включает следующие действия: расстановку кулачков и упоров на барабанах, размещаемых на распределительном валу; сборку гитар сменных колес в кинематических цепях главного движения и распределительного вала, закрепление режущих инструментов и их наладку на выполнение заданных размеров.
До наладки необходимо выполнить комплекс технологических и конструкторских работ, а также изготовить дисковые кулачки, управляющие движениями суппортов. В начале этих работ по чертежу
121
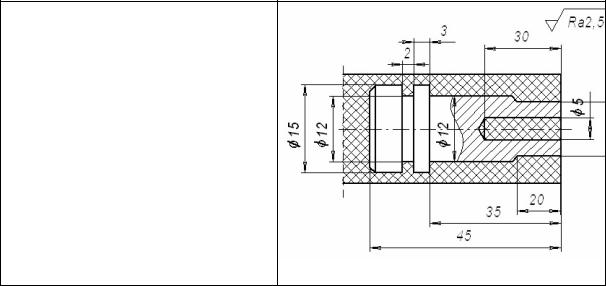
изготавливаемой детали разрабатывают план технологической токарноревольверной автоматной операции с указанием выполнения всех требующихся технологических переходов и всех вспомогательных действий узлов станка в требуемой последовательности. Завершает автоматический цикл отвод верхнего суппорта после отрезки готовой детали отрезным резцом, закрепленным на этом суппорте.
Пример разработки фрагмента последовательности работы узлов станка на данной операции приведен в табл. 1.16.
Таблица 1.16 План токарно-револьверной автоматной операции (фрагмент)
Чертеж детали (с припусками и напусками на
обработку)
№ |
|
Этапы |
Действующий узел |
Режущий |
||
пп |
автоматического цикла |
станка |
|
инструмент |
||
|
|
|
|
|
|
|
1 |
Поворот |
револьверной |
Револьверная |
|
|
|
|
головки |
и |
установка |
головка |
|
|
|
упора в рабочую позицию |
|
|
|
||
|
|
|
|
|
|
|
2 |
Подвод |
|
|
Револьверный |
|
|
|
|
|
|
суппорт |
|
|
|
|
|
|
|
|
|
3 |
Перемещение |
прутка до |
Механизмы |
пере- |
|
|
|
упора и его закрепление |
мещения и |
зак- |
|
||
|
|
|
|
репления прутка |
|
|
|
|
|
|
|
|
|
4 |
Быстрый отвод |
|
Револьверный |
|
|
|
|
|
|
|
суппорт |
|
|
|
|
|
|
|
|
|
|
Подвод |
|
|
Задний суппорт |
|
122
№ |
Этапы |
Действующий узел |
Режущий |
пп |
автоматического цикла |
станка |
инструмент |
|
|
|
|
5 |
Подрезание торца |
То же |
Подрезной резец |
|
Поворот |
Револьверная |
|
|
|
головка |
|
|
|
|
|
6 |
Подвод |
Револьверный |
|
|
|
суппорт |
|
|
|
|
|
7 |
Точение d = 15 мм |
То же |
Проходной резец |
8 |
И т. д. |
|
|
|
|
|
|
После разработки плана операции производят расчет времени, которое требуется на выполнение отдельных переходов, и в целом полное время изготовления детали Тшт. На основе этого времени определяют частоту вращения главного распределительного вала по формуле nXII = 1/Тшт и определяют параметры колес гитары сменных зубчатых колес А/В (рис. 1.38), устанавливаемых на валах IV и V. План операции позволяет разработать циклограмму операции, представляемую в виде схемы последовательность работы узлов станка и временные интервалы их действий, и приступить к проектированию управляющих кулачков К5, К6 ,
К7 , К1 0.
По окончании конструкторской разработки управляющих кулачков их изготавливают в инструментальном цехе предприятия. Только после готовности кулачков можно приступить к непосредственной наладке станка на выполнение заданной операции.
Содержание работы
Работа включает: изучение устройства и назначения токарноревольверного автомата модели 1А118 и его узлов, механизмов, знакомства с кинематической схемой, разработку последовательности работы узлов станка при изготовлении конкретной детали в соответствии с индивидуальным заданием, оформление этой последовательности в виде технологического документа и подготовку отчета.
Порядок проведения работы
1. Изучите назначение и устройство токарно-револьверного автомата модели 1А118.
123
2. Проследите за изготовлением детали учебным мастером при работе станка в автоматическом режиме, обратите внимание на последовательность работы основных узлов и механизмов станка, опишите эту последовательность преподавателю.
3. Получите от преподавателя индивидуальное задание и разработайте совместно с преподавателем план токарно-револьверной автоматной операции детали по этому заданию.
Примечания. При разработке плана операции учитывайте следующие особенности работы токарно-револьверного автомата: допустимая ширина лезвия фасонного резца не должна превышать 6 мм; допустимая глубина резания резцом не может быть более 2 мм; изготовление резьбового отверстия выполняют за три перехода: сверление, зенкование фаски, нарезание резьбы.
Одновременно реализуемые переходы указывайте в одной позиции плана операции.
Содержание отчета
1.Наименование работы.
2.Номер, формулировка и исходные данные индивидуального задания (табл. 1.17).
Индивидуальное задание: «Вычертить и описать работу фрагмента кинематической схемы токарно-револьверного автомата, обеспечивающего функционирование рабочего узла станка «……..». Разработать план токарно-револьверной автоматной операции изготовления детали и представить его в виде таблицы «План токарно-револьверной автоматной операции».
3.Фрагмент кинематической схемы станка, относящийся к кинематической цепи заданного преподавателем механизма; описание его работы: назначение, способ включения, способ изменения скорости движения узла, формула кинематических связей.
4.Чертеж детали по индивидуальному заданию и план токарно-
револьверной автоматной операции для ее изготовления по форме табл. 1.16.
124
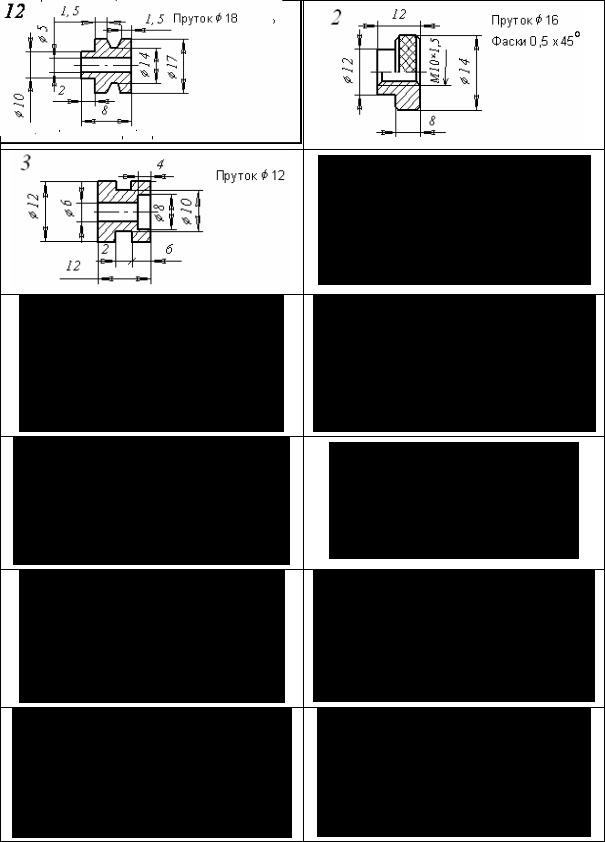
Таблица 1.17
Индивидуальные задания
125
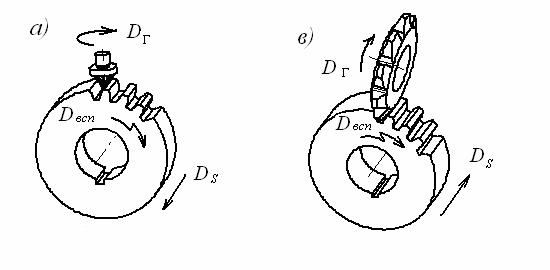
1 . 9 . НАЗНАЧЕНИЕ И УСТРОЙСТВО ЗУБОФРЕЗЕРНОГО СТАНКА
Цель работы: знания методов нарезания венцов зубчатых колес, устройства, назначения и кинематической схемы зубофрезерного станка модели 5310; умения читать кинематическую схему станка, рассчитывать число зубьев и подбирать сменные зубчатые колеса гитары скоростей, гитар цепей движений обкатки и подачи при нарезании прямозубого зубчатого колеса.
Методы нарезания венцов зубчатых колес
Образование зубьев зубчатого колеса путем удаления материала впадины режущим инструментом выполняют фрезерованием, строганием, долблением, протягиванием, шевингованием и шлифованием. При этом формообразование профиля боковых поверхностей зубьев может осуществляться двумя методами: копированием пальцевой (рис. 1.40, а) и дисковой (рис. 1.40, б) модульными фрезами и обкаткой (рис. 1.41).
Рис. 1.40. Схемы обработки венцов зубчатых колес методом копирования
Метод копирования характеризуется тем, что процесс фрезерования осуществляется режущим инструментом, профиль режущей кромки которого соответствует профилю впадины зуба нарезаемого колеса. При изготовлении зубчатых колес методом обкатки нарезаемому колесу и зуборезному инструменту сообщают кинематически согласованные движения, совокупность которых воспроизводит движения звеньев зубчатой, реечной или червячной передачи. В связи с этим боковая поверхность зуба на венце
126
заготовки образуется как огибающая последовательных положений режущих кромок инструмента в их движении относительно заготовки зубчатого колеса.
Нарезание зубчатого венца методом обкатки осуществляют различными технологическими способами: зубодолблением (рис. 1.41, а, б), зубофрезерованием (рис. 1.41, в) и зубостроганием (рис. 1.41, г). Наибольшее распространение в промышленности получило зубофрезерование.
Зубофрезерованием по методу обкатки можно нарезать венцы цилиндрических зубчатых колес с прямыми (рис. 1.41, в) и винтовыми (рис. 1.42, а) зубьями, а также венцы червячных колес (рис. 1.42, б). Режущим инструментом в этих случаях является червячная модульная фреза, которая представляет собой винт с одно– или многозаходной трапецеидальной резьбой и несколькими наклонными стружечными канавками, служащими для образования режущих лезвий и размещения стружки.
Главным движением резания при зубофрезеровании методом обкатки является вращение фрезы Dг. Заготовка в этом случае совершает вращательное (круговое) движение DS кр с частотой вращения nо, об/мин, так, что
nо = nф k/z , |
(1.34) |
где nф – частота вращения фрезы, об/мин; k – число заходов фрезы, z – число зубьев нарезаемого зубчатого колеса.
При изготовлении цилиндрических (прямозубых и винтовых) колес по методу обкатки фрезе наряду с главным движением резания Dг сообщают движение вертикальной подачи DS в вдоль оси заготовки. Введение этого движения обеспечивает нарезание зубьев на всей ширине венца.
Для получения винтовых зубьев заготовке помимо движений обкатки (согласованных по частоте вращений фрезы и заготовки) и вертикальной подачи фрезы DS в необходимо сообщить дополнительное вращение ∆DS кр. Скорость его должна быть согласована с вертикальной подачей Sв следующим образом: при опускании фрезы на шаг винтовой впадины зубчатого колеса заготовка должна дополнительно повернуться на один оборот.
127
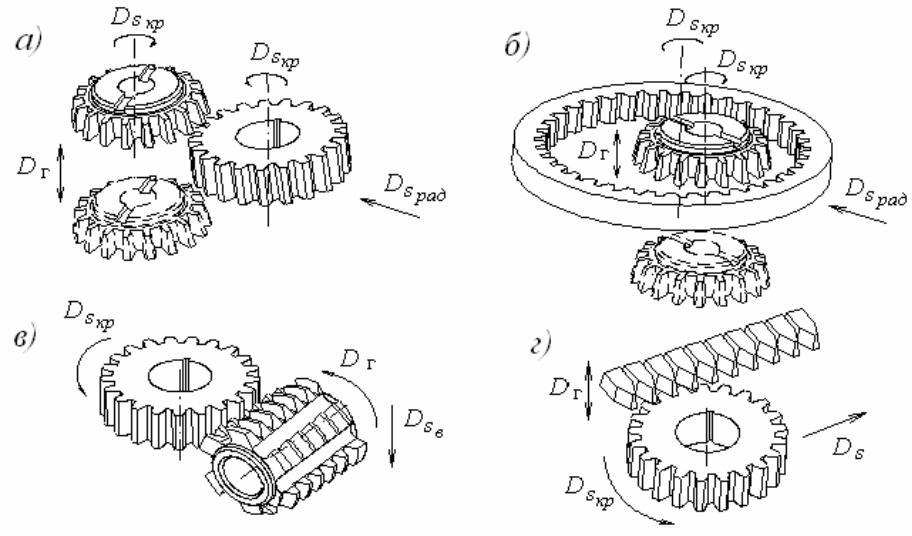
128
Рис. 1.41. Схемы обработки венцов зубчатых колес методом обкатки

Рис. 1.42. Схемы фрезерования венцов цилиндрических (а) и червячных (б) зубчатых колес
При нарезании цилиндрических зубчатых колес фрезу устанавливают так, чтобы передняя поверхность ее лезвия, образованная пересечением стружечной канавкой витка фрезы, в зоне резания была перпендикулярна направлению впадины нарезаемого колеса. В связи с этим шпиндель станка, на котором закрепляют червячную фрезу, поворачивают на угол ω, определяемый направлениями и углами подъема (наклона) витков фрезы µф и зубьев изготавливаемого колеса µк.
При принятом на рис. 1.42, а направлении положительных значений углов ω значение этого угла определяют по формулам, приведенным в таблице 1.18.
Таблица 1.18 Формулы определения угла поворота червячной фрезы при нарезании
колес c винтовыми зубьями
№ |
Направление |
Направление |
Формула определения |
|
подъема витков |
||||
п.п. |
наклона зуба колеса |
угла ω |
||
|
фрезы |
|
|
|
1 |
правое |
правое |
ω = µ ф – µ к |
|
2 |
левое |
ω = µ ф + µ к |
||
|
||||
3 |
левое |
правое |
ω = –µ ф – µ к |
|
4 |
левое |
ω = –µ ф + µ к |
||
|
129
Примечание. Правое и левое направления углов определяют по правилам правого и левого буравчика.
Нарезание венцов червячных зубчатых колес зубофрезерованием методом обкатки имеет свою специфику по отношению к изготовлению цилиндрических колес. Движение вертикальной подачи фрезы DS в в этом случае отсутствует. Угол наклона оси фрезы ω принимают равным нулю. Фрезу устанавливают так, что ее ось располагается на середине венца колеса. Заготовке при резании сообщают движение радиальной подачи DS р (рис. 1.42, б). К особенностям этого способа следует отнести и то, что червячная фреза по своим размерам (диаметру), профилю режущих кромок и числу заходов должна соответствовать червяку, в зацеплении с которым будет работать изготавливаемое зубчатое колесо.
Назначение зубофрезерного станка и его основные узлы
Зубофрезерный станок модели 5310 предназначен для нарезания цилиндрических прямозубых и винтовых, а также червячных колес методом обкатки. При чистовом фрезеровании червячной фрезой достигается седьмая – восьмая степени точности зубчатого венца и шероховатость поверхностей зубьев по параметру Rа = 6,3–1,6 мкм. Станок применяют в условиях серийного производства при нарезании зубчатых колес диаметрами от 60 до 180 мм с модулями от 1 до 4 мм.
Внешний вид зубофрезерного станка показан на рис. 1.43. Станок имеет сборную станину, состоящую из основания 1 и вертикальной стойки 13. На горизонтальных направляющих станины размещены салазки 2, несущие на себе круглый вращающийся стол 3 и стойку 5 с опорным кронштейном 8. Заготовку устанавливают на оправке 4, нижний конец которой центрируют и закрепляют в отверстии стола 3, а верхний конец — в опорном кронштейне 8. Кронштейн крепится на стойке 5 рукояткой 6.
На вертикальных направляющих стойки 13 находится фрезерный суппорт 12 с поворотной частью 11, в которой смонтирован шпиндель 9. Фрезу 10 устанавливают на двухопорной оправке, закрепляемой в отверстии шпинделя и на подшипниковой опоре поворотной части 11. На передней стенке стойки 13 расположены пульты управления станком 14 и 17. Стойки 5 и 13 соединены сверху балкой 7, обеспечивающей станку повышенную жесткость.
130