
Тут есть жесткость воды
.pdf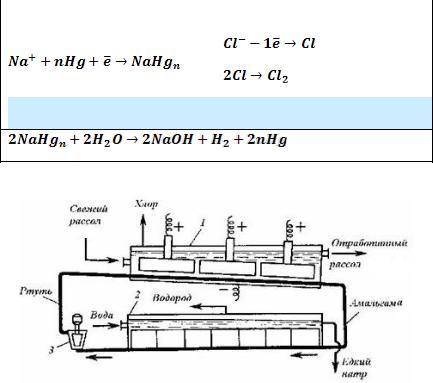
Электролизёр представляет собой электролитическую ванну. Корпус ванны разделён на катодное 3 и анодное 5 пространства пористой диафрагмой 1. Диафрагма плотно прилегает к перфорированному стальному катоду 2. В анодном пространстве расположены графитовые аноды 4.
Очищенный раствор NaCl (рассол) концентрацией 305-310 г/л подают в анодное пространство. Вследствие гидростатического давления он фильтруется через диафрагму и катод в катодное пространство. Из катодного пространства непрерывно отводят водород и раствор гидроксида натрия, а из анодного – газообразный хлор.
Образовавшийся хлор-газ содержит 95-96% Сl2. Его охлаждают до 20 С (при этом конденсируется влага) и осушают концентрированной серной кислотой. Катодный продукт – раствор гидроксида натрия – содержит 120-140 г/л NaOH и 170-180 г/л неразложившегося NaCl. Раствор выпаривают, при этом NaCl выпадает в осадок, т.к. его растворимость резко снижается с увеличением концентрации NaОН. После выпарки и плавки получают безводный гидроксид натрия (едкий натр).
Газообразные продукты – хлор и водород при любом способе производства отличаются высокой чистотой. При электролизе с ртутным катодом и третий продукт – раствор гидроксида натрия имеет высокую концентрацию NaОН и является химически чистым. Щёлочь, полученная диафрагменным методом, содержит примеси NaCl.
Электролиз с ртутным катодом. В электролизёрах с ртутным катодом на аноде также как и в первом случае разряжаются ионы хлора. На ртутном катоде разряжаются только ионы натрия Na+. Выделившийся металлический натрий растворяется в ртути, образуя амальгаму NaHgn. Амальгаму натрия затем разлагают водой, при этом выделяются гидроксид натрия, водород и ртуть. Ртуть вновь поступает на электролиз.
Катод – жидкая ртуть |
Анод - графит |
|
|
|
|
Разлагатель
Схема электролизёра с ртутным катодом представлена на рис. 6.29.
Рис. 6.29. Схема электролизёра с жидким ртутным катодом: 1 – электролизёр; 2 – разлагатель; 3 – насос.
340
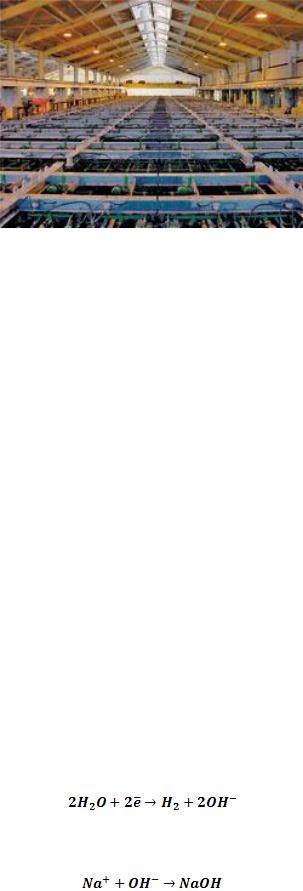
Рис. 6.30. Ртутные электролизёры.
Самым распространённым является горизонтальный электролизёр с ртутным катодом. Он представляет собой стальной аппарат прямоугольного сечения, герметично закрытый крышкой. В крышке расположены отверстия, в которых укреплены графитовые аноды. Дно ванны имеет небольшой уклон, по нему непрерывно движется тонкий слой ртути. Таким образом, дно ванны является катодом.
С передней стороны в электролизёр подают свежий рассол, содержащий 310 г/л NaCl. В процессе электролиза часть поваренной соли разлагается с образованием хлора и амальгамы натрия. Хлор отводят через крышку ванны, а амальгаму натрия разлагают чистой горячей водой в разлагателе. Образующийся водород поступает в коллектор водорода, а раствор, содержащий 50% NaOH, выводится как готовый продукт. Отработанный рассол донасыщают хлоридом натрия и возвращают в электролизёр.
Электролиз с ртутным катодом позволяет получать очень чистую щёлочь. Однако, использование ртути чрезвычайно вредно для людей и окружающей среды. Поэтому для получения химически чистых растворов гидроксида натрия стали применять электролиз раствора NaCl с ионообменной мембраной.
Мембранный метод. Особенностью этого метода является наличие нефильтрующей полимерной мембраны, которая разделяет анодное и катодное пространство в электролизёре (рис. 6.31.). Мембрана выполняет роль фильтра для селективного переноса ионов натрия из анодного пространства в катодное. Насыщенный рассол подают в анодную камеру. Ионообменная мембрана предотвращает попадание хлорид-ионов в катодную камеру и препятствует переносу гидроксид-ионов в анодную камеру. Хлор выделяется на аноде и выводится из анодной камеры с обеднённым рассолом. Ионы натрия и частично вода проходят через мембрану в катодную камеру. Сюда же подают воду в количестве, необходимом для образования щёлочи заданной концентрации. В катодном пространстве происходит восстановление воды с выделением водорода и образованием гидроксид-ионов:
Перенесённые из анодного пространства через мембрану катионы натрия образуют с гидроксид-ионами щёлочь:
Полученная щёлочь выводится из катодной камеры.
341
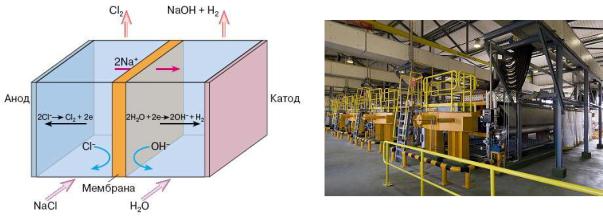
Рис.6.32. Общий вид цеха с Рис. 6.31. Схема мембранного электролизёра. мембранными электролизёрами.
Мембранный способ имеет значительные преимущества перед диафрагменным, поскольку позволяет получать щёлочь высокой чистоты. По сравнению же с ртутным методом мембранный метод более сложен по аппаратурному оформлению и эксплуатации, но значительно безопаснее. В мембранном процессе не используют ртуть, что исключает загрязнение окружающей среды.
Переработка щёлока в гидроксид натрия. Электролитический щёлок, получаемый электролизом с ртутным катодом и мембранным методом, не содержит хлорида натрия. Для получения из него гидроксида натрия щелок упаривают до заданной концентрации и затем обезвоживают.
Щёлок, получаемый электролизом с железным катодом, содержит 170—200 г/л хлорида натрия. Процесс переработки этого щелока заключается в выделении из него хлорида натрия, возвращаемого в технологический процесс, упаривании раствора и обезвоживании полученного плава едкого натра для получения твердого продукта. Выделение хлорида натрия из щелока основано на его изотермической кристаллизации. Растворимость хлорида натрия в водных растворах гидроксида натрия понижается с увеличением концентрации последнего. Поэтому при упаривании щелока из него выпадает растворенный в нем хлорид натрия. Упаривание до концентрации выше 50% масс. практически нецелесообразно, так как за этим пределом растворимость хлорида натрия почти не изменяется. Выделившийся хлорид натрия после охлаждения раствора отделяют на фильтре, промывают и вновь используют для электролиза (обратная соль).
Для получения твёрдой щёлочи очищенный от хлорида натрия и упаренный щёлок обезвоживают (плавят) в котлах, обогреваемых топочными газами, или в вакуумвыпарных установках непрерывного действия, обогреваемых высококипящим органическим теплоносителем.
Технический гидроксид натрия (едкий натр) выпускают в твердом виде (плавленный и в виде чешуек) с содержанием NaOH не менее 95%, и в виде водного раствора.
Технологическая схема производства. Технологическая схема (рис. 6.33.) включает процессы получения рассола, его очистку от примесей, сам процесс электролиза (основная стадия), выпарку раствора каустической соды, и первичную переработку хлора и водорода
– охлаждение, осушку и компримирование.
342
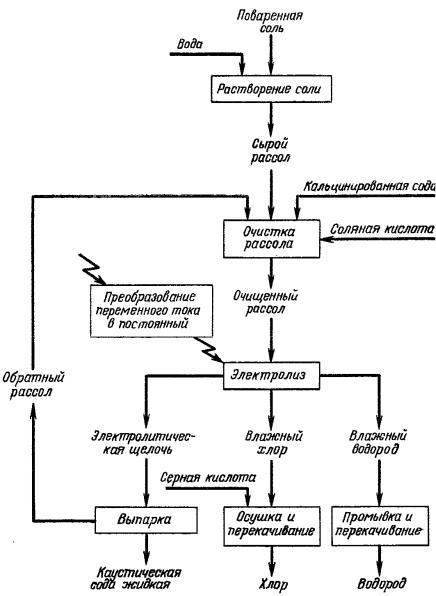
Твёрдая поваренная соль хранится на складе соли. Её растворяют и полученный рассол передают в цех очистки. Концентрация рассола обычно 310 г/л NaCl. Этот рассол предварительно очищают от химических примесей – ионов Ca2+ и Mg2+ - путём перевода их в нерастворимые соединения CaCO3 и Mg(OH)2.
Рис. 6.33. Принципиальная схема производства хлора, каустической соды и водорода
Основной процесс получения хлора, каустической соды и водорода осуществляется в цехе электролиза. Постоянный ток подводится к электролизёрам с преобразовательной подстанции, находящейся рядом с цехом.
Влажный хлор из электролизёров поступает в отделение осушки серной кислотой, а затем компрессорами перекачивается на склад или потребителям. Водород охлаждают водой и передают потребителям.
Электролитическую щёлочь из цеха электролиза перекачивают в цех выпарки и в виде 42-50%-ного раствора передают на склад или в отделение плавки.
343

На процесс электролиза существенное влияние оказывает температура. Обычно электролизёры работают при температуре 95 С. При такой температуре давление насыщенных водяных паров возрастает, поэтому с газами уносится (испаряется) большое количество влаги. Кроме того, часть воды расходуется в процессе электролиза. В связи с этим при увеличении температуры повышается концентрация гидроксида натрия в электролитической щёлочи.
6.3.3. Гальванотехника
Электрохимические технологии, связанные с нанесением покрытий, называют гальванотехникой. Гальванотехнические работы осуществляют в гальванических цехах.
Наибольшее распространение в технике получили операции цинкования, меднения, никелирования и хромирования. Специализированные предприятия используют осаждение других металлов – серебрение, золочение, платинирование и др. Эти операции осуществляют в гальванических ваннах.
Покрытия классифицируют по назначению:
1.защитные покрытия, которые предназначены для повышения коррозионной устойчивости металлических (стальных) изделий (например, цинковые покрытия);
2.защитно-декоративные покрытия обеспечивают и защиту от атмосферной коррозии, и одновременно придают изделию декоративный вид (например, никелевые и хромовые покрытия);
3.покрытия с оптическими свойствами могут быть светоотражающими (серебряные зеркала) или светопоглощающими (чёрный хром);
4.электропроводящие покрытия используют для обеспечения надёжности электрических контактов; для этих целей используют никелевые покрытия, а также покрытия из серебра, золота и других благородных металлов;
5.неметаллические покрытия (фосфатные, оксидные и др.).
Гальваническое покрытие представляет собой металлическую плёнку, которая наносится на поверхность металлических и других изделий
В основе технологии нанесения покрытий лежит электрохимическая реакция, протекающая на катоде:
Выделяющийся металл формируется в виде тонкого слоя (покрытия) на поверхности детали (рис. 6.34.).
Сущность гальванического процесса заключается в том, что обрабатываемое изделие присоединяют в качестве катода к отрицательному полюсу источника постоянного тока и погружают в ванну с электролитом. Анодом, присоединяемым к положительному полюсу, служат пластины из металла, которым необходимо покрыть изделие. При прохождении постоянного тока через электролит на катоде разряжаются положительно заряженные ионы и выделяется металл. Металл анода растворяется и переходит в раствор в виде ионов металла вместо выделившихся на катоде.
344
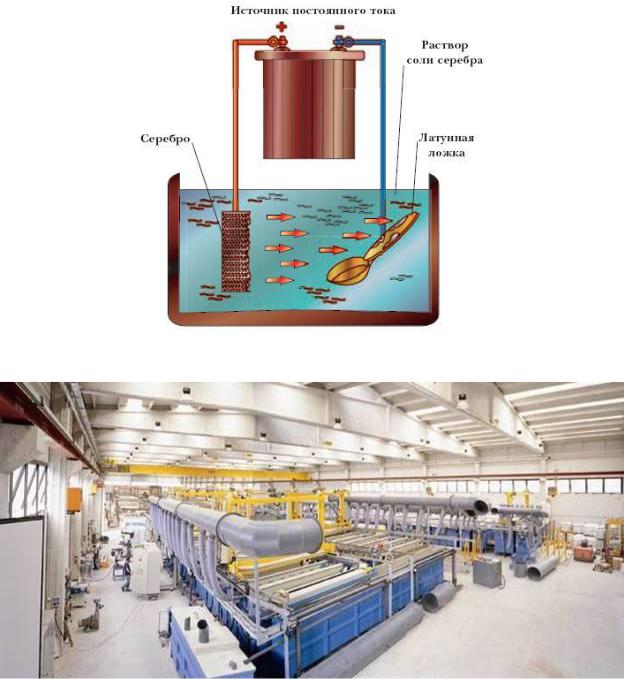
Рис. 6.34. Схема ванны для нанесения гальванического покрытия
Рис. 6.35. Общий вид гальванического цеха.
Существует две области гальванотехники – гальваностегия и гальванопластика.
К гальваностегии относятся процессы осаждения тонкого слоя металла на заготовку.
Гальванопластика основана на электролизе водных растворов солей металлов, которые в процессе электролиза выделяют металл, осаждающийся толстым слоем на поверхности деталей. Гальванопластику используют для получения точных металлических копий изделий.
345
6.3.4. Вопросы для самоконтроля по теме «Технология электрохимических производств»
Какие процессы относятся к электрохимическим процессам?
Как классифицируют электрохимические процессы?
Законы электролиза.
Напишите реакции , лежащие в основе получения хлора, гидроксида натрия и водорода электрохимическим методом на твёрдом железном катоде, жидком катоде и в мембранных электролизёрах.
Перечислите области применения хлора, водорода и каустической соды.
Назовите основные типы электролизёров, нарисуйте их схемы и объясните принцип работы.
Назовите основные стадии технологического процесса получения хлора, каустической соды и водорода электрохимическим методом.
Дайте определение гальванотехники.
Области применения гальванотехнических процессов.
На каких процессах основано нанесение гальванических покрытий?
Нарисуйте схему ванны для нанесения гальванического покрытия.
346
7.ТЕХНОЛОГИЯ ПРОИЗВОДСТВА ОРГАНИЧЕСКИХ ВЕЩЕСТВ
7.1.ПРОИЗВОДСТВО БЕНЗОЙНОЙ КИСЛОТЫ
7.1.1. Общая характеристика производства и применения бензойной кислоты.
Основными промышленными способами производства бензойной кислоты являются:
жидкофазное каталитическое окисление толуола кислородосодержащим газом;
синтез бензойной кислоты на основе галоидопроизводных толуола;
декарбоксилирование фталевого ангидрида.
Из описанных в литературе за последнее десятилетие различных способов получения бензойной кислоты, не нашедших до настоящего времени промышленного развития, следует отметить: жидкофазное каталитическое окисление толуола кислородосодержащим газом в среде монокарбоновой алифатической кислоты с выходом бензойной кислоты 70 – 90 %; жидкофазное каталитическое окисление кумола кислородом в пропионовой кислоте с выходом бензойной кислоты 80 – 90 %; синтез бензойной кислоты из хлоробензола, окиси углерода и воды под давлением 500-700 атм с выходом бензойной кислоты 80%; окисление толуола соединениями серы с выходом бензойной кислоты 60-90%.
Кроме того известен ряд старых способов получения бензойной кислоты, малоперспективных для создания крупнотоннажных производств, например, омыление бензонитрила, карбоксилирование и карбонилирование бензола, каталитическое окисление толуола воздухом в паровой среде, жидкофазное окисление толуола различными химическими окислителями: азотной кислотой, соединениями хрома, маргонцовокислым калием, двуокисью марганца и гипохлоридом натрия.
Первые публикации по разработке промышленного способа получения бензойной кислоты жидкофазным окислением толуола кислородосодержащим газом относятся к началу 40-х годов. В годы второй мировой войны процесс был осуществлен в Германии в промышленном масштабе. В настоящее время это самый распространённый и экономичный способ крупнотоннажного производства бензойной кислоты. Различные варианты технологических схем для синтеза бензойной кислоты окислением толуола кислородом воздуха разработаны и введены в эксплуатацию фирмами США, Японии, России.
Получение бензойной кислоты жидкофазным окислением толуола описывается следующим уравнением:
С6Н5СН3 + 1,5О2 = С6Н5СООН + Н2О – 163 ккал
Реакция толуола протекает по цепному механизму с вырожденным разветвлением и представляет собой сложную совокупность последовательных и параллельных элементарных стадий. Активными центрами элементарных реакций являются свободные радикалы различного строения и различной реакционной способности, причем качественный и количественный составы этих лабильных частиц непрерывно изменяются
347
по мере развития процесса окисления вследствие присутствия в зоне реакции продуктов химического превращения, которые участвуют в сложном механизме окисления толуола.
Всоставе оксидата различными исследователями, в зависимости от условий проведения процесса, идентифицировано свыше 30 компонентов, основными из которых, помимо бензойной кислоты и непрореагировавшего толуола, являются бензилбензоат, бензальдегид, бензиловый спирт, бензилацетат и дифенил.
Вряде патентов окисление толуола предложено проводить в присутствии промотирующих и инициирующих добавок. В качестве промоторов катализатора окисления толуола запатентованы органические и неорганические бромиды.
Области применения бензойной кислоты
1. |
Получение |
солей-катализаторов |
2. |
Фармацевтические средства |
|
окисления, |
поликонденсации, |
|
|
|
сополимеризации, |
|
|
|
|
переэтерификации |
|
|
|
3. |
Капролактам |
4. |
Бензол хлорид |
|
5. |
Перефторат калия |
6. |
Красители |
|
7. |
Перекись бензоила |
8. |
Косметические препараты |
|
9. |
Салициловая кислота |
10. |
Аналитическая химия |
11.Коррозийная защита металлов
Антикоррозионные композиции
Ингибиторы коррозии
Щелочестойкие полиэфирные покрытия
12.Сельское хозяйство и пищевая промышленность
Химические средства защиты растений
Гигиенические препараты для животных
Консервант пищевых продуктов
Бактерицидные упаковочные материалы
Консервант растительного сырья и кормов животного происхождения
13.Лакокрасочная промышленность
Составляющие универсальной колероварочной пасты
Для замедления загустевания красок
1.Полимерная и резиновая промышленность
|
Эластичные |
полимеры |
|
Производство |
|
Стабилизатор |
|
|
|
|
модифицированных |
галогеносодержащих |
|
|
Изоляционные лаки |
|
алкидных смол |
смол |
|
|
|
Синтетический клей |
|
Матирование |
|
Отвердитель |
|
|
Ингредиент |
резиновых |
|
поверхности |
эпоксидных смол |
|
|
смесей |
|
|
полиэтилен |
|
Вулканиза |
|
|
|
|
348 |
|
|
|
Загуститель |
|
терефталатного |
|
ция |
|
ненасыщенных |
|
волокна |
|
галогеносодержащи |
|
полиэфирных смол |
|
Замедлитель |
|
х эластомеров |
|
Регулятор |
|
подвулканизации |
|
Пластификат |
|
молекулярного веса |
|
Нуклирующее вещество |
|
оры синтетических |
|
полиамидов |
|
при производстве |
|
смол и резин |
|
|
|
пенопластов |
|
|
14. Производство горюче-смазочных материалов |
|
|
|
|
|
|||||||
|
Термостатильные смазки |
|
|
|
Антидетонационная |
присадка |
к |
|||||
|
Пластичные смазки |
|
|
|
|
моторному топливу |
|
|
|
|||
|
|
|
|
|
|
|
|
|
|
|||
|
|
|
|
|
|
|
Эмульгатор |
для |
эмульсионных |
|||
Антиобледенители иантифризы |
|
|
смазочных масел |
|
|
|
||||||
|
|
|
|
|
|
|
|
|
|
|||
|
Стабилизаторы смазочных масел |
|
|
Стабилизатор |
твердых |
ракетных |
||||||
|
|
|
|
|
|
|
топлив |
|
|
|
|
|
15. Целлюлозо-бумажная и текстильная промышленность |
|
|
|
|
|
|||||||
|
Копировальные бумаги |
|
|
Пластификаторы бумаг и эфиров |
||||||||
|
Получение |
целлюлозы |
из |
|
целлюлозы |
|
|
|
|
|
||
|
|
|
|
|
|
|
|
|||||
|
лигноцеллюлозных материалов |
|
|
Очистка |
оксиэтиловых |
эфиров |
||||||
|
|
|
|
|
|
целлюлозы от щелочи |
|
|
|
|||
Водоотталкивающая |
отделка |
|
|
|
|
|
|
|
|
|||
|
текстильных материалов |
|
|
|
Гомогенизирующее |
вещество |
в |
моющих композициях
Свойства бензойной кислоты (С6Н5СООН)
Бензойная кислота представляет собой белые блестящие моноклинные листочки или иглы, бензоат натрия – белый кристаллический порошок. В 100 мл воды при температуре 23 °С растворяется 63 г бензоата натрия, а бензойной кислоты всего лишь 0,34 г. Бензойная кислота лучше растворяется в жирных маслах: в 100 г жирных масел растворяется 1-2 г бензойной кислоты.
Бензойная кислота и, в меньшей мере, ее соли обладают фунгистическими и фунгистатическими свойствами, они активны по отношению к ряду микроорганизмов. Бензойная кислота подавляет жизнедеятельность дрожжей, менее интенсивно действуют на бактерии масляно-кислого брожения и почти совсем не влияет на развитие молочнокислого брожения, мало – на бактерии уксуснокислого брожения и почти совсем не влияет на развитие молочнокислых бактерий и плесеней.
Бензойная кислота и ее соли подавляют в микробных клетках активность ферментов, ответственных за окислительно-восстановительные реакции, а также ферментов, расщепляющих жиры и крахмал. Эти консерванты подавляют рост дрожжей и бактерий масляно-кислого брожения. На бактерии уксуснокислого брожения их влияние несколько ниже и совсем незначительно – на молочнокислую флору и плесень. Наиболее эффективно их действие в кислой среде – при рН не выше 5.
349