
kontemirov
.pdf1) Технологические процессы по характеру ориентации заготовок относительно инструментов с целью обеспечения однозначной кинематической связи их взаимного движения при обработке можно подразделить на два класса.
К первому классу относятся процессы, при осуществлении которых требуется обязательная ориентация заготовок относительно рабочего инструмента, а характер их взаимного движения обусловлен строгой кинематической зависимостью. К этому классу относится большинство процессов механической обработки и сборки. Автоматизация технологических процессов первого класса наиболее сложная и трудоемкая.
Ко второму классу причисляют процессы, при выполнении которых не требуется ориентация заготовок, а рабочий инструмент представляет собой активную обрабатывающую среду. К таким процессам можно отнести термическую обработку мелких деталей, выполняемую в специальной таре; мойку, сушку, травление в кислотных ваннах; окрашивание методом погружения; очистка деталей в галтовочных барабанах; полирование в свободном абразиве и т.п. Так как при выполнении таких процессов отсутствует кинематическая связь между движением инструмента (среды) и заготовки, а также необходимость ориентации в пространстве последних, автоматизация процессов второго класса более проста.
Существуют и технологические процессы промежуточного класса. В одном случае заготовки должны занимать в пространстве строго определенное положение, а рабочий инструмент представляет собой активную обрабатывающую среду (промежуточный класс 1/2). К таким процессам можно отнести окрашивание методом пульверизации, напыление покрытий, некоторые виды термической обработки, например, длинных валов в вертикальном положении или в «заневоленном» состоянии в специальном приспособлении и т.п. В других случаях обрабатываемый материал подается без ориентирующих движений в рабочую зону инструмента, занимающего строго определенное, зафиксированное положение в пространстве (промежуточный класс 2/1). Примерами таких технологических процессов могут служить прессование заготовок из пластмасс, литье в песчаную форму станин металлорежущих станков (направляющими вниз, так как в нижней части отливки будет наиболее качественный и плотный металл, а шлаки как более легкие фракции накапливаются в менее ответственной части станины).
С точки зрения непрерывности технологические процессы можно разделить на три вида:
·дискретные;
·непрерывные и
·роторные.
Первый вид технологических процессов выполняется на станках-автоматах и полуавтоматах дискретного действия, характеризующихся строгой цикличностью выполняемых операций (или переходов). Для этого вида технологических процессов обязательно наличие вспомогательного неперекрываемого времени в структуре циклового (операционного) времени на обработку. То есть время, затрачиваемое на выполнение вспомогательных переходов загрузки-выгрузки, холостого перемещения рабочих органов, деления, смены позиций и т.д. в дискретных автоматических машинах не совмещены полностью с временем выполнения основных переходов. Таким образом цикловая производительность дискретных технологических машин составляет

,
где tМ и tВ - соответственно машинное (основное) и вспомогательное времена.
Повышение производительности в дискретных технологических машинах и системах возможно за счет сокращения машинного времени путем форсирования режимов обработки, уменьшения рабочих ходов, а также за счет сокращения вспомогательного времени при уменьшении количества и величин холостых ходов рабочих органов, совмещения их во времени с рабочими ходами.
В пределе, при полном совмещении вспомогательных переходов с основными, машины дискретного действия превращаются в технологические автоматы непрерывного действия, реализующие второй вид технологических процессов. При этом обработка или сборка осуществляются в течении определенного промежутка времени без периодической остановки оборудования для выполнения вспомогательных переходов установки заготовок и съема деталей (изделий). По непрерывным технологическим процессам могут осуществляться:
·волочение проволоки или прутков;
·непрерывная безоправная навивка спиральных пружин;
·пескоструйная или дробеструйная очистка заготовок от окалины;
·травление, лужение или эмалирование проводов;
·торцовое фрезерование плоскостей деталей на карусельно-фрезерных станках;
·конвейерное протягивание наружных поверхностей;
·бесцентровое шлифование;
·нарезание резьб гаечными метчиками и т.д.
На рис. 1.6. приведены примеры некоторых из перечисленных непрерывных технологических процессов.
Для этого вида автоматизированных технологических процессов производительность определяется зависимостью
,
где VТ - скорость технологического движения, например скорость подачи VS при бесцентровом шлифовании или скорость резания V при непрерывном конвейерном протягивании;
l, lP - соответственно размер обрабатываемой поверхности и конструктивный или технологический разрыв между смежными заготовками в направлении вектора скорость технологического движения.
Наивысшая производительность машин непрерывного действия, равная технологической производительности метода обработки, будет иметь место при движении заготовок через рабочее пространство непрерывным потоком, то есть при lP=0.
Данный вид технологических процессов характеризуется высокой производительностью и возможностью относительно легкой автоматизации по сравнению с дискретными
процессами. Он достаточно широко применяется в массовом и крупносерийном автоматизированных производствах относительно несложных деталей.
Третий вид технологических процессов осуществляется на автоматическом технологическом оборудовании роторного или роторно-конвейерного типа. Главной особенностью таких машин является взаимодействие заготовки и инструмента в процессе непрерывного транспортного перемещения в пространстве с одинаковой скоростью по радиусным траекториям (в роторно-конвейерных линиях по радиусным и линейным траекториям - рис. 1.7).
В многопереходных (многопозиционных) роторных линиях заготовка последовательно автоматически передается с одного инструментального ротора на другой с помощью транспортных роторов или цепного непрерывного конвейера. Производительность роторной автоматической линии определяется более высокой транспортной скоростью движения заготовки VТР:
,
где Р - линейный шаг расположения заготовок в рабочих и транспортных роторах (конвейере) линии.
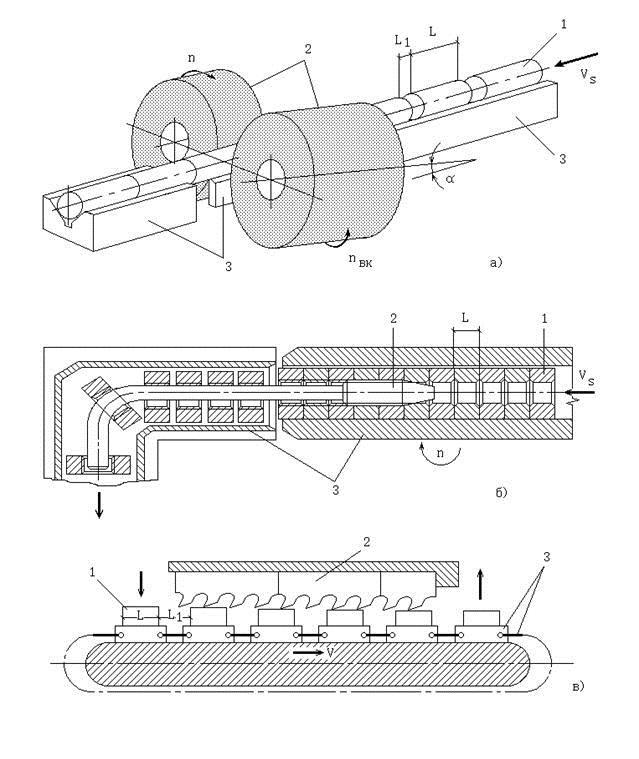
Рис. 1.6. Примеры непрерывных технологических процессов: а - бесцентровое шлифование; б - нарезание резьб гаечным метчиком; в - плоское конвейерное протягивание; 1- заготовка; 2 - инструмент; 3 - элементы средств технологического оснащения.

Рис. 1.7. Схемы роторной (а) и роторно-конвейерной (б) автоматических линий: 1 - технологические роторы; 2 - транспортные роторы; 3 - вспомогательные роторы.
Роторные технологические процессы, обладая очень высокой производительностью, обеспечивают меньшую точность обработки, чем непрерывные и тем более дискретные процессы. Это обусловлено влиянием кинематических и динамических погрешностей, возникающих при транспортном совместном движении заготовки и инструмента в процессе их формообразующего взаимодействия. Кроме того роторное оборудование обладает меньшей жесткостью. Другим недостатком этого вида технологических процессов является их слабая гибкость - возможность переналадки на выпуск новой продукции. Вследствие конструктивной сложности, заложенной в самом принципе действия роторных машин, наибольшая их эффективность наблюдается при массовом производстве достаточно простых деталей и изделий, требующих для кинематической связи инструмента и заготовки в процессе обработки простых движений.
Перечисленные классы и виды технологических процессов имеют различный удельный вес и некоторые особенности в условиях различных типов автоматизированного машиностроительного производства. Так роторные автоматические линии находят применение только в массовом производстве продукции устойчивого спроса.
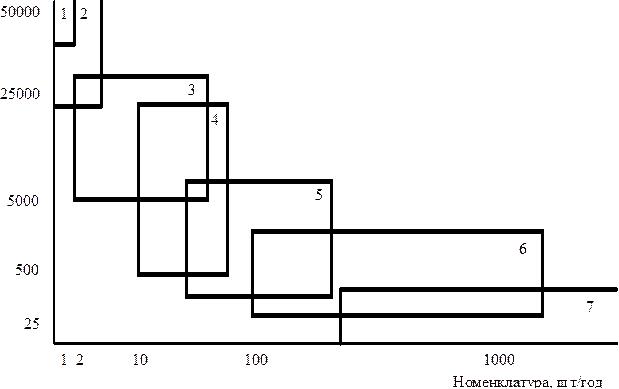
Примерами могут служить производства одноразовых медицинских шприцев, швейной фурнитуры, патронов, деталей крепежа (болтов, винтов, заклепок, шурупов и т.п.). Широко применяют роторное автоматическое оборудование в пищевой и медицинской промышленности. Требования массового автоматизированного производства невелируют главные недостатки роторных машин - малую гибкость и простоту объектов производства - за счет эффективной эксплуатации преимуществ - очень высокой производительности при компактности оборудования.
Автоматы и автоматические линии с непрерывным технологическим процессом также находят наиболее широкое применение в массовом производстве. Удельный вес таких процессов здесь наивысший, так как преимущества машин непрерывного действия наиболее полно отвечают требованиям массового автоматизированного производства, они превосходят роторные в точности, гибкости и стоимости, а дискретные - в производительности. Достаточно широко используется целый ряд непрерывных технологических процессов в серийном производстве (при любой серийности) ввиду наличия универсальных и специализированных станков непрерывного действия: бесцентрово-шлифовальных, карусельно- и барабанно-фрезерных, карусельношлифовальных, гайконарезных, вертикальных многошпиндельных полуавтоматов и др.
Тем не менее в серийном производстве преобладает дискретная технология, отличающаяся высокой точностью, качеством, мобильностью, большими резервами по режимам обработки и базирующаяся на более универсальном, гибком, жестком и дешевом оборудовании. Особое место в серийном производстве занимает оборудование с числовым программным управлением (ЧПУ). Именно этот тип оборудования послужил фундаментом для эффективной автоматизации средне- и мелкосерийных производств, создания гибких автоматизированных систем. Станки-автоматы и полуавтоматы с ЧПУ, автоматические линии на их базе и гибкие производственные системы начинают занимать доминирующее положение при автоматизации современного серийного машиностроительного производства за счет очень высокой гибкости, концентрации технологических возможностей, скоростных режимов обработки, использования преимуществ от САПР, АСТПП и возможности управления от ЭВМ.
Рис. 1.8. Примерные зоны эффективного использования технологического оборудования различной универсальности и автоматизированности: 1 - роторные и
роторно-конвейерные автоматические линии; 2 - автоматические линии из специальных станков; 3 - переналаживаемые агрегатные автоматические линии; 4 - цикловые автоматы и полуавтоматы; 5 - гибкие производственные системы (ГПС); 6 - автоматы и полуавтоматы с ЧПУ; 7 - станки с ручным управлением.
Этапы развития автоматизированных систем управления
Современная АСУТП (автоматизированная система управления технологическим процессом) представляет собой многоуровневую человеко–машинную систему управления. Создание АСУ сложными технологическими процессами осуществляется с использованием автоматических информационных систем сбора данных и вычислительных комплексов, которые постоянно совершенствуются по мере эволюции технических средств и программного обеспечения.
Появлению программного обеспечения полностью автоматизирующего процессы управления большим количеством разнородного технологического оборудования, оснащенного микроконтроллерами и/или микро–ЭВМ, предшествовало несколько этапов.
Первый этап отражает внедрение систем автоматического регулирования (САР). Объектами управления на этом этапе являются отдельные параметры, установки, агрегаты; решение задач стабилизации,
программного управления, слежения переходит от человека к САР. У
человека появляются функции расчета задания и параметры настройки регуляторов.
Второй этап – автоматизация технологических процессов. Объектом управления становится рассредоточенная в пространстве система; с
помощью систем автоматического управления (САУ) реализуются все более сложные законы управления, решаются задачи оптимального и адаптивного управления, проводится идентификация объекта и состояний системы.
Характерной особенностью этого этапа является внедрение систем
телемеханики в управление технологическими процессами. Человек все больше отдаляется от объекта управления, между объектом и диспетчером выстраивается целый ряд измерительных систем, исполнительных механизмов, средств телемеханики, мнемосхем и других средств отображения информации (СОИ).
Третий этап – автоматизированные системы управления технологическими процессами – характеризуется внедрением в управление технологическими процессами вычислительной техники. Вначале – применение микропроцессоров, использование на отдельных фазах управления вычислительных систем; затем активное развитие человеко– машинных систем управления, инженерной психологии, методов и моделей исследования операций и, наконец, диспетчерское управление на основе использования автоматических информационных систем сбора данных и современных вычислительных комплексов.
От этапа к этапу менялись и функции человека (оператора/диспетчера),
призванного обеспечить регламентное функционирование технологического процесса. Расширяется круг задач, решаемых на уровне управления;
ограниченный прямой необходимостью управления технологическим процессом набор задач пополняется качественно новыми задачами, ранее имеющими вспомогательный характер или относящиеся к другому уровню управления.
Диспетчер в многоуровневой автоматизированной системе управления технологическими процессами получает информацию с монитора ЭВМ или с электронной системы отображения информации и воздействует на объекты,
находящиеся от него на значительном расстоянии с помощью телекоммуникационных систем, контроллеров, интеллектуальных исполнительных механизмов.
Основой, необходимым условием эффективной реализации диспетчерского управления, имеющего ярко выраженный динамический характер, становится работа с информацией, т. е. процессы сбора, передачи,
обработки, отображения, представления информации.
От диспетчера уже требуется не только профессиональное знание технологического процесса, основ управления им, но и опыт работы в информационных системах, умение принимать решение (в диалоге с ЭВМ) в
нештатных и аварийных ситуациях и многое другое. Диспетчер становится главным действующим лицом в управлении технологическим процессом.
Говоря о диспетчерском управлении, нельзя не затронуть проблему технологического риска. Технологические процессы в энергетике,
нефтегазовой и ряде других отраслей промышленности являются потенциально опасными и при возникновении аварий приводят к человеческим жертвам, а также к значительному материальному и экологическому ущербу.
Статистика говорит, что за тридцать лет число учтенных аварий удваивается примерно каждые десять лет. В основе любой аварии за исключением стихийных бедствий лежит ошибка человека.
В результате анализа большинства аварий и происшествий на всех видах транспорта, в промышленности и энергетике были получены интересные данные. В 60–х годах ошибка человека была первоначальной причиной аварий лишь в 20% случаев, тогда как к концу 80–х доля
“человеческого фактора” стала приближаться к 80 %.
Одна из причин этой тенденции – старый традиционный подход к построению сложных систем управления, т. е. ориентация на применение новейших технических и технологических достижений и недооценка
необходимости построения эффективного человеко–машинного интерфейса,
ориентированного на человека (диспетчера).
Таким образом, требование повышения надежности систем диспетчерского управления является одной из предпосылок появления нового подхода при разработке таких систем: ориентация на оператора/диспетчера и его задачи.
Первый этап автоматизации – охватывает примерный промежуток времени между двумя мировыми войнами и характеризуется разработкой, созданием и использованием в производстве отдельных рабочих машин и станков-автоматов.
1.Универсальные станки с ручным управлением обладали небольшой производительностью,
почти нулевым коэффициентом автоматизации (имелся механизированный самоходный суппорт), однако они имели высокую гибкость и универсальность.
2.Универсальные автоматы и полуавтоматы (например, многошпиндельные токарные станки), которые имели более высокий коэффициент автоматизации Kа и более высокую
производительность Q:
Второй этап автоматизации - характеризовался разработкой и внедрением систем автоматических машин (прежде всего автоматических линий).
5. Автоматическая линия (АЛ) - это система машин, расположенных в последовательности технологического процесса, связанная единой транспортной системой, имеющая единую систему автоматического управления и предназначенная для выполнения всех технологических операций без участия человека. Задача человека сводится к первоначальной наладке оборудования и устранению неполадок. Структурная схема АЛ представлена на рис.31.
6.Станки и участки станков с ЧПУ – высокоавтоматизированное универсальное оборудование для автоматизации мелкосерийного и единичного производства, особенностью которых явилось: большая производительность, высокий коэффициент автоматизации, высочайшая гибкость и легкость переналадки. Существенным недостатком станков с ЧПУ была их ручная загрузка и разгрузка.
7.Промышленные роботы (ПР) и роботизированные технологические комплексы (РТК) - это перепрограммируемые рабочие машины, предназначенные для воспроизведения двигательных функций руки человека. Именно внедрение ПР позволило решить вопросы автоматического обслуживания станков с ЧПУ.
8.Внедрение средств вычислительной техники в производство
Использование ЭВМ при автоматизации производства на этом этапе развивалось в двух направлениях:
–создание микропроцессорных систем управления технологическим оборудованием (автоматами, станками с ЧПУ, АЛ, ПР, РТК);
–автоматизация обработка технологической информации (САПР, АСТПП, АСКИ, АСУП).
Задачи, решаемые на II этапе:
–разработка межстаночного транспорта;