
1190_Detali_mashin_i_podemno_transportnye_ustro
.pdf21
ЛАБОРАТОРНАЯ РАБОТА № 4
ИЗУЧЕНИЕ КОНСТРУКЦИЙ МЕХАНИЧЕСКИХ ПРИВОДОВ
1. Цель работы
Ознакомление с конструкциями механических приводов, их сборочных единиц, назначением и применением. Оценка силовых и кинематических параметров, которые может обеспечить конкретный привод.
2. Общие сведения
Механическая энергия, используемая для приведения в движение рабочих органов машины (орудия), представляет собой энергию вращательного движения вала приводного двигателя (чаще всего электрического).
Приводные двигатели не всегда могут быть соединены с исполнительными механизмами машин (барабанами, звездочками транспортирующих устройств и др.) непосредственно из-за несовпадения их скоростей (скорости исполнительных механизмов ниже), габаритов машин, требований техники безопасности, удобства обслуживания. В связи с этим возникает необходимость помещать между двигателем и исполнительным механизмом специальное устройство – механический привод [1, 3, 4].
Механический привод представляет собой одну или несколько механических передач (открытых или закрытых), последовательно соединенных.
Назначение механического привода – передача энергии от источника
(двигателя) к исполнительному механизму (рабочему органу машины) с одновременным преобразованием параметров вращательного движения: частота вращения и угловая скорость понижаются, вращающий момент увеличивается.
Механический привод монтируется на плите или сварной раме, к конструкциям которых предъявляются требования жесткости и точности взаимного расположения соединяемых поверхностей.
Конструкции приводов весьма разнообразны. Выбор типа привода диктуется машиной, при этом учитываются его стоимость, компактность, безопасность и надежность.
Механические приводы применяют в работе вентиляторов, насосов,
металлорежущих станков, конвейеров, шнеков, лебедок кранов и др. На рис. 4.1 представлены кинематические схемы приводов исполнительных механизмов, движение которых осуществляется от электродвигателя (М): ленточного конвейера (рис. 4.1, а); цепного конвейера (рис. 4.1, б); механизма подъема крана (рис. 4.1, в).
Механический привод (рис. 4.1, а) барабана (1) ленточного конвейера состоит из соединительной муфты (2), двухступенчатого зубчатого цилиндрического редуктора (косозубого) (3), открытой цепной передачи (4).
22
Механический привод (рис. 4.1, б) тяговых звездочек (1) цепного конвейера включает: клиноременную передачу (2), одноступенчатый червячный редуктор (3) и соединительную муфту (3).
Механический привод (рис. 4.1, в) барабана (1) механизма подъема крана включает: соединительную муфту (2), двухступенчатый зубчатый цилиндрический редуктор (3), соединительную муфту (4).
Для соединения валов с неточно совмещенными осями применяют компенсирующие муфты [2] (зубчатые или цепные), которые компенсируют небольшие радиальные, осевые, угловые или комбинированные смещения.
Муфты для механических приводов подбирают по диаметру вала и расчетному моменту.
Приводы могут быть с постоянной и переменной скоростью (со ступенчатым или плавным изменением скорости). Для обеспечения изменения скорости вместо редуктора устанавливают коробку скоростей или вариатор.
3.Порядок выполнения работы
3.1.Ознакомиться с конструкцией привода, имеющегося в лаборатории (рис. 4.1, а) (правила по технике безопасности при изучении механического привода). Записать паспортные данные электродвигателя – его мощность Р (кВт) и частоту вращения nдв (об./мин).
3.2.Измерить мерной линейкой межосевое расстояние быстроходной
ступени редуктора – аб (мм), тихоходной ступени редуктора – ат (мм) и общее межосевое расстояние редуктора – ар (мм).
3.3.Подсчитать: – число зубьев шестерни быстроходной ступени z1;
–число зубьев колеса быстроходной ступени z2;
–число зубьев шестерни тихоходной ступени z3;
–число зубьев колеса тихоходной ступени z4.
3.4.Рассчитать передаточные отношения:
– |
первой ступени u1 = z2/ z1; |
(4.1) |
– |
второй ступени u2 = z4/ z3; |
(4.2) |
– |
редуктора в целом uр = u1 · u2. |
(4.3) |
3.5.Замерить межосевое расстояние цепной передачи ац (мм) и шаг цепи рц (мм) (рис. 4.2). По величине шага цепи из табл. 4.1 установить тип цепи, записать ее обозначение и все параметры.
3.6.Подсчитать: – число зубьев ведущей звездочки z5;
– число зубьев ведомой звездочки z6.
Найти передаточное отношение цепной передачи |
|
uц = z6/ z5. |
(4.4) |
3.7. Вычислить общее передаточное отношение данного привода |
|
uпр = uр · uц . |
(4.5) |
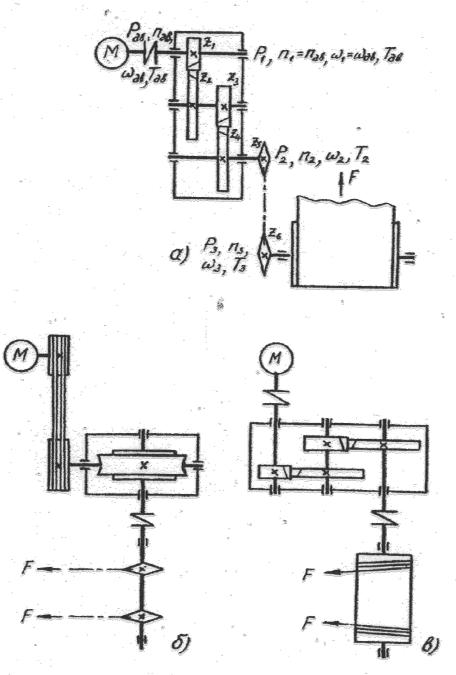
23
Рис. 4.1. Кинематические схемы механических приводов
3.8. Определить коэффициент полезного действия (КПД) данного привода (учитывает совокупные механические потери энергии в его элементах)
ηпр = ηм · ηр · ηц · ηпп · ηбар, |
(4.6) |
где ηм – КПД соединительной муфты; ηр – КПД двухступенчатого цилиндрического редуктора; ηц – КПД открытой цепной передачи;
ηпп – КПД пары подшипников приводного вала; ηбар – КПД приводного барабана (фрикционного).
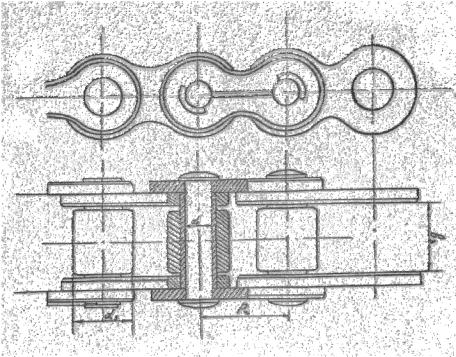
24
Значения КПД приведены в табл. 4.2.
Таблица 4.1
Приводные роликовые цепи (однорядные) типа ПР [4]
Условное |
Шаг |
Внутрен |
Диаметры |
Разрушаю- |
Масса |
|
обозначение |
цепи |
няя |
валика |
ролика |
щая |
1 м |
цепи |
pц, мм |
ширина |
d, мм |
d1, мм |
нагрузка |
цепи, |
|
|
Ввн, мм |
|
|
F, кН |
кг |
ПР-9,525 – 9,1 |
5,525 |
5,72 |
3,28 |
6,35 |
9,1 |
0,45 |
ПР-12,7 – 18,2 |
12,7 |
7,75 |
4,45 |
8,51 |
18,2 |
0,75 |
ПР-15,875 – 22,7 |
15,875 |
9,65 |
5,08 |
10,16 |
22,7 |
1,00 |
ПР-19,05 – 31,8 |
19,05 |
12,70 |
5,96 |
11,91 |
31,8 |
1,90 |
ПР-25,4 – 60 |
25,4 |
15,88 |
7,95 |
15,88 |
60,0 |
2,60 |
ПР-31,75 –88,5 |
31,75 |
19,05 |
9,55 |
19,05 |
88,5 |
3,80 |
ПР-38,1 – 127 |
38,1 |
25,40 |
11,12 |
22,23 |
127,0 |
5,50 |
ПР-44,45 – 172,4 |
44,45 |
25,40 |
12,72 |
25,40 |
172,4 |
7,50 |
Рис. 4.2. Цепь приводная роликовая однорядная (ПР)
3.9. Вычислить мощности, передаваемые элементами привода:
–мощность вала электродвигателя Рдв (кВт) (по паспорту);
–мощность быстроходного вала редуктора Р1 (кВт)
|
Р1 |
= Рдв · ηм; |
(4.7) |
– |
мощность тихоходного вала редуктора Р2 (кВт) |
|
|
|
Р2 = Р1 · ηр; |
(4.8) |
|
– |
мощность вала приводного барабана Р3 (кВт) |
|
|
|
Р3 = Р2 |
· ηц · ηпп · ηбар. |
(4.9) |
25
|
|
|
|
|
|
|
Таблица 4.2 |
|
|
Элементы привода |
|
|
|
|
КПД |
Редуктор зубчатый: одноступенчатый |
|
|
|
|
0,99 |
||
|
|
двухступенчатый |
|
|
|
|
0,97 |
|
|
трехступенчатый |
|
|
|
|
0,92 |
Зубчатая открытая передача |
|
|
|
0,93…0,96 |
|||
Редуктор червячный с червяком: однозаходным |
|
|
0,70…0,80 |
||||
|
|
двухзаходным |
|
|
0,75…0,85 |
||
|
|
четырехзаходным |
|
|
0,80…0,90 |
||
Цепная передача: открытая |
|
|
|
0,92…0,93 |
|||
|
|
закрытая |
|
|
|
0,95…0,97 |
|
Ременная передача |
|
|
|
0,94…0,97 |
|||
Пара подшипников качения |
|
|
|
0,99…0,995 |
|||
Муфта соединительная |
|
|
|
0,98…0,99 |
|||
Приводной барабан (фрикционный) |
|
|
|
|
0,92 |
||
3.10. Рассчитать частоту вращения n (об/мин) и угловые скорости ω |
|||||||
(рад/сек): |
|
|
|
|
|
|
|
|
– вала электродвигателя и быстроходного вала редуктора |
||||||
|
|
nдв = n1 (по паспорту); |
ωдв = ω1 = π · nдв/30; |
|
(4.10) |
||
|
– |
тихоходного вала редуктора n2 = n1/ uр; |
ω2 = ω1/ uр; |
(4.11) |
|||
|
– |
вала приводного барабана |
n3 = n2/ uц; |
ω3 = ω2/ uц. |
(4.12) |
||
3.11. Подсчитать вращающие моменты Т (Нм), значения мощности |
|||||||
подставлять в формулы в кВт: |
Тдв = 103Рдв/ωдв; |
|
|
||||
– |
на валу электродвигателя |
|
(4.13) |
||||
– |
на быстроходном валу редуктора Т1 = 103Р1/ω1; |
|
(4.14) |
||||
– |
на тихоходном валу редуктора |
Т2 = 103Р2/ω2; |
|
(4.15) |
|||
– |
на валу приводного барабана |
Т3 = 103Р3/ω3. |
|
(4.16) |
3.12.Познакомиться с конструкцией соединительной муфты, определить, к какому типу она относится. Проверить правильность подбора муфты [1, 3, 4], для чего замерить диаметры соединяемых валов: диаметр
вала электродвигателя dдв и диаметр входного вала двухступенчатого цилиндрического зубчатого редуктора dвх.
3.13.Вычислить расчетный вращающий момент на муфте Трас (Нм)
Трас = Кр · Тдв, |
(4.17) |
где Кр = 1,3 – коэффициент динамичности или режима работы (при спокойной работе).
4.Оформление отчета
4.1.Титульный лист по образцу. Цель работы.
Общие сведения, кинематическая схема привода (рис. 4.1, а).
4.2.Проводимые измерения и расчеты, итоги которых свести в
табл. 4.3.
26
|
|
Таблица 4.3 |
Параметры привода |
Обозначение |
Значение |
|
|
|
Мощность электродвигателя |
Рдв, кВт |
|
Частота вращения вала электродвигателя |
nдв, об/мин |
|
Передаточное отношение редуктора |
uр |
|
Передаточное отношение цепной передачи |
uц |
|
Передаточное отношение привода |
uпр |
|
КПД привода |
ηпр |
|
Межосевые расстояния: |
|
|
1 ступени редуктора |
а1, мм |
|
2 ступени редуктора |
а2, мм |
|
редуктора в целом |
ар, мм |
|
цепной передачи |
ац, мм |
|
Тип цепи и ее условное обозначение |
рц, мм |
|
Шаг цепи |
|
|
Мощность на валу приводного барабана |
Р3, кВт |
|
Частота вращения вала приводного барабана |
n3, об/мин |
|
Угловая скорость вала приводного барабана |
ω3, рад/сек |
|
Вращающий момент на валу приводного |
Т3, Нм |
|
барабана |
|
|
Диаметр вала электродвигателя |
dдв, мм |
|
Диаметр быстроходного вала редуктора |
d1, мм |
|
Расчетный момент муфты |
Трас, Нм |
|
Тип муфты |
|
|
4.3. Вывод по закрепленной за лабораторной работой теме с обоснованием полученных результатов.
5.Контрольные вопросы
5.1.Что собой представляет механический привод, его назначение, применение.
5.2.Из каких конструктивных элементов состоит привод?
5.3.Как определить передаточное отношение привода?
5.4.Как вычислить КПД привода?
5.5.Какой тип цепи использован в приводе?
5.6.Какой тип муфт используют в механических приводах?
5.7.Как изменяется на валах привода частота их вращения и угловые
скорости?
5.8.Как изменяется вращающий момент на валах привода?
5.9.Как изменяется мощность на валах привода?
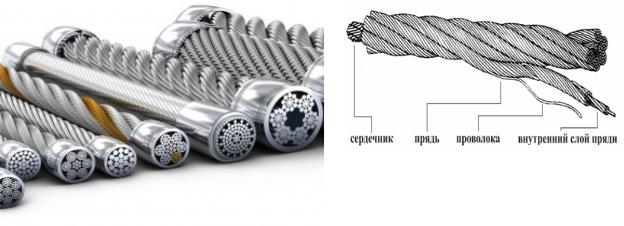
27
ЛАБОРАТОРНАЯ РАБОТА № 5
ИЗУЧЕНИЕ КОНСТРУКЦИЙ СТАЛЬНЫХ КАНАТОВ
1. Цель работы
Изучить конструкцию, методику расчета и нормы выбраковки стальных проволочных канатов.
Оборудование и приборы: образцы канатов, штангенциркуль.
2. Общие сведения о конструкциях стальных канатов
Большое распространение в качестве гибкого рабочего органа в грузоподъемных машинах находят проволочные стальные канаты [2]. Их изготавливают из стальной или оцинкованной проволоки марок В, I или II по ГОСТу 7372 – 79 диаметром 0,2...3 мм и с расчетным пределом прочности проволоки при растяжении 140...260 кГ/мм2 (1400...2600 МПа) (рис. 5.1). Проволоку марки В (высококачественную) применяют в особо ответственных случаях, например, в устройствах для подъема людей. Для специальных целей канаты изготавливают из проволоки из нержавеющей стали.
Рис. 5.1. Выпускаемые канаты |
Рис. 5.2. Конструкция каната |
Различают канаты двух типов: одинарной и двойной свивки. Канат одинарной свивки получают путем однократного скручивания по спирали определенного количества проволок (рис. 5.2). В грузоподъемных машинах в основном применяют канаты двойной свивки: сначала проволоки свивают в пряди вокруг центральной проволоки, а затем несколько (как правило, шесть) прядей свивают в канат вокруг сердечника (рис. 5.3). Сердечники могут быть стальными или органическими, изготовленными из пеньки, пропитанной смазкой. При изгибе каната на блоках или барабане смазка выдавливается в зону контакта проволок и уменьшает силу трения между ними.
Многопрядные канаты могут быть с параллельной (односторонней) свивкой – когда проволоки в прядях и пряди в канате свиваются в одном направлении, и крестовой свивки – когда направления свивки проволок в прядях и прядей в канате противоположные (рис. 5.4). Канаты
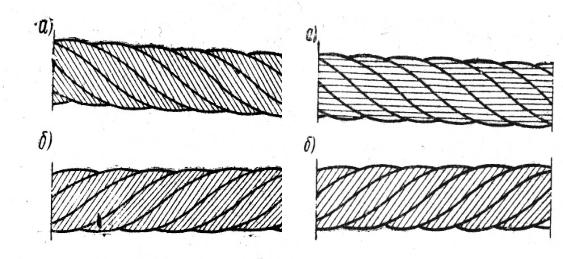
28
односторонней свивки более гибки и долговечны, однако они самопроизвольно раскручиваются при свободном подвешивании груза на них. Канаты крестовой свивки не раскручиваются, имеют большую структурную прочность, поэтому в грузоподъемных машинах применяют главным образом именно канаты крестовой свивки.
Рис. 5.3. Направление свивки наружного слоя в канате: а – правое; б – левое
Рис. 5.4. Направление свивки:
а– крестовая свивка;
б– параллельная свивка
Конструктивно имеются следующие особенности изготовления канатов. Пряди могут быть свиты из проволок одного диаметра – это канаты типа ТК с точечным контактом проволок в прядях. Если пряди свивают из проволок различного диаметра, контакт проволок в прядях получают линейный, и такие канаты относятся к типу ЛК. Имеются также конструкции канатов с комбинированным контактом проволок в прядях, их относят к типу ТЛК (с точечным и линейным контактами). Различные конструкции стальных канатов, применяемых в настоящее время в грузоподъемных машинах, изображены на рис. 5.5.
Принята следующая система условного обозначения стальных канатов: а) ТК-6 × 19 = 114 + 1 о.с. ГОСТ 2688-80 – канат с точечным контактом проволок в прядях, имеющий 6 прядей по 19 проволок (общее количество
проволок в канате – 114) и один органический сердечник (рис. 5.5, а; 5.6); б) ЛК-О 6 × 19 = 114 + 7 х 7 ГОСТ 7668-80 – канат с линейным
контактом, буква «О» в обозначении указывает на то, что проволоки отдельных слоев прядей имеют одинаковый диаметр, канат состоит из 6 прядей по 19 проволок в каждой, а также имеет стальной сердечник, изготовленный из 7 прядей, каждая из которых состоит из 7 проволок
(рис. 5.5, б; 5.6);
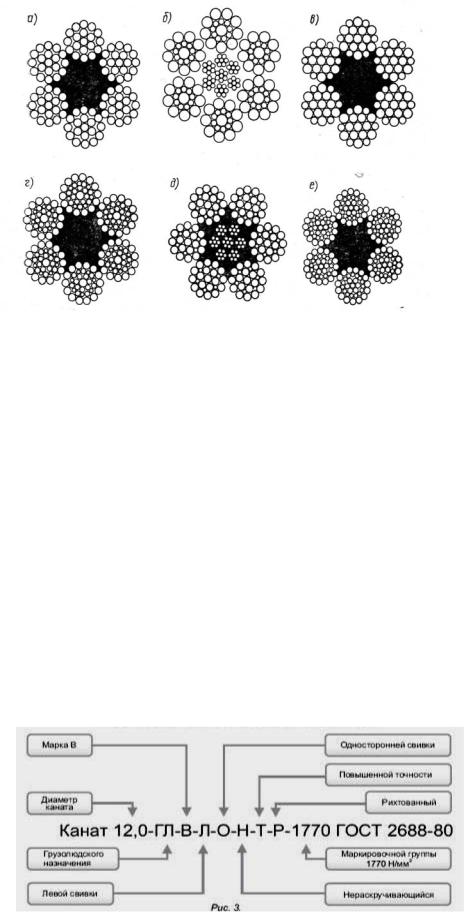
29
Рис. 5.5. Конструкции стальных канатов:
а– ТК (6×10 +1 о.с.); б – ЛК-О (6×19+1 о.с.);
в– ЛК-Р (6×19+1 о.с.); г – ЛК-РО (6×36+1 о.с.);
д– ЛК-З (6×25+7×7); е – ТЛК-О (6×37+1 о.с.)
в) ЛК-Р 6 × 19 = 114 + 1 о.с. ГОСТ 2688-80 – канат с линейным контактом, «Р» – проволоки в верхнем слое прядей двух различных диаметров, сердечник органический (рис. 5.5, в; 5.6);
г) ЛК-РО 6 × 36 = 216 + 1 о.с. ГОСТ 7668-80 – канат с линейным контактом, «РО» – проволоки в отдельных слоях прядей имеют разный и одинаковый диаметры, канат имеет 6 прядей по 36 проволок (всего 216 проволок) и один органический сердечник (рис. 5.5, г; 5.6);
д) ЛК-З 6 × 25 = 150 + 7 × 7 ГОСТ 7667-80 – канат с линейным контактом, «З» – между двумя слоями проволок располагаются заполняющие проволоки меньшего диаметра, сердечник стальной (рис. 5.5, д; 5.6);
е) ТЛК-О 6 × 37 = 222 + 1 о.с. ГОСТ 7667-80 – канат с комбинированным (точечным и линейным контактом), проволоки отдельных слоев имеют одинаковый диаметр, сердечник органический (рис. 5.5, е, 5.6).
Рис. 5.6. Пример условного обозначения каната
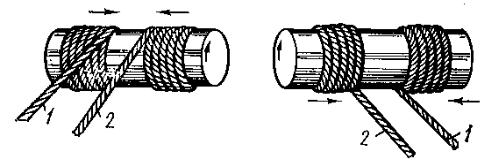
30
Канаты типа ТК применяют только для ненапряженных режимов работы. Канаты типа ЛК более гибкие и износостойкие, их срок службы значительно больше, чем у канатов типа ТК.
3. Выбор каната по направлению свивки
По направлению свивки прядей канаты изготавливают правого и левого направления. В канатах правой свивки пряди идут слева направо, в канатах левой свивки – наоборот: справа – вверх – налево (рис. 5.3).
Выбор каната по направлению свивки имеет большое значение для его правильной эксплуатации при навивке на барабан. При навивке каната на гладкий барабан за каждый оборот барабана канат смещается на величину одного своего диаметра, что дополняет его деформацию изгиба деформацией кручения. Поэтому для создания более благоприятных условий для работы каната следует так подбирать направления свивки, чтобы канат в процессе работы дополнительно подкручивался; это приводит к увеличению его плотности и срока службы.
Рекомендуемые направления свивки каната в зависимости от направления укладки его витков на барабан приведены на рис. 5.7, где стрелками показаны направления перемещения канатов, навиваемых на барабан. При вращении барабана по часовой стрелке канаты смещаются к середине барабана. В случае наматывания канатов на барабан сверху канат правой свивки должен навиваться на левую часть барабана, а канат левой свивки – на правую его часть (левый рис. 5.7). При наматывании снизу (правый рис. 5.7) необходимо поменять канаты местами.
Рис. 5.7. Подбор канатов по направлению свивки: 1 – канат правой свивки; 2 – канат левой свивки
4.Расчет и подбор стальных канатов
Впроцессе работы каната его отдельные проволоки испытывают различные напряжения: смятия, растяжения, изгиба и кручения. Величины указанных напряжений зависят от многих факторов: конструкции и диаметра каната, диаметров проволок в его прядях, материала и конструкции сердечника, типа свивки, размеров и конструкции барабана и блоков и т.д. Установить математическую зависимость для расчета канатов с учетом совместного воздействия всех факторов практически невозможно. В