
Додаткова_література / Додаткова література / tsp
.pdf
нагреваемым поверхностям кромок, подлежащих свариванию, или вдоль их оси). В
случае бокового нагрева возможно сдавливание при продолжающемся воздействии пламени, а при торцевом – пламя перед сдавливанием должно быть удалено. Так как при удалении пламени кромки быстро окисляются кислородом воздуха, их следует нагревать до поверхностного оплавления, чтобы окислы выдавливались вместе с жидким металлом. Этот вид сварки применяется при выполнении стыков трубопроводов и ряда деталей железнодорожного транспорта, изготавливаемых из углеродистых сталей.
Контактная сварка. Принцип нагрева при контактной сварке заключается в
выделении тепла при прохождении электрического тока по любому электрическому сопротивлению.
Q = 0,24IUt = 0,24I2Rt.
В последовательной цепи на участке большего сопротивления (каким является место контакта двух подлежащих сварке поверхностей) выделяется большее количество тепла. Выбором соответствующей мощности сварочной машины можно обеспечить сварку деталей быстрым (0,003 – 10 с) их нагревом и последующим сжатием. Обычно нагрев осуществляется переменным током применением силовых понижающих трансформаторов. Различают три основных вида контактной сварки: стыковая, точечная и шовная
Рис. 1.4. Схемы контактной сварки.
Стыковая контактная сварка (рис. 1.4, а). Осуществляется по двум схемам: сварка сопротивлением и сварка оплавлением.
При сварке сопротивлением подлежащие сварке детали 1 и 2 соосно зажимают в неподвижном 3 и подвижном зажимных устройствах (губках) машины.
Далее детали приводят в контакт друг с другом с давлением Р и включают трансформатор 5 посредством контактора 6. Проходящий по деталям электрический ток, разогревает их в зоне контакта. Металл в этой размягчается и происходит осадка
– пластическое деформирование нагретого объема для осуществления сварки.
При сварке оплавлением напряжение на свариваемые детали подают до того как они сведены, т.е. когда между торцами заготовок есть зазор. При медленном сближении деталей появляется контакт то в одной, то в другой точках, приводя к быстрому их оплавлению. Такой процесс приводит к постепенному оплавлению всей
11

поверхности. В нужный момент контактор 6 выключает ток и поверхности нагретых элементов сдавливают. При этом выдавливаются остатки жидкости и освобожденные от нее твердые, нагретые до пластического состояния объемы металла свариваются.
Точечная контактная сварка (рис. 1.4, б) осуществляется для соединения элементов внахлестку. Свариваемые листы 2 и 3 зажимают неподвижным 4 и подвижным 1 электродами машины. При включении трансформатора 5 контактором 6 выделяется тепло вблизи внутренних контактных поверхностей деталей и часть металла расплавляется , образуя ядро литого металла 7. После выключения тока и
увеличения давления Р осуществляется затвердевание жидкого металла и местное сваривание в районе литой точки.
Шовная контактная сварка (рис. 1.4, в) осуществляется так же, как и точечная, обеспечивая получение не только прочного, но и сплошного герметического шва. Это достигается последовательной постановкой ряда точек с частичным перекрытием последующей точки предыдущей. Свариваемые элементы 2 и 3 зажимают между электродами 1, 4, выполненными в виде дисков. Диски, вращаясь, протаскивают свариваемые элементы между собой, а периодическое включение и выключение тока приводит к последовательной сварке точек.
Индукционная сварка (рис. 1.5). Нагрев металла до сварочной температуры осуществляется с помощью специальных индукторов 3, питаемых от источников тока 4 высокой частоты. Форма индуктора должна соответствовать форме нагреваемого изделия.
3 |
4 |
Р Р
. |
2 |
1 |
|
Рис. 1.5. Схема индукционной сварки.
Диффузионная сварка. При сварке различных химически активных
материалов необходимо максимально исключить возможность их взаимодействия с атмосферой в период выполнения сварочной операции. Это достигается применением вакуума; свариваемые изделия помещают в специальную камеру, из которой насосами удаляют воздух до получения вакуума 10-3 – 10-5 мм. рт. ст. После
достижения такого вакуума осуществляют нагрев изделия индуктором и дают сварочное давление.
Вакуум предохраняет от окисления свариваемые поверхности, обеспечивает распад окислов, находящихся на поверхностях. Одновременно происходит удаление адсорбированных газов. Это позволяет получать качественные соединения ряда
металлов и металлов с неметаллами при относительно небольшой пластической деформации вблизи места соединения.
Термитная сварка. При термитной сварке источником тепла является экзотермическая реакция (с выделением тепла) взаимодействия порошкообразных
12
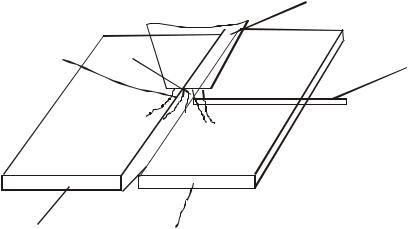
окисла и элемента с большей активностью (сродством) к кислороду. Например, если
в тигель из огнеупорного материала поместить смешанные порошки алюминия и закиси железа и создать местный нагрев до 7500 С, то начнется реакция
Fe2O3 + 2Al = Al2O3 + 2Fe + Q,
которая распространяется на весь объем порошка и в оптимальных условиях полученные продукты реакции (Al2O3, Fe) теоретически должны нагреться до 30000 С. Практически эта температура оказывается ниже и составляет около 2200 – 24000 С,
при которой и железо и окись алюминия расплавлены и как несмешивающиеся жидкости разделяются по плотности (жидкое железо собирается у дна тигля, а Al2O3
– в верней его чести). Аккумулированный такой жидкостью запас тепла может быть использован для сварки давлением или плавлением.
Область применения термитной сварки среди прочих видов сварки относительно невелика.
Газовая сварка. Это сварка плавлением, при которой источником тепла является высокотемпературное пламя горючих газов в смеси с кислородом. В качестве горючих газов применяют ацетилен, водород, природный газ (метан), пары керосина пропанобутановую смесь.
Кромки двух листов 1 и 2 (двух деталей) (рис. 1.6) подвергаются местному нагреву сосредоточенным пламенем 3 до расплавления. Образовавшаяся ванна 4 контактирует с кромками обоих листов. После образования ванны пламя перемещают по линии стыка листов в направлении стрелки V, металл под пламенем расплавляется, а позади пламени в связи с охлаждением – затвердевать. Этот затвердевший металл и образует сварной шов 5 между исходными листами (деталями). Подобрав соответственно режим (мощность пламени, скорость его относительного перемещения по кромкам листов) можно получить необходимое проплавление металла и, следовательно, рабочее сечение шва.
Обычно для швов, которые должны обеспечить прочность, сопоставимую с прочностью свариваемых элементов, требуется получить сквозное проплавление соединяемых деталей (на всю их толщину). Если толщина металла велика и обеспечить сквозное проплавление трудно, то кромки под сварку обрабатывают со
скосом и полученную разделку заполняют добавочным расплавленным присадочным металлом 6. Этот присадочный металл обычно представляет собой прутки (стержни), подаваемые в пламя, расплавляющиеся в нем и пополняющие сварочную ванну.
5
3 4
6
V
2 |
1 |
13
Рис. 1.6. Схема газовой сварки.
Для различной толщины свариваемого металла применяют различную удельную мощность сварочного пламени, которая характеризуется часовым расходом ацетилена в литрах, приходящимся на 1 мм толщины свариваемого металла.
В процессе сварки пламя не только расплавляет металл, но и защищает расплавленную ванну от вредного влияния кислорода и азота атмосферного воздуха. Поэтому при сварке необходимо, чтобы расплавленный основной металл и конец присадочного металла находились все время в восстановительной зоне пламени.
Изменением угла наклона горелки к поверхности свариваемого металла можно изменить интенсивность расплавления свариваемого металла. Наиболее интенсивно металл расплавляется при перпендикулярном расположении горелки.
При необходимости горелка может передвигаться по направлению сварки или прямолинейно, или с поперечными и круговыми движениями.
1.4 Кислородная резка
Кислородная резка основана на сгорании металла в струе кислорода. Металл при резке нагревают пламенем, который образуется при сгорании горючего газа в кислороде. Кислород, сжигающий металл, называют режущим. В процессе резки струю режущего кислорода подают к месту реза отдельно от кислорода, идущего на образование горючей смеси для подогрева металла. Касаясь нагретого металла, режущая струя кислорода интенсивно окисляет и сжигает его верхние слои. Процесс
окисления верхних слоев металла сопровождается выделением большого количества тепла, которое идет на прогрев нижних слоев металла. Процесс сгорания разрезаемого металла распространяется на всю толщину, образующиеся окислы выдуваются из места реза струей режущего кислорода.
Металл, подвергаемый резке кислородом, должен удовлетворять следующим требованиям: температура воспламенения металла в кислороде должна быть ниже температуры его плавления, окислы металла должны иметь температуру плавления ниже, чем температура плавления самого металла, и обладать хорошей жидкотекучестью, металл не должен обладать высокой теплопроводностью.
1.5 Электродуговая сварка
При дуговой сварке нагрев металла осуществляется электрической дугой. При
устойчивом длительном протекании тока через ионизированный газовый промежуток между двумя электродами, подсоединенными к источнику питания, выделяется тепловая и световая энергия. Температура, развиваемая в дуге, может быть очень высокой, значительно превышающей температуру плавления свариваемых металлов.
Сварка дугой косвенного действия. Осуществляется нагревом металла дугой, горящей между двумя неплавящимися электродами, подключенными к различным полюсам источника электрической энергии. Свариваемое изделие в электрическую цепь не включено. Дуга горит независимо от свариваемого изделия. Нагретые газы столба дуги контактируют с поверхностью металла, нагревают его и, при достаточной мощности дуги, расплавляют. Сварка может выполняться как без
14
добавочного присадочного металла, так и с применением присадки, подаваемой в дугу в виде прутка.
Сварка неплавящимся электродом. Выполнятся, когда свариваемое изделие включено в цепь дуги и является одним из ее полюсов. Второй полюс дуги находится на неплавящемся электроде. (Сварка на прямой и обратной полярности, на переменном токе.) Эффективность при этом способе значительно выше, чем при сварке дугой косвенного действия, при одинаковой электрической мощности дуги.
Сварка плавящимся электродом. Выполнятся по такой же схеме, как и при неплавящемся электроде (изделие включено в цепь дуги и является одним из полюсов). Электрод является металлическим, интенсивно расплавляется дугой, и обеспечивает введение в сварочную ванну дополнительного (наплавленного) металла.
Этот вид сварки является наиболее эффективным видом сварки плавлением и в связи с этим имеет наибольшее распространение в промышленности при изготовлении и ремонте металлических конструкций.
Разновидности сварки плавящимся электродом.
1.Ручная дуговая сварка (РДС) – когда сварка осуществляется специальными штучными электродами с обмазкой для защиты дуги и сварочной ванны. Подача
электрода в зону плавления и перемещение электрода вдоль шва осуществляется сварщиком вручную.
Для изготовления электродов должны быть правильно подобраны электродная проволока и состав покрытия электродов. Марки проволоки имеют условное обозначение, например Св-08ГА: первые две буквы означают, что эта проволока сварочная, следующие за ними цифры и буквы характеризуют содержание различных элементов в металле проволоки – первые две цифры – выраженная в сотых долях процента массовая доля углерода, в данной марке она равна 0,08%. Буква Г указывает на содержание в проволоке марганца, в данном случае 0,8 – 1,1%, а буква А – на изготовление ее высококачественной стали с уменьшенным содержанием вредных примесей (серы и фосфора). В других марках после первых двух цифр, указывающих на содержание углерода, ставятся буквы и цифры: обозначают содержание отдельных элементов, цифры – их массовою долю в процентах.
Табл. Обозначение элементов в марках электродной проволоки.
Элемент |
Буквенное |
Элемент |
Буквенное |
|
обозначение |
|
Обозначение |
Азот |
А |
Кремний |
С |
Ниобий |
Б |
Титан |
Т |
Вольфрам |
В |
Ванадий |
Ф |
Марганец |
Г |
Хром |
Х |
Медь |
Д |
Цирконий |
Ц |
Молибден |
М |
Алюминий |
Ю |
Никель |
Н |
|
|
15
Впроволоке Св-10Х11ВМФН содержится в процентах: углерода 0,1; хрома
10 – 12; вольфрама 1 – 1,4; молибдена 1 – 1,3; ванадия 0,25 – 0,5; никеля 0,9 – 1,1.
Всостав покрытия входят ряд материалов, которые выполняют определенные функции при сварке. Покрытие образуется из хорошо размолотых и перемешанных материалов, связанных жидким стеклом и нанесенных на стержни под давлением.
Применяемые для электродного покрытия материалы разделяют на группы в соответствии с их функциями.
К материалам, образующим шлак, относятся полевой шпат, кремнезем, магнезит, мрамор др.
К газообразующим материалам относятся минералы, которые кроме шлака образуют защитный газ – это мрамор, магнезит и др. Кроме того, в состав покрытия вводят органические вещества – крахмал, целлюлозу, древесную муку и др., которые выделяют только защитный газ.
Важную роль играют стабилизирующие вещества, предназначенные для обеспечения устойчивости горения дуги. К ним относятся соединения щелочных и щелочноземельных металлов калия, натрия, кальция и др.
Для восстановления окисленного в процессе сварки металла применяют специальные раскислители, к которым относятся ферросплавы – ферромарганец, ферросилиций, ферротитан и др. Эти же ферросплавы служат легирующими материалами, которые увеличивают содержание марганца, титана и др. элементов в металле шва. Кроме того, для легирования иногда используют порошкообразные металлы. В покрытие также вводят пластификаторы, улучшающие его пластические свойства.
Согласно ГОСТ 9467—75 электроды подразделяются на типы. ГОСТ предусматривает 14 типов электродов для конструкционных сталей и 9 типов для теплоустойчивых сталей. Типы электродов для сварки конструкционных сталей
обозначают буквой Э, после которой следуют цифры минимального временного сопротивления наплавленного этим электродом металла в кгс/мм2, например электроды Э42 должны гарантировать минимальное временное сопротивление 420 МПа. Буква А, стоящая после цифр (например, Э46А) означает, что электроды этого типа обеспечивают более высокие пластические свойства наплавленного металла, чем без буквы А. Типы электродов для сварки теплоустойчивых сталей также обозначают буквой Э, после которой следуют буквы и цифры, характеризующие химический состав наплавленного металла.
Каждому типу электродов может соответствовать несколько марок электродов. Марка электродов характеризуется определенным составом покрытия, маркой электродного стержня, технологическими свойствами, свойствами металла шва.
Условное обозначение электродов для сварки конструкционных сталей состоит из обозначения марки электрода, типа электрода, диаметра стержня, типа покрытия и номера ГОСТа. Например, УОНИ-13/45-Э42А-4,0-Ф ГОСТ 9467—75 расшифровывается: УОНИ-13/45 – марка электрода; Э42А – тип электрода; 4,0 – диаметр электродного стержня в мм; Ф – фтористо-кальциевый тип покрытия.
2. Полуавтоматическая сварка – подача электрода в зону плавления осуществляется автоматически, а перемещение вдоль шва – вручную.
16

3. Автоматическая сварка – подача электрода и в зону плавления и перемещение вдоль шва осуществляется автоматически.
Сварка плавящимся электродом может выполняться:
а) открытой дугой, когда в область дуги не подается защитный газ или флюс; зона дуги доступна наблюдению. Защита от воздействия воздуха часто осуществляется специальными веществами (газообразующими, шлакообразующими), вносимыми с электродом обычно в виде покрытия;
б) дугой под флюсом, когда место горения закрыто порошкообразным флюсом, расплавляющимся теплом дуги и образующим шлак; в этом случае дуга не видна – она горит в пространстве (газовой полсти), изолированном от окружающей среды слоем шлака и нерасплавившегося порошкообразного флюса.
В) дугой, защищенной от воздуха специальной газовой защитой, например углекислым или инертными газами. Этот способ называют сваркой в защитных газах.
Плазменная обработка металлов.
Для получения плазменной дуги служит устройство, называемое плазмотроном. Существует два типа плазмотронов – с дугой прямого и с дугой косвенного действия.
|
1 |
|
Газ |
5 |
2 |
|
|
|
3 |
4
Рис. 1.7. Схема устройства плазмотрона.
Вплазмотронах прямого действия (рис.1.7) плазменная дуга создается между стержневым электродом 1, вмонтированным в газовую камеру 2, и обрабатываемым изделием 4. Сопло 3 электрически нейтрально и служит для сжатия и стабилизации дуги.
Вплазмотронах косвенного действия плазменная дуга создается между электродом 1 и соплом 3.
Сжатие столба дуги происходит следующим образом: рабочий газ, проходящий через столб дуги, нагревается, ионизируется и выходит из сопла плазмотрона в виде плазменной струи. Слой газа, омывающий столб газа снаружи, остается относительно холодным, образуя тепловую и электрическую изоляцию
между плазменной дугой и каналом сопла. Плотность тока в плазмотронах достигает
100 А/мм2, а температура 15000 – 300000 С.
Процесс возбуждения дуги непосредственно между электродом и изделием осуществить очень трудно. В связи с этим вначале возбуждается дуга между электродом и соплом (дежурная), а затем при касании ее факела изделия происходит
17
автоматическое зажигание основной дуги между электродом и изделием. После возбуждения основной дуги дежурная дуга отключается. Дежурная дуга питается от того же источника через токоограничивающее сопротивление.
В плазмотронах с дугой прямого действия в изделие вводится дополнительное тепло за счет электрического тока и к.п.д. их значительно выше, чем у плазмотронов косвенного действия. В связи с этим плазмотроны с дугой прямого действия целесообразно применять для сварки, резки, наплавки, а плазмотроны с дугой косвенного действия – для напыления, нагрева и т.д.
Электрошлаковая сварка. Процесс идет в пространстве, ограниченном кромками свариваемой детали и ползунами (рис. 1.8). Тепло в шлаковой ванне выделяется за счет прохождения в ней тока Iш. В холодном состоянии шлак практически не электропроводен. Поэтому для наведения шлаковой ванны сначала возбуждают дугу, которая расплавляет флюс, образуется шлаковая ванна, которая гасит дугу, в результате чего начинается шлаковый процесс. В результате тепловыделения в шлаке увеличивается его электропроводность. Объем расплавленного шлака увеличивается, и весь ток от электрода 5 к свариваемому изделию 1 будет проходить через шлаковую ванну 3. Вследствие выделения тепла в шлаковой ванне расплавляются электрод 5 и кромка свариваемого изделия 1, образуя металлическую ванну 2. Для предотвращения вытекания расплавленного металла и шлака применяют специальные медные формирующие устройства 4 (ползуны).
Этот способ применяется для сварки металлов достаточно большой толщины, причем шов выполняется на всю толщину свариваемого металла за один проход. В
промышленности освоена сварка изделий с толщиной металла в месте выполненного шва около 1 м.
Электроннолучевая сварка. Сварка осуществляется в вакуумной камере при давлении 10-1 – 10-5 мм рт.ст. (1.3 – 0,0013 Па). Тепло в изделии, подлежащее сварке, выделяется в результате торможения электронов направленного электронного луча. Луч формируется в специальной электронной пушке, имеющей нагреваемый катод (эмиттер). Питание пушки осуществляется от высоковольтного выпрямителя.
Фокусировка пучка электронов обеспечивается воздействием электромагнитных полей специальной фокусирующей электромагнитной линзы.
Выполнение сварных швов на изделии заданной длины и направления обеспечивается перемещением сварочного стола при помощи привода, или электронного луча вследствие перемещения пушки, или отклонения луча с помощью электромагнитной отклоняющей системы.
18

|
I |
|
6 |
5 |
4 |
|
Lв |
|
4 |
|
|
U |
Lш |
|
3 |
||
|
||
2 |
|
1
Рис. 1.8. Схема электрошлаковой сварки, 1 – сваренное изделие; 2 – жидкий металл; 3 – шлаковая ванна; 4 – ползуны; 5 – электрод; 6 – скользящий контакт.
Этот способ применяется при изготовлении изделий из легкоокисляющихся или тугоплавких металлов. Он может обеспечить высокие скорости сварки и малые деформации свариваемых изделий. Лазерная сварка . В 1960 – 1961гг. появились первые лабораторные макеты оптических квантовых генераторов (ОКГ) или так называемые лазеры. В настоящее время лазерная сварка находит применение
вприборостроении.
Всоответствии с квантовой теорией энергия элементарных излучателей может изменяться только скачками, кратными некоторому значению, постоянному для данной частоты излучения. Минимальная порция энергии называется квантом
энергии
w = hγ,
где h – постоянная Планка (6,625*10-34 В*А*с2), γ – частота излучения.
В любой микросистеме, включающей в себя молекулы, атомы, ионы и электроны, их движение и ориентация соответствуют дискретному ряду энергий – энергетическим состояниям или уровням. Внешние источники энергии, взаимодействуя с микросистемой, изменяют ее внутреннюю энергию. При этом
частицы совершают переход с одного энергетического уровня на другой (возбуждаются). Для перевода активных частиц из равновесного в возбужденное состояние служат источники возбуждения, которые называются генераторами накачки. Они могут воздействовать на активное вещество следующими основными способами:
световым полем; потоком электронов;
потоком радиоактивных частиц; химическим возбуждением.
19
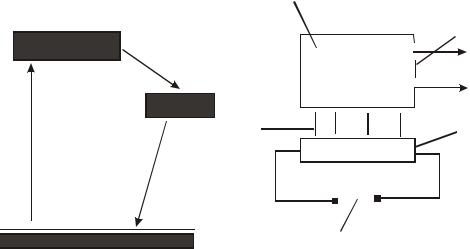
Энергия |
4 |
Высший уровень 2 |
5 |
|
Метастабильный уровень 3
3 2
Л = 6943А
Основное состояние |
1 |
|
|
Рис. 1.9. Схема энергетических уровней ионов хрома в |
Рис. 1.10. Принципиальная блок схема действия ОКГ |
рубине |
1 – источник питания; 2 – источник возбуждения; 3 – |
|
электромагнитное поле; 4 – активное вещество; 5 – |
|
полупрозрачное зеркало, образующее открытый |
|
резонатор. |
Наиболее применимы системы возбуждения световым полем, состоящие из источника света – газоразрядной лампы «накачки» спирального или карандашного типа и рефлектора. Источником питания обычно является конденсатор большой мощности, заряжаемый от выпрямителя.
Механизм возбуждения и излучения показан на примере трехуровневого лазера, где в качестве активного вещества используется синтетический рубин с примесью хрома. (рис. 1.9 и 1.10). При освещении кристалла рубина белым или зеленым светом ионы хрома возбуждаются и переходят на высший уровень 2, поглощая энергию зеленой части спектра. Уровень 2 нестабилен и частицы быстро совершают безизлучательный переход на промежуточный (метастабильный) уровень 3, где может находиться значительное число частиц. При воздействии на кристалл
слабого излучения соответствующей частоты или при переходе хотя бы одной из частиц на низший уровень все частицы с промежуточного уровня совершают переход (λ = 6943 А – красный цвет) на основной уровень 1 синфазно. Это и создает когерентное излучение, монохроматическое, так как уровень 3 узкий.
Узконаправленность и резонансное усиление энергии достигается с помощью объемного резонатора, имеющего два строго параллельных зеркала, например, торцы кристалла, между которыми тысячекратно отражаются световые лучи. В ОКГ одно из зеркал делается полупрозрачным, и через него происходит выход излучения.
Энергия, излучаемая в современных лазерах, составляет величины от единиц до сотен Дж. Плотность энергии до ста Дж./мм2.
Вопросы для самопроверки к разделу 1.
1.Чем обеспечивается монолитность твердых тел?
2.Чем обеспечивается связь атомов твердых тел?
3.Перечислите виды элементарных связей атомов в твердых телах.
20