
- •Калиниченко О.И., Зыбинский П.В., Хохуля А.В.
- •Рекомендовано научно-издательским советом Донецкого национального технического университета в качестве учебного пособия для студентов, обучающихся по направлению «Горное дело» специальности «Бурение»
- •Донецк 2012
- •Калиниченко О.И., Зыбинский П.В., Хохуля А.В.
- •Рецензенты:
- •ПРЕДИСЛОВИЕ
- •2 ОСНОВЫ ГОРНОЙ ТЕХНОЛОГИЧЕСКОЙ СИСТЕМЫ
- •Число оборотов ротора изменяют при помощи передаточных механизмов лебедки или же путем замены приводных колес. Чтобы не связывать работу лебедки с работой ротора, в ряде случаев применяют индивидуальный, т.е. не связанный с лебедкой, привод.
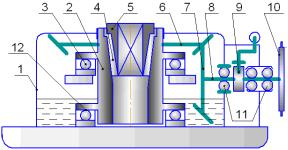
вала трансмиссии. Роторы всех типов устанавливают строго по центру скважины.
Ротор имеет стальную станину 1, во внутренней полости которой на двух радиаль- но-упорных подшипниках 3 и 12 установлен
стол 2 с зубчатым вен-
Рис. 3.12. Принципиальная схема ротора цом 6. На наружном конце вала 8 расположено приводное колесо 10 (присоединительный фланец), а на внутреннем
конце коническая шестерня 7, находящаяся в постоянном зацеплении с зубчатым венцом 6. На средней части вала для стопорения стола ротора в заданном положении имеется храповое колесо 9. Вкладыш ротора 4 состоит из двух половин. Для предохранения вкладыша ротора от произвольного вертикального перемещения вверх ротор имеет специальные стопоры. Вкладыши 5 являются зажимами для ведущей трубы. Станина ротора воспринимает и передает на основание все нагрузки, возникающие в процессе бурения и при спускоподъемных операциях. Внутренняя полость станины представляет собой масляную ванну.
Число оборотов ротора изменяют при помощи передаточных механизмов лебедки или же путем замены приводных колес. Чтобы не связывать работу лебедки с работой ротора, в ряде случаев применяют индивидуальный, т.е. не связанный с лебедкой, привод.
Буровые насосы служат для нагнетания большого количества бурового раствора (20— 50 л/с) по бурильным трубам в скважину и обратно на поверхность. При глубоком бурении применяются в основном двухцилиндровые поршневые насосы двойного действия (рис. 3.13). Используются также и трехцилиндровые плунжерные насосы одинарного действия, которые при одной и той же гидравлической мощности имеют меньшую массу, чем поршневые (рис. 3.14).
Насосы состоят из двух основных частей – приводной и гидравлической, соединенных между собой в единую конструкцию, смонтированную на раме 18. Приводная часть включает в себя эксцентриковый вал (коленчатый вал) 10, который через шкив 6, трансмиссионный вал 7 и зубчатую передачу 8 получает движение от двигателя и передает через кривошип 9 шатунам 19. Каждый шатун своей головкой соединен с ползуном (крейцкопфом) 5, размещенным между накладками станины. К ползуну прикреплен
196

|
шток 4. |
|
|
|
Гидравлическая |
||
|
часть состоит из гид- |
||
|
равлического |
блока, |
|
|
всасывающего 12 и на- |
||
|
гнетательного |
11 кол- |
|
|
лекторов и компенсато- |
||
|
ра 14, например, сфе- |
||
|
рического. |
|
|
|
Гидравлический |
||
|
блок включает |
в себя |
|
|
цилиндры |
3, |
поршни |
Рис. 3.13. Принципиальная схема поршневого насоса |
(штоки) 2, всасываю- |
||
щие 13 и |
нагнетатель- |
ные клапаны 1.
От двигателя вращение передается через приводной шкив 6 на входной вал 7. Через пару зубчатых колес 8 на входном валу вращение передается на коленчатый вал 10. При вращении вала 10 вращается кривошип 9, который приводит в движение шатун 19, последний придает возвратнопоступательное перемещение ползуну 5. С ползуном через шток 4 соединен плунжер 2 (или поршень 2, см. рис. 3.13).
Гидравлический блок плунжерных насосов (рис. 3.14) имеет три плунжера, три всасывающих клапана 13 и три нагнетательных 1. Работа такого насоса, относящегося к механизмам простого действия, заключается в следующем. При ходе плунжера вправо в камере клапанов создается разрежение, поэтому нагнетательный клапан 1 закрывается, а всасывающий клапан 13 открывается, и жидкость под действием атмосферного давления по всасывающему коллектору 12 поступает через всасывающий клапан 13 в камеру насоса. Плунжер 2, дойдя до крайнего правого положения, начинает
|
двигаться |
влево. При |
||
|
этом |
ходе плунжера |
||
|
создается |
«сжатие» |
||
|
жидкости, |
всасываю- |
||
|
щий клапан 13 закры- |
|||
|
вается, а нагнетатель- |
|||
|
ный |
1 открывается |
и |
|
|
пропускает |
жидкость |
||
|
через |
нагнетательный |
||
|
коллектор 11 в напор- |
|||
|
ный |
трубопровод, |
по |
|
|
которому жидкость че- |
|||
Рис. 3.14. Принципиальная схема плунжерного бурового |
рез вертлюг-сальник |
и |
||
насоса |
бурильную |
колонну по- |
||
|
|
|
|
|
197 |
|
|
|
|

дается в скважину.
Подача рассмотренного плунжерного насоса за один оборот кривошипного вала определяется рабочим объемом цилиндра Q1 FS .
Поскольку кривошипный вал насоса делает n об/мин, то, с учетом
потерь, которые вызываются некоторым запаздыванием открывания и закрывания клапанов, неплотностью пригонки поршня, клапанов, наличием воздуха - фактическая подача насоса Q равна
Q F S n m , м3/с,
60
где F – площадь поперечного сечения плунжера, м2; S - ход плунжера, м; m - количество цилиндров (плунжеров 3); n - число двойных ходов
плунжера; - коэффициент подачи.
Гидравлический блок поршневых насосов, относящихся к установкам двойного действия, как правило, имеет два цилиндра 3 с поршнями 2. Каждый цилиндр имеет два всасывающих клапана 13 и два нагнетательных 1 (рис. 3.13).
В отличие от выше рассмотренного плунжерного насоса, у поршневого насоса двойного действия всасывание и нагнетание совершается при каждом рабочем ходе. В процессе хода поршня слева направо жидкость поступает в левую рабочую полость цилиндра 3 и выталкивается поршнем из правой рабочей полости цилиндра через правый клапан 1 в коллектор 11, и далее в напорный трубопровод объеме
Q1 (F f )S ,
где f – площадь сечения штока, м2; F - площадь сечения цилиндров;
S - длина хода поршня.
При перемещении поршня 2 справа налево жидкость поступает в правую рабочую полость цилиндра 3 и одновременно через левый клапан 1 вы-
талкивается из левой рабочей полости в объеме Q1 FS .
Таким образом, за один оборот вала из цилиндра насоса в напорный трубопровод поступает жидкость в объеме Q1 FS (F f )S .
Фактическая подача насоса Q при числе цилиндров m , равна
Q m(2F f )n S ,
60
Для снижения колебаний давления на выходе из насоса, вызванных неравномерностью подачи промывочной жидкости предназначены компенсаторы. Сферический пневматический компенсатор состоит из корпуса 14, разделенного на две полости резиновой диафрагмой 16, армированной металлическим сердечником 17. Верхняя полость внутри диафрагмы заполняется воздухом или азотом при определенном начальном давлении (в пределах 0,3…0,6 от рабочего давления). На крышке компенсатора установлено
198
вентильное устройство с манометром 15. Во время работы насоса жидкость при давлении выше начального давления газа в полости компенсатора, проходя через отверстие нагнетательного коллектора, поднимает диафрагму и сжимает газ до тех пор, пока давление газа не станет равным давлению перекачиваемой насосом жидкости.
В те периоды, когда мгновенная подача жидкости превышает среднюю подачу, жидкость поступает в компенсатор, дополнительно сжимая газ, а когда подача меньше средней – недостаток подачи возмещается за счет увеличения объема газа компенсатора.
Силовой привод обеспечивает функционирование всей буровой установки, снабжая энергией лебедку, буровые насосы и ротор. Причем, силовым приводом ротора чаще всего является привод буровой лебедки.
Привод установки может быть автономным, не зависящим от системы энергоснабжения (например, дизельный или дизель-электрический) и неавтономный с питанием от промышленных электросетей (электрический).
Силовой привод может быть индивидуальным и групповым. Индивидуальный привод приводит в действие один исполнительный механизм (например, насос), групповой – два и более исполнительных механизма.
Электрический привод от электродвигателей переменного и постоянного тока отличается простотой в монтаже и эксплуатации, высокой надежностью и экономичностью, но применим только в электрифицированных районах.
Дизельный привод применяют в районах, не обеспеченных электроэнергией необходимой мощности. Преимуществами двигателей внутреннего сгорания (ДВС) при использовании в качестве привода являются высокий КПД, небольшие расходы топлива, воды и масла. Основной недостаток ДВС - отсутствие реверса, поэтому необходимо специальное устройство для получения обратного хода.
Дизель-электрический привод состоит из приводного электродвигателя, связанного с исполнительным механизмом, генератора, питающего этот электродвигатель, и дизеля, приводящего во вращение вал генератора.
Обобщенная схема расположения основного оборудования и с приводом от двигателей внутреннего сгорания приведена на рис. 3.15.
Дизели ДВС №2, №3 и №4 (групповой привод) предназначены для привода лебедки и одного насоса №2. Дизель №1 служит приводом насоса №1 (индивидуальный привод). Дизели в групповом приводе соединяются при помощи клиноременной трансмиссии.
Лебедка состоит из двух частей: собственно лебедки и коробки передач, соединенной при помощи двух карданных валов.
Привод ротора осуществляется от лебедки. Передача вращения на валы коробки передач, лебедки, ротора и буровых насосов осуществляется через шинно-пневматические муфты (ШПМ), включение и выключение кото-
199
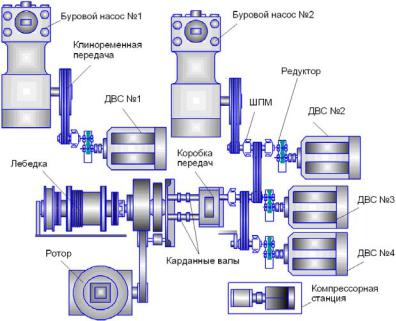
рых обеспечивается дистанционно сжатым воздухом, подающимся в пневматическую систему буровой установки от компрессорной станции.
Суммарная мощность силового привода буровых установок составляет от 1000 до 4500 кВт. В процессе бурения она распределяется на привод буровых насосов и ротора. При проведении спускоподъемных операций основная энергия потребляется лебедкой, а остальная часть расходуется в основном компрессорами, вырабатывающими сжатый воздух, используемый в качестве источника энергии ШПМ, машинных буровых ключей, служащих для свинчивания и развинчивания бурильных и обсадных труб и др.
Рис. 3.15. Обобщенная схема расположения силового привода оборудования буровой установки
Оборудование для спуско-подъемных операций. Для производства спускоподъемных операций предусматривается определенный набор оборудования, применяющегося как для захвата и удержание на весу бурильной колонны в процессе ее спуска или подъема, так и для свинчивания и развинчивания труб.
Для захвата и удержания на весу колонны бурильных (обсадных) труб служат элеваторы, которые с помощью штропов подвешивается на крюке
(рис. 3.16).
Элеваторы отличаются размерами, грузоподъемностью и конструктивным исполнением. Широкое распространение имеют элеваторы серии
200
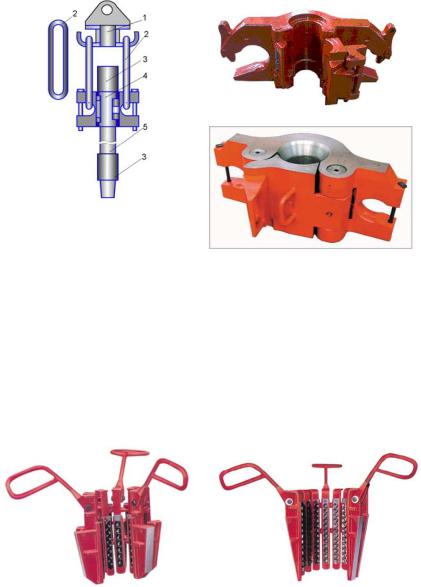
КМ (с цилиндрическим плоским захватом) и серий DDZ и CDZ (с конусным захватом труб) (рис. 3.17).
Рис. 3.16. Схема захвата и удержания на весу колонны бурильных (обсадных)
труб с помощью элеватора:
1 – крюк; 2 - штропы; 3 – замок бурильной колонны; 4 – элеватор; 5 - бурильная труба
а)
б)
Рис. 3.17. Внешний вид элеваторов:
а) – КМ; б) - СDZ
В процессе спускоподъемных операций подвеска и удержание бурильной колонны в роторном столе обеспечивается с помощью клиньев, которые вручную устанавливаются во вкладыш ротора. Клинья имеют коническую расточку, что обеспечивает надежное прижатие их к поверхности бурильной колонны.
Среди современных моделей клиньев можно выделить ручные клиновые захваты типа DCS (рис. 3.18), которые могут работать в диапазоне от 76 до 355 мм, а также CMS-XL для работы с обсадными трубами, внешний диаметр которых попадает в диапазон от 168 до 762 мм (рис. 3.19).
Рис. 3.18. Ручные клиновые |
Рис. 3.19. Ручные клиновые захваты для |
захваты типа DCS |
обсадных труб типа CMS-XL |
|
201 |
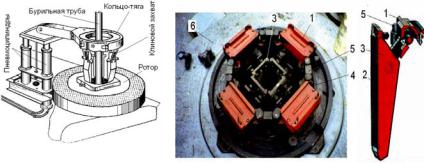
Для механизированного захвата и освобождения бурильных и обсад-
ных труб применяются автоматические клиновые захваты типа ПКР (на-
пример, ПКР-560). Клиновой захват монтируется в роторе и имеет четыре клина (рис. 3.20-3.21).
Рис. 3.20. Схема пневматиче- |
Рис. 3.21. Пневматические клинья ПКР-560, |
ского клинового захвата |
встроенные в ротор |
Корпус ПКР-560 (4) устанавливается в роторе 6 вместо роторных вкладышей и имеет четыре вертикальных паза для направления штоков 5, связанных в нижней части с кольцом-тягой (рис. 3.20). Перемещение тяги вверх и вниз обеспечивается пневмоцилиндрами, управление которыми вынесено на пульт бурильщика. Во внутреннее отверстие корпуса устанавливаются клинья 3. Клинья при помощи держателей 1 шарнирно прикреплены к кольцу-тяге. Конусная поверхность клиньев выполнена в виде плоскости. Клинья снабжены плашками 2 с зубчатой насечкой, обеспечивающей надежный захват бурильных и обсадных труб.
Для захвата бурильных и обсадных труб с наружными диаметрами 50…178 мм и удержания их на весу в устье нефтяных скважин в процессе спускоподъемных операций при ремонте и бурении скважин используются спайдеры типа СПГ (рис. 3.22). Для удержания на весу колонны обсадных труб диаметром 194-450 мм применяются спайдеры типа СОТШ или САГ-2.
В состав спайдеров типа СПГ входят следующие основные узлы: 1 - корпус с блоком клиньев 2; 3 – дверца; 4 - цилиндр (гидравлический или пневматический); 5 - система рычагов с защелкой.
Спайдеры типа СОТШ состоят из стального литого корпуса с отверстием в центре для пропуска труб. В корпус спайдера установлен комплект из четырех плашек. Плашки связаны с кольцом при помощи пальцев. Вращая кольцо на некоторый угол в одну, или в другую сторону, можно поднимать или опускать плашки и тем самым захватывать трубы плашками или освобождать их от контакта с трубами. Вращение кольца с плашками обеспечивается рычагом, установленным в радиальное отверстие кольца. Каждый комплект плашек приспособлен для захвата только одного диаметра, а
202
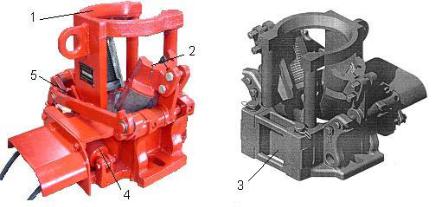
корпус спайдера в зависимости от размера конусного отверстия допускает установку комплектов плашек для труб двух-трех размеров.
Рис. 3.22. Внешний вид спайдеров типа СПГ
Для механизации работ по свинчиванию и развинчиванию бурильных и обсадных труб в процессе спускоподъемных операций используются автоматические буровые ключи типа АКБ и подвесные ключи типа ГКШ и др. Как правило, ключами АКБ производится свинчивание труб, а последующее докрепление их резьбовых соединений выполняется с помощью машинных ключей типа КМБ и ПБК.
Стационарный автоматический буровой ключ АКБ - 3М или его мо-
дификация АКБ-3М2 (рис. 3.23) устанавливается между лебедкой и ротором на специальном фундаменте. Ключ состоит из трех основных элементов: блока ключа (6, 9), каретки 2 с пневмоцилиндрами 4, закрепленной на стойке 5, и пульта управления 3. Механизмы ключа работают при помощи пневмодвигателя 8 и пневмоцилиндров 4 от сети сжатого воздуха.
Блок ключа – основной механизм, выполняющий операции свинчивания и развинчивания труб. В передней части блока ключа имеются два трубозажимных устройства – верхнее 9 и нижнее 6. Верхнее предназначено для захвата и вращения трубы, нижнее для захвата колонны труб и удержания её от проворота. По направляющим полозьям блок ключа перемещается вдоль каретки под действием двух пневматических цилиндров 4, обеспечивая подвод трубозажимного устройства к бурильной трубе и отвод от неё. Вращение трубозажимного устройства блока ключа осуществляется от пневмодвигателя 8 через редуктор 7.
Каретка свободно вращается в верхней части колонны, и её положение при работе фиксируется. Каретка с блоком ключа может перемещаться вдоль колонны по высоте. Нижней частью ключ жестко крепится к основа-
203
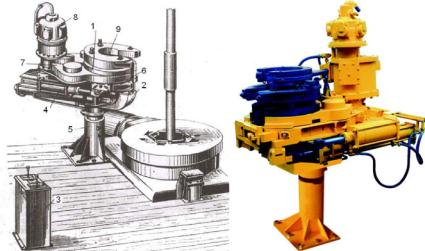
нию буровой. Управление работой ключа обеспечивается дистанционно с пульта 3.
Рис. 3.23. Схема размещения и основные |
|
элементов бурового ключа АКБ-3М: |
Рис. 3.24. Внешний вид автома- |
1 – блок ключа; 2 – каретка; 3 – пульт |
тического бурового ключа АКБ-4 |
управления; 4 - пневмоцилиндры; 5 - стой- |
(АКБ-3М2) |
ка; 6, 9 – устройства блока ключа; 7 - ре- |
|
дуктор; 8 - двигатель |
|
На базе ключа АКБ-3М2 разработан ключ буровой автоматический АКБ-4 (рис.3.24), снабженный двухскоростной коробкой передач, которая, по сравнению с АКБ-3М обеспечивает более высокий крутящий момент (70 кНм против 30 кНм), что позволяет обходиться без применения машинных ключей для докрепления или раскрепления труб. Крутящий момент прикладывается к свинчиваемому соединению без ударов, что значительно снижает износ бурильных труб и зажимных элементов самого ключа. На ключе установлен ограничитель крутящего момента, что позволяет свинчивать соединения с заранее заданным моментом, по достижении которого пневмомотор отключается.
Ключ АКБ-3М2.Э2 в отличие от АКБ-4 имеет двухскоростной электропривод. Ключ снабжен также системой обогрева (в зимний период)
Для докрепления и раскрепления резьбовых соединений труб наиболее часто применяются машинные ключи типа КМБ (рис. 3.25 и 3.26) с диапазоном захвата труб диаметром от 60 до 451мм. Операция докрепления и первичного раскрепления резьбовых соединений бурильных и обсадных колонн, осуществляется двумя машинными ключами; при этом один ключ (задерживающий) – неподвижный, а второй (завинчивающий) – подвижный. Ключи подвешиваются в горизонтальном положении. Для этого в верхней
204
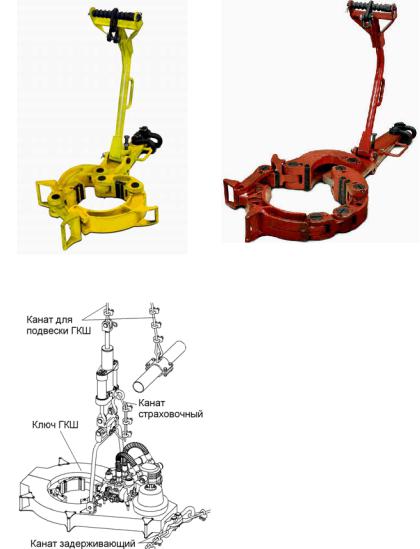
части вышек (у палатей) на специальных пальцах укрепляют ролики и через них перекидывают стальной канат. Один конец этого каната прикрепляется к подвеске ключа, а другой – к противовесу, уравновешивающему ключ, и облегчающему перемещение ключа вверх или вниз.
Рис. 3.25. Внешний вид ключа |
Рис. 3.26. Внешний вид ключа машинного |
||
машинного бурового КМБ-М |
бурового КМБ 60-451. |
||
|
Автоматические |
подвесные |
|
|
гидравлические ключи типа ГКШ, |
||
|
предназначены |
для свинчивания и |
|
|
развинчивания обсадных труб с на- |
||
|
ружными диаметрами 114 – 324 мм |
||
|
(рис. 3.28) и бурильных труб с на- |
||
|
ружными диаметрами от 50 мм до |
||
|
141 мм (рис. 3.29). |
|
|
|
Гидравлический |
ключ ГКШ |
|
|
подвешивается на вышке или мачте |
||
|
на канате (рис. 3.27). |
|
|
|
Принцип |
работы ключей, |
|
|
представленных на рис. 3.28 и 3.29 и |
||
|
заключается в следующем. Энергия |
||
|
потока жидкости, направленная че- |
||
|
рез гидрораспределитель 3, преоб- |
||
|
разуется гидромотором 2 во враща- |
||
Рис. 3.27. Схема монтажа гидроключа |
тельное движение вала. Рабочая зо- |
||
ГКШ |
на вращения ротора ограждена за- |
||
|
слонкой 8. |
|
|
|
205 |
|
|

Вал гидромотора через зубчатый редуктор 1 и коробку передач 4 приводит в движение ротор ключа в сборе с челюстями 7. Происходит автоматический захват трубы. Цилиндры подвески 10, установленные на оси подвески 5, жестко связанной с рамой 5 компенсируют вес ключа при свинчивании или развинчивании трубы, тем самым, снижается осевую нагрузку на трубу и элементы ключа.
В состав гидрораспределителя входит клапан давления 11, позволяющий регулировать давление в линии нагнетания и получать необходимые моменты свинчивания труб. Контроль давления нагнетания жидкости осуществляется по
манометру.
В ГКШ для обсадных труб (рис. 3.28) усилие предварительного поджатия главной подвижной челюсти определяется постоянным магнитом, установленным на эту челюсть. При работе ГКШ с обсадными трубами компенсация реактивного момента на ключе обеспечивается с помощью задерживающего каната.
В ГКШ для работы с бурильными трубами (рис. 3.29, а), управление гидромотором обеспечивается рукоятками «а» и
«б». Рычаг «б» позволяет управлять секцией гидромотора с меньшим объемом (повышенная частота вращения при меньшем крутящем момента), а рычаг «а» – секцией гидромотора с большим объемом (пониженная частота вращения при большем крутящем момента). При одновременном отклонении рычагов управления в одну и ту же сторону крутящий момент на роторе гидроключа максимальный.
Гидроключи ГКШ для бурильных труб комплектуются стопорным устройством, предназначенным для компенсации реактивного момента на ключе и предотвращения возможного вращения колонны бурильных труб в скважине при их свинчивании и развинчивании (рис. 3.29, б, в).
206
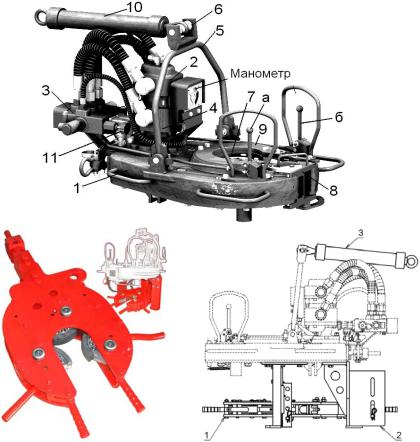
а)
б) |
в) |
Рис. 3.29. Ключ ГКШ для свинчивания (развинчивания) бурильных труб: а – внешний вид ГКШ (1- редуктор; 2 – гидромотор; 3 - гидрораспределитель;
4 – коробка передач; 5 – рама; 6 – ось; 7 – «челюсти»; 8 – заслонка; 9 – ротор; 10 – цилиндры подвески; 11 – клапан); б – стопорное устройство; в – схема монтажа стопорного устройства (1 – стопорное устройство в сборе; 2 – крепление для стопорного устройства; 3 – цилиндр подвески)
В последнее время, как в отечественной практике, так и за рубежом, особенно при бурении на море, используются буровые установки с силовым вертлюгом в виде верхнего подвижного вращателя (рис. 3.30). Система верхнего привода является относительно новым типом механизмов буровых установок, при этом силовой вертлюг обеспечивает производство целого ряда технологических операций, выполняя функции крюка, вертлюга и ротора, а также механических и машинных ключей.
207

При его пользовании не нужна бурильная ведущая труба, а также намного облегчается труд помощника бурильщика, поскольку подвижный вращатель (в функции элеватора) механически подается в необходимую позицию.
Рис. 3.30. Внешний вид установки G-75 с силовым вертлюгом
Привод силовых вертлюгов обеспечивается от электродвигателей постоянного и переменного тока, а также гидравлического двигателя. Основными элементами системы верхнего привода являются: направляющие рельсы; блок двигателя с трансмиссией (как правило, двух-, трехскоростной) и
208
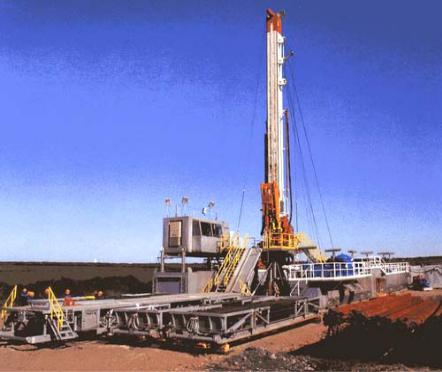
стволом для присоединения бурового шланга; блок трубодержателя и элеватор для бурильных труб.
В общем случае, система верхнего привода обеспечивает: вращение бурильной колонны при бурении, проработке и расширении ствола скважины методом «сверху-вниз» и «снизу-вверх»; свинчивание, закрепление, раскрепление и развинчивание бурильной колонны; проведение спускоподъемных операций; проведение операций по спуску обсадных труб; наращивание бурильной колонны свечами и одиночными трубами; промывку скважины.
На рис. 3.31 показан общий вид канадской буровой установки TT SENSA с силовым вертлюгом.
Рис. 3.31. Общий вид буровой установки TT SENSA
Технико-технические данные установок такого типа можно рассматривать как наиболее продуктивные для условий бурения скважин в угольных регионах Украины. Кроме мобильности, компактности, большой грузоподъемности, возможности развертывания на месте бурения в течение нескольких часов такая установка имеет ряд технических достоинств, таких как: отсутствие растяжек устойчивости буровой вышки; наличие реечного
209
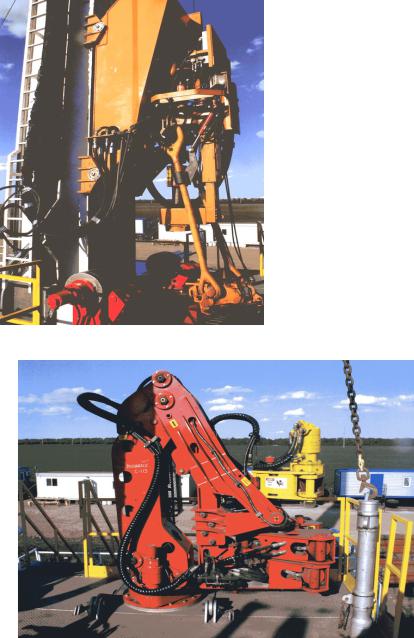
механизма для спускоподъемных операций (рис. 3.32), что позволяет быстро (2-3 мин.) наращивать или заменять бурильные трубы; обеспечение вращения бурового инструмента с помощью вертлюга – подвижного вращателя, заменяющего ротор на нулевой площадке, упрощающего конструкцию и обслуживание процесса бурения. Для выполнения операций свинчивания-развинчивания бурильных труб используется гидравлический ключ
«NNS SENSA» (рис. 3.33).
Рис. 3.32. Реечный механизм установки TT SENSA
Рис. 3.33. Гидравлический ключ буровой установки TT SENSA
210

Рис. 3.34. Схема компоновки бурильной колонны
Бурильная колонна. Бурильная колонна связывает поверхностное оборудование с породоразрушающим инструментом и представляет собой многозвенную систему инструментов между вертлюгом на поверхности и долотом на забое скважины.
Бурильная колонна служит средством передачи вращательного движения от ротора к долоту; создания нагрузки на долото; подвода бурового раствора к турбобуру (при турбинной бурении), к винтовому двигателю (при бурении винтовыми двигателями); восприятия реактивного момента забойного двигателя; подвода бурового раствора к забою при всех способах бурения.
Основными элементами, составляющими бурильную колонну, являются (рис. 3.34): ведущая бурильная труба, бурильные трубы, замки, утяжеленные бурильные трубы, переводники, опорноцентрирующие элементы (центратор, калибратор, стабилизатор, протектор) и др.
Ведущие бурильные трубы явля-
ются соединительным звеном между вертлюгом и бурильными трубами и служат для передачи вращения от ротора к бурильной колонне в процессе углубки скважины или для восприятия ротором реактивного момента забойного двигателя. Эти трубы имеет чаще всего квадратное сечение (рис. 3.35), и проходят через квадратное отверстие в роторе. Ведущие трубы выпускаются длиной 13-17 м, со стороной квадрата 112, ,140 и 155 мм и диаметром канала соответственно 74, 85 и 100 мм.
Утяжеленные бурильные трубы
(УБТ) (рис. 3.36), устанавливаются непосредственно над долотом или забой-
211

ным двигателем и служат для создания осевой нагрузки на долото и повышения устойчивости (жесткости) нижней части колонны. Поскольку, благодаря весу УБТ остальная, выше расположенная бурильная колонна оказывается растянутой, создаются предпосылки для обеспечения прямолинейности скважины. На долото должно быть приложено максимум 85 % общего веса УБТ. Остальной вес используется для растяжения бурильной колонны во избежание ее продольного изгиба. Сбалансированные УБТ (УБТС) изготавливают из хромоникельмолибденовых сталей. Концы УБТС подвергаются термообработке. УБТС изготавливают в основном диаметрами 178, 203 и 229 мм длиной 6 м. Масса одного метра труб составляет, соответственно -
156, 215 и 273 кг.
Рис. 3.35. Ведущие трубы
Рис. 3.36. Утяжеленные бурильные трубы: а – круглого сечения; б – со спиральными канавками
212

Обычные гарячекатанные УБТ выпускаются диаметрами 95, 108, 146, 178, 203, 219 и 245 мм,
длиной 6, 8 и 12 м. Масса одного метра труб составляет, соответственно
- 47, 59, 98, 145, 192, 220 и 258 кг.
Бурильные трубы
составляют основную часть колонны. Они предназначены для передачи вращения долоту (при роторном бурении) и восприятия реактивного момента при бурении забойными двигателями, создания нагрузки на долото, подачи бурового раствора на забой скважины для очистки его от разбуренной породы и охлаждения долота, подъема из скважины изношенного долота и спуска нового и др.
Бурильные трубы, как правило, имеют коническую резьбу с обеих сторон. Для обеспечения прочности резьбовых соединений концы труб де-
лают утолщенными. По способу изготовления трубы могут быть цельными и с приваренными соединительными концами (рис. 3.37, а).
По конструктивному исполнению цельные трубы могут быть с высаженными наружу концами (рис. 3.37, в) и трубы с высаженными внутрь концами (рис. 3.37, б).
Трубы всех типов изготавливаются длиной: 6; 8 и 11,5 м с номиналь-
ными наружными диаметрами 60; 73; 89; 102, 114, 127, 140 и 168 мм. Тол-
щина стенок труб составляет от 7 до 11 мм.
213
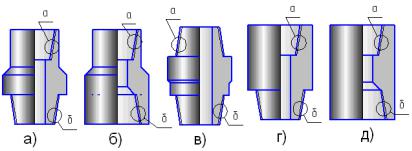
На концах бурильных труб нарезают мелкую наружную резьбу, на которую навинчивают замки, служащие для соединения бурильных труб при составлении бурильных свечей.
Замки предназначены для соединения бурильных труб. Замок состоит из замкового ниппеля 1 и замковой муфты 2, соединяющихся между собой крупной конической резьбой (рис. 3.37, б, в). В зависимости от области применения, различают: замки с нормальным проходным сечением (ЗН) для соединения труб с высаженными внутрь концами; замки с широким (ЗШ) и с увеличенным (ЗУ) проходным сечением для соединения труб с высаженными наружу концами.
К вспомогательным составляющим колонны относятся переводники различного назначения и опорно-центрирующие элементы.
Переводники представляют собой разновидность соединительных элементов бурильной колонны с резьбой различного профиля и размерами. Их подразделяют на две группы: штанговые – для соединения ведущей трубы с вертлюгом и бурильными трубами; промежуточные – для соединения других элементов колонны.
По назначению переводники для бурильных колонн подразделяются на переходные (П) (рис. 3.38, а), муфтовые (М) (рис. 3.38, б) и ниппельные
(Н) (рис. 3.38, в). Выделенные индексы используются при маркировке переводников (например, шифр переводника П-101/88 обозначает Переходный переводник с замковой резьбой «а» - З-101 и замковой резьбой «б» - З-88).
Рис. 3.38. Переводники для бурильной колонны и ведущих бурильных труб
Переводники выпускаются как с левой (Л), так и с правой резьбой (без индекса).
Переводники для ведущих труб подразделяются на верхние (ПВ) (рис. 3.38, д) и нижние (ПН) (рис. 3.38, г). При маркировке переводников указывается его индекс, сторона квадрата и присоединительная резьба «б» (например, шифр переводника ПВ 140хЗ-147 обозначает Переводник верхний со стороной квадрата 140 мм и присоединительной левой резьбой «б» З- 147Л). Для переводников типа ПН характерным является правая нарезка резьбы «б».
214
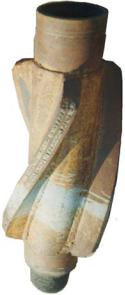
К опорно-центрирующим элементам колонны бурильных труб отно-
сятся калибраторы, центраторы, стабилизаторы и протекторы. Калибратор предназначен для калибрования ствола скважины (по
диаметру долота) и улучшения работы долота за счет уменьшения поперечных колебаний труб в призабойной части скважины.
Калибраторы включаются в состав компоновки между долотом и утяжеленными бурильными трубами. К наиболее распространенному виду таких устройств относятся калибраторы лопастного типа (рис. 3.39).
|
Центратор – элемент компоновки, |
|
|
предназначенный для центрирования бу- |
|
|
рильной колонны в месте установки центра- |
|
|
тора. В отличие от калибраторов центратор |
|
|
способствует только соосному размещению |
|
|
компоновки и оси скважины. Он устанавли- |
|
|
вается в сжатой части компоновки в местах |
|
|
предполагаемых изгибов утяжеленных бу- |
|
|
рильных труб и выполняет роль промежу- |
|
|
точных опор. Предназначен центратор для |
|
|
предупреждения искривления ствола при |
|
|
бурении скважины. Боковые элементы цен- |
|
|
тратора касаются стенок скважины, обеспе- |
|
Рис. 3.39. Калибратор |
чивая соосность бурильной колонны и сква- |
|
жины. |
||
|
Как правило, центраторы и калибраторы используются в качестве опорно-центрирующих элементов при бурении глубоких скважин с высокими осевыми нагрузками на долото.
Стабилизатор устанавливается над долотом и предназначен для центрирования и сохранения жесткости бурильной колонны на участке длины стабилизатора. В качестве стабилизатора наиболее часто используют утяжеленные бурильные трубы спирального сечения (см. рис. 3.36, б).
Протекторы предназначены для предохранения бурильных труб и соединительных замков от поверхностного износа, а обсадной колонны - от протирания при перемещении в ней бурильных труб. Обычно применяют протекторы с плотной посадкой, представляющие собой резиновое кольцо, надетое на бурильную колонну над замком. Наружный диаметр протектора превышает диаметр замка.
Породоразрушающий инструмент предназначен для концентриро-
ванной передачи энергии горной породе с целью ее разрушения.
215

При бурении нефтяных и газовых скважин основным породоразрушающим инструментом, являются долота, которые классифицируются на три типа:
1)долота режуще-скалывающего действия, разрушающие породу лопастями (лопастные долота);
2)долота дробяще-скалывающего действия, разрушающие породу зубьями или штырями, расположенными на шарошках (шарошечные долота);
3)долота режуще-истирающего действия, разрушающие породу алмазными зернами или твердосплавными штырями, которые расположены в торцевой части долота (алмазные и твердосплавные долота).
Лопастные долота в зависимости от конструкции и оснащенности твердым сплавом предназначаются для бурения мягких и средней твердости пород. Такие долота выпускают трех типов:
-двухлопастные 2Л (рис. 3.40, а) диаметрами от 76 до 165 мм (шифр: 2Л-76: долото двухлопастное диаметром 76 мм)
-трехлопастные 3Л (рис. 3.40, б); диаметрами от 120 до 470 мм (шифр долота диаметром 120 мм: 3Л-120);
-многолопастные (шестилопастное долото истирающе-режущего типа 6ИР диаметрами от 76 до 270 мм).
Нередко для расширения ствола скважины используются пикообразные долота (пикобуры, рис. 3.40, в), изготавливаемые диаметром от 98 до 445 мм. Шифр долота, например, диаметром 98 мм: ПР-98.
Под действием нагрузки на забой лопасти таких долот врезаются в породу, а под влиянием вращающего момента – скалывают ее. В корпусе долота имеются отверстия, через которые жидкость из бурильной колонны направляется к забою скважины.
Лопастные долота не применяются при бурении забой-
ными буровыми машинами (турбобурами, винтовыми двигателями и электробурами), так как при бурении ими требуется большой крутящий момент.
Шарошечные долота выпускаются с одной, двумя, тремя, четырьмя и даже с шестью шарошками. По целевому назначению выделяются шаро-
216
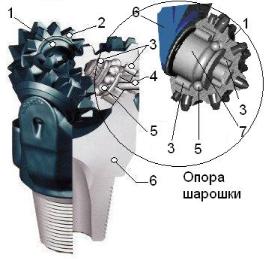
шечные долота для бурения сплошным забоем (рис. 3.42) и долота для бурения кольцевым забоем с отбором керна (рис. 3.43).
При вращении долота, шарошки, перекатываясь по забою, совершают сложное движение, вращаясь вокруг собственной оси и оси долота. При этом зубцы или штыревые вставки шарошек наносят удары по породе, дробят и скалывают ее.
Наибольшее распространение для бурения сплошным забоем получили трехшарошечные долота.
|
Долото состоит |
из |
трех |
|
|
одинаковых по размеру ша- |
|||
|
рошек 1 и трех идентичных |
|||
|
лап 6 (рис. 3.41). |
|
|
|
|
Три |
лапы |
сварены |
|
|
вместе и образуют цилинд- |
|||
|
рическую секцию, |
которая |
||
|
имеет резьбу для присоеди- |
|||
|
нения к бурильной колонне. |
|||
|
В лапах выполнены отвер- |
|||
|
стия (для циркуляции рас- |
|||
|
твора). Каждая лапа имеет |
|||
|
цапфу 7 (опору шарошки), с |
|||
|
проточками под шарики 5 и |
|||
|
ролики 3, на которые уста- |
|||
Рис. 3.41. Устройство трехшарошечного |
навливается |
шарошка |
1. |
|
Фиксация цапфы в корпусе |
||||
долота |
лапы обеспечивается |
зам- |
ком (штифтом) 4. Шарошки
долота снабжены зубцами 2.
Существуют несколько форм зубцов, каждая из которых предназначена для соответствующей твердости разбуриваемой горной породы.
Долота с фрезерованными на теле шарошки зубцами (рис. 3.42, а), используют при бурении мягких пород
Штыревые долота с зубьями из карбид-вольфрамовых вставок применяются для бурения средних и твердых пород.
Причем, долота с остроконечными вставными зубцами (рис. 3.42, б) используют для бурения средней твердости пород, а долота с круглыми и полусферическими вставками (рис. 3.42, в) применяют для бурения средних и твердых пород.
Кроме трехшарошечных в практике бурения часто применяют одношарошечные долота (рис. 3.45) и двухшарошечные долота (рис. 3.44).
Одношарошечные долота применяются для бурения твердых пород, залегающих на большой глубине. Они состоят из одной лапы, на цапфе которой свободно вращается на шариковых опорах сферическая шарошка, в
217
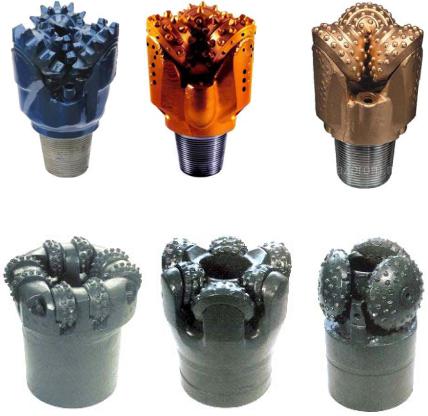
тело которой запрессованы твердосплавные цилиндрические зубья (штыри) с полусферической или призматической рабочей поверхностью.
а) |
б) |
|
в) |
Рис. 3.42. Трехшарошечные долота для бурения сплошным забоем
а) б) в)
Рис. 3.43. Трехшарошечные долота для бурения кольцевым забоем
Двухшарошечные долота предназначены для бурения мягких и вязких пород с пропластками пород средней твердости. Такие долота, как и трехшарошечные, представляют собой неразборную конструкцию, состоящую из двух сваренных между собой лап, на цапфах которых смонтированы свободно вращающиеся на опорах шарошки с зубьями для разрушения пород. Долота являются гидромониторными с двумя боковыми каналами, в которых устанавливаются сменные насадки, направляющие струю бурового раствора на периферийную часть забоя скважины.
218
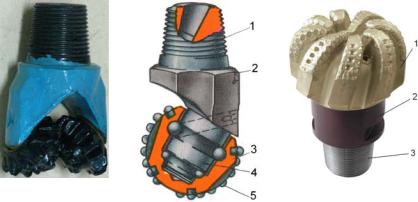
Алмазные долота (рис. 3.46) предназначены для бурения скважин при прохождении твердых и абразивных пород, в которых эффективность применения шарошечных долот резко снижается.
Рис. 3.44. Внешний |
Рис. 3.45. Одношарошечное |
Рис. 3.46. Внешний вид |
вид двухшарошечно- |
долото: 1 – присоедини- |
алмазного долота |
го долота |
тельная резьба; 2 – лапа; 3 – |
|
|
шарошка; 4 – опора шарош- |
|
|
ки; 5 – зубья |
|
Алмазные долота, подобно лопастным, не имеют самостоятельно движущихся частей. Они состоят из фасонной (секторной) алмазонесущей головки (матрицы) 1, выполненной из порошкообразного твердосплавного материала, и стального корпуса 2 с присоединительной замковой резьбой 3.
Режущие элементы алмазного долота состоят из большого количества небольших, как правило, синтетических алмазов или выполняются в виде вставок из сверхтвердых материалов, размещенных по определенной схеме и закрепленных на рабочей поверхности матрицы
Алмазы устанавливаются и закрепляются в процессе изготовления матрицы методом порошковой металлургии (совместное формирование, прессование и спекание в графитовой форме композиции матрицы и алмазов). Для изготовления долот для бурения мягких пород используют крупные алмазы, а для долот, предназначенных для разрушения твердых пород – мелкие.
Профиль рабочей поверхности секторов матрицы может быть выпук- ло-вогнутым, ступенчато-конусным и др.
Алмазные долота изготавливаются диаметрами 91…391 мм и используют при бурении, как с отбором, так и без отбора керна.
219
3.2.3. Промывка скважины и очистка отработанного в скважине бурового раствора
Промывка скважины является одной из самых ответственных операций, выполняемых при бурении.
Первоначально назначение промывки ограничивалось очисткой забоя от частичек выбуренной породы и их выносом из скважины, а также охлаждением долота. Однако по мере развития бурового дела функции бурового раствора расширились. Теперь сюда входят: вынос выбуренной породы из скважины; передача энергии турбобуру или винтовому двигателю; предупреждение поступления в скважину нефти, газа и воды; удержание частичек разбуренной породы во взвешенном состоянии при прекращении циркуляции жидкости в скважине; охлаждение и смазка трущихся деталей долота; уменьшение трения бурильной колонны о стенки скважины; уменьшение проницаемости стенок скважины, благодаря образованию на них плотной глинистой корки.
Применяемая при бурении нефтяных и газовых скважин прямая схема промывки заключается в принудительной подаче по колонне бурильных труб к забою скважины жидкого или газожидкостного очистного агента. От забоя очистной агент по кольцевому каналу между бурильными трубами и стенками скважины (или обсадной колонны) движется к устью скважины. При этом продукты разрушения забоя (шлам) выносятся на поверхность.
Сбор и очистка отработанного бурового раствора, приготовление новых его порций и закачка очищенного раствора в скважину обеспечивается
циркуляционной системой буровой установки (рис. 3.47).
Очистка промывочной жидкости осуществляется как за счет естественного выпадения частиц породы в желобах 2 и емкостях 6, так и принудительно в механических устройствах (виброситах 3, гидроциклонах 4). Использованный буровой раствор из устья скважины 1 через систему желобов 2 поступает на расположенную наклонно и вибрирующую сетку вибросита 3. При этом жидкая часть раствора свободно проходит через ячейки сетки, а частицы шлама удерживаются на сетке и под воздействием вибрации скатываются под уклон. Для дальнейшей очистки буровой раствор с помощью шламового насоса 5 прокачивается через гидроциклоны 4. За счет тангенциального ввода происходит вращение исходной пульпы в цилиндре гидроциклона. При этом более тяжелые и крупные твердые частицы, поступающие с исходной пульпой, отбрасываются центробежной силой на внутреннюю поверхность цилиндра и увлекаются вращающимся нисходящим потоком вниз. Под действием радиальной составляющей потока (от стенок к центру) легкие и мелкие зерна уносятся во внутреннюю зону. Часть опускающегося вниз пристенного вихревого потока в нижней зоне конуса поворачивается вверх, формируя слив. В гидроциклонах удается отделить частицы породы размером до 10…20 мкм.
220
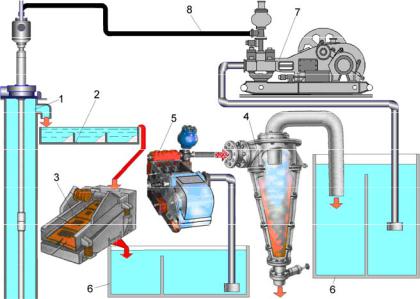
Окончательная очистка раствора от мельчайших взвешенных частиц породы производится в емкости 6 (правой на рис. 3.47) с помощью химических реагентов, под действием которых очень мелкие частицы как бы слипаются, после чего выпадают в осадок.
Очищенный буровой раствор буровыми насосами 7 по нагнетательному трубопроводу 8 вновь подается в скважину. По мере необходимости в систему вводится дополнительное количество заранее приготовленного нового раствора, хранящегося в на буровой в цистернах.
Рис. 3.47. Принципиальная схема циркуляционной системы
В настоящее время при бурении скважин в устойчивых породах широко используется техническая вода; в слабоустойчивых породах и других сложных геологических условиях применяют глинистые и специальные растворы; в поглощающих горизонтах – аэрированные жидкости; в сухих разрезах, при отсутствии водопроявлений, - сжатый воздух, природный газ и другие газообразные агенты.
Вода как пресная, так и минерализованная, в том числе морская, может с успехом применяться при проходке устойчивых и не размывающихся пород в условиях, когда пластовое давление нефтегазоносных горизонтов не превышает гидростатическое при данной глубине скважины.
Применение воды наиболее целесообразно при бурении гидромониторными и алмазными долотами, использовании забойных двигателей, при
221
вскрытии продуктивных водоносных горизонтов, если в последнем случае нельзя применить газообразные агенты.
Глинистые растворы, в зависимости от состава и способа приготовления, помимо очистки забоя, выноса шлама и охлаждения инструмента обеспечивают: закрепление стенок скважины в результате образования тонкой глинистой корки, поддерживаемой избыточным гидростатическим давлением столба раствора в скважине; предупреждение оседания шлама на забой при прекращении циркуляции вследствие быстрого превращения раствора из золя в гель (структурообразование); противодавление на высоконапорные горизонты, устраняющее выбросы нефти, газа и воды, достигаемое повышением плотности раствора за счет введения в него тонко измельченных минералов-утяжелителей; смазку шарошечных долот, бурильных и обсадных труб, уменьшение их износа; устранение потерь циркуляции в пористых и трещиноватых породах и др.
Для приготовления глинистых растворов используют распространенные в природе осадочные горные породы – глины, представляющие собой смесь минералов, основными среди которых являются монтмориллонит, иллит (гидрослюда), каолинит и др. Различают глинистые растворы на пресной воде и минерализованные. Их подразделяют также на малоглинистые, с нормальной концентрацией глины и утяжеленные.
Растворы на нефтяной основе применяют для повышения отдачи нефтеносных пластов при вскрытии и гидравлическом разрыве, а также в неустойчивых глинисто-соленосных отложениях. Для приготовления этих растворов используют сырую нефть и дизельное топливо. Для увеличения плотности и придания структурных свойств в качестве твердой фазы используют измельченный битум, добавляют негашеную известь.
Солевые растворы приготавливают на пресной технической воде растворением в ней NaCl, реже CaCl2, иногда других солей и применяют при бурении в отложениях солей, сильно засоленных глин и в многолетних мерзлотах.
Газообразные очистные агенты начали использовать с начала 50-х
годов ХХ столетия для вскрытия продуктивных горизонтов, при бурении по необводненным или мерзлым породам, а также в безводных районах и в условиях потерь циркуляции. Используются сжатый воздух, природный газ, выхлопные газы двигателей внутреннего сгорания, азот.
Аэрированная жидкость (смесь воды или раствора с воздухом или газом), позволяющая в широких пределах регулировать плотность и гидростатическое давление, получила наиболее эффективное применение как надежное средство предупреждения осложнений из-за потерь циркуляции в самых неблагоприятных условиях. Аэрация промывочной жидкости может выполняться механическими способами: с помощью смесителя при одновременной работе насосов и компрессоров; без компрессоров с помощью струйного насоса эжекционного типа, засасывающего атмосферный воздух.
222

Существует также химический способ аэрации – за счет обработки исходной жидкости на приеме насосов пенообразующими поверхностно активными веществами.
Пена находит применение как разновидность промывочных агентов. Важным достоинством пены являются малый расход воды, высокая транспортирующая и удерживающая способность, отсутствие потерь циркуляции в поглощающих породах за счет прочности структуры, смазывающее действие, и в тоже время высокая охлаждающая способность в силу эффекта испарительного охлаждения.
3.2.4. Производственный цикл строительства скважины
Рис. 3.48. Производственный цикл сооружения скважины
Производственный цикл строи-
тельства скважины – это совокупность рабочих процессов, производимых в определенном порядке в соответствии с правилами сооружения скважин. Основные элементы цикла приведены на рис. 3.48.
Подготовительные работы
выполняются до начала вышкомонтажных работ. Специальная подготовительная бригада прокладывает к месту сооружения буровой трубопроводы, линии электропередачи и связи, доставляет материалы, изготавливает блочные основания и планирует площадку под буровую. В исключительных случаях фундаменты под оборудование сооружает вышкомонтажная
бригада.
После возведения фундаментов и доставки элементов буровой установки на место заложения скважины приступают к монтажу металлической вышки. После окончания и частично во время монтажа вышки монтируют оборудование. Этими работами занимается буровая бригада, в обязанности которой входят: оснастка талевой системы; установка ротора; оснащение буровой элементами малой механизации; обкатка дизелей и проверка бурового оборудования; приготовление промывочной жидкости и бурение шурфа под ведущую трубу. Около насосов размещаются емкости для промывочной жидкости. От устья скважины к приемной емкости насоса монтируют циркуляционную систему, состоящую из желобов, имеющих небольшой
223
уклон и несколько поворотов, а также гидравлические и механические очистители промывочной жидкости (вибросита, гидроциклоны и др.).
Безотносительно к способу разрушения горных пород собственно процесс бурения скважины включает ряд операций: спуск бурильных труб (колонн) с породоразрушающим инструментов в скважину; разрушение породы забоя; вынос разрушенной породы из скважины; подъем бурильных труб из скважины для замены сработавшегося разрушающего инструмента и повторения операций.
При достижении определенной глубины производят крепление стенок скважины обсадными трубами с последующим цементированием пространства между стенкой скважины и спущенными трубами (разобщение пластов).
К операциям технологического характера, которые не участвуют в непосредственной проводке скважины, но также являются обязательными, относятся: предупреждение и ликвидация осложнений и аварий; подготови- тельно-заключительные работы, связанные с проведением геофизических исследований в скважине; профилактический ремонт бурового оборудования и механизмов.
Испытания и исследования скважины включают работы, связанные: с измерениями пространственного положения ствола скважины; испытаниями на приток воды, нефти, газа; проведением исследований для изучения геологического разреза скважины электротехническими, магнитными, акустическими, радиоактивными и другими методами.
Втом случае, если все рабочие операции выполняются одной и той же бригадой, то они являются последовательными. При этом, как правило, подготовительные и монтажно-демонтажные работы выполняются специализированными монтажными бригадами, имеющимися в структуре управлений буровыми работами. Что касается испытаний и исследований скважин, то этими работами занимаются отдельные геофизические отряды.
Процесс бурения. Бурильная колонна (через ведущую трубу) получает вращение от ротора. Во время бурения происходит непрерывный спуск (подача) бурильного инструмента таким образом, чтобы часть веса его нижней части (в виде требуемой осевой нагрузки) передавалась на долото.
Впроцессе бурения скважина постепенно углубляется. После углубления скважины на длину ведущей трубы необходимо нарастить колонну бурильных труб. Наращивание выполняется следующим образом. Сначала останавливается промывка. Далее бурильная колонна поднимается из скважины настолько, чтобы ведущая труба полностью вышла из ротора. При помощи пневматического клинового захвата инструмент подвешивается на роторе. Затем ведущая труба отвинчивается от колонны бурильных труб и вместе с вертлюгом спускается в шурф, который представляет собой дополнительную слегка наклонную скважину глубиной 15…16 м, располагаемую
вуглу буровой. После этого, на предварительно отсоединенный от вертлюга
224
крюк с помощью элеватора подвешивается заранее подготовленная труба. После свинчивания этой трубы с колонной бурильных труб, раскрепляется клиновой захват, колонна опускается в скважину и на уровне замка вновь подвешивается на роторе. Подъемный крюк снова соединяется с вертлюгом
иподнимается вместе с ведущей трубой из шурфа. Ведущая труба соединяется с колонной бурильных труб. Раскрепляется клиновой захват, колонна снимается с ротора, и после включения бурового насоса, долото осторожно доводится до забоя. После этого бурение продолжается.
При бурении долото изнашивается и возникает необходимость в его замене. Для этого бурильный инструмент, как и при наращивании, поднимается на высоту, равную длине ведущей трубы, подвешивается на роторе, отсоединяется ведущая труба от колонны и спускается с вертлюгом в шурф. Затем бурильная колонна поднимается на высоту, равную длине бурильной свечи и с помощью клиновых захватов подвешивается на роторе. Свеча отсоединяется от колонны, и нижний конец ее устанавливается на специальную площадку – подсвечник, а верхний заводится в специальный кронштейн. В такой последовательности поднимаются из скважины все свечи. После этого заменяется долото и начинается спуск бурильного инструмента. Этот процесс осуществляется в порядке, обратном подъему бурильной колонны из скважины.
3.3.Краткая характеристика промыслового освоения нефтяных
игазовых месторождений.
Из нефтяных скважин в общем случае извлекается сложная смесь, состоящая из нефти, попутного нефтяного газа, воды и механических примесей (песка, окалины и проч.). В таком виде транспортировать продукцию нефтяных скважин по магистральным трубопроводам нельзя. Во-первых, вода – это балласт, перекачка которого приводит к непроизводительным затратам. Во вторых - при совместном течении нефти, газа и воды имеют место значительно большие потери давления на преодоление сил трения, чем при перекачке одной нефти. В-третьих, минерализованная пластовая вода вызывает ускоренную коррозию трубопроводов и резервуаров, а частицы механических примесей – абразивный износ оборудования.
Поэтому, прежде чем попасть к потребителю (нефте- и газоперерабатывающим заводам), извлекаемая из скважины нефть проходит сложную многокомпонентную обработку на нефтяных промыслах (рис. 3.49), представляющих собой технологический комплекс для добычи и сбора нефти на месторождении, а также обработки продукции скважин (нефти, нефтяного газа, пластовой воды) с целью подготовки нефти к дальнейшему транспортированию.
225

Структурная схема сбора и подготовки продукции скважин на неф-
тяном промысле приведена на рис. 3.50.
Продукция скважин по трубопроводу поступает на групповую замерную установку (ГЗУ), где по каждой скважине периодически замеряют количество поступающей из нее нефти, определяют содержание в последней воды и нефтяного газа (по замерам подсчитывают суточный дебит каждой скважины по нефти и по газу). Затем нефть направляется на центральный пункт сбора нефти, газа и воды (ЦПС).
При значительной удаленности ГЗУ от ЦПС нефть поступает вначале на дожимную насосную станцию (ДНС), предназначенную для создания
Рис. 3.49. Внешний вид нефтяного промысла дополнительного на-
пора в системе внутрипромыслового транспорта. Кроме того, здесь осуществляется первая ступень сепарации
нефти, где выделяется до 90% растворенного нефтяного газа. После ДНС частично разгазированная нефть и газ поступают на ЦПС. В случае близкого расположения ГЗУ и ЦПС первая ступень сепарации нефти осуществляется непосредственно на ЦПС, где производится сбор и промысловая обработка продукции нефтяных скважин.
В состав ЦПС входят установки подготовки нефти, очистки пластовых вод, осушки и очистки газа, резервуарные парки, насосные станции, газокомпрессорные станции, система технологических трубопроводов, фа-
кельная система, объекты энерго - и водоснабжения и др.
Продукция скважин по внутрипромысловым нефтегазосборным трубопроводам поступает к установке подготовки нефти, где обеспечивается сепарация, обезвоживание и обессоливание нефти, после чего нефть перекачивается в товарные резервуары или на головные сооружения магистрального нефтепровода. Вода, выделенная из нефти при ее обезвоживании и
226

обессоливании, направляется на установки по очистке воды, где остаточное содержание в ней нефти и механических примесей снижается до 50 мг/л. Затем вода подается к кустовым насосным станциям, с помощью которых закачивается в продуктивный горизонт для поддержания пластового давления. Осушенный нефтяной газ поступает на прием компрессорной станции, откуда направляется на газоперерабатывающий завод.
Рис. 3.50. Схема сбора и подготовки продукции скважин на нефтяном промысле
Природный газ, поступающий из скважины, также как и нефть не является чистой продукций и содержит примеси твердых частиц (песок, окалина), конденсат тяжелых углеводородов, пары воды, а в ряде случаев сероводород и углекислый газ. Присутствие в газе твердых частиц приводит к абразивному износу труб, устьевой арматуры и компрессорного оборудования, засорению контрольно-измерительных приборов. Конденсат тяжелых углеводородов оседает в пониженных точках газопроводов, уменьшая их проходное сечение. Наличие водяных паров в газе приводит к коррозии трубопроводов и оборудования, а также к образованию в трубопроводах гидратов – снегоподобного вещества, способного полностью перекрыть сечение труб.
Весьма вредной примесью является сероводород. При его содержании большем, чем 0,01 мг в 1 л воздуха рабочей зоны, он ядовит. Кроме того, в присутствии влаги сероводород способен образовывать растворы сернистой и серной кислот, резко увеличивающих скорость коррозии труб, арматуры и оборудования.
Углекислый газ вреден тем, что снижает теплоту сгорания газа, а также приводит к коррозии оборудования.
227
Для очистки газа от механических примесей, тяжелых углеводородов, паров воды, сероводорода и углекислого газа предназначен газовый промысел, представляющий собой технологический комплекс, для добычи и сбора газа с площади месторождения, а также обработки газа и конденсата (смесь жидких углеводородов, выделяющаяся из природного газа) с целью подготовки их к дальнейшему транспортированию.
Добыча газа на промысле обеспечивается фондом эксплуатационных скважин, число которых определяются запасами газа, строением и количеством продуктивных горизонтов, размерами и конфигурацией залежи. На площади месторождения скважины располагаются отдельными объектами или кустами из 2-5 скважин. Контроль разработки месторождения осуществляется на газовом промысле с помощью наблюдательных скважин.
Промысловая подготовка газа и конденсата осуществляется с помощью технологического оборудования сборного пункта, основу которого составляют адсорбционные колонны для извлечения кислых компонентов (Н2S и СО2), и других примесей поглощением их адсорбентом (активный уголь, силикагель и др.), а также сепараторы для очистки газа от механических примесей.
3.4. Особенности освоения морских углеводородных месторожде-
ний.
Основные узлы бурового оборудования и технология проходки морских нефтяных и газовых скважин в основном не отличаются от бурения скважин на суше, однако имеют некоторые особенности, обусловленные наличием толщи воды между устьем и буровой установкой. Прежде всего, для монтажа и размещения буровой установки нужны плавучие или стационарные сооружения с рабочими площадями, размеры которых объективно предполагают необходимость компактного размещения на них оборудования буровой установки.
При работах с плавучих сооружений для компенсации вертикальных перемещений бурильной колонны между талевым блоком и крюком монтируется специальное устройство — компенсатор вертикальных перемещений. Противовыбросовое подводное оборудование устанавливается на морское дно и связано с устьем скважины с помощью водоотделяющей колонны с компенсаторами вертикальных и горизонтальных перемещений.
Условия эксплуатации технологического оборудования буровой установки требуют жесткого соблюдения общесудовых правил и экологических требований при работах в морских открытых акваториях. Последнее требование обусловливает применение закрытой и замкнутой циркуляционной системы промывки скважины, очистки и приготовления бурового рас-
228
твора. Имеется также так же целый ряд дополнительных технических и технологических ограничений, продиктованных требованиями безопасного ведения работ на море. В конечном итоге, специфика и сложные в техническом отношении операции бурения в морских условиях определяют повышенные затраты и стоимость освоения морских месторождений по сравнению с аналогичными работами на суше. При этом, стоимость разработки месторождений с увеличением глубин моря резко возрастает. Так, на глубине 30 м стоимость разработки в 3 раза выше, чем на суше, на глубине 60 м
—в 6 раз и на глубине 300 м — в 12 раз.
Вмировой практике, производство морских буровых работ обеспечивается с помощью плавучих буровых средств (ПБС), которые в зависимости от способа их установки над скважиной в процессе бурения, разделяются на две основные группы. К первой группе относятся ПБС опирающиеся при бурении на морское дно (самоподъемные плавучие буровые установки). Ко второй группе – безопорные ПБС, производящие бурение в плавучем состоянии - полупогружные буровые установки и буровые суда.
Самоподъемные плавучие буровые установки (СПБУ) применяют преимущественно в разведочном бурении на морских нефтяных и газовых месторождениях в акваториях с глубинами вод 30—120 м. Эти установки состоят из понтона, служащего корпусом установки, и трех и более выдвижных опорных колонн, установленных по углам корпуса (рис. 3.51). Большой запас плавучести платформ позволяет размещать на них технологическое, энергетическое и вспомогательное оборудование, запасы материалов, топливо, питьевую и технологическую воду, инструмент, жилые и служебные помещения, склады, вертолетную площадку и др. В точке заложения скважины, опоры опускаются на дно и задавливаются в грунт. При этом корпус с буровым оборудованием поднимается по этим опорам на такую высоту над уровнем моря, чтобы во время шторма волна не доставала платформы (обычно 9…15 м). Подъем платформы над поверхностью моря и ее опускание осуществляют, в основном, механическими устройствами подъема, состоящими из зубчатой рейки, встроенной в конструкцию опор и установленного на корпусе шестеренчатого механизма, шестерня которого находится постоянно в зацеплении с рейкой. Привод механизма подъема осуществляется от электродвигателя с редуктором, а также при помощи домкратов или тросовых оснасток лебедок, установленных непосредственно на платформе. Поэтому основания на выдвижных опорах часто называют самоподнимающимися.
По окончании бурения платформу опускают на воду, опоры извлекают из грунта. В заданный пункт СПБУ с инструментом и материалами буксируется на плаву, при этом опоры подняты и возвышаются над понтоном.
Полупогружные плавучие буровые установки (ППБУ) применяют в разведочном бурении на морских нефтяных и газовых структурах и место-
229
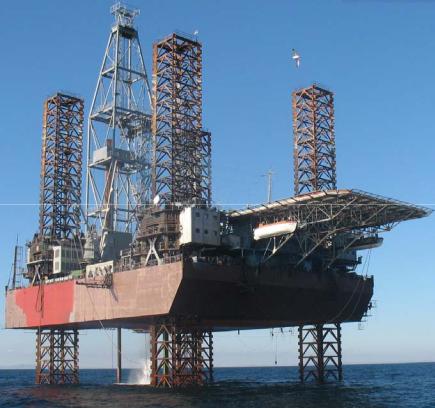
рождениях при глубинах моря до 600 м, где неприменимы СПБУ. Они не опираются на морское дно, а находятся на плаву над местом бурения на огромных понтонах.
При глубине моря 200—300 м, горизонтальное смешение ППБУ относительно точки бурения в течение всего периода бурения и испытания скважины ограничивается удерживающими якорями массой 15 т и более (например, ППБУ «Шельф» для бурения разведочных нефтяных и газовых скважин глубиной до 6000 м, рис. 3.52).
Рис. 3.51. Самоподъемная буровая платформа СПБУ «Сиваш» (Украина)
В более глубоких водах применяется динамическое позиционирование ППБУ, за счет подруливающих и ходовых винтов. Последние постоянно находятся в работе в автоматическом режиме управления.
ППБУ состоят из верхнего корпуса, стабилизирующих колонн и нижних понтонов. Колонны в верхней части присоединены к корпусу, а в
230
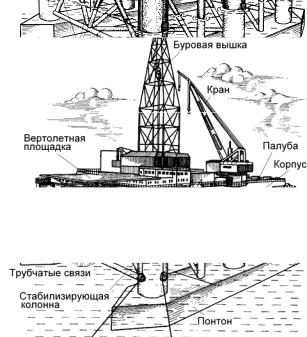
нижней — к понтонам. Понтоны и корпус соединены между собой и с колоннами прочными трубчатыми связями. Стабилизирующие колонны ППБУ разделены на водонепроницаемые отсеки, в которых размещены склады материалов, насосные отделения и другое оборудование. В нижних понтонах и
стабилизирующих колоннах размещены цистерны балластной и технической воды, топлива, масла и др. Рабочая
Рис. 3.52. Общий вид ППБУ типа «Шельф» (верхняя) палуба представляет собой конструкцию трех-, четырех-, пяти- и более угольной формы, на которой
размещены двух- и трехъярусные водонепроницаемые надстройки для размещения экипажа, а также энергетические и технологические блоки, складские помещения и другое оборудование. В рабочем положении на точке бурения цистерны нижних понтонов заполняются необходимым количеством морской водой и погружаются на расчетную глубину под воду (как правило, до 30 м от поверхности моря) при этом действие волн на платформу уменьшается.
Втранспортном положении понтоны полностью опорожняются
инаходятся на поверхности моря, верхний корпус возвышается над водой. Платформы транспортируют двумя-тремя мощными буксирами, но имеются также самоходные установки, оборудованные гребными винтами с приводом от электромоторов.
Буровые суда (БС) относятся ко второму типу безопорных оснований. В качестве бурового используют морское судно, специально построенное или реконструированное для размещений оборудования и инструмента
ипроведения буровых работ в акваториях морей и океанов. Отличительной особенностью БС является наличие в центральной части судна шахты, как правило, прямоугольного или квадратного сечения, с установленной над
231

ней буровой вышкой. На некоторых судах буровые вышки после окончания бурения скважины опускаются с помощью специальных устройств и укладываются в горизонтальном положении, снижая этим парусность и понижая центр тяжести судна на переходах и перегонах. На рис. 3.53 показан внешний вид одного из крупнейших в мире буровых судов «CHIKYU».
Рис. 3.53. Внешний вид бурового судна CHIKYU
Благодаря высокой маневренности и скорости перемещения, большой автономности буровые суда применяют при строительстве глубоких морских нефтяных и газовых скважин, а также для бурения поисковых и разведочных скважин в отдаленных районах при глубинах моря до 1500 м и более. Большие запасы (до 100 дней работы) обеспечивают бурение нескольких скважин, а большая скорость передвижения (до 24 км/ч) — быст-
232
рую их перебазировку с законченной бурением скважины на новую точку. Водоизмещение таких судов достигает 30 тыс.т.
Над точкой бурения судно (в рабочем состоянии) находится на плаву и при глубине моря до 200 м удерживается с помощью якорных систем. Удержание БС над точкой бурения при глубине моря свыше 200 м обеспечивается с помощью динамической системы стабилизации и осуществляется автоматически с помощью информационно-командного комплекса, управляющего системой динамического позиционирования, в виде акустических приборов, работа которых основана на регистрации импульсов, посылаемых от донных маяков, располагаемых вблизи устья скважины, и их приемке гидрофонами под днищем судна. Благодаря такой системе ориентации и удержания БС над устьем, выполняется бурение скважины на глубинах вод более 6000 м.
На палубах БС размещается циркуляционная система с полным комплектом оборудования для приготовления, обработки и очистки бурового раствора (цистерны, вибросита, дегазаторы, пескоотделители и др.). Для посадки и взлета вертолетов имеется взлетно-посадочная площадка, огражденная брусом (комингсом) и устройствами для швартовки и закрепления вертолета. Погрузочно-разгрузочные операции с трубами производят краном на главной палубе.
Добыча нефти и газа из морских месторождений углеводородов, а также подготовка продукции к транспортировке осуществляется на морских нефтегазовых промыслах. Отличие морских нефтегазовых промыслов от подобных комплексов на суше заключается в необходимости размещения основного и вспомогательного оборудования на специальных гидротехнических сооружениях (например, на стационарных платформах или специализированных плавучих установках).
Морская стационарная платформа (МСП)— это буровое основание,
опирающееся на дно акватории и возвышающееся над уровнем моря. Так как по окончании эксплуатации скважины МСП остается на месте сооружения, то схемой бурения морской скважины в отличие от схемы строительства наземной скважины предусмотрено наличие водоотделяющей колонны, изолирующей скважину от толщи воды.
Устьевое оборудование (превенторы, устройство для отвода промывочной жидкости из скважины в системы очистки и др.), а также промысловое оборудование (технологические комплексы для сбора и подготовки продукции скважин) монтируется на МСП.
Стационарные платформы, используемые при глубине моря до 300 м, представляют собой конструкцию, состоящую из подводной и надводной частей (3.54). Подводная часть опирается на дно и выполняется в виде трубчатой металлической решетки, состоящей из 4-12 колонн диаметром до 2,5
233

м (более 45% известных конструкций МСП) или железобетонных свай (гравитационные платформы).
Глубоководная стационарная платформа, как правило, является самостоятельным нефтепромыслом.
Рис. 3.54. Эксплуатационная стационарная буровая платформа:
1 – буровая вышка; 2 – грузовой кран; 3 – стеллажи для труб; 4 – жилой блок; 5 – бункера для порошковых материалов; 6 – компрессорные станции; 7 – трубо-
проводы продукции скважин; 8 – насосно-турбинный блок; 9 – комплекс оборудования для подготовки нефти и газа; 10 – блок сжигания газа; 11 – газовыхлопные трубы дизелей; 12 – вертолетная площадка.
234
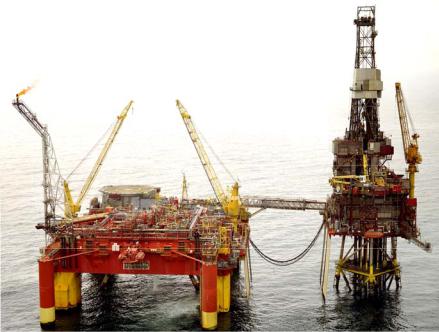
Надводная часть платформы состоит из площадки, возвышающейся над уровнем моря, на которой размещают устья скважин и промысловое оборудование для сбора и подготовки продукции, факел для сжигания попутного газа, а также энергетическое оборудование, жилые помещения, вертолетная площадка, буровая вышка для капитального и текущего ремонтов скважины, причальные сооружения, крановое оборудование и др.
В большинстве случаев блок подготовки нефти и факел для сжигания попутного газа выполняются в виде отдельных, располагающихся в непосредственной близости модулей (рис. 3.55).
Рис. 3.55. Эксплуатационная стационарная платформа STATOIL
Наряду со стационарными металлическими платформами, применяются массивные железобетонные платформы гравитационного типа, занимающих около 25% от известных МСП (рис. 3.56). Они снабжены мощным бетонным основанием, опирающимся на морское дно. В этом основании размещаются не только направляющие колонны для бурения, но также ячейки-резервуары для хранения добытой нефти и дизельного топлива, используемого в качестве энергоносителя, многочисленные трубопроводы. Элементы основания доставляют к месту монтажа в виде крупных блоков.
235
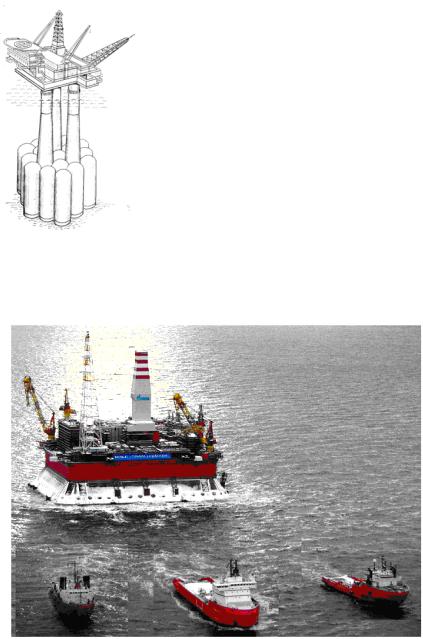
|
Морское дно в месте установки гравитаци- |
|
онных платформ должно быть тщательно подго- |
|
товлено. Даже небольшой уклон дна грозит рас- |
|
колу основания. Поэтому перед постановкой бу- |
|
ровой на «точку» все выступающие камни уби- |
|
рают, а трещины и впадины на дне заделывают |
|
бетоном. |
|
Гравитационная морская стационарная |
|
платформа (ГМСП) — буровое основание, изго- |
|
товленное из железобетона и стали. Она строится |
|
в глубоководных заливах и затем с помощью бук- |
|
сиров доставляется на точку бурения эксплуата- |
|
ционных и разведочных скважин (рис. 3.57). Здесь |
|
ГМСП позиционируется и притапливается до по- |
Рис. 3.56. Гравитационная |
садки на подготовленное основание. |
ГМСП предназначена не только для буре- |
|
МСП |
ния скважин, но и для добычи и хранения нефти |
|
до отправки ее танкерами к месту переработки. Платформа обладает большим весом, поэтому для удержания ее на точке бурения не требуется дополнительных устройств.
Рис. 3.57. Транспортирование ППБУ морскими буксирами
236
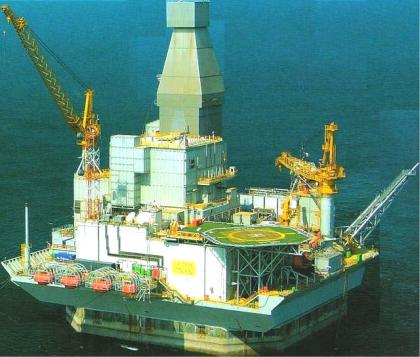
После разработки месторождения производится консервация всех скважин, отсоединение установки от устьев скважин, до получения плавучести и транспортировка на новую точку в пределах данной площади или в другой регион бурения и добычи нефти и газа. В этом заключается преимущество ГМСП перед МСП, которая, после разработки месторождения, остается в море навсегда.
При глубинах моря свыше 60 м весь комплекс морского нефтегазового промысла размещается на переоборудованных или специально построенных полупогружных платформах.
Одной из крупнейших в мире платформ является ППБУ «Орлан» (рис.
3.58)
Рис. 3.58. Эксплуатационная полупогружная платформа «Орлан» (Россия)
В процессе освоения морских месторождений существенное значение имеет этап подготовки продуктивных площадок к морскому буровому производству. Учитывая большую общую массу поднимаемого корпуса, надежность устойчивости СПБУ зависит от прочности грунта. В связи с чем, размещение платформы на точке бурения производится после установления пригодности грунта морского дна в качестве фундамента для опорных ног и
237
якорных систем. Учитывая, что газовые месторождения разрабатывают при условии сообщения с береговым потребителем подводным газопроводом, обустройству площадок под строительство СПБУ предшествует этап детальных инженерно-геологических изысканий грунтов. Эти исследования включают бурение большого числа скважин разной глубины (от 4 до 100 м и более) с отбором образцов грунта.
Как правило, пробоотбор до глубины 6…8 м выполняется легкими техническими средствами, эксплуатирующимися с борта буровых и неспециализированных судов. Бурение более глубоких инженерно-геологических скважин шурфов осуществляют с буровых судов, удерживаемых на якорях (до 200 м глубины воды), или судов с динамической стабилизацией при глубине воды более 200 м.
В отечественной практике освоения морских месторождений основной объем бурения инженерно-геологических скважин глубиной до 50 м выполняется установками УМБ -2М и УМБ-130М, разработанными в Донецком национальном техническом университете. Основными элементами установки являются гидроударный буровой снаряд, погружающийся в донные породы за счет динамических нагрузок, формирующихся гидроударным механизмом, являющимся структурной составляющей снаряда, и придонное основание (стабилизирующая опора).
Установки эксплуатируются с борта как буровых, так и не специализированных судов и работают по технологической схеме, предусматривающей возможность поинтервальной проходки скважин с использованием в течение рейса двух способов разрушения пород на забое:
-с отбором керна за счет частотно-ударного погружения бурового снаряда в осадки на заданную глубину (рис. 3.59, б, г);
-без отбора керна за счет размыва пород на ранее пройденном без крепления интервале ствола скважины (рис. 3.59, в).
Принципиальная схема поинтервальной проходки скважины установкой УМБ-2М приведена на рис. 3.59. Установка относится к легким техническим средствам, и позволяет бурить скважины глубиной до 20 м. Заданный режим разрушения пород на интервале скважины обеспечивается дистанционным переключением специальных узлов гидроударного механизма.
Вкачестве рабочего агента для привода гидроударного механизма используется морская вода. Подача морской воды производится буровым насосом, установленным на палубе судна.
Для бурения инженерно-геологических скважин глубиной до 50 м используется установка УМБ-130М (рис. 3.60). В отличие от установки УМБ-2М стабилизация бурового снаряда на дне обеспечивается придонным основанием, связанным системой канатов с плавсредством. Все операции по спуску и подъему опоры производятся грузовой лебедкой при помощи талевой системы, в виде системы шкивов, закрепленных на палубе и основании опоры
238

Талевый направляющий трос за счет компенсирующего груза постоянно находиться в натянутом состоянии, в том числе, при ограниченном дрейфе и вертикальных перемещениях судна, обеспечивая возможность вертикального спуска и подъема бурового снаряда.
В комплектации УМБ-130М стабилизирующая опора предназначена не только для удержания гидроударного бурового снаряда в вертикальном положении на морском дне, но и одновременно является направлением при спуске гидроударного снаряда при последующем рейсе, обеспечивая одноствольную многорейсовую проходку скважины. В процессе проходки скважины стабилизирующая опора постоянно находится на точке бурения.
Рис. 3.59. Технологическая схема бурения |
Рис. 3.60. Технологическая схема |
скважины установкой УМБ-2М: |
бурения скважин установками |
1 – трос; 2 – нагнетательный шланг; 3 - гид- |
УМБ-130М |
роударник; 4 – подвижная каретка; 5 - на- |
|
правляющие стойки; 6 – колонковый набор; |
|
7 – донное основание опоры |
|
239 |
|
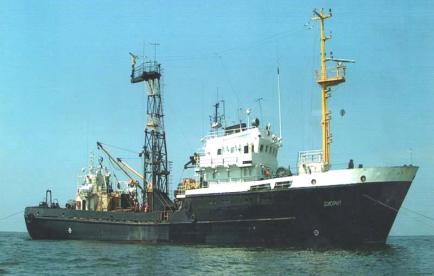
Спуск и подъем бурового снаряда выполняется с помощью буровой лебедки через канат 1, конец которого закреплен на специальном грузовом переходнике, который структурно относится к гидроударнику.
Взарубежной практике для бурения на шельфе сравнительно неглубоких разведочных скважин (до 50 м), а также для бурения инженерногеологических скважин на глубину 100…150 м выполняется с помощью многочисленных специализированных буровых судов. Такие суда, в центральной части корпуса имеют «шахту», над которой установлена буровая вышка. Технологический комплекс каждого судна дополнен также системами для проведения скважинных геотехнологических исследований. Суда оборудованы якорной системой удержания для работы на глубинах моря до 80 м и системой динамического позиционирования для работы на глубинах свыше 80 м.
Вотечественном морском буровом производстве избирательность такого вида плавсредств весьма ограничена. Сегодня Украина располагает единственным специализированным судном НИС «Диорит», относящееся к серии судов буровых судов водоизмещением 1260 т, укомплектованных буровым агрегатом ЗИФ-1200 (рис. 3.61). Эксплуатационно-технические возможности судна обеспечивают вращательное бурение поисковоразведочных и инженерно-геологических скважин глубиной до 150 м при глубине моря до 100 м.
Рис. 3.61. Буровое судно «Диорит» (Украина»)
240
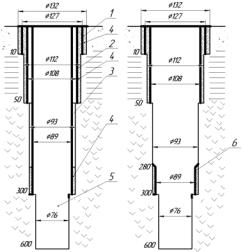
3.5. Бурение геологоразведочных скважин
При разведке полезных ископаемых ведущая роль принадлежит колонковому бурению. При колонковом бурении из скважины извлекается керн, по которому составляется геологическое описание участка или района работ и производится опробование пород для выяснения содержащихся в них полезных компонентов. Скважины колонковым способом можно бурить с земной поверхности и в горных выработках в самых различных направлениях, различным породоразрушающим инструментом и в породах любой твердости и устойчивости.
Конечный диаметр геологоразведочной скважины на твердые полезные ископаемые в основном определяется требованием получения достаточного объема керна для его исследований и возможностью спуска в ствол скважины забойных устройств и геофизического оборудования для скважинных исследований.
Например, для большинства рудных полезных ископаемых достаточным диаметром является 46 мм, на месторождениях редких и благородных металлов с весьма сложной текстурой рекомендуется диаметр 76 мм. Большие диаметры 93…112 мм применяются для разведки химически ценных полезных ископаемых таких, как апатит, сера, соль, графит, слюда, асбест, а также при разведке строительных материалов.
а) б)
Рис. 3.62. Примеры схематического изображения конструкции скважин
Наиболее часто конструкция скважины изображается в виде схемы (рис. 3.62).
Удобной формой представления конструкции является также описание ее в виде шифра. Например, приведенная схема конструкции (рис. 3.62, а) может быть записана в виде:
132/127ц(10)112/108ц(50)93/89ц б(300)76(600).
Здесь / - знак крепления. Перед и после знака «/», цифры, обозначающие, соответственно диаметр бурения в мм (по схеме это цифры 132; 112; 93 и 76) и
диаметр обсадных труб в мм (по схеме это 127; 108 и 89). Дополнительные знаки обозначают: «ц» - цементирование всей ко-
241
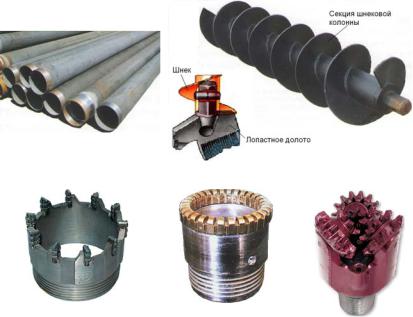
лонны; «цб» - цементирование башмака колонны. Цифра в круглых скобках (10), (50), (300), (600) – глубина бурения или крепления (м).
Если в конструкции скважины предусмотрена потайная колонна (хвостовик), то такая особенность отмечается в шифре дополнительной записью с указанием знака «цб», если цементируется башмак и знак «ц» рядом с цифрой глубины верха потайной колонны, если он цементируется. Так, шифр скважины (рис. 3.62, б) имеет вид
132/127ц(10)112/108ц(50)93/89цб(280ц…300)76(600).
При составлении конструкции скважин необходимо ориентироваться как в сортаменте обсадных труб, так и в размерах породоразрушающего инструмента, используемого как при бурении геологоразведочных скважин.
Для бурения геологоразведочных скважин используются обсадные трубы (рис. 3.63) с толщиной стенки 5 мм и диаметрами: 57, 73, 89, 108, 127 и 146 мм. Для бурения этой категории скважин применяются шарошечные (рис. 3.67), лопастные долота и коронки для бурения с отбором керна - алмазные (рис. 3.66) и твердосплавные (рис. 3.65), имеющие диметр 36, 46, 59, 76, 93, 112, 132 и 151 мм. При проходке неглубоких скважин в мягких и рыхлых породах широко используются шнековые буровые снаряды, состоящие из лопастного долота и шнековой колонны диаметром 65 - 300 мм
(рис. 3.64).
Рис. 3.63. Обсадные трубы |
Рис. 3.64. Инструмент для шнекового бурения |
Рис. 3.65. Твердосплавная |
Рис. 3.66. Алмазная |
Рис. 3.67. Шарошеч- |
коронка |
коронка |
ное долото |
|
242 |
|
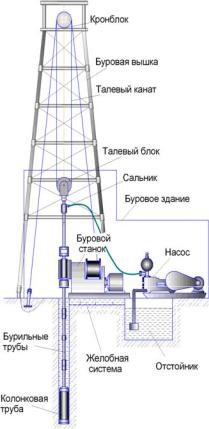
3.5.1. Буровые установки, оборудование и инструмент
Разведочное колонковое бурение осуществляется различными буровыми установками с использованием специального бурового оборудования и инструментов.
По целевому назначению основными классами буровых комплексов являются установки, специализируемые по использованию:
- для разведки твердых полезных ископаемых;
- для бурения неглубоких скважин при геологической съемке, картировании и поисках полезных ископаемых;
- для бурения скважин специального назначения, в том числе, в условиях морских акваторий и подземных горных выработок.
- для проходки инженерногеологических, гидрогеологических и структурно-поисковых скважин.
По транспортабельности буровые установки подразделяются на
стационарные, передвижные и самоходные.
Стационарные буровые ус-
тановки предназначены для длительного бурения скважин глубиной до 2000 м и более, перемещаются отдельными блоками с использованием специализированных транс-
портных средств. В состав установки входят буровой станок, насосы, буровая вышка с талевой оснасткой, сальник, оборудование и инструмент для и выполнения спуско-подъемных операций, буровое здание и вспомогательные привышечные сооружения (рис. 3.68).
Технические решения основных узлов входящих в состав установок могут быть различны. Поэтому существуют отдельные классификации элементов буровых комплексов (станков, насосов, вышек и др.).
243
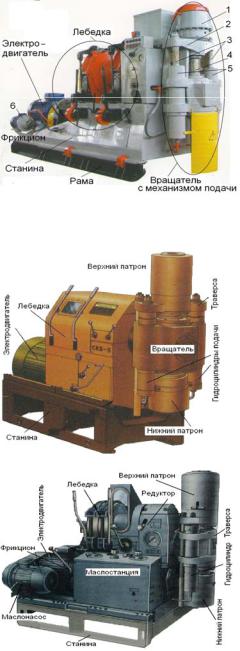
Рис. 3.69. Внешний вид станка СКТО-75: 1 – гидравлический патрон; 2 – траверса; 3 – штоки цилиндров подачи; 4 – шпиндель; 5 –цилиндры подачи; 6 - маслонасос
Рис. 3.70. Внешний вид станка СКБ-5
Рис. 3.71. Внешний вид станка СКБ-4
244
Буровой станок пред-
ставляет собой машину, как правило, с тремя основными исполнительными органами: вращателем, механизмом подачи и лебедкой (рис. 3.69).
Вращатель сообщает вращение колонне бурильных труб и с помощью механизма подачи, в виде гидроцилиндров и зажимных патронов, обеспечивает через колонну бурильных труб осевую нагрузку на забой скважины.
Посредством лебедки через талевую оснастку выполняется спуск и подъем снаряда (бурильной колонны, колонковых труб с породоразрушающим инструментом).
Монтажно-несущим элементом станка, где размещаются его исполнительные органы, является станина, которая крепится на раме.
Вбольшинстве современных станков вращательного бурения (СКТО-75 (ЗИФ1200МР), рис. 3.69), СКТО-65
(ЗИФ-650), СКБ-4 (рис. 3.71),
СКБ-5 (рис. 3.70) лебедка и вращатель получают механическую вращательную энергию (мощность, частоту вращения и крутящий момент) от двигателя через трансмиссию, представляющую собой комплекс различных устройств и механизмов, соединяющих двигатель с исполнительными органами станка.
Всоставе трансмиссии выделяются (рис. 3.72):
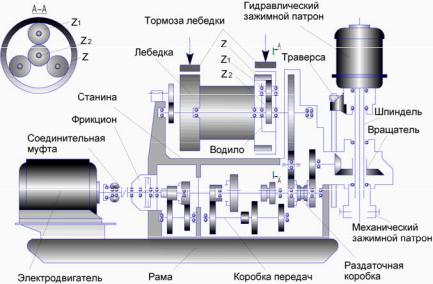
упругая соединительная муфта, соединяющая выходной вал дви-
гателя и входной вал фрикциона;
фрикцион, элементами которого являются диски, часть из которых связана с входным валом, а часть с выходным валом и имеют возможность осевого перемещения друг относительно друга по шлицам входного вала и муфты выходного вала. Усилие поджатия дисков друг к другу регулируется рукояткой включения, а за счет силы трения между парами дисков при их прижатии друг к другу обеспечивается плавная передача вращения от вала двигателя на выходной вал фрикциона, и далее – на входной вал коробки передач;
коробка передач служит для ступенчатого регулирования частоты вращения, и представляет собой редуктор с различными парами зубчатых колес, включение которых производится путем перемещения по шлицам выходного вала перемещающейся шестерни зубчатой пары;
раздаточная коробка – это редуктор с несколькими выходными валами, вращение каждого из которых обеспечивает привод лебедки или вращателя.
Рис. 3.72. Кинематическая схема станка СКТО -75
Шпиндель представляет собой полый вал, как правило, с шестигранной внешней поверхностью. Внутри него размещается ведущая бурильная труба, которая закрепляется при помощи зажимных патронов. Вращение на шпиндель, а, следовательно, и на ведущую трубу передается горизонталь-
245
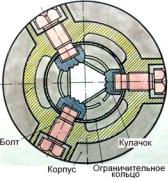
ной конической шестерней вращателя, имеющей шестигранную внутреннюю поверхность, соответствующую форме шпинделя. Путем такого сочленения шпиндель получает вращение, и имеет свободу вертикального перемещения.
Гидравлический зажимной патрон с помощью расположенных в нем плашек усилием пружин заклинивает ведущую трубу во вращателе. Раскрепление патрона при перехвате бурового снаряда в ходе углубки скважины, а также при наращивании бурильной колонны и при спуско-подъемных операциях осуществляется гидравлической системой станка.
Механический патрон (рис. 3.73)
обеспечивает закрепление ведущей трубы, исключая ее осевое перемещение при наращивании бурильной колонны. Зажимные плашки (кулачки) патрона сдвигаются (раздвигаются) с помощью специальных болтов.
В буровых станках СКБ-4 и СКБ-5 как верхний, так и нижний зажимные патроны являются гидравлическими с автоматическим перехватом при наращивании бурильной колонны. Управление патронами осуществляется гидравлической системой станка.
Вращатель буровых станков через траверсу связан с силовыми цилиндрами подачи.
Траверса представляет собой горизонтальную балку, жестко закрепленную центральной своей частью на шпинделе станка, а концами – на рабочих штоках гидроцилиндров подачи, и служит для передачи осевого усилия от штоков гидроцилиндров подвижному шпинделю бурового станка и от него через гидравлический зажимной патрон бурильной колонне.
Силовые гидроцилиндры являются исполнительным органом, преобразующим рабочее давление в гидросистеме в усилие подачи и энергию потока масла в гидросистеме в работу поступательного перемещения штоков гидроцилиндров под нагрузкой.
Таким образом, шпиндель бурового станка через пару конических шестерен (вращатель) получает вращение от привода, а через траверсу – осевые усилия перемещения от гидроцилиндров подачи. Зажимные патроны передают вращение и осевое усилие от шпинделя бурильной колонне.
Лебедка – один из основных функциональных блоков бурового станка – представляет собой механическую систему планетарного типа.
Принцип работы лебедки следующий. Центральная солнечная шестерня Z2 неподвижно (на шпонке) закреплена на валу лебедки и получает
вращение от раздаточного редуктора. В постоянном зацеплении с ней нахо-
246
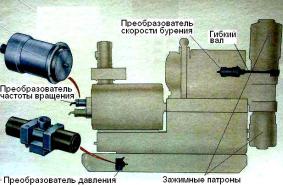
дятся три шестерни сателлитов Z1 , имеющие возможность вращаться как
вокруг собственной оси, так и обегать вокруг солнечной шестерни, получая вращение от нее через зубчатое зацепление. Оси сателлитов закреплены на водиле – массивном стальном диске, свободно (на подшипниках) сидящем
на валу лебедки. Одновременно сателлиты Z1 находятся в постоянном за-
цеплении с внутренним зубчатым венцом Z , выполненным в шкиве барабана лебедки, и могут вращать его, оставаясь на месте, либо обегать его и солнечную шестерню, если заторможен (остановлен) зубчатый венец. При обегании сателлитами зубчатого венца и солнечной шестерни водило начинает вращаться. При остановке водила начинает вращаться, получая вращение от солнечной шестерни через сателлиты, зубчатый венец, а вместе с ним и барабан лебедки. Водило и зубчатый венец снабжены тормозными колодками, воздействуя посредством рычага на которые можно затормозить (остановить) их вращение. Остановкой водила рычагом тормоза подъема обеспечивается вращение барабана лебедки. Происходит наматывание ходового конца каната талевой оснастки на барабан лебедки. При торможении зубчатого венца и барабана рычагом тормоза спуска фиксируется неподвижность талевой оснастки.
При раскреплении тормозных колодок происходит сматывание каната
сбарабана лебедки под действием веса снаряда.
Вотличие от рассмотренных агрегатов, буровой станок СКБ-7 оснащен тиристорным приводом и не имеют в своем составе коробки передач (рис. 3.74). Станки комплектуются плавно регулируемым электроприводом, состоящим из реверсивного и нереверсивного агрегатов, релейного шкафа и пульта управления. Вращатель оборудован двумя гидроцилиндрами и двумя зажимными патронами: верхним – пружинно-гидравлическим и нижним
– гидравлическим. Подача инструмента, регулирование осевой нагрузки, управление патронами, а также операции перемещения станка по раме от
Рис. 3.74. Структура станка СКБ-7
247
устья скважины и обратно обеспечиваются электрогидравлической системой управления. Все элементы и механизмы гидросистемы станка собраны в единый блок. Планетарный редуктор лебедки станка собран в литом стальном корпусе, и расположен слева от барабана лебедки, который закреплен на станине. Управление лебедкой установлено на вынос-

ном пульте управления.
Буровая установка УКБ-8 не имеет в своем составе бурового станка как такового. Она состоит из отдельных конструктивно независимых блоков: блока ротора, блока лебедки, блока подачи, блока насосной установки, блока гидросистемы и пр. Примерная схема расположения оборудования установки приведена на рис. 3.75.
В отличие от рассмотренных установок в УКБ-8 используется роторный вращатель, который представляет собой механизм редукторного типа. Основным его рабочим элементом является горизонтально расположенный дискообразный стол с относительно большим центральным проходным отверстием, и зубчатым венцом, выполненным по его наружному диаметру. Ротор не имеет жесткой конструктивной и кинематической связи с механизмом подачи, и является самостоятельным механизмом.
Рис. 3.75. Схема размещения оборудования установки УКБ-8:
1 – буровые насосы НБ5; 2 –усилитель; 3 – главный привод (электродвигатель переменного и генератор постоянного тока); 4 – регулятор подачи; 5 – электростанция ПЭС-15Л; 6 – блок лебедки; 7 – система охлаждения лебед-
ки; 8 – устье скважины; 9 – подсвечник; 10 – верстак; 11 – датчик давления; 12 – стеллаж; 13 – маслостанция; 14 – гидравлический пульт управления; 15 – электрический пульт управления; 16 – контрольно-измерительная аппара-
тура КУРС-613; 17 – шкаф тиристорный; 18 – реостат; 19 – шкаф управления постоянного тока; 20 – шкаф управления переменного тока
Буровые вышки служат для проведения спускоподъемных операций. В практике геологоразведочных работ используются деревянные и металлические вышки. По конструкции к основным типам буровых вышек относятся (рис. 3.76):
248
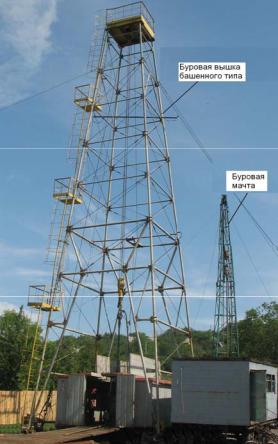
вышки башенного типа, особенностью которых является то, что талевая оснастка размещается внутри контура конструкций, образующих несущий ствол вышки;
буровые мачты, представляющие собой буровые вышки, талевая оснастка которых полностью или частично вынесена за контур конструкций, образующих их несущий ствол.
При бурении глубоких скважин стационарными буровыми установками вышки монтируются на фундаментах. Во многих случаях вместо фундаментов нижнее основание вышки изготовляется в виде двух полозьев из
стальных швеллеров, связанных поперечными поясами.
Башенные вышки собирают на специально подготовленной площадке. Поднимают их с помощью автокрана и тракторов, применяя для этого закрепленную на оттяжке подъемную стрелу, установленную между полозьями вышки, и отнесенную талевую оснастку, свободный конец которой прикрепляется к скобе трактора.
Буровые мачты более совершенны в инженерном отношении, чем вышки башенного типа. Они изготовляются на заводах и имеют высокую степень сборочной готовности (составляются из нескольких легко соединяемых блоков). Некоторые конструк-
ции буровых мачт передвижных и самоходных установок выполняются
249

складными или опускающимися с использованием гидравлических подъемных устройств.
Грузоподъемность буровых вышек (мачт) выбирают с учетом веса наиболее тяжелой колонны бурильных или обсадных труб и сил трения, возникающих в скважине при подъеме колонны.
Вес колонны, опущенной в скважину, наполненную промывочным раствором, определяют по формуле
QgL 1 ж ,
где - коэффициент, учитывающий приращение веса колонны за счет соединений бурильных труб (для ниппельного соединения к=1,05; для
- замкового к=1,1); g - вес 1 м трубы; L - длина колонны труб; ж - удельный вес жидкости; - удельный вес материала труб.
Наибольшая нагрузка на крюк при подъеме колонны из скважины составляет
Qkp Q ,
где – коэффициент, учитывающий силы трения колонны о стенки скважины и возможный прихват труб породой: для мелких скважин =2; для глубоких = 1,5…1,25.
Спуско-подъемные операции производятся с крюком на конце лебедочного каната (однострунная талевая оснастка), когда вес колонны не превышает грузоподъемности лебедки (рис. 3.77, а). Если вес колонны на крюке превышает грузоподъемность лебедки, операции производятся с применением полиспаста (многострунной талевой оснастки) (рис. 3.77, б, в, г).
В соответствии с величиной Qkp и грузоподъемностью лебедки стан-
ка ( Рл ), решается вопрос о талевой оснастке. Число струн подвижного (та-
левого) блока, т.е. число ветвей каната ( m ), за исключением ветви наматываемой на барабан лебедки и, если таковой есть – мертвого конца каната (рис. 3.77, г) с учетом к.п.д. талевой оснастки ( =0,9…0,97), равно
m Qкр , Pл
Таким образом, при номинальном значении грузоподъемности Рл , лебедкой можно поднять колонну весом Qkp Рлт .
Нагрузку на кронблочную раму Q0 определяют следующим образом:
без применения талевой оснастки (рис. 3.77, а) Q0 2Qкр ;
при закреплении свободного конца каната на кронблоке или талевом (подвижном) блоке (рис. 3.77, б, в)
250
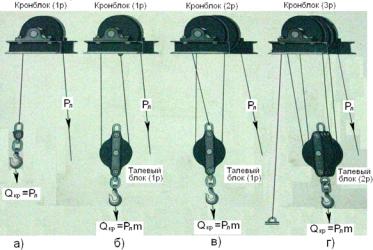
|
|
|
|
|
Q |
|
|
|
1 |
|
|
Q |
Q |
P |
Q |
|
кр |
Q |
1 |
|
|
; |
|
|
|
||||||||||
0 |
кр |
л |
кр |
|
m |
кр |
|
|
|
|
|
|
|
|
|
|
|
|
|
m |
|
при закреплении свободного конца каната на якоре (система с мертвым концом каната, рис. 3.77, г)
|
|
|
|
2Q |
|
|
|
2 |
|
Q |
Q |
2P |
Q |
кр |
Q |
1 |
|
. |
|
|
|
||||||||
0 |
кр |
л |
кр |
m |
кр |
|
|
|
|
|
|
|
|
|
|
|
m |
Сравнивая приведенные зависимости для определения Q0 видно, что
нагрузка на кронблок при одной и той же нагрузке на крюк меньше при закреплении свободного конца каната на талевом блоке или кронблоке, чем при талевой системе по рис. 3.77, г. Однако распределение нагрузки на ноги копра симметричнее при талевой оснастке с мертвым концом каната.
Поэтому при глубоком бурении применяют оснастку по схеме с мертвым концом каната.
Рис. 3.77. Схемы талевы оснасток:
а) – однострунная оснастка; б) – двухструнная оснастка с закреплением ветви каната на кронблоке; в) трехструнная оснастка с закреплением ветви каната на талевом блоке; г) – четырехструнная оснастка с неподвижным (мертвым)
концом каната, закрепленным у основания вышки;
Буровые насосы являются неотъемлемой составной частью технологической установки для бурения скважин и предназначены для нагнетания в скважину промывочной жидкости для очистки забоя от шлама выбуренных пород и охлаждения породоразрушающего инструмента. Кроме того, насос может выполнять роль силовой установки гидропривода забойных гидравлических машин (гидроударников, эжекторных насосов и т.п.).
251
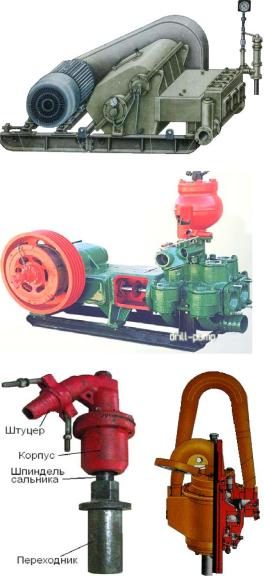
|
|
|
Учитывая, что гео- |
|||||
|
|
логоразведочные |
сква- |
|||||
|
|
жины имеют относитель- |
||||||
|
|
но |
небольшие диаметры |
|||||
|
|
и глубину, по сравнению |
||||||
|
|
с размерами нефтяных и |
||||||
|
|
газовых скважин, |
насосы |
|||||
|
|
для |
геологоразведочной |
|||||
|
|
отрасли должны обеспе- |
||||||
|
|
чивать подачу в пределах |
||||||
Рис. 3.78. Внешний вид плунжерного насоса НБ4 |
от 10-20 л/мин (при буре- |
|||||||
|
|
нии алмазными коронка- |
||||||
|
|
ми малого диаметра) |
до |
|||||
|
|
300 л/мин, в редких слу- |
||||||
|
|
чаях - до 500 л/мин. По- |
||||||
|
|
этому |
|
характеристика |
||||
|
|
парка буровых |
носов |
в |
||||
|
|
основном ограничивается |
||||||
|
|
отмеченными расходами |
||||||
|
|
жидкости |
при |
давлении |
||||
|
|
от 2,0 до 6,0 МПа. |
|
|
||||
|
|
|
В |
|
современной |
|||
|
|
практике |
|
бурения |
разве- |
|||
Рис. 3.79. Поршневой буровой насос НБ-32 |
дочных |
скважин |
наибо- |
|||||
|
|
лее широкое применение |
||||||
|
|
получили поршневые на- |
||||||
|
|
сосные установки НБ-32 |
||||||
|
|
и |
НБ-50 |
(рис. |
3.79), |
а |
||
|
|
также плунжерные – НБ- |
||||||
|
|
25/1,6; НБ-63/4,0; НБ- |
||||||
|
|
120/4,0; НБ-160/6,3; НБ4- |
||||||
|
|
320/63 и НБ-320/10 (рис. |
||||||
|
|
3.78). |
|
|
|
|
|
|
|
|
|
Для |
присоедине- |
||||
|
|
ния |
|
нагнетательного |
||||
|
|
шланга бурового насоса к |
||||||
|
|
вращающейся |
колонне |
|||||
Рис. 3.80. Внешний вид |
Рис. 3.81. Внешний |
бурильных труб исполь- |
||||||
зуется |
сальник |
(рис. |
||||||
сальника |
вид вертлюга- |
3.80), |
или |
вертлюг- |
||||
|
сальника |
|||||||
|
сальник (рис. 3.81), кото- |
|||||||
|
|
рый одновременно обеспечивает и подвеску колонны бурового снаряда к серьге талевого блока.
252
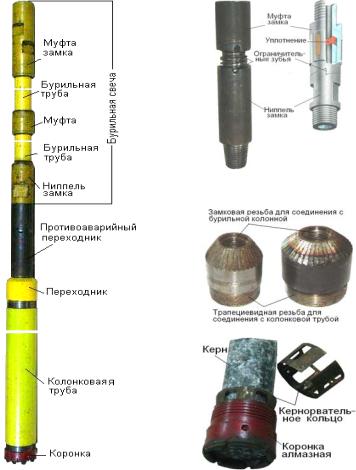
Буровой снаряд для колонкового бурения скважин включает колонко-
вый набор и колонну бурильных труб (рис. 3.82, а).
Колонковый набор в общем случае состоит из коронки (алмазной или твердосплавной) с кернорвательным кольцом (рис. 3.82, г), колонковой трубы, обыкновенного (рис. 3.82, в) и противоаварийного (рис. 3.82, б) переходников. Колонковая труба необходима для приема столбика выбуренного керна; коронка – для кольцевого разрушения горной породы на забое скважины с формированием столбика керна; кернорвательное кольцо - для отрыва и удержания керна внутри колонковой трубы при подъем ее из скважины.
б) Внешний вид противоаварийных переходников
в) Внешний вид переходника
а) Элементы бурового снаряда г) Коронка с кернорвателем
Рис. 3.82. Буровой снаряд и его элементы.
253

Колонна бурильных труб служит для передачи крутящего момента и осевой нагрузки на коронку, а также транспортирования в скважину промывочной жидкости. Состоит из отдельных отрезков труб, как правило, длиной 4,5 м, соединенных между собой муфтами (ниппелями) и замками. С колонковым набором колонна бурильных труб соединяется через противоаварийный переходник.
В большинстве случаев отдельные бурильные трубы соединяются в свечи (соединения из двух, трех и четырех труб).
При муфтово-замковом соединении, трубы между собой соединяются муфтами, а на концах свечи навинчиваются элементы замка: на верхний - ниппель, имеющим одну прорезь под ведущую вилку труборазворота, а на нижний – муфта замка с двумя прорезями под подкладную вилку и трубозахват, применяемого элеватора.
Стальные трубы геологоразведочного сортамента с муфтовозамковым соединением (СБТМ) выпускаются диаметрами 42, 50 и 63,5 мм с толщиной стенки, соответственно, 5, 5,5 и 6 мм. Для таких труб используются муфты и замки с наружным диаметром, соответственно, 57, 65 и 83
мм.
При ниппельном соединении труб обеспечивается гладкоствольность бурильной колонны за счет соответствия наружного диаметра труб и их соединений. Геологоразведочным сортаментом предусматривается выпуск ниппельных стальных труб с внутренней высадкой (СБТН), имеющих наружный диаметр 42, 54 и 68 мм с толщиной стенки в невысаженной части, соответственно, 5, 4,5 и 4,5 мм. Для таких труб используются ниппели с наружным диаметром на 0,5 мм, превышающим номинальный диаметр соответствующей трубы. Для соединения труб в свечи применяются ниппели с одной прорезью и имеющие с двух концов цилиндрическую наружную резьбу. Для соединения свечей в колонну используются ниппели с одной парой прорезей под ведущую вилку (на нижнем конце свечи) и с двумя парами прорезей для подкладной вилки труборазворота и элеватора (на верхнем конце свечи).
Кроме стальных бурильных труб для бурения скважин диаметром 76, 59, 46, 36 и 26 мм используются легкосплавные трубы (ЛБТН) с наружным диаметром 68, 54, 42, 34 и 24 мм. Толщина стенки труб диаметром: 24 мм
составляет 4,5 мм; 34 мм – 6,5 мм; 42 мм – 7 мм; 54 – и 68 мм -9 мм. Такие трубы имеют ниппельное соединение, в виде замка, состоящего из одно- и двухпрорезного ниппелей (рис.3.83).
Рис. 3.83. Элементы замка ниппельного соединения труб
254
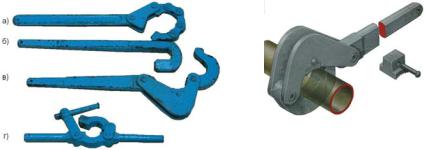
К вспомогательному инструменту для колонкового бурения относят-
ся ключи для бурильных, колонковых и обсадных труб, короночные ключи, шарнирные хомуты и фарштуль.
Ключи для бурильных труб (рис. 3.84) предназначены для их свинчивания (развинчивания) с захватом, как за гладкую поверхность, так и для захвата замков и ниппелей за прорезь.
Ключ состоит из рукоятки и рабочего сектора, который может быть одноэлементным (литым или кованным), выполненным за одно с рукояткой; шарнирным с откидными скобами, оснащенными плашками; с цепным захватом и др.
Одноэлементный ключ (рис. 3.84, б) применяется для замков и ниппелей, имеет головку, зев которой служит для захвата замков и ниппелей за их прорези.
Рабочим сектором цепных ключей (рис. 3.84, а) является накидная цепь, длина которой соответствует периметру сечения трубы, и снабжена упорным зубом.
д)
Рис. 3.84. Ключи для бурильных труб:
а) ключ цепной; б) ключ одноэлементный для замков и ниппелей; в) – ключ шарнирный с откидными скобами; г) - шарнирный хомут; д) – рабочее положение шарнирного ключа при захвате бурильной трубы.
Для захвата труб и их соединений за гладкую часть при свинчивании или развинчивании применяются шарнирные ключи, рабочий сектор которых состоит из двух откидных скоб, соединенных между собой шарнирно на осях (рис. 3.84, в). На внутренней поверхности наружной скобы закрепляется плашка, которая исключает проскальзывание ключа (в закрытом положении) относительно поверхности трубы. При захвате поверхности трубы зуб короткого плеча рукоятки упирается в опорную ось закрывающей скобы, фиксируя ключ в закрытом положении (рис. 3.84, д).
Шарнирный хомут (рис. 3.84, г) является трубозахватным устройством и, в основном, служит для закрепления его на бурильной трубе в любом месте при необходимости подвешивания колонны на устье скважины, или поворота снаряда в скважине вручную.
255
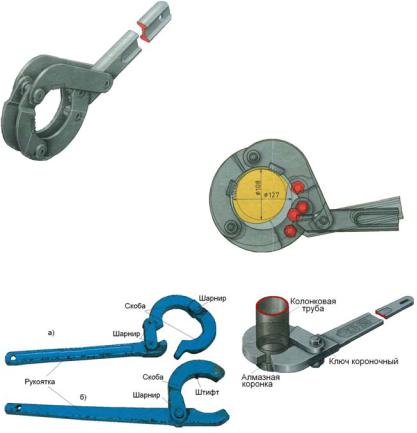
Ключи для колонковых и обсадных труб в отличие от шарнирных ключей для бурильных труб имеют три шарнирно закрепленных скобы, на двух из которых установлены удерживающие плашки (рис. 3.85, а, б) Как правило, внутренняя откидная скоба имеет две опорные оси, на каждую из которых может опираться зуб рукоятки, что позволяет применять один ключ для двух смежных размеров труб, например, 73 мм / 89 мм или 108 мм
/ 127 мм (рис. 3.85, в).
б)
а)
Рис. 3.85. Шарнирный: а) ключ в ра- |
|
бочем (закрытом) положении; б) - |
|
элементы ключа; в) – положение |
|
рабочего сектора ключа для двух |
|
смежных размеров труб: 108 мм / |
|
127 мм. |
в) |
в)
Рис. 3.86. Короночные ключи: а) гладкозахватный двухшарнирный ключ; б) – ключ для работы с алмазными коронками; в) - рабочее положение ключа при захвате алмазной коронки
Для свинчивания (развинчивания) тонкостенных колонковых труб и твердосплавных коронок используются гладкозахватные ключи, которые в отличие от шарнирных ключей не имеют удерживающих зубчатых плашек
(рис. 3.86, а).
256
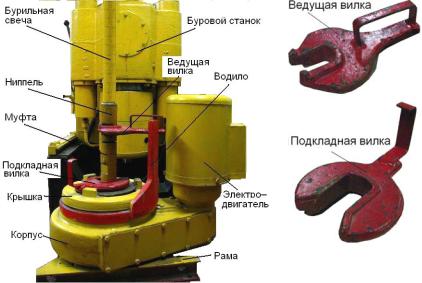
Короночные ключи предназначены для работы с алмазными коронками, имеющими цилиндрические углубления на корпусе; имеют одну откидную скобу, в теле которой запрессован штифт (рис. 3.86, б).
Оборудование и инструмент для выполнения и механизации спуско-
подъемных операций. К такому виду оборудования относятся: трубозахватные устройства (элеваторы), труборазворот и вспомогательный инструмент (наголовники для полуавтоматических элеваторов, подкладные и ведущие вилки).
Труборазворот РТ-1200М (рис. 3.87) предназначен для свинчивания и развинчивания бурильных и обсадных труб и входит в состав буровых установок типа УКБ (на базе станков СКБ-4 и СКБ-5), а также станков СКТО65 и СКТО-75.
Механизм устанавливается на устье скважины и пропускает свечу через центральное отверстие в корпусе, в котором размещен редуктор, передающий вращение от электродвигателя водилу. Бурильная колонна удерживается на подкладной вилке, которая предварительно вставлена в нижнюю прорезь муфты замка и размещена в отверстии неподвижного корпуса механизма. Ведущая вилка вводится в прорезь ниппеля замка отвинчиваемой свечи. При включении механизма, водило воздействует на ведущую вилку и развинчивает замковое соединение, освобождая свечу от бурильной колонны.
Верхняя прорезь муфты замка служит для захвата колонны кольцевым элеватором или наголовником полуавтоматического элеватора.
Рис. 3.87. Механизация операций свинчивания и развинчивания бурильной колонны с помощью труборазворота РТ-1200М
257

|
|
При |
использовании |
|
|
кольцевого элеватора (рис. |
|||
|
3.88, а) его |
надевание (снятие) |
||
|
на двухпрорезную муфту замка |
|||
|
в процессе выполнения спуско- |
|||
|
подъемных операций осущест- |
|||
|
вляется вручную. В корпусе |
|||
|
элеватора имеется продольный |
|||
|
паз с уступом внизу, на кото- |
|||
|
рый |
опираются |
заплечики |
|
|
верхнего прореза муфты замка. |
|||
|
На корпусе помещается под- |
|||
|
вижное кольцо, которое при- |
|||
|
поднимают при надевании эле- |
|||
|
ватора и затем опускают для |
|||
|
предотвращения |
выпадения |
||
|
замка в процессе спуска или |
|||
Рис. 3.88. Внешний вид и элементы кольцевого |
подъема бурильной |
колонны. |
||
При |
снятии |
элеватора кольцо |
||
элеватора (а) и фарштуля (б) |
поднимается, и элеватор отво- |
дится в сторону. Корпус шарнирно соединен с серьгой, зашплинтованной гайкой.
Фарштуль (рис. 3.88, б) используется для подъема или спуска колонны бурильных труб с захватом и удержанием ее за нижнюю часть муфты или замка поверхностью прорезной вилки фарштуля. Устройство состоит из подъемной серьги и корпуса, выполненного в виде прорезной вилки, над которой размещается муфта или замок бурильных труб. Ширина зева прорезной вилки соответствует диаметру бурильных труб, которые фиксируются в корпусе фарштуля с помощью страховочного штифта.
Для выполнения спуско-подъемных операций без участия рабочего используются полуавтоматические элеваторы, работающие в комплексе с наголовниками, надеваемыми на верхнюю прорезь муфты замка каждой поднятой и установленной на подкладной вилке свечи бурильной колонны.
Полуавтоматический элеватор (на примере элеватора МЗ-50-80), схема которого изображена на рис. 3.89, состоит из корпуса с прорезным зевом и серьги, соединенной с корпусом на осях. К серьге приварен отражатель, для отсоединения элеватора от свечи, извлеченной из скважины. В корпусе элеватора выполнена вертикальная цилиндрическая расточка с опорным буртиком в нижней части для подхвата свечи за наголовник. Закрытие зева выполняется поворотным роликом, фиксирующимся подпружиненной защелкой.
При подъеме колонна бурильных труб с надетым на прорезь муфты замка наголовником устанавливается на подкладной вилке труборазворота
258
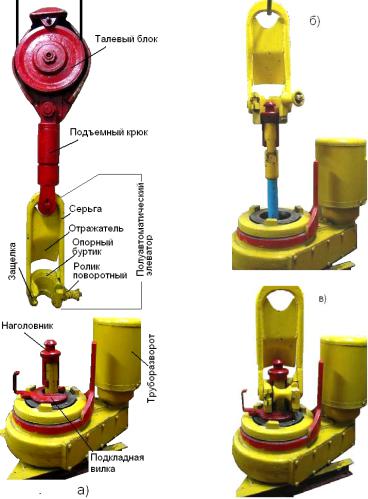
(рис. 3.89, а). Под буртик наголовника заводится элеватор. При подъеме снаряда поворотный ролик элеватора оставляют открытым (рис. 3.89, б). После подъема, развинчивания замкового соединения и установки свечи на подсвечник элеватор опускается, перемещаясь вдоль трубы; при этом за счет планки отражателя элеватор выходит из контакта с бурильной трубой и в свободном виде опускается к устью скважины.
Рис. 3.89. Спуско-подъемные операции с использованием полуавтоматического элеватора
259
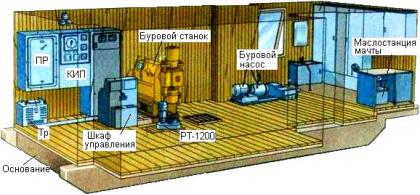
При спуске колонны элеватор надевается на нижний конец свечи, установленной на подсвечник и с закрытым поворотным роликом поднимается по свече вверх, подхватывая ее в верхней части за наголовник. Свеча приподнимается, и вручную подводится к устью скважины, опускается в скважину через центральное отверстие труборазворота и устанавливается на подкладной вилке (рис. 3.89, в). После этого последовательно снимаются элеватор и наголовник. Затем элеватор надевается на следующую свечу, установленную на подсвечник, и цикл работы повторяется.
Буровые здания предназначены для размещения в них бурового оборудования, защиты его и персонала, обслуживающего буровую установку от непогоды и строятся из различных материалов и разных размеров.
Врайонах работ с относительно мягким климатом буровое здание строится из дощатых щитов и обшивается утеплителем.
Вместностях с суровым климатом здание выполняется в виде сруба из бревен или брусьев.
По способу транспортировки и сборки буровые здания могут быть щитовыми и блочными.
Щитовые здания монтируются на основании из отдельных размерных щитов, соединяющихся между собой болтами. При перевозке производится разборка щитов, при этом основание здания с оборудованием транспортируется отдельно от разобранных конструкций.
Блочные здания состоят из одного или двух блоков, которые при перевозке не разбираются. Двухблочные здания состоят из станочного и насосного блоков.
Передвижные установки (рис. 3.91) характеризуются наличием такого элемента, как транспортная база в виде саней или колесных платформ, на которой буровая установка размещается не только при перевозках, но и во время бурения скважин.
Рис. 3.90. Размещение оборудования в блоке передвижной установки
260
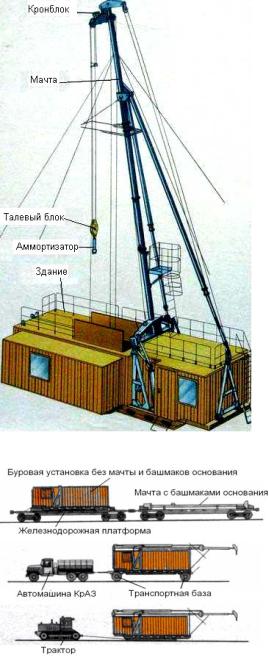
Рис. 3.91. Передвижная установка УКБ-5П
Рис. 3.92. Перевозка установки УКБ-5П
261
Основу технологических комплексов данного класса составляют установки типа УКБ (УКБ-4П, УКБ5П и УКБ-7П). Они представляют собой комплекс бурового и энергетического оборудования, контрольноизмерительной аппаратуры, обеспечивающей все виды работ при проходке скважины.
Основание установки выполнено в виде металлических саней, на замкнутой раме которых смонтированы мачта и буровое здание. Внутри здания располагается буровой станок, буровой насос, труборазворот, шкаф управления и др. (рис. 3.90).
Перевозка установки УКБ-4П обеспечивается единым блоком железнодородным транспортом или по автомобильным дорогам с помощью тягача на собственных полозьях основания бурового здания или с помощью колесной тележки ТБ-15.
Установка УКБ-5П может перевозится с разделением мачты и бурового здания (рис. 3.92).
Блочная конструкция установки УКБ-7П позволяет перевозить ее отдельными блоками: станочным, насосным, вспомогательным.
В целом, стационарные и передвижные уста-
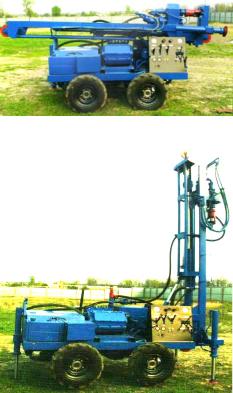
новки для бурения на твердые полезные ископаемые представляют собой наиболее полные и универсальные технологические комплексы, способные при необходимости решать любые задачи разведочного характера, в том числе осуществлять бурения гидрогеологических, инженерногеологических и другого назначения скважин, хотя с меньшей эффективностью, чем специализированные установки.
Специализированные буровые установки.
Для бурения неглубоких скважин при геологической съемке, картировании или для бурения инженерно-геологических, гидрогеологических скважин или скважин специального назначения используются, в основном, самоходные, иногда переносные установки. Такие установки представляют собой особый класс буровых технологических комплексов, позволяющих бурить скважины в диапазоне диаметров от 93 до 900 мм в породах любых категорий, как вращательным способом с промывкой (или с продувкой) и без промывки скважин (шнеками), так и ударно-вращательным, ударно-
канатным или ударнозабивным способом. Установки монтируются на шасси автомобилей, или на собственной колесной или гусеничной транспортной базе.
Для бурения скважин
Рис. 3.93. Малогабаритная буровая установ- |
на воду, а также с целью вы- |
||||
ка КЗБТ-Б1 в транспортном положении |
полнения |
|
инженерно- |
||
|
геологических |
изысканий, |
|||
|
геологической съемки и кар- |
||||
|
тирования |
Киевским |
заво- |
||
|
дом буровой техники разра- |
||||
|
ботана |
малогабаритная ус- |
|||
|
тановка КЗБТ-Б1 (рис. 3.93- |
||||
|
3.94). Установка применяет- |
||||
|
ся для бурения колонковым |
||||
|
способом диаметром 93 мм |
||||
|
на глубину до 120 м, с про- |
||||
|
мывкой |
при |
бескерновом |
||
|
бурении диаметром 112 мм |
||||
|
– до 80 м, шнеками диамет- |
||||
|
ром 200 мм – до 30 м. |
Ус- |
|||
|
тановка укомплектована мо- |
||||
|
дернизированным насосом |
||||
Рис. 3.94. Установка КЗБТ-Б1 в рабочем |
НБС (на базе насоса НБ- |
||||
положении |
120/4,0) |
с |
повышенной по- |
||
262 |
|
|
|
|
|
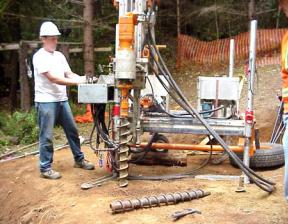
дачей жидкости (до 300 л/мин). Скорость самоходного передвижения по участку работ до 3 км/ч. Масса установки – 2500 кг. Элементы установки
|
размещаются на собст- |
|||
|
венной |
колесной |
или |
|
|
гусеничной |
транспорт- |
||
|
ной базе. |
|
|
|
|
Для бурения мел- |
|||
|
ких скважин при поис- |
|||
|
ковых, |
съемочных |
и |
|
|
других работах исполь- |
|||
|
зуются также малогаба- |
|||
|
ритные |
установки |
вра- |
|
|
щательного бурения без |
|||
|
промывки. К ним отно- |
|||
|
сятся |
механические |
||
|
пробоотборники МП-1, |
|||
Рис. 3.95. Шнековое бурение скважины |
(см. рис. 2.29), а также |
|||
целый |
ряд |
передвиж- |
||
малогабаритной передвижной установкой |
ных и самоходных ус- |
тановок для шнекового бурения с упрощенной структурой и кинематикой привода (рис. 3.95).
Транспортирующая часть – колонна шнеков соединяется со шпинделем вращателя. Разрушение породы при шнековом бурении производится двухили трехлопастными долотами. Диаметр по окружности лопастей долота обычно на 15 – 20 мм больше диаметра шнека. Шнек представляет собой трубу, на которой по винтовой линии с шагом 0,6 – 0,8 диаметра шнека приварена спираль – стальная лента. Долото со шнеком и шнеки между собой соединяются при помощи быстроразъемных замков.
Шнековое бурение весьма эффективно в мягких, сыпучих породах и в галечниках, гранулометрический размер которых меньше расстояния от трубы шнека до края ленты. Вращающийся шнек при транспортировке породы на поверхность как бы оштукатуривает стенки скважины, повышая их устойчивость. В сочетании с высокой скоростью бурения это дает возможность получать скважины в мягких породах и даже в песках, период устойчивого состояния которых, соизмерим со временем бурения скважины. При проходке указанных пород, как правило, принудительная подача инструмента применяется лишь на стадии забуривания первого шнека на глубину около 1 м, а затем бурение продолжается под воздействием собственного веса инструмента при возможно большей скорости вращения.
Среди легких установок для бурения неглубоких скважин в твердых и крепких породах весьма эффективно зарекомендовала себя переносная малогабаритная установка, разработанная в Цзилиньском университете (Китай) (рис. 3.96). Установка может бурить скважины различного целевого на-
263
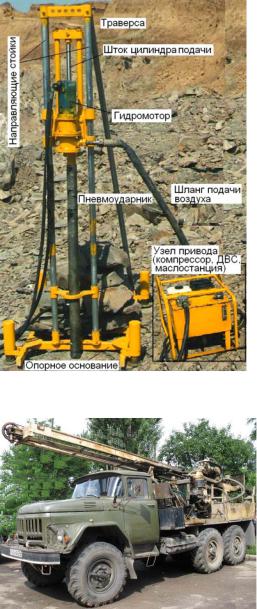
Рис. 3.96. Малогабаритная переносная установка (Китай)
Рис. 3.97. Установка УРБ2А-2 в транспортном положении
264
значения и представляет собой мобильную разборную конструкцию при массе отдельных узлов до 30 кг. Установка реализует ударновращательный способ бурения с помощью малогабаритного гидродвигателя и пневмоударника.
К более тяжелым буровым установкам относятся самоходные установки роторного типа или с подвижным вращателем, предназначенные для вращательного бурения гидрогеологических, геофизических и структурных скважин.
Установки с подвижным вращателем
(рис. 3.97-3.98) смонти-
рованы на шасси автомобиля и приводятся в действие от его двигателя. На раме установки размещены: мачта с подвижным вращателем, гидродомкраты перемещения вращателя и опорные гидравлические домкраты; гидродомкрат подъема мачты; раздаточная коробка; буровой насос или компрессор; гидравлические устройства и пульт управления. Отбор мощности на механизмы установки (буровой насос или компрессор, маслонасосы для привода гидродвигателя подвижного
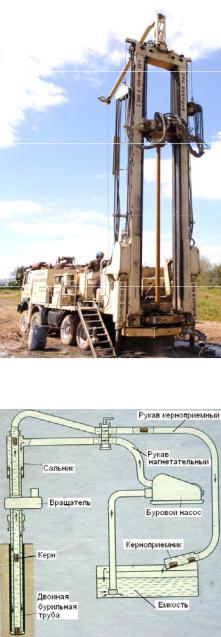
Рис. 3.98. Самоходная установка с подвижным вращателем на точке бурения
Рис. 3.99. Схема бурения с гидротранспортом керна
265
вращателя и домкратов) производится от трансмиссии автомобиля через коробку отбора мощности, связанную валом с раздаточной коробкой.
Вращатель, перемещающийся по мачте, служит для передачи крутящего момента на буровой снаряд, а также для свинчивания (развинчивания) бурильных труб. Управление установкой осуществляется с пульта, на котором расположены органы оперативного управления и приборы контроля процесса бурения. Буровой инструмент может перевозиться на автомобильном прицепе.
К установкам с подвижным вращателем относятся также самоходные установки
КГК-100 и КГК-300 (рис. 3.99- 3.100) предназначены для бурения с непрерывной доставкой из скважины на поверхность керна и шлама восходящим потоком промывочной жидкости.
Комплект технических средств для бурения с гидротранспортом керна включает: специальные твердосплавные коронки, керноприемный снаряд с керноломом, двойные бурильные трубы, промывочный сальник, обеспечивающий подвод жидкости от бурового насоса к кольцевому зазору и отвод ее из центрального канала вместе с керном, систему промывки, позволяющую оперативно регулировать направление потока и доставлять керн
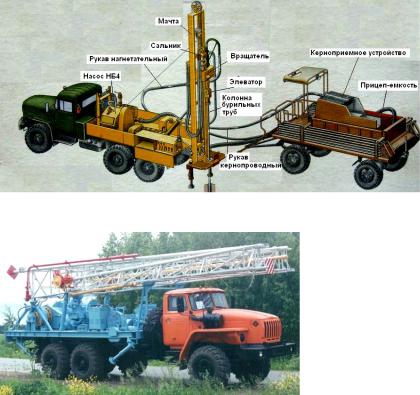
по шлангам к керносборному устройству.
Керносборное устройство состоит из перфорированных или сетчатых лотков, перемещаемых цепным транспортером. Лотки поочередно заполняются керном, который затем перекладывается в керновые ящики. Гидротранспорт керна используются при бурении скважин глубиной до 100 и до 300 м в породах I-V категорий на стадиях поисков и разведки руд полиметаллов, золота, бокситов, нерудных строительных материалов, а также при геофизических и гидрогеологических исследованиях.
Жидкость нагнетается к забою по кольцевому зазору между поверхностями труб двойной бурильной колонны (наружными трубами - передающими осевую нагрузку и крутящий момент, и внутренними, служащими кернопроводом).
Применения установок КГК позволяет значительно сократить время бурения скважин, прежде всего, за счет исключения из производственного цикла подъема инструмента для извлечения керна из колонковых труб.
Рис. 3.100. Установка КГК-300 для бурения с гидротранспортом керна
Установки с роторным вращате-
лем типа УРБ (рис. 3.101) и БА (рис. 3.102) структурно идентичны выше рассмотренным установкам и предназначены для бурения структурно - поисковых, разведочных и гидрогеологических сква-
Рис. 3.101. Внешний вид установки УРБ-12У жин вращательным способом с очисткой
266
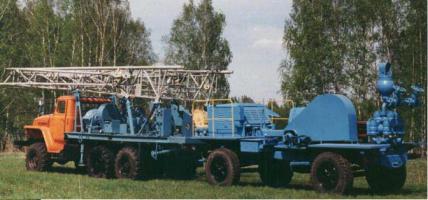
забоя скважины промывкой.
Буровой блок установок смонтирован на шасси автомобиля. На раме бурового блока размещаются: мачта (как правило, складывающаяся), опорные винтовые домкраты для разгрузки шасси автомобиля во время бурения, коробка отбора мощности, коробка передач, лебедка, ротор, буровой насос, генератор, гидравлические домкраты подъема мачты, компрессор, гидравлические и пневматические устройства. Отбор мощности на механизмы бурового блока осуществляется от трансмиссии автомобиля через коробку отбора мощности, соединенную через карданный вал с коробкой передач бурового блока. Привод бурового насоса, лебедки и ротора – от коробки передач, а привод генератора, компрессора и маслонасоса – от коробки отбора мощности. Буровые установки оснащаются механизмом для свинчивания (развинчивания) бурильных труб. В ряде конструкций насосно-силовой блок может быть смонтирован на двухосном автомобильном прицепе (рис. 3.102).
Рис. 3.102. Внешний вид самоходной буровой установки 1БА15В
3.5.2. Промывка скважин
Промывка скважин является необходимым элементом технологического процесса при вращательном бурении скважин. С ее помощью осуществляют непрерывную очистку забоя от шлама (разбуренной породы) и охлаждение породоразрушающего инструмента. В зависимости от состава очистные агенты могут выполнять дополнительные функции:
-сохранять и повышать устойчивость стенок скважины;
-удерживать частицы выбуренной породы во взвешенном состоянии при прекращении циркуляции;
-снижать вибрации и трение бурового снаряда о стенки скважины и
др.
267
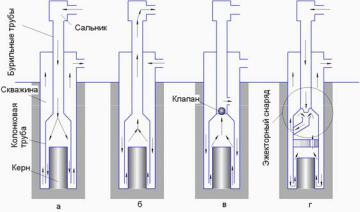
Существует четыре схемы циркуляции жидкости в скважине: прямая, обратная, призабойная (местная) и комбинированная.
Прямая циркуляция (рис. 3.103, а) заключается в принудительной подаче жидкости насосом по бурильной колонне к забою и от забоя по кольцевому каналу между бурильными трубами и стенками скважины к устью. При этом продукты разрушения забоя выносятся на поверхность.
Обратная циркуляция промывочной жидкости (рис. 3.103, б) осуществляется через загерметизированное устье скважины в кольцевой канал, по которому жидкость достигает забоя, а затем, с помощью эрлифта или насоса поднимается к поверхности по внутреннему каналу бурильных труб.
Местная (призабойная) циркуляция (рис. 3.103, в) может достигаться как за счет расхаживания бурового снаряда, так и с помощью забойных насосов. При расхаживании, в процессе подъема снаряда происходит заполнение колонковой трубы жидкостью, находящейся в скважине, а при спуске снаряда она вытесняется через обратный клапан над переходником и снова возвращается на забой. Интенсивность местной циркуляции зависит от частоты расхаживания снаряда. При использовании забойных насосов движение жидкости в колонком наборе обеспечивается вытеснителем, который механически связан с поршнем погружного гидродвигателя, совершающим возвратно-поступательные движения.
Комбинированная циркуляция (рис. 3.103, г) создается с помощью спе-
циального эжекторного снаряда. Жидкость, движущаяся по колонне бурильных труб вниз, на выходе из насадки имеет высокую скорость истечения. В результате этого в камере диффузора снижается давления и оказывается меньше гидростатического давления столба жидкости в скважине. Промывочная жидкость из колонковой трубы через отверстия перегородки устремляется в камеру диффузора, и далее, в скважину. При этом в призабойной части скважины обеспечивается интенсивная циркуляция жидкости.
Рис. 3.103. Схемы циркуляции промывочной жидкости в скважине
268
Вынос выбуренной породы из скважины на поверхность будет происходить при условии, что скорость восходящего потока V больше скорости
падения частиц в спокойной жидкости U на величину желаемой скорости выноса . Обычно принимается условие
V k(U ) ,
где k 1,1…2 – коэффициент неравномерности скорости движения потока по сечению скважины.
Подача насоса Qн , обеспечивающая вынос частиц, определяется вы-
ражением
Qн VFкс 4 Dc2 d 2 V ,
где Fкс - площадь кольцевого сечения между бурильными трубами и скважиной; Dc - диаметр скважины, d - диаметр бурильных труб.
В табл. 3.1. приведены рекомендуемые средние скорости восходящего потока V в кольцевом сечении скважины.
Таблица 3.1. Рекомендуемые скорости восходящего потока жидкости
Породоразрушающий инструмент |
Скорость V , м/с при промывке |
|
|
водой |
глинистым рас- |
|
|
твором |
Коронки алмазные |
0,5…0,8 |
0,4…0,5 |
Коронки твердосплавные |
0,25…0,6 |
0,2…0,5 |
Долота шарошечные |
0,6…0,8 |
0,4…0,6 |
Долота лопастные |
0,6…1,0 |
0,6…0,8 |
Чтобы обеспечить выход промывочной жидкости из скважины при достаточной скорости ее движения буровой насос должен развивать давление, преодолевающее все сопротивления на пути следования жидкости. Эти потери определяются по формулам, известным из гидравлики. Практически насосы, используемые при разведочном бурении должны развивать давление до 2 МПа при бурении неглубоких скважин (150-250 м); до 4 МПа для проходки скважин глубиной до 1000 м; для более глубокого бурения – до
6…8 МПа.
В качестве промывочных растворов (очистных агентов) используется техническая вода, глинистые растворы, специальные утяжеленные и безглинистые растворы, воздух, аэрированные (насыщенные воздухом) жидкости и др.
Для изменения параметров и свойств растворов, последние обрабатываются специальными реагентами – коллоидами и электролитами.
К коллоидам относятся: углещелочной реагент (УЩР), торфощелочной реагент (ТЩР), сульфит спиртовая барда (ССБ), карбоксиметилцеллю-
269

лоза (КМЦ), гипан и др. Эти реагенты существенно влияют на изменение (снижение) такого параметра, как водоотдача глинистых растворов
Реагенты-электролиты – это водные растворы кислот, щелочей и солей. К ним относятся: известь, жидкое стекло, кальцинированная сода, поваренная соль, хлористый кальций, алебастр и др. Электролиты вводятся в раствор непосредственно или в составе реагентов-коллоидов для изменения вязкости, статического напряжения сдвига и других параметров.
Все промывочные жидкости и растворы реагентов приготовляют централизованным способом на глиностанции или непосредственно на буровой.
Централизованный способ, как правило, организовывается в крупных геологоразведочных партиях и экспедициях и является наиболее производительным и экономичным, к тому же в этом случае создаются и более благоприятные условия для контроля за качеством раствора.
При бурении единичных скважин или при затруднениях с доставкой раствора к ним, глиномешалки устанавливают на буровой. Раствор и реагенты приготовляют в одно – или двухвальных глиномешалках.
На рис. 3.104 показан внешний вид двухвальной глиномешалки, которая состоит из корпуса, крышки и привода. В корпусе размещены валы, на которые надеты рабочие колеса. Валы соединены между собой открытой зубчатой передачей. Вращение ведущего вала осуществляется клиноременной передачей от шкива привода. В крышке расположен загрузочный люк. В нижней части корпуса имеется спусковой патрубок, закрывающийся клапаном при помощи рычага и противовеса. Электродвигатель установлен на
салазках привода, по которым он перемещается при натяжении клиноременной передачи.
Перед включением электродвигателя в корпус предварительно заливается вода и загружается небольшая порция глины. По мере размешивания добавляется порциями глина и химические реагенты до получения глинистого раствора с не-
обходимыми параметрами.
Очистка промывочной жидкости от частиц выбуренной породы осуществляется гидравлическим или механическим способом. В первом случае основной силой, отделяющей шлам, является сила тяжести. Это происходит при протекании раствора по очистной системе: желобам и отстойникам. Наиболее распространена очистка раствора в желобной системе (рис.3.105).
270
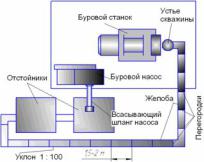
Успех очистки зависит от скорости движения раствора по желобам и их длины (чем длина больше, тем лучше очистится раствор). Средняя скорость движения раствора по желобам должна быть 0,1…0,15 м/с. Условием хорошей очистки раствора является применение перегородок по всей длине желобов и необходимость регулярной очистки желобов и отстойников от шлама.
При механическом способе очистки используются вибрационные сита и гидроциклоны. Структурная схема такого способа очистки, аналогична приведенной на рис. 3.42.
3.5.3. Технологические операции и режимы бурения скважин.
После выполнения подготовительных работ, связанных с монтажем буровой вышки, основного бурового оборудования и обустройства желобной системы, выполняется сборка бурового снаряда. Снаряд опускается в скважину на колонне бурильных труб, которая при достижении заданной глубины скважины, подвешивается на корпусе труборазворота с помощью подкладной вилки. Ведущая труба на скобе сальника подвешивается на крюк талевого блока, закрепляется в зажимных патронах шпинделя и соединяется с бурильной колонной. Включается насос и скважина наполняется промывочной жидкостью. Затем, не прекращая необходимой подачи жидкости, опускают снаряд на забой, включают его вращение, создают нужную нагрузку на коронку и начинают углубку скважины, постоянно контролируя принятые режимы бурения.
После углубки скважины на определенный интервал, величина которого зависит от твердости пород, стойкости коронки или сохранности керна, производят специальную промывку для полного удаления шлама, производят заклинивание и срыв керна и поднимают его из скважины на поверхность вместе с буровым снарядом. При этом колонну бурильных труб разъединяют на отдельные свечи, длина которых определяется высотой буровой вышки. После извлечения керна буровой снаряд на колонне бурильных труб, последовательно соединяя свечи, опускают в скважину.
Основными факторами технологического режимы колонкового бурения являются осевая нагрузка на забой, скорость вращения коронки, качество и количество жидкости, подаваемой в скважину.
Осевая нагрузка на забой зависит от физико-механических свойств пород и материала резцов, а также от опорной поверхности резцов коронки.
271
Под действием осевой нагрузки и вращения коронки при подаче промывочной жидкости в скважину резцы погружаются в породу и производят ее резание, скалывание и истирание.
Для внедрения резцов в породу необходимо выполнения условия
C Fp ,
где C - осевая нагрузка на забой; - прочность породы на сжатие; Fp - опорная поверхность резцов коронки, контактирующих с породой.
При использовании твердосплавных коронок осевую нагрузку на забой обычно определяют из расчета нагрузки на каждый резец коронки
C C0m ,
где C0 – рекомендуемая для выбранного типа коронки нагрузка на
один резец; m - число основных резцов в коронке.
Число оборотов выбранного типа твердосплавной коронки n подбирается из расчета рекомендуемой средней окружной скорости ее вращения для различного типа пород
n |
120Vk |
|
|
, |
|
D |
d |
k |
|
||
|
k |
|
|
|
где Vk - рекомендуемая средняя окружная скорость коронки; Dk и dk - соответственно наружный и внутренний диаметры коронки.
При бурении алмазными коронками величины C и n выбираются по обобщенным данным для диапазона категорий пород, группы их трещиноватости и диаметра коронки.
Количество промывочной жидкости, подаваемой в скважину, как при твердосплавном, так и при алмазном бурении определяется по формуле
Qн VFкс ,
где Fкс - наибольшая площадь кольцевого зазора между стенками
скважины (или внутренними стенками обсадной колонны) и бурильными трубами; V - рекомендуемая скорость восходящего потока для данных горнотехнических условий бурения скважины.
При использовании долот режим бескернового бурения определяется
расчетами: осевая нагрузка C C0Dд ; частота вращения n 90Vd ;
Dд
расход промывочной жидкости Q qDд . В приведенных формулах:
Dд - диаметр долота, см; C0 - рекомендуемая нагрузка на см диаметра долота, кН/см; Vд - рекомендуемая окружная скорость вращения, м/с; q - рекомендуемый расход жидкости на см диаметра долота, л/мин/см.
272
3.6. Бурение скважин из подземных горных выработок
Бурение скважин из подземных горных выработок является специфической областью бурового производства. По целевому назначению такие скважины можно условно разделить на две группы - разведочные и технические.
Задачи разведочных скважины определяются стадиями разведки. В процессе предварительной и детальной разведки бурение скважин необходимо, прежде всего, для выявления промышленных контуров месторождения и оценки качества полезных ископаемых. В стадии эксплуатационной разведки задача скважин заключается в уточнении деталей геологического строения, поиска потерянных рудных тел повышения разведанности отдельных горизонтов и выявлении новых запасов для продления срока существования рудника или шахты.
Технические скважины, пробуренные из подземных горны выработок, могут решать задачи вентиляции, водоотлива, прокладки коммуникаций и др. На угольных месторождения такие скважины решают весьма важную задачу, связанную с дегазацией массива угольного пласта, отрабатываемого участка. Их длина обычно составляет от 120 до 240 м, а иногда более 1000 м. В Украине такие скважины в основном бурят на 30-50 м, при этом чаще всего применяют бурение наклонных скважин, с помощью которых осуществляется дегазация пород, залегающих ниже и выше рабочего пласта.
Для бурения скважин в стесненных условиях подземных горных выработок чаще всего используются специализированные буровые станки и комплексы. В отечественной практике весьма широко и успешно применяется полуавтоматический буровой станок НКР100МА (рис. 3.106, а), оборудованный вращательным и подающим механизмом. Основными элементами станка являются: подающий патрон, перемещающийся по направляющим, электродвигатель, неподвижный патрон с редуктором и пневматическим захватом, пульт управления, подающие пневматические цилиндры. Станок снабжен отражательным щитком для защиты бурильщика от шлама и воды, выходящих из скважины. В комплект станка входят буровые штанги, пневмоударник, распорная колонка, ручная грузоподъемная лебедка.
Положение станка по высоте регулируется ручной лебедкой. Пневматический захват с редуктором является основным базовым
элементом станка, на котором закреплены все перечисленные узлы. С помощью пневмозахвата удерживается и вращается колонна буровых штанг, когда подающий патрон разъединяется со штангой для последующего захвата ее на новом месте.
Подающий патрон предназначен для подачи и вращения бурового инструмента во время бурения или при выдаче его из скважины. Патрон пе-
273
ремещается по двум направляющим с помощью пневматических подающих цилиндров.
Бурильная колонна состоит из отдельных свинченных между собой штанг и предназначена для подачи пневмоударника в скважину, подвода к нему сжатого воздуха и создания крутящего момента на забое скважины. Колонна наращивается по мере проходки скважины и разбирается при извлечении инструмента из нее.
На пульте управления станком имеются: кран управления подачей, кран управления пневмоударником и др.
Установка станка под любым углом достигается двухшарнирным креплением его на распорной колонке.
От электродвигателя «Д» (рис. 3.106, б) крутящий момент передается бурильной колонне 10 через трансмиссию, включающую: вал 11, планетарный редуктор, состоящий из солнечной шестерни 1, сателлитов 2 (3), неподвижного венца 4, выполненного в корпусе редуктора; и зубчатые пары 12-5 и 6-7 с пневматическими захватами, соответственно, неподвижного и подающего патронов.
Автоматическая работа агрегата осуществляется следующим образом (рис. 3.106, б). При рабочем ходе, когда бурение ведется на режиме с регулируемым усилием подачи снаряда на забой скважины, сжатый воздух поступает в камеру «а» подающего патрона и перемещает поршень 9 влево (считая от забоя скважины) и кулачками зажимает штангу 10. В то же время сжатый воздух поступает в камеру «в» неподвижного патрона, перемещает поршень 13 вперед и разжимает кулачки, освобождая штангу.
От регулятора давления через золотник и золотниковые переключатели пульта управления станка сжатый воздух поступает в цилиндры 8, обеспечивая подачу подвижного патрона к забою скважины.
Как только подвижный патрон достигает крайнего переднего положения, он с помощью тяги и рычага повернет золотник, и направление движения сжатого воздуха изменится. После поворота золотника сжатый воздух будет поступать в камеру «г» неподвижного патрона, переместит назад его поршень 13 и с помощью кулачков зажмет штангу 10. В это же время через дроссельный канал сжатый воздух поступает в камеру «б» подающего патрона, перемещает поршень 9 вперед и, отжимая кулачки, освобождает штангу 10. Теперь колонна штанг удерживается неподвижным патроном, а подвижный, освободившись от штанги, перемещается в заднее крайнее положение и, как только достигнет его, с помощью тяги и рычага повернет золотник в первоначальное положение, и цикл повторится. При извлечении колонны штанг из скважины зажимные патроны работают в обратном режиме
Станок НКР100МА позволяет бурить скважины диаметром 85 – 105 мм на глубину до 50 м в любом направлении. При бурении станки устанавливаются камерах. Горизонтальные и слабонаклонные скважины бурят из
274

камер высотой не менее 2,2 м. При бурении вертикальных скважин высота камеры увеличивается до 2,5 – 2,9 м. Если скважины бурят из выработок большой высоты, то колонка может быть установлена горизонтально. Бурение в породах небольшой крепости ведется вращательным способом коронкой режущего типа. В крепких породах и породах средней крепости коронка заменяется пневмоударником
Рис. 3.106. Общий вид (а) и кинематическая схема (б) станка НКР-100МА.
275
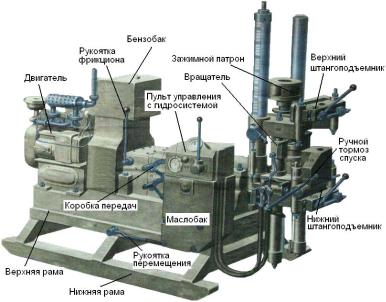
Для бурения скважин глубиной до 100 м из подземных горных выработок находят применение установки на базе станков БСК-2м1-100. Особенностью применения таких установок является необходимость использование специально оборудованной выработки (камеры) вместо буровой вышки.
Установка БСК-2м-100 состоит из двух основных блоков: бурового станка и бурового насоса. Кроме того, в состав установки входит комплект навесного оборудования к станку. Буровой станок имеет привод от электродвигателя или от двигателя внутреннего сгорания (БСК-2м1-100, рис. 3.107).
Вращатель рассчитан на пропуск штанг диаметром 33,5 и 42 мм. Все силовое оборудование размещено на верхней раме, которая перемещается по нижней раме для освобождения устья скважины на время спускоподъемных операций. Рама перемещается рукояткой. В процессе бурения бурильная труба закрепляется механическим зажимным патроном, снабженным сменными плашками. Спуско-подъемные операции производят автоматически с помощью гидросистемы станка и штангоподъемников, которые установлены на подвижной траверсе. В корпусе штангоподъемников есть два держателя, которые при движении траверсы в одну сторону захватывают бурильные трубы, а при движении в обратную сторону освобождаются.
Рис. 1.107. Внешний вид бурового станка БСК-2м1-100
276

В зависимости от расположения штангоподъемника можно спускать или поднимать буровой снаряд. Свинчивают и развинчивают трубы вручную. Станок раскрепляется стойками при установке в камере подземной выработки.
Скважины глубиной более 100 м бурят станками класса СКБ-4, СБА500 и СКТО-65 и др.
Камеры для бурения с использованием таких станков состоят из подходной горной выработки и машинной камеры (машинного зала) для размещения бурового оборудования. Формы камер для бурения скважин приведены на рис. 3.108.
Рис. 3.108. Камеры для размещения бурового оборудования для бурения скважин: а) – вертикальных; б) – наклонных; в) - горизонтальных
277
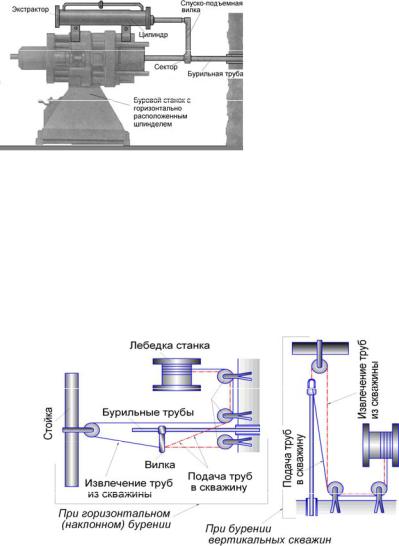
Спуско-подъемные операции в условиях подземных горных выработок выполняют с помощью экстрактора (рис. 3.109) или через лебедку станка с помощью системы блоков (рис. 3.110).
Экстракторы монтируются на вращателях, станине станка или на распорных колонках.
Экстракторы представляют собой гидравлический или пневматический цилиндр с находящимся внутри поршнем и штоком, на конце которого закреплен эксцентрично расположенный сектор с насечкой.
При движении штока в одну сторону, бурильная труба захватывается сектором, а при движении в обратную - сектор проскальзывает по ней. Гидравлический экстрактор рабо-
тает на воде, подаваемой буровым насосом. Подача жидкости или воздуха в разные полости цилиндров переключается на специальном пульте управления с помощью золотника. Пневматический экстрактор подключается к магистрали сжатого воздуха.
Спуско-подъемные операции с использованием станков типа СКБ, СКТО и СБА осуществляются по схемам, приведенным на рис. 3.110. Блоки для направления троса на барабан лебедки располагаются недалеко от устья скважины в груди забоя выработки. Кронблочный блок служат для направления троса по оси скважины.
Рис. 3.110. Выполнение спуско-подъемных операций с помощью троса и блоков
278
Буровая установка «Старт» (рис. 3.111) предназначена для бурения по углю горизонтальных и наклонных опережающих скважин диаметром 250 и 300 мм, глубиной до 30 м в лавах пологих пластов мощностью 0,8— 1,9 м, опасных по внезапным выбросам угля или газа. В некоторых случаях возможно бурение опережающих скважин в угольных забоях подготовительных (в зависимости от паспорта бурения и габаритов) выработок и вспомогательных скважин диаметром 250 и 300 мм различного назначения (вентиляционных, водоспускных, разведочных и др.).
Встесненных забоях, где недостаточно места для размещения всего оборудования установки, ее можно применять для бурения скважин без дистанционного наращивания штанг.
Вкомплект оборудования установки «Старт» входят пульт дистанционного управления 1, гидропульт 2, буровой инструмент 3, распорные стойки 4 и 7, буровой станок 5, питатель для автоматической дистанционной зарядки буровых штанг 13, пускатель, оросительное устройство и портативная лебедка, установленная на раме станка и с приводом от патрона вращателя. Лебедка используется для перемещения станка по лаве. При необходимости оборудование комплектуют переносным шнековым перегружателем 8 с отдельным электроприводом. Перегружатель предназначен для транспортирования выбуренного угля на конвейер лавы. Машина может быть использована и без питателя 13 (при бурении вентиляционных, водоспускных, разведочных и других скважин).
Станок предназначен для сообщения буровому инструменту вращательного и возвратно-поступательного движения.
Буровой станок с электроприводом состоит из вращателя 10, который свободно подвешен к раме станка, и гидроцилиндра подачи 6, встроенного в раму станка. Стойки 4 и 7 предназначены для удержания рамы в рабочем положении. Стойки распираются между почвой и кровлей пласта. Вращатель состоит из электродвигателя 9 и планетарного редуктора 11, который через разъемный патрон 12 передает вращение буровому ставу.
Подача штанг в буровой станок в процессе бурения скважины производится автоматически питателем 13 магазинного типа, включающего десять штанг. Дозирующий механизм питателя приводится в действие от отдельного гидроцилиндра, который осуществляет возвратно-поступательное движение двух пар отсекателей. Последние при этом последовательно подают по одной штанге на ось бурения. Гидроцилиндр управляется дистанционно с помощью золотника на пульте управления 1. Пульт располагается на расстоянии не менее 20 м от места бурения. На нем находятся электроблок управления электрической частью станка 2 и привод гидросистемы станка с гидроаппаратурой (манометром, индикатором загрузки).
Перегружатель 8 представляет собой шнековый конвейер, состоящий из корпуса, задней опоры, транспортирующих шнеков, редуктора и электродвигателя.
279
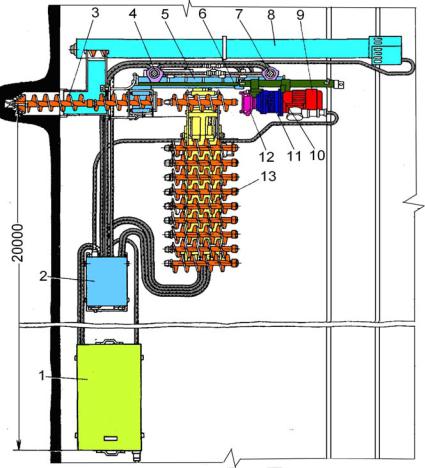
Ловитель штанг предназначен для их извлечения из скважины при аварии (поломке, развинчивании и т. п.). Ловитель представляет собой направляющую, которая соединяется со штангой с помощью конической замковой резьбы.
Лебедка используется для механизации транспортирования станка и пульта управления по лаве к месту бурения. Она устанавливается на направляющей раме станка и приводится во вращение от патрона вращателя.
Рис. 3.111. Буровая установка «Старт
280

Среди современной техники для бурения дегазационных глубоких и разведочных скважин выделяются станки и оборудование немецкой фирмы Deilmann-haniel mining system. Станки применяются главным образом для бурения дегазационных и разведочных скважин. Бурение скважин обеспечивается в условиях всех типов пород, на угольных пластах, а также в зонах обрушения или в зонах разрыхленных пород. В зависимости от назначения и параметров скважин имеются два базовых исполнения бурового станка – тяжелое (GBH) и легкое (PD300). Оба станка могут быть оснащены бурильной головкой как вращательного, так и ударно-вращательного бурения.
Буровой станок PD300 (рис. 3.112-3.113)с электрогидравлическим приводом предназначен для бурения дегазационных скважин. Станок имеет гидравлическую приводную головку вращательного действия, состоит из жесткого бурового лафета, изготовленного из призматических профилей. В положении бурения распор лафета осуществляется двумя механическими и двумя гидравлическими выдвижными опорами.
Система подачи выполнена в виде сдвоенного пакета гидроцилиндров. В передней части рамы лафета смонтировано гидравлическое направляющее устройство, служащее для центрирования и направления буровых штанг в процессе бурения и в качестве зажимного устройства для развинчивания буровых штанг, а так же для фиксирования (удерживания) в скважине колонны бурильных труб. Для последующего крепления скважины обсадными трубами зажимное устройство механически отводится в сторону. Управление станком осуществляется при помощи автономного пульта управления
По транспортабельности буровые станки PD300 могут быть передвижными или самоходными, у которых база станка размещается на самоходной гусеничной тележке (рис. 3.114).
Рис. 3.112. Буровой станок PD300 с гидроприводом вращательного действия
281

Рис. 3.113. Бурение дегазационной скважины буровым станком PD300 с гидравлическим перфоратором
Буровой дегазационный станок ти-
па GBH (рис. 3.115)
состоит из бурового лафета, на котором находятся направляющие салазки для перемещения вперед и назад. Система подачи состоит из трех, соединенных между собой гидроцилиндров с высокими усилиями подачи и возврата. В пе-
редней части с обеих сторон рамы смонтированы две гидравлические телескопические опоры для распора бурильного агрегата в положении бурения. Для выравнивания неровностей почвы в нижней части дополнительно установлено два механически регулируемых опорных элемента.
282
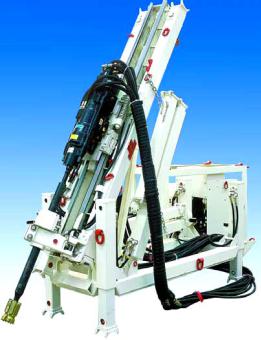
|
|
Зажимное |
устройст- |
|||
|
во для буровых штанг, рас- |
|||||
|
положенное по центру ра- |
|||||
|
мы, служит для наращива- |
|||||
|
ния и рассоединения ко- |
|||||
|
лонны |
буровых |
штанг. |
|||
|
Центрирование |
|
бурового |
|||
|
става |
в |
процессе |
бурения |
||
|
осуществляется |
роликовой |
||||
|
направляющей. Для закреп- |
|||||
|
ления и разъединения бу- |
|||||
|
ровых штанг |
используется |
||||
|
специальное |
гидравличе- |
||||
|
ское зажимное устройство. |
|||||
|
|
Вращение |
|
буровых |
||
|
штанг |
осуществляется |
||||
|
мощным |
гидравлическим |
||||
|
ротационным |
|
приводом. |
|||
|
Для оптимального согласо- |
|||||
|
вания |
с |
индивидуальными |
|||
|
задачами |
бурения |
ротаци- |
|||
|
онные приводы оснащают- |
|||||
Рис. 3.115. Внешний вид бурового станка GBH |
ся различными устройства- |
|||||
|
ми |
регулирования вра- |
щающего момента и числа оборотов. Ротационный привод позволяет использовать погружные перфораторы для специального применения. Для кернового бурения применяются ротационные приводы с проходными штангами и гидравлическими зажимными колодками. Для управления и контроля буровых работ служит пульт управления, установленный на гидроагрегате, который можно использовать в качестве переносного пульта непосредственно на месте бурения. Обычно гидроагрегат монтируется на транспортной раме и оборудован необходимыми приводными узлами, элементами снабжения и контроля. При работе с ударно-вращательной бурильной головкой предусмотрена функция режима забуривания и автоматическое включение/выключение ударного механизма. При работе с вращательной бурильной головкой управление предусматривает автоматическое регулирование подачи в зависимости от нагрузки сопротивления.
В последние годы на шахтах Донбасса успешно используется буровая установка фирмы «Флетчер» (3.116).
Новая американская технология по подземному бурению направленных дегазационных скважин большой протяженности (до 1 км) позволяет дегазировать очистные забои при отработке лав обратным ходом.
283
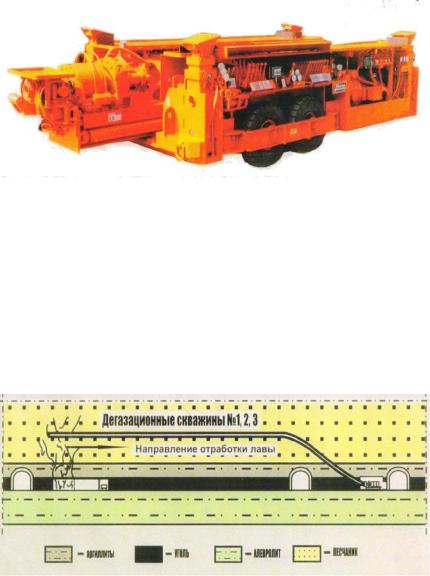
Рис. 3.116. Буровая установка фирмы «Флетчер» для бурения дегазационных скважин
Все элементы буровой установки размещены на низкоседящей колесной платформе. Для закрепления установки в положении бурения она снабжена четырьмя выдвижными гидравлическими стойками.
Оснастка станка измерительной аппаратурой и программным обеспечением для постоянного контроля и обработки данных позволяет отслеживать и изменять место нахождения забоя скважины в любой момент времени.
На рис. 3.117. приведен пример трасс скважин 1, 2 и 3 пробуренных установкой в кровле угольного пласта одной из шахт Донбасса.
Рис. 3.117. Схема бурения наклонно-горизонтальных скважин установкой фирмы «Флетчер»
284
3.7. Бурение стволов и восстающих горных выработок
Буровая технология сооружения шахтных стволов характеризуется тем, что без присутствия людей в забое выполняются основные технологические процессы: разрушение породы, выдача ее из забоя и возведение крепи. Отсутствие буровзрывных работ повышает уровень безопасности и снижает экологическую напряженность в районе строительства ствола. Перспективность способа дополняется возможностью проходки стволов практически в любых горно- и гидрогеологических условиях (в мягких, обводненных, неустойчивых породах), где альтернативные способы невозможны без применения специальных дорогостоящих технологий (предварительное замораживание, тампонирование пород).
К основным технологическим этапам бурения шахтных стволов от-
носятся:
1.Разбивка оси ствола, подвод электроэнергии, технической воды, подготовка и разработка промплощадки. Для бурения стволов необходима горизонтальная площадка примерно 1,5 га, имеющая дорогу с твердым покрытием. На этой площадке устраиваются отстойники для промывочной жидкости; до глубины 5-10 м проходится устье выработки; сооружаются фундаменты для технологического оборудования и выполняется строительство производственных и бытовых помещений.
2.Транспортирование и монтаж бурового оборудования.
3.Собственно бурение. Этот процесс слагается из выполняемых одновременно стадий разрушения породного массива, уборки с забоя и выдачи на поверхность разрушенной породы, очистки буровой жидкости от выбуренной породы, а также временного крепления.
4.Возведение крепи. Этот процесс слагается из последовательно выполняемых стадий замены глинистого раствора на воду, монтажа крепи, ее спуск, стыкование секций и тампонажа затрубного пространства. С точки зрения затрат времени сюда относится также стадия затвердевания тампонажной смеси.
5.Осушение (откачка буровой жидкости). В процессе откачки жидкости проверяется качество крепи ствола, устраняются выявленные дефекты крепления и при необходимости выполняется контрольный тампонаж затрубного пространства.
6.Сбойка ствола с горизонтальной выработкой.
7.Демонтаж бурового оборудования.
8.Монтаж постоянного копра, армировка ствола и его оборудование по функциональному назначению (установка вентилятора, средств подъема
ит.п.)
Технологические схемы выполнения процессов собственно бурения и возведения крепи определяют в основном конструкцию буровой установки.
285

Для бурения стволов используются установки, предназначенные для бурения нефтяных и газовых скважин, а также специальные установки для бурения шахтных стволов.
Технологические схемы бурения и буровые установки принципиально различаются приводом (способом передачи энергии к исполнительному органу), расположением привода, видом используемой энергии, способом выдачи разрушенной породы, увязкой процессов бурения и возведения крепи. Наиболее существенным отличительным признаком является вид привода установки. В соответствии с этим критерием различают установки с роторным приводом и установки с забойнымБурениеприводомстволов. установками с роторным приводом. Принцип ро-
торного бурения состоит в том, что вращение исполнительного органа (долота) осуществляется через колонну бурильных труб от ротора, установленного на поверхности. По мере проходки бурильные трубы наращиваются с поверхности. При вращении исполнительного органа порода на забое измельчается и в последствии удаляется благодаря циркуляции промывочной жидкости. По этому принципу работают установки L-35 фирмы WIRT.
При бурении по роторной схеме установками L-35 функционируют четыре основные системы: система разрушения породы (бур), система привода исполнительного органа, грузоподъемная система и система удаление разрушенной породы на поверхность.
Система разрушения породы (бур) (рис. 3.118) включает долото,
утяжелитель, переводник, стабилизатор или стабилизатор-калибратор ствола. На долоте, в зависимости от диаметра бурения, располагается от 24 до 31 шарошек. Шарошки устанавливаются в кронштейнах шарошкодержателей, выполненных на стальном корпусе долота бура и крепятся к стойкам кронштейна болтами.
В качестве утяжелителей используются заполненные свинцом цилиндрические металлоконструкции. Масса каждого утяжелителя составляет 20-25 т. Для создания необходимого контактного давления зубьев шарошки на породу над долотом размещается несколько утяжелителей, которые болтами соединяются как между собой, так и с долотом и переводником. Как правило, вес утяжелителей подбирается таким образом, чтобы в процессе эффективного разрушения породы бурильные трубы находились в растянутом состоянии, что обеспечивает постоянную вертикальную стабилизацию бура в стволе и повышает вероятность сохранения вертикальности траектории ствола на полную глубину бурения.
Переводник в верхней части имеет патрубок с фланцевым узлом, служащим для соединения с бурильными трубами, и одновременно являющимся опорным узлом для раскрывающегося захватного устройства гидроэлеватора, при выполнении операций спуска и подъема бура.
286
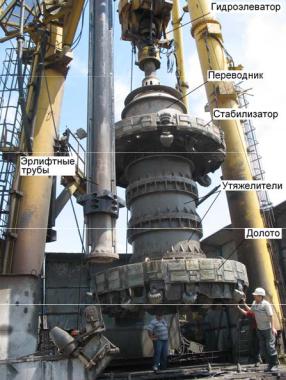
Как правило, сверху и снизу утяжелителей устанавливаются стабилизаторы, уменьшающие колебание колонны.
Система при-
вода состоит из ротора, ведущей трубы и колонны бурильных труб.
Ротор предназначен для передачи вращения от электродвигателя бурильной колонне через специальные захватывающие вкладыши и ведущую трубу. В установке L-35 ротор смонтирован на неподвижной раме и в процессе подготовки к бурению он с по-
мощью крана уста- Рис. 3.118. Бур установки L-35 навливается на раз-
движные платформы
на устье ствола.
Ведущая труба соединяется болтовым соединением с бурильными трубами и сальником вертлюгом, служащим для отвода промывочной жидкости из забоя скважины в отстойник.
Колонна бурильных труб состоит из отдельных бурильных труб длиной 6 и 12 м с внутренним диаметром 300 мм. Тип соединения труб – фланцевое с помощью болтов М42. По наружной поверхности эрлифтных труб расположены воздухоподающие трубки. Для создания герметичности между фланцами бурильных труб устанавливается резиновая прокладка. Для свинчивания и развинчивания болтов фланцевого соединения используются гайковерты, которые работают от вспомогательного компрессора, входящего в комплект буровой установки.
Грузоподъемная система (рис. 3.119) состоит из буровой вышки; буровой лебедки; талевой системы, включающей кронблок, гидроэлеватор и талевый канат. В процессе монтажа и демонтажа, при отделении от талевой системы, бур и бурильная колонна опираются на раздвижную платформу.
287

Для подъема и установки на платформу ротора, перемещения к устью элементов бура, переводника и бурильных труб применяется грузовой кран КАТО. Для выполнения дополнительных погрузочно-разгрузочных работ используется колонный кран КПБ-3М.
Рис. 3.119. Внешний вид оборудования грузоподъемной системы установки L-35
Система выноса породы (пульпы) включает систему циркуляции раствора по бурильным трубам и затрубному пространству, систему очистки раствора, буровые насосы (компрессоры) и обвязку насосов.
При бурении ствол заполняется буровым раствором, создающим гидростатическое давление на стенки выработки, и выполняющим тем самым функции временной крепи. Жидкость в системе циркуляции по бурильным трубам и затрубному пространству используется для гидротранспортировки разрушенной породы на поверхность. На поверхности пульпа очищается от породы в отстойниках или сито-гидроциклонных устройствах.
288
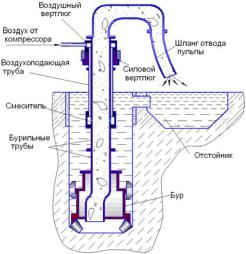
При работе с установкой L-35 удаление разрушенной породы выполнено при циркуляции жидкости по обратной схеме: жидкость перемещается по стволу, а пульпа поднимается по трубам с помощью эрлифта (рис. 3.120).
|
Для осуществления об- |
||
|
ратной циркуляции эрлифтом в |
||
|
бурильную колонну |
компрес- |
|
|
сором через воздухоподающие |
||
|
трубки эрлифтной |
колонны |
|
|
подается сжатый воздух, кото- |
||
|
рый выше зоны смесителя, за- |
||
|
глубленного под уровень жид- |
||
|
кости на 70-100 м, аэрирует |
||
|
жидкость в бурильной колон- |
||
|
не. За счет разности плотно- |
||
|
стей жидкости |
в |
затрубном |
|
пространстве и |
аэрированной |
|
|
смеси внутри колонны жид- |
||
|
кость перетекает из затрубного |
||
|
пространства в трубы и далее в |
||
|
смеси с воздухом через пуль- |
||
Рис. 3.120. Схема удаления разрушенной поро- |
поотводящий шланг попадает в |
||
ды из скважины при работе с установкой L-35 |
отстойник, откуда через канал |
||
|
возвращается в ствол. |
Производительность циркуляционной системы для эффективной работы эрлифта и охлаждения инструмента задается в пределах 900-1200 м3/ч.
Работы по возведению крепи (рис. 3.121). Устье ствола закрепляется бетоном и сталебетоном. Выполнение этого этапа крепления ствола обусловлено необходимостью защиты породных стенок от размыва буровой жидкостью, соединения ствола с желобной системой, задания направления стволу, размещения исполнительного органа в период забуривания. Устье ствола также является основанием для подроторной рамы, на которой удерживается исполнительный орган и колонна бурильных труб при бурении, а также секции обсадных труб во время спуска крепи в ствол.
Бетонная крепь в устье возводится при помощи деревянной или раздвижной металлической опалубки. При проходке устьев стволов крепь представляет собой обсадную металлическую трубу, опущенную на забой в буровую жидкость. Зазор между стенками трубы и породы тампонируется цементно-песчаным раствором с добавлением щебня и камня. Глубина устьев составляет 10-30 м в зависимости от прочности грунта.
Для закрепления и изоляции неустойчивых пород, перекрытия зон поглощения и водонапорных горизонтов спускают кондуктор. В зависимости от горно-геологических условий разреза его обычно опускают на глуби-
289
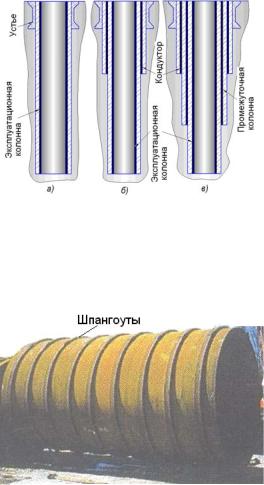
ну 30-100 м и тампонируют цементно-песчаным раствором до устья.
При бурении в сложных горно-геологических условиях глубоких стволов часто возникает необходимость возведения крепи на одном, или нескольких интервалах промежуточными колоннами, которые тампонируются до устья, на 10-15 м выше отметки низа кондуктора или на всю длину колонны.
Эксплуатационная колонна обсадных труб опускается до проектной глубины, и перекрывает ствол до устья или выше отметки низа предыдущей колонны на 10-15 м.
Наиболее рациональной является одноколонная конструкция (рис.
|
3.121, а). |
|
|
|
Однако |
часто встре- |
|
|
чаются конструкции ство- |
||
|
лов, в состав которых вхо- |
||
|
дят дополнительные участ- |
||
|
ки возведения крепи в виде |
||
|
кондуктора (рис. 3.121, б), |
||
|
или кондуктора и проме- |
||
|
жуточной колонны, кото- |
||
|
рую можно крепить на всю |
||
|
глубину (рис. 3.121, в). |
||
|
В |
отечественной |
|
|
практике |
для |
крепления |
Рис. 3.121. Конструкции стволов, проходимых |
стволов, |
пройденных буре- |
|
способом бурения |
нием |
преимущественно |
|
|
применяется крепь в виде |
||
металлического цилиндра из листовой стали |
толщиной 12-20 мм высотой |
||
1,5-2,6 м. |
|
|
|
Листы для изготовления обсадной трубы изгибаются на листогибочной машине с получением определенного диаметра. Как правило, перед на-
|
чалом |
формирования ци- |
|
|
линдра на будущей наруж- |
||
|
ной |
поверхности |
листов |
|
привариваются шпангоуты |
||
|
в виде полосы металла тол- |
||
|
щиной 20 мм или швеллера |
||
|
№№ 12-20 (рис. 3.122). |
||
|
|
Изогнутые |
листы |
|
свариваются между |
собой |
|
|
вдоль |
образующей |
полу- |
|
ченного цилиндра обсадной |
||
Рис.3.122. Обсадная труба со шпангоутами из |
трубы. |
|
|
швеллера |
|
|
|
290 |
|
|
|
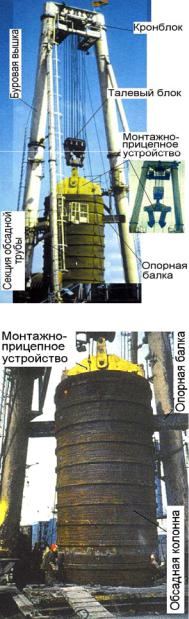
Рис. 3.123. Спуск секции обсадной колонны
Рис. 3.124. Сваривание секций крепи
гнетается воздух (рис. 3.121, а).
Взависимости от диаметра и веса крепи, глубины ствола крепь возводится погружным или секционным способом.
При погружном способе крепь собирается (свариваются отдельные секции крепи) на поверхности и опускается в ствол на полную глубину.
Вобсадных трубах, предназначенных для спуска в ствол, вырезаются окна для монтажных балок и монтажного прицепного устройства, устанавливаются контрольные пробки. При сборке секции обсадные трубы краном подают на приемный мост к устью ствола. В верхние окна заводят крюки монтажного прицепного устройства. При помощи талевой системы труба опускается в устье ствола до посадки на опорные балки. Затем производится спуск монтажного прицепного устройства, его освобождение от первой трубы и присоединение ко второй трубе (рис. 3.123). Поднимается вторая труба и устанавливается на верхний торец первой трубы. Стыки труб свариваются (рис. 3.124). Сваренные трубы поднимают на 0,5 м и выводят монтажную балку из окон нижней трубы. Окна заваривают заглушками. Трубы опускают до устья,
ипоследующее их наращивание производится аналогично.
Вслучае, когда вес колонны труб превышает грузоподъемность буровой установки, может быть применен способ спуска на воздушной подушке или на плаву (рис. 3.125).
При спуске колонны на плаву к верхней части колонны приваривается труба с цементным мостом, содержащим клапан. Под цементный мост на-
По мере погружения колонны под мост
291
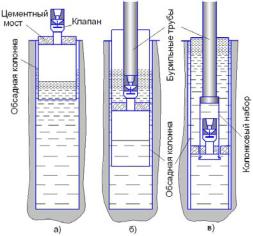
подкачивается воздух через спущенные и соединенные с клапанным устройством трубы (рис. 3.121, б), которые поднимают на поверхность после понижения веса на крюке до заданной величины. После спуска колонны через трубы, из воздушной подушки выпускают воздух с одновременным доливом жидкости в скважину. Трубы поднимают, подсоединяют колонковый набор, которым обуривают и извлекают клапанное устройство (рис. 3.121, в).
Сущность секционного способа возведения крепи состоит в том, что крепь опускают в ствол, заполненный осветленной жидко-
стью, отдельными сварными секциями длиной 40-100 м.
Нижнюю секцию крепи устанавливают на забой ствола, удерживая на прицепном устройстве. Затрубное пространство тампонируется цементнопесчаным раствором на 2/3 высоты секции. Затем прицепное устройство отделяется, поднимается на поверхность, собирается следующая секция и опускается в ствол до соприкосновения с предыдущей, соединяется с ней при помощи стыкующего устройства. Затрубное пространство тампонируется таким образом, чтобы цементное кольцо находилось на отметке, считая от которой не затампонированный отрезок второй секции составит 1/3 ее высоты. Операция повторяется до тех пор, пока крепь не выйдет в устье ствола.
Установки с забойным приводом. Технической основой установок является забойный агрегат реактивно-турбинного бурения (РТБ). В Украине для сооружения стволов способом РТБ наибольшее распространение получила установка «Уралмаш 4Э-76», поверхностный комплекс которой в общих чертах подобен серийной роторной установке для бурения нефтяных и газовых скважин, и состоит из тех же основных элементов (рис. 3.126). Главное их различие заключается в принципе действия и схеме привода исполнительного органа, который находится в буре, что исключает передачу силовых нагрузок, прежде всего, крутящего момента через ротор и бурильную колонну.
292
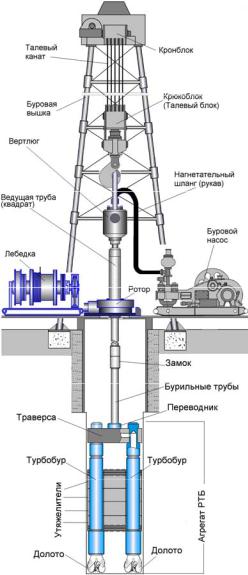
Агрегат РТБ представляет собой жесткую конструкцию, в которой соединены два или четыре турбобура. Агрегат посредством переводника соединяется с колонной бурильных труб. Противоположным концом переводник соединен с траверсой, которая является также элементом подачи жидкости к гидродвигателям, в качестве которых используются турбобуры. Из траверсы промывочная жидкость поступает в турбобуры и приводит во вращение их валы. Вместе с валами турбобура вращаются навинченные на них долота.
Промывочная жидкость, пройдя через турбобуры, омывает забой вблизи долот и по затрубному пространству поднимается на поверхность, вынося частицы разбуренной породы, т.е. в скважине имеет место прямая циркуляция жидкости.
В агрегатах РТБ долота осуществляют сложное движение. Вместе с валом турбобура они вращаются по часовой стрелке вокруг собственной вертикальной оси и одновременно, за счет возникающего на корпусе турбобура реактивного момента, долота вместе с агрегатом вращаются против часовой стрелки вокруг вертикальной оси ствола. Как правило, если величина
реактивного момента недостаточна, и для предотвращения непроизвольного развинчивания резьбовых соединений бурильной колонны, агрегату сооб-
293
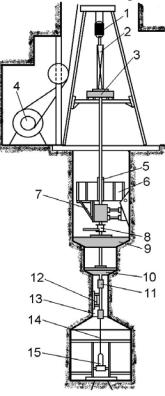
щается вращение ротором по часовой стрелке.
Закрепление стенок ствола выполняется аналогично проходки стволов установками L-35 с использованием таких же труб и способов спуска обсадных колонн (погружным или секционным способом).
Проходка стволов из подземной выработки выполняется по двум технологическим схемам: бурение сверху вниз со спуском основной массы разбуриваемой породы на нижележащий горизонт шахты; бурение снизу вверх со спуском породы в шахту (способ «рейз-боринг»).
При бурении по схеме сверху вниз (рис. 3.127) вначале по центру будущего ствола бурят пилот-скважину 13 относительно небольшого диаметра (300-500 мм). Затем ее расширяют до заданного диаметра в одну или несколько фаз, используя для этого расширитель со ступенями 10 и 9. Разбу-
|
риваемая |
порода ссыпается через |
|||
|
скважину в шахту, где загружается в |
||||
|
вагонетки, откатывается к стволу и |
||||
|
выдается на поверхность. |
|
|||
|
Вращение буровому инстру- |
||||
|
менту сообщается ротором 3 через |
||||
|
ведущую трубу 2 с верхнего гори- |
||||
|
зонта. При бурении по такой схеме |
||||
|
осевое усилие на расширитель пере- |
||||
|
дается через натяжной вертлюг 11 и |
||||
|
создается главным образом в ре- |
||||
|
зультате натяжения цепи 14 тяговым |
||||
|
устройством 15, расположенным на |
||||
|
нижележащем горизонте. Центрация |
||||
|
бура относительно проектной |
оси |
|||
|
ствола обеспечивается двумя на- |
||||
|
правляющими устройствами 7 и 12. |
||||
|
Поступление воды на поверхности |
||||
|
расширителя |
обеспечивается |
про- |
||
|
мывочным фланцем 8. |
Спуск |
(из- |
||
|
влечение) |
бурового |
инструмента |
||
|
производится |
с помощью талевого |
|||
|
каната лебедки 4, соединяющегося |
||||
|
через вертлюг 1 (крюкоблок) с бу- |
||||
|
рильной колонной. |
|
|
||
|
Отличительным |
признаком |
|||
Рис. 3.127. Схема бурения слепого |
этой схемы является также принци- |
||||
ствола «сверху вниз» со спуском раз- |
пиальная возможность параллельно |
||||
буриваемой породы на нижележа- |
с процессом |
бурения |
возведения |
||
щий горизонт шахты |
крепи с полка 6. В центральной час- |
||||
|
294 |
|
|
|
|
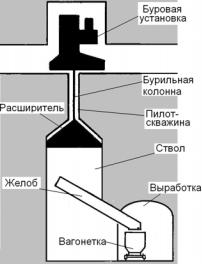
ти полка концентрично с бурильной колонной установлена ограждающая труба 5, исключающая, при крепежных работах, контакт рабочих с вращающимися бурильными трубами.
Схема роторного фазного бурения, с расширением пилотной скважины снизу вверх и спуском разрушенной породы в выработку нижележащего горизонта шахты (способ «рейз-боринг») показан на рис. 3.128. «Рейс-боринг» - верти-
кальное или направленное под углом более 700 вверх расширение предварительно пробуренной пилотскважины. Пилот скважина бурится для обеспечения возможности соединения бура-расширителя с колонной бурильных труб и спуска разбуриваемой породы непосредственно в вагонетки или на почву вы-
работки нижнего горизонта с последующей уборкой породы. Проектное сечение ствола достигается бурением в несколько фаз с использованием расширителей разного диаметра. Расширитель, приводимый во вращение посредством бурильных труб и ротора, кроме того, при помощи гидродомкратов подтягивается вверх.
Ограничивающим условием использования способа является достаточная устойчивость пород, при которой не было бы необходимости крепления стенок скважины в период ее расширения.
Обычно такой способ бурения производится из горных выработок для спуска горной породы, материалов, оборудования с верхних горизонтов шахты на нижележащие, а также для последующего размещения в них буров стволопроходческих комбайнов.
Бурение скважин и восстающих выработок. В угольной промыш-
ленности при отработке продуктивных пластов, когда требуется проведение большого числа сбоек, предназначенных для нарезки лав, спуска воды, вентиляции, дегазации пластов и проходке углеспускных печей широко используются буросбоечные машины. В рудной промышленности для выбуривания вертикальных, или близких к вертикальным, восстающих выработок - гезенков, предназначенных для вентиляции, спуска руды, породы, воды применяют гезенко-бурильные машины.
295
В целом буросбоечные и гезенко-бурильные машины обеспечивают проведение вертикальных и наклонных скважин большого диаметра (до 1,5 м) длиной до 150 м.
Для бурения в слабых породах скважин диаметром 250-390 мм с разбуриванием их до 450-850 мм достаточно часто используется буросбоечная машина СБМ-3У (рис. 3.129-3.130). На машине применен вращательноподающий механизм дифференциально-винтового типа, смонтированный в редукторе и работающий от электродвигателя.
Редуктор поворачивается в вертикальной плоскости от 0 до 900 с помощью червячной пары с ручным приводом. Электродвигатель и редуктор установлены на раме станка, которая может перемещаться по рельсовой колее на полускатах.
Шпиндель станка заканчивается буровым замком, который перемещается по направляющим параллелям, центрирующим его движение. В верхней части расположена рама с подхватом, которым поддерживается буровой инструмент во время наращивания или сокращения его длины.
Машина доставляется к месту работы на тележке, с которой может сниматься на время бурения, и раскрепляться в выработке распорными стойками.
Рабочий инструмент состоит из забурника, расширителей (прямого и обратного хода), опорных фонарей и буровых штанг, которые для бурения под небольшим углом наклона (до 450) выполняются со шнеками, способствующими удалению разбуренной породы (шлама). Для сбора шлама устанавливают уловитель. Буровые штанги длиной по 0,6 м имеют соединительную конусную резьбу и крепятся в буровом замке. По мере углубления скважины на длину штанги последнюю поддерживают с помощью подхвата, а буровой замок спускают до отказа вниз. После подстановки очередной штанги подхват убирается, и продолжается бурение. Через каждые 6-8 штанг устанавливается одна штанга с опорным фонарем, предотвращающим искривление бурильной колонны в скважине. Опорный фонарь скользит вдоль скважины, опорными лапами удерживаясь на штанге, которая вращается в нем.
Забурник выполняется в виде спирали диаметром около 110 мм. Под забурником размещается расширитель. Забурник выбуривает передовую скважину, которая помогает сохранять заданное направление и облегчает дальнейшее разрушение забоя, а режущие кольца расширителя прорезают в забое концентрические щели. Целички, остающиеся между щелями, разрушаются роликовыми скалывателями.
С помощью редуктора и дифференциально-винтовой подачи шпинделю станка обеспечивается вращение и подача снизу вверх или сверху вниз (соответственно при бурении и расширении скважин), вращение без подачи и маневровая подача вверх и вниз без вращения шпинделя.
296
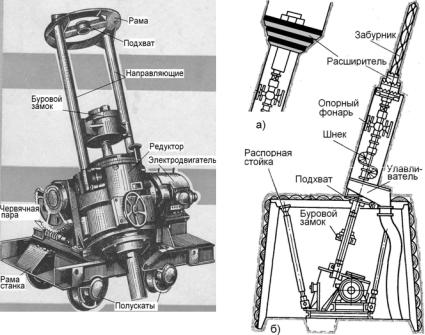
Рис. 3.129. Буросбоечная машина |
Рис. 3.130. Размещение СБМ-3У в |
СБМ-3У |
выработке |
Для проведения восстающих выработок под углом наклона 40—90°, круглого сечения (скважин), диаметром 1 м и длиной до 100 м широко используется буровая установка «Стрела 77» (рис. 3.131), которая может работать по породам с коэффициентом крепости до 10 на шахтах любой категории по газу.
Пройденные выработки могут быть использованы в качестве скатов, гезенков для спуска угля и породы, перемещения людей, доставки материалов, вентиляции и других целей. Машина изготовляется с пневмоили электроприводом; управляется она дистанционно с расстояния до 20 м от места проведения выработки. Она также обеспечивает бурение направляющей пи- лот-скважины диаметром 190 мм, с последующим ее разбуриванием до 1 м.
Машина состоит из бурового снаряда-вращателя, невращающегося бурового става, механизма подачи, механизма поворота, маслостанции, пневмоили электроаппаратуры, тележки, оросительной системы.
Снаряд-вращатель предназначен для разрушения породы; он состоит из пневмомотора или электродвигателя, передающего крутящий момент исполнительному органу через плоский планетарный редуктор. Исполнитель-
297
ный орган выполнен в виде водила с тремя долотами, на каждом из которых закреплено по три шарошки со съемными зубчатыми венцами.
По оси исполнительного органа расположено еще одно долото с тремя шарошками для разрушения породы в центральной части забоя при проведении пилот-скважины диаметром 190 мм.
Невращающийся буровой став подачи, состоит из штанг длиной по 600 мм, переходника и долота; на каждой пятой штанге смонтированы направляющие фонари. Бурильная колонна (буровой став) предназначена для перемещения снаряда-вращателя на длину проводимой выработки и для передачи на нее осевых усилий от механизма подачи.
Механизм подачи предназначен для установки буровой машины со снарядом-вращателем на требуемый угол наклона проводимой выработки и для подачи на забой снаряда-вращателя через буровой став. Базовой конструкцией механизма подачи является жесткая направляющая рама, на которой смонтированы все узлы механизма подачи. Внутри рамы установлен в начальном положении снаряд-вращатель. В направляющих рамы передвигается каретка при помощи двух гидродомкратов.
Своей нижней частью рама опирается посредством роликов на секционный монорельс с башмаками, уложенными на почве выработки. Под рамой расположены два установочных гидродомкрата, которыми машина устанавливается под определенным углом наклона. Двумя верхними гидродомкратами рама неподвижно распирается в выработке.
Механизм поворота расположен в задней части каретки, он имеет гидроцилиндр, который удерживает став подачи от вращения, и воспринимает реактивный крутящий момент при работе исполнительного органа. Кроме того, механизм поворота используется для регулировки при постановке и съеме буровых штанг. Став подачи и снаряд-вращатель при наращивании и съеме буровых штанг, удерживаются гидравлическим зажином, расположенным в верхней части рамы.
Маслостанция предназначена для питании гидроцилиндров подачи, поворота, захвата става, подачи и распора. На ней установлен также регулятор нагрузки для автоматизированного управления проведением выработки. Маслостанция выполнена в виде отдельного блока и соединена с механизмом подачи гибкими высоконапорными рукавами.
Установка с электроприводом дополнительно комплектуется станцией управления, аппаратурой контроля воздуха, аппаратурой контроля метана, индивидуальным устройством предупредительной сигнализации и пусковым агрегатом.
Оросительная система предусматривает подачу воды под давлением от насосной установки в штреке через фильтр по гибкому рукаву в выработку для охлаждения электродвигателя и к форсункам подавления пыли.
298
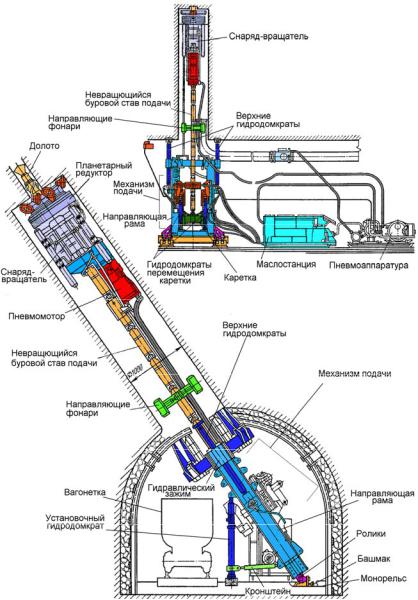
Рис. 3.131. Конструкция буровой установки «Стрела -77»
299
Для проветривания проводимой выработки к буровому ставу на первом фонаре, крепится вентиляционный став, к третьему фонарю - датчик содержания метана.
Бурильная машина устанавливается в выработке или в нише под заданным углом наклона, надежно закрепляется распорными домкратами и опробывается вхолостую.
Забуривание производят с устья скважины на глубину до 1 м с минимальной нагрузкой во избежание искривления скважины. Далее ведут бурение обычным способом на длину направляющей трубы, которую затем закрепляют в устье скважины. Режим бурения характеризуется осевой нагрузкой на инструмент, частотой его вращения, а при бурении с промывкой — количеством подаваемой воды. По мере углубления скважины можно увеличивать скорость подачи и осевое усилие, выбирая при этом оптимальный режим бурения, не допуская перегрузки двигателя станка и заштыбовки бурового инструмента. Заштыбовка ликвидируется вращением инструмента с подачей вверх-вниз.
При бурении угольный штыб из скважины отводится по направляющему лотку в вагонетку. К устью скважины подводятся форсунки для создания водо-воздушной завесы и пылеподавления.
Бурение и разбуривание скважин ведутся участками на длину одной штанги. Затем машину останавливают и наращивают очередную штангу. Буровой инструмент отсоединяют от шпинделя и удерживают в скважине с помощью подхвата, имеющегося на машине. Шпиндель опускают вниз и в промежуток между ним и последней штангой, находящейся в скважине, вставляют очередную штангу.
300
4 ГОРНО-БУРОВАЯ ТЕХНОЛОГИЧЕСКАЯ СИСТЕМА
Горная система в чистом виде применяется крайне редко и в процессе освоения месторождений горное производство предполагает, прежде всего, последовательное или совмещенное использование горной и буровой технологических систем. Обе системы или элементы этих систем всегда присутствуют при проходке как эксплуатационных, так и горно-разведочных выработок. Например, подготовительным этапом для добычи угля из тонких пластов бурошнековой установкой является необходимость выполнения всего комплекса проходческих работ для подготовки участка к размещению и эксплуатации БШУ. При проходке шурфов, стволов, подготовительных и нарезных выработок, имеют место способы, основанные на разрушении массивов горных пород агрегатами с буровым исполнительным органом (проходческие комбайны типа ПК, стволовые проходческие комбайны, буросбоечные машины, шурфопроходческие установки, агрегаты для бурения стволов и др.). Принципиальным, с точки зрения реализации такой системы,
является комбинированный способ проходки стволов, когда неустойчивый интервал мягких пород проходится бурением, а дальнейшая углубка выработки выполняется традиционным буровзрывным способом.
Комбинированный способ проходки шахтных стволов заключается в пространственном и временном совмещении двух технологий – бурения и буровзрывных работ. Ствол от нулевой отметки и до глубины залегания неустойчивых мягких пород проходят буровой установкой (как правило, интервал бурения составляет 0-150…200 м), а дальше по крепким и относительно устойчивым породам применяется буровзрывной способ. Пробуренная верхняя часть ствола крепится сталебетонной крепью. Параллельно с сооружением первых 150…200 м ствола, строится поверхностный комплекс по принятой постоянной схеме производства.
Технологическая схема выполнения процессов бурения и возведения крепи полностью соответствует рассмотренной выше технологии сооружения шахтных стволов установками L-35. Отличие заключается в использовании, как правило, двухфазного способа бурения заданного интервала ствола. Учитывая относительно большой диаметр ствола (6…7 м), предварительным этапом производства является бурение пилот-скважины диаметром 1.2…1,4 м с последующим расширением ее до проектного сечения ствола на глубину 150…200 м специальным буром-расширителем. В дальнейшем на этом интервале ствола секционным способом возводится крепь в виде стальных труб с тампонажем затрубного пространства песчаноцементным раствором (рис. 4.1).
Проходка обводненных неустойчивых пород на глубину до 40 м и более может быть осуществлена путем погружения сплошной стальной оболочки, нижний торец которой оснащен шарошками (рис. 4.2). Сформиро-
301
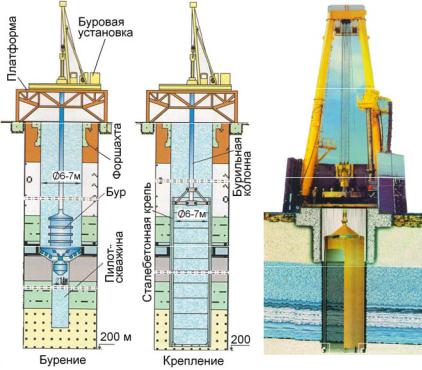
ванная внутри оболочки горная масса, в последствии удаляется на поверхность, а затрубное пространство тампонируется песчано-цементной смесью.
Рис. 4.1. Этап бурения при сооружении ствола |
Рис. 4.2. Проходка ствола в |
комбинированным способом |
неустойчивых обводненных |
|
породах |
До начала строительства ствола буровзрывным способом параллельно с бурением на промышленной площадке проводится большой объем строительно-монтажных работ от планировки до сооружения объектов и монтажа оборудования. Как правило, используются мобильные комплексы передвижных или перевозимых инвентарных блоков, оборудования, сооружений и фундаментов заводского изготовления: передвижное проходческое оборудование (подъемно-транспортное, энергетическое и т.п.); крупноблочные технологические металлоконструкции для проходки ствола (копры, проходческие полки, бункера, подшкивные площадки, разгрузочные станки); инвентарные сооружения производственного, подсобновспомогательного и административно-бытового назначения (в передвижносном, контейнерном и сборно-разборном исполнении) (рис. 4.3).
302

Рис. 4.3. Инвентарные блоки при |
Рис. 4.4. Этап БВР при сооружении |
подготовке стволов к проходке |
ствола комбинированным способом |
После выполнения подготовительных строительно-монтажных работ и размещения проходческого оборудования в стволе, на глубине перехода к буровзрывному способу сооружается бетонный опорный венец (башмак) (рис. 4.4). В дальнейшем, в соответствии с выбранной технологической схемой выполняются работы проходческого цикла до проектной глубины ствола с использованием традиционной горной технологической системы.
Горно-буровая технологическая система широко известна как составляющая геологоразведочных систем. В комбинированной горно-буровой системе разведки удельный вес и значение скважин, пробуренных из под-
303
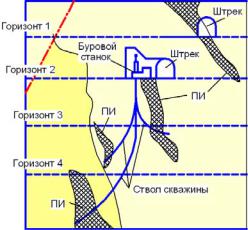
земных горных выработок, становится особенно существенным при построении рациональной разведочной сети. Наиболее эффективно такая система проявляется на стадии эксплуатационной разведки, когда решаются задачи уточнения деталей геологического строения, поиска «потерянных» рудных тел, повышения сте-
|
пени разведанности отдель- |
|||
|
ных горизонтов и выявления |
|||
|
новых запасов для продления |
|||
|
срока существования рудни- |
|||
|
ка. В целом, замена проходки |
|||
|
части горных выработок глу- |
|||
|
бокими |
горизонтальными, |
||
|
наклонными |
или вертикаль- |
||
|
ными скважинами дает боль- |
|||
|
шую экономию предприятию, |
|||
|
сокращает сроки разведки. |
|||
|
Этап |
|
детальной |
раз- |
|
ведки сложных рудных |
ме- |
||
|
сторождений |
наиболее |
эф- |
|
|
фективно выполняется с по- |
|||
Рис. 4.5. Схема разведки месторождения с |
мощью комплекса горных и |
|||
горно-разведочными выработками и бурени- |
буровых работ. Как правило, |
|||
ем и направленных скважин на нижние |
разведка верхней части ме- |
|||
горизонты рудника |
сторождения |
выполняется |
двумятремя и более горизонтами горных выработок (в гористой местности - штольнями), пройденными через 20-60 м. Для сгуще-
ния разведочной сети между горизонтами могут быть пробурены восстающие и наклонные скважины, типы и глубина которых определяется задачами геологической информативности бурения (рис. 4.5).
Важным условием применения горно-буровой системы является также снижение удельных затрат на прирост запасов руды в сопоставлении стоимостей проходки горно-разведочных выработок или бурения скважин с поверхности (с учетом затрат на строительство и содержание дорог, площадок для буровых, водопроводов и др.).
304
Вопросы и темы модульного контроля знаний. Литература для самоподготовки.
I.Основные сведения о скважинах
1.Определения: «Бурение скважин», «Буровая скважина». Типы и схемы расположения скважин.
2.Элементы и параметры скважин.
3.Общие сведения о конструкции скважины.
II.Общие сведения о бурении нефтяных и газовых скважин
1.Особенности выбора конструкции нефтяной и газовой скважины. Назначение обсадных колонн. Методика определения диаметра обсадной колонны и размеров долота под обсадную колонну.
2.Требования к интервалам цементирования обсадных колонн.
3.Способы бурения скважин.
III. Буровые установки. Оборудование и инструмент для бурения скважин
1.Структурные элементы буровой установки.
2.Буровая вышка – назначение и основные параметры.
3.Состав и назначение оборудования для выполнения спускоподъемных операций.
4.Назначение и устройство вертлюга-сальника.
5.Назначение и устройство ротора.
6.Назначение, основные элементы и принцип работы буровых насосов. Подача буровых плунжерных и поршневых буровых насосов.
7.Назначение и структурная схема силового привода установок.
8.Оборудование для захвата и удержания на весу бурильной колонны и обсадных труб.
9.Назначение и основные элементы автоматического бурового ключа АКБ-3М.
10.Назначение и технология использования машинных буровых ключей.
11.Монтаж, устройство и принцип работы гидроключей ГКШ.
12.Основные элементы бурильной колонны. Назначение и основные параметры ведущих, утяжеленных и бурильных труб.
13.Назначение, типы и маркировка переходников в составе бурильной колонны.
14.Перечень и назначение опорно-центрирующих элементов колонны бурильных труб.
15.Назначение и типы основного породоразрушающего инструмента.
16.Конструктивные особенности и область применения лопастных долот.
17.Шарошечные долота. Типы и область применения. Конструктивные особенности 3-х шарошечного долота.
305
IV. Промывка скважины и очистка отработанного в скважине бурового раствора
1.Назначение и схема промывки скважины.
2.Циркуляционная система буровой установки.
3.Типы и область применения очистных агентов.
V. Производственный цикл строительства скважины. Последовательный перечень и содержание рабочих процессов производственного цикла сооружения скважины
VI. Промысловое освоение углеводородных месторождений
1.Схема сбора и подготовки продукции скважин на нефтяном промысле.
2.Особенности сбора и подготовки газа на газовых промыслах.
VII. Особенности освоения морских углеводородных месторождений
1.Специфика выполнения буровых работ на морских акваториях.
2.Общая характеристика и область применения самоподъемных плавучих буровых установок.
3.Общая характеристика и область применения полупогружных буровых установок.
4.Общая характеристика и область применения буровых судов.
5.Добыча нефти и газа из морских месторождений. Морские стационарные платформы (назначение, типы, основные элементы).
6.Технологические схемы и установки для бурения неглубоких ин- женерно-геологических скважин на шельфе (УМБ-2М, УМБ-130М).
VIII. Бурение геологоразведочных скважин
1.Конструкции и способы описания конструкции скважин.
2.Назначение и структурная схема стационарной буровой установки.
3.Стационарный буровой станок. Перечень и назначение основных элементов бурового станка.
4.Состав и назначение элементов трансмиссии бурового станка.
5.Назначение, типы и конструктивные особенности буровых вышек и мачт.
6.Назначение и схемы талевых оснасток. Определение числа струн талевой оснастки.
7.Состав и назначение элементов бурового снаряда для колонкового бурения скважин.
8.Элементы и параметры бурильных колонн.
9.Вспомогательный инструмент для колонкового бурения (перечень, назначение и особенности конструкции).
10.Оборудование и инструмент для выполнения и механизации спус- ко-подъемных операций (состав, назначение). Технология выполне-
306
ния спуско-подъемных операций с использованием полуавтоматического элеватора.
11.Буровые здания (типы, назначение).
12.Общая характеристика передвижных установок. Особенности перевозок установок.
13.Легкие специализированные установки для бурения скважин (типы, область применения).
14.Самоходные буровые установки (типы, область применения).
IX. Промывка скважин
1.Функции очистных агентов.
2.Схемы циркуляции промывочной жидкости в скважине.
3.Определение необходимого расхода жидкости для эффективной циркуляции раствора в скважине.
4.Типы очистных агентов.
5.Приготовление и способы очистки раствора.
X.Технологические операции и режимы бурения геологоразведочных скважин.
XI. Бурение скважин из подземных горных выработок
1.Целевое назначение бурения скважин из подземных горных выработок.
2.Область применения, структура и кинематика бурового станка
НКР-100МА.
3.Схемы выполнения операций по извлечению бурильных колон из скважины в условиях подземных выработок.
4.Область применения и принцип работы буровой установки «Старт».
XII. Бурение стволов и восстающих горных выработок
1.Основные системы, функционирующие при бурении стволов роторными установками L-35.
2.Схема удаления разрушенной породы из скважины при работе с установкой L-35.
3.Конструкции стволов, проходимых способом бурения. Особенности конструкции обсадных труб и технологические схемы крепления ствола.
4.Структура установки с роторным агрегатом.
5.Схема бурения ствола из подземной горной выработки по технологической схеме «сверху-вниз».
6.Схема бурения ствола из подземной горной выработки по способу «Рейс-боринг».
7.Технологическая схема проходки выработок буросбоечной машиной СБМ-3У .
8.Конструктивные особенности и технология бурения восстающих установкой «Стрела-77».
307
XIII. Горно-буровая технологическая система
1.Особенности комбинированного способа проходки шахтных стволов.
2.Горно-буровая технологическая система - как составляющая геологоразведочных систем.
Литература:
1.Вадецкий Ю.В. Бурение нефтяных и газовых скважин: Учебник для нач. проф. образования. М.: Изд-во «Академия», 2008. – 352 с.
2.Власюк В.И., Калинин А.Г., Анненков А.А. Бурение и опробование ра-
зведочных скважин: Учебное пособие для вузов.- М.: Изд-во ЦентрлитНеф-
теГаз, 2010. – 864 с.
3.Волков А.С., Долгов Б.П. Вращательное бурение разведочных сква-
жин. - М.: Недра, 1988. -320 с.
4.Калинин А.Г., Ошкордин О.В., Питерский В.М., Соловьев Н.В. Разве-
дочное бурение: Ученик для вузов. – М.: ООО «Недра-Бизнесцентр», 2000.
–748 с.
5.Качан В.Г., Купчинский И.А. Бурение шахтных стволов и скважин.-
М.: Недра. 1984. – 275 с.
6.Ларин К.Л. Геологоразведочное дело. Разведочное бурение и техника безопасности. – Киев, издательское объединение «Вища школа». Голов-
ное изд-во, 1978. - 304 с.
7.Литвиненко В.С., Калинин А.Г. Основы бурения нефтяных и газовых скважин: Учебное пособие. М.: Изд-во ЦентрлитНефтеГаз, 2009. – 544 с.
8.Нескоромных В.В., Калинин А.Г. Направленное бурение: Учебное пособие. – М.: Изд-во ЦентрлитНефтеГаз, 2008. – 384 с.
9.Пилипець В.І., Тулуб С.Б., Левіт В.В. Буріння стволів шахт та технічних свердловин, Підручник для вузів. – Донецьк: Норд-Прес, 2009. – 564 с.
10.Пилипец В.И. Бурение скважин и добыча полезных ископаемых: Учебник для вузов. – Донецк, ООО «Типография «Новый мир», 2010. – 760 с.
11.Пилипец В.И. Разведочное бурение скважин и добыча полезных ископаемых: Учебник для вузов. – Донецк: Норд-компьютер, 2007. – 246 с.
12.Шамшев Ф.А., Тараканов С.Н., Кудряшов Б.Б. Техника и техноло-
гия разведочного бурения. М.: Недра. 1983. – 565 с.
13.Юшков А.С., Пилипец В.И. Геологоразведочное бурение. – Донецьк:
Норд-Прес, 2004. – 464 с.
308
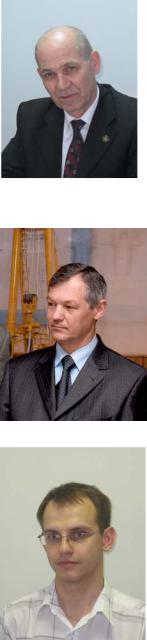
КАЛИНИЧЕНКО ОЛЕГ ИВАНОВИЧ, доктор технических наук, професор, членкореспондент Украинской технологической академии, професор кафедры технологи и техники геологоразведочных работ Донецького национального технического университета
ЗАБИНСКИЙ ПЕТР ВАСИЛЬЕВИЧ,
кандидат технических наук, генеральный директор ЗАО «Компания «Юговостокгаз»
ХОХУЛЯ АЛЕКСАНДР ВЛАДИМИРОВИЧ,
магистр бурения, ассистент кафедры технологи и техники геологоразведочных работ Донецького национального технического университета
309