
- •Калиниченко О.И., Зыбинский П.В., Хохуля А.В.
- •Рекомендовано научно-издательским советом Донецкого национального технического университета в качестве учебного пособия для студентов, обучающихся по направлению «Горное дело» специальности «Бурение»
- •Донецк 2012
- •Калиниченко О.И., Зыбинский П.В., Хохуля А.В.
- •Рецензенты:
- •ПРЕДИСЛОВИЕ
- •2 ОСНОВЫ ГОРНОЙ ТЕХНОЛОГИЧЕСКОЙ СИСТЕМЫ
- •Число оборотов ротора изменяют при помощи передаточных механизмов лебедки или же путем замены приводных колес. Чтобы не связывать работу лебедки с работой ротора, в ряде случаев применяют индивидуальный, т.е. не связанный с лебедкой, привод.
2 ОСНОВЫ ГОРНОЙ ТЕХНОЛОГИЧЕСКОЙ СИСТЕМЫ
Горная технологическая система представляет собой комплекс подземных и открытых горных выработок, необходимых для освоения месторождений полезных ископаемых. Учитывая целевой характер стадий освоения месторождений, горная система объединяет две группы выработок –
разведочные и эксплуатационные (рис. 2.1). Первые служат для целей раз-
ведки залежи полезного ископаемого, вторые – для его разработки.
2.1. Классификация горных выработок
Работы, которые производятся при выемке вмещающих пород или полезного ископаемого при разведке или разработке месторождений, называются горными работами. В результате горных работ в толще полезного ископаемого или вмещающих (пустых) пород образуются полости, назы-
ваемые горными выработками.
Полезное ископаемое может быть использовано лишь после его разработки, когда оно отделено от массива и доставлено на поверхность. Разработка месторождения складывается из трех этапов: вскрытие, подготовка и очистная выемка. В связи с этим эксплуатационные горные выработки подразделяются на капитальные, подготовительные и очистные.
К капитальным относятся выработки, по которым осуществляется доступ к месторождению или его части. Это вскрывающие выработки, а также выработки, сохраняемые в течение всего срока службы шахты.
Подготовительные выработки проводят от капитальных. Они служат для подготовки части залежи к очистным работам.
После проведения подготовительных выработок приступают к извлечению полезных ископаемых, в результате чего образуются очистные выработки.
Назначение разведочных горных выработок ограничено задачами геологических поисково-съемочных работ и разведки месторождений полезных ископаемых. Это обусловливает с одной стороны временный характер таких выработок, срок службы которых заканчивается получением информации, предусмотренной геологическим заданием, с другой стороны возможности выбора прогрессивных способов и технологии производства разведочных выработок сужены спецификой условий их проведения.
Поиски и разведку месторождений полезных ископаемых не редко проводят в экономически не освоенных и труднодоступных районах, где часто отсутствуют подъездные пути, линии электропередач и другие виды стационарных источников энергии. Сложность проведения горноразведочных выработок состоит также в том, что они характеризуются малыми сечениями, небольшими и, в основном, не постоянными объемами,
36
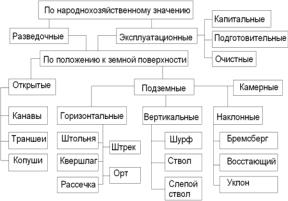
рассредоточенностью, нестационарностью условий и сезонностью работ. Как правило, направление горно-разведочных выработок часто меняется вследствие необходимости прослеживания и геологического изучения рудного тела. При проведении разведочных выработок на каком-либо объекте приходится иметь дело с большим многообразием горных пород, с вероятностью пересечения рыхлых и скальных пород различного литологического и петрографического состава.
Несмотря на выделенные особенности в некоторых случаях разведочные выработки впоследствии используются в качестве эксплуатационных.
В зависимости от расположения горных выработок относительно земной поверхности их разделяют на открытые и подземные. Открытые выработки по всей длине примыкают к земной поверхности. В сечении такие выработки не имеют замкнутого контура. Подземные выработки расположены под земной поверхностью и лишь некоторые из них, примыкают к поверхности. Такие выработки по периметру сечения ограничены поверхностями горной породы.
К открытым горным выработкам
относятся канавы, траншеи и копуши. Эти выработки широко применяются при геологическом изучении поверхностных участков месторождений.
Канава – гор-
ная выработка, искусственно созданная в земной коре, связанная с земной поверхностью и имеющая значительную протяженность при ограниченных поперечных сечениях. Глу-
бина канав обычно не превышает 5 м. Длина их значительно больше глубины и измеряется десятками, а в некоторых случаях сотнями метров. Как правило, бока канав глубиной более 2 м закрепляются деревянной крепью.
Канавные работы применяются на всех стадиях геологических исследований. Особенно большое значение канав в начале разведки, так как именно эти горные выработки позволяют определить направление и объем дальнейших работ, дают начальное представление о форме рудного тела и качестве полезного ископаемого. Канавы проходят для обнажения из-под
37
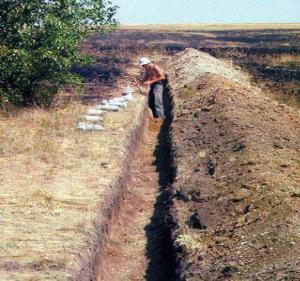
рыхлых отложений мощностью до 5 м не только коренных пород, но и полезных ископаемых, а также подготовки запасов по категориям А, В,С1 и С2 . Поис- ково-съемочные канавы проходятся с целью вскрытия коренных пород. Поис- ково-разведочные канавы проходятся для вскрытия рудных тел и закладываются по простиранию рудного тела, если его ширина
Рис. 2.2. Проходка разведочных канав не превышает 2 м, и
по простиранию – ес-
ли ширина рудного тела превышает 2 м.
Помимо разведочных канав, при разведке и разработке месторождений могут проводиться канавы, предназначенные для других целей, например, для защиты выработок от затопления ливневыми или паводковыми водами, отвода карьерных и шахтных вод.
Траншея - открытая горная выработка (канавообразная), проводимая с целью разведки или разработки месторождения полезного ископаемого. Траншея отличается от канавы значительно большими размерами поперечных сечений и формой сечений, обеспечивающей устойчивость боков горной выработки без крепления.
При разработке месторождений применяются разрезные и дренажные траншеи. Первые характеризуются наличием выездных поверхностей и являются транспортными выработками. Вторые служат для отвода, главным образом грунтовых и ливневых вод.
Площади поперечных сечений траншеи могут измеряться десятками квадратных метров, а эксплуатационных – сотнями.
Копуша – ямообразная горная выработка небольшой площади и малой глубины (до 1 м). Обычно копуши проводят в мягких породах при съемке и поисках месторождений полезных ископаемых для взятия породных образцов в наносах.
Подземные горные выработки по сравнению с открытыми горными выработками характеризуются большим разнообразием.
38
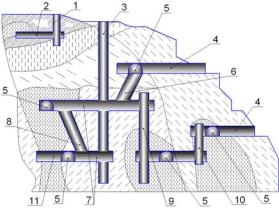
По положению оси горных выработок к горизонтальной плоскости выделяются выработки вертикальные, горизонтальные и наклонные. Они могут иметь непосредственный выход на земную поверхность или не иметь его (рис. 2.3).
К вертикальным горным выработкам относятся стволы шахт, гезенки и шурфы.
Шахтный ствол (3) – вертикальная (реже наклонная) горная выработка круглого или прямоугольного сечения, имеющая непосредственный выход на поверхность и предназначенная для обслуживания подземных горных работ, выполняемых при разведке и разработке месторождений полезных ископаемых.
Стволы делятся на главные и вспомогательные.
Главный ствол предназначен для выдачи полезного ископаемого, вспомогательный – для спуска-подъема людей, материалов, оборудования, проветривания и других вспомогательных целей. Часто стволы выполняют несколько функций одновременно и называются по главной из них.
Слепой ствол (9) – вертикальная горная выработка, не имеющая выхода на поверхность, проводится между горизонтами, предназначен для обслуживания подземных горных работ, проводимых при разведке или разработке полезного ископаемого (в первую очередь для подъема полезного ископаемого с нижних горизонтов на верхние). Слепой ствол может быть также использован для вентиляции, спуска и подъема людей, материалов, оборудования, породы.
Гезенк (10) – вер-
тикальная выработка, не имеющая непосредственного выхода на поверхность и предназначенная для спуска полезного ископаемого под действием силы собственного веса или в специальных сосудах механическим способом. Гезенк может быть также использован для вентиляции и спуска (подъема) людей, материалов, оборудования. Существенного различия
пым стволом нет. между гезенком и сле-Шурф (1) – вертикальная горная выработка (реже наклонная)
имеющая выход на поверхность, обычно малого сечения (до 4 м2) и не-
39
большой глубины (до 40 м), предназначенная для разведочных целей, обслуживания горных работ или для производства взрывных работ (карьеры). С помощью шурфов вскрывают и изучают толщу коренных пород. Из них иногда проходят рассечки (рис. 2.4).
На шахтах шурфы используются в качестве вспомогательных выработок, соединяющих подземные горизонтальные выработки с поверхностью, например, для вентиляции. Размеры этих шурфов могут быть значительно больше указанных выше.
К подземным горизонтальным выработкам относят: штольни, штре-
ки, квершлаги, рассечки и др. Название горизонтальные выработки – несколько условно, поскольку большинство из них проводится с небольшим уклоном, облегчающим перевозку грузов и сток воды.
Штольня (4) – горная выработка, имеющая выход на поверхность, проведенная к месторождению горизонтально или с незначительным подъемом; предназначена для обслуживания горных работ, разведки месторождений полезных ископаемых, и может выполнять функции откаточных, вентиляционных и водоотливных выработок. Штольня проходится только в гористой местности, и ее устье располагается на склоне горы.
Штрек (5) - горизонтальная горная выработка, не имеющая выхода на поверхность, проведенная по простиранию наклоннозалегающего месторождения или в любом направлении при горизонтальном его залегании. Предназначена для обслуживания горных работ при разведке или разработке месторождения. В большинстве случаев штреки проводят по полезному ископаемому, однако, при разработке, а иногда и при разведке месторождения их могут проводить и по вмещающим породам.
Штреки, пройденные по пустым породам вдоль полезного ископаемого, называются полевыми. Штрек, по которому идет основной поток полезного ископаемого и груза называется главным. Штрек, пройденный между главными штреками, называется промежуточным.
Квершлаг (7) – горизонтальная горная выработка, не имеющая выхода на поверхность и предназначенная для разведки месторождения и обслуживания горных работ. Квершлаг проходится по вмещающим породам вкрест простирания или под некоторым углом к простиранию полезного ископаемого, соединяя ствол шахты с рудным телом, и служит для транспортировки грузов, передвижения людей, вентиляции, водоотлива, прокладки электрических кабелей и линий связи. Устье квершлага может располагаться в боковой стенке камерной выработки, ствола или штольни.
Орт (11)- горизонтальная горная выработка, не имеющая выхода на поверхность, проводимая вкрест простирания мощной залежи полезного ископаемого (при крутом и наклонном падении) между висячим и лежачим боками в пределах их горизонтальной мощности. В ряде случаев орт может выходить за пределы залежи до полевых штреков. Устье орта располагают в боку штрека.
40
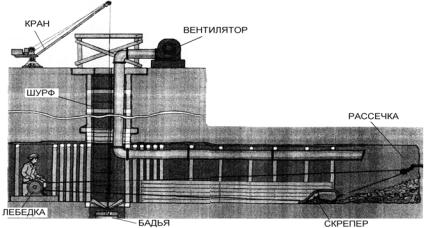
Рассечка (2) – горизонтальная горная выработка, не имеющая выхода на поверхность, проводимая из шурфов (рис. 2.4), штолен или штреков вкрест простирания горных пород, для поисков и разведки полезного ископаемого. Длина рассечки до 30 м, реже до 100 м.
Рис. 2.4. Рассечка, пройденная из шурфа
Промежуточное положение между вертикальными и горизонтальными выработками занимают наклонные выработки, отличающиеся специфическими особенностями их проведения и транспортировки по ним грузов. При разработке и разведке полезных ископаемых наиболее широко применяются бремсберги, уклоны и восстающие. Кроме того, к наклонным выработками относятся наклонные шурфы, стволы и штольни. Они имеют то же назначение и те же основные признаки, что и одноименные вертикальные или горизонтальные выработки, отличаясь от них лишь положением в земной коре.
Бремсберг (6) - наклонная горная выработка, не имеющая выхода на поверхность, пройденная, как правило, по направлению падения полезного ископаемого и предназначенная для спуска груза, полезного ископаемого на откаточный штрек.
Уклон (8) - наклонная горная выработка, не имеющая выхода на поверхность и предназначенная для подъема горных пород, груза на откаточный штрек. Нередко используется для подачи свежего воздуха с верхних горизонтов на нижние. Проходится, как правило, на угольных шахтах.
Восстающая горная выработка (восстающий) – наклонная (верти-
кальная) горная выработка, не имеющая выхода на поверхность, проводимая по восстанию залежи при разведке или разработке месторождения для
41
проветривания, спуска полезного ископаемого или породы, доставки материалов и оборудования, подачи энергии и воды. Длина – до 100 м при площади сечения до 5 м2 . Восстающие, пройденные по вмещающим породам, называют полевыми.
При подземной разработке угольных месторождений в качестве очистной выработки применяют лавы. Лава – выработка расположенная, как правило, по падению пласта между двумя штреками. Один из штреков (нижний), предназначенный для транспортирования полезного ископаемого, называется откаточным, второй (верхний) – вентиляционным. Лава имеет значительные размеры по длине (350 м и более). Ширина лавы 2-3 м, высота равна мощности пласта. Длина забоя равна длине лавы. Лава перемещается в результате выемки угля, а образовавшееся выработанное пространство закладывается породой или обрушается.
Вблизи шахтного ствола располагается целый ряд горизонтальных и камерообразных выработок, которые называются выработками около-
ствольного двора.
Околоствольный двор (рис. 2.5) - совокупность выработок, служащих для соединения ствола с остальными выработками шахты, и специальных камер для размещения общешахтных производственных служб. Тип околоствольного двора зависит от производительности шахтного ствола (количества выдаваемой руды и породы), способа подъема руды (в скипах или клетях), числа стволов, обслуживаемых околоствольным двором, принятой схемы проветривания.
На крупных шахтах, имеющих большую производительность, обычно устраивают круговые околоствольные дворы (рис. 2.5, а), обеспечивающие поточность движения транспорта, а в шахтах небольшой производительно-
сти — тупиковые (рис. 2.5, б).
Выработки, имеющие сопоставимые размеры длины, высоты и ширины (сравнительно короткие выработки с большой площадью поперечного сечения) называются камерами. Они являются, в основном, вспомогательными и служат для размещения и хранения под землей оборудования, материалов и др.
Насосная камера служит для размещения 3-4 насосов с электродвигателями. Располагают насосную камеру обычно вблизи клетевого ствола. Камеру горизонтальным ходком соединяют с главной откаточной выработкой, а наклонным – со стволом. В горизонтальном ходке устраивают герметичные двери, закрываемые на случай затопления камеры. (Ходок в камеру
– горизонтальная или наклонная выработка, проведенная по полезному ископаемому в околоштрековом целике, соединяющая штрек с эксплуатационной камерой).
Водосборник – служит для сбора шахтной воды, поступающей по водоотводным канавкам со всей шахты. Его устраивают из двух самостоятельных, закрепленных бетонной крепью выработок (для удобства чистки
42
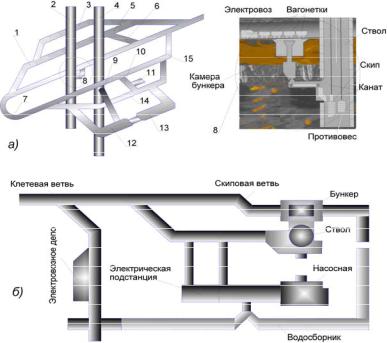
без остановки работы насосов). Водосборник должен вмещать не менее 8- часового нормального водопритока.
Рис. 2.5. Схема околоствольного двора:
1 – обходная выработка; 2 – главный ствол; 3 – склад взрывчатых материалов;4 – вспомогательный ствол; 5,6 – камеры депо; 7 – порожняковая ветвь; 8 – камера бункера; 9 – наклонный ходок; 10 – камера ожидания; 11 – медпункт; 12 – насосная камера; 13 – камера электрической подстанции; 14 – посадочная камера; 15 – грузовая ветвь; а - схема кругового околоствольного двора; б – схема тупикового околоствольного двора
Камера электроподстанции служит для размещения электрооборудования, запитываемого от центральной поверхностной подстанции, и распределения электрической энергии к главным подземным потребителям. Камеру обычно блокируют с насосной камерой.
Камера электровозного депо служит для стоянки электровозов во время перерывов в работе, их осмотра и ремонта, а при аккумуляторных электровозах, и для зарядки батарей в шахте. Длина депо зависит от числа
итипов электровозов и преобразовательных устройств.
Камера ожидания располагается вблизи вспомогательного ствола шахты и служит для пребывания рабочих в ожидании поезда, доставляюще-
43
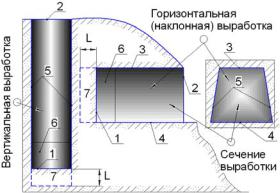
го их на участок, для отдыха перед подъемом на поверхность. Камера должна иметь два выхода (по обе стороны от ствола) для перехода с порожняковой на грузовую ветвь околоствольного двора и наоборот.
Камера опрокидывателя и бункерная камера служат для разгрузки вагонеток и загрузки скипов на главном стволе.
2.2. Элементы и параметры горной выработки
Поверхности породы, ограничивающие горную выработку, являются
ееэлементами (рис. 2.6).
Забой (1) – поверхность горной выработки, передвигающаяся в пространстве в результате выемки вмещающей горной породы или полезного ископаемого. Различают забои очистные и подготовительные. Последние, в свою очередь делятся на действующие, запасные и резервные забои.
Действующие забои – забои, в которых систематически производятся
очистные или подготовительные работы.
Запасные забои - забои, полностью подготовленные, но не оснащенные выемочными машинами. При необходимости они могут быть оснащены выемочным оборудованием и превращены в действующие или резервные забои.
Резервные забои – забои, полностью подготовленные и оснащенные необходимым оборудованием, и могут быть в любое время введены в действие.
Подвигание забоя
(7)– расстояние ( L ), на которое переместится забой за определенный промежуток времени.
Устье (2) – место примыкания горной выработки к земной поверхности или к другой горной выработке, из которой она берет начало.
Кровля (3), подошва (4), бока (5) – по-
верхности горной поро-
Рис. 2.6. Элементы горной выработки ды, ограничивающие вы-
работку, соответственно,
сверху, снизу и с боков.
Призабойное пространство (6) – часть горной выработки, непосредственно примыкающая к забою, и предназначена для размещения рабочих и проходческого (добывающего) оборудования.
44
К параметрам горных выработок относятся протяженность (длина, глубина) и площади сечения выработки.
Различия в длинах (глубинах) горных эксплуатационных и разведочных выработок в ряде случаев несущественны. Например, длина разведочных штолен иногда измеряется километрами, а глубина стволов разведочных шахт достигает 400 м и более.
Площади поперечного сечения разведочных выработок, как правило, определяются из условия возможности, целесообразности и эффективности проходческих работ. Поэтому обычно они имеют по сравнению с эксплуатационными выработками меньшее сечение. Исключением из этого являются стволы разведочных шахт и выработки, проводимые при детальной и эксплуатационной разведках, и предназначаемые впоследствии для использования в процессе разработки месторождения.
Площадь поперечного сечения выработки в свету Sсв - площадь,
заключенная между крепью горной выработки и ее почвой, за исключением площади балластного слоя и рельсового пути.
Площадь поперечного сечения выработки вчерне Sч - проектная
площадь выработки.
Площадь поперечного сечения выработки в проходке Sпр - дейст-
вительная площадь горной выработки ограниченная ее контуром в забое:
Sпр 1.04 1.12 Sч .
2.3.Горные предприятия
Горное предприятие – самостоятельная производственная единица, осуществляющая разведку, добычу и обогащение полезных ископаемых. Горное предприятие, осуществляющее добычу и первичное обогащение полезных ископаемых, называется горнодобывающим. Существуют следующие виды горнодобывающих предприятий: шахта (разведочная шахта), рудник, карьер (разрез), прииск.
Шахта является самостоятельным горнопромышленным предприятием, осуществляющим добычу полезного ископаемого подземным способом и отгрузку его потребителю или на центрально-обогатительные фабрики. К шахте относятся также подземные и наземные сооружения для разработки месторождения.
Разведочная шахта – предприятие, осуществляющее разведку месторождений подземным способом и представляющая собой совокупность подземных горных выработок, предназначенных для разведки полезных ископаемых.
Рудник – горнопромышленное предприятие, состоящее из одной или нескольких производственных единиц (шахт, карьеров), служащее в основ-
45
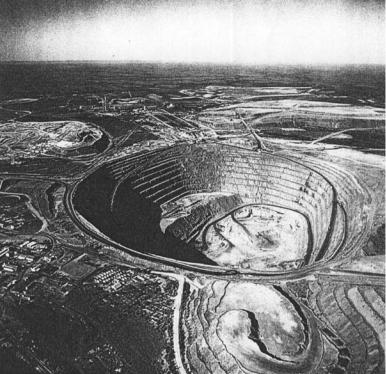
ном для подземной добычи руд, горно-химического сырья и строительных материалов.
Карьер – представляет собой совокупность разнообразных горных выработок (траншей, котлованов и др.), погрузочное, транспортное и отвальное хозяйства, механические мастерские и др., осуществляющее разведку и разработку месторождения открытым способом.
Карьеры по добыче угля и россыпных полезных ископаемых называ-
ют разрезом.
Рис. 2.7. Карьер
Месторождение, разрабатываемое открытым способом, разделяется на отдельные слои, обычно с учетом изменения качества полезного ископаемого или наличия пустых пород. Разработка каждого верхнего слоя опережает разработку нижнего, поэтому карьер имеет уступчатую форму (рис. 2.7).
Прииск – горнодобывающее предприятие по разработке россыпных месторождений полезных ископаемых, преимущественно золота, платины и алмазов.
46
2.4. Процессы при проведении горных выработок
Горные работы предполагают собой необходимость выполнения производственных и рабочих процессов, связанных с проведением, поддержанием горных выработок и выемке полезного ископаемого.
Производственный процесс – процесс труда, направленный на достижение конечной цели - создание конкретных материальных благ (например, добыча угля, руды) и характеризуется постоянством предмета труда, которым является горный массив. Результатом труда является добытое полезное ископаемое. По технологическому и организационному содержанию производственный процесс представляет собой совокупность комплексов рабочих процессов, необходимых для разведки и добычи полезного ископаемого.
Рабочий процесс представляет собой четко очерченную часть производственного процесса (например, выемка угля комбайном, размельчение разрыхленной породы, возведение крепи). В общем случае рабочий процесс представляет собой совокупность основных и вспомогательных опера-
ций.
Основные операции (разрушение горного массива; проветривание; уборка породы; крепление выработок) определяют содержание и конечную цель рабочего процесса.
Вспомогательные операции (настилка рельсового пути, устройство водоотливной канавки, навеска вентиляционных труб и др.) сопутствуют основным и способствуют их успешному выполнению.
Проведение выработок и очистная выемка, как горные работы, основаны на разрушении горного массива.
2.5. Разрушение горного массива
Процесс разрушения в основном сводится к отбойке от породного массива некоторого количества горных пород. Если в результате отбойки горной массы отделяются крупные куски породы, не подлежащие транспортировке на поверхность, их измельчают до транспортабельных (кондицион-
ных) размеров (вторичное дробление).
Методы разрушения породы при отбойке и вторичном дроблении разнообразны и осуществляются различными способами: с помощью ручной отбойки, средствами гидромеханизации, с помощью отбойных молотков, с использованием комбайнов и стругов, с применением буровзрывных работ.
Ручная отбойка довольно широко распространена при проведении горно-разведочных выработок в мало связных и мягких породах. Данный способ применяют также при рыхлении крепких пород в небольших
47

объемах, например, при пересечении шурфов с маломощной прослойкой крепких пород. Уплотненные мягкие, ломкие и хрупкие породы отбивают с помощью кайл. Крепкие породы отделяют от массива киркой и молотком, а трещиноватые — стальным клином, загоняемым в трещины забоя тяжелым молотом или ломом.
При проведении подземных выработок ручная отбойка применяется при выполнении отдельных операций – скалывании граней с боковых стенок при возведении крепи, зачистке и оборке забоя, навеске вентиляционных
труб и др.
|
|
|
Гидравличе- |
|||
|
ское разрушение по- |
|||||
|
род основано на ис- |
|||||
|
пользовании кинети- |
|||||
|
ческой |
|
энергии |
|||
|
струи воды, выбра- |
|||||
|
сываемой |
из |
гидро- |
|||
|
монитора. |
Гидромо- |
||||
Рис. 2.8. Гидромонитор:1—насадка; 2 — ствол; |
нитор |
представляет |
||||
собой |
|
устройство |
||||
3 — гидроцилиндры поворота ствола; 4 — подводящая |
для |
создания |
плот- |
|||
труба; 5 – салазки |
ной |
направленной |
||||
|
||||||
|
водяной |
|
струи |
и |
||
|
управления ее поле- |
|||||
|
том. |
|
Основными |
|||
|
элементами |
гидро- |
||||
|
монитора |
являются |
||||
|
подводящий |
патру- |
||||
|
бок, шарнирные уз- |
|||||
|
лы, ствол и насадка |
|||||
|
(рис. 2.8). Вода с по- |
|||||
|
мощью |
насосов |
по- |
|||
|
дается в подводящий |
|||||
|
патрубок, далее че- |
|||||
|
рез шарниры и ствол |
|||||
Рис. 2.9. В забое гидрошахты |
поступает в насадку. |
|||||
|
Шарнир |
|
позволяет, |
|||
|
перемещая |
ствол, |
изменять направление полета струи. В качестве ходовой части гидромонитора используются металлические салазки и гусеничные тележки с гидромеханическим и электромеханическим приводом.
48
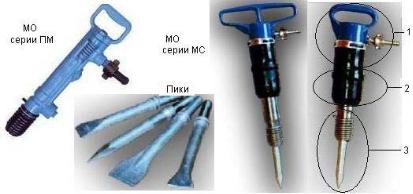
Гидравлическое разрушение применяется на открытых работах при разработке наносных отложений и в отдельных случаях при подземной добыче полезных ископаемых. Гидравлическую отбойку производят одновременно с транспортировкой разрушенной породы по трубам или наклонным канавам.
Размыв породы на открытых работах производится гидромониторами с давлением струи обычно 1…2 МПа при расходе воды 250…4000 м3/ч.
Для подземной гидроотбойки и смыва перемятых, выветрелых и разрыхленных взрывом углей, других полезных ископаемых и горных пород, используются гидромониторы, воду к которым подают под давлением до 6 МПа при расходе до 400 м3/ч. Требуемый напор гидромонитора достигается насосами высокого давления.
Считается, что эффективная отбойка породы, имеющей коэффициент крепости f , происходит при развиваемом напоре Н 5 f .
Отбойные молотки (рис. 2.10) — это легкие породоразрушающие машины ударного действия, являющиеся простейшим средством механизации отбойки. Они предназначены для отбойки угля различной крепости, разрушения и разрыхления мягких руд и грунта. Отбойные молотки используют также при проведении горно-разведочных выработок, поскольку они облегчают труд проходчика и увеличивают его производительность. Применение их возможно при наличии компрессорных установок.
Рис. 2.10. Внешний вид отбойных молотков
Структурно отбойный молоток состоит из пускового устройства 1, воздухораспределительного механизма 2 и ударного узла 3. Принцип действия пневматического отбойного молотка основан на использовании энергии сжатого воздуха для обеспечения возвратно-поступательного движения поршня–ударника. Ход поршня – ударника, при котором наносится удар по пике, называется рабочим ходом, обратный ход – холостой. При нажатии на
49
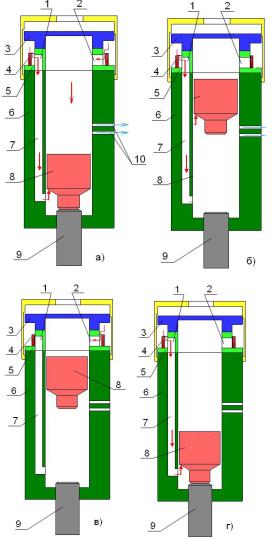
рукоятку пускового устройства сжатый воздух поступает в воздухораспределительный механизм, принцип работы которого приведен на рис. 2.11.
|
|
Холостой |
ход. |
|||
|
При |
достижении кла- |
||||
|
панной коробки 3 сжа- |
|||||
|
тый воздух попадает к |
|||||
|
кольцевому клапану 4. |
|||||
|
По каналам 7 в стволе |
|||||
|
6 сжатый воздух по- |
|||||
|
ступает |
к |
|
поршню- |
||
|
ударнику 8 (рис. 2.11, |
|||||
|
а). Давление под порш- |
|||||
|
нем – ударником рас- |
|||||
|
тет, а над ним падает, |
|||||
|
так как сжатый воздух |
|||||
|
будет |
выходить |
через |
|||
|
выпускные |
|
отверстия |
|||
|
10. За |
счет |
разности |
|||
|
давлений |
кольцевой |
||||
|
клапан |
перебрасывает- |
||||
|
ся, открывая |
впускное |
||||
|
отверстие 1 и закрывая |
|||||
|
отверстие 2 седла кла- |
|||||
|
пана 5. |
|
|
|
|
|
|
|
Поршень |
удар- |
|||
|
ник |
движется |
вверх, |
|||
|
проходит |
выпускные |
||||
|
отверстия 10 (рис. 2.11, |
|||||
|
б) давление под ним |
|||||
|
уменьшается, |
а |
над |
|||
|
ним |
|
увеличивается. |
|||
|
Кольцевой |
клапан пе- |
||||
|
ребрасывается. Воздух |
|||||
|
начнет поступать через |
|||||
Рис. 2.11. Принцип работы воздухораспределитель- |
канал 2 в верхнюю по- |
|||||
лость |
|
над |
|
поршнем. |
||
ного механизма отбойного молотка |
Это |
положение |
соот- |
|||
|
ветствует началу рабочего хода поршня – ударника (рис. 2.11, в).
Рабочий ход. Под действием сжатого воздуха поршень-ударник устремляется вниз, проходит выпускные отверстия 10, и наносит удар по пике
50
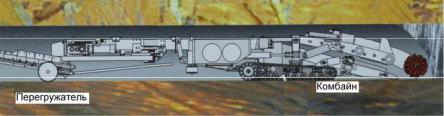
9. Сжатый воздух, находящийся над поршнем-ударником, выходит в выпускные отверстия. Давление над поршнем-ударником резко падает, и кольцевой клапан 4 перебрасывается (рис. 2.11, г). Давление под поршнемударником растет. Начинается холостой ход поршня – ударника.
Таким образом, переключение клапана происходит за счет разности давлений в клапанной коробке над и под клапаном при открывании выхлопных отверстий поршнем - ударником.
Эффективная работа наиболее известных отбойных молотков (МО2МС, МО-3МС, МО -4МС) обеспечивается при номинальном расходе воздуха 1,5 м3/мин и давлении воздуха 0,5 МПа. Энергия удара составляет 4055 Дж при частоте ударов от 23 до 17 с-1.
Механическое разрушение углей и пород с использованием комбай-
нов. Горный комбайн – это комбинированная горная машина, совмещено во времени выполняющая отделение от массива полезного ископаемого, пустой породы (или и того и другого вместе) и погрузку горной массы в транспортные средства.
Рис. 2.12. Схема работы комбайна в горной выработке
Современные проходческие комбайны позволяют эффективно разрушать горные породы с коэффициентом крепости f 5 .
Всоответствии с выполняемыми функциями комбайны имеют исполнительные органы для механического разрушения и погрузки горной породы, органы подачи комбайна на забой и перемещений в забое, двигатель, устройства для подавления или поглощения пыли и другое вспомогательное оборудование.
Всовременных проходческих комбайнах используются исполнительные органы с коническими резцовыми коронками или шаровыми фрезами, установленными на стреле (рис. 2.15); в виде шнека с закрепленными на нем зубками (рис. 2.13-2.14); с буровым или роторным резцовым исполнительным органом (рис. 2.16).
Очистные комбайны для крутых пластов, работающие по восстанию или падению пласта погрузочным органом не оснащаются, так как отбитое полезное ископаемое перемещается вниз под действием собственного веса или потоком воды (гидротранспортом).
51
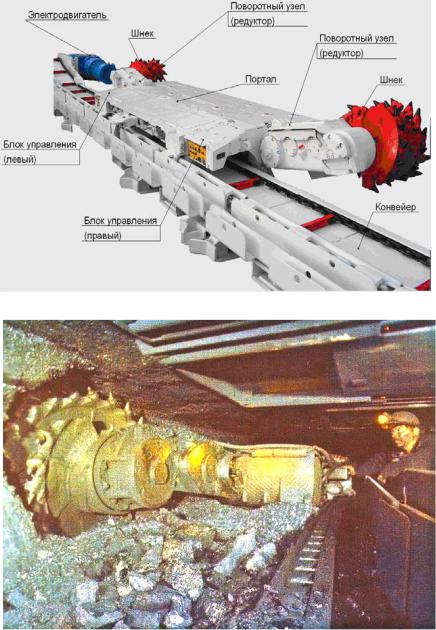
Рис. 2.13. Внешний вид добычного комбайна УКД 200-250
Рис. 2.14. Комбайн в забое угольной шахты
52
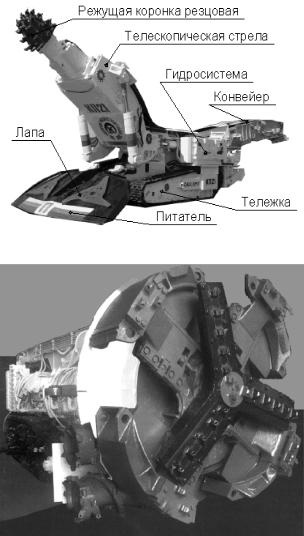
Горные комбайны разделяют на фланговые, применяемые в длинных очистных забоях на пологих и крутых пластах, и фронтальные – в коротких очистных и подготовительных забоях на пластах с углом падения до 10о.
Рис. 2.15. Внешний вид проходческого комбайна КП21
Рис. 2.16. Проходческий комбайн с роторным резцовым исполнительным органом (ПК-8).
щими совместно с конвейером комбайна
Фланговые комбайны
(рис.2.13- 2.14) -
это машины цикличного действия; движутся вдоль забоя по почве или по раме забойного конвейера и последовательно вынимают полосы полезного
ископаемого. Здесь, для погрузки используют его же или специальный грузчик.
Фронтальные комбай-
ны (рис. 2.15 - 2.16) обрабатывают массив, передвигаясь по почве в направлении оси проходимой выработки. Погрузка горной массы фронтальными комбайнами обычно производится исполнительным органом с нагребающими лапами бокового захвата или шнеками, действую-
53
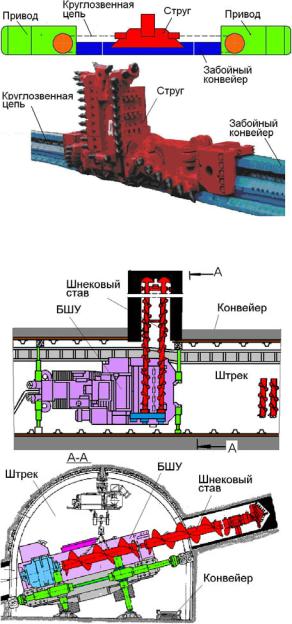
Рис. 2.17. Схема и внешний вид буроструговой установки.
Рис. 2.18. Бурошнековая установка (БШУ)
54
Струговые установки работают в очистных забоях (лавах) и предназначены для разрушения массива угля, дробления угля на транспортабельные куски, передачу угля на призабойное транспортное средство.
В целом, струговая выемка является одним из наиболее прогрессивных способов добычи угля. Она имеет ряд существенных преимуществ перед комбайновой, заключающихся в следующем: улучшается сортность добываемого угля и уменьшается пылевыделение; более простое оборудование; низкая энергоемкость процесса разрушения и погрузки угля на конвейер; возможность применения на весьма тонких пластах; наибольшая пригодность для полной автоматизации технологического процесса выемки угля в длинных очистных забоях.
Структурная схема струговой установки приведена на рис. 2.17. Установка
представляет собой исполнительный орган – струг, оснащенный резцами. Перемещение струга осуществляется при помощи приводов, расположенных по концам лавы (или вынесены на штреки). Тяговым органом, передающим усилие от привода, является круглозвенная цепь. Струг перемещается по ставу забойного конвейера. При движении вдоль забоя струг снимает стружку угля толщиной 50…150 мм. Отбитый таким образом уголь корпусом струга грузится на конвейер.
Бурошнековые установки (БШУ) (рис. 2.18) используются для добычи угля из тонких пластов. БШУ располагается в штреке и производит бурение спаренным шнековым ставом по пласту. Разрушенный коронками уголь транспортируется из скважины шнековым ставом на конвейер, который располагается в штреке.
Взрывной способ разрушения горных пород универсален, и является наиболее распространенным. Около 90% минерального сырья в Украине добывается с помощью взрывных работ. Взрывная отбойка части горной массы от целого массива может применяться при любой крепости полезного ископаемого и пород.
При добыче рудных полезных ископаемых и проведении горных выработок по крепким породам, взрывное разрушение является единственным способом, имеющим промышленное применение.
Взрывной способ разрушения основан на применении взрывчатых веществ (ВВ), при быстротечном разложении которых, освобождающаяся энергия взрыва отделяет от массива и осуществляет дробление породы. Чтобы осуществить взрывное разрушение с достаточной эффективностью,
ВВдолжно быть размещено в специально образуемых в породе полостях, называемых зарядными камерами. В зависимости от формы и размеров этих полостей, различают следующие способы ведения взрывных работ: шпуровой, скважинный, камерными и накладными взрывами.
Шпуровой метод взрывных работ применяется при проведении горных выработок, в отдельных случаях для отбойки угля в очистных забоях (рис. 2.19, ДОБЫЧА УГЛЯ В ШАХТЕ) и руд в блоках при небольшой мощности рудных залежей. (Шпур – цилиндрическая полость в горной породе, имеющая глубину до 5 м, диаметр до 75 мм и предназначенная для размещения заряда ВВ).
Скважинный способ применяются при массовой отбойке руды в блоках мощных рудных тел, а также на открытых горных работах для разрушения пород в уступах (рис. 2.19, ДОБЫЧА РУДЫ В КАРЬЕРЕ). (Взрывная скважина – горная выработка цилиндрической формы глубиной более 5
ми диаметром 75 мм и более, пройденная в породе способом бурения).
Метод камерных зарядов применяется в отдельных случаях для отбойки руды в блоках, а также для осуществления массовых взрывов на поверхности. С этой целью проводятся специальные горные выработки, не-
55
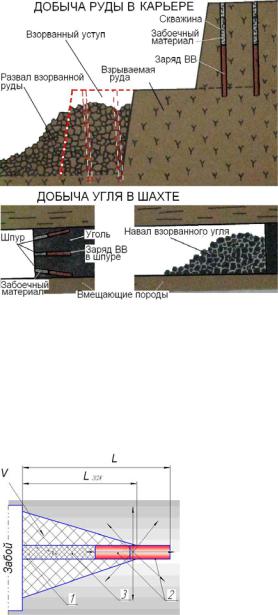
Рис. 2.19. Разрушение пород с использованием БВР при добыче полезного ископаемого
редко с нишами, в которых размещают сосредоточенные заряды ВВ. Их масса может достигать нескольких тонн и даже десятков тонн.
Метод накладных зарядов
применяется для дробления негабарита, т.е. для дополнительного измельчения (вторичного дробления) кусков породы на месте их образования. Применение этого способа допускается и на подземных работах за исключением шахт, опасных по газу и пыли.
В общем случае взрывной способ разрушения горных пород предполагает неразрывность буровых и взрывных работ, что обосновывает принятый в горном деле термин «буровзрывные работы», которые включают проходку зарядных полостей для размещения зарядов ВВ, заряжание ВВ, их забойку и возбуждение (инициирование) взрыва.
На угольных шахтах основным является метод шпуровых зарядов. Этот метод является также доминирующим при проведении горных выработок в процессе разведки и разработки рудных месторождений полезных ископаемых.
При шпуровом методе взрывных работ в забое выработки пробуривают шпуры 1 глубиной L (рис. 2.20). В шпуре размещается заряд ВВ 2. Остав-
шуюся часть шпура заполняют забойкой Рис. 2.20. Конструкция шпура 3, состоящей их смеси глины с песком
или другого пластичного или сыпучего
56
материала. Процесс помещения заряда в шпур и заполнение его забойкой называется заряжанием шпуров.
При взрыве заряда ВВ в глубине массива пород возникает большое давление газов, образовавшихся при взрыве. Это давление разрушает и от-
брасывает определенный объем породы V , подвигая забой на длину за-
ходки Lзах .
Таким образом, взрывные работы при шпуровом методе заключаются в бурении шпуров, заряжании и взрывании ВВ.
Бурение шпуров, осуществляемое различными способами и механизмами, заключается в одновременном или последовательном выполнении двух операций – разрушение породы в забое шпура и удаление из него разрушенной горной породы.
Разрушение породы при бурении шпура достигается за счет передачи на забой механических нагрузок, вызывающих в породе напряжения, величина которых превышает ее прочность. Этот вид бурения шпуров называют механическим, и является доминирующим.
Разрушенная порода из шпура удаляется водой, воздушной струей или механическим способом.
Под термином «механическое бурение» иногда понимают бурение с помощью машин, противопоставляя ему ручное бурение, осуществляемое человеком с использованием простейших инструментов. В данном случае в термин «механическое бурение» вкладывается другое понятие: механическим называется такое бурение, при котором разрушение породы в шпуре достигается за счет ручной или машинной передачи на нее механических нагрузок.
Механизмы, применяемые для машинного бурения шпуров, называются бурильными машинами. Они, как правило, компактны, транспортабельны и имеют относительно небольшую мощность. Эти особенности обеспечивают удобство их эксплуатации в горно-разведочных выработках. В условиях разведки месторождений они также облегчают транспортировку оборудования к месту производства работ и позволяют проводить последние при недостаточной энерговооруженности геологоразведочных предприятий.
Бурильные машины оборудуются преимущественно электрическим, пневматическим или гидравлическим приводами; в некоторых конструкциях машин используются бензиновые моторы.
Вращательные машины называют сверлами. Разрушение пород при бурении шпуров сверлами обеспечивается вращающимся и прижимаемым к забою породоразрушающим инструментом, оснащенным резцами. Им же транспортируют из шпура разрушенную породу, для чего буровую штангу изготовляют из витой стали, которая при вращении, работая по принципу шнека, перемещает разрушенную породу от забоя шпура к его устью.
57
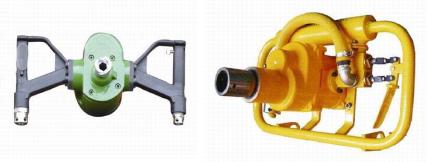
По массе и мощности двигателей сверла разделяют на ручные и колонковые. Бурение шпуров ручным сверлом производится с рук; масса таких сверл не превышает 25 кг при мощности на валу до 1,5 кВт. Колонковые сверла, имеющие более значительную массу (до 120 кг) и мощность до 3 кВт, монтируются для бурения шпуров на специальных колонках, устанавливаемых в забоях горных выработок.
Ручные сверла (РС) предназначены для бурения шпуров диаметром до 46 мм и глубиной до 2 м в мягких и средней крепости породах. По роду потребляемой энергии РС делятся на пневматические (ПРС), гидравлические (ГРС) и электрические (ЭРС).
Ручное пневматическое сверло (рис. 2.21) состоит из ротационного двигателя, редуктора, пусковой ручки, шпинделя с патроном. Сжатый воздух к сверлу подводится гибким шлангом. При помощи пусковой рукоятки производится пуск и остановка ПРС. Регулирование скорости вращения обеспечивается изменением количества воздуха, поступающего в двигатель.
В последние годы находят применение гидравлические сверла. (ГРС) (рис. 2.22). Отличительной их особенностью является применение безредукторного гидропривода с увеличенным крутящим моментом и повышенной мощностью, что дает возможность уменьшить массу сверла и повысить пределы применения их в более крепких породах. Техническая характеристика некоторых ПРС и ГРС приведена в табл. 2.1.
Рис. 2.21. Внешний вид ручного |
Рис. 2.22. Внешний вид ручного гидравли- |
пневматического сверла |
ческого сверла |
Таблица 2.1. Краткая техническая характеристика ПРС и ГРС
Буровое сверло |
Пневматическое |
|
Гидравлическое |
||||
|
ZQS 35 |
|
СР3-1м |
СР3Б-1м |
"Гном" |
MYS 50 |
|
Скорость, об/мин |
1200 |
|
315 |
|
750 |
700 |
1000 |
Крутящий момент, Нм |
70 |
|
716 |
|
716 |
8,5 |
50 |
Коэффициент крепости, f |
до 6 |
|
4-5 |
|
4-5 |
до 10 |
до 10 |
Масса, кг. |
11 |
|
13.5 |
|
13.5 |
до 6 |
20 |
|
|
58 |
|
|
|
|
|
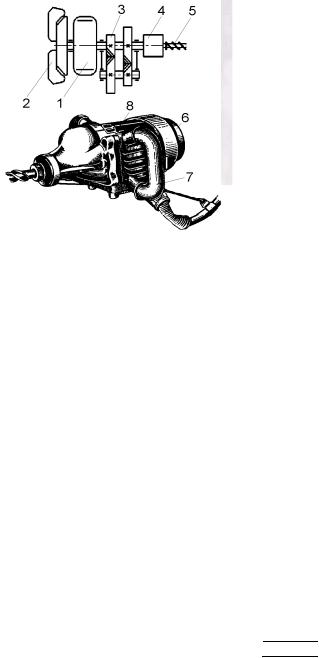
|
Внешний вид и принци- |
|||||
|
пиальная схема ручного элек- |
|||||
|
трического сверла |
(ЭРС) по- |
||||
|
казаны соответственно на рис. |
|||||
|
2.23 и 2.24. Основными час- |
|||||
|
тями машины являются элек- |
|||||
|
тродвигатель 1 и редуктор 3. |
|||||
|
На одном из концов вала ро- |
|||||
|
тора насажена шестерня ре- |
|||||
|
дуктора 3, на другом вентиля- |
|||||
|
тор 2, |
предназначенный |
для |
|||
|
охлаждения электродвигателя. |
|||||
Рис. 2.23. Внешний вид ручного электриче- |
Редуктор |
сверла, |
состоящий |
|||
ского сверла |
из двух |
пар |
цилиндрических |
|||
|
(конических) шестерен, под- |
|||||
|
шипника и шпинделя 4, за- |
|||||
|
ключен в алюминиевый кор- |
|||||
|
пус 8. К задней части корпуса |
|||||
|
электродвигателя |
крепится |
||||
|
алюминиевый колпак 6, за- |
|||||
|
крывающий |
вентилятор. |
В |
|||
|
шпинделе |
4 закрепляется |
||||
|
штанга |
5. |
Для |
удержания |
||
|
сверла и передачи усилия на |
|||||
|
забой |
корпус имеет две ручки |
||||
|
7. На правой ручке имеется |
|||||
|
рычаг, при нажатии на кото- |
|||||
|
рый |
срабатывает |
пусковое |
|||
Рис. 2.24. Устройство ручного |
устройство |
|
|
|
||
При работе сверло удер- |
||||||
электрического сверла |
живается в руках, или устанав- |
ливается на простейших подставках. Осевое усилие при бурении по углям и
мягким породам создается вручную. Техническая характеристика |
некото- |
||||||
рых ЭРС приведена в табл. 2.2. |
|
|
|
|
|
||
|
Таблица 2. 2. Техническая характеристика ручных электрических |
||||||
сверл |
|
|
|
|
|
|
|
|
Показатели |
|
Электрические сверла |
|
|
||
|
ЭР 14Д2М |
СЭР 19М |
ЭР 18Д2М |
ЭРП 18Д2М |
ZM15D |
|
|
|
Частота вращения, об/мин |
860 |
340-700 |
640 |
300 |
1200 |
|
|
Крутящий момент, Нм |
108 |
250, 120 |
203 |
408 |
28 |
|
|
Коэф. крепости пород, f |
до 4 |
до 4 |
до 4 |
до 4 |
до 6 |
|
|
Масса, кг |
16,5 |
18.0 |
18.0 |
24,5 |
16 |
|
|
|
|
59 |
|
|
|
|
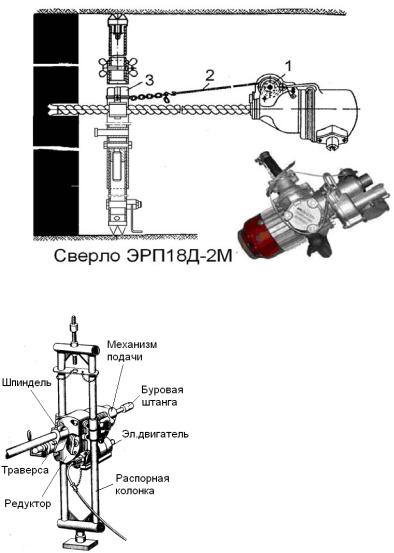
В более крепких породах применяют ручные электросверла с принудительной подачей. Такие сверла имеют дополнительный редуктор с барабанчиком 1 (рис. 2.25) для наматывания подающего канатика 2, один конец которого крепят на раздвижной стойке 3, установленной у забоя. При бурении, канатик наматывается на барабан и создает необходимое усилие подачи
Рис. 2.25. Электросверло с принудительной подачей
Колонковые сверла при работе устанавливают на распорных трубках, колонках (рис. 2.26) или манипуляторах (рис. 2.27). Манипуляторы позволяют оперативно, с высокой долей механизации обеспечить подъем и спуск бурильной машины, и фиксированную ее установку в необходимом положении при
|
обуривании забоя выработки. |
||
|
Принципиальная |
схема бурения |
|
|
шпура колонковым сверлом (например, |
||
|
сверлом ЭБГП1) заключается в сле- |
||
|
дующем (рис. 2.28). В исходном поло- |
||
|
жении буровая штанга с резцом выдви- |
||
|
нута из траверсы на 0,9 м и подведена к |
||
Рис. 2.26. Колонковое сверло |
забою. |
Шпиндель |
удерживается в |
крайнем |
левом положении и может |
||
|
60 |
|
|
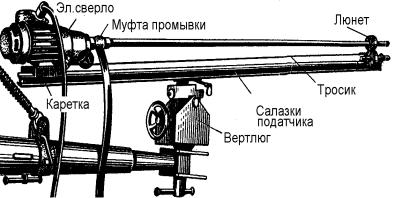
свободно вращаться относительно патрона.
Рис. 2.27. Манипулятор для установки электросверла
Далее включается подача, и штоки гидроцилиндров начинают перемещать траверсу в направлении забоя (бурение I). При выдвижении штоков и рабочем вращении шпинделя буровая штанга без вращения подается вперед до соприкосновения резца с породой. После этого шпиндель под действием напорного усилия жестко соединяется с патроном. При этом штанге с резцом сообщается вращение: она начинает внедряться в породу.
После того как шпур пробурен на глубину, равную ходу подачи (0,9 м), траверса отводится в исходное положение. При этом патрон и буровая штанга не вращаются (отсутствует напорное усилие со стороны забоя).
При отводе траверсы в исходное положение с заторможенной буровой штангой она вместе с винтовым упором на ее хвостовике выдвигается из шпинделя. Буровая штанга при этом остается в шпуре, т. е. происходит ее перехват. Винтовой упор в шпинделе занимает новое положение.
Далее повторяют бурение шпура (бурение II, III) прежним способом еще на глубину 0,9 м. При втором перехвате шпур добуривают до полной глубины — 2,2 м.
После этого реверсируют электродвигатель (вместе с ним и насос), траверса отводится в исходное положение, шпиндель при этом вращается в противоположном направлении. Винтовой упор будет ввинчиваться по резьбе в шпиндель, т. е. буровая штанга будет вытягиваться из шпура и втягиваться в шпиндель. Затем при помощи рукоятки управления золотником сообщают траверсе осевое движение в направлении от забоя и тем самым буровую штангу выводят полностью из шпура.
61
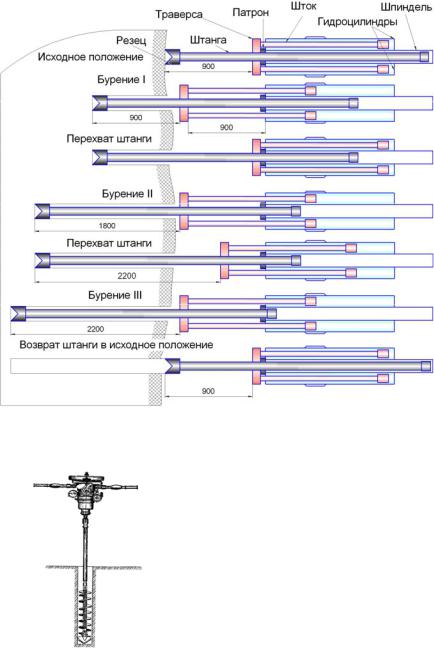
Рис. 2.28. Принципиальная схема бурения шпура колонковым сверлом ЭБГП1
Бурильные машины с бензиновым двигателем. Использование элек-
|
трических, пневматических или гидравличе- |
|||
|
ских бурильных машин возможно при нали- |
|||
|
чии энергетических источников |
достаточной |
||
|
мощности, между тем в ряде случаев горно- |
|||
|
разведочные работы в поисковых и разведоч- |
|||
|
ных партиях проводятся при отсутствии энер- |
|||
|
гоисточников. При этом ручное бурение шпу- |
|||
|
ров для взрывной отбойки может быть заме- |
|||
|
нено бурением машинами, имеющими не- |
|||
|
большие бензиновые двигатели. |
|
||
|
Для вращательного бурения небольших |
|||
|
скважин |
шнеками |
при |
инженерно- |
Рис. 2.29. Мотобур |
геологических исследованиях, |
применяются |
||
|
62 |
|
|
|
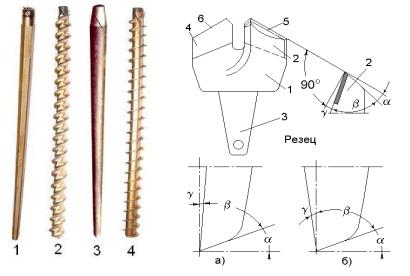
мотобуры М-1, МП-1 и ДС-1 (рис. 2.29), представляют собой сверла с бензиновым двигателем, и могут с успехом использоваться для бурения шпуров
впородах до V категории по буримости.
Инструмент для бурения шпуров вращательным способом. Буро-
вым инструментом для вращательного бурения шпуров являются буры, состоящие их штанги и резца. Штанга имеет хвостовик, которым ее вставляют
впатрон (шпиндель) РС.
Штанги для вращательного бурения шпуров предназначены для передачи закрепленному на них буровому резцу осевого усилия и крутящего момента от шпинделя РС (рис. 2.30): 1 - шестигранные для бурения с продувкой, промывкой шпуров; 2 - витые цельнотянутые; 3 - круглые; 4 - витые полые для бурения шпуров, как с продувкой (промывкой), так и без, а также для удаления штыба из шпура в процессе бурения.
Резцы для вращательного бурения шпуров имеют различную конст-
рукцию, которая зависит от условий бурения. Их изготавливают из быстрорежущей стали или обычной углеродистой стали и армируют пластинками твердого сплава ВК-6, ВК-8 и др., а также пластинами алмазного композиционного термостойкого материала (АКТМ).
Резец состоит из корпуса 1 (рис. 2.31), перьев 2 и хвостовика 3. Перья имеют переднюю 4 и заднюю 5 грани лезвия 6.
Рис. 2.30. Штанги для вращаРис. 2.31. Перья резца с положительным
тельного бурения шпуров (а) и отрицательным (б) углами заточки
63
Резцы бывают угольные и породные. Отличаются они длиной и толщиной перьев, углами заострения ( , ) (рис. 2.31, а ,б) и величиной рас-
сечки между перьями. Резцы, применяемые для бурения по углю и мягким породам, имеют большую рассечку и длину перьев и меньший угол заострения . Породные резцы имеют короткие перья, меньшую рассечку и
большой угол , что повышает его прочность. При увеличении крепости породы увеличивается угол заострения , уменьшается задний и передний углы и . Угол в крепких породах получает отрицательное значение, т.е. расположен левее осевой линии (рис. 2.31, б).
Некоторые типы и внешний вид резцов показаны на рис. 2.32.
Резцы угольные типа РУ15 предназначены для вращательного бурения шпуров ручными пневмо, гидро и электросверлами по мягким и средней крепости углям и мягким (слабым) породам не имеющих твердых включений ( f =4-6). Резцы имеют клиновидный хвостовик с отверстием
для шплинтования. Для резцов характерно наличие большого диаметра раствора (разрыва между перьями) и удлиненных перьев, что способствует снижению усилия подачи. Благодаря V-образному раствору режущего типа резцы хорошо работают по вязким малоабразивным породам.
Резцы породные РП-42 предназначены для вращательного бурения шпуров в крепких породах при f до 8. Конструкция резцов позволяет рабо-
тать с повышенными скоростями бурения. Соединение резца со штангой – конусное.
Резцы РШ181 предназначены для вращательного бурения шпуров для различного технологического назначения в породах с коэффициентом
крепости f до 8 с помощью буровых установок и ручных сверл. Резцы
имеют хвостовик с наружной метрической резьбой для соединения со штангой.
Резцы алмазные PSH140 (РШ140) предназначены для вращательного бурения с промывкой шпуров в твердых, монолитных породах с коэффи-
циентом крепости f до 16. Конструктивными особенностями резцов явля-
ются: четырехперая форма с алмазными пластинами; округлая форма режущих кромок для повышенной прочности резца; твердосплавные вставки на юбке резца для повышения сопротивления истиранию. Соединение резцов со штангой – конусное; в корпусе имеется отверстие для промывки.
Алмазные резцы РШ183 предназначены для вращательного бурения шпуров под анкерное крепление в породах с коэффициентом крепости f до
12 с помощью буровых установок и ручных сверл. Имеют хвостовик с наружной метрической резьбой для соединения с буровой штангой.
64
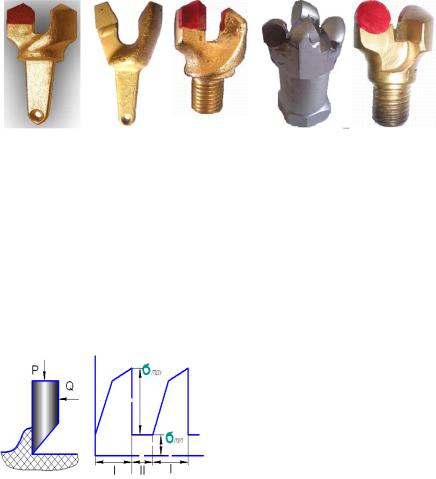
Резец пород- |
Резец уголь- |
Резец |
Резец алмазный |
Алмазный |
ный РП-42 |
ный РУ15 |
РШ181 |
PSH140 |
резец РШ183 |
|
|
|
(РШ140) |
|
|
Рис. 2.32. Внешний вид резцов для бурения шпуров |
|
Механизм разрушения пород при вращательном бурении шпуров заключается в следующем (рис. 2.33). Под непрерывным действием силы Р (осевое усилие), создающей поступательное движение, резец углубляется в породу, раздавливая ее под лезвием, а под действием силы Q , создаю-
щей вращательное движение, резец срезает стружку породы. Разрушенная порода выдается из шпура, например, витковыми спиральными буровыми штангами.
При вращательном способе бурения порода разрушается главным образом скалыванием и, в незначительной мере – смятием. Элементарный цикл разрушения характеризуется
двумя периодами:
I – формирование перед режущей гранью главной величины давления без существенного продвижения резца. В этот период усилие на лезвии и потребляемая мощность станка увеличиваются до
Рис. 2.33. Схема разрушения породы при |
max . |
|
|
II |
– период скола главного |
||
вращательном бурении |
|||
объема элемента разрушаемой поро- |
|||
|
ды. При этом, сопротивление породы и потребляемая мощность резко снижаются до min Резец проходит не-
который участок до встречи с ненарушенной породой, нанося при этом удар по породе. Сопротивление движению резца снова быстро увеличива-
ется до max и цикл разрушения повторяется.
Для вертикального перемещения резца необходимо приложить силу, которая определяется по формуле
P (D d)tg ,
65
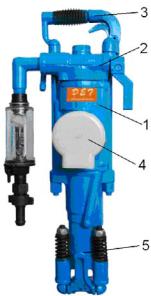
где 13 14 f 106 , Па – критическое сопротивление породы внедре-
нию; - глубина внедрения резца; D - диаметр резца; d - диаметр раствора перьев резца; - угол заострения лезвия; - передний угол заточки резца;
- угол, заключенный между задней гранью лезвия и основной плоскостью (задний угол заострения резца); a tg - ширина полосы раз-
давленной породы.
При заданных величинах Р и глубина внедрения резца рав-
на
|
P |
|
|
. |
|
D d tg |
Механическая скорость бурения V находится по формуле
V mn ,
где n – частота вращения снаряда; m - число лезвий резца.
Рис. 2.34. Внешний вид пневматического перфоратора YT28T, для бурения с пневмоподдержек
66
Ударно-поворотное буре-
ние шпуров осуществляется пневматическими перфораторами или бурильными молотками, которые имеют меньшую массу на единицу развиваемой мощности, невелики по габаритности и просты в обслуживании. Ими можно бурить шпуры в породах любой крепости как при проведении горных выработок и подземной разработке месторождений, так и при отбойке пород на карьерах небольшой производительности и вторичном дроблении негабарита.
Перфоратор (рис. 2.34)
включает корпус 1, механизм управления 2, рукоятку 3, виброгасящее устройство, глушитель шума 4, буродержатель 5. В корпусе 1 смонтированы ударно-поворотный механизм и воздухораспредели-
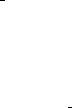
тельное устройство.
Ударно-поворотный механизм предназначен для нанесения порш- нем-ударником ударов по хвостовику бура и его поворота при обратном движении поршня-ударника.
Воздухораспределительное устройство предназначено для попере-
менной подачи сжатого воздуха в поршневую и штоковую полости цилиндра перфоратора.
Механизм управления предназначен для подвода сжатого воздуха к воздухораспределительному устройству. Включает кран, который имеет четыре положения – «Стоп», «Забуривание», «Работа», «Продувка».
Виброгасящее устройство предназначено для защиты бурильщика от вибрации. Состоит из рукоятки 3, соединенной с легкой сварной рамой, имеющей направляющие кронштейны. В трубах сварной рамы, как правило, расположены пружины с ползунами, ось которых проходит через отверстие
вприливе цилиндра перфоратора. В ряде перфораторов между направляющим кронштейном и упорными кольцами на трубах установлены две вспомогательные пружины.
Глушитель шума 4 представляет собой резиновую камеру, надетую на выхлопную горловину.
Буродержатель 5 предназначен для закрепления буровой штанги и соединен стяжными болтами со стволом.
Принцип работы пневматического перфоратора заключается в том,
что поршень-ударник под действием сжатого воздуха, поступающего от воздухораспределительного устройства, совершает возвратно - поступательные движения. При движении вперед он наносит удар по хвостовику штанги, при движении назад – проворачивает инструмент посредством храпового механизма и геликоидального винта.
При впуске сжатого воздуха в верхнюю часть цилиндра 4 (рис. 2.35), поршень-ударник 6, двигаясь в цилиндре вниз (рабочий ход), выталкивает воздух из нижней части цилиндра через выхлопное отверстие 5. Когда поршень перекроет выхлопное отверстие, воздух, оставшийся в нижней части цилиндра, сжимается и по каналу 9 в корпусе цилиндра, поступает в кольцевой канал 18, оказывая давление на клапан 11. Как только поршень при дальнейшем движении вперед откроет выхлопное отверстие 5, давление в цилиндре над поршнем 6 снизится и клапан 11 переместится вниз, перекрыв кольцевое отверстие 8.
Сжатый воздух начнет поступать в нижнюю часть цилиндра 3 по каналу 9. Поршень начнет движение вверх. После перекрытия поршнем выхлопного отверстия 5 воздух в верхней части цилиндра сжимается и давит на нижнюю поверхность клапана 11. Как только вновь откроется выхлопное отверстие 5, давление воздуха в нижней части цилиндра и, следовательно, над клапаном снизится. Клапан под воздействием избыточного давления в
67
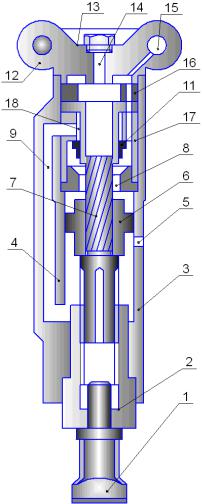
Рис. 2.35. Схема ручного перфоратора: 1 – долото; 2 – бур; 3 – корпус; 4 - цилиндр; 5 – выхлопное отверстие; 6 – поршень; 7 – геликоидальный стержень; 8 – кольцевое отверстие; 9 – канал; 11 - кольцевой клапан; 12 – рукоятка; 13 – крышка; 14 – промывная трубка;
15 – пусковой кран; 16 – храповое кольцо; 17 – направляющая втулка; 18 – кольцевой канал
68
камере над поршнем переместится в крайнее верхнее положение. Воздух снова начнет поступать в верхнюю часть цилиндра, и процесс повторится.
При впуске сжатого воздуха в нижнюю часть цилиндра поршень-ударник движется вверх (холостой ход). При этом он, двигаясь по канавкам стержня 7 поворотного устройства, поворачивается на некоторый угол. Одновременно поворачивается бур 2. При рабочем ходе система «пор- шень-бур» не поворачивается, а поворачивается геликоидальный стержень 7. В крайнем нижнем положении боек наносит удар по хвостовику бура. Под действием удара коронка бура внедряется в породу.
По принципу действия все перфораторы одинаковы и отличаются друг от друга конструкциями отдельных узлов и деталей.
Перфораторы делятся на переносные, телескопные и колонковые.
Переносные перфорато-
ры (рис. 2.36) предназначены для бурения шпуров в горизонтальных и наклонных выработках. Для облегчения труда бурильщиков при обуривании забоев горизонтальных и наклонных выработок эти перфораторы снабжают установочно–подающими пневматическими поршневыми поддержками (рис. 2.37).
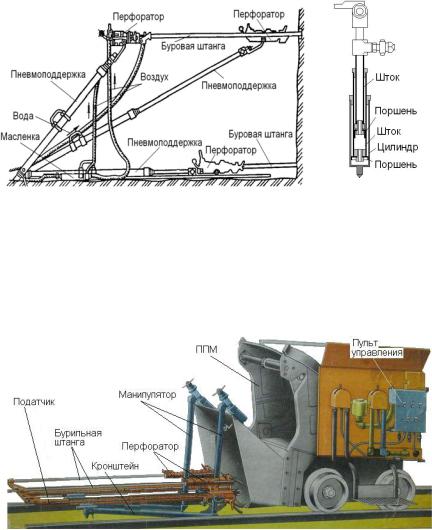
|
Рис. 2.37. Пневмати- |
|
Рис. 2.36. Схема установки переносного перфоратора на |
ческая поддержка: |
|
пневмоподдержке в забое горной выработке |
1 – шток; 2 – пор- |
|
шень; 3 - цилиндр |
||
|
В некоторых случаях переносные перфораторы размещаются на манипуляторах, которые механизируют перемещение в призабойном пространстве податчика с перфоратором. Манипуляторы крепят на погрузочных машинах (рис. 2.38), распорных стойках и т.д.
Рис. 2.38. Установка манипулятора на погрузочной машине
Достаточно часто используются стреловидные манипуляторы в составе легких буровых установках (УБЛ). Такие установки распространены при проходке горно-разведочных выработок сечением 4 м2 и более; в ряде случаев – для бурения шпуров под анкерную крепь. Для бурения шпуров глубиной до 2 м в горных выработках сечением до 5 м2 находит примене-
69
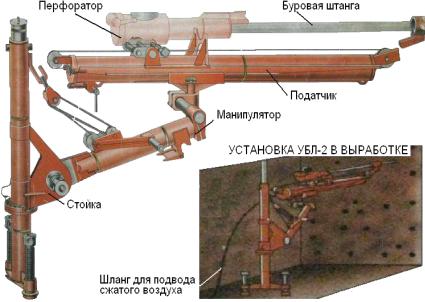
ние установка УБЛ-2 (рис. 2.39). При этом в выработках сечением свыше 5 м2 могут быть применены одновременно две установки.
Рис. 2.39. Легкая буровая установка УБЛ-2
Телескопные перфораторы (рис. 2.40 - 2.41). Применяют перфора-
торы для бурения восстающих шпуров под углом 450 и более. Они представляют собой конструктивное единое целое перфоратора и телескопного подающего устройства (пневматической поддержки) в виде выдвигающегося штока с поршнем (длина подачи до 650 мм, усилие подачи до 1600 Н). Телескопическая колонка, цилиндр и ствол перфоратора находятся на одной оси и соединяются между собой стяжными болтами. При поступлении сжатого воздуха в камеру поршня податчика цилиндр подачи вместе с бурильным молотком поднимается вверх, создавая осевое давление на забой шпура. Включение и выключение, как самого перфоратора, так и телескопной колонки производится рукояткой пускового крана.
Колонковые перфораторы (рис. 2.42) используют для бурения шпуров и скважин в крепких породах в горизонтальных выработках. Их устанавливают на специальных распорных колонках (стойках), манипуляторах или каретках. Подача на забой - принудительная автоматическими винтовыми, реечными, канатными и гидравлическими податчиками.
70
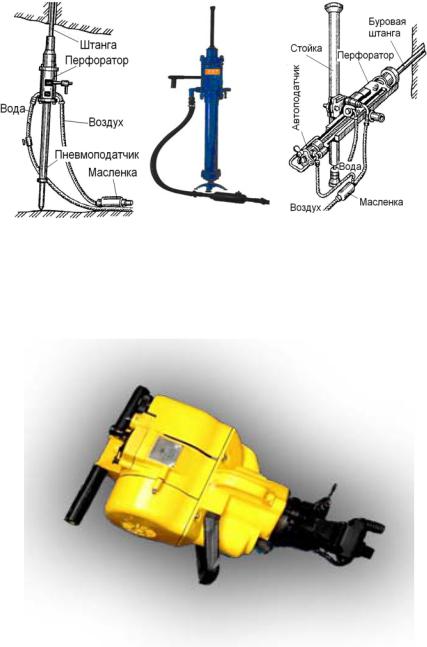
Рис. 2.40. Схема уста- |
Рис. |
2.41. Внешний |
Рис. 2.42. Схема установ- |
|
новки |
телескопного |
вид |
телескопного |
ки колонкового перфора- |
перфоратора |
перфоратора YSP45 |
тора |
Перфоратор YN27A с бензиновым двигателем (рис. 2.43) предна-
значен для ударно-поворотного бурения шпуров диаметром 28 – 43 мм, глубиной до 6 м, разрушения и дробления горной породы, бетона, кирпичной кладки, асфальта и других материалов.
Рис. 2.43. Внешний вид бензиновый перфоратора YN27A
71
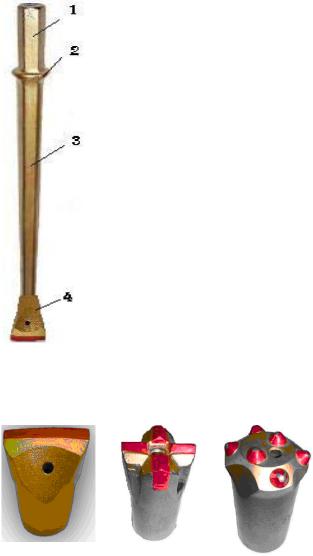
Инструментом для бурения шпуров ударно-поворотным способом
являются буры с головками или чаще со съемными коронками. При этом буры могут быть цельными или составными.
|
В общем случае бур представляет собой стер- |
|||||
|
жень, изготовленный из пустотелой буровой стали |
|||||
|
шестигранного или круглого сечения диаметром 22 – |
|||||
|
32 мм. Он состоит из головки или съемной коронки 4 |
|||||
|
(рис. 2.44), стержня (штанги) 3 с буртиком 2 и хвосто- |
|||||
|
виком 1. Хвостовик воспринимает удары поршня бу- |
|||||
|
рового механизма, а головка бура или коронка воздей- |
|||||
|
ствует на породу, разрушая ее. Головка бура или съем- |
|||||
|
ная коронка армируется пластинкой твердого сплава. |
|||||
|
Коронка соединяется со штангой с помощью резьбы |
|||||
|
или гладкого конуса. Осевой канал бура с отверстиями |
|||||
|
в коронке имеет диаметр 7 – 9 мм и предназначен для |
|||||
|
подачи воды на забой шпура при бурении с промывкой |
|||||
|
или сжатого воздуха при бурении с продувкой. При |
|||||
|
бурении с пылеотсосом диаметр осевого канала при- |
|||||
|
нимают 12 мм. Буры изготовляются из легированной |
|||||
|
стали с последующей поверхностной закалкой. |
|
||||
|
Съемные коронки, армированные твердым, спла- |
|||||
|
вом получили наиболее широкое применение в горной |
|||||
|
промышленности. Коронки имеют отверстия для про- |
|||||
|
мывки, продувки или отсоса пыли из шпура. Выбор |
|||||
|
типа бура и коронок зависит от физико-механических |
|||||
|
свойств горных пород и условий бурения. |
|
|
|||
Рис. 2.44. Бур для |
Наибольшее |
распространение |
имеют |
коронки |
||
однодолотные, (рис. 2.45), крестовые (рис. 2.46) и шты- |
||||||
ударно - поворотно- |
ревые (рис. 2.47). Коронки армируют вставками (пла- |
|||||
го бурения |
||||||
стинками) из твердых сплавов. Угол заточки лезвия со- |
||||||
|
||||||
|
ставляет 90 - 120 (меньший угол для более мягких по- |
|||||
|
|
|
род). |
Коронки |
||
|
|
|
применяются |
|||
|
|
|
при |
бурении |
||
|
|
|
шпуров |
пере- |
||
|
|
|
носными перфо- |
|||
|
|
|
раторами с энер- |
|||
|
|
|
гией удара |
до |
||
|
|
|
90-120 Дж в |
|||
|
|
|
крепких |
и весь- |
||
Рис. 2.45. Однодо- |
Рис. 2.46. Кре- |
Рис. 2.47. Шты- |
ма крепких |
мо- |
||
лотная коронка |
стовая коронка |
ревая коронка |
нолитных |
гор- |
ных породах вы-
72

сокой абразивности. Соединение коронок со штангой – конусное.
Механизм разрушения пород при ударно-поворотном бурении шпу-
ров. Ударно-поворотный способ бурения заключается в том, что инструмент клиновидной или другой формы внедряется в породу под действием значительной по величине, но кратковременной динамической нагрузки, направленной по оси инструмента Руд (рис. 2.48). Осевое усилие незначительно и обеспечивает в момент удара только контакт инструмента с породой. При
ударе, лезвие внедряется в породу на глубину h . После каждого удара вследствие упругости инструмента и породы, а также незначительного осевого усилия инструмент отскакивает от забоя и бур специальным механизмом машины поворачивается на некоторый угол 15 30о . Вновь нано-
сится удар. При этом лезвие, внедряясь в породу, делает в ней новую бороздку вблизи от первой и т.д. Этим обеспечивается обработка забоя по всей площади. На начальной стадии внедрения долота формируется зона 1, в объеме которой порода находится в тонкоизмельченном состоянии. За пределами этой зоны образуется зона трещиноватости 2, в которой криволинейными трещинами порода разбита на отдельности неправильной формы. У свободной поверхности зона трещиноватости проявляется в форме скола отдельных элементов. Толщина зоны трещиноватости и размеры зоны скола определяются свойствами породы, энергией удара, скоростью приложения нагрузки, размерами и формой инструмента.
При повороте лезвия инструмента на 180о за чис-
|
ло ударов |
no 180 порода |
||||||
|
|
|
|
|
|
|
|
|
|
забоя разрушается на вели- |
|||||||
|
чину h |
|
|
|
|
|
||
|
|
P cos |
sin |
|
|
|||
|
h |
|
2 |
|
2 |
|
, м |
|
|
|
|
|
|
|
|||
|
|
|
|
|||||
|
|
2 D sin |
2 |
|
|
|||
|
|
|
|
|
|
|
||
|
где P – сила удара |
|||||||
Рис. 2.48. Схема разрушения породы при |
бура, Н; D - диаметр бура, |
|||||||
м; - сопротивление по- |
||||||||
ударно-поворотном способе бурения |
||||||||
роды сжатию, Па; |
- угол |
|||||||
|
приострения лезвия; - угол внутреннего трения породы.
При известном числе ударов n , углубка шпура hш составляет вели-
чину
73
hш hn , м no
Механическая скорость бурения молотками, можно определить по эмпирической формуле
Vм |
13,4 A n |
, м/с |
|
60 d 2 0,59 |
|||
|
|
где А – энергия удара поршня, Дж; n - частота ударов поршня, Гц;- предел прочности породы на сжатие, МПа 10 ; d - диаметр шпура, мм.
При ударно-поворотном бурении, большая часть горной породы разрушается под действием сжимающих нагрузок при вдавливании лезвия в породу, и лишь незначительная часть подвергается разрушению скалыванием (противоположно тому, что имеет место при вращательном бурении).
Так как сопротивление породы сжатию в 7-10 раз больше чем сдвигу, то и удельные энергетические затраты при ударном бурении значительно больше, чем при вращательном (в породах средней и ниже средней крепости, где применимо вращательное бурение).
Установки для бурения шпуров. Для механизации бурения шпуров и повышения производительности бурения широкое применение получили бурильные установки. Такая установка представляет собой бурильную машину, состоящую из бурильной головки с подающим механизмом (податчиком), установленную на гидрофицированном манипуляторе на тележке. Установка позволяет одной штангой бурить в необходимом направлении шпуры на глубину до 4 м.
Структурная схема бурильной установки приведена на рис. 2.49. Установка состоит из: механизма перемещения 1 (ходового устройства), который может быть колесно-рельсовым, гусеничным или пневмошинного типов. Как правило, выполняются в виде самостоятельного органа – чаще всего тележки. Привод механизмов перемещения может осуществляться от электро-, пневмоили дизельных двигателей; привода исполнительного органа 2 и 3 в виде бурильной головки вращательного или вращательноударного бурения. Рациональная область применения первых - породы крепостью до 8 по шкале проф. М.М. Протодьяконова, вторых - породы крепостью 8-15.
Бурильные головки состоят из приводного двигателя 2 (электрического, пневматического или гидравлического), редуктора, ударного устройства 3; штанги (круглого витого и шестигранного сечения) с резцом 4; манипулятора 6, который предназначен для размещения, пространственных перемещений, установки и удержания в требуемом положении податчика с бурильной головкой; податчика 7, который служит для перемещения бурильной головки относительно стрелы 5 на забой, с заданным осевым уси-
74
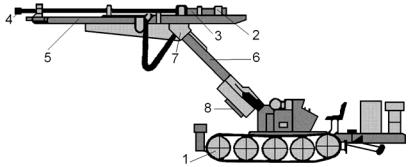
лием, требуемой скоростью подачи, и отвода головки в исходное положение после окончания бурения.
Податчики могут иметь постоянную длину и быть телескопическими. Первые используются когда линейные размеры выработки превышают длину податчика, вторые - позволяют обурить забой выработки с полной раздвижностью податчика, а кровлю и бока выработки - укороченными шпурами с помощью сложенного податчика.
В качестве привода податчиков используют пневмоили гидродвигатели. Ход податчика может быть от 2 до 4,5 м, усилие подачи 1,5-20 кН, скорость подачи бурильной головки при бурении до 0,3 м/с, а при обратном ходе -от 0,2 до 0,4 м/с. Кронштейн 8 для установки податчика выполняется шарнирным с обеспечением свободы как в вертикальной, так и в горизонтальной плоскостях, с помощью гидроцилиндров, которые в составе системы гидропривода установки, обеспечивающих необходимое число степеней свободы при пространственных перемещениях податчика 7 с бурильной головкой.
Для бурения шпуров установка выставляется в выработке и фиксируется. При помощи манипулятора податчик выставляется в точку бурения под необходимым углом. Включается буровая головка (вращение) и производится бурение шпура, путем перемещения буровой головки на забой посредством податчика.
Рис. 2.49. Общая структурная схема бурильной установки
Конструкция электрической бурильной установки БУЭ1М (рис. 2.50). Бурильная установка БУЭ1М предназначена для бурения шпуров и выбуривания угля при проведении горизонтальных выработок, преимущественно однопутного сечения от 6 до 13 м2 в свету, по породам с коэффициентом крепости до 16 в шахтах, опасных по газу и пыли.
Бурильная установка БУЭ1М выпускается в двух исполнениях: с бурильной головкой вращательного действия для бурения шпуров по породам
75
крепостью f = 4 ÷ 8 (три частоты вращения шпинделя — 151, 317 и 731 об/мин) и вращательно-ударного - для пород крепостью f = 6 ÷ 16, при этом бурильная установка может работать и во вращательном режиме (две частоты вращения шпинделя — 144 и 375 об/мин). Выбуривание угля производится установкой в подготовительных выработках со смешанными угольным и породным забоями, в которых применение взрывных работ по углю запрещается.
Установка БУЭ1М состоит из бурильной машины с бурильной головкой 1, установленной на конце стрелы, манипулятора 6, рамы-бака 7 для масла, шасси 8, гидросистемы с пультом управления 9, электрооборудования 10, сиденья 11 для машиниста, буфера 12. Бурильная машина, в свою очередь, состоит из бурильной головки 1 с электродвигателем мощностью 7,5 кВт и редуктором 2, буровой штанги 3, податчика 4 с гидроцилиндрами
инаправляющей рамой. При выбуривании угля скважинами диаметром 300
ммпредусмотрена установка штанги с коронкой 5, оснащенной резцами, вместо штанги для бурения шпуров.
Для бурения шпура в патрон бурильной головки вставляется хвостовик штанги с резцом на конце. Патрон удерживается двумя выступами. Через муфту боковой промывки и отверстие в хвостовике подводится вода под давлением, которая далее по осевому каналу в штанге поступает на забой для промывки шпура.
Бурильная головка на забой подается гидроцилиндровым механизмом подачи.
Манипулятор гидрофицирован, что позволяет выполнять следующие операции: вращение стрелы манипулятора вместе с бурильной машиной
относительно продольной оси па угол 180°; подъем стрелы в вертикальной плоскости и поворот в горизонтальной при помощи двух гидроцилиндров; подъем и поворот бурильной машины относительно манипулятора посредством гидроцилиндров в вертикальной и горизонтальной плоскостях;перемещение направляющей балки податчика по кронштейну манипулятора гидроцилиндром надвигания.
От электродвигателя (мощностью 7,5 кВт) через редуктор приводится в действие насос гидросистемы.
Передвижение бурильной установки по рельсовому пути осуществляется приводом хода, который состоит из гидромотора и трехступенчатого редуктора.
Шасси служит основанием бурильной установки и состоит из рамы, к которой на полуосях крепятся правая и левая ходовые тележки. На тележках смонтированы ходовые колеса, рельсовые захваты и четыре маневровых катка, попарно на каждой тележке. С помощью двух гидроцилиндров, тележки могут быть раздвинуты или сдвинуты относительно рамы шасси с учетом размеров колеи (600— 900 мм). Благодаря этому в транспортном по-
76
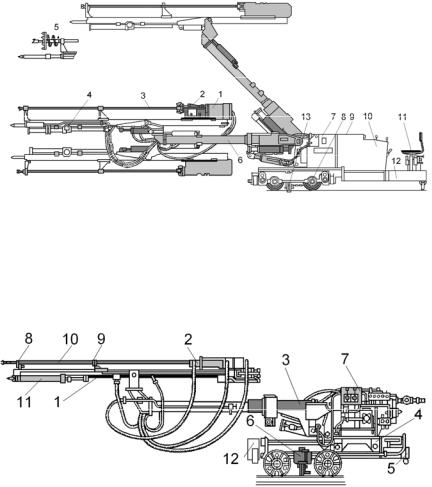
ложении бурильная установка занимает небольшую ширину (600 мм), что имеет существенное значение в горных выработках малого сечения.
Рис. 2.50. Конструкция установки БУЭ1М
Конструкция пневматической бурильной установки БУ1М (рис. 2.51). Пневматическая бурильная установка БУ1М вращательно-ударного действия предназначена дли бурения шпуров по породе с коэффициентом крепости f = 6 ÷ 16 при проведении горизонтальных горных выработок сечением от 6 до 20 м2.
Рис. 2.51. Конструкция бурильной установки БУ1М
Бурильная установка БУ1М состоит из винтового автоподатчика 1; одной пневматической бурильной головки 2 вращательно - ударного действия; манипулятора 3; верхней тележки 4; нижней тележки 5; двух рельсовых захватов 6; маслостанции с пультами гидравлического и пневматического
77
управления 7; неподвижного люнета 8; подвижного люнета 9; буровой штанги 10 с коронкой; двух пневматических упоров 11.
Перед началом бурения тележка 5 закрепляется с помощью рельсовых захватов и боковых опор, распираемых в стенки выработки. Перемещение буровой головки по забою и удержание ее в заданном положении производится манипулятором, который установлен на верхней тележке и имеет пневматическое управление. Кроме того, имеются два пневматических упора 11, расположенных на конце стрелы; они упираются в забой и придают машине устойчивость при забуривании. Пульт управления расположен на верхней тележке. Бурение ведется с боковой промывкой шпуров. Бурильная установка имеет устройство, позволяющее перекатывать ее на соседний путь в двухпутевой выработке.
Особенностью машины БУ-1М является применение вращательноударного способа бурения, при котором для разрушения породы одновременно используется энергия удара, крутящий момент и осевое усилие. Из-за значительной величины крутящего момента, вращение бура осуществляется от отдельного привода (вращателя) (шестеренный пневмодвигатель мощностью 3,7 кВт) несвязанного с ударным механизмом.
Приводом винтового податчика служит шестеренный пневмодвигатель мощностью 18,4 кВт, работающий совместно с двухступенчатым цилиндрическим редуктором.
Вращение манипулятора вокруг своей оси осуществляется шестеренным пневмодвигателем мощностью 18,4 кВт через червячный редуктор.
Для управления манипулятором в вертикальной и горизонтальной плоскости используются два гидроцилиндра, которые получают питание от маслостанции. Приводом маслостанции служит шестеренный пневмодвигатель мощностью 18,4 кВт.
Третий гидроцилиндр предназначен для надвигания верхней тележки относительно нижней.
Установка Boomer/Rocket Boomer 280 c транспортной базой DC15
иDC16, и установочной мощностью 55 кВт (рис. 2.52), разработанная компанией Атлас Копко применяется для бурения шпуров в штольнях и шахтах
сгидравлической системой управления вращением подъема и ударов. Конструктивно установка включает: 1 – буровой станок; 2 – подат-
чик; 3 – телескопическая буровая стрела; 4, 5 – передняя и задняя опоры; 6 – кабельный барабан; 7 – барабан водяного шланга; 8 – защитная крышка; 9, 10 – задний и передний цилиндры стрелы; 11 – цилиндр наклона податчика; 12 – цилиндр выноса податчика; 13 – вращатель; 14 – панель управления буровым агрегатом; 15 – люнет средний.
При работе буровая установка закрепляется в выработке гидродомкратами.
78
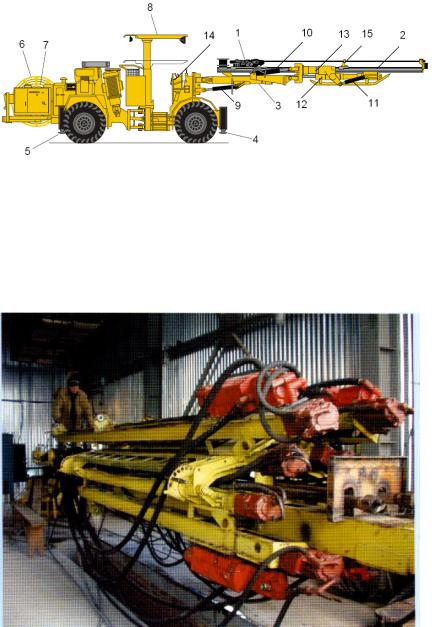
Рис. 2.52. Установка B/RB с транспортной базой DC15 и DC16:
В вертикальных стволах шахт для механизированного бурения шпуров и скважин применяются подвесные каретки, выполненные в виде рамы, закрепленной в забое домкратами, с установленными на ней манипуляторами, автоподатчиками и бурильными молотками.
При проходке стволов бурильными установками (каретками) типа БУКС шпуры бурят тяжелыми ручными перфораторами (2-4 перфоратора) (рис. 2.53). После обуривания забоя рама поднимается к подвесному полку.
Рис. 2.53. Бурильная установка БУКС-1м (в сборочном цехе)
79
В бурильных каретках применяются длинноходовые, канатнопоршневые, цепные или винтовые податчики, позволяющие бурить шпуры глубиной до 3,5 м и более одним длинным буром. При работе буровой каретки в забое электроэнергия к ней подается по кабелю, вода и сжатый воздух по шлангам.
2.6. Уборка породы в горных выработках
Порода, отделенная от массива, должна быть выдана на поверхность, или удалена из призабойного пространства. Работы по уборке горной массы связаны с погрузочными и транспортными операциями, которые выполняют различными способами с использованием разнообразных машин и оборудования.
Погрузка породы - процесс перемещения взорванной (отбитой) горной массы в средства транспорта (подъема) является одним из основных технологических процессов при проведении подземных горных выработок и занимает до 50-70% времени в цикле проходки выработок. В горизонтальных и наклонных горных выработках этот процесс осуществляется: скреперными установками; породопогрузочными машинами; погрузочнодоставочными машинами; вручную. В вертикальных горных выработках погрузка производится: погрузочными машинами с грейферным забирающим ковшом или вручную.
Перемещение горной породы по горизонтальным или наклонным (до 30о) горным выработкам называется в общем случае транспортировкой, а при использовании колесных транспортных средств – откаткой.
Перемещение горной породы вниз по наклонным (свыше 30о) и вертикальным горным выработкам называется спуском, а вверх до поверхности или до вышележащего горизонта расположенных выработок – подъемом. Процесс перемещения грузов по стволам шахт называют шахтным подъе-
мом.
При проведении разведочных канав, траншей и шурфов транспортировка горных пород из забоев на поверхность может не выделяться в самостоятельную операцию, а совмещаться с их отбойкой, например, при проведении разведочных канав с помощью канавокопателя или скрепера.
В целом, комплекс операций, предназначенных для перемещения горных пород из выработок на поверхность или в другие горные выработки, на горных предприятиях носит название рудничного транспорта.
Перемещение горных пород на поверхности от устья ствола или штольни до складов, погрузочных устройств или отвалов называют поверх-
ностным транспортом.
80
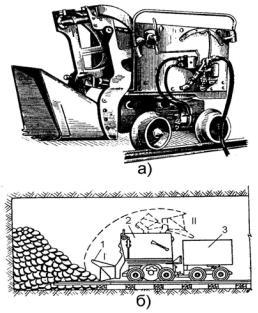
Основные сведения об оборудовании для погрузки породы в горных выработках.
Механизированная погрузка породы при проведении горизонталь-
ных и наклонных выработок выполняется погрузочными машинами и скреперными установками.
По характеру работы погрузочного органа, погрузочные машины подразделяются на машины периодического и непрерывного действия. Отечественные погрузочные машины периодического действия имеют погрузочный орган в виде ковша, а непрерывного действия – в виде двух парных нагребающих лап. По направлению захвата (зачерпывания) погружаемой массы различают машины с нижним, боковым и верхним захватами.
Погрузочные машины имеют колесно-рельсовую или гусеничную ходовую часть.
Ковшовые погрузочные машины успешнее, чем машины непрерывного действия, работают при погрузке крепких, крупнокусковых, неравномерно раздробленных и тяжелых горных пород. Машины непрерывного действия являются более производительными, чем машины периодического действия, но их целесообразнее применять при погрузке пород некрепких,
средней крепости и хорошо раздробленных.
Рис. 2.54. Погрузочная машина периодического действия:
а) - общий вид; б) - схема работы
81
Погрузочные машины периодического действия по способу передачи груза на транспортное средство делятся на машины прямой и сту-
пенчатой погрузки. Машина прямой
погрузки с нижним за-
хватом (ППН) (рис. 2.54)
состоит из механизма перемещения, поворотной платформы с механизмом поворота, погрузочного органа и механизма подъема ковша. Механизм перемещения машины (ходовая часть) состоит из массивной рамы, пневматического или электрического двигателя и двух пар колес для передвижения по рельсовому пути.
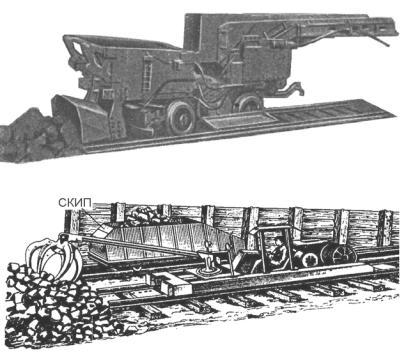
Погрузочный орган представлен ковшом, укрепленным на двух кулисах, и
механизмом подъема ковша.
Процесс погрузки породы погрузочной машиной включает следующие операции (рис. 2.54, б). Шахтную вагонетку 3 прицепляют к хвостовой части машины. Перед зачерпыванием породы машина 2 вместе с прицепленной вагонеткой отходит от отвала породы на 1—2 м для разгона, после чего ковш 1 опускается на почву выработки, и в таком положении машина совершает ход вперед. При движении вперед ковш внедряется в отвал породы, одновременно с внедрением ковша в породу включается механизм подъема ковша. Дальнейший подъем ковша происходит до опрокидывания его через верх, когда порода высыпается в вагонетку. Верхняя часть машины с механизмом подъема ковша может поворачиваться в обе стороны на 30° от осевой линии, чем обеспечивается увеличение фронта погрузки породы.
У машин ступенчатой погрузки с нижним захватом (рис. 2.55) раз-
грузка ковша производится не непосредственно в вагонетку, а в бункер, из которого порода поступает на конвейер и затем в вагонетку.
Рис. 2.55. Погрузочная машина 2ППН-5
Рис. 2.56. Погрузочная машина для проходки уклонов и наклонных шахтных стволов (КНС-1)
82
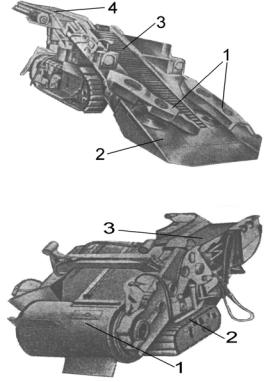
Для погрузки горной массы в двухпутных уклонах и стволах, проходимых с уклоном до 55о, используется погрузочная машина (рис. 2.56), которая в зависимости от угла наклона, крепости и кусковатости пород может быть оборудована съемным многолопастным грейфером, прямой или обратной лопатой. Рабочий орган зачерпывает породу в забое, и вместе с машиной перемещается вдоль пути к месту разгрузки в скип, стоящий на другом пути.
|
Машина |
|
непре- |
||
|
рывного действия боко- |
||||
|
вого захвата (ПНБ) с за- |
||||
|
гребающими |
|
лапами |
||
|
(рис. 2.57) состоит из |
||||
|
забирающего |
механиз- |
|||
|
ма, скребкового пере- |
||||
|
грузочного |
конвейера, |
|||
|
ленточного |
транспорте- |
|||
|
ра, гусеничного хода, |
||||
|
гидравлической |
|
уста- |
||
|
новки, |
электрооборудо- |
|||
Рис. 2.57. Погрузочная машина непрерывного дей- |
вания и пульта управле- |
||||
ствия бокового захвата (ПНБ-3) |
ния. Загребающие лапы |
||||
|
и скребковый |
перегру- |
|||
|
зочный конвейер приво- |
||||
|
дятся в движение в од- |
||||
|
них моделях обособлен- |
||||
|
ными двигателями, а в |
||||
|
других—через редукто- |
||||
|
ры от одного двигателя. |
||||
|
Ленточный транспортер |
||||
|
предназначается |
для |
|||
|
транспортировки горной |
||||
|
массы |
от |
скребкового |
||
Рис. 2.58. Погрузочная машина непрерывного дей- |
конвейера машины в ва- |
||||
гонетки. |
|
|
|
||
ствия нижнего захвата |
Процесс погрузки |
||||
|
|||||
|
породы |
состоит |
в сле- |
дующем. Два рычага-лапы 1 загребают породу на наклонный полок 2 и дальше на желоб приемного цепного скребкового конвейера 3; далее порода перемещается ленточным конвейером 4, и ссыпается в вагонетку. Конвейер может подниматься и опускаться до требуемой высоты, а также поворачиваться в стороны на угол до 45° от продольной оси, что позволяет осуществлять погрузку в вагонетки, стоящие на разных путях.
К погрузочным машинам непрерывного действия нижнего захвата
83
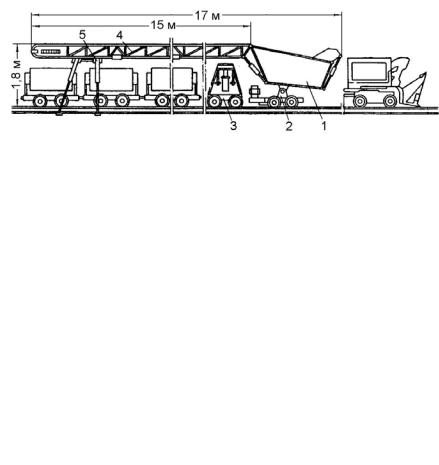
относятся машины с исполнительным органом 1 барабанно-лопастного типа (рис. 2.58). Они также перемещаются на гусеничном ходу 2 и осуществляют загрузку вагонетки с помощью ленточного перегружателя 3
Для уменьшения простоев машин и достижения большей производительности при погрузке породы применяют перегружатель (рис. 2.59). Перегружатель монтируется на колесном ходу и перемещается по рельсам, являясь промежуточным звеном между погрузочной машиной и основным транспортным средством. От погрузочной машины порода поступает в приемный бункер 1, расположенный на основной тележке 2, а из него по ленточному транспортеру, размещенному на портальной части (консоли) 4 – в состав, включающий пять – восемь вагонеток.
Рис. 2.59. Ленточный перегружатель ПЛ-3
Портальная часть во время передвижения из забоя (или в забой) опирается на вспомогательную тележку 3, на которой установлено два пневмоцилиндра. Во время уборки породы консоль поддерживается при помощи четырех телескопических опорных стоек 5.
При проведении выработок небольшой протяженности (до 100 м) с площадью сечения 2,7—4,0 м2 при уборке породы широко применяют скреперные установки. При их использовании исключается необходимость настилки рельсовых путей в горных выработках. Скреперная установка состоит из: скрепера (рис. 2.60 - 2.61), пневматической или электрической лебедки, головного (грузового) каната, прикрепляемого к передней части скрепера, хвостового каната, забойного и направляющего
роликов.
При работе скрепер совершает периодическое движение от забоя к месту разгрузки и обратно. К за-
Рис. 2.60. Внешний вид скреперов бою порожний скрепер перемещается хвостовым канатом. При движе-
84
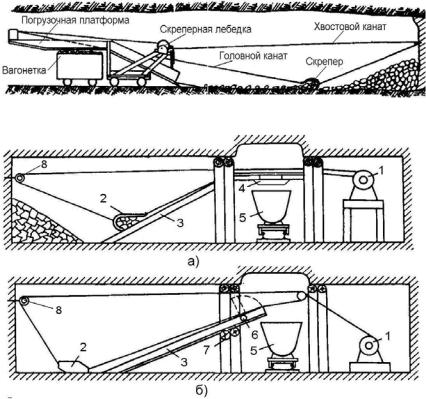
нии от забоя, с помощью головного каната скрепер, внедряясь в разрыхленную горную массу, самозагружается и доставляет ее волоком по почве выработки к месту разгрузки. Если погрузка породы осуществляется в вагонетку, то в состав установки входит также скреперный полок, под которым размещается загружаемая вагонетка.
Скреперные установки могут быть: передвижными (рис. 2.61), когда скреперные лебедки устанавливают на специальных платформах, смонтированных на колесах, которые подкатывают к забою перед каждой уборкой породы и отгоняют после окончания уборки породы в безопасное место; и переносными, (рис. 2.62), когда скреперные лебедки устанавливают на более или менее длительный срок на одном месте. При этом, как правило, переносные скреперные полки применяются при проведении рассечек.
Рис. 2.61. Схема передвижной скреперной установки
Рис. 2.62. Переносные скреперные полки: а) – неподвижный скреперный полок; б) – шарнирно откидывающийся полок; 1 - лебедка; 2 – скрепер; 3 – полок; 4 – разгрузочный люк; 5 – вагонетка; 6 – шарнир; 7 – брусья; 8 - забойный ролик
85
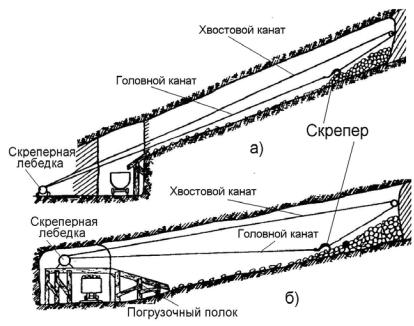
При скреперной погрузке породы через полок в вагонетку, полок сооружают таким образом, чтобы обеспечить удобство его перемещения в следующую рассечку, а также возможность доставки в забой рассечки необходимых материалов.
Погрузка породы в наклонных выработках в зависимости от угла наклона и направления проходки (снизу вверх или сверху вниз) выполняется в основе своей теми же техническими средствами, что и при проходке горизонтальных выработок. При углах наклона выработок (уклона, наклонного ствола) до 5-8о для погрузки породы возможно применение погрузочных машин с удерживающим приспособлением, чаще всего в виде дополнительной лебедки с канатом, предохраняющим машину от сползания в забой и облегчающим ее перемещение вверх.
Погрузка породы погрузочными машинами в наклонных выработках осуществляется в вагонетки или скипы, которые также перемещаются по выработкам с помощью лебедок и канатов.
Основным техническим средством механизированной уборки породы при проведении наклонных выработок являются скреперные установки, включающие скреперные полки, если уборка породы выполняется с перегрузкой ее в вагонетки или скипы.
Рис. 2.63. Проходка наклонной выработки со скреперной уборкой породы
86
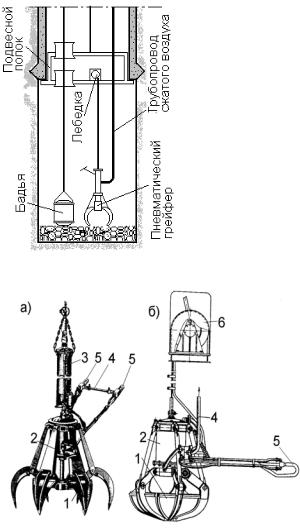
При проходке выработок при наклоне менее 35о взорванная (отбитая) порода доставляется до откаточного штрека скрепером. При этом скреперная лебедка устанавливается напротив проводимой выработки по одному из способов, показанных на рис.2.63.
Погрузка породы в вертикальных горных выработках производится пневматическими грейферными грузчиками и стволовыми породопогрузочными машинами.
|
|
Грейферы подвешиваются на высо- |
|||||||
|
те 12—15 м от забоя на канатах лебедок, |
||||||||
|
устанавливаемых на подвесном проходче- |
||||||||
|
ском полке, (рис. 2.64) или на поверхно- |
||||||||
|
сти. Перемещение подвешенного грейфера |
||||||||
|
по забою осуществляется вручную или с |
||||||||
|
помощью механизмов. |
|
|
|
|
|
|||
|
|
При проходке разведочных вырабо- |
|||||||
|
ток, |
характеризующихся |
|
ограниченной |
|||||
|
площадью сечения возможно применение |
||||||||
|
только легких, сравнительно небольших |
||||||||
|
размеров грейферных грузчиков с ручным |
||||||||
|
вождением (КС-3, ПГШ-15). |
|
|
груз- |
|||||
|
|
Пневматический грейферный |
|||||||
|
чик КС-3 (рис. 2.65, а) включает: шестило- |
||||||||
|
пастной грейфер 1; пневматический затвор |
||||||||
Рис. 2.64. Схема размещения |
2, служащий для открывания и закрывания |
||||||||
грейфера; пневматический |
подъемник |
3, |
|||||||
пневмопогрузчика в стволе |
|||||||||
|
|
|
для подъема грейфе- |
||||||
|
|
|
ра при выгрузке по- |
||||||
|
|
|
роды в бадью и опус- |
||||||
|
|
|
кания |
на |
забой для |
||||
|
|
|
зачерпывания |
поро- |
|||||
|
|
|
ды; водило 4 с орга- |
||||||
|
|
|
нами |
управления |
5 |
||||
|
|
|
пневмозатвором |
|
и |
||||
|
|
|
пневмоподъемником. |
||||||
|
|
|
|
Рабочий |
цикл |
||||
|
|
|
погрузки |
пневмати- |
|||||
|
|
|
ческим |
грейферным |
|||||
|
|
|
грузчиком |
состоит |
в |
||||
|
|
|
следующем. После |
||||||
|
|
|
взрывания |
шпуров, |
|||||
|
|
|
проветривания и при- |
||||||
Рис. 2.65. Грейферные пневмопогрузчики: |
ведения |
ствола |
шах- |
||||||
а) – КС-3; б) – ПГШ-15 |
|
ты в |
безопасное со- |
||||||
|
87 |
|
|
|
|
|
|
|
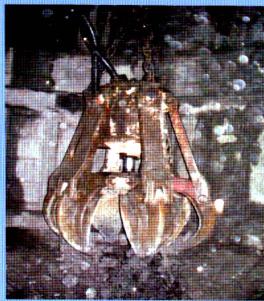
стояние грейферный грузчик опускают лебедкой к забою, и оставляют в подвешенном состоянии на расстоянии 1,5—2 м от породы. При помощи пневматического подъемника грейфер с раскрытыми лопастями опускается на разрыхленную взрывом породу и под действием собственного веса, внедряется в нее. Загрузка грейфера (захват породы) происходит в период закрытия лопастей усилием пневматического затвора. После зачерпывания породы грейфер при помощи пневматического подъемника поднимается на 1,0—1,5 м (в зависимости от высоты бадьи), и далее, используя водило 4, устанавливается над бадьей и, раскрыв лопасти, разгружает породу в бадью, после чего цикл повторяется. Продолжительность одного цикла составляет
30 - 40 с.
В отличие от КС-3 в пневмопогрузчике ПГШ-15 (рис. 2.65, б) отсутствует пневмоподъемник. Подъем и опускание грейфера во время работы осуществляются лебедкой 6, устанавливаемой на натяжной раме. Управление лебедкой дистанционное с водила грейфера.
Для полной механизации процесса погрузки породы в бадьи при проведении вертикальных стволов диаметром более 5,5, м применяется универсальная стволовая погрузочная машина КС-2у/40 (рис. 2.67). Применение этой машины полностью исключает тяжелый ручной труд при вождении грейферного грузчика по забою. При этом механизм вождения включает такие элементы как круговой монорельс, тележка поворота с пневмоприводом и тельфер с кареткой его радиального перемещения.
Рис. 2.66. Грейфер машины КС-2у/40
88
Универсальная машина КС-2у/40 выпускается в двух модификациях: с одним грейфером для стволов диаметром 5,5—6,5 м и с двумя грейферами для стволов диаметром 7—8 м. Машина КС-2у/40 имеет пневматический грейфер 1, подвешенный на канате к тельферу 2. Тельфер помещается в раме 3, которая одним концом шарнирно соединена с центральной опорой 4, а другим концом прикреплена к тележке поворота 5, перемещающейся по круговому монорельсу 6.
Круговой монорельс и центральная опора прикрепляются к нижнему эта-
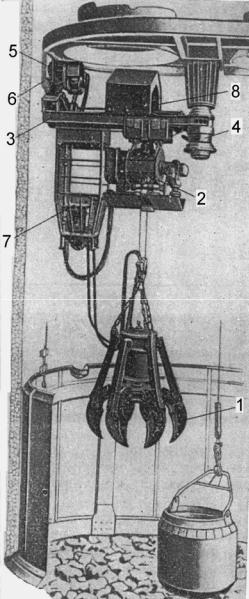
жу подвесного полка. Управление машиной осуществляется дистанционно с кабины машиниста 7. Благодаря радиальному и круговому перемещению грейфера породу можно забирать в любой точке забоя ствола. Питание механизмов производится сжатым воздухом. В процессе погрузки породы выделяют две фазы, отличающиеся по интенсивности погрузки. Это связано с тем, что степень разрушения массива по глубине взорванных шпуров неодинакова. В верхней зоне порода разрушена так, что ее погрузка производится только машиной, без применения ручного труда (первая фаза). Вторая фаза наступает, когда качество дробления породы снижается настолько, что погрузка производится с применением ручного труда – предварительного рыхления, подкидки породы, зачистки. Зачистка забоя производится для исключения попадания мелких кусков породы в шпуры при их бурении.
Объем породы во второй фазе погрузки зависит от качества взрывных работ, свойств породы и типа погрузочной машины. Высота слоя породы во второй фазе для КС-3 составляет 0,2 м; для КС-2у/40 – 0,3 м.
Рис. 2.67. Погрузочная машина КС-2у/40
89
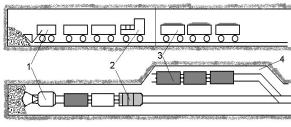
Организация работ по погрузке породы в горизонтальных горных выработках.
При использовании породопогрузочных машин на колеснорельсовом ходу для их перемещения, за передвигающимся к забою породным развалом, возникает необходимость в наращивании рельсового пути. Поэтому в непосредственной близости от забоя применяется временный рельсовый путь в виде пары выдвижных рельсов длиной 4 или 8 м, которые укладываются повернутыми на 90о внутри ранее уложенного звена основного пути. Во время работы машины реборды ее колес перемещаются по шейкам выдвижных рельсов. Проталкивание (выдвигание) рельсов производится ковшом погрузочной машины. После того, как звено выдвижных рельсов продвинется на величину, равную нормальной длине рельсов, вместо выдвижного укладывают постоянное звено пути.
Впроцессе погрузки возникает ситуация, когда ширина выработки превосходит фронт погрузки используемой машины. В этом случае часть породы может быть погружена только после перекидки ее вручную в зону действия ковша. При проведении горно-разведочных выработок такие условия встречаются сравнительно редко, поскольку эти выработки имеют преимущественно небольшое поперечное сечение. Объемы породы, убираемой
сприменением ручного труда, возрастают при проходке различного назначения уширений, камер и т.д.
При погрузке в одиночные вагоны обязательной операцией процесса является обмен груженых вагонеток на порожние.
Воднопутных выработках такой обмен производится с использова-
нием тупиковых и замкнутых разминовок, накладной разминовки, специальных вогоноперестановщиков и др.
Тупиковые и замкнутые разминовки представляют собой ответвление от основного рельсового пути на одну вагонетку или на их состав. При недостаточной ширине выработки в месте разминовки производят расширение выработки. Маневровые операции выполняют с помощью электровоза или вручную.
Расстояние между разминовками составляет 40-60, реже 100 м.
Рис. 2.68. Схема обмена вагонеток в забое при помощи тупиковой разминовки
90
При использо-
вании тупиковой раз-
миновки (рис. 2.68) по-
рожний состав подается электровозом в забой выработки и производится загрузка первой вагонетки. Затем этот состав загоняют в тупик, где груженая вагонетка отце-
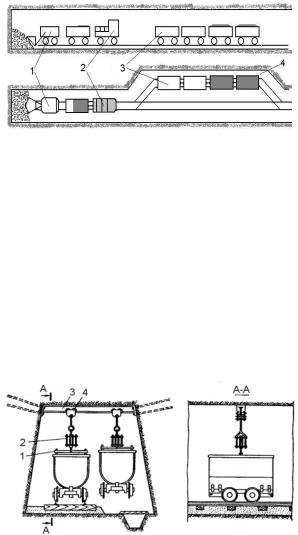
пляется, и затормаживается на разминовке. Порожние вагонетки снова подаются в забой, где производится загрузка. Такая последовательность операций повторяется до тех пор, пока не будет загружен весь состав, который впоследствии забирается электровозом и подается к стволу.
Замкнутые раз-
миновки так же, как и
|
тупиковые, устраива- |
||||
|
ются обычно через 40 – |
||||
|
75 м. Состав порожних |
||||
|
вагонеток |
ставится на |
|||
|
разминовку (рис. 2.69). |
||||
|
Электровозом |
подго- |
|||
|
няют |
к |
погрузочной |
||
Рис. 2.69. Схема обмена вагонеток на замкнутой |
машине одну вагонет- |
||||
ку и |
после |
загрузки |
|||
разминовке |
|||||
|
ставят ее на разминов- |
ку в хвост состава; каждая последующая порожняя вагонетка берется от головы состава, а груженная загоняется на разминовку в хвост. После загрузки всех вагонеток состав откатывается электровозом.
Горизонтальный вагоноперестановщик (рис. 2.70) представляет со-
бой простейший подъемный кран. В выработке на небольшом расстоянии от забоя (не меньше длины состава) укрепляется на штырях двутавровая балка 3, или укрепляется горизонтальная колонка. На балках устанавливается передвижная роликовая тележка 4, снабженная пневматическим подъемником в виде вертикально действующего пневматического цилиндра 2. На выходящем конце штока поршня имеется траверса 1 с приспособлениями, позволяющими захватывать вагонетку, приподнимать ее с рельсового пути на высоту до 150 мм и перемещать в сторону, чтобы освободить рельсовый путь
|
и пропустить по нему |
||||
|
другие |
|
вагонетки, |
||
|
электровоз или погру- |
||||
|
зочную машину. |
|
|||
|
|
|
Организация |
||
|
маневров |
при |
этом |
||
|
следующая. |
После |
|||
|
подъема |
и отвода в |
|||
|
сторону |
одной |
ваго- |
||
|
нетки |
из |
пришедшего |
||
Рис. 2.70. Горизонтальный вагоноперестановщик: |
состава головная ваго- |
||||
нетка |
устанавливается |
||||
1 – траверса; 2 – пневматический цилиндр; 3 – балка; |
|||||
4 - тележка |
под |
погрузку. |
По |
||
окончании ее загрузки, |
|||||
|
|||||
91 |
|
|
|
|
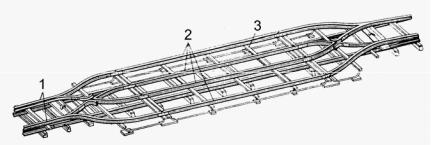
состав с этой вагонеткой откатывается от забоя электровозом за вагонопере-
становщик, а вагонетка, отведенная ранее в сторону, ставится на рельсовый путь впереди состава и электровозом проталкивается под погрузку. Во время погрузки этой вагонетки при помощи вагоноперестановщика следующая порожняя вагонетка отводится от состава в сторону. Операция продолжается до тех пор, пока не будет загружен весь состав.
Обмен вагонеток с применением накладных разминовок (рис. 2.71).
Такой способ рационален в однопутных выработках. Накладная разминовка изготовляется из легких рельсов 2, смонтированных на плите или приваренных к металлическим шпалам 3. Разминовка укладывается на основной путь 1. Одна ее ветвь используется как грузовая, а другая – как порожняковая. Концевые секции разминовки имеют стрелочные переводы для съезда на основной рельсовый путь. На порожняковую ветвь электровозом подается состав порожних вагонеток, откуда по одной они подаются вручную к погрузочной машине. Груженые вагонетки с помощью маневровой лебедки или вручную откатывают на грузовую ветвь разминовки. По мере подвигания забоя разминовку перемещают лебедкой или погрузочной машиной. Обычно применяют разминовки на 4 – 6 вагонеток.
Рис. 2.71. Накладная стрелка-разминовка
Основные сведения о транспортировании породы при проведении горных выработок.
Неотъемлемой и важнейшей частью производственного процесса проведения выработок является транспортирование грузов (породы, полезного ископаемого, оборудования, материалов) и рабочего персонала.
По месту работы транспорт подразделяется на подземный (перемещение грузов по горным выработкам) и транспорт на поверхности (перемещение грузов на поверхности от устья ствола, штольни, шурфа).
При горно-разведочных работах объем перевозок по горным выработкам относительно невелик. При разработке же месторождений, особенно открытым способом, количество перемещаемых горных пород очень боль-
92

шое и достигает миллионов тонн в год и более. Расстояние перевозок в этом случае изменяется от десятков метров до десятков километров.
В условиях геологоразведочных работ откатка по горизонтальным выработкам выполняется в основном с помощью электровозов; по наклонным выработкам на участках доставки – скреперами или под действием собственного веса, на участках откатки – с помощью средств канатного транспорта; по вертикальным горным выработкам – подъемными машинами
илебедками.
Рудничный транспорт в горизонтальных и наклонных горных вы-
работок (доставка и откатка грузов).
Под термином доставка понимается перемещение горной породы или полезного ископаемого до места погрузки в основные транспортные средства. Доставка может быть не механизированной, например, вручную; под действием собственного веса, и механизированной - скреперами; конвейерами; самоходными погрузочно-транспортными машинами.
К ручной доставке относят перелопачивание породы, ее переноску и перевозку в небольших тачках или вагонетках. Ручная доставка в настоящее время имеет весьма ограниченную область применения и может быть пригодной в качестве основного способа только для перемещения небольших количеств горных пород на незначительные расстояния.
Доставка под действием собственного веса — перемещение отбитой породы по горной выработке под действием силы тяжести — является простейшим и весьма выгодным способом транспортировки. Обязательным условием при этом является достаточный наклон почвы выработки, по которой должна скатываться порода. При угле наклона почвы выработки, превышающем 35°, порода перемещается непосредственно по почве выработки, а при углах наклона от 25 до 35°—скатывается по уложенным на почве доскам, железным листам или желобам. При разведке месторождений полезных ископаемых доставка пород этим способом применяется только при проведении восстающих. Переместившаяся по очистному пространству порода (руда) через рудоспуски поступает непосредственно к разгрузочным устройствам (люкам).
Схемы люков с различными системами затворов показаны на рис. 2.72. Наиболее распространены секторные, пальцевые и цепные люковые затворы.
Двухсекторный люковый затвор (рис. 2.72, а) состоит из днища 1, люковых затворов 2, открывающихся в момент загрузки вагонетки пневматическими цилиндрами 7 (иногда вручную), бортов 3, лобовины 4, отбойника 5 и рамы 6.
Пальцевый затвор (рис. 2.72, б) состоит из пяти-семи пальцев 1, насаженных на общую ось 2. Пальцы изготавливают из рельсов. При натяжении троса 3 пальцы поднимаются. Если при опускании затвора под один из пальцев попадает руда, остальные могут свободно опускаться на днище и
93
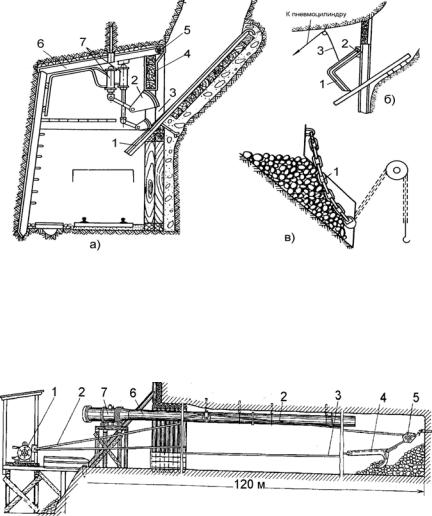
перекрывать поток породы.
Люк с цепным затвором (рис. 2.72, в) состоит из нескольких тяжелых якорных цепей 1, которые перекрывают поток руды. Открывают люк подъемом цепей, натягиваемых пневматическими цилиндрами.
Рис. 2.72. Схемы люковых затворов
Скреперная доставка пород получила широкое распространение при разведке месторождений полезных ископаемых штольнями. Основными машинами для доставки являются скреперные установки. Скреперная установка для доставки породы в отличие от скреперного грузчика не имеет погрузочной платформы; скреперная лебедка устанавливается на почве выработки, а скрепер разгружается в отвал (рис. 2.73).
Рис. 2.73. Скреперная уборка породы в отвал при проходке штольни: 1 – скреперная лебедка; 2 – холостая ветвь каната; 3 - рабочая ветвь каната; 4 – скрепер; 5 – забойный ролик; 6 – вентиляционный трубопровод, 7 - вентилятор
94
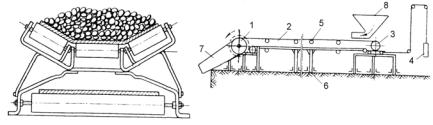
Производительность скреперной доставки зависит от расстояния, на которое необходимо перемещать породу, мощности скреперной лебедки и размеров скрепера. Наиболее производительная работа достигается при расстоянии доставки, не превышающем 40 м. Емкость скреперов изменяется в пределах от 0,1 до 1 м3 и более.
Конвейерная доставка осуществляется ленточными, пластинчатыми и скребковыми конвейерами. Этот вид доставки применяется в основном при разработке пологопадающих рудных тел.
Несущим органом стационарного ленточного конвейера (рис. 2.74) является гибкая прорезиненная лента 2, которая приводится в движение барабаном 1. На противоположном конце конвейера имеется направляющий барабан 3. Лента поддерживается роликами 5, укрепленными на раме конвейера. Так как движение ленте сообщается силой трения между приводным барабаном и лентой, необходимо поддерживать постоянное натяжение ленты, что обеспечивается натяжным устройством 4. Загрузку ленты осуществляют через бункер 8, для разгрузки служит лоток 7. Конвейер поддержива-
ется на опорах 6.
Рис. 2.74. Схема стационарного ленточного конвейера
Скребковый конвейер (рис. 2.76) представляет собой металлический желоб, по дну которого движется цепь с прикрепленными к ней скребками. При движении скребки захватывают породу и перемещают ее по желобу.
Такие конвейеры позволяют транспортировать груз под углом до 30о.
Пластинчатые изгибающиеся конвейеры (рис. 2.75) имеют тот же принцип действия, что и ленточные. Несущая лента в этих конвейерах изготовлена из стальных пластин, укрепленных на звеньях двух тяговых шарнирных цепей. На цепях имеются ролики, которые катятся по направляющим. Цепи приводятся в движение от звездочек приводного устройства. Так же, как и в ленточных конвейерах, с противоположного конца имеется натяжное устройство.
95
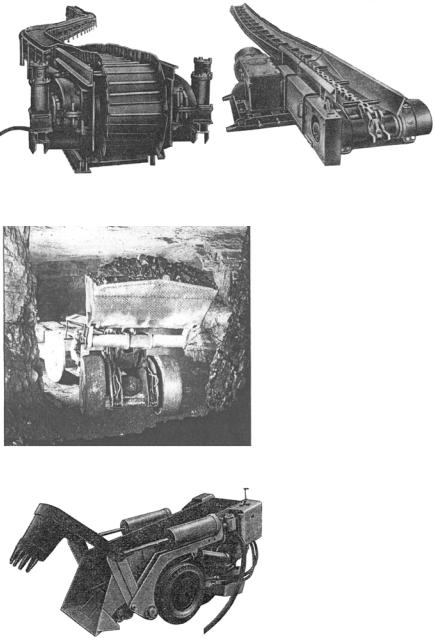
Рис. 2.75. Пластинчатый изгибаю- |
Рис. 2.76. Цепной скребковый передвиж- |
щийся конвейер |
ной конвейер |
Рис. 2.77. Погрузочно-доставочная машина ПДН
Рис. 2.78. Пневматическая погрузочнодоставочная машина ПДВ
96
При небольшой длине транспортирования для уборки породы в горизонтальных выработках находят применение по-
грузочно-транспортные машины. Достоинством исполнения погрузочнотранспортных машин является малое число операций и минимальное количество оборудования, используемого при уборке породы.
Типичным представителем таких машин является машина с ковшовым грузонесущим кузовом нижнего захвата
(ПДН-1) (рис. 2.77). Раз-
грузка машины может производиться в рудоспуски, на почву или в приемный лоток перегружателя.
На рис. 2.78 показана пневматическая по- грузочно-доставочная машина ПДВ-2. Погру-
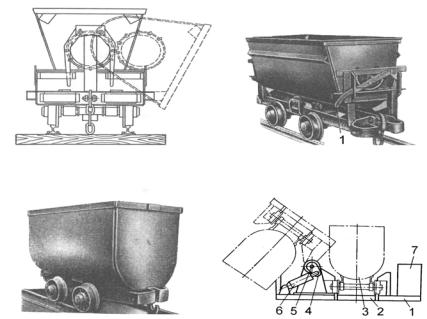
зочный орган машины работает по принципу верхнего захвата. Руда поступает на донный скребковый конвейер. Разгрузка осуществляется через тор-
цевую часть вагонетки включением конвейера.
Основным видом перемещения горных пород по транспортным выработкам (ортам, штрекам, квершлагам, бремсбергам, штольням, наклонным стволам шахт и траншеям) является откатка в вагонетках по рельсовым путям. Этот вид транспорта широко применяется также для перевозки материалов, оборудования и людей.
К основным типам рудничных вагонеток можно отнести вагонетки с опрокидным кузовом (УВО) и с неопрокидным глухим кузовом (УВГ).
Рис. 2.79. Опрокидные вагонетки
Рис. 2.80. Вагонетка |
Рис. 2.81. Боковой опрокидыватель ваго- |
с неопрокидным кузовом |
неток: 1 – рама; 2 – клеть; 3 – вагонетка; |
|
4 – силовой рычаг; 5 – вал; 6 – гидроци- |
|
линдр; 7 - маслостанция |
Конструкции вагонеток с опрокидным кузовом и саморазгружающихся таковы, что разгрузка их может производиться без специальных устройств или с помощью простейших устройств. Эти вагонетки разгружаются при поворачивании кузова вокруг горизонтальной оси, открывании дна, боковых или торцовых стенок.
97
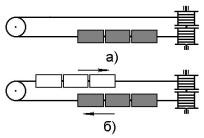
Вагонетка с опрокидным кузовом, показанная на рис. 2.79 разгружается вручную при подъеме рычага 1 вверх. Полезный объем кузова рудничных вагонеток меняется в широких пределах — от 0,32 до 5 м3.
Кузов глухих вагонеток (рис. 2.80) жестко соединен с рамой. Такие вагонетки при разгрузке необходимо опрокидывать; разгрузка их производится с помощью специальных механических устройств — опрокидывате-
лей (рис. 2.81).
В практике горно-разведочных работ при небольших объемах работ нередко применяется ручная откатка одиночных вагонеток. При этом перевозимый груз не должен превышать 1т при скорости движения вагонеток 0,5—1 м/с. Производительность откатчика составляет 1,2—1,7 т-км/смену.
Канатная откатка, или иначе, откатка неподвижными двигателями заключается в том, что одиночные вагонетки или составы вагонеток перемещаются по горной выработке, будучи прицепленными к канату, приводимому в движение лебедкой (рис. 2.82). В процессе откатки канаты наматываются, или сматываются с барабанов.
При откатке двумя канатами составы вагонеток передвигаются поочередно по одному и тому же пути двумя канатами - головным, перемещающим груженый состав, и хвостовым, огибающим концевой шкив (рис. 2.82, а).
При откатке по двухпутной выработке одновременно движутся груженные и порожние составы, связанные между собой соединительным ка-
натом (рис. 2.82, б).
Канатная откатка осуществляется при относительно небольшой протяженности горизонтальных или
наклонных горных выработках; прямолинейность выработок— желательное условие.
Локомотивная откатка является основным видом рудничного транспорта на геологоразведочных работах, и широко применяется для перемещения грузов по горизонтальным или слабонаклонным выработкам добычных предприятий. Грузы транспортируются составами вагонеток, образующими вместе с локомотивами поезда.
Наиболее распространенным видом локомотивов являются электровозы. По способу питания они делятся на контактные (КР, К), и аккумуляторные (АРП, АРВ). Контактные электровозы получают ток от контактного (троллейного) провода и рельсовых путей. Аккумуляторные электровозы питаются от аккумуляторных батарей, располагающихся на самом электро-
98
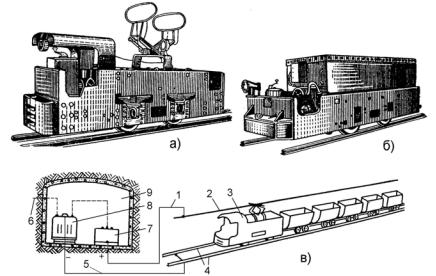
возе или прицепленном к нему тендере.
Контактные электровозы 3 (рис. 2.83, а) снабжены тяговыми двигателями постоянного тока (U = 250 В). Для преобразования высокого напря-
жения, поступающего в камеру 9 по кабелю 6 (рис. 2.83, в), в низкое, и переменного тока в постоянный предназначены электроподстанция 8 и выпрямитель 7. Постоянный ток с подстанции по кабелю 1 поступает в контактную сеть. Обычно к воздушному контактному проводу подсоединяется положительный полюс источника тока. Обратным проводом в сети являются рельсовые пути 4. Они соединяются с помощью отсасывающего кабеля 5. Подача тока к двигателю осуществляется с помощью специального токосъемника, скользящему по контактному проводу 2.
Рис. 2.83. Рудничные электровозы
Контактные электровозы более надежны в эксплуатации, отличаются простотой конструкции и наиболее экономичны. Основным их недостатком является искрение на токоприемнике, скользящем при движении электровоза по контактному проводу. Поэтому в подземных горных выработках, опасных по газу и пыли, применение контактных электровозов ограничено или совершенно исключается. В этих ситуациях используется аккумуляторный электровоз (рис. 2.83, б)
Откатку породы при проведении горных выработок от места погрузки до околоствольного двора или устья штольни производят по рельсовым путям.
99
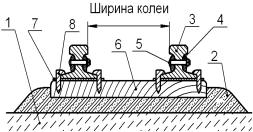
Рельсовый путь (рис. 2.84) состоит из двух частей: основания или нижнего строения пути (почва выработки – 1) и верхнего строения пути – балластного слоя 2, шпал 6, рельсов 3, и крепежной арматуры (костыли 8,
подкладки 7, стыковые на-
Рис. 2.84. Основные элементы рельсового пути кладки 4 для соединения рельсов между собой, болты
5).
Балластный слой выполняет роль упругой подушки, между почвой выработки и шпалами, которая воспринимает давление подвижного состава, передаваемого рельсами и шпалами. Кроме того, балласт препятствует сдвигу шпал и способствует отводу воды от пути. В качестве материала для балласта применяется щебень и гравий из крепких горных пород, а также местную породу, полученную в процессе проходческих работ. Толщина балластного слоя под шпалами должна быть не менее 100 мм.
Шпалы служат для передачи и распределения давления от рельсов на балласт. Длина шпал в 1,8-2 раза должна превышать ширину колеи. При укладке шпалы погружают в балласт на 2/3 их толщины.
Рельсы для настилки путей в горных выработках используются шести типов: Р-8, Р-10, Р-11, Р-15, Р24. В зависимости от типа масса 1 м рельса - 8…24 кг. Расстояние между внутренними краями головок рельсов называется шириной колеи. Подземные пути могут иметь ширину колеи, равную 600, 750 или 900 мм. При проведении разведочных выработок ширина колеи обычно равна 600 мм.
Настилку рельсового пути начинают с раскладки шпал (по шаблону). Концы шпал со стороны людского прохода выравнивают по шнуру. Рельсы укладывают на шпалы таким образом, чтобы стыки рельсов находились друг против друга. Рельсы крепятся к каждой шпале не менее чем двумя костылями. После прошивки рельсов, между шпалами загружают балластный слой 1, и производят подъем пути на балласт. Подъем пути осуществляют ломами или путевым домкратом. Присыпку балласта осуществляют лопатами, а окончательную подбойку – маховыми подбойниками.
Для перевода подвижного состава с одного пути на другой при достаточно интенсивной откатке используются стрелочные переводы. В зависимости от положения стрелочных переводов по отношению к рельсовым путям их разделяют на несколько видов: односторонние (правые и левые); съезды (для перевода поездов с одного пути на другой, параллельный) и др.
100

Рис. 2.85. Рельсовые пути со стрелочными переводами в откаточном штреке
По устройству переводного механизма различают стрелочные переводы с ручным и механическим приводом. Стрелочный перевод (рис. 2.86, а) состоит из следующих элементов: стрелки, переводных рельсов 3, усов 4, контррельсов 5, крестовины 6, переводного механизма 7.
Стрелка состоит из неподвижных рамных рельсов 2 и подвижных перьев 1, соединенных между собой поперечной стяжкой, с которой соединена шарнирно штанга переводного механизма. Передние концы перьев делают в виде острия и выгибают так, чтобы они плотно прилегали к рамным рельсам, что создает условия для плавного перехода для подвижного состава. Пе-
Рис. 2.86. Стрелочный перевод рья скользят по опорным подушкам из широкой
101
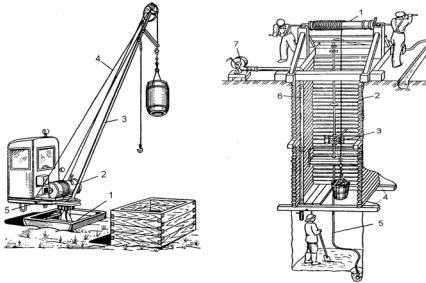
полосовой стали, закрепленным на шпалах.
Крестовины (рис.2.86, б) бывают клепапанные, сварные и литые. В крестовинах различают сердечник 1, на вершине острия которого в точке 5 находится ее центр; усовики 2, желоба 3, горловину 4 – самое узкое место между усовиками
Контррельсы 5 (рис. 2.86, а) пришивают к шпалам внутри колеи против крестовины для направления реборд колес в соответствующую канавку (желоб) крестовины. Они препятствуют сходу подвижного состава с рельсового пути.
Подъем при проходке разведочных шурфов и стволов шахт.
Самым простейшим средством механизации операций подъема при проходке шурфов являются разборные деревянные или металлические ручные воротки. Подъем породы, производят в небольших бадьях, подвешиваемых на канатах диаметром 8 – 10 мм к воротку, установленному над устьем шурфа (рис. 2.88). Спуск и подъем людей – в бадьях и седлах; материалы и другие предметы длиной до 2 м транспортируются в бадьях, а при длине более 2 м применяются специальные серьги. Подъем негабаритных кусков породы производится специальным приспособлением, выполненным из металлической сетки или синтетических материалов.
Рис. 2.87. Подъемный кран КП-1М: |
Рис. 2.88. Подъем породы при проведе- |
1 – опорная площадка; 2 – лебедка; |
нии шурфа: 1 – вороток; 2 – крепь; 3 – |
3 – стрела; 4 – канат; 5 – поворот- |
насос; 4 - опорный венец; 5 – шланг; 6 – |
ная рама |
вентиляционные трубы; 7 - вентилятор |
|
102 |
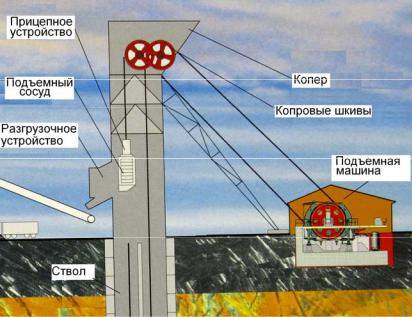
Проходка глубоких шурфов с площадью сечения 3,2 – 4 м2 может производиться более совершенными подъемными устройствами, в виде воротков с механическим приводом, специальных подъемных кранов (рис. 2.87) и шурфопроходческих агрегатов
При проведении стволов шахт для спуска и подъема применяются более сложные устройства, называемые подъемными установками, основными частями которых являются: проходческий копер, подъемная машина (стационарные и передвижные проходческие лебедки), подъемные сосуды (бадьи, скипы), прицепные устройства, канаты и шкивы (рис. 2.89).
Рис. 2.89. Подъемная установка
Копры, предназначены для установки направляющих подъемных шкивов на такой высоте, которая позволяет поднимать бадьи (скипы, клети) над устьем для разгрузки и производить погрузку выдаваемой породы в транспортные средства. На копре устанавливают также дополнительные шкивы для канатов вспомогательных лебедок, предназначенных для подвески различного вспомогательного оборудования. Проходческие копры имеют сборно-разборную конструкцию из стальных труб или другого сортаментного металла, обеспечивающую высокую прочность, простоту сборки и разборки, а также возможность многократного использования. Копры имеют разнообразные конструкции: А образные, четырех стоечные, шатро-
вые, башенные, цилиндрические (рис.2.90 – 2.91).
103
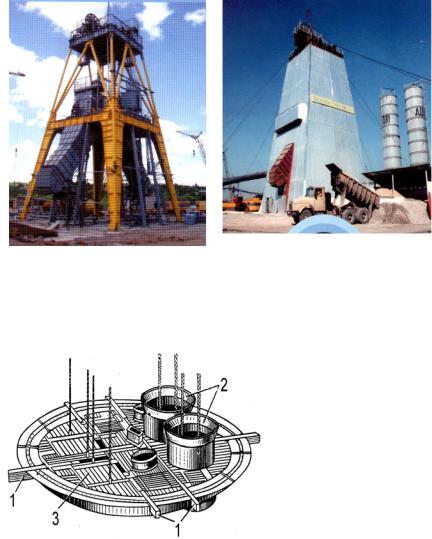
Рис. 2.90. Проходческий копер |
Рис. 2.91. Проходческий обшитый |
|
копер |
Размер внутрикопровой площадки определяется разносом стоек копра, обеспечивающим его устойчивость и удобство работы около устья ствола.
|
|
Устье ствола шах- |
||||
|
ты перекрывается нулевой |
|||||
|
рамой, |
предохраняющей |
||||
|
работающих |
в |
стволе. |
|||
|
Нулевая |
рама |
|
разведоч- |
||
|
ного |
ствола сооружается |
||||
|
из двутавровых |
балок и |
||||
|
листовой стали. В нуле- |
|||||
|
вой |
раме |
устраиваются |
|||
|
проемы для бадей и лест- |
|||||
|
ниц, перекрываемые ля- |
|||||
|
дами и, имеющими выре- |
|||||
|
зы для пропуска канатов |
|||||
Рис. 2.92. Нулевая рама: |
(рис. |
2.92). Нулевая рама |
||||
1 – опорные пальцы; 2 – раструбы; 3 - ляда |
используется |
как пло- |
||||
|
щадка для |
подготовки к |
спуску в ствол материалов, посадки людей в бадьи.
Подъемная машина (рис. 2.93) представляет собой лебедку с электрическим приводом 2, оборудованную рабочими 3 и аварийными 4 тормозами, измерительной аппаратурой и сигнализацией. В подъемной машине с барабанными механизмами навивки подъемные канаты 5 навиваются на ба-
104
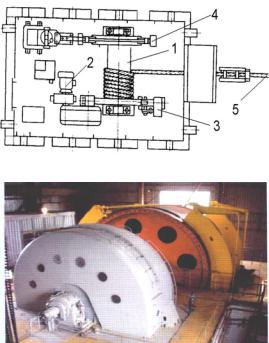
Рис. 2.93. Структура стационарной проходческой лебедки (подъемной машины)
Рис. 2.94. Внешний вид стационарной проходческой лебедки
рабан 1 в один ряд, (двухрядная навивка допускается только в исключительных случаях). Ширина барабана зависит от его канатоемкости, а диаметр барабана, так же, как и диаметр направляющих шкивов, определяется диаметром подъемных канатов или диаметром проволок, из которых они свиты.
Направляющие подъемные шкивы монтируются в верхней части копра над шкивной площадкой. Диаметр шкивов (до 6 м и более)
выбирают в зависимости от диаметра подъемных канатов.
Для спуска и подъема горной породы, материалов, оборудования и людей применяются проходческие бадьи, скипы и клети.
Подъемные сосуды присоединяются к канатам с помощью специальных прицепных устройств, причем конец каната огибает овальную обойму (ковш) прицепного устройства и скрепляется с прямой ветвью каната посредством зажимов («жимков»).
Основными элементами прицепного устройства (рис. 2.95, б) являются крюк 1 с защелкой 2, исключающей самопроизвольное отцепление бадьи, и вертлюга 3, устраняющего вращение крюка.
Проходческая бадья (рис. 2.95, а) состоит из корпуса цилиндрической формы, выполненного из листовой стали толщиной 8-12 мм и дужки диаметром 50-60 мм. Последняя соединена с корпусом шарнирно.
Различают два вида проходческих бадей – самоопрокидывающиеся и несамоопрокидывающиеся.
В комплект самоопрокидывающейся бадьи дополнительно включается направляющая рамка, а также эксцентричные кронштейны, которые устанавливаются на верхней приемной площадке копра.
При опускании бадьи на кронштейны она опрокидывается, порода
105
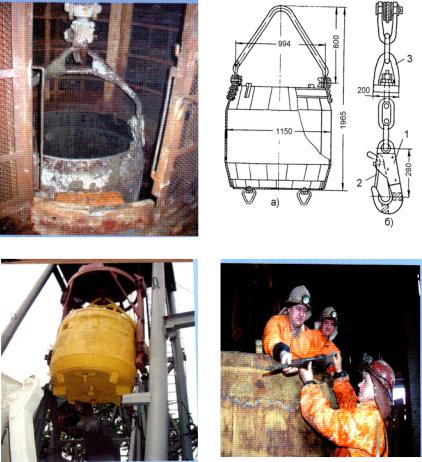
высыпается и по желобу поступает в транспортное средство Несамоопрокидывающиеся бадья разгружается путем ее наклона с
помощью крюка, подвешенного на торосе.
Рис. 2.95: а) – бадья; б) - прицепное устройство,
Рис. 2.96. Самоопрокидывающаяся |
Рис. 2.97. Погрузка людей и |
бадья перед разгрузкой |
оборудования в бадью |
Для предотвращения раскачивания бадьи (скипа) при движении в стволе, над прицепным устройством бадьи размещается специальная рамка (направляющая каретка) (рис. 2.98), которая перемещается по направляющим канатам.
Скорость перемещения бадьи регламентируется правилами безопасности; ее максимальное значение при подъеме и спуске людей 8 м/с, мате-
106
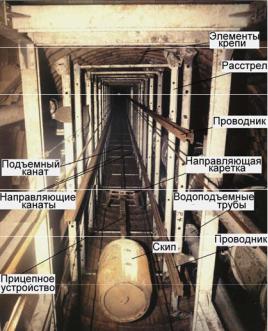
|
риалов |
и |
оборудования |
||||||
|
(движение по направляю- |
||||||||
|
щим канатам) - 12 м/с. |
|
|
||||||
|
|
Проходческие |
бадьи |
||||||
|
типизированы |
по |
емкости: |
||||||
|
самоопрокидывающиеся |
– |
|||||||
|
1,0; |
1,5; |
2,0; |
3,0; |
4,0; |
5,0; |
|||
|
5,5; 6,5 м3; несамоопроки- |
||||||||
|
дывающиеся – 0,75; 1,0 м3. |
||||||||
|
|
В |
процессе |
проведе- |
|||||
|
ния шурфов и разведочных |
||||||||
|
стволов наиболее часто ис- |
||||||||
|
пользуют |
шурфопроходче- |
|||||||
|
ские бадьи емкостью от 0,05 |
||||||||
|
до 0,25 м3, при значитель- |
||||||||
|
ных |
размерах |
проходимой |
||||||
|
горной |
выработки |
исполь- |
||||||
|
зуют |
проходческие |
бадьи |
||||||
|
емкостью 1,5 м3 и более. |
||||||||
|
|
В тех случаях, когда |
|||||||
|
подъемные установки пред- |
||||||||
Рис. 2.98. Размещение бадьи в стволе шахты |
назначены |
исключительно |
|||||||
для |
выдачи из подземных |
||||||||
|
выработок полезного ископаемого или пустых пород и производительность подъема велика, используется скиповой подъем (рис. 2.99), а в качестве подъемных сосудов применяются скипы.
Скип представляет собой металлический ящик цилиндрической или, призматической формы, шарнирно укрепленный на подвесной раме. Рама всегда занимает вертикальное положение.
Скипы бывают опрокидные, с отклоняющимся кузовом и неопрокид-
ные.
Опрокидной скип (рис. 2.100, а) наиболее прост по конструкции, имеет кузов призматической формы с плоским днищем, соединенный шарнирно с рамой в нижней части и опирающийся на нижнюю балку рамы. На боковых стенках скипа имеются ролики, движущиеся при опрокидывании скипа по разгрузочным кривым. К верхней балке рамы крепится подвесное устройство, соединяющее скип с канатом подъемной машины. Загрузка скипа производится через верх кузова, разгрузка также через верх при повороте кузова на 135-1450 при взаимодействии разгрузочных роликов кузова с разгрузочными кривыми на копре (рис. 2.100, б).
Скип с отклоняющимся кузовом (рис. 2.101, а) имеет откидное дни-
ще в виде затвора с бортовыми стенками. Кузов шарнирно подвешен к
107
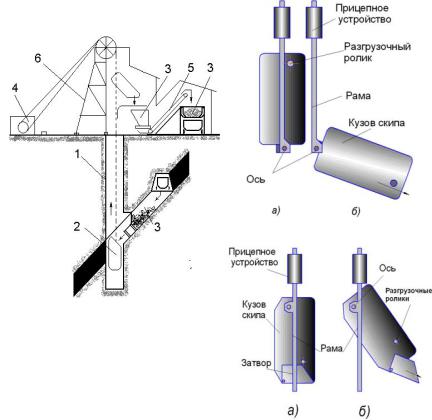
верхней части рамы.
Разгрузка скипа происходит при отклонении кузова на 150 от взаимодействия разгрузочных роликов кузова с разгрузочными кривыми копра. При этом затвор катится по наклонным направляющим на раме и устанавливается под углом 45-550 , открывая разгрузочное отверстие и направляя в бункер разгружаемый материал (рис. 2.101, б).
Рис. 2.100. Принципиальная схема конструкции опрокидного скипа
Рис. 2.99. Схема скиповой уборки породы: 1 – ствол; 2 – скип; 3 – приемный бункер; 4 – подъемная машина; 5 – транспортер; 6 – копер; 7 – накопитель руды
Рис. 2.101. Принципиальная схема конструкции скипа с отклоняющимся кузовом
Неопрокидные скипы разгружают на земной поверхности через откидывающуюся боковую стенку или откидное дно, автоматически открывающееся при вкатывании ролика в разгрузочные направляющие, при этом гор-
ная порода высыпается в приемный бункер.
В начале опускания при выходе роликов из разгрузочных направляющих опрокидные и неопрокидные скипы приобретают первоначальное
108
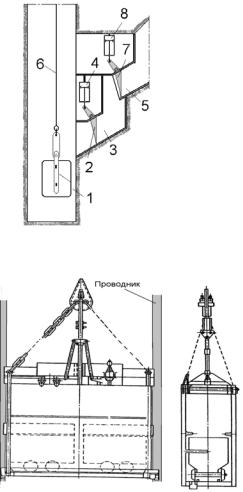
положение, в котором и перемещаются по стволу шахты вниз для очередной загрузки породой из подземных бункеров.
На действующих шахтах эксплуатируются скипы вместимостью от 2,0 до 35 м3. Наибольшая грузоподъемность скипов 55 -60 т.
Загрузка скипов рудой осуществляется в подземной горной выработке из загрузочных бункеров (рис. 2.102) В нижней части бункера устраиваются дозаторы (мерные ящики). Достаточно мелкая порода «самотеком» поступает из бункера в дозатор, а из последнего пересыпается в скип.
Бункера и дозаторы оборудуются затворами с пневмоприводами. Для заполнения дозатора 3 в цилиндр 8 подается сжатый воздух; затвор 7 открывается и руда из бункера 5, заполняет дозаторный ящик. Затвор 2 в это время закрыт. Для загрузки скипа 1 воздух подается в цилиндр 4. Затвор 2 открывается
ируда из дозатора по желобу поступает
вскип.
|
|
Клеть (рис. 2.103) представляет |
|||||||
|
собой подъемный сосуд в виде плат- |
||||||||
|
формы, укрепленной на каркасной раме, |
||||||||
|
с крышей и дверцами. В клетях спуска- |
||||||||
|
ют и поднимают людей, вагонетки с |
||||||||
Рис. 2.102. Схема загрузки скипа |
горной |
породой и |
другие |
грузы. |
При |
||||
из загрузочного бункера. |
клетьевом подъеме порода транспорти- |
||||||||
руется |
в вагонетках, закатываемых в |
||||||||
|
|||||||||
|
|
|
клети. На платформе клети |
||||||
|
|
|
в зависимости от ее разме- |
||||||
|
|
|
ров может размещаться од- |
||||||
|
|
|
на или несколько вагонеток. |
||||||
|
|
|
Во избежание больших по- |
||||||
|
|
|
перечных |
размеров |
клети, |
||||
|
|
|
что привело бы к необхо- |
||||||
|
|
|
димости проходить стволы |
||||||
|
|
|
шахт |
увеличенных |
|
попе- |
|||
|
|
|
речных |
|
сечений, |
иногда |
|||
|
|
|
применяют |
двухэтажные |
|||||
|
|
|
клети. |
|
|
|
|
|
|
|
|
|
Фиксированное |
по- |
|||||
|
|
|
ложение клети при переме- |
||||||
Рис. 2.103. Схема одноэтажной клети |
|
щении ее по стволу обеспе- |
|||||||
|
чивается |
направляющими |
|||||||
на две вагонетки |
|
|
|||||||
|
|
(металлическими или дере- |
|||||||
|
|
|
|||||||
|
109 |
|
|
|
|
|
|
|
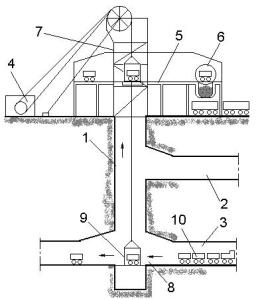
вянными проводниками). |
|
Горная порода в обык- |
||||||
|
|
|||||||
|
новенной |
клети транспорти- |
||||||
|
руется из подземных вырабо- |
|||||||
|
ток |
на |
земную поверхность |
|||||
|
следующим образом (рис. |
|||||||
|
2.104). В клеть 9, установлен- |
|||||||
|
ную на специальный кулачко- |
|||||||
|
вый |
(посадочный) |
механизм |
|||||
|
(см. рис. 2.106), служащий |
|||||||
|
для остановки клетей против |
|||||||
|
погрузочной (приемной) пло- |
|||||||
|
щадки |
8 |
|
околоствольного |
||||
|
двора, вкатывают вагонетку с |
|||||||
|
горной |
породой. |
Вагонетку |
|||||
|
закрепляют на рельсах клети |
|||||||
|
стопорами |
или защелками |
в |
|||||
|
необходимом |
для |
транспор- |
|||||
|
тировки |
положении. Дверцы |
||||||
|
клети закрывают, и стволовой |
|||||||
Рис. 2.104. Схема клетевого подъема: |
(рабочий, |
работающий |
на |
|||||
подъеме |
в |
околоствольном |
||||||
1 – ствол; 2 ,3 - горизонтальные выработки; |
||||||||
дворе) подает сигнал подъе- |
||||||||
4 – подъемная машина; 5,8 – приемные площад- |
||||||||
ки; 6 – опрокидыватель; 7 – копер; 9 – клеть; |
ма. |
Клеть |
поднимается |
по |
||||
10 - состав вагонов |
стволу 1 до верхней приемной |
|||||||
|
площадки 5, |
против которой |
вновь устанавливается на кулачки посадочного механизма; после открытия дверей и стопоров вагонетка выкатывается из клети, а взамен ее в клеть устанавливается порожняя вагонетка, предназначенная для спуска в подземные выработки.
Смена вагонеток в клети (груженой на порожнюю или наоборот) при небольшой производительности подъема осуществляют обычно вручную, при более значительной производительности эта смена производится с помощью специальных механических устройств — толкателей (рис. 2.105), служащих для перемещения одиночных вагонов и составов на небольшие расстояния.
При переднем ходе каретки 3 рычаг 4 упирается в борт вагонетки 2 и заталкивает ее в клеть 1. При обратном ходе рычаг автоматически поднимается, проходит над вагонеткой, а затем опускается. Для удобства загрузки и выгрузки клетей применяют обычно сквозное движение через клеть. При этом стоящий в клети порожний вагон выталкивается груженым вагоном, вкатываемым в клеть
110
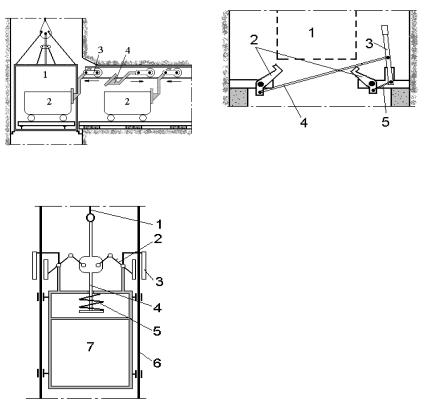
Рис. 2.106. Принципиальная схема кулач-
Рис.2.105. Схема замены в клети при кового (посадочного) механизма: помощи толкателя вагонеток 1 –клеть; 2 – кулачки; 3 – рычаг; 4- тяга
|
Каждая клеть должна быть обо- |
|
рудована специальным устройством, |
|
называемым парашютом (рис. 2.107), |
|
предназначенным для предотвращения |
|
падения клети 7 в шахтном стволе при |
|
обрыве подъемного каната. |
|
При обрыве подъемного каната 1, |
|
разжимается приводная пружина 5 и |
|
опускает шток 4, что вызывает поворот |
|
рычагов 2. Захваты 3 соприкасаются с |
|
тормозными канатами 6. Под действием |
|
веса клети, захваты зажимают канаты |
|
или прижимаются (врезаются) в про- |
Рис. 2.107. Принципиальная схема |
водники, по которым скользит клеть, в |
результате чего, последняя плавно ос- |
|
парашютного устройства |
танавливается. |
Организация работ в забое ствола при подъеме породы бадьями.
При проходке стволов применяют однобарабанные и двухбарабанные подъемные машины и в соответствии с этим – одноконцевой и двухконцевой подъем.
Одноконцевой подъем может быть организован по двум схемам а и б
(рис. 2.108).
а) Одноконцевой подъем без перецепки бадьи (рис. 2.108, а). Выпол-
няется при такой глубине ствола, когда время погрузки породы меньше или соизмеримо со временем полного оборота бадьи. Во время движения бадьи по стволу и ее разгрузки на поверхности погрузочные работы в забое приостанавливаются.
б). Одноконцевой подъем с перецепкой бадей (рис. 2.108, б). Порож-
няя бадья опускается на забой, а вторая бадья находится под погрузкой. После ее загрузки и прибытия на забой порожней бадьи производится пере-
111
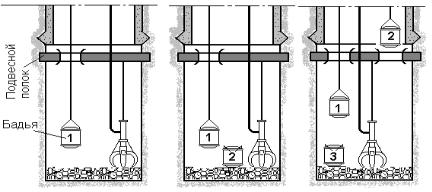
цепка бадей. Такой способ применяется при глубине ствола, когда время погрузки породы больше времени полного оборота бадьи, т.е. когда исключается простой погрузочной машины.
Одноконцевой подъем является неуравновешенной системой. Поэтому, когда подъем производится в сосудах небольшой грузоподъемности и с небольших глубин, к подъемной машине прицепляют одну ветвь каната, в других случаях для достижения более благоприятного режима работы подъемной машины к ее барабанам прицепляют две ветви каната, на одну из них навешивают подъемный сосуд, на другую— противовес (компактный груз, уравновешивающий подъемный сосуд).
Двухконцевой подъем (рис. 2.108, в) является более производительной схемой бадъевого подъема. Такой подъем функционирует следующим образом. Две бадьи, одна из которых груженная, движутся в стволе: груженая поднимается по стволу, порожняя опускается вниз. В это время третья бадья отцеплена от каната и находится в забое ствола под погрузкой. Бадья, поднятая на поверхность, без отцепки от каната разгружается, а порожняя бадья на забое отцепляется и ставится под погрузку. Вместо нее к канату прицепляется третья загруженная бадья.
Двухконцевой подъем целесообразно применять при проходке стволов значительной глубины и большой площади поперечного
а) |
б) |
в) |
Рис. 2.108. Схемы работы подъема сосудов
2.7. Крепление горных выработок
Подземные горные выработки далеко не всегда сохраняют свою первоначальную форму. Часто стенки, кровля или даже почва горной выработки деформируется. Деформация горной выработки является следствием то-
112
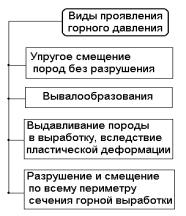
го, что горные породы находятся в равновесно-напряженном состоянии, возникающем под действием веса вышележащих слоев пород и реакции нижележащих. В нетронутом массиве силы, действующие на породу, взаимно уравновешиваются. Однако в результате проведения выработок рав- новесно-напряженное состояние пород нарушается. В горных породах, граничащих с выработкой, возникают внутренние силы, направленные к ее контуру - проявляется так называемое горное давление.
Для сохранения формы и расчетных размеров сечения горных выработок необходимо возведение крепи. Перемещающийся внутрь выработки ее породный контур в некоторый момент вступает в контакт с крепью. Крепь препятствует этому перемещению, вследствие чего возникает горное давление на крепь, которое постепенно возрастает до тех пор, пока система «порода-крепь» не придет в состояние равновесия, или крепь будет разрушена. Конструкция крепи должна отвечать условиям ее работы, т.е. учитывать величину и режим горного давления.
Общие сведения о горном давлении. В общем случае горное давление
– это силы, возникающие в массиве горных пород, окружающих горные выработки, действующие на крепь, массив и целики обусловленные: собственным весом пород; тектоническими нарушениями; разностью температур.
Различные механические явления, происходящие в результате воздействия на контур выработки этих сил, называются проявлением горного давления (рис. 2.109).
Процесс проявления горного давления (особенно когда выработка остается долгое время незакрепленной) протекает до тех пор, пока кровля ее не примет форму свода. Этот процесс, как правило, протекает в виде отслоения горной породы (рис. 2.110). Это явление проявляется особенно интенсивно в тех случаях, когда выработка пройдена в несвязных породах или в породах, обладающих незначительной устойчивостью.
Таким образом, если горное давление превышает прочностные показатели пород, выработка деформируется или разрушается. Чтобы предотвратить это явление, в практике горных работ применяют различные средства, т. е. им придают наи-
Рис.2.109. Виды проявления более устойчивые формы или возводят горного давления специальные строительные конструкции в
виде крепи.
113
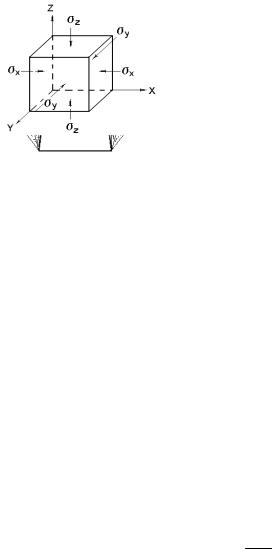
Рис. 2.110. Отслоения горной породы с образованием естественной свода над выработкой
Рис. 2.111. Напряжения, действующие на элементарную породную частицу в массиве
В толще земной коры в нетронутом массиве горные породы испытывают давление, обусловленное силой тяжести вышележащих толщ. При отсутствии тектонических сил и температурных градиентов, напряжения от собственного веса пород пропорциональны глубине. В массиве, не имеющем пустот, тектонических трещин и выработок, максимальная величина главных напряжений, действующих на горизонтальную площадку (в вертикальном направлении) на поверхности любой элементарной породной
частицы z , расположенной на рас-
стоянии H от земной поверхности, составит (рис. 2.111)
z H ,
где - приведенный объемный
вес вышележащих пород.
Напряженное состояние пород зависит не только от величины z , но и
от имеющих место тектонических процессов. Для районов, подверженных тектоническим нарушениям, при оценке z ,
вместо H принимается расчетная глубина Нр 1.5Н .
В результате воздействия величины z , боковые грани ее будут ис-
пытывать противодавление и она окажется в равновесно-напряженном состоянии в условиях всестороннего (трехосного) сжатия. Напряжения, действующие в горизонтальном направлении на вертикальные площадки, являются производными от z и определяются упругими деформационными
свойствами пород на рассматриваемой глубине. При этом:для упругого массива
х y 1 H 1 Н ;
для сыпучего массива
х y 2 H tg2(45o 2 ) H ,
114

где 1 1 - коэффициент бокового распора для упругой среды;
2 tg2(45o 2 ) - коэффициент бокового распора для сыпучей среды; -
угол внутреннего трения сыпучего массива; - коэффициент Пуассона.
Боковой распор в сыпучей среде обеспечивает зависание отдельных кусков породы за счет трения и зацепления друг с другом. Зависание будет продолжаться до тех пор, пока собственный вес куска не превысит силу трения между смежными кусками.
Массив горных пород лишенный сил сцепления между отдельными структурными блоками (массив горных пород в связи с наличием трещиноватости рассматривается как состоящий из отдельных структурных блоков, размером в), рассматривается как сыпучий, если оцениваемая область массива В (например, ширина выработки) в 3-4 раза превышает максимальный размер структурного блока (Вв 3 4) .
Оценка возможности рассматривать массив как упругую или сыпучую среду обеспечивается сравнением действующих напряжений Rсж с
прочностью горной породы сж
При сж Rсж , - возможно разрушение массива на отдельные струк-
турные блоки. В этом случае массив можно рассматривать как сыпучую среду.
Пределы прочности массива на сжатие Rсж и растяжение Rр устанавливаются зависимостями
|
Rсж сжКс ; |
Rр рКс , |
где сж |
- предел прочности пород на сжатие; р 0,1 сж - предел |
|
прочности пород на растяжение; Кс 0.2 0.9 |
- коэффициент структурного |
ослабления, представляющего собой отношение прочности пород в массиве к прочности в куске. Для Вв 14 , Кс 0.2 ; - коэффициент длительной
прочности. Значение коэффициента рекомендуется принимать: для пород
с хрупким характером разрушения (граниты, кварциты, песчаники с кварцевым цементом и т.п.) = 1 0,7, а для пород, испытавших пластические де-
формации перед разрушением (песчанистые, углистые сланцы известняки средней крепости и т.п.), = 0,5 0,7.
Принимая массив как сыпучий, а действующие напряжения в массиве - предельными, можно определить угол внутреннего трения по формуле
115
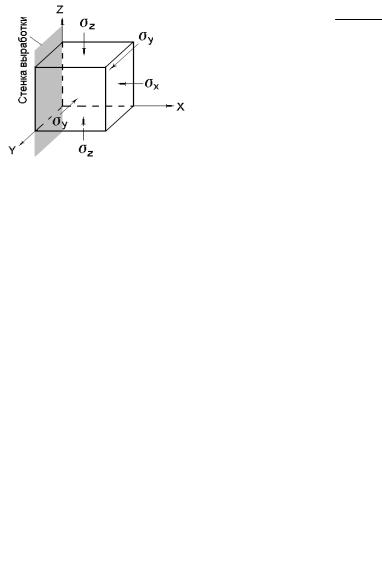
Рис. 2.112. Нарушение равновесного состояния напряжений, действующих на элементарную породную частицу в стенке выработки
tg Rсж Rр ,
Rсж Rр
arctg .
Когда в земной коре проводятся горные выработки, равновеснонапряженное состояние породы нарушается, поскольку изменяется первоначальный характер распределения напряжений в массиве (рис. 2.112), вследствие этого в массиве, граничащем с выработкой, возникают внутренние силы, направленные к контуру выработки
(горное давление).
.
Оценка напряженного состояния пород на контуре и расчет устойчивости незакрепленной выработки.
Под устойчивостью горных пород понимают их способность сохранять равновесие при обнажении.
Устойчивость горной выработки – способность ее сохранять задан-
ные ей размеры и форму в течение всего срока эксплуатации.
При проведении горизонтальной (наклонной) выработки в ее кровле и почве появляются области пониженных напряжений, а в боках – области повышенных напряжений. В кровле выработки вместо сжимающих напряжений, существовавших ранее в массиве,
Рис. 2.113. Распределение напряжений на контуре горизонтальной выработки
х или у , появляются растягивающие
напряжения. Повышение и понижение напряжений оценивается коэффициентом концентрации напряжений, под которым понимают отношение величины напряжений, существовавших в этой же точке до проведения выработки. На контуре выработки в массиве упругих пород напряженное состояние вне зоны влияния очистных работ, крупных пустот и тектонических трещин оценивается величиной максимальных сжимающих напряжений для боков и минимальных растягивающих напряжений в кровле (рис. 2.113):
для боков |
max |
K1 H ; |
для кровли |
min |
K2 H 1 , |
116
где K1 и K2 - коэффициенты концентрации сжимающих и растягивающих
напряжений.
Растягивающие напряжения в кровле на небольшой высоте переходят в сжимающие напряжения. Коэффициент концентрации сжимающих напряжений до проведения выработок равен единице. Коэффициент концентрации растягивающих напряжений принимается в долях от сжимающих и
зависит от формы выработки: K1 2 - для любой формы выработок; K2 1
для трапециевидных выработок; для выработок прямоугольно-сводчатой формы: K2 0.4 - при f 12 ; K2 0.3 при f 12 . В выработках кругло-
го сечения К2 0,2.
Оценка устойчивости контура незакрепленной выработки выполняется обычно для одноосного напряженного состояния по величине максимальных напряжений в рассматриваемой точке и определяется запасом прочности, численно показывающим во сколько раз допускаемые (расчетные) напряжения меньше предела прочности (временного сопротивления) массива горных пород.
Запас прочности вводится для расчета устойчивости обнажений горных пород в выработке по предельному состоянию, под которым понимают такое состояние, при котором выработка перестает удовлетворять заданным требованиям (находиться без крепи в период эксплуатации).
После определения напряжений max |
|
и min |
запасы прочности по- |
|||||||
родного массива в кровле nк и боках выработки nб |
оцениваются формула- |
|||||||||
ми: |
|
|
|
|
|
|
|
Rр |
|
|
|
|
R |
|
|
|
|
|
|||
n |
|
|
сж |
; |
n |
|
|
|
|
. |
|
|
|
|
|
||||||
б |
|
тах |
|
|
к |
|
min |
|
||
|
|
|
|
|
|
|
|
|
На основании полученных значений nк и nб делается вывод об устойчивости пород на контуре выработки:
n 4 - кровля и бока устойчивы;
1 n 4 - кровля и бока относительно устойчивы;
n 4 - кровля и бока неустойчивы.
Для определения величины горного давления в горизонтальных выработках используются расчетные методы, которые базируются на теории сводообразования и учитывают только активную нагрузку, действующую на крепь. Крепь в этом случае не препятствует сводообразованию.
В табл. 2.3 приведена классификация режимов нагрузки на крепь при соответствующих запасах прочности породного массива.
117
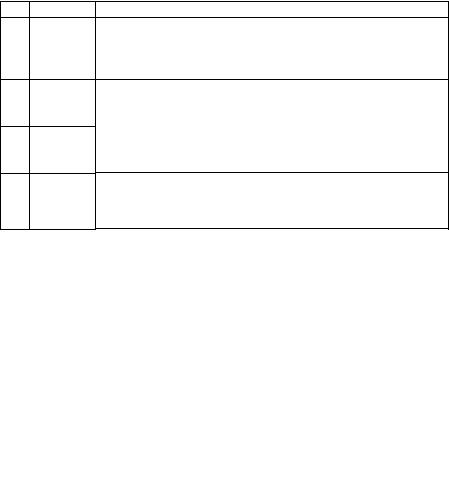
Таблица 2.3. Условный номер и классификация режимов нагрузки
№ Запас
1
nк 4 nб 4
2nк 1 nб 4
3nк 1 nб 1
41 nк 4
1 nб 4
Режим заданной нагрузки на крепь и расчетная схема Нагрузка на крепь отсутствует, и выработка может быть пройдена без крепи. В местах геологических нарушений, для пород, склонных к выветриванию необходимо покрытие выработки набрызг-бетоном толщиной до 3 см Крепь несет полную нагрузку со стороны кровли от веса
пород внутри свода естественного равновесия (обрушения). Бока устойчивы.
Крепь несет полную нагрузку со стороны кровли и боков; образуется новый контур выработки: в кровле - свод, в боках - призмы сползания.
Крепь не несет полной постоянной нагрузки со стороны кровли и боков; образуется новый контур выработки: в кровле - свод, в боках - призмы сползания.
В вертикальных горных выработках напряженное состояние пород оценивается максимальными вертикальными напряжениями на стенке (отдельно для протяженных участков и для участков сопряжения с другими выработками) и минимальными сжимающими напряжениями в горизон-
тальной плоскости (рис. 2.114). Максимальные сжимающие на-
пряжения
тах К3 H ,
Рис. 2.114. Распределение напряжений на контуре вертикальной выработки
где К3 – коэффициент концен-
трации сжимающих напряжений ( K3 3 - для протяженных участков;
K3 6 - для участков сопряжения с
другими выработками). Протяженный участок отсчитывается от уровня 20 м к сопряжению (рис. 2.114).
Минимальные сжимающие напряжения в горизонтальной плоскости определяются зависимостями:
для сечений круглой формы
тіп 2 Н 1 ; для сечений прямо-
угольной формы тіп Н 1 .
Контур вертикальной выработки можно считать устойчивым, если действующие напряжения на контуре не превышают прочность массива на сжатие и растяжение
118
|
|
Rсж |
|
1 ; |
R |
р |
1. |
|
|
|
|
|
тах |
min |
|
|
|||||
|
|
|
|
|
|
|
||||
Устойчивость контура вертикальной выработки оценивается по кри- |
||||||||||
терию устойчивости С , (табл. 2.4). При этом |
|
|
|
|
|
|||||
С |
|
|
|
КуН |
|
|
|
|
|
, |
26,3 К |
R |
5,25 0,0056К |
R |
|
||||||
|
|
сж |
|
|
|
|
сж |
|
|
где Ку - коэффициент воздействия на вертикальную выработку других выработок ( Ку =1,5 – для участков сопряжения; Ку =1 – для протяженных участков выработки); К - коэффициент, учитывающий угол залегания по-
род. Для пород залегающих горизонтально |
К =1. Для пород, залегающих |
||||||||
под углом , величина К определяется по формуле |
|
|
|||||||
|
|
К |
|
|
1 |
|
. |
|
|
|
|
|
|
|
|
|
|
||
|
|
1 |
0,5Sin |
|
|
||||
|
|
|
|
|
|
||||
Таблица 2.4. Группа и состояние устойчивости контура от величиныС |
|||||||||
|
|
|
|
|
|||||
|
Группа |
Состояние устойчивости пород |
С |
||||||
|
I |
Устойчивые |
|
|
|
|
|
<3 |
|
|
II |
Среднеустойчивые |
|
|
3…6 |
|
|||
|
III |
Неустойчивые |
|
|
|
|
|
6…10 |
|
|
IV |
Очень неустойчивые |
|
|
>10 |
|
Расчет горного давления производят с целью определения нагрузок на крепь и расчета ее прочных размеров.
При проведении горизонтальных горных выработок выбор расчетной схемы горного давления в скальных породах, которые не испытывают перед разрушением заметных пластических деформаций, можно выполнить на основе запаса прочности, используя классификацию режимов заданной нагрузки (табл. 2.3).
Горное давление на крепь, если оно определяется по теоретическим или эмпирическим формулам, принимается в качестве нормативного. В
этом случае расчетная нагрузка ( Qр ) определяется путем умножения нормативной нагрузки ( Q ) на коэффициент перегрузки ( nп ): Qр Qnп . Для камер и других выработок околоствольного двора nп =1.5, для остальных выработок - nп =1.2.
119
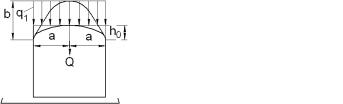
Для nк 4 и nк 1 (условный номер 2, табл. 2.3) нормативная нагрузка на крепь ( Q ) со стороны свода обрушения определяется по расчетному методу, предложенному М.М. Протодьяконовым (табл. 2.5).
Таблица 2.5. Расчетные формулы для определения горного давления в горизонтальных горных выработках
|
|
|
|
Форма выработки |
|
|
|
|
|
|
|
|
|
|
Трапециевидная |
|
|
|
|
Прямоугольно-сводчатая |
|
|
|||||||
|
|
|
|
|
|
|
|
|
|
|
|
|
|
|
|
|
|
|
Расчетные |
формулы |
|
|
|
|
|
|
|
|
|
1. Нагрузка на единицу длины |
1. Нагрузка на единицу длины вы- |
|
||||||||||||
выработки |
4a2 |
|
|
работки |
|
|
|
|
|
|
|
|
|
|
Q |
. |
|
|
4 |
|
|
a |
|
|
|
|
|||
|
|
|
Q |
|
|
|
|
h0 |
|
|
||||
|
|
|
|
|
||||||||||
|
|
|
|
|
|
|
|
|
||||||
|
3tg |
|
|
3 |
|
a |
|
|
|
|
||||
|
|
|
|
|
tg |
|
|
|
||||||
2. Высота свода обрушения |
2. Высота свода обрушения |
|
||||||||||||
b a / tg . |
|
|
b a / tg . |
|
|
|||||||||
3. Интенсивность максимального |
3. Интенсивность |
|
максимального |
|
||||||||||
нормативного давления |
нормативного давления |
|
|
|||||||||||
g1 b . |
|
|
g1 (b h0 ) . |
|
|
|
|
|
|
|
||||
|
|
|
||||||||||||
Где a – полупролет выработки; |
- удельный вес пород; - угол внут- |
|
||||||||||||
реннего трения пород; |
h0 - высота искусственного свода выработки по |
|
||||||||||||
проекту. |
|
|
|
|
|
|
|
|
|
|
|
|
|
|
|
|
|
|
|
|
|
||||||||
Для случая |
nк 1 |
и nб 1 когда кровля и бока неустойчивы (услов- |
ный номер 3, табл. 2.3) в кровле образуется свод обрушения, а в боках призмы сползания и отделившаяся порода начинает оказывать давление на крепь. За счет призм сползания полупролет выработки по кровле увеличивается на величину
C1 hctg ,
где arctg(450 / 2) – угол сползания породных призм; h - высота выработки.
120
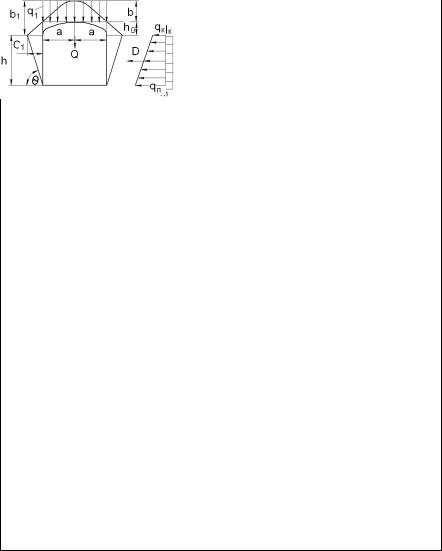
Нормативная нагрузка на крепь ( Q ) со стороны свода обрушения оп-
ределяется по расчетному методу, |
предложенному П.И. |
|
Цимбаревичем |
|||||||||
(табл. 2.6). |
|
|
|
|
|
|
|
|
|
|||
|
|
|
|
|
|
|
|
|
|
|
|
|
|
|
|
|
|
Форма выработки |
|
|
|
|
|
|
|
Трапециевидная |
|
|
Прямоугольно-сводчатая |
|||||||||
|
|
|
|
|
|
|
|
|
|
|
|
|
|
|
|
|
Расчетные |
формулы |
|
|
|
|
|
|
|
1. Нагрузка со стороны кровли на |
1. Нагрузка со стороны кровли на |
|||||||||||
единицу длины выработки |
единицу длины выработки |
|||||||||||
|
Q 2ab . |
Q 2a(b1 h0 ) . |
||||||||||
2. Высота свода обрушения |
2. Высота свода обрушения |
|||||||||||
b a hctg hctg . |
b |
a hctg . |
||||||||||
|
|
tg |
|
|
1 |
|
|
tg |
|
|
|
|
|
|
|
|
|
|
|
|
|
|
|||
3. Интенсивность максимального |
3. Интенсивность |
максимального |
||||||||||
нормативного давления со сторо- |
нормативного |
давления со стороны |
||||||||||
ны кровли |
|
|
кровли |
|
|
|
|
|
|
|||
|
g1 b . |
|
|
g1 (b1 h0 ) . |
||||||||
4. Интенсивность бокового дав- |
4. Интенсивность бокового давления |
|||||||||||
ления у кровли |
|
|
у кровли |
|
|
|
|
|
|
|||
|
qк b 2 . |
qк b1 2 . |
||||||||||
5. Интенсивность бокового давле- |
5. Интенсивность бокового давления |
|||||||||||
ния у почвы |
|
|
у почвы |
|
|
|
|
|
|
|||
|
qn b h 2 . |
qn b1 h 2 . |
||||||||||
6. Боковое давление пород |
6. Боковое давление пород |
|||||||||||
|
D |
qk qn |
|
h . |
D |
qk qn |
h . |
|||||
|
|
|
||||||||||
2 |
|
- коэффициент |
|
2 |
|
|
|
|||||
где 2 tg2(45o ) |
бокового распора для сыпучей сре- |
Таблица 2.6. Расчетные формулы для определения горного давления в горизонтальных горных выработках
2
ды.
121
Рассмотренная классификация режимов заданной нагрузки не включает все возможные сочетания показателей (запасов) прочности пород, однако позволяет оценить возможную ситуацию и выбрать расчетную схему применительно к конкретному случаю.
Например, если кровля относительно устойчива (1 nк 4 ), а бока неустойчивы ( nб 1), то для определения горного давления может приме-
няться расчетная схема приведенная в табл. 2.6. В этом случае нормативную нагрузку со стороны кровли (при 1 nк 4 ) определяют путем деления
нормативной нагрузки Q на действующий коэффициент запаса прочности nк , а со стороны боков будет полная нагрузка D .
При неустойчивой кровле ( nk 1) и относительно устойчивых боках (1 nб 4 ) применяют также расчетную схему по табл. 2.6 и поступают
аналогично вышеописанному. Такой подход к определению нагрузки правомерен, поскольку развитие дефектов в породном массиве, а также деформаций увеличивается с ростом напряжений. Если деформируемые породы не склонны к упрочнению, то деформации и степень нарушенности массива пропорциональны величине действующих в массиве напряжений.
Классификация (табл. 2.3) неприменима к слабым неустойчивым породам, которые задолго до разрушения склонны к пластическому течению,
при коэффициенте длительной прочности 0 5. (мергель, сланцы, доли,
глины и т.п.). В этих породах нагрузка на крепь должна определяться по СНиП П-94-80.
При определении нагрузки на крепь наклонной выработки рассматривается вертикальный разрез, а не нормальное сечение выработки (рис.
2.115). При этом вертикальное давления Q со стороны свода обрушения
раскладывается на две составляющие N и T :
N Qсоs , Т siп ,
где - угол наклона выработки.
Непосредственно на крепь оказывает давление нагрузка N , а T действует вдоль кровли выработки, стремясь опрокинуть рамную крепь или сколоть набрызг-бетонную крепь, если модуль упругости или деформации пород и крепи не совпадают.
Согласно рекомендациям П.И. Цимбаревича величину горного давления следует определять как:
1.N Qсоs , если 45о ;
2.N Qсоs45о , если 45о 80о ;
3.При 80о выработка рассматривается как вертикальная.
122
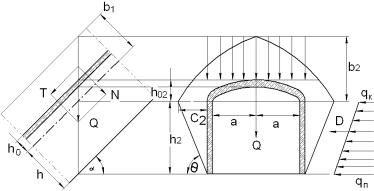
Величину горного давления при слоистой кровле, когда выработка пройдена по напластованию пород, следует определять, как для горизонтальных выработок.
В однородных породах все линейные размеры выработки при определении горного давления подставляются в соответствующие формулы с учетом угла наклона выработки. Вертикальная высота выработки увеличи-
вается до h2 h / cos , при этом увеличивается и высота свода обрушения до b2 (a h2ctg )tg h02 . Зная высоту b2 , легко определить вертикальную нагрузку Q 2ab2 и ее составляющие T и N по формулам, приведенным в табл. 2.6.
Рис. 2.115. Расчетная схема определения горного давления в наклонной выработке
Расчет горного давления в вертикальных горных выработках выпол-
няется в следующей последовательности.
1. Определяют нормативное горизонтальное (радиальное) давление (Рн, кПа) по формулам:
при С 6 , Рн 10 2C 1 ;
при С 6 , Рн 10 3C 7 ,
где С - критерий устойчивости; – параметр, учитывающий технологию проходческих работ: при последовательной и параллельной технологических схемах 0 ; при совмещенной технологической схеме: 2 (при
С6 ), и 3 (при С 6 ).
2.Определяют расчетное давление пород ( Рр, кПа) по зависимости
,Рр nmуnнPн1 0,1 rо 3
где rо – радиус выработки в свету или приведенный радиус выработ-
123
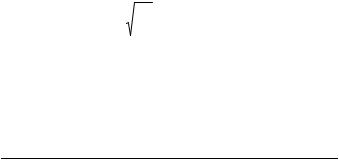
ки при ее прямоугольной форме - r |
|
|
|
Sсв |
); n 1,3 – |
коэффициент пере- |
|
o |
|
|
|||||
|
|
|
|
|
|
||
|
|
|
|
|
|
|
|
грузки крепи; mу |
- коэффициент условий работы крепи ( mу 0,5 - для на- |
||||||
брызг-бетонной |
крепи; mу 0,8 |
- |
для |
монолитной |
бетонной крепи; |
mу 0,75 - для сборной крепи); пн - коэффициент приведения к расчетному (максимальному) давлению при неравномерной эпюре нагрузок (табл. 2.7)
Таблица 2.7. Значения коэффициента nн |
|
||
Угол залегания |
nн , при схемах проходки |
||
пород , |
|
|
|
Последовательная и параллельная |
Совмещенная |
||
|
|||
< 10о |
2.00 |
1.75 |
|
10…35о |
2.50 |
2.00 |
|
> 35о |
2.75 |
2.25 |
Геологоразведочные шурфы проходят часто в наносных малосвязанных песчано-глинистых отложениях. В этом случае расчетное горизонтальное давление на крепь следует определять по формуле
|
|
o |
|
|
|
|
|
|
|
|
nk rotg(45 |
|
/ 2) 1 |
ro |
|
|
1 |
|
|
P |
|
|
|
|
, кПа, |
||||
|
|
o |
|
||||||
n |
1 |
|
|
|
/ 2) |
|
|
||
|
ro Htg(45 |
|
|
||||||
|
|
|
|
|
|
|
|
|
|
где k - коэффициент, принимаемый равным 1,7 если нет проемов в крепи; 2tg tg(45o / 2) - безразмерный коэффициент.
Основные крепежные материалы для изготовления горной крепи.
Горна крепь – искусственное сооружение, возводимое в выработке для предотвращения обрушения неустойчивых пород и сохранения необходимой площади поперечного сечения выработки на период эксплуатации.
По назначению крепежные материалы можно разделить на основные, используемые для несущей конструкции крепи (древесина, металл, камень, бетон, железобетон), и вспомогательные (водоизоляционные материалы, гвозди, болты, хомуты и др.).
Древесина. Для крепления горных выработок используют как хвойные, так и лиственные сорта породы дерева. Наиболее широко применяющиеся породы и сорта леса приведены на рис. 2.116.
Срок службы леса в шахтных условиях зависит от качества древесины и от условий, в которых находится крепь. Если по закрепленной древесиной выработке проходит сухой холодный воздух, то лес сохраняется лучше, чем при влажном и теплом. Срок службы крепи из хвойных пород дерева в плохих условиях составляет 3-6 месяцев; в средних условиях (при
124
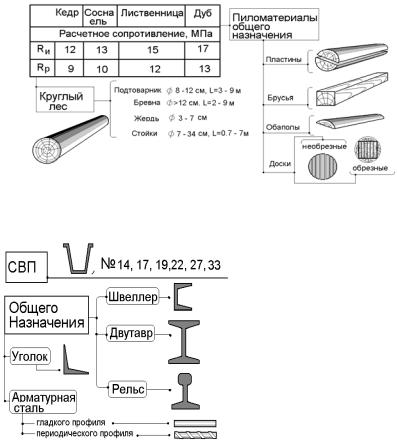
хорошем проветривании, но при переменном увлажнении и высыхании) – 1.5 – 3 года; в хороших (в сухих, хорошо проветриваемых выработках) до 5
лет.
Основным мероприятием, позволяющим продлить срок службы крепи, являются сушка и пропитка древесины специальными составами, называемыми антисептиками. Антисептики – это растворы минеральных солей (фтористый натрий, хлористый цинк и др.) от действия которых белки и углеводы (целлюлоза) древесины свертываются, а среда, получаемая при этом, становится ядовитой для грибков.
Рис. 2.116. Сортамент древесины для крепления выработок
Рис. 2.117. Сортамент металла для изготовления крепи
125
Металл. По прочности, долговечности и конструктивным возможностям металл является одним из наиболее современных материалов для крепи. Металлическую крепь изготавливают из черных металлов
– стали и чугуна. Для изготовления металлических рамных крепей преимущественное использование имеет желобчатый шахтный профиль проката СВП (специальный взаимозаменяемый профиль) шести типоразмеров, номер которого соответствует массе 1 м в кг.
В качестве стального проката применяют также швеллерные балки № 14 - 24;
двутавровые балки №14 - 30, , железнодорожные рельсы Р-38 и Р-43, рудничные рельсы Р-18, Р-24, Р-33, уголок и арматурную сталь (рис. 2.117).
Достоинством стали, как крепежного материала является высокая прочность при растяжении и сжатии. Для изготовления металлической шахтной крепи широко применяют специальные стали, характеризующиеся
высокой прочностью и пластичностью (предел текучести от 520 до 650 Н/мм2), и временным сопротивлением на разрыв от 700 до 900 Н/мм2.
Камень. Естественные камни – это изверженные, осадочные или метаморфизованные породы, добытые в карьерах или при проходке выработок. Широкого применения естественные обработанные камни не получили из-за большой стоимости их изготовления. Более широкое применение имеют искусственные камни (кирпич, бетониты), использующиеся при креплении капитальных выработок.
Бетон - затвердевшая смесь раствора цемента с песком, щебнем или гравием.
Для различной бетонной крепи используют портландцемент различных марок. Состав бетона обозначают в виде: 1:А:Б, (где 1 – весовая часть цемента; А – количество частей песка; Б – количество частей щебня или гравия). В зависимости от соотношения объемов цемента и песка растворы делятся на жирные (1:2 и 1:2.5) нормальные (1:3 и 1:3.5) и тощие (1:4). Для горной промышленности применяют жирные и нормальные растворы
(табл. 2.8).
Таблица 2.8. Состав и параметры бетона |
|
|
|
|
|||
|
|
Раствор |
Соотношение частей рас- |
||||
сж 100; 150; 200; 250; 300. |
|
|
твора |
|
|
||
|
|
1 |
1 |
1 |
|
1 |
1 |
|
|
А |
2 |
2.5 |
|
3 |
3.5 |
и( р) 0.1 |
0.17 сж |
|
|
|
|
|
|
|
|
|
|
|
|
|
|
|
|
Б |
4 |
5 |
|
5 |
6 |
Прочность бетона определяется его маркой, которая получается при испытании бетонного кубика с ребром 20 см на сжатие ( сж ) в возрасте 28
дней при температуре 18-20оС.
Железобетон. Для повышения механической прочности, особенно при изгибе и растяжении, бетон армируют сталью. Такой бетон называют железобетоном. В железобетоне используются свойства обоих материалов,
– бетон хорошо работает на сжатие, а металл на растяжение.
Бетон прочно сцепляется со стальной арматурой (круглая сталь диаметром 8-30 мм), и предохраняет сталь от коррозии. Для сборного железобетона кроме гладкой круглой арматуры применяют прутья периодического профиля из горячекатаной стали, и холоднотянутую проволоку диаметром
до 10 мм.
126
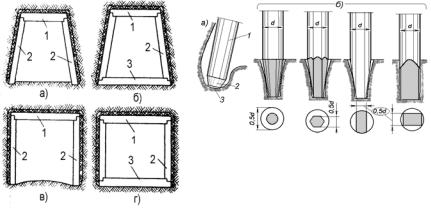
Основные конструкции крепи горизонтальных горных выработок.
Деревянная крепь широко применяется в выработках со сроком службы до 2 лет (при соответствующей обработке до 5 лет), в условиях установившегося давления и при невозможности извлечения крепи для повторного использования.
Основной конструкцией деревянной крепи является неполная крепежная рама трапециевидной (рис. 2.118, а) или реже прямоугольной формы (рис. 2.118, в), состоящей из верхняка 1 и двух стоек 2. Верхняк и стойки изготавливают из круглого леса диаметром более 15 см; в трапециевидной раме угол наклона стоек принимают равным 80-85о.
Выработки со слабой (пучащейся) почвой крепят полными крепежными рамами; дополнительным элементом полной рамы является лежень 3 (рис. 2.118, б, г), укладываемый на почву выработки.
Нижние концы стоек иногда заостряют на конус, при этом конструкция крепи становится податливой; после установки рамы она при большом первичном горном давлении сверху может опускаться без поломок на 10-15 см за счет внедрения в породу почвы и смятия заостренных концов (рис. 2.119). Податливость крепи обеспечивает увеличение срока ее службы. Чтобы под влиянием бокового давления стойки рамы не выжимались внутрь выработки, концы их заводят в лунки глубиной 10 – 20 см, устраиваемые в
почве выработки.
Рис. 2.119. Заделка концов стоек: а) жесткая крепь; б) – податливая крепь; 1 стойка; 2 – конец стойки; 3 - лунка
Рис. 2.118. Крепежные рамы
При умеренном горном давлении, крепежные рамы устанавливают вразбежку (рис. 2.120, а) на расстоянии 0.5 – 1.5 м друг от друга; при значительном давлении их устанавливают вплотную одна к другой – сплошное крепление (рис. 2.120, б). В местах замкового соединения раму тщательно
127
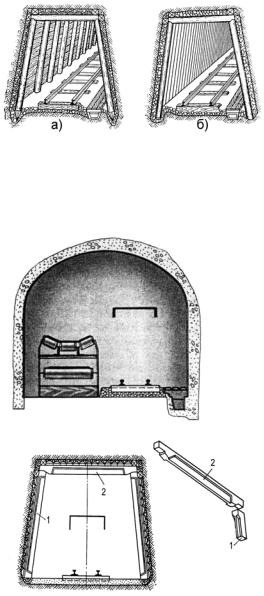
Рис. 2.120. Установка крепежных рам: а – вразбежку; б – сплошное крепление
расклинивают деревянными клиньями. При креплении вразбежку, кровлю и бока выработки для предохранения от вывалов породы ограждают затяжкой из обапол (при крепких породах бока выработки не затягивают). Диаметр крепежного леса рассчитывают исходя из величины горного давления.
|
|
Бетонную и желе- |
||||
|
зобетонную крепь (моно- |
|||||
|
литную и сборную) при- |
|||||
|
меняют на горных пред- |
|||||
|
приятиях |
для |
крепления |
|||
|
выработок с большим сро- |
|||||
|
ком |
службы. |
Бетонную |
|||
|
крепь (рис. 2.121) приме- |
|||||
|
няют в виде стенок с пло- |
|||||
|
ским или сводчатым пере- |
|||||
|
крытием в камерах и ка- |
|||||
|
питальных |
горных |
выра- |
|||
|
ботках при значительном, |
|||||
Рис. 2.121. Монолитная бетонная крепь |
но установившемся |
гор- |
||||
ном давлении. |
|
|
||||
|
|
|
||||
|
|
Основные операции |
||||
|
возведения бетонной кре- |
|||||
|
пи: приготовление бетон- |
|||||
|
ной смеси, доставка ее к |
|||||
|
месту |
работ, |
сооружение |
|||
|
опалубки, подача, распре- |
|||||
|
деление |
и |
уплотнение |
|||
|
смеси в опалубке. Бетон- |
|||||
|
ную смесь готовят глав- |
|||||
Рис. 2.122. Сборная железобетонная крепь |
ным образом централизо- |
|||||
ванно |
на |
поверхности, |
||||
|
доставляя к месту укладки в специальный контейнерах или по трубам, а за опалубку укладывают механизированным способом с помощью бетоноукладчиков (рис. 2.123). Толщина бетонной крепи зависит от размеров выра-
128
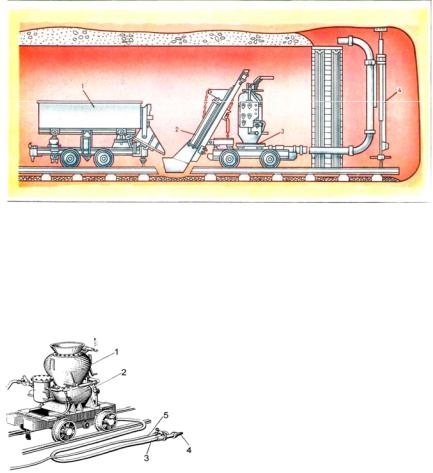
ботки и крепости пород. В горизонтальных и наклонных выработках толщина свода в замке – не менее 17 см, стены – не менее 20 см, в вертикальных выработках толщина стены не менее 30 см.
Рис. 2.123. Бетоноукладочный комплекс в забое: 1 – бетоновоз; 2 - загрузочное устройство; 3 - пневмонагнетатель; 4 – раздвижная упорная стойка
В настоящее время монолитную железобетонную крепь, особенно в зонах неустановившегося горного давления применяют редко. Более распространенной является сборная железобетонная крепь (рис. 2.122), а также рамная крепь из стальпластбетона.
|
Набрызг-бетонная крепь. Про- |
||
|
стейшей |
конструкцией |
набрызг- |
|
бетонной крепи является сплошное по- |
||
|
крытие стенок и кровли слоем набрыз- |
||
|
гбетона заданной толщины. Покрытие |
||
|
набрызгбетона имеет неправильную |
||
|
форму. Форма покрытия по существу, |
||
|
повторяет контур поверхности выработ- |
||
Рис. 2.124. Машина для нанесения |
ки, и толщина набрызг-бетонной крепи |
||
меняется от нескольких миллиметров на |
|||
набрызгбетона |
выступах породной поверхности до 5-7 |
см в углублениях, составляя в среднем 2
– 3 см. В крепких породах увеличивать толщину слоя бетона свыше 3 см нецелесообразно, поскольку существенно
возрастает расход материалов. На выступающих поверхностях толщина бетона не должна превышать 3 см. В углублениях бетон нужно набрызгивать так, чтобы лишь грубо выровнять поверхность.
Для крепления набрызг-бетоном применяют машины типа БМ-60,
129
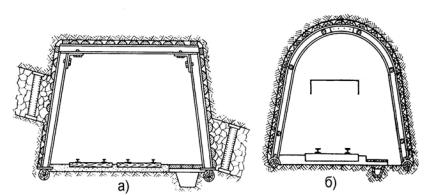
БМ-70 и др. (рис. 2.124). Сухая смесь из верхней камеры 1 поступает в материальный шлюз 2, где попадает в карманы вращающегося дозатора и потоком воздуха по шлангу 3 направляется к соплу 4. Смешиваясь с водой, по шлангу 5 раствор набрызгивается на поверхность выработки.
Металлическая крепь применяется в подготовительных и капитальных выработках в породах любой устойчивости и в зоне влияния очистных работ, а также при значительном горном давлении. Она может применяться в виде жесткой (рамной или арочной) крепи. Выработки, находящиеся в зоне влияния очистных работ, крепят арочной податливой или арочной шарнирной крепью.
Рис.2.125. Жесткая металлическая крепь
Рамную крепь (рис. 2.125, а) изготовляют из рельсовых или двутавровых балок. Стойки соединяют с верхняком с помощью литых башмаков или накладок, уголков и болтов с гайками.
Жесткая арка (рис. 2.125, б) состоит из двух полуарок, соединяемых в центральной части свода с помощью соединительных планок и болтов.
Арочную податливую крепь (рис. 2.126) выполняют из балок специального профиля. Она состоит из трех, четырех и пяти звеньев: арочного верхняка и двух, трех и четырех криволинейных стоек. Концы верхняка телескопически входят в стойки, что обеспечивает податливость крепи. Места соединения стягивают стальными хомутами 3. Величина податливости регулируется затягиванием хомутов с помощью гаек 5 и планок 4. Между собой арки соединяют стяжками 6, из полосовой стали, рельсов, или спецпрофиля. Стойки арки опираются стальными башмаками 1 на деревянные лежни 2.
Арочная шарнирная крепь (рис. 2.127) состоит из двух металлических двутавровых или рельсовых полуарок 1, свободно опирающихся в стыках на деревянные прогоны 4, и двух деревянных, металлических или железобетонных стоек 2. По длине каждого прогона монтируют две-три арки. Прого-
130
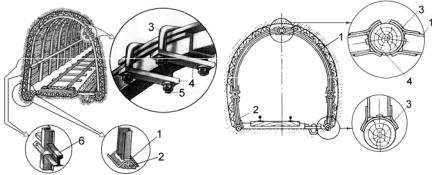
ны по длине выработок соединяют между собой строительными скобами. К концу каждой полуарки приварен штампованный башмак 3, который охватывает деревянный прогон, и образует шарнир. Податливость крепи достигается за счет смятия деревянных прогонов в шарнире или смятия заостренных концов деревянных стоек.
Рис. 2.126. Арочная податливая крепь |
Рис. 2.127. Арочная шарнирная крепь |
Каменную крепь из кирпича и бетонитов возводят на цементном растворе. Наиболее распространена крепь с прямыми стенками и сводчатым перекрытием. Обладает теми же качествами, что и бетонная.
Анкерная крепь предназначена для упрочнения массива горных пород и повышения устойчивости его обнажений путем скрепления различных по прочности слоев. Как самостоятельный вид крепи используется в породах с
коэффициентом крепости f 4 .
В анкерной крепи используют стержни из древесины, металлические стержни из мягкой конструкционной стали диаметром 20 – 38 мм с клинощелевыми замковыми устройствами, железобетонные и полимербетонные, закрепляемые по всей длине шпура (рис. 2.128).
Установка распорного металлического анкера (рис. 2.128, а) осуществляется следующим образом: стержень 2 с клином 1 вставляют в шпур до упора клина в дно шпура. По хвостовику стержня, выступающему из устья шпура, наносят удары (ручным или пневматическим молотком), вследствие чего клин входит в прорезь стержня, раздвигает разрезанные его части, и заклинивает их в шпуре. На выступающий конец стержня надевают деревянную подкладку 3, шайбу 6 и, завинчивая гайку 7, прижимают подкладку плотно к породе.
Иногда взамен стальных применяют деревянные стержни 3 из натуральной и прессованной древесины диаметром 30-80 мм, закрепляемые в шпурах нижним 5 и верхним 1 клиновыми замками (рис. 2.128, б) .
131
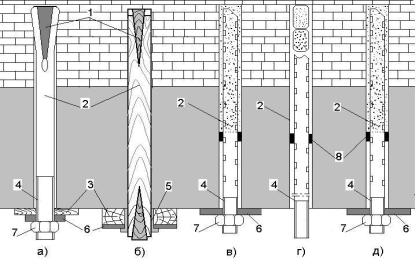
Рис. 2.128. Конструкции анкерной крепи:
1 – клин; 2 – стержень; 3 – подкладка; 4 –резьба; 5 – втулка; 6 – опорная плита; 7 – гайка; 8 - пробка а ) - металлический анкер с клиновым замком; б) – деревянный анкер; в) – железобетонный анкер; г) – процесс установки сталеполимерного анкера; д) – закрепление в шпуре сталеполимерного анкера.
Прочность стержней из прессованной древесины на разрыв, приближается к прочности стали. Древесина способно быстро набухать, впитывая влагу, что используется в некоторых конструкциях крепи не только для усиления их распора в шпуре, но и для натяжения. Стержень 2 с продольными прорезями на обоих концах можно устанавливать с набухающей деревянной подкладкой 3, между опорной шайбой 6 и породой, обеспечивающей натяжение стержня.
Чаще закрепление анкера обеспечивается с помощью цементных (песчано-цементных) растворов, которые подаются в шпур в ампулах (или специальным насосом) (рис. 2.128, в) или химическим составом (рис. 2.128, г), когда в шпур вводится необходимое количество ампул с химическим закрепителем (смола и отвердитель). Затем стержень, вращаемый с помощью сверла или перфоратора и подаваемый ко дну шпура, разрывает ампулы, перемешивая их содержимое. После затвердения цементного или полимерного раствора на выступающую часть анкера устанавливают опорную плиту, и создают предварительное натяжение гайкой (рис. 2.128, д).
Если выработка закреплена только анкерной крепью, то в местах интенсивной трещиноватости возможны отдельные вывалы или осыпание породы между анкерами. В этом случае прибегают к комбинированной крепи
132
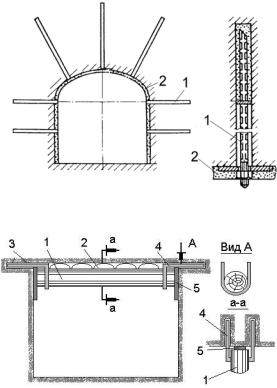
Рис. 2.129. Комбинированная крепь из анкеров и набрызгбетона
Рис. 2.130. Подвесная крепь
верхняков помещают затяжку 2 из обапол или досок.
(рис. 2.129). После ус-
тановки анкеров 1 выработку дополнительно крепят набрызгбетоном 2; иногда покрытие набрызгбетоном производят по проволочной сетке
При сравнительно устойчивой кровле и крепких устойчивых боковых стенках используется
подвесная (бесстоечная) крепь. Элемента-
ми такой крепи являются деревянный верхняк 1 с распорными планками 5, и металлические подвески 4. Под кровлей выработки в боках пробуривают короткие шпуры, в которые вставляют подвески 4, а в них укладывают деревянные верхняки
1 (рис. 2.130). При не-
обходимости поверх
Смешанная крепь изготавливается из двух и более различных материалов. Крепь применяют как постоянную (реже как временную) при креплении сопряжений и капитальных выработок (чаще камер) с большим сроком службы, и при значительном горном давлении.
При креплении такой крепью более прочный материал используется в элементах, непосредственно воспринимающих горное давление. Некоторые конструкции смешанной крепи приведены на рис. 2.131: рамы из деревянных или железобетонных трубчатых стоек 1 и металлических верхняков 2 (рис. 2.131, а); в виде сплошной крепи из каменных стен и сводчатого перекрытия из монолитного бетона (рис. 2.131, б); в виде сплошной крепи из каменных или бетонных стенок с перекрытием из металлических или деревянных балок (рис. 2.131, в).
133
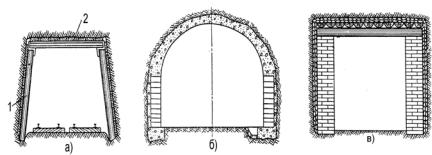
Рис. 2.131. Конструкции смешанной крепи
Костровая крепь представляет собой располагаемые на некотором расстоянии друг от друга крепежные конструкции столбчатой формы, которая собирается из отдельных деревянных, металлических или пневмобаллонных элементов, укладываемых друг на друга в определенном порядке. Применяется в очистных выработках в качестве посадочной крепи при управлении горным давлением способами обрушения и плавного опускания кровли. В подготовительных выработках используется для закладки пустот над крепью при значительных вывалах породы из кровли выработки.
На современных шахтах деревянную костровую крепь применяют при управлении горным давлением плавным опусканием кровли на почву, металлическую – обрушением кровли в лавах с пологопадающими пластами.
Костры собирают из деревянных или металлических брусьев, балок длиной от 0.7 до 1.2 м. В качестве деревянных элементов используют рудничные стойки и брусья. В качестве балок для металлических костров – отрезки отожженных (для уменьшения хрупкости) старых рудничных рельсов или двутавра. Конструкции придают форму прямоугольной или треугольной клетки, заполняемой или не заполняемой породой (рис. 2.132, в, г).
В очистном забое костровую крепь размещают по падению пласта параллельно забою в один или два ряда (рис. 2.132, а). Расстояние между кострами в ряду по падению 2 – 3 м.
Для плавного опускания кровли в лавах крутопадающих пластов используется пневматическая костровая крепь из соединенных между собой 2- 4 мягких подушкообразных оболочек, которые изготавливаются из резинокорда и рукавных капроновых тканей (рис. 2.132, г).
Костровую крепь для закладки пустот применяют при восстановлении заваленных выработок, когда высота свода обрушения не превышает 2- 3 м. Костры выкладывают над крепью (рис. 2.132, б) таким образом, чтобы давление по возможности передавалось на стойки рам, а не на верхняки.
134

Рис.2.132. Костровая посадочная крепь
Временная крепь горизонтальных и наклонных выработок. При от-
сутствии возможности возводить постоянную крепь вслед за подвиганием забоя, для безопасного ведения буровзрывных работ и погрузки породы устанавливают временную крепь.
Назначение временной крепи - предохранять проходчиков от возможных вывалов или обрушения кусков породы с кровли.
При рамной деревянной крепи ее возводят в призабойном пространстве на участке около 3 м от забоя, сразу же после взрывания шпуров, проветривания и осмотра забоя, а при монолитной бетонной крепи – на участ-
ках в 20-40 м в зависимости от условий и свойств боковых пород.
В горизонтальных и наклонных выработках применяются следующие
135
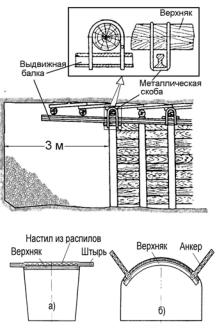
виды временной крепи: консольная выдвижная; подвесная (при отсутствии в выработке бокового давления и пучения пород); рамная (при наличии бокового давления).
Консольная выдвижная предохранительная крепь
(рис. 2.133) состоит из двух консольно-расположенных у кровли выработки металлических балок и опирающегося на них предохранительного перекрытия в виде настила из деревянных распилов или из верхняков с затяжками.
Консольные балки свободно подвешиваются на скобах к верхнякам постоянной крепи; конструкция скоб позволяет легко передвигать балки с перекрытием вслед за забоем выработки. При сплошной бетонной или железобетонной постоянной крепи консольные балки подвешиваются в скобах к анкерам, за-
крепляемым в породах кровли.
Подвесная временная крепь (рис. 2.134) представляет собой перекрытие в виде
деревянного верхняка на штырях (рис. 2.134, а), или в виде верхняка из спецпрофиля (швеллера или стальной полосы) и двух-трех анкеров, с помощью которых верхняк удерживается под кровлей выработки. На верхняк укладывается затяжка или металлическая сетка.
Рамная временная крепь может быть переносной (повторно используемой) и непереносной. Переносные рамные крепи - металлические арки, трапециевидные или прямоугольные рамы с быстроразъемными соединительными узлами. Конструкция этих крепей аналогична серийно выпускаемым металлическим, применяемым для постоянного крепления выработок.
Непереносные рамные временные крепи – серийные крепежные металлические рамы, которые устанавливаются непосредственно у забоя и используются в дальнейшем в качестве составной части постоянной крепи. При установке в выработках постоянной бетонной или железобетонной крепи непереносная крепь остается в бетонном массиве в виде жесткой ар-
матуры.
136
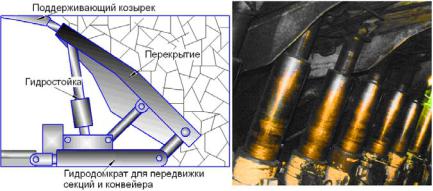
Механизированные крепи (МК). Механизированной называется крепь очистных комплексов и агрегатов, все секции которой кинематически связаны между собой и передвигаются с помощью домкратов вслед за подвиганием забоя. Она состоит из отдельных секций, каждая из которых имеет основание, гидравлические стойки, верхняк и гидравлический домкрат для передвижки секций. МК ограждает призабойное пространство, механизирует процесс крепления и управления кровлей. Секции механизированной крепи устанавливаются в забой по всей длине лавы.
По характеру взаимодействия с боковыми породами МК подразделяются на крепи поддерживающего, оградительно-поддерживающего и под- держивающе-оградительного типов.
Крепи поддерживающего типа применяются на пластах тонких и частично средней мощности. В них оградительные элементы могут отсутствовать, или выполнять вспомогательную роль, предотвращая проникновение обрушенных пород в рабочее пространство лавы.
Оградительно-поддерживающая крепь (рис. 2.135) имеет серповид-
ное ограждение, поддерживающее обрушенные породы кровли и предотвращающее их проникновение в рабочее пространство лавы, а также козырек, поддерживающий кровлю непосредственно у забоя.
Крепи поддерживающе-оградительного типа имеют поддерживаю-
щие и оградительные элементы, активно воспринимающие нагрузку со стороны пород кровли.
Секции крепей могут быть одно- и многостоечными. По числу рядов стоек они могут быть одно-, двух и трехрядными. Передвижение секций и передвижка конвейера осуществляется гидродомкратом, расположенным в нижней части основания. Передвижка секций состоит из следующих операций: разгрузка секции из-под давления, подтягивание ее гидродомкратом к конвейеру, распор.
Рис. 2.135. Схема МК оградительно-поддерживающего типа
137
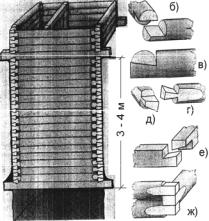
Особенности конструкции крепи наклонных выработок. Крепь на-
клонных выработок в зависимости от их назначения и срока службы может быть деревянной, металлической, бетонной и железобетонной. В горно-
разведочных выработках практически находит применение только деревянная крепь. Основной конструкцией деревянной крепи для выработок с наклоном до 45о является крепежная рама, при большем наклоне – венец. При наклоне менее 15о выработки обычно крепят рамами трапециевидной формы, при больших углах применяют прямоугольные рамы.
Характерные изменения в конструкциях крепи выработок с различными углами наклона сводятся к следующему:
- при 10о – неполные крепежные рамы по своей конструкции не отличающиеся от крепи горизонтальных выработок, однако расклинку рам производят с большей тщательностью;
- при (10 – 20о) – между стойками смежных рам устанавлива-
ются распорки;
- при (30 – 45о) – крепь упрочняется поперечными лежнями, т.е. неполные крепежные рамы заменяются на полные крепежные рамы, между которыми верху и внизу устанавливают распорки;
- при 45о – крепь превращается в венцовую на стойках, причем
при выработках значительного сечения в конструкцию венцовой крепи входят и опорные венцы.
Наклонные выработки могут крепиться также сплошной рамной или венцовой крепью.
а)
Рис. 2.136. Сплошная венцовая крепь. Соединение элементов венца
Крепь вертикальных выра-
боток. Для крепления вертикальных горных выработок – стволов шахт, шурфов, восстающих и др., как и для прочих выработок, применяют деревянную, металлическую, бетонную, железобетонную, анкерную и комбинированную крепь.
Деревянную крепь применя-
ют для крепления выработок небольшой площади сечения и малым сроком службы (стволы разведочных шахт, шурфы различного назначения, восстающие и др.). Такая крепь представляет собой прямоугольные венцы из круглого леса, брусьев, пластин или толстых досок
(рис. 2.136).
138

Различают венцовую крепь сплошную, на стойках и подвесную. Сплошную венцовую крепь (рис. 2.136, а) применяют для крепления
выработок, проводимых по слабым породам, испытывающим всестороннее горное давление. Венцы укладывают один на другой вплотную в виде сруба. Элементы венца соединяют между собой в виде прямых односторонних (рис. 2.136, б) и двусторонних (рис. 2.136, ж) или в виде косых односторонних (рис. 2.136, в, е) и двусторонних (рис. 2.136, г, д) «лап».
В конструкции крепи выделяются опорные (основные) и обычные (рядовые) венцы. У основного венца, служащего для поддержания рядовых венцов бревна по короткой или длинной стороне имеются выступающие на 0,3-0,5 м концы (пальцы), которые заводятся в специальные лунки, устраиваемые в стенках выработки.
По способу возведения сплошная венцовая крепь может выполняться
снизу-вверх или сверху-вниз.
Рис. 2.137. Возведение деревянной крепи снизу-вверх
Рис. 2.138. Возведение деревянной крепи сверху-вниз
Способ возведения крепи снизу-вверх используется при условии, что породы допускают обнажение стенок выработки на 4-8 м.
Укладка основного и рядовых венцов приведена на рис. 2.137.
Каждый брус опорного венца вставляют одним из выступающих пальцев в меньшую по сечению лунку, а вторым выступающим пальцем укладывают горизонтально через заводную лунку.
Опорные венцы тщательно расклиниваются, а лунки забутовываются. Иногда вместо опорного венца по короткой стороне выработки в лунки укладываются два опорных бревна.
На опорный венец (опорные бревна) укладываются рядовые венцы. Пространство между стенками шурфа и крепью забутовывается кусками породы. Работы по возве-
139
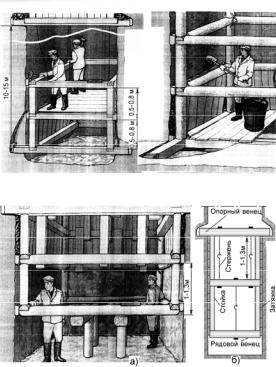
дению крепи на длине звена (4-8 м) выполняются до вышерасположенного опорного венца.
В слабых, неустойчивых породах сплошная венцовая крепь возводится сверху-вниз вслед за проходкой. При этом элементы рядовых венцов подвешивают к основному венцу скобами (рис. 2.138).
|
|
Венцовая крепь на |
||||
|
стойках |
|
(рис.2.139) |
|||
|
применяется при устой- |
|||||
|
чивых породах или ко- |
|||||
|
гда |
устойчивость |
боко- |
|||
|
вых |
пород |
позволяет |
|||
|
пройти 1,5-3 м шурфа |
|||||
|
без крепления. Крепь на |
|||||
|
стойках устанавливается |
|||||
|
снизу-вверх. |
|
Длина |
|||
|
звеньев принимается в |
|||||
|
пределах 5-10 м. Рядо- |
|||||
Рис. 2.139. Возведение крепи на стойках |
вые |
венцы |
устанавли- |
|||
|
вают на стойках длиной |
|||||
|
0,5-0,8 м. Стойки с эле- |
|||||
|
ментами |
венца обычно |
||||
|
соединяют в паз и скре- |
|||||
|
пляют скобами. Рас- |
|||||
|
стояние между венцами |
|||||
|
затягивают досками или |
|||||
|
горбылем |
и |
забутовы- |
|||
|
вают вынимаемой поро- |
|||||
|
дой. |
Подвесная |
крепь |
|||
|
|
|||||
|
(рис. 2.140) применяется |
|||||
Рис. 2.140. Возведение подвесной крепи: |
при проходке шурфов в |
|||||
глинистых породах, ко- |
||||||
а – крепь на досках; б – инвентарная крепь |
||||||
|
гда можно пройти уча- |
сток шурфа на глубину 1-1,5 м без крепления. При этом используется подвесная крепь на досках или металлических стержнях (металлическая инвентарная крепь, рис. 2.140,
б).
К установленному в выработке опорному венцу на подвесках из горбылей (стержней) подвешивают промежуточный венец и соединяют оба венца между собой стойками. В процессе углубки нижний венец подпирается временными стойками, длина которых с углубкой увеличивается. Расстояние между венцами затягивают горбылем или досками, и забучивают. Рядовые и основные венцы расклиниваются деревянными клиньями.
140
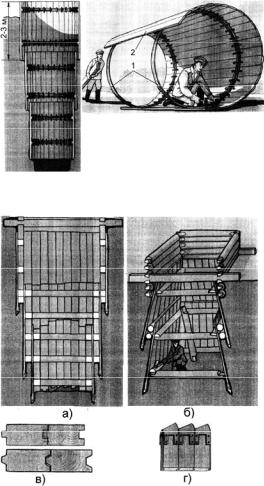
При проходке шурфов круглого сечения (в мягких породах) используется каркасная крепь, состоящая из металлических каркасов 1 и деревянной опалубки 2. Звенья крепи длиной 2-3 м различного диаметра собираются на поверхности и опускаются в пройденный участок, формируя ступенчатую форму шурфа (рис. 2.141). Диаметр каждого последующего уступа меньше предыдущего на 0,2 – 0,3 м. Диаметр самого нижнего уступа 1 м.
|
|
При проходке шур- |
||||
|
фов в весьма неустойчи- |
|||||
|
вых |
породах, |
плывунах |
|||
|
применяется |
опережаю- |
||||
|
щая забивная крепь. Креп- |
|||||
|
ление |
|
забивной |
крепью, |
||
|
которая |
может |
быть как |
|||
|
наклонной (рис. 2.142, б), |
|||||
|
так и вертикальной (рис. |
|||||
|
2.142, а), производится в |
|||||
|
следующей |
последова- |
||||
Рис. 2.141. Крепление шурфов круглого сечения |
тельности: в устойчивых |
|||||
каркасной крепью |
породах над плывуном ус- |
|||||
|
танавливается |
основной |
||||
|
венец, к которому на ско- |
|||||
|
бах подвешиваются рядо- |
|||||
|
вые венцы до кровли плы- |
|||||
|
вуна; внутри нижнего на- |
|||||
|
ружного венца размещает- |
|||||
|
ся внутренний венец; ме- |
|||||
|
жду этими венцами поме- |
|||||
|
щают деревянные брусья, |
|||||
|
плотно подогнанные друг |
|||||
|
к другу (рис. 2.142, в), ко- |
|||||
|
торые забиваются в поро- |
|||||
|
ду на 0,2-0,3 м, с услови- |
|||||
|
ем, чтобы брусья по пери- |
|||||
|
метру |
опускались |
равно- |
|||
|
мерно; внутри крепи вы- |
|||||
|
бирается порода. |
Нижние |
||||
|
торцы брусьев усиливают- |
|||||
Рис. 2.142. Крепление шурфа забивной крепью: |
ся металлом (рис. 2.142, г). |
|||||
|
После забивки кре- |
|||||
а – вертикальная крепь; б – наклонная крепь; |
|
|||||
пи на всю длину на забое |
||||||
в – соединение брусьев крепи; г – усиление брусь- |
||||||
ев металлом |
снова |
|
устанавливаются |
|||
наружный и внутренний |
||||||
|
||||||
|
венцы, |
между |
которыми |
|||
141 |
|
|
|
|
|
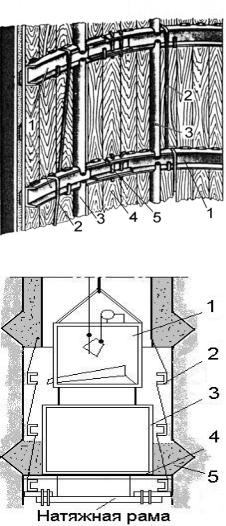
помещаются деревянные брусья. Операция забивки крепи повторяется. Бетонная крепь представляет собой сплошной монолитный цилиндр
с опорными венцами, устраиваемыми через каждые 30-60 м. Применяют бетонную крепь и без опорных венцов.
При проходке ствола на глубину звена его крепят временной крепью, состоящей из составных металлических колец, подвешиваемых по мере подвигания забоя в направлении сверху вниз. Кольца металлической крепи (рис. 2.143) изготовляют из швеллерных балок 1, которые соединяются штырями 5. Расстояние между кольцами временной крепи обычно 1,0-1.5 м. Для подвешивания колец используют
Рис. 2.143. Временная крепь ствола крючья 2 из круглой стали диаметром 25-30 мм. Между
кольцами для большей жесткости устанавливают стойкираспорки 3 из металлических труб. Пространство между кольцами и стенками затягивают досками 4.
По окончании проходки звена сооружают опорный венец (рис. 2.144). Расстояние между опорными венцами устанавливается в зависимости от устойчивости пород. Опорные венцы 5 обычно возводятся с подвесного проходческого полка 1 с использованием опалубки 3 и деревянного помоста 4
Рис. 2.144. Возведение бетонной крепи с |
При |
укладке |
бетона в |
опорными венцами: |
опорном венце заделываются |
||
|
крючья |
подвески |
первого |
кольца временной крепи. Над опорным венцом возводят бетонную крепь. Кольца временной крепи 2 постепенно убирают. Если при этом имеется
142
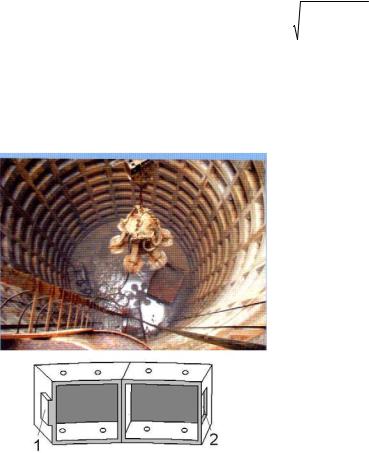
опасность обрушения породы, то временную крепь не убирают, а оставляют внутри бетона. Как правило, бетонную смесь при возведении крепи подают с поверхности по специальным бетоноводам. Толщину крепи из монолитного бетона в зависимости от условий принимают от 200 до 500 мм, иногда и более.
При определении прочных размеров крепи ее толщину d определяют по формулам
|
Pp Rвн |
|
150 |
|
|
сж |
|
|
|
d |
|
, или d R |
|
1 |
|
, |
|||
сж Pp |
сж |
|
сж 2Pр |
|
|||||
|
|
вн |
|
|
|||||
|
|
|
|
|
|
|
где Рр - наружное давление на кольцо крепи; Rвн - внутренний ради-
ус бетонного кольца; сж - допустимое напряжение материала кольца.
Монолитный железобетон применяют в случае неравномерного давления на крепь ствола. Толщина крепи 200-400 мм. Рабочую арматуру рас-
полагают горизонтально, а распределительную вертикально. |
|
|||
|
|
Сборный |
железобе- |
|
|
тон применяют в виде от- |
|||
|
дельных |
камней, которые |
||
|
могут иметь формы сегмен- |
|||
|
тов |
или прямоугольников. |
||
|
Железобетонные |
сегменты |
||
|
называют |
тюбингами. Из |
||
|
тюбингов собирают кольца |
|||
|
крепи, имеющие взаимную |
|||
|
связь (рис. 2.145). Сечение |
|||
|
ствола в этом случае круг- |
|||
|
лое. Соединение |
тюбингов |
||
|
в |
кольцо |
осуществляется |
|
|
благодаря наличию на од- |
|||
|
ном ребре выпуклой по- |
|||
|
верхности 1, а на другом – |
|||
|
соответствующей |
вогнуто- |
||
|
сти 2. Кольца подвешивают |
|||
|
на болтах к выше установ- |
|||
Рис. 2.145. Тюбинговая крепь ствола |
ленному |
тюбинговому |
||
кольцу. Для предупрежде- |
ния обрыва болтов, соединяющих тюбинги, проводится тампонаж за тюбингового пространства после установки не более шести колец, а также расклинку тюбинговой крепи не менее чем в четырех местах перед каждым взрыванием.
Тюбинговая крепь возводится с подвесного полка или непосредст-
143
венно из забоя.
Наличие у тюбингов кольцевых ребер существенно повышает аэродинамическое сопротивление стволов. Крепь из тюбингов стоит дорого, а поэтому крепь из монолитного бетона успешно конкурирует с крепью из тюбингов.
2.8. Вентиляция горных выработок
Основной задачей вентиляции горных выработок является исключение вредного воздействия на человека ядовитых газов, содержащихся в рудничном воздухе, высоких и низких температур, предотвращения опасного скопления газа и пыли в выработке. В общем случае проветривание, как производственная операция, обеспечивает безопасность и высокую производительность работ.
Рудничным называется воздух, поступающий в подземные горные выработки и претерпевающий изменения в процессе перемещения по ним. Эти изменения выражаются, прежде всего, в уменьшении содержания кислорода и увеличении содержания углекислого газа.
К основным причинам уменьшения содержания кислорода в воздухе выработок относятся окисление горных пород, древесины, ведение взрывных работ, работа двигателей внутреннего сгорания.
В рудничном воздухе может оказаться целый ряд ядовитых газов, к предельно-допустимым концентрациям (ПДК) которых (в объеме рудничного воздуха) Правила безопасности предъявляют жесткие требования
(табл. 2.9).
Рудничная пыль - мелкие и мельчайшие частицы твердого минерального вещества, которые долгое время способны находиться в рудничной атмосфере, во взвешенном состоянии или осевшие на поверхностях выработок.
Взвешенная в воздухе рудничная пыль называется аэрозолем. Наиболее опасными являются пылинки крупностью от 0,2 до 10 мкм, способные проникать в альвеолы легких. Витающая в воздухе пыль, если ее концентрация превышает санитарные нормы, может явиться причиной профессиональных легочных заболеваний (пневмокониоз).
Поэтому санитарные нормы строго ограничивают количество пыли (ПДК) в рудничном воздухе, и, прежде всего минеральной пыли, содержа-
щей кристаллический кремнезем ( SiO2 ), являющийся источником такой болезни, как силикоз:
-для пыли, содержащей 70%SiO2 - 1 мг/м3;
-для пыли, содержащей 10 70%SiO2 - 2 мг/м3;
-для пыли, содержащей 10%SiO2 - 4 мг/м3.
144
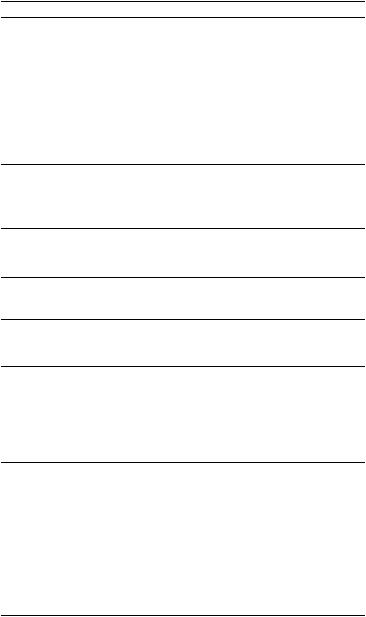
Таблица 2.9. Условия образования и ПДК ядовитых газов в выработ-
ках |
|
|
Причина образования. Последствия. ПДК. |
|
|
Газ |
|
|
|
||
Окись угле- |
Взрывные работы, рудничные пожары, взрывы метана и |
|
|||
рода СО |
угольной пыли, работа |
двигателей внутреннего сгорания |
|
||
|
(ДВС). Смертельное отравление наступает после непродол- |
|
|||
|
жительного вдыхания воздуха с содержанием СО =0,4%. |
|
|||
|
ПДК 0.0016%, (20 мг/м3). |
|
|||
Углекислый |
Взрывные работы, работа ДВС, гниение древесины, окисле- |
|
|||
газ, СО |
ние угля, выделение из массива горных пород и подземных |
|
|||
2 |
вод. |
|
При содержании |
СО =15-20% человеку угрожает |
|
|
|
|
|
2 |
|
|
смерть. ПДК 0,5% - у рабочих мест; 0,75%- всей шахты |
|
|||
Сероводо- |
Выделение из калийных солей и минеральных источников. |
|
|||
род H 2S |
Разложение серосодержащих пород шахтными водами, гние- |
|
|||
|
ние древесины и органических веществ. |
|
|||
|
ПДК 0.00066%, (10 мг/м3) |
|
|||
Сернистый |
Взрывные работы по сернистым породам, выделение из мас- |
|
|||
газ SO2 |
сива горных пород, содержащих серу. |
|
|||
|
ПДК 0.00035%, (10 мг/м3) |
|
|||
Окись азота |
Взрывные работы. При контакте с кислородом образует NO2 |
|
|||
NО |
и N |
О . ПДК 0.00025%, (5 мг/м3) |
|
||
|
|
2 |
4 |
|
|
Аммиак |
Разложение азотсодержащих соединений, особенно при |
|
|||
NН3 |
взрывных работах в апатит-нефелиновых рудах. |
|
|||
|
ПДК |
0,0025%, (20 мг/м3) |
|
|
|
Водород |
Встречается на калийных и угольных месторождениях как |
|
|||
Н2 |
примесь к метану и углеводородам, выделяется при зарядке |
|
|||
|
аккумуляторов. Горит и взрывается при содержании в воз- |
|
|||
|
духе от 4 до 72 %, температура воспламенения 577-590 о С. |
|
|||
|
Взрывается мгновенно без индукционного периода. |
|
|||
|
ПДК = 0,5% |
|
|
||
Метан |
В больших количествах встречается на угольных месторож- |
|
|||
СН4 |
дениях, в меньших – на месторождениях калийных солей, в |
|
|||
|
небольших – не месторождениях других полезных ископае- |
|
|||
|
мых. Образует с воздухом взрывчатую смесь. При концен- |
|
|||
|
трации СН4 : 5—16%—взрывоопасен. Метановоздушная |
|
|||
|
смесь взрывается при температуре 635 о С и более. |
|
|||
|
Согласно правилам безопасности концентрация СН4 в ис- |
|
|||
|
ходящей струе из забоев |
1%, в исходящей струе шахты |
|
||
|
0,75%, в поступающей струе 0,5%. |
|
|||
|
|
|
145 |
|
|
При определенных концентрациях и температурах, пыль может воспламеняться и гореть. Воспламенение и горение пыли в свою очередь может вызвать взрыв.
В угольных шахтах пыль может взорваться при полном отсутствии метана. При содержании угольной пыли в воздухе метановоздушная смесь
становится взрывчатой при количестве метана менее 5%. Если СН4 нахо-
дится в воздухе в количестве 2 %, и пыль содержит летучие горючие вещества более 15%, то она взрывается. Опасная концентрация пыли в рудничном воздухе: в газовых шахтах – 5 г/м3; в не газовых шахтах – 16-20 г/м3.
Важными фактором, влияющими на климатические условия в выработке, является температура. При температуре воздуха выше +22°С начинается снижение работоспособности проходчика. Если принять работоспособность при температуре 18—22°С за 100%, то при 26°С она составит 84%, а при 30°С — лишь 60%. Кроме того, у рабочих повышается утомляемость и вероятность травмирования.
При температуре свыше 26°С принимаются специальные меры по ее снижению. Охлаждение воздуха осуществляется с помощью воздухоохладительных приборов, установленных на поверхности шахт.
Холодильные машины для кондиционирования воздуха применяются в том случае, когда горные породы и воздух в шахтах имеют повышенную температуру, при которой другие средства не обеспечивают требуемого охлаждения воздуха.
Контроль состава рудничной атмосферы. При проведении и экс-
плуатации выработок систематически контролируется содержание в их атмосфере кислорода, углекислого газа, вредных веществ, в том числе пыли, а также скорость воздуха, его температура и влажность, которые не должны превышать предельно-допустимых концентраций и норм.
Периодичность контроля. В соответствии с правилами безопасности систематическому контролю подлежат следующие параметры рудничного воздуха:
концентрации в рудничном воздухе кислорода, углекислого газа, метана, оксидов углерода и азота;
концентрация водорода в зарядных камерах;
запыленность воздуха;
расход и скорость движения воздуха;
относительная влажность воздуха при его температуре более 20°С;
температура воздуха.
Периодичность контроля воздуха должна составлять: в выработках не газовых шахт I и II категории по газу (табл. 2.10), а также в камерах — не реже одного раза в месяц; в выработках шахт III категории — не реже 2 раз в месяц; в выработках сверхкатегорийных шахт и опасных по внезапным выбросам — не реже 3 раз в месяц.
146
Содержание СН4 замеряют в шахтах I и II категорий—не менее 2
раз в смену и в шахтах III категории и сверхкатегорийных—не менее 3 раз в смену. Степень покрытия и слеживаемость инертной пыли должны проверяться ежесуточно.
Таблица 2.10. Разделение шахт на категории
Категория |
Количество СН4 , выделяющегося на 1 т добычи, м3 |
шахты |
|
I |
До 5 |
II |
От5 до 10 |
III |
От 10 до 15 |
IV, сверхка- |
Свыше 15 (или шахты, разрабатывающие взры- |
тегорийные |
воопасные пласты) |
Для получения информации о составе и состоянии рудничной атмосферы применяются два метода – химико-аналитический (лабораторный анализ) и экспресс-метод (оперативный анализ).
Экспресс-метод позволяет быстро определять содержание газов в забоях, выработках и камерах непосредственно во время измерения с помощью переносных приборов.
Химико-аналитический метод основан на отборе проб шахтного воздуха, взятого в подземной выработке и последующем их анализе в химической лаборатории.
В экспресс-методе применяются два типа газоанализаторов – химические универсальные газоопределители и интерференционные газоопределители.
Действие химических газоопределителей основано на изменении окраски реактива в стеклянных ампулах при пропускании через них исследуемого воздуха. С помощью таких приборов устанавливают содержание СО, Н2S, SO2, NO2 и CO2. Длина окрашенной части столбика индикаторного вещества в ампуле пропорциональна концентрации определяемого газа.
Действие интерференционных газоопределителей основано на принципе измерения смещения интерференционной картины в связи с разностью показателей преломления от одного источника лучей света, пропускаемых через чистый воздух и газовоздушную смесь (шахтные интерферометры). С помощью таких приборов определяется концентрация О2, CH4 и CO2.
Для определения содержания водорода используются приборы, дей-
ствие которых основано на изменении теплопроводности газовой смеси в
зависимости от концентрации в ней H2.
Основным способом определения весовой концентрации пыли является фильтрация запыленного воздуха через предварительно взвешенный фильтр. В связи с осаждением пыли в фильтре, последний получает привеску. Разделив привес пыли на количество просасываемого воздуха, опреде-
147
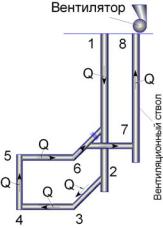
ляют весовую концентрацию пыли. Для экспресс-метода определения концентрации пыли применяется пылемер ФПГ-6, работа которого основана на принципе фотометрического изменения интенсивности луча света, проходящего через запыленный воздух.
Скорость движения воздуха в выработках измеряется с помощью приборов, называемых анемометрами. По конструкции анемометры бывают крыльчатыми (техническими) с пределами измерения от 0,1 до 10 м/с, чашечными – от 1 до 20 м/с и термоэлектрическим - до 0,5 м/с.
Относительная влажность воздуха контролируется с помощью гиг-
рометров, гигрографов и психрометров. Нормы на допустимую относительную влажность воздуха в горных выработках в Правилах безопасности не содержатся, однако этот параметр воздуха горных выработок учитывается и влияет на величину максимально допустимой температуры.
Измерение температуры производится спиртовыми или ртутными термометрами, а также термографами – приборами для измерения температуры с записью ее значений на ленте в виде графической зависимости от времени.
Схемы проветривания шахт. Вентиляционная сеть шахты – это система соединенных между собой подземных выработок шахты, обеспечивающая направление движения воздуха для проветривания, включающая также источник тяги (вентилятор). Движение воздуха в вентиляционной сети поддерживается при помощи напора (или разрежения), создаваемого одним или несколькими вентиляторами.
Различают четыре вида вентиляционных соединений выработок: последователь-
ное, параллельное, диагональное и комбинированное.
Последовательным (рис.2.146) назы-
вают такое соединение выработки, при котором вентиляционная струя в объеме Q дви-
|
жется последовательно по каждой выработке |
||
|
(1 2 3; 3 4, 4 5, 5 6 7 8) не |
||
|
разветвляясь. |
|
|
|
|
Параллельным соединением выработок |
|
|
называют такое соединение, при котором вы- |
||
|
работки в одном пункте (на рис. 2.147 – это |
||
|
пункт 3) разветвляются, а в другом общем |
||
|
пункте (6), соединяются в соответствии с |
||
Рис. 2.146. Последовательная |
чем, |
происходит разветвление воздушной |
|
схема вентиляционного соеди- |
струи, |
и ее слияние. На рисунке параллель- |
|
нения выработок |
ными |
будут струи 3 4; |
5 6 и 3 7; |
|
8 6, |
каждая из которых, |
в свою очередь, |
148
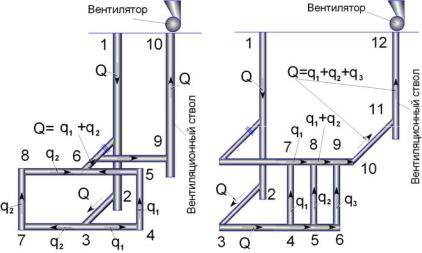
представляет последовательное соединение нескольких выработок. Диагональным соединением называют такое соединение, при котором
две параллельные выработки соединяются между собой еще одной (простое соединение), или несколькими дополнительными выработками (сложное соединение) (рис.2.148).
Смешанным (комбинированным) соединением является вся система соединений выработок шахты, считая от устья воздухоподающей шахты и заканчивая диффузором вентилятора
Рис. 2.147. Параллельная схема венти- |
Рис. 2.148. Диагональная схема венти- |
ляционного соединения выработок |
ляционного соединения выработок |
Схемы проветривания тупиковых выработок. В зависимости от дли-
ны или глубины выработок и с учетом конкретных горно-геологических и горнотехнических условий, вентиляция таких выработок осуществляется с помощью вентиляторов местного проветривания и вентиляционных труб, а в некоторых случаях путем использования турбулентной диффузии и продольных перегородок.
За счет диффузии разрешается проветривание горизонтальных выработок протяженностью не более 10 м, а вертикальных – глубиной не более
5 м.
Местное проветривание тупиковых выработок с использованием вентиляторов производится нагнетательным, всасывающим и комбинированным способами.
149
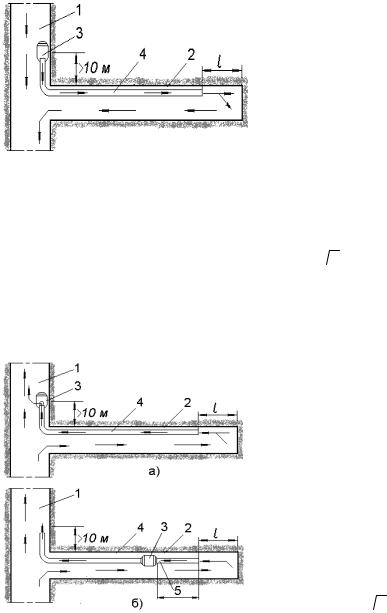
|
При нагнетательном |
|
способе проветривания (рис. |
|
2.149) вентилятор 3 устанав- |
|
ливается на свежей струе вы- |
|
работки 1 на расстоянии не |
|
менее 10 м от устья проветри- |
|
ваемой выработки 2. Свежий |
|
воздух поступает в призабой- |
|
ное пространство по вентиля- |
|
ционным трубам 4, а загряз- |
Рис. 2.149. Схема нагнетательного спо- |
ненный удаляется от забоя по |
соба проветривания вентиляторами |
выработке. |
|
Достоинства этого спо- |
соба: быстрое освобождение призабойного пространства от ядовитых газов после взрывных работ; возможность применения, как металлических труб, так и легких, эластичных труб из прорезиненной ткани. Расстояние уста-
новки труб до забоя устанавливается в пределах l 6 S (где S - сечение
выработки), но не более чем на 8 м в горизонтальной выработке, а в вертикальной – не более чем на 5 м.
Недостатком нагнетательного способа проветривания состоит в том, что удаление вредных газов и пыли происходит через всю выработку с небольшой скоростью, что при значительной длине выработки увеличивает время проветривания. Такой способ рекомендуется для проветривания вы-
работок длиной до 300 м.
При всасывающем спо-
собе проветривания (рис. 2.150, а) вентилятор 3 устанавливается в основной выработке со стороны исходящей струи воздуха на расстоянии не менее 10 м от устья проветриваемой выработки 2 и отсасывает воздух по трубам 4 из призабойного пространства.
Для эффективного проветривания максимальное отставание конца труб от забоя
Рис. 2.150. Схема всасывающего способа проветривания вентилятором
150
должно быть l 3 S .
Всасывающий способ целесообразен для проветривания протяженных вырабо-
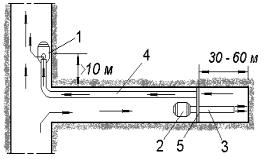
ток, поскольку независимо от длины выработка не загрязняется (за исключением призабойной части) ядовитыми продуктами взрыва, что позволяет на части длины выработки начинать некоторые работы до полного удаления из забоя газов.
Основной недостаток способа заключается в том, что в ходе проветривания у забоя не происходит интенсивного перемешивания воздуха. Зона разрежения, из которой вентилятором засасывается воздух, имеет небольшую глубину. Вследствие этого у забоя могут образовываться области застоя с повышенной концентрацией ядовитых газов. Поэтому такой способ не эффективен в выработках с большой площадью поперечного сечения. Кроме того, из-за необходимости близкого подвода конца трубопровода к забою, имеют место поломки труб при взрывных работах, а также, учитывая, что на участке от забоя до вентилятора в трубе нет избыточного давления, исключается возможность применения труб из прорезиненного материала.
Частично последний недостаток устраняется путем размещения вентилятора 3 (если имеется возможность) в проветриваемой выработке с использованием в призабойной части трубопровода из металлических труб 5
|
(рис. 2.150, б). |
|
||
|
|
При комбинирован- |
||
|
ном способе (рис. 2.151) по |
|||
|
длине |
выработки |
прокла- |
|
|
дывается трубопровод 4, по |
|||
|
которому из забоя |
с помо- |
||
|
щью вентилятора 1 отсасы- |
|||
|
вается |
загрязненный воз- |
||
|
дух, а в призабойной части |
|||
|
– дополнительно трубопро- |
|||
Рис. 2.151. Схема комбинированный способ |
вод 3 для подачи к забою |
|||
свежего воздуха вентилято- |
||||
проветривания вентиляторами |
||||
|
ром 2. |
|
|
Нагнетательный вентилятор 2 устанавливается за пределами зоны, загрязняемой вредными газами и пылью при взрывных работах, которая, в среднем, составляет около 50 м. Для устранения подсоса загрязненного воздуха нагнетающим вентилятором 2, его производительность принимается на 10-20% ниже производительности всасывающего вентилятора 1 (при сооружении перемычки 5 на расстоянии 30 – 60 м от забоя), и на 30% ниже - при отсутствии перемычки.
При любом способе проветривания производительность вентилятора местного проветривания не должна превышать 70% того количества воздуха, которое подается к его всасу за счет общешахтной депрессии, иначе эти вентиляторы будут нарушать принятую схему вентиляции.
Местное проветривание производится не только после взрывания
151
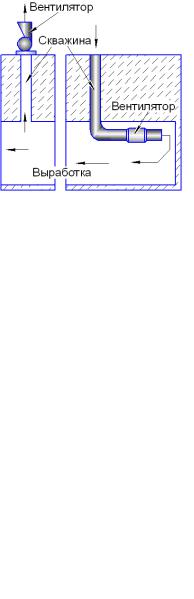
шпуров в забое, но и в момент погрузки породы, бурения и других работ.
|
Проветривание выработок с помо- |
|
щью скважин (рис. 2.152). При значитель- |
|
ной длине выработок, сравнительно не- |
|
большом расстоянии до земной поверхно- |
|
сти или при наличии вышерасположенно- |
|
го разведочного горизонта (на разведоч- |
|
ной шахте) целесообразно использовать |
|
для проветривания вентиляционные сква- |
|
жины. Предпочтение скважинному вари- |
|
анту проветривания отдается на основе |
|
технико-экономического сравнения этого |
|
способа с обычным при прокладке трубо- |
|
провода по всей выработке. |
Рис. 2.152. Варианты схем про- |
Применение скважин позволяет ос- |
вободить выработку на основной ее длине |
|
ветривания выработок вентиля- |
от трубопровода. При бурении вентиляци- |
ционными скважинами |
онных скважин можно получить дополни- |
|
тельную геологическую информацию о |
горных породах.
Сами скважины, выполнившие функцию как вентиляционные, могут быть использованы для других технических целей – прокладки труб и кабелей, доставки длинномерных материалов и т.д.
Скважины работают преимущественно во всасывающем режиме, а вентилятор устанавливается над устьем скважины. В соответствии с Правилами безопасности скорость движения воздуха по скважинам не ограничивается.
Рис. 2.153. Вентилятор местного проветривания ВМ-6
При проведении горизонтальных горно-разведочных выработок наибольшее распространение получили нагнетательный и комбинированный способы проветривания с применением осевых вентиляторов типа ВМ (рис. 2.153) и
СВМ.
В качестве вентиляционных труб широко применяются гибкие вентиляционные трубы, изготовленные из специальной хлопчатобумажной ткани с двухсторонним резиновым покрытием. Промышленностью выпускаются также гибкие трубы на основе капроновой ткани, комбинированной ткани (лавсан с хлопком) с покрытием резиной или по-
152
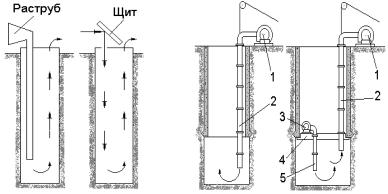
лихлорвинилом. Наряду с гибкими получают распространение и жесткие трубопроводы из синтетических материалов, а также металлические трубы.
Проветривание шурфов и стволов. В простейшем случае проветри-
вание шурфов (при глубине до 10 м) может осуществляться с использованием скоростного напора ветра. Для этого над устьем шурфа устанавливается щит или раструб (рис. 2.154), соединенный с трубопроводом, опущенным в шурф.
Во всех других случаях проветривание шурфов и стволов осуществляется с помощью вентиляторов.
Проветривание шурфов и стволов шахт при проходке осуществляется путем нагнетания свежего воздуха по вентиляционным трубам (рис. 2.155, а). Этот способ эффективен при глубине ствола до 350 м и времени проветривания 30 мин.
При большей глубине стволов нередко используется комбинированная схема проветривания (рис. 2.155, б). В этом случае вентилятор 1 работает по всасывающей схеме через трубы 2, а вентилятор 3, установленный на подвесном проходческом полке 4, работает по нагнетательной схеме, через металлические трубы 5. Наращивание труб производится с проходческого полка. Трубы крепятся к стенкам ствола, а на конец трубопровода устанавливается насадка, обеспечивающая эффективное проветривание с расстояния 10-15 м при времени проветривания 20-30 мин.
|
а) |
б) |
Рис. 2.154. Схемы проветривания |
Рис. 2.155. Схемы проветривания ство- |
|
неглубоких шурфов |
лов вентиляторами |
Расчет параметров проветривания тупиковых выработок и выбор вентилятора.
Воздухопотребность разведочных выработок зависит от интенсивности загрязнения воздушной среды и нормативных требований.
Расчет необходимого количества воздуха Q (м3/с) производится по разным факторам (табл. 2.11): 1 - по числу людей, одновременно занятых в
153
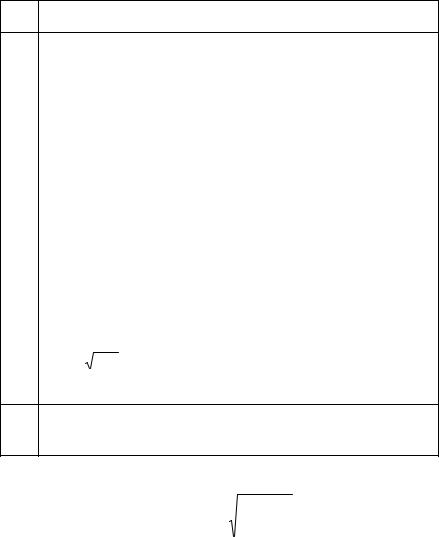
подземных условиях в наиболее многолюдную смену; 2 - по пылевому фактору; 3 - по интенсивности выделения газов, образующихся при взрывных работах; 4 - по эффективной скорости движения воздуха; 5 - по «скрытой энергии» дочерних продуктов распада радона (при разведке месторождений радиоактивных руд); 6 - по суммарной мощности ДВС, работающих в выработке.
Таблица 2.11. Необходимое количество воздуха для проветривания выработки Фак Необходимое количество воздуха тор
1
ловека, м3/с; n - общая численность людей в наиболее многолюдную смену
2 |
n |
|
|
|
|
Q q ; где n - число действующих выработок, в которых вы- |
|||
|
i 1 |
|
|
|
|
полняются работы, сопровождающиеся пылевыделением; |
q - ко- |
||
|
личество воздуха, необходимое для одного забоя, м3/с ; |
|
||
|
q VmiпS ; Vmiп - минимальная скорость струи, обеспечивающая пы- |
|||
|
леудаление (Vmiп =0.35 м/с); S - площадь сечения выработки |
|||
3* |
n |
|
|
|
|
Q q ; где n - число тупиковых выработок, в которых в течение |
|||
|
i 1 |
|
|
|
|
смены ведутся буровзрывные работы; q - количество воздуха, не- |
|||
|
обходимое для каждой выработки, м3/с* ; |
|
||
4 |
Qmiп 60VS ; |
где V - |
минимальная скорость движения воздуха по |
|
|
выработке, |
равная |
0,15 м/с; с учетом пылевого |
фактора |
|
V 0,35м/ с. |
|
|
|
|
|
|
|
|
5 |
Q 74 ДW ; где Д - общий дебит радона в систему проветри- |
|||
|
||||
|
ваемых выработок, атом/с; W - общий объем проветриваемых вы- |
|||
|
работок, м3. |
|
|
|
6 Q 0,113N ; где: 0,113- минимально допустимое количество воз-
духа на кВт мощности ДВС, м3/с; N - суммарная мощность работающих ДВС, кВт *для нагнетательного способа проветривания необходимое количест-
во воздуха q может быть определено по формуле В.Н.Воронина
q |
2,25 |
|
3 |
AW 2 b |
; |
|
60t |
|
|
Kу2 |
|
|
154 |
|
|
|
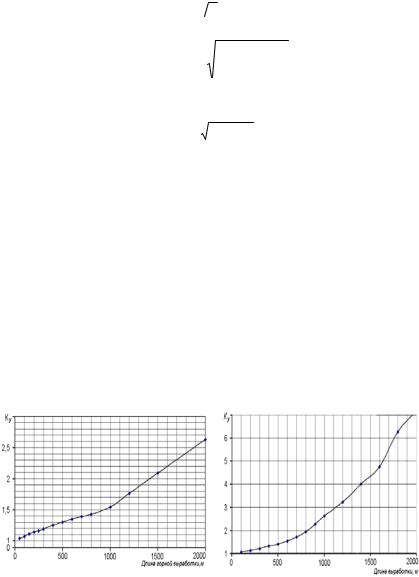
*при всасывающем способе проветривания при максимальном удалении конца вентиляционных труб 0,5 S величина q может быть определена по формуле А.И. Ксенофонтовой
|
2,13 |
|
|
A |
|
|
q |
|
AbS 15 |
|
|
|
; |
60t |
|
|||||
|
|
|
S |
|
*при комбинированном способе проветривания для оценки значения q используется формула В.Н. Воронина
q |
2,3 |
|
|
2 |
2 |
|
|
|
AbS |
L |
|
, |
|||
60t |
|
|
|||||
где t время проветривания, |
мин; |
|
A - количество одновременно |
взрываемого ВВ, кг; W SL - объем проветриваемой выработки, м3; b - газовость ВВ: b = 40 л/кгпри взрывании по породам; b =100 л/кг – при взрывании по углю; Ку - коэффициент утечек воздуха в трубах; - коэффици-
ент обводненности ( =0,3 – для горных выработок, проводимых по водоносным породам; =0,6 – для горных выработок, проводимых по влажным породам; =0,8 – для горных выработок, проводимых по сухим породам);
L – расстояние от забоя до перемычки или конца всасывающего трубопровода, м.
Для определения коэффициентов утечек воздуха гибких трубопроводов ( Ку ) диаметром до 600 мм при длине звена 20 м, и для трубопроводов
диаметром 700-1200 мм при длине звена 10 м можно использовать графические зависимости, предложенные, соответственно на рис. 2.156 и 2.157.
Рис. 2.156. Графическая зависимость |
Рис. 2.157. Графическая зависимость |
для определения утечек воздуха гибких |
для определения утечек воздуха гиб- |
трубопроводов диаметром до 600 мм |
ких трубопроводов диаметром 700- |
при длине звена 20 м |
1200 мм при длине звена 10 м |
155 |
|
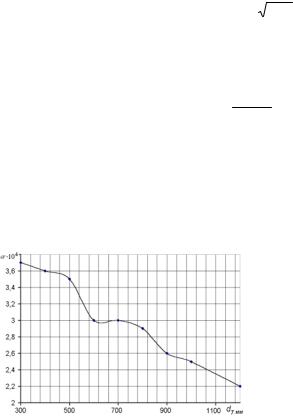
Для металлических трубопроводов коэффициент утечек воздуха подсчитывается по формуле
|
|
1 |
|
L |
2 |
|
Ky |
|
|
KcdT |
T |
|
, |
|
3 |
Lзв |
0.1R 1 |
|||
|
|
|
|
|
||
где LТ - длина трубопровода, м; |
dТ – диаметр трубопровода, м; Kс - |
удельный стыковой коэффициент воздухопроницаемости; Lзв - длина звена,
м; R - аэродинамическое сопротивление, Нс2/м8.
R 6,5 LT , dT5
где – коэффициент аэродинамических сопротивлений металлических труб (рис. 2.158). При использовании старых труб коэффициент повышается на 25%, при использовании новых и гладких труб – снижается на
25%.
Коэффициент Kс зависит от качества сборки трубопровода: удовлетворительное с допустимыми утечками воздуха Kc =0,002-0,005; хорошее с
незначительными утечками воз-
духа - Kc =0,001-0,002; удовле-
творительное качество сборки допускается при длине трубопровода до 450 м; Kc =0,003 при
уплотнении стыков с помощью прокладок из пенькового каната и промасленного картона; Kc =0,0006 – при уплотнении с
помощью резиновых прокладок и качественной сборке.
Рис. 2.158. Зависимость величины от
диаметра труб
Выбор вентиляционной установки местного проветривания. Из определенного расчетным путем необходимого количества воздуха (по факторам 1-6) (табл. 2.11) выбирается
максимальное значение ( Qз ).
В соответствии с правилами безопасности воздухопотребность действующих выработок должна быть увеличена в 1,43 раза - Qп 1,43Qз .
Необходимая производительность вентилятора определяется из выражения
Qв КуQп , м3/с
156

Депрессия вентилятора Нв, Па рассчитывается по формуле
Нв Нс Нм Нд ,
где Нс КуRQ2 - статическая составляющая депрессии; Нм 0,2Нс - местные потери давления;
Нд VT2 - динамическая составляющая потерь давления; 2g
12 Н/м3 - удельный вес воздуха.
По расчетным вентиляционным параметрам Нв и Qв подбирают
ближайшие типоразмеры вентиляторов местного проветривания.
Если Нв и Qв ниже необходимых параметров, то принимается более
мощный вентилятор или трубопровод большего диаметра, так как с его уменьшением растет аэродинамическое сопротивление и, как следствие, возрастает расход электроэнергии.
Рис. 2.159. Последовательное подключение вентиляторов
Рис. 2.160. Каскадное расположение вентиляторов
157
В практике геологоразведочных работ применяют совместное подключение вентиляторов местного проветривания. Подключение может быть последовательным и параллельным.
Если вентилятор по Нв подобрать нельзя, то
принимают к установке два или несколько вентиляторов, работающих последовательно в одном металлическом трубопроводе. При такой установке вентиляторы должны
обеспечить расчетное Qв
и в сумме давать давление, равное Нв . Вентиля-
торы рассредоточивают по длине трубопровода (рис. 2.159).
Если для проветривания применяют гибкие прорезиненные трубы, то
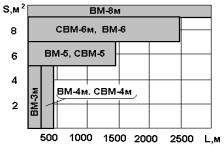
вентиляторы устанавливают один за другим без разрывов со стороны свежей струи воздуха - так называемое каскадное расположение вентиляторов (рис. 2.160). В этом случае вентиляторы должны иметь одинаковую произ-
водительность Qв (подачу) и будут обеспечивать суммарную депрессию
Нв (давление).
При комбинированном способе проветривания двумя вентиляторами без перемычки количество воздуха в конце всасывающего трубопровода определяется по формуле А.И. Ксенофонтовой. После определения Q рас-
считывается производительность всасывающего вентилятора Qвс в
том же порядке, как и для нагнетательного способа проветривания. Подача нагнетательного вентилятора принимается с учетом соотношения Qн 0,8Qвс .
Приближенно тип вентилятора может быть определен по
Рис. 2.161. Область применения рис. 2.161. вентиляторов
2.9. Водоотлив при проходке горных выработок
Водоотливом называется комплекс мер по удалению на поверхность воды, поступающей в горные выработки из водоносных пород.
Водоприток в горные выработки оценивается количеством притекающей в них в единицу времени воды (м3/ч) и может достигать нескольких десятков, а в целом по шахте – сотен и даже тысяч кубометров в час.
Водоотлив при проходке вертикальных горных выработок. Приток воды в вертикальные горные выработки (шурфы, стволы) является следствием вскрытия водоносных пластов, которые дренируют воду в выработку.
Наиболее простым и надежным способом водоотлива является выдача возы из забоя бадьями одновременно с выдаваемой породой (рис. 2.162). Такой способ применяется при проходке шахтных стволов с водопритоком до 3м3/ч, и шурфов с водопритоком до 0.3м3/ч. При этом бадьи наполняются водой забойными (зумпфовыми) насосами.
Количество воды, выдаваемое бадьями на поверхность определяется, по формуле Qб nKзVбКп (где n - число подъемов в час; KзVб - полезная
вместимость бадьи, м3 (уровень воды должен быть на 10 см ниже кромки бадьи); Кз - коэффициент заполнения бадьи; Vб - вместимость бадьи, м3;
158
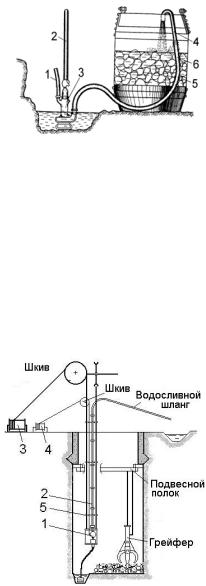
Кп (Кр 1) / Кр - коэффициент пустот в породе; Кр - коэффициент раз-
рыхления породы). |
В тех случаях, когда приток во- |
|
|
||
|
ды превышает возможную производи- |
|
|
тельность бадьевого подъема воды, во- |
|
|
доотлив из вертикальных горных вы- |
|
|
работок осуществляется насосами. При |
|
|
этом может быть использован одно- |
|
|
ступенчатый водоотлив (прямой) ко- |
|
|
гда откачка воды из водосборника |
|
|
производится сразу на поверхность, |
|
Рис. 2.162. Откачка воды в бадью: 1 |
или многоступенчатый водоотлив, ко- |
|
гда из нижних горизонтов вода перека- |
||
и 2 – шланги для подачи и отвода воз- |
чивается в промежуточные водосбор- |
|
духа; 3 –забойный насос; 4 – патру- |
ники вышележащих горизонтов и за- |
|
бок; 5 – бадья; 6 - шланг |
||
тем на поверхность. |
||
|
||
|
При одноступенчатом водоот- |
ливе применяются подвесные насосы. Такая схема водоотлива (рис. 2.163) используется, когда глубина выработки не превышает величину напора подвесного насоса. Насос 1 и став водоподъемных труб 2, подвешиваются на двух ветвях каната. Один конец каната закрепляется на подшкивной площадке копра, другой огибает блок, установленный на раме насоса. При подъеме насоса канат навивается на барабан проходческой лебедки 3. Кабель навивается на барабан кабельной лебедки 4. Водоподъемные трубы и кабель крепятся к канату специальными хомутами 5, устанавливаемыми в
зависимости от глубины выработки через 4-6 м. |
|
|
|
|
|
На поверхности к ставу труб |
|||
|
подсоединяется водосливной шланг, |
|||
|
по которому вода поступает в водо- |
|||
|
отливную канавку. |
|
|
|
|
Как правило, водоотлив по |
|||
|
одноступенчатой схеме применяется |
|||
|
при проходке стволов, глубина ко- |
|||
|
торых не превышает 350 м. |
|
||
|
В процессе водоотлива насос |
|||
|
должен находиться в 4-5 м от забоя, |
|||
|
а приемный клапан |
всасывающего |
||
|
шланга помещаться в приямок, в ко- |
|||
|
тором собирается вода. |
|
|
|
|
Перед взрывными |
работами |
||
|
водоотлив временно |
прекращается. |
||
Рис. 2.163. Одноступенчатый |
Насос поднимается |
над |
забоем |
на |
проходческий водоотлив: |
20-25 м. При подъеме |
насоса |
от |
|
|
159 |
|
|
|
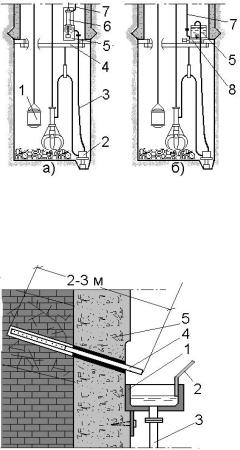
верхнего конца става демонтируется 3-4 секции водоподъемного става. После проветривания ствола и проверки его состояния насос опуска-
ют в ствол, «храповик» всасывающего шланга погружают в приготовленный приямок; на поверхности по мере опускания насоса наращивают демонтированные ранее трубы и насос включают в работу. Необходимость подъема насоса и монтажно-демонтажные работы с трубопроводом являет-
ся существенным недостатком одноступенчатого водоотлива. |
|
|
|
|
|||||
|
|
|
|
Применение |
двух- |
||||
|
|
ступенчатого |
водоотлива |
с |
|||||
|
|
применением |
вертикально- |
||||||
|
|
го |
подвесного |
насоса |
6 |
||||
|
|
(рис.2.164, а) или центро- |
|||||||
|
|
бежного |
насоса |
|
8 |
||||
|
|
(рис.2.164, б) частично уст- |
|||||||
|
|
раняет этот недостаток. |
|
||||||
|
|
|
|
Забойный насос 2 от- |
|||||
|
|
качивает воду из приямка, и |
|||||||
|
|
по |
шлангу 3 |
перекачивает |
|||||
|
|
ее в резервуар 5 подвесного |
|||||||
Рис. 2.164. Двухступенчатый проход- |
насоса 6, который затем по |
||||||||
напорному трубопроводу 7 |
|||||||||
ческий водоотлив: |
|
||||||||
|
поднимает воду на поверх- |
||||||||
а) – с подвесным насосом; б) – с центробеж- |
|||||||||
ным насосом. |
|
ность. |
Резервуар |
и |
насос |
||||
|
|
размещаются на подвесном |
|||||||
|
|
полке 4. Перед взрывными |
|||||||
|
работами забойный насос 2 с нагне- |
||||||||
|
тательным (гибким) шлангом 3 |
||||||||
|
поднимается в бадьях 1 на безопас- |
||||||||
|
ную высоту, что в отличие от одно- |
||||||||
|
ступенчатой схемы исключает не- |
||||||||
|
обходимость |
демонтажа |
верхней |
||||||
|
части водяного става перед взрывом |
||||||||
|
для подъема подвесного насоса. |
|
|||||||
|
|
Для уменьшения водоприто- |
|||||||
|
ка в забой ствола применяют способ |
||||||||
|
водоулавливания, заключающийся в |
||||||||
|
том, что на определенном участке |
||||||||
Рис. 2.165. Схема водоулавливания с |
ствола, в первую очередь в зоне во- |
||||||||
помощью колец: |
доносных |
пластов, |
устраиваются |
||||||
1 – водоулавливающее кольцо (же- |
водосборные |
желоба |
(водоулавли- |
||||||
лоб); 2 – козырек; 3 – трубопровод; 4 |
вающие кольца). Из |
желоба |
вода |
||||||
– перфорированная труба; 5 – бе- |
перепускается в баки нижерасполо- |
||||||||
тонная крепь ствола |
женной перекачной станции по тру- |
||||||||
|
|||||||||
|
160 |
|
|
|
|
|
|
|

бопроводу. Наиболее эффективна схема водоулавливания путем осуществления искусственного дренажа перекрытого бетонной крепью водоносного пласта с отводом воды через водоулавливающее кольцо (рис. 2.165) в баки перекачной станции (см. рис.168, г).
Водоулавливающее кольцо обычно изготавливается из швеллерных балок, или листовой стали. Для лучшего улавливания воды кольцо имеет козырек, который в зоне подвесного полка делается откидным.
Водоотлив при проходке горизонтальных выработок осуществляется с помощью водоотливных канавок (рис. 2.166), которые сооружаются одновременно с проходкой выработки.
В крепких породах в месте расположения канавки бурят один – два шпура. Взрывание зарядов в них осуществляется при ведении взрывных работ в забое. После уборки породы канавку оформляют до проектного сече-
ния отбойным молотком. В породах с f 10 и притоке воды до 100 м3/ч, канавки не крепят. В породах с f 10 канавки закрепляют: при деревянной
крепи выработок – древесиной; при монолитной бетонной крепи выработок
– монолитным бетоном; при металлической и сборной железобетонной крепи - железобетонными или асбоцементными лотками. Сверху канавку перекрывают деревянными щитами или
железобетонными плитами.
В процессе проведения штолен вода по канавке вытекает непосредственно на поверхность, а при проведении других выработок она стекает к водосборнику шурфа или ствола, откуда откачивается насосами на поверхность.
Форма и размеры поперечных сечений канавок зависят от величины притока воды, скорости ее течения, которая в свою очередь зависит от угла наклона канавы в сторону водосбора. Последний соответствует продольному уклону выработки и
равен 0.03-0.005.
Пропускная способность канавы определяется выражением Q S1kV ( S1 – площадь поперечного сечения канавы; V - скорость потока воды по
канавке; k =0.75 – коэффициент, учитывающий допускаемый уровень воды в канаке). Чтобы шлам не оседал в канаве необходимо условие V (0.25-0.5 м/с), а чтобы не допускать размыва русла канавы - V 1.8-2.5 м/с.
161
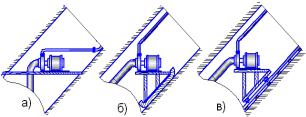
Для улавливания воды при проведении наклонных выработок в их поч-
ве через каждые 5-10 м оборудуются поперечные канавки, из которых вода поступает в продольную канавку, а затем в водосборник. Туда же откачивается вода из забоя забойным насосом. Далее, с помощью стационарного водоотлива вода откачивается непосредственно на поверхность или подается к промежуточному водосборнику.
Забойные насосы устанавливают горизонтально на специальных рамах, оборудованных полозьями или колеса-
ми (рис. 2.167, б, в) а
также на переносных полках (рис. 2.167, а). По выработкам насосы перемещают-
ся на салазках или на колесах по рельсовым путям с помощью канатов и лебедок, устанавливаемых на поверхности или в камерах промежуточных насосных станций.
Нагнетательный трубопровод насоса периодически наращивается по мере углубки выработки. С этой целью насос соединяется с напорным трубопроводом гибким рукавом.
При небольших водопритоках в наклонные выработки, так же как и при проведении вертикальных выработок, вода может удаляться вместе с породой в вагонетках или скипах.
Стационарный водоотлив. Вода, выделяющаяся из горных пород по канавке квершлага, поступает в водосборник, который расположен рядом с насосной камерой главного водоотлива (рис. 2.168). Водосборник представляет собой горную выработку, предназначенную для сбора шахтных вод. Состоит он из двух выработок, соединенных между собой водосливным ходком, устраиваемым у кровли водосборника, или из одной выработки, перегороженной на 2/3 высоты водосборника на две части. Вода, поступающая в первую часть водосборника, отстаивается, и переливается самотеком во вторую часть более чистой, без крупных частиц породы. Во второй части водосборника вода еще больше отстаивается от мелких частиц и, осветленная, поступает в приемные колодцы главного водоотлива и насосами перекачивается на поверхность.
Насосная камера с водоотливными установками помещается у водосборника, и соединяется с ним выработками.
При притоках воды более 50 м3/ч главная водоотливная установка состоит из 3-х одинаковых насосов (рабочего, резервного и находящегося в
162

ремонте), каждый из которых рассчитан на откачку суточного притока за 20
ч.
Рис. 2.168. Схемы водоотлива на шахтах:
а) - схема расположения выработок главного водоотлива; 1 – ствол; 2 – трубно-кабельный ходок; 3 – насосная камера и центральная подстан-
ция; 4 – водозаборный колодец; 5 – околоствольный двор; б) - прямой водоотлив при одном горизонте; в) – прямой водоотлив при нескольких горизонтах; г) – ступенчатый водоотлив с насосными камерами вышележащих горизонтов
2.10. Освещение горных выработок.
Необходимое условие безопасности горных работ – надлежащее освещение рабочего места.
Нормами регламентируются количественные и качественные характеристики освещения горных выработок: уровень освещенности; равномер-
ное распределение светового потока на рабочих поверхностях; отсутствие пульсаций и резких изменений освещенности во времени; условия тенеобразования; яркость всех окружающих поверхностей, включая потолки и стены помещений и др. Предусматривается также аварийное освещение, позволяющее эвакуировать людей или продолжать работу при выходе из строя рабочего освещения.
На шахтах общее равномерное освещение предусматривается во всех выработках, камерах и помещениях. Общее локализованное освещение применяется при проходке вертикальных стволов и подготовительных выработок. В очистных выработках применяется система комбинированного осве-
163
щения. При этом общее освещение осуществляется осветительной установкой, размещенной на перекрытии механизированной крепи, а местное - световым прибором, установленном на комбайне.
Осветительные установки питаются от стационарной электрической сети или автономных источников электрической энергии. Система питания стационарной осветительной системы в основном трехфазная.
Основной светотехнической единицей, используемой для оценки качества освещения, является освещенность Е , под которой понимается отношение светового потока к площади, освещаемой поверхности. Величина Е оценивается в люксах (лк).
Для оценки зрительного восприятия освещаемого объекта используется светотехническая величина, называемая светимостью. Светимость R определяется как отношение светового потока, испускаемого светящейся поверхностью, к площади этой поверхности. Единица измерения R - люксы.
В подземных условиях светимость горных пород и других объектов обусловлена в основном их отражающей способностью, оцениваемой коэффициентом отражения . В зависимости от горных пород их светимость
изменяется в 15-20 раз и более. Например, путем побелки поверхности выработок значение можно увеличить с 0,02-0,08 до 0,4-0,5.
Зависимость между светимостью и освещенностью имеет вид
R E .
Нормы освещенности подземных горных выработок регламентируются Правилами безопасности ведения горных работ. Минимальная освещенность в наименее освещенной точке рабочей поверхности изменяется от 1лк на уклонах и бремсбергах для транспортировки груза, до 75 лк на людских ходках и в подземных здравпунктах. Минимальная освещенность некоторых подземных объектов приведена в табл. 2.12.
Таблица. 2.12. Нормы освещенности подземных объектов
Объекты |
Плоскость нормирования осве- |
Еmin , лк |
|
щенности |
|
Забои горизонтальной |
Горизонтальная на почве |
15 |
выработки |
Вертикальная на забое |
10 |
Откаточные выработки |
Горизонтальная на почве |
5 |
Разминовки |
Горизонтальная на почве |
2 |
Скреперные лебедки |
На рабочей поверхности |
20 |
Склады ВВ и ВМ |
Горизонтальная на почве |
30 |
Околоствольный двор |
Горизонтальная – 0,8 м от почвы |
15 |
|
164 |
|
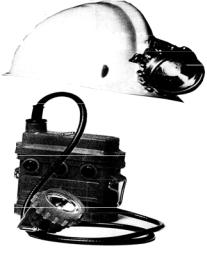
Для освещения горных выработок применяют сетевые (стационарные) и индивидуальные (переносные) светильники. Кроме того, некоторые типы забойных машин и все электровозы имеют осветительные фары.
Переносные светильники изготовляют головными и ручными. Головные светильники (рис. 2.169) выполняются из ударопрочного материала, и имеют два режима работы: рабочий и аварийный (с уменьшенным расходом энергии).
|
Головные светильники состоят |
||||
|
из корпуса с аккумуляторной батаре- |
||||
|
ей и прожектора, соединенных между |
||||
|
собой гибким кабелем. |
|
|
|
|
|
В ручном светильнике освети- |
||||
|
тельная фара смонтирована на корпу- |
||||
|
се, в котором помещен аккумулятор. |
||||
|
Аккумуляторные |
батареи |
све- |
||
|
тильников |
обеспечивают |
продолжи- |
||
|
тельность |
непрерывного |
горения |
||
|
лампы в рабочем режиме – не менее |
||||
|
10 часов. Прожектор имеет приспо- |
||||
|
собление для крепления к каске. |
|
|||
|
Стационарные шахтные |
све- |
|||
|
тильники для освещения подземных |
||||
|
работ питаются от электрической сети |
||||
|
напряжением 127 В. |
|
|
|
|
Рис. 2.169. Светильник шахтный го- |
Очистные забои |
освещаются |
|||
переносными лампами при напряже- |
|||||
ловной СГД.5М.0.5 |
нии до 36 В. |
|
|
|
Взрывобезопасные люминесцентные светильники серии СШЛ (рис. 2.170) применяются для освещения штреков и забоев шахт, и работающие от сети напряжением 127 В. В светильниках СШЛ2 (рис. 2.171), в отличие от СШЛ1, применяются по две компактные люминесцентные лампы мощностью 11 Вт и 18 Вт.
Для освещения забоев вертикальных горных выработок при строительстве шахт опасных по газу и пыли, а также для освещения полков, пройденной части ствола и околоствольных выработок, используется светильник проходческий стволовой взрывобезопасный «Проходка-2» (рис. 2.172) Светильник работает при номинальном напряжении 220 в. В качестве источника света применяется дуговая ртутная лампа высокого давления ДРЛ мощностью 125 Вт.
Для освещения забоев, оборудованных механизированными комплексами, в угольных шахтах, опасных по газу и пыли предназначены светильники забойные взрывобезопасные СЗВ.1.2М (рис. 2.173, а), с источни-
165
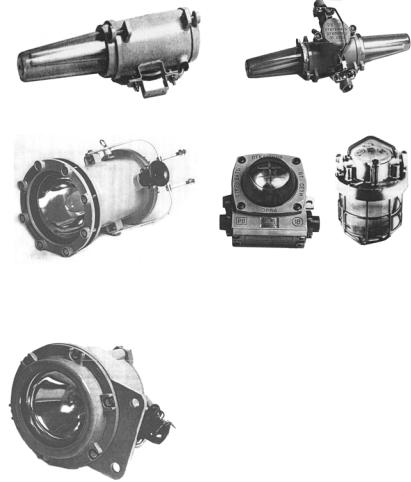
ком света в виде лампы накаливания, работающей при номинальном напряжении 127 В.
В местах, где допускается применение рудничного электрооборудования повышенной надежности, используются стационарные шахтные светильники СШС (рис. 2.173, б). Корпус светильника, защитная решетка и стеклянный колпак предохраняют лампу от влаги, пыли и механических повреждений. Светильники работают при номинальном напряжении 127, 220
в.
Рис. 2.170. Светильники штрековые |
Рис. 2.171. Светильники штрековые |
одноламповые СШЛ1 |
двухламповые СШЛ 2 |
|
а) |
б) |
Рис. 2.172. Светильник «Проходка-2» |
Рис. 2.173. Светильники стационар- |
|
|
ные: а) – СЗВ. 1.2М; б) - СШС |
|
Расстояние между светильниками мощностью 100 Вт на главных от- |
||
|
каточных выработках и разминов- |
|
|
ках должно быть 7…8 м, в проводи- |
|
|
мых выработках - 5…6 м. |
|
|
Для местного освещения вы- |
|
|
работок шахт опасных по газу и пы- |
|
|
ли предназначена |
фара ФРЭ 1.1. |
|
М.Г. (рис. 2.174), которая устанав- |
|
|
ливается на комбайнах, погрузоч- |
|
|
ных машинах и др. горнопроходче- |
|
Рис. 2.174. Фара рудничная |
ском оборудовании, имеющим ис- |
|
точник питания с выходным напря- |
||
электровозная ФРЭ-4 |
жением 36 В. |
|
|
|
|
|
166 |
|
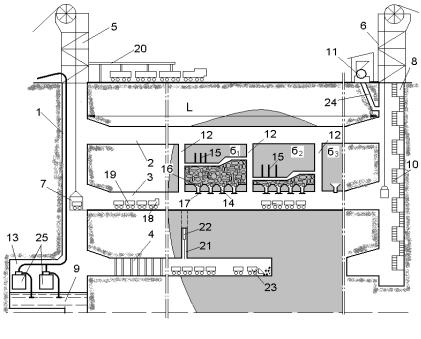
2.11. Общая характеристика подземного способа разработки месторождений полезных ископаемых
После вскрытия и детальной разведки месторождения приступают к его разработке. Под разработкой месторождения понимают весь комплекс работ по извлечению полезного ископаемого. Если месторождение залегает неглубоко от поверхности, его разрабатывают открытым способом, при глубоком залегании — подземным способом.
На рис. 2.175 показана обобщенная схема разработки месторождения подземным способом.
Рис. 2.175. Обобщенная схема разработки месторождения подземным способом
Для доступа к месторождению его вскрывают, т. е. с поверхности проходят шахтный ствол 1, от которого проводят горизонтальные выработки 2, 3, 4, разбивающие все месторождение по вертикали на этажи. Над стволом расположен копер 5, вблизи него в специальном здании установлена подъемная машина, которая перемещает по стволу подъемный сосуд
— клеть 7, служащую для спуска и подъема людей, материалов, полезного ископаемого и т. д.
167
Кроме главного подъемного ствола проходят вспомогательный ствол 8, служащий в качестве запасного выхода на поверхность и обеспечивающий нормальные условия для проветривания. Как правило, этот ствол оборудуется вспомогательной подъемной установкой и имеет лестничное отделение 10. На поверхности вблизи вспомогательного ствола расположено здание вентиляционной установки с вентилятором 11. Расстояние L между главным и вспомогательным стволами зависит от способа вскрытия и изменяется в широких пределах - от нескольких десятков метров до 2—3
км
Отработку рудного тела обычно ведут в нисходящем порядке, т. е. сначала извлекают руду в верхнем этаже между штреками 2 и 3, затем в нижележащем - между штреками 3 и 4 и т. д. Процесс извлечения руды называют очистной выемкой.
Производству очистной выемки предшествуют подготовительные работы. Этаж вертикальными выработками (восстающими 12) делят на блоки б1, б2 и т. п., в пределах которых происходит целый ряд горизонтальных и вертикальных выработок (ходки, рудоспуски и др.). Определенный порядок производства подготовительных работ и очистной выемки на-
зывается системой разработки.
Процесс очистной выемки при системе с магазинированием руды состоит из нескольких производственных операций.
Магазинирование полезного ископаемого – накопление отбитого полезного ископаемого в очистной выработке.
Отделение руды от массива (отбойку) осуществляют взрыванием зарядов ВВ, располагаемых в шпурах 15. Шпуры бурят бурильными маши- нами-перфораторами непосредственно с поверхности отбитой руды. Взорванная руда под действием собственного веса поступает к рудоприемным воронкам 16 и рудоспускам 14, где через люки 17 ее выпускают в вагонетки 19 и затем транспортируют электровозами 18 к стволу шахты. Вагонетки по одной - две поднимают в клети 7 на поверхность и, на эстакаде 20 разгружают в большегрузные вагоны, в которых руду отвозят на обогатительную фабрику или потребителю.
Очистную выемку и подготовительные работы на этаже ведут одновременно в нескольких блоках. Так, блоки б1 и б2 находятся в стадии очистной выемки, а блок б3 — в стадии подготовки. Таким образом, этаж представляет собой часть шахтного поля, ограниченного по падению и восстанию основными откаточными выработками 2 и 3.
Одновременно с очистной выемкой на верхнем этаже вскрывают и подготавливают нижний этаж. На рис. 2.175 показано проведение откаточного штрека 4 и проходка восстающего 21. Погрузку руды при проведении выработок осуществляют погрузочными машинами 23, бурение шпуров при проходке восстающего — перфораторами 22.
168
В процессе разработки подземные выработки необходимо проветривать, так как при взрывах образуется много вредных газов и пыли. Загазованный и запыленный воздух отсасывается через вспомогательный ствол и вентиляционный канал 24 вентилятором 11. Свежий воздух поступает через главный ствол.
Подземная разработка связана с большими притоками грунтовых вод, которые собираются в водосборнике 9. Для откачки этих вод (водоотлива) в насосной камере 13 устанавливают насосы 25.
2.12. Основы открытой разработки полезных ископаемых
При открытом способе добычи все горные работы проводят в открытых горных выработках непосредственно с земной поверхности и включают два основных вида работ – вскрышные и добычные. Вскрышные работы заключают в удалении пустых пород для обеспечения доступа к полезному ископаемому с целью дальнейшей его добычи. В результате вскрышных работ образуется карьер.
Вскрышные и добычные работы ведутся совместно, причем вскрышные несколько опережают добычные работы во времени и пространстве.
Отличительные признаки открытых горных работ: добыча производится лишь после удаления пустых пород; размеры открытых горных выработок по всем направлениям значительны, что позволяет применять мощное оборудование больших размеров; удаление пустых пород и добыча полезного ископаемого производится в основном экскаваторным способом; горнотранспортное оборудование характеризуется большими размерами и высокой производительностью.
Открытым способом разрабатываются месторождения полезных ископаемых любой формы, залегающих в разнообразных природных условиях.
Месторождение при открытой разработке делят на горизонтальные или наклонные слои, которые отрабатывают с опережением верхними слоями нижних. Поэтому борта карьера, т.е. его боковые поверхности, имеют ступенчатую или уступную форму.
Уступом называется часть толщи пород, имеющая рабочую поверхность в форме ступени и разрабатываемая самостоятельными средствами выемки, погрузки и транспорта (рис. 2.176). Обычно высота уступа принимается не менее высоты черпания экскаватора и на большинстве карьеров составляет 10-15 м, а иногда достигает 20-40 м.
Различают рабочие и нерабочие уступы. На рабочих уступах производится выемка пород или добыча полезного ископаемого. Уступ имеет ниж-
нюю и верхнюю площадки, откос и бровки.
169
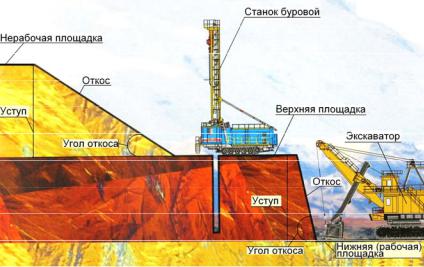
Откосом уступа называется наклонная поверхность, ограничивающая уступ со стороны выработанного пространства. Линии пересечения откоса уступа с его верхней и нижней площадками называются верхней и нижней бровками.
Горизонтальные поверхности рабочего уступа, ограничивающие его по высоте, называют нижней и верхней площадками. Площадка, на которой расположено оборудование для разработки, называется рабочей площадкой. Ширина рабочих площадок составляет 40-70 м и более. Если площадка свободна, ее называют нерабочей.
Угол наклона уступа к горизонтальной плоскости называется углом откоса уступа. Угол откоса рабочих уступов обычно равен 65-80о, а нера-
бочих – 45…60о.
Уступ разрабатывают последовательными параллельными полосами – заходками шириной 10-20 м с применением или без применения буровзрывных работ. Торец заходки называется забоем. Часть заходки по ее длине, подготовленная для разработки, называется фронтом работ уступа.
Боковые поверхности, ограничивающие карьер и его выработанное пространства, называют бортом карьера.
Рис. 2.176. Основные элементы уступа
В ходе разработки месторождения открытым способом можно выде-
лить четыре периода: подготовительный, строительный, эксплуатационный, заключительный.
170
Подготовительный период включает работы по подготовке месторождения, осушению и ограждению от вод поверхностного стока.
Встроительный период входят работы по созданию начального фронта вскрышных работ, строительство транспортных коммуникаций.
Эксплуатационный период охватывает горные работы по вскрыше и добыче.
Заключительный период – это работы по рекультивации нарушенных горными работами земель.
Подготовка пород к выемке заключается в разрушении массива различными способами на куски, удобные для последующей выемки, погрузки
итранспортирования. Рыхлые и мягкие породы могут разрабатываться непосредственно из массива экскаваторами или другими выемочными машинами. Подготовка полускальных пород ведется обычно навесными рыхлителями на тракторах тяжелого типа. Подготовка к выемке скальных пород осуществляется посредством буровзрывных работ, при этом кусковатость взорванных пород должна быть оптимальной.
Буровзрывные работы – это комплекс бурения и взрывания скважинных зарядов. Бурение скважин на уступе осуществляется в один, два или три ряда при помощи станков вращательного или ударно-вращательного действия, которые подразделяются на шнековые и шарошечные. Станки шнекового бурения типа СБШ и СБР применяют, в основном, на разрезах для бурения по углю. Станки шарошечного бурения используются при бурении скальных пород, и имеют в качестве рабочего органа вращающиеся шарошечные долота.
Бурение скважин осуществляется вертикально или наклонно глуби-
ной 25-60 м.
Выемка и погрузка горных пород – отделение от массива мягкой или предварительно разрыхленной крепкой породы с последующей погрузкой в транспортные средства или непосредственно в отвал.
Вкачестве основных средств механизации используются экскаваторы, в этом случае выемка и погрузка сливаются в один процесс – выемочнопогрузочные работы.
Экскаватор – самоходная машина цикличного или непрерывного действия. Они могут быть одноковшовые и многоковшовые. Экскаваторы цикличного действия (одноковшовые) (рис. 2.176) последовательно выполняют операции копания и перемещения горной массы в ковше, поворачиваясь вокруг своей оси.
Кмногоковшовым экскаваторам непрерывного действия относятся роторные машины (рис. 2.177), которые производят выемку и погрузку горной массы в результате перемещения ковшей по круговой траектории. Такие экскаваторы имеют рабочий орган в виде роторного колеса диаметром
до 18 м с ковшами, установленными на конце стрелы. Число ковшей на роторе до 12, а емкость ковшей от 0,3 до 8 м3.
171
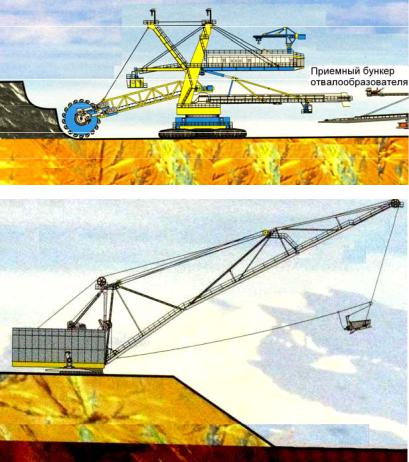
Из экскаваторов с канатной связью широкое применение имеют драглайны. Драглайн – это шагающий экскаватор, использующиеся на карьерах для перевалки пород вскрыши в выработанное пространство, из забоев, расположенных как ниже, так и выше горизонта установки экскаватора (рис. 2.178). Вместимость ковша шагающего драглайна достигает 120 м3 при длине стрелы до 125 м.
Рис. 2.177. Роторный экскаватор
Рис. 2.178. Шагающий экскаватор Драглайн
При открытой разработке в карьерах с относительно малым объемом работ (до 3 млн. т) и расстоянии транспортирования до 500 м в качестве основного выемочно-погрузочного оборудования используются скреперы и одноковшовые погрузчики. Одноковшовый погрузчик представляет собой
172
колесное шасси с опускающейся стрелой, на конце которой шарнирно закреплен ковш. После загрузки ковша погрузчик отъезжает от породного развала на расстояние, достаточное для подъезда автосамосвала под ковш погрузчика. После разгрузки ковша автосамосвал отъезжает; освобождая погрузчику проезд к забою для наполнения ковша.
Карьерный транспорт – это комплекс средств перемещения горной массы от забоев до пунктов разгрузки. Он является связывающим звеном в общем технологическом процессе открытой разработки месторождения.
На открытых горных работах используются почти все известные виды и технические средства перемещения грузов. Наибольшее распространение получил железнодорожный, автомобильный и конвейерный транспорт. В ограниченных объемах применяются скиповые подъемники, канатноподвесные дороги, гидравлические трубопроводы, конвейерные поезда, вертолеты и др.
Средствами железнодорожного транспорта являются рельсовые пути и подвижной состав. Рельсовые пути на карьерах бывают стационарными и временными, периодически перемещаемыми вслед за подвиганием фронта работ на уступах. Технологический подвижной состав состоит из локомотивов и вагонов. В качестве локомотивов применяются, в основном, электровозы и тепловозы. Глубина применения железнодорожного транспорта не превышает 300-350 м.
Подвижный состав в виде карьерного автотранспорта представлен автосамосвалами и полуприцепами. Наибольшее применение при транспортировании вскрыши получили автосамосвалы типа БелАЗ грузоподъемностью 40, 75, 110 и 180 т. Для транспортирования угля применяются углевозы – самосвалы типа БелАЗ грузоподъемностью 40 и 105 т и полуприцепы углевозы БелАЗ грузоподъемностью 120 т, с донной разгрузкой.
Для передвижения автоамосвалов в карьере сооружаются стационарные и временные дороги. Стационарные автодороги строятся в капитальных траншеях, на поверхности и соединительных транспортных бермах на длительный срок, имеют дорожное покрытие. Временные автодороги, сооружаемые на уступах и отвалах, периодически перемещаются вслед за подвиганием фронта работ и, как правило, не имеют дорожного покрытия.
Конвейерный транспорт (рис. 2.179) применяется преимущественно для перемещения мягких пород и угля, а также мелкораздробленных скальных пород. При проведении открытых горных работ, наибольшее применении получили ленточные конвейеры с шириной ленты от 1 до 3,6 м и скоростью движения до 6 м/с.
Комбинированный транспорт – при нем последовательно используются для перемещения одного и того же груза различные виды транспорта. Наибольшее распространение получила комбинация автомобильного и железнодорожного транспорта, при которой горная масса доставляется из забоев автотранспортом до перегрузочных пунктов, а затем железнодорож-
173
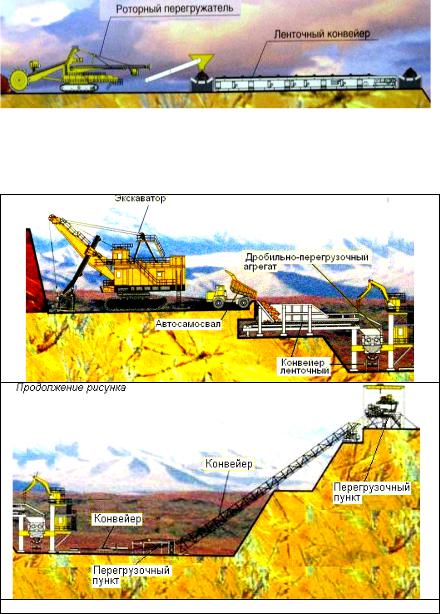
ным на поверхность до отвалов. Этот вид комбинации эффективен на нижних уступах при глубине до 150 м.
Рис. 2.179. Конвейерный транспорт
Комбинация автомобильного транспорта с конвейерным, применяется для глубоких горизонтов карьера, расположенных ниже 150 м от поверхности. Здесь горная масса выдается на поверхность по кратчайшему пути (рис. 2.180).
Рис. 2.180. Схема комбинированного транспорта в карьере
174
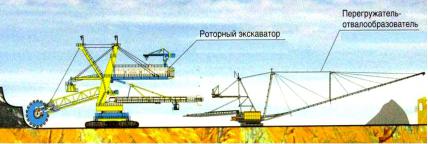
На высокогорных карьерах, где спуск горной массы при перепаде высот 200-800 м другими средствами затруднен, применяется комбинация автомобильного транспорта с рудоспусками или подвесными канатными дорогами..
Отвалообразование - технологический процесс размещения пустых пород, удаляемых при разработке месторождения открытым способом. Отвалообразование вскрышных работ производится на специально отведенных для этих целей площадках, называемых отвалами. Отвалы в комплексе с техническими устройствами, средствами механизации составляют отвальное хозяйство карьеров.
Отвалы бывают внутренние и внешние. Внутренние отвалы располагаются в выработанном пространстве карьера, внешние – за его пределами. Внутренние отвалы возможны при разработке месторождения с углом падения до 12о. Для перемещения породы во внутренние отвалы применяют драглайны и механические лопаты.
Внешнее отвалообразование применяется при разработке наклонных и крутонаклонных месторождений. Для складирования пород при транспортировании их на внешние отвалы используются механические лопаты, драглайны, бульдозеры и др.
В качестве отвалообразующего механизма при доставке породы на отвалы автомобильным транспортом применяются бульдозеры, а в благоприятных условиях (например, при наличии глубокие оврагов и балок) применяют драглайны.
Отвалообразование при конвейерном транспорте осуществляется консольными ленточными отвалообазователями-перегружателями, которые ведут прием, транспортирование и укладку породы в отвал (рис. 2.181). Отвалообразователи имеют достаточно внушительную длину консоли (до 225 м) и обеспечивают высоту отсыпки породы до 90 м. Производительность отвалообразователей достигает 12000 м3/ч.
Рис. 2.181. Отвалообразование с помощью перегружателя-отвалообразователя при конвейерном транспорте
175
Вопросы и темы модульного контроля знаний. Література для самоподготовки
1.Общие сведения о месторождениях полезных ископаемых.
1.1.Общие понятия и определения: месторождение; полезное ископаемое; полезных ископаемые по видам физического состояния, форме тел и промышленному использованию.
1.2.Понятия о залежах и месторождениях нефти и газа.
1.3.Общие понятия о запасах и ресурсах полезных ископаемых
1.4.Степень изученности и категории запасов полезных ископаемых.
2.Основы механики и виды разрушения горных пород.
2.1.Горные породы как объект воздействия горными выработками и скважинами (горная порода, породный массив, породный образец); горные породы по степени связности.
2.2.Физические свойства горных пород.
2.3.Механические свойства и технологические параметры пород.
2.4.Виды разрушения горных пород.
3. Основы горной технологической системы.
3.1.Классификация горных выработок.
3.2.Виды, назначение и специфика проведения горно-разведочных выработок.
3.3.Открытые горные выработки.
3.4.Подземные вертикальные горные выработки.
3.5.Подземные горизонтальны горные выработки.
3.6.Подземные наклонные горные выработки.
3.7.Околостольный двор и камерные выработки.
3.9.Элементы и параметры горных выработок.
3.10.Горные предприятия.
4. Разрушение горного массива. Методы и способы разрушения пород.
4.1.Структура и принцип действия отбойного молотка.
4.2.Для чего предназначены и основные элементы горного комбайна.
4.3.Для чего предназначены и принцип работы струговой установки?
4.4.Для чего предназначены и принцип работы бурошнековой установки?.
4.5.Общая характеристика взрывного способа отбойки породы. Способы и методы взрывных работ при проведении выработок.
4.6.Способы бурения шпуров. Область применения основных способов бурения.
4.7.Типы привода бурильных машин.
4.8.Приведите общие сведения о ручных электросверлах. Принципиальное устройство электросверла. Виды механизмов и приспособлений, применяемые при бурении различными видами сверл.
4.9.Принципиальная схема бурения шпуров колонковыми сверлами.
176
4.10.Инструмент для бурения шпуров вращательным способом (штанги, резцы).
4.11.Механизм разрушения пород при вращательном бурении шпу-
ров.
4.12.Структурная схема и принцип работы перфораторов для ударноповоротного бурения шпуров.
4.13.Переносные, колонковые и телескопные перфораторы. Виды механизмов и приспособлений, применяемых при бурении различными видами перфораторов.
4.14.Инструмент, применяемый при бурении шпуров ударноповоротным способом.
4.15.Механизм разрушения пород при ударно - поворотном бурении шпуров.
4.16.Область применения и особенности конструкции установок для бурения шпуров.
5. Уборка породы в горных выработках (общие понятия: погрузка породы, транспортировка и откатка, спуск, подъем, рудничный транспорт).
5.1.Признаки деления и типы породопогрузочных машин.
5.2.Процесс погрузки породы погрузочными машинами периодического и непрерывного действия.
5.3.Назначение и основные элементы перегружателя.
5.4.Скреперные установки. Условия и технология погрузки породы скреперными установками.
5.5.Схема размещения, конструктивные особенности и технология погрузки породы грейферными пневмопогрузчиками в вертикальных горных выработках.
5.6.Погрузка породы в стволах с использованием стволовых погрузочных машин типа КС-2у/40.
5.7.Устройства разминовок и организация работ в горизонтальных выработках при обменных операциях.
5.8.Виды, технологические схемы и оборудование для доставки породы в горизонтальных и наклонных выработках.
5.9.Устройство рельсового пути. Схемы рельсовых переводов. Назначение и конструктивные особенности временных рельсовых путей в призабойной зоне.
5.10.Средства и технология подъема породы при проходке шурфов.
5.11.Состав и назначение элементов подъемной установки при проведении стволов.
5.12.Устройство, типы и условия применения подъемных сосудов для уборки породы в вертикальных горных выработках.
5.12.Состав и конструктивные особенности оборудования для клетевого подъема.
5.13.Организация работ в забое ствола при подъеме породы бадьями.
177
6. Крепление горных выработок.
6.1.Горное давление. Виды проявления горного давления.
6.2.Оценка напряженного состояния пород на контуре горизонтальной горной выработки.
6.3.Оценка напряженного состояния пород на контуре вертикальной горной выработки.
6.4.Расчет горного давления при проведении горизонтальных горных выработок.
6.5.Особенности расчета горного давления при проведении наклонных горных выработок.
6.6.Расчет горного давления при проведении вертикальных горных выработок.
6.7.Материалы, которые могут использоваться для изготовления крепи горных выработок. Основные требования к крепежным материалам.
6.8.Типы, и конструктивные элементы постоянных крепей горизонтальных горных выработок.
6.9.Условия применения податливой крепи. Область применения и конструктивные особенности арочных металлических и шарнирных крепей.
6.10.Бетонные смеси для возведения монолитной крепи выработок.
6.11.Область применения и особенности возведения набрызгбетонной крепи.
6.12.Область применения и конструкция сборной железобетонной крепи.
6.13.Область применения анкерной крепи. Группы анкеров по конструкции, используемому материалу и принципу возведения.
6.13.Комбинированные крепи с использованием анкеров для крепления горизонтальных и наклонных выработок.
6.14.Конструкции и технология возведения временной крепи горизонтальных и наклонных горных выработок.
6.15.Особенности исполнения конструкции крепи наклонных горных выработок.
6.16.Деревянная крепь вертикальных горных выработок. Область применения, конструкции и способы возведения.
6.17.Монолитная бетонная крепь вертикальных горных выработок.
6.18.Тюбинговая крепь, процесс возведения тюбинговой крепи в стволах.
7. Вентиляция горных выработок.
7.1.Условия образования и ПДК ядовитых газов и пыли в рудничном воздухе подземных горных выработок.
7.2.Контроль состава рудничной атмосферы. Периодичность контро-
ля.
178
7.3.Способы и схемы проветривания шахт.
7.4.Схемы проветривания тупиковых выработок.
7.5.Схемы и способы проветривания шурфов и стволов шахт.
7.5.Факторы, по которым производится расчет расхода воздуха для проветривания выработок.
7.6.Выбор вентилятора местного проветривания выработок.
8. Водоотлив при проходке горных выработок.
8.1.Область применения и технология бадъевого водоотлива при проходке вертикальных горных выработок.
8.2.Схемы проходческого водоотлива при проведении вертикальных горных выработок с помощью насосов.
8.3.Способы уменьшения водопритока в забой ствола и улавливание воды при проведении наклонных выработок.
8.4.Стационарный водоотлив. Схемы водоотлива на шахтах.
9. Освещение горных выработок.
9.1.Характеристики освещения горных выработок.
9.2.Нормы освещенности подземных объектов.
9.3.Особенности применения сетевых и переносных светильников.
10. Разработка месторождений.
10.1.Общая характеристика подземного способа разработки месторождений.
10.2.Открытая разработка полезных ископаемых (вскрышные и добычные работы, основные элементы карьерного уступа, периоды разработки месторождения, оборудование для выемки, погрузки и перемещения горной породы)
Литература для самоподготовки
1.Багдасаров Ш.В., Верчеба А.О., Пальмов И.И. Справочник горного инженера геологоразведочных партий. - М.: Недра, 1986. - 356 с.
2.Борисов С.С., Клоков М.П., Горновой Б.А. Горное дело. - М.: Недра, 1972. – 358 с.
3.Брылов М.Ф. Горное дело. –М.: Недра,1975.
4.Брылов С.А., Грабчак Л.Г., Комащенко В.М. Горно-разведочные и буровзрывные работы. - М.: Недра. 1989.
5.Воздвиженский Б.И., Мельничук И.П., Пешалов Ю.А. Физико-
механические свойства горных пород и влияние их на эффективность бурения. – М.: Недра, 1973. – 240 с.
6.Гайко Г.И. История освоения земных недр. – Донецк: Східний видавничий дім, 2009. – 292 с.
7.Грабчак Л.Г., Брылов С.А., Комащенко В.И. Проведение горно-
разведочных выработок и основы разработки МПИ. - М.: Недра. 1988.
179
8.Егоров П.В., Бобер Е.А., Кузнецов Ю.Н., Косьминов Е.А., Решетов С.Е., Красюк Н.Н. Основы горного дела; Учебник для вузов. – М.: Издательство МГРУ, 2000. - 408 с.
9.Килячков А.П., Брайцев А.В. Горное дело: Учебник для техникумов.
– М.: Недра, 1989. – 422 с.
10.Лидин Г.Д., Воронина Л.Д., Каплунов Д.Р. и др. Горное дело: Терминологический словарь. М.: Недра, 1990. -694 с.
11.Мельников Н.И. Проведение и крепление горных выработок: Учебник для техникумов. – М.: Недра, 1988. – 336 с.
12.Проведение горно-разведочных выработок. Справочник. /под редакцией Хорева В.А. - М.: Недра, 1990. – 410 с.
13.Смирняков В.В., Вихряев В.И., Очкуров В.И. Технология строитель-
ства горных предприятий: Учебник для вузов. – М.: Недра, 1989. – 573 с.
14.Сыркин П.С., Мартыненко И.А., Данилкин М.С. Шахтное и подзем-
ное строительство. Технология строительства горизонтальных и наклонных выработок: Учебное пособие /Шахтинский институт ЮРГТУ. Новочеркасск: ЮРГТУ, 2002. - 430 с.
15.Шехурдин В.К., Несмотряев В.И., Федоренко П.И. Горное дело. -М.:
Недра, 1987. – 440 с.
180
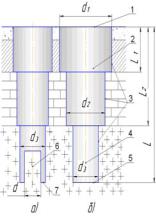
3БУРОВАЯ ТЕХНОЛОГИЧЕСКАЯ СИСТЕМА
Вобщем случае буровая технологическая система представляет собой комплекс скважин, необходимых для разведки и эксплуатации конкретного геологического объекта.
Впрактике разведки большинства месторождений полезных ископаемых (за исключением рудных, которые характеризуются очень сложным геологическим строением) основной является буровая разведочная сеть. На промыслах предназначенных для добычи нефти и газа, скважины относятся
кключевым элементам соответствующих технологических комплексов. Скважина является основной структурной единицей в технологических схемах добычи полезных ископаемых путем подземного выщелачивания ряда металлов, выплавки серы, газификации углей и др.
3.1. Основные сведения о буровых скважинах
Бурение скважин представляет собой процесс безлюдного образования горной выработки круглого сечения, путем разрушения пород специальным техническими средствами (буровыми установками и инструментами) с извлечение продуктов разрушения на поверхность.
Скважина является горной выработкой, пройденной в массиве горных пород с заранее заданным положением в пространстве, протяженность (глубина) которой значительно превышает ее диаметр.
Рис. 3.1. Элементы и параметры скважины
Элементы буровой скважины (рис. 3.1).
Устье скважины (1) – место примыка-
ния скважины к земной поверхности или к горной выработке, из которой она берет начало.
Стенки скважины (3) – ограничиваю-
щие скважину боковые поверхности горной породы.
Ствол скважины (2) – пространство,
занимаемое скважиной в массиве горной породы.
Ось ствола скважины (4) – вообра-
жаемая линия, соединяющая центры поперечных сечений ствола скважины.
Забой (дно) скважины (5, 7) – поверх-
ность горной породы, перемещающаяся в пространстве в результате воздействия на нее
181
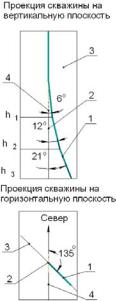
породоразрушающего инструмента. В зависимости от способа разработки различают сплошные забои 5 и кольцевые забои 7.
При сплошном бурении разрушение породы производится по всей площади забоя. Сплошным забоем обычно бурят технические и эксплуатационные скважины, или интервалы разведочных скважин, геологические разрезы которых хорошо изучены на предыдущих этапах изысканий.
При бурении кольцевым забоем в центре скважины остается колонка (столбик) породы диаметром d – керн (6). Этот способ бурения называется колонковым. Керн извлекается из скважины для изучения параметров и свойств пройденных пород. Колонковое бурение применяют при поисках и разведке полезных ископаемых, инженерно-геологических и других изысканиях.
Параметры скважины (рис. 3.1 – 3.2).
Протяженность (длина) скважины – это расстояние от устья до за-
боя по оси ствола. Глубина скважины ( L ) или ее интервалов при ступенчатой конструкции ствола скважины ( L1, L2... ) – это проекция длины скважи-
ны или ее интервалов на вертикальную ось. Длина и глубина численно равны только для вертикальных скважин, однако они не совпадают у наклонных и искривленных скважин.
Рис. 3.2. Углы пространственного положения скважины
Конечный диаметр скважины ( d 3 ) опреде-
ляется целевым назначением скважины и соответствует размеру породоразрушающего инструмента, применяющегося для разрушения пород на забое.
Диаметры интервалов скважины ( d1 , d2 , d 3 ) имеют место при ступенчатой конструкции
ствола и также соответствуют размеру породоразрушающего инструмента, применяющегося для разрушения пород на заданном интервале скважины.
Углы, определяющие пространственное положение буровой скважины:
зенитный угол – угол отклонения проекции оси скважины 1 на вертикальную плоскость 3 от вертикали 2; (на рис. 3.2 «Проекция скважины на вертикальную плоскость» показаны примеры положения ствола скважины относительно верти-
кали: на глубине h1 зенитный угол 6o ; на глу-
бине h2 , 12o ; на глубине h3 , 3 21o );
азимутальный угол (азимут скважины)
182
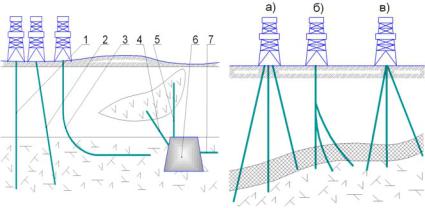
– угол, измеряемый в горизонтальной плоскости от северного направления по ходу часовой стрелки до горизонтальной проекции вертикальной плоскости 3, в которой лежит ось искривленной скважины 1. На рис. 3.2 «Проекция скважины на горизонтальную плоскость» показан пример азимуталь-
ного отклонения скважины 135o на глубине h3 .
Типы и схемы расположения скважин. В зависимости от заданной проектной траектории, скважины подразделяются на следующие типы (рис. 3.3).
Вертикальные (1) – направленные вертикально вниз. Учитывая, что ось скважины практически всегда имеет пространственное искривление, то скважину, при небольшой интенсивности искривления (обычно меньше десятой доли градуса на 10 м длины ствола) и малой суммарной величине отклонения от вертикали (< 1-2 о), также называют вертикальной.
Восстающие вертикальные (5) - скважины, заданные вверх (из горной выработки).
Наклонные (2) – направленные наклонно вниз к вертикали; скважины (заданные вверх под углом к вертикали – восстающие наклонные (4)).
Горизонтальные (3) – наклонно-направленные скважины, заканчивающиеся горизонтальным участком, ствол которого может достигать сотен метров или скважины, пройденные горизонтально, например, из горной вы-
работки, при начальном зенитном угле 900 (7).
По таким признакам как методика и схемы бурения, скважины могут иметь кустовое, многоствольное и многозабойное расположение (рис. 3.4).
Рис. 3.3. Типы скважин в зависимости |
Рис. 3.4. Схемы расположения |
от заданной траектории |
скважин |
Кустовое расположение (рис. 3.4, а) предполагает бурение нескольких скважин на ограниченной площадке, в пределах которой перемещается
183
буровая установка. Метод кустового бурения предполагает наличие нескольких устьев, при этом расстояние между устьями соседних скважин зависит от длины и траектории ствола предыдущей скважины. Между точками забуривания двух соседних скважин это расстояние составляет величину не менее 30 м, если разница в азимутах забуривания < 10о. Если азимуты забуривания обличаются на 10о…20о и более, расстояние между точками заложения скважин составляет соответственно 20 и 10 м.
Многоствольная скважина (рис. 3.4, б), имеет основной ствол и два или более дополнительных, являющихся продолжением основного. Такая скважина имеет одно устье, а количество забоев равняется числу дополнительных стволов. Любая многоствольная скважина является наклоннонаправленной, так как для бурения нового ответвления требуется отклонить ствол от первоначального направления.
Многозабойные скважины характеризуются бурением двух или более скважин одной буровой установкой последовательным спуском снаряда и углубкой того или иного ствола. Каждый ствол скважины имеет устье и забой. Например, известный еще в 60-е годы ХХ века способ двуствольного бурения предполагал оборудование установки двумя роторами, расположенными на расстоянии 1,5 м друг от друга, и перемещающимся кронблоком. При этом бурение скважины ведется попеременно в обоих стволах: из одного ствола извлекается бурильная колонна и, не устанавливая на подсвечник, колонна переносится к соседней скважине, свинчивается с породоразрушающим инструментом и опускается в скважину. Таким образом, попеременно по мере износа долот в каждой скважине ведут спускоподъемные операции, пока глубина скважин не достигнет проектной отметки.
По целевому назначению (области применения) буровые скважины условно можно разделить на три основные категории: геологоразведочные,
эксплуатационные (добычные) и технические.
Геологоразведочные скважины проводятся с целью изучения геологического строения определенного района, поисков и разведки полезных ископаемых, проведения инженерно-геологических и гидрогеологических изысканий.
Глубина разведочных скважин определяется, в основном, перспективными задачами или достигнутыми отметками разработки на действующих участках конкретных месторождений. Например, в Донбассе, где горизонты добычи углей на ряде шахт превышают 1500 м, глубина разведочных скважин составляет 2000 м и более. Нефтяные и газовые месторождения разведуют скважинами, глубина которых достигает 7000 – 8000 м.
На современном этапе в Украине в больших объемах выполняется бурение относительно неглубоких (до 150-200 м) скважин при проведении инженерно-геологических и гидрогеологических изысканий под строительство жилых зданий, промышленных сооружений, мостов гидротехнических
184
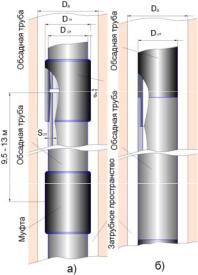
сооружений, оросительных каналов и т.п. На каждой площадке строительства важно получить образцы пород с ненарушенной структурой (монолиты), чтобы изучить свойства пород, на которых будут воздвигнуты те или иные сооружения.
Эксплуатационные скважины бурятся для извлечения из недр нефти, газа, минеральных, обыкновенных и термальных вод и некоторых твердых полезных ископаемых (минеральных солей, серы, медных руд, урана цинка, золота и др. металлов).
Технические скважины проводятся для различных технических целей: для размещения зарядов взрывчатых веществ; для взрывного отделения породы от массива при открытых и подземных разработках; для дегазации угольных пластов; для вентиляции горных выработок, прокладки коммуникаций, лесоспуска, засыпки выработанного пространства и тушения пожаров в выработках; создания подземных газохранилищ и др.
Рис. 3.5. Обсадные колонны для крепления скважин: а – соединение обсадных труб в колонне муфтами; б – соединение обсадных труб в колонне методом «труба в
трубу»; Dм - диаметр муфты; Doт - наружный диаметр обсадной трубы; Sот -
толщина стенки обсадной трубы; - зазор между стенкой скважины и обсадной колонной; Dд - диаметр долота (скважи-
ны)
185
Конструкция скважины.
Как правило, в разрезе ствола бурящейся скважины встречаются горизонты, сложенные из горных пород различной крепости и устойчивости. Пересечение пород, нарушающих устойчивость стенок скважины или трещиноватых пород, являющихся причиной поглощения промывочной жидкости вызывают осложнения, которые в ряде случаев делают невозможным дальнейшую проходку нижележащего интервала скважины с заданными технологическими режимами бурения. При бурении скважин на жидкие и газообразные полезные ископаемые особенно важным является предотвращение перетока флюидов (нефти, газа, воды и их смеси) из одного пласта в другой. Поэтому при сооружении скважин возникает необходимость крепить ее ствол и разобщать (изолировать) пласты, содержащие различные флюиды
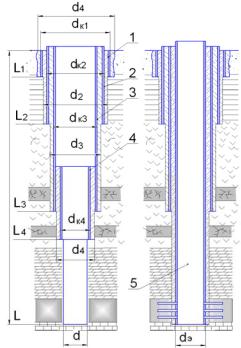
путем спуска в нее обсадных колонн, в виде соединенных между собой специальных стальных труб, называемых обсадными (рис. 3.5).
Так как одно крепление стенок скважины обсадными трубами, не создает условий для полной изоляции осложняющих горизонтов и разобщения пластов, то затрубное пространство заполняют глиноцементным или цементным раствором при помощи специального цементировочного оборудования и приспособлений.
Таким образом, в результате механического бурения, крепления и цементации скважины создается подземное сооружение определенной конструкции.
В общем случае, под конструкцией скважины (рис. 3.6) понимается совокупность данных о диаметрах бурения участков ствола
( d, d1, d2 , d3, d4... ), длинах ( L1, L2 , L3, L4... ) и диаметрах обсадных колонн ( dk1, dk 2 , dk3, dk 4... ), а также, при необходимости – информация об интерва-
лах цементирования обсадных колонн.
По функциональному назначению типовой перечень обсадных колонн геологоразведочных скважин включает направляющую колонну 1 (направление), кондуктор 2 и промежуточные (технические) колонны 3 и 4.
Направляющая колонна
(1) служит для защиты поверхностных пластов от размыва буровым раствором и предотвращения размыва устья скважины с дальнейшим отводом потока жидкости из ствола в очистную систему.
|
|
Кондуктор (2) является |
||
|
|
второй обсадной |
колонной, |
|
|
|
спускаемой в ствол скважины |
||
|
|
для крепления верхних неус- |
||
|
|
тойчивых интервалов разреза, |
||
|
|
а также для перекрытия по- |
||
|
|
глощающих пластов и изоля- |
||
|
|
ции водоносных |
горизонтов |
|
|
|
от загрязнения. Если наносы |
||
|
|
имеют небольшую мощность |
||
|
|
и относительно |
устойчивы в |
|
|
|
период бурения, то кондуктор |
||
|
|
одновременно |
может быть |
|
а) |
б) |
использован и |
как направ- |
|
ляющая колонна. |
|
|||
Рис. 3.6. Конструкции скважин |
После того как кондук- |
|||
|
|
|||
|
|
186 |
|
|
тор зацементирован, через него спускают долото меньшего размера и бурят новый ствол до требуемой глубины, зависящей от геологических условий бурения. Это участок ствола крепится промежуточной обсадной колонной 3, которая служит для предотвращения осложнений и аварий в скважине при бурении последующего интервала. Число промежуточных колонн может быть несколько. Их количество определяется исходя из несовместимости условий бурения нижележащего интервала скважины по отношению к ранее пробуренному из-за возможных осложнений в вышележащих участках ствола, если последний не закреплен обсадной колонной.
Промежуточные колонны могут быть сплошными (3), перекрывающими весь ствол скважины от забоя до устья, независимо от крепления предыдущего интервала и не сплошными (хвостовиками) (4), служащими для крепления только необсаженного интервала скважины с некоторым перекрытием предыдущей обсадной колонны.
При бурении эксплуатационных скважин, например, для добычи углеводородных полезных ископаемых, где предполагается необходимость соединения продуктивного пласта с дневной поверхностью, к типовому перечню обсадных колонн добавляется эксплуатационная колонна 5, которая служит для приема и извлечения на поверхность нефти или газа. Одновременно эксплуатационная колонна обеспечивает крепление и разобщение продуктивных горизонтов, и изоляцию их от других горизонтов геологического разреза скважины.
Процесс бурения скважины и спуска обсадных труб продолжается до тех пор, пока не будет решена геологическая задача или достигнута глубина залегания нефти или газа.
По числу обсадных колонн, спускаемых в ствол скважины, различают одно-, двух-, трех- и многоколонные конструкции скважин. При этом при подсчете колон, входящих в конструкцию скважины, направление, а для добычных скважин и кондуктор, не учитывают.
3.2. Бурение нефтяных и газовых скважин
Руководящим документом для начала бурения скважин является гео- лого-технический проект, важную часть которого составляет конструкция скважины. Обоснованная конструкция скважины во многом определяет способ проходки тех или иных интервалов, технологию, буровое оборудование и инструмент.
Разработка конструкции скважины, а именно, выбор диаметров обсадных колонн и диаметров долот осуществляется снизу вверх. При разработке конструкции добычной скважины, ее конечный диаметр зависит от
187
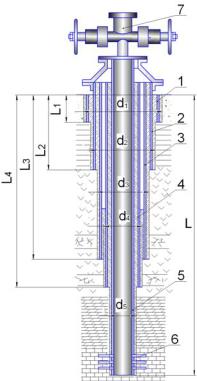
заданного диаметра эксплуатационной колонны, который является исходным для проектирования всей конструкции скважины. Диаметр эксплуата-
ционной колонны ( dэ ) зависит от условий ее эксплуатации, или задается
заказчиком на буровые работы. Современные методы эксплуатации скважин дают возможность в большинстве случаев ограничиться спуском об-
садных труб диаметром dэ = 146 мм. При весьма высоких среднесуточных
дебетах (более 300 т нефти и 500 тыс. м3 газа) может потребоваться спуск обсадной колонны диаметром dэ = 168 мм, а при низких дебитах нефти или
газа обсадные трубы диаметром dэ = 114 мм оказываются вполне достаточ-
ными.
Кроме функций приема и извлечения на поверхность нефти или газа эксплуатационная колонна одновременно обеспечивает крепление и разобщение продуктивных горизонтов, и изоляцию их от других горизонтов геологического разреза скважины. В нижней части колонны, находящейся в продуктивном пласте, перфорируют (простреливают) ряд отверстий в стенке обсадной трубы и цементной оболочке.
После того, как установлен
|
или |
выбран |
dэ , |
определяется |
|
диаметр долота Dд = |
d5 (рис. 3.7), |
||
|
которым предстоит бурить ствол |
|||
|
скважины под эксплуатационную |
|||
|
колонну. |
Dд обусловливается |
||
|
|
Выбор |
||
|
следующими факторами: диа- |
|||
|
метром муфты обсадной колонны |
|||
|
Dм |
(см. рис. |
3.5); |
величиной |
|
зазора между муфтой и стенками |
|||
|
скважины ( ) для заполнения ее |
|||
Рис. 3.7. Конструкция скважины |
цементным раствором (табл. 3.1). |
Чтобы определить диаметр долота, которым предстоит бурить
ствол под эксплуатационную колонну, используется формула
Dд d5 Dм 2 , мм,
188
Таблица 3.1. Рекомендуемые зазоры для заданных диаметров об-
садных колонн |
|
|
|
|
|
|
|
Наружный диаметр об- |
114 |
140, 146 |
168 |
219 |
273 |
324 |
377 |
садной колонны Dот , мм |
127 |
159 |
194 |
245 |
299 |
351 |
426 |
Диаметр муфтыDм , мм |
133 |
159, 166 |
188 |
245 |
299 |
351 |
402 |
|
146 |
180 |
216 |
270 |
324 |
376 |
451 |
Кольцевой зазор , мм |
15 |
20 |
25 |
30 |
35 |
45 |
50 |
После того как установлен диаметр долота |
d5 , определяют диаметр |
предыдущей колонны (промежуточной колонны или, если таковой нет – кондуктора). При этом разница между внутренним диаметром этой (преды-
дущей) колонны и размером долота Dд , проходящим через нее, находится в
пределах 6 – 10 мм. Наружный диаметр обсадной трубы выбирается как ближайший к размеру Dот Dд 2Sот (6...10мм)
Методика определения размеров долота Dд = d4 , d3 ,d2 для бурения
ствола скважины под промежуточные колонны или кондуктор аналогична предыдущему рассуждению.
Нефтяная (газовая) скважина обычно начинается с бурения ствола диаметром d1 =394—914 мм и глубиной L1 =60—100 м. Для защиты поверх-
ностных пластов от размыва буровым раствором и предотвращения размыва устья скважины с дальнейшим отводом потока жидкости из ствола в очистную систему, верхний участок скважины крепится направляющей колонной обсадных труб (1).
В районах, где много растительности и неустойчивая почва, направление (диаметром 762—1067 мм) вдавливается агрегатом для забивания
свай на глубину около L1 =30 м.
Кондуктор 2 спускается в ствол скважины, пробуренный диаметром d2 на глубину L2 , достаточную для крепления верхних неустойчивых ин-
тервалов разреза, а также для перекрытия поглощающих пластов и изоляции водоносных горизонтов от загрязнения. Если наносы имеют небольшую мощность и относительно устойчивы в период бурения, то кондуктор одновременно может быть использован и как направляющая колонна. В зависимости от целевого назначения на него устанавливается противовыбросовое или другое технологическое оборудование (7). При глубине спуска кондук-
тора L2 100м , необходимо произвести проверку соблюдения условия, а
именно, после извлечения бурильной колонны из скважины жидкость должна сохраняться внутри кондуктора на уровне не менее 10 м над его башмаком.
После того как кондуктор зацементирован, через него спускают долото меньшего размера и бурят новый ствол до требуемой глубины. Глубина
189
зависит от геологических условий и пластовых давлений. Это участок ство-
ла крепится промежуточной обсадной колонной 3
При составлении конструкции необходимо ориентироваться как в сортаменте обсадных труб, так и в размерах породоразрушающего инструмента, используемого для бурения скважины.
Наиболее часто в практике буровых работ применяются трубы, имеющие 18 номинальных наружных диаметров ( Dom ) от 114 до 508 мм.
Трубы каждого размера изготовляют с несколькими толщинами стенок ( Sот ). Например, трубы диаметром 114 мм изготавливаются с толщиной
стенки 6,4; 7,4 и 8,6 мм. Трубы диаметром 127 мм выпускаются с толщиной стенки 6,4; 7,5 и 9,2 мм. Трубы диаметром 140 и 146 мм имеют толщину 7; 7,7; 8,5; 9,2 и 10,7 мм. Толщина стенок труб диаметром 168 – 324 мм находится в диапазоне 7,3 – 14,8 мм. Трубы диаметром 351, 377 и 426 мм имеют толщину стенки 9; 10; 11 и 12 мм. При этом наружный диаметр обсадных труб остается постоянным. Диаметр бурения этой категории скважин определяется размером долот, которые выпускаются диаметрами до 914 мм.
При проектировании конструкции скважины необходимо также учитывать требования к интервалам цементирования:
за кондуктором – до устья скважины; за промежуточными колоннами нефтяных скважин, проектная глу-
бина которых до 3000 м, - с учетом геологических условий, но не менее 500 м от башмака колонны;
за промежуточными колоннами разведочных, поисковых, параметрических, опорных и газовых скважин вне зависимости от глубины, и нефтяных скважин глубиной более 3000 м – до устья скважин;
за эксплуатационными колоннами нефтяных скважин с учетом пере-
крытия башмака предыдущей колонны - не менее 100 м. Это же условие распространяется на газовые и разведочные скважины при осуществлении мероприятий, обеспечивающих герметичность соединений обсадных труб (сварные соединения труб, специальные высокогерметичные резьбовые соединения и др.). Во всех остальных случаях цемент должен подниматься до устья скважины.
3.2.1. Способы бурения скважин на нефть и газ
Нефтяные и газовые скважины сооружаются методом вращательного бурения. Породы на забое скважины разрушаются вращающимся долотом, на которое действует осевая нагрузка. Разрушенная порода удаляется из скважины закачиваемым в колонну труб и выходящим через заколонное пространство буровым раствором, пеной или газом. По характеру разрушения горных пород на забое имеет место сплошное и колонковое бурение.
190
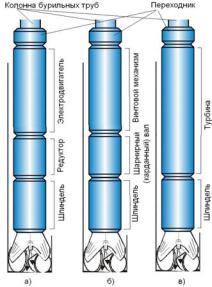
По способу передачи крутящего момента долоту различают роторное бурение и бурение забойными двигателями.
Роторный способ наиболее распространен и составляет более 80% выполняемых объемов буровых работ. При этом способе долото вращается вместе со всей колонной бурильных труб. Крутящий момент на колонну передается через ведущую трубу, располагающуюся внутри вращающегося стола ротора. Нагрузка на долото создается частью веса бурильных труб.
При бурении забойными двигателями (турбобурами, электробурами, винтовыми двигателями), которые устанавливаются непосредственно над долотом, бурильная колонна в формировании крутящего момента на долото не участвует, и ограничена функциями элемента для создания осевой нагрузки и подачи жидкости на забой скважины. Принцип работы забойных двигателей основан на преобразовании гидравлической энергии потока промывочной жидкости (в элементах турбобура и винтового двигателя) или электрической энергии (в элементах электробура) в механическую энергию вращения вала и соединенного с ним долота.
Бурение электробуром. Электробур структурно состоит из трех элементов: электродвигателя переменного тока, защищенного от проникновения жидкости; понижающего редуктора; и шпинделя (рис. 3.8, а). Энергия к нему подается с поверхности по кабелю, расположенному внутри колонны бурильных труб. Электробур присоединяют к нижнему концу бурильной колонны, а долото крепится к вращающемуся валу шпинделя, который является промежуточным узлом для передачи крутящего момента и нагрузки от вала двигателя на долото.
Бурение винтовыми (объемными) двигателями. Винтовой дви-
гатель (рис. 3.8, б) включает винтовой механизм, шарнирный вал и шпиндель, и представляет собой разновидность забойной гидравлической машины, в которой энергия потока промывочной жидкости преобразуется в энергию вращательно-
го движения вала винтового механизма. Корпус механизма является неподвижным и при помощи переводника соединяется с колонной бурильных труб. Вращающий момент от вала винтового механизма посредством шар-
191
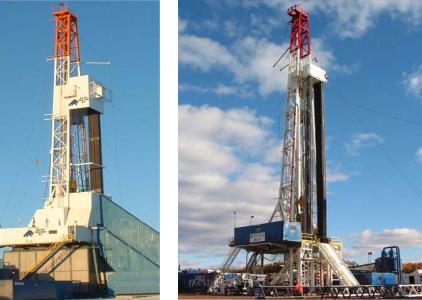
нирного соединения (карданного вала) передается на вал шпинделя, на котором закрепляется долото.
Турбинное бурение. Турбобур (рис. 3.8, в) представляет собой гидравлическую турбину, приводимую во вращение энергией потока промывочной жидкости. В корпусе турбобура закреплены неподвижные турбинные колеса, лопасти которых обеспечивают направленное движение потока на лопатки вращающихся (рабочих) турбинных колес, жестко установленных на валу турбины. При этом величина крутящего момента на валу представляет собой сумму моментов формирующихся на каждом рабочем колесе, количество которых в турбине достигает 100 шт и более. Шпиндель турбобура кроме обычных функций (передача крутящего момента и нагрузки на долото), выполняет роль уплотнительного узла, способствуя созданию необходимого перепада давления на лопатках гидротурбин.
3.2.2. Буровые установки. Оборудование и инструмент для бурения скважин
Бурение скважин осуществляется буровой установкой, представляющей собой комплекс наземного оборудования, необходимого для выполнения операций по проводке скважины (рис. 3.9 – 3.10).
Рис. 3.9. Внешний вид современных установок для бурения скважин на нефть и газ
192
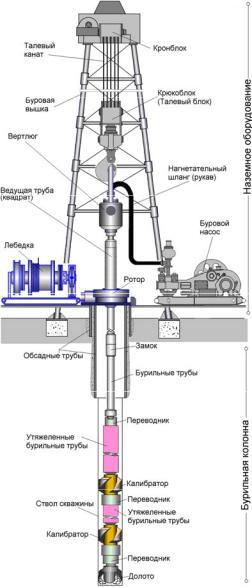
Связующим звеном междудолотом, находящимся на забое скважины, и буровымоборудованием, расположеннымнаповерхностиявляетсябурильнаяколон-
на(рис. 3.10).
Рис. 3.10. Принципиальная схема установки для бурения скважин
193
В общем случае, наземный комплект буровой установки включает: буровую вышку; оборудование для выполнения спускоподъемных операций; вертлюг; ротор; буровые насосы; силовой привод; ключи для механизации операций по свинчиванию и развинчиванию бурильных и обсадных труб; циркуляционную систему бурового раствора.
Буровая вышка – это сооружение над скважиной для спуска и подъема бурового инструмента, бурильных и осадных труб, размещения бурильных свечей после подъема их из скважины; защиты буровой бригады от ветра и атмосферных осадков.
Основными параметрами вышки являются грузоподъемность, высота, емкость «магазинов» для размещения свечей бурильных труб (соединенные между собой дветри бурильные трубы), размеры нижнего и верхнего оснований, длина свечи, масса.
Грузоподъемность вышки – предельно допустимая вертикальная статическая нагрузка, которая не должна быть превышена в процессе всего цикла проводки скважины.
Высота вышки определяет длину свечи, которую
можно извлечь из скважины и от величины которой зависит продолжительность спускоподъемных операций. С ростом глубины бурения высота и грузоподъемность вышек увеличивается. Так, для бурения скважин на глубину 300…500 м используются вышки высотой 16…18 м; на глубину 2000…3000 м – высотой 42 м; и на глубину 4000…6500 м – высотой 53 м.
Размеры верхнего и нижнего оснований характеризуют условия работы буровой бригады с учетом размещения бурового оборудования, бурильного инструмента и средств механизации спускоподъемных операций.
Общая масса буровых вышек составляет несколько десятков тонн.
Оборудование для выполнения спускоподъемных операций включает талевую систему и лебедку.
Талевая система является полиспастом (системой блоков), который в буровой установке предназначен, в основном, для уменьшения натяжения талевого каната, а также для снижения скорости движения бурильного инструмента, обсадных и бурильных труб.
Талевая система состоит из кронблока, талевого блока и бурового крюка (или крюкоблока, представляющего собой совмещенную конструкцию талевого блока и бурового крюка).
Талевый блок перемещается вверх и вниз по вышке во время свинчивания и развинчивания труб.
Кронблок — это неподвижный блок, находящийся в верхней части вышки.
Каждый блок имеет ряд шкивов, через которые проходит талевый канат, один конец которого крепится к барабану лебедки, а другой закреплен неподвижно под подвышечным основанием к специальному механизму крепления (мертвый конец).
Буровая лебедка является одним из основных узлов подъемной части буровой установки. В комплекте с талевой системой лебедка предназначена для выполнения следующих операций: спуска и подъема бурильных и обсадных труб; удержания на весу бурильного инструмента; производства вспомогательных работ по свинчиванию и развинчиванию бурильных и обсадных труб; подтаскиванию различных грузов, подъема оборудования в процессе монтажа установок и т.п.
При бурении бурильная колонна подвешивается на крюке с помощью вертлюга.
Вертлюг (рис. 3.11) устанавливают над ведущей трубой. Его основная функция — исключить передачу вращательного движения от ведущей трубы или бурильной колонны к талевому канату. Это осуществляется вращением нижней части вертлюга на мощных роликовых подшипниках. Поскольку вертлюг должен выдержать вес всей бурильной колонны, он должен быть очень прочным и иметь те же номинальные характеристики, что и талевый блок. Корпус 4 вертлюга подвешивается на буровом крюке (или
194
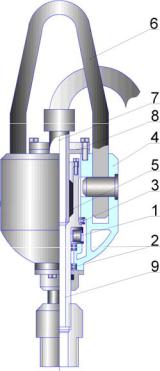
крюкоблоке) с помощью штропа 6. В центре корпуса проходит напорная труба 7, переходящая в ствол 9, соединенный с бурильными трубами.
|
Напорная труба и ствол жестко |
||||
|
не связаны. Вращающийся ствол 9 |
||||
|
опирается |
на |
опорный |
роликовый |
|
|
подшипник 1, воспринимающий на- |
||||
|
грузку бурильной колонны. Кроме ос- |
||||
|
новного опорного подшипника, на |
||||
|
верхней поверхности опорной части |
||||
|
вращающегося ствола имеется опор- |
||||
|
ный шариковый подшипник 3, вос- |
||||
|
принимающий нагрузку на ствол, на- |
||||
|
правленную вверх. Помимо двух |
||||
|
опорных, в системе предусмотрены |
||||
|
два радиальных подшипника 2, цен- |
||||
|
трирующих ствол относительно кор- |
||||
|
пуса 4. Для уплотнения зазоров между |
||||
|
вращающимися и неподвижными де- |
||||
|
талями в вертлюге имеются сальники, |
||||
|
один из которых (5) является основ- |
||||
|
ным, уплотняющим зазор между шту- |
||||
|
цером напорной трубы 7 и вращаю- |
||||
|
щимся стволом 9. Вследствие тяжелых |
||||
|
условий работы основной подшипник |
||||
|
работает в масляной ванне. |
|
|||
|
Для |
соединения с |
бурильной |
||
|
колонной на нижний конец ствола |
||||
Рис. 3.11. Принципиальная схема |
вертлюга навинчивается переводник с |
||||
левой резьбой. Подача промывочной |
|||||
вертлюга-сальника |
|||||
жидкости от неподвижной нагнета- |
|||||
|
|||||
|
тельной линии к вертлюгу и далее к |
||||
|
вращающимся |
бурильным трубам |
осуществляется при помощи гибкого резинового шланга (рукава). Напорный рукав (шланг) состоит из внутреннего и наружного резино-
вых слоев. Между слоями размещаются чередующиеся слои прорезиненной ткани, капроновые или металлические корды (плетенки). В настоящее время применяют буровые шланги, рассчитанные на давление 32, 25, 20, 16 и10 МПа. Буровыешлангивыпускаютсядлинойот 10 до 18 м с условными внутренними диаметрами 63, 80 и 100 мм.
Ротор (рис. 3.12) – это редуктор, передающий вращательное движение вертикально подвешенной колонне бурильных труб от горизонтального
195