
изоляции, свойства металла и сварных швов, механические напряжения);
разработка методики планирования ремонтных работ, отвечающей требованиям максимальной эффективности, разработка критериев оценки эффективности ремонта;
разработка эффективных и безопасных методов ремонта трубопроводов;
разработка методов дальнейшего (послеремонтного) слежения за техническим состоянием трубопроводов.
Выполнение данных работ требует решения множества сопутствующих задач, например:
развить средства диагностики (разработать новые приборы и совершенствовать известные);
подготовить трубопроводы для проведения диагностики новыми приборами и техническими средствами;
разработать критерии отбраковки участков трубопроводов (не подлежащих ремонту);
разработать критерии возможности повторного использования демонтированных труб и других элементов трубопроводов;
разработать технологии упрочнения (восстановления, ремонта) трубопроводов, не отвечающих современным требованиям (например, со сварными стыками на подкладных кольцах, сварных стыков, выполненных газопрессовой сваркой); решить вопросы по обеспечению нормативной базой (нормативными документами) по всем видам работ на магистральных нефтепроводах с учетом современных требований надзорных органов и реального состояния трубопроводов; разработать критерии и компьютерные программы для составления оптимальных планов ремонта в современных условиях (развитие внутритрубной диагностики, значительная, но неполная выявляемость дефектов, большой объем диагностической информации, недостаток технических и финансовых
средств); совершенствовать расчетные методы, отражающие влия-
ние всех важных факторов на прочность, надежность, безопасность трубопроводов.
Вышеперечисленный список проблем и задач не претендует на абсолютную полноту, а только отражает взгляд авторов на предмет, их опыт и знания.
Решение большей части вышеперечисленных проблем и задач в конечном счете направлено на то, чтобы обеспечить безопасность магистральных нефтепроводов. Понятие «безопасность» до 1998 г. в основном применяли в сочетании с по-
27
нятиями «правила безопасности» и «охрана труда». Эти понятия изначально были ориентированы на то, чтобы ограничивать поведение работающего персонала на различных объектах во избежание несчастных случаев, связанных с эксплуатацией исправного оборудования. О том, исправно ли это оборудование и насколько оно надежно, опять же вопрос прямо не стоял (оборудование должно было быть исправным и не исчерпавшим установленные ресурсы, в том числе временные).
В начале 90-х годов XX века, с ужесточением контроля за состоянием окружающей среды (после массовых отравлений водой и воздухом, заражений и заболеваний) стали применять понятие «экологическая безопасность».Это понятие также было ориентировано на то, чтобы не допустить ущерба окружающей среде в процессе эксплуатации оборудования в исправном состоянии. Если же происходила авария с выходом нефти наповерхность земли (воды), проблема оценки экологической безопасности не поднималась, а тут же приступали к оценке размеров ущерба в рублях и искали виновника. Этот виновник и должен был покрыть затраты на «восстановление» окружающей среды. Полного восстановления, конечно, не достигали, но работа на этом считалась выполненной.
Таким образом, случаи аварий, разрушений, катастроф на магистральных нефтепроводах, как и других промышленных объектах, рассматривались как совершенно неожиданные, случайные явления. Они даже как-то находились в одном ряду с природными катаклизмами типа вулканов, землетрясений, ураганов, потопов и т.д. Поскольку природные катаклизмы невозможно избежать и надежно предсказать, то подсознательно считалось, что технические катаклизмы также невозможно избежать и предсказать. Во всяком случае, теорий по техногенным катастрофам, которые можно было бы применить на практике, не встречалось.
В соответствии с одним из законов философии, количество когда-нибудь переходит в качество (или наоборот). Наша промышленность это смогла доказать к концу 90-х годов ХХ века. Всякого рода техногенные катастрофы, аварии, разрушения участились настолько, что общая картина стала обретать другое качество. Расследования причин разрушений всякий раз давали примерно одни и те же результаты. Причины были следующие: наличие дефекта на конструкции, нарушение технологии, невнимательность или халатность персонала, ошибки в прочностных расчетах, недооценка какихто важных источников риска и опасности.
28
Наблюдалось интересное явление. Поскольку в прочностных расчетах обычно используют достаточно большие запасы, разрушения почти никогда не происходили сразу, только по одной причине. Надо было совпасть сразу нескольким причинам в одном месте и в одно время, чтобы разрушение все-таки произошло. Для того, чтобы убедиться в этом, достаточно рассмотреть несколько разрушений на магистральных нефтепроводах, в расследовании причин которых участвовали авторы настоящей работы.
1. Катастрофа на 1431 км продуктопровода Омск − Альметьевск в июне 1989 г.(недалеко от НПС Улу-Теляк).
Продуктопровод диаметром 720 мм протяженностью почти 2000 км был построен в 1985 г. и начал перекачивать продукт − широкие фракции легких углеводородов. Этот продукт при нормальных условиях (атмосферное давление, комнатная температура) представляет газ тяжелее воздуха, обладает характерным запахом, воспламеняется (взрывается) от искры, подобно природному газу, действует на организм отравляюще. Транспортируется по трубопроводу в жидком состоянии под давлением порядка 4,0 МПа. При разгерметизации трубы продукт выходит в атмосферу, переходя в газообразное состояние и охлаждаясь до температуры ниже −20 °С от быстрого расширения. Поэтому этот газ представляет собой белый туман, стелящийся по поверхности земли. В отличие от бытового газа на основе метана такой газ не поднимается в воздух, а медленно «течет» по рельефу местности, заполняя низины и ущелья.
Продуктопровод должен был проходить не ближе 5 км от населенных пунктов. Небольшие деревни, находящиеся вблизи от трассы, предусматривалось переселить в другие районы. Строительство велось несколькими строительными трестами по интенсивному плану. В установленный срок были проведены гидроиспытания. Но принять трубопровод в эксплуатацию и начать перекачку продукта не позволил один пункт − рядом осталась деревня Казаяк-Хуснуллино с жителями. Переселение деревни оказалось делом хлопотным, долгим и это затягивало срок пуска. Проще оказалось на данном участке обойти деревню, хотя это тоже было непросто. Местность была горная, сильно пересеченная. Лимиты были исчерпаны и по времени, и по материалам, и по финансовым ресурсам. За короткое время построили обходной участок, который включал и переход через железную дорогу Уфа − Челябинск с интенсивным движением поездов.
29
Для пуска продуктопровода вроде бы не осталось формальных причин. Расстояние до населенного пункта выдержано, гидроиспытание трубопровода проведено, акты подписаны. Только при этом допущен целый ряд нарушений:
обходной участок трубопровода остался неиспытанным; контроль качества строительства практически отсутство-
вал; на трубах допущено много механических дефектов в виде
продольных царапин, глубина которых достигала 30 % толщины стенки;
изоляция труб местами отсутствовала.
Приемку в эксплуатацию продуктопровода подписал завод, перерабатывающий данный продукт, который никогда не занимался проблемами трубопроводного транспорта, особенно на такие большие расстояния и такого опасного продукта. После приемки продуктопровод был все же передан на баланс управления «Уралсибнефтепровод» под нажимом правительства того времени.
В этот период времени модным становился термин «безлюдная технология». Многие предприятия как наперегонки искали способы сокращения количества персонала на своих объектах. Процент сокращения штатов становился одним из важнейших показателей планов того времени. Явление коснулось как трубопроводных управлений, так и управлений железными дорогами. В результате были сокращены обходчики и на продуктопроводе, и на железной дороге.
Продуктопровод эксплуатировался в циклическом режиме, характерном для всех магистральных нефтепроводов. Давление поддерживалось не выше проектного, но в среднем 1 раз в сутки оно падало по разным причинам. В течение 3-х лет эксплуатации продуктопровода произошло порядка 1000 перепадов давления. При таком режиме происходит усталостное накопление повреждений металла на концентраторах напряжений, какими являются имеющиеся царапины. Постепенно появляются усталостные трещины, которые растут и превращаются в сквозную трещину (свищ). С этого момента начинается выход сжатого газа из трубы. Происходит сильное охлаждение трубы и грунта от расширения газа (эффект холодильника). Металл становится более хрупким. Сквозная трещина быстро растет в длину и переходит в магистральную трещину. Трубопровод раскрывается на длине порядка 3−5 диаметров. Сжатым газом выбрасывается грунт над трубой, появляется воронка. Начинается интенсивный выход газа. За короткое время образовывается облако, которое покрывает
30
большую площадь. Поскольку разрыв трубы произошел на седловине горной местности, тяжелое облако ползет (течет) по двум ущельям. Один поток облака идет по ущелью в сторону железной дороги и накрывает ее на 1710-м км. Другой поток идет в сторону деревни Казаяк-Хуснуллино, но не успевает дойти до нее. От проходящих поездов (дорога электрифицирована) появляется искра, детонирует все облако вышедшего газа. Волей судьбы в этот момент встречаются именно на этом месте два пассажирских поезда и оказываются в сплошном огне. Ударная волна выбрасывает один электровоз и часть вагонов за откос. До деревни огонь не доходит. Ударная волна от взрыва облака проходит выше деревни, но наносит повреждения зданиям других деревень, находящихся на расстоянии до 10 км от места катастрофы. Лес полностью выгорает на большой площади. В огне оказываются около 1200 человек.
Система автоматического слежения обнаруживает падение давления со значительным опозданием из-за того, что в сжатом (сжиженном) газе законы гидравлики значительно отличаются от нефти, бензина и других обычных жидкостей.
Таким образом, для того, чтобы «получить» данную катастрофу, необходимо было допустить очень много ошибок и оплошностей.
Обследование технического состояния трубопровода с привлечением многих специалистов, в том числе зарубежных, показало, что дальнейшая эксплуатация продуктопровода для транспортировки данного продукта представляет реальную опасность для 52-х населенных пунктов, в том числе для городов Златоуст, Кропачево, Сим. В течение 1989−1990 гг. выполнен большой объем работ по повышению надежности продуктопровода (замена дефектных участков). После повторного обследования технического состояния авторитетная комиссия решила, что продуктопровод в таком состоянии можно эксплуатировать в течение 3-х лет, но с определенным риском. С протестами против повторного пуска продуктопровода выступили жители всех близлежащих населенных пунктов и руководители Башкортостана, Челябинской, Курганской областей, профсоюзные и общественные организации. Решено данный трубопровод использовать в качестве нефтепровода от Тобольска до Миннибаево (с демонтажом опасных участков). В настоящее время данный трубопровод не эксплуатируется, некоторые участки демонтированы.
Данный пример показывает, насколько важно обеспечение
31
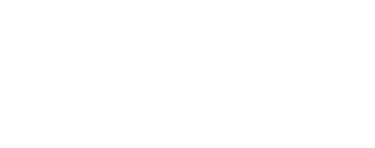
надежности трубопровода на каждом этапе его жизни: проектирования, изготовления труб, строительства, контроля качества монтажа, эксплуатации, диагностического обследования. При несоблюдении некоторых требований можно получить очень большие затраты и потери.
2. Разрушение магист рального нефт епровода № 9 Грушовая − Шесхарис в мае 1997 г.
Нефтепровод диаметром 1016 мм построен в 1995 г. хорватской фирмой ИНА-РОСС по собственному проекту. Трубопровод предназначался для подачи нефти из резервуаров нефтебазы «Грушовая» в нефтебазу «Шесхарис» при наливе танкеров. Поскольку нефтебаза «Грушовая» находится на высоте нескольких сот метров над уровнем моря, для снижения статического давления был сооружен узел регулирования давления. В середине нефтепровода была установлена задвижка, используемая только при ремонтных работах или подготовительных технологических операциях. В остальное время эта задвижка всегда находилась в открытом положении. Конструкция узла регулирования имела вид, показанный на рис. 1.2.
Ошибка конструкции состояла в том, что к магистральной трубе были врезаны два ответвления под углом 45° в одном сечении (такие конструкции российскими нормами не допускаются). В расчетах прочности допущены ошибки. Не учтены два фактора, ослабляющие магистральную трубу на месте врезки ответвлений:
1) при врезке под 45° магистральная труба ослаблена на отрезке длиной АВ, который больше диаметра ответвления на
42%;
2)в одном сечении магистральной трубы имеются два ос-
Рис. 1.2. Схема устройства узла регулирования давления
32
лабляющие отверстия АB и CD, соответствующие двум ответвлениям.
Кроме того, допущены дефекты сварки − непровары на несущих сварных швах (это обнаружено обследованием макрошлифов после аварии).
Была внедрена технология транспортировки нефти при неполном сечении трубопровода (самотеком). На монитор диспетчера выводилась вся информация о состоянии трубопровода, включая положение задвижки, давления на контрольных точках.
В ночь с 27 на 28 мая 1997 г. задвижка оказалась закрытой (вероятно, в предыдущую смену проводились какие-то работы). Информация об этом имелась на экране монитора, но диспетчер ее не заметила и дала команду на подачу нефти по трубопроводу и начало загрузки иностранного танкера. Началась подача нефти с нефтебазы «Грушовая», но она не доходила до нефтебазы «Шесхарис». Прошло значительное время, пока диспетчер не обнаружила закрытую задвижку; заметив, испугалась и решила исправить ошибку и дала команду, как можно быстрее открыть задвижку. Это была вторая ошибка диспетчера. Надо было остановить подачу нефти с «Грушовой» и спокойно выйти из нештатной ситуации.
После быстрого открытия задвижки поток нефти устремляется вниз, сжимает газовую компоненту в трубе, разрушает узел регулирования давления, преодолевает все препятствия на своем пути и попадает в открытое море. В момент разрыва трубы от силы отдачи участок трубопровода откатывается в обратном направлении (наверх) и падает со своих опор (нефтепровод надземный). По разным оценкам от 40 до 200 т нефти попадает в море. Трубопровод на полгода выходит из строя.
Данный пример также показывает, что авария произошла при возникновении нескольких ошибок одновременно в одном месте. Как показали результаты обследований, данной аварии не было бы, если исключить хотя бы одну из допущенных ошибок (ошибка в расчетах прочности, дефекты сварки, ошибки диспетчера). При таком количестве ошибок запасов прочности конструкций не хватает.
3. Авария на 333-ом км магист рального нефт епровода Туймазы − Омск − Новосибирск-II (ТОН-II) в 1999 г.
Нефтепровод ТОН-II диаметром 720 мм построен в 1959 г. В 1998 г. проведено внутритрубное обследование дефектоскопом «Ультраскан WM» и выявлены опасные дефекты. В число таких дефектов попалдефект следующего вида(рис. 1.3).
33
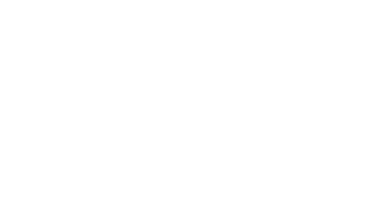
Рис. 1.3. Форма комбинированной заплаты на стенке трубопровода
В трубопроводе 1 во время строительства, испытаний или вытеснения продуктом (точных сведений нет) было вырезано технологическое окно, примыкающее к стыковому шву 4. Затем это окно было заварено с применением заплаты 3. При этом качество сварки получилось неудовлетворительное; сварной шов 5 содержал глубокие непровары. Поэтому решили на этом месте трубу усилить с помощью дополнительной (накладной) заплаты 2. При этом угловой шов 6 по периметру заплаты 2 получился тоже с дефектами в виде прожогов на переходе к основному металлу. Таким образом, здесь были допущены следующие нарушения норм:
технологическое окно вырезано прямо на сварном стыке трубопровода (должно быть не ближе 100 мм от стыка);
накладная заплата имеет прямоугольную форму (должна быть овальной, чтобы не было углов);
сварка выполнена неквалифицированными сварщиками. После внутритрубной дефектоскопии проведены шурфовка, визуальный осмотр дефекта, дополнительное дефектоскопическое обследование. Далее было решено ликвидировать этот дефект путем замены трубы. Работу решили выполнить через месяц, чтобы завершить начатые срочные дела, подготовиться и согласовать технологии. До этого было решено снизить рабочее давление путем приостановки перекачки нефти по данному участку трубопровода, направив поток по другому трубопроводу. При этом нефтепровод решили не опорожнять. Местность была горная.
34
После приостановки потоканефти расчетное статическое давление составляло 15,5 кг/ см2, что на 2 кг/ см2 меньше рабочего давления. Однако после переключения потока нефти на другой трубопровод произошло разрушение на остановленном нефтепроводе с выбросом некоторого объема нефти на поверхность земли и попаданием в реку. Это говорило о том, что фактически давление в трубе в момент разрушения было выше, чем до остановки перекачки.
Обследование аварийной катушки подтвердило наличие дефектов, отмеченных выше. Расчетные оценки разрушающего давления в момент разрушения трубы приводили к значению не ниже 40 кг/ см2. Причем такое давление не вызвало удивления у специалистов по эксплуатации, хотя причину повышения давления после остановки перекачки никто не раскрыл.
Остается допустить, что после переключения потока нефти по другому трубопроводу давление в отключенном участке возросло из-за негерметичности системы задвижек. Давление от другого (работающего) нефтепровода через негерметичные задвижки передалось на отключенный участок. Таким образом, допущено дополнительное нарушение технологического характера, при котором произошло повышение давления на дефектном участке.
Данный случай также подтверждает, что разрушение произошло по нескольким причинам сразу. Каждая причина в разной степени приближала трубу к аварии.
Примеров аварий и катастроф, подобных описанным, можно привести много. Спрашивается, можно ли было избежать этих аварий и что для этого необходимо делать?
Можно! Для этого необходима эффективно действующая
государст венная сист ема эксперт изы промышленной без-
опасност и магистральных нефтепроводов. Экспертиза должна объективно оценить источники опасности, разработать рекомендации по обеспечению безопасности. Система экспертизы промышленной безопасности (ЭПБ) в нашей стране создана в 1997 г. с принятием федерального закона «О промышленной безопасности опасных производственных объектов». Система экспертизы в настоящее время находится на стадии становления и динамично развивается и совершенствуется. Основные принципы системы ЭПБ сформулированы
изаключаются в следующем.
1.Независимост ь. Экспертные организации должны быть независимыми от организаций, чьи объекты подлежат экс-
35
пертизе. Методы достижения независимости определены в постановлениях Госгортехнадзора России.
2. Компет ент ност ь. Экспертизу имеют право проводить только те организации и эксперты, которые в установленном порядке аккредитованы и аттестованы. Процедура аккредитации также определена.
В настоящее время разработаны требования к экспертным организациям, порядок проведения экспертизы, требования к заключениям.
Экспертизу проводят по следующим четырем направлениям:
проект ной документ ации на строительство, расширение, реконструкцию, техническое перевооружение, консервацию и ликвидацию опасных производственных объектов;
зданий и сооружений на опасных производственных объектах;
т ехнических уст ройст в, применяемых на опасных производственных объектах;
деклараций безопасност и и иных документов, связанных с эксплуатацией опасных производственных объектов.
Список опасных производственных объектов регулярно уточняется (объекты магистральных нефтепроводов входят в список).
Экспертные организации в пределах своей области аккредитации должны иметь в наличии все основные нормативные документы, приборы, оборудование, подготовленных экспертов.
При экспертизе технических устройств требуется, чтобы в составе экспертной организации была лаборатория неразрушающих методов контроля, аттестованная в установленном порядке. Лаборатория должна иметь аттестованные и поверенные средства измерений, методики измерений, подготовленных и аттестованных специалистов.
Как показывает опыт работы по экспертизе безопасности, в особенности технических устройств и технологий, основной проблемой является недостаток методик и других нормативных документов. Этот недостаток вызван двумя основными обстоятельствами:
большая часть технических устройств, включая трубопроводы, отслужила установленный срок, но требуется дальнейшая эксплуатация, поскольку пока их невозможно заменить; существующие нормативы (особенно ГОСТ и ТУ) ориентированы на изготовление новых изделий; как обследовать отслужившие изделия − остается пока много вопросов;
36