
- •Рис. 9.2. К расчету теплообмена в реакторе вытеснения
- •Рис. 7.2. К примеру 10.1
- •Рис. 11.4. К примеру 11.1
- •Рис. 11.9. К расчету шпилек
- •Рис. 11.10. К примеру 11.3
- •Рис. 11.11. К примеру 11.5
- •Рис. 13.10. Рамные мешалки
- •Рис. 13.11. Якорные мешалки
- •Предисловие
- •Экологическое и технико-экономическое обоснование проектов химических производств.
- •Этапы проведения экологической экспертизы
- •Принципы экологической экспертизы
- •Рис. 1.1. Общая система организации проектирования
- •Рис. 1.2. Основные этапы и стадии разработки проектов для промышленного строительства
- •1.2. Задание на проектирование
- •Рис. 1.3. Пример построения розы повторяемости и силы ветров
- •Рис.1.4. Схема выпадения дымовых частиц при наличии зеленых защитных насаждений между застройкой и источником задымления и при отсутствии их:
- •Рис. 1.5. Совмещенная схема движения загрязненных нижнего и верхнего потоков
- •1.5. Разработка проектной документации по охране окружающей среды
- •1.5.2. Разработка прогноза загрязнения воздуха
- •1.5.4. Прогноз воздействия объекта при возможных авариях
- •1.6. Технологический процесс как основа промышленного проектирования
- •Рис. 1.6. Схема производства серной кислоты контактным способом:
- •Рис. 1.8. Процессы и аппараты химической технологии
- •Рис. 1.9. Виды оборудования химической технологии
- •Рис. 1.11. Уровни организации химического предприятия
- •1.7. Генеральный план химических предприятий
- •Рис. 1.12. Генеральный план предприятий химической промышленности
- •1.8. Типы промышленных зданий
- •1.8.1. Одноэтажные промышленные здания
- •Рис. 1.13. Одноэтажное здание павильонного типа:
- •Рис. 1.14. Многоэтажное производственное здание:
- •1.8.2. Многоэтажные здания
- •Рис. 1.15. Многоэтажное производственное здание:
- •Рис. 1.16. Поперечные разрезы зданий I и II очередей сернокислотного производства:
- •1.8.3. Вспомогательные здания и помещения химических предприятий
- •1.8.4. Склады промышленных предприятий
- •1.9. Инженерные сооружения
- •инженерных сооружений
- •1.10. Специальные вопросы проектирования химических предприятий
- •2.1. Основные стадии проектирования химических производств и оборудования
- •Рис. 2.1. Основные стадии проектирования
- •2.2. Виды конструкторских документов
- •2.4.1. Курсовое проектирование
- •2.4.2. Дипломное проектирование
- •2.4.3. Пример использования АвтоЛиспа
- •Рис. 2.2. Схема установки для ректификации трехкомпонентной смеси:
- •СИСТЕМЫ АВТОМАТИЗИРОВАННОГО ПРОЕКТИРОВАНИЯ
- •3.1. История развития САПР
- •3.2. Основные принципы создания САПР
- •Рис. 3.1. Модульная структура программного обеспечения
- •Рис. 3.2. Области использования ЭВМ в процессе проектирования
- •3.4. Автоматическое изготовление чертежей
- •3.5. Основные преимущества автоматизации проектирования
- •3.6. Основные требования к САПР
- •Рис. 3.3. Схема взаимодействия пользователя со средствами САПР:
- •3.7. Связь САПР с производством, расширение области применения
- •3.8. Система автоматизированного проектирования цементных заводов
- •3.8.1. Функционирование САПР
- •ВВЕДЕНИЕ В ПРОЕКТИРОВАНИЕ
- •4.1. Проектно-сметная документация
- •4.2.1. Исходные положения
- •4.2.2. Обоснование способа производства химической продукции
- •ВЫБОР И РАЗРАБОТКА ТЕХНОЛОГИЧЕСКОЙ СХЕМЫ ПРОИЗВОДСТВА
- •5.1. Общие положения
- •5.2. Последовательность разработки технологической схемы
- •Рис. 5.1. Примерная схема стадий технологического процесса:
- •Рис. 5.2. Блок-схема физико-химических процессов, протекающих в гетерофазном реакторе с мешалкой
- •5.3. Принципиальная технологическая схема
- •5.4. Размещение технологического оборудования
- •Выбор технологического оборудования химических производств
- •6.1. Основные типы химических реакторов
- •Рис. 6.1. Установка для непрерывного процесса:
- •Рис. 6.5. Изменение концентрации веществ в реакторах:
- •Рис. 6.6. Реакторы смешения:
- •6.2. Химические факторы, влияющие на выбор реактора
- •6.2.1. Реакции расщепления
- •Рис. 6.7. Относительный выход реакции расщепления:
- •Реактор
- •6.2.2. Реакции полимеризации
- •6.2.3. Параллельные реакции
- •Объем реактора
- •РВНД
- •6.3. Эскизная конструктивная разработка основной химической аппаратуры
- •6.3.1. Общие положения
- •6.3.2. Реакторы
- •6.4. Оптимизация процессов химической технологии
- •УРАВНЕНИЯ МАТЕРИАЛЬНОГО БАЛАНСА ТЕХНОЛОГИЧЕСКОГО ПРОЦЕССА
- •7.1. Стехиометрические расчеты
- •7.2. Термодинамический анализ процессов
- •7.2.1. Равновесие химической реакции
- •Рис. 1.1. Зависимость коэффициента активности газв от приведенных давления и температуры
- •7.2.2. Расчет состава равновесной смеси
- •7.3. Общее уравнение баланса массы
- •7.4. Практический материальный баланс
- •7.5. Физико-химические основы технологического процесса
- •8.1. Общие положения
- •8.2. Расчет объемов реакторов
- •8.2.1. Основные положения химической кинетики
- •8.2.2. Расчет идеальных реакторов
- •8.3. Определение объемов аппарата
- •Тепловой расчет основного оборудования
- •9.1. Общее уравнение баланса энергии
- •Рис. 9.1. К примеру 9.1
- •9.2. Практический тепловой баланс
- •9.3. Теплообмен в реакторах
- •9.4. Расчет энтальпий и теплоемкостей
- •9.6. Расчет реактора периодического действия
- •Рис. 9.3. К тепловому расчету реактора периодического действия
- •9.7. Степень термодинамического совершенства технологических процессов
- •Рис. 9.6. Технологическая схема 1:
- •Рис. 9.7. Технологическая схема 2
- •Рис. 9.8. Схемы использования тепла реакций:
- •Гидравлические расчеты
- •10.1. Расчет диаметра трубопровода
- •Пары, насыщенные при абсолютном давлении (МПа)
- •Рис. 10.1. Зависимость коэффициента трения от критерия Рейнольдса и степени шероховатости трубы
- •10.3. Гидравлическое сопротивление кожухотрубчатых теплообменников
- •10.4. Подбор насосов
- •МЕХАНИЧЕСКИЙ РАСЧЕТ
- •11.1. Расчет сварных химических аппаратов
- •11.1.1. Основные расчетные параметры
- •11.1.2. Расчет на механическую прочность
- •11.1.3. Требования к конструированию
- •11.1.4. Расчет цилиндрических обечаек
- •Рис. 11.1. Номограмма для определения толщины цилиндрических обечаек, работающих под наружным давлением
- •Рис.11.2. Схема пользования номограммой на рис. 11.1:
- •11.1.5. Расчет крышек и днищ
- •Рис. 11.3. Основные конструкции днищ сварных аппаратов:
- •11.1.6. Подбор стандартных элементов
- •11.2. Расчет толстостенных аппаратов
- •Рис. 11.7. Основные конструкции уплотнений затворов высокого давления:
- •Рис. 11.8. К расчету усилий, действующих на затворы высокого давления
- •КОНСТРУКционНЫЕ МАТЕРИАЛЫ В ХИМИЧЕСКОМ МАШИНОСТРОЕНИИ
- •12.1. Виды конструкционных материалов
- •12.2. Коррозия металлов и сплавов
- •12.2.1. Виды коррозии
- •12.2.2. Виды коррозионных разрушений
- •12.2.3. Способы борьбы с коррозией
- •12.3. Влияние материала на конструкцию аппарата и способ его изготовления
- •12.3.1. Конструкционные особенности аппаратов из высоколегированных сталей
- •Рис. 12.1. Сварка встык:
- •Рис. 12.2. Способы подготовки кромок под сварку
- •Рис. 12.4. Способы сварки легированной и углеродистой стали
- •12.3.2. Конструктивные особенности эмалированных аппаратов
- •Рис. 12.5. Элементы конструкции эмалированных аппаратов
- •Рис 12.6. Пайка элементов медных аппаратов
- •12.3.3. Конструктивные особенности аппаратов из цветных металлов
- •Рис. 12.7. Основные типы паяных соединений
- •12.3.4. Конструктивные особенности аппаратов из пластмасс
- •ОФОРМЛЕНИЕ ОТДЕЛЬНЫХ ЭЛЕМЕНТОВ ХИМИЧЕСКОЙ АППАРАТУРЫ
- •13.1. Оформление поверхности теплообмена
- •Рис. 13.5. Реактор со змеевиковой рубашкой
- •Рис. 13.6. Рубашка с вмятинами
- •Рис. 13.8. Вывод змеевика через крышку аппарата:
- •13.2. Перемешивающие устройства
- •Рис. 13.12. Листовая мешалка
- •Рис. 13.13. Пропеллерные мешалки
- •Рис. 13.14. Турбинные мешалки открытого (а) и (б) закрытого типа
- •Рис. 13.15. Крепление мешалок к ступице:
- •13.3. Уплотнения вращающихся деталей
- •Рис. 13.18. Одинарное торцовое уплотнение:
- •ТРУБОПРОВОДЫ И ТРУБОПРОВОДНАЯ АРМАТУРА
- •Рис 14.5. Фасонные части трубопроводов
- •Рис. 14.7. Крепление горизонтальных и вертикальных трубопроводов на подвесках
- •Рис. 14.8. Компенсаторы:
- •ВСПОМОГАТЕЛЬНОЕ ОБОРУДОВАНИЕ ХИМИЧЕСКИХ ЗАВОДОВ
- •15.1. Виды вспомогательного оборудования
- •Рис. 15.1. Схема многостадийного диспергирования твердой фазы с контрольной классификацией продукта
- •15.2. Транспортные средства
- •15.2.1. Классификация транспортных средств для твердых материалов
- •15.2.2. Машины для транспортировки жидкостей и газов
- •ТЕХНОЛОГИЧЕСКИЕ СХЕМЫ И ОБОРУДОВАНИЕ ДЛЯ ГРАНУЛИРОВАНИЯ ДИСПЕРСНЫХ МАТЕРИАЛОВ
- •16.1. Классификация методов гранулирования и особенности уплотнения гранул
- •Рис. 16.1. Тарельчатый гранулятор:
- •Рис. 16.2. Гранулятор барабанного типа конструкции НИИХиммаша
- •16.3. Основные закономерности и аппаратурное оформление метода экструзии
- •16.5. Гранулирование в псевдоожиженном слое
- •16.6. Технологические схемы процессов гранулирования дисперсных материалов
- •Рис. 16.11. Технологическая схема гранулирования шихты методом окатывания
- •Рис. 16.13. Схема уплотнения шихты в роторном грануляторе
- •Рис. 16.14. Схема гранулирования шихты методом экструзии
- •Рис. 16.15. Схема установки для компактирования шихты
- •ЛИТЕРАТУРА
Г л а в а 13
_________________________________________________________________
ОФОРМЛЕНИЕ ОТДЕЛЬНЫХ ЭЛЕМЕНТОВ ХИМИЧЕСКОЙ АППАРАТУРЫ
_________________________________________________________________
13.1. ОФОРМЛЕНИЕ ПОВЕРХНОСТИ ТЕПЛООБМЕНА
Большинство химических процессов протекает с выделением или поглощением тепла. Достаточно часто в реакторе необходимо держать режим, близкий к изотермическому, поэтому приходится предусматривать теплообмен между реакционной массой и теплоносителем. Чаще всего теплообмен происходит через разделяющую теплоносители стенку, т. е. рекуперативно.
Теплообменными поверхностями обычно являются наружные поверхности аппаратов, снабженные рубашками. Если наружные поверхности реакторов недостаточны, то при невысокой вязкости получаемых продуктов внутри аппаратов устанавливают дополнительные поверхности: змеевики, стаканы.
С точки зрения удобства обслуживания, очистки реактора и простоты его конструкции предпочтительнее наружные теплообменные элементы (рубашки и приварные элементы). 0днако их поверхность теплообмена ограничена наружной поверхностью аппарата. Кроме того, коэффициент теплоотдачи к наружным теплообменным элементам примерно в 2 раза ниже, чем к внутреннему змеевику.
Конструкция теплообменных рубашек зависит от параметров теплоносителей или хладоагентов. При давлениях обогревающей или охлаждающей среды 0,8–0,9 МПа применяются гладкие рубашки, при давлениях до 2,7 МПа – змеевиковые рубашки, изготовленные из прокатных профилей: труб, уголков и т. п., а также рубашки с вмятинами и, например, каркасные.
Рубашки. Как правило, их приваривают к корпусу реактора или делают съемными, когда приварка невозможна (например, для аппаратов, изготовленных из чугуна), а также, когда необходим постоянный контроль за поверхностью теплообмена. Различают: гладкие рубашки, змеевиковые, с вмятинами, каркасные.
Гладкие рубашки. Такая рубашка по своей конструкции повторяет по форме обогреваемый реактор (рис. 13.1).
293
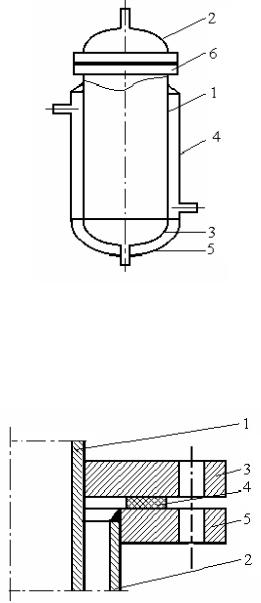
Рубашки выполняются из стали и стандартных выпуклых днищ. Обычно рубашку приваривают на 80−150 мм ниже соединения с корпусом, но в некоторых случаях, когда коэффициент заполнения аппарата невелик, а обогрев или охлаждение верхней незаполненной его части нежелательны, рубашку делают небольшой по высоте.
В пространство между корпусом реактора и рубашкой подается теплоноситель. Пар подают в нее через верхний штуцер, а конденсат отводят через нижний. Жидкие теплоносители обычно вводят через нижний штуцер, а выводят через верхний.
Диаметр рубашки обычно принимают на 50−100 мм больше диаметра реактора. Таким образом, зазор между корпусом аппарата и рубашкой колеблется в пределах от 25 до 150 мм. Зазор между стенками стараются сделать минимальными, чтобы увеличить скорость теплоносителя. Большие зазоры характерны для парообразных теплоносителей.
Крепление гладких рубашек к корпусу реакторов может быть разъемным и неразъемным.
Разъемное крепление применяют для аппаратов, работающих в тяжелых условиях, когда необходимо периодически контролировать поверхность нагрева, очищать ее. Конструкция разъемного крепления рубашки к корпусу представлена на рис. 13.2.
Недостатком такой конструкции является наличие дополнительного фланцевого соединения, что ведет к увеличению расхода материалов и веса реактора. К котлу приваривается фланец 3, к которому на болтах крепится рубашка. Этот второй фланец 3 приваривается на 50−100 мм ниже уровня жидкости в аппарате. Следует заметить, что фланец
для крепления рубашки на чугунных аппаратах отливается заодно с корпусом. Этот способ крепления позволяет легко осуществить монтаж и демонтаж рубашки.
294
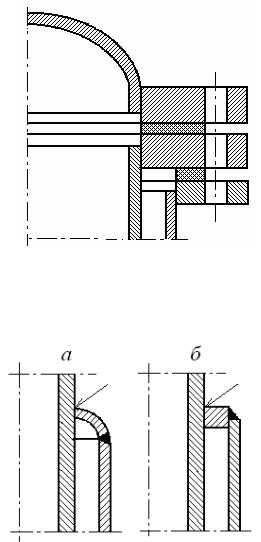
Если требуется, чтобы рубашка полностью покрывала боковую поверхность реактора, то ее крепят прямо к фланцу аппарата, как показано на рис. 13.3.
Более простым и надежным является неразъемное соединение крышки реактора с обечайкой рубашки сваркой, которую осуществляют с помощью отбортовки (рис. 13.4,а) или приварного кольца (рис. 13.4,б).
Крепление рубашек кольцами экономически выгодно в условиях мелкосерийного и индивидуального производства, так как это не требует применения дорогостоящей оснастки.
Недостатком конструкции 13.4,б является высокая концентрация напряжений в месте приварки кольца к корпусу и к рубашке, а также повышенный расход металла и увеличение веса реактора.
Поэтому более удобны плавные конические переходы, называемые воротниками, которые являются и компенсаторами температурных удлинений (рис. 13.4,а). Кстати, этот компенсатор необходим и тогда, когда конус изготовлен из стали Х18Н10Т, а корпус рубашки из стали Ст3.
Для изготовления воротников требуется специальная оснастка, что экономически выгодно при серийном их производстве.
При больших давлениях в рубашке, особенно при отсутствии крепления рубашки к днищу аппарата, когда уравновешиваются силы давления, стремящиеся вытолкнуть корпус аппарата из рубашки, это соединение не применимо.
Наличие рубашки усложняет крепление нижнего спускного штуцера. При небольшой разнице линейных удлинений рубашки и корпуса возможна приварка штуцера одновременно к корпусу и рубашке.
Для удаления инертных газов, создающих подушку, которая исключает часть теплообменной поверхности из процесса теплообмена, в верхней части рубашки предусматривается продувочный штуцер.
295
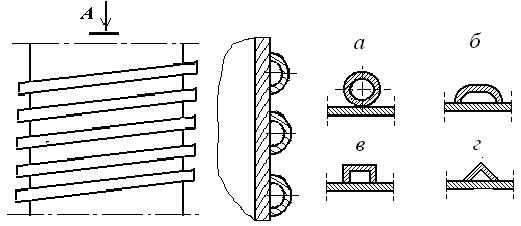
Гладкая рубашка изготавливается из углеродистой стали. Однако следует учитывать, что приварка углеродистой стали к корпусу из нержавеющей стали небольшой толщины (3−6 мм) может ухудшить антикоррозионные свойства металла корпуса. Поэтому, когда среда обладает значительной агрессивностью или требуется высокая чистота продукта, приварка рубашки из стали Ст3 к корпусу аппарата из стали ХI8H9T, например, без промежуточной детали из нержавеющей стали, недопустима.
Змеевиковая рубашка. Она представляет собой спираль из прокатного профиля, приваренную к корпусу аппарата. Приваривать спираль виток к витку не следует, так как это ведет лишь к перерасходу металла, усложняет изготовление аппарата, повышает гидравлическое сопротивление теплообменного устройства.
Участок внутренней поверхности корпуса между витками рубашки можно рассматривать как ребра, от шага змеевика зависит длина ребер. Такие аппараты легче, чем аппараты с гладкими рубашками, так как толщина корпуса и рубашки в первом случае меньше, чем во втором. Приварные элементы располагаются на поверхности аппарата по-разному – в виде спирали, навитой на цилиндрический корпус аппарата, или зигзагообразно по образующей цилиндра.
В тех случаях, когда не требуется большой поверхности теплообмена или, когда теплоноситель находится под большим давлением, применяют приварные теплообменные элементы в виде труб (рис. 13.5,а) или полутруб (рис. 13.5,б.). Возможно также применение приварных элементов из проката − швеллеров (рис. 13.5,в) или уголков (рис. 13.5,г). Минимальное расстояние между приварными элементами определяют из условий доступа к сварным швам.
Рис. 13.5. Реактор со змеевиковой рубашкой
На практике обычно не бывает необходимости устанавливать теплообменные элементы очень близко, так как благодаря хорошей теплопроводности металла участки стенки, прилегающей к приварному элементу, также участвуют в теплообмене.
296