
[elib.tsogu.ru]_kompjuternye-tekhnologii...83-a5 (2)
.pdf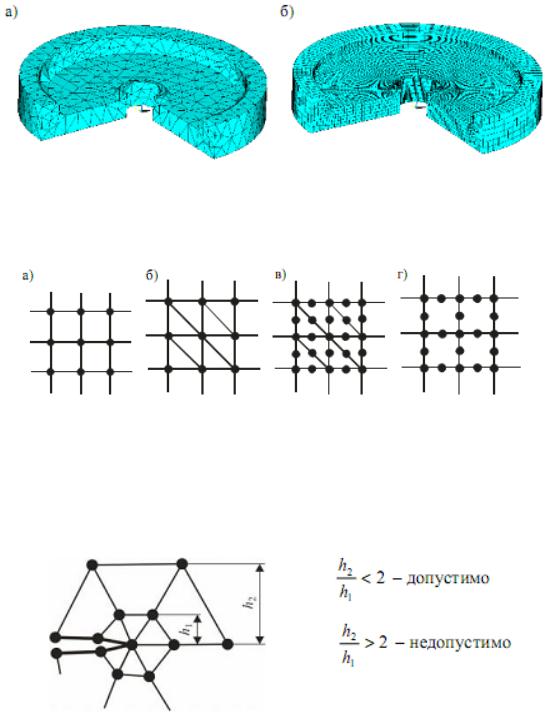
–сетка треугольных элементов с промежуточными узлами (рис. 2.12 в) имеет точность, близкую к сетке прямоугольных элементов с четырьмя узла-
ми (рис. 2.12 а);
–прямоугольная сетка с восемью узлами (рис. 2.12, г) предпочтительнее сетке треугольных элементов с промежуточными узлами (рис. 2.12, в), несмотря на большую площадь прямоугольных элементов;
–аппроксимация смещений кубическим полиномом (элемент третьего порядка) не требует мелкой сетки.
Рис. 2.11. Примеры свободного и регулярного разбиения
Рис. 2.12. Различные типы конечно-элементных сеток
Заметим, что точность результатов расчетов уменьшается, если существенно различаются размеры соседних элементов вблизи концентратора напряжений рис. 2.13.
Рис. 2.13. Допустимые размеры элементов
51
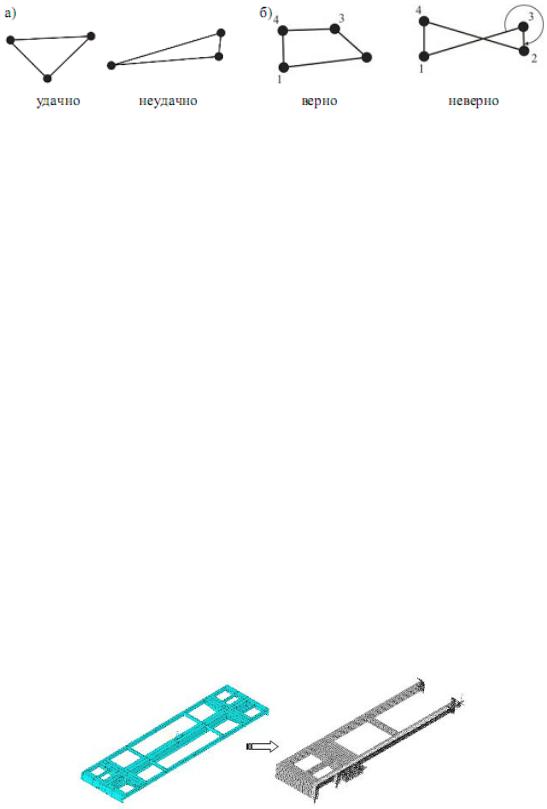
Форма конечных элементов также влияет на точность вычислений. Следует избегать слишком вытянутых элементов, так как элементы с примерно одинаковыми размерами сторон дают меньшую ошибку (рис. 2.14 а). Запрещается использовать четырехугольные элементы с углами, превышаю-
щими 180° (рис. 2.14 б).
Рис. 2.14. Примеры форм элементов
Задание граничных условий – один из ответственных этапов конечноэлементного анализа. Этот этап моделирования необходим для того, чтобы обеспечить соответствие перемещений узлов модели аналогичных узлов натурной конструкции. Здесь должны указываться ограничения, наложенные на конструкцию связями, при этом перемещения в зависимости от особенностей работы конструкции могут приобретать как нулевые, так и ненулевые значения. Кроме того, на этой стадии моделирования задаются силовые факторы, действующие на исследуемые объекты.
Граничные условия (перемещения или силы) прикладываются только к узлам. Необходимо обратить особое внимание на то, что число граничных условий должно быть минимально необходимым, чтобы отразить реальную работу конструкции. Так, например, не следует фиксировать все степени свободы в каждом узле элемента; нельзя прикладывать силу в том же направлении, в котором в данном узле запрещено смещение; полное отсутствие закрепления вдоль какой-либо из осей может привести при анализе
ксдвигу вдоль этой оси. Если конструкция имеет оси или плоскости симметрии, то при назначении граничных условий необходимо это учитывать. Так, например, рама вагона (рис. 2.15) имеет две плоскости симметрии. Очевидно, что при ее статических расчетах нет необходимости моделировать всю конструкцию целиком (при условии симметричной схемы нагружения). Можно смоделировать только часть конструкции (½ или ¼), имея в виду, что в точках на плоскостях симметрии перемещения, направленные по нормалям
кэтим плоскостям, отсутствуют. Это обстоятельство учитывается соответствующими граничными условиями.
Рис. 2.15. Моделирование рамы вагона
52
Несмотря на высокий уровень развития программного обеспечения, реализующего МКЭ, результаты расчетов могут оказаться неверными. Использование вычислительной техники в роли «черного ящика», без понимания основных процессов и этапов вычислений, может привести к существенным ошибкам. Приступая к конечно-элементному анализу, исследователь должен понимать:
–к какой области анализа относится данная задача;
–какая часть всей конструкции должна исследоваться подробнее;
–какие упрощения можно допустить при создании расчетной модели. Ошибки могут возникать на различных стадиях анализа: постановке зада-
чи, построении конечно-элементной модели, численном решении. Например, при постановке задачи выбранный тип конечного элемента или его размер может не соответствовать физическому поведению материала конструкции. Еще одним источником ошибок при постановке задачи является некорректное задание граничных условий. Ошибки построения модели (дискретизации) возникают при замене реальной конструкции недостаточным числом конечных элементов. Ошибки, связанные с численным решением, как правило, проявляются при решении задач, в которых имеют место нелинейности.
3.САПР ТЕХНОЛОГА
3.1.Разработка технологии механической обработки изделий
Процесс формирования технологического процесса (ТП) в общем случае – совокупность процедур структурного и параметрического синтеза с принятием и последующим анализом проектных решений. Принятие решения по каждой задаче, за исключением задач расчетного характера, производится в результате выбора известных типовых решений с учетом условий применимости. Для этого достаточно описать весь набор типовых решений, а также условий, при которых может быть выбрано каждое из решений.
По уровню решаемых задач типовые решения подразделяются на две группы: локальные и глобальные. Локальное типовое решение относится к частной технологической задаче, определяющей технологический элемент (например, модель станка при назначении станка на операцию). Глобальное типовое решение охватывает весь круг решаемых задач. Примером такого решения является типовой ТП изготовления деталей определенного типа, выбранный из множества типовых ТП.
Учитывая все перечисленные факторы: характер решаемых задач (расчетные или нерасчетные), разновидности типовых решений (локальные или глобальные), используемые уровни унификации обработки, можно выделить следующие методы автоматизированного проектирования ТП:
1)прямое документирование;
2)параметрическое проектирование;
53
3)использование техпроцессов аналогов;
4)проектирование на основе типизации или унифицированных ТП;
5)синтезирование единичного ТП.
Метод прямого документирования использует средства оформления документации, отбора информации из базы данных и предоставляет технологу следующие возможности:
•набора и корректировки текста проектного документа в специализированном редакторе;
•просмотра и распечатки данных, копирования, удаления записей по одной и блоками, нумерации переходов и операций;
•обращения к справочникам, базам данных средств оснащения, типовых текстов, нормативов;
•подключения новых справочных информационных массивов;
•формирования архива и работы с ним;
•автоматического формирования технологической документации.
Из перечня выполняемых функций видно, что уровень автоматизации очень низкий, а проектирование – трудоемкий процесс. При данном методе не требуется специальное описание информации о детали. Технолог работает с чертежом детали, как и в случае ручного проектирования, и все решения принимает сам. Данным методом можно получить ТП на любую деталь.
Сущность параметрического метода заключается в разделении функций между ЭВМ и человеком. Технологическое проектирование в этом случае состоит из двух этапов.
Первый этап – ручное проектирование ТП. На этом этапе вручную решаются следующие трудно формализуемые творческие по характеру задачи:
•формирование структуры ТП (технологического маршрута и последовательности переходов в операциях);
•выбор модели оборудования и методов обработки;
•выбор технологических баз, схем установки и типов приспособлений;
•установление размерной структуры ТП и технических требований на расположение поверхностей.
Второй этап – автоматизированное проектирование параметров ТП и отдельных операций. Он начинается с ввода в ЭВМ информации о детали (наименование, материал, твердость, покрытие и т.д.), структуре ТП (номер, наименование операций, переходов), размерной структуре. Затем в автоматическом режиме решаются следующие задачи проектирования:
•расчет припусков на обработку, операционных размеров и допусков на них;
•выбор средств технологического оснащения (режущего, вспомогательного и измерительного инструментов);
•расчет режимов резания и норм времени;
•формирование документации;
•формирование информации для АСУП.
Системы автоматизированного проектирования рассматриваемого типа легко адаптируются к производственным условиям, требуют введения небольшого объема исходных данных и легко воспринимаются технологами.
54
С их помощью можно проектировать ТП для широкой номенклатуры деталей, включая и сложные. Однако эффективность решений в таких системах во многом зависит от квалификации технолога.
Как и в случае прямого документирования, здесь не требуется специальное описание информации о детали. Данные о детали и заготовке, необходимые для выполнения расчетов, вводятся по запросу системы в диалоговом режиме. Системы параметрического проектирования являются автоматизированными системами низкого уровня, с которых целесообразно начинать автоматизацию технологического проектирования. Они помогают быстрее снять так называемый психологический барьер, существующий между технологом и вычислительной техникой, отработать организацию работ на предприятии при проектировании ТП с помощью ЭВМ, создать, отладить
иосвоить базы данных технологического назначения.
Воснову метода использования техпроцессов аналогов положен
принцип заимствования ранее принятых технологических решений. В процессе эксплуатации системы проектирования накапливаются типовые, групповые и единичные технологии, унифицированные операции, планы обработки конструктивных элементов и поверхностей. При формировании текущей технологии пользователю предоставлен доступ к соответствующим архивам и библиотекам, хранящим накопленные решения. Схема автоматизированного получения ТП в этом случае будет следующая: деталь → деталь-аналог → процесс на деталь-аналог → процесс на элемент→ процесс на деталь.
Для нахождения детали-аналога необходимы анализ чертежа детали и определение класса, группы детали по конструктивным и технологическим признакам. Выбор детали-аналога и ТП на эту деталь производится по сформированному коду или текстовому описанию детали. ТП на деталь-аналог подвергается преобразованию на основе информационной модели текущей детали: структура ТП преобразовывается путем исключения лишних структурных элементов ТП (операций, переходов) или внесения необходимых элементов, если в ТП детали-аналога такие элементы структуры отсутствуют. Все эти действия выполняются по методике прямого документирования. Метод аналога чаще применяется при проектировании ТП для деталей типовых форм, отличающихся только размерами (например, одновенцовые зубчатые колеса, валы-шестерни).
Метод требует ввода информации о детали на уровне конструкторскотехнологического кода. Уровень автоматизации низкий, повышается производительность труда технолога, сокращаются сроки и трудоемкость технологической подготовки производства.
Метод проектирования на основе типизации и метод использования аналогов называют также методом анализа или адресации. После ввода описания детали находится технологический процесс на аналогичную деталь или унифицированный ТП на комплексную деталь. Комплексная деталь – это абстрактная деталь, включающая все поверхности деталей, входящих в группу подобных деталей. Далее для формирования индивидуального ТП необходимо организовать вторую процедуру – анализ и доработку найденного аналогичного
55
или унифицированного ТП на комплексную деталь в соответствии с чертежом текущей детали. В методе типизации используются все три уровня унификации обработки, и метод воплощает идею «от общего к частному».
Проектирование на основе унифицированных ТП является основным методом проектирования ТП при эксплуатации гибких производственных систем. Применение этого метода дает наибольший эффект при наличии на производстве групповых и типовых ТП, т.к. метод не нарушает существующей специализации производственных подразделений, упрощает процесс проектирования САПР, не требует трудно формализуемых процедур синтеза новых структур.
Метод синтеза используется для оригинальных деталей. Его нельзя причислить к методам, значительно сокращающим трудоемкость проектирования, но вместе с тем его использование оправдано в случаях изготовления уникальных для данного производства деталей [25]. Базу метода составляют локальные типовые решения. Технологический процесс в целом формируется (синтезируется) из решений частных задач, определяющих элементы ТП. Частные задачи решаются по-разному: в диалоге (автоматизированное проектирование) или по алгоритмам из базы знаний экспертной системы. Это деление определяется уровнем участия человека при принятии решения в процессе проектирования. При диалоговом проектировании технолог все определяющие решения (о структуре и параметрах ТП, операций, переходов, об оборудовании и оснащении) принимает самостоятельно, а ЭВМ оказывает ему методическую, организационную и информационную помощь.
Метод прямого документирования, параметрический и, как видно уже из названия, синтез ТП относятся к группе методов проектирования синтезом. В этих случаях ТП создается, составляется, синтезируется из типовых решений либо с использованием, либо без использования баз знаний.
3.2. САПР подготовки управляющих программ для станков с ЧПУ
Бурное развитие производительных сил, произошедшее в начале XXI века, привело к существенным изменениям в организации производственного процесса не только в нашей стране, но и во всем мире.
Основные черты этих изменений в области применения автоматизированного оборудования с ЧПУ заключаются в следующем:
Во-первых, наблюдается повсеместный переход к использованию многоцелевых обрабатывающих центров (ОЦ) токарной и фрезерной группы, позволяющих довести до максимума концентрацию обработки заготовки на одном рабочем месте. Возможность полной обработки сложных деталей за одну-две операции не только повышает точность получения размеров, но и в разы (это крайне важно!) сокращает длительность производственного цикла изготовления деталей. В результате сократилось потребление станков с ЧПУ в количественном аспекте. Вместо трех или четырех станков с ЧПУ токарной и фрезерной группы приобретается один многоцелевой ОЦ, стоимость которого, правда, вдвое превышает стоимость станка традиционной компоновки.
56
Во-вторых, большие изменения произошли в области инструментальной подготовки производства. С одной стороны, появились фирмы выпускающие высокопроизводительный режущий инструмент, обеспечивающий высокое качество обработки, необходимую стойкость и производительность. С другой стороны, большинство предприятий больше не в состоянии содержать инструментальные цеха для того, чтобы изготавливать собственный режущий инструмент. В результате при расширении типоразмеров и характеристик предлагаемого инструмента соответствующие службы предприятий вынуждены ориентироваться на ограниченный комплект фрез, сверл и резцов, которые заказываются для оснащения конкретного рабочего места. При этом используемые БД инструмента на этих рабочих местах становятся менее универсальными и разнообразными. Зато каждому инструменту можно смело поставить в соответствие оптимальные с точки зрения производительности (а при желании — с точки зрения экономичности) режимы резания. Это дает возможность формализовать выбор режимов резания при использовании CAD/ CAM-систем.
В-третьих, изменения коснулись и возможностей конструкторскотехнологического проектирования. Повсеместно происходит переход от использования 2D-моделей к 3D-моделям деталей и сборок. Соответственно расширяются возможности 3D-моделирования. Это касается вопросов не только расчета УП для 4- и 5-осевых станков, но и формирования алгоритмов обработки отдельных конструкторско-технологических элементов (КТЭ). Рассматривается возможность представления 3D-модели детали как совокупности КТЭ по принципу модульной системы. Дело остается только за разработкой стандартов, описывающих структуру КТЭ, включая требования к точности и шероховатости поверхностей.
Подводя итоги всему вышесказанному, можно сделать простые, но важные выводы:
количество автоматизированных станков и применяемой технологической оснастки на производстве постепенно сокращается;
САПР технологического назначения достигли уровня, позволяющего полностью формализовать процесс обработки, чего раньше не удавалось.
Эти выводы позволяют сформулировать новые требования к структурному содержанию CAM-систем, отвечающие современным производственным условиям.
На рис. 3.1 показана структурная схема работы традиционной CAMсистемы. Общим для традиционных систем является то, что пользовательтехнолог в интерактивном режиме подбирает для каждого перехода объект обработки (формирует КТЭ) и средства обработки (выбирает режущий инструмент, стратегию и режимы обработки). В результате формируется файл CLDATA, содержащий информацию о траектории движения инструмента и месте ввода технологических команд. Эта информация является, по сути, универсальной и уже в дальнейшем преобразуется в NC-коды конкретного станка в ходе работы блока «постпроцессор». В свое время ориентация на такие «инвариантные» постпроцессоры была весьма прогрессивной, так как
57
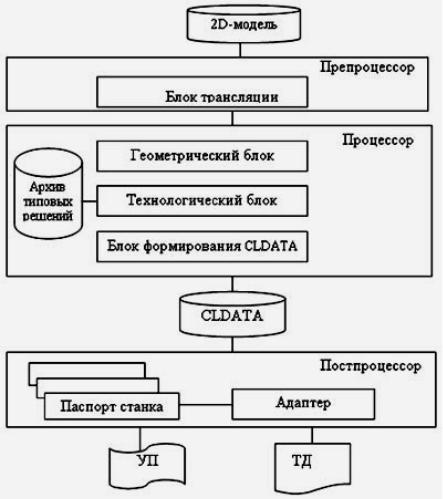
позволяла использовать одни и те же исходные данные о траектории для различных станков с ЧПУ. И в настоящее время такой подход является эффективным, если применяемые станки обладают близкими технологическими возможностями.
Но ситуация в производственной сфере предприятия изменилась. Правильно ли в данных условиях уповать на универсальность информации
вCLDATA? Ведь заранее известно, что данная обработка предназначена для определенного станка? Поэтому необходимо расширить возможности блока «процессор», встраивая в него конфигурации, учитывающие специфику имеющегося станка. При этом можно использовать представление о детали как о совокупности объемных конструкторско-технологических элементов (КТЭ), для каждого из которых имеется алгоритм обработки. Выбирая нужную конфигурацию процессора, можно использовать настройки, характерные для конкретного станка, включая особенности применяемого инструмента и возможности использования для программирования станочных циклов обработки. Учитывая высокую стоимость одного часа работы многофункционального станка, следует особенно тщательно проектировать операционную технологию, моделировать
в3D все компоненты технологической системы, выполнять проверку на соударение и использовать элементы групповой обработки.
Рис. 3.1. Структурная схема традиционной CAM-системы
58
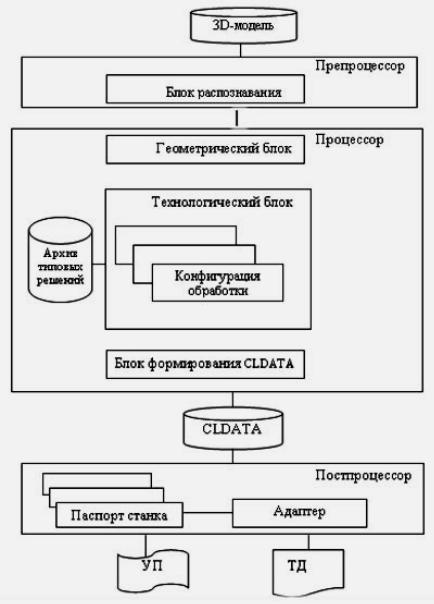
Новая структурная схема организации CAM-системы представлена на рис. 3.2. Отличия в предложенной структуре CAM-системы касается двух взаимосвязанных направлений:
стандартизация данных о детали на основе формализации параметров КТЭ;
создание конфигураций обработки, предназначенных для отдельных рабочих мест (или групп подобных рабочих мест).
Рис. 3.2. Структурная схема CAM-системы на основе автоматизации обработки КТЭ
Второе направление означает, что на этапе процессора вводятся ограничения на функциональность применяемого оборудования. Известно, что сверление с использованием приводного инструмента на 4-осевом токарном ОЦ и сверление на ОЦ обычной компоновки — это не одно и то же. Это касается и моделирования, и получения NC-кода. Конфигурации обработки должны учитывать применяемый режущий и вспомогательный инструмент.
59
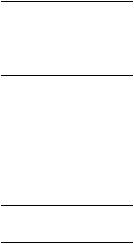
Зачастую этот инструмент приобретается специально для конкретного рабочего места (станка) и не может использоваться для других станков. Введение конфигураций обработки позволит применять в рамках проектирования в CAM высокоскоростного фрезерования именно для тех станков, которые для этого предназначены. В результате для постпроцессирования остаются задачи расчета NC-кода, визуализации обработки и проверки соударений, а также окончательного расчета времени обработки. Примером такой системы может служить решение FeatureCAM фирмы Delcam, представленные в таблице 3.1.
|
Решение FeatureCAM фирмы Delcam |
Таблица 3.1 |
||
|
|
|||
|
|
|
|
|
|
Операции |
Уровень использования в составе: |
||
|
|
традиционных |
|
|
№ |
Задачи технологической |
CAD/CAM-систем |
CAD/CAM-систем |
специализированных |
п/п |
подготовки производства, |
на основе автома- |
на основе автома- |
САПР технологиче- |
|
решаемые в системе авто- |
тизации техноло- |
тизации обработки |
ского назначения |
|
матически |
гических перехо- |
КТЭ |
|
|
|
|||
|
|
дов |
|
|
|
Считывание информации о |
|
|
|
1 |
детали в 3D-виде из элек- |
+/– |
+ |
+ |
|
тронной модели |
|
+ |
|
2 |
Распознавание КТЭ |
– |
+/– |
|
3 |
Разработка технологическо- |
– |
– |
+/– |
|
го маршрута |
|
|
|
4 |
Разработка операционной |
– |
+ |
+/– |
|
технологии |
|
|
|
|
Ведение (оформление и из- |
|
|
|
5 |
менение) технологической |
+/– |
+/– |
+ |
|
документации |
|
|
|
6 |
Расчет траектории движе- |
+ |
+ |
– |
|
ния инструмента |
|
|
|
7 |
Формирование управляю- |
+ |
+ |
– |
|
щих программ |
|
|
|
Примечание: + — задача полностью решена в компьютерной среде;
– — решение задачи в компьютерной среде отсутствует; +/– — задача частично решена в компьютерной среде.
Разработка технологического маршрута включает:
выбор поверхностей для черновых и чистовых баз;
расчет припусков на обработку;
расчет технологических размерных цепей;
выбор оборудования;
проектирование приспособлений для закрепления заготовки или выбор из существующих;
выбор средств контроля обработанных поверхностей;
прогнозирование трудоемкости обработки.
Разработка операционной технологии заключается в следующем:
60