
[elib.tsogu.ru]_kompjuternye-tekhnologii...83-a5 (2)
.pdfмониторинг, проведение постоянного анализа соответствия процессов и изделия запланированным показателям. Что касается описания процессов, то для этого в системе присутствует модуль динамического моделирования предприятия, который позволяет, еще до начала внедрения системы, описать все необходимые процессы предприятия.
Источником всех данных об изделии является PDM-система (Product Data Management – система управления данными об изделии), которая аккумулирует данные об изделии и информационных процессах его жизненного цикла.
На уровне высшего менеджмента предприятия должны работать OLAPсистемы (On-Line Analytic Processing – оперативный многомерный анализ данных) и DM-системы (Data Mining – интеллектуальный анализ данных).
Аналитическая обработка в реальном времени (OLAP) – это технология обработки информации, включающая составление и динамическую публикацию отчетов и документов. OLAP используется аналитиками для быстрой обработки сложных запросов к базе данных. С помощью подобных систем менеджеры, обеспечивающие принятие решений, могут просматривать и анализировать данные именно в том виде, который для них наиболее удобен, агрегировать и детализировать информацию, получать промежуточные итоги, использовать графическое представление информации, а также выпускать отчеты, необходимые руководству предприятия для принятия решений, основанных на фактах в соответствии с принципом менеджмента качества ИСО 9000.
Технологии интеллектуального анализа данных (Data Mining) могут быть использованы при исследовании проблем качества продукции, процессов и подготовке оптимальных решений. Основное назначение этой технологии — автоматизированный поиск (выявление ранее неизвестных) функциональных и логических закономерностей в многомерном хранилище, использование выявленных закономерностей для прогнозирования (интерполяции и экстраполяции) требуемых данных. Методы (Data Mining) разделяются на статистические (дескриптивный анализ, корреляционный и регрессионный анализ, факторный анализ, дисперсионный анализ, компонентный анализ, дискриминантный анализ, анализ временных рядов) и кибернетические (искусственные нейронные сети, эволюционное программирование, генетические алгоритмы, ассоциативная память, нечеткая логика, деревья решений, системы обработки экспертных знаний).
4.6.Контрольно-измерительные машины
Вусловиях современного производства в таких отраслях, как общее машиностроение, авиационная, аэрокосмическая и медицинская промышленность, требования к точности и скорости измерений непрерывно повышаются. По этой причине возрастает роль измерительных средств, точность
которых должна быть на порядок выше, чем допустимая погрешность. В соответствии с этими тенденциями в последние годы наблюдается стремительное развитие конструкций и технических возможностей координатноизмерительных машин (КИМ).
101
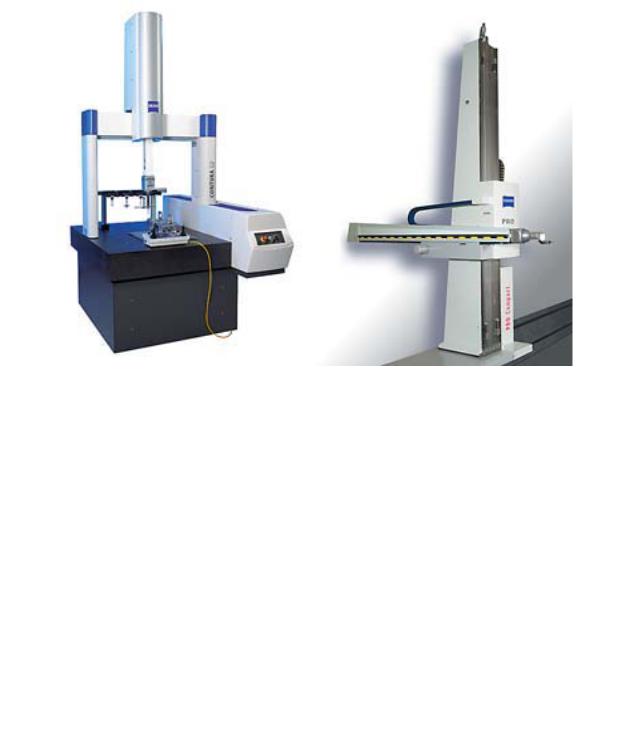
Несмотря на разнообразие моделей КИМ, их можно сгруппировать по типам исполнения:
1.3D-портальные (рис. 4.4 а).
2.Стоечные (рис. 4.4 б).
3.Шарнирно-сочлененные КИМ типа «рука» (рис. 4.5 а).
4.Шестиосевые на основе платформы Стюарта (рис. 4.5 б).
5.Фото- и рентгенографические (рис. 4.6).
6.Лазерные дальномеры с объемным сканированием (Laser Tracker) (рис. 4.7).
аб
Рис. 4.4. Координатно-измерительная машина: а) 3D-портальная, б) стоечная
Непременные требования ко всем измерительным машинам — точность и быстрота измерений, адаптируемость к условиям реального производства, простота в обучении персонала и эксплуатации КИМ. Одними из самых точных — ввиду хорошей сбалансированности конструкции и традиционной кинематики — являются установки портального типа.
По количеству выпускаемых КИМ в Европе несомненное лидерство остается за фирмой Carl Zeiss IMT GmbH (г. Оберкохен, Германия). Среди измерительных машин портального и стоечного типов, выпускаемых этой компанией, особый интерес по соотношению «цена-качество», пожалуй, представляет серия CONTURA G2, которая выпускается в трех вариантах исполнения.
102
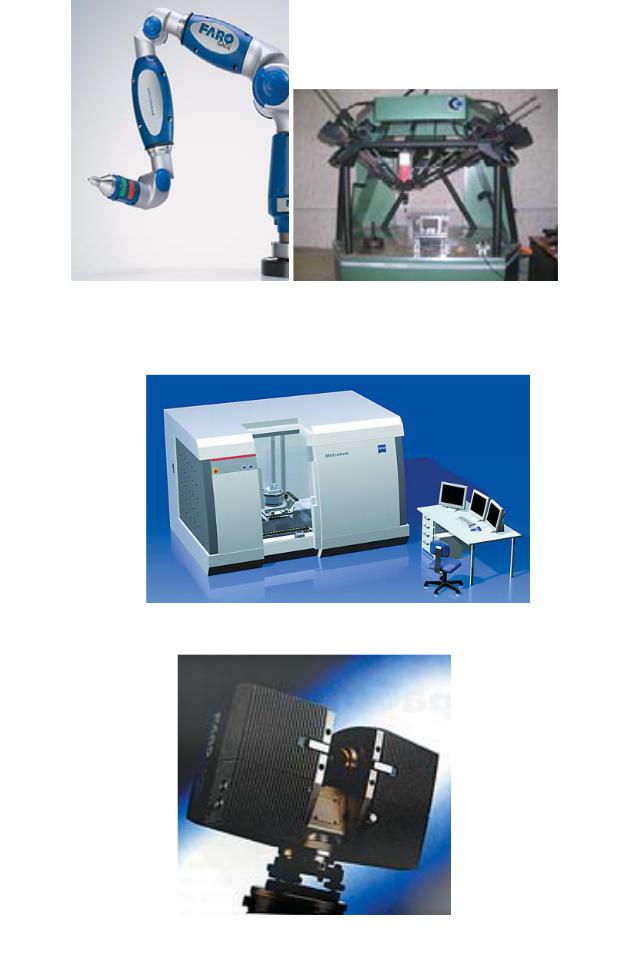
а |
б |
Рис. 4.5. Координатно-измерительные машины:
а) шарнирно-сочлененная типа «рука», б) на основе платформы Стюарта
Рис. 4.6. Рентгенографическая координатно-измерительная машина
Рис. 4.6. Лазерный дальномер с объемным сканированием
103
Модель CONTURA G2 Activ оснащена измерительной головкой активного сканирования VAST XT (патент Carl Zeiss), позволяющей получать результаты измерений формы и положения. Максимальная длина щупа
— 500 мм, что позволяет проводить измерения корпусных деталей с глубоко расположенными элементами.
CONTURA G2 RDS имеет поворотную головку RDS, пассивный сканирующий датчик VAST XXT или бесконтактный оптический датчик ViScan. Поворотная головка способна выполнять разворот вокруг двух взаимно перпендикулярных осей в диапазоне углов ±180° с дискретностью 2,5°. Такая конфигурация сенсорики позволяет проводить измерения элементов во множестве различных угловых положений, а также в деталях с большим количеством отверстий.
CONTURA G2 Direct оснащена пассивным сканирующим датчиком VAST XXT, установленным без поворотной головки. Область применения — контроль небольших деталей с несложной геометрией.
Вцелом серия CONTURA G2 имеет пять типоразмеров со следующими диапазонами максимальных измерений по осям Х: 700–1000 мм; Y: 700–2100 мм; Z: 600 мм. Погрешность линейного измерения при температуре окружающей среды от +18 до +22 °С составляет МРЕ 1,8 мкм + L/300 по ISO 10360, а с опцией HTG температурный диапазон измерений расширяется до показателей от +18 до +26 °С.
Стол и направляющая по оси Y в КИМ CONTURA G2 изготовлены из специального гранита, а направляющие по X и Z изготовлены из специального керамического материала. Портал перемещается на воздушных подшипниках.
Вкачестве программного обеспечения (ПО) в CONTURA G2 используется пакет CALYPSO Software с русскоязычным интерфейсом на базе CAD. Он позволяет составлять и модифицировать программы измерительных операций с визуальной метрологией, оптимизировать последовательность операций, получать высокую производительность для разнообразной сенсорики, использовать разнообразные программные функции, формулы и параметры. Дружественный русскоязычный интерфейс облегчает работу оператору.
Компанией Carl Zeiss также выпускается измерительный комплекс METROTOM, который позволяет в автоматизированном режиме осуществлять технологию метротомографии. При ее использовании измеряемая деталь помещается в поле слабого рентгеновского излучения, затем ее рентгеновское изображение фокусируется на специальном экране-приемнике и запоминается в памяти компьютера. Далее деталь поворачивается на небольшой угол, и процесс повторяется до тех пор, пока она не сделает полный оборот. Полученный трехмерный массив данных, содержащий информацию о детали, обрабатывается компьютером, визуализируется на экране монитора и содержит полную информацию о геометрии наружных поверхностей, а также о внутренней структуре (имеющихся трещинах, раковинах, пористости). Результаты исследования распечатываются в виде протокола измерений. Установка соответствует директивам радиационной безопасности согласно DIN 54113 для полностью защищенных приборов этого типа.
104
С помощью комплекса METROTOM можно выполнять следующие операции:
измерения размеров в диапазоне 300x300x300 мм;
сравнение геометрии изделий;
обратный инжиниринг;
анализ повреждений и дефектов;
анализ пористости;
контроль сборки.
Тенденция к миниатюризации многих изделий в таких отраслях, как робототехника или имплантология в медицине, привели к расширению производства микрокомпонентов. По этой причине возрастает потребность в повышенной точности изделий малых размеров, в разработке методик проверки геометрии микродеталей, причем выпускаемых довольно большими партиями. Уменьшение размеров и допусков приводит к более жестким техническим требованиям к измерительным машинам и их сенсорике. Идя навстречу этим тенденциям, фирма Carl Zeiss разработала машину F25 для измерения микрокомпонентов. Расположение ее осей позволяет соблюдать принцип Abbe comparator на уровне измерительного стола. Оси установлены на аэростатических подшипниках и оборудованы линейными приводами. Машина оснащена одним тактильным и одним оптическим датчиком (камерой слежения). Высокая чувствительность обеспечивается пьезоэлектрическим принципом работы датчика с малым измерительным усилием, исключающим повреждение измеряемой микродетали. Оптическая камера облегчает работу оператора при малых размерах детали и щупа. В качестве программного обеспечения используется метрологический программный пакет CALYPSO.
Для изготовлении высокоточных медицинских деталей, например, имплантантов для суставов, внутривенных катетеров, а также отдельных видов хирургических инструментов, где качество измерений играет особую роль, применяются новые специализированные КИМ, с CAD-моделированием и программным обеспечением CAM 10 Studio. При двухкоординатном контроле оптически проверяют качество изготовления поверхности искусственных суставов, при трехкоординатном — соблюдение заданных размеров.
Однако по технологии производства не всегда нужна микронная точность и не всегда есть возможность использования стационарных КИМ. К примеру, при изготовлении кузовов легковых автомобилей из штампованных элементов неточность готовых деталей может составлять до нескольких миллиметров, а сам процесс сборки требовать периодического контроля непосредственно на месте. Поэтому в сегменте измерительных систем появились мобильные координатно-измерительные машины, обладающие универсальными возможностями, автономностью, простотой в эксплуатации и обучении работе с ними — и притом с более низкой, чем у портальных установок, стоимостью. Таким оборудованием можно проводить 3D-контроль в диапазоне от 0 до 70 м с точностью от ±5 до ±176 мкм. К их числу относятся шарнирно-сочлененные измерительные машины (типа «рука») в 6- и 7-осевом исполнении, а также устройства типа Laser Tracker (лазерныеКИМ).
105
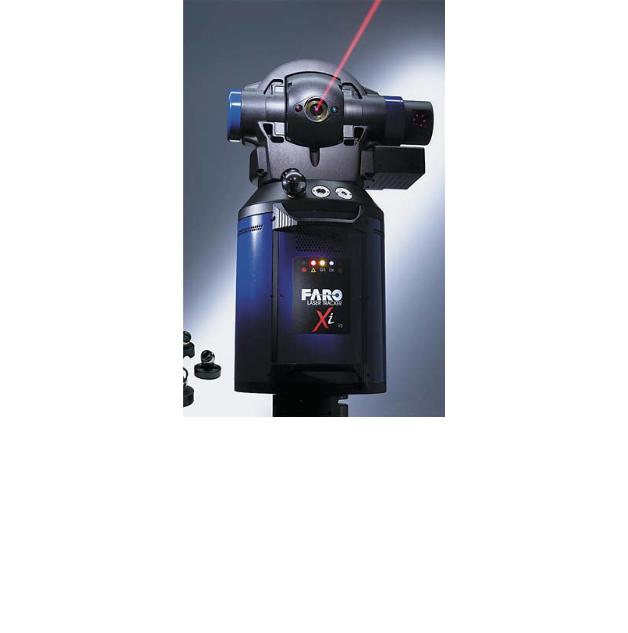
Лидером в производстве мобильного координатно-измерительного оборудования, занявшим на сегодняшний день около 80 % мирового рынка, является фирма FARO Technologies Inc. (США). Например, ее модель Quantum FaroArm позволяет проводить измерения с точностью ± 0,025 мм, Gage Plus — 0,006 мм.
Применяемая фирмой технология Faro ScanArm предусматривает соче-
тание датчика Laser Line Probe (LLP) c кинематикой FaroArm рис. 4.7, таким образом, получается бесконтактный метод контроля с точностью от ±53 мкм.
В случае использования бесконтактного метода с лазерной головкой LLP V 3 либо контактного метода с жесткими щупами, оборудование FARO оказывается удобно использовать как для контроля, так и для реинжиниринга производства. Оборудование компании широко применяется в аэрокосмической, автомобильной, судостроительной промышленности — для измерения линейных и угловых размеров, контроля формообразующих поверхностей крупногабаритных изделий с точностью от ±11 мкм.
4.7. Бесконтактная координатно-измерительная машина.
Из украинских фирм, предлагающих 3-координатные измерительные машины, только ЧП «СпецМаш» поставляет оборудование собственного изготовления, причем с очень выгодным для отечественных предприятий соотношением «цена-качество». Компания выпускает разнообразные модели КИМ — от настольных, потребителем которых являются метрологические службы заводов, до машин, предназначенных для работы непосредственно в производственных цехах. Диапазон их измерений по осям: X — 320–600
мм, Y — 320–650 мм, Z — 270–450 мм.
106
Благодаря качеству обработки основных деталей, получаемых из специального гранита, достигается высокая точность конструкции машин в целом. Применение аэростатических подшипников и сбалансированной кинематики на моделях КИМ 550-Р, КИМ 550-М (А), КИМ 330-РМ позволяет сохранять высокую жесткость и идеальную ортогональность системы координат на протяжении всего срока эксплуатации. В программном обеспечении применена система САА (Computer Aided Accuracy) — компьютерная корректировка ошибок кинематики, что позволяет выдавать точные результаты измерений.
Представленные возможности некоторых ведущих производителей измерительных машин доказывают, что совершенствование КИМ ведется по пути развития точности и скорости измерений, внедрения новых систем сенсорики и адаптроники, реализации концепции открытой архитектуры в программном обеспечении, позволяющей импортировать файлы САПР и формировать программы линейных измерений, создавать единую мультисенсорную измерительную систему с простым и понятным оператору интерфейсом.
Контроль изготовленных деталей по-прежнему является важным процессом обеспечения качества. Технологии контроля качества за последние несколько лет претерпели существенные изменения, как в сфере используемого оборудования, так и программного обеспечения. Зонды и сканирующее оборудование теперь способны гораздо быстрее собирать данные. Основным средством точного измерения остаются координатно-измерительные машины. Однако для их работы необходимы специальные программы контроля каждого компонента, а сложная геометрия деталей требует создания многоосевых траекторий движения зонда для эффективного измерения в единой структуре производства.
Подготовка таких программ контроля обычно выполнялась как отдельная задача, независимая от процесса управления жизненным циклом изделия. За основу часто брались чертежи. При таком сценарии результаты достигаются медленно, высока вероятность ошибок и ограничены возможности обратного отслеживания проекта, производственной модели и данных. Во время внесения изменений в проект может возникнуть несогласованность
спрограммой контроля из-за ее отставания.
Вэтом пособии мы рассмотрим новое приложение от компании Siemens, предназначенное для подготовки усовершенствованных программ машинного контроля. Данное приложение автоматически создает программы
контроля, используя производственную информацию об изделии (PMI) из моделей CAD. Для полной проверки алгоритма и создания готовой программы используются новейшие методы 3D-моделирования.
К созданию нового приложения специалистов компании Siemens PLM Software подтолкнуло несколько факторов. Во-первых, новейшие технологии высокоскоростного зондирования и сканирования позволяют собирать данные в 10–100 раз быстрее, чем прежде. Это позволяет выполнять не только больше измерений за единицу времени, но и гораздо более сложные измерения. Такие системы невозможно программировать вручную или в режиме «обучения», поэтому возникает особая потребность в средствах
107
программирования, работающих в автономном режиме. Серьезной проблемой для программистов в области контроля является то, что методы, используемые сегодня при создании таких сложных программ, слишком дороги и требуют большого количества времени.
Специалисты Siemens PLM Software также заметили, что все большее число клиентов переходит на использование полностью трехмерных определений изделий в САПР. Помимо геометрии деталей, это касается и всех производственных данных, которые сохраняются в виде производственной информации об изделии (PMI), вложенной в 3D-модель. Для использования
вцелях контроля эти данные могут включать сведения о допусках, например для размеров и положения физических элементов относительно общей геометрии. Если при использовании инструментов в последующих процессах можно воспользоваться преимуществами наличия всех необходимых данных
впроектируемой модели, то увеличивается вероятность того, что контроль выявит выполнение требований к изделию не только с точки зрения геометрии, но и с точки зрения производства.
Другой проблемой является изолированность процессов программирования координатно-измерительных машин, выполнения программ контроля и сбора данных от процессов проектирования и производства. Пользователи хотят, чтобы все перечисленные операции были интегрированы в общий рабочий процесс управления жизненным циклом изделия, а данные сохранялись в системе управления разработкой изделий. Также необходимо, чтобы системам измерения были доступны заданные программы контроля непосредственно из системы управления разработкой изделия (PDM). Кроме того, после сбора всех данных измерений необходима возможность передачи их обратно в PDM-систему для последующего использования технологами производства и конструкторами.
Внастоящее время программные продукты PLM Software компании Siemens обладают уникальными новаторскими технологиями в области решений для программирования координатно-измерительных машин, позволяющими в значительной степени автоматизировать процесс и интегрировать его
вобщую инфраструктуру системы управления жизненным циклом изделия. Новый подход к созданию программ для координатно-измерительных
машин Программа NX CMM Inspection Programming представляет собой новый модуль системы NX 7.5. Он полностью интегрирован в систему NX, поэтому пользовательский интерфейс выглядит так же, как в любом другом приложении NX, что является несомненным преимуществом для постоянных пользователей системы. Новые пользователи NX также оценят усовершенствования и графические средства взаимодействия с моделью, которые компания Siemens реализовала в новой версии, сделав работу в системе еще более удобной.
Специалисты Siemens решили встроить новую программу контроля для координатно-измерительных машин в NX, поскольку эта система полностью основана на 3D-моделях и обладает всеми средствами САПР для работы с геометрией, создания данных PMI и их интеграции. В NX также представлена проверенная технология, которая может применяться при создании
108
программ контроля для моделирования работы машин. Основная цель создания нового приложения заключалась в обеспечении высокого уровня автоматизации и программирования на основе PMI-данных модели.
Работу можно начать с выбора целевой координатно-измерительной машины (так же, как это делает программист станка с ЧПУ в системе NX CAM). Для этого нужно выбрать предустановленный шаблон процесса контроля из библиотеки, размещенной рядом с библиотеками шаблонов других приложений NX. Деталь, подлежащая контролю, переносится в систему NX (в системе предусмотрено множество преобразователей моделей для форматов, отличных от NX) и помещается на стол контроля целевой координатноизмерительной машины.
В первоначальной версии программы поддерживается 3-осевое сканирование и 5-осевое измерение с использованием датчика касания. По информации Siemens, следующие версии будут поддерживать также и одновременное 5-осевое сканирование. На этом этапе программа проявляет одну из самых впечатляющих своих функций. Компания Siemens PLM Software разработала уникальную функцию, названную Link PMI. Небольшая кнопка в верхней строке меню позволяет быстро выполнять огромный набор задач. Команда Link PMI фактически берет трехмерную геометрию детали
исвязанные с моделью данные PMI, извлекает заданные характеристики и допуски и создает необходимые операции контроля. Все эти действия выполняются при помощи нажатия одной кнопки! Достаточно открыть каталог информации, чтобы увидеть, что вместо пустой структуры, импортированной из шаблона, мы имеем заполненную структуру контрольных характеристик, данных и операций контроля, полученных программой из модели детали
ипреобразованных в программу контроля. Траектории контрольноизмерительной машины создаются на основе типов контрольных характеристик и связанных с ними данных PMI. Компания Siemens использует предварительно заданные шаблоны для сохранения данных контроля. Эти шаблоны
создают основу для автоматического вычисления траекторий контроля на основании типов характеристик.
Для некоторых деталей, в моделях которых доступны данные PMI, выполнение команды Link PMI позволяет экономить от 80 до 90 % времени, которое тратится на программирование с использованием традиционных средств. Конечно, в случае работы с деталями, которые не содержат данные PMI, когда имеющихся данных недостаточно или программист хочет добавить в программу дополнительные измерения, можно воспользоваться меню, в котором предоставлены все операции ручного создания программы.
Можно выбрать один из множества предварительно заданных методов контроля, а затем указать точки или характеристики на 3D-модели. После этого система NX создаст необходимую траекторию.
После создания программы контроля система NX CMM может вывести ее в формат, воспринимаемый программным обеспечением координатноизмерительной машины. Достаточно просто выбрать необходимый постпроцессор для создания инструкций в формате DMIS (Dimensional Measurement
109
Interface Specification) или на встроенном языке программирования, например GeoMeasure или Calypso. Однако прежде чем отправлять программу
вцех, ее рекомендуется проверить, чтобы убедиться в правильности операций контроля и отсутствии пересечений траекторий. При создании сложных программ такая проверка может понадобиться и в процессе создания программы, когда требуется внести изменения.
Для решения этой задачи компания Siemens предусмотрела алгоритмы многоуровневой проверки траекторий инструмента и моделирования работы машины. Система NX CMM поставляется в комплекте с множеством моделей стандартных координатно-измерительных машин. Можно импортировать 3D-модели машин или создавать собственные в системе NX CAD. Модуль создания станков позволяет добавлять в модели координатно-измерительных машин необходимую кинематику и пределы движений. Моделирование работы основано на инструкциях DMIS и позволяет видеть в точности то, что будет использовано в цехе.
Поскольку приложение для контроля программирования координатноизмерительных машин входит в состав системы NX, оно обладает всеми преимущества интеграции с PDM-системой Teamcenter, которая является основой PLM-решения от компании Siemens. Данные контроля автоматически сохраняются в Teamcenter в разделах операций контроля. Пользователям системы Teamcenter доступны функции сохранения шаблонов, инструментов, зондов и правил контроля, а также программ контроля и файлов вывода, связанных с соответствующей версией детали.
Возможность управления данными контроля и связывания их с основными записями данных о детали позволяет решать одну из важнейших задач производства. Эта задача заключается в обеспечении совпадения геометрии CMM с проектной моделью и используемой производственной геометрией. Система Teamcenter может передавать последующим процессам информацию об изменениях, которые могут повлиять на эти процессы. Ассоциативные связи внутри системы NX также играют в этом немаловажную роль, упрощая процесс обновления связанных моделей деталей в случае изменения первоначального проекта. Позиционирование системы CMM в общей структуре производственного решения.
Компания Siemens ожидает внедрения приложения NX CMM Inspection Programming на многих предприятиях. Небольшие предприятия, приобретающие, как правило, одну лицензию на использование системы NX CAM или NX для проектирования инструментов, оценят преимущества расширения возможностей при использовании той же системы и тех же моделей. У более крупных компаний, использующих расширенные системы, появится возможность более глубокой интеграции процессов управления качеством
вобщий процесс управления жизненным циклом изделия, воспользовавшись преимуществами интеграции с Teamcenter. Поэтому компания Siemens представляет новое приложение как часть производственного решения, расширяющего возможности системы NX в виртуальной среде, вместе с системами NX для программирования станков с ЧПУ, NX для подготовки моделей деталей
110