
61.06 ЗХТ лекції
.pdfвилуговування, полімеризація в середовищі рідких мономерів із утворенням твердих полімерів, поліконденсація в рідкій фазі з утворенням твердих високомолекулярних продуктів, коагуляція в колоїдних системах, диспергування твердих частинок у рідині, адсорбція розчинених у рідині речовин та їх десорбція, іонний обмін між рідинами та іонообмінними смолами тощо.
Більшість процесів у системі Р-Т відбувається у дифузійній області, тому в реакторах використовують різні способи їх інтенсифікацій зокрема, збільшення відносної лінійної швидкості руху фаз (перемішування) і збільшення площі поверхні контакту фаз (подрібнення твердої сировини, застосування пористого твердого матеріалу).
Реактори для здійснення процесів у системі Р-Т поділяють залежно від того, як інтенсифікують процес* на такі, в яких:
1.забезпечується висока лінійна швидкість рідини відносно твердої фази
2.відбувається перемішування системи Р-Т.
Реактори першого типу охоплюють апарати з фільтрувальним шаром і
з псевдозрідженим (“киплячим шаром ”) твердого матеріалу.
Реактори з фільтрувальним шаром - це циліндричні апарати, в нижній частині яких горизонтально або похило встановлена ситоподібна чи ковпачкова тарілка. На тарілці розміщений шар пористого твердого матеріалу, через який пропускають рідину. Чим більша пористість твердого матеріалу, тим більша величина міжфазової твердої поверхні. Головний опір дифузії рідкого компонента створюють внутрішні канали пор, тобто у системі Р-Т процеси переважно відбуваються у внутрішньодифузійній області.
За гідродинамічним режимом ці апарати наближаються до реакторів ідеального витіснення, за тепловим режимом - адіабатичні.
Для підвищення ефективності процесу використовують батареї (каскади) реакторів з фільтрувальним шаром, які називають дифузорами.
Реактори з фільтрувальним шаром мають такі переваги: простота конструкції, стабільність технологічного режиму, низькі енерговитрати. Головним недоліком цих реакторів є низька інтенсивність роботи.
Реактори з псевдозрідженим шаром твердого зернистого матеріалу в рідині застосовують тоді, коли рідкий і твердий реагенти істотно відрізняються за густиною, а зерна мають великі розміри. Конструкція такого апарата є аналогічною до апарата для реалізації процесів у системі Г-Т.
5.3. Реактори для каталітичних процесів – гетерогенний каталіз
Гетерогенні каталітичні процеси (як газо-, так і рідкофазові) зазвичай здійснюють з використанням твердих каталізаторів у реакторах, які ще називають контактними апаратами (КА). До контактних апарати ставлять
такі вимоги: безперервний режим роботи, висока інтенсивність роботи, забезпечення оптимального (особливо температурного) режиму процесу,
71
мінімальний гідравлічний опір, простота конструкції й легкість обслуговування.
Каталітичні реактори класифікують за фазовим станом реагентів і каталізатора, способом контакту між реагентом і каталізатором, конструктивним виконанням теплообмінних пристроїв.
За фазовим станом реагентів і каталізатора каталітичні реактори поділяють на чотири групи.
1)Реакційне середовище - газ; каталізатор - твердий:
• КА поверхневого контакту;
• КА з фільтрувальним (нерухомим) шаром каталізатора;
• КА із псевдозрідженим (киплячим) шаром каталізатора;
• КА з рухомим каталізатором.
2)Реакційне середовище - рідина; каталізатор - твердий:
• реактори з нерухомим каталізатором;
• реактори із псевдозрідженим (киплячим) шаром каталізатора;
• реактори з потоком завислих частинок каталізатора в рідині;
• реактори з мішалками.
3)Реакційна система: газ-рідина; каталізатор - рідина або суспензія (завислі частинки каталізатора у рідині):
• плівкові насадкові колони;
• барботажні колони;
• реактори з мішалками.
4)Реагуючі речовини - рідини, що не змішуються; каталізатор - рідина: реактори з мішалками.
Більшість промислових каталітичних реакторів належить до групи І Найбільш поширеним типом реакторів є реактори з нерухомим шаром
каталізатора. Для адіабатичного режиму каталізатор у вигляді часток різної форми засипають в апарат(а). Характерний розмір часток(зерен) каталізатора складає 3-8 мм Шар розташовується на жорстких опорних гратах, що витримують масу каталізатора і перепад тиску в шарі. Маса завантаженого каталізатора може складати тонни і навіть десятки тонн у великотоннажних виробництвах(сірчаної кислоти, аміаку).
Щоб дрібні зерна каталізатора не провалювалися і не закривали отвори в опорних гратах, на неї зазвичай насипають тонкий шар крупнокускового матеріалу, а згори – каталізатор.
Каталізатор насипають "в навалювання", після чого потрібно ретельне вирівнювання шару для забезпечення рівномірного проходження через нього реакційній суміші.
Використання варіанту адіабатичного реактора часто призводить до великих перепадів температур по висоті каталітичного шару і істотного відхилення середньої температури від її оптимального значення. Для того, щоб наблизити температурний режим до оптимального використовуються багатотоннажні(багатосекційні) реактори, в яких вирівнювання температурного
72
режиму здійснюють зніманням або підведенням тепла за допомогою теплообмінних пристроїв між секціями або шляхом подання між секціями захоложенного або перегрітого реагенту(компонента) (б, в).
Часто потрібне відведення тепла безпосередньо з реакційної зони. З цією метою використовують реактори типу кожухотрубних теплообмінників - універсальний тип каталітичного реактора(г). Зазвичай в трубки завантажують каталізатор, а в міжтрубний простір поступає теплоносій. Якщо необхідно знімати тепло, то в міжтрубний простір знизу поступає конденсат, а згори відводиться водяна пара. У іншому варіанті в міжтрубному просторі циркулює сольовий розплав - нитрит-нитратная суміш - NaNO3 - NaNO2 - KNO3. Закумульоване їм тепло далі використовується для генерування водяної пари. Діаметр трубок зазвичай невеликий, оскільки об'єм тепла лімітується теплопровідністю в каталітичному шарі і при великому діаметрі слід чекати високих градієнтів температур по перерізу каталітичного шару.
Для забезпечення теплотою ендотермічних процесів використовують гарячі димові гази. У останньому випадку реактор є трубчастою піччю(д). Відводити тепло реакції можна не лише теплоносієм, але і свіжій реакційною сумішшю.
Інша група реакторів - із зваженим(киплячим) або висхідним шаром каталізатора. При поданні реакційної суміші знизу шару з достатньою швидкістю тверді частки витатимуть в повітрі, не відносячись з ним (е); в цьому випадку застосовують частки не більше за 1 мм Це забезпечує повне використання їх внутрішньої поверхні. Циркулюючі частки вирівнюють температуру в шарі - процес в ньому протікає практично ізотермічно. Інтенсивний рух часток забезпечує хороший тепловідвід - коефіцієнт тепловіддачі від киплячого шару більш ніж на порядок перевищує такий від нерухомого шару. Рухливість каталітичного шару дає можливість організувати течію твердих часток через реактор, що істотно для процесу з активністю каталізатора, що міняється. Завдяки цьому можна організувати безперервний транспорт його із зони реакції в зону регенерації і назад. В цілому така система "Реактор - регенератор" забезпечує безперервність процесу в цілому. Такий тип реакційного вузла можна організувати в процесі каталітичного крекінгу нафтопродуктів, в якому каталізатор швидко закоксовується, втрачаючи свою активність. Його безперервно виводять з реактора в регенератор (ж), де відбувається "випалювання" коксу і відновлюється активність каталізатора.
При організації псевдозрідженого шару частина газу проходить шар у вигляді пухирів. Коефіцієнт массопередачи між пухирями і іншою частиною шару невисокий - фактично утворення пухирів газу - це утворення байпасних потоків. Це небажане явище, оскільки в пухирях реация не йде і це в цілому знижує продуктивність. Усувається це явище шляхом розбиття пухирів. Це здійснюється спеціальною массообменной насадкою, наприклад, у вигляді дротяних спіралей. Інший спосіб змусити працювати пухирі - додати в
73
каталізатор дуже дрібну фракцію. Такий катализаторная "пил" потрапляє в пухирі, де частково протікатиме реакція.
Циркуляція часток в псевдозрідженому шарі викликає стирання каталізатора. Для очищення газу від пилу після реактора встановлюють циклони.
Якщо швидкість газового потоку буде такою, що тверді частки захоплюватимуться їм, то реалізується режим пневмотранспорта (з) і реакція у висхідному потоці каталізатора. Така організація процесу ефективна для швидких реакцій - оскільки час проходження реакційної суміші в довгому вузькому реакторі невеликий. Теплота реакції йде не лише на нагрів(охолодження) реакційної маси, але і на нагрів(охолодження) твердого каталізатора, що летить з нею, теплоємність якого в 3000-600 разів більше теплоємності газу. Процес протікає майже ізотермічно. Відокремивши каталізатор в циклоні, його нагрівають або охолоджують в окремому апараті і повертають в процес.
КОНТРОЛЬНІ ПИТАННЯ
1.Які реактори називають адіабатичними?
2.Які реактори називають ізотермічними?
3.Які реактори називають полі термічними?
4.Наведіть приклади реакторів для здійснення гетерогенних процесів
усистемі газ-рідина.
5.Наведіть приклади промислових реакторів для системи газ-тверда речовина.
6.Наведіть приклади реакторів для реалізації процесів у системі рідина-тверда речовина.
7.Принцип дії реакторів для каталітичних процесів.
8.Що таке реактори з киплячим шаром?
74
ТЕМА 6. СТРУКТУРА ТА ОПИС ХІМІКО-ТЕХНОЛОГІЧНИХ СИСТЕМ
Структура хіміко-технологічних систем. Моделі хіміко-технологічних систем. Технологічні зв'язки та їх види. Методи та етапи розробки хімікотехнологічних систем. Технологічні концепції створення хіміко-технологічних систем. Аналіз хіміко-технологічних систем.
6.1. Структура хіміко-технологічних систем
Сучасне хімічне виробництво є складною структурою, яку називають хімікотехнолоґічною системою (ХТС).
Хіміко-технолоґічна система - це сукупність технологічних апаратів, в яких здійснюються фізико-хімічні процеси з метою одержання заданої кількості певного продукту необхідної якості.
Кожен апарат в ХТС виконує певну функцію. У системному аналізі його називають елементом ХТС.
Хіміко-технолоґічна система складається з головної ХТС та підсистем.
Головна ХТС призначається для перетворення сировини у цільовий продукт. Вона охоплює операції з підготовки сировини до хімічного перетворення, здійснення головного технологічного процесу-хімічного перетворення (воно може складатися з низки послідовних чи паралельних хімічних процесів), виділення та очищення утвореного цільового продукту.
Головна ХТС не може працювати без допоміжних підсистем, зокрема:
1.енергетичної;
2.водопідготовки та водопостачання;
3.перероблення відходів та знешкодження шкідливих викидів;
4.управління технологічними процесами та апаратами.
Усі операції з перетворення сировини в цільові продукти, які відбуваються в головній ХТС, та процеси в підсистемах здійснюються в спеціальних машинах, апаратах та інших пристроях.
За їх участю:
1.транспортується сировина, напівпродукти, матеріали, енергоносії тощо (для цього призначаються насоси, транспортери тощо);
2.здійснюються хімічні перетворення (це - реактори);
3.відбувається масообмін між фазами (для цього, наприклад, використовують абсорбери, адсорбери, мембранні апарати, розчинювачі тощо);
4.речовини нагріваються або охолоджуються (теплообмінники);
5.змінюється фазовий (агрегатний) стан речовин (конденсатори, випарники);
6.створюється тиск або розрідження (компресори, вакуум-
насоси);
75
7. змінюються геометричні параметри (розміри) речовин (дробарки, млини, гранулятори).
Елементи в хіміко-технолоґічній системі обов’язково з’єднуються між собою технологічними потоками, які ще називаються технологічними зв’язками.
Розрізняють матеріальні та енергетичні потоки (зв’язки).
Матеріальний потік - це переміщення речовин у будь-якому фазовому стані в просторі від елемента до елемента в межах ХТС. Він здійснюється за допомогою трубопроводів, газоходів, різноманітних транспортерів тощо.
Енергетичний зв’язок - це потік енергії (теплової, електричної, світлової, електромагнітної тощо), яка підводиться до елемента ХТС відповідними засобами. Наприклад, теплова енергія може підводитись трубопроводами, якщо теплоносій - газ, пара чи рідина; електрична - кабелями; електромагнітна - спеціальними трактами (хвилеводами).
Інформаційний потік - це сигнали в електричній чи пневматичній (за допомогою стисненого повітря) формі, якими передається інформація про перебіг технологічного процесу в окремому елементі ХТС або його вузлі, про параметри матеріального або енергетичного потоків при транспортуванні від елемента до елемента, а також команди для керування робочими (виконавчими) пристроями.
Розрізняють первинний та вторинний (зворотний) інформаційні потоки.
Первинний інформаційний потік (зв’язок) надходить від елементів або потоків у спеціальний пункт збирання та оброблення технологічної інформації, який на виробництві називають операторною кімнатою. Тут відбувається його розшифровування засобами мікропроцесорної чи аналогової техніки, автоматичне порівнювання з нормативними величинами. Тут же
формується зворотний (вторинний) інформаційний потік, яким регулюються параметри роботи окремого елемента ХТС, узгоджується робота сукупності елементів або підсистем ХТС. Таке регулювання відбувається внаслідок того, що вторинний потік надходить до певного виконавчого механізму, який регулює витрати реагентів, теплоносія, рівні розчинів в ємностях і реакторах тощо.
Робота та стан кожного елемента або його окремих вузлів та технологічних потоків характеризуються певними кількісними показниками, які називаються параметрами.
Технологічний потік характеризується параметрами стану й параметрами властивостей.
Параметрами стану є температура, тиск, концентрація, витрата речовин.
До параметрів властивостей належать густина, в’язкість, теплоємність, ентальпія, магнітні та електростатичні характеристики потоку.
Елемент ХТС характеризують такі параметри:
76
1.вхідних потоків;
2.вихідних потоків;
3.технологічні;
4.конструктивні;
5.управління.
Особливості ХТП залежать від природи реагуючих речовин і визначають технологічні параметри (константи швидкостей реакцій та рівноваги, ступінь перетворення та селективність, коефіцієнти масота теплопередачі тощо).
До конструктивних параметрів належать геометричні характеристики елемента (загальний та реакційний об’єми, співвідношення між діаметром і висотою, об’єм каталізатора, площа поверхні масота теплообміну, наявність та розміщення теплообмінних поверхонь тощо). Вибір цих параметрів залежить від необхідної продуктивності, яку повинен забезпечити елемент, теплового ефекту реакції, необхідності застосування каталізатора, оптимальних умов реалізації процесу.
Для того, щоб ефективність ХТП в елементі була максимальною, необхідно визначити умови цього процесу:
•температуру,
•тиск,
•гідродинамічний режим,
•потребу в застосуванні каталізатора,
тобто слід підібрати параметри управління ХТП, які ще називають параметрами технологічного режиму.
Значення цих параметрів визначають на підставі знань з кінетики та статики для конкретного процесу, областей його перебігу, відомостей про вплив конкретних чинників на його швидкість. Теоретичні розрахунки перевіряють та уточнюють експериментально. Наприклад, якщо реакція належить до оборотних екзотермічних, то температури визначають в межах оптимальних значень; якщо процес гетерогенний - визначають область перебігу та відповідні способи його інтенсифікації.
За характером зміни найважливіших параметрів системи в часі, тобто за типом функціонування, ХТС поділяють на:
а) ХТС, що працюють безперервно - вони характеризуються сталими параметрами (температурою, тиском, витратою реагентів, продуктів тощо) у часі. Прикладом таких ХТС може бути одержання метанолу із синтез-газу, виробництво сульфатної кислоти, синтез аміаку тощо;
б) ХТС, що працюють циклічно (періодично) - параметри системи змінюються з певною періодичністю. Прикладом такої системи є виробництво коксу, цикл роботи якої складається із завантаження вугілля у коксову піч; коксування, вивантаження коксу. На кожному етапі коксування значення параметрів (температури, складу твердої речовини та газової фази) змінюються;
77
в) ХТС, що працюють напівперіодично (безперервно-періодично) - деякі параметри такої системи є сталими в часі, а інші - змінними. У виробництві негашеного вапна (СаО) завантаження печі є періодичним (витрата вапняку змінюється в часі), а вивантаження продукту, тобто масова витрата СаО, і температура випалювання в зоні реакції є сталими;
г) гнучкі ХТС - це перспективний напрямок організації виробництва, як правило, малотоннажного. Гнучкість полягає в тому, що залежно від потреби споживача промисловий об’єкт може переходити з випуску одного виду продукції на інший на цьому самому обладнанні, тобто елементна база гнучкої ХТС є практично сталою. Очевидно, що в цьому випадку параметри функціонування системи будуть змінюватись залежно від переорієнтації виробництва.
6.2. Моделі ХТС Метою функціонування будь-якої ХТС є забезпечення виробництва
певного продукту необхідної якості та заданого обсягу. Щоб синтезувати нову ХТС, тобто створити нове виробництво, або покращити роботу існуючого, необхідно вміти всебічно проаналізувати цю ХТС. Для того слід описати цю ХТС; такий опис називають моделлю ХТС.
Залежно від способу опису ХТС моделі поділяють на три види:
описові; графічні; математичні.
До описових моделей належать такі підвиди: власне описові (операційноописові) та хімічні.
Операційно-описова модель - це текстовий опис виробництва, який охоплює характеристику сировини, матеріалів, напівпродуктів і продуктів.
У цій моделі зазначається послідовність здійснення всіх технологічних операцій внаслідок яких сировина перетворюється в цільовий продукт певної якості Тут же наводиться опис роботи елементів системи та особливості процесів» що відбуваються в них, зазначаються технологічні параметри перебігу цих процесів.
Перевагою такої моделі є можливість детально описати конкретне виробництво як ХТС і за необхідності текстово пояснити нюанси здійснення технологічного процесу.
Недолік цієї моделі полягає в тому, що для досить складних ХТС описова модель є громіздкою, бо текст може бути великого обсягу. Через це досить важко зразу охопити все виробництво як цілісну систему, особливо, якщо воно передбачає випуск декількох видів продукції чітко розділити її на окремі підсистеми.
У хімічній моделі (другий підвид описових моделей) наводяться лише рівняння хімічних реакцій, які відбуваються у цій ХТС. Ця модель характеризує виробництво як систему послідовних, паралельно-послідовних
78
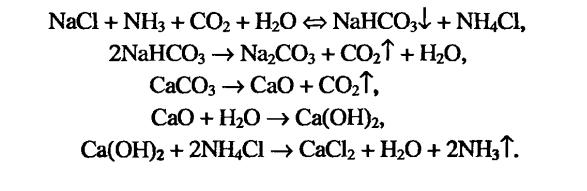
хімічних перетворень. У ній наводять всі реакції як цільові, так і побічні, які відбуваються на будь-якій із стадій виробництва.
Перевагою цієї моделі є виділення сутності ХТС, що базується на системі певних хімічних процесів. Головний недолік моделі - відсутність даних про підготовчі операції, особливості здійснення хіміко-технолоґічних процесів в окремих елементах.
Хімічна модель дає змогу порівнювати різні способи виробництва певного продукту: доступність і вартість сировини, можливість утворення побічних продуктів або екологічно небезпечних речовин як відходів виробництва. Отже, можна наближено оцінити витрати на придбання сировини, реаґентів та матеріалів, вартість утилізації або знешкодження відходів, попередньо визначитись з енергетичними витратами, обсягами капітальних вкладень тощо.
Приклад - виробництво кальцинованої соди
Графічні (іконографічні моделі) підрозділяють на:
•функціональні;
•блокові (структурні);
•операторні;
•технологічні.
Графічні моделі, як випливає з їх назви, - це певне графічне, тобто схематичне, зображення ХТС. Тому традиційно їх ще називають схемами.
Кожен з підвидів цих моделей застосовується на певному етапі синтезу хімікотехнолоґіч ної системи, тобто має конкретне практичне значення на відповідному етапі розроблення та виготовлення проектно-конструкторської документації.
Підставою для розроблення графічних моделей є описові моделі. Функціональна схема (модель) складається з окремих вузлів (підсистем),
зображених прямокутниками із написом всередині. Кожен вузол призначений для здійснення окремої технологічної операцій, наприклад, розмелювання, розчинення, абсорбції газу, термічного розкладу, нейтралізації, екстракції, ректифікації тощо, причому вузол може складатись з одного або декількох видів обладнання (елементів). Вузли розташовані в тій послідовності, яка необхідна для перероблення сировини з одержанням продукту, і зв’язані між собою
79

технологічними потоками. Саме тому функціональна схема дає найзагальнішу уяву про функціонування виробництва як хіміко-технолоґічної системи. Недоліком цієї моделі є повна відсутність відомостей про типи обладнання, яке застосовується для реалізації технологічного процесу.
Рис.6.1. Функціональна модель виробництва кальцинованої соди. Структурна (блокова) схема складається із зв’язаних між собою
технологічними потоками блоків, які відповідають окремим елементам ХТС. На схемі зображають напрям руху технологічних потоків, тобто ця модель дає уяву про послідовність здійснення технологічних процесів чи операцій в елементах ХТС. Порівняно з функціональною моделлю блокова схема загалом дає можливість визначити кількість основних елементів у ХТС чи окремих підсистемах. Однак блокова схема, як і функціональна, не несе інформації про типи конкретних елементів та про кількісні параметри їх роботи.
Рис.6.2. Типовий приклад структурної схеми.
80