
61.06 ЗХТ лекції
.pdfоксидами в ньому. |
Розрізняють |
три види модулів цементу. |
1.Силікатний (кремнеземний) модуль - відношення вмісту оксиду кремнію до сумарного вмісту оксидів алюмінію і заліза. n =% SiО2 / (% Аl2О3 +% Fе2О3)
2.Глиноземний модуль - відношення вмісту оксиду алюмінію до змісту оксиду
заліза: р =% Аl2О3 /% Fе2О3
3. Гідравлічний модуль - відношення вмісту основного оксиду кальцію до сумарного вмісту кислотних оксидів кремнію, алюмінію і заліза:
m =% СаО / (% SiО2 +% Аl2О3 +% Fе2О3).
Затвердіння портланд-цементу засноване на реакціях гідратації, що входять до його складу силікатів і алюмосилікатів, з утворенням кристалогідратів різного складу:
3СаО*SiО2 + (n +1)Н2О = 2СаОSiО2*nН2О + Са(ОН)2
При змішуванні порошку цементу з водою (зачиннення) маса твердне, процес
затвердіння |
протікає |
через |
|
ряд |
|
послідовних |
стадій: |
|||
- |
Утворення |
|
насичених |
|
розчинів |
|
силікатів; |
|||
- |
Гідратація |
|
силікатів |
і |
утворення |
кристалогідратів; |
||||
- |
Кристалізація |
маси |
(схоплювання) |
і |
зростання |
кристалів; |
||||
- |
Утворення |
зростків |
кристалів |
і |
зміцнення маси (тверднення). |
|||||
Для |
додання цементу певних властивостей |
у |
нього |
вводять |
добавки: |
- гідравлічні, що підвищують водостійкість; пластифікуючі, підвищують еластичність маси; кислотостійкі, що додають цементу корозійну стійкість до кислих середовищ; інертні, для здешевлення продукції (пісок); регулюючі час схоплювання маси (гіпс).
Виробництво портланд-цементу складається з двох стадій: отримання клінкеру та його подрібнення.
1. Отримання клінкеру може здійснюватися двома способами - мокрим і сухим, які розрізняються методами приготування сировинної маси для випалу. Мокрим способом сировину подрібнюють у присутності великої кількості води, отримуючи пульпу, що містить до 45% води. У цьому методі забезпечується висока однорідність суміші, знижується запиленість, але збільшуються витрати на випаровування води. Сухим способом компоненти сировини сушать, подрібнюють і змішують в сухому вигляді. Така технологія є енергозберігаючою, тому питома вага виробництва цементу по сухому методу безперервно зростає. Виробництво клінкеру включає операції дроблення, розмелювання і коректування складу сировини і подальшої високотемпературної обробки отриманої шихти - випалу. Сировиною у виробництві портланд-цементу служать різні вапняні породи і глина, а також мергелі, що представляють однорідні суміші тонкодисперсних вапняку та глини. Для випалу шихти використовуються барабанні обертові печі діаметром 3.5-5 м і довжиною до 185 м. Компоненти сировини, що надходить в піч, послідовно проходять в ній зони сушіння, підігріву, кальцинації, екзотермічні реакції
191
утворення силікатів, спікання і охолодження. Клінкер після печі охолоджується в барабанних холодильниках.
2. Подрібнення клінкеру. Охолоджений клінкер витримують на складі протягом 10-15 діб для видалення вільного оксиду кальцію, змішують з добавками і подрібнюють в дробарках і багатокамерних млинах до частинок розміром 0.1 мм і менше.
Основна маса портланд-цементу використовується для виготовлення бетону та виробів з нього. Бетоном називається штучний камінь, отриманий при затвердінні зачиненої водою суміші цементу, піску і наповнювача.
КОНТРОЛЬНІ ПИТАННЯ
1.Що називають керамікою?
2.Вихідна сировина для отримання кераміки.
3.Суть технології отримання керамічних виробів.
4.Основні види кераміки та їх технологія.
5.Скло, види скла та технологія його отримання.
6.В’яжучі матеріали, класифікація та технологія отримання.
192
ТЕМА 19. ХІМІЧНЕ ПЕРЕРОБЛЕННЯ ПАЛИВ
Методи хімічного перероблення палив. Хімічне перероблення твердих палив. Коксування кам'яного вугілля. Перероблення коксового газу. Газифікація твердих палив. Гідрогенізація вугілля. Перероблення нафти. Характеристика та класифікація нафт. Основні нафтопродукти. Методи переробки нафти та нафтопродуктів. Очищення нафтопродуктів. Перероблення природних газів.
19.1. Методи хімічного перероблення палив
Переважно процеси перероблення палив здійснюються за високих температур і називаються ―пірогенетичними‖. Вони можуть бути як некаталітичними, так і каталітичними. У будь-якому випадку пірогенетичні процеси є складними гетерогенними процесами, які описуються системою фізико-хімічних і хімічних процесів.
Розрізняють такі методи пірогенетичного хімічного перероблення палив: піроліз, газифікація, гідрогенізація, крекінг, риформінг. Вибір того чи іншого методу перероблення визначається, перш за все, агрегатним станом палива.
Піроліз полягає у високотемпературних некаталітичних процесах деструкції та інших хімічних перетвореннях компонентів палива без доступу повітря (кисню).
Крекінг є різновидом піролізу, який також полягає у нагріванні рідкої та газоподібної сировини до температур, за яких відбуваються термодеструктивні процеси. Крекінг поділяють на термічний - він відбувається лише під дією температури, і каталітичний - перетворення речовин здійснюється за високих температур у присутності каталізатора
Риформінг — це крекінг легких нафтопродуктів за підвищених температури та тиску: термічний риформінг здійснюється лише під дією цих чинників, а каталітичний — у присутності каталізатора в середовищі водню.
Газифікація - це перетворення органічної частини твердого та рідкого палива її частковим окисненням у горючі гази. У цьому процесі низькокалорійні види твердого або рідкого палив, які мають порівняно невисоку енергетичну цінність, перетворюються у газоподібне, що характеризується вищою теплотворною здатністю або використовуються як сировина для хімічної промисловості. Газифікація поділяється на каталітичну і некаталітичну.
Гідрогенізація (гідрування) - це високотемпературне каталітичне оброблення палив воднем за високих тисків, що приводить до утворення нових, переважно насичених вуглеводнів, які можуть перебувати у різних агрегатних станах.
Типовими процесами хімічного перероблення твердих палив є піроліз, газифікація, гідрогенізація.
Піролізу (некаталітичному високотемпературному перетворенню) піддають, переважно, кам’яне вугілля, зокрема, ті його сорти, які здатні спікатись. Залежно від сфери подальшого застосування основних продуктів,
193
піроліз здійснюють у різних температурних діапазонах. Процес, який здійснюють за температур 500...580 °С - так званий низькотемпературний піроліз, називають напівкоксуванням, за температур 700...800 °С - середньотемпературним коксуванням, а в інтервалі 900... 1050 °С - коксуванням.
Продуктами коксування є кокс (основний продукт), коксовий газ, смоли, масла та інші речовини. Для коксування придатне так зване коксівне вугілля, яке здатне переходити у пластичний стан.
До температури 250 °С відбувається випаровування фізичної вологи та виділення оклюдованих (сорбованих) газів, СО2, СО. За температури близько
300 °С починається виділення пари пірогенної вологи та кам’яновугільної смоли. Внаслідок підвищення температури до 350 °С вугілля переходить у пластичний стан. Цей процес здійснюється через декілька стадій. Спочатку відбувається плавлення високомолекулярних сполук, зокрема бітумів, без їх термічної деструкції. Воно не має чітко визначеного температурного діапазону, бо залежить від якісного і кількісного складу вугілля, який визначається умовами утворення вугілля і відрізняється в різних родовищах
Удіапазоні температур 360...400 °С починає розвиватись термічна деструкція певних видів молекул з утворенням сполук з молекулярними масами від 300 до 600. Вони є майже нелеткими і разом з тим порівняно невеликими, що надає їм властивість за температур близько 400 °С утворювати істинні розчини.
Нелеткі сполуки утворюють так званий ―метапласт‖, який має певні сорбційні властивості - він поглинає частину летких компонентів, що є причиною гальмування газовиділення. Компоненти метапласту не є термостабільними, тому за температур 500..550 °С відбувається розклад пластичної маси з виділенням газу та смоли, яка складається з парафінових, нафтенових, ненасичених і ароматичних вуглеводнів, та затвердненням маси з формуванням напівкоксу.
Усередньому з 1 т вугілля під час коксування утворюється, мас.%: коксу - 70...80; смоли - 2...4; сирого бензолу - 0,8...1,2; коксового газу - 15...22; сульфату амонію - 1...1,2. Така сталість виходів продуктів коксування зумовлена тим, що коксуванню як цільовому процесу виробництва металургійного коксу підлягають тільки спеціальні сорти вугілля або їх суміші (шихти). Крім того, виявляється нівелююча дія високої температури, за якої всі сполуки перетворюються у найбільш термостабільні форми.
Кам’яновугільна смола, яка конденсується під час охолодження прямого коксового газу, складається із кількох тисяч індивідуальних речовин. Із них вдалось виділити та ідентифікувати лише близько 650 сполук. Вони переважно належать до незаміщених конденсованих ароматичних вуглеводнів. Серед них вміст лише 11 сполук перевищує 1 %, а найбільший вміст має нафталін - близько 10 %. Іншими сполуками, що у доволі високих концентраціях знаходяться у смолі, є інден, циклопентадієн, фенол, флуорен, пірен, антрацен,
194
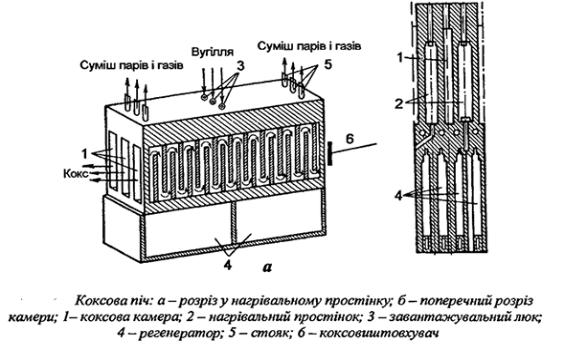
фенантрен, о-крезол, карбазол, хінолін та інші. Використовують кам’яновугільну смолу для виділення індивідуальних сполук або їх сумішей (пеки, оливи тощо).
Кокс одержують у високотемпературних реакторах, які називаються коксовими печами. Коксова піч складається із батареї камер (70 і більше), кожна з яких працює у періодичному режимі, споруджених спільною кладкою та зв’язаних між собою спільними механізмами для завантаження вугільної шихти й вивантаження коксу. Коксовий газ виводиться із коксової батареї безперервно через спільний для усіх камер газовий колектор.
Коксові печі належать до печей непрямого нагрівання: нагрівання шихти здійснюється підведенням теплоти через стінки камери, які футеровані вогнетривкою динасовою цеглою. Оскільки коксування є високотемпературним ендотермічним процесом, то потребує постійного підведення теплоти. Для одержання якісного коксу й максимального вилучення із нього летких компонентів коксування здійснюють за певної швидкості нагрівання та до заданої температури (температурний режим процесу залежить від сортів вугілля, яке коксують). Оскільки стінки камери, вугільна шихта і проміжні продукти коксування характеризуються низькою теплопровідністю, то для забезпечення оптимальних режимів коксування, особливо швидкості підведення теплоти, камери виготовляють у вигляді вузьких каналів завширшки 0,4, завдовжки 13...14, заввишки 4...4,5 м за товщини стінки близько 0,1 м. Завантаження такої камери становить близько 15 т вугільної шихти.
Рис.19.1. Коксова піч.
Коксова піч складається з почергово розташованих коксових камер 1 і нагрівальних простінків 2. Коксова камера 1 оснащена рухомими стінками: передньою (машинною) і задньою (коксовою). Через передню стінку у камеру
195
вводиться коксовиштовхувач 6 - своєрідний поршень із прямокутною робочою пластиною, яким продукт (кокс) виштовхується з камери через пройму коксової стінки. Під час завантажування камери шихтою і роботи обидві стінки щільно прилягають до камери. Завантажують вугільну шихту через отвори 3 у стелі камери.
Вугільна шихта нагрівається теплотою, що виділяється внаслідок згоряння газоподібного палива у простінках 2. Сюди вводиться паливо, наприклад зворотний коксовий газ, і нагріте у регенераторах 4 повітря. Топкові гази, що утворюються під час згоряння палива, огинають камеру, нагріваючи її згори та з протилежного боку, і надходять у регенератор. Тут вони нагрівають інертну насадку, а потім надходять у димову трубу. Через деякий час (20...30 хв) газові потоки перемикають, при цьому топкові гази проходять через регенератори сусідньої камери, а повітря - через гарячу насадку регенератора працюючої камери. Газоподібні продукти коксування виводяться з камери через вихідні патрубки (стояки) 5. Після закінчення коксування перекривають вихід коксового газу — патрубок 5, відкривають обидві стінки коксової камери і виштовхують кокс виштовхувачем 6 у гасильний вагон, у якому кокс транспортується у гасильну башту, де охолоджується водою - загартовується, для запобігання його загоряння.
Під час коксування утворюється парогазова суміш, яка називається прямим коксовим газом. Вона містить водень, метан та інші вуглеводні, у тому числі ароматичні, оксиди вуглецю, смолу, аміак, сірководень, ціанисті сполуки, водяну пару, тверді частинки. Із коксових камер газ виходить із середньою температурою близько 700 °С і надходить у загальний газозбірник 1, який інтенсивно зрошується попередньо охолодженою надсмольною водою. За цих умов газ охолоджується до 80 °С, унаслідок чого відбувається часткова конденсація смоли і очищення газу від твердих частинок. Надалі газ надходить у трубчастий холодильник 2, де охолоджується до ЗО °С; тут відбувається подальша конденсація смоли та водяної пари, конденсатом частково абсорбується аміак та інші гази - утворюється надсмольна вода. Смола та надсмольна вода стікають у збірниксепаратор 3, де вони розділюються внаслідок різниці густин.
Частина смоли під час інтенсивного охолодження конденсується в газовому об’ємі з утворенням туману, який разом із завислими твердими і рідкими частинками (аерозолями) вилучається із газу в електрофільтрі 4. Рідка фаза із електрофільтра 4 надходить у збірник 3. Очищений газ ексгаустером 5 (нагнітачем) подається у підігрівач 6, а з нього у сатуратор 7, де аміак поглинається розчином сульфатної кислоти з утворенням розчину амонію сульфату. Одночасно розчином поглинаються й деякі інші газоподібні речовини, що містяться у коксовому газі.
Надалі газ подається у насадкову башту-холодильник 8, яка зрошується холодною водою, де охолоджується до 25 °С. Звідти він надходить у насадкові скрубери 9 для вловлювання сирого бензолу. Як поглинач сирого бензолу та
196
його гомологів використовують солярове масло, яке після цього спрямовують у дистиляційну колону для регенерації масла з метою її повторного використання як абсорбента.
Отриманий після вилучення сирого бензолу та сполук сірки газ називається зворотним коксовим газом. Він містить, %: 54...60 водню, 23...ЗО метану, 5...7 СО, а решта - це вуглеводні, азот, кисень, СО2
Напівкоксуванням називається низькотемпературний (до 500...600 °С) піроліз низькоякісного твердого палива (кам’яного і бурого вугілля, сланців, торфу) без доступу повітря. Основне призначення напівкоксування полягає в одержанні штучного рідкого і газоподібного палив, що характеризуються значно вищою калорійністю (теплотворною здатністю), ніж вихідне паливо, а також сировини для хімічної промисловості.
Під час напівкоксування зазначених палив одержують напівкокс, смолу і напівкоксовий газ. Але їх вихід, якісний і кількісний склад істотно залежать від виду сировини. Зокрема, напівкокс, одержаний унаслідок піролізу різних сортів вугілля, використовують як паливо або як компонент шихти, яку надалі коксують. Напівкоксовий газ, який містить значні кількості метану та водню, застосовується як беззольне паливо з доволі високою теплотворною здатністю; крім того, він служить сировиною для деяких хімічних виробництв. Смола є джерелом для одержання фенолу, масел, насичених вуглеводнів.
Основним продуктом напівкоксування горючих сланців є смола, з якої одержують моторні палива, розчинники, органічні мономери. Напівкокс, що містить близько 10 % вуглецю і 90 % мінеральних речовин, використовують у технологіях в’яжучих речовин, а газ - як паливо для нагрівання сировини у процесах напівкоксування.
Газифікація твердих палив Газифікація - високотемпературний гетерогенний процес часткового
окиснення органічних компонентів твердого палива з одержанням горючих газів (переважно Н2, СО, CH4). Ці гази використовують як штучне газоподібне
паливо або як сировину (синтез-газ, газ-відновник) для ряду хімічних, нафтохімічних, металургійних виробництв.
Газифікуються практично всі види твердого палива (кам’яне та деревне вугілля, торф, напівкокс). Останніми роками все масштабнішою стає газифікація деревини, особливо, відходів деревооброблення - кори, тирси, стружки тощо.
Для газифікації твердого палива як реагенти застосовують повітря, водяну пару, суміші водяної пари з повітрям або киснем. Відповідно розрізняють повітряне, парове, повітряно-парове та киснево-парове види дуття, унаслідок чого одержують так звані генераторні (тобто ті, що утворилися, генерувалися) гази: повітряний, водяний тощо.
Повітряний газ утворюється внаслідок взаємодії вуглецю палива з киснем повітря за такими основними послідовними реакціями:
197
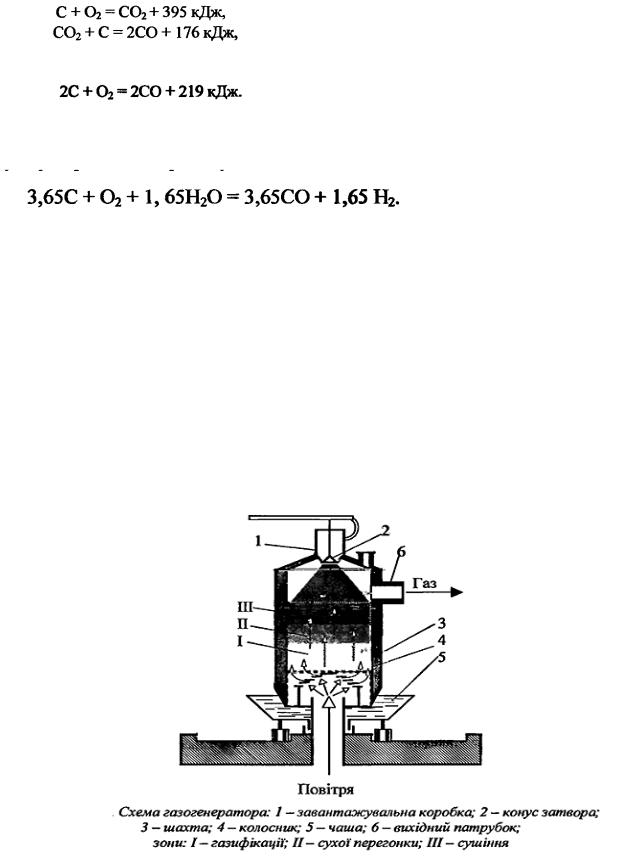
Напівводяний (пароповітряний) та оксиводяний (парокисневий) генераторні гази одержують за реакціями взаємодії вуглецю з киснем і водяною парою. Сумарне рівняння процесу має такий вигляд:
Газогенератор - це вертикальний апарат циліндричної форми, футерований зсередини вогнетривкою цеглою. Завантаження апарата твердим паливом у вигляді грудок здійснюється через завантажувальну коробку 1, яка розташована у верхній частині газогенератора (при опущеному конусі затвора 2). Поступово після перетворення нижніх шарів палива у газоподібні продукти, верхні шари палива переміщуються шахтою донизу, а назустріч паливу через колосник 3 надходить дуттєвий газ.
Рух палива донизу здійснюється через три зони, у яких відбуваються специфічні процеси. У верхній зоні (І) паливо, яке завантажили в апарат, підсушується гарячим генераторним газом й переміщується у другу зону - сухої перегонки, де відбувається подальше нагрівання маси внаслідок протитечійного руху генераторного газу до температур, за яких відбувається видалення летких компонентів.
Рис.19.2. Схема газогенератора.
У нижній зоні нагріте тверде паливо взаємодіє з компонентами дуттєвого газу. Саме тут утворюються генераторні гази, які рухаються вгору через шар
198
твердого палива і виводяться через патрубок 5. Шлаки як побічні продукти газифікації й надалі переміщуються донизу і через чашу 6, заповнену водою, яка відіграє роль гідрозатвора, виводяться з газогенератора. Свіжий дуттєвий газ вводиться в апарат знизу через колосник. Унаслідок проходження через шлак дуттєвий газ нагрівається, а шлак, відповідно, охолоджується.
19.2. Гідрогенізація вугілля
Методом гідрогенізації бурого і кам’яного вугілля, сланців та інших видів твердого палива одержують синтетичне (штучне) рідке паливо - замінник нафтопродуктів.
Цей процес належить до високотемпературних гетерогенних каталітичних процесів, які відбуваються за високих тисків у присутності газоподібного водню. Суть гідрогенізації полягає в тому, що в органічній масі, наприклад, вугіллі, відбувається руйнування слабких внутрішньомолекулярних і міжмолекулярних зв’язків, унаслідок чого високомолекулярні органічні сполуки перетворюються у низькомолекулярні вуглеводні, які переходять у рідку фазу, а потім гідруються (насичуються воднем за подвійними ненасиченими зв’язками) з подальшою деструкцією. Унаслідок цього утворюються рідкі насичені вуглеводні. Через те, що під час гідрогенізації відбуваються інтенсивні процеси руйнування органічних речовин, його ще називають деструктивною гідрогенізацією. Джерелом Водню є газоподібний водень, що підводиться ззовні, та Водень, який входить до складу компонентів вугілля.
19.3. Переробка нафти
Нафта належить до природних рідких горючих копалин. Залежно від складу сира нафта може мати певний колір - від жовтогарячого із зеленкуватим відтінком до чорного і характеризуватись різною в’язкістю, яка особливо
залежить від температури. Густина нафти коливається в межах 0,80...0,95
3
кг/дм . Важливою характеристикою нафти, що визначає її придатність до транспортування і перепомповування, є температура застигання, тобто така температура, за якої нафта втрачає свою плинність; для різних нафт вона коливається в інтервалі температур від-20 до +20 °С.
Усі зазначені характеристики нафти передусім визначаються складом нафти, який має органічну і мінеральну частини. Переважаючою є, безумовно, органічна складова; мінеральна частина сирої нафти утворена СаС12, М^СЬ,
сполуками ванадію, нікелю, калію, титану, фосфору, галію, твердими глинистими частинками і незначною кількістю води.
Органічна частина нафти складається, в основному, з рідких і розчинених твердих та інших вуглеводнів (90...95 % від маси), а також смолистих і асфальтенових речовин, органічних кислот, сірко- і азотвмісних органічних сполук. Елементний склад вуглеводневої частини нафти різних родовищ може змінюватись у доволі широких межах .
Класифікують нафти за переважаючим вмістом вуглеводнів певних класів (типів). За таким принципом класифікації нафти поділяють на:
199
•парафінові (найбагатші за бензиновими фракціями і містять твердий парафін);
•парафіно-нафтенові;
•нафтенові;
•нафтено-ароматичні;
•парафіно-нафтено-ароматичні (асфальтові) - найважчі з нафт;
•ароматичні.
Слід зауважити, що парафінові, нафтенові й ароматичні нафти, крім зазначених, містять ще й інші вуглеводні, але у порівняно невеликих кількостях. У деяких класифікаціях ці три класи нафт окремо не виділяють.
За вмістом твердих парафінів, які визначають температуру застигання, нафти поділяють на малопарафінисті (до 1,5 % твердих парафінів); парафінисті (1,5...6 %) і високопарафінисті (понад 6 %). За вмістом сполук сірки нафти класифікують на малосірчисті (до 0,5 % S), сірчисті (0,5—2 % S) і високосірчисті (понад 2 % S).
Для оцінювання якості нафти і вибору методів подальшого перероблення важливим є визначення її фракційного складу за температурами кипіння (табл. 8.3). Найціннішими є нафти з переважальним вмістом низькокиплячих компонентів (вуглеводнів); густина таких нафт є найменшою серед усіх інших, тому їх називають легкими. Відповідно, чим більше висококиплячих вуглеводнів міститься у нафті, тим вона є ―важчою‖.
Сира нафта, яку видобуто із родовища, містить різні домішки, які ускладнюють її складування та перероблення. До таких домішок належать: супутній газ, вода, мінеральні солі та механічні домішки.
Супутній газ є цінною самостійною сировиною або паливом; до того ж, якщо він є розчином у нафті, то він заважає переробленню нафти і призводить до збільшення її втрат під час зберігання, бо разом із газом випаровується частина низькокиплячих бензинових фракцій. Попередня (груба) сепарація газу здійснюється у газовідділювачах, де відбувається десорбція газу внаслідок розбризкування нафти та зменшення тиску. Тонке відділення здійснюється у стабілізаційних установках, де газ із нафти відганяється у спеціальних ректифікаційних колонах.
Вода і механічні домішки відділяються відстоюванням, яке часто здійснюють за дещо підвищених температур. Якщо вода утворює з нафтою стійкі емульсії, що містять від 20 до 60 % води у вигляді крапельок з розмірами (0,1... 10 мкм), то застосовують деемульгатори - поверхнево-активні речовини, які сприяють руйнуванню плівок навколо водних частинок емульсії Особливо активно руйнуються емульсії в електричному полі змінного струму високої напруги (30...40 кВ). Мінеральні солі переважно є добре розчинними у воді, тому виводяться з нафти у разі її зневоднення.
Продукти нафтоперероблення можна підрозділити на такі групи:
світлі нафтопродукти (бензин, лігроїн, гас);
солярові нафтопродукти (газойль, дизельні палива);
200