
61.06 ЗХТ лекції
.pdf
Утворений активний радикал R, реагуючи з молекулами мономеру, дає початок нового ланцюга:
* |
* |
|
R + CH2=CH |
|
RCH2-CH |
|
XX .
Уразі утворення неактивного радикала, не здатного продовжити реакційний ланцюг, відбувається припинення полімеризації.
21.2.Іонна полімеризація
Активними центрами іонної полімеризації є іони, що утворюють у неполярних розчинниках іонні пари. У полярних розчинниках виникають сольватно-розділені іонні пари і вільні іони.
Залежно від природи каталізаторів і заряду утворених іонів розрізняють катіонну і аніонну полімеризацію.
21.3. Катіонна полімеризація
Катіонна полімеризація протікає під дією кислот і каталізаторів ФіделяКрафтса (АlCl3, ВF3, SnCl4, FеСl3 і т.п.), тобто електронакцепторних речовин. У присутності води, кислот, ефірів та інших речовин, що відіграють роль співкаталізатора, утворюється активний каталітичний комплекс, який ініціює реакцію:
BF3 +HOH →(BF3 OH )− H+ .
При взаємодії цього комплексу з молекулою мономеру утворюється активний карбенієвий центр:
+ |
- |
+ |
- |
|||
CH2=CH + H (BF3OH) |
|
H3C- |
CH(BF3OH) |
|||
|
||||||
|
|
|
|
|
|
. |
X |
|
|
X |
|||
|
|
|
221
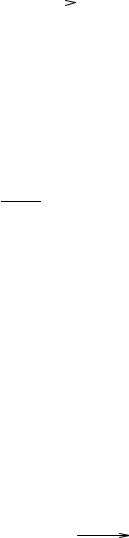
Реакція зростання полягає в приєднанні молекул мономера до активного карбенієвого центру з регенерацією цього активного центру на кінці ланцюга:
+ |
- |
|
|
|
|
|
+ |
- |
||||
|
|
|
|
|
||||||||
H3C- |
CH(BF3OH) + nCH2=CH |
|
H- |
-CH2-CH- |
-CH2-CH(BF3OH) |
|||||||
|
||||||||||||
|
|
|
|
|
|
|
|
|
|
|
|
|
X |
X |
|
|
|
X |
|
n X |
. |
Швидкість росту описується рівнянням
k |
р kин |
2 |
|
r= |
kо |
[C] [M ] , |
(21,2) |
де [С] - концентрація каталізатора.
Катіонна полімеризація протікає, як правило, з дуже високою швидкістю, що дозволяє проводити процес при низьких температурах. Наприклад, полімеризацію ізобутілену проводять при t = -100 °С в середовищі рідкого етилену.
Обрив ланцюга відбувається як молекулярна реакція з відщепленням протона від сусіднього з карбенієвим іоном атома вуглецю і дисоціації каталітичного комплексу:
|
|
|
|
|
+ |
- |
-H2O |
H- |
|
|
|
|
|
|
|
|
|
|
|
-CH -CH- |
-CH=CH |
||||||||
|
|
|
|
|
||||||||||
H- |
-CH -CH- |
-CH -CH(BF OH) |
|
|
2 |
|
|
|
2 |
|||||
|
2 |
|
|
2 |
3 |
-BF3 |
|
|
|
|
|
|
|
|
|
|
|
|
|
|
|
|
|
|
|
|
|
|
|
|
|
|
|
|
|
|
|
|
X |
|
n |
|
||
|
|
X |
|
n |
|
|
|
|
. |
|||||
|
|
|
|
|
|
|
||||||||
|
|
|
|
|
|
|
21.4. Аніонна полімеризація
Аніонна полімеризація протікає в присутності лужних металів, металоорганічних сполук, аміду натрію, алкоголятів лужних металів та інших електронодонорних сполук. Найбільше практичне значення має полімеризація, що протікає під дією лужних металів або їх алкинів.
Полімеризація акрилонітрилу під дією аміду калію в рідкому аміаку викликається вільними іонами, внаслідок дисоціації аміду:
222
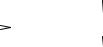
KNH2↔K++NH−2
Утворення карбоаніона відбувається при взаємодії амідного іона з молекулою мономеру:
- |
|
|
|
|
H |
|
|
|
H N-CH -C - |
||
NH +CH =CH |
|
||||
|
|||||
2 |
2 |
|
2 |
2 |
|
|
|
|
|
|
CN. |
|
CN |
|
|
Зростання ланцюга відбувається в результаті взаємодії утвореного карбаніони з молекулою мономеру з утворенням нового аніону. Обрив ланцюга відбувається шляхом взаємодії карбаніона з молекулою аміаку з регенерацією амідного іона, тобто протікає реакція передачі ланцюга.
21.5. Іонно-координаційна полімеризація
Іонно-координаційна полімеризація викликається комплексними каталізаторами Циглера-Натта. Найчастіше в якості каталізаторів використовують металоорганічні сполуки алюмінію і хлориди титану.
Активні центри при іонно-координаційної полімеризації являють собою металоорганічні сполуки перехідного металу. Вони виникають у присутності співкаталізатора або при взаємодії вихідних мономерів з металгідридними центрами на поверхні каталізатора.
Утворення активного металографічного з'єднання відбувається наступним чином:
TiCl3 +Al(C2 H5)3→Cl3Ti−C2 H5+Al(C2 H5)Cl .
Зростання полімерного ланцюга здійснюється шляхом впровадження молекули мономера по зв'язку в перехідний зв'язок метал-вуглець:
223
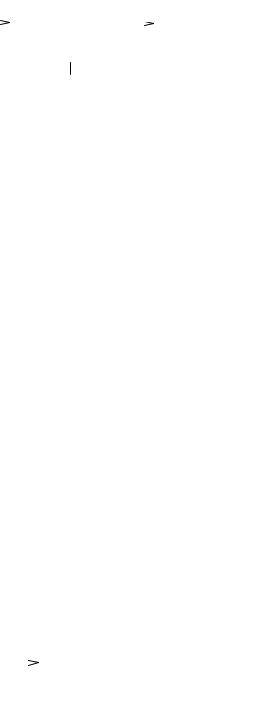
Cl Ti-C H +CH =CH |
|
Cl Ti-C H |
|
nCH2=CHX |
|
Cl Ti- |
|
|
|
|
||||||||||
|
|
-CH -CH- |
-C H |
|||||||||||||||||
|
|
|
|
|||||||||||||||||
3 |
2 |
5 |
2 |
|
|
2 |
|
2 |
5 |
|
|
3 |
2 |
|
|
2 |
5 |
|||
|
|
|
|
|
|
|
|
|
|
|
|
|
|
|
|
|
|
|
|
|
|
|
|
X |
|
|
|
|
|
|
|
|
|
|
|
|
|
|
|
|
|
|
|
|
|
|
CH2 -CH |
|
|
|
|
|
|
X |
|
n |
|
|||||
|
|
|
|
|
|
|
|
|
|
|
|
|
||||||||
|
|
|
|
|
|
|
|
X |
|
|
|
|
|
|
|
|
|
|
|
.
Стадії введення молекули мономера передує її координація на металі з утворенням нестійкого π - компонента. Тому комплексні каталізатори отримали назву іонно-координаційних. Обрив ланцюга відбувається в результаті міграції атома водню від атома вуглецю до металу з утворенням гідриду перехідного металу і полімерної молекули.
Використання для полімеризації комплексних металоорганічних каталізаторів призводить до утворення стереорегулярних полімерів. Ці каталізатори мають високу стереоспеціфічность.
21.6.Способи проведення полімеризації
Упромисловості полімеризація здійснюється наступними основними способами: в газовій фазі, блоці (масі), розчині, емульсії і суспензії.
21.7.Газова полімеризація
ГазофазнІй полімеризації підлягають газоподібні мономери (етилен, пропілен). Процес ініціюється киснем, який додається в мономер в невеликих кількостях (0,002 ÷ 0,008% об.) і проводиться під великим тиском. При взаємодії етилену з киснем утворюються пероксидні або гідропероксіидні сполуки етилену:
CH2=CH2 + O2 |
|
H2C-CH2 |
CH2=CH |
|
. |
||||
|
|||||||||
|
|
|
|
|
|
|
|
|
|
|
|
O O або |
|
OOH |
Нестійкий пероксидний зв’язок- О - О під дією температури розривається з утворенням ди- і монорадикалів: ОСН2-СН2О· и СН2=СНО·. Вільні радикали ініціюють полімеризацію етилену.
21.8. Блокова полімеризація
Блокову полімеризацію або полімеризацію в масі проводять у конденсованої фазі у відсутності розчинника. У результаті полімеризації
224
утворюється концентрований розчин (або розплав) полімеру в мономері або монолітна тверда маса (блок).
Зазвичай блокову полімеризацію проводять у присутності ініціаторів або при термічному ініціюванні. У міру збільшення ступеня полімеризації мономера збільшується молекулярна маса середовища і її в'язкість, що утрудняє відведення тепла із зони реакції. У результаті цього можуть виникати місцеві перегріви реакційної маси, внаслідок чого полімер виходить неоднорідним за молекулярною масою. Тому блокову полімеризацію проводять з малою швидкістю.
21.9. Полімеризація в розчині
Можливі два способи проведення полімеризації в розчині. За першим способом застосовується розчинник, який розчиняє і мономер, і полімер. Одержуваний розчин полімеру (лак) використовують як такий або полімер виділяють. За другим способом застосовують розчинник, який розчиняє мономер, але не розчиняє полімер. Утворений полімер випадає в осад.
При полімеризації в розчині значно поліпшується відвід тепла, яке виділяється в ході реакції, але в результаті протікання реакцій передачі ланцюга через розчинник одержувані полімери мають більш низьку молекулярну масу.
21.10. Полімеризація в емульсії
При емульсійній полімеризації в якості дисперсійного середовища зазвичай використовують воду. Для стабілізації емульсії застосовують різні емульгатори (олеат, пальмітат, і інші солі жирних кислот). Емульсійну полімеризацію проводять у присутності водорозчинних ініціаторів (персульфат калію, пірофосфати, бікарбонати). Для зменшення розгалуженості ланцюга додають меркаптани. Для створення тонкої емульсії реакційну суміш енергійно перемішують, в результаті чого мономер розбивається на дрібні краплі, вкриті шаром емульгатора.
Полімеризація протікає в адсорбційних шарах емульгатора на поверхні полімерно-мономерних частинок. Зростаюча макромолекула є центром, навколо якого утворюється частинка латексу. Отриманий латекс коагулюють, вводячи в систему розчин електроліту, а осад полімеру відокремлюють. В результаті емульсійної полімеризації виходить полімер з великою молекулярною масою і низьким ступенем полідисперсності.
Можливість застосування емульсійного способу в ряді випадків обмежує утворення великої кількості стічних вод, що вимагають очищення від токсичних мономерів, а також трудомісткість стадії сушіння тонкодисперсного
225
полімеру. Крім того, недоліком способу є забруднення полімеру залишками емульгатора та інших добавок, що погіршує його електричні властивості.
21.11. Полімеризація в суспензії
Полімеризація в суспензії проводиться також у воді. Для підвищення стійкості утвореної більш грубою емульсії використовують слабкі емульгатори - полівініловий спирт, водорозчинні ефіри целюлози, желатин, глину, оксид алюмінію і т. п. Застосовувані ініціатори розчиняються у мономері.
Полімеризація відбувається в краплях, що представляють, по суті, невеликі блоки, тому таку полімеризацію іноді називають крапельної (гранульною) полімеризацією.
На відміну від емульсійної полімеризації в даному випадку відпадає необхідність у проведенні коагуляції, тому що утворені гранули полімеру вільно виділяються з водної фази.
21.12. Пластичні маси
До пластмас відносять велику групу матеріалів, головною складовою частиною яких є природні або синтетичні ВМС, здатні при підвищеній температурі і тиску переходити в пластичний стан, формуватися під впливом зовнішніх сил і потім після охолодження або затвердіння стійко зберігати природну форму.
ВМС - найважливіша складова частина, що скріпляє всі компоненти в одне монолітне ціле і що додає композиції пластичність, здатність формуватися, а також електроізоляційні, антикорозійні та інші найважливіші властивості. Для цього використовуються, крім синтетичних полімерів, ефіри целюлози, білкові речовини, асфальти і пеки. За складом пластмаси можна розділити на ненаповнені, що представляють собою чисті або з дуже незначними добавками полімери, і наповнені пластики - суміші, що містять наповнювачі, пластифікатори, барвники, стабілізатори, отверджувачі та інші добавки.
Наповнювачі - тверді речовини, які вводяться для додання або посилення пластичній масі певних фізичних властивостей: міцності, теплостійкості, а також зниженні усадки під час затвердіння. Одночасно наповнювач збільшує негорючість виробів, часто водостійкість. В якості наповнювачів застосовуються органічні й мінеральні сполуки. Вони можуть бути у вигляді порошків (деревна, слюдяна і кварцове борошно, сажа графіт і т.д.), волокнистих матеріалів (бавовна, азбестове волокно і т.д.) і у вигляді полотна (папір, слюда і т.д.). Пластифікатори - малолеткі, здебільшого рідкі речовини, що підвищують пластичність композиції при підвищеній температурі і що додають відформованим виробу морозостійкість, велику еластичність і пружність. Найбільш поширеними пластифікаторами є
226
касторове масло, дибутилфталат, та інші порівняно доступні органічні сполуки.
Барвники застосовуються для додання виробу бажаного забарвлення. Вони повинні не тільки добре поєднуватися з пластмасою, але і витримувати без змін властивостей вплив температури, води і, отже, зберігати свій колір не тільки в процесі формування, але і в умовах подальшої експлуатації отриманого виробу.
Отверджувачі, наприклад, гексаметилентетрамін (уротропін) та інші, викликають перехід деяких пластмас у неплавкий стан внаслідок утворення полімерів тривимірної структури. У пластмаси часто вводяться і інші добавки в невеликих кількостях: прискорювачі - забезпечують затвердіння з потрібною швидкістю; стабілізатори, що сприяють тривалому збереженню пластмасою своїх початкових властивостей; мастила, полегшують пресування і ін. Пластмаси використовуються як конструкційні матеріали при виготовленні різноманітних вузлів і деталей машин, апаратів, приладів та інших технічних пристроїв, які призначені для роботи в умовах тривалого корозійного впливу. Більшість пластмас легше металів в 4-6 разів. Стійкі до морської води піно-і поропласти навіть при тривалому перебуванні у воді практично зберігають свою вантажопідйомність. Цінною властивістю пластмас є їх значна механічна міцність, що не поступається для деяких видів навіть чорному металу. Пластмаси відрізняються високими діелектричними властивостями і малою теплопровідністю, в 100-500 разів меншою, ніж у металів. Багато пластмас негорючі. Великою перевагою пластмас є їх висока стійкість до атмосферних впливів, стійкість у різних агресивних середовищах і здатність до формування у вироби складної конфігурації найбільш продуктивними методами. У той же час пластмаси мають і низку недоліків: нижча в порівнянні з металами термостійкість (більшість пластмас можуть працювати при температурі не вище 150 С), пластмаси піддаються старінню, яке проявляється у процесах
окислення, |
потемніння, |
зниження |
твердості |
і |
міцності. |
Залежно від |
хімічного складу пластмаси |
діляться |
на чотири класи: |
1. Пластичні маси, що містять ВМС, одержувані ланцюговою полімеризацією. У цей клас входять пластмаси на основі полімерів етилену і його різних похідних, полімерів вінілового спирту та його похідних та ін
2.Пластичні маси на основі ВМС, одержуваних поліконденсацією і ступінчастою полімеризацією: феноло-альдегідних смол (фенопласти), амідо - і аміно-формальдегідних смол (амінопласти), кремнійорганічних полімерів і ін
3.Пластичні маси, що містять природні хімічні модифіковані полімери; прості і складні ефіри целюлози та ін.
4.Пластичні маси на основі природних і нафтових асфальтів, а також смол,
одержуваних деструкцією різних органічних речовин. Сорти пластмас позначають буквами і цифрами. Так, наприклад, фенопласт К- 18-2 розшифровується наступним чином: «Композиція з феноло-формальдегіду смоли № 18 та деревного борошна».
227
З полімеризаційних смол найбільш широко застосовуються поліетилен, полістирол, полімери та сополімери хлористого вінілу, поліпропілен, полівінілацетат, поліізобутілен та ін.. Як приклад можна розглянути отримання та властивості поліетилену (-СН2-СН2-) n. Його отримують з етилену трьома способами:
- Полімеризацією під тиском 1000-2000атм при Т = 180-200С з використанням як ініціатора невеликих кількостей кисню (0.005-0.05%);
-Полімеризацією при атмосферному або невеликому тиску (2-6 атм) і невисокій температурі (60-70 С) у присутності комплексних металоорганічних каталізаторів у середовищі нафтового вуглеводню при повній відсутності вологи і кисню;
-Полімеризацією при тиску 20-50 атм на окисних каталізаторах і 110-140 С. Поліетилен, отриманий останніми двома способами (поліетилен низького тиску) має строго лінійну будову, більш високий молекулярний вагу до 70000 і температуру плавлення на 20 С вище, ніж поліетилен високого тиску з розгалуженою структурою. Полімеризація етилену при високому тиску являє собою ланцюгову реакцію, що протікає по радикальному механізму з
виділенням великої кількості тепла nС2Н4 → (-С2Н4-) n + 3650 кДж, тому важливий для нормального ходу процесу систематичний відвід тепла і суворе регулювання температури. Швидкість процесу полімеризації і вихід полімеру залежать від ступеня чистоти вихідного газу, кількості ініціатора, температури, тиску. Полімеризація етилену під тиском здійснюється або в апаратах трубчастого типу або в реакторах з мішалкою. Етилен з необхідною кількістю кисню стискається в компресорі до тиску 1200-1500 атм і надходить у реактор, де при температурі 200 С йде процес блокової полімеризації. Отримана суміш розплавленого поліетилену і непрореагованого етилену надходить у газовідокремлювач, в якому після зниження тиску відбувається відділення полімеру від газу. Полімер направляється на стабілізацію, фарбування та грануляцію, а етилен йде на промивку. Ступінь конверсії вихідного етилену в полімер за один прохід становить 10-20%. Сумарне перетворення етилену в результаті неодноразової циркуляції досягає 95-97%. Вироби з поліетилену високого тиску щоб уникнути деформації можна використовувати тільки при температурі не вище 80 С. Такий поліетилен має
електроізоляційні |
властивості, |
еластичніст |
і |
високу |
хімічну стійкість. |
|
|
|
|
Іонна полімеризація етилену в присутності гетерогенних |
комплексних |
каталізаторів Циглера (комплекси чотирихлористого титану і тріетілалюмінія) здійснюється таким чином: очищений етилен подається в суспензію металлорганічного комплексного каталізатора в низкокиплячому бензині, непрореагований етилен відокремлюється від полімеру і каталізатора в системі сепараторів і після очищення повертається в процес, а полімер направляється на переробку. Процес може бути періодичним і безперервним. Поліетилен
228
низького тиску має велику щільність і більш високу теплостійкість. До поліконденсаційних смол відносяться феноло-альдегідні, аміно - формальдегідні, поліефірні, епоксидні та ін.. Частина з них термопластичні, але більша частина термореактивноі. Вироби на основі цих смол після затвердіння можуть експлуатуватися тривалий час у більш широкому інтервалі температур і при підвищенні температури вони менше змінюють свої фізико-хімічні властивості, ніж вироби з більшості полімеризацій смол. Феноло-альдегідні смоли виходять в результаті реакції поліконденсації фенолів або споріднених сполук: крезолу, ксилолів з альдегідами (формальдегід, ацетальдегід, фурфурол і т.д.) у присутності каталізаторів (кислих або лужних). У ході реакції виходять проміжні продукти, здатні до подальшої взаємодії, з утворенням більш складних продуктів конденсації. Ця різноманітність пояснюється тим, що в ядрі фенолу є три рухливих атоми водню, здатних до реакції заміщення. В результаті поліконденсації фенолу з альдегідами виходять смоли двох типів: термопластичні і термореактивні. Термопластичні смоли, відомі під назвою новолачних, утворюються при надлишку фенолу у вихідній суміші і застосуванні кислих каталізаторів. Термореактивні феноло-формальдегідні смоли (резольні) виходять при надлишку формальдегіду і в присутності лужного каталізатора. Резольні смоли при нагріванні переходять в неплавкий і нерозчинний стан. Залежно від ступеня затвердіння розрізняють три стани резольних смол: резол (або бакелит А) - суміш низькомолекулярних продуктів, що плавиться при нагріванні і розчинна у спирті або ацетоні, що має лінійну структуру; резитол - друга стадія, в яку переходить резол при нагріванні або при тривалому зберіганні; резит виходить в останній стадії поліконденсації при виробництві готових виробів. Резит неплавкий та не розчиняється. Наша промисловість випускає новолачні і резольні смоли в сухому і рідкому стані, а також у вигляді емульсій і лаків. Технологічний процес складається з основних операцій: 1) підготовка сировини (плавка фенолу, підготовка формаліну), 2) дозування та завантаження сировини в реактор; 3) конденсація (варіння) смоли; 4) сушка і слив смоли; 5) охолодження готової смоли і її подальша переробка.
Переробка пластичних мас може проводитися найрізноманітнішими методами. Формування виробів засноване на пластичності цих матеріалів при підвищенні температури. Основними факторами, що впливають на процес формування, є температура, час і тиск. Вироби отримують пресуванням, литтям під тиском, штампуванням, склеюванням та зварюванням окремих частин. Вибір того чи іншого методу для отримання виробів залежить від виду вихідного матеріалу і його типу, форми майбутніх виробів.
КОНТРОЛЬНІ ЗАПИТАННЯ
1.Дати визначення високомолекулярним сполукам
2.Основні типи механізмів полімеризації.
229
3.Що таке мономер.
4.Технологія отримання поліетилену високого та низького тисків. Як вказані технології впливають на властивості полімерів.
5.Наповнювачі, отверджувачі, барвники в технології отримання пластмас.
6.Технологія виробництва феноло-альдегідних смол.
230