
SML / Лекция_5
.pdf94
5 ЛИТЬЕ ПОД РЕГУЛИРУЕМЫМ ДАВЛЕНИЕМ
5.1 Общие сведения
Методы литья под регулируемым низким давлением основаны на ис-
пользовании для заполнения формы и кристаллизации расплава разницы дав-
ления газа, действующего на зеркало расплава в печи установки и в полости литейной формы (регулируемое газовое давление), или давления в металле,
создаваемого электромагнитным насосом. По величине скоростей течения ме-
талла в форме литье под регулируемым давлением занимает промежуточное
место между обычным литьем в кокиль и литьем под давлением.
Общим технологическим признаком этих методов является заполнение формы расплавом посредством выдавливания его снизу вверх из тигля уста-
новки через металлопровод под действием перепада газового давления Δp .
На рисунке 5.1 представлены упрощенные схемы установок для литья под ре-
гулируемым газовым давлением.
Если давление газа в полости формы ( pф) равно атмосферному ( pа ), а
заливка формы осуществляется благодаря созданию избыточного давления газа
над поверхностью расплава в тигле установки ( pп = p |
), то такой процесс |
||
|
|
изб |
|
называется литье под низким давлением (рисунок 5.1, a), которое равно |
|||
p = pп − р |
= р |
− ра. |
(5.1) |
ф |
изб |
|
|
Термин низкое давление используют потому, что для заполнения рас-
плавом формы требуется избыточное давление обычно не более 0,05 МПа.
Предположим, что в камерах, где расположены форма и тигель с метал-
лом, создано одинаковое, но более высокое, чем атмосферное, давление воздуха
или газа, т.е. рк = рф = рп. Далее подачу воздуха в камеру формы прекращают,
а в камеру печи подача его продолжается. Тогда за счет разницы давления р расплав будет подниматься по металлопроводу (рисунок 5.1, б). При этом
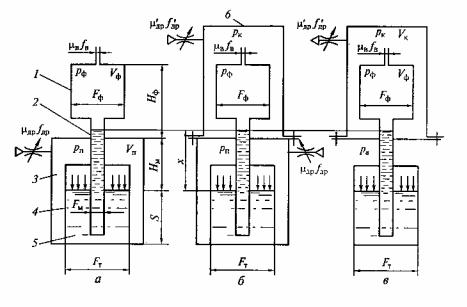
95
Рисунок 5.1 – Схемы установок для литья под регулируемым давлением:
а – под низким давлением; б – с противодавлением; в– с вакуум- ным всасыванием; 1 – литейная форма; 2 – металлопровод; 3 – герметичная печь установки; 4 – тигель с расплавом; 5 – расплав;
6 – камера, герметизирующая форму; μв , μдр , μдр' – коэффици-
енты расхода соответственно вентиляционной системы формы,
дросселя камеры печи, дросселя камеры формы; fв, fдр, fдр' –
площади сечения вентиляционной системы формы, дросселя пе- чи, дросселя камеры формы; pа – атмосферное деление; рф,
Vф , рп , Vп, рк , Vк – соответственно давление и объем формы,
свободного пространства печи, камеры для размещения формы; Fф, Fм, Fт – площади поперечного сечения рабочего про-
странства соответственно формы, металлопровода и зеркала ме- талла в печи; S – высота металла в тигле; H м – незаполненная металлом к началу процесса высота металлопровода; Нф – высо-
та напора в форме; x – уровень металла
|
|
|
96 |
р = рп − р |
= р |
− ( ра + р ) . |
(5.2) |
ф |
изб |
ф |
|
Аналогичного результата можно достичь, если на втором этапе понижать
давление В камере формы, оставляя постоянным давление в камере печи. Такие процессы называются литьем под низким давлением с противодавлением или сокращенно литьем с противодавлением.
|
Если в герметичной камере 6 с формой создавать вакуум, а над металлом |
||
в |
тигле сохранять атмосферное давление, то за счет перепада давления |
||
( |
p = pa + p |
ф |
) начнется заполнение формы. Такой способ литья называют ли- |
|
|
|
тье вакуумным всасыванием (рисунок 5.1, в).
Анализ характера движения металла при заполнении форм в рассматри-
ваемых способах показывает, что при определенных режимах наблюдаются яр-
ко выраженные колебания скорости заполнения расплавом литейной формы. В
качестве примера на рисунке 5.2 показаны изменения уровня металла (х) и ско-
рости течении металла в форме (и) при заполнении панели размером 350 × 550 × 5 мм сплавом АЛ4 на установке литья под низким давлением.
Для уменьшения отрицательного эффекта пульсации скорости заполне-
ния металлом формы применяют следующее:
∙используют первый период колебательного процесса в случае неболь-
ших невысоких отливок с малым временем заполнения формы;
∙уменьшают амплитуду колебательного процесса в случае высоких и металлоемких отливок путем правильного выбора конструктивных па-
раметров установки и технологических параметров процесса.
В целом, к снижению пульсации скорости заполнения приводят увеличе-
ние свободного пространства печи, или отношения Vп /Vф, отношения Fт / Fф,
площади сечения дросселя fдр, повышение давления воздуха или газа в реси-
вере (магистрали). Для литья вакуумным всасыванием большое значение имеют параметр ω = µв fв/(µдр fдр ) и отношение Vк /Vф.
Для всех этих способов характерны следующие общие черты:
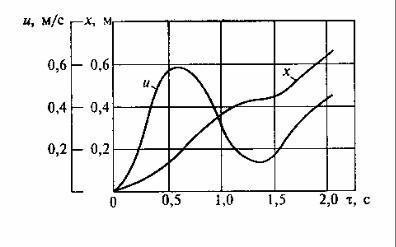
97
Рисунок 5.2 – Изменение уровня металла (х) и скорости заполнения формы (и)
при литье панели под низким давлением
98 1. Для подъема расплава из тигля установки до верхней точки полости
формы на высоту H м + H |
ф |
, т.е. для ее заполнения, необходимо приложить к |
|||
|
|
|
|
|
|
расплаву в тигле избыточное относительно формы давление равное |
|
||||
p зал |
= ρg (H м + H |
ф |
+ H ) + pпот, |
(5.3) |
|
|
|
|
|
|
где ΔH – понижение уровня расплава в тигле при заполнении формы;
pпот – гидравлические потери в системе.
2. Скорость подъема расплава можно регулировать, изменяя скорость на-
растания давления p зал. При большой скорости нарастания p зал скорость подъема расплава может стать настолько большой, что расплав будет фонтани-
ровать из металлопровода, тогда как при оптимальной скорости подъема рас-
плав быстро, но плавно заполняет полость формы.
3. Скорость нарастания давления в установке зависит от того, как быстро будет изменяться проходное сечение отверстия в регуляторе, через которое газ подается в камеру установки или отсасывается из нее, от величины давления подаваемого газа, от соотношения геометрических размеров системы в целом,
от свободных объемов камер 6 и 3 (см. рисунок 5.1, б), объема формы, а также степени прогрева таза, подаваемого в камеру установки, и т.д.
4. В связи с неустановившимся движением расплава в металлопроводе и полости формы характер и скорость его движения зависят от скорости нараста-
ния давления, геометрических характеристик системы – размеров тигля, пло-
щади его зеркала, диаметра и длины металлопровода, размеров полости формы и т.д., а также от гидравлических сопротивлений ее звеньев – металлопровода,
полости самой формы, литниковой системы.
Таким образом, установки литья под регулируемым давлением – слож-
ные динамические системы, позволяющие регулировать скорость заполнения формы расплавом. С использованием таких установок можно заполнять фор-
мы тонкостенных отливок, изменять продолжительность заполнения отдель-
ных участков формы отливок сложной конфигурации с переменной толщиной стенки с целью управления процессом теплообмена расплава и формы, доби-
99
ваясь рациональной последовательности затвердевания отдельных частей от-
ливки.
Приложение дополнительного давления на затвердевающий в форме рас-
плав обеспечивает улучшение условий питания отливки и, как результат, ее качества – механических свойств и герметичности.
В рассматриваемых процессах после заполнения формы давление дейст-
вует на расплав, который из тигля через металлопровод поступает в затверде-
вающую отливку и питает ее. Благодаря этому усадочная пористость в таких отливках уменьшается, плотность и механические свойства возрастают.
Способы литья под регулируемым давлением создают возможность уменьшения газовой и газоусадочной пористости в отливках. Например, в спо-
собе заполнения формы по схеме, показанной на рисунке 5.1, в, реализуется возможность после заполнения форм перекрыть металлопровод в верхнем се-
чении специальным затвором, а затем создать в камере установки давление,
существенно большее атмосферного. При этом отливка будет затвердевать в условиях всестороннего газового давления. Внешнее всестороннее давление уменьшает выделение газов из металла при кристаллизации отливки, препятст-
вует зарождению и росту газовых пузырьков в расплаве. За счет действия все-
стороннего давления газа объем отливки уменьшается на некоторую малую ве-
личину по ее внешним контурам, а поскольку масса расплава в форме остается прежней, то питание отливки становится более интенсивным, объем усадочных пор в ней уменьшается.
Используя ту же схему установки (см. рисунок 5.1, б), можно в начале процесса создать в камерах 6 и 3 вакуум и осуществить дегазацию расплава, а
затем, понизив давление в камере 6, заполнить форму в условиях вакуумного всасывания. Дегазация расплава приводит к понижению содержания раство-
ренных в расплаве газов и уменьшению пористости отливок. Возможен и дру-
гой ход процесса: после дегазации расплава и заполнения формы вакуумным всасыванием перекрыть затвором металлопровод в верхнем сечении и создать в камере 6 избыточное давление, осуществляя кристаллизацию отливки в усло-
100
виях всестороннего газового давления. Такой способ литья получил название вакуумно-компрессионное литье. Применение этого способа литья обеспечива-
ет возможность резко уменьшить газоусадочную пористость в отливках, повы-
сить их герметичность и механические свойства.
Литье под регулируемым давлением осуществляется на специальных ус-
тановках, в которых процесс заполнения формы расплавом выполняется авто-
матически. Конструкции установок и машин для этих литейных процессов час-
то предусматривают и автоматизацию операций сборки и раскрытия форм, вы-
талкивания отливки и ее удаления из формы. Таким образом, процессы литья под регулируемым давлением обеспечивают, наряду с высоким качеством от-
ливок, возможность автоматизации их производства.
В практике наибольшее применение нашли следующие процессы литья под регулируемым давлением: литье под низким давлением; литье под низким давлением с противодавлением; литье вакуумным всасыванием; литье вакуум-
ным всасыванием с кристаллизацией под давлением, т. е. вакуумно-
компрессионное литье.
5.2 Литье под низким давлением
Установки для литья под низким давлением обычно состоят из механиз-
мов сборки и разборки форм, отделения отливок от формы и стержней (по су-
ществу это элементы кокильной машины), агрегата заливки (печи-металло-
раздатчика), гидравлической, пневматической и электрической систем управ-
ления. Многочисленные конструкции разработанных универсальных и специа-
лизированных установок различаются: размерами рабочей зоны для размеще-
ния формы, числом подвижных элементов для сборки и разборки формы, типа-
ми печей-металлораздатчиков, компоновочной схемой, реализующей варианты обслуживания отдельных агрегатов установки, степенью автоматизации вспо-
могательных операций.
Ha рисунке 5.3 показана одна из установок литья под низким давлением для получения отливок из алюминиевых сплавов в металлических формах с го-
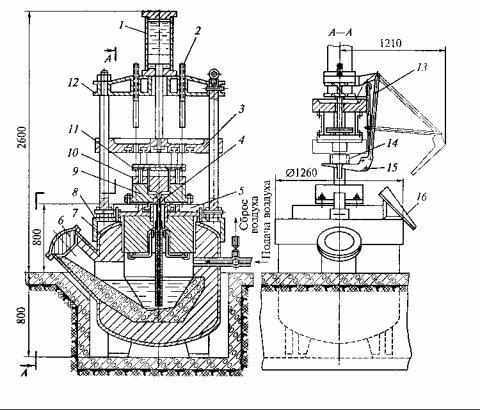
101
Рисунок 5.3 – Установка литья под низким давлением для получения отливок
из алюминиевых сплавов;
1 – гидроцилиндр; 2 – штанги для движения плиты толкателей; 3
– подвижная траверса; 4 – металлопровод; 5 – плита; 6 – крышка заливочного окна; 7 – металлораздатчик; 8 – рама печи; 9 – нижняя половина формы; 10 – верхняя половина формы; 11 – плита толкателей; 12 – неподвижная траверса; 13 – рычажный механизм; 14 – отливка; 15 – приемный лоток; 16 – склиз
102
ризонтальной плоскостью разъема. Металлораздатчик установки 7 – гермети-
зированная электропечь сопротивления ванного типа с заливочной горловиной,
закрывающейся футерованной крышкой 6 на поролоновой прокладке. На раме печи 8 расположена плита 5 с металлопроводом 4 из жаростойкого материала.
К нижней стороне этой плиты на болтах подвешен свод печи с нагревателями, а
на верхней плоскости закреплена нижняя неподвижная половина формы 9.
Верхняя половина формы 10 крепится в пазах подвижной траверсы 3. На не-
подвижной траверсе 12 размещен гидроцилиндр, предназначенный для пере-
мещения верхней половины формы. Регулируемые по высоте штанги 2 служат для выталкивания отливки плитой толкателей 11 из верхней половины формы.
Отливка 14 удаляется из рабочего пространства установки вспомогательным устройством, состоящим из приемного лотка 15, перемещаемого рычажным механизмом 13. При раскрытой форме лоток 15 находится под отливкой, при закрытой – отходит в сторону, сбрасывая отливку на склиз 16. Металлопровод 4
погружают в расплав таким образом, чтобы его конец не доходил до дна тигля на 40 – 60 мм. Полость в отливке может быть выполнена металлическим, обо-
лочковым или песчаным стержнем.
Воздух или инертный газ под давлением до 0,05 МПа через систему регу-
лирования поступает по трубопроводу внутрь камеры установки и давит на зер-
кало расплава. Вследствие разности давления в камере установки и атмосфер-
ного давления расплав поступает в форму снизу через металлопровод со скоро-
стью, регулируемой давлением в камере установки. После окончания заполне-
ния формы давление в системе можно увеличивать до конца затвердевания от-
ливки, после чего автоматически открывается клапан, соединяющий камеру ус-
тановки с атмосферой. Давление воздуха в камере снижается до атмосферного и незатвердевший расплав из металлопровода сливается в тигель. После охла-
ждения отливки до заданной температуры форма раскрывается, отливка вытал-
кивается и цикл повторяется.
Литье под низким давлением применяется и самостоятельно, и как до-
полнение к другим способам литья в качестве эффективного метода автомати-
103
ческого заполнения формы жидким металлом. В последнем случае удобство способа связано с отсутствием необходимости герметизации формы. Его ис-
пользуют для получения отливок в песчаные, металлические и графитовые формы. Самостоятельно способ литья под низким давлением используют чаще для литья в кокили или в кокили с песчаными оболочковыми стержнями, так как процесс сборки кокиля легче автоматизировать.
Способ литья под низким давлением характеризуется следующими ос-
новными преимуществами, определяющими области его распространения и конструктивные особенности установок:
1. Управление гидродинамическими параметрами течения металла позво-
ляет заполнить форму с минимальными потерями теплоты, что особенно важно для сложных тонкостенных крупногабаритных отливок. Заполняемость форм возрастает в 1,3 – 1,5 раза.
2. При подводе металла в наиболее массивные части отливок питание их в процессе кристаллизации осуществляется через металлопровод, что позволяет упростить конструкцию литниково-питающей системы, сократить расход жид-
кого металла на нее, так как часто отсутствует необходимость устанавливать прибыли.
3. Избыточное давление в сплаве после заполнения формы улучшает ус-
ловия питания кристаллизующихся его слоев, как в тонких, так и в массивных сечениях отливки, увеличивает скорость затвердевания металла благодаря ин-
тенсификации теплообмена его с формой. Это способствует повышению плот-
ности, измельчению структуры металла отливок. В результате чего прочность металла увеличивается на 15 – 25%, а пластичность в 1,5 – 2 раза.
4. Подача металла в форму снизу обеспечивает ее плавное заполнение,
уменьшение развития эффектов разбрызгивания и перемешивания металла,
способствующих его окислению и захвату воздуха.
5. Уменьшается возможность окисления металла в печи и исключается вероятность попадания в форму шлака и флюса с зеркала расплава, так как ме-
талл поступает в форму из глубинных слоев ванны печи.