
SML / Лекция_5
.pdf104
6. Полностью решена проблема автоматизации процесса заливки литей-
ной формы жидким металлом.
7. Низкие в сравнении с литьем под давлением скорости течения металла при заполнении формы позволяют использовать как металлические, так и разо-
вые элемента формы из других менее прочных материалов, что накладывает меньше ограничений на конструктивное оформление отливок.
8.Повышенная скорость затвердевания и охлаждения отливок сокращает
в1,5 раза время выдержки отливки в металлической форме по сравнению с литьем в кокиль, что увеличивает производительность установок.
Наряду с указанными выше преимуществами способ литья под низким давлением имеет недостатки, в числе которых: невысокая стойкость части ме-
талоопровода, постоянно погруженной в расплав (это затрудняет использова-
ние способа для таких сплавов с высокой температурой плавления, как чугун и сталь); сложность регулирования скорости потока расплава в форме, вызванная скоротечностью операции и динамическими процессами, происходящими в ус-
тановке при заполнении ее камеры воздухом; возможность изменения свойств сплава при длительной выдержке его в печи установки.
Преимущества и недостатки способа определяют рациональную область его применения. Основную долю продукции литья под низким давлением со-
ставляют отливки из алюминиевых сплавов. Реже этим способом изготовляют отливки из медных сплавов, стали и чугуна, в том числе высокопрочного с тол-
щиной стенки до 3 мм (в песчаную форму). Минимальная толщина стенок от-
ливок из алюминиевых сплавов, полученных этим способом, равна 1,5 мм,
средняя толщина для крупных отливок – 3 – 6 мм. Для медных сплавов мини-
мальная толщина стенок отливок – 3 мм. Характерную номенклатуру отливок,
полученных литьем под низким давлением, составляют:
∙отливки, к которым предъявляются повышенные требования по плот-
ности, герметичности и прочности (рабочие колеса и другие детали гидравлических устройств, корпусные детали лодочных моторов, дис-
ки автомобильных колес, другие силовые детали);
105
∙протяженные тонкостенные отливки, для которых при гравитационной заливке трудно обеспечить заполнение формы (оболочковые и корпус-
ные отливки, роторы электродвигателей, выпускные коллекторы и др.),
∙разностенные отливки с одним или несколькими тепловыми узлами,
питание которых может быть обеспечено одним или несколькими ме-
таллопроводами (блоки и крышки цилиндров, картер маховика и др.).
Вкрупносерийном и массовом производстве часть отливок производят на специализированных установках для изготовления одной или однотипных де-
талей. При этом динамические характеристики системы изменяются незначи-
тельно, и процесс литья становится более устойчивым.
Особенности формирования отливки при литье под низким давлени-
ем. Заполнение форм расплавом при этом способе литья может осуществляться со скоростями потока, которые можно регулировать. Для получения качествен-
ных отливок предпочтительно заполнять форму сплошным потоком при скоро-
стях, обеспечивающих последовательное заполнение формы, исключающее за-
хват воздуха расплавом, образование в отливках газовых раковин, попадание в них оксидных плен и неметаллических включений. Однако неизбежное при этом уменьшение скорости потока, необходимое для сохранения его сплошно-
сти, сопряжено с возможностью преждевременного охлаждения и затвердева-
ния расплава, т.е. с процессами, недопустимыми в период до полного заполне-
ния формы. Поэтому, как и в других литейных процессах, при литье под низ-
шим давлением важно согласование гидравлических и тепловых режимов за-
полнения формы расплавом.
5.3 Литье с магнитодинамической подачей металла в форму
Процесс, похожий на литье под низким давлением, осуществляют, ис-
пользуя магнитодинамический принцип подачи расплава в форму. По одному из вариантов магнитодинамического насоса расплав из тигля 3 (рисунок 5.4)
попадает в металлопровод 1 (центральнай канал) через два боковых вертикаль-
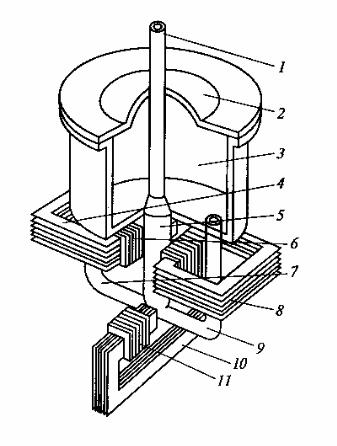
106
Рисунок 5.4 – Схема магнитодинамического насоса:
1 – металлопровод; 2 – крышка печи; 3 – тигель с расплавом; 4, 8
– индукторы; 5 – центральный канал; 6 – обмотка индукторов; 7,
9 – боковые каналы, 10 – электромагнит; 11 – обмотки магнита
107
ных канала 7 и 9, а также через горизонтальные каналы. Участок соединения каналов расположен в межполюсном зазоре электромагнита 10. При включении обмоток индукторов в сеть переменного тока в металле возникает электриче-
ский ток, который, взаимодействуя с внешним магнитным потоком, создает давление, действующее на расплав.
При наличии двух индукторов раздельное управление электромагнитны-
ми системами обеспечивает различные функциональные возможности такой установки.
1. Режим насоса – при синфазном включении индукторов и электромаг-
нита металл из печи по боковым каналам поступает в центральный канал – маг-
нитопровод под некоторым давлением, величина которого определяется элек-
трическими параметрами индукторов и электромагнита.
2. Режим стопора – при реверсивном включении электромагнита направ-
ление движения металла изменяется на обратное. Выбором режимов работы индукторов и электромагнита можно поддерживать необходимый уровень ме-
талла в металлопроводе.
3. Режим хранения – при противофазном включении индукторов через металл в каналах протекает удвоенный ток, а металл циркулирует в ванне печи,
поступая через один боковой канал и вытекая через другой. Выбором режима работы индукторов можно поддерживать необходимую температуру металла в печи.
Общими признаками этого процесса с литьем под низким давлением яв-
ляются величины скоростей течения металла в форме и сходная методика оп-
ределения гидравлических и тепловых параметров литья. Однако, в отличие от установок с газовым давлением, при этом способе не требуется герметизация металлораздатчика, что позволяет доливать металл в металлораздатчик без ос-
тановки процесса литья. К дополнительным преимуществам магнитодинами-
ческого процесса относятся следующие:
∙отсутствие сжимаемой газовой среды в камере установки упрощает реализацию необходимых режимов литья;
108
∙повышенная, по сравнению с литьем под низким давлением, точность выполнения заданных режимов из-за меньшей инерционности элек-
тромагнитного воздействия;
∙улучшенные условия регулирования тепловых условий литья (можно обеспечить перегрев расплава непосредственно в канале металлопро-
вода).
Котличиям негативного характера относятся: большая опасность выде-
ления растворенного в расплаве газа и попадания его в отливку из-за отсутст-
вия избыточного давления в ванне расплава, а также большая сложность экс-
плуатации установок.
5.4 Литье с противодавлением
Данный способ литья является развитием способа литья под низким дав-
лением. Установка для литья с противодавлением (рисунок 5.5, а) состоит из двух камер I и II. В камере I, устройство которой подобно герметической каме-
ре установки литья под низким давлением, располагается тигель 7 с расплавом
6. В камере II находится форма 3 (обычно металлическая). Камеры I и II разде-
лены герметичной крышкой 4, через которую проходит металлопровод 2, со-
единяющий тигель 7 и форму 3. Камеры I и II прочно соединены одна с другой зажимами 5.
В начале процесса сжатый воздух или инертный газ при требуемом по технологии давлении, например 0,12 МПа, поступает через вентили 8 – 10 в
камеры I и II. Вентиль 1 при этом закрыт, и расплав в тигле 7 остается непод-
вижным. По достижении заданного давления вентиль 10 закрывается, а вентиль
1 постепенно открывается. В результате давление в камере II понижается, и
под действием разности давлений в камерах I и II расплав поднимается по ме-
таллопроводу и заполняет форму.
Можно, наоборот, повысить давление в камере печи через вентиль 8. По-
сле заполнения формы давление в камерах I и II можно повысить, сохраняя их
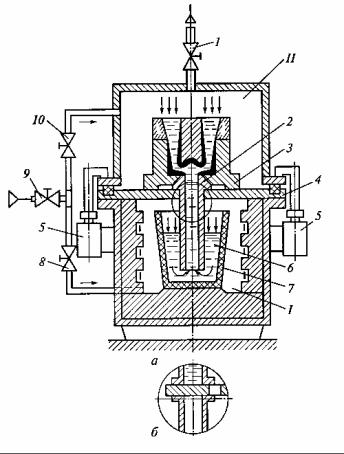
109
Рисунок 5.5 – Схема установки для литья с противодавлением (а) и устройства
для перекрытия металлопровода (б):
1, 8–10 – вентили пневмосистемы установки; 2 – металлопровод; 3 – форма; 4 – крышка печи; 5 – зажим; 6 – расплав; 7 – тигель; прямыми стрелками показано направление действия воздуха на расплав; I и II – нижняя и верхняя камеры установки
110
перепад равным таковому в период заполнения формы. Обычно значение дав-
ления при кристаллизации отливки выше, чем при литье под низким давлением
(0,4 – 0,6 МПа), что улучшает питание отливки, уменьшает усадочную и газо-
вую пористость, повышает плотность отливки. По существу в этом процессе совмещены два способа литья: способ литья под низким давлением, исполь-
зуемый для заполнения полости формы, и способ кристаллизации отливок под всесторонним давлением газа или воздуха.
Давление воздуха, при котором происходит заполнение формы распла-
вом, будет равно разности давлений в нижней pI и верхней pII камерах уста-
новки: p = pI − pII . Скорость подъема расплава в металлопроводе и полости формы так же, как и при литье под низким давлением, будет зависеть от всей совокупности конструктивных и пневматических характеристик системы, оп-
ределяющих скорость нарастания разности давлений p во время работы ус-
тановки. Поэтому закономерности процессов заполнения формы, приведенные ранее, справедливы и для процесса литья под низким давлением с противодав-
лением.
Необходимо учитывать, что при повышении давления увеличивается плотность используемого газа, что сопровождается увеличением его теплопро-
водности. В результате время, как охлаждения, так и последующего затверде-
вания отливок при литье с противодавлением может сократиться на 10 – 20%.
Наряду с рассмотренным вариантом конструкции установок для литья с противодавлением используют также установки с механическим перекрытием металлопровода после заполнения формы затвором специальной конструкции
(рисунок 5.5, б), установленным в месте, обозначенном на рисунке 5.5, а круж-
ком. В установках такого типа по окончанию заполнения формы и перекрытия металлолровода затвором давление в нижней камере понижается до атмосфер-
ного, а в верхней повышается до необходимого технологического. Такие уста-
новки могут иметь менее прочную нижнюю камеру.
В отличие от литья под низким давлением при литье с противодавлением

111
заполнение литейной формы происходит в условиях всестороннего повышен-
ного газового давления. Это препятствует выделению растворенных в металле газов не только при затвердевают отливки, но и при течении расплава в форме.
Отмеченное явление, наряду с кристаллизацией отливки под более высоким га-
зовым давлением и с повышенной скоростью, приводит к измельчению струк-
туры металла, улучшению его физико-механических и эксплуатационных свойств (таблица 5.1).
Таблица 5.1 – Пределы прочности (σ в ) отливок из сплава АЛ9, полученных
разными способами
Способ литья |
σ в , МПа |
|
|
Литье в кокиль |
130 – 150 / 200 – 220 |
|
|
Литье под низким давлением |
165 – 180 / 220 – 225 |
|
|
Литье с противодавлением |
170 – 185 / 225 – 250 |
|
|
Примечание: В числителе – предел прочности литого металла, в знаменателе – после закалки с кратковременным искусственным старением
Способ литья с противодавлением дает наибольший эффект при изготов-
лении отливок с массивными стенками равномерной толщины из алюминиевых и магниевых сплавов, кристаллизующихся в широком интервале температур.
Использование второй стадии процесса – кристаллизации под всесторонним избыточным давлением – для тонкостенных отливок не всегда приводит к за-
метному улучшению их свойств. Это объясняется тем, что продолжительность кристаллизации тонкостенных отливок мала, т.е. в данном случае отливка за-
твердевает прежде, чем давление в верхней камере установки достигнет необ-
ходимой величины.
112
5.5 Литье вакуумным всасыванием
Принцип литья вакуумным всасыванием состоит в том, что расплав за-
полняет форму под действием разрежения, создаваемого в ее полости, после чего при затвердевании металла образуется отливка. Скорость заполнения фор-
мы расплавом можно регулировать, изменяя разность между атмосферным давлением и давлением в полости формы.
Кроме общих преимуществ, характерных для способов литья под регули-
руемым давлением, литье вакуумным всасыванием имеет ряд своих досто-
инств, а именно:
∙увеличенная заполняемость полости формы жидким металлом, что позво-
ляет получать особо тонкостенные отливки (толщина стенки до 1 мм, а
иногда и меньше);
∙отсутствие необходимости герметизации печи с жидким металлом, что упрощает конструкцию установок и их обслуживание.
Однако последнее обстоятельство ухудшает условия длительного хране-
ния расплавов, склонных к окислению. Используют два варианта установок для литья вакуумным всасыванием.
Установки первого типа (рисунок 5.6) имеют две камеры: нижнюю I и
верхнюю II. Нижняя камера I представляет собой раздаточную печь с электри-
ческим или газовым обогревом, в которой располагается тигель 3 с расплавом.
Верхняя камера II расположена на крышке 4 нижней камеры. В крышке 4 раз-
мещен металлопровод 5.
Форму 6 устанавливают и закрепляют в камере II так, чтобы литник 7 со-
единялся с металлопроводом 5. Верхняя камера II герметически соединяется с крышкой 4 при помощи цилиндра прижима 1. Полость верхней камеры через вакуумпровод 2 соединена с ресивером, в котором насосом создается разреже-
ние, регулируемое системой управления.
В начале цикла клапан управления открывается, в камере II создается разрежение. При этом расплав за счет разности давлений и камерах I и II по
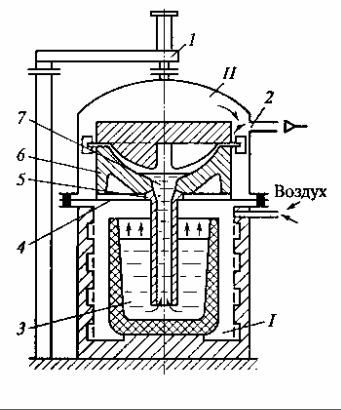
113
Рисунок 5.6 – Схема установки для литья ваккумным всасыванием:
1 – прижим камеры II; 2 – вакуумпровод; 3 – тигельная печь со- противления; 4 – крышка нижней камеры; 5 – металлопровод; 6 – форма; 7 – литниковая система; I, II – камеры