
SML / Лекция_5
.pdf114
металлопроводу 5 поднимается, заполняя полость формы. После затвердевания отливки клапан системы управления соединяет полость камеры II с атмосфе-
рой, давление в верхней и нижней камерах становится одинаковым, и остатки незатвердевшего расплава сливаются из металлопровода 5 в тигель 3. Камера II
снимается, форма 6 с отливкой извлекается, и цикл может повторяться.
Предпочтительной номенклатурой отливок для этого способа являются различные колеса вентиляторов с прямыми и изогнутыми лопатками, колеса компрессоров с лопатками толщиной 0,7 – I мм и др.
При литье вакуумным всасыванием улучшаются механические свойства отливок. Например, по сравнению с литьем в кокиль предел прочности отливок из алюминиевого сплава АЛ9 увеличивается на 5 – 10%, а относительное удли-
нение – на 30 %. Это объясняется лучшими условиями питания отливки через металлопровод.
Установки второго типа используют только для литья слитков и загото-
вок простой конфигурации в водоохлаждаемые кристаллизаторы. Носок ме-
таллического водоохлаждаемого кристаллизатора 1 (рисунок 5.7) погружается в расплав, находящийся в тигле 2 раздаточной печи. Рабочая полость кристал-
лизатора, образующая отливку, соединяется вакуумпроводом с вакуумным ре-
сивером 3. Разрежение в системе создается вакуумным насосом 6 и регулиру-
ется натекателем 5. Поворотом распределительного крана 4 рабочая полость кристаллизатора соединяется с вакуумным ресивером 3, при этом в полости кристаллизатора создается разрежение, и расплав поступает внутрь кристалли-
затора.
После затвердевания отливки носок кристаллизатора извлекают из рас-
плава, поворотом крана 4 рабочую полость соединяют с атмосферой и отливка выпадает из кристаллизатора в приемный короб.
Особенности формирования отливки. Форма может заполняться рас-
плавом с требуемой скоростью, плавно без разбрызгивания, сплошным фрон-
том. Расплав, заполнивший форму, затвердевает в условиях вакуума. Газы, со-
держащиеся в расплаве, могут выделяться из него, благодаря чему создаются
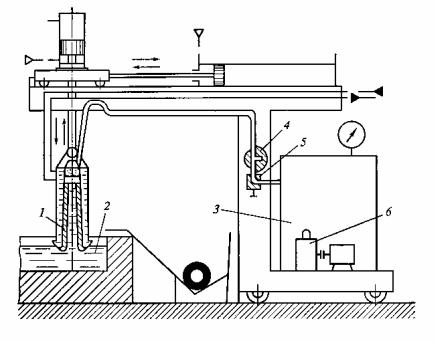
115
Рисунок 5.7 – Схема установки для литья слитков, втулок, гильз способом ва-
куумного всасывания:
1 – водоохлаждаемый кристаллизатор; 2 – тигель с расплавом; 3 – вакуумный ресивер; 4 – вакуумный кран; 5 – регулирующий на- текатель; 6 – вакуумный насос
116
условия для получения отливок без газовых раковин и пористости. Одновре-
менно под действием давления воздуха на зеркало расплава последний посто-
янно питает затвердевающую отливку, в результате чего она может быть полу-
чена плотной, без усадочных дефектов. Однако для получения плотных отливок требуется согласовать скорости затвердевания и питания отливки.
Обычно при литье вакуумным всасыванием расплав засасывается в тон-
костенный металлический водоохлаждаемый кристаллизатор, в котором за-
твердевание отливки протекает с высокой скоростью. Это способствует устра-
нению ликвации в отливках.
Способом вакуумного всасывания можно получать пустотелые заготовки типа втулок без стержней. В этом случае после всасывания расплава в кристал-
лизатор и намораживания на внутренних стенках кристаллизатора корочки твердого расплава заданной толщины вакуум отключается и незатвердевший расплав сливается обратно в тигель. Таким способом получают плотные заго-
товки втулок без газовых и усадочных раковин и пористости. Однако внутрен-
няя поверхность втулок бывает волнистой из-за неравномерного затвердевания металла. Это приводит к необходимости увеличения припуска на обработку ре-
занием внутренней поверхности втулки. Для уменьшения припуска можно от-
ливать такие заготовки с применением стержня, установленного внутри кри-
сталлизатора.
Литьем вакуумным всасыванием получают отливки из легких и медных сплавов, чугуна и стали. Наиболее часто его используют для литья заготовок втулок, вкладышей, подшипников скольжения из дефицитных и дорогостоящих медных сплавов.
5.6 Вакуумно-компрессионное литье
Данный способ литья совмещает процесс предварительного вакуумиро-
вания расплава для понижения содержания в нем газов, заливку расплава в форму вакуумным всасыванием и воздействие всестороннего давления воздуха
117
на затвердевающую отливку.
Установка (рисунок 5.8) состоит из двух камер, в верхней из которых рас-
полагается металлическая или песчаная форма 1, литниковая система которой соединяется с верхней частью металлопровода 3. Форму покрывают стальным колпаком 2 и для герметичности запирают специальными затворами. В нижней камере размещают тигель 4, после чего камеру закрывают герметичной крыш-
кой 5. Камеры формы и тигля соединяются с вакуумной системой трубопрово-
дами 7 и 8 для дегазации расплава и формы. По окончанию дегазации гидроци-
линдр 6 поднимает тигель с расплавом, и металлопровод погружается в металл.
Затем давление в камере формы постепенно снижают, создавая в нижней и верхней камерах разность давлений, за счет которой расплав из тигля поступает в полость формы. Разность давлений в камерах формы и тигля обычно не пре-
вышает 25 кПа. После заполнения формы отверстие металлопровода перекры-
вают, и в камеру формы по трубопроводу 8 подают сжатый воздух. При этом отливка затвердевает под всесторонним давлением. При затвердевании отливки в форме давление в верхней камере выше давления выделения газов из раство-
ра, поэтому оставшиеся после вакуумирования газы из расплава не выделяют-
ся, и газовая пористость не образуется. Это способствует улучшению механи-
ческих свойств материала отливки.
Особенности использования литья под регулируемым давлением в массовом и мелкосерийном производстве. При использовании методов литья под регулируемым газовым давлением в массовом производстве, важной явля-
ется проблема производительности установок. Поэтому представляет интерес использование многопозиционных машин для литья под низким давлением и литья вакуумным всасыванием, аналогичных карусельным кокильным маши-
нам. В таких машинах отделение кокиля и металлораздатчика от металлопро-
вода происходит на позиции заливки после заполнения формы металлом и его затвердевания. Дальнейшее охлаждение отливки, извлечение ее из формы и сборку кокиля проводят на других позициях карусели.
В мелкосерийном производстве некрупных предприятий острее стоит

118
Рисунок 5.8 – Схема установки вакуумно-компрессионного литья:
1 – форма; 2 – стальной колпак; 3 – металлопровод; 4 – тигель с расплавом; 5 – крышка нижней камеры; 6 – гидроцилиндр подъе- ма тигля с расплавом; 7, 8 – трубопроводы пневмосистемы уста- новки
119
проблема загрузки специального оборудования из-за недостатка номенклатуры изделий с экономически оправданным объемом производства. В этих условиях может оказаться эффективным использование универсальных комбинирован-
ных установок литья под регулируемым газовым давлением, позволяющих реа-
лизовать несколько рассмотренных ранее технологических процессов или их комбинаций.
Основным требованием при создании такого оборудования является на-
личие двух надежно герметизированных камер для расплава и формы. Из вы-
пускаемых в настоящее время машин этому требованию полнее отвечают уста-
новки для литья с противодавлением. Дополнительно оснащенные специаль-
ными модулями, эти установки обеспечивают получение отливок методами ли-
тья под низким давлением, с противодавлением, вакуумным всасыванием, ли-
тья в вакуумируемую форму и возможными комбинациями этих методов.
Опыт показывает, что использование такой универсальной установки по-
зволяет увеличить коэффициент загрузки оборудования с 0,2 – 0,4 до 0,7 – 0,8.
При этом приблизительно 15% всех отливок изготовляются с применением ва-
куумного модуля, на долю литья с противодавлением приходится приблизи-
тельно 10 – 15%, а на литье под низким давлением – 70 – 75%.