
Металловедение
.pdf241
Нержавеющие стали. Углеродистые и низколегированные стали не ус-
тойчивы против коррозии. Антикоррозионными свойствами обладает сталь в том случае, если она содержит большое количество хрома или хрома и никеля.
Химический состав некоторых нержавеющих сталей приведен в табл.15.
Хромистые нержавеющие стали. Содержание хрома в нержавеющей ста-
ли должно быть не менее 12%. При меньшем содержании хрома сталь не спо-
собна сопротивляться коррозии, так как ее электродный потенциал становится отрицательным.
Наибольшая коррозионная стойкость стали 12X13 (мартенситно-
ферритного класса) достигается после закалки в масле с температуры 1000-
1100° С, отпуска при 700-750° С и полировки. Структура после термической обработки - феррит и карбиды хрома. Твердость НВ200-250. Эта сталь стойка в слабоагрессивных средах (воздух, вода, пар). Применяется для деталей с повы-
шенной пластичностью (клапаны гидравлических прессов, предметы домаш-
него обихода и др.).
Таблица 15
Химический состав (%) некоторых нержавеющих сталей (ГОСТ 5632-72)
Марка стали |
Класс стали |
Элементы |
|
|
Прочие |
|
|
|
|
|
элементы |
|
|
С |
Сг |
Ni |
|
|
|
|
|||
|
|
|
|
|
|
12X13 |
Мартеисптно- |
0,09-0,15 |
12-14 |
- |
- |
|
ферритный |
|
|
|
|
40X13 |
Мартенсит- |
0,36-0,45 |
12-14 |
- |
- |
|
ный |
|
|
|
|
12X17 |
Ферритный |
≤0,12 |
16-18 |
- |
- |
0КХ17Т |
» |
≤0,08 |
16-18 |
- |
5.С-0,8 Ti |
12Х18НЭ |
Аустенитный |
≤0,12 |
17-19 |
8-10 |
- |
12Х18Н9Т |
|
≤0,12 |
17-19 |
8-10 |
5.С-0,8 Ti |
|
» |
|
|
|
|
04Х18Н10 |
» |
≤0,04 |
17-19 |
9-11 |
- |
10Х14П4НЗ |
» |
0,09-0,14 |
12,5-14 |
2,8- |
1315 Mn |
|
|
|
|
3,5 |
|
09X15Н8Ю |
Аустенитно- |
≤0,09 |
14-16 |
7-9,4 |
0,7-1,3 А1 |
|
мартснснтный |
|
|
|
|
08Х21Н6М2Т |
Аустенитно- |
≤0,08 |
20-22 |
5,5- |
1,8-2,5 Мо |
|
фсррптный |
|
|
6,5 |
0,2-0,1 Ti |
|
|
|
|
|
|
242
Сталь 40X13 (мартенситного класса) применяют после закалки в масле с температуры 1000-1050° С и отпуска при температуре 180-200° С со шлифо-
ванной и полированной поверхностью. После термической обработки эта сталь обладает высокой твердостью (HRC52-55), структура мартенсит; применяется для хирургических инструментов, пружин, предметов домашнего обихода и др.
Более коррозионностойка (в кислотных средах) сталь ферритного класса
12X17, применяемая (в отожженном состоянии) для оборудования азотнокис-
лотных заводов и заводов пищевой промышленности. Для изготовления свар-
ных конструкций эта сталь не рекомендуется в связи с тем, что при нагреве ее до температур выше 900-950° С и быстрого охлаждения (при сварке) происхо-
дит обеднение периферийной зоны зерен хромом (ниже 12%), вследствие выде-
ления карбидов хрома на их границах, что приводит к межкристаллитной кор-
розии.
Для предотвращения этого вида коррозии применяют сталь с титаном
(08Х17Т). Титан связывает углерод в тугоплавкие карбиды TiC, не растворяю-
щиеся в феррите при нагреве, и поэтому выделения карбидов хрома и обедне-
ния хромом периферийной зоны зерен не происходит. Сталь 08Х17Т применя-
ют для тех же целей, что и сталь 12X17, а также и для сварных конструкций.
Хромоникелевые нержавеющие стали. Эти стали содержат большое ко-
личество хрома и никеля, мало углерода и относятся к аустенитному классу.
Кроме аустенита, в этих сталях находятся карбиды хрома.
Для получения однофазной структуры аустенита сталь (например, 12X18119) закаливают в воде с температуры 1100-1150° С; при этом достигает-
ся наиболее высокая коррозионная стойкость, но прочность сравнительно не-
высокая. Для повышения прочности сталь подвергают холодной пластической деформации и применяют в виде холоднокатаного листа и ленты для различных деталей.
243
Так же как и хромистая сталь ферритного класса, сталь 12Х18Н9 склонна к межкристаллитной коррозии при нагреве закаленной стали до 550-750° С (на-
пример, при сварке или при работе в условиях повышенных температур). При-
чины возникновения межкристаллитной коррозии те же - обеднение перифе-
рийной зоны зерен хромом ниже 12% вследствие выделения из аустенита кар-
бидов хрома.
Для предотвращения межкристаллитной коррозии в состав стали вводят титан (например, сталь 12Х18Н9Т) или снижают в стали содержание углерода
(например, сталь 04Х18Н10).
Хромоникелевые нержавеющие стали аустенитного класса имеют боль-
шую коррозионную стойкость, чем хромистые нержавеющие стали, и их широ-
ко применяют в химической, нефтяной и пищевой промышленности, в авто-
строении, транспортном машиностроении, а также в строительстве.
Для экономии дорогостоящего никеля его частично заменяют марганцем.
Например, сталь 10Х14Г14НЗ рекомендуется как заменитель стали 12Х18Н9.
Сталь аустенитно-мартенситного класса 09Х15Н8Ю применяют для тяжелона-
груженных деталей, работающих в атмосферных, уксуснокислых и других со-
левых средах и для упругих элементов. Сталь аустенитно-ферритного класса
08Х21Н6М2Т применяют для изготовления деталей и сварных конструкций,
работающих в средах повышенной агрессивности - уксуснокислых, сернокис-
лых, фосфорнокислых.
Рассмотрим теперь стали с особыми физическими свойствами.
§ 2. Магнитные стали и сплавы
Основными характеристиками магнитных сталей и сплавов являются сле-
дующие магнитные свойства: остаточная индукция Вr, выраженная в гауссах
(Гс), коэрцитивная сила Нc - в эрстедах (Э) и магнитная проницаемость μ.
Магнитная проницаемость μ = B/H, где В - магнитная индукция, т. е.
число магнитных силовых линий, проходящих через 1 см2 сечения образца;
244
Н - напряжение магнитного поля (намагничивающая сила), т. е. сила, с которой магнитное поле действует на изолированный магнитный полюс, равный едини-
це, Э.
Если магнитная проницаемость положительная, т. е. больше единицы, то такие тела называются парамагнитными, а если отрицательная (меньше едини-
цы), то - диамагнитными. Частным случаем парамагнитных тел являются фер-
ромагнитные тела - железо, никель и кобальт, магнитная проницаемость кото-
рых во много раз больше, чем у других парамагнитных тел.
Магнитные сплавы в зависимости от коэрцитивной силы и магнитной проницаемости делят на магнитотвердые - сплавы с большой коэрцитивной си-
лой, малой магнитной проницаемостью, их применяют для постоянных магни-
тов, и магнитомягкие, для которых характерны малая коэрцитивная сила и вы-
сокая магнитная проницаемость (трансформаторная и динамная стали).
Магнитотвердые стали и сплавы. Эти стали и сплавы, применяемые для изготовления постоянных магнитов, имеют большую устойчивую коэрци-
тивную силу. Такими материалами являются высокоуглеродистые стали, леги-
рованные стали и специальные сплавы, химический состав и магнитные свой-
ства которых приведены в табл. 16.
Таблица 16
Химический состав (%) и магнитные свойства некоторых сталей и спла-
вов для постоянных магнитов
Марка |
Элементы |
|
|
|
Магнитные свойства |
||
стали |
С |
Сr |
Со |
Ni, AI, Сu |
остаточ- |
коэрци- |
|
|
|
|
|
|
ная |
ин- |
тивная |
|
|
|
|
|
дукция Вr, |
сила Нc, Э |
|
|
|
|
|
|
Гс |
|
|
|
|
|
|
|
не менее |
|
|
ЕХ |
0,95-1,10 |
1,30-1,60 |
- |
- |
9 000 |
|
53 |
ЕХЗ |
0,90-1,10 |
2,80-3,60 |
- |
- |
9 500 |
|
60 |
ЕХ5К5 |
0,90-1,05 |
5,50-6,50 |
5,50- |
- |
8 500 |
|
100 |
Сплав |
- |
- |
6,50 24 |
14Ni; |
- |
|
- |
ЮНДК24 |
|
|
|
9Аl; 4Сu |
12 300 |
|
500 |
245
Углеродистые стали (У10 - У12) после закалки имеют достаточно боль-
шую коэрцитивную силу (Нc = 60-65 Э), но так как они прокаливаются на не-
большую глубину, то их применяют для изготовления магнитов сечением 4-7
мм.
Хромистые стали по сравнению с углеродистыми прокаливаются значи-
тельно глубже, поэтому из них изготовляют более крупные магниты. Магнит-
ные свойства этих сталей такие же, как и углеродистых; хромо кобальтовые стали имеют более высокие магнитные свойства.
Специальные магнитные сплавы имеют очень высокие магнитные свой-
ства, что позволяет изготовлять из них магниты небольшого размера, но боль-
шой мощности. Магнитные сплавы имеют очень высокую твердость, но хрупки и не обрабатываются резанием. Магниты этих сплавов изготовляют литьем или спеканием из порошка.
Магнитомягкие стали и сплавы. Эти стали и сплавы имеют малую коэр-
цитивную силу и большую магнитную проницаемость. Магнитомягкими мате-
риалами являются электротехническое железо (железо Армко), электротехни-
ческая сталь и железоникелевые сплавы (пермалои).
Электротехническое железо (марки Э, ЭА, ЗАА) содержит не более
0,04%С, имеет высокую магнитную проницаемость (μmax = = 3500-4500 Гс/Э) и
малую коэрцитивную силу (Нc = 0,8-1,2 Э) и применяется для сердечников, по-
люсных наконечников электромагнитов и др.
Электротехническая сталь (ГОСТ 802-58) содержит кремний, растворен-
ный в феррите. Он сильно увеличивает магнитную проницаемость (μmax = 8000-
17 000 Гс/Э), снижает коэрцитивную силу (Нc = 0,4-0,6 Э).
Более высокие магнитные свойства имеет крупнозернистая с определен-
ной структурой, т. е. преимущественным расположением зерен вдоль листа,
электротехническая сталь при содержании в ней менее 0,05% С.
246
Электротехническую горячекатаную сталь по содержанию кремния делят на четыре группы: низколегированная (0,8-1,8% Si) - Э11, Э12, Э13; среднеле-
гированная (1,8-2,8% Si) - Э21, Э22; повышеннолегированная (2,8-3,8% Si) -
Э31, Э32; высоколегированная (3,8-4,8% Si) - Э41 - Э48.
Буква Э означает, что сталь электротехническая, первая цифра (1-4) - со-
держание кремния (в процентах), вторая цифра (1-8) - гарантированные ГОСТ электрические и магнитные свойства. При маркировке холоднокатаной стали после первых двух цифр ставят или один нуль (например, Э310, Э340), обозна-
чающий, что сталь текстурованная, или два нуля (например, Э1100, Э3200) -
сталь малотекстурованная.
Стали групп Э1 и Э2 называют динамной сталью, а стали групп' ЭЗ и Э4 -
трансформаторной сталью. Динамная сталь содержит меньше кремния и поэто-
му по сравнению с трансформаторной сталью более пластична, но менее маг-
нитомягкая.
Трансформаторная сталь относится к ферритному классу сталей и имеет высокие магнитные свойства, но она более хрупкая.
Железоникелееые сплавы (пермаллои) - эти сплавы содержат 45-80% ни-
келя, и дополнительно их легируют хромом, кремнием-, молибденом. Магнит-
ная проницаемость этих сплазов очень вы-' сокая.
Наиболее высокие свойства имеет пермаллрй марки 79НМ (79% Ni и 4%)
Mo). После специальной термической обработки его магнитная проницае-
мость μ0 = 30 000 и μmax = 220 000 Гс/Э.
Из-за очень высокой начальной магнитной проницаемости пермаллои применяют в аппаратуре, работающей в слабых полях (телефон, радио).
Ферриты-магнитомягкие материалы, получаемые спеканием смеси по-
рошков ферромагнитной окиси железа Fe203 и окислов двухвалентных металлов типа МО (ZnO, NiO, MgO и др.). В отличие от других магнптомягких материа-
лов у ферритов очень высокое удельное электросопротивление, достигающее
247
1012 Ом·см, что определяет их применение в устройствах, работающих в облас-
ти высоких и сверхвысоких частот.
§ 3. Сплавы с высоким электросопротивлением
Эти сплавы применяют для изготовления электронагревателей и для эле-
ментов сопротивлений и реостатов.
Сплавы для электронагревателей обладают высокой жаростойкостью, вы-
соким электрическим сопротивлением, удовлетворительной пластичностью в холодном состоянии. Указанным требованиям удовлетворяют железохромоа-
люминиевые сплавы, например, марок Х13Ю4 - фехраль (≤0,15% С; 12-15% Сr; 3,5-5,5% А1), ОХ23Ю5 - хромаль (≤0,05%С; 21,5-23,5% Сr; 4,6-5,3% Аl) и ни-
келевые сплавы, например, марок X15IT60-ферронихром, содержащий 25%) Fe,
Х20Н80 - нихром. Стойкость нагревателей из железохромоалюминиевых спла-
вов выше, чем у нихромов. Сплавы производят в виде проволоки и ленты и их применяют для бытовых приборов (сплавы Х13Ю4, Х15Н60, Х20Н80), а также для промышленных и лабораторных печей (сплав ОХ23Ю5).
Сплавы для элементов сопротивления и реостатов обладают высоким электросопротивлением, малой величиной температурного коэффициента элек-
тросопротивления в области рабочих температур и неизменностью электриче-
ских свойств во времени. Указанным требованиям удовлетворяют сплавы ман-
ганин МНМцЗ-12 (11,5-13% Мn; 2,5-3,5% Ni; Сu - остальное) и константан МНМц40-1,5 (1-2% Мn; 39-41% Ni; Сu - остальное). Эти сплавы имеют очень малый температурный коэффициент электросопротивления в области темпера-
тур: манганин от -60 до +800С и константан от -60 до +350° С.
§ 4. Сплавы с заданным коэффициентом теплового расширения
Эти сплавы содержат большое количество никеля. Сплав 36Н, называе-
мый инваром (≤0,05% Си 35-37% Ni), почти не расширяется при температурах от -60 до +1000 С. Он применяется для деталей приборов, требующих постоян-
248
ных размеров в интервале климатических изменений температур (детали геоде-
зических мерных приборов и др.).
Сплав 29НК, называемый коваром (≤0,03% С; 28,5- 29,5% Ni; 17-18% Со),
имеет низкий коэффициент теплового расширения в интервале температур от -
70 до +420° С. Он применяется для деталей, впаиваемых в стекло при создании вакуумноплотных спаев,
§5. Сплавы с заданными упругими свойствами
Кэтим сплавам относится сплав 40КХНМ (0,07-0,12% С; 15-17% Ni; 19-
21% Сr; 6,4-7,4% Мо; 39-41% Со). Это высокопрочный с высокими упругими свойствами, немагнитный, коррозионностойкий в агрессивных средах сплав.
Применяется для заводных пружин часовых механизмов, витых цилиндриче-
ских пружин, работающих при температурах до 400° С.
К ним относится также сплав 42НХТЮ (≤0,05% С; 41,5- 43,5% Ni; 5,3-
5,9% Сr; 2,4-3% Ti; 0,5-1% А1). Это высокопрочный сплав с низким темпера-
турным коэффициентом модуля упругости до 100СС. Он применяется для упру-
гих чувствительных элементов, работающих при температуре до 100° С.
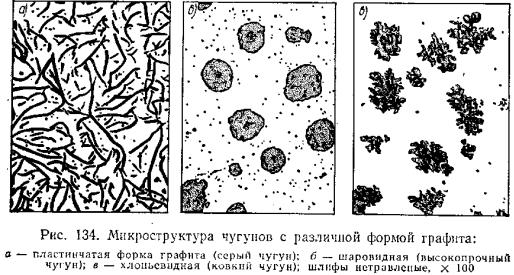
249
Глава XV
ЧУГУН
Чугуном называют сплавы железа с углеродом с содержанием более 2% С (точнее более 2,14% С -точка Е на диаграмме Fe-Fe3C, см. рис. 65).
В зависимости от состояния углерода в чугуне различают:
белый чугун, в котором весь углерод связан в цементит (структуры бело-
го чугуна рассмотрены в гл. VI);
серый чугун, в котором весь углерод находится в свободном состоянии в виде графита или часть углерода (большая) находится в виде
графита, а часть в связанном состоянии в виде цементита, но количество связанного углерода равно или меньше эвтектоидного. Форма графита пла-
стинчатая (рис. 134, а);
высокопрочный чугун, то же, что серый чугун, но форма графита шаро-
видная (рис. 134, б);
ковкий чугун, то же, что серый чугун, но форма графита хлопьевидная
(рис. 134, в).
Как видно из приведенной классификации чугуна, отличи-
тельной осо-
бенностью се-
рого, высоко-
прочного и ков-
кого чугунов
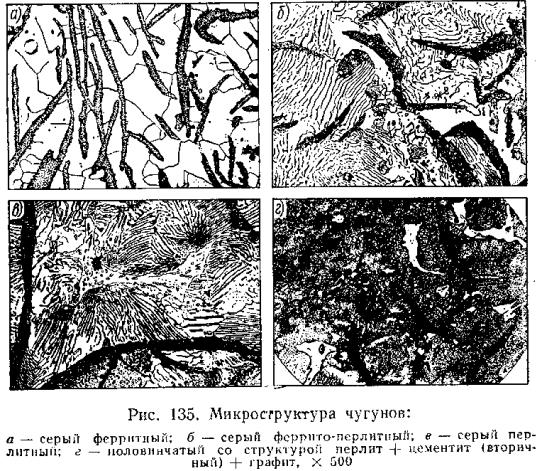
250
является наличие в структуре свободного углерода - графита. В зависимости от формы и расположения графитных включений они в большей или меньшей степени ослабляют металлическую основу, в которой находятся,
§ 1. Серый чугун
Смешанная кристаллизация. Диаграмма состояния сплавов системы же-
лезо - цементит (Fe - Fe3C, см. рис. 65) характеризует образование структур бе-
лых чугунов, в которых углерод находится в связанном состоянии в виде це-
ментита. В белых чугунах нет свободного углерода, т. е. нет графита.
Диаграмма состояния сплавов системы железо - графит (см. рис. 71) ха-
рактеризует образование структур чугуна, в котором весь углерод находится в свободном состоянии в виде графита, т. е. нет цементита и структура феррито-
графитная (рис. 135, а).