
Металловедение
.pdf221
Жаростойкость сталей аустенитного класса 800-8500 С. Для работы при
800-1100° С применяют жаропрочные сплавы на никелевой основе, например ХН77ТЮР, ХН55ВМТФКЮ для лопаток турбин. Эти сплавы стареющие и под-
вергаются такой же термической обработке (закалке и старению), как и ста-
реющие стали аустенитного класса. Жаростойкость сплавов на никелевой осно-
ве до 1200° С.

Марка стали (сплава) |
Класс стали |
|
|
Эле- |
|
|
Прочие элементы |
|
|
|
|
менты |
|
|
|
|
|
С |
Cr |
Ni |
Mo |
V |
|
|
|
|
|
|
|
|
|
15ХМ |
Перлитный |
0,11-0,18 |
0,-1,1 |
- |
0,4-0,55 |
- |
- |
12Х1МФ |
> |
0,08-0,15 |
0,9-1,2 |
- |
0,25-0,35 |
0,15-0,3 |
- |
15X11МФ |
Мартенситный > |
0,12-0,19 |
10-11,5 |
- |
0,6-0,8 |
0,25-0,4 |
- |
40Х9С2 |
> |
0,35-0,45 |
8-10 |
- |
- |
- |
2-3 Si |
20Х12ВНМФ |
Аустенитный |
0,17-0,23 |
10,5-12,5 |
0,5-0,9 |
0,5-0,7 |
0,15-0,3 |
0,5-0,9 Мп; 0,7-1,1 W |
09Х14Н16Б |
> |
0,07-0,12 |
13-15 |
14-17 |
- |
- |
1-2 Мп; 0,9-1,3 Nb |
45Х14Н14В2М |
> |
0,4-0,5 |
13-15 |
13-15 |
0,25-0,4 |
- |
2-2,8% W |
40Х15Н7Г7Ф2МС |
Сплав |
0,38-0,47 |
14-16 |
6-8 Ос- |
0,65-0,95 |
1,5-1,9 |
0,9-1,4 Si; 6-8 Мп |
ХН77ТЮР |
|
≤0,07 |
19-22 |
нова |
- |
- |
2,4-2,8 Ti; ≤0,01 В |
|
> |
|
|
|
|
|
0,0-1 Al |
ХН55ВМТФКЮ |
|
≤0,12 |
9-12 |
> |
4-6 |
0,2-0,8 |
1,4-2 Ti; 3,6-4,5 Al |
|
|
|
|
|
|
|
4,5-6,5 W |
|
|
|
|
|
|
|
12-16 Co; ≤0,02 В |
|
|
|
|
|
|
|
|
состав Химический 72) |
11 Таблица |
ГОСТ(сплавов и сталей жаропрочных некоторых (%) |
|
-5632 |
222 |
223
Глава XIII
ИНСТРУМЕНТАЛЬНЫЕ СТАЛИ И ТВЕРДЫЕ СПЛАВЫ
Инструментальные стали применяют для изготовления трех основных групп инструмента: режущего, измерительного и штампов. В связи с условиями работы инструмента к инструментальным сталям предъявляют определенные требования.
Сталь для режущего инструмента (резцы, сверла, метчики, фрезы, про-
тяжки и др.) должна обладать высокой твердостью, превышающей твердость обрабатываемого материала; износостойкостью; теплостойкостью, т. е. способ-
ностью стали сохранять при нагреве рабочей кромки, возникающем в эксплуа-
тации, структуру и свойства, необходимые для резания.
Измерительный инструмент (гладкие и резьбовые калибры и др.) служит для проверки размеров изготовляемых деталей.
Сталь для измерительного инструмента должна быть твердой и длитель-
ное время сохранять размеры и форму инструмента.
Штампы служат для деформирования металла в холодном и горячем со-
стояниях.
Сталь для штампов холодного деформирования (вытяжные, гибочные,
высадочные штампы, дыропробивные пуансоны, ролики для накатывания резь-
бы и др.) должна иметь высокую твердость, износостойкость и достаточную вязкость.
Сталь для штампов горячего деформирования (ковочные, прошивные, об-
резные штампы и др.) должна иметь высокие механические свойства, которые должны сохраняться и при повышенных температурах, глубоко прокаливаться и обладать стойкостью против разгара.
В связи с различными условиями работы инструментальные стали но на-
значению делят на следующие группы: стали для режущих инструментов; стали для измерительных инструментов; штамповые стали.
224
В особую группу инструментальных материалов входят так называемые твердые сплавы, применяемые для инструмента, работающего при особо высо-
ких скоростях резания.
§ 1. Стали для режущих инструментов
Режущий инструмент изготовляют из углеродистых, легированных и бы-
строрежущих сталей.
Углеродистые стали. Это заэвтектоидные стали марок У9 (0,9% С), У10 (1,0% С), У11 (1,1% С), У12 (1,2% С).
Основной исходной хорошо обрабатывающейся структурой заэвтектоид-
ной стали является зернистый перлит; цементитная сетка не допускается. По-
этому заэвтектондную сталь отжигают по одному из режимов отжига на зерни-
стый перлит.
Углеродистую инструментальную сталь для получения высокой твердо-
сти (HRC60-64) закаливают в воде с 770-810° С, но, несмотря на быстрое охла-
ждение, инструмент прокаливается на небольшую глубину - диаметром до 10-
12 мм. Структура после закалки - мартенсит и цементит.
Отпускают инструмент из углеродистых инструментальных сталей при разных температурах (160-240° С) в зависимости от назначения инструмента и требуемой твердости.
Высокая твердость закаленной стали сохраняется при нагреве (отпуске)
до 200° С. При более высоких температурах нагрева (выше 200° С) твердость значительно понижается.
Поэтому инструмент, изготовленный из углеродистых инструментальных сталей, должен работать в таких условиях, чтобы в процессе работы режущая кромка не нагревалась до температуры выше 200° С.
Сталь У9 применяют для ножовочных полотен и деревообрабатывающего инструмента (сверла, фрезы, ножи и др.). Стали У10, У11, У12 - для различного металлорежущего инструмента (сверла, метчики, развертки, фрезы, плашки и
225
др.), напильников. Сталь У13 - для бритвенных ножей, лезвий острого хирурги-
ческого инструмента, напильников.
Легированные стали. Химический состав некоторых легированных ста-
лей, применяемых для изготовления режущих инструментов, приведен в табл.
12.
По сравнению с углеродистыми легированные стали 9ХФ, 11ХФ, 13Х
имеют следующие преимущества: более равномерное распределение карбидов в структуре; меньший рост зерна при нагреве под закалку; большую прокали-
ваемость (возможность применения для инструмента большего сечения); боль-
шую пластичность в отожженном состоянии; возможность применения при за-
калке более умеренных охладителей - масла, горячих сред (меньшая деформа-
ция инструмента); более высокую прочность (при изгибе) в закаленном состоя-
нии; более высокие режущие свойства; более постоянные и однородные свой-
ства в разновременно обрабатываемых партиях инструмента.
Таблица 12
Химический состав (%) некоторых легированных сталей для режущих инструментов (ГОСТ 5950-73)
Марка |
Элементы |
|
|
|
|
стали |
С |
Mn |
Si |
Cr |
W, V |
9ХФ |
0,80-0,90 |
0,30-0,60 |
0,15-0,35 |
0,40-0,70 |
0,15-0,30V |
11ХФ |
1,05-1,15 |
0,40-0,70 |
0,15-0,35 |
0,40-0,70 |
0,15-0,30 V |
13Х |
1,25-1,40 |
0,30-0,60 |
0,15-0,35 |
0,40-0,70 |
- |
X |
0,95-1,10 |
0,15-0,40 |
0,15-0,35 |
1,30-1,65 |
- |
9ХС |
0,85-0,95 |
0,30-0,60 |
1,20-1,60 |
0,95-1,25 |
- |
ХВГ |
0,90-1,05 |
0,80-1,10 |
0,15-0,35 |
0,90-1,20 |
1,20-1,60W |
ХВСГ |
0,95-1,05 |
0,60-0,90 |
0,65-1,00 |
0,60-1,10 |
0,50-0,80W |
|
|
|
|
|
0,05-0,15V |
Назначение этих сталей следующее: 9ХФ - для круглых и ленточных пил,
для ножей при холодной резке металла; 11ХФ - для метчиков и другого режу-
щего инструмента диаметром до 30 мм, закаливаемого с охлаждением в горя-
чих средах; 13Х - для бритвенных ножей и лезвий, острого хирургического ин-
струмента, шаберов, гравировального инструмента.
226
Основной легирующий элемент в сталях X, 9ХС, ХВГ, ХВСГ - хром.
Сталь X легирована только хромом. Повышенное содержание хрома значитель-
но увеличивает прокаливаемость. Сталь X прокаливается в масле насквозь в се-
чении до 25 мм (твердость в середине не ниже HRC60), а сталь У10 только в сечении до 5 мм. Применяют сталь X для токарных, строгальных и долбежных резцов в лекальных и ремонтных мастерских. Сталь 9ХС кроме хрома легиро-
вана кремнием. По сравнению со сталью X она имеет большую прокаливае-
мость - до 35 мм; повышенную теплостойкость - до 250-260° С (сталь X до 200-
210° С); лучшие режущие свойства; более равномерное распределение карби-
дов. Из стали 9ХС изготовляют сверла, развертки, фрезы, метчики, плашки.
Сталь ХВГ легирована хромом, вольфрамом и марганцем. Она имеет большую прокаливаемость, чем сталь 9ХС, - до 45 мм. Являясь малодеформи-
рующейся сталью, глубоко прокаливающейся, сталь ХВГ применяют для круп-
ных и длинных протяжек, длинных метчиков, длинных разверток и т. п.
Сталь ХВСГ - сложнолегированная сталь и по сравнению с 9ХС и ХВГ лучше закаливается и прокаливается. При охлаждении в масле она прокалива-
ется насквозь в сечении до 80 мм. Она меньше чувствительна к перегреву. Теп-
лостойкость ее такая же, как у стали 9ХС. Сталь ХВСГ применяют для круглых плашек, разверток, крупных протяжек и другого режущего инструмента.
Быстрорежущие стали. Эти стали широко применяют для изготовления разнообразного режущего инструмента, работающего при высоких скоростях резания, в тяжелых условиях. Качество резцов, сверл и других инструментов зависит от качества быстрорежущей стали, тщательности и правильности изго-
товления инструмента и от его правильной термической обработки. Быстро-
режущие стали являются сложнолегированными.
Быстрорежущие стали имеют высокую теплостойкость (до 620-640° С) и
износостойкость. Более высокую теплостойкость имеют стали с повышенным
227
содержанием ванадия и кобальтовые стали. Химический состав и теплостой-
кость быстрорежущих сталей приведены в табл. 13.
Таблица 13
Химический состав (%) и теплостойкость некоторых быстрорежущих сталей(ГОСТ 19265-73)
Марка |
Элементы |
|
|
|
Теплостойкость, |
||
стали |
С |
Сr |
W |
V |
Mn, Co |
0С |
|
Р18 |
0,7-0,8 |
3,8-4,4 |
17,0-1 8,5 |
1,0-1,4 |
- |
|
|
Р12 |
0,8-0,9 |
3,1-3,6 |
12,0-13,0 |
1,5-1,9 |
- |
620 |
|
P6M5 |
0,80-0,88 |
3,8-4,4 |
5,5-6,5 |
1.7-2.Г |
5,0-5,5 Мо |
|
|
Р14Ф4 |
1,2-1,3 |
4,0-4,6 |
13,0-14,5 |
3,4-4,1 |
- |
|
|
4,8-5,8 Мо |
630 |
||||||
Р6М5К5 |
0,80-0,88 |
3,8-4,3 |
6,0-7,0 |
1,7-2,2 |
|||
4,8-5,3 Со |
|
||||||
|
|
|
|
|
|
||
Р10К5Ф5 |
1,45-1,55 |
4,0-4,6 |
10,0-11,5 |
4,3-5,1 |
5,0-6.0 Со |
640 |
|
Р9КЮ |
0,9-1,0 |
3,8-4,4 |
9,0-10,5 |
2,0-2,6 |
9,0-10,5 Со |
||
|
Быстрорежущая сталь принадлежит к ледебуритному классу легирован-
ных сталей. В литом состоянии структура быстрорежущей стали состоит из ле-
дебуритной эвтектики, имеющей «скелетообразный» вид, и продуктов распада аустенита (рис. 129, а). В литой быстрорежущей стали имеются три типа кар-
бидов: первичные (ледебуритная эвтектика), вторичные, выделившиеся при ох-
лаждении из аустенита, и эвтектоидные, образовавшиеся в результате перлит-
ного превращения.
Для разрушения неблагоприятной формы карбидов (ледебуритной эвтек-
тики) и устранения хрупкости литую быстрорежущую сталь подвергают горя-
чей обработке (прокатке, ковке), а затем отжигу при температуре 830-850° С.
Твердость быстрорежущей стали после отжига НВ207-255.
На рис. 129, б показана микроструктура правильно отожженной быстро-
режущей стали - сорбитообразный перлит (феррит + мелкие эвтектоидные кар-
биды) и избыточные карбиды (вторичные и первичные). Легирующие примеси находятся в быстрорежущей стали растворенными в феррите и в виде карбидов.
228
Для закалки быстрорежущую сталь нагревают до высоких температур
(рис. 130), например сталь Р18 до 1270-1300° С.
П
роцесс закалки быстрорежущей стали состоит из медленного нагрева (подогре-
за) до 800-8Г)0° С, выдержки при этой температуре, быстрого (окончательного)
нагрева до температуры закалки, кратковременной выдержки и охлаждения
(обычно в масле). При нагреве до температуры 800-8500С из исходной структу-
ры сорбитообразного перлита с карбидами образуется структура аустенит +
карбиды. Но аустенит при данной температуре содержит всего 0,2% углерода и мало легирован, так как основная масса карбидов находится вне твердого рас-
твора. Поэтому если быстрорежущую сталь закалить, например, с температуры
900J С, то она не будет теплостойкой и будет иметь твердость HRC45-50.
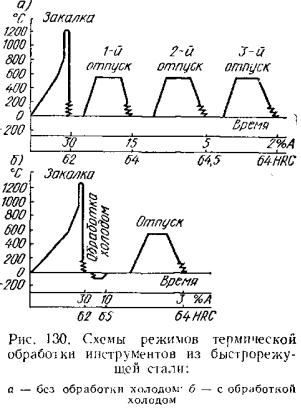
229
Для увеличения легированности аустенита и количества углерода прово-
дят окончательный нагрев до высокой температуры (закалки). Структура при
1300° С - аустенит + карбиды, т. е. такая же, как при 8500 С, но в связи с тем, что при нагреве в данном температурном ин-
тервале большая часть карбидов раство-
ряется, аустенит при 13000С получается значительно более легированным.
При охлаждении (закалке) быстро-
режущей стали аустенит распадается с образованием мартенсита, но не весь,
часть его (25-30%) сохраняется в виде остаточного аустенита. Поэтому струк-
тура после закалки представляет собой мартенсит + карбиды + остаточный аустенит (рис. 129, в). Твердость после за-
калки HRC~62. После закалки быстрорежущую сталь подвергают отпуску при температуре 550-570° С. При отпуске происходит выделение из мартенсита мелкодисперсных карбидов ванадия и вольфрама (дисперсионное твердение мартенсита), а также превращение остаточного аустенита в мартенсит, в связи с чем твердость быстрорежущей стали получается более высокой (HRC ~ 64).
Обычно отпуск быстрорежущей стали дается двух-трехкратный длитель-
ностью по 1 ч при каждом отпуске (рис. 130, а).
Точка Мк быстрорежущей стали располагается ниже нуля. Поэтому для устранения остаточного аустенита быстрорежущую сталь можно обрабатывать холодом (при температуре-75-80° С). В этом случае вместо трехкратного дается однократный отпуск (рис. 130, б). Микроструктура нормально закаленной и от-
230
пущенной быстрорежущей стали состоит из мартенсита и карбидов (см. рис. 129, г).
Иногда после закалки быстрорежущая сталь получается хрупкой с гру-
бым зернистым изломом. Такой излом быстрорежущей стали называется «наф-
талинистым». Причины образования нафталинистого излома - слишком высо-
кая температура (выше 1050-1100° С) конца горячей обработки с небольшой степенью деформации при последнем обжатии и повторная закалка без проме-
жуточного отжига.
Для улучшения режущих свойств и повышения стойкости инструмент из быстрорежущих сталей подвергают низкотемпературному (при 540-570° С)
цианированию: жидкостному, газовому или твердому.
В результате низкотемпературного цианирования на поверхности быст-
рорежущей стали образуется тонкий (0,02-0,07 мм) планированный слой,
имеющий высокую твердость (HV 1000-1100) и повышенную теплостойкость
(~ 650° С).
Для повышения антикоррозийных свойств и некоторого улучшения ре-
жущих свойств инструмент из быстрорежущей стали можно подвергнуть обра-
ботке в атмосфере перегретого пара при температуре отпуска, т. е. при 550-5700
С.
§ 2. Стали для измерительных инструментов
Для изготовления измерительных инструментов применяют стали X, ХВГ
и др.
Для измерительного инструмента (особенно высоких классов точности)
большое значение имеет постепенное изменение размеров закаленного инстру-
мента в течение длительного времени, что связано с уменьшением тетрагональ-
ное™ решетки мартенсита, мартенситным превращением остаточного аустени-
та и уменьшением и перераспределением внутренних напряжений. Поэтому при термической обработке измерительного инструмента большое внимание