
Cagle R.B. - Blueprint for Project Recovery[c] A Project Management Guide (2003)(en)
.pdf
C O N F I G U R A T I O N M A N A G E M E N T P L A N O U T L I N E |
235 |
configuration control boards and the interfaces between the CM organization and outside organizations.
4.CONFIGURATION MANAGEMENT PHASING AND MILESTONES
The sequence of events and milestones for implementation of CM in phase with major program milestones and events. The establishment of configuration control boards and the conduct of configuration audits.
5. DATA MANAGEMENT
The methods for meeting the CM technical data requirements.
Y 6. CONFIGURATION IDENTIFICATIONL
The identification of the Hardware FConfiguration Items (HWCIs) and Com-
puter Software Configuration Item (CSCIs). M 7. INTERFACE MANAGE ENT
The procedures for the Eestablishment of interface agreements.
8. CONFIGURATION CONTROL
The responsibilities and authority of your configuration control board, the classification of changes, and the level of authority for change approval/concurrence.
9. CONFIGURATION STATUS ACCOUNTING
The procedures for collecting, recording, processing, and maintaining CM data.
10. CONFIGURATION AUDITS
The approach to plans, procedures, documentation, and schedules for functional and physical configuration audits and the format for reporting results of in-process configuration audits.

236 |
B L U E P R I N T F O R P R O J E C T R E C O V E R Y |
11. SUBCONTRACTOR/VENDOR CONTROL
The methods you will use to ensure subcontractor/vendor compliance with configuration management requirements.
The above outline is a condensed version of the table of contents advocated in MIL-STD-973. Source: www.edms.redstone.army.mil/edrd/973appa.html
Additional References:
MIL-STD-973
MIL-HDBK-61
EIA 649
ISO-10007
See: www.cmiiug.com/Standards.htm for additional information.
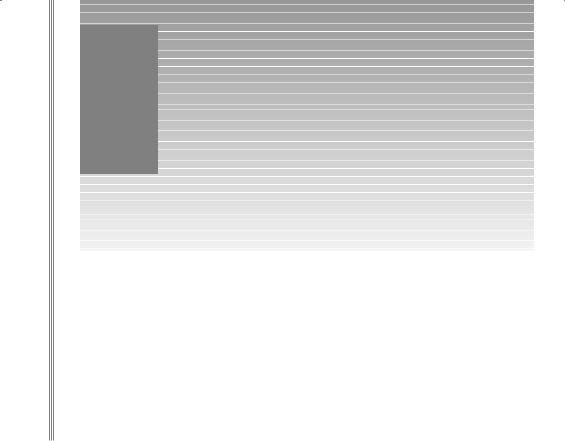
A T T A C H M E N T 6
QUALITY ASSURANCE PLAN OUTLINE
PROGRAM
QUALITY ASSURANCE PLAN
1 . |
Q UA L I T Y M A N A G E M E N T |
1 . 1 |
Q UA L I T Y P O L I C Y |
The purpose of this Quality Assurance Plan is to detail the quality assurance principles and to establish the structure of the Program quality assurance
237

238 B L U E P R I N T F O R P R O J E C T R E C O V E R Y
program consistent with Company Quality Assurance Policies and theCompany Quality Assurance Plan.
1.2QUALITY OBJECTIVES
The following quality principles are intended to be consistent with Company quality policies and plans.
All measurements will include quantitative determinations.
Methods will be consistent.
Measurements will be linked to a standard value.
1.3RESPONSIBILITIES AND AUTHORITY.
The Program Quality Assurance Representative is responsible for the day-to-day implementation of the Program Quality Assurance Program, including documenting all data and identifying out-of-tolerance situations.
2.STRUCTURE OF QUALITY SYSTEMS
2.1QUALITY ORGANIZATIONAL STRUCTURE
The Company Quality Assurance Director reports directly to the Vice President/General Manager.
The Program Quality Assurance Representative reports operationally to the Program Program Manager and functionally to the Company Quality Assurance Director.
2.2RESOURCES AND PERSONNEL
Each participant in Company shares responsibility for achieving the quality objectives. Therefore, portions of the program’s budget are allocated to the quality assurance function as it relates to and supports the Program .
2.3OPERATIONAL PROCEDURES
The Program Quality Assurance Plan will include a Program Quality Control Plan that outlines the specifics of controlling product quality on theProgram .

Q U A L I T Y A S S U R A N C E P L A N O U T L I N E |
239 |
2.4QUALITY MANUAL AND RECORD KEEPING
The Quality Assurance Representative is responsible for maintaining quality assurance records during the conduct of all phases of the Program .
2.5THE PROGRAM QUALITY ASSURANCE PLAN WILL
BE UPDATED AS REQUIRED
Each update will be treated as an original plan and shall follow the same authorization path. The Program Quality Assurance Plan shall be updated as necessary to incorporate any new or updated changes found necessary to theCompany Quality Assurance Policies, Plans, or Procedures.
QUALITY CONTROL PLAN
The Quality Control Plan, in conjunction with Company Policy ( M-M Policy 07000 Series), provides direction, control, and authorization for the overall quality control of equipment and data on the Program Program.
SUGGESTED OUTLINE
1.Introduction
2.Scope
3.Applicable Documents
4.Management Organization
5.Quality System Planning
6.Contract Review
7.Design Control
8.Document Control
9.Purchasing

240 |
B L U E P R I N T F O R P R O J E C T R E C O V E R Y |
A.Purchaser Supplied Products
B.Product Identification and Traceability
10.Process Control
A.Inspection and Testing
B.Inspection, Measuring, and Test Equipment
C.Inspection and Test Status
D.Control of Non-Conforming Product
E.Corrective Action
11.Handling, Storage, Packing, and Delivery
12.Quality Records
13.Quality Audits
14.Training
15.Servicing
16.Statistical Techniques
17.Quality System Effectiveness Factors
Additional Notes:
There is usually considerable overlap between Configuration Management (CM) plans, Data Management (DM) plans, and Quality plans of all levels (i.e., Quality Assurance and Quality Control).
The above Quality Assurance Plan and Quality Control Plan are excerpts from the Modern-Management Policies, Plans, and Processes presented in the Strategy for Success workshops. To that end, words that appear in angle brackets ( ) are part of a ‘‘global’’ update (i.e., ‘‘Find and Replace’’) process that allows the users to enter their specific data throughout the plans.
Additional references that may contribute to developing your plan are:
Data Item Description: DI-QCIC-81379
ANSI/ASQC Quality Standards Q91 and Q92
ISO 9001 and 9002
MIL-Q-9858 and MIL-I-45208 (both for reference only)
MIL-STD-2167 AND 2168
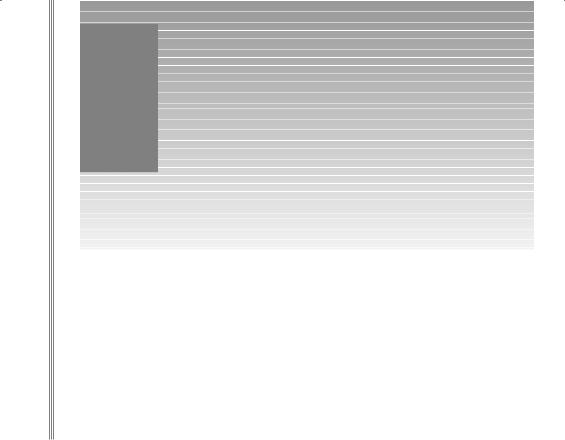
A T T A C H M E N T 7
REQUIREMENTS
TRACEABILITY MATRIX
One of the best methods of generating entries for the Requirements Traceability Matrix (RTM) is to conduct a ‘‘shalls’’ review and use those results as requirement entries in the RTM. If you have not accomplished this task before, don’t worry. It is rather simple nowadays with the ‘‘find’’ function on most word processing programs. There are, of course, applications dedicated to pulling ‘‘shalls’’ and ‘‘wills’’ from requirements documents and creating an RTM for you. If you use one of these programs, don’t trust it completely. Although they are quite good, they do make mistakes in judgment. It’s up to you to ensure that the RTM is complete and accurate.
The U.S. Army defines traceability as:
The capability to track system requirements from a system function to all elements of the system which, collectively or in-
241
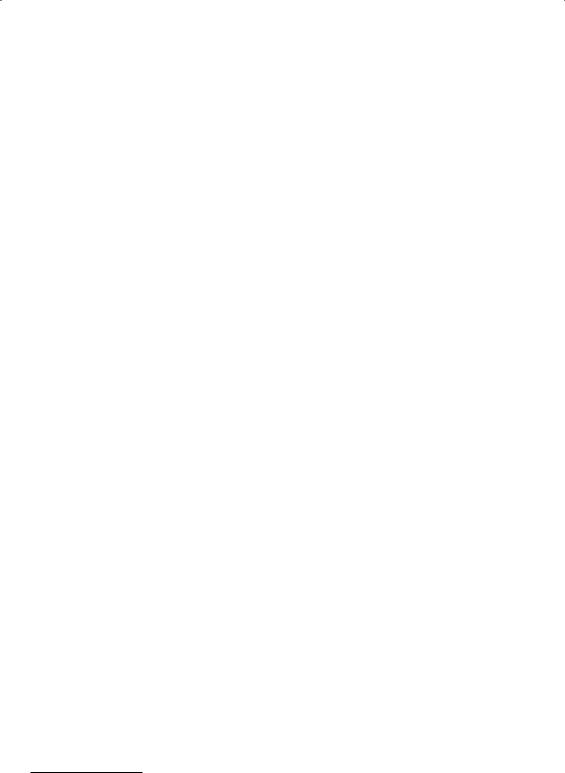
242 |
B L U E P R I N T F O R P R O J E C T R E C O V E R Y |
dividually, perform the function; an element of the system to all functions which it performs; a specific requirement of the source analysis or contractual constraint which originated the requirement. Traceability includes tracking allocation design (and technical program) requirements through the work breakdown structure between the system level and the lowest level of assembly.*
Most requirements documents, including SOWs and specifications, contain statements that follow the general convention of ‘‘The system shall . . . . . .’’ These are referred to as ‘‘shalls’’ and, in some cases, ‘‘musts’’ that constitute the core requirements of the system. Care must be taken to evaluate the use of the words ‘‘will’’ and ‘‘should’’ by the document creator. In some cases, ‘‘wills’’ or even ‘‘shoulds’’ are treated the same as ‘‘shalls’’ while in other cases ‘‘shalls’’ are mandatory and ‘‘wills’’ are optional. If the word ‘‘goal’’ shows up, try to get it quantified. I assure you that your interpretation of a goal will be different than the customer’s interpretation of it.
To ensure that your system or product is exactly what the customer has specified, conduct a ‘‘shalls’’ and ‘‘wills’’ search, and place the results in an RTM. The usual convention is to place the reference paragraph on the far left and the requirement in the next column. Further columns trace the requirement through your system following the way your company does business and the nature of the output product. The concept, however, is the same regardless of methodology or product.
You can create and print forms for this purpose or you can use a spreadsheet application such as Excel or Lotus to accomplish the same purpose. To start the process, use your word processing program such as MS Word or MS Works or MacWrite or a similar program to search for the ‘‘shalls’’ and ‘‘wills.’’ When you find one, simply copy and paste and include the paragraph number. If your programs are compatible, such as MS Office, it is a simple matter to transfer the entries from the word processing program to the spreadsheet program.
Be cautious in the construction of your RTM. Don’t necessarily limit it to ‘‘shalls’’ and ‘‘wills.’’ If you customer has some other way of stating mandatory and lesser requirements, that is certainly the convention to follow.
The point and purpose of an RTM is to trace a requirement from its begin-
*U.S. Army Field Manual (FM), 770–778.

R E Q U I R E M E N T S T R A C E A B I L I T Y M A T R I X |
243 |
ning in the requirements document (contract) to its final proof, such as the System Test. There must be enough detail in the RTM to point immediately to the place, paragraph, table, etc., where the requirement is allocated.
You should assign each requirement to a monitor. The monitor should be listed in a column in the RTM. You may assign more than one requirement to a person but don’t simply assign all requirements to the chief engineer. Show the actual person responsible for that requirement.
In general, your RTM should look similar to Table A7-1.
T a b l e A 7 - 1 — R e q u i r e m e n t s T r a c e a b i l i t y M a t r i x ( R T M )
|
|
|
|
|
Unit |
System |
|
|
SOW/ |
|
WBS |
S/C SOW/ |
Test |
Test |
|
|
Spec Para |
Requirement |
Number |
Spec Para |
Number |
Para |
Monitor |
|
SOW |
|
|
|
|
|
|
|
|
|
|
|
|
|
|
|
|
|
|
|
|
|
|
4.3.1 |
Security |
06-03-02 |
N/A |
T-0304 |
4.4.1 |
Smith |
|
|
|
|
|
|
|
|
|
|
|
|
|
|
|
|
|
|
Spec |
|
|
|
|
|
|
|
|
|
|
|
|
|
|
3.2.1 |
System weight |
02-04-03 |
3.4.6 |
T-0045 |
3.4.1 |
Jones |
|
|
|
shall be less |
|
|
|
|
|
|
|
than 10,000 |
|
|
|
|
|
|
|
pounds |
|
|
|
|
|
|
|
|
|
|
|
|
|
The same concept and organization can be applied to a Subcontract Requirements Traceability Matrix (SRTM) and used by your subcontractor.
For a small project, you can use a spreadsheet program. For a larger program you can use a spreadsheet ‘‘workbook’’ with requirements in one sheet, WBS information on the second sheet, etc. You can then link the cells together with hyperlinks from a master sheet to form a thread of information for each requirement.
You can also do the same thing with a Relational Data Base (RDB). The RDB will require more up-front time but will result in a more cohesive product.
The current industry standard is a family of products titled DOORS (for large and enterprise wide projects) and DOORSrequireIT (for smaller projects). Both are commonly referred to as ‘‘Doors.’’ Doors is available from:
Telelogic DOORS North America
400 Valley Road, Suite 200

244 |
B L U E P R I N T F O R P R O J E C T R E C O V E R Y |
Mt. Arlington, NJ 07856
Phone: 949-830-8022
Fax: 949-830-8023
To order: 877-275-4777
E-mail: doorssupport.us@telelogic.com
Web site: www.telelogic.com/doors