
Механика Прикладная механика лекции
.pdf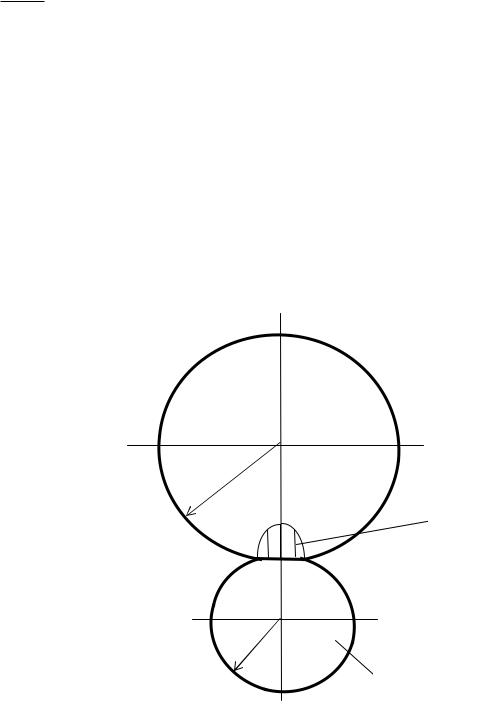
s пред ,
max
где s коэффициент запаса прочности;
пред предельное напряжение (при постоянной нагрузки равно пределу текучести пред т , при переменных – пределу выносливости
пред -1).
max максимальное напряжение в опасном сечении детали.
Контактная прочность. Работоспособность деталей машин в некоторых случаях ограничивается прочностью рабочих поверхностей изза действия контактных напряжений.
E2
2
H
1
E1
Рис. 11.1
При контакте двух цилиндров (рис. 11.1) максимальное контактное напряжение H , которое возникает на поверхности контакта, опре-
деляется по формуле Герца. Условие контактной прочности при этом имеет вид:
51

H |
|
|
|
|
qEпр |
|
|
|
HP , |
|
|
пр |
2 1 2 |
|
|||||||
|
|
|
|
|||||||
|
|
|
|
|
|
|
|
|
где q нагрузка на единицу длины контактной линии;
E |
|
|
2E1 E2 |
приведенный модуль упругости; |
пр |
|
|||
|
|
E1 E2 |
||
|
|
|
коэффициент Пуассона;
HP допустимое контактное напряжение;
пр приведенный радиус кривизны, который определяется из выражения
11 1 .
gh 1 2
Жесткость. Жесткость это способность деталей сопротивляться образованию деформации. При расчете на жесткость учитываются ограничения на значения деформаций, возникающих под действием внешних нагрузок.
Актуальность расчета на жесткость возрастает при применении высокопрочных материалов. Жесткость деталей машин обычно определяется приближенно и равна собственной жесткости детали.
Износостойкость. Одной из причин выхода из строя деталей машин является повышенный их износ. В процессе эксплуатации могут иметь место следующие виды изнашивания: механическое, молекуляр- но-механическое, коррозионно-механическое, абразивное, усталостное и др.
Для уменьшения изнашивания применяют конструктивные и технологические меры: смазка трущихся поверхностей, применение уплотнительных устройств, увеличение чистоты поверхности детали, нанесение специальных покрытий, применение термообработки и упрочнения поверхностного слоя.
Оценкой износостойкости деталей является интенсивность изнашивания I h , которая определяется по зависимости:
I h hLL ,
где hL толщина снятого в результате изнашивания слоя;
52
L путь перемещения точки, в которой фиксируется износ, относительно сопряженной поверхности.
Расчет на износостойкость обычно проводят косвенным методом, например, по ограничению давление p на контактируемых поверхностях
p p .
Теплостойкость. Теплостойкость – способность деталей сохранять работоспособность при изменении температуры.
Нагрев деталей машин может привести к следующим последстви-
ям:
1)понижение прочности материала и появление ползучести;
2)снижение защищающей способности масляных пленок;
3)изменению зазоров;
4)понижение точности работы машины.
Расчеты на теплостойкость сводятся к составлению условия теплового баланса. Для обеспечения нормальной работы машины должно выполняться условие:
Qвыд Qотв ,
где Qвыд количество выделенного тепла; Qотв количество отведенного тепла.
Виброустойчивость. Виброустойчивость – способность детали сохранять работоспособность при воздействии знакопеременных нагрузок и колебаний с заданной частотой и амплитудой.
Вибрация приводит к усталостному разрушению деталей, порождает шум и снижает качество обработки в металлорежущих станках.
Расчет на виброустойчивость является обязательным при проектировании высокоскоростных механизмов и заключается. Наиболее опасными являются резонансные колебания, при которых возможно разрушение деталей. Для устранения резонанса необходимо, чтобы частота собственных колебаний детали p не совпадала с частотой внешних периодически изменяющих сил
p .
53

Допускаемые напряжения и коэффициенты запаса прочности.
Выбор допускаемых напряжений может производиться двумя методами: табличным и дифференциальным.
Табличный метод прост и удобен для пользования, поэтому им пользуются в тех случаях, когда имеются таблицы допускаемых напряжений и коэффициентов запаса прочности.
Дифференциальный метод заключается в том, что коэффициенты запаса прочности определяют по зависимостям, в которых учитываются различные факторы, влияющие на прочность детали.
Допускаемый коэффициент запаса прочности рекомендуется определять по зависимости:
s s1s2 s3 ,
где s1 коэффициент, учитывающий точность расчета;
s2 коэффициент, учитывающий однородность материала;
s3 коэффициент, учитывающий степень ответственности детали. В случае сложного напряженного состояния не зависимо от вида
цикла изменения напряжения коэффициент запаса прочности определяют по зависимости:
s |
|
s s |
|
, |
||
|
|
|
|
|||
s 2 |
s 2 |
|||||
|
|
|
|
|||
|
|
|
|
|
|
где s , s коэффициенты запаса прочности по нормальным и касательным напряжениям, которые определяются по формулам:
s |
|
|
|
|
|
1 |
; s |
|
|
|
|
1 |
, |
|
|
k |
|
a m |
|
k |
|
a m |
|||||
|
|
|
|
|
|
|
|
||||||
|
|
|
|
|
|
|
|
|
|
|
|
||
|
|
|
|
|
|
|
|
||||||
|
|
|
|
|
|
|
|
|
где 1 , 1 пределы выносливости материала при изгибе и кручении; k , k эффективные коэффициенты концентрации при изгибе и
кручении;, коэффициенты, учитывающие влияние абсолютных раз-
меров детали на величину предела выносливости при изгибе и кручении;
, коэффициенты, учитывающие влияние на предел выносливости состояния поверхности детали при изгибе и кручении;
54
, коэффициенты, учитывающие влияние ассиметрии цикла на прочность детали при изгибе и кручении;
a , a амплитуды цикла напряжений при изгибе и кручении;
m , m средние напряжения цикла при изгибе и кручении.
Машиностроительные материалы. Выбор материала и термооб-
работки деталей машин определяются следующими факторами:
1)необходимостью обеспечения требуемой надежности деталей в течение заданного срока;
2)экономическими факторами и условиями изготовления.
Детали (зубчатые колеса, валы и т.п.), размеры которых определяются условиями прочности, изготавливают из материалов с высокими прочностными характеристиками. Для этого используют улучшаемые или закаливаемые стали, а также чугун повышенной прочности.
Детали, размеры которых определяются жесткостью, выполняют из материалов с высоким модулем упругости.
Для изготовления деталей (пружин) с большими упругими перемещениями применяют закаливаемые до высокой твердости стали, резину и пластмассы с большим отношением предела упругости в к мо-
дулю упругости E .
В антифрикционных узлах применяют антифрикционные материалы (бронзы, баббиты, антифрикционные пластмассы и т.п.), которые характеризуются низким коэффициентом трения, высокой износостойкостью, хорошей прирабатываемостью и высоким сопротивлением схватыванию.
Во фрикционных узлах используются фрикционные материалы (металлокерамика, пластмассы на основе асбеста и др.), которые характеризуются большим и постоянным коэффициентом трения, высокой износостойкостью и теплостойкостью, хорошей прирабатываемостью, малым износом при работе без смазочного материала.
Детали, работающие при высоких температурах, изготавливают из жаростойких или жаропрочных сплавов.
Шероховатость поверхностей. Шероховатость поверхности это совокупность неровностей поверхности с относительно малыми шагами, рассматриваемых на базовой длине. Основными параметрами для оценки шероховатости являются: Ra среднее арифметическое откло-
нение профиля; Rz высота неровностей профиля по десяти точкам. Шероховатость поверхностей деталей машин играет значитель-
ную роль. С уменьшением шероховатости до некоторого оптимального величины сжижает износ трущихся поверхностей, повышает прочность деталей, улучшает их внешний вид. Однако стоимость обработки деталей машин увеличивается значительно быстрее, чем точность их изго-
55
товления. Поэтому шероховатость поверхности деталей машин выбирается в каждом конкретном случае в зависимости от их назначения.
Допуски и посадки. Точность является важнейшим показателем деталей машин, существенно влияющая на все критерии работоспособности и надежности механизмов.
Детали машин не могут быть изготовлены абсолютно точно и всегда имеют некоторые отклонения от номинальных размеров. Эти отклонения регламентируются стандартной системой допусков и посадок.
Допуск размера представляет собой разность между наибольшим и наименьшим допустимым предельным размером и обозначается буквой T .
Допуски установлены в соответствии с девятнадцатью квалитетами, обозначаемые в порядке понижения точности 0,1; 0; 1; 2; … 17. Детали общемашиностроительного производства выполняются преимущественно по квалитетам 4 … 11.
Разность между охватывающим и охватываемым размерами определяет посадку, т.е. характер соединения двух сопряженных деталей. Положительная разность между размерами отверстия и вала называется зазором, а отрицательная – натягом.
Посадки разделяют на три группы: с натягом, с зазором и переходные посадки, в которых может быть как зазор, так и натяг.
Посадки обозначаются строчными буквами латинского алфавита для вала и заглавными буквами для отверстия. Характер посадки определяются полями допусков сопрягаемых деталей, т. е. допусками и их расположение относительно номинального размера, определяемым основным отклонением.
Различают две системы посадок: система отверстия и система вала. В посадках по системе отверстия предельные размеры отверстия остаются неизменными, а получение различных посадок осуществляются за счет изменения предельных размеров вала. В системе вала – наоборот.
Выбор системы посадок при проектировании деталей машин имеет экономическое значение. При равных условиях система отверстия обходится значительно дешевле системы вала. Так как не требует применения дорогостоящего инструмента для обработки отверстия для получения различных посадок.
Технологичность деталей машин. Технологичной называют та-
кую конструкцию, которая изготовляется при минимальных затратах труда, времени и средств в конкретных условиях производства и обеспечивает заданные эксплуатационные показатели. Технологичность детали в большой мере определяется ее формой, рациональным выбором материала и вида термообработки, способом получения заготовки, тре-
56
буемой точностью изготовления и шероховатостью обрабатываемых поверхностей. Технологичность деталей должна полностью соответствовать технологичности машины. Детали должны быть изготовлены так, чтобы были обеспечены возможность сборки и разборки узлов машины, удобный осмотр и смазка трущихся поверхностей, легкая замена изношенных частей при ремонте и т. п.
Правильный выбор способа получения заготовки во многом определяет возможность применения необходимого материала, минимальные габаритные размеры и вес, наименьшую стоимость готовой детали и т. д. Заготовкой называют деталь первоначальной формы. Окончательная форма детали придается чаще всего в процессе механической обработки на станках. Заготовки могут быть получены отливкой, ковкой, штамповкой, нарезкой из проката, сваркой и автогенной резкой.
Литые заготовки получают, заливая расплавленный металл в специальные (земляные или металлические) формы. Материал для литой заготовки должен обладать жидкотекучестью, легкоплавкостью, малой усадкой и т. п. Литьем можно получить деталь сложной формы с малыми припусками на обработку или даже без дополнительной обработки (точное литье), но оно экономически выгодно лишь при крупносерийном и массовом производстве вследствие больших затрат средств на изготовление моделей. К недостаткам литых деталей относятся их пониженная надежность, плохая сопротивляемость ударным и вибрационным нагрузкам, невозможность изготовления с тонкими и резко различными по толщине стенками.
Вследствие неравномерного остывания металла и его усадки при охлаждении в литой заготовке могут появиться пороки (раковины, трещины, коробление), внутренние напряжения. Все это приводит к снижению механической прочности металла.
Чтобы предупредить появление указанных явлений при конструировании литых деталей, необходимо придавать им наиболее простую форму, предусматривать равномерную толщину стенок. Если последнее невозможно, то необходимо создать постепенный переход от толстой стенки к тонкой. Чтобы не появлялись трещины, углы детали необходимо закруглять. Для свободного извлечения модели из формы следует предусмотреть литейные уклоны порядка 1/5—1/10. Толщина стенок чугунных литых деталей должна быть не менее 8—10 мм, а стальных — не менее 10—12 мм. Сталь имеет худшие литейные свойства, чем чугун. Она значительно дороже чугуна, поэтому там, где это возможно, вместо стали следует применять для отливок чугун.
Заготовки, изготовленные ковкой, более прочны, чем литые, од-
нако процесс изготовления их более дорогой. Поэтому кованые заготовки применяют для наиболее ответственных деталей. Сложные по форме
57
ибольшие детали ковать трудно, а иногда и невозможно. Поэтому кованые заготовки рекомендуется применять для деталей сравнительно простых форм. Свободная ковка малоэкономична и может быть использована лишь в индивидуальном производстве.
Штамповку применяют в серийном и массовом производстве. Она отличается высокой производительностью, поэтому экономически более выгодна, чем ковка. Материал для штампованных деталей должен обладать высокой пластичностью. Для того чтобы при штамповке металл хорошо затекал во все углубления штампов, необходимо предусматривать соответствующие уклоны и закруглять все наружные углы выступающих элементов детали.
Сварку применяют преимущественно для изготовления деталей из уголков, швеллеров, профильного проката, листов и т. д. (станин, рам, шкивов, барабанов и т. п.). Часто выгодно применять сварку в комбинации со штамповкой. При этом получают экономичные, легкие тонкостенные заготовки сложной формы.
Фасонные заготовки из толстых листов получают при помощи автогенной резки.
Для получения деталей машин точных размеров и низкой шероховатости поверхности их заготовки обрабатывают резанием. Обработка резанием стоит дорого, поэтому при проектировании деталей необходимо стремиться к сокращению механической обработки на станках. Для уменьшения отхода металла в стружку форма и размеры заготовки должны быть близкими к форме и размерам готовой детали. При проектировании деталей, подвергаемых механической обработке, следует отдавать предпочтение деталям цилиндрической и конической формы, а также плоским как наиболее простым и дешевым в изготовлении. Одновременно следует стремиться к минимальному числу и минимальной площади обрабатываемых поверхностей.
Технологичность тесно связана с масштабом и условиями производства. Например, сварная конструкция, будучи технологичной при индивидуальном производстве, может оказаться нетехнологичной при массовом производстве, где более целесообразно применять литье или штамповку.
Повышение точности изготовления деталей машин, снижение шероховатости обрабатываемых поверхностей влечет за собой повышение трудоемкости и стоимости их изготовления. Поэтому как точность, так
ишероховатость поверхности не должны быть более высокими, чем требуется для обеспечения нормальной работы машины.
58
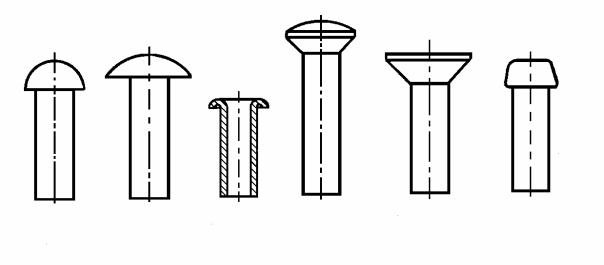
12. Заклепочные соединения
Виды заклепок и заклепочных швов. Заклепочное соединение -
неразъемное соединение деталей при помощи заклепок.
Заклепка - крепежная деталь, состоящая из стержня цилиндрической формы и закладной головки. Основные типы заклепок показаны на
(рис. 12.1).
В соответствии с назначением заклепочные соединения подразделяются на прочные, плотные и прочноплотные соединения.
Прочные заклепочные соединения применяются в стальных конструкциях подъемно-транспортных сооружений, фермах, узлах машин общего назначения.
Плотные заклепочные соединения применяются в конструкциях, требующих герметичность соединения.
Прочноплотные заклепочные соединения применяются в тех случаях, когда они должны обеспечивать кроме прочности еще и герметичность.
а |
б |
в |
г |
д |
е |
|
|
|
Рис. 12.1 |
|
|
Впрочных заклепочных соединениях применяют заклепки с полукруглой головкой (рис. 12.1,а); с плоской головкой (рис. 12.1,е), предназначенных для работы в коррозионных средах; с потайной головкой (рис. 12.1,д), применяемых при недопустимости выступающих частей; с полупотайной головкой (рис. 12.1,г) для соединения тонких листов; пустотелые со скругленной головкой (рис. 12.1,в) для соединения тонких листов и неметаллических деталей, не допускающих больших нагрузок.
Вплотных и прочноплотных заклепочных соединениях применяют заклепки с полукруглой низкой головкой (рис. 12.1,б). Формирова-
59
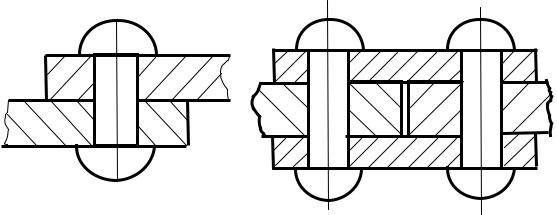
ние замыкающей головки происходит в результате расклепывания стержня заклепки, вставленной в отверстия, соединяемых деталей.
Для облегчения ввода заклепки отверстия в деталях делают несколько больше, чем диаметр заклепки. Изготовление отверстий осуществляют путем сверления (точный способ) или путем продавливания (грубый способ). Диаметр отверстия d0 в деталях зависит от диаметра заклепки d и способа изготовления отверстия.
В процессе клепки за счет протекания поперечной упругопластической деформации стержня заклепки происходит заполнения технологического зазора между стержнем и стенками отверстия. Клепку производят без нагрева заклепок, если их диаметр не превышает 12 мм, и с нагревом до температуры 1000 ... 11000С, если диаметр больше 12 мм. Формирование замыкающей головки у заклепок из цветных металлов и сплавов проводят без нагрева.
а |
б |
|
Рис. 12.2
Виды и параметры заклепочных швов. В зависимости от распо-
ложения соединяемых деталей различают заклепочные швы внахлестку (рис. 12.2,а) и встык с одной накладкой и двумя накладками (рис. 12.2,б).
Геометрические параметры заклепочного шва определяют по эмпирическим зависимостям.
Диаметр заклепок в односрезном силовом соединении определяют по зависимости:
d 2s,
где s - толщина соединяемых элементов.
Для двухсрезных заклепочных соединений диаметр заклепки определяют из соотношения
d 1,5s.
60