
МУ по выполнению ПЗ № 2 ОП
.pdf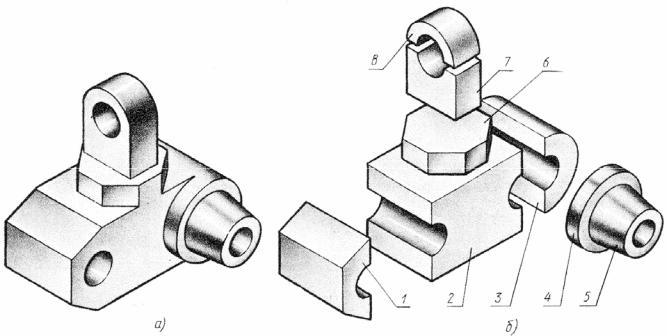
Пример анализа формы детали дан на рисунке 6.
Рисунок 6 – Пример состава детали из различных простейших геометрических тел или их частей
Деталь, представленная на рисунке 6, состоит из следующих элементов: 1 — часть шестигранной призмы с отверстием;
2— параллелепипед с отверстиями;
3— часть полого цилиндра;
4— цилиндр полый;
5— конус с цилиндрическим отверстием;
6— восьмиугольная призма;
7— параллелепипед с отверстием;
8— часть полого цилиндра.
Форма детали определяет технологический процесс ее изготовления; если сконструировать деталь несимметричной формы (рисунок 7, а), то изготовить ее на металлорежущем станке сложнее, чем симметричную (рисунок 7, б).
21
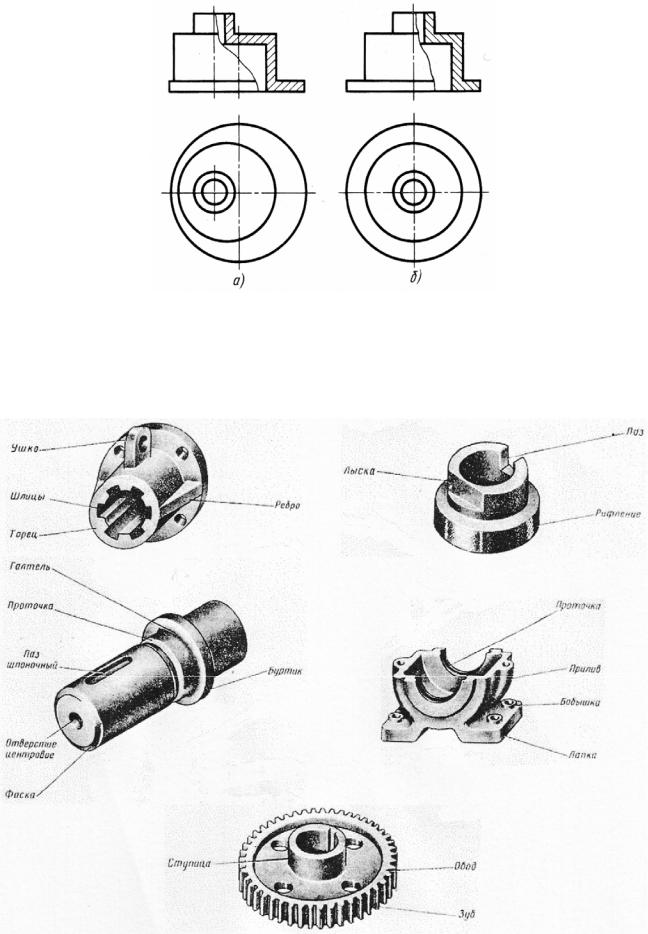
Рисунок 7 – Примеры несимметричной и симметричной форм деталей
На рисунке 8 дано представление о наиболее часто встречающихся элементах деталей и их наименования.
Рисунок 8 – Примеры несимметричной и симметричной форм деталей и наименования их элементов
22
4.1.5 Обоснование выбора баз и системы простановки размеров
Детали работающей машины находятся или в неподвижном состоянии, или в относительном движении. Так, детали редуктора или коробки передач – корпус, крышки, стаканы и пр. — неподвижны. Валы со всеми установленными на них деталями вращаются относительно неподвижного корпуса. В то же время, ряд деталей, расположенных на валу, таких, как зубчатые колеса, кольца подшипников качения, втулки и пр., неподвижны относительно вала.
При сборке машины детали устанавливают одну относительно другой в определенном положении. Установку, или, как говорят, базирование, деталей выполняют как по плоским, так и по цилиндрическим поверхностям или по комбинации этих поверхностей, которые называют базовыми или базами.
Базовые поверхности деталей создают при их проектировании, поэтому очень важно, чтобы на этапе разработки конструкции были созданы хорошие базы — одно из необходимых условий надежной работы машин.
При конструировании узлов и деталей машин особый интерес представляет базирование деталей — тел вращения, т.е. колес, валов, втулок, колец, стаканов и пр.
Под базированием понимают придание детали или узлу (изделию) требуемого положения относительно выбранной системы координат. Под погрешностью базирования понимают отклонение фактически достигнутого положения детали или узла (изделия) от требуемого.
4.1.5.1 Определение основной базы
При посадках с зазором и переходных посадках погрешность базирования зависит от величины зазора в сопряжении вала с отверстием Z (рисунок 9, а).
Возможны два случая базирования.
1.Зазор Z относительно мал и деталь 1 соприкасается с валом по цилиндру
вточках а, b и по торцу в точке с (рисунок 9, б). Между торцами детали и
заплечика вала остается клиновой зазор. Основная база в этом случае — цилиндр (отверстие детали 1).
23
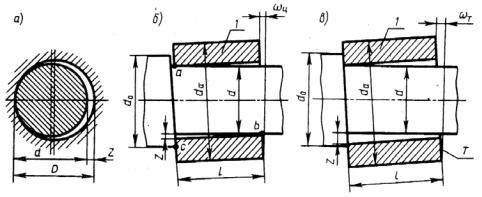
Рисунок 9
2. Зазор Z относительно велик и деталь 1 полностью прилегает к торцу заплечика вала (рисунок 9, в). Основная база — торец детали 1.
При посадках с натягом зазор в сопряжении деталей отсутствует, и можно было бы предположить, что детали всегда устанавливают на валу точно, без перекоса. Однако практика показывает, что вследствие возможных нецентрального приложения силы запрессовки, погрешностей геометрической формы сопряженных поверхностей, неоднородности материала и других причин даже при посадках с натягом деталь может быть установлена на валу с перекосом. Чаще всего это происходит при посадке узких деталей с относительно малым отношением l/d. В таких случаях для повышения точности базирования на валу предусматривают заплечик, к торцу которого при сборке поджимают деталь, т.е. переходят от базирования по цилиндру к базированию по торцу. Детали с относительно большим отношением l/d не требуют поджатия к торцу заплечика вала и достаточно точно базируются по цилиндрической поверхности сопряжения.
Нельзя указать точный критерий для оценки погрешности базирования при посадках с натягом. Приближенно, из опыта принимают: при l/d ≥ 0,7 основная база — цилиндр; при l/d < 0,7 основная база — торец.
4.1.5.2 Базирование деталей по торцам
Торцы деталей часто используют в качестве поверхностей для базирования других сопряженных с ними деталей. Одним из элементов сборочного комплекта
24
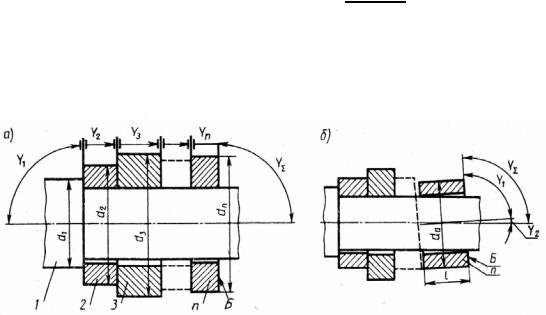
являются втулки и кольца. Условно подобные детали с отношением l/d ≥ 0,7
называют втулками, а с отношением l/d < 0,7 — кольцами. Точность расположения торцов втулок (колец) непосредственно влияет на точность базирования по ним деталей всего комплекта. Кольца базируют относительно вала только по торцу, а втулки — по торцу или по цилиндру. В соответствии с этим можно выделить для рассмотрения две схемы.
Схема 1. Основная база для п-го кольца — торец (рисунок 10, а). Детали сборочного комплекта при схематизации заменяют кольцами, установленными на валу с зазорами (детали 2, 3, ..., п). Торец Б кольца п используют как базу для сопряженной с ним детали (на рисунке 10, а деталь не показана).
Рисунок 10
Ксхеме 1 приводят также сборочные комплекты, в которых детали 2, 3, ...,
пимеют отношение длины к диаметру отверстия менее 0,7 даже при установке их на валу с натягом.
Схема 2. Основная база для п-й втулки — цилиндр. Такая схема соответствует относительно большой длине втулки и малому зазору в сопряжении ее с валом (рисунок 10, б).
Детали, установленные левее втулки п, не влияют на точность
расположения базового торца Б втулки.
25
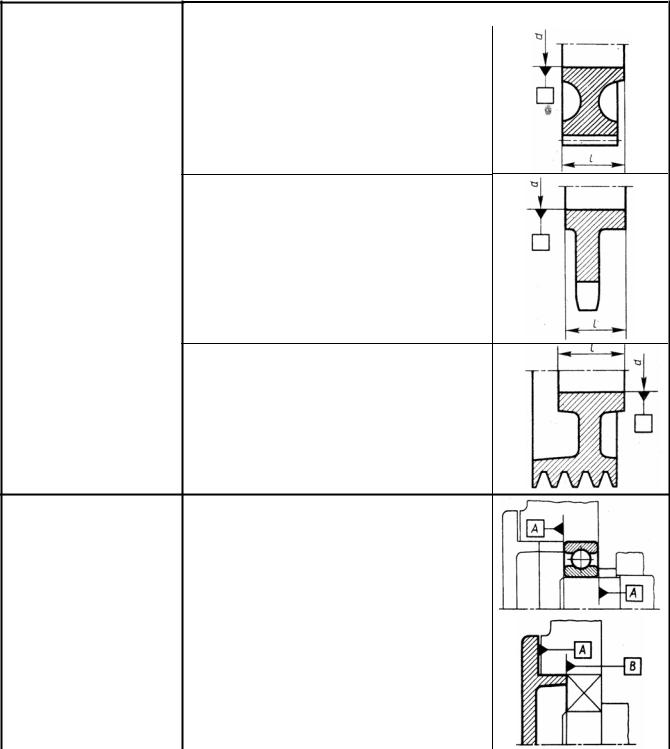
4.1.5.3 Основная база типовых деталей
В таблице 1 приведены типовые детали машин, широко встречающиеся в учебных проектах, и основные базы этих деталей. Знак условного обозначения баз
.
Таблица 1
Основная база |
Примеры деталей |
|
Зубчатые, червячные колеса при l/d < 0,7 |
Звездочки цепных передач при l/d ≥ 0,7
Цилиндр
Шкивы ременных передач, полумуфты при l/d ≥ 0,7
Кольца подшипников качения
Торец
Базовые поверхности, обозначенные буквой
А, предназначены для базирования самих Крышки подшипников качения
деталей, буквой
В— для базирования сопряженных деталей
26
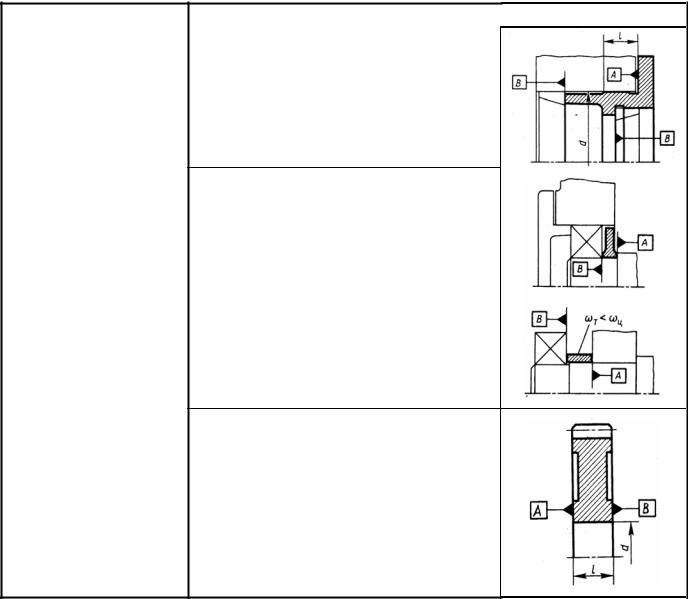
Продолжение таблицы 1
Основная база |
Примеры деталей |
|
|
Стаканы короткие при l/d < 0,7 |
|
Втулки, дистанционные кольца, мазеудерживающие кольца, маслоотражающие шайбы и др.
Торец
Базовые поверхности,
обозначенные буквой А, предназначены для базирования самих деталей, буквой
В— для базирования сопряженных деталей
Зубчатые и червячные колеса при l/d < 0,7
4.2 Конструкции основных деталей и узлов машин и механизмов
Любая машина, механизм состоит из деталей и узлов, агрегатов, которые различным образом соединены между собой.
Детали могут быть простыми (болт, гайка, шайба, шпонка и т.п.) или сложными (корпус редуктора, станина станка, коленчатый вал, блок цилиндров двигателя внутреннего сгорания и т.п.).
Детали частично или полностью объединяют в узлы.
Узел представляет собой законченную сборочную единицу, состоящую из ряда деталей, имеющих общее функциональное назначение (подшипник качения, муфта, редуктор и т.п.). Сложные узлы могут включать несколько простых узлов
27
(подузлов); например, редуктор включает валы с насаженными на них зубчатыми колесами, подшипниками и т.п.
Агрегат — сборочная единица, обладающая полной взаимозаменяемостью, возможностью сборки отдельно от других составных частей изделия.
Среди большого разнообразия деталей и узлов машин выделяют такие, которые входят в состав различных машин, выполняют одну и ту же функцию (болты, валы, муфты, механические передачи и т.п.). Эти детали и узлы называют деталями и узлами общего назначения.
Есть и такие детали, которые встречаются только в определенных машинах,
например, грузозахватные устройства подъемно-транспортных машин, крыльчатка центробежного насоса, лопатки вентилятора и др. Такие детали называют деталями специального назначения или специфическими деталями.
В ходе практического занятия № 2 «Основы конструирования машин, механизмов и их деталей» будут рассмотрены конструкции деталей общего назначения.
По назначению детали машин, механизмов общего назначения классифицируют на: соединения, механические передачи, подшипники, муфты, смазочные и уплотнительные устройства и корпусные детали.
4.2.1 Конструкции соединений деталей машин и механизмов
4.2.1.1 Классификация соединений деталей машин и механизмов
Соединения деталей, применяемые в машиностроении, принято делить на неподвижные, в которых две или несколько деталей жестко скреплены друг с другом, и подвижные, обеспечивающие перемещение одной детали относительно другой (рисунок 11).
Каждый из этих двух типов соединений подразделяют на две основные группы: неразъемные и разъемные.
Неразъемными называются такие соединения, которые могут быть разобраны только путем разрушения или недопустимых остаточных деформаций
28
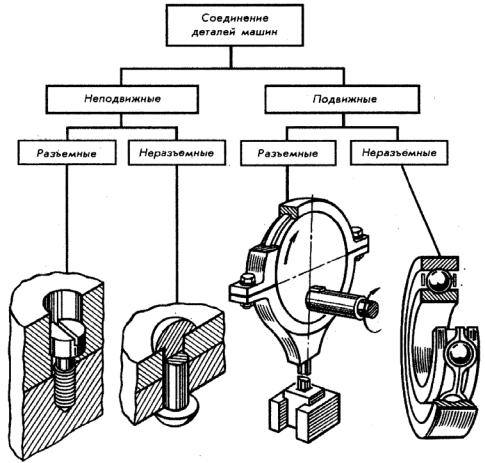
одного из элементов конструкции. Неразъемные неподвижные соединения осуществляются механическим путем (запрессовкой, склепыванием, загибкой,
кернением и чеканкой), с помощью сил физико-химического сцепления (сваркой, пайкой и склеиванием) и путем погружения деталей в расплавленный материал (заформовка в литейные формы, в пресс–формы и т.п.). Подвижные неразъемные соединения собирают с применением развальцовки, свободной обжимки. В основном это соединения, заменяющие целую деталь, если изготовление ее из одной заготовки технологически невозможно или затруднительно и неэкономично.
Рисунок 11
Разъемными называются такие соединения, которые позволяют производить многократную сборку и разборку сборочной единицы без повреждения деталей. К разъемным неподвижным соединениям относятся резьбовые, штифтовые, шпоночные, шлицевые, а также соединения, осуществляемые переходными посадками. Разъемные подвижные соединения
29
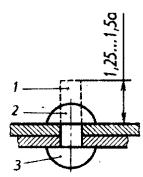
имеют подвижные посадки (посадки с зазором) по цилиндрическим, коническим, винтовым и плоским поверхностям.
4.2.1.2 Неразъемные соединения
4.2.1.2.1 Заклепочные соединения
Заклепочные ( клепаные) соединения относятся к неразъемным соединениям. Чтобы разобрать это соединение, необходимо срубить или высверлить заклепки.
Соединение деталей заклепками показано на рисунке 12.
Рисунок 12
Заклепочное соединение состоит из листов, соединенных с помощью заклепок, вставленных в отверстия в деталях. Функцию соединительных элементов в заклепочных соединениях выполняют заклепки — стержни 1 круглого поперечного сечения с головками на концах. Непоставленные в соединение заклепки имеют по одной головке, которая называется закладкой 3; вторая головка образуется в процессе клепки, ее называют заклепывающей 4. При расклепывании происходит осаживание стержня, который полностью заполняет отверстия, выполненные в соединяемых деталях.
4.2.1.2.1.1 Конструкции и материалы заклепок
Конструкции заклепок разнообразны (рисунок 13). Головки заклепок также могут быть различной формы.
Стандартом предусмотрено несколько типов заклепок нормальной точности общего назначения, основными из которых в общем машиностроении являются: с
30